Проектний розрахунок консольного пересувного крана
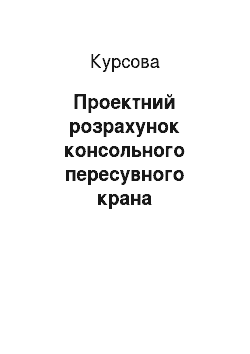
Механізм пересування крана розташований біля приводного колеса. Для забезпечення заданої швидкості пересування крана було обрано двигун серії MTF потужність 7,5 кВт. Для передачі крутного моменту було обрано конічно-циліндричний редуктор типу КЦ. В результаті відхилення фактичної швидкості пересування крана від заданої складає 1% що є допустимим відхиленням. Методичні вказівки до курсового… Читати ще >
Проектний розрахунок консольного пересувного крана (реферат, курсова, диплом, контрольна)
Міністерство освіти i науки України Запорізький національний технічний університет Кафедра ДМ і ПТМ ПОЯСНЮВАЛЬНА ЗАПИСКА ДО КУРСОВОГО ПРОЕКТУ 3 ДИСЦИПЛІНИ ВАНТАЖНОПІДЙОМНА, ТАРНСПОРТУЮЧА ТА ТРАНСПОРТНА ТЕХНІКА Проектний розрахунок консольного пересувного крана ГОСТ 2.106−96
Запоріжжя 2012
РЕФЕРАТ ПЗ: 65 сторінки, 19 таблиць, 11 рисунків, 8 джерел літератури.
Об'єкт — кран консольний пересувний.
Метою курсового проекту було проектування консольного пересувного електричного крана. При проектуванні було зроблено розрахунок механізму підйому для вантажопідйомності 8 т, обрана кратністю поліспаста — 2 і відповідно обраний барабан з двосторонньою навивкою; механізму пересування візка; механізму пересування крана.
Сама металоконструкція спроектована таким чином, що механізми підйому і пересування візка заходяться на вантажному візку, що рухається по двом горизонтальним балкам прикріпленим до вертикальних. Механізм пересування крана розташований на горизонтальній поперечині, безпосередньо біля приводного колеса. Стійкість крана у вертикальній площині забезпечується за допомогою горизонтальних роликів, розташованих на кінцях вертикальних балок. Горизонтальні балки по яких рухається вантажний візок мають коробчасту будову.
Графічна частина виконана за допомогою графічного редактора «3D КОМПАС 12», розрахункова — за допомогою «Microsoft Word».
Ключеві слова: ПОЛІСПАСТ, КРАН, ПІДВІСКА, ГАК, КАНАТ, ПІДШИПНИК, ТРАВЕРСА, ВІЗОК, РЕДУКТОР, КОЛЕСО.
ЗМІСТ Вступ
1. Розрахунок механізму підйому вантажу
1.1 Вибір схеми підйому вантажу та кратності поліспаста
1.2 Вибір вантажного каната
1.3 Розрахунок гвинтів кріплення каната до барабана
1.4 Розрахунок розмірів барабана
1.5 Вибір гака
1.6 Розрахунок елементів підвіски
1.6.1 Вибір підшипника гака
1.6.2 Розрахунок блока
1.6.3 Розрахунок траверси
1.6.4 Розрахунок підшипників блока
1.7 Розрахунок потужності двигуна, його вибір
1.8 Вибір редуктора
1.9 Вибір гальма механізму підйому
1.10 Вибір муфт
1.11 Перевірка електродвигуна за часом розгону та нагрівом
2. Механізм пересування візка
2.1 Вибір схеми механізму пересування
2.2 Вибір ходових коліс
2.3 Опір пересуванню візка
2.4 Вибір двигуна
2.5 Вибір редуктора
2.6 Вибір муфти
2.7 Вибір гальм
2.8 Перевірка двигуна
3. Механізм пересування крана
3.1 Вибір схеми механізму пересування крана
3.2 Вибір ходових колес та горизонтальних роликів
3.3 Опір пересування крана
3.4 Вибір двигуна
3.5 Вибір редуктора
3.6 Вибір муфти
3.7 Вибір гальм
3.8 Перевірка двигуна Висновки Перелік використаної літератури Додатки ВСТУП Консольні крани набули значного поширення і зараз важко знайти машинобудівний завод без цих кранів. Застосовуються консольні пересувні крани в основному для обслуговування окремих агрегатів. Зазвичайн крани даного типу не є визначальними в виробничому процесі роботи цехів, однак їх наявність значно поліпшує технологію обслуговування окремих ділянок виробництва.
Консольні крани, як правило, невеликої вантажопідйомності (до 10 т). Виліт стріли у межах 3−10 м. Крани встановлюють під стінкою і, нерідко, зоною їх обслуговування є територія вздовж всієї стіни цеху.
Однією з переваг даного типу кранів є їх відносна простота конструкції та управління. Кран складається з двох вертикальних балок, до яких кріпиться балка з механізмом пересу4вання крана, та дві горизонтальні балки коробчастого перерізу по яких рухається візок. Механізм підйому та пересування візка розташовані на вантажному візку.
Вхідні данні
Тип крану… Консольний Вантажопідйомність…Q = 8 т;
Висота підйому вантажу… Н = 6 м;
Вильот…L = 5 м;
Швидкість підйому вантажу… Vван = 0,15 м/с;
Режим роботи… Важкий Тривалість включення… ПВ = 40%
Група режиму роботи механізму…М6
Швидкість руху візка…Vв= 0,7 м/с Маса крана, не більше…14 т Рисунок В1 — Консольний пересувний електричний кран
1. РОЗРАХУНОК МЕХАНІЗМУ ПІДЙОМУ ВАНТАЖУ
1.1 Вибір схеми механізму підйому та кратності поліспаста Механізм підйому знаходиться на вантажному візку. Кінематична схема механізму підйому є традиційною: крутний момент від електродвигуна через зубчату муфту передається на редуктор, з редуктора — на барабан (рисунок 1.1).
Рисунок 1.1 — Схема механізму підйому Для даного крана з заданою вантажопідйомністю найдоцільніше буде застосувати здвоєний поліспаст кратністю iп=2 з скороченою підвіскою (рисунок 1.2).
Визначаємо ККД поліспаста:
де = 0,98 — ККД блоку на підшипниках кочення;
— кратність поліспаста.
