Сутність процесу зварювання
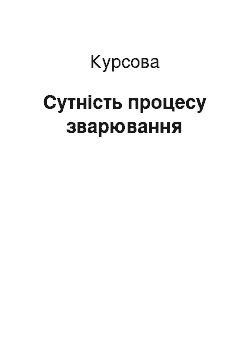
Цей вид зварюванняохоплює ряд споріднених технологій, подібних до зварювання під флюсом (рис. 1.2). Роль флюсу в них відіграє газ, що виходить зі зварювального сопла та охоплює кінець електрода, дугу і зварювальну ванну. Можна одержувати різні характеристики дуги, використовуючи аргон, гелій, вуглекислий газ або суміш перерахованих газів і вводячи при необхідності малі добавки кисню. Головні… Читати ще >
Сутність процесу зварювання (реферат, курсова, диплом, контрольна)
МІНІСТЕРСТВО ОСВІТИ І НАУКИ УКРАЇНИ Кафедра Маркетингу
КУРСОВА РОБОТА
З НАВЧАЛЬНОЇ ДИСЦИПЛІНИ
«Зварювальне виробництво»
на тему «Сутність процесу зварювання»
Зміст Вступ Розділ 1. Загальна характеристика процесу зварювання
1.1 Основні характеристики процесу зварювання
1.2 Класифікація та види зварювання
1.3 Вимоги до якості технології процесу зварювання Розділ 2. Маркування, транспортування та зберігання зварювальних апаратів Висновки Список використаних джерел
Вступ зварювання нагрівання з'єднання Зварювання з’явилося ще в бронзовому віці, коли людина почала набувати досвід при обробці металів для виготовлення знарядь праці, бойової зброї, прикрас та інших виробів.
Першим відомим способом зварювання було ковальське. А із винайденням бронзи, яка є твердішою і гірше піддається куванню, виникло ливарне зварювання.
У 1802 році російський академік Василь Володимирович Петров звернув увагу на те, що при пропусканні електричного струму через два прутики з вугілля або металу між їхніми кінцями виникає яскрава дуга (електричний розряд), яка має дуже високу температуру. Він дослідив та описав це явище, а також указав на можливість використання тепла електричної дуги для розплавлення металів і ти заклав основи дугового зварювання металів.
Але існують відомості про те, що англійський хімік сер Гемфрі Деві в 1800 році першим дослідив електричну дугу і описав можливе застосування її в промисловості.
Лише через 80 років російські інженери — Микола Миколайович Бенардос і Микола Гаврилович Слав’янов застосували відкриття В. В. Петрова на практиці та розробили різні промислові способи зварювання металів електричною дугою. Створені ними способи зварювання є основою сучасних методів електричного зварювання металів.
Бурхливий розвиток зварювальних технологій і обладнань почався за часів світової війни. Британці почали використовувати зварювальні процеси при побудові військових кораблів із суцільнозварними корпусами.
Упродовж 20-х років ХХ ст. головні акценти в зварювальних технологіях ставилися на розвиток автоматичного зварювання. Застосування автоматичного зварювання в оборонній промисловості дало винятковий ефект і забезпечило можливість різкого збільшення випуску бойових машин, боєприпасів і озброєння високої якості. В умовах військового часу застосування під флюсом для виробництва техніки стало вирішальним чинником різкого нарощування обсягів виробництва у стислі терміни.
Зварювання повсюдно витіснило спосіб нероз'ємного з'єднання деталей за допомогою заклепок.
На сьогоднішній день зварювання є найбільш розповсюдженим способом з'єднання детелей при виготовленні металоконструкцій. Широко застосовується зварювання в комплексі з литтям, штампуванням і спеціальним прокатом окремих елементів заготовок виробів, майже повністю відтіснивши складні та дорогі суцільнолиті та суцільноштамповані заготовки.
Розділ 1. Загальна характеристика процесу зварювання
1.1 Основні характеристики процесу зварювання Зварювання — технологічний процес утворення нероз'ємного з'єднання між матеріалами при їх нагріванні та/або пластичному деформуванні за рахунок встановлення міжмолекулярних і міжатомних зв’язків.
Відомо близько 70 способів зварювання. В основу їхньої класифікації покладені дві ознаки: агрегатний стан матеріалу в зоні зварювання та вид енергії, яка використовується для утворення з'єднання.
Для забезпечення зварюваності двох частин матеріалу необхідно зблизити їх настільки, щоб створити можливість для утворення міжатомних зв’язків. Це можливо в тому випадку, коли атоми двох частин матеріалу зближуються на відстань, меншу ніж 4*10−10 м. Такі умови можна створити трьома шляхами:
· стисненням деталей без термічної обробки,
· нагріванням матеріалу до розтоплювання,
· нагріванням до пластичного стану та одночасним стисненням деталей.
Стисненням без нагрівання, можна зварювати в окремих випадках лише пластичні метали: алюміній, мідь, свинець та ін. Це так зване «холодне» зварювання. Другий спосіб застосовується для металів і сплавів, які здатні переходити в пластичний стан при нагріванні до температур, нижчих від температури плавлення (сталь, алюміній та ін.), що дозволяє здійснювати зварювання в пластичному стані шляхом стиснення двох попередньо нагрітих частин металу. При стисненні оксидна плівка плівка на поверхнях дотику руйнується і стає можливим взаємопроникнення (дифузія) кристалічних зерен однієї частини в зерна іншої, що забезпечує їх зварювання. З підвищенням температури нагріву величина зусилля, потрібного для стиснення, зменшується.
Третій спосіб — зварювання плавленням, при якому стиснення деталей не потрібне. Цим способом можна зварювати всі метали і сплави, в тому числі і такі, які при нагріванні не переходять у пластичний стан, а відразу переходять в рідкий стан (чавун, бронза, литті сплави алюмінію та магнію та ін.).
Зварювання забезпечує ряд переваг, основні з яких приводиться нижче:
1. Економія металу внаслідок найбільш повного використання робочих перетинів елементів зварних конструкцій, додання їм найдоцільнішої форми відповідно до діючих навантажень і зменшення ваги з'єднаних елементів. У зварних конструкціях вага металу зварних швів становить від 1 до 2%, у той час як у клепаних вага заклепок і косинок — не менш 4% від ваги виробу. Зварювання дає до 25% економії металу в порівнянні із клепкою, а в порівнянні з литтям в окремих випадках — до 50%.
