Розробка технологічного процесу виготовлення деталі — «Корпус»
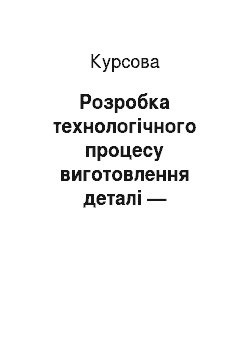
Вибір виду і форми заготовки Спосіб лиття для деталі не заданий. Оскільки деталь містить необроблювані поверхні, то за рекомендаціями вибір способу лиття проводимо за чотирма ознаками: — точність розмірів і висота шорсткості таких поверхонь, а також матеріал і тип виробництва (середньосерійний) — (табл. 2.2.1.). Спосіб вважається обраним, якщо значення усіх чотирьох ознак в таблиці, характерних… Читати ще >
Розробка технологічного процесу виготовлення деталі — «Корпус» (реферат, курсова, диплом, контрольна)
Міністерство освіти і науки України Житомирський державний технологічний університет Кафедра ТМ і КТС Група МС-112
Курсовий проект з дисципліни: «Технологія машинобудування»
Тема: «Розробка технологічного процесу виготовлення деталі - «Корпус» «
Житомир
Зміст Завдання на проектування Вступ
1. Призначення і характеристика об'єкта виробництва
2. Технологічний розділ:
2.1 Аналіз технологічності деталі
2.2 Вибір виду і форми заготовки
2.3 Розрахунок припусків на обробку
2.3.1 Розрахунок припусків табличним методом
2.3.2 Визначення припусків розрахунково-аналітичним методом
2.4 Розробка технологічного процесу
2.5 Вибір металорізального обладнання
2.6 Розрахунок режимів різання
2.7 Технічне нормування технологічного процесу
3. Організаційний розділ
4. Конструкторський розділ
4.1 Обґрунтування необхідності проектування спеціального пристрою для однієї з операцій
4.2 Розробка теоретичної схеми базування та затискання на заданій операції
4.3 Розрахунок похибок базування, затискання та встановлення заготовки в пристрої
4.4 Розробка загальної схеми взаємодії сил та моментів, що діють на заготовку. Визначення необхідної величини сили затискання
4.5 Визначення фактичної сили затискання заготовки в пристрої
4.6 Опис принципу роботи спроектованого пристрою
4.7 Технічні вимоги на виготовлення конструкції пристрою Література
Завдання на проектування Вихідними даними для проектування є:
— робоче креслення деталі типу «Корпус», для якої розробляється технологічний процес (наведено в додатку до курсової роботи);
— річна програма випуску деталей: N = 5000 шт./рік.
За цим даними необхідно спроектувати операційний технологічний процес виготовлення заданої деталі.
Вступ Машинобудування — провідний комплекс галузей в промисловості. Його рівень визначає подальший розвиток всього народного господарства.
Розвиток машинобудування ставить нові проблеми, пов’язані з підвищенням якості виробів, продуктивності праці і вимагає їх вирішення. Сучасне машинобудування використовується практично в усіх сферах людської діяльності, досягло величезних успіхів у підвищенні її ефективності і врешті перетворилось у технологічну базу промисловості, що визначає рівень технічного розвитку країни та її безпеки.
Технологія машинобудування, як галузь науки, займається дослідженням технологічних процесів виготовлення машинобудівних виробів з метою використання результатів дослідження для забезпечення необхідної якості та кількості виробів з найвищими техніко-економічними показниками.
Сучасна технологія розвивається за наступними основними напрямками: створення нових матеріалів; розробка нових технологічних принципів, методів, процесів, обладнання; механізація і автоматизація технологічних процесів, що зменшує безпосередню участь в них людини.
Будівництво матеріально-технічної бази і необхідність безперервного підвищення продуктивності праці на основі сучасних засобів виробництва ставить перед машинобудуванням досить відповідальні задачі. До їх числа відносяться підвищення якості машин, зниження їх матеріаломісткості, трудомісткості і собівартості виготовлення, нормалізація та уніфікація їх елементів, запровадження поточних методів виробництва, його механізація і автоматизація, а також скорочення термінів підготовки виробництва нових об'єктів. Вирішення вказаних задач забезпечується поліпшенням конструкції машин, удосконаленням технології їх виготовлення, застосуванням прогресивних засобів і методів виробництва.
У зв’язку з неперервно зростаючими вимогами до якості виробів, швидкої зміни номенклатури виробів зростає обсяг технологічної підготовки виробництва за одиницю часу. Таким чином виникає проблема, яка полягає в тому, що технолог в сучасних умовах повинен виконувати не тільки більший обсяг роботи, а й робити її на більш якісному рівні. Вирішення цієї проблеми полягає в автоматизації праці технолога, а це в свою чергу, вимагає подальшого розвитку наукових основ технології машинобудування. Все це повинно проходити в напряму більш глибокого вивчення закономірностей технологічних процесів, підвищення рівня узагальнень, формалізації результатів досліджень, застосування математичних методів, удосконалення методів розрахунку та розробки технологічних процесів, проектування засобів технологічного оснащення, методів організації технологічної підготовки виробництва.
1. Призначення і характеристика об'єкта виробництва Призначення деталі
По заводському шифру на кресленні деталі визначаємо, що вона входить до приводу поздовжніх подач револьверного супорту верстату 1В340Ф30.
Токарно-револьверний верстат з револьверною головкою на хрестовому супорті з ОСУ підвищеної точності мод. 1В340Ф30 призначений для виконання різноманітних токарних робіт у межах встановленої потужності, в основному, при обробці складних деталей зі ступінчатим і криволінійним профілем. Верстат призначений для роботи в умовах серійного та дрібносерійного виробництва.
Основні переваги верстату:
— конструкція 8-ми позиційної револьверної головки забезпечує високу жорсткість (фіксація головки на плоскі зубчасті колеса) і високу швидкодію;
— обробка деталей з прутка в автоматичному циклі;
— широкий діапазон нарізуваних різьб, включаючи багатозаходні;
— хрестовий супорт з вертикальною віссю револьверної головки дозволяє виконувати всі види токарної обробки малою кількістю інструментів;
— наявність оперативної системи управління дозволяє робітнику на робочому місці, в ході обробки першої деталі за допомогою засобів ручного управління та використовуючи елементи автоматичного управління формувати керуючу програму, яка дозволяє уже наступну деталь обробляти в автоматичному циклі.
Задана деталь (корпус) призначена для закріплення кулькової гвинтової пари поздовжнього переміщення супорту верстата.
Поздовжні переміщення револьверного супорту здійснюються за допомогою високомоментного електродвигуна, що встановлюється на кронштейні, який кріпиться до правого торцю станини. Обертання двигуна на пару гвинт-гайка кочення передається зубчастою пасовою передачею. Опорою гвинта служать підшипники, що встановлюються в КОРПУС (задана деталь), який жорстко кріпиться на правому торці станини. Для контролю положення револьверного супорту існує датчик зворотного зв’язку, вал якого з'єднаний з парою гвинт-гайка кочення за допомогою спеціальної муфти. Натягування зубчастого пасу здійснюється переміщенням кронштейну у вертикальній площині.
Характеристика матеріалу деталі
Матеріал деталі, виходячи з креслення, — сірий чавун СЧ 20. Сірий чавун є технологічним матеріалом, йому властива гарна рідко текучість, мала схильність до утворення усадочних дефектів в порівнянні із чавунами інших типів. З нього можна виготовляти виливки самої складної конфігурації з товщиною стінок від 2 до 500 мм. Механічні властивості сірого чавуну забезпечуються в литому стані або після термічної обробки.