Рисунок 1.2 — Схема поліспаста
1.2 Вибір вантажного каната У відповідності з правилами Держгірпромнагляду канат вибирають за розривним зусиллям :
де =5.6 — коефіцієнт використання (запасу міцності) каната відповідно до режиму роботи М6;
— найбільше зусилля в канаті, кН:
де — - маса вантажу, т;
a — кількість гілок каната, які намотуються на барабан;
m — кількість відхиляючих блоків;
— маса підвіски, т;
Канати вибирають за ГОСТ 2688–80. Згідно отриманого розривного зусилля створюваного в канаті обираємо канат ЛК-Р 6×19+1о.с. по ГОСТ 2688–80 діаметром 15,0 мм (додаток В).
Таблиця 1.2 — Характеристика каната
Параметр | Значення | |
Діаметр каната, мм | 15,0 | |
Маркувальна група, МПа | ||
Розрахункова вага 1000 м каната, кг | 844,0 | |
Розрахункове розривне зусилля, кН | 125,500 | |
1.3 Розрахунок гвинтів кріплення каната до барабана Зусилля натягу каната в місці кріплення, кН:
де — основа натурального логарифма;
— коефіцієнт тертя між канатом та барабаном;
(1,5 витка) — кут обхвату барабана незмотуємими гілками, прийнятий за правилами Держгірпромнагляд.
Необхідне число гвинтів кріплення канату:
де =10.376 мм — внутрішній діаметр болта М12.
МПа — допускне напруження розтягу для гвинтів із сталі 3.
Кількість гвинтів = 3.
1.4 Розрахунок розмірів барабана Мінімально допустимий діаметр барабана по центру каната, мм:
де — діаметр каната, мм;
— коефіцієнт, який залежить від типу машини і групи режиму роботи;
Приймаємо: Dб = 300 мм.
340 мм.
Число витків нарізок на барабані з однієї сторони:
Приймаємо z = 17 мм.
де — висота підйому вантажу, м;
— діаметр барабана по центру каната, м;
4 — число витків кріплення каната та запасних.
Довжина нарізки на барабані з однієї строни, мм:
де — крок нарізки на барабані, мм:
p=1,1•15=16,5
Приймаємо: p=17 мм.
Загальна довжина барабану, мм:
де — довжина гладкої частини на кінцях барабана, мм;
В=120 мм — довжина не нарізної частини барабана;
Приймаємо: L=800 мм Товщину стінки барабана приймають рівну
Приймаємо? = 18 мм Стінки барабана перевіряють по напруженню стиску:
для барабанів із сталі 25Л = 120 МПа.
Умова виконується. Отже приймаємо? — 18 мм.
1.5 Вибір гака Гак вибирають за номінальною вантажопідйомністю та групою режиму роботи для машинного приводу. Звичайно приймають кований однорогий гак за ГОСТ 6627–74. Обираємо гак № 16Б (додаток Г).
Таблиця 1.3 — Основні розміри гака
Параметр | Значення | Параметр | Значення | ||
D, мм | l, мм | ||||
S, мм | l1, мм | ||||
d0 мм | М56 | L, мм | |||
d1, мм | Маса, кг | 12.2 | |||
1.6 Розрахунок елементів підвіски
1.6.1 Вибір підшипника гака Упорний підшипник гака вибирають за статичною вантажопідйомністю
() і діаметром шийки гака (d1).
d1 — 60 мм.
Підбираємо підшипник кульковий упорний одинарний № 8212 ГОСТ 7872 легкої серії, (додаток Д).
Таблиця 1.4 — Характеристика підшипника
Умовне позначення | d, мм | D, мм | Н, мм | r, мм | C, H | Cо, H | Маса, кг | |
1,5 | 0,69 | |||||||
1.6.2 Розрахунок блока Рисунок 1.3 — Блок Розраховуємо діаметр блока по осі каната, мм:
де — діаметр каната, мм;
2 — коефіцієнт, який залежить від типу машини і групи режиму роботи;
Приймаємо Dбл=340 мм Ширина блока, мм:
Приймаємо Вбл. = 74 мм.
Діаметр відхиляючого блока по вісі каната, мм:
Приймаємо Dв. бл=240 мм.
1.6.3 Розрахунок траверси Рисунок 1.4 — Траверса Матеріал …сталь 40
Границя міцності …
Границя текучості…
Границя втоми …
Розрахункова відстань Аск між опорами блока та поперечини:
Аск = 1,4· В + · іп·а =1.4· 110+·2·2=228мм Де В — ширина траверси, необхідна з умов розміщення упорного підшипника № 8212
Приймаємо В = 110 мм.
де Dп — діаметр зовнішнього кільця упорного підшипника (D=95)
Діаметр отвору в траверсі для проходу шийки гака, мм:
d=d1+2=65+2=67 мм Згинаючий момент в середньому перерізі:
Допустиме напруження згину при пульсуючому циклі:
Де К=1,6 — коефіцієнт запасу міцності для механізмів підіймання гайкових кранів при розрахунку на втому, з урахуванням режиму роботи К?=1,8 — ефективний коефіцієнт концентрації напружень, при? в=580 МПа
??=0,7 — масштабний фактор для вуглецевих сталей.
Мінімальна висота траверси, мм:
Приймаємо Н=77мм, Н0=82мм Довжину траверси визначаємо з урахуванням можливості розміщення, монтажу упорного підшипника № 8212 та загвинчування гакової гайки:
Згинаючий момент:
Мінімальний діаметр цапфи траверси розраховуємо за напруженням згину
Де dц — число, кратне 5, по внутрішньому діаметру підшипника: dц =55мм ,
Допустиме напруження:
Ефективний коефіцієнт концентрації напружень від посадки внутрішнього кільця підшипника, при dц>50мм і ?в=580 МПа.:
Ефективний коефіцієнт концентрації напружень від галтелі в місці з'єднання цапфи траверси К?=2,25 при:
h = (H0 — dц)/2 = (85 — 55)/2 = 15 мм — висота переходу з діаметра dц на висоту траверси H0, виміряна по радіусу.
h/r = 15/2 = 7.5; r/dц =2/55 = 0,04, де r = 2 мм — радіус галтелі.