2. Використання зварювання на будівництві будинків дозволяє зменшити вагу сталевих конструкцій на 15%, полегшує виготовлення й збільшує міцність всієї конструкції. При спорудженні доменних печей застосування зварювання замість клепки дозволяє заощаджувати від 12 до 15% металу, у конструкціях кроквяних ферм — 10−20%, у конструкціях піднімальних кранів — 15−20%.
3. Скорочення строків робіт і зменшення вартості виготовлення конструкцій за рахунок зниження витрати металу та зменшення трудомісткості робіт. Так, наприклад, при будівлі великих доменних печей на металургійних заводах виготовлення кожуха печі зі сталевих листів за допомогою зварювання здійснюється менш ніж за два місяці. Виконання такого кожуха за допомогою клепки вимагає не менше ніж півроку.
4. Можливість виготовлення зварних виробів складної форми зі штампованих елементів замість кування або лиття. Такі конструкції називаються штампозварними і застосовуються в автомобілебудуванні, авіабудуванні, вагонобудуванні. За допомогою зварювання можна виготовляти деталі з металу, що пройшов різну попередню обробку, наприклад зварювати прокатані профілі зі штампованими литими або кутими заготовками. Можна зварювати і різнорідні метали: нержавіючі сталі з вуглецевими, мідь зі сталлю й ін.
5. Можливість широкого використання зварювання і різання при ремонті, де ці способи обробки металу дозволяють швидко та з найменшими витратами відновлювати зношене або несправне устаткування, і зруйновані спорудження.
6. Здешевлення технологічного устаткування, тому що відпадає необхідність у використанні дорогих свердлильних, діропробивних верстатів і клепальних машин.
7. Герметичність одержуваних зварних з'єднань.
8. Зменшення виробничого шуму та поліпшення умов праці робітників.
Зварюванням можна одержати зварні з'єднання із міцністю вищою за міцність основного металу. Тому зварювання широко застосовують при виготовленні досить відповідальних конструкцій, що працюють при високих тисках і температурах, а також при динамічних (ударних) навантаженнях — парових казанів високого тиску, мостів, літаків, гідроспоруд, арматури залізобетонних конструкцій й ін.
1.2 Класифікація та види зварювання При класифікації процессів зварювання виділяють три основних фізичних ознаки:
· форма енергії, яка вводиться в зону зварювання;
· наявність тиску;
· вид інструмента — носія енергії.
Інші ознаки умовно відносять до технічних та технологічних.
За видом енергії, що вводиться у вироб основні зварювальні процеси поділяють на:
1. термічні (Т)
2. термомеханічні (Т М)
3. термопресові (ТП)
4. механічні (М)
5. пресово-механічні (ПМ).
Форма енергії, що застосовується в джерелі енергії для зварювання (електрична, хімічна та ін.), як класифікаційна ознака не використовується, тому що вона характеризує головним чином не процес, а обладнання для зварювання.
Всі відомі в даний час процеси зварювання відбуваються за рахунок уведення двох видів енергії - термічної та механічної, або їх сполучення.
За агрегатним станом матеріалу в зоні зварювання всі способи поділяються на зварювання плавленням або тиском. При зварюванні плавленням характерна відсутність зовнішніх стискуючих зусиль. При зварюванні тиском обов’язковим є стискання.
Класифікація зварювання металів регламентована за фізичними, технічними і технологічними ознаками. За фізичними ознаками всі способи зварювання об'єднані в три класи:
1. термічний,
2. термомеханічний,
3. механічний.
Основою фізичних ознак класифікації є форма енергії, яка використовується для утворення зварного з'єднання.
Основою технічних ознак класифікації є спосіб захисту металу в зоні зварювання, безперервність зварювання і ступінь його механізації.
Технологічні ознаки класифікації встановлюються для кожного виду зварювання окремо. Наприклад, дугове зварювання можна класифікувати за такими ознаками: видом електрода і дуги; характером впливу дуги на основний метал; родом і полярністю зварювального струму та ін. Електрошлакове можна класифікувати за такими ознаками: видом електрода; наявністю коливань електрода; кількістю електродів.
Далі наводиться класифікація видів зварювання за фізичними ознаками, як найбільш розповсюджена.
Термічний клас До термічного класу відносять види зварювання, які здійснюються плавленням основного матеріалу, тобто місцевим розплавленням поєднуваних частин із використанням теплової енергії.
Електродугове зварювання
Електродугове зварювання — зварювання плавленням, під час якого нагрів відбувається електричною дугою, найбільше широко застосовувана група процесів зварювальної технології. Для зварювання необхідне потужнострумове джерело живлення низької напруги, до одного затискача якого приєднується зварна деталь, а до іншого — зварювальний електрод.
Головна роль дугового розряду — перетворення електричної енергії в теплоту. При температурі близько 5500° С газ у розряді є сумішшю іонізованих часток. Характер дугового розряду залежить від присадочного металу, основного металу, захисного середовища, параметрів електричного кола та інших факторів.
Ручне дугове зварювання
Ручне дугове зварювання є найпоширенішим видом електрозварювання, застосовується для зварювання м’якої та легованої сталей, чавуну, нержавіючих сталей, у деяких випадках кольорових металів (рис. 1.1). Електрод має вигляд стрижня діаметром 1,5 — 10 мм, закріплений в ручному електродотримачі.
Рис. 1.1. Ручне дугове зварювання При дотику електрода до металевої зварної деталі, замикається електричне коло, й кінець електрода нагрівається. Якщо потім електрод відвести на 3 — 5 мм від деталі, то встановлюється дуговий розряд, за рахунок якого далі і підтримується струм. Інтенсивне локальне нагрівання викликає розплавлювання основного металу (металу деталі) поблизу дуги розряду. Кінець електрода теж плавиться, і метал електрода вливається в розплавлену «зварювальну ванну» основного металу.
Зварювальник, стежачи за тим, щоб дуговий проміжок не змінювався, веде електродом уздовж стикованих країв зварюваних деталей. При проходженні електрода утворюється розплавлена зварювальна ванна з основного металу і металу електрода, який потім одразу ж кристалізується. В результаті однократного проходження дуги по контуру зварювання утвориться зварювальний валик.
Зварювання під шаром флюсу Даний процес зварювання аналогічний ручному дуговому зварюванні, але відрізняється від нього тим, що електродом служить дріт, який подається з котушки і підводиться до місця зварювання через шар флюсу, який наноситься у міру просування тримача електрода або зварювальної головки. Саму дугу при цьому не видно. Процес зварювання допускає майже повну автоматизацію і може забезпечувати високу продуктивність при великій товщині зварюваних деталей.