Область застосування чавуну СЧ 20 наведена в табл. 1.1.:
Таблиця 1.1. Застосування чавуну СЧ 20
Вимоги до деталей | Деталі, що виготовляються | |
Умовні напруження згину приблизно до 30 МПа | Станини довбальних верстатів, вертикальні стійки фрезерних, стругальних та розточувальних верстатів | |
Умовні тиски між поверхнями, що труться > 0,5 МПа (> 0,15 МПа у виливках масою більше 10 т) або піддавання поверхонь загартуванню | Станини з направляючими більшості металорізальних верстатів, зубчасті колеса, маховики, гальмівні барабани, диски зчеплення | |
Висока герметичність | Гідро циліндри, гільзи, корпуси гідронасосів, золотників і клапанів середнього тиску) до 8 МПа) | |
Механічні властивості матеріалу заданої деталі представлені у табл. 1.2.
Таблиця 1.2. Механічні властивості сірого чавуну СЧ 20 за ГОСТ 1412–85
Товщина стінки, мм | Границя міцності на розтяг, МПа, не менше | Твердість НВ | |
Хімічний склад чавуну вказаний в табл. 1.3.
Таблиця 1.3. Масова доля складових елементів сірого чавуну СЧ 20, у %
C | Si | Mn | P | S | |
не більше | |||||
3,3 — 3,5 | 1,4 — 1,7 | 0,6 — 0,9 | 0,3 | 0,12 | |
2. Технологічний розділ
2.1 Аналіз технологічності деталі
Деталь виготовляється з сірого чавуну литтям, тому конфігурація зовнішнього контуру і внутрішніх поверхонь не викликає значних труднощів при отриманні заготовки. Однак виливка потребує застосування стержневої формовки для утворення внутрішніх порожнин (для формування внутрішніх отворів застосовується збірні стержні).
Багато поверхонь деталі необроблювані, тобто отримуються литтям.
До внутрішніх оброблюваних поверхонь ш 85Н7 та ш 95Н7, окрім точності обробки самих отворів, ставиться жорсткий доступ щодо їх співвісності. Такі вимоги можуть бути забезпечені обробкою поверхонь з однієї установки. Форма і розташування отворів зручні для обробки з одного боку виливки.
До плоских поверхонь висуваються вимоги щодо їх паралельності, це забезпечується при взаємному їх базуванні. Конструкція деталі допускає обробку площин на прохід, такій обробці нічого не заважає.
Передбачена обробка ряду глухих отворів, що використовуватимуться як кріпильні, тому наскрізними отворами їх замінити не можна.
Дещо складною є обробка отворів, розташованих на зовнішній циліндричні поверхні. Отвори розташовані під різними кутами до площини входу-виходу. Тому така обробка вимагає спеціального поворотного пристрою.
В цілому деталь є досить технологічною, допускає застосування високопродуктивних режимів обробки, оскільки:
— до оброблюваних поверхонь є вільний доступ інструмента;
— жорсткість деталі є достатньою і не обмежує режимів різання;
— базові поверхні мають велику протяжність;
— відсутні оброблювані площини, що розташовані під тупими або гострими кутами;
— в конструкції відсутні внутрішні різьби великого діаметру.
2.2 Вибір виду і форми заготовки Спосіб лиття для деталі не заданий. Оскільки деталь містить необроблювані поверхні, то за рекомендаціями [п.3, 10] вибір способу лиття проводимо за чотирма ознаками: — точність розмірів і висота шорсткості таких поверхонь, а також матеріал і тип виробництва (середньосерійний) — (табл. 2.2.1.). Спосіб вважається обраним, якщо значення усіх чотирьох ознак в таблиці, характерних для цього способу, відповідають значенням цих ознак, наведеним у кресленні деталі.
Таблиця 2.2.1. Алгоритм вибору основних способів лиття
Спосіб лиття | Умови вибору основних способів лиття | |||||||
Економічно рекомендована товщина стінки, мм | Найменший діаметр отвору, що проливається, мм | Найменший радіус скруглення, мм | Точність розмірів, в квалітетах | Висота шорсткості по Ra, мкм | Матеріал заготовки | Тип виробництва заготовок | ||
Під тиском | 2…4 | 0,5 | 10…14 | 2,5…0,32 | Кольорові сплави | с/с, б/с, масовий | ||
В кокіль | 5…12 | 12…16 | 20…2,5 | Кольорові сплави, чавун | с/с, б/с, масовий | |||
По виплавлюваним моделям | 2…7 | 12…14 | 10…1,25 | Сталь, кольорові сплави | д/с, с/с, б/с, масовий | |||
В оболонкові форми | 4…9 | 11…14 | 20…2,5 | Кольорові сплави, сталь, чавун | с/с, б/с | |||
В піщані форми | 5…15 | 14…17 | 80…10 | Будь-який | одиничний, д/с, с/с | |||
Відцентрове | 5…20 | ; | ; | 12…16 | 40…5 | Чавун, сталь, бронза | с/с, б/с, масовий | |
За наведеними чотирма основними ознаками для деталі за заданим кресленням відповідає лиття у піщано-глинисті форми. Такий же спосіб рекомендовано згідно [табл.4.2., 11].
Згідно [п.14, 10] оцінимо вибраний спосіб лиття за запропонованими економічними оціночними показниками.
Таблиця 2.2.2. Показники порівняння основних способів лиття (чим менше число, тим кращий показник: 1 — найкращий; 5 — найгірший)
Спосіб лиття | Продук-тивність | Вихід годного (якість лиття) | Вартість оснастки | Тривалість засвоєння технології лиття | Ріст економічності із ростом серійності | Сума балів | |
Під тиском | |||||||
В кокіль | |||||||
По виплавлюваним моделям | |||||||
В оболонкові форми | |||||||
В піщані форми | |||||||
За показниками табл. 2.2.2. обраний спосіб лиття є найбільш економічно вигідним.
Зобразимо форму майбутньої заготовки, встановимо розміри, що визначають її. Серед них виділимо виконавчі розміри (ті, за якими ведеться розрахунок припусків) і позначимо їх великими буквами латинського алфавіту (A, B, C …).
Решта розмірів не мають відношення до оброблюваних поверхонь. За ними не ведеться розрахунок припусків (розміри для довідок, розміри необроблюваних поверхонь, кутові розміри…).
Розрахунок виливки для заданої деталі будемо проводити згідно.