??=0,8 — масштабний фактор,
1.6.4 Розрахунок підшипників блока Підшипники блока обираємо за діаметром цапфи траверси та динамічною вантажопідіймальністю С:
де — еквівалентне навантаження на підшипник, Н
Де: Н — номінальне навантаження на один з двох підшипників блока, з розподілом по 0,6 на кожний.
Кт = 1 — коефіцієнт температури Кн = 0,55 — коефіцієнт навантаження, для середнього режиму роботи М5
V = 1,2 — при обертанні зовнішнього кільця підшипника КБ = 1,2 — коефіцієнт безпеки, для механізму підіймання
— ресурс служби підшипника, год. (5000 год. для М5)
Частота обертання блока, хв.-1:
;
Де — швидкість підйому вантажу, м/с;
— кратність поліспаста;
— діаметр блока по осі каната, м.
За прийнятим діаметром цапфи та динамічною вантажопідйомністю вибираємо підшипники кулькові радіальні однорядні № 211 ГОСТ 8338–75 легкої серії (додаток Е) Таблиця 1.5 — Характеристика радіального кулькового підшипника
Умовне позначення | d, мм | D, мм | Н, мм | r, мм | C, H | Cо, H | Маса, кг | |
2.5 | 0,60 | |||||||
1.7 Розрахунок потужності двигуна, його вибір Потужність, яка необхідна для підйому номінального вантажу, кВт:
де, т ;
— швидкість підйому вантажу, м/с;
— загальний ККД механізму підйому;
— ККД, відповідно, поліспаста, барабана, редуктора та муфти; звичайно приймають =0,85…0,9.
З каталогу вибираємо двигун:
Двигун з фазним ротором серії MTF типорозміру312−6 (додаток Є).
Таблиця 1.6 — Характеристика двигуна
Потужність, кВт | ||
Частота обертання, хв.-1 | ||
Момент інерції ротора, кг/м2 | 0,312 | |
Максимальний момент, Нм | ||
Маса | ||
Потужність вибраного двигуна перевіряють за нагріванням де — коефіцієнт приведення потужності, для режиму роботи М5;
= 0,86 — коефіцієнт, який визначає еквівалентну за нагрівом двигуна потужність; - потужність двигуна при ПВ 25%.
1.8 Вибiр редуктора Передаточне відношення механізму підйому :
=
де nб — частота обертання барабана, хв-1 ;
де швидкість підйому вантажу, м/с;
— діаметр барабана по осі каната, м.
=
З каталога обираємо (Додаток Ж):
Вибираємо редуктор Ц2 — 500, з передаточним числом (найближче до потрібного), потужність, що передається — 28,5 кВт >, при швидкохідного вала, для важкого режиму роботи (ПВ=40%).
Перевіряємо фактичну швидкість підіймання вантажу:
Відхилення від заданої швидкості
що допустимо, [V]= 5%.
1.9 Вибір гальм механізму підйому Необхідний гальмівний момент, Нм;
де — коефіцієнт запасу гальмування, відповідно для режиму роботи М6.
По гальмівному моменту вибираємо гальмо ТКТ-300/200 (додаток З).
Таблиця 1.8 — Характеристика гальма ТКТ-300/200
Гальмівний момент, Нм | ||
Діаметр гальмівного шківа, мм | ||
Ширина гальмівної колодки, мм | ||
Тип електромагніта | МО200Б | |
Маса, кг | ||
1.10 Вибір муфт Для з'єднання валів електродвигуна з швидкохідним валом редуктора використовують муфти, які можуть у деякій мірі компенсувати не співвісність валів, яка виникає в процесі виготовлення та монтажу.
Муфту вибирають по розрахунковому моменту, Нм де — номінальний момент, який передає муфта;
=1,8 — коефіцієнт, який враховує ступінь відповідальності механізму;
=1,3 — коефіцієнт, який враховує режим роботи механізму При виборі муфти слід дотримуватись умови:
За розрахунковим моментом та діаметром гальмівного шківа обираємо зубчату муфту з гальмівним шківом (додаток І).
Таблиця 1.9 — Характеристика зубчатої муфти
D, мм | D1, мм | к | d | dк | Найбільший гальмівний момент, Нм | Момент інерції муфти, кгм2 | Маса муфти, кг | ||
не більш | |||||||||
69,5 | 0,625 | ||||||||
Рисунок 1.4 — Муфта зубчата з гальмівним шківом
1.11 Перевірка електродвигуна за часом розгону та нагрівом Час пуску електродвигуна має відповідати умові:
Де — зведений до валу момент інерції мас, що рухаються при підйомі та опусканні вантажу, кг•м2;
де = 1,2 — коефіцієнт, який враховує момент інерції деталей, що обертаються, крім ротора двигуна й муфти;
— відповідно момент інерції ротора двигуна і муфти, кгм2;
— номінальна за вантажопідйомністю маса вантажу, кг;
— радіус барабана, м;
Середній пусковий момент електродвигуна, Нм:
де — середня кратність пускового моменту;
= 2,0 — для двигуна трифазного струму з фазним ротором;
Частота обертання ротора двигуна, с-1:
Момент на валу двигуна від маси вантажу, Нм:
— що не задовольняє вимогам Одже двигун буде гальмувати за рахунок електричного опіру.
2. МЕХАНІЗМ ПЕРЕСУВАННЯ ВІЗКА
2.1 Вибір схеми механізму пересування Обираємо схему пересування візка з центральним приводом і тихохідним валом (рисунок 2.1).
Рисунок 2.1 — Схема механізму пересування візка
1 — двигун; 2 — гальмо; 3 — редуктор; 4 — муфта; 5 — ходове колесо
2.2 Вибір ходових колес Визначаємо максимальне навантаження на колесо візка, кН :
де, Qmax — максимальна вантажопідйомність, т
GB — маса візка, т:
З урахуванням максимального навантаження, швидкості пересування та групи режиму роботу механізму обираємо колеса (додаток К).
Таблиця 2.1 Параметри ходового колеса візка
Діаметр колеса та тип рейки | Швидкість руху, м/с | Допускний тиск, кН | |
250/Р15 | 1,32 | 48,5 | |
Діаметр цапф валів коліс:
d0 =(0.2…0.3)Dk=(0.2…0.3)250=50…75
Приймаємо: d0 =70 мм
2.3 Опір пересування візка Максимальний опір пересування візка:
де WTP — сила опору тертя у підшипниках та на доріжках кочення ходових коліс з ребордами, Н:
де µ=0,03 — коефіцієнт тертя кочення ходових коліс по рейці [4];
f=0,015 — коефіцієнт тертя ковзання [4];
Кр=2,5 — коефіцієнт тертя в підшипниках опор вала [4];
Dk=25 см — діаметр ходових коліс.