Швидкість зварювання за такої технології більша, але потрібен час для підготовки деталей до зварювання. Тому зварювання під флюсом економічно виправдане тільки при великому обсязі робіт.
Зварювання плавким електродом
Цей вид зварюванняохоплює ряд споріднених технологій, подібних до зварювання під флюсом (рис. 1.2). Роль флюсу в них відіграє газ, що виходить зі зварювального сопла та охоплює кінець електрода, дугу і зварювальну ванну. Можна одержувати різні характеристики дуги, використовуючи аргон, гелій, вуглекислий газ або суміш перерахованих газів і вводячи при необхідності малі добавки кисню. Головні переваги таких технологій — можливість зварювання хімічно активних металів (алюмінію, магнію, нержавіючої сталі, міді, нікелю), чистота, можливість візуального контролю, більша швидкість і можливість зварювання в незручних положеннях. Діапазон товщини — від 0,1 мм до дуже великих. Для сопла може бути передбачене водяне охолодження.
Рис. 1.2. Зварювання плавким електродом. 1 — напрямок зварювання, 2 — оболонка захисна, 3 — дріт зварювальний, 4 — газ захисний, 5 — ванна рідкого металлу, 6 — шов зварний, 7 — метал основний.
Важливі різновиди такої технології - дугове зварювання методом обпирання і варіанти імпульсно-дугового зварювання. Ці різновиди дозволяють одержувати деякі специфічні характеристики зварювання за рахунок зміни умов переносу металу через дугу. Вони дають переваги при зварюванні тонких листів у будь-якому просторовому положенні, а також деталей великого поперечного перерізу у вертикальному і навісному положеннях.
Зварювання неплавким електродом
Цей метод відрізняється від попередніх тим, що в ньому використовується короткий вольфрамовий неплавкий електрод. Під дією тепла від дугового розряду плавиться основний метал поблизу дуги. Присадковий метал, якщо він необхідний, підводить окремо у вигляді стрижня або дроту намотаного на котушки. Зона зварювання обдувається ззовні інертним газом (аргоном або гелієм) для захисту від атмосферного повітря.
Такий метод допускає точний контроль як при ручному, так і при механізованому зварюванні деяких металів (алюмінію, магнію, нікелю, нержавіючої сталі) і деталей складних контурів. Параметри зварювальної машини вибираються з урахуванням зварюваного металу і вимог до виробу. Наприклад, при зварюванні алюмінію і магнію зварювальною машиною змінного струму коло зварювального струму повинне доповнюватися високочастотним колом стабілізації дуги, або використовують джерело струму з більшою напругою розімкнутого кола.
Газополум’яне зварювання
Газополум’яне зварювання — зварювання плавленням, під час якого кромки з'єднуваних частин нагрівають полум’ям газів, що спалюються на виході пальника для газового зварювання. Гази зазвичай підводять до зварювального пальника по гнучких шлангах від газових балонів високого тиску, обладнаних редукційним клапаном, що знижує тиск. Зварювальник тримає в одній руці пальник, а в іншій — присадковий прутик. Даний метод особливо підходить для зварювання сталевих трубопроводів малого діаметра, а також для приєднання арматур до трубопроводів, для ремонтних робіт, пайки-зварювання (рис. 1.3).
Рис. 1.3. Кисневе зварювання Обладнання для газового зварювання можна використати для розрізання сталевих елементів товщиною 10 — 15 мм і більше. Існує також спеціальне устаткування для підводного різання. При так званому різанні кисневим списом нагріта сталь окислюється і видувається з утвореного вузького прорізу, тонким струменем кисню, який підводиться під високим тиском.
Електрошлакове зварювання
Електрошлакове зварювання — зварювання плавленням, при якому для нагрівання металу використовують тепло, що виділяється при проходженні електричного струму через розплавлений електропровідний шлак.
Плазмове зварювання
Плазмове зварювання — зварювання плавленням, при якому нагрів кромок деталей, які необхідно з'єднати, відбувається за рахунок тепла потоку плазми, утвореної дуговим розрядом і спрямованої на деталі через сопло.
Електронно-променеве зварювання
Електронно-променеве зварювання — в даному способі зварювання, для нагріву призначених для з'єднання частин використовують енергію електронного променя. Тепло виділяється за рахунок бомбардування зони зварювання спрямованим електронним потоком.
Лазерне зварювання
Місцеве розплавлення призначених для з'єднання частин при лазерному зварюванні здійснюється енергією світлового проміння, отриманого від оптичного квантового генератора — лазера (рис 1.4).
Рис. 1.4. Апарат для лазерного зварювання
Термітне зварювання
При термітному зварюванні використовують тепло, яке утворилося в наслідок спалювання терміт — порошку (суміші алюмінію і окислів заліза).
Термомеханічний клас
Контактне зварювання
Контактне зварювання — технологічний процес утворення з'єднання в результаті нагрівання металу пропущеним через нього електричним струмом і пластичної деформації зони з'єднання під дією направленого на стиск зусилля.
За допомогою контактного зварювання виготовляють до 90% конструкцій, що зварюють тиском, і близько 50% всіх зварних конструкцій. Це показує переваги контактного зварювання перед іншими способами: високою продуктивністю (час зварювання однієї точки або стику становить 0,02…1,0 с), малою витратою допоміжних матеріалів (води, повітря), високою якістю і надійністю зварених з'єднань при невеликому числі параметрів, за якими потрібно слідкувати, що знижує вимоги до кваліфікації зварника. Це екологічно чистий процес, що легко піддається механізації і автоматизації.
Недоліки контактного зварювання: відносна складність устаткування, труднощі неруйнівного контролю зварних з'єднань.
Точкове зварювання
При даному методі кромки призначених для з'єднання металевих листів, накладають один на інший з досить великим напуском, щоб можна було стиснути їх двома електродними стрижнями (з регульованим зусиллям) на час проходження потужного імпульсу струму. Місце контакту двох щільно стиснених поверхонь сильно нагрівається струмом, і в цьому місці вони сплавляються, утворюючи точкове з'єднання. Якщо зварювання виконане правильно, то при тестуванні звареного з'єднання воно руйнується не по зварювальній границі.
