Сухе гасіння коксу
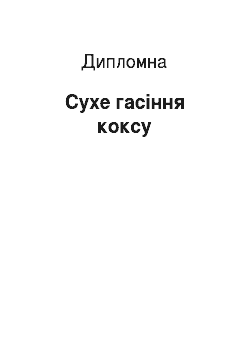
У гасильній башті є зрошувальний пристрій, куди вода подається або самопливом з напірного бака, або безпосередньо насосом. При першому методі капітальні витрати вище, складніше комунікації, вище витрата електроенергії, періодично потрібно очищати напірний бак. У зв’язку з цим зараз на більшості заводів освітлена вода із збірки подається в зрошувальну систему гасильної башти насосом, який… Читати ще >
Сухе гасіння коксу (реферат, курсова, диплом, контрольна)
ЗМІСТ Вступ
1. Аналітична частина
1.1 Вплив коксохімічного виробництва на навколишнє середовище
1.2 Аналіз існуючих технологій гасіння коксу
1.2.1 Технологія мокрого гасіння коксу
1.2.2 Технологічна схема, принцип роботи та коефіцієнт корисної дії
процесу сухого гасіння коксу
1.3 Вплив технології сухого гасіння коксу на навколишнє середовище
1.4 Розрахунок матеріального балансу коксування вугільної шихти
1.5 Висновки до аналітичної частини
2. Основна частина
2.1 Розрахунок кількості коксових камер і основного устаткування
2.2 Обґрунтування вибору сухого гасіння
2.3 Технологічна схема установки сухого гасіння коксу
2.4 Експлуатація та удосконалення роботи установки сухого гасіння коксу
2.5 Порівняльна характеристика якості коксу сухого та мокрого гасіння
Висновки
ВСТУП В Україні 80% коксу охолоджують мокрим гасінням. При цьому при виробництві кожної тони коксу утворюється 0,3−0,4 м3 хімічно забруднених стічних вод. Виключити утворення такого стоку неможливо, тому що вода надходить у технологічний процес із сировиною (з вугільною шихтою) і утворюється в процесі коксування. Після біохімічного очищення стічні води коксохімії не можуть бути скинуті безпосередньо у водойми. Очищені стоки направляють на контактне охолодження (гасіння) виданого з камер коксування коксу. Все його тепло витрачається на випарювання води в атмосферу. Утворюється потужний викид шкідливих речовин в атмосферу через залишковий вміст аміаку та інших речовин у воді, що надходить на гасіння.
В зв’язку з вище викладеним, дуже актуально розглянути основні технічні характеристики технологічної схеми сухого гасіння, основні екологічні характеристики, вплив на стан атмосферного повітря, а також розробити заходи вдосконалення устаткування сухого гасіння коксу.
При рішенні ряду наукових завдань можна використовувати наявні передумови для створення великомасштабного хімічного реактора для виробництва на базі тепла розжареного коксу газоподібних відновників для доменного процесу або синтез-газів для отримання моторних палив 1.
Одним з найперспективніших шляхів, що дозволяють вирішити ці завдання — це заміна традиційного мокрого гасіння коксу на прогресивний метод сухого гасіння коксу, заснований на високоефективному використанні величезних ресурсів вторинного тепла розжареного коксу, які при мокрому гасінні викидаються в атмосферу разом з парою і великими кількостями шкідливих речовин.
Цей шлях дає можливість не тільки використовувати фізичне тепло розжареного коксу для отримання пара енергетичних параметрів з подальшим його використанням як енергоносія, але і значно підвищити якість коксу, а також техніко-економічні показники доменного процесу і коксохімічних підприємств; особливе значення при цьому набуває можливості рішення екологічних проблем, що мають велику перспективу в справжньому майбутньому.
Рішення цих завдань засноване на фізико-хімічних процесах, лежачих в основі новітніх технологій 1.
Передбачається, що запропонована технологія сухого гасіння коксу згідно проекту Гипрококсу, дозволить виключити викиди шкідливих речовин в атмосферу та підвищити якість коксу.
1. АНАЛІТИЧНА ЧАСТИНА
1.1 Вплив коксохімічного виробництва на навколишнє середовище
Коксохімічне виробництво ПАТ «АрселорМіттал Кривий Ріг» відноситься до числа підприємств — забруднювачів природного середовища міста Кривий Ріг. У процесі виробничої діяльності КХВ можна виділити наявність наступних екологічних аспектів: викиди забруднюючих речовин в атмосферу від стаціонарних джерел забруднення; утворення стічних промислових стоків; вплив промислової діяльності на якість атмосферного повітря в робочій зоні; утворення промислових та побутових відходів.
Усі основні виробничі цехи коксохімічного виробництва вносять свій внесок у загальні валові викиди забруднюючих речовин в атмосферу. Найбільший об'єм викидів від стаціонарних джерел має коксовий цех № 1. Відповідно до ДСТУ ССБП 12.1.005−88 припустимий вміст вугільного пилу в повітрі не повинен перевищувати 4 мг/м3. Насправді ж запиленість у багато разів перевищує припустиму норму. Вона коливається від одиниць до тисяч міліграмів у кубічному метрі повітря.
Технологічний процес коксування супроводжується викидами шкідливих речовин з повітряників агрегатов і ємностей.
У вуглепідготовчому цеху (ВПЦ) при розвантаженні, складуванні, дробленні вугілля, при дозуванні компонентів вугільної шихти, а також із труб аспіраційних установок в атмосферу викидається вугільний пил. З димарів гаража розморожування вугілля виділяються продукти згоряння очищеного (зворотного) коксового газу: оксиди азоту, окис вуглецю, сірчистий ангідрід (табл. 1.2). Коксові цехи є основними забруднювачами повітряного басейну серед всіх цехів КХВ. Джерелами утворення викидів забруднюючих речовин в атмосферу є процеси завантаження шихти в коксові печі, видачі готового коксу з печей, гасіння коксу в гасильних баштах із застосуванням очищеної на біохімічній установці води, коксові рампи, коксосортувальня й опалювальна система коксових батарей. При завантаженні шихти в камери коксування в атмосферу надходять забруднюючи речовини (табл.1.1). Виділення забруднюючих речовин обумовлено витисненням газоповітряної суміші з камер коксування при завантаженні шихти, а також початком утворення й виділення летючих компонентів процесу коксування.
При видачі коксу виділення шкідливих речовин проходить зі стояків перед видачею коксу й під час приймання коксового пирога в гасильні вагони, а також під час проходження (руху) гасильних вагонів зі коксом під башти гасіння.
При мокрому гасінні коксу водою, що пройшла біохімічне очищення, відбувається втрата води в кількості 0,5−0,6 м3 на 1 т виробленого коксу.
На коксових рампах відбувається випарювання вологи після мокрого гасіння. При транспортуванні коксу, у місцях перепадів, а також при його сортуванні відбувається виділення коксового пилу, що забруднює атмосферне повітря.
Одним з основних джерел утворення забруднюючих речовин є опалювальні системи коксових батарей.