Таблиця 2.3.1. Параметри відливки згідно ГОСТ 26 645–85
Спосіб лиття | в піщано-глинисті форми | |||||||||||
Клас розмірної точності виливок | ||||||||||||
Степінь точності поверхні виливок | ||||||||||||
Ряд припусків на механічну обробку | ||||||||||||
Степінь жолоблення елементів виливок | ||||||||||||
Допуск нерівностей поверхні виливки, мм | 1,2 | |||||||||||
Допуск форми і розташування поверхонь виливки, мм (Тфрп. отл.) | 1,6 | |||||||||||
Допуск маси виливки = 12%Gотл., кг | 0,052 | |||||||||||
Мінімальний ливарний припуск на сторону, мм | ||||||||||||
Клас точності маси | ||||||||||||
Виконавчий розмір | Допуск розміру деталі, мм (Тр.д.) | Допуск розміру виливки, мм (Тр.отл.) | Допуск форми і розташування поверхонь деталі, мм Тфрп. д. = 0,25Тр.д. | Вид обробки за співвідношенням Тр.д./Тр.отл. | Вид обробки за співвідношенням Тфрп. д/ Тфрп. отл. | Результуючий вид обробки | Загальний допуск, мм Тобщ. | Припуск на сторону, мм (Прст.) | Середній розмір деталі, мм | Кінцевий розмір виливки, мм | ||
A | Ш 95H7 (+0,035) | 0,035 | 2,2 | 0,875 | Тонка | Тонка | Тонка | 3,2 | 3,1 | 95,0175 | 88,82 | |
B | Ш 85H7 (+0,035) | 0,035 | 2,2 | 0,875 | Тонка | Тонка | Тонка | 3,2 | 3,1 | 85,0175 | 78,82 | |
C | 130 IT14/2 ± 0,500 | 1,0 | 2,4 | 0,25 | Напівчистова | Чистова | Чистова | 3,2 | 3,0 | |||
2.3 Розрахунок припусків на обробку
2.3.1 Розрахунок припусків табличним методом Розрахунок виливки за цим методом будемо проводити згідно 3 — [3]:
За табл. 9, в залежності від вибраного способу лиття, найбільшого габаритного розміру виливки (318 мм) та типу сплаву (сірий чавун) визначимо клас розмірної точності виливок 7 — 12. Для заданого типу виробництва (середньосерійного) найдоцільніше обрати клас розмірної точності — 9.
За табл. 11, в залежності від вибраного способу лиття, найбільшого габаритного розміру виливки (318 мм) та типу сплаву (сірий чавун) визначимо степінь точності поверхонь виливок 10 — 17. Для заданого типу виробництва (середньосерійного) оберемо степінь точності поверхонь виливок — 15.
За табл. 12, обраному степеню точності поверхонь виливок — 9, відповідає шорсткість поверхні Ra = 50 мкм.
За табл. 14, в залежності від вибраного степеню точності поверхні, визначимо ряд припусків на подальшу механічну обробку — 8 (6…9).
Мінімальний ливарний припуск на обробку поверхні виливки для усунення нерівностей та дефектів литої поверхні призначаємо в залежності від ряду припусків за табл. 5, [3]: мінімальний ливарний припуск на сторону — 1 мм.
За табл. 10, в залежності від відношення найменшого розміру виливки до найбільшого (16/318 0,0503) визначимо степінь жолоблення елементів виливки — (5…8) 7.
За табл. 2, в залежності від степеню жолоблення елементів виливки (7) та номінального розміру нормованої ділянки виливки (найбільша ділянка для якої регламентується форма і розташування поверхні = 318 мм) визначимо допуск форми і розташування поверхонь виливки = 1,6 мм.
В залежності від степені точності поверхонь виливки визначимо за табл. 3, допуск нерівностей поверхонь виливки — 1,2 мм.
За [ГОСТ 25 347−82] визначимо допуски та граничні відхилення розмірів деталі. Всі попередні і подальші результати зводимо в табл. 2.3.1.
За табл. 1, в залежності від класу розмірної точності та номінального розміру виливки (за номінальний розмір виливки приймаємо відповідний номінальний розмір деталі, що задана) визначаємо для кожного виконавчого розміру допуск розміру виливки.
За табл. 7, в залежності від допуску відповідного розміру виливки та співвідношенням між допусками розміру деталі та виливки попередньо визначаємо вид завершальної механічної обробки кожної поверхні.
За табл. 8, в залежності від допуску відповідного розміру виливки та співвідношенням між допусками форми і розташування поверхонь деталі та виливки попередньо визначаємо вид завершальної механічної обробки кожної поверхні.
Співставляючи отримані результати, приймаємо остаточний вид завершальної механічної обробки як найточніший з двох визначених за таблицями 7 та 8 для кожного виконавчого розміру.
За табл. 16, в залежності від допуску відповідного розміру виливки та допуску форми і розташування поверхонь виливки визначаємо для кожного розміру загальний допуск елементу виливки, який враховує допуск розміру виливки, а також допуск форми і розташування поверхні.
За табл. 6, в залежності від загального допуску елементу виливки, ряду припусків (4) і методу завершальної обробки для кожного розміру визначаємо загальний припуск на сторону. Причому згідно п. 4.2.1, [3], загальні припуски на сторону для поверхонь обертання та протилежних поверхонь, що використовуються взаємних баз при їх обробці, призначають по половинним значенням загального допуску.
Визначаємо середній розмір деталі (враховуючи граничні відхилення):
Визначаємо остаточні розміри виливки з урахуванням припусків на сторону, додаючи або віднімаючи (виходячи з креслення) його одинарну або подвійну (для діаметральних розмірів) його величину.
Допуски усіх розмірів на оброблювані поверхні обраний за стандартом допуск буде симетричним, тобто табличне значення допуску необхідно поділити навпіл і вказати зі знаком «±» .
Визначаємо формовочні уклони за [табл. 1, с. 3 ГОСТ 3212–92]:
За кресленням деталі невказані ливарні радіуси дорівнюють 3…5 мм.
За табл. 13, в залежності від вибраного способу лиття, номінальної маси виливки (10…100 кг) та типу сплаву (сірий чавун) визначимо клас точності маси виливок 6 — 13. Для заданого типу виробництва оберемо клас точності маси виливок — 10.
За табл. 4, в залежності від номінальної маси виливки (10…40 кг) та класу точності маси виливок 10, визначаємо допуск маси виливки у відсотках від номінальної маси виливки — 12%.
2.3.2 Визначення припусків розрахунково-аналітичним методом Спираючись на попередні розрахунки та на робоче креслення деталі визначимо всі необхідні величини та зведемо їх у відповідні таблиці.
Поверхня 1 і 2 — площини: Г і протилежна їй (за кресленням) Так як ці поверхні протилежні та використовуються для взаємного базування, приймемо, що припуски для них матимуть рівне значення.
Таблиця 2.3.2.1.
Технологічні переходи обробки поверхні 1, 2 | Елементи припуску, мкм | zmin, мкм | ||||
RZ | T | с | е | |||
Заготовка | ; | ; | ||||
1 — чорнове фрезерування | ||||||
2 — чистове фрезерування | ; | |||||
За [табл. 27, с. 65, 6] в залежності від способу лиття, класу точності виливки визначимо величини RZ та T для заготовки, результати занесемо в табл. 2.3.2.1.
RZ — висота мікронерівностей поверхні;
Tглибина дефектного поверхневого шару;
За [табл. 29, с. 67, 6] в залежності від виду обробки визначимо величини RZ та T для всіх переходів обробки поверхні 1, 2 (чорнове і чистове фрезерування).
За [табл. 31, с. 68, 6] в залежності від типу деталі та способу базування (за протилежною площиною) визначимо розрахункову формулу для сумарного значення просторових відхилень:
тут — жолоблення,
L = 318 мм — найбільша довжина в напрямку обробки (довжина оброблюваної поверхні);
мкм — питома кривизна заготовок в мкм на 1 мм довжини (визначаємо за [табл. 8, с. 183, Т1, 13] або за [табл. 32, с. 72, 6] в залежності від виду деталі та способу отримання заготовки).
тоді сумарне значення просторових відхилень:
(мкм) За рекомендаціями [с.74, 6] визначимо коефіцієнт уточнення форми після чорнового фрезерування — 0,05.