Шовне зварювання
Шовне зварювання проходить так само, як і точкове. Різниця між ними у тому, що при шовному зварюванні деталі затискаються між електродами-роликами, які в процесі зварювання обертаються, переміщаючи зварювані деталі. Імпульси зварювального струму виникають один за іншим через установлену паузу. Сукупність багатьох точок, що взаємно перекривають одна одну, утворює суцільний зварний шов.
Стикове зварювання
За допомогою стикового зварювання з'єднують прути, профільний прокат, труби по всій площі їхніх торців (рис. 1.5). Деталі затискають в електродах-лещатах, потім притискають одну до одної з'єднувальними поверхнями, і пропускають зварювальний струм. Розрізняють стикове зварювання опором і оплавленням.
При зварюванні опором деталі притискають із великим зусиллям (2…5 кгс/мм2). Зварювальний струм нагріває деталі до температури 0,8…0,9 від температури плавлення. У стику відбувається пластична деформація, з'єднання утворюється без розплавлення металу. Цим способом не завжди вдається забезпечити рівномірне нагрівання деталей великого перетину по всій площі і досить повно виділити зі стику деталей окисні плівки. Тому стикове зварювання опором застосовують тільки для з'єднання деталей малого перетину (до 200…300 мм2): дротів, труб, прутів з низьковуглецевих сталей.
Рис. 1.5. Стикове зварювання нереривним оплавленням труби газопроводу діаметром 1420 мм При зварюванні оплавленням деталі притискають одна до іншої дуже малим зусиллям при включеному зварювальному трансформаторі. Окремі контакти поверхонь миттєво оплавляються, виникають нові контакти, які оплавляються теж. Під дією електродинамічних сил рідкі прошарки металу оплавлених контактів разом з окислами і забрудненнями викидаються зі стику деталей. Поверхні поступово оплавляються, після чого зусилля стиску різко збільшують — відбувається осад. При цьому протягом 0,1 с через стик ще пропускають струм. Рідкий метал разом із залишковими окислами, витісняється із зони стику в ґрат — з'єднання утворюється між твердими, але пластичними поверхнями. При зварюванні оплавленням хімічно активні зони металів у місцях з'єднання захищають інертними газами.
Дифузійне зварювання
При дифузійному зварюванні поверхні, що з'єднуються, стискають і нагрівають (але не до розплавлювання металу) у вакуумі. Зварний шов утворюється в результаті дифузії одного матеріалу в інший. Застосування такої технології економічно виправдано тільки тоді, коли потрібно виготовляти деталі з дорогих матеріалів (титану, цирконію і т. д.) з дуже малими допусками на розміри. Основні області застосування дифузійного зварювання — авіакосмічна, електронна, інструментальна промисловість, ядерні технології.
Ковальське зварювання
Ковальське (горнове) зварювання — найдавніший вид зварювання стисканням. Протягом майже трьох тисячоліть людство широко користувалося залізом, не вміючи його розплавити, тому до заліза не можна було застосовувати давно відоме ливарне зварювання, і було винайдене ковальське зварювання, спосіб, призначений для заліза. Розквіту і розвитку ковальського зварювання надзвичайно сприяв і сам спосіб виробництва заліза, що існував протягом тисячоліть до другої половини XIX сторіччя.
Суть ковальського зварювання полягає в тому, що при деформуванні відбувається зближення металевих поверхонь, і між атомами кристалічних ґраток починають діяти потужні сили притягання. У випадку, якщо матеріал має високу пластичність, його можна зводити (зварювати) нагріванням у ковальському горні. При виконанні зварювання до зварювального флюсу можна додати обпилки низьковуглецевої сталі: у процесі горіння вони поглинають вуглець, і зварювання виходить при цьому помітно міцнішим.
Механічний клас
Зварювання вибухом
Тепло виділяється локально за рахунок тертя між з'єднуваними поверхнями. Рух викликається контрольованим вибухом, що з величезною силою стискає контактуючі поверхні. У зоні зварювання відбуваються взаємопроникнення хвилеподібної форми і часткова сплавка. Метод застосовується для плакування таких металів, як сталь, стороннім матеріалом, наприклад алюмінієм.
Зварювання тертям
Розігрів поверхонь відбувається за рахунок обертання деталі навколо іншої, нерухомої, зберігаючи контакт між поверхнями. При наступному різкому притисненні поверхонь деталей локалізоване нагрівання приводить до їхньої сплавки.
Ультразвукове зварювання
Зварювання відбувається під дією ультразвукового променя в місці з'єднання попередньо стиснутих деталей. Точковим або безперервним швом зварюються тонкі алюмінієві і мідні фольги, а також пластикові плівки. Зварювальним інструментом служить ультразвуковий випромінювач, який перетворює електричні коливання в механічні. Використовується для запечатування пакувальної алюмінієвої фольги і пластикової плівки. Виконання швидке і економічне.
Індукційне зварювання
Метал нагрівається пропущенням через нього струмом високої частоти після чого різко здавлюється. Струми високої частоти найбільш зручні для введення в метал індукційним безконтактним способом; крім того, вони зручні для концентрації в зоні нагрівання з використанням поверхневого ефекту та ефекту близькості і великого індуктивного опору шунтувальних шляхів. Тому практично завжди використовують струми високої частоти від лампових або машинних генераторів. Найбільше застосування метод знаходить при зварюванні труб.
1.3 Вимоги до якості технології процесу зварювання Утворення зварного з'єднання у зв’язку із уведенням концентрованої енергії до зони з'єднання супроводжується складними фізичними і хімічними процесами (рис. 1.6).
Рис. 1.6. Зварне з'єднання в перерізі
До основних фізичних процесів при зварюванні плавленням відносять електричні, теплові, механічні процеси в джерелах нагріву; плавлення основного і електродного (присадкового) матеріалу, їх перемішування, формування та кристалізація зварювальної ванни; введення і розповсюдження тепла в зварюваному з'єднанні.
До головних хімічних процесів відносять хімічні реакції в газовій та рідкій фазах, на межах фаз при взаємодії компонентів покриттів, флюсів, захисних газів з рідким металом і утворенням оксидів, шлаків, окисленням поверхні тощо.
Фізичні та хімічні процеси при зварюванні відбуваються водночас і в одному місці, тому їх поєднують під загальним визначенням — фізико-хімічні процеси.
Зварне з'єднання при зварюванні плавленням включає до свого складу зварний шов (ділянку зварного з'єднання, яка утворилася в наслідок кристалізації зварювальної ванни), зону сплавлення, зону термічного впливу та основний метал. З'єднання виконане зварюванням тиском в твердому стані складається із зони зварювання, зони термомеханічного впливу, основного металу.
