Проектування печі для варіння скла
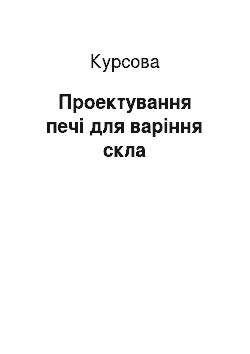
Скловарна піч, призначається для варіння скла та його підготовки до формуванню. У скловарної печі шихта (сировинні компоненти) в процесі нагрівання (зазвичай до 1500−1600°С) проходить стадії сілікатоутворення, взаємного розчинення силікатів і залишкового кремнезему, освітлення (знегажування), а потім перетворюється на скломасу, придатну для формування виробів. До періодичних відносяться горшкові… Читати ще >
Проектування печі для варіння скла (реферат, курсова, диплом, контрольна)
Вступ
Скловарна піч, призначається для варіння скла та його підготовки до формуванню. У скловарної печі шихта (сировинні компоненти) в процесі нагрівання (зазвичай до 1500−1600°С) проходить стадії сілікатоутворення, взаємного розчинення силікатів і залишкового кремнезему, освітлення (знегажування), а потім перетворюється на скломасу, придатну для формування виробів. До періодичних відносяться горшкові, а також невеликі ванні печі. Ці печі застосовуються для варіння спеціальних стекол: оптичного скла, кольорового, світлотехнічного скла, кришталю та ін., вироблення яких виробляється переважно вручну. Горшкові скловарні печі вельми неекономічні (ККД близько 8%), але в них можна одночасно варити скло різного складу, причому в горщиках порівняно легко здійснити перемішування і отримати однорідну скломасу. Більш економічні періодичні ванні скловарні печі; застосовуються переважно для варіння. У безперервно діючих ванних печей здійснюється варіння масових промислових стекол (листове скло, тарне та ін.), що виробляються машинним способом .У таких стадії варіння протікають в певних зонах при подальшому переміщенні розплаву по довжині печі. Конструкції ванних скловарних печей розрізняються за напрямом полум’я, способу виділення варочної і виробленої частин у скляному розплаві (наприклад, плаваючих шамотних тіл. Наприклад, для виробництва листового скла застосовують безперервно діючі ванні печі з поперечним полум’ям; довжина басейну до 60 м, ширина 10 м, глибина до 1,5 м, басейн вміщає до 2,5 тис. т скломаси. Продуктивність безперервних ванних Скловарна піч до 300 т / добу і більше скломаси. Басейни ванних печей споруджуються з вогнетривів.
скловарний горіння варочний паливо
1. Технологічні основи скловаріння
Технологія виробництва скла включає операції, реалізовані як поза робочого простору (реактора) скловарної установки (підготовка шихти, формування, охолодження та обробка готових виробів), так і в робочому просторі (нагрівання і плавлення шихтових матеріалів з?? процесами силікатів-і скло утворення, дегазація і гомогенізація скломаси, охолодження скломаси до заданої температури видачі - студка) Основна маса виробленого у світі скла (більш 90%) виплавляється з содовою або сульфатної шихти.
Содова шихта — трьохкомпонентна, що складається з кварцового піску, соди кальцинованої і вапняку СаСОз.
Сульфатная шихта — чотирьохкомпонентна, що складається з кварцового піску, сульфату натрію, вапняку и вуглецю С.
До складу шихти обов’язково вводиться бій скла, відходи його виробництва і використання в кількості до 30—50%.
Підготовка шихти включає дроблення її: чим менше частки піску, вапняку, крейди, гранули кальцинованої соди або сульфату натрію, тим вища продуктивність печей, швидкість плавлення, гомогенізації і якість скломаси, сушку піску (при вмісті вологи вище 1%) або, навпаки його зволоження (до 0,5−1%), змішання компонентів (чим однорідніше суміш, тим вище швидкість гомогенізації і, отже, краще якість скла, менше витрати часу енергоресурсів на перемішування скломаси), введення шихт в піч (шаром товщиною не більше 30 мм). Матеріали, завантажені в піч, піддаються тепловій обробці зі складним температурним графіком (мал. 1.1).
Мал. 1.1. Температурний графік процесу в скловарних печах:
а) горшкові (тигельні); б — ванні; С — скло сортове; СП — те ж саме, поливане; Э — теж саме, електровакуумне.