Визначимо залишкові просторові відхилення після чорнової обробки:
(мкм) Похибка встановлення заготовки при обробці плоских поверхонь, паралельних установочній базі, визначається за формулою:
При такій схемі базування (на протилежну площину) похибка базування:
Похибку закріплення визначимо за [табл. 40, с. 82, 6] в залежності від характеристики базової поверхні, поперечних розмірів заготовки та типу затискного пристосування:
240 мкм Отже, похибка встановлення заготовки:
=240 мкм Похибка встановлення заготовки після чорнового розточування:
(мкм) При послідовній обробці протилежних або окремо розташованих площин величина мінімального припуску на обробку визначається за формулою згідно [табл.26, с. 65, 6]:
Припуск на чорнову обробку:
(мкм) Припуск на чистову обробку:
(мкм) Згідно з рекомендаціями [прим.3, табл. 25, с. 64, 6] доцільно з міркувань режимних умов обробки припуск, розрахований на чорнову обробку, розподілити між чорновою та напівчистовою обробкою: 60…70% припуску зняти на чорновій обробці, 30…40% - на чистовій.
Отже, припуск на чорнову обробку приймемо = 755 мкм, на напівчистову = 503 мкм.
З урахуванням цього таблиця розрахункових розмірів матиме вигляд (табл.2.3.2.2.):
Таблиця 2.3.2.2.
Технологічні переходи обробки поверхні 1,2 | zmin, мкм | bр, мм | д, мм | bmin, мм | bmax, мм | zпрmin, мм | zпрmax, мм | |
Заготовка | ; | 131,261 | 2,4 | 131,26 | 133,66 | ; | ; | |
1- чорнове фрезерування | 130,506 | 1,0 | 130,51 | 131,51 | 0,75 | 2,15 | ||
2- напівчистове фрезерування | 130,003 | 0,63 | 130,0 | 130,63 | 0,51 | 0,88 | ||
3- чистове фрезерування | 129,875 | 0,25 — на обробку (за кресл. = 1,0) | 129,88 | 130,13 | 0,12 | 0,5 | ||
1,38 | 3,53 | |||||||
Визначимо розрахункові розміри, починаючи з кінцевого розміру (за кресленням), шляхом послідовного додавання розрахункового мінімального припуску кожного технологічного переходу:
(мм)
(мм)
(мм)
(мм) За [табл.7, с. 30, 6], кресленням деталі і СТ СЭВ 145−88 визначимо відповідно допуск розміру виливки, готової деталі та допуск для відповідної стадії обробки в залежності від точності отримуваних розмірів (враховуючий параметр шорсткості на певній стадії, спираючись на [табл. 20, с. 827, 7]), дані занесемо в таблицю.
Розрахуємо значення максимальні значення оброблюваного розміру, отримані результати в таблицю:
(мм)
(мм)
(мм)
(мм) Розрахуємо максимальну і мінімальну величину припусків, результати зведемо в таблицю:
Загальні припуски визначаємо, сумуючи проміжні припуски по переходам, і їх значення записуємо внизу відповідних граф таблиці:
(мм)
(мм) Загальний номінальний припуск:
(мм)
— відповідно верхні відхилення заготовки та деталі
Номінальний розмір заготовки:
(мм) Перевірка правильності розрахунків:
Можна судити про правильність виконання розрахунків.
Поверхня 3 — отвір ш95Н7
Таблиця 2.3.2.3.
Технологічні переходи обробки поверхні 3 | Елементи припуску, мкм | 2zmin, мкм | dр, мм | ||||
RZ | T | с | е | ||||
Заготовка | ; | ; | 89,215 | ||||
1- чорнове розточування | 92,415 | 94,62 | |||||
2- чистове розточування | ; | 94,635 | 95,02 | ||||
За [табл. 27, с. 65, 6] в залежності від способу лиття, класу точності виливки визначимо величини RZ та T для заготовки, результати занесемо в табл. 2.3.2.3.
RZ — висота мікро нерівностей поверхні;
Tглибина дефектного поверхневого шару;
За [табл. 30, с. 67, 6] в залежності від виду обробки визначимо величини RZ та T для всіх переходів обробки поверхні 3 (чорнове, чистове розточування).
Сумарне значення просторових відхилень для заготовки даного типу при обробці отвору 3 визначається:
Визначимо жолоблення:
(мкм) — жолоблення,
L = 45ммдовжина оброблюваного отвору;
мкм — питома кривизна заготовок в мкм на 1 мм довжини (визначаємо за [табл. 32, с. 72, 6] в залежності від виду деталі та способу отримання заготовки).
d = 95 мм — діаметр оброблюваного отвору.
Сумарне зміщення отвору у виливці відносно зовнішньої її поверхні являє геометричну суму в двох взаємно перпендикулярних площинах [рис.15, с. 86, 6]:
(мкм) де — допуски на розміри (Б) і (Г) за класом точності, що відповідає даній виливці (2 клас) — визначаємо за [табл. 7, с. 30, 6].
Отже, сумарне значення просторових відхилень складе:
(мкм) За рекомендаціями [с.74, 6] визначимо коефіцієнт уточнення форми після чорнового розточування — 0,05.
Визначимо залишкові просторові відхилення після чорнової обробки:
(мкм) Похибка встановлення заготовки визначається за формулою:
При такій схемі базування (у призмі) похибка базування :
(мкм)
= 2000 мкм — допуск на розмір (Д) за класом точності, що відповідає даній виливці (2 клас) — визначаємо за [табл. 7, с. 30, 6]; 90є - кут призми.
Похибку закріплення визначимо за [табл. 40, с. 82, 6] в залежності від характеристики базової поверхні (отримана литтям), поперечних розмірів заготовки та типу затискного пристосування:
180 мкм Отже, похибка встановлення заготовки при чорновому розточуванні:
(мкм) Похибка встановлення заготовки після чорнового розточування:
(мкм)
При обробці зовнішніх поверхонь обертання величина мінімального припуску на обробку визначається за формулою згідно [табл.26, с. 65, 6]:
Припуск на чорнову обробку:
(мкм) Припуск на чистову обробку:
(мкм) Згідно з рекомендаціями [прим.3, табл. 25, с. 64, 6] доцільно з міркувань режимних умов обробки припуск, розрахований на чорнову обробку, розподілити між чорновою та напівчистовою обробкою: 60…70% припуску зняти на чорновій обробці, 30…40% - на чистовій.
Отже, припуск на чорнову обробку приймемо? 3,2 мм, на напівчистову? 2,22 мм.
З урахуванням цього таблиця розрахункових розмірів матиме вигляд:
Таблиця 2.3.2.4.
Технологічні переходи обробки поверхні 3 | 2zmin, мкм | dр, мм | д, мм | dmin, мм | dmax, мм | 2zпрmin, мм | 2zпрmax, мм | |
Заготовка | ; | 89,215 | 2,2 | 87,02 | 89,22 | ; | ; | |
1- чорнове розточування | 92,415 | 0,350 | 92,07 | 92,42 | 3,2 | 5,05 | ||
2- напівчистове розточування | 94,635 | 0,200 | 94,44 | 94,64 | 2,22 | 2,37 | ||
3- чистове розточування | 95,035 | 0,035 | 94,97 | 95,04 | 0,4 | 0,56 | ||
5,82 | 7,98 | |||||||
Визначимо розрахункові розміри, починаючи з кінцевого розміру (за кресленням), шляхом послідовного віднімання (оскільки поверхня внутрішня) розрахункового мінімального припуску кожного технологічного переходу:
(мм)
(мм)
(мм)
(мм) За [табл.7, с. 30, 6], кресленням деталі і ГОСТ 25 347–82 визначимо відповідно допуск розміру виливки, готової деталі та допуск для відповідної стадії обробки в залежності від точності отримуваних розмірів, дані занесемо в табл. 2.3.2.4.
Розрахуємо значення мінімальних діаметральних розмірів і зведемо отримані результати в табл. 2.3.2.4.