В формуванні структури і властивостей зварного з'єднання при зварюванні плавленням визначна роль належить тепловим процесам, при зварюванні тиском — пластичній деформації (рис. 1.7).
Зварне з'єднання — ділянка конструкції, в якій окремі її частини поєднанні шляхом місцевого сплавлення або спільного пластичного деформування матеріалів цих елементів, у наслідок чого виникає міцне зчеплення матеріалів, яке засноване на міжатомної взаємодії. До складу зварного з'єднання входить зварний шов, зона термічного впливу і прилеглі до неї ділянки основного металлу.
Рис 1.7. Основні типи зварних з'єднань. 1 — стикове без розділення кромок, 2 — кутове, 3 — напускне, 4 — таврове Зварний шов — ділянка зварного з'єднання, утворена в наслідок кристалізації металу зварної ванни.
Зона термічного впливу — ділянка прилеглого до зварного шва основного матеріалу, яка не піддалася розплавленню, структура і властивості якої при зварюванні змінюються внаслідок нагріву та пластичної деформації.
Групи зварних швів:
1. За положенням у просторі — нижні, горизонтальні, вертикальні, стельові. Найпростіші для виконання є нижні шви, найважчі - стельові.
2. За відношенням до діючих зусиль — флангові, торцеві (лобові), комбіновані та косі.
3. За довжиною — неперервні, переривчасті.
4. За ступеню опуклості - нормальні, опуклі та увігнуті.
5. За типом з'єднання — стикові і кутові (валикові).
Типи зварних з'єднань
Стикові з'єднання
Стикові з'єднання є найбільш розповсюдженими майже при всіх способах зварювання, тому що дають найменші власні напруження і деформації під час зварювання.
Стикові з'єднання в основному застосовують для конструкцій з листового металу. Вони потребують мінімальної витрати основного і наплавленого металу і часу на зварювання, можуть бути виконані рівноміцними до основного металу.
Напускні з'єднання
Напускні з'єднання застосовуються переважно при дуговому зварюванні будівельних конструкцій зі сталі товщиною не більше, ніж 10 — 12 мм. Вони не потребують спеціальної обробки кромок, окрім обрізки. Рекомендується зварювати листи з обох боків, у випадку одностороннього зварювання може відбутися потрапляння вологи в щілини між листами і подальше іржавіння в цьому місці.
Таврові з'єднання
Таврові з'єднання широко використовуються при дуговому зварюванні; виконуються без скосу кромок та зі скосами з одного чи обох боків. Вертикальний лист повинен мати достатньо рівно обрізану кромку. При односторонньому і двосторонньому скосі кромки вертикального листа між вертикальним і горизонтальним листами залишається зазор в 2 — 3 мм для кращого провару.
Кутові з'єднання
Кутові з'єднання застосовуються при зварюванні різним чином попередньо оброблених кромок листів. Зварювані частини розташовують під прямим або іншим кутом і зварюють по кромках. Такі з'єднання застосовуються переважно при зварюванні резервуарів, що працюють під незначним внутрішнім тиском газу або рідини.
Прорізні з'єднання
Прорізні з'єднання застосовують у випадку коли довжина нормального напускного шва не забезпечує достатньої міцності. Прорізні з'єднання бувають закритого чи відкритого типу. Проріз зазвичай виконують кисневої різкою.
Торцеві (бокові) з'єднання
В даному випадку листи з'єднуються своїми поверхнями і зварюються по суміжних торцях.
З'єднання з накладками
Даний тип з'єднання використовується у випадках коли з інших причин не можуть бути замінені стиковими або напускними з'єднаннями.
З'єднання електрозаклепками
За допомогою даного типу з'єднання отримують міцні, але не щільні з'єднання. Верхній лист просвердлюється і отвір заварюється так, щоб був захоплений нижній лист.
Класифікація за фізичними ознаками показує, що кожна група процесів може бути реалізована за допомогою певного джерела енергії. Для виконання якісного зварювання джерело енергії повинно відповідати певним вимогам: технологічна і конструктивна доцільність використання; економічність перетворення енергії; обмеження шкідливих побічних ефектів і ін.
Джерело енергії для термомеханічних і механічних процесів зварювання повинно забезпечувати концентрацію теплової і механічної енергії в зоні зварювання, а також тиск достатній для створення фізичного контакту, активації і хімічної взаємодії атомів поверхонь, які з'єднуються.
В зварювальній техніці джерелом енергії є: електродуга, плазма, електронний, іонний, світловий промінь, газове полум’я, ядерні і хімічні реакції. Використовується теплота, яка виділяється при терті, проходженні електроструму через метал або рідкий шлак.
Джерело енергії для термічних процесів зварювання плавленням повинно забезпечувати концентрацію теплової енергії і температури в зоні зварювання або пляма нагріву заданих розмірів, достатнє для плавлення матеріалу і провару його на потрібну глибину, але без інтенсивного випаровування.
При зварюванні металів у процесі їх нагрівання і наступного охолодження виникають значні температурні напруження, а після охолодження виробу — залишкові напруження.
Основними причинами, які викликають напруження і деформації при зварюванні, є нерівномірне нагрівання, усадка наплавленого металу при переході його з рідкого стану в тверду, структурні зміни наплавленого і основного металу в зоні термічного впливу, форма деталей, їх розміри, зона нагрівання при зварюванні.
До основних засобів боротьби з названими вище напруженнями відносяться попереднє підігрівання виробів перед зварюванням, сповільнене охолодження, рекристалізаційний відпал стальних виробів при 550…650° С, легке проковування шва ударянням молотка для багатошарових швів.
Для боротьби з деформацією металу при зварюванні рекомендують зворотноступеневий порядок нанесення швів; деформування деталі перед зварюванням у зворотному напрямі на величину, що виникає при зварюванні; зрівноважування деформацій; збільшення відведення тепла від зварювального виробу; жорстке закріплення елементів при зварюванні в спеціальних пристроях.
Дефекти зварних з'єднань бувають зовнішніми і внутрішніми. До зовнішніх при дуговому і газовому зварюванні належать: нерівномірність поперечного перетину (уздовж швів), незаповнені кратери, підрізи основного металу, зовнішні тріщини, відкриті пори та ін. Внутрішні - непроварювання країв або несплавлення окремих шарів при багатошаровому зварюванні, внутрішні. пори і тріщини, шлакові включення і т.д.