Шихтові матеріали завантажуються в зони високих (1300 — 1500 ° С) температур, тому одночасно з їх нагрівом плавлення починаються і завершуються реакції сілікатоутворення. Одночасно з сілікатоутворенням в шихті і утворених евтектоїдному сілікатному розплаві йдуть процес видалення вільної та гідратної вологи, окислення металів переходу їх із нижчих оксидів до вищих (,), видалення летких (борної кислоти та її солей, оксидів свинцю, миш’яку, сурми, селену та ін.), розчинення надлишку кремнезему, утворення, освітлення і гомогенізації скломаси — головні і завершальні етапи варіння («провару») скла.
Внаслідок високої в’язкості і тому слабкого розвитку і конвекційних струмів процес розчинення кремнезему відрізняється малою інтенсивністю (великою тривалістю). Тривалість провару за Ф.Г. Солінову визначається максимальною температурою скломаси
де a і b — константи, що залежать від хімічного складу і фізичних характеристик шихти (а = 50 200; b = 0,2 0,9).
Освітлення і гомогенізація скломаси — складні та відповідальні технологічні операції, що проводяться при максимальних температурах 1600—1800 °С. Освітлення скломаси здійснюється тривалої її витримкою при високій: температурі і механічним перемішуванням (барботажем) скломаси шляхом продувки різними газами, а також добавками в шихту спеціальних освітлювачів (сульфату натрію 0,30,5, азотнокислого калію до 1, триоксида миш’яку до 0,02, сірчанокислого амонію 0,51,0, повареної солі 1—2,0% та ін.). Освітленню сприяє підвищення тиску або, навпаки, вакуумування, застосування ультразвуку та ін.
Гомогенізація скломаси через її високу в’язкість, великого поверхневого натягу і слабкого розвитку конвекційних струмів також є складною технологічною операцією. Гомогенізація дещо посилюється при барботажі і підвищенні температури скломаси, проте головним залишається тривалість витримки при стабільних тепловому і температурних режимах.
Заключною операцією скловаріння є охолодження (студка) скломаси, тобто зниження її температури на 200−300 ° С з метою підвищення в’язкості до значень, необхідних технологією витяжки (формувань). Для цього скломаса в горшкових печах охолоджується шляхом зменшення подачі палива (тобто зниженням теплового навантаження), а у ванних печах скломаса перетікає в третю ванну — в зону, в якій паливо не подається взагалі або подача його виробляється лише в кількостях, достатніх для підтримки заданого зниженого температурного рівня.
1.1 Теплові та конструктивні схеми скловарних установок
Залежно від форми і розмірів (місткості) ванн розрізняють скловарні установки горшкові і ванні. Горшкові печі - це реактори періодичної дії, призначені для виробництва високоякісного (оптичного, кварцового і т. п.) скла.
Шихта, завантажується в горщики — тиглі місткістю від 14 до 1000 кг, виготовлені з вогнетривких матеріалів (шамотних високо глиноземних, динасових, графітових, платинових і т.п.). Горщики, як правило, закриваються кришками, виготовленими з таких же вогнетривких матеріалів.
Ванні печі (печі безперервної дії) є основною ланкою установок для виробництва віконного, посудного, в тому числі кришталевого, скла, а також склопроката і склоблоків. Ванни вміщають 50−500 т скломаси. Як горшкові, так і ванні печі споруджуються полум’яними (паливними), електричними і полум’яно-електричними. В якості палива зазвичай використовується газоподібне паливо (в основному природний газ).
За способом підігріву повітря (у рекуператорах або регенераторах) полум’яні печі відповідно поділяються на регенеративні і рекуперативні. На мал. 1.2 наведені теплові схеми трьох найбільш поширених типів скловарних установок.