(мм)
(мм)
(мм)
(мм) Розрахуємо максимальну і мінімальну величину припусків, результати зведемо в таблицю:
Загальні припуски визначаємо, сумуючи проміжні припуски по переходам, і їх значення записуємо внизу відповідних граф таблиці:
(мм)
(мм) Загальний номінальний припуск:
(мм)
— відповідно верхні відхилення заготовки та деталі
Номінальний діаметр заготовки:
(мм) Перевірка правильності розрахунків:
Можна судити про правильність виконання розрахунків Поверхня 4 — отвір ш85Н7
Розрахунки проведемо аналогічно поверхні 3, результати зведемо в табл. 2.3.2.5.
Таблиця 2.3.2.5
Технологічні переходи обробки поверхні 4 | 2zmin, мкм | dр, мм | д, мм | dmin, мм | dmax, мм | 2zпрmin, мм | 2zпрmax, мм | |
Заготовка | ; | 79,215 | 2,2 | 77,02 | 79,22 | ; | ; | |
1- чорнове розточування | 82,415 | 0,350 | 82,07 | 82,42 | 3,2 | 5,05 | ||
2- напівчистове розточування | 84,635 | 0,200 | 84,44 | 84,64 | 2,22 | 2,37 | ||
3- чистове розточування | 85,035 | 0,035 | 84,97 | 85,04 | 0,4 | 0,56 | ||
5,82 | 7,98 | |||||||
Загальний номінальний припуск:
(мм)
— відповідно верхні відхилення заготовки та деталі
Номінальний діаметр заготовки:
(мм) Перевірка правильності розрахунків:
Можна судити про правильність виконання розрахунків.
2.4 Розробка технологічного процесу Всі заповнені відповідні технологічні карти приведені в додатку до курсового проекту.
2.5 Вибір металорізального обладнання Вихідними даними для вибору металорізального устаткування є:
— метод обробки відповідних поверхонь або їх поєднання;
— точність та шорсткість поверхонь;
— припуски на обробку;
— обсяг і тип виробництва.
На основі цих даних вибираємо верстати для технологічного процесу, що проектується, згідно з рекомендаціями [с. 50, 6], їх характеристики наведемо нижче в табл. 2.5.1.
Таблиця 2.5.1. Технічні характеристики металорізального обладнання
№ опер. | Назва операції | Обладнання | Характеристики верстату | ||
010, | фрезерна | вертикально-фрезерний верстат 6Н13П | — робоча поверхня столу, мм: | 400 Ч 1600 | |
— число швидкостей шпинделя: | |||||
— межі частот обертання шпинделя, об/хв; | 30 — 1500 | ||||
— число подач столу: | |||||
— межі подач столу, мм/хв: | 7,8 — 1180 | ||||
— потужність приводу головного руху, кВт | |||||
— габарити, мм: | 2475Ч2170Ч2250 | ||||
— маса, кг: | |||||
15, | фрезерно; розточна | вертикально-фрезерний верстат з ЧПК 6Р13Ф3 | — робоча поверхня столу, мм: | 400 Ч 1600 | |
— число швидкостей шпинделя: | |||||
— межі частот обертання шпинделя, об/хв; | 40 — 2000 | ||||
— регулювання подач: | безступінчасте | ||||
— межі подач столу, мм/хв: | 3 — 4800 | ||||
— швидкість прискореного руху роб. органів, мм/хв: | |||||
— потужність приводу головного руху, кВт | 7,5 | ||||
— габарити, мм: | 2595Ч3200Ч2965 | ||||
— маса, кг: | |||||
30, | свердлувальна | вертикально-свердлильний верстат з ЧПК 2Р135Ф2 | — робоча поверхня столу, мм: | 400 Ч 710 | |
— найбільший діаметр обробки, мм | |||||
— число швидкостей шпинделя: | |||||
— межі частот обертання шпинделя, об/хв; | 31,5 — 1400 | ||||
— межі подач, мм/хв: | 10 — 500 | ||||
— число подач: | |||||
— швидкість прискореного ходу столу, мм/хв: | |||||
— потужність приводу головного руху, кВт | |||||
— габарити, мм: | 2500Ч1800Ч2700 | ||||
— маса, кг: | |||||
свердлувальна | радіально-свердлильний верстат 2Н55 | — найбільший діаметр обробки, мм | |||
— число швидкостей шпинделя: | |||||
— межі частот обертання шпинделя, об/хв; | 20 — 2000 | ||||
— межі подач, мм/об: | 0,056 — 2,5 | ||||
— число подач: | |||||
— потужність приводу головного руху, кВт | 4,5 | ||||
— габарити, мм: | 2625Ч968Ч3265 | ||||
— маса, кг: | |||||
2.6 Розрахунок режимів різання
Операція 010: чорнове фрезерування поверхні шириною 220 мм та довжиною 318 мм
Вихідні дані:
матеріал: СЧ20, HB 230, МПа;
шорсткість поверхні після обробки: Rz = 40 мкм;
обробка без охолодження згідно [табл. 39, с. 288, 13]
верстат: 6Н13П;
потужність двигуна головного руху — 10 кВт;
діапазон частоти обертання шпинделя — 31,5…1500 об/хв;
регулювання — ступінчасте.
інструмент: [табл. 94, с. 187, 13]
фреза торцева ш 250, матеріал твердосплавних пластин — ВК6, кількість зубів z =24, ширина B = 47 мм (ГОСТ 9473−80), головний кут в плані ц = 60є.
Глибина різання:
Призначаємо глибину різання рівною припуску на обробку (згідно розрахованих раніше значень):
t = 1,8 мм Подача:
Приймаємо подачу на зуб фрези sz в межах 0,14…0,24 мм/зуб за [табл. 33, с. 283, 13] в залежності від потужності верстата (5−10 кВт), оброблюваного та оброблюючого матеріалів.
Враховуючи примітку до [табл. 33, с. 283, 13], оскільки ширина фрезерування більша 30 мм, зменшуємо табличне значення подачі на 30%:
sz = 0,098…0,168 мм/зуб
Приймемо подачу sz? 0,1 мм/зуб Подача на оберт складе:
(мм/об) Швидкість різання (колова швидкість фрези):
В цій формулі:
D = 250 мм — діаметр фрези;
B = 47 мм — ширина фрези
z = 24 — кількість зубів інструменту Значення коефіцієнта СV та показників степеню в цій формулі визначаємо за [табл. 39, с. 288, 13] в залежності від типу фрези, виду операції, матеріалу ріжучої частини:
СV = 445, q = 0,2, x = 0,15, y = 0,35, u = 0,2, p = 0, m = 0,32
Т = 240 хв — період стійкості фрези за [табл. 40, с. 290, 13].
Загальний поправочний коефіцієнт на швидкість різання:
В цій формулі:
За [табл. 1, с. 261, 13] поправочний коефіцієнт, що враховує вплив фізико-механічних властивостей оброблюваного матеріалу на швидкість різання для сірого чавуну:
де — показник степені, що визначається за [табл. 2, с. 262, 13]
Поправочний коефіцієнт, що враховує вплив стану поверхні заготовки на швидкість різання за [табл. 5, с. 263, 13]: ;
Поправочний коефіцієнт, що враховує вплив інструментального матеріалу на швидкість різання за [табл. 6, с. 263, 13]:
Отже, розрахункова швидкість різання:
(м/хв)
Розрахункова частота обертання ріжучого інструменту:
(об/хв) Розрахункова хвилинна подача:
(мм/хв) Узгодимо за паспортними даними верстата отримані результати і остаточно приймемо:
Фактична частота обертання:
(об/хв) Фактична хвилинна подача:
(мм/хв) Уточнимо значення швидкості та подачі на зуб:
(м/хв)
(мм/зуб) Сила різання:
Головна складова сили різання (при фрезеруванні - колова сила):
Значення коефіцієнта Ср та показників степеню в цій формулі визначаємо за [табл. 41, с. 291, 13] в залежності від типу фрези, оброблюваного і оброблюючого матеріалів:
Ср = 54,5, q = 1,0, x = 0,9, y = 0,74, u = 1,0, w= 0.