Контактне точкове і шовне зварювання може давати великі вм’ятини в основному металі, пропалювання і виплеск металу, а в середині зварних з'єднань — тріщини, пори та інші дефекти.
Дефекти у зварних з'єднаннях утворюються з різних причин. Так, нерівномірність перетину швів при дуговому і газовому зварюванні пояснюється порушенням режиму зварювання, підрізування — великим струмом і великою потужністю зварювального пальника, утворення пор у зварних швах — насиченістю їх воднем, азотом та іншими газами, тріщин — застосуванням сталей з підвищеним вмістом вуглецю або легуючих домішок, сірки і фосфору, непроварів — мала величина струму або недостатня потужність пальника, погане зачищення кромок тощо.
Основними видами контролю якості зварних з'єднань є: випробування зварних швів на щільність (гідравлічні, пневматичні, часова проба), механічні випробування металу шва і зварних з'єднань (границя міцності, текучості, пластичність, статичний згин, ударна в’язкість), металографічні дослідження (макроскопічний і мікроструктурний аналізи зварних швів), просвічування швів рентгенівськими і гама-променями, ультразвуковий і магнітний методи контролю.
Для створення безпечних умов різних видів зварювальних процесів слід пам’ятати, що всі проводи і струмоведучі частини установок повинні мати добру ізоляцію, їх корпуси, зварювальні кожухи вимикачів — надійно заземлені. Зварювальник повинен мати щитки і шоломи з захисним склом, й брезентові рукавиці, захисні окуляри, спецодяг і спецвзуття. Робоче місце зварювальника має бути огороджене ширмами або знаходитися в спеціальних кабінах, забезпечених приточно-витяжною вентиляцією і місцевими витяжними пристроями.
Особливо уважними слід бути при експлуатації ацетиленових генераторів, кисневих балонів, іншої газозварювальної апаратури. Недопустимим є витік газів із генераторів, трубопроводів, балонів, кидання балонів та ін.
Розділ 2. Маркування, транспортування та зберігання зварювальних апаратів Для зварювання застосовуються зварювальні трансформатори і спеціальні установки на їх основі, зварювальні випрямлячі, перетворювачі й агрегати та ін.
Зварювальний агрегат. Зварювальний арарат складається із генератора постійного струму і приводного бензинового або дизельного двигуна внутрішнього згорання. У ньому хімічна енергія згоряння палива перетворюється в механічну, а потім в електричну енергію. Агрегати використовують в основному для ручного зварювання в монтажних і польових умовах, де відсутні електричні мережі. Зварювальні агрегати можна класифікувати за такими ознаками: за типом генератора — із колекторним і вентильними; за видом привода — із бензиновим і дизельним (іноді електричним) двигуном; за способом установки — пересувні, стаціонарні.
Агрегати мають падаючі зовнішні характеристики і призначені для ручного зварювання в польових умовах, складаються, наприклад, із генератора постійного струму ГД-303 і бензинового двигуна моделі «Волга» (ГАЗ-320−01), зєданих за допомогою фланця.
Двигун моделі ГАЗ-320−01 — бензиновий чотиритактний, чотирьохциліндровий, відрегульований на частоту обертання 2000 об/хв. Потужністю 29 кВт. На двигуні встановлені зарядний генератор, статер, розподільник запелювання і котушка запалювання. Двигун запускають від акумуляторной батареї.
Зварювальні трансформатори забезпечують ступінчасте і плавне регулювання зварювального струму. Вони перетворюють змінну мережну напругу в знижену, необхідну для зварювання. Це найбільш прості і дешеві джерела, широко використовувані при ручному зварюванні й автоматичному зварюванні під флюсом. Спеціалізовані установки на основі трансформаторів застосовують для зварювання алюмінієвих сплавів електродом, що не плавиться, у захисному газі.
Для ручного зварювання застосовують зварювальні трансформатори з рухомими котушками (типу ТД) і рухомими магними шунтами (СТШ-500, СТЩ-500−80).
Зварювальні випрямлячі спочатку знижують зміннц напругу, потім випрямляють її і подають на дугу. Постійний струм має деякі перваги, зокрема більш високу усталеність дуги порівняно з дугою змінного струму. Випрямлячі застосовують для ручного, напівавтоматичного та автоматичного зварювання, а також у якості універсальних джерел. У зварюваьному випрямлячі змінна напруга мережі спочатку перетворюється в знижену, а потім випрямляється і подається на дугу. Випрямлячі можуть допвнюватись різними допоміжними пристроями, що розширюють їх технологічні можливості. Зазвичай окреме джерело призначене для живлення струмом однієї дуги, це однопостове джерело. У цехах із великим числом постів зварювання доцільним є використання багатопостового джерела.
Для ручного дугового зварювання випускають випрямлячі ВД-201, ВД-301, Вд-306, ВД-5.
Зварювальний перетворювач представляє собою комбінацію електродвигуна змінного струму і зварювального генератора постійного струму. У цьому випадку електична енергія мережі змінного струму перетворюється в механічну енергі. Електродвигуна, обертає вал генератора і перетворюється в механічну енергію постійного зварювального струму. Тому ККД перетворювачів невеликий, через наявність обертових частин вони менш надійні і зручні в експлуатації порівняно з випрямлячами. Перетворювачі випускають тільки для ручного і папівавтоматичного зварювання.
Стабілізатори дуги змінного струму подають на дуговий проміжок стабілізуючий імпульс у момент переходу струму через нульове значення. Стабілізатор фактично повторно запалює дугу і підтримуж її горіння, поки напруга зварювального трансформатора не стане достатньою для живлення дугового розряду.
Для поліпшення горіння дуги при зварюванні на змінному струмі використову. ться стабілізатор дуги СД-2 на 50 Гц і стабілізатор для малостійких дуг на 100 Гц.
Стабілізатори дуги на 100 Гц випускають у комплекті зі зварювальними трансформаторами на 250 і 125 А, створюючи живлення «Розряд-250» або «Розряд-125».
Джерело живлення «Розряд-250» складається з трансформатора, аналогічного за побудовую трансформатору ТСМ-250, і стабілізатора на 100 Гц, аналогічного стабілізатору СД-2.