Рис. 1.2. Теплові схеми скловарних установок:
1 — паливні (газові, газомазутні, мазутні); 2 — електротопливні (електрогазові); 3 — електричні; А — горшковые (тигельні) однокамерні; Б — ванні (двох -, трьох — та багатокамерні); М — матеріал, шихта; ТП— продукт; В — повітря; ДГ — димові гази; Э — електроенергія; Т — паливо (газ); ИМ — вихідний матеріал Скловарна установка з горшковою регенеративної піччю (мал. 1.3) складається з робочої камери 1 (на один-п'ять горщиків 2), регенераторів 3, розташованих під робочою камерою і з'єднаних з нею вертикальними каналами 4, пальників висококалорійного палива 5, димової труби (на малюнку не показана) і кнурів 6, з'єднують димову трубу з низом регенераторів. Кожен горщик встановлюється на двох металевих брусах, покладених на під 7 по бортах зливного жолоба 8 з пробкою 9 для випуску скломаси (при руйнуванні горщика) в збірник 10 некондиційного скла ерклеза.
Рис. 1.3. Скловарна установка з горшковою регенеративної піччю Під 7 виконується із шамотної цегли або спеціальних блоків товщиною до 300 мм. Стіни 11 з садочним 12 і вироботочним 13 вікнами, що закриваються заслінками 14 і головним склепінням 15, виконуються з динасового сводової цегли. Під переходить на потужну (товщиною 740−1100 мм) розділову стінку 16 регенераторів, за допомогою якої навантаження від маси печі і садки передаються на фундамент печі 17. Повітряні регенератори 3 (правий і лівий) мають насадку з шамотної цегли, викладену зазвичай по Сіменсу з осередками 115X115 мм. Кладка регенераторів і робочої камери ретельно ізольована шаром теплоізоляційного цегли.
Ванна скловарна піч, опалювальна природним газом (рис. 1.4), складається з робочої камери 1 і повітрянагрівтелей (рекуператорів) 2. Робоча камера підрозділяється на басейн з варильною 3 та виробленою 4 частинами, розділеними у верхній частині масивної розділової стінкою 5.
Басейн утворений плоским подом, поздовжніми і поперечними стінками, викладеними з високовогнетривких, найчастіше муллітові або ціркономуллітових, блоків (брусів з розмірами 1000X400X300 мм), охолоджуваних в нових печах зовні металевими холодильниками 6. Полум’яний простір складається з двох зон — вручений і вироблених, відокремлюваних розділової стінкою, викладеної над човном. У поздовжніх стінах варильної камери розташовуються пальники 7 (на регенеративних печах-голівки), торцева стінка 8 має садочне вікно 9 для завантаження шихти і дві - чотири пальники для регулювання температури. Введення повітря для охолодження подається через патрубок 10.
Рис. 1.4. Ванна скловарна піч
2. РОЗРАХУНОК СКЛОВАРНОЇ ПЕЧІ
Виконати розрахунок скловарної регенеративної ванної печі для варіння побутового скла. Продуктивність печі 80 т / добу.
2.1 Вибір основних рішень проекту
Для здійснення технологічного процесу виробництва скляних ізоляторів пропонується регенеративна скловарна піч з поперечним напрямком полум’я. Підготовка скломаси до формування здійснюється в вироблених каналах, що мають глибину 0,3−0,4 м, з самостійним опаленням і можливістю регулювання температури скломаси по довжині каналу за допомогою керамічних шиберів. За полум’яному простору варильна і студочная частини повністю розділені; по скломасі поділ здійснюється за допомогою протоки.
Інтенсифікація процесу варіння досягається зменшенням глибини басейну в зоні завантаження шихти, установкою барботажа і порогу в зоні освітлення і гомогенізації скломаси. Передбачається ізоляція стін басейну і склепіння печі ефективними теплоізоляційними матеріалами.
Для отримання високої якості скломаси, що надходить на формування, і більшої тривалості міжремонтного періоду роботи печі передбачені наступні конструктивні вузли:
1. Подвійне дно з донного бруса в зоні варіння, що дозволяє зберегти тепло в придонних шарах скломаси і зменшити втрати тепла в навколишнє середовище. При капітальних ремонтах можлива мінімальна заміна дна, що зменшує матеріаломісткість капіталовкладення. Подвійна бакоровая плитка, що позитивно впливає на збереження шамотних брусів дна і сприяє найменшому їх роз'їданню.
2. Передбачений поріг в зоні максимальних температур, він позитивно впливає на освітлення скломаси, хімічну і термічну однорідність; це усереднює потоки скломаси, поділяє скломасу на два потоки: варильний і вироблений і не дає не провареній скломасі проникати на вироблення.