Поправочний коефіцієнт на якість оброблюваного матеріалу знаходимо в [табл. 9, с. 264, 13]:
Отже, колова сила:
(Н)
Величини решти складових сили різання визначаємо із їх співвідношення з головною складовою — коловою силою за [табл. 42, с. 292, 13]:
Горизонтальна сила (сила подачі):
(Н)
Вертикальна сила:
(Н)
Радіальна сила:
(Н)
Осьова сила:
(Н) Крутний момент на шпинделі:
(Н•м) Ефективна потужність різання:
(кВт)
Основний технологічний час підраховується за формулою згідно [п. ІІ, с. 190, 9]:
(хв), тут
L — довжина шляху, що проходить інструмент в напрямку подачі;
l — довжина оброблюваної поверхні (за кресленням) = 318 мм;
l1— величина на врізання і перебіг інструменту, що визначається за [дод. 4, арк. 6, с. 378, 9] в залежності від типу фрези (торцьова), схеми її установки (симетрична) й ширини фрезерування (за кресленням = 220 мм);
sхв— хвилинна подача фрези, визначена раніше;
ічисло проходів.
Операція 015: Фрезерно-розточувальна (чорнова)
Вихідні дані:
матеріал: СЧ20, HB 230, МПа;
шорсткість поверхні після обробки: Rz = 40 мкм;
обробка без охолодження згідно [табл. 39, с. 288, 13]
верстат: 6Р13Ф3;
потужність двигуна головного руху — 7,5 кВт;
діапазон частоти обертання шпинделя — 40…2000 об/хв;
діапазон подач за координатами X, Y, Z — 3…4800 мм/хв;
число ступеней регулювання частоти обертання — 18
ФРЕЗРУВАННЯ Розрахунок режимів різання проводимо аналогічно операції 010.
інструмент: [табл. 94, с. 187, 13]
фреза торцева ш 160, матеріал твердосплавних пластин — ВК6, кількість зубів z =16, ширина B = 46 мм (ГОСТ 9473−80)
Глибина різання:
Рівна припуску на обробку: t = 1,8 мм Подача:
За [табл. 33, с. 283, 13] з урахуванням поправки на ширину фрезерування:
sz? 0,1 мм/зуб Подача на оберт складе:
(мм/об) Швидкість різання:
де
D = 160 мм — діаметр фрези;
B = 46 мм — ширина фрези
z = 16 — кількість зубів інструменту Значення коефіцієнта СV та показників степеню в цій формулі визначаємо за [табл. 39, с. 288, 13]:
СV = 445, q = 0,2, x = 0,15, y = 0,35, u = 0,2, p = 0, m = 0,32
Т = 190 хв — період стійкості фрези за [табл. 40, с. 290, 13].
Загальний поправочний коефіцієнт на швидкість різання:
В цій формулі:
За [табл. 1, с. 261, 13]: ,
За[табл. 5, с. 263, 13]: ;
З [табл. 6, с. 263, 13]: .
Отже, розрахункова швидкість різання:
(м/хв) Розрахункова частота обертання ріжучого інструменту:
(об/хв) Хвилинна подача:
(мм/хв) Узгодимо за паспортними даними верстата і остаточно приймемо фактичну частоту обертання:
(об/хв) Тоді фактична хвилинна подача:
(мм/хв) Уточнимо значення швидкості різання:
(м/хв)
Сила різання:
Головна складова сили різання:
Значення коефіцієнта Ср та показників степеню в цій формулі визначаємо за [табл. 41, с. 291, 13]:
Ср = 54,5, q = 1,0, x = 0,9, y = 0,74, u = 1,0, w= 0.
Поправочний коефіцієнт на якість оброблюваного матеріалу знаходимо в [табл. 9, с. 264, 13]:
Отже, колова сила:
(Н) За [табл. 42, с. 292, 13]:
Горизонтальна сила (сила подачі):
(Н)
Вертикальна сила:
(Н)
Радіальна сила:
(Н)
Осьова сила:
(Н) Крутний момент на шпинделі:
(Н•м) Ефективна потужність різання:
(кВт) Основний технологічний час згідно [п. ІІ, с. 190, 9] та [п. 2.2.6., с. 104, 4]:
(хв) РОЗТОЧУВАННЯ Вибір глибини різання:
Враховуючи раніше визначені припуски на обробку та рекомендації [карти 2.2., с. 174, 4] визначаємо глибину різання для поверхонь 1 та 2:
— чистове розточування t3 = 0,4 мм
— напівчистове розточування t2 = 1,1 мм
— для чорнового розточування t1 = (6,2/2 -1,1 — 0,4) = 1,6 мм Різальний інструмент:
Для обробки поверхонь 1 і 2 вибираємо розточувальні різці з пластинами з твердого сплаву за ГОСТ 9795–84 типу 4, виконання 1 (керуючись заводським техпроцесом), позначення різця — 2142−0444 (лівий, з кутом врізання 10є).
Геометричні параметри різця:
— переріз різця: hЧb = 16Ч16 мм;
— довжина різця L = 63 мм;
— довжина пластина l = 12 мм;
— тип пластин за ГОСТ 25 396–82: 07;
— головний кут в плані: ц = 60є,
— допоміжний: ц1 = 35є.
Вибір матеріалу твердосплавних пластин проводимо відповідно до рекомендацій додатку [Д. 2.1., с. 444, 4].
Для чорнової обробки деталі (СЧ20) приймається твердий сплав ВК6, Решту геометричних параметрів різця вибираємо за [Д. 2.7., с. 450, 4] :
Для чорнової обробки:
— б = 6є - задній кут;
— г = 8є - передній кут;
— f = 0,4 мм — ширина фаски різальної кромки;
— с = 0,02 мм — радіус округлення різальної кромки;
— rв = 0,8 мм — радіус вершини різця.
Нормативний період стійкості за [Д. 2.10., с. 459, 4]: Т = 30 хв.
Вибір подач Для чорнового розточування за [табл. 12, с. 267, 13] при заданому перерізі різця та глибині різання рекомендується подача S = 0,2…0,3 мм/об.
Приймаємо подачу S = 0,22 мм/об.
Швидкості різання Визначатимемо їх за формулами теорії різання, згідно [п. 3, с. 265, 13]:
Значення коефіцієнтів в цій формулі знаходимо за [табл. 17, с. 266, 13]:
Швидкісний коефіцієнт:
В цій формулі:
За [табл. 1, с. 261, 13]: ,
За [табл. 5, с. 263, 13]: ;
За [табл. 6, с. 263, 13]: ;
Отже, загальний швидкісний коефіцієнт:
;
При внутрішній обробці (розточуванні) згідно рекомендацій за [табл. 17, с. 270, 13] на швидкість різання додатково водиться поправочний коефіцієнт 0,9:
Таким чином швидкість різання:
(м/хв);
Розрахункова частота обертання шпинделя визначається за наступною формулою:, розраховане значення уточнюємо за паспортом верстата:
Поверхня 1 (ш95 Н7): (об/хв); об/хв;
Поверхня 2 (ш85 Н7): (об/хв); об/хв;
Уточнюємо значення швидкості різання:
Поверхня 1 (ш95 Н7): (м/хв)
Поверхня 2 (ш85 Н7): (м/хв) Сила різання:
Величини тангенційної PZ, радіальної PY і осьової PX складових сили різання при розточуванні визначаються за формулою:
За [табл. 22, с. 274, 13] знаходимо коефіцієнти для визначення складових сили різання:
;
;
.