В умовному позначенні зварювального обладнання перша літера означає тип виробів (Т — трансформатор, В — випрямляч, Г — генератор, П — перетворювач, А — агрегат, У — установка); друга — вид зварювання (Д — дугове, П — плазменне); третя — спосіб зварювання (Ф — під флюсом, Г — у захисних газах, У — універсальне джерело декількох способів, П — переносне; відсутність літери вказує на ручне зварювання покритими електродами); четверта — дає подальше пояснення призначення джерела (М — багатопостовий, О — однопостовий). Одну або дві наступні цифри використовують для позначення номінального струму (округлення в сотнях ампер), наступні дві цифри показують реєстраційний номер виробу. Наступна літера означає кліматичне виконання (У — для країни з помірним кліматом, Т — з тропічним), остання цифра показує категорію розміщення джерела: 1 — для роботи на відкритому повітрі, 2 — у приміщеннях, де коливання температури і вологи несуттєво відрізняються від коливань на відкритому повітрі, 3 — у закритих приміщеннях, де коливання температури, вологи і вплив піску і пилу істотно менше, ніж на відкритому повітрі, 4 — у приміщеннях із штучним регулюванням кліматичних умов, 5 — в приміщеннях із підвищеною вологою.
Наприклад умовне позначення, джерела ВДГМ-1602УЗ розшифровується так: В — випрямляч; Д — для дугового зварювання; Г — у захисних газах; М — багатопостовий; 16 — із номінальним струмом 1600 А; 02 — друга модифікація; У — для країн із помірним кліматом; 3 — для роботи в закритих приміщеннях.
Проводи. Для підключення джерел струму до мережі використовують проводи марки ПРГ, для підключення до джерела електротримача — проводи марки ПРГД. Вибір перетину проводів залежить від потужності джерела або сили зварювального струму.
Зварювальні електроди. Це металеві стижні, виготовлені з дротів діаметром 0,3 … 1,2 мм, довжиною 350 … 450 мм, покриті спеціальною обмазкою, до складу якої входять флюси для розкислення меалу шва, що стабілізують дугу добавки і рідке скло як сполучне.
Електроди для зварювання вуглецевих сталей позначають літерою Е і цифрою, що показує середню міцність металу шва. Для зварювання низько вуглецевих сталей застосовують електроди Е38, Е42, Е46, Е50, Е55, Е60. Межа міцності зварного шва 40…50 кг/мм2 (400…500 мПа). Електроди типів Е38А-Е50А застосовують у тому випадку, коли до металу зварного шва пред’являються підвищенні вимоги по чистоті і знижений вміст шкідливих домішок, сірки і фосфору), тобто до підвищеної пластичності.
Електроди Е70, Е85, Е100, Е125, Е150 використовуються для зварювання високо вуглецевих інструментальних сталей. Мічність зварного шва після зварювання цими електродами 70.150 кг/мм2 (700…1500 мПа).
Для зварювання легованих сталей застосовують електроди з легованих сталей. Ці електроди маркують за іншими принципом, наприклад, Е-12Х13, після літери Е казуються хімічний склад металу електрода, тобто марка сплаву.
Для зварювання жароміцних, жаростійких і корозостійких сплавів застосовують електроди типів Е-06Х13Н, Е-10Х17Т, Е-12Х11ПН МФ і т.ін.
Для механізованого зварювання під флюсом і наплавлення під флюсом застосовують зварювальний і плав очний дріт. Дроти виготовляються різних марок. У маркування зварювальних дротів перед маркою матеріалу добавляють літери Св. — зварювальння. Якщо дріт обміднений, то після марки матеріалу дороту ставлять літеру О. Перед літерами Св. Ставлять зазвичай діаметр дроту. Наприклад, 3Св-08А — зварювальний дріт підвищеної якості діаметром 0,3 мм, що містить у середньому 0,08% вуглецю; 1,6Св-О8Г2С-Озварювальний дріт діаметром 1,6 мм, марки О8Г2С (0,08% С, 2% Mn і 1% Si) з омідненою поверхнею. Літера Ш після марки показує, що дріт призначений для зварювання сталі, виплавленої електрошлаковим переплавом 2Св-30Х25Н16-Ш.
Електроди повинні бути упаковані в герметичні пластмасові коробки або в пачки з подальшим укладанням пачок у герметичні металеві або кртонні коробки. Кожну коробку упаковують у поліетилен. Маса коробок з електродами не повинна перевищувати 3 кг — для електродів діаметром до 2,5 мм, 5 кг — для електродів діаметром 3,0…4,0 мм і 8 кг — для електродів діаметром понад 4,0 мм.
Коробки і пачки упаковують у ящики з картону, дерева або плит ДВС. Маса ящиків не повинна перевищувати 50 кг. На ящик наносять напис «Обережно, крихке», «Боїться вологи». На кожній коробці повинна бути етикетка, що містить дані про електроди у відповідності зі стандартом. Кожна партія електродів супроводжується сертифікатом, що засвідчує відповідність електродів вимогам стандарту або технічної умови. Сертифікат містить наступні відомості: товарний знак підприємства, умовне позначення електродів, номер партії і дату виготовлення, марку дроту з зазначенням стандарту, масу партії, кг, і гарантійний термін збереження. Електроди транспортують будь-якими видами транспорту з дотриманням умов, що охороняють їх від впливів атмосферних осадів і механічних ушкоджень. На складах електроди зберігають у сухих, опалюваних приміщеннях при температурі не нижче 15оС на стелажах або піддонах.
Огляд та очищення зварювальної установки та її пускової
апаратури повинні здійснюватись не рідше 1 разу на місяць. Справність електрозварювальних установок слід перевіряти через кожні 6 місяців, звертаючи особливу увагу на стан ізоляції, результати перевірки записувати в журнал обліку, перевірки та випробування електроінструменту. Опір ізоляції обмоток трансформатора відносно корпусу та між обмотками повинен бути не менше 0,5 МОм. Опір ізоляції струмопровідних частин
зварювального ланцюга має бути не менше 0,5 МОм.
Електрозварювальні установки та всі допоміжні прилади
й апарати до них, що встановлюються на відкритому повітрі, повинні
бути захищені від опадів навісами із негорючих матеріалів. Місце установки зварювального апарата повинно мати надійну огорожу та застережні плакати з охорони праці. Виводи електрозварювальної установки повинні бути
прикриті відкидними козирками та мати написи «Мережа 380/220 В»
(U-380/220 В) та рівень напруги холостого ходу; установки для
ручного зварювання додатково повинні бути оснащені покажчиком
значення зварювального струму (амперметр або шкала на регуляторі
струму). У разі прокладення проводів та при кожному їх
переміщенні слід запобігати пошкодженню їх ізоляції, а також
контакту проводів з водою, маслами, сталевими канатами, шлангами
ацетиленових апаратів, газополуменевою апаратурою та з трубопроводами.