У цеху уловлення виконується очищення коксового газу з одержанням товарної продукції - бензолу сірого кам’яновугільного, смоли тяжкої уловлення, сульфату амонію. Основними джерелами викидів забруднюючих речовин в атмосферу є: градирня кінцевого охолодження коксового газу, люки та повітряники хімічної апаратури, відкриті ємкості та відстійники.
У цеху сіркоочистки виконується очищення коксового газу після цеху уловлення від сірководню з утворенням сірчаної кислоти. Через повітряники технологічного обладнання викидаються в атмосферу забруднюючи речовини.
КХВ у своїй виробничій діяльності не виконує забір води з природних водних об'єктів, має замкнутий цикл водоспоживання. Скиди усіх видів вод у природні водойми на КХВ відсутні.
Таблиця 1.1- Перелік забруднюючих речовин, які викидаються в атмосферне повітря стаціонарними джерелами викидів основних цехів КХВ «АМКР»
Найменування забруднюючої речовини | Найменування цеху | |||||
Вуглепідготовчий цех | Коксові цехи № 1, 2 | Цех улов-лювання | Цех сірко-очистки | ЦЕЗ | ||
Пил вугільний | х | |||||
Пил коксовий | х | |||||
Оксид вуглецю | х | х | х | х | ||
Оксиди азоту | х | х | х | х | ||
Діоксид сірки | х | х | х | х | х | |
Сажа | х | |||||
Аміак | х | х | х | |||
Фенол | х | х | х | |||
Водню ціанід | х | х | х | х | ||
Сірководень | х | х | х | х | ||
Бензол | х | х | ||||
Нафталін | х | х | х | |||
Толуол | х | |||||
Ксилол | х | |||||
Бенз (а)пірен | х | х | ||||
Сірчана кислота | х | х | ||||
Піридин | х | |||||
Промислові стоки в повному обсязі, через фенольну каналізацію, подаються на біохімічну установку, де очищуються від вмісту забруднюючих речовин. Після очищення на БХУ очищенні води подаються на мокре гасіння коксу, тобто КХВ має замкнутий цикл технологічного водопостачання.
Коксовий цех забруднює атмосферу викидами пилу, сірчистих з'єднань, окислу вуглецю, фенолу і іншими шкідливостями, що утворюються головним чином при завантаженні і видачі коксу, гасінні коксу, від систем аспірації коксосортування і перевантажувальних вузлів, а також від димарів (табл.1.2).
При завантаженні шихти без інжекції від однієї печі, за даними Гипрококсу, виділяється: пороши 1,25 кг при насипній шихті і 0,76 кг при трамбованій; оксид вуглецю 2,18 кг; смоли і масел 1,59 кг; бензолових вуглеводнів 0,57 кг.
Таблиця 1.2 — Викиди забруднюючих речовин в атмосферу коксового цеху
Викиди забруднюючих речовин в атмосферу | Устаткування, де утворюються забрудню-ючі речовини | Найменування забруднюючої речовини | Напрямок повторного використання, метод очищення | Метод очищення (утилізація, знешкодження) | Питомі викиди, г/т коксу | |
Завантаження шихти | Коксова батарея № 1 | Пил вугільний | Бездимне завантаження із застосуванням методу паро-інжекції | Без очищення | 5−15 | |
Азоту діоксид | 1,5−4 | |||||
Аміак | 1−2,5 | |||||
Сірки діоксид | 1,2−3 | |||||
Сірководень | 0,5−1 | |||||
Вуглецю оксид | 1−5 | |||||
Бензол | 1−2 | |||||
Фенол | 0,05−0,2 | |||||
Бенз (а)пірен | 0,0001 | |||||
Ціан. водень | 0,05−0,2 | |||||
Видача коксу | Коксова батарея № 1 | Пил коксовий | Відсутні | Без очищення | 200−350 | |
Азоту діоксид | 10−20 | |||||
Аміак | 1−3 | |||||
Сірки діоксид | 10−15 | |||||
Сірководень | 0,5−2 | |||||
Вуглецю оксид | 10−30 | |||||
Бензол | 2−5 | |||||
Нафталін | 0,3−1 | |||||
Фенол | 0,5−1,5 | |||||
Бенз (а)пірен | 0,0005−0,001 | |||||
Ціан. водень | 0,5−1,5 | |||||
Двері коксових печей | Коксова батарея № 1 | Пил коксовий | Відсутні | Без очищення | 0,1−0,5 | |
Аміак | 0,5−1 | |||||
Сірки діоксид | 1−1,5 | |||||
Сірководень | 0,5−1 | |||||
Вуглецю оксид | 3−5 | |||||
Бензол | 1−1,5 | |||||
Нафталін | 0,5−1 | |||||
Фенол | 0,3−0,6 | |||||
Бенз (а)пірен | 0,0001−0,0005 | |||||
Ціан. водень | 0,1−0,3 | |||||
Кількість сірководню і сірчистого газу, що виділяються при завантаженні однієї печі, залежать від вмісту сірки в шихті. У разі застосування інжекції при завантаженні шихти викиди знижуються в 2,1 разу, а при бездимному завантаженні - в 16 разів. При видачі коксу від однієї печі виділяється 2,8 кг пилу і 0,606 кг окислу вуглецю. Показники викидів через димарі залежать від палива, вживаного для опалювання коксових батарей. Максимальна розрахункова кількість викидів визначається кількістю коксу, що поступає на гасіння. При сухому гасінні коксу за одну видачу, за даними Гипрококсу, виділяється 1,6 кг пилу і 1,12 кг окислу вуглецю.
Для розрахунку викидів хімічних цехів можна приймати, що у відділеннях конденсації і аміачно-сульфатном на кожну батарею доводиться сім повітряників, з яких виділяються аміак (0,02 г/хв), а також невелика кількість сірководню, пиридинових основ і ціаністого водню.
У відділенні уловлювання і дистиляції бензолу на кожну батарею доводиться по одну повітрянику висотою 5−9 м з викидами в кількості 1,6 г/хв.
Цех очищення коксового газу від сірководню викидає в атмосферу сірчистий газ — 1,34 г/хв на одну батарею. Газ, викидається через труби, заввишки близько 30 м із швидкістю викиду 2,6 м/хв. і температурою 50 оС.
Крім того, хімічні цехи забруднюють атмосферу наступними викидами від вентиляційних установок (на одну батарею) [4]:
Пари бензолу…0,216
Ароматичні вуглеводні …0,2
Оксид вуглецю… 0,058
1.2 Аналіз існуючих технологій гасіння коксу Технологічний процес виробництва коксу закінчується видачею його з печей при температурі 950−1100 С. Щоб запобігти горінню розжареного коксу після вивантаження з печі, а також зробити кокс придатним для транспортування і зберігання, необхідно понизити його температуру до 250−100 С, при якій виключається самозагорання і тління, тобто необхідно кокс «гасити» 1. Гасіння коксу є важливою технологічною операцією, від якої залежить вміст і коливання в ньому вологи, його якість, а також термін служби транспортерів і умови праці на коксосортувалках 1.
