Виготовлення виробів литтям
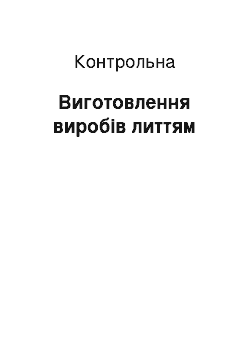
Листи і плитки із шлакосітала (ГОСТ 19 246 — 82) застосовуються в легких зовнішніх стінних панелях для лицювання стін, покриття підлоги в спорудах, а також для футерівки обладнання, яке працює в умовах агресивного середовища абразивного впливу. Листи виготовляються довжиною від 900 до 3600 мм, шириною від 300 до 600 мм, товщиною від 6,8 до10 мм. Плити випускаються шириною і довжиною від 250… Читати ще >
Виготовлення виробів литтям (реферат, курсова, диплом, контрольна)
Міністерство освіти і науки України Національний університет водного господарства та природокористування Кафедра експлуатації гідромеліоративних систем Контрольна розрахункова робота з дисципліни.
«Основи промислової технології і матеріалознавства».
Виготовлення виробыв литтям Виконав:
Студент 1 курсу Групи ЕП — 13.
Мазурок А.А.
Ост. № з/к 38.
Перевірив: Романюк І.В.
Рівне-2006.
Зміст.
- 1. Виготовлення виробів литтям
- 1.1 Загальні відомості про виготовлення виробів литтям
- 1.2 Ливарні сплави та їх властивості
- 1.3 Лиття в разові ливарні форми
- 1.4 Лиття в багаторазові ливарні форми
- 2. Підготовлення металевих форм до заливання розплавом
- 2.1 Лиття в кокіль
- 2.2 Дефекти відливків та їх виправлення
- 3. Скло та скловироби
- 4. Особливості оформлення комплектів документів на процеси кування та штампування
- 5. Розрахунок матеріального балансу технологічних процесів
- 5.1 Економічна ефективність технологічних процесів
- 5.2 Висновки за результатами розрахунків
- Список використаної літератури
1. Виготовлення виробів литтям.
1.1 Загальні відомості про виготовлення виробів литтям.
Лиття — один з найдавніших і найпоширеніших способів виготовлення виробів і заготівок для деталей машин і механізмів.
Литтям називають виготовлення заготівок для виробів заповненням, наперед виготовлених ливарних форм, розплавленим металом, сплавом або іншим конструкційним матеріалом.
Після кристалізації й охолодження металу або сплаву виріб витягують з форми та передають на механічне оброблення.
Відливками називають вироби, виготовленні литтям.
Ливарні форми можуть бути разовими та багаторазовими. Разові форми використовують лише один раз; для звільнення відливка від форми останню руйнують. Багаторазові форми використовують сотні й тисячі разів; відливки витягають з форми витрушуванням або виштовхуванням.
Перші вироби, отримані литтям, належать до ІІІ-ІІ тис. до н. е. Спочатку вироби виливали з бронзи, потім із чавуну. Значного розвитку чавунне лиття набуло в ХІІІ-ХІУ ст. Деталі, вилиті зі сталі, отримали лише в XIX ст., з алюмінієвих і магнієвих сплавів — кілька десятків років тому. Тепер виливають відливки з нержавіючих і жароміцних сталей, магнітних та інших сплавів з особливими властивостями,.
Найдавнішим виробом, отриманим литтям, який маємо в Україні, дзвін. Його відлито у 1341 р. Тепер він знаходиться на дзвіниці Свято-Юрського собору у Львові. Маса цього дзвону становить 415 кг.
Галузь машинобудування, яка займається виготовленням виробів литтям, називають ливарним виробництвом.
Жодна галузь машино — та приладобудування не обходиться без деталей, виготовлених литтям. Частка деталей, виготовлених литтям, у машинах становить близько 50%, а у верстатах — близько 80%. Литтям виготовляють блоки циліндрів і поршні двигунів внутрішнього згоряння, лопаті газових турбін тощо.
Найбільшу кількість відливків — близько 70% загальної маси — виливають із сірого чавуну, далі йдуть сталеві відливки, відливки з мідних, алюмінієвих та інших сплавів.
1.2 Ливарні сплави та їх властивості.
Чисті метали мають незначні ливарні властивості, тому з них не виготовляють відливків. Із сплавів для виготовлення відливків використовують лише ті, які мають добрі ливарні властивості.
Ливарними сплавами називають ті сплави, які мають добрі ливарні властивості.
До них належать чавуни, сталі, бронзи, сілюміни тощо.
Найважливіші ливарні властивості сплавів — текучість розплаву, усадка, ліквація, температура плавлення.
Текучістю називають здатність розплаву швидко заповнювати порожнину ливарної форми.
Текучість сплавів залежить від температури нагрівання: з підвищенням температури текучість розплавів зростає. У процесі виготовлення відливків використовують сплави з оптимальною економічно вигідною температурою плавлення.
Усадкою називають властивість розплавів зменшувати свій об'єм при охолодженні від температури заливання до кімнатної.