У цехах заводів, монтажно-заготівельних майстернях та
за умови довготермінової роботи електрозварника в монтажній зоні
на одному місці встановлюється стаціонарна чи переносна кабіна або
місце роботи зварювальника обгороджується світлонепроникною ширмою
(щитками) чи завісами з негорючих матеріалів заввишки не менше 1,8
м для захисту очей від дії випромінювання електричної дуги.
Просвіт між підлогою і нижньою частиною стінок (ширм) повинен бути
заввишки 150−200 мм для забезпечення доступу свіжого повітря в
кабіну чи обгороджене робоче місце. На зовнішньому боці щитів
роблять написи: «Бережи очі від зварювальної дуги», «Дивитись на
зварювальну дугу без темних захисних скелець небезпечно". Площа
робочого місця електрозварника повинна бути не меншою 4 кв. м,
ширина проходу між робочим місцем і устаткуванням — не менше 1 м.
Не можна ставити зварювальні пересувні машини в захаращених місцях. Ширина проходів до них має бути не меншою 0,8 м, відстань від зварювального апарата до стіни — не менше 0,5 м, відстань між зварювальним та ацетиленовим апаратами — не менше 3 м.
Висновки Звбрювання — технологічний процес утворення нероз'ємного з'єднання між матеріалами при їх нагріванні та/або пластичному деформуванні за рахунок встановлення міжмолекулярних і міжатомних зв’язків.
Відомо близько 70 способів зварювання. В основу їхньої класифікації покладені дві ознаки: агрегатний стан матеріалу в зоні зварювання та вид енергії, яка використовується для утворення з'єднання.
Є три шляхи забезпечення зварюваності двох частин матеріалу: стисненням деталей без термічної обробки; нагріванням матеріалу до розтоплювання; нагріванням до пластичного стану та одночасним стисненням деталей.
Класифікація зварювання металів регламентована за фізичними, технічними і технологічними ознаками. За фізичними ознаками всі способи зварювання об'єднані в три класи: термічний, термомеханічний, механічний.
Основою фізичних ознак класифікації є форма енергії, яка використовується для утворення зварного з'єднання. Основою технічних ознак класифікації є спосіб захисту металу в зоні зварювання, безперервність зварювання і ступінь його механізації. Технологічні ознаки класифікації встановлюються для кожного виду зварювання окремо. Наприклад, дугове зварювання можна класифікувати за такими ознаками: видом електрода і дуги; характером впливу дуги на основний метал; родом і полярністю зварювального струму та ін. Електрошлакове можна класифікувати за такими ознаками: видом електрода; наявністю коливань електрода; кількістю електродів.
Зварне з'єднання — ділянка конструкції, в якій окремі її частини поєднанні шляхом місцевого сплавлення або спільного пластичного деформування матеріалів цих елементів, у наслідок чого виникає міцне зчеплення матеріалів, яке засноване на міжатомної взаємодії.В формуванні структури і властивостей зварного з'єднання при зварюванні плавленням визначна роль належить тепловим процесам, при зварюванні тиском — пластичній деформації.Джерело енергії для термічних процесів зварювання плавленням повинно забезпечувати концентрацію теплової енергії і температури в зоні зварювання або пляма нагріву заданих розмірів, достатнє для плавлення матеріалу і провару його на потрібну глибину, але без інтенсивного випаровування.
При зварюванні металів у процесі їх нагрівання і наступного охолодження виникають значні температурні напруження, а після охолодження виробу — залишкові напруження.
Основними причинами, які викликають напруження і деформації при зварюванні, є нерівномірне нагрівання, усадка наплавленого металу при переході його з рідкого стану в тверду, структурні зміни наплавленого і основного металу в зоні термічного впливу, форма деталей, їх розміри, зона нагрівання при зварюванні.
Основними видами контролю якості зварних з'єднань є: випробування зварних швів на щільність (гідравлічні, пневматичні, часова проба), механічні випробування металу шва і зварних з'єднань (границя міцності, текучості, пластичність, статичний згин, ударна в’язкість), металографічні дослідження (макроскопічний і мікроструктурний аналізи зварних швів), просвічування швів рентгенівськими і гама-променями, ультразвуковий і магнітний методи контролю.
Для створення безпечних умов різних видів зварювальних процесів слід пам’ятати, що всі проводи і струмоведучі частини установок повинні мати добру ізоляцію, їх корпуси, зварювальні кожухи вимикачів — надійно заземлені. Зварювальник повинен мати щитки і шоломи з захисним склом, й брезентові рукавиці, захисні окуляри, спецодяг і спецвзуття. Робоче місце зварювальника має бути огороджене ширмами або знаходитися в спеціальних кабінах, забезпечених приточно-витяжною вентиляцією і місцевими витяжними пристроями.
Особливо уважними слід бути при експлуатації ацетиленових генераторів, кисневих балонів, іншої газозварювальної апаратури. Недопустимим є витік газів із генераторів, трубопроводів, балонів, кидання балонів та ін.
Список використаних джерел
1. Болотников А. А. Товароведение. Ч. II: Курс лекций. — К.: МАУП, 2002. — 144 с.: ил. — Библогр.: с. 140−141.
2. Вікіпедія — http://uk.wikipedia.org
3. Оснач О. Ф. Товарознавство. Промислове обладнання, прилади, інструменти. Навчальний посібник. — К: Центр учбової літератури, 2007. — 304с.
4. Теория сварочных процессов: Учеб. для ВУЗов по спец. «Оборудование и технология сварочного производства» /под ред. В. В. Фролова. — М.: Высшая школа, 1988. — 559 с.
5. Технология конструкционных материалов. Под ред. д-ра техн. наук проф. Г. А. Прейса. — К.: Вища школа. Головное изд-во, 1984. — 359с.
6. Технология и оборудование сварки плавлением /под ред. Г. Д. Никифорова. Учебник для студентов ВУЗов. М.: Машиностроение 1978. — 327 с.
7. Федин А. П. Сварочное производство — Минск «Вышейшая школа», — 1992. ?303 с.
8. Чвертко А. І., Тимченко В. А., Установки і верстати для електродугового зварювання і наплавлення. — К., 1999. — 304с.