Існують два методи охолодження гасіння коксу: мокрий і сухий. При мокрому гасінні кокс охолоджують шляхом зрошування його певною кількістю води в спеціальному пристрої гасильній башті. Пристрій обладнано системою трубопроводів, форсунок-розпилювачів, через які вода подається на розжарений кокс, що знаходиться у вагоні.
При сухому гасінні охолодження проводять шляхом продування через шар розжареного коксу інертного газу, циркулюючого в замкнутій системі. Нагрітий інертний газ проходить на котел-утилізатор і таким чином використовується тепло коксу 1.
Виданий з печей кокс охолоджується водою (мокре гасіння), або циркулюючими газами (сухе гасіння коксу). При мокрому гасінні, поки що найбільш поширеному, тепло розжареного коксу не використовується, при сухому — використовується для отримання пара високих параметрів.
1.2.1 Технологія мокрого гасіння коксу Штанга видачі коксовиштовхувача виштовхує кокс з камери в гасильний вагон. При цьому кокс повинен бути рівномірно розподілений по довжині, що сприяє рівномірній вологості коксу[1]. Гасильний вагон при прийомі коксу пересувається з швидкістю, відповідної швидкості просування штанги видачі в печі. Потім кокс з можливо більшою швидкістю транспортують до гасильної башти з тим, щоб запобігти його горінню в дорозі.
кокс сухе гасіння
1 — металеві ворота з тамбуром; 2 — напрямні щити; 3 — дросельні клапани; 4, 5 — ланки зрошувального пристрою; 6 — важіль механізму керування спускним клапаном; 7 — спускний клапан; 8 — відбивні екрани Рисунок 1.1 — Гасильна вежа та зрошувальний пристрій
1 — металеві ворота з тамбуром; 2 — напрямні щити; 3 — дросельні клапани;
4, 5 — ланки зрошувального пристрою; 6 — важіль механізму керування спускним клапаном; 7 — спускний клапан для промивання зрошувального пристрою; 8 — відбивні екрани Рисунок 1.2 — Гасильна вежа та зрошувальний пристрій
Гасильна вежа являє собою залізобетонний каркас із витяжною трубою і пристроєм для гасіння коксу — зрошувальною системою (рис. 1.1−1.2). Розміри гасильної вежі визначаються габаритами гасильного вагона. Висота веж
— від 25 до 40 м, але не менш 15 м від верху коксової батареї. Над зрошувальним пристроєм є підсклепінний простір для водяних парів. При малому підсклепінному просторі пар від гасіння коксу частково виходить назовні з боку в'їзду гасильного вагона, зволожуючи електроапаратуру електровоза та погіршуючи видимість при підході електровоза до вежі.
Щоб запобігти зменшенню тяги у витяжній трубі від надходження у вежу зовнішнього повітря, у торці вежі, протилежному в'їзду вагона, установлюють тамбур довжиною 3−3,5 метри з металевими воротами. Тамбур також охороняє від поломки воріт, якщо електровоз буде загальмований із запізненням. Нижнє залізобетонне перекриття гасильної вежі має ухил для стоку води. Рейковий шлях закріплюється на дерев’яних шпалах, вільно покладених на нижнє залізобетонне перекриття. Кріпильні деталі виготовляють із нержавіючої сталі. Для зменшення віднесення краплі води над зрошувальним пристроєм установлюють дерев’яну насадку (краплевідбійник). Насадка промивається від відкладень шламу водою, подачею її з насосної по трубопроводу до колектора з форсунками. Нова гасильна вежа, що працює в комплексі з вагоном з донним зрошенням розпеченого коксу, має верхню частину конфузорно-дифузорного типу, що зменшує викид шкідливих речовин в атмосферу. Втрата швидкості пароповітряної суміші, що вилітає, у дифузорній частині приводить до випадання великих крапель води у внутрішній простір вежі.
Пароповітряна суміш, що піднімається над вагоном, проходить через систему краплевідбійників, розташованих у основі витяжної труби та у верхній її частині. Конструкція краплевідбійників передбачає можливість зміни прохідного перетину для пароповітряної суміші. Над нижніми краплевідбійниками встановлена система пилопароподавлення. Відбувається додаткове зрошення з форсунок системи пилопароподавлення, що сприяє скороченню виносу твердих часток і інших пароподібних викидів з гасильної вежі.
У гасильній башті є зрошувальний пристрій, куди вода подається або самопливом з напірного бака, або безпосередньо насосом. При першому методі капітальні витрати вище, складніше комунікації, вище витрата електроенергії, періодично потрібно очищати напірний бак. У зв’язку з цим зараз на більшості заводів освітлена вода із збірки подається в зрошувальну систему гасильної башти насосом, який автоматично включається при підході вагону з коксом до гасильної башти і виключається після закінчення заданого часу гасіння. Витрата води на гасіння коксу складає 3−4 м3 на тонну сухого валового коксу, причому безповоротна витрата на випаровування, краплинне віднесення і зволоження коксу складає приблизно 0,35−0,5 м3, тобто 10−12% від загальної кількості води, поданої на гасіння. Решта води стікає в спеціальні залізобетонні відстійники, де відстоюється від дрібних частинок коксу, що захоплюються з вагону. З басейну вода знову подається насосами на гасіння коксу. Коксовий шлам, що збирається у відстійниках, періодично забирається грейферним краном у вагони і відвантажується споживачам, найчастіше на агломерацію залізняку. Час гасіння залежить від властивостей вугільної шихти, температури обігріву і періоду коксування, гранулометричного складу коксу, якості води і складає 100−150 с. З яких 80−90 с — власне зрошування коксу водою, а 30−50 с — відстоювання вагону під гасильною баштою для стоку зайвої води. Час гасіння встановлюється постійним для кожного періоду коксування, контролюється і підтримується автоматично.
Водяна пара, що утворюється при заливці розжареного коксу, віддаляється через витяжну трубу.
З метою зменшення віднесення крапель і пилу в гасильній башті встановлюються краплевідбійники. Бажано, щоб при проведенні мокрого гасіння коксу його вологість була невеликою і стабільною, а швидкість охолодження не перевищувала таких значень, при яких посилюється утворення тріщин.
Для того, щоб понизити вологість коксу і підвищити його стабільність, необхідно зменшити час контакту води і коксу, що можливо при збільшенні подачі води на зрошування. Проте при цьому підвищується швидкість охолодження і збільшується глибина виникаючих тріщин. Після закінчення стоку води з вагону останній відвозить і розвантажує охолоджений кокс на похилий майданчик — коксову рампу, яка по довжині звичайно вміщає 4−5 печей. Довжина коксової рампи складає 60−70 м залежно від корисного об'єму печі. На рампі кокс витримується до подачі на сортування 12−16 хв.
Перевагами мокрого гасіння коксу є низька вартість установки, простота обслуговування, мала енергоємність устаткування.