Wі - сила інерції, Н:
де [a]=0,15 м/с2 — допустиме прискорення [4];
2.4 Вибір двигуна Потужність двигуна механізму пересування візка:
Де W — опір пересування візка;
VB=0.72 м/с — швидкість пересування візка;
?3=0,85 — загальний ККД механізму пересування візка;
? — середня кратність пускового моменту, ?=1.5;
З каталогу вибираємо двигун з фазним ротором серії MTF типорозміру 012−6 (додаток Є).
Таблиця 2.3 — Характеристика двигуна
Потужність, кВт | 2,2 | |
Частота обертання, хв.-1 | ||
Момент інерції ротора, кг/м2 | 0,029 | |
Максимальний момент, Нм | ||
Маса | ||
2.5 Вибір редуктора Загальне передаточне число механізму пересування:
де
Редуктор механізму пересування вибираємо по передаточному числу, частоті обертання двигуна і за групою режиму роботи.
Підбираємо редуктор ВКН — 420.
Таблиця 2.4 — Характеристика редуктора ВКН
Передаточне число | Частота обертання вхідного вала, хв-1 | Допустимий крутний момент на вихідному валу, Нм | ККД, % | Маса, кг | |
Фактична швидкість пересування візка:
м/с Відхилення від заданої швидкості:
Умова допустимої величини відхилення фактичної швидкості від заданої виконується.
2.6 Вибір муфти Муфту для з'єднання вала двигуна та редуктора підбираємо за розрахунковим моментом:
Де ТНОМ — номінальний момент, який передає муфта від двигуна редуктору;
К1=1,2 — коефіцієнт, що враховує ступінь відповідальності механізму[4];
К2=1,2 — коефіцієнт, що враховує режим роботи механізму[4].
Нм За моментом підбираємо, для з'єднання вала двигуна з швидкохідним валом редуктора, муфту пружну втулково-пальцеву з гальмівним шківом по ГОСТ 21 424–93 (додаток І).
Таблиця 2.5 — Муфта втулково-пальцева
D | В | Кількість пальців | Максимальний гальмівний момент, Нм | Вага, кг | Момент інерції, кг•м2 | |
0,125 | ||||||
Рисунок 2.2 — Муфта втулково-пальцева з гальмівним шківом Для з'єднання проміжного вала з валом редуктора, або з цапфою колеса обираємо за розрахунковим моментом, Нм:
Де ТНОМ — номінальний момент, який передає муфта від двигуна редуктору;
К1=1,2 — коефіцієнт, що враховує ступінь відповідальності механізму[4];
К2=1,2 — коефіцієнт, що враховує режим роботи механізму[4].
Нм За моментом підбираємо, муфту зубчату за ГОСТ 5006–55 (додаток І).
Таблиця 2.6 — Муфта зубчата
D | B | В1 | Допустимі | Вага, кг | Момент інерції, кг•м2 | ||
Крутний момент, Нм | Частота Обертання, хв.-1 | ||||||
16,1 | 0,1 | ||||||
Рисунок 2.3 — Муфта зубчата
2.7 Вибір гальм Гальма вибираються та регулюються за гальмівним моментом, який забезпечує допустиме сповільнення при гальмуванні вантажного крана або візка, Нм:
де =89 с-1 — кутова швидкість двигуна;
— тривалість гальмування крана або візка з вантажем, с:
Де = 0,2…0,3 м/с2;
зведений до вала двигуна момент інерції рухомих мас, кгм2;
де — момент інерцiї обертаючих мас, = 1,1…1,2;
— момент інерції ротора двигуна, кгм2;
— момент інерції муфти, кгм2;
— радіус колеса, м;
— передаточне число редуктора ;
— загальний ККД.
ТСТ — момент сил опору при усталеному русі навантаженого візка, Нм:
де — опір руху навантаженого візка, Н;
— діаметр ходового колеса, м.
Від`ємне значення моменту вказує на те що тормоз ставити не обов`язково тому что буде відбуватися самогальмування, але за правилами Держміськтехнагляду обираємо гальмо ТКТ-200/100 (додаток З).
Таблиця 2.7 — Характеристика гальма ТКТ-200/100
Гальмівний момент, Нм | ||
Діаметр гальмівного шківа, мм | ||
Ширина гальмівної колодки, мм | ||
Тип електромагніта | МО100Б | |
Маса, кг | ||
Вибрані гальма перевіряються за тривалістю гальмування ненавантаженого крана або візка за умовою Де ТСТ1 — момент сил опору при усталеному русі ненавантаженого візка при гальмуванні, Нм:
де — опір руху ненавантаженого візка, Н:
= 1 при Q = 0;
— Зведений момент інерції рухомих мас, кгм2 :
— мінімальний час гальмування ненавантаженого візка, при якому відсутнє ковзання коліс по рейках (> 1,2), с:
— найменше зусилля на приводні колеса при русі без вантажу, Н:
=0,2 — коефіцієнт зчеплення коліс з рейками при роботі в приміщенні.
2,17>1,68
Умова виконується.
2.8 Перевірка двигуна Перевірка за часом розгону:
— середній пусковий момент двигуна, Нм:
— номінальний момент двигуна, Нм:
?= 1,5…1,6
Інші складові дивитись в пункті 2.7.
Умова виконується.
Перевірка запаса зчеплення коліс з рейкою:
Де, Wi1 — сила інерції при розгоні ненавантаженого візка, Н:
— опір у цапфах приводних коліс при русі без вантажу, Н:
де — найменше зусилля на приводні колеса при русі без вантажу, Н;
= 0,015 — коефіцієнт тертя у цапфах приводних коліс;
— діаметр цапфи, м.
— коефіцієнт зчеплення колеса з рейкою, при роботі у приміщенні.
Умова виконується Визначимо еквівалентну потужність електродвигуна, яка не допускає перегрівання обмоток, кВт:
де, К25=0,75 — коефіцієнт приведення потужності для режиму роботи М5;
y=1,12 — коефіцієнт який визначає еквівалентну за нагрівом двигуна потужність для механізму пересування візка.
