Характеристика і вибір вибійних двигунів та установок для проведення капітального ремонту свердловин
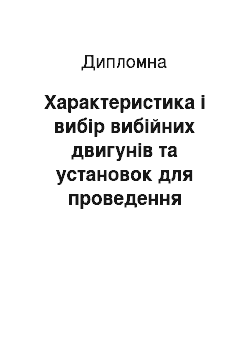
Методи боротьби з формуванням парафінистих відкладень в привибійній зоні пластів Всі відомі методи можна розділити на два напрями: методи попередження формування парафінистих відкладень і методи їх видалення. У свою чергу, кожний напрям можна розділити на ряд груп, вживання яких залежить від технічної озброєності промислів і економічної доцільності того або іншого методу. Великий розвиток в даний… Читати ще >
Характеристика і вибір вибійних двигунів та установок для проведення капітального ремонту свердловин (реферат, курсова, диплом, контрольна)
Удосконалення системи струмовідводу до електробура Е 164−8 МР
1 ІНФОРМАЦІЙНИЙ ОГЛЯД
1.1 Методи підвищення продуктивності пластів Всі існуючі методи підвищення продуктивності добувних і прийомистості нагнітальних свердловин направлені або на зниження гідравлічних опорів в привибійній зоні продуктивного пласта, або на збільшення депресії на пласт. Для зниження гідравлічних опорів в привибійній зоні продуктивного пласта, залежно від причин, що їх викликають, застосовують різні методи дії, з яких найбільш широко поширені кислотні обробки і дія органічними розчинниками. Для збільшення депресії на пласт застосовують різного вигляду методи обмеження притоків води в свердловини. [2]
1.1.1 Физико-хімічна дія на привибійну зону продуктивних пластів В даний час для відновлення і збільшення проникності привибійної зони пласта широке поширення набули різного роду кислотні обробки: солянокислотні, пінокислотні, термокислотні, газокислотні і глинокислотні. Головною метою кислотних обробок є досягнення максимального нафтовилучення. Це можливо при залученні в експлуатацію низкопроникних і раніше закольматованих пропластків. Особливу важливість набувають кислотні обробки, разом з іншими видами дії на привибійну зону продуктивних пластів, при експлуатації родовищ в складних гірсько-геологічних умовах, коли поклади мають великі поверхи нефтегазоносності і складені низькопроникними пісчано-алевролітовими пластами з прослоями глин і аргилітів. По своїй істоті физико-хімічна дія на привибійну зону не може не приводити до підвищення продуктивності свердловин. Проте, з огляду на те, що ці процеси є багатокомпонентними, їх ефективність визначається сумою чинників, залежних від властивостей об'єкту дії (пласт і свердловина), достовірності причин, що зумовили зниження продуктивності і відповідності запроектованого методу і його технології об'єкту. Тому вибір методу дії і технології його здійснення повинні базуватися на ретельному і багаточинниковому аналізі і вивченні зв’язків між об'єктом дії - конкретною свердловиною з її геолого-технічною характеристикою і предметом дії - методом з його механізмом, технологією і регламентом вживання.
До одного з прогресивних методів кислотних обробок, вживаних в даний час, можна віднести дію на привибійну зону продуктивного пласта азотною кислотою. Ефективність вживання азотної кислоти і композицій на її основі забезпечує те, що сама азотна кислота і продукти її реакції з породою пласта знижують в’язкість нафт з великим змістом асфальто-смолянистих речовин. Крім того, продукти реакції азотної кислоти з породою пласта надають деемульгуючу дію на обводнюючу пластову нафту. Проте різні кислотні склади на основі азотної кислоти, як і чиста азотна кислота, надзвичайно сильні окислювачі. Використання останньої для кислотних обробок викликає сильну корозію і руйнування елементів ущільнювачів і устаткування нафтопромислу.
Тому, якщо одержати продукт на основі азотної кислоти, якому були б властиві всі її позитивні властивості, окрім одного — високої корозійної активності, можна з упевненістю сказати про появу нового напряму в розробці технологічних процесів по кислотній дії на продуктивний пласт. [2]
1.1.2 Методи боротьби з формуванням парафінистих відкладень в привибійній зоні пластів Всі відомі методи можна розділити на два напрями: методи попередження формування парафінистих відкладень і методи їх видалення. У свою чергу, кожний напрям можна розділити на ряд груп, вживання яких залежить від технічної озброєності промислів і економічної доцільності того або іншого методу. Великий розвиток в даний час як у нас в країні, так і за рубежем одержав напрям по попередженню формування парафінистих відкладень. По своєму технологічному єству їх можна розділити на ряд груп: гідродинамічні методи, засновані на підтримці тиску, при якому ще не проходить випадання парафіну з пластової нафти в привибійній зоні продуктивних пластів; теплові методи, засновані на підтримці в пласті температури, вище за температуру плавлення парафіну; і нарешті, хімічні методи, що припускають використання розчинів полімерів і композицій на їх основі.
Методи видалення парафінистих відкладень підрозділяються на теплові, що використовують для видалення парафінистих відкладень енергію різних теплоносіїв і нагрівальних елементів на найпрогресивніші хімічні методи очищення привибійної зони продуктивних пластів і промислового устаткування різними хімічними реагентами і їх композиціями.
До теперішнього часу на промислах Прикарпаття проблема боротьби з парафінистими відкладеннями розв’язувалася, в основному, шляхом вживання теплових методів. Проте їх вживання приводить до великих матеріальних і трудових витрат. Так, наприклад, для проведення однієї термообробки на свердловинах Бистрицкого родовища необхідні одна-дві паротеплові установки, дві автоцистерни з теплоносієм і бригада робітників. Тривалість однієї операції складає порядку однієї робочої зміни. Якщо врахувати, що періодичність теплових обробок складає в середньому 10−15 днів, а кількість свердловин, що постачають нафту, 14, то доцільність вживання даного методу в умовах Бистрицького родовища стає очевидною. Тому назріла необхідність в умовах Прикарпатських родовищ, що добувають високопарафіністу нафту, знайти самі відповідні і рентабельні методи видалення парафінистих відкладень в привибійній зоні продуктивних пластів. Такими методами можуть бути хімічні методи депарафінізації за допомогою різних хімічних реагентів і композицій на їх основі. Практика вживання цих методів на промислах країни показала доцільність і рентабельність їх вживання. Проте індивідуальність підходу до вибору хімічних реагентів і композицій на їх основі ообумовлює необхідність більш глибокого і детального підходу до вибору найефективніших з них. [2]
1.1.3 Методи ізоляції і обмеження притоків пластових вод в свердловини Обмеження притоків пластових вод входить в комплекс заходів щодо збільшення продуктивності свердловин і підвищення нафтовіддачі пласта.
При проведенні робіт по обмеженню водопритоків переслідують наступні цілі: скорочення об'ємів попутної води, що видобувається, збільшення дебіта свердловин по нафті і регулювання процесу розробки родовища або окремих його блоків, зокрема, шляхом поліпшення характеру витіснення нафти водою в районі свердловини або групи свердловин. Важливо відзначити, що кінцевий результат по всіх показниках безпосередньо пов’язаний з якістю проведення ізоляційних робіт — досягнутою вибірковістю. Так, наприклад, в НГДУ «Долінанефтегаз» ВАТ «Укрнафта» з 5 проведених в 1990 році операцій по обмеженню водопритоків в свердловинах тільки 2 з них були успішними. В результаті по двох цих свердловинах вдалося понизити притоки води на 13 305 м3, що склало 0,6% від загального об'єму попутно здобутої води по НГДУ. В цілому по ВАТ «Укрнафта» в 1990 р. операції по обмеженню водопритоків проведені на 44 свердловинах, що складає 2% від діючої фундації. Додатково ж здобуто нафти в результаті проведених операцій 20 430 тонн, що складає 0.46% від річного об'єму добичі.
Таким чином, як випливає з приведеного аналізу, розраховувати на те, що при нинішніх об'ємах використання заходів щодо обмеження водопритоків і кількості води, що попутно здобувається, ізоляційні роботи істотно скоротять витрати на підйом вод, немає підстави. До того ж тут необхідно відзначити і те, що упевнено вибрати свердловину, обмеження притоків води в якій привиде до позитивного результату, складно.
Виходячи з цього, нами на перший план висувається мета — збільшення дебіта свердловини по нафті після проведення заходів щодо обмеження водопритоків.
У разі якісного проведення робіт на їх результат впливають два чинники: ступінь зниження продуктивності свердловини і можливість підйомного устаткування.
Пропонована зміна продуктивності свердловин в результаті ізоляційних робіт, разом з характеристикою роботи підземного устаткування, повинна враховуватися при обґрунтуванні доцільності проведення робіт на даній свердловині. Оскільки коефіцієнт продуктивності свердловини після ізоляційних робіт зменшується, то точка спільної роботи пласта і підйомника зміщуватиметься у бік великих депресій на пласт. Залежно від ступеня зменшення коефіцієнта продуктивності при цьому ж підйомному устаткуванні і режимі його роботи можливе істотне зниження дебіта свердловини, якщо точка спільної роботи переміщається в область низьких продуктивностей підйомника. Якщо зміна продуктивності така, що точка спільної роботи переміщається в області мало змінної продуктивності підйомника, то дебіт свердловини після ізоляційних робіт зміниться трохи. Для газліфтних свердловин можливе навіть збільшення дебіта свердловин по рідині, якщо точка спільної роботи переміщається з області оптимальної витрати робочого агента в область максимальних продуктивностей. Тому, допускаючи вірогідність зниження коефіцієнта продуктивності по нафті при переважному його зниженні по воді, найбільший приріст дебіта свердловини по нафті буде досягнутий, якщо після ізоляційних робіт точка спільної роботи пласта і підйомника залишатиметься в області максимальної продуктивності. Менш сприятливі умови, в яких збільшення депресії на пласт приведе до різкого зниження продуктивності підйомника. В цьому випадку падіння дебіта свердловини по рідині складно компенсувати зменшенням обводнення продукції, дебіт свердловини по нафті виявиться нижче, ніж до проведення ізоляційних робіт, навіть якщо частка нафти в продукції буде збільшена. [2]
1.2 Аналітичний огляд існуючих конструкцій мобільних бурових установок для підземного ремонту свердловин Для підземного ремонту свердловин, які не обладнанні стаціонарними вишками, застосовують підіймальні установки — агрегати. які являють собою змонтовану на транспортній базі лебідку, вишку з талевою системою та іншим обладнанням й інструментом. З їх допомогою при підземному ремонті на свердловинах проводяться операції, пов’язані із спуском або підйомом свердловинного експлуатаційного обладнання, яке знаходиться в середині свердловини, а також обладнання різного типу, яке використовується при проведенні технологічних операцій. Застосовувані при підземному ремонті агрегати поділяють на агрегати, які призначенні для поточного і капітального ремонтів. Останні мають більш високу вантажопідіймальність і крім обладнання, призначеного для поточного ремонту можуть бути обладнанні також промивочним насосом, ротором, вертлюгом та іншими пристроями для обертання колони Установка тракторна підіймальна УПТ-1−50 призначена для спускопідйомних робіт з насосними штангами, насосно-компресорними і бурильними трубами в процесі поточного і капітального ремонту свердловин, не обладнаних стаціонарними вежами.
Установка, змонтована на тракторі Т-130МГ-1, складається з телескопічної двухсекціоної вежі висотою 19 м і однобарабанного лебідочного блоку з приводом від двигуна трактора.
Технічна характеристика:
Вантажопідйомність, т 50;
Потужність приводу, кВт 117,6;
Габаритні розміри, мм 11 100×2475×4090;
Маса, кг 24 530.
Агрегат А-50У призначений для спускопідйомних операцій при поточному і капітальному ремонті свердловин глибиною до 3500 м з укладанням труб на містки, розбурювання цементної пробки в колонах діаметром 141−168 мм і їх промивання.
Таблиця 1.2.1
Характеристика агрегату А-50У при оснащенні талевої системи 4х3
Швидкість | Швидкість каната, м/с | Швидкість талевого блоку, мм | Частота обертання вала барабана, об/хв | Вантажопідйомність, т | |
I | 1,088 | 0,181 | 39,8 | 50,0 | |
ІІ | 1,9 | 0,317 | 69,8 | 34,5 | |
ІІІ | 4,17 | 0,695 | 153,0 | 12,6 | |
IV | 7,8 | 1,215 | 268,0 | 7,5 | |
Агрегат складається з трансмісії, двобарабанної лебідки (піднімальний і тартальный барабани), телескопічної вежі з талевою системою, ротора з гідроприводом, компресора, гідродомкратів підйому, вежі і системи керування агрегатом і лебідкою. Вантажопідйомність агрегату при роботі піднімального барабана лебідки й оснащенню талевої системи 4×3.
Максимальний натяг підіймального каната — 100 кн, тартального — 73 кн, діаметр талевого каната 25 мм, тартального — 13 мм.
Телескопічна щогла в робочому положенні має кут нахилу 6°, висота її до осі чотирьохроликового кронблока, що має спеціальний ролик для тартального каната, 22 400 мм.
Керування механізмами агрегату, оснащеного обмежником підйому крюкоблока, пневматичне від компресора М-155−2. Охолодження гальм підіймального і тартального барабанів повітряне.
Привід навісного устаткування агрегату і промивного насосу здійснюється від ходового двигуна автомобіля КрАЗ-257 при роботі на прямій передачі. Добір потужності здійснюється від розподільної коробки автомобіля.
Частота обертання вала і потужність ротора приведені нижче.
Швидкість І, ІІ;
Частота обертання, про/хв 40, 70;
Потужність гідравлічного двигуна М-20, квт 23,5, 44.
Максимальний тиск у гідросистемі приводу ротора 13 МПа, а робочий 8 МПа.
Промивний насос 9 МГР змонтований на двохосьовому автопричепі 2ПН-2. Максимальний тиск насоса дорівнює 16 МПа при подачі 6,1 дм3/с. Максимальна подача 9,95 дм3/с і забезпечується при тиску 6 МПа.
Габаритні розміри агрегату (у мм): довжина — 12 460, ширина — 2650, висота — 4160, маса агрегату без насосного причепа 22 400 кг, маса насосного причепа 4124 кг. 1]
Агрегат АзІНМАШ 37-а максимальною вантажопідйомністю 32 т, змонтований на шасі автомобіля Краз-255Б, призначений для поточного ремонту сверловин глибиною до 2900 м. Привід навісного устаткування лебідки здійснюється від тягового двигуна автомобіля ЯМЗ-238 потужністю 176 квт при частоті обертання вала 2100 про/хв через коробку швидкостей і розподільну коробку автомобіля.
Агрегат комплектується автоматом АПР-2ВБ або АПР-ГП (гідропривідний) при використанні НКТ і автоматом АШК-Т — при використанні штанг.
Вежа зварна, решітчаста, телескопічна, двохсекційна з відкритою передньою гранню. Забезпечена вона обмежниками підйому верхньої секції і підйому крюкоблока. При досягненні крюкоблоком критичного верхнього положення обмежник відключає фрикціон лебідки і включає гальмо.
Талева система складається з одноосьового чотирьохроликового кронблока і крюкоблока 2КРБ2×28 (двохроликового талевого блока і трирогового гака з амортизаційною пружиною).
Гідравлічна система забезпечує підйом вежі і домкратів задньої опори, а також служить приводом для лебідки висування верхньої секції вежі й автомата АПР-ГП для згвинчування і розгвинчування НКТ.
Пневматична система призначена для керування муфтами вмикання барабана, гідронасоса, дистанційного керування зщепленням двигуна, керування гальмом при спрацюванні протизатискувача. Керування гальмовим пристроєм лебідки — ручне з пневматичним підсилювачем від ножної педалі. Відстань від осі опорних домкратів домкратів до центру свердловини повинне бути 1500 мм. Оснастка талевої системи 3×2, максимальний діаметр каната 21,5 мм.
Габаритні розміри агрегату 10 180×2700×4000 мм, маса його 19 600 кг, у тому числі заправлення 300 кг.
Освітлення агрегату, робочої площадки і містків здійснюється вибухобезпечними світильниками ФВН-64−1 і ФВН-64−2 з подачею енергії від базового генератора або від мережі через трансформатор і вирівнювач.
Установка для поточного капітального ремонту свердловин КОРО-80. Комплекс використовується при спуско-підйомних операціях з них та бурильними трубами при розбурюванні цементних мостів, ловильних роботах, фрезеруванню, нагнітанні в свердловину рідин і проведенню робіт по капітальному та поточному ремонті до 5000 м.
Таблиця 1.2.2
Технічна характеристика агрегату Азинмаш-37А
Номінальна вантажопідйомність, т | ||
Максимальна вантажопідйомність, т | ||
Діаметр бочки барабанам, мм | ||
Довжина бочки барабана, мм | ||
Діаметр гальмового шківа, мм | ||
Число гальмових шківів | ||
Число гальмових стрічок | ||
Ширина стрічки, мм | ||
Охолодження гальма | Повітряне, примусове | |
Висота вишки від землі до осі кронблока, м | ||
Висота підйому гака, м | ||
Комплекс складається з трьох блоків: самохідної підйомної установки УПА-80, змонтованої на чотирьохвісному автомобілі МАЗ-537 високої прохідності, насосного блоку БНП-15 Гр, змонтованому на двовісному причепі МАЗ-8926. [1]
КОРО-80 комплектується малогабаритним ротором р-200, промивочним вертлюгом ВП-80×200, механізованими ключами КгП з гідроприводом (для бурильних труб діаметрами 73 та 89 мм), механізованими ключами АПР-ГП для насосно-компресорних труб і комплектом інструмента для спуско-підйомних операцій.
Установка для ремонту свердловин TW 125 СА-А6-МАЗ 547 змонтована на автошасі МАЗ 547 з двигуном Caterpillar при 3408 С-DITA 505 СР/200 об/хв. І трансмісією Allison м/s 5000 С з конвертом ТС 6800.
Технічна характеристика:
Максимальна робоча вантажопідйомність на крюку
(з відтяжними дошасі), тс125
Статична вантажопідйомність вежі (з відтяжками до шасі), тс150
Максимальна довжина підіймальних труб, м18
Діаметр талевого канату, мм25
Кількість передач на лебідці5 + 1 R
Максимальна робоча глибина для підземного ремонту свердловини НКТ 2 7/8ґґ, м7100
НКТ 3 ½ґґ, м6700
НКТ 4 ½ґґ, м4800
ремонту свердловин з трубами 2 7/8ґґ, м5200
ремонту свердловин з трубами 3 ½ґґ, м4800
ремонту свердловин з трубами 4 ½ґґ, м3500
Висота вежі, м33,4
Максимальна швидкість вітру з максимальним навантаженням на крюку, км/год 70
без навантаження на крюку, км/год120
Рівні установки балкона верхнього робочого:
рівень І, м15,3
рівень ІІ, м16,5
рівень ІІІ, м17,7
рівень IV, м21,4
Ємність для складання свічок 18 м для:
БТ 4 ½ґґ, м3000
БТ 3 ½ґґ, м4000
Робоча температура, °С29 ч 49
Силовий блок установки САТ 3408 С-РІТА 505 к. с/2100 об/хв.
Автошасі МАЗ 547
тип автошасі МАЗ 547;
двигун — тип ЯМЗ;
потужність 350 к. с/2100 об/хв;
гідродинамічна трансмісія 8401/10−14
кількість швидкостей 4 + 2R;
міжосьова відстань 2300;
формула коліс 12×12.
При даному обладнанні і інструменті цією установкою можливо виконувати слідуючи операції:
— підйом та спуск НКТ;
— підйом та спуск глибинних насосів;
— фрезерування;
— буріння;
— нагнітання в свердловину рідини та проведення робіт по капітальному ремонту свердловини до 7100 м.
Установка УПА 60А (60×80) призначена для освоєння, підземного та капітального ремонту свердловин, виконує операції:
— розбурювання цементних пробок в трубах діаметром 146−168 мм (5−6ґґ);
— спуск і підйом НКТ і бурильних труб, промивка свердловин;
— встановлення експлуатаційного обладнання на усті свердловини;
— проведення ремонтних робіт і робіт по ліквідації аварій.
Всі механізми установки, за виключенням промивочного насоса монтуються на шасі автомобіля КрАЗ-65 101. 1]
1.3 Аналітичний огляд вибійних двигунів, що застосовуються при КРС
1.3.1 Турбобури Турбобур є забійний гідравлічний двигун з багатоступінчатою турбіною. Гідравлічна енергія потоку бурового розчину приводить в обертання вал, сполучений з валом шпінделя і долотом. Для різних умов буріння вітчизняна промисловість випускає турбобури, що розрізняються по діаметру, числу секцій, розташуванню і конструкції опор і пристрою турбінних апаратів. Уніфікована секція турбобура, вживана для одноі багатосекційних турбобурів, не має осьової опори, а осьові навантаження сприймаються опорою, розташованій в секції шпінделя.
Рисунок 1.3.1 — Уніфікована турбінна секція турбобура ЗТСШ-195
Уніфікована турбінна секція турбобура ЗТСШ-195 (рисунок 1.3.1) складається з перевідника 1, згвинченого на конусному різьбленні з корпусом 8, в якому знаходяться пакети статорів гідрогальма 7 і турбіни 10, що стискаються регулювальними кільцями 11 і фіксуються нижнім перевідником 12. Цей перевідник забезпечений ніпелем з конусним замковим різьбленням, до якого приєднується друга секція турбобура або секція шпінделя, а при транспортуванні нагвинчується ковпак Група деталей, що обертається: регулююче кільце 3, втулки ущільнення 4 і розпір 5, радіальні опори середня і верхня 6 і пакети роторів гідрогальма 7 і турбіни 10, закріплені на валу секції 9 стягнутою напівмуфтою 2.
У багатосекційних турбобурах вали секцій з'єднуються за допомогою конусних або шліцьових муфт на різьбах з невеликим кутом конусності.
Рисунок 1.3.2 — Ступінь секції турбобура Турбіна складається з великого числа ступенів (до 370). Кожен ступінь (рисунок 1.3.2) складається із статора із зовнішнім 2 і внутрішнім 3 ободами, між якими розміщені лопатки 4, і ротора, обід 1 якого забезпечений лопатками 5. Лопатки статора і ротора розташовані під кутом один до одного, унаслідок чого потік рідини, що поступає під кутом з каналів статора на лопатки ротора, міняє свій напрям і тисне на них. В результаті цього створюються сили, прагнучі повернути закріплений на валу ротор в один бік, а закріплений в корпусі статор — в інший.
Далі потік розчину з каналів ротора знов поступає на лопатки статора другого нижче розташованого ступеня, на лопатки її ротора, де знов змінюється напрям потоку розчину. На роторі другого ступеня також виникає момент, що крутить. В результаті розчин під дією енергії тиску, що створюється буровим насосом, розташованим на поверхні, проходить всі ступені турбобура. У багатоступінчатій турбіні розчин рухається уздовж її осі. Активний крутний момент, створюється кожним ротором, підсумовується на валу, а реактивний (рівний по величині і протилежний по напряму), створюваний на лопатках статора, підсумовується на корпусі турбобура.
Реактивний момент через корпус турбобура передається сполученій з ним бурильній колоні, а активний — долоту. На створення крутного моменту перепад тиску, що спрацьовує в турбобурі, складає від 3 до 7 Мпа, а іноді і більш. Це є великим недоліком турбобура, що поглинає значну частину енергії, що створюється насосом і витрачає її на обертання долота, а не на очищення і ефективне руйнування забою свердловини, що практично виключає можливість застосування доліт гідромоніторів.
1.3.2 Гвинтовий вибійний двигун Гвинтовий двигун є забійний агрегат (рисунок 1.3.3) з гідравлічним об'ємним двигуном, що приводиться в дію потоком бурового розчину, який закачується в бурильну колону з поверхні насосами.
Гвинтовий двигун складається із статора і ексцентрично розташованого гвинтового ротора, що є як би зубчатою парою з внутрішнім зачепленням з гвинтовими зубами. Число зубів статора на один більше зубів ротора, що дозволяє йому здійснювати планетарний рух, як би обкатуючись по зубах статора: вісь ротора при цьому рухається по колу діаметром, рівним подвійному ексцентриситету е. Для з'єднання ротора з валом шпінделя, співісного розташованого з корпусом, служить кульова двохшарнірна муфта, компенсуюча ексцентриситет.
Шпіндель гвинтового двигуна схожий по конструкції з шпінделем турбобура. Він укріплений на радіальних резинометалевих підшипниках і забезпечений кульовою п’ятою для сприйняття осьового навантаження. Вал шпінделя — порожнистий, у верхній частині забезпечений каналами для проходу рідини до долота, що приєднується через перевідник до нижньої частини валу двигуна. Корпус останнього через перевідник прикріпляється до нижньої частини бурильної колони.
Рисунок 1.3.3 — Гвинтовий вибійний двигун: 1, 6, 7 — верхній, середній і нижній перевідники; 2 — переливний клапан; 3 — ротор; 4 — статор; 5 — двохшарнірне з'єднання; 8 — сполучна муфта; 9 — корпус шпінделя; 10 — упорна багаторядна кульова опора; 11 — радіальний підшипник; 12 — вал шпінделя; 13 — ніпель; 14 — наддолотний перевідник.
Гвинтові двигуни і насоси мають ряд переваг, що дозволило використовувати їх як гідравлічні забійні двигуни:
відсутність клапанних і золотникових розподільників потоку рідини;
відсутність відносного переміщення деталей пари, що труться, ротор — статор;
безперервна зміна положення лінії контакту робочих органів при обертанні ротора дозволяє потоку бурового розчину видаляти абразивні частинки з камер і шлюзів.
1.3.3 Електробури Електробур служить для приводу в обертання долота. Він є забійним агрегатом з електричним двигуном трифазного змінного струму. Електроенергія до нього передається з поверхні по кабелю, розташованому усередині колони бурильних труб. Устаткування на установці при бурінні електробуром застосовується в основному таке ж, як і при бурінні роторним або турбінним способом. Електробурами бурять свердловини глибиною до 5000 м.
Декілька відмінною є схема електропостачання електробурової установки. Силовий трансформатор потужністю 630 КВт з номінальним струмом 155 А має дві вторинні обмотки. Одна з них служить для живлення електробура і має 25 ступенів регулювання напруги в межах 1100— 2300 В. Друга вторинна обмотка напругою 525 В призначена для живлення електродвигунів приводу лебідки і ротора.
На установці застосовується додатково комплектний пристрій для включення і захисту електробура, вимірювання електричних параметрів і сигналізації про стан електробура. Цей пристрій складається із станції управління, навісних шаф, вольтметра і трьох амперметрів, блоку вимірювання опору ізоляції системи токопроводу — електробур і кнопки для включення і виключення електробура.
Рисунок 1.3.4 — Схема живлення електробура по системі два дроти — труба На рисунку 1.3.4(а) показана компоновка бурильної колони з електробуром, що складається з асинхронного трифазного електродвигуна 8 змінного струму з короткозамкненим ротором, редуктора-вставки 9 для зниження частоти обертання, шпінделя 10 для сприйняття осьових навантажень, до якого приєднується долото 11. Двигун електробура сполучений з пристроєм для контролю його ізоляції 7.
У бурильну колону також входять УБТ 6 і бурильні труби 5, зворотний клапан 4, привідна труба 3, усередині яких розташований кабель, що підводить електроенергію до електробура. Струм до електровертлюга 2 поступає від силового трансформатора. Бурильна колона сполучена із звичайним вертлюгом 1, підвішеним на крюку до талевої системи бурової установки.
На рисунку 1.3.4(б) показана схема підведення струму до електробура по системі два дроти — труба (ДПТ), третій дріт електродвигуна сполучений з колоною труб.
Тиск на долото для руйнування породи так само, як і при роторному бурінні, створюється нижньою частиною бурильної колони, яка сприймає реактивний момент. Розбурена порода виноситься на поверхню буровим розчином по кільцевому простору між стінками свердловини і бурильною колоною. Буровий розчин, що нагнітається насосами через вертлюг всередину колони бурильних труб з кабелем, підводиться до електродвигуна і по його порожнистому валу через отвори у валах редуктора вставки і шпінделя поступає до долота. Двигун, редуктор і підшипники шпінделя наповнені маслом і мають систему захисту від проникнення всередину бурового розчину.
Перевагами електричного двигуна в порівнянні з гідравлічним є: незалежність частоти обертання від навантаження на долото, моменту і інших параметрів від кількості рідини, що подається, її щільності і фізичних властивостей і глибини свердловини; постійність частоти обертання, велика перевантажувальна здатність електродвигуна; можливість контролю кривизни, відхилення стовбура свердловини і процесу роботи з поверхні землі. До недоліків електродвигуна відносяться необхідність одночасної подачі до забою двох видів енергії - електричної і гідравлічної і складність конструкції.
2. ОПИС ТЕХНОЛОГІЧНОГО ОБЛАДНАННЯ
2.1 Гвинтовий вибійний двигун За прототип приймаємо вибійний гвинтовий двигун Д1−95. Він відноситься до машин об'ємної (гідростатичної) дії. За принципом дії гвинтової вибійний двигун являє собою планетарно-роторну гідравлічну машину об'ємного типу з внутрішнім косозубим зачепленням.
Двигун містить ротор і статор, поперечний переріз яких показано на рисунку Сталевий статор усередині має привулканізовану гумову обкладку з гвинтовими зубами лівого напрямку. На сталевому роторі нарізані зовнішні гвинтові зуби також лівого напрямку. Число зубів ротора на одиницю менше числа зубів статора, у результаті чого для здійснення зачеплення вісь ротора зміщена щодо осі статора на величину ексцентриситету, рівну половині висоти зуба. Кроки гвинтових ліній ротора і статора прямо пропорційні числу зубів. Спеціальний профіль зубів ротора і статора забезпечує їхній безупинний контакт між собою, утворюючи на довжині кроку статора одиничні робочі камери.
Промивна рідина, що надходить у двигун від насосів бурової установки, може пройти до долота тільки в тому випадку, якщо ротор повертається щодо статора, обкатуючись під дією неврівноважених гідравлічних сил.
Ротор, роблячи планетарний рух, повертається по годинниковій стрілці (абсолютний рух), у той час як геометрична вісь ротора переміщається щодо осі статора проти годинникової стрілки (переносний рух).
За рахунок різниці в числах зубів ротора і статора переносний рух редукується в абсолютне з передаточним числом, рівним числу зубів ротора, що забезпечує знижену частоту обертання і високий крутний момент на виході.
Загальний вигляд двигуна показаний на рисунку 2.1.1.
Рисунок 2.1.1 — Двигун гвинтовий вибійний: 1 — секція двигуна, 2 — секція шпінделя Гвинтовий вибійний двигун Д1−95 має в своєму складі наступні елементи.
Переливний клапан призначений для зливу промивної рідини з бурильних труб при підйомі колони з гвинтовим вибійним двигуном, а також для заповнення бурильної колони при спуску.
Клапан виконаний у виді окремого вузла і приєднується до секції двигуна на замковому різьбленні 3−171 ГОСТ 5286–75. Пристрій клапана показаний на рисунку 2.1.2.
Рисунок 2.1.2 — Переливний клапан:
1 — перевідник; 2 — корпус; 3 — камера; 4 — сідло; 5 — стержень; 6 — тарілка; 7 — фланець; 8 — гайка; 9 — упор; 10 — кільце регулювальне; 11 — шайба; 12 — манжета; 13 — пружина; 14 — гайка; 15 — кільце ущільнювальне; 16 — кільце ущільнювальне; 17 — штифт; 18 — дріт обв’язувальний; 19 — кільце регулювальне.
У вихідному положенні клапан під впливом пружини 13 відкритий, і промивна рідина може вільно переливатися з бурильної колони в затрубний простір і назад (при виключених бурових насосах).
При включенні насоса за рахунок швидкісного напору рідини тарілка клапана з манжетою 12, переборюючи опір пружини 13, переміщається вниз і закриває клапан, роз'єднуючи внутрішню порожнину від затрубного простору.
Промивна рідина через отвори в камері 3 надходить у двигун. При припиненні подачі рідини від насосів під дією пружини 13 клапан відкривається. Карданний вал (рисунок 2.1.3) служить для передачі крутного моменту і осьового гідравлічного навантаження з ексцентрично (планетарно) обертового ротора на вал шпиндельної секції.
Рисунок 2.1.3 — Карданний вал: 1 — напівмуфта; 2 — гайка; 3 — планка; 4 — кільце; 5 — манжета; 6 — ролик; 7 — втулка; 8 — обійма; 9 — вал.
У торцях напівмуфт 1 і вала 9 виконані кільцеві канавки, у яких із зазором розміщені обойми 8. Ролики 4 встановлені в радіальних отворах напівмуфт, обойм і вала також з визначеним зазором. Герметизація внутрішньої порожнини шарнірів здійснюється манжетами 5 і гайками 2.
Осьове навантаження сприймається торцями напівмуфт і вала. При роботі двигуна осі напівмуфт роблять прецесійний рух щодо осі вала; при цьому ролики перекочуються без ковзанні, по поверхні отворів елементів карданного вала.
Шпиндельна секція (рисунок 2.1.4) служить для передачі осьового зусилля з бурильних труб на долото і містить у собі багаторядний упорно-радіальний кульковий підшипник, три радіальні гумометалеві опори, сальник торцевий (чи сальник з гумовими кільцями), змонтовані в корпусі, перевідники.
Рисунок 2.1.4 — Секція шпиндельна:
1 — перевідник нижньої секції; 2 — муфта; 3 — втулка регулювальна; 4 — кільце регулювальне; 5 — втулка підкладна; 6 — опора нижня; 7 — втулка нижньої опори; 8 — сальник торцевой; 9 — кільце; 10-вал шпинделя; 11 — втулка підкладна; 12 — кільце; 13 — пакет упорних підшипників; 14 — втулка упорна; 15 — кільце; 16 — втулка кільця ущільнюючого; 17 — втулка регулювальна; 18 — втулка завзята; 19 — перевідник; 20 — гайка; 21 — перевідник; 22 — корпус.
Багаторядний упорно-радіальний кульовий підшипник сприймає осьове і частково радіальне навантаження; Радіальні гумо-металічні опори сприймають радіальне навантаження.
Рисунок 2.1.5 — Сальник торцевий: 1 — втулка-шестерня; 2 — кільце; 3 — штифт; 4 — пружина; 5 — втулка; 6 — втулка; 7 — втулка; 8 — гвинт; 9 — кільце ущільнювальне.
Технічна характеристика гвинтового вибійного двигуна Д1−195 наведено в таблиці 1.
Сальник торцевий (рисунок 2.1.5) служить для запобігання перетікання промивної рідини через осьову опору шпиндельної секції при створенні великих перепадів тиску на долоті. Елементи, що ущільнюють, виконані у виді твердосплавних контактних кілець, що притискаються друг до друга пружинами 4. Одне з кілець закріплено на валу, а інше — у корпусі.
Втулка 7 має внутрішні зуби, що знаходяться в зачепленні з зовнішніми зубами втулки-шестірні 1, завдяки чому виключається їхній взаємний поворот і мається можливість щодо осьового переміщення, обумовленого зношенням підшипників шпиндельної секції і зношенням твердосплавної торцевої пари сальника.
Центратор служить для обмеження амплітуди поперечних коливань нижньої частини шпиндельної секції і додання напрямку долоту.
Технічна характеристика гвинтового вибійного двигуна Д1−95:
Кінематичне відношення | 9:10 | |
Витрата бурового розчину, л/с | 25…35 | |
Частота обертання вала, с" 1 | 1,5…1,9 | |
Перепад тиску, МПа | 4,3…6,7 | |
Момент сили на валу, кНм | 5,2…7,2 | |
Максимальна потужність, кВт | 50…85 | |
Діаметр доліт, які використовуються, мм | 215,9…244,5 | |
Зовнішній діаметр, мм | ||
Довжина, мм | ||
Маса, кг | ||
Приєднувальні різьби ГОСТ 5286–75: | ||
до бурильних труб | 3−147 | |
до долота | 3−117 | |
2.2 Установки для проведення КРС Установка УБВ600 (рис. 2.2.1.) призначена для буріння структурно-пошукових свердловин обертальним способом з очищенням забою свердловини промивкою.
Установка складається з трьох основних блоків: лебідко-щоглового, насосного блоку і робочого майданчика з містками і стелажами для труб. Лебідко-щогловий і насосний блоки, змонтовані на шасі автомобіля КрАЗ, приводяться в дію від його двигуна.
На рамі лебідко-щоглового блоку встановлені щогла з помостами, лебідка, роздаточний редуктор, трансмісія приводу лебідки, гідродомкрати підйому щогли, компресор, пневматичні і гідравлічні пристрої. [3]
Відбір потужності на механізми лебідко-щоглового блоку виконується від трансмісії автомобіля через коробку відбору потужності, сполучену карданною передачею з роздаточним редуктором. Привід компресора, маслонасоса, живлячого гідродомкрати підйому щогли, гідророзкріплювача і гідромотора пристрою забурки шурфу — від роздаточного редуктора. Привід лебідки — через карданну передачу, трансмісію і ланцюгову передачу. Привід бурового ротора, встановленого на робочому майданчику, — від валу барабана лебідки ланцюговими передачами через проміжний вал.
На рамі насосного блоку змонтовано два бурові насоси зі всмоктуючими і напірними лініями, центральний і спарюючий редуктори, трансмісія, електрогенератор, резервний компресор, системи пневматичного управління, пневматичні і електричні пристрої.
Відбір потужності на механізми насосного блоку здійснюється від трансмісії автомобіля через коробку відбору потужності, зв’язану карданою передачею з центральним редуктором. Привід електрогенератора від центрального редуктора через клинові ремені. Привід спарюючого редуктора і трансмісії - від центрального редуктора через шино — пневматичні муфти. Привід бурових насосів — від трансмісії і спарюючого редуктора через клинореміну передачу. Привід резервного компресора — від індивідуального електродвигуна.
Рисунок 2.2.1 — Бурова установка УБВ — 600: 1 — лебідко-щогловий блок; 2 — насосний блок; 3 — компресор; 4 — генератор; 5 — трансмісія насосного блока; 6, 7 — бурові насоси; 8 — робоча площадка; 9 — пристрій забурки шурфу; 10 — мостки; 11 — стелажі для труб; 12 — підсвічник; 13 — ротор; 14 — пульт керування; 15 — бурова лебідка; 16 — допоміжна лебідка; 17 — компресор; 18 — трансмісія лебідко-щоглового блока; 19 — маслобак.
Спарюючий редуктор сполучений карданною передачею з трансмісією лебідко — щоглового блоку, що забезпечує привід всіх механізмів бурової установки від будь-якого з двох двигунів у разі виходу з ладу або зупинки на профілактику одного з них.
Для буріння лебідко — щогловий і насосний блоки встановлюють на фермах. Висота підроторної підстави — достатня для монтажу противикідного устаткування.
Барабан лебідки має чотири діапазони частоти обертання. Зміна кожного діапазону проводиться введенням в зачеплення відповідної пари шестерень коробки відбору потужності і включенням відповідної шино — пневматичної муфти лебідки. Ротор має п’ять діапазонів частоти обертання: два робочих і три допоміжних. Зміна робочих частот обертання проводиться введенням в зачеплення відповідної пари шестерень коробки відбору потужності, а допоміжних введенням в зачеплення відповідної пари шестерень коробки зміни передач автомобіля. [15]
Для механізації допоміжних робіт бурова установка обладнана електролебідкою, гідророзкріплювачем, підвісними ключами для труб і пристроєм для їх підвіски, трубним візком і зварювальним трансформатором.
Електролебідка може бути використана при монтажі бурової в установки для підтягання і підйому вантажів, а також під час буріння для згвинчення і розгвинчування різьбових з'єднань труб, викиду труб на містки або підтягання їх до ротора, відведення ротора від гирла свердловини при спуску обсадних труб великого діаметра і інших робіт.
Самохідність основних блоків і габарити допоміжного устаткування, розрахованого на транспортування універсальним автотранспортом, забезпечують перебазування основного устаткування бурової установки за один рейс.
Управління установкою здійснюється з пульта, на якому розміщено органи оперативного управління і прилади контролю процесу і режиму роботи механізмів установки.
Технічна характеристика установки:
Шифр | УБВ — 600Н | |
Тип | Самохідний | |
Вантажопідйомність, тс | ||
максимальна | ||
номінальна | ||
Глибина буріння, м | ||
Діаметр буріння, мм | ||
початковий | ||
кінцевий | ||
Транспортна база лебідко-щоглового та насосного блоків | Автомобіль КрАЗ — 250 | |
Привід механізмів | Двигун базового автомобіля КрАЗ, потужністю 240 лс при 2100 об/хв.; ЯМЗ-238 | |
Потужність силового приводу (розрахункова), лс | ||
лебідко — щоглового блоку | ||
насосного блоку | ||
Довжина свічі, м | ||
Швидкість підйому, м/сек. | ||
мінімальна | 0,181 | |
максимальна | 1,215 | |
Лебідка | Однобарабанна з ланцюговим приводом двострічковим гальмом. | |
Натяг каната (максимальний), то | 9,8 | |
Оснастка талевої системи | 3х4 | |
Висота щогли до осі кронблока, м | 22,4 | |
Кронблок | Чотирьох роликовий | |
Ротор | Р 360 | |
Частота обертання стола ротора, об/хв. | ||
робоча | 105 та 183 | |
допоміжна | 30,54 та 254 | |
Потужність, що передається ротором, л.с. | ||
Прохідний отвір стола, мм | ||
Промивний насос | УНБ — 125 | |
Кількість наосів | ||
Робоча площадка | Двосекційна, зварна з профільного прокату | |
Габарити площадки, мм: | ||
довжина | ||
ширина | ||
висота | ||
Містки із стелажами | Двосекційні, зварні з профільного прокату | |
Полати | Консольні, зварні з профільного прокату | |
Кількість магазинів для труб, шт | ||
Діаметр труб, мм | 73 — 89 | |
Джерело енергії для освітлення допоміжного обладнання | Сінхроний електрогенератор ЕСС-5−83−6-МІОІ | |
Потужність генератора, кВа | ||
Напруга, вольт | 400/230 | |
Частота обертання ротора | ||
Габаритні розміри лебідко-щоглового блоку в транспортному положенні, мм | ||
довжина | ||
ширина | ||
висота | ||
Габаритні розміри насосного блоку в транспортному положенні, мм | ||
довжина | ||
ширина | ||
висота | ||
Маса лебідко-щоглового блоку в транспортному положенні, кг | ||
Навантаження на передню вісь, повне | ||
Навантаження на задню теліжку, повне | ||
Маса насосного блоку в транспортному положенні, кг | ||
Навантаження на передню вісь, повне | ||
Навантаження на задню теліжку, повне | ||
Маса комплекту з пристосуваннями та запчастинами, кг | ||
3. ТЕХНІКО-ЕКОНОМІЧНЕ ОБҐРУНТУВАННЯ Принцип дії гвинтового вибійного двигуна наступний. Двигун містить ротор і статор, поперечний переріз яких показано на рисунку 3.1.1. Сталевий статор усередині має привулканізовану гумову обкладку з гвинтовими зубами лівого напрямку. На сталевому роторі нарізані зовнішні гвинтові зуби також лівого напрямку. Число зубів ротора на одиницю менше числа зубів статора, у результаті чого для здійснення зачеплення вісь ротора зміщена щодо осі статора на величину ексцентриситету, рівну половині висоти зуба. Кроки гвинтових ліній ротора і статора прямо пропорційні числу зубів. Спеціальний профіль зубів ротора і статора забезпечує їхній безупинний контакт між собою, утворюючи на довжині кроку статора одиничні робочі камери.
Промивна рідина, що надходить у двигун від насосів бурової установки, може пройти до долота тільки в тому випадку, якщо ротор повертається щодо статора, обкатуючись під дією неврівноважених гідравлічних сил.
Ротор, роблячи планетарний рух, повертається по годинниковій стрілці (абсолютний рух), у той час як геометрична вісь ротора переміщається щодо осі статора проти годинникової стрілки (переносний рух).
За рахунок різниці в числах зубів ротора і статора переносний рух редукується в абсолютне з передаточним числом, рівним числу зубів ротора, що забезпечує знижену частоту обертання і високий крутний момент на виході.
Загальний вигляд двигуна показаний на рисунку 3.1.1.
Тобто, робоча рідина, що подається насосами з поверхні, пройшовши крізь насосно-компресорні труби потрапляє у гвинтовий вибійний двигун, далі - до вибою свердловини та крізь між трубний простір піднімається на поверхню. Даний процес називають прямою циркуляцією робочої рідини.
Рисунок 3.1.1 — Двигун гвинтовий вибійний: 1 — секція двигуна, 2 — секція шпінделя.
При виконанні капітального ремонту свердловин нерідко доводиться застосовувати процес зворотної циркуляції робочої рідини. Це пов’язано з необхідністю промивки вибою. При зворотній циркуляції робоча рідина рухається по наступній схемі: насос — міжтрубний простір — вибій свердловини — гвинтовий вибійний двигун — колонна насосно-компресорних труб. За такої схеми робоча рідина, що містить вибійний бруд та пропанат, потравляє до вибійного двигуна засмічуючи основні робочі елементи останнього та зменшуючи його міжремонтний період.
Цю проблему пропонуємо вирішити за допомогою технічного рішення, описаного у четвертому розділі даного дипломного проекту
4. ТЕХНІЧНА ЧАСТИНА
4.1 Призначення, виконувані функції, умови роботи розглядуваного обладнання Модульні турбогвинтові двигуни (Рис. 4.1.1) включають три основні вузли: шпиндель 1, турбінну секцію 2 і гвинтовий модуль 3. Конструкцією передбачені різні варіанти агрегатування вказаних вузлів. У залежності від поставлених технологічних задач можуть використовуватися такі варіанти компоновок: шпиндель і гвинтовий модуль, шпиндель і турбінна секція та шпиндель, турбінна секція і гвинтовий модуль. Монтаж цих компоновок може здійснюватися як в умовах цеху, так і безпосередньо на свердловині.
Модульні турбогвинтові двигуни органічно поєднують стабільність енергетичної характеристики в часі та високу жорсткість лінії моментів, що забезпечує досягнення більш високих показників роботи доліт, ніж при використанні турбобурів або гвинтових двигунів.
Шляхом заміни гвинтового модуля на інший можна ступінчато регулювати частоту обертання від 80 до 270 об/хв.
При інших рівних умовах турбогвинтові двигуни мають значно більший ресурс на відмову, ніж гвинтові двигуни.
При роботі на малоабразивному буровому розчині ресурс турбогвинтових двигунів на відмову становить 400—500 год.
Висока надійність двигуна забезпечується використанням в його конструкції оригінальних технічних рішень. Це вузли з'єднання торсіона з ротором гвинтового модуля і валом турбінної секції, пристрій для зменшення дії на опори двигуна неврівноваженої маси торсіона і гвинтового ротора та ін. Використовувані у турбінній секції робочі органи забезпечують високі енергетичні показники двигуна в цілому.
Рисунок 4.1.1 Модульний турбогвинтовий двигун: а — вид загальний, б — схема. 1 — шпіндель; 2 — турбінна секція; 3 — гвинтовий модуль; 4, 5 — відповідно ротор і статор; 6 — торсіон; 7 — з'єднання торсіона звалом турбінної секції; 8 — вал турбінної секції; 9 — ступінь турбіни; 10 — осьова опора шпинделя; 11 — долото.
Турбогвинтові двигуни застосовують при температурах до 120 °C і промиванні свердловин буровими розчинами густиною до 1700 кг/м3 та об'ємним вмістом вуглеводневих сполук до 5%. Турбогвинтові двигуни використовують для буріння вертикальних свердловин суцільним вибоєм та з відбором керна, а в компоновці із шпинделем-відхилювачем — для проходження викривлених ділянок свердловин.
Основна особливість турбогвинтових двигунів полягає у можливості переходу гвинтової пари з режиму роботи двигуна (ДР) в насосний режим (НР) і навпаки. Це відбувається за рахунок зміни знаку перепаду тиску на гвинтовій парі. В режимі роботи двигуна джерелом механічної енергії є тиск, створений буровим насосом, а в насосному режимі — механічна енергія, що подається з вала турбінної секції. Дослідженнями М.Г. Ескіна, В. А. Литвяка і В.П. Шумілова обґрунтовані особливості робочих характеристик турбогвинтових двигунів, що свідчать про їх перевагу у порівнянні з турбобурами та гвинтовими двигунами. На рис. 4.1.2 показані деякі робочі характеристики турбогвинтового двигуна, одержані так само, як для гвинтового двигуна Д-195 та уніфікованої турбіни 26/16,5−195.
При роботі турбогвинтового двигуна у режимі двигуна в близькій до холостого режиму гвинтової пари області А спостерігається поєднання переваг і зникнення недоліків турбобура та гвинтового двигуна.
Момент на виході турбогвинтового двигуна створюється, в основному, турбінною секцією. Полегшений (в 5—10 разів) режим роботи гвинтової пари призводить до зменшення зносу та підвищення її ресурсу.
Для турбогвинтових двигунів спостерігається більша жорсткість (крутизна) моментної характеристики Мтг(п) у порівнянні з турбобурами. Це забезпечує більш стійку роботу двигуна у лівій частині моментної характеристики Мтг(п). Одним із недоліків турбобура є можливість переходу з робочих частот у зону високих аж до частот холостого режиму. Особливість характеристики турбогвинтового двигуна при насосному режимі виключає таку можливість (рис. 4.1.2).
Рисунок 4.1.2 — Залежності моменту турбогвинтового двигуна:
Мтг, Мг, Мт — моменти турбогвинтового двигуна, гвинтової пари і турбінної секції;4ргг, ртг, рг, рт — перепади тиску на турбогвинтовому двигуні, гвинтовій парі і турбінній секції; птгх, пгх — частота обертання холостого ходу турбогвинтового двигуна і гвинтової пари; птго— частота обертання, яка відповідає нульовому перепаду тиску на гвинтовій парі; ДР, НР — двигунний і насосний режими роботи гвинтової пари; А — область режимів турбогвинтового двигуна При агрегатуванні турбогвинтових двигунів можуть бути використані відроблені гвинтові пари від вибійних гвинтових двигунів. Досвід їх випробування показав, що зношені гвинтові пари (для двигуна ДЗ-172 із зазорами в парі понад 0,8 мм) успішно застосовують як стабілізатор запобігання переходу на високі частоти обертання.
Результати випробувань турбогвинтових двигунів із використанням турбобурів ТПС-172 і гвинтових пар від двигуна ДЗ-172 показали, що найсприятливіші умови роботи двигуна створюються тоді, коли гвинтова пара розміщується між верхньою і середньою секціями турбобура.
До недоліків турбогвинтових двигунів слід віднести значну (у порівнянні із гвинтовими двигунами) довжину, що ускладнює їх використання при бурінні горизонтальних і сильновикривлених свердловин. Турбогвинтові двигуни характеризуються також низьким ККД (0,2—0,3).
4.2 Конструктивні варіанти та їх порівняльний аналіз розглядуваного обладнання Модульні турбогвинтові двигуни типу ТВД випускають діаметрами 195 і 240 мм із урахуванням максимального використання уніфікації вузлів серійних турбобурів, високомоментної турбіни А7ПЗ і серійних гвинтових пар. Така компоновка двигуна забезпечує високі значення моменту сили на валі при відносно низькій частоті його обертання. При цьому передбачається розвантаження гвинтового модуля на номінальному режимі роботи двигуна: модуль або підвищує, або поглинає момент сили тільки при подоланні пікового значення моменту на долоті або його перевантаженні. Це сприяє підвищенню безвідмовної роботи гвинтової пари.
Універсальні турбогвинтові двигуни типу ТПС-У з перетворювачами частоти обертання випускають діаметрами 172 і 195 мм. Турбогвинтові двигуни цього типу комплектуються взаємозамінними двома або трьома турбінними секціями з плаваючими статорами (ТПС), перетворювачем частоти обертання вихідного вала (гвинтового модуля) та шпиндельною секцією з осьовою опорою.
Турбогвинтові двигуни ТПС-У забезпечують при постійній продуктивності бурових насосів ступінчасту зміну частоти обертання вихідного вала в діапазоні 80—400 об/хв у залежності від конструктивного виконання гвинтових пар. Конструктивна схема цих двигунів дозволяє одержати практично постійну частоту обертання вала при зміні осьового навантаження на долото в широких межах. Конструкція шпиндельної секції забезпечує роботу двигуна при бурінні гідромоніторними долотами з перепадом тиску в їх насадках 6—8 МПа.
Уніфіковані модульні турбогвинтові двигуни 2ТУ-240КД з покращеними енергетичними і експлуатаційними характеристиками комплектуються взаємозамінними уніфікованими модулями. Нижня секція являє собою односекційний турбобур ТУ-240К. Середня секція двигуна конструктивно виконана аналогічно серійній з використанням турбін зменшеної висоти точного лиття (37/11−240ТЛ). Верхня секція двигуна є активним гальмівним модулем, що вміщує в одному корпусі турбінну частину і робочі органи гвинтового двигуна, які з'єднуються з допомогою знімного торсіона. Особливістю гальмівного модуля є його повна взаємозамінність із серійною секцією. Верхня секція також оснащена турбінами зменшеної висоти.
4.3 Техніко організаційні заходи, що проводяться при бурінні свердловин Регулювання турбінної секції
Рухомі і нерухомі деталі турбінної секції кріплять фрикційним способом, причому необхідне зусилля стиснення, що забезпечує опір провертання на валу і в корпусі, досягається згвинченням конусних різьбових з'єднань з відповідним натягом і установкою регулювальних кілець, необхідної довжини. Деталі на валу кріпляться нагвинчуванням напівмуфти і створенням натягу між внутрішнім торцем напівмуфти і торцем різьблення валу. Аналогічно необхідне монтажне зусилля стиснення деталей корпусу створюється при згвинченні перевідника і корпуса і підбором довжини регулювального кільця.
Таким чином, при монтажі турбін створюються осьові деформації, як внутрішніх рухомих, так і зовнішніх нерухомих деталей турбіни і радіальних підшипників секції. Якщо деформація деталей, що обертаються, відрізняється від деформації нерухомих, то змінюється відстань між вхідними кромками крайніх ступенів ротора і воно не буде рівне відстані між відповідними вхідними кромками ступенів статора. Це приводить до зменшення довжини вільного осьового ходу валу турбінної секції. При монтажі повинно бути забезпечено рівність деформацій стиснення деталей, що обертаються і не обертаються, що забезпечує максимальний люфт зібраного валу турбіни. На практиці це досягається регламентацією величин натягу конічних різьб.