До недоліків широко вживаного в даний час методу мокрого гасіння коксу відноситися наступне:
— великі втрати тепла з гарячим коксом. Ці втрати складають приблизно 40−45% від загальних витрат тепла на проведення процесу коксування або 4−4,5% від теплоти згорання скоксованного вугілля. На сучасному заводі продуктивністю 1,5−2 млн. т коксу на рік ці втрати складають 60−90 тис. т умовного палива [2];
— значні витрати електроенергії на зрошування коксу водою;
— пари води, що виділяються при гасінні коксу, містять в собі різні агресивні компоненти, якi викликають посилену корозію металевих конструкцій поблизу гасильної башти і забруднюють атмосферу [2];
— стікаюча з коксу вода викликає корозію гасильного вагону і він виходить з ладу після декількох місяців експлуатації. Тому гасильні вагони будують з неіржавіючої сталі;
— в результаті швидкого випаровування вологи при зрошуванні коксу водою відбувається додаткове утворення тріщин в коксі, що позначається на його гранулометричному складі [2];
— дрібні фракції коксу містять значну кількість вологи (до 12−15%), що ускладнює їх грохочення і можливість ефективного використання 3.
1.2.2 Технологічна схема, принцип роботи та коефіцієнт корисної дії процесу сухого гасіння коксу Способи сухого гасіння коксу і установки для їх реалізації базуються на охолодженні коксу в камері гасіння коксу охолоджувальним агентом, який циркулює в системі циркуляції охолоджувального агента [3]
Камера гасіння коксу являє собою вертикально розташовану шахту, футеровану вогнетривкою кладкою, в яку за допомогою засобу дозованого завантаження подають кокс.
Гасіння коксу в камері гасіння здійснюється пропусканням через шар коксу охолоджувального агента, інертного по відношенню до коксу. Під час проходження охолоджувального агента через шар коксу відбувається теплообмін, в результаті якого кокс віддає своє тепло охолоджувальному агенту, який потім відводиться з камери гасіння коксу в систему циркуляції охолоджувального агента.
Система циркуляції охолоджувального агента містить, як правило, фільтр грубого очищення, звичайно виконаний у вигляді пилеосадного бункера, котел-утилізатор, що являє собою відносно герметичну камеру, в якій розміщені теплообмінні поверхні, яким охолоджувальний агент віддає тепло, і засіб для відведення надлишкового об'єму охолоджувального агента з системи циркуляції. Після котла-утилізатора встановлено фільтр тонкого очищення охолоджувального агента, виконаний у вигляді циклона, далі розташований тягодуттьовий пристрій, наприклад, димосос.
Під час роботи УСГК частина системи циркуляції постійно перебуває під значним розрідженням, що приводить до присисань повітря в систему циркуляції охолоджувального агента. У систему циркуляції охолоджувального агента входить свічка, як засіб для відведення надлишкового об'єму охолоджувального агента, яка призначена для скидання в атмосферу надлишкового об'єму охолоджувального агента, що утворюється в системі циркуляції охолоджувального агента в результаті присисань повітря. У результаті, УСГК працює в певному аеродинамічному режимі, а саме, у верхній частині камери гасіння коксу підтримують значення тиску, близьке до атмосферного (так званийаеродинамічний нуль), що попереджає викид охолоджувального агента під час подачі (завантаження) коксу в камеру гасіння коксу, а також запобігає потраплянню в охолоджувальний агент повітря, присутність якого в охолоджувальному агенті приводить до вигару коксу. Підтримання у верхній частині камери гасіння коксу аеродинамічного нуля здійснюється за рахунок скидання надлишкового об'єму охолоджувального агента в атмосферу через свічку системи циркуляції охолоджувального агента. Свічка системи циркуляції охолоджувального агента встановлена після тяго дуттьового пристрою. У процесі роботи УСГК в нижній частині камери гасіння коксу значення тиску перевищує атмосферне на 200−300 кгс/м2, внаслідок великого опору коксу під час проходження охолоджувального агента через кокс, що приводить до викидів охолоджувального агента з камери гасіння коксу в момент вивантаження коксу на транспортний засіб, наприклад, конвеєр. Для того, щоб запобігти викиду охолоджувального агента з нижньої частини камери гасіння коксу, встановлюють засіб для безперервного вивантаження коксу, який зазвичай складається з дозатора і проміжного бункера. Визначення величини присисання повітря в систему циркуляції охолоджувального агента здійснюється в процесі роботи УСГК. Так, під час роботи УСГК, датчик тиску, розташований у верхній частині УСГК, постійно контролює значення тиску верхній частині камери гасіння коксу. При збільшенні тиску у верхній частині камери гасіння коксу відбувається скидання надлишкового об'єму охолоджувального агента з системи циркуляції охолоджувального агента через свічку в атмосферу.
Під час скидання надлишкового об'єму охолоджувального агента через свічку в атмосферу здійснюють виміри кількості охолоджувального агента за допомогою відомих засобів, наприклад, витратомірів. Після чого визначають, який надлишковий об'єм охолоджувального агента був скинутий в атмосферу в одиницю часу (год). Потім ділять отримане значення на значення кількості охолоджувального агента, яке прийшлось на гасіння коксу в камері гасіння коксу за той же проміжок часу (год), після чого отримують коефіцієнт присисання повітря. На основі коефіцієнта присисання повітря судять про ефективність роботи УСГК. Коефіцієнт присисання повітря в УСГК може становити до 15%. При коефіцієнті присисання повітря, рівному 15%, УСГК зупиняють на капітальний ремонт. При сухому гасінні коксу тепло розжареного передається газоподібному теплоносію, який потім поступає до теплообмінної поверхні. Як теплообмінний апарат, де використовується вторинне тепло, можна застосовувати паровий котел, повітряабо газопідігрівач або поєднання різних теплообмінних апаратів і силових установок[4].
В період гасіння коксу в системі безперервно циркулює охолоджуючий газ, що прокачується вентилятором (димососом). Розжарений кокс, що при цьому знаходиться в гасильній камері, охолоджується, а циркулюючий газ нагрівається. Тепло газу в теплообміннику передається вторинному теплоносію. Процес охолодження відбувається поволі і рівномірно і не супроводжується утворенням додаткових тріщин в коксі. Циркулюючий газ, послідовно проходячи через шари коксу, нагрівається до 600−800 С, а температура коксу знижується з 950−1050 С в зоні завантаження до 150−250 С в зоні вивантаження[4].
Установка сухого гасіння коксу містить:
a) камеру гасіння коксу, б) систему циркуляції охолоджувального агента, яка включає котел-утилізатор і примикає до камери гасіння коксу, в) засіб для вивантаження коксу з камери гасіння коксу.
Спосіб сухого гасіння коксу включає:
a) дозоване завантаження коксу в камеру гасіння коксу, б) охолодження коксу в камері гасіння коксу охолоджувальним агентом, який циркулює в системі циркуляції охолоджувального агента, в) подачу коксу з камери гасіння коксу в засіб для вивантаження коксу, г) вивантаження коксу з засобу для вивантаження коксу на транспортний засіб.
За конструктивним оформленням установки сухого гасіння коксу можна розбити на чотири основні групи:
— багатокамерні з малими камерами гасіння, кожна з яких обслуговує 2−4 печі [4];
— контейнерні, в яких кокс поступає в спеціальні контейнери і в них — в камери гасіння [4];
— камерні бункерного типа з накопичувачами гарячого коксу у форкамері, система Гипрококсу. ;
— камерні бункерного типа підземного і надземного розташування 5.