Умова виконується.
3. МЕХАНІЗМ ПЕРЕСУВАННЯ КРАНА
3.1 Вибір схеми механізму пересування крана Обираємо схему пересування крана з центральним приводом і тихохідним валом (рисунок 3.1).
Рисунок 3.1 — Схема механізму пересування крана
1 — двигун; 2 — гальмо; 3 — редуктор; 4 — муфта; 5 — ходове колесо підйом вантаж кран візок
3.2 Вибір ходових колес та горизонтальних роликів Визначаємо максимальне навантаження на колесо крана, кН :
де, Qmax — максимальна вантажопідйомність, т
GB — вага візка, т;
Gк — вага крана, т.
Визначаємо навантаження на горизонтальні опорні ролики (дивись рисунок 3.1), кН:
Де З урахуванням максимального навантаження, швидкості пересування крана та групи режиму роботу механізму обираємо ходових колеса та горизонтальні ролики (додаток К).
Рисунок 3.2 — Розрахункова схема консольного поворотного крана Таблиця 3.1 Параметри ходового колеса та горизонтальних роликів
Діаметр колеса та тип рейки | Швидкість руху, м/с | Допускний тиск, кН | ||
Ходові колеса (Dк) | 400/Р38 | 1,25 | ||
Горизонтальні ролики (Dр) | 500/КР70 | 1,32 | ||
Діаметр цапф валів ходових коліс, мм:
dк =(0.2…0.3)Dk=(0.2…0.3)400=80…120
Приймаємо: d =100 мм Діаметр цапф валів роликів, мм:
dр =(0.2…0.3)Dk=(0.2…0.3)500=100…150
Приймаємо: d 1=130 мм
3.3 Опір пересування крана Максимальний опір пересування візка:
де WTP — сила опору тертя у підшипниках та на доріжках кочення ходових коліс та роликів, Н:
де µ=0,03 — коефіцієнт тертя кочення коліс по рейкам[4];
µр=0,05
f=0,015 — коефіцієнт тертя в підшипниках опор вала [4];
Wі - сила інерції, Н:
де [a]=0,15 м/с2 — допустиме прискорення [4];
3.4 Вибір двигуна Потужність двигуна механізму пересування крана, Н:
Де W — опір пересування крана, Н;
Vк=1 м/с — швидкість пересування крана;
?3=0,85 — загальний ККД механізму пересування крана;
? =1,5 — середня кратність пускового моменту;
З каталогу вибираємо двигун з фазним ротором серії MTF типорозміру 211−6 (додаток Є).
Таблиця 3.2 — Характеристика двигуна
Потужність, кВт | 7.5 | |
Частота обертання, хв.-1 | ||
Момент інерції ротора, кг/м2 | 0,115 | |
Максимальний момент, Нм | ||
Маса | ||
3.5 Вибір редуктора Загальне передаточне число механізму пересування:
де
Редуктор механізму пересування вибираємо по передаточному числу, частоті обертання двигуна і за групою режиму роботи.
Підбираємо редуктор КЦ 1−250 (додаток Л).
Таблиця 3.3 — Характеристика редуктора КЦ1−250
Передаточне число | Частота обертання вхідного вала, хв-1 | Допустимий крутний момент на вихідному валу, Нм | ККД, % | Маса, кг | |
19,3 | |||||
Фактична швидкість пересування крана, м/с:
Відхилення від заданої швидкості:
Умова допустимої величини відхилення фактичної швидкості від заданої виконується.
3.6 Вибір муфти Муфту для з'єднання вала двигуна та редуктора підбираємо за розрахунковим моментом:
Де ТНОМ — номінальний момент, який передає муфта від двигуна редуктору;
К1=1,2 — коефіцієнт, що враховує ступінь відповідальності механізму[4];
К2=1,2 — коефіцієнт, що враховує режим роботи механізму[4].
Нм За моментом підбираємо, для з'єднання вала двигуна з швидкохідним валом редуктора, муфту пружну втулково-пальцеву з гальмівним шківом по ГОСТ 21 424–93 (додаток І).
Таблиця 3.4 — Муфта втулково-пальцева
D | В | Кількість пальців | Максимальний гальмівний момент, Нм | Вага, кг | Момент інерції, кг•м2 | |
0,125 | ||||||
Рисунок 3.3 — Муфта втулково-пальцева з гальмівним шківом Для з'єднання проміжного вала з валом редуктора, або з цапфою колеса обираємо муфту за розрахунковим моментом, Нм:
Де ТНОМ — номінальний момент, який передає муфта від двигуна редуктору;
К1=1,2 — коефіцієнт, що враховує ступінь відповідальності механізму[4];
К2=1,2 — коефіцієнт, що враховує режим роботи механізму[4].
Нм За моментом підбираємо, муфту зубчату за ГОСТ 5006–55 (додаток І).
Таблиця 3.5 — Муфта зубчата
D | B | В1 | Допустимі | Вага, кг | Момент інерції, кг•м2 | ||
Крутний момент, Нм | Частота Обертання, хв.-1 | ||||||
16,1 | 0,85 | ||||||
Рисунок 3.4 — Муфта зубчата
3.7 Вибір гальм Гальма вибираються та регулюються за гальмівним моментом, який забезпечує допустиме сповільнення при гальмуванні вантажного крана або візка, Нм:
де =87,4с-1 — кутова швидкість двигуна;
— тривалість гальмування крана з вантажем, с:
Де = 0,2…0,3 м/с2;
зведений до вала двигуна момент інерції рухомих мас, кгм2;
де = 1,1…1,2; - момент інерцiї обертаючих мас,
— момент інерції ротора двигуна, кгм2;
— момент інерції муфти, кгм2;
— радіус колеса, м;
— передаточне число редуктора ;
— загальний ККД.
ТСТ — момент сил опору при усталеному русі навантаженого візка, Нм:
де — опір руху навантаженого візка, Н;
— діаметр ходового колеса, м.
По гальмівному моменту та діаметру гальмівного шківа муфти вибираємо гальмо ТКТ-200/100 (додаток З).