3. Надходження скломаси в вироблені канали здійснюється через протоку, що дозволяє швидко остудити скломасу до бажаної температури і перешкоджає вступу гарячих потоків скломаси в вироблену частину.
Параметри роботи печі: паливо — природний газ; температура варки — 1530 єС; питомий об'єм — 800 кг/м2· добу.
2.2 Визначення основних розмірів і опис конструкції печі
Визначаємо площу варочної частини басейну:
Fвар Р/ Рf 80 000 /800 100 м2
де Р — продуктивність печі по скломасі, кг/добу;
Рf — питомий об'єм скломаси, кг/м2· добу, приймаємо по практичним даним 800 кг/м2· добу.
Дно басейну виконується з многошамотних брусів розміром 1,0Ч0,4Ч0,3 м та покривається двома шарами бакоровой плитки товщиною 0,1 м. Стіни басейну збираються з бакорових брусів. Товщина бакорових стін 0,25 м. Для зменшення втрат тепла в навколишнє середовище передбачена ізоляція стін басейну легковажним шамотом і алюмохромофосфатним газобетоном.
Ширина варочної частини 5,5 м (з урахуванням розкладки 15-ти донних брусів по ширині дна басейну, ширина донного бруса 0,4 м).
bб 15? 0,4 6,0 м, bвар 6,0 0,5 5,5 м, lвар 80 /5,5 14,55 м ,
співвідношення l/b 14,55/5,5 2,65.
В табл. 1.1 наведена загальна характеристика печі. Для завантаження шихти піч обладнана виносним, повністю герметизованою кишенею з установкою чотирьох плунжерних завантажувачів.
Таблиця 2.1 Загальна характеристика печі
Параметри печі | Одиниця виміру | Значення | |
Площа * варочної частини * виробочого каналу | м2 м2 | 80,0 9,34 | |
Варильна зона: * довжина Ч ширина * глибина | мЧм м | 14,55 Ч 5,5 от 1,4 до 1,1 | |
Вироботочний канал: * довжина по поздовжньої оси печі * ширина х глибина | м мЧм | 0,9 10,6 Ч 0,3−0,4 | |
Габарити протоки * довжина Ч ширина Ч висота | мЧмЧм | 1,2 Ч 0,6 Ч 0,4 | |
Характеристика горілок: * кількість * підвід палива * площа вліт * кут нахилу | пари м2 єС | бічній 2,63 | |
Тип сопла горілки для подачі палива Діаметр вихідного перетину сопла пальника: * зовнішній діаметр, * внутрішній діаметр | мм мм | ||
Регенератор: Кількість ходів по повітря (підхідних газів) Тип насадок Розмір комірок насадок Загальний обсяг насадок | м м3 | Лихте 0,12 Ч 0,12 | |
Вироботочний канал: * довжина по поздовжньої осі печі * ширина х глибина | м мЧм | 1,55 4,5 Ч 1,1 | |
Кількості завантажувачів | шт | ||
Переливний поріг | трапецеїдальний | ||
Висота склепіння печі над скломасою | м | 2,185 | |
Система обдуву огорож печі | Обдуваються стіни басейну | ||
Широкий завантажувальний кишеня дозволяє активізувати процес варіння, т. к. шихта розподіляється на великій площі басейну печі і тим самим зменшується її шар, а значить швидше відбувається прогрів як зверху, так і від розплавленої скломаси знизу, збільшується швидкість силікатів-і склоутворення, прискорюється процес варіння, забезпечується якісний провар скломаси.
Установка бакорових арок над завантажувальним кишенею забезпечує збереження торцевої стіни, найменше її роз'їдання шихтними матеріалами. Виносна арка з многошамота герметично закриває кишеню, що усуває запилювання шихти і втрати тепла в навколишнє середовище за рахунок випромінювання.
Для інтенсифікації процесу скловаріння піч обладнується системою бурління скломаси, що збільшує продуктивність, позитивно впливає на хімічну і термічну однорідність скломаси. Передбачено звуження частини варильного басейну до протоку, що дозволяє уникнути застійних зон в басейні перед протокою, позитивно впливає на хімічну і термічну однорідність скломаси, що надходить в студочную частину.