Проектом пропонується до застосування найбільш ефективну технологію сухого гасіння у установках бункерного типу. У установках бункерного типу процес гасіння наближається до безперервного, тому з теплотехнічної точки зору вони ефективніші ніж багатокамерні, працюючими як установки періодичної дії. При цьому забезпечується достатньо постійний і рівномірний температурний режим, що сприяє надійній роботі вогнетривкої кладки елементів установки. Крім того, в установках бункерного типа системи Гипрококсу, забезпечених форкамерою, до котла-утилізатора підводиться порівняно постійна кількість тепла при постійній температурі. Це в свою чергу зумовлює інтенсивніший теплообмін в казані і рівномірний вихід пари.
Питома продуктивність установок бункерного типа, в яких середня температура гріючого газу знаходиться в межах 700−800 С, на 4,67,5 кг/(м2ч), або 25,7−41% вище питомої паропродуктивності багатокамерних установок, в яких середня температура гріючого газу не перевищує 500 С. Необхідна поверхня нагріву при одній і тій же паропродуктивності для бункерної установки майже на 50% менше, ніж для камерних установок.
Перевагами сухого гасіння є:
— використання вторинного тепла;
— зменшення екологічного збитку у зв’язку з виключенням викидів шкідливих речовин, що мають місце при мокрому гасінні коксу і при виробництві еквівалентної кількості пари при спалюванні палива в парокотельнях;
— вища продуктивність по парі, що пояснюється підвищеною температурою циркулюючих газів перед казаном, що становить 750−830 С. На сучасних установках сухого гасіння коксу (УСГК) виробітку пари досягає 450−490 кг/т коксу;
— практично безперервний процес охолоджування коксу, що забезпечує рівномірну продуктивність казанів;
— нижча собівартість одержуваної пари (вона на 50−60% нижче за собівартість пари, що виробляється в котельних теплоелектроцентралі заводів)[5];
— підвищена якість коксу, що пояснюється попередньою витримкою його у форкамері, повільним, в порівнянні з мокрим гасінням, охолодженням циркуляційними газами і тривалим переміщенням в камері. В результаті стабілізується готовність коксу і його гранулометричний склад, а також поліпшуються фізико-механічні властивості. Випробування показали, що при використанні коксу сухого гасіння збільшується продуктивність доменної печі і знижується його витрата на проведення доменної плавки витрата коксу у доменному процесі знижується на 3−5%; продуктивність доменої пічі збільшується на таку ж величину.
При сухому гасінні в порівнянні з мокрим гасінням практично виключені викиди в атмосферу коксового пилу, оксиду вуглецю, аміаку, фенолів, сірководню та інші. В результаті різко скорочується збиток, який при мокрому гасінні наноситься навколишньому середовищу[5].
1.3 Вплив технології сухого гасіння коксу на навколишнє середовище
Технологічний процес коксування супроводжується викидами шкідливих речовин. У таблиці 1.3 приведено гранічно допустимі концентрації (ГДК) небезпечних і шкідливих речовин, які виділяються при виробництві коксу[6].
Сухе гасіння коксу розроблено й здійснюється як альтернатива мокрому гасінню з метою утилізації тепла гарячого коксу й ліквідації шкідливих викидів в атмосферу.
Основні речовини, що забруднюють атмосферу при сухому гасінні коксу — це пил і окису вуглецю.
Таблиця1.3 — Гранично допустимі концентрації (ГДК) шкідливих речовин в повітрі робочої зони
№ п/п | Найменування забруднюючої речовини | Величина ГДК, мг/м3 | Клас небезпеки | Об'єм викидів г/сек | |
Азота окисли | 21,034 | ||||
Пил | 150−400г/т | ||||
3. | Аміак (NH3) | 1,9 | |||
4. | Цианістий водень | 0,3 | 0,095 | ||
5. | Сірководень | 0,105 | |||
6. | Оксид вуглецю | 1,502 | |||
7. | Бенз (а) пирен | 0,15 | 0,35 | ||
8. | Фенол (карболонова кислота) | 0,3 | 0,095 | ||
Шкідливі речовини попадають в атмосферу при завантаженні камери УСГК коксом з газами вентиляції вузла розвантаження коксу й з надлишковим теплоносієм, що утворюється. Для зниження кількості викидів пилу використовують безпилове завантаження камер і систему очищення газів вентиляції вузла розвантаження коксу. Знешкодження від оксиду вуглецю не виробляється. Викиди в атмосферу для різних УСГК залежать від їхнього технічного стану й рівня експлуатації.
Технічним обстеженням великої кількості установок показано, що сумарні викиди пилу й оксиду вуглецю (без обліку викидів при завантаженні) для камер продуктивністю 50 т/годину складають відповідно 0,8−3,4 кг/т коксу. Для камер, продуктивністю 70 т/годину кількість пилу, що викидається знизилася до 0,4 кг/т, але при цьому значно збільшилися викиди оксиду вуглецю — до 29,2 кг/т коксу, тобто більш ніж в 8 разів. Причому для камер зазначеної продуктивності, що мають герметичні затвори вузла розвантаження коксу, більше 90% оксиду вуглецю викидається в атмосферу зі свіч димососу. Повністю виключити викиди шкідливих речовин з УСГК не представляється можливим, тому що вони закладені прийнятою технологією охолодження.
У камері УСГК (при г теплообмінних поверхнях котла й герметичному газовому тракті) протікають два паралельних процеси:
— у накопичувальній камері при ізотермічній витримці коксу й температурах ~ 1050 °C протікають реакції твердофазної поліконденсації з виділенням низькомолекулярних газів, у тому числі оксиду вуглецю, водню й метану; без вживання спеціальних заходів вміст зазначених газів перевищує передбачене правилами безпечної експлуатації УСГК [8];
— циркулюючий газовий теплоносій утворюється при пуску камери в експлуатацію в результаті взаємодії повітря з розпеченим коксом. При цьому утворюється діоксид вуглецю при > 900 °C реагує з вуглецем коксу з утворенням оксиду вуглецю; у результаті зсуву рівноваги убік останнього вміст оксиду вуглецю також перевищує значення, регламентоване правилами безпечної експлуатації УСГК.
Розглянуті процеси проаналізовані за умови герметичності газового тракту УСГК. На практиці досягти повної герметизації неможливо. У результаті підсмоктування повітря на ділянках тракту кисень повітря взаємодіє з вуглецем коксу, що веде до збільшення його «вигару» і утворенню надлишкового теплоносія. При сухому гасінні коксу в порівнянні з мокрим гасінням практично виключені викиди в атмосферу коксового пилу, оксиду вуглецю, аміаку, фенолів, сірководню. В результаті різко скорочується збиток, який при мокрому гасінні наноситься навколишньому середовищу.
У останніх проектах УСГК застосовано ряд нових систем, що запобігають шкідливим викидам. Зокрема, до них відносяться: безпилове завантаження камери коксом; утилізація надмірного циркулюючого газу; стабілізація оптимального гідравлічного режиму в завантажувальному пристрої і інші. Слід також відзначити, що конструкція дут'євого пристрою УСГК дозволяє здійснити регульовану зональну (по висоті камери) подачу циркулюючого газу, що, у свою чергу, дозволяє залежно від крупності і температури розжареного коксу вибрати оптимальний режим гасіння, при якому забезпечується високий коефіцієнт корисної дії з скороченням питомої витрати циркулюючого газу до мінімально необхідної величини[8].