Таблиця 3.6 — Характеристика гальма ТКТ-200/100
Гальмівний момент, Нм | ||
Діаметр гальмівного шківа, мм | ||
Ширина гальмівної колодки, мм | ||
Тип електромагніта | МО100Б | |
Маса, кг | ||
Вибрані гальма перевіряються за тривалістю гальмування ненавантаженого крана або візка за умовою Де ТСТ1 — момент сил опору при усталеному русі ненавантаженого крана при гальмуванні, Нм:
де — опір руху ненавантаженого крана, Н:
Де Н11 — навантаження на горизонтальні ролики ненавантаженого крана, Н:
— Зведений момент інерції рухомих мас, кгм2 :
— мінімальний час гальмування ненавантаженого крана, при якому відсутнє ковзання коліс по рейках (> 1,2), с:
— найменше зусилля на приводні колеса при русі без вантажу, Н:
=0,2 — коефіцієнт зчеплення коліс з рейками при роботі в приміщенні.
4,51>1,296 с Умова виконується.
3.8 Перевірка двигуна Перевірка за часом розгону:
— середній пусковий момент двигуна, Нм:
— номінальний момент двигуна, Нм:
?= 1,5…1,6
Інші складові дивитись в пункті 3.7.
Умова виконується.
Перевірка запаса зчеплення коліс з рейкою:
Де, Wi1 — сила інерції при розгоні ненавантаженого крана, Н:
— опір у цапфах приводних коліс при русі без вантажу, Н:
де — найменше зусилля на приводні колеса при русі без вантажу, Н;
= 0,015 — коефіцієнт тертя у цапфах приводних коліс;
— діаметр цапфи, м.
— коефіцієнт зчеплення колеса з рейкою, при роботі у приміщенні.
Умова виконується Визначимо еквівалентну потужність електродвигуна, яка не допускає перегрівання обмоток, кВт:
де, К25=0,75 — коефіцієнт приведення потужності для режиму роботи М5;
y=1,25 — коефіцієнт який визначає еквівалентну за нагрівом двигуна потужність для механізму пересування крана.
Умова виконується.
ВИСНОВКИ В даній курсовій роботі виконано проектний розрахунок консольного пересувного електричного крана вантажопідйомність 8 тон, режим роботи — важкий (М6).
Розраховано механізм підйому вантажу. Для якого було обрано крановий двигун серії MTF потужність 15 кВт, для передачі крутного моменту обрано редуктор типу Ц2У. Швидкість підіймання вантажу відхиляється від заданої на 2%, дане відхилення знаходиться в допустимих межах. По розрахованому гальмівному моменту було підібрано гальмо — ТКТ-300/200. По розривному зусиллю обрався канат для механізму підйому діаметром 15 мм типу ЛКР. Кратність обраного поліспаста — 2, відповідно число гілок каната що йдуть на барабан — 2.
Розраховано механізм пересування візка. Для забезпечення заданої швидкості пересування візка було обрано двигун серії MTF потужність 2,2 кВт, циліндричний редуктор типу ВКН. Центральна схема приводу. В результаті швидкість пересування візка відхиляється від заданої на 2,7%, що знаходиться в допустимих межах.
Механізм пересування крана розташований біля приводного колеса. Для забезпечення заданої швидкості пересування крана було обрано двигун серії MTF потужність 7,5 кВт. Для передачі крутного моменту було обрано конічно-циліндричний редуктор типу КЦ. В результаті відхилення фактичної швидкості пересування крана від заданої складає 1% що є допустимим відхиленням.
Проектування крана відбувалось на основі вже існуючих прикладів. Розрахунок елементів також зроблений по вже розробленим та прийнятим схемам. Спроектований кран відповідає всім нормам і є класичним прикладом стаціонарного консольного пересувного електричного крана.
ПЕРЕЛІК ВИКОРИСТАНОЙ ЛІТЕРАТУРИ
1 Справочник по кранам: В2 т. /Под общей редакцией М. М. Гохберга — М.: Машиностроение, 1988.
2 Подьемно-транспортные машины. Атлас конструкций /Под редакцией М. П. Александрова и Д. Н. Решетова. — М.: Машиностроение, 1973. — 256 с.
3 Пузырьков П. И. Крюковые подвески грузоподъёмных машин: Учебное пособие.-Днепропетровск:Арт-Пресс, 1999.-128с.
4 Правила устроиства и безопасной эксплуатации грузоподъемных кранов. — Харьков «Форт», 2002 г.
5 Подшипники каченя: Справочник — каталог /О.Н. Черменский, Н. Н, Федотов. — М.: Машиностроение, 2003. — 576 с.
6 Методичні вказівки до курсового проекту «Вантажопідйомна, транспортуюча та транспортна техніка» для студентів спеціальності 8.90 214 «Підйомно-транспортні, будівельні, дорожні машини і обладнання» усіх форм навчання / О.І. Вільчек, В.І. Глушко, О.М. Руднєв. — Запоріжжя: ЗНТУ, 2002. — 66с.
7 Методичні вказівки до курсового проекту «Вантажопідйомна, транспортуюча та транспортна техніка» для студентів спеціальності 8.90 214 «Підйомно-транспортні, будівельні, дорожні машини і обладнання» усіх форм навчання «Розрахунок велосипедного крана» /О.М. Руднєв, М. В. Безкурський. — Запоріжжя: ЗНТУ, 2003. — 62с.
8 Методичні вказівки до курсового проекту «Вантажопідйомна, транспортуюча та транспортна техніка» для студентів спеціальності 8.90 214 «Підйомно-транспортні, будівельні, дорожні машини і обладнання» усіх форм навчання «Розрахунок настінного поворотного крана з електричним талем» /О.М. Руднєв, М. В. Сидоренко, А.К. Корнієнко. — Запоріжжя: ЗНТУ, 2003. — 48 с.
Додаток А
Розрахунок гальма ТКТ-200/100 механізму пересування крана
Виконуємо розрахункову схему колодкового гальма [рис. Б.1].
Рисунок Б.1 — Розрахункова схема колодкового гальма ТКТ-200/100
Необхідний гальмівний момент Тг = 16,35 Н· м.
Діаметр гальмового шківа Де [р] - допустимий питомий тиск між гальмівною накладкою та шківом;
[р] =0,2…0,4 МПа.
Приймаємо [р] =0,2 МПа;
f — коефіцієнт тертя між гальмівною накладкою та шківом;
f =0,35…0,42. Приймаємо f=0,35.
Приймаємо
Задаємося довжиною плечей гальмівного важеля Приймаємо
Приймаємо
Нормальний тиск на колодку гальма Висота гальмової колодки Приймаємо
Ширина гальмової колодки Приймаємо із умови можливості кріплення магніту до важеля гальма.