Полум’яний простір печі - підвісний. Воно на 300 мм ширше басейну. Стіни полум’яного простору в зоні засипки шихти виконуються двошаровими: бакор 33−250 мм і динас — 250 мм. Заміна динасу на бакор сприяє збільшенню терміну служби печі. Стіни полум’яного простору за переливним порогом виконуються традиційно з динасу товщиною 500 м.
Підвісний склепіння печі виконується з динасу товщиною 400 мм, ізолюється шаром піску товщиною 30 мм і динасові легковаговиком товщиною 130 мм.
Передбачається зменшення глибини басейну в зоні варіння на 300 мм шляхом укладання другого шамотної бруса.
Введення палива здійснюється традиційно в «щічки» пальників через горілочні камені. Це забезпечує ефективне змішання палива з повітрям і повне його згорання.
Розміри вироботочного каналу приймаються конструктивно з умови розміщення двох живильників.
Канальна система вироблення забезпечує якісну підготовку скломаси для рівномірної подачі її в живильники. При цьому є можливість задавати, регулювати і контролювати температуру. Вироботочний канал розділяється по полум’яному простору керамічними шиберами, що дозволяє задавати температуру для різного виду скловиробів, що вимагають різну температуру формувань. На стіні каналу навпроти виходу скломаси з протоки передбачається розміщення пальники з метою коригування температури скломаси, що надходить на формування.
2.3 Теплотехнічний розрахунок
2.3.1 Розрахунок горіння палива
В якості палива застосовується природний газ ГОСТ 5542–87 Північного родовища.
Таблиця 2.2 Склад газоподібного палива Північного родовища
Склад сухого газу,% об. | Теплопровідна здатність кДж/ | ||||||
СН4 | С2Н6 | С3Н8 | N2 | СО2 | |||
97,6 | 0,1 | 0,1 | 1,9 | 0,3 | |||
Вихідні дані складу повітря:
N2 = 79%, О2 = 21%, вологовміст d?? 10 г/кг сухого повітря.
2.3.2 Перерахунок складу палива на робочий
де — вміст вологи в паливі, %
вологість природного газу 1,06%
Сума всіх компонентів робочого палива з вологою становить 100%
2.3.3 Визначення теоретичного витрати повітря
Теоретичний об'єм повітря, необхідний для повного окислення всіх горючих компонентів м палива, розраховується за рівняннями реакцій горіння.
Для газу:
Lo 4,76? 0,01? (2CH4 3,5C2H6 5C3H8),
де 4,76 — коефіцієнт, що враховує кількість обсягів повітря необхідне, щоб ввести один об'єм кисню.
Lo 4,76? 0,01? (2? 96,56 3,5? 0,1 5? 0, 1)
9,33 198 м³ /м3.
2.3.4 Визначення дійсного витрати повітря
Розрахунок дійсного витрати повітря виробляємо, приймаючи коефіцієнт надлишку повітря рівним б = 1,2. Справжнє кількість повітря:
L? Lo, L 1, 2? 9, 33 198 11,2 м³ /м3 .
2.3.5 Обсяг і склад продуктів горіння
Загальний обсяг продуктів горіння складається з обсягів продуктів окислення горючих складових палива, обсягу азоту, що надходить з палива і повітря, і обсягу кисню, що не бере участь в окисленні пального (надходить з надлишкового повітря).
Для газоподібного палива:
VCO2 0,01? (CO2 CH4 2C2H6 3C3H8), м3 /м3;
VCO2 0,01? (0,3 96,56 2? 0,1 3? 0,1) 0,984 м³ /м3;
VH2O 0,01? (2CH4 3C2H6 4C3H8 5C4H10 6C5H12 W 0,16? d? L), м3 /м3,
де d — вологовміст повітря.
м3 /м3
м3 /м3
м3 /м3
м3 /м3
Загальна кількість продуктів горіння при б = 1,2:
м3 /м3
Процентний склад продуктів горіння
2.3.6 Уточнення температури горіння
Тепломісткість продуктів горіння:
кДж/
де — физичне тепло повітря, кДж/
За розрахованим Тепломісткість визначимо за допомогою i-t діаграми (додаток1), приймаючи пірометричний коефіцієнт горіння з = 0,6 дійсну температуру горіння.
кДж/
Дійсна температура горіння палива 1550 єС.
2.3.7 Матеріальний баланс процесу горіння
Масу газів знаходимо множенням обсягу компонента на його щільність.