1.4 Розрахунок матеріального балансу коксування
Матеріальний баланс коксування складається на підставі закону збереження маси речовин:
УGвих.= УGкiн, (1.1)
де УGвих — сума вагів сухої вугільної шихти (вихідних продуктів процесу) і кількості вологи, що поступила з нею в коксові печі;
УGкiн — сума вагів коксу, газу, смоли і інших хімічних продуктів (кінцевих продуктів), одержаних при коксуванні вугільної шихти.
На коксохімічному виробництві кінцеві продукти, за винятком пірогенетичної води, враховують достатньо точно. Тому для складання матеріального балансу використовують дані цехів технічних звітів. Щоб визначити вихід пірогенетичної вологи, застосовують розрахунковий метод — визначають вміст кисню у вугільній шихті і підраховують вихід пірогенетичної вологи[10].
Останніми роками значно змінилася сировинна база коксування, оскільки почали застосовувати у великих кількостях газове вугілля і частково інші (тощі, довгополум’яні), які раніше не використовувалися для отримання металургійного коксу. У зв’язку з цим змінився вихід коксу і летючих продуктів коксування; знадобилося змінити деякі загальноприйняті формули, наблизити їх до фактичних виходів кінцевих продуктів[10].
Початкові дані для розрахунку. Технічний аналіз шихти.
Початковими даними для розрахунку якості шихти є:
а) склад шихти по марках[10];
б) якість вугілля окремих марок[10].
Шихта призначена для отримання доменного коксу на коксохімічному заводі без вуглезбагачувальної фабрики, тому вона складається із збагаченого вугілля, що одержується заводом з ЗФ і ЦЗФ[10].
Вихідні дані для розрахунку.
Розрахункова одиниця завантаження — 1000 кг робочої шихти. Технічний аналіз шихти, що йде на брикетування представлено у таблиці 1.4.
Таблиця 1.4 — Склад вугільної шихти
ЦЗФ і марка | Частка в ших-ті, % | Технічний аналіз, % | Товщина пластичного шару, у | R0, % | ||||
1.Київська Ж | 13,3 | 11,0 | 8,8 | 1,56 | 36,0 | 1,11 | ||
2.Червонолим. Ж | 3,3 | 12,0 | 7,3 | 2,94 | 36,0 | 1,0 | ||
3.Печорська 2 Ж | 15,0 | 10,0 | 8,9 | 0,66 | 32,0 | 0,99 | ||
4.Калінінська Ж | 6,7 | 12,0 | 7,0 | 2,25 | 36,0 | 1,16 | ||
5.Постніковс. Ж | 1,7 | 12,0 | 8,4 | 2,82 | 36,0 | 1,02 | ||
6.Східна К+КЖ | 16,7 | 10,0 | 10,8 | 0,6 | 27,0 | 1,21 | ||
7.Північна К | 10,0 | 9,0 | 10,2 | 0,63 | 25,0 | 1,22 | ||
8. MV blend | 20,0 | 9,5 | 8,4 | 1,0 | 28,0 | 1,07 | ||
9. Чумаковська К | 5,0 | 12,0 | 8,4 | 2,71 | 28,0 | 1,34 | ||
10. Вузловська К | 8,3 | 12,0 | 8,4 | 1,65 | 28,0 | 1,44 | ||
Вологість шихти
(1.2)
Вміст золи
(1.3)
Вміст масової частки загальної сірки
(1.4)
Вихід летючих речовин
(1.5)
Товщина пластичного шару
(1.6)
Очікувана якість коксу,%
Вміст золи
Ак=Аdш· Коз, (1.7)
де Коз — коефіцієнт озоленя 1,29
Ак = 8,5· 1,29 = 10,97 ~ 11,0%
Вміст масової частки загальної сірки
Sк=Sdш· Кc, (1.8)
де Кc — коефіцієнт перерахунку сірки 0,8
Sк = 1,24· 0,8 = 0,99%
Показники технічного аналізу відповідають рекомендованим значенням (таблиця 1.5). Величини виходу летючих речовин Vdaf = 30,1% і товщини пластичного шару у=18,9 мм дозволять прогнозувати отримання доменного коксу задовільної міцності.
Таблиця 1.5 — Технічний аналіз вугільної шихти
Масова частка загальної вологи, % Wrш | Вміст золи, %, Adш | Вміст масової частки загаль-ної сірки, %, Sdш | Вихід летю-чих речо-вин, %, Vdaf | Товщина пластичного шару у, мм | |
10,4 | 8,5 | 1,24 | 30,1 | 18,9 | |
Елементний склад вугільної шихти зазвичай визначається експериментально. Тут він прийнятий за літературними даними для типової вугільної шихти (таблиця 1.6).
Таблиця 1.6 — Елементний аналіз вугільної шихти
Вуглець, % Сdaf | Водень, % Hdaf | Кисень, % Odaf | Азот, % Ndaf | |
87,51 | 5,22 | 5,40 | 1,87 | |
Показники технічного аналізу (Adш та Sdш) перераховуємо із сухої на робочу шихту
(1.9)
(1.10)
Перерахування показників елементарного аналізу шихти з органічної на робочу масу:
(1.11)
%
%
%
%
Для перевірки правильного розрахунку отримані данні зводимо в контрольний рядок
(1.12)
1.4.1 Прихідна частина балансу
За одиницю робочої шихти Grш приймається 1000 кг.
Кількість сухої шихти, що завантажується в камеру коксування
Gdш= Grш -Gw, (1.13)
де Gw — кількість вологи в одиниці робочої шихти, кг
(1.14)
Тоді кількість сухої шихти
Gdш= 1000−104=896 кг або 89,6% від робочої шихти.
1.4.2 Витратна частина балансу
При шаровому коксуванні утворюється ряд продуктів. Орієнтовно визначимо (у зв’язку з рядом припущень) вихід цих продуктів розрахунковим шляхом (вихід яких не нижче 0,1%).
1.4.2.1 Вихід сухого валового коксу із сухої шихти
Gdk = 94,84 — (0,635•Vdш), (1.15)
де Vdafш — вихід летючих речовин від сухої шихти, %.
(1.16)
Тоді Gdk=94,84-(0,635•27,5)=77,38%
1.4.2.2 Вихід сухого валового коксу на робочу шихту
(1.17)
1.4.2.3 Вихід зворотнього сухого коксового газу (відпрацьований газ — після вилучення хімічних летючих продуктів коксування)
Від робочої шихти
(1.18)
де А2 — емпіричний коефіцієнт (2,542,99). Приймаємо 2,80.