Необхідна робота відгальмовування для вибору електромагніта
Де — рекомендований відхід колодки для гальма ТКТ-200/100;
— коефіцієнт, що враховує знос накладок та деформацію важелів;
— ККД важільної системи гальма;
Вибираємо електромагніт МО-100Б з умови, А < [А].
Робота розгальмовування магніту МО-100Б Де — максимальний кут повороту якоря, при якому забезпечується момент електромагніта, яки вказаний у технічній характеристиці;
— момент електромагніту;
— для ПВ=40%;
— момент сили ваги якоря;
Зусилля пружини, необхідне для створення розрахункового гальмового моменту Де — плече якоря електромагніта;
Розрахунок ведемо для Р1=344,69 Н.
Припускаємо, що зусилля пружини при розгальмовуванні не перевищить більш ніж на 25% зусилля при загальмовуванні гальма.
Вибір пружини робимо за ГОСТ 13 768–68
Враховуючи необхідність розміщення всередині пружини штоку гальма, вибираємо пружину № 88, 1 класу, що має наступні параметри:
Р3 = 670 Н — зусилля пружини при максимальній деформації;
d = 4,5 мм — діаметр дроту;
D =28 мм — зовнішній діаметр пружини;
Z1 =310,4 Н/ммжорсткість одного витка;
f3 = 2,159 мм — найбільший прогин одного витку.
За умовою стійкості пружини її висота у вільному стані Н0 не повинна перевищувати 5D.
Приймаємо Н0 =120 мм.
Число робочих витків пружини
.
Приймаємо n=18.
Загальне число витків пружини з урахуванням опорних Довжина пружини при загальмованому гальмі
Додаткова деформація пружини при розгальмуванні
Найбільше зусилля в пружині при розгальмуванні
Отже, умова за допустимим зусиллям для підібраної пружини виконується.
Додаток Б
Розрахунок буферного пристрою Механізм пересування крана
Буфери служать для пом’якшення ударів при наїздах на упори. В нашому ви-падку використовуємо гумові буфери. Ці буфери виготовляють монолітними або наборними з ряду пластин (до 20). Вони мають малу віддачу, так як 30−50% кіне-тичної енергії гаситься внутрішнім тертям. До недоліків цих буферів слід віднести порівняно швидке зношування при частих ударах. Розрахунок буферів виконуєть-ся із умови поглинання кінетичної енергії електричної талі з моменту її удару о буфер і до повної зупинки. Попередньо обираємо буфер БР250 ОСТ 24.191.37−78 [рис. Е.1] з такими технічними характеристиками [табл. Е.1]:
Таблиця Е.1 — Технічна характеристика буферу БР250 ОСТ 24.191.37−78.
D | H | Корпус буфера | Фланець | Максимальні робочі | ||||||||
D1 | h | R | Маса | D2 | Н1 | t | зусилля | хід | Е | |||
мм | кг | мм | кН | м | Н м | |||||||
12,8 | 16,5 | 252,5 | 0,0888 | |||||||||
Рисунок .1 — Буферу БР80 ОСТ 24.191.37−78.
Визначимо найбільше зусилля гуми буферу в момент удару, Н:
де m — маса рухомих частин крану (металоконструкції, візка), кг;
V1 — швидкість конструкції в момент удару, м/с;
n — кількість буферів, які одночасно сприймають удар, n=1;
S — хід буферу, S=0,0888 м;
Визначимо напруження стиску в гумовому буфері, МПа:
де F — площа поперечного перерізу гуми буферу, F=0,04 м²;
[?] - допустиме напруження стиску гумового буферу;
де ?в — межа міцності при розриві гуми, ?в=4,5 Мпа;
Отже остаточно обираємо буфер БР250 ОСТ 24.191.37−78 оскільки він задовольняє всім вимогам.
Механізм пересування візка Попередньо обираємо буфер БР160 ОСТ 24.191.37−78 [рис. Е.1] з такими технічними характеристиками [табл. Е.1]:
Таблиця Е.1 — Технічна характеристика буферу БР160 ОСТ 24.191.37−78.
D | H | Корпус буфера | Фланець | Максимальні робочі | ||||||||
D1 | h | R | Маса | D2 | Н1 | t | зусилля | хід | Е | |||
мм | кг | мм | кН | м | Н м | |||||||
4,4 | 162,5 | 52,5 | 0,0544 | |||||||||
Визначимо найбільше зусилля гуми буферу в момент удару, Н:
де m — маса рухомих частин крану (металоконструкції, візка), кг;
V1 — швидкість конструкції в момент удару, м/с;
n — кількість буферів, які одночасно сприймають удар, n=1;
S — хід буферу, S=0,0544 м;
Визначимо напруження стиску в гумовому буфері, МПа:
де F — площа поперечного перерізу гуми буферу, F=0,02 м²;
[?] - допустиме напруження стиску гумового буферу;
де ?в — межа міцності при розриві гуми, ?в=4,5 Мпа;
Отже остаточно обираємо буфер БР160 ОСТ 24.191.37−78 оскільки він задовольняє всім вимогам.