Таблиця 2.3 Матеріальний баланс процесу горіння
Прихід | кг | Витрата | кг | |
=97,60,717 Повітря: | 69,9 0,136 0,202 2,44 0,59 0,85 334,4 1106,88 14,41 | Нев’язка | 194,54 172,05 1109,64 55,73 — 2,15 | |
1529,81 | 1529,81 | |||
Нев’язка балансу
3. Тепловий баланс варочної частини
Прихід
1.Хімічна теплота згоряння природного газу
кВт
2.Фізична теплота повітря, що йде на горіння
кВт
Загальний тепловий потік буде дорівнювати:
кВт
Витрата
1.На процеси скло утворення
кВт
кг/с
— теоретичний витрата тепла на варіння скла, приймаємо:
Нагрівання скломаси до 1400
Нагрівання продуктів дегазації до 1400
Тепловий ефект реакції склоутворення:
Теплота плавлення скла:
Випаровування вологи шихти:
Разом у витраті 2968 кДж Тепло, внесене шихтою і боєм при 30
Витрата тепла на процес склоутворення складає: 2968−38=2930кДж на 1 кг одержуваної скломаси
=2930кДж/кг скломаси.
3.1 Тепловий потік, що втрачається та відходять газами
кВт
де — температура відхідних газів, приймаємо рівною температурі варіння 1530єС.
— теплоємність димових газів, кДж/, за складом продуктів згоряння при температурі 1530єС:
кДж/
де — об'ємна частка газу в суміші
3.2 Тепловий потік, що витрачається випромінюванням
У вигляді променистого потоку тепло з варочної частини втрачається через отвори в стінах печі: завантажувальний кишеню, влетівши пальників, оглядові вікна і отвори.
3.3 Випромінювання під вліт пальників
де сумарна площа перерізу вліт пальників (2,5% від площі варильного басейну) ,
температура газового середовища варочної частині печі, єС;
середня температура задньої стінки пальників, єС.
Висота вліт D=0,4 м, форма отвору — витягнутий прямокутник, = 0,7, тоді
3.4 Втрати тепла через завантажувальну кишеню
Випромінювання через завантажувальний кишеню відбувається в щілину між аркою завантажувального кишені і верхнім обрізом басейну.
Арка виконана з бакору і многошамота, загальна товщина арки S=1540мм. Висота щілини D=0,2 м, довжина щілини L= 4,5 м.
Розраховуємо площу випромінювання Температура в зоні засипки шихти
єС,
Температура навколишнього середовища єС.
3.5 Втрати тепла випромінюванням через оглядові вікна та отвори
де - сумарна площа перерізу отворів, =0,045 ;
Z — тривалість відкриття (застосовується при розрахунку втрат теплоти випромінюванням через оглядові вікна та отвори для відбору проб), ч, приймаємо 24 ч,
— температура газового середовища варильного басейну, =1803 єС,
— температура навколишнього середовища, єС,
єС,
єС, — температура зовнішнього повітря .
Висота влетів D=0,4 м, форма отворів — витягнутий прямокутник
= 0,7, тоді приймаємо
Сумарні втрати тепла випромінюванням складуть:
3.6 Втрати тепла з вибиваємимі газами через оглядові вікна та отвори
де — кількість газів, відходячих з отвору, м3/с.
де F — сумарна площа перерізу отворів, м2, F=0,045 м2 ,
z — тривалість відкриття отвору, z = 4ч, Hвисота від рівня нульового тиску в печі до середини отвору, H=0,31 м,
— щільність повітря при 40 єС,
- щільність димових газів при 1530 єС,
Підставляючи отримані значення, отримаємо величину втрат тепла з вибивається газами:
3.7 Втрати теплоти від кладки в навколишнє середовище
Дно басейну виконано з наступних матеріалів:
· Бакор ВК-33, товщина слою д=0,2 м, лб = 2,1+0,215*t,
· Шамот ШС-33, товщина слою д=0,2 м, лш = 0,7+0,64*t,
tвн =1200 єС, tнар=250 єС, tокр=50 єС.
Задаємося середніми температурами слойок:
єС, єС.