Від сухої шихти
(1.19)
1.4.2.4 Вихід кам`яновугільної смоли
Від робочої шихти
(1.20)
Від сухої шихти
(1.21)
1.4.2.5 Вихід сирого бензолу
Від робочої шихти
(1.22)
Від сухої шихти
(1.23)
1.4.2.6 Вихід 100%-го аміаку
Від робочої шихти
(1.24)
де b — емпіричний коефіцієнт переходу азоту шихти в аміак (0,11−0,15)
Приймаємо 0,14; 17 — молекулярна маса аміаку; 14 — атомна маса азоту.
Від сухої шихти
(1.25)
1.4.2.7 Вихід сірки в перерахуванні на сірководень
Від робочої шихти
(1.26)
де КS— коефіцієнт переходу сірки в сірководень (0,17−0,29). Приймаємо
0,24; 34- молекулярна маса сірководню; 32 — атомна маса сірки.
Від сухої шихти
(1.27)
1.4.2.8 Вихід пірогенетичної вологи
Від робочої шихти
(1.28)
де — спостережувальна кількість пірогенетичної вологи; - коефіцієнт переходу кисню шихти в пірогенетичну вологу, Кп.в.=0,334±0,505, у середньому Кп.в.=0,44; 18 — молекулярна маса води; 16 — атомна маса кисню.
Від сухої шихти
(1.29)
Зведений матеріальний баланс надано у таблиці 1.7.
Таблиця 1.7 — Зведений матеріальний баланс коксування вугільної шихти
Прихідна частина | Витратна частина | |||||
Стаття | Кількість | Стаття | Склад,% | |||
Маса, кг | % | Робоча маса | Суха маса | |||
Завантажена суха шихта | 89,6 | Кокс валовий | 69,33 | 77,38 | ||
Волога шихти | 10,4 | Смола безводна | 3,39 | 3,78 | ||
Сирий бензол | 1,045 | 1,17 | ||||
Коксовий газ | 13,16 | 14,68 | ||||
Аміак | 0,21 | 0,23 | ||||
Сірководень | 0,28 | 0,32 | ||||
Пірогенетична волога | 2,16 | 2,41 | ||||
Волога шихти | 10,4 | ; | ||||
Нев’язка балансу | 0,02 | 0,03 | ||||
Разом | Разом | |||||
1.5 Висновки до аналітичної частини
1. Визначені недоліки процесу мокрого гасіння, які полягають в наступному:
— великі втрати тепла з гарячим коксом. Ці втрати складають приблизно 40−45% від загальних витрат тепла на проведення процесу коксування або 4−4,5% від теплоти згорання вугілля [2];
— значні витрати електроенергії на зрошування коксу водою;
— пари води, що виділяються при гасінні коксу, містять в собі різні агресивні компоненти, якi викликають посилену корозію металевих конструкцій поблизу гасильної башти і забруднюють атмосферу [2];
— в результаті швидкого випаровування вологи при зрошуванні коксу водою відбувається додаткове утворення тріщин в коксі, що позначається на його гранулометричному складі [2];
— дрібні фракції коксу містять значну кількість вологи (до 12−15%), що ускладнює їх грохочення і можливість ефективного використання 3.
2. Основними перевагами сухого гасіння коксу є можливість не тільки ефективного використання величезних вторинних ресурсів тепла шляхом заміни гасильної установки мокрого гасіння сучасним теплотехнічним агрегатом, який утилізує більше 80% тепла, що виноситься з печі розжареним коксом. Кожна тонна коксу, погашеного сухим способом, дозволяє одержати близько 400−500 кг пара енергетичних параметрів.
3. Застосування сухого гасіння коксу зменшує забрудненість навколишнього середовища, у зв’язку з виключенням викидів шкідливих речовин (коксового пилу, оксиду вуглецю, аміаку, фенолів, сірководню і ін.), що мають місце при мокрому гасінні коксу.
2. ОСНОВНА ЧАСТИНА
2.1 Розрахунок кількості коксових камер і основного устаткування
Вибираємо для проектування печі з нижнім підведенням тепла конструкції Гипрококсу системи ПВР з об'ємом камери 41,6 м3, заввишки 7 м, шириною камери 450 мм. Основною перевагою коксових печей з нижнім підведенням є можливість більше точного й легко здійсненного дозування кількості тепла по довжині опалювального простінка, що створює передумови для забезпечення однакової якості коксу по довжині камери коксування й підвищення продуктивності печей.
Для розрахунку кількості металургійного коксу (Рм.к.d) т/рік задана робоча шихта в кількості 1 350 000 т/рік
(2.1)
де ав.к. — вихід з сухого валового коксу металургійного коксу (для металургійного коксу +25 мм ав.к. = 0,94ч0,96; Квихід валового коксу за сухою шихтою, %, береться з матеріального балансу коксування К = 69,33%
При заданій продуктивності металургійного коксу потреба в сухому валовому коксі складе:
(2.2)
Продуктивність коксового цеху складає 2 158 505 т валового коксу на рік. Розрахунок необхідної кількості печей в коксовому цеху проводимо по формулі:
(2.3)
де n — кількість печей в коксовому блоці; Рмк — задана продуктивність по металургійному коксу, т/ч; t — оборот печей, ч (приймаємо 17 ч); К — вихід сухого валового коксу від сухої шихти; авк — вихід металургійного коксу; Vк — корисний об'єм камери, м3; умс — насипна маса шихти, т/м3 (приймаємо 0,79).
Приймаємо для проектування 2 батареї по 82 печі в кожній.
При визначенні числа печей в батареї враховують, що при збільшенні числа печей знижуються питомі капітальні витрати, скорочується загальна протяжність і площа коксового цеху. В той же час від числа печей в батареї залежить ступінь завантаження коксових машин, вартість яких складає 35−45% від вартості батареї.
Вугільна башта розміщується по осі коксових батарей і є бункерною спорудою, з якої коксові печі завантажуються вугільною шихтою за допомогою завантажувального вагону. Кожна вугільна башта розташовується між двома батареями.
Корисна місткість визначається добовою потребою коксового цеху у вугільній шихті.
(2.4)
де Q — добова потреба в шихті, т/добу; N — число батарей, шт.; n — число печей в батареї, шт.; Vк — корисний об'єм коксування, м3; у — насипна маса шихти, т/м3; t — час обороту печі, ч;
т Приймаємо для проектування вугільну башту місткістю 8000 т.
Розрахунок кількості комплектів обслуговуючих машин.
Кількість комплектів обслуговуючих машин може бути розрахована по формулі:
(2.5)
де n — кількість печей в блоці; tобсл — час прийнятий на обслуговування однієї печі, хв; - період коксування, ч; tц — час на поточний ремонт в межах циклу комплекту Приймаємо число комплектів 2, вважаючи, що кожна батарея обслуговується окремим комплектом машин. Для коксового блоку з двох батарей приймається наступне число коксових машин (табл.2.1):
Таблиця 2.1 — Кількість технологічного устаткування
Коксові машини | Робочі | Резервні | |
Коксовиштовхувачі | |||
Завантажувальні вагони | |||
Дверез'ємні машини з коксонапрямними | |||
Електровози | |||
Розрахунок кількості камер гасіння.
В цілях утилізації тепла гасіння коксу і захисту повітряного простору і водного басейну на проектованому заводі передбачається сухе гасіння коксу, здійснюване в установках бункерного типа системи Гіпрококсу з котлом-утилізатором.