Додаток В Таблиця Б.1 — Канати дротяні сталеві
Діаметр, мм | Маса каната (1000 м), кг. | Маркувальна група, МПа | ||||
Розривне зусилля, кН | ||||||
Канат ЛК-О 67+1 о.с. по ГОСТ 3069–70 | ||||||
3,7 4,0 4,9 5,9 | 47,7 54,0 83,7 120,0 | 6,740 7,640 11,850 16,950 | 7,595 8,590 13,050 18,700 | 8,290 9,375 14,350 20,450 | 8,945 10,100 ; ; | |
Канат ЛК-Р 619+1 о.с. по ГОСТ 2688–80 | ||||||
8,3 9,1 9,9 11,0 12,0 13,0 14,0 15,0 16,5 18,0 19,5 21,0 22,5 24,0 | 256,0 305,0 356,6 461,6 527,0 596,6 728,0 844,0 1025,0 1220,0 1405,0 1635,0 1850,0 2110,0 | ; ; ; ; ; 71,050 86,700 100,000 121,500 145,000 167,000 194,500 220,000 250,500 | 34,800 41,500 48,850 62,850 71,750 81,250 98,950 114,500 139,000 166,000 191,000 222,000 251,000 287,000 | 38,150 45,450 53,450 66,800 78,550 89,000 108,000 125,500 152,000 181,500 209,000 243,500 275,000 314,000 | 41,600 49,600 58,350 75,150 85,750 97,000 118,000 137,000 166,000 198,000 228,000 265,500 303,500 343,000 | |
Канат ЛК-З 625+1 о.с. по ГОСТ 7667–80 | ||||||
8,1 9,7 11,5 13,0 14,5 16,0 17,5 19,5 21,0 | 236,5 342,5 464,0 605,0 763,5 941,5 1140,0 1357,5 1594,0 | ; ; 54,900 71,500 90,350 110,500 134,500 160,000 188,500 | 31,900 46,300 62,700 81,750 102,500 126,500 153,500 183,000 215,000 | 35,100 50,850 68,900 89,450 113,000 139,500 169,000 201,000 236,500 | 38,050 35,100 74,750 97,200 122,500 151,000 183,000 218,500 256,500 | |
Додаток Г Таблиця В.1 — Гаки кранові однорогі машинного приводу за ГОСТ 6627– — 74
Но-мер гака | Вантажопідйомність, т | Номінальні розміри, мм | |||||||||||
Режим роботи | D | S | d1 | d0 | L | не менше | |||||||
3 М, 4 М | 5 М, 6 М | Тип А | Тип Б | ||||||||||
1,0 1,25 1,6 2,0 2,5 3,2 4,0 5,0 6,3 8,0 10,0 12,5 16,0 20,0 25,0 | 0,8 1,0 1,25 1,6 2,0 2,5 3,2 4,0 5,0 6,3 8,0 10,0 12,5 | М20 М20 М24 М27 М30 М33 М36 М42 М48 М52 М56 М64 Трап Трап Трап | |||||||||||
Додаток Д Таблиця Г.1 — Упорні одинарні і подвійні шарикопідшипники ГОСТ 7872 і нестандартні
Додаток Е Таблиця Д.1 — одинарні радіальні шарикопідшипники ГОСТ 8338 і нестандартні
Додаток Є
Таблиця Е.1 — Характеристики кранових двигунів з фазним ротором серії MTF
Типо розмір двигу; на | Потужність Р, кВт і частота обертання ротора n, хв-1 | Момент інерції ротора, кгм2 | Макси; мальний момент, Тmax, Нм | Ма-са, кг | ||||||
ПВ=15% | ПВ=25% | ПВ=40% | ||||||||
Р | n | Р | n | Р | n | |||||
MTF 011−6 012−6 111−6 112−6 211−6 311−6 312−6 411−6 412−6 | 2,0 3,1 4,5 6,5 10,5 14,0 19,5 30,0 40,0 | 1,7 2,7 4,1 5,8 9,0 13,0 17,5 27,0 36,0 | 1,4 2,2 3,5 5,0 7,5 11,0 15,0 22,0 30,0 | 0,022 0,03 0,05 0,07 0,115 0,225 0,312 0,5 0,7 | ||||||
Додаток Ж Таблиця Є.1 — характеристики редукторів типу Ц2
Додаток З Таблиця Ж.1 — Колодкові гальма з короткоходовими електромагнітами
Тип гальма | Діаметр галь; мівного шківа, мм | Шири; на галь; мівної колодки В, мм | Гальмівний момент, Нм при ПВ механізму,% | Відхід колодок від шківа мм | Тип електро-двигуна | Маса гальма з електро магни; том, кг | ||
ТКТ-100 ТКТ-200/100 ТКТ-200 ТКТ-300/200 ТКТ-300 | 0,4 0,4 0,5 0,5 0,7 | МО100Б МО100Б МО200Б МО200Б МО300Б | ||||||
Додаток І
Таблиця З.1 — Основні розміри втулково-пальцьової та зубчастої муфт згальмівним шківом.
А. | Б. | |||||||||
D, мм | D1, мм | к | d | dк | Найбільший гальмівний момент, Нм | B, мН | Момент інерції муфти, кгм2 | Маса муфти, кг | ||
не більш | ||||||||||
А. Пружна втулочно-пальцьова муфта | ||||||||||
; | ; | 19,5 49,5 69,5 89,5 89,5 | 0,008 0,125 0,625 2,25 5,0 | |||||||
Б. Зубчаста муфта | ||||||||||
; ; | ; ; | 64,5 49,5 69,5 89,5 129,5 | 0,1 0,15 0,625 1,75 3,75 | |||||||
Примітка: dк — розміри маточин при конічній розточці.
Додаток К Таблиця І.1 — Основні характеристики ходових коліс та горизонтальних роликів
Дiаметр колеса та тип рейки | 160/Р8 | 200/Р11 | 250/Р15 | |||||||
Режим роботи | Л | С | В | Л | С | В | Л | С | В | |
Швидкiсть руху, м/с | Допускний тиск, кН | |||||||||
0.33 | 26.8 | 15.4 | 10.8 | 42.5 | 23.2 | 16.3 | 70.0 | 58.3 | 50.0 | |
0.67 | 22.9 | 12.6 | 8.7 | 34.6 | 19.0 | 13.2 | 70.0 | 58.3 | 41.5 | |
1.32 | 18.6 | 10.2 | 7.1 | 28.0 | 15.4 | 10.7 | 70.0 | 48.5 | 33.8 | |
1.67 | 17.3 | 9.6 | 6.6 | 26.3 | 14.4 | 10.0 | 70.0 | 46.6 | 31.6 | |
2.0 | 16.2 | 9.0 | 6.2 | 24.9 | 13.4 | 9.4 | 70.0 | 42.2 | 29.6 | |
Дiаметр колеса та тип рейки | 320/Р24 | 400/Р38 | 500/кр70 | |||||||
Режим роботи | Л | С | В | Л | С | В | Л | С | В | |
Швидкiсть руху, м/с | Допускний тиск, кН | |||||||||
0.33 | 65.0 | |||||||||
0.67 | 84.5 | 59.0 | ||||||||
1.32 | 68.5 | 47.8 | 90.0 | |||||||
1.67 | 64.0 | 44.5 | 84.0 | |||||||
2.0 | 60.0 | 42.0 | 78.0 | |||||||
Додаток Л Таблиця К.1 — Характеристики редукторів типу КЦ1