Для шару матеріалу розраховуємо значення коефіцієнтів теплопровідності матеріалів при прийнятих температурах:
б=2,1+0,215*960=4,164 Вт/м*град, лш =0,7+0,64*605=1,087 Вт/м*град.
Визначаємо термічні опори кожного слою:
Коефіцієнт теплопередачі:
Величина питомого теплого потоку:
=1,67=1586,5 Вт/м2.
Граничні температури шарів:
єС
єС.
Середні температури шарів:
Підраховуємо різницю між прийнятою орієнтовно і знайденої в першому наближенні середньою температурою для кожного шару:
Оскільки різниця по абсолютній величині перевищує 50 єС, то розрахунок повторюємо при отриманих у першому наближенні значеннях середніх температур шарів.
Друге приближення:
tб = 1162 єС ,
tш= 686 єС.
лб=2,1+0,215*1162=4,6 Вт/м*град, лш= 0,7+0,64*686= 1,14 Вт/м*град.
Таким чином, питомий тепловий потік дорівнює g=1672Вт/м2. Аналогічно розраховуємо величину питомого теплового потоку через всі елементи кладки: дно після порога, стіни басейну, стіни полум’яного простору, склепіння печі. Результати розрахунків представлені у таблиці 1.4.
Розраховуємо площі огороджень як середнє арифметичне між внутрішньою та зовнішньою поверхнею:
Приймемо позначення для басейну, полум’яного простору і зводу:
bб — ширина басейну, 5,5 м; - довжина басейну до порога, 8,6 м;
— довжина басейну після порога, 4,3 м;
— ширина полум’яного простору, 14,65 м;
— довжина полум’яного простору, 14,65 м;
уб — товщина стіни басейну з ізоляцією, 0,45 м;
уп.п — товщина стіни полум’яного простору з ізоляцією, 0,5 м;
усв — товщина зводу, 0,56 м;
— ширина завантажувального кишені, 4,5;
— довжина завантажувального кишені, 1,55 м;
h1 — висота брусів басейну до переливного порогу, 1,1 м;
h2 — висота брусів басейну після переливного порогу, 1,4 м;
ѓсв — висота підйому зводу, 0,6 м ;
ѓз.к — висота арки завантажувального кишені, 0,4 м ;
б — центральний кут, при ѓ=1/8 прольоту б=56є;
hп.п — висота полум’яного простору, 2,2 м.
Площа басейну складається з площі до порогу і площі після порогу.
Площа дна басейну до порогу складається з площі варочної частини до порогу и завантажувальну кишені:
Fдна1= Fвар+Fз.к,
Площа стін басейну:
Площа стін полум’яного простору:
Площа поздовжніх стін:
Площа торцевої стіни:
.
Підставляючи отримані значення, отримаємо:
Площа зводу:
де r — радіус зводу, м, який визначається за наступною формулою:
Тоді
Розрахунок площі огородження без ізоляції:
1. Площа дна до порогу
2. Площа дна після порогу
3. Площа стін басейна
4. Площа стін полум’яного простору
5. Площа зводу Розрахунок середньої площі огородження:
Розрахуємо тепловий потік, що втрачається через огородження, за наступною формулою:
Результати розрахунку втрат тепла через кладку печі наведено в табл 1.4
Таблиця 3.4 Втрати тепла
Елемент кладки | Матеріал | Товщина, м | Температура всередині поверхні кладки,?С | Температура на зовнішній поверхні кладки, ?С | Питомий тепловий потік, Вт/м2 | Площа, м2 | Теплові втрати, кВт | |
Дно печі до порогу | Бакор Шамот | 0,2 0,6 | 57,8 | 96,5 | ||||
Дно печі після порогу | Бакор Шамот | 0,2 0,3 | 25,3 | 75,3 | ||||
Стінки варильного басейну | Бакор Шамот Ал.хр.фос | 0,25 0,15 0,05 | 56,8 | 189,5 | ||||
Стінки полум’яного простору | Динас | 0,5 | 53,9 | 270,1 | ||||
Звід печі | Динас Кварцовий пісок Динас-легковаг | 0,4 0,03 0,13 | 91,3 | 311,7 | ||||
Разом | 943,1 | |||||||
3.8 Тепловий потік, що втрачається на нагрів зворотних потоків скломаси
де n — коефіцієнт потоку скломаси, приймаємо n=1,2,
теплоємність скломаси при середній температурі,
1,18 кДж/нм3*град,
t1, t2 — температури прямого та зворотного потоків, єС .