Продуктивність однієї камери УСГК складає 1200−1300 т на добу.
Виходячи з продуктивності заводу, нам необхідно гасити:
2 050 580 / 0,95 = 2 158 505,2 т валового коксу на рік.
Для цього необхідно побудувати:
2 158 505,2 / 450 000 = 4,79камери УСГК.
Приймаємо для проектування 5 камер УСГК 11.
Коксовий цех призначено для одержання коксу та коксового газу з вугільної шихти, що подається по конвеєрних трактах вуглеподачі з вуглепідготовчого цеху.
До складу коксового цеху входять батареї коксових печей з допоміжними й обслуговуючими пристроями й спорудженнями; коксові машини (коксоштовхачі, вуглезавантажувальні вагони, дверезнімні машини, гасильні, коксовозні вагони з електровозами), вугільні башти для оперативного запасу вугільної шихти. Газове господарство коксових батарей складається з газопідводящої арматури, пристрою для перемикання та регулювання газових і повітряних і димових потоків, регулювання гідравлічного режиму.
У складі коксового цеху може бути декілька коксових батарей. Коксові батареї компонуються в блоки, що об'єднуються загальною вугільною баштою, системою приймання видаваного з печі готового коксу і його гасіння (рисунок 2.1). Розташування коксових батарей визначається компоновкою коксового цеху. Вугільна башта може розташовуватися між двома коксовими батареями.
У комплект коксових машин коксової батареї входять: коксовиштовхувач, завантажувальний вагон, дверезнйомна машина коксової сторони.
Проектні та фактичні виробничі потужності коксових батарей надано у таблиці 2.2.
Таблиця 2.2 — Проектні та фактичні виробничі потужності коксових батарей
№ коксових батарей | Рік уведення в експлуатацію | Потужність коксових батарей, тис. тонн коксу 6% вологості | ||||
I етап реконструкції КХВ | II етап реконструкції КХВ | III етап реконструкції КХВ | ||||
Проектна | Виробнича на 01.01.2007 | |||||
б № 1 | 22.02. 1949;29.12.1971 | 14.01. 1975;30.08.1991 | 12.10.1999 р. | 566,8 | 566,3 | |
б № 2 | 30.09. 1949;29.12.1971 | 26.01. 1974;30.08.1991 | 17.04.1996 р. | 566,8 | 566,3 | |
б № 3 | 01.06. 1951;27.10.1976 | 17.03. 1978;16.09.1999 | Зупинено, перебуває на реконструкції | 630,0 | ; | |
б № 4 | 12.12. 1951;27.10.1976 | 01.03. 1979;13.03.1996 | 18.01.2007 | ; | ||
б № 5 | 1960;1984 | 16.06.1986 | 479,0 | 448,9 | ||
б № 6 | 1961;1984 | 30.09.1985 | 479,0 | 448,9 | ||
Блок з двох коксових батарей обслуговується одним коксовозним вагоном, який доставляє гарячий кокс до гасильного пристрою.
Коксоштовхачі призначені для відкриття, відводу та установки дверей, виштовхування коксу з коксових камер, очищення дверей і рам, планування шихти в камері та збирання планирного вигреба в бункер.
Завантажувальний вагон призначено для набору шихти з вугільної башти, транспортування шихти до печей, завантаження печей, очищення стояків від графіту. Завантажувальний вагон складається з: механізму пересування, механізму чищення стояків, механізму відкривання й закривання затворів вугільної вежі; механізму відкривання й закривання шиберів на бункерах завантажувального вагона.
Проектом пропонується для гасіння коксу використовувати циркуляційні гази, тому на торці батареї або проти фронту печей замість гасильної башти споруджено установку сухого гасіння коксу.
Створення установок сухого гасіння коксу забезпечить підвищення одиничної потужності коксової батареї за рахунок збільшення об'єму, інтенсифікація процесу коксування за рахунок застосування вогнетривких матеріалів з підвищеною міцністю і теплопровідністю зробило вплив на компоновку коксового цеху.
При сухому гасінні час на обслуговування печі коксовозним вагоном скорочується приблизно на дві хвилини. У цих умовах головним стає час, необхідний для обслуговування печі вуглезавантажувальним вагоном (за умови бездимного завантаження), яке складає 650 сек.
2.2 Обґрунтування вибору сухого гасіння Основними перевагами сухого гасіння коксу є можливість ефективного використання величезних вторинних ресурсів тепла шляхом заміни гасильної установки мокрого гасіння сучасним теплотехнічним агрегатом.
Вибір типу установки сухого гасіння коксу залежить від багатьох чинників і може бути зроблений правильно тільки з урахуванням всіх умов даного підприємства. Нижче розглядаються основні чинники, які необхідно враховувати при виборі установки.
Порівняння в основному торкатиметься багатокамерних і бункерних установок і у меншій мірі контейнерних і жаротрубних, оскільки установки останніх двох типів не знайшли широкого застосування на крупних коксових заводах унаслідок малої продуктивності. Камерні установки бункерного типа не примикають до коксових печей, тому аварійні або планові зупинки їх за наявності резервного блоку або при мокрому гасінні не відображаються на роботі коксової батареї. При багатокамерному способі, коли УСГК примикає до коксових печей, будь-яка зупинка камери гасіння спричиняє за собою припинення процесу коксування. Для усунення цього недоліку пропонується розміщувати гасильні камери на деякій відстані від батареї, передбачивши між ними передавальний пристрій. Проте це пов’язано не тільки з технічними труднощами, але і з додатковими витратами.
У установках бункерного типа процес гасіння наближається до безперервного, тому з теплотехнічної точки зору вони ефективніші ніж багатокамерні, працюючими як установки періодичної дії. При цьому забезпечується достатньо постійний і рівномірний температурний режим, що сприяє надійній роботі вогнетривкої кладки елементів установки. Крім того, в установках бункерного типа системи Гипрококсу, забезпечених форкамерою, до казана-утилізатора підводиться порівняно постійна кількість тепла при постійній температурі. Це в свою чергу зумовлює інтенсивніший теплообмін в казані і рівномірний вихід пари.
Питома продуктивність установок бункерного типа, в яких середня температура гріючого газу знаходиться в межах 700−800 С, на 4,6−7,5 кг/(м2ч), або 25,7−41% вище питомої паропродуктивності багатокамерних установок, в яких середня температура гріючого газу не перевищує 500 С. Необхідна поверхня нагріву при одній і тій же паропродуктивності для бункерної установки майже на 50% менше, ніж для камерних установок.
Установки камерного типа компактніші в порівнянні з багатокамерними.
Для розміщення установок камерного типа потрібні значно більші площі, ніж для розміщення установок бункерного типа. Багатокамерні установки громіздкі, причому займана ними площа різко зростає при зниженні маси однієї порції коксу завантаженого коксу і тієї ж добової продуктивності. Бункерна установка незалежно від маси однієї порції коксу займає одну і ту ж площу. Таким чином, для бункерної установки створюються сприятливіші умови для розміщення її на діючому заводі.