Усадка залежить від хімічного складу сплаву, температури заливання розплаву та інших чинників. Розрізняють усадку об'ємну та лінійну.
Ліквацією (від лат. «liquatio» — розтоплення, розплавлення) називають неоднорідність хімічного складу сплаву в різних частинах відливка після кристалізації й охолодження до кімнатної температури.
Ліквація залежить від хімічного складу сплавів і швидкості охолодження відливка. Так, у чавунах і сталях сірка, фосфор і вуглець збираються у верхній і центральній частинах відливка. Важкі компоненти сплавів збираються у нижній частині відливка. Ліквації запобігають перемішуванням розплавів перед заливанням у форми та прискореним охолодженням у процесі кристалізації.
Ліквація істотно впливає на властивості відливка: чим вона менша, тим кращі механічні властивості відливка.
1.3 Лиття в разові ливарні форми.
Найпоширенішими способами лиття в разові форми є лиття в піщано-глиняні форми; лиття в оболонкові форми та у форми, виготовлені за моделями, які витоплюються, розчиняються або перетворюються на газ. Найбільшу кількість відливків виробляють у піщано-глиняних формах.
1.4 Лиття в багаторазові ливарні форми.
Спільним недоліком способів лиття в разові ливарні форми є те, що форми використовують лише один раз і для того, щоб витягнути відливок, форму руйнують.
У формах багаторазового використання можна виготовити сотні тисяч штук відливків. Ці форми виготовляють із чавуну, сталі, алюмінієвих та інших сплавів.
Використання багаторазових форм у ливарному виробництві має ряд переваг порівняно з литтям у разові форми:
відсутність стрижневих і фермових сумішей, модельно-опокового обладнання, дільниць для звільнення форми від моделі та вибування форм;
зменшення кількості пилу в ливарному цеху та поліпшення санітарних умов праці;
обслуговування багаторазових форм не потребує фахових робітників;
вища продуктивність праці;
отримані відливки мають велику щільність, а також точність розмірів і малу шорсткість поверхні, що скорочує або зовсім вилучає механічне оброблення їх на різальних верстатах.
Проте лиття в металеві форми має недоліки: велику вартість металевих форм, через що їх застосовують лише в серійному та масовому виробництві; деякі форми трудно виготовити для відливків складної конфігурації тощо.
Серед відомих способів лиття в багаторазові форми найширше застосовують лиття в кокіль, відцентрове лиття, лиття під тиском тощо.
2. Підготовлення металевих форм до заливання розплавом.
Перед заливанням розплаву у форму на її внутрішню поверхню, яка контактує з розплавом, наносять вогнетривке покриття або спеціальну фарбу, щоб збільшити тривалість використання форми, поліпшити поверхню відливка, полегшити звільнення відливка від форми, а в разі отримання сталевих відливків — запобігти поверхневому гартуванню.
Потім форми нагрівають до температури 100−300°С. Нагрівання форми полегшує заповнення її розплавом і. захищає від передчасного руйнування внаслідок великої різниці температури форми та розплаву.
Металеві форми на відміну від разових не газопроникні, тому для запобігання утворенню браку у форми вставляють газовиводи у вигляді трубок або форму чи розплав вакуумують.
2.1 Лиття в кокіль.
Кокілем (від франц, «coquslle «- черепашка, мушля) називають ливарну форму багаторазового використання, у якій отримують відливки.
Форма може бути суцільною або збірною. Суцільні кокілі використовують для виготовлення малих відливків простої форми. Великі та складні, відливки отримують у збірних кокілях, які складаються з двох півформ. Внутрішні поверхні відливків виготовляють за допомогою стрижнів, які в складній формі можуть бути розбірними. Найчастіше кокілі виготовляють із чавуну та сталі.
Перед заливанням розплаву на внутрішню поверхню кокілю наносять покриття, пульверизатором або помазком і вставляють газовиводи на глибину 0,2−0,5 мм.
Після кристалізації розплаву й охолодження відливок, виштовхують або витрясають з кокілю. Унаслідок швидкого охолодження відливки, отримані в кокілях, мають дрібнокристалічну структуру і відповідно добрі механічні властивості.
В одному кокілі можна виготовити 300−500 сталевих відливків масою 100−150 кг, 5000 дрібних відливків з чавуну або кілька десятків тисяч відливків з алюмінієвих сплавів.
Лиття в кокіль — дуже продуктивний спосіб виготовлення відливків. Залежно від обсягу виробництва всі операції лиття в кокіль виконують ручним, механізованим та автоматизованим: способами. Отримані відливки мають дуже точні: розміри, і малу шорсткість поверхні, що зменшує або зовсім вилучає механічне оброблення на різальних верстатах.
Недоліком цього способу є велика вартість кокілів і труднощі в процесі виготовлення тонкостінних відливків.
Лиття під тиском називають спосіб виготовлення відливків, при якому форму заповнюють розплавом під тиском поршня.
Лиття під тиском — один з найпродуктивніших способів виготовлення невеликих і точних за розмірами відливків в основному із сплавів кольорових металів.
Відливки отримують у сталевих прес-формах. Розплав заповнює прес-форму під тиском поршня до 300 МПа. Після кристалізації розплаву й охолодження відливка прес-форма розкривається і відливок виштовхується в контейнер. При цьому способі лиття можна виготовити відливки з малими отворами (діаметром до 2 мм), різзю та малою товщиною стінок (близько 0,5 мм).
Прес-форму заповнюють розплавом за частки секунди. Одночасно закупорюються газовиводи прес-форми і з її порожнини не повністю витісняється повітря та гази, що утворилися в процесі випаровування та згоряння покриття. Це спричинює утворення газових включень у відливках. Для запобігання цьому прес-форму та розплав перед заливанням вакуумують.
Відливки в прес-формах виготовляють на поршневих машинах. Найчастіше застосовують поршневі машини з холодною та гарячою камерами стискання.
1. Машини з холодною камерою стискання. ЇХ застосовують для виготовлення відливків з алюмінієвих, магнієвих і мідних сплавів, а також із сталі та чавуну.
Машина складається з прес-форми та камери стискання. Камери стискання можуть бути горизонтальними та вертикальними. Тиск поршня на розплав у машині з горизонтальною камерою стискання нижчий, ніж з вертикальною, і становить 40−200 МПа, Машини з горизонтальною камерою стискання застосовують частіше. Вони простіші в обслуговуванні й мають на 10−20% більшу продуктивність.
На машинах з горизонтальною камерою стискання розплав заливають у камеру стискання міркою і подають поршнем до прес-форми, яка складається з рухомої та нерухомої частин.
Після кристалізації розплаву й охолодження відливка, яке триває кілька секунд, прес-форма розкривається; рухома частина прес-форми відходить вліво, відливок разом із литником відокремлюється від форми штовхачами і падає в контейнер. І все починається спочатку: підготовлення форми до заливання розплаву, заливання розплаву в камеру стискання тощо.
2. Машина з гарячою камерою стискання. У цих машинах камера стискання розмішена безпосередньо в тиглі з розплавом і зазнає його дії. Тиск поршня на розплав становить 10−30 МПа. Ці машини застосовують для виготовлення відливків із цинкових, магнієвих і алюмінієвих сплавів, які мають невисоку температуру плавлення. Тиглі виготовляють із матеріалів, які є корозієстійкими в цих розплавах. На цих машинах виготовляють відливки від кількох грамів до 25−30 кг. Це дуже продуктивні машини (понад 3000 відливків за 1 год).
Недоліками, лиття під тиском є малі розміри відливків (максимальна маса, відливка 50 кг), їх пористість, велика вартість і складність виготовлення прес-форм.
2.2 Дефекти відливків та їх виправлення.
Контроль якості відливків починають із зовнішнього їх огляду, потім перевіряють їх розміри, механічні властивості, хімічний; склад та структуру.
Якщо відливки не відповідають вимогам; кажуть, що вони браковані. Основними причинами отримання бракованих відливків є порушення технології виготовлення ливарних форм, заливання їх розплавом та звільнення відливків від форм.
Браковані відливки мають дефекти, основними з яких є раковини (газові, усадкові, шлакові та ін), тріщини (гарячі, холодні), пошкодження поверхні відливків (пригар, оксидні плівки, спаї тощо), невідповідність форми, розмірів і маси відливка кресленню виробу (перекіс, недоливи, переливи, короблення тощо).
Раковини виникають з різних причин. Так, газові раковини мають відливки, виготовлені в сирих формах або у формах, які мають велику здатність виділяти гази та низьку здатність пропускати їх. Погано розкиснений розплав також спричинює утворення газових раковин. Під час різкого переходу від тонкої частини виливка до товстої виникають усадкові раковини та нещільність. Причиною утворення усадкових раковин є надто перегрітий розплав, шлакові раковини спричинені недосконалістю конструкції шлаковловлювачів.
Тріщини у відливках виникають унаслідок недостатньої податливості форм і стрижнів та нерівномірного охолодження. У першому випадку утворюються гарячі тріщини, у другому-холодні.
Дефекти поверхні спричинені недостатньою вогнетривкістю фермової та стрижневої сумішей. Унаслідок цього виникає пригар.
Доливання форми прохолодним розплавом призводить до утворення спаю, який погіршує міцність виробу.
Невідповідність форми, розмірів і маси відливка кресленню виробу може виникнути з багатьох причин: неточно складена форма і вставлені стрижні (буде перекіс), заливання форми прохолодним розплавом (зменшиться його текучість), нерівномірне охолодження окремих частин відливка (спричинить виникнення внутрішніх напружень і, як наслідок, — короблення).
Дефекти поділяють на виправні та невиправні.
Не виправні дефекти мають великі розміри. Виправляти такі дефекти економічно невигідно. Відливки з такими дефектами переплавляють.
Виправні дефекти мають малі розміри, їх економічно, вигідно виправляти.
3. Скло та скловироби.
Скло — це твердий прозорий аморфний матеріал, який отримується охолодженням склоутворюючих сплавів різного хімічного складу. Основу його складають неорганічні окиси, які знаходяться в кварцовому піску, кварцитах або піщинках, мірабліте (у вигляді натрію або кальцієва соди), поташі або калієвої селітри, меле, вапняку, мармуру, доломіту, магнезиту, польових шпатах та ін. У складі скла входять різні домішки: освітлювачі (для видалення газових крапель, хлористий натрій, плавиковий шпат, триоксид миш`яку та ін), глушителі (для виробництва непрозорого скла, сполучення фтору і фосфору); барвники (сполучення кобальту, хрому, срібла, золота, оксиди заліза, міді, та інший металів); безбарвники (для надання скломасі безкольорового вигляду); наповнювачі (скляний бій).
Виробництва скла включає склад шихти, ретельне її подрібнення, змішування і варку в печах при температурі до 1600хС. Отриману скломасу охолоджують до температури, при якій виникає найбільш сприятлива для формування виробів. Будівельне скло і скловироби отримують витяжкою, прокаткою, пресуванням і відливкою, після чого для зменшення крихкості піддають опалюванню. Випалене скло ріжуть на листи (листове), сортують і упаковують для відправки споживачам.
Властивості скла, а відповідно, його сорт визначають хімічним складом, будовою, методами обробітку і наявності дефектів (подряпин, інших включень, газових крапель і т.д.).
Виробництво випускає скло віконне, візерункове, вітринне, арматурне і інше.
Скло віконне (ГОСТ 111−78) призначене для вставлення скла у віконні рами, вітражі, балконні двері, світлових і світло ліхтарів, теплиць, оранжерей, та інших прозорих огорожних конструкцій промислових, сільськогосподарських, житлових та суспільних приміщень та споруд. Виробляється товщиною від 02 до 6 мм, розміром від 500 на 400 до 1600 на 2200 мм, трьох сортів (вищої категорії, 1-го та 2-го сортів). Віконне скло виготовляють прозорим та безкольоровим, допускається зеленуватий та голубуватий відтінок.
Скло листове візерункове (ГОСТ 5533−86) призначене для заповнення світлових щілин і пристроїв для внутрішніх огороджень в приміщеннях і спорудах різного значення. Виготовляють скло товщиною від 3,5 до 7 мм, довжиною від 600 до 2500 мм, шириною від 400 до 1600 мм, 1-го, 2-го сортів безкольорове та кольорове з візерунком на одній або двох сторонах.
Скло вітринне неполіроване (ГОСТ 7380−77) призначене для вставлення скла в вітринні щілини та вітражі суспільних споруд, виставкових, торгівельних, адміністративних, спортивних та інших споруд. Виготовляється товщиною 6,5 мм, розміром листів від 3950×2950 до 1950×1750 мм. Скло випускають безкольоровим, допускається легкі зеленуваті та голубуваті відтінки.
Скло арматурне листове (ГОСТ 7481−78) призначене для вставлення скла в ліхтарі промислових та житлових споруд, віконних сплетінь, дверних фільонок, пристроїв перегородок. Всередині листа скла паралельно його поверхні в процесі формування неперервної стрічки методом горизонтального прокату вміщена світла металічна сітка з комірками прямокутної форми. Поверхня листового арматурного скла звичайно буває кована, з однієї сторони візерункова або рельєфна. Скло виготовляється товщиною 5,5 мм (безкольорове) і 6 мм (кольорове), довжиною від 800 до 2000 мм, шириною від 400 до 1600 мм, вищої якості або 1 -го сорту.
Скло вітринне поліроване (ГОСТ 13 454−77) призначене для виготовлення вітрин і вітражів суспільних споруд. Скло виготовляється товщиною 6,5 і 8 мм, розмірами листів від 4450×2950 до 1380×1340 мм, вищої якості і 1-го сорту.
Будівельні скловироби виготовляють у вигляді труб, блоків, плитки, листів та інше.
Труби скляні і фасонні частини до них (ГОСТ 8894−86) призначене для напірних, безнапірних та вакуумних трубопроводів, що використовуються для транспортування рідких, газоподібних та твердих речовин з різними фізико-хімічними властивостями при температурі від — 50 до 120ъС (в якості деталей апаратів при температурі від — 50 до 250ъС. Труби виготовляються внутрішнім діаметром від 40 до 200 мм, зовнішнім діаметром від 45 до 221 мм, товщиною стінки від 4 до 11 мм. Фасонні частини — це відводи під кутом 90, 75,60, 45, 30 і 15ъ, відводи подвійні, уступи, трійники, рівнопрохідні трійники перехідні, хрестовини і переходи.
Блоки скляні пустотілі (ГОСТ 9272−81) являють собою пустотілі вироби, отримані зварюванням по периметру двох половинок, внутрішня поверхня яких рельєфна або гладенька. Вони виготовляються не пофарбовані та кольорові, квадратної та прямокутної форми довжиною 194, 244 і 294 мм, шириною 194, 244 мм, товщиною 75 і 98 мм, масою 2,8, 3,8, 4,2, 4,3 кг. Склоблоки застосовують для кладки світлопрозорих огороджуючих конструкцій споруд і будівель.
Плитки скляні лицювальні ковро-мозаїчні та коври з них (ГОСТ 17 057−89) виготовляються із кращого скла різного кольору. Застосовують для зовнішнього та внутрішнього лицювання споруд. Плитки виготовляються квадратні та прямокутні товщиною від 4 до 9 мм, розмірами від 100×100 і 200×200 (квадратні), від 120×60 до 250×140 (прямокутні). Лицева сторона лицювальних плиток гладенька або рельєфна, а зворотна рельєфна (для кращого щеплення розчином або мастикою). Коврово-мозаїчні плитки являють собою малорозмірні (до 45 мм) різнокольорові пласкі вироби з кращого скла. Вони постачаються у вигляді коврів, наклеєними лицевою стороною на папір. Після кладки папір змивається водою.
Листи і плитки із шлакосітала (ГОСТ 19 246 — 82) застосовуються в легких зовнішніх стінних панелях для лицювання стін, покриття підлоги в спорудах, а також для футерівки обладнання, яке працює в умовах агресивного середовища абразивного впливу. Листи виготовляються довжиною від 900 до 3600 мм, шириною від 300 до 600 мм, товщиною від 6,8 до10 мм. Плити випускаються шириною і довжиною від 250 до 600 мм, товщиною від 6 до 15 мм. Шлакоситали являють собою склокристалічні матеріали, які отримують із скла і шлаку металургійних заводів. По міцності, водостійкості, кислотостійкості і електроізоляційним властивостям вони мають перевагу над цеглою та бетоном.
До скловиробів відносять також марбліт (прямокутні або квадратні лицювальні плитки із глушаного темно-зеленого або чорного з блискучими вкрапленнями (кристалами) скла, товщиною 5−12 мм), скломармур (лицювальні декоративні плити або листи із скла, які мають різнокольоровий мармуроподібний колір, товщиною 8−25 мм), склокремнезит або склокристаліт (лицювальні декоративні плити, які отримують із гранул скла певного хімічного складу, кремнезему та інших добавок; виготовляється товщиною 15 і 20 мм); піноскло (матеріал пористої структури, який виготовляється випіканням скляного порошку, постачається у вигляді блоків, плит або профільних виробів і застосовується в якості теплоізоляційного декоративного, акустичного і лицювального матеріалів).
Листове скло упаковують у пірамідовидні контейнери (ємністю до 300 м2), ящики із дощок або перекладають папером і складають в пачки (листи площею до 0,1 м2). При цьому листи встановлюють вертикально, торці вирівнюють. Для виключення можливості зміщення вільне місце заповнюють гофрованим картоном, стружкою або іншими матеріалами.
Малогабаритні скловироби складають на торець рядами в пакетах на піддони або в контейнери (склоблоки), стопками (коврово-мозаїчні плитки), дерев`яні ящики або картоні пакети масою нетто не більше 40 кг (лицювальні плитки), касети (решіткова дерев`яна тара масою нетто не більше 50 кг — марбліт склокремнезит, емальовані плитки), паперові або поліетиленові мішки масою до 50 кг.
Труби складають в ящики або контейнери з ущільнювачами. Їх кінці обмотують 3−6 шарами паперу або захищають ковпачками із поліматеріалу. В кожний контейнер або ящик вкладають паспорт з вказівкою найменування заводу-виробника, найменування і сорту скла і його розмір та кількість. На тару наносять попереджувальний напис та знаки: «Обережно, крихке!», «Верх, не кантувати», «Боїться вологи».
Скло та скловироби транспортуються усіма видами критого транспорту запобігають зсувам, коливанням. Тару з листовим склом встановлюють на торець в напрямку руху. При погрузці та розгрузці вживаються заходи, які забезпечують збереження від механічних пошкоджень та опадів. Скло та скловироби зберігають в сухих закритих складський приміщеннях на пірамідах або стелажах, спираючи на гумові, повстяні або дерев`яні прокладки під кутом 10о до вертикалі (листове скло). При довгостроковому зберіганні в вологих умовах в результаті лугування одно і двовалентних оксидів скло може втратити прозорість. Найменший гарантійний термін зберігання у коврово-мозаїчних плиток — не більше 30 діб з моменту виготовлення.
4. Особливості оформлення комплектів документів на процеси кування та штампування.
Одним із прогресивних методів обробки металів є процеси штампування і кування.
Значення вказаних методів обробки на підприємствах галузей промисловості постійно зростає, удосконалюються технології цих методів, обладнання та технологічне оснащення.
ГОСТ 3.1403−85, який визначає види та комплектність технологічних документів (далі по тексту — документів), встановлює і загальні правила оформлення форм документів — карт технологічних процесів (КТП) кування та об`ємного штампування.
Форми документів, які викладені в стандарті - уніфіковані, їх побудова і склад граф для внесення інформації дозволяють виконавцю застосовувати єдиний бланк форми для розробки документів технологічних процесів кування та об`ємного штампування.
Слід відмітити, що форми 1 і 2 є універсальними та не залежать від методу їх проектування, тобто застосовуються при функціонуванні САПР-Т, так і при розробці документів написання від руки.
Розглянемо особливості оформлення документів технологічних процесів (далі процесів) кування, об`ємного та листового штампування.
При розробці документації штампування і кування в форми КТП допускається вводити рядок із службовим символом «Р», необхідний для запису інформації про декілька технологічних режимів, які застосовуються при виконанні операцій. В цьому випадку розміри граф рядка зі службовим символом «Р» визначає розробник документу з врахуванням:
можливості співпадання вертикальних ліній, які розмежовують графи попередніх рядків, з лініями, які розмежовують графи рядка із службовим символом «Р», для більш доцільної побудови рядків документу;
необхідність запису в графах рядка «Р» інформації про конкретні параметри технологічних режимів з зазначенням, в ряді випадків, відповідних одиниць величин.
Аналогічні положення про введення рядка із службовим символом «Р» в маршрутну карту (МК), визначену ГОСТ 3.1118−82, яка застосовується при розробці документів листового штампування та, в ряді випадків, кування.
При цьому необхідно підкреслити, що технологічні режими допускається вказувати в змісті операції на тих же рядках (на одному рядку), тобто на рядках із службовим символом «О» .
В залежності від деталізації опису змісту процесу (маршрутний, маршрутно-операційний або операційний) склад комплекту документів відповідного процесу буде різний.
Розробка документів одиничного технологічного процесу (ОТП) маршрутного опису кування або об`ємного штампування визначається застосуванням карт технологічного процесу, який передбачає опис всіх операцій виготовлення виробу (наприклад, кування), які виконуються в одному виробничому підрозділі заводу.
В цьому випадку КТП замінює в комплекті документів процесу МК, і в КТП вказують зміст всіх операцій виготовлення виробу, включаючи операції технологічного контролю транспортування, збору і здавання технологічних відходів.
З метою скорочення термінів розробки документації допускається в комплект документів об`ємного штампування і кування вводити обліковану копію креслення (графічний документ на ковку), оформлення якого проводиться відповідно з вимогами ГОСТ 3.1126−88.
Розробка документів ЄТП з використанням маршрутних карт, які виконують функції документів встановлених діючим стандартом дозволить скоротити кількість видів форм документів, які застосовуються на виробництві. В цьому випадку необхідно враховувати деякі особливості оформлення МК.
Наприклад, при заміні форм КТП кування і об`ємного штампування маршрутною карткою, інформацію характерну для КТП, необхідно записувати в графу МК, яка виділена для особливих вказівок; рядки з інформацією про елементи витрат матеріалу, властиві КТП, необхідно розміщувати в МК після рядка із службовими символами «Б» або «К/М».
Розробка документів одиничних технологічних процесів листового штампування характеризується застосуванням МК в якості КТП (МК/КТП) при маршрутному опису процесу і в якості ОК листового штампування (МК/ОК) при операційному опису процесу.
Дозволяється не вказувати в документах процесів інформацію про трудовитрати при умові розробки техніко-нормувальних карт (ТНК), правила оформлення яких наведенні в рекомендаціях Р 50−72−88. ТНК в цьому випадку можуть бути включенні в склад комплекту документів процесів; позначення цього виду документа вибирається розробником процесу по правилам, які встановленні ГОСТ 3.1201−85, використовуючи резервний код.
Комплекти документів типових технологічних процесів кування та об`ємного штампування можуть бути представлені в кількох варіантах за рахунок введення в них різних видів документів.
Один із варіантів — застосування при розробці ТТП документів, встановлених ГОСТ 3.1121−84; їх оформлення в загальному випадку зв`язане з включенням в бланки форм відомості деталей до ТТП (ГТП) або типовим операціям (ТО) — ВТО блоків інформації про елементи витрат матеріалу і їх масі. Графи інформації є в формах КТП, встановлених ГОСТ 3.1403−85, наприклад рядок «МОЗ» в формі 1 вказаного стандарту, тобто рядок елементів витрат матеріалу.
Вся дана інформація заноситься в ВТП і вказується «в прив’язці» до відповідного позначення виробу по конструкторському документу.
В основному надпису карт типових ТП (ГОСТ 3,1121−84) або МК/КТТП позначення виробів, які виготовляються по ТТП — не проставляється.
В КТП/КТІ або МК/КТІ вноситься перемінна інформація про кожен виріб одного позначення. При цьому варіанті в комплект документів необхідно вводити відомість технологічних документів (ВТД), встановлено ГОСТ 3,1122/84, для показу в ній складу для проведення оперативної роботи з документами ТТП.
В комплектах документів ЄТП, ТТП і ТО широко застосовують карти ескізів (КЕ) для розробки креслень кування відображення даних по розмірам заготовок, їх виготовлених розмірів. Необхідно підкреслити, що з метою скорочення кількості документів, які застосовуються в виробництві, зображення ескізів на формах, встановлених ЄСТД, може виконуватися в нижній зоні форми. В цьому випадку нижній зоні полі документа присвоюється службовий символ «О» .
Розробка комплектів документів на типові ТП листового штампування характеризується застосуванням одного виду документа — МК як основного документа. В комплект документів типових процесів можуть входити — МК/КТІ листового штампування. Основною відмінністю складу документів ТТП кування і штампування є включення в них форм КТІ викройки заготовок або МК/КТІ визначених правилами ГОСТ 3,1402−84.
В зміст процесів кування і штампування необхідно включати операції збору і здачі технологічних відходів.
5. Розрахунок матеріального балансу технологічних процесів.
Дано: загальна початкова маса сировини і матеріалів -5500 кг, в ній сухого вапняку, мергелю та вугілля відповідно 15%, 29%, 6%. Вологість мінеральної сировини 25%, вологість повітря 51%. В 1 ТП одержано 1200 кг клінкеру і 60% кисню і в 2ТП — 1800 кг клінкеру і 55% кисню.
Розв’язання:
Визначаємо всі вхідні початкові матеріали: в процесі переробки використовують вапняк, мергель, вугілля, повітря, які вміщують вологу.
Визначаємо маси вапняку, мергелю, вугілля в сухому стані за відносною кількістю від початкової маси всієї речовини:
Хвапняку = (М*х%) /100% = (5500*15) /100=825 кг;
Хмергелю = (М*х%) /100% = (5500*29) /100 = 1595 кг;
Хвугілля = (М*х%) /100% = (5500*6) /100 =330 кг;
Визначаємо загальну масу мінеральної сировини в сухому стані:
825+1595+330=2750 кг;
Розраховуємо загальну масу мінеральної сировини з водою:
(2750*100%) / (100% -25%) = 3667 кг;
Розраховуємо масу води, яка знаходилася в мінеральній сировині:
3667−2750 = 917 кг;
Визначаємо із умов балансу кількість повітря, що використовується в процесі випалювання клінкеру:
5500−3667 =1833 кг;
Розраховуємо кількість вологи в повітрі за його вологістю:
(1833*51%) /100% = 935 кг;
Визначаємо кількість сухого повітря:
1833−935 = 898 кг;
Визначаємо загальну кількість вологи, що була в матеріалах:
917+935 = 1852 кг;
Перевіряємо баланс вхідних матеріалів у твердій, рідкій та газовій формах:
825+1595+330+1852+898 = 5500 кг;
Визначаємо кількість одержаного кисню в 1 та 2 процесах:
1 ТП = (5500*60%) /100% = 3300 кг;
2 ТП = (5500*55%) /100% = 3025 кг;
Розраховуємо загальну масу одержаної продукції:
1 ТП = 1200+3300 = 4500 кг;
2 ТП = 1800+3025 = 4825 кг;
Розраховуємо кількість виробничих втрат матеріалів:
1 ТП = 5500−4500 = 1000 кг;
2 ТП = 5500−4825 = 675 кг.
За результатами розрахунків складаємо таблиці МБ для 1 ТП і 2 ТП, розраховуємо в таблицях кількість матеріалів у відносних одиницях:
Матеріальний баланс 1 ТП.
Сировина і матеріали. | Продукція та витрати. | |||||
Назва. | Маса, кг. | %. | Назва. | Маса, кг. | %. | |
Вапняк сухий. | Клінкер | |||||
Мергель сухий. | Кисень. | |||||
Вугілля сухе. | Втрати. | |||||
Повітря сухе. | ||||||
Вода. | ||||||
Всього. | Всього. | |||||
Матеріальний баланс 2 ТП.
Сировина і матеріали. | Продукція та витрати. | |||||
Назва. | Маса, кг. | %. | Назва. | Маса, кг. | %. | |
Вапняк сухий. | Клінкер | |||||
Мергель сухий. | Кисень. | |||||
Вугілля сухе. | Втрати. | |||||
Повітря сухе. | ||||||
Вода. | ||||||
Всього. | Всього. | |||||
Визначаємо втрати мінеральної сировини на одиницю основної продукції:
1 ТП = (825+1595+330) /1200 = 2,29 кг/кг;
2 ТП = (825+1595+330) /1800 = 1,53 кг/кг.
Аналізуємо результати розрахунків і за кількістю відходів та питомою витратою мінеральних ресурсів визначаємо більш раціональний ТП: за втратами — другий, за матеріалоємністю та виходом основної продукції - другий.
5.1 Економічна ефективність технологічних процесів.
Дано: Річна програма машинобудівного підприємства Nп=125 шт., маса деталі q=8 кг, Вартість 1 кг матеріалу См =1,2 грн., коефіцієнт використання матеріалу в ТП1 = 0,75 ТП 2 = 0,65, заробітна плата наладчиків в ТП1 Сн = 5000 грн., в ТП2 Сн = 8400 грн., вартість спеціальної оснастки в ТП1 і=4000 грн., в ТП2 і=9200 грн., норма штучного часу виготовлення деталей в 1ТП tшт=47 год., в 2ТП tшт=52 год., кількість технологічних операцій в 1ТП n=8, 2ТП n=10, тарифна ставка виконання операцій в 1ТП r=3грн/год, в 2ТП r=2грн/год, норма відрахувань на соціальні потреби Св=32%, накладні витрати поточного характеру в 1ТП =59, в 2ТП =44%, коефіцієнт використання оснастки в ТП1 k=0,62, в ТП2 k=0,82.
Розв’язання:
1. Розраховуємо масу початкового матеріалу для виготовлення всієї партії деталей:
М1 = (q*N) /1 = (8*125) /0,75 = 1333,3 кг;
М2 = (q*N) /2 = (8*125) /0,65 = 1538,5 кг.
2. Визначаємо вартість матеріалу:
m1= См*М1 =1,2*1333,3 = 1599,96 грн.;
m2= См*М2 =1,2*1538,5 = 1846,2 грн.
3. Розраховуємо заробітну плату основних робітників, задіяних у ТП:
Зпл1 = tшт.1*r1*n1 = 47*3*8 =1128 грн.;
Зпл2 = tшт.2*r2*n2 = 52*2*10 = 1040 грн.
4. Визначаємо величину нарахувань на заробітну плату:
Н1 = (Зпл.1*Св) /100% = (1128*32) /100 = 361 грн.;
Н2 = (Зпл.2*Св) /100% = (1040*32) /100 = 333 грн.
5. Визначаємо заробітну плату основних робітників з нарахуваннями:
З1 = Зпл.1+Н1 = 1128+361 = 1489 грн.;
З2 = Зпл.2+Н2 =1040+333 = 1373 грн.
6. Визначаємо накладні витрати поточного характеру:
В1= (Зпл.1*1) /100% = (1128*59) /100 = 665,5 грн.;
В2= (Зпл.2*2) /100% = (1040*44) /100 = 457,6 грн.
7. Розраховуємо поточні витрати на виготовлення заданої партії деталей:
а1=m1+З1+В1 = 1599,96+1489+665,5 = 3755 грн.;
а2=m2+З2+В2 = 1846,2+1373+457,6 = 3676,8 грн.
8. Розраховуємо одноразові поточні витрати на створення технологічних ліній:
в1=Сн1+і1*k1 = 5000+4000*0,62 = 7480 грн.;
в2=Сн2+і2*k2 = 8400+9200*0,82 = 15 944 грн.
9. Визначаємо розміри критичної партії продукції 2 ТП:
Nкр. = (в2 — в1) / (а1 — а2) = (15 944−7480) / (3755−3676,8) = 108 шт.
10. Будуємо графік порівняння собівартості виготовлення партій деталей за 1ТП і 2ТП:
S1=а1*N+в1 = 3,8*125+7,5= 482,5 тис. грн.;
S2=а2*N+в2 = 3,7*125+15,9 = 478,4 тис. грн.
Графік порівняння собівартості процесів.
5.2 Висновки за результатами розрахунків.
За річного випуску продукції менше 108 шт. економічно доцільно використовувати перший варіант ТП, при річній програмі більше 108 доцільно прийняти другий варіант ТП, оскільки собівартість випуску продукції є меншою.
Визначаємо собівартість однієї деталі в заданій партії:
S1од. = (482,5*1000) /125=3860 грн.;
S2од. = (478,4*1000) /125=3827 грн.
Визначення коефіцієнта використання матеріалів.
Визначити КВМ при виготовленні стакана діаметром D=80мм, висотою h=45мм, отвором у дні діаметром d=30мм. Товщина стрічки t=2,5 мм і довжиною L=2000мм.
Розв’язання:
Для виготовлення просторового виробу типу стакан виготовляють у формозмінюванних штампах за допомогою таких операцій як:
1 — вирубування отвору;
2 — відокремлення заготовки від матеріалу;
3 — витягування стакана на висоту h.
Намалюємо схему розкладки деталі в стрічці.
Для виготовлення виробу типу стакан діаметром D і висотою h необхідно спочатку вирубати заготовку у формі круга D0, витягнути стакан.
Діаметр заготовки D0 визначається за умовою:
(D02) /4+ Dh.
D0=D2+4Dh.
D0=802+4*80*45=144,2 мм.
З таблиці № 1 методички, виходячи з товщини стрічки матеріалу t=2,5 мм визначаємо ширину кромки і ширину перемички:
в=а=2,0 мм.
Крок подачі стрічки дорівнює найбільшому розміру деталі в напрямі подачі:
К=в=144,2+2=146,2 мм;
Визначаємо ширину стрічки:
В=D0+2*а=144,2+2*2,0=148,2 мм.
Визначаємо кількість деталей, яку можна виготовити із стрічки:
Nд=L/K=2000/146.2=13 шт.
Визначаємо чисту площу однієї деталі:
Fg=Fk-Fотв.
Fk= (D2) /4=3,14* (144,2) 2/4=16 323мм2.
Fотв= (d2) /4=3,14*302/4=706,5 мм2.
Fg=16 323−706,5=15 616,5 мм2.
Визначаємо КВМ:
КВМ= (Nд*Fg) /ВL=13*15 616,5/149*2000*100%=68%.
Висновок: раціональне використання матеріалу.
Список використаної літератури.
1. «Основи технології». — Збожна О. М. — 2002.
2. Технологические документации. — справочное пособие. — 1992.
3. Ассортиментный справочник по промышленному сырью и материалов. — Войчар А. В., Мальченко А. М. — 1991.