3.9 Невраховані втрати
Приймаються невраховані втрати в сумі 5% від приходу тепла.
кВт.
Витрата палива за рівнянням теплового балансу, визначається м3/ч:
.
Підставляючи знайдене значення витрати палива в статті теплового балансу, складаємо тепловий баланс печі.
Таблиця 3.1 Тепловий баланс скловарної печі
Прихід | Кількість тепла | Витрати | Кількість тепла | |||
кВт | % | кВт | % | |||
1.Тепло горіння палива 2.Тепло підігріву повітря | 7442,41 3711,59 | 66,7 33,3 | 1.На варку 2. Унесення з димовими газами 3. Втрати випромінюванням 4. На нагрівання зворотних потоків 5. Втрати в навколишнє середовище 6.Втрати з відходящими газами 7. Невраховані втрати | 2712,89 6366,36 340,94 21,85 943,1 85,28 553,22 | 24,61 57,74 3,09 0,20 8,56 0,78 5,02 | |
Сума | Сума | 11 023,6 | ||||
Нев’язка балансу 1,2%.
4. Техніко-економічні показники роботи печі
Питомий зйом скломаси з площі варильного басейну:
де площа варочної частини, м2.
Теплова потужність печі:
Питомий витрата тепла на варіння:
Витрата умовного палива:
5. Економія палива
Економія палива за рахунок впровадження комбінованої схеми використання теплоти відходячих газоподібних продуктів скловарної печі.
Комбінована схема передбачає послідовне споживання тепла відхідних газів в рекуператорах і котлах утилізаторах. Зазвичай першою сходинкою є повітронагрівачі. Але зараз є і установки в яких тепло спочатку використовується для отримання пари, а потім — для підігріву повітря. Економія палива по розглянутій схемі
Слід мати на увазі, що в комбінованій схемі у зв’язку з скороченням витрат палива при роботі печі на підігрітому повітрі відповідно зменшується вихід пари в котлі-утилізатори. Тому при визначенні параметра величину необхідно помножити на співвідношення .
Враховуючи це:
— 0,565 частка тепла відхідних газів, використана на підігрів повітря і названа ступенем регенерації
— 0,67 частка
кДж/кг
— 0,67 ККД автономного котла
кДж/кг
=
=7 292 548,95 кВт
Висновки
У результаті виконаних розрахунків показана ефективність використання для варіння технічного скла регенеративної ванної печі з протокою з поперечним напрямком полум’я. Особливістю печі є оформлення студійної частини у вигляді двох каналів з?? можливістю тонкого регулювання температури скломаси, що надходить на формування. У результаті організації використання теплоті газоподібних продуктів для підігріву повітря на горіння, а також подальша регенерація теплоті газів після регенеративного пристрою в котлі утилізаторі загальна економія палива складає: 548,95 кВт Отримане цифрове значення відповідає реальним показником роботи печей подібного типа.
Список литературы
1. Воробьев Х. С., Мазуров Д. Я., Соколов А. Л. Теплотехнологические процессы и аппараты силикатных производств. — М.: Высшая школа, 1965. — 773 с.
2. Волгина Ю. М. Теплотехническое оборудование стекольных заводов. — М.: Стройиздат, 1982. — 276 с.
3. Левченко П. В. Расчеты печей и сушил силикатной промышленности. — М.: Высшая школа, 2007. — 368 с.
4. Мазуров Д. Я. Теплотехническое оборудование заводов вяжущих материалов. — М.: Высшая школа, 1975. — 288 с.
5. Никифорова Н. М. Теплотехника и теплотехническое оборудование предприятий промышленности строительных материалов и изделий. — М.: Высшая школа, 1981. — 270 с.
6. Огнеупоры и огнеупорные изделия. — М.: Издательство стандартов, 1975. — 671 с.
7. Роговой М. И., Кондакова М. Н., Сагановский М. И. Расчеты и задачи по теплотехническому оборудованию предприятий промышленности строительных материалов. — М.: Стройиздат, 1975. — 320 с.
8. Справочник по проектированию цементных заводов / под ред. С. И. Данюшевского. Л.: Стройиздат, 1969. — 240 с.