Поправочний коефіцієнт на силу різання являє собою добуток наступних коефіцієнтів:
За [табл.9, с. 264 і табл.23, с. 275, 13] визначаються поправочні коефіцієнти для складових сили різання в залежності від:
— механічних властивостей матеріалу, що оброблюється ;
;
Поправочні коефіцієнти що враховують вплив геометричних параметрів:
— головного кута в плані - КРцХ = 1,11; КРцУ =0,77; КРцZ = 0,94;
— переднього кута — КРгХ = КРгУ = КРгZ =1,0;
— кута нахилу різальної кромки — КРлХ = 0,8; КРлУ = 1,3; КРлZ = 1,0;
Тоді:
;
;
.
Складові сили різання:
(Н);
(Н);
(Н);
Потужність різання розраховують за формулою:
Поверхня 1 (ш95 Н7): (кВт);
Поверхня 2 (ш85 Н7): (кВт);
Визначення основного часу:
Основний технологічний час на перехід, підраховується за формулою згідно [р. ІІ, с. 55, 92]:
Поверхня 1 (ш95 Н7): (хв);
Поверхня 2 (ш85 Н7): (хв);
Сумарний основний час на операції:
(хв)
Операція 020: напівчистове і чистове фрезерування поверхні шириною 220 мм та довжиною 318 мм
Вихідні дані:
матеріал: СЧ20, HB 230, МПа;
шорсткість поверхні після обробки: Rа = 2,5 мкм;
обробка без охолодження згідно [табл. 39, с. 288, 13]
верстат: 6Н13П;
потужність двигуна головного руху — 10 кВт;
діапазон частоти обертання шпинделя — 31,5…1500 об/хв;
регулюванняступінчасте.
інструмент: [табл. 94, с. 187, 13]
— фреза торцева ш 250, матеріал твердосплавних пластин — ВК6, кількість зубів z =24, ширина B = 47 мм (ГОСТ 9473−80); - напівчистове обробка
— фреза торцева ш 250, матеріал твердосплавних пластин — ВК3М, кількість зубів z = 24, ширина B = 47 мм (ГОСТ 9473−80); - чистова обробка Глибина різання:
Призначаємо глибину різання рівною припуску на обробку:
t = 0,8 мм — для напівчистової;
t = 0,4 мм — для чистової;
Подача:
Для напівчистової обробки приймаємо подачу на зуб фрези sz за [табл. 33, с. 283, 13] з урахуванням поправки на ширину фрезерування:
sz? 0,07 мм/зуб;
Подача на оберт складе: (мм/об)
Для чистової обробки приймаємо подачу на оберт s за [табл. 37, с. 285, 13]:
s = 0,6 мм/об Подача на зуб складе:
(мм/зуб) Швидкість різання:
Значення коефіцієнта СV та показників степеню в цій формулі визначаємо за [табл. 39, с. 286, 13:
СV = 445, q = 0,2, x = 0,15, y = 0,35, u = 0,2, p = 0, m = 0,32
Т = 240 хв — період стійкості фрези за [табл. 40, с. 290, 13].
Загальний поправочний коефіцієнт на швидкість різання:
де За [табл. 1, с. 261, 13]: ,
За [табл. 5, с. 263, 13]: ;
За [табл. 6, с. 263, 13]: .
Отже, розрахункова швидкість різання:
(м/хв)
— при напівчистовому фрезеруванні;
(м/хв)
— при чистовому фрезеруванні;
Розрахункова частота обертання ріжучого інструменту:
(об/хв) — при напівчистовому фрезеруванні;
(об/хв) — при чистовому фрезеруванні;
Розрахункова хвилинна подача:
(мм/хв) — при напівчистовій обробці;
(мм/хв) — при чистовій обробці;
Узгодимо за паспортними даними верстата, приймемо фактичну частоту обертання і хвилинну подачу:
(об/хв); (мм/хв) — при напівчистовій обробці;
(об/хв); (мм/хв) — при чистовій обробці;
Уточнимо значення швидкості та подачі на зуб:
(м/хв) — при напівчистовій обробці;
(м/хв) — при чистовій обробці;
(мм/зуб) — при напівчистовій обробці;
(мм/зуб) — при чистовій обробці;
Сила різання:
Головна складова сили різання:
Значення коефіцієнта Ср та показників степеню в цій формулі визначаємо за [табл. 41, с. 291, 13]:
Ср = 54,5, q = 1,0, x = 0,9, y = 0,74, u = 1,0, w= 0.
За [табл. 9, с. 264, 13]:
Отже, колова сила:
(Н) — при напівчистовій обробці;
(Н) — при чистовій обробці;
За [табл. 42, с. 292, 13]:
Горизонтальна сила (сила подачі):
(Н) — при напівчистовій обробці;
(Н) — при чистовій обробці;
Вертикальна сила:
(Н) — при напівчистовій обробці;
(Н) — при чистовій обробці;
Радіальна сила:
(Н) — при напівчистовій обробці;
(Н) — при чистовій обробці;
Осьова сила:
(Н) — при напівчистовій обробці;
(Н) — при чистовій обробці;
Крутний момент на шпинделі:
(Н•м) — при напівчистовій обробці;
(Н•м) — при чистовій обробці;
Ефективна потужність різання:
(кВт) — при напівчистовій обробці;
(кВт) — при чистовій обробці;
Основний технологічний час згідно [п. ІІ, с. 190, 9]:
(хв) — для напівчистової обробки;
(хв) — для чистової обробки;
Сумарний основний час на операції:
(хв)
Операція 025: Фрезерно-розточувальна (чистова і напівчистова)
Вихідні дані:
матеріал: СЧ20, HB 230, МПа;
обробка без охолодження згідно [табл. 39, с. 288, 13]
верстат: 6Р13Ф3;
потужність двигуна головного руху — 7,5 кВт;
діапазон частоти обертання шпинделя — 40…2000 об/хв;
діапазон подач за координатами X, Y, Z — 3…4800 мм/хв;
число ступеней регулювання частоти обертання — 18
Розрахунок режимів різання проводимо аналогічно операції 015.
ФРЕЗЕРУВАННЯ
Інструмент: [табл. 94, с. 187, 13]
— фреза торцева ш 160, матеріал твердосплавних пластин — ВК3М, кількість зубів z =16, ширина B = 46 мм (ГОСТ 9473−80); - для чистової обробки;
— фреза торцева ш 160, матеріал твердосплавних пластин — ВК6, кількість зубів z =16, ширина B = 46 мм (ГОСТ 9473−80); - для напівчистової обробки;
Глибина різання:
Призначаємо глибину різання рівною припуску на обробку:
t = 0,4 мм — для чистової обробки;
t = 0,8 мм — для напівчистової обробки.
Подача:
Для напівчистової обробки приймаємо подачу на зуб фрези sz за [табл. 33, с. 283, 13], враховуючи поправку на ширину фрезерування:
sz? 0,07 мм/зуб Подача на оберт складе:
(мм/об)
Для чистового фрезерування приймаємо подачу на оберт фрези s за [табл. 37, с. 285, 13]:
s = 0,6 мм/об Тоді подача на зуб:
(мм/об) Швидкість різання:
Значення коефіцієнта СV та показників степеню в цій формулі визначаємо за [табл. 39, с. 286, 13]:
СV = 445, q = 0,2, x = 0,15, y = 0,35, u = 0,2, p = 0, m = 0,32
Т = 190 хв — період стійкості фрези за [табл. 40, с. 290, 13].
Загальний поправочний коефіцієнт на швидкість різання:
Отже, розрахункова швидкість різання:
(м/хв) — при напівчистовій обробці;
(м/хв) — - при чистовій обробці;
Розрахункова частота обертання ріжучого інструменту:
(об/хв) — при напівчистовій обробці;
(об/хв) — при чистовій обробці;
Узгодимо за паспортними даними верстата і остаточно приймемо фактичну частоту обертання:
(об/хв) — при напівчистовій обробці;
(об/хв) — при чистовій обробці;
Фактична хвилинна подача:
(мм/хв) — при напівчистовій обробці;
(мм/хв) — при чистовій обробці;
Уточнимо значення швидкості різання:
(м/хв) — при напівчистовій обробці;
(м/хв) — при чистовій обробці;
Сила різання: Головна складова (при фрезеруванні - колова сила):
Значення коефіцієнта Ср та показників степеню в цій формулі визначаємо за [табл. 41, с. 291, 13]:
Ср = 54,5, q = 1,0, x = 0,9, y = 0,74, u = 1,0, w= 0.
Поправочний коефіцієнт на якість оброблюваного матеріалу знаходимо в [табл. 9, с. 264, 13]:
Отже, колова сила:
(Н) — при напівчистовій обробці;
(Н) — при чистовій обробці;
Величини решти складових сили різання визначаємо за [табл. 42, с. 292, 13]:
Горизонтальна сила (сила подачі):
(Н) — при напівчистовій обробці;
(Н) — при чистовій обробці;
Вертикальна сила:
(Н) — при напівчистовій обробці;
(Н) — при чистовій обробці;
Радіальна сила:
(Н) — при напівчистовій обробці;
(Н) — при чистовій обробці;
Осьова сила:
(Н) — при напівчистовій обробці;
(Н) — при чистовій обробці;
Крутний момент на шпинделі:
(Н•м) — при напівчистовій обробці;
(Н•м) — при чистовій обробці;
Ефективна потужність різання:
(кВт) — при напівчистовій обробці;
(кВт) — при чистовій обробці;
Основний технологічний час на перехід згідно [п. ІІ, с. 190, 9] та [п. 2.2.6., с. 104, 4]:
де
(хв) — при напівчистовій обробці
(хв) — при чистовій обробці
РОЗТОЧУВАННЯ Глибина різання:
Враховуючи раніше визначені припуски на обробку та рекомендації [карти 2.2., с. 174, 4] визначаємо глибину різання для поверхонь 1 та 2 складе:
— чистове розточування t3 = 0,4 мм
— напівчистове розточування t2 = 1,1 мм
Інструмент:
Для обробки поверхонь 1 і 2 вибираємо розточувальні різці з пластинами з твердого сплаву за ГОСТ 9795–84 типу 4, виконання 1, позначення різця — 2142−0444 (лівий, з кутом врізання 10є).
Геометричні параметри різця:
— переріз різця: hЧb = 16Ч16 мм;
— довжина різця L = 63 мм;
— довжина пластина l = 12 мм;
— тип пластин за ГОСТ 25 396–82: 07;
— головний кут в плані: ц = 60є,
— допоміжний: ц1 = 35є.
Вибір матеріалу твердосплавних пластин проводимо відповідно до рекомендацій додатку [Д. 2.1., с. 444, 4].
Для чорнової та напівчистової обробки деталі (СЧ20) приймається твердий сплав ВК6, Решту геометричних параметрів різця вибираємо за [Д. 2.7., с. 450, 4] :
Для напівчистової обробки:
— б = 6є - задній кут;
— г = 8є - передній кут;
— f = 0,4 мм — ширина фаски різальної кромки;
— с = 0,02 мм — радіус округлення різальної кромки;
— rв = 0,8 мм — радіус вершини різця.
Для чистової обробки (форма передньої поверхні - без фаски):
— б = 8є - задній кут;
— г = 12є - передній кут;
— с = 0,02 мм — радіус округлення різальної кромки;
— rв = 0,6 мм — радіус вершини різця.
Нормативний період стійкості за [Д. 2.10., с. 459, 4] - Т = 30 хв.
Вибір подач:
Для напівчистової обробки: за [табл. 12, с. 267, 13]: S = 0,18 мм/об.
Для чистового розточування отворів за [табл. 19, с. 271, 4]: s = 0,05 мм/об Швидкості різання:
Визначатимемо їх за формулами теорії різання, згідно [п. 3, с. 265, 13]:
Значення коефіцієнтів в цій формулі знаходимо за [табл. 17, с. 266, 13]:
Швидкісний коефіцієнт: ,
— для чистової обробки: ;
— для напівчистової обробки: ;
При внутрішній обробці (розточуванні) згідно рекомендацій за [табл. 17, с. 270, 13] на швидкість різання додатково водиться поправочний коефіцієнт 0,9:
Таким чином, розрахункова швидкість різання:
— для напівчистового розточування:
(м/хв);
— для чистового розточування
(м/хв);
Частота обертання шпинделя визначається за наступною формулою:, розраховані значення уточнюємо за паспортом верстата:
Поверхня 1 (ш95 Н7):
— для напівчистової обробки: (об/хв); об/хв;
— для чистової обробки: (об/хв); об/хв;
Поверхня 2 (ш85 Н7):
— для напівчистової обробки: (об/хв); об/хв;
— для чистової обробки: (об/хв); об/хв;
Уточнимо швидкість різання:
:
Поверхня 1 (ш95 Н7):
для напівчистової обробки: (м/хв)
— для чистової обробки: (м/хв)
Поверхня 2 (ш85 Н7):
— для напівчистової обробки: (м/хв)
— для чистової обробки: (м/хв) Сила різання Величини тангенційної PZ, радіальної PY і осьової PX складових сили різання при розточуванні визначаються за формулою:
За [табл. 22, с. 274, 13] знаходимо коефіцієнти для визначення складових сили різання:
;
;
.
Поправочний коефіцієнт на силу різання являє собою добуток наступних коефіцієнтів:
За [табл.9, с. 264 і табл.23, с. 275, 13] визначаються поправочні коефіцієнти для складових сили різання в залежності від:
— механічних властивостей матеріалу, що оброблюється ;
;
Поправочні коефіцієнти що враховують вплив геометричних параметрів:
головного кута в плані - КРцХ = 1,11; КРцУ =0,77; КРцZ = 0,94;
— переднього кута — КРгХ = КРгУ = КРгZ =1,0;
— кута нахилу різальної кромки — КРлХ = 0,8; КРлУ = 1,3; КРлZ = 1,0;
Тоді:
;
;
.
Складові сили різання:
— при напівчистовій обробці: (Н);
(Н);
(Н);
— при чистовій обробці: (Н);
(Н);
(Н);
Потужність різання: ,
Поверхня 1 (ш95 Н7):
— напівчистове розточування: (кВт);
— чистове розточування: (кВт);
Поверхня 2 (ш85 Н7):
— напівчистове розточування: (кВт);
— чистове розточування: (кВт);
Визначення основного часу:
Основний технологічний час на перехід за формулою згідно [р. ІІ, с. 55, 92]: