Композиционные триботехнические матеріали з урахуванням олигомеров сшивающихся смол
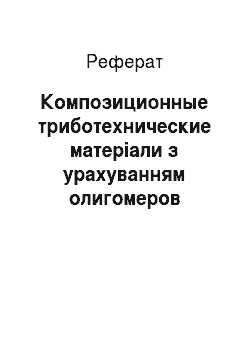
Маятниковий копер працює за принципом Шарпи. Маятник гойдається на осі, обертався в підшипниках, закріплених на вилкообразной чавунної стійці. У частині стійки є опори закріплення зразка. Відстань між опорами можна регулювати відповідно розмірам зразка. На напівкруглої шкалою, розташованої центрично з віссю маятника, є розподілу в відповідність до роботою удару різних маятників. У піднятий… Читати ще >
Композиционные триботехнические матеріали з урахуванням олигомеров сшивающихся смол (реферат, курсова, диплом, контрольна)
Дипломна робота на тему:
Композиційні триботехнические матеріали з урахуванням олигомеров сшивающихся смол.
Виконав Будько Юрій Анатольевич.
Керівник Овчинников Е.В.
Завкафедрою Струк В.А.
Адреса: [email protected].
р. Гродно.
Запровадження 5.
Глава I. Літературний огляд на тему: ''Композиційні триботехнические матеріали з урахуванням сшивающихся смол '' 6.
1.1. Типи композиційних матеріалів 6.
1.2. Самосмазывающие матеріали з урахуванням сшивающихся сполучних 8.
1.3. Вибір типу сшивающегося зв’язувальної виготовлення матеріалу. 11.
1.4. Унікальність кременю 16.
1.4.1. Непізнаний кремінь 16.
1.4.2. Взаємодія кременю з і виявлені у своїй ефекти 17.
1.4.3. Фізико-хімічні й інші властивості кременю 18.
1.4.4. Дослідження термічної стабільності кременю методами термогравиметрии і ДТА-анализа 19.
1.4.5. Застосування активованої кременем води у медичній практиці 21.
Глава II. Методи дослідження 23.
2.1. Метод термічного аналізу 23.
2.2.Определение коефіцієнта тертя і питомої зносу 26.
2.3. Атомно-силовая мікроскопія (АСМ) 27.
2.4. Визначення ударної в’язкості 30.
2.5. Рентгеноструктурный аналіз 31.
Глава III. Дослідження структури та властивостей полімерних матеріалів, модифікованих кремнийсодержащими добавками 33.
3.1. Результати рентгеноструктурного аналізу 33.
3.1.1.Рентгеноструктурный аналіз кременю 33.
3.1.2. Рентгеноструктурный аналіз ПЭНД, модифікованого кремнієм 35.
3.2. Стійкість полімеру до термоокислению (по ДТА і ТG аналізу) 40.
3.3. Ударне в’язкість полімеру 44.
3.4. Триботехнические характеристики 44.
Глава IY. Технологія виготовлення триботехнических матеріалів на основі полімерів 45.
4.1. Принципи створення композиційних матеріалів з урахуванням полімерів 46.
4.2. Виготовлення виробів методом контактного формування 49.
4.3. Виготовлення виробів методами вільного і відцентрового лиття 52.
4.4. Технологічний регламент виготовлення композиційних матеріалів з урахуванням ненасичених поліефірних смол 55.
4.5. Механічна обробка поліефірних матеріалів 57.
Глава Y. Вимоги техніки безпеки під час роботи з полиэфирными смолами і инициирующими добавками 62.
5.1. Збереження поліефірних смол і ініціюючих добавок 62.
5.2. Переробка поліефірних смол 64.
Література 68.
Розвиток сучасного машинобудування вимагає рішення багатьох негараздів у області полімерної матеріалознавства, граючих роль забезпеченні надійності і довговічності машин і творення механізмів, приладів та різних устройств.
Істотне зниження матеріаломісткості виробництва можна забезпечити з допомогою масового застосування ефективних металопродукції, пластичних та інших прогресивних материалов.
Найбільшого використання у машинобудуванні знайшли такі великотоннажні полімери, як полиамиды, полиолефины, фенолформальдегидные і эпоксидные смоли. Потенційні можливості великотоннажних полімерів вивчені досить добре, проте реалізовані в повному обсязі. Особливо перспективне як сполучних композиційних матеріалів (КМ) конструкційного призначення застосування олигомеров низькотемпературного отверждения. У цьому найважливішим застосування ненасичених поліефірних смол (НПЭС), використовуваних як сполучних для склопластиків в суднобудуванні, будівництві, машинобудуванні, як пленкообразующих і компонентів просочувальних і заливальних складів, клеїв, замазок, виготовлення товарів народного потребления.
Метою роботи було вивчення структури та властивостей полімерів, модифікованих кремнієм. Кремній є дешевим матеріалом. З іншого боку, встановлено його унікальне вплив на воду (відбувається активація води). А активована кремнієм вода надає позитивний вплив на організм людини, животных[16]. От і спробували досліджувати вплив кремнію на структуру і фізико-механічні властивості матеріалів. Дослідження проводилися на полиэтилене низький тиск. Скло обраний тому, що якого є технологічнішим і дешевим, проти эпоксидными і фенолформальдегидными смолами.
Глава I. Літературний огляд на тему: ''Композиційні триботехнические матеріали з урахуванням сшивающихся смол ''.
1.1. Типи композиційних материалов.
Композиційні материалы—это матеріали, які з двох чи більше компонентів (окремих волокон чи інших армирующих складових і сполучній їх матриці) і які мають специфічними властивостями, відмінними від сумарних властивостей їхніх складових компонентів. Компоненти композитів не повинні розчинятися чи іншим чином поглинати одне одного. Вони повинні бути добре сумісні. Властивості композиційних матеріалів не можна визначити лише з властивостями компонентів, не враховуючи їх взаимодействия[24].
Композиційні матеріали класифікуються зазвичай з вигляду армирующего наповнювача: волокнисті (армирующим компонентом служать волокнисті структури); шаруваті; наповнені пластики (армирующим компонентом є різні частки). Натомість наповнені пластики може бути розділені на насипні (гомогенні) і кісткові (початкові структури, заповнені сполучною). Армирующие компоненти можуть становити різні волокна, порошки, мікросфери, кристали і «вуса» із органічних, неорганічних, металевих матеріалів чи кераміки. Найбільш поширені такі сполучні, використовувані в армованих пластиках: полиэфиры, феноли, эпоксидные компаунды, силікони, алкиды, меламины, полиамиды, фторуглеродные сполуки, ацетали, поліпропілен, поліетилен і полістирол. Сполучні можна розділити на термопласты (здатні розм’якшуватися і укріпляти за зміни температури) і реактопласты, чи термореактивные смоли (сполучні, у яких при нагріванні відбуваються необоротні структурні і хімічні перетворення). Нині найбільшого поширення отримали термореактивные связующие.
Під час розробки і виготовленні нових композиційних матеріалів, і навіть під час створення конструкцій їх враховувати вплив зовнішніх умов (температура, висока вологість) для цієї матеріали. Необхідно враховуватиме й ряд специфічних властивостей композиційних матеріалів. Так, облік повзучості, що є характерним властивістю багатьох композиційних матеріалів, змушує проектувальників відмовитися від цілого ряду традиційних решений.
Мета створення композиційної матеріалу є об'єднання схожих чи різних компонентів щоб одержати матеріалу з новими заданими властивостями і характеристиками, відмінними від властивостей і характеристик вихідних компонентів. З появою що така матеріалів виникла можливість селективного вибору властивостей композитів, необхідні потреб кожної конкретної області застосування. Композиційні матеріали, вони виявилися і економічніші, і зручними в проектуванні, сьогодні використовуються скрізь — з виробництва іграшок та тенісних ракеток до застосування в космічних апаратах (теплоізоляцію, мікросхеми і др.).
Армирующие компоненти можуть бути включені у складі армованих пластиків зміни властивостей термочи реактопластов. Сучасна промисловість композиційних матеріалів широко варіює різні поєднання армирующих компонентів і сполучних, вибір яких визначається як технічні параметри, і ціною. Армовані пластики найбільш часто використовують у два види: листовий матеріал (типовий приклад такої матеріалу — це папір, просякнута меламинофенольным сполучною, чи стекловолоконные мати, просочені полиэфирным сполучною) і пресовані пластики (найчастіше використовують просочені фенольным або іншими сполучною мінеральні, бавовняні та інші волокна). Більшість властивостей отриманих композиційних матеріалів виявляється вищими, ніж властивості вихідних компонентів. До композитам слід також вважати і різні матеріали, конструкционное призначення яких те, як і одного з компонентів. Такі матеріалами є, наприклад, покриті поливиниловой плівкою вироби, використовувані в летальних апаратах; металопластикові обличкування і т.д.
Нині найпоширенішими компонентами при створенні матеріалів є скляні, полиамидные, азбестові волокна, папір (целлюлозные волокна), бавовну, сизаль, джут та інші натуральні волокна. Дедалі більше місця в технології виробництва композитів займають такі матеріали, як вуглецеві, графітові, борні, сталеві волокна і «вуса» (дуже короткі армирующие волокна, зазвичай кристалічні). Вибір тієї чи іншої армирующего наповнювача визначається ціною, складом і технологічними вимогами, що висуваються до властивостями армованих пластиков[2,4].
1.2. Самосмазывающие матеріали з урахуванням сшивающихся связующих.
Для виготовлення підшипників ковзання тяжелонагруженных і високошвидкісних вузлів тертя найбільш використовуваними є сшивающие полімерні сполучні - фенолформальдегидные, эпоксидные та інші смоли. У тому числі особливо цікаві фенолформальдегидные смоли, мають розвинену сировинну базу, які мають високими питомими фізико-механічними характеристиками. За підсумками цього зв’язувальної створено групу композиційних матеріалів та покрить антифрикционного призначення, знайшли широке використання у машиностроении[9].
Як функціональних добавок, що поліпшують зносостійкість і знижують коефіцієнт тертя, в фенолформальдегидные смоли вводять графіт, дисульфид молібдену, фторопласт-4, порошки металів і оксидів, що утворюють на поверхнях тертя стійку плівку перенесення. Ефективним методом підвищення фрикционных характеристик для композицій подібного типу є реалізація термоактивационного ефекту. Суть ефекту залежить від освіті у зоні тертя багатокомпонентної плівки, що з сухий мастила і металлополимера, який генерується у процесі тертя, завдяки розкладанню під впливом локальних температур введеній у склад композиції металлосодержащей солі. Розширення нагрузочно-скоростного діапазону реалізації термоактивационного ефекту вдається досягти при використанні спеціальних методів обробки робочої поверхні металевого валу. Так, фосфатирование валу зі сталі 45 протягом 3−15 хв дозволяє знизити нагрузочно-скоростные режими тертя, що зумовлюють освіту металлополимерной антифрикционной плівки, за одночасного зниженні коефіцієнта тертя. Освіта фосфатного шару лежить на поверхні валу сприяє закріплення частинок мастильних компонентів, які у матеріалі підшипника, збільшує час перебування в зоні тертя і тих самим забезпечує стабільну роботу вузла трения.
Дедалі більше поширення машинобудуванні отримують композиційні матеріали з урахуванням сшивающихся сполучних холодного отверждения. Переваги таких матеріалів: висока технологічність виготовлення й переробки, зокрема можливість використання в польових і ремонтних умовах сприяє поліпшенню їхнього широкому застосуванню. Серед таких композитів нині найбільш відомі матеріали з урахуванням эпоксидных смол та його різних модификаций.
Останніми роками увагу привертають ненасичені поліефірні смоли. Дані сполучні мають нижчу вартість проти эпоксидными, високі експлуатаційні показники. Істотним вадами поліефірних смол є низька ударна в’язкість, високі усадка і коефіцієнт тертя. Традиційні сухі мастила не забезпечують значного поліпшення фрикционных характеристик поліефірних смол. Найбільший ефект зниження коефіцієнта тертя досягнуть під час введення компонентів, формують у зоні тертя розділювальні верстви, наприклад, легкоплавких поліолефінів. Під дією температурах зоні фрикційного контакту лежить на поверхні полімерної підшипника формується плівка розплаву полиолефина, яка знижує адгезионное взаємодія полиэфирного зв’язувальної з металевою поверхностью.
Однією із визначальних достоїнств поліефірних сполучних проти матеріалами аналогічного класу є можливість регулювання часу перебування у частково зшитому (резиноподобном) стані. Композиційний матеріал, що у резиноподобном стані, то, можливо легко трансформований у вироби складної конфігурації без використання складної технологічної оснастки. Достатня тривалість гумоподібної стану — від десятків хвилин за кілька годин — дозволяє формувати великогабаритні вироби з великою масою. Використовуючи цей ефект, можна формувати багатошарові вироби, кожен шар яких має специфічними властивостями. Особливу увагу цю рису розроблених композицій набуває під час виготовлення великогабаритних підшипників скольжения.
Розроблено технологічна оснащення і технологічний регламент, дозволяють застосовувати композиційні матеріали з урахуванням ненасичених поліефірних смол ремонту та відновлення техніки в польових условиях.
Для вузлів непорозуміння з підвищеними вимогами за надійністю і довговічності розроблений матеріал Хтиболон. Композиція включає термореактивное сполучне (эпоксидное, фенолформальдегидное, фурановое чи їх суміші) і армирующий заповнювач як односпрямованих чи хаотично розташованих вуглецевих волокон чи вуглецевих тканин. Додатково в склад запроваджені тверді мастила, порошки полімерів, металів, базальтові, скляні, металеві волокна чи ткани[3,8].
1.3. Вибір типу сшивающегося зв’язувальної виготовлення материала.
Під час розробки складу сшивающегося зв’язувальної з урахуванням поліефірних смол необхідно виходити з таких критериев:
1. Сполучне повинен мати високу життєздатність при введеної отверждающей системе;
2. Сполучне має мати оптимальної в’язкістю задля забезпечення хорошого заповнення литьевой формы.
3. Реакційна здатність смоли має перевищувати оптимального значення, з єдиною метою мінімізації температури саморазогрева у процесі отверждения.
Для управління технологічними характеристиками зв’язувальної з урахуванням поліефірних смол використовують різні прийоми. До складу зв’язувальної вводять добавки, дозволяють змінювати в’язкість системи залежно від механічного впливу. Як таких добавок застосовують оксид кремнію, бентоніт, заміщені сечовини, сополимеры вінілхлориду, винилацетата і т.п.
Крім таких добавок у складі зв’язувальної вводять загущающие добавкиоксиди, гидроксиды і солі двовалентних металів. Процес загущения має три стадії: стадію низького загущающего ефекту, стадію різкого зростання в’язкості і стадію стабільної вязкости.
По швидкості наростання в’язкості при загущении можна назвати ряд: MgO>Ca (OH)>CaO>Mg (OH), а, по граничною в’язкості ряд: MgO>CaO>Ca (OH)>Mg (OH). Становище загусників у низці визначається маркою смолы.
На процес хімічного загущения сшивающегося з урахуванням поліефірних смол істотно впливає низка чинників: кількість загущающей добавки, дисперсність, присутність активаторів, інгібіторів чи регуляторів структурування, будівлі ненасыщенного полиэфира, зміст карбоксильных груп, рівномірність розподілу добавки в объеме.
Однією з основних критеріїв вибору зв’язувальної є його життєздатність, тобто. тривалість перебування смоли в вязкотекучем стані після введення яка ініціює системи. Момент переходу композицій в текучого (желеобразное) стан називається желатинизацией чи гелеобразованием. Період із часу введення яка ініціює системи до гелеобразования називається часом гелеобразования.
Час гелеобразования залежить від природи й концентрації компонентів отверждающей системи, обсягу (маси) приготовленого зв’язувальної, природи й концентрації інгібіторів, природи й кількості наповнювача, впливу теплових і електричних полів, випромінювань, вібрацій тощо. Після гелеобразования починається стадія структурування, протягом якого композиція має частково зшиту структуру, що забезпечує високу деформативність. Такий стан композиції називають резиноподобным, а його досягнення — часом гумоподібної состояния.
Управляючи параметрами желатинезации і гумоподібної стану, вдається регулювати технологічні і прочностные характеристики композиций.
Швидкість зшивки смоли залежить від оптимального складу перекису, її кількості і температуры.
Для отверждения смоли використовують 0,5−3% ініціатора чи суміші инициаторов.
Найбільше використання у практиці отримали инициирующие системи отверждения, містять перекисный ініціатор і прискорювач, як якого використовують стирольные розчини нафтената кобальту, розчини диметиланилина в стиролі і т.п.
Для двухкомпонентных отверждающих систем існує область температур переробки, у яких можна досягти оптимальних характеристик які зшили сполучних. Наприклад, системі перекис бензолу + диметиланилин вона становить 15−30 з, системі перекис метилэтилкетона + нафтенат кобальту — 20−40 з, гидроперекись трет-бутила + нафтенат кобальту — 60−70 с.
Підвищення змісту іонів металу (кобальту) в нафтенате призводить до збільшення його активности.
До складу отверждающей системи та композиції вводять соускорители, які забезпечують високу швидкість отверждения навіть за негативних температурах.
Збільшення швидкості отверждения можна досягти запровадження у склад зв’язувальної солей амонію органічних кислот, ацетилацетонов металів V, Al, Mo, Mn, Fe, Cr, галогенних солей міді т.п.
При переробці сшивающихся смол необхідно регулювати швидкість отверждения, знижуючи її як у стадії гелеобразования з метою підвищення технологічної життєздатності, і на стадії гумоподібної стану із метою зниження экзотермического ефекту отверждения. Тому до складу отверждающей системи вводять уповільнювачі отверждения. Як інгібіторів використовують воду, спирти і т.п.
У ідеальному разі інгібітор забезпечує тривале збереження розчинів полиэфиров в мономерах і необхідну їхнє гелеобразования, але з повинен уповільнювати отверждение і мати негативний вплив на властивості отвержденных продуктов.
Ефективної яка ініціює системою, увеличивающей час гумоподібної стану до 60 хв., є комбінація перекисного і гидроперекисного ініціатора, прискорювача з гидрохиноном і дифенилпропаном. Композиції з тривалим резиноподобным станом (протягом кількадобового) отримують, використовуючи у складі яка ініціює системи похідні ферроценов.
Істотною проблемою є збільшення фізико-механічних і експлуатаційних властивостей поліефірних сполучних. У чистому вигляді сполучні на основі поліефірних смол застосовуються дуже рідко. До складу сполучних для підвищення службових характеристик вводять функціональні інгредієнти, що знижують коефіцієнт тертя, зменшують знос, підвищують міцність, теплостойкость, ударну в’язкість і т.п.
Специфіка композицій з урахуванням поліефірних смол полягає у необхідності шляхом введення наповнювачів і модифікаторів одночасного управління технологічними і експлуатаційними характеристиками, наприклад, технологічної живучістю, часом гумоподібної стану, міцністю, теплостойкостью.
Найважливішим недоліком зв’язувальної з урахуванням поліефірних смол є нестабільність технологічних характеристик і, усадки, яка сягає 6−9%. Усадка зв’язувальної переважно пов’язані з кількістю прореагировавших подвійних зв’язків насиченого полиэфира і мономера.
Внесок стиролу в усадку сягає 17%, ненасыщенного полиэфира — 3%. У загальну усадку значний внесок вносить і термоусадка у процесі охолодження. Традиційне регулювання усадки шляхом введення наповнювачів для композицій з урахуванням поліефірних смол малоэффективно.
Для зниження усадки великий ефект дають дисперсні полімери: поліетилен, полістирол, полиметилметакрилат. Усі наповнювачі в малоусадочных композиціях ділять на виборах 4 класса:
1. нерозчинні при кімнатної температурі в стиролі, але набухающие у ньому за умов формования;
2. що утворюють диспергированную фазу як эмульсии;
3. містять крім термопласта і олигомера ненасичений полиэфир;
4. повністю растворяющиеся в смоле.
Для зниження усадки у складі сполучних з урахуванням поліефірних смол вводять эластомеры, поліетилен, поліпропілен, стеарат цинку, перманганат калію і глинозем, крейда разом із полистиролом і поливинилацетатом.
Ефективним методом зниження усадки є одночасне запровадження дисперсного поліетилену і кремнійорганічних рідин. На підвищення зносостійкості композиції з урахуванням поліефірних смол використовують різноманітні наповнювачі і модифікатори: графіт, дисульфид молібдену, фторопласт-4, порошки металів та його оксидів. Проте традиційні наповнювачі знижують коефіцієнт тертя і підвищують зносостійкість матеріалу лише за великих ступенях наповнення (20−40 мас%), що дуже знижує їх технологічні і прочностные характеристики. Ефективнішим прийомом виявляється введення до складу композицій легкоплавкого полімеру у поєднанні з сухий змазкою і мастильним маслом.
Хороший ефект характеризується запровадження у сшивающее з урахуванням поліефірних смол марки ПН-1 стеклоткани і залізного порошку. На підвищення зносостійкості в сшивающее рекомендовано вводити поліпропіленові і полиамидные волокна. Матеріал із хорошою зносостійкості отримують при модифицировании смоли карбонатом кальцію, стекловолокном і политетрафторэтиленом. Зносостійкість сполучних підвищує волокно з поливинилового спирта.
Абразивостойкие матеріали отримують при наповненні зв’язувальної з урахуванням поліефірних смол порошкообразным поліетиленом і стекловолокнистым наповнювачем [1,21,22].
Выводы:
1. Найбільш ефективною сполучною і розробити абразивосодержащего матеріалу є ненасичені поліефірні смоли. 2. Технологічні переваги ненасичених поліефірних смол проти інші види сшивающихся сполучних полягають у следующем:
5. можливість регулювання технологічної живучести:
6. можливість формування виробів методом вільної заливки;
7. можливість створення композицій з малої регульованої усадкой. 3. Експлуатаційні переваги ненасичених поліефірних смол залежить від следующем:
8. можливість управління прочностными і триботехническими властивостями в широких пределах;
9. можливість виготовлення виробів складної геометричній форми і великих розмірів. 4. Під час створення композиційної матеріалу в обробці металевих поверхонь необходимо:
10. підібрати отверждающую систему для регулювання часу гелеобразования і гумоподібної состояния;
11. підібрати абразивний заповнювач з максимальною здатністю абразивного дії з відношення до металлам;
12. розробити склад зі стабільною і низьким значенням усадки.
1.4. Унікальність кремня.
1.4.1. Непізнаний кремень.
Чимало й видано багато спільних зусиль знадобиться ученим різних напрямів науки для пізнання кременю — каменю, який своїми унікальними властивостями поклав початок людської цивілізації. Не одне тисячоліття тривав кам’яний століття, протягом усього його кремінь залишався неперевершеним матеріалом виготовлення знарядь праці і, наконечників для копій і стріл тощо. Пізніші цивілізації продовжували використовувати кремінь для поливи, силікатних емалей, шліфувальних порошків та інших. Більше чотирьох століть кремінь справно служив для поджига порохових зарядів в гарматах і рушницях. Кремнієві жорна для помелу зерна дозволяли отримувати борошно з чудовими выпечными і смаковими свойствами[16].
Наприкінці 1970;х років ХХ століття А. Д. Малярчиков виявив, що з природному воздухообмене, температурі довкілля вище +40С, вода за хорошого контакту з кременем набуває несподівані властивості і може зберігати їх невизначено довгий час (з кременем чи ні нього) участь у закритому посудині. З іншого боку, за ті самі умовах перетворюється на протягом кількадобового біологічно заселена вода відновлює свої питні свойства.
1.4.2. Взаємодія кременю з і виявлені у своїй эффекты.
11 Червня 1984 року у посудину зі свіжої водогінної водою було вміщено шматочок кременю. Одночасно інший посудину наповнювався той самий водогінної водою (контрольної). Судини зберігалися лише у й тією самою кімнаті, але оптично ізольовані друг від друга.
Через 9 років тому після початку експерименту проведено порівняння якості активованої кременем води (АКВ) і контрольної. АКВ продовжує залишатися виключно прозорою, не цвіте, немає запаху, посудину чистий. Контрольна вода зацвіла, протухнула, а стінки судини вкрилися великим кількістю водоростей. З допомогою універсальної індикаторної папери визначено кислотність АКВ і контрольної води. Різниці виявлено був, в обох випадках рН=7.
Науковий практичним інтерес представляє дослідження поведінки АКВ в капілярних системах, як яких вибиралися зразки у вигляді циліндра заввишки 20 мм, одержані із однієї й тієї самого кореня дерева і висушені в кімнатних умовах перетворюється на течениие8 років. Пропитывающими рідинами служили дистильована вода, активована кременем вода протягом п’яти місяців, і контрольна вода (дистильована неактивированная).
Встановлено значне (в 1,5 — 2,5 разу) збільшення швидкості підйому АКВ проти неактивованої водою. Перший стример на поверхні зразка з’явився через 4 хв від початку просочення кремінної водою і лише крізь 10 хв від початку просочення контрольної водою. Масове поява стримеров спостерігалося через 7 хв від початку просочення АКВ і лише крізь 17 хв від початку просочення контрольної водою, у своїй величина електричного сигналу АКВ саме його стабілізації в 1,2 разу перевищувала аналогічний сигнал контрольної воды.
Проведено порівняння величин коефіцієнта поверхового натягу і косинуса кута змочування АКВ і контрольної воды.
Знайдено, що твір величини коефіцієнта поверхового натягу на косинус кута змочування для АКВ і контрольної води відповідно становить 0,11 і 0,05 Н/м, тобто. обмірювані величини відрізняються теж приблизно двічі. Отже, ефект підйому активованої кременем води, можна пояснити впливом кременю на капиллярноповерхневі властивості воды.
1.4.3. Фізико-хімічні й інші властивості кремня.
У складі кременів виявлено зміст близько 20 хімічних елементів (магнію, кальцію, фосфору, стронцію, заліза, марганцю, міді, цинку, кобальту, нікелю, хрому, свинцю, алюмінію, бору, кадмію, молібдену, титану, кремнію, олова, барію) в концентратах екстрактів кременів чорного сірого і червоного, у тому настоях на дистильованої і водогінної воде.
Кремень червоний відрізняється з інших досліджених мінеральних утворень тим, що у складі помітному кількості присутні органічні ненасичені сполуки, мають характерне флюорисцентное свечение.
Концентрації практично всіх основних домішок в кремнях різного віку і її забарвлення дуже близькі, водночас, залежно від його віку різняться за змістом кальцію, калію, алюмінію і заліза. Домішок важких елементів в кремниях різного віку, кольору, із різних родовищ виявлено не было.
Зареєстровано ефект зменшення вихідного кількості барію і кальцію в водогінної воді у її активировании кременями відзначених різновидів часом більш як на 200%.
Досліджені можливості стабілізації (подовження термінів придатності) широко що застосовуються у медичній практиці препаратів групи біогенних стимуляторів шляхом їх приготування на активованої кременями воді. Виявлено помітне стабілізуюче дію активованої кременями води складу препарату «Екстракт алоэ».
1.4.4. Дослідження термічної стабільності кременю методами термогравиметрии і ДТА-анализа.
Метод термічного аналізу грунтується на реєстрації зміни маси зразка залежно від температури. Експериментально отримана крива залежності зміни маси від температури характеризує термостабильность і склад досліджуваного образца[23,27].
Для визначення температурної стабільності кременю були підготовлені три проби зразків з розмірами частинок 3,0−3,5 мм; 1,0−2,0 мм (1,0 мм відповідно. Нагрівання зразків проведено за програмі зі швидкістю 50С/мин в інтервалі температур 20 — 800 градусів. У процесі експерименту реєструвалися три криві: зміни температури (Т), маси (ТG) і теплового потоку. По експериментальним даним розраховувалися швидкість зміни є і зміни энтальпии.
ДТА-исследования кременю показали, що фізичних перетворень чи хімічних реакцій, що з зміною энтальпии, які супроводжуються помітним поглинанням чи виділенням тепла, в досліджуваному інтервалі температур немає. Втім, можна пояснити і сильним размытием процесу розкладання фракцій в кремне.
Результати термічного аналізу наведені у таблиці № 1.
Таблиця № 1.
|Температура, градусів |Втрати маси (TG), % | | |3,0 — 3,5 мм |1,2 — 2,0 мм |(1,0 мм | |140 |0,000 |-0,174 |-0,050 | |190 |0,000 |-0,141 |-0,012 | |234 |0,000 |-0,113 |0,000 | |280 |0,000 |-0,113 |0,000 | |322 |-0,019 |-0,084 |0,000 | |365 |-0,060 |-0,100 |0,034 | |407 |-0,171 |-0,194 |0,166 | |450 |-0,284 |-0,340 |0,316 | |490 |-0,382 |-0,460 |0,446 | |534 |-0,483 |-0,562 |0,562 | |574 |-0,502 |-0,645 |0,624 | |616 |-0,537 |-0,641 |0,647 | |660 |-0,521 |-0,694 |0,660 | |700 |-0,531 |-0,709 |0,744 | |741 |-0,548 |0,710 |0,745 | |800 |-0,607 |-0,720 |0,746 |.
Аналіз даних втрат маси досліджуваних проб показує, що втрати маси лежать у межах 0,6 — 0,8%, у своїй, що менше розміри частинок, то більше вписувалося для заданої температури втрата маси, що пов’язані з більшої поверхнею частиц.
Помітна втрата маси зразку спостерігається, починаючи з 3000С. Інтервал розкладання становить близько градусів. Це було пов’язано ні з широким діапазоном розкладання якихось фракцій, що у кремені, а, скоріш лише від повільними диффузионными процесами, які визначають вихід летючих фракцій від щирого частинок кремня.
1.4.5. Застосування активованої кременем води у медичній практике.
Про несподіваних властивості кременю, судячи з усього, у Білорусі знали з найдавніших часів. Можливо, стихійно користувалися люди і води, соприкасавшейся з кременем. М. М. Синявский після застосування АКВ як сечогінного кошти, став застосовувати її на лікування гіпертонічної хвороби. Застосовував новогрудский кремінь чорного кольору: наполягав при нормальних умов протягом три доби у скляній банку, прикритої марлею. До кожного конкретної людини прийом АКВ залежить потреби в питво. У середньому Синявський рекомендує чверть склянки після їжі. Застосування АКВ дозволило йому вилікувати сотні хворих, котрі страждали на гіпертонію. Останніми роками АКВ застосовувалася М. М. Синявским на лікування трофічних виразок, опіків, желчеі сечокам’яної хвороби, запальних процесів сечостатевої системи та т.д.
Гнійне отделяемое з трофічних виразок зазвичай містить багату кокковую флору. Багаторічні трофічні виразки зі смородом містять паличку синьо-зеленого гною. При перев’язці (уранці й увечері) така виразкова поверхню покривається стерильною марлевою серветкою, рясно змоченою АКВ. При подсыхании (між перев’язками) серветка додатково змочується АКВ. Спостереження показали, що за 2−3 діб сморід зникає, і виразкова поверхню очищається від некротических тканин, паличка синьо-зеленого гною також зникає. У цьому різко зменшується кокковая флора, і швидко з’являються рожеві грануляції, що поступово заповнюють раневой дефект з наступним заживлением язвы.
Синявским встановлено, що у п’ятий-шостий день прийому АКВ (6−8 разів у добу) в хворих з багаторічними трофічними виразками нижніх кінцівок зростає кількість Ті В-лимфоцитов. І це говорить про здібності АКВ відновлювати втрачений чи ослаблений імунітет. Крім цього, АКВ знижує холестерин крові, особливо в ожирении.
Можна рекомендувати активовану кременем воду як після гоління, запобігання зморщок, загоєння ран тощо. Миття голови АКВ зміцнює волосяні сумки, і навіть сприяє отрастанию волос.
По глибоке переконання М. М. Синявского, АКВ перешкоджає розвитку аденоми і імпотенції чоловіки, і навіть попереджає безплідність у женщин.
При зовнішніх запальних процесах АКВ рекомендується як примочок, компресів, змочених тампонів (зовнішнє слуховий прохід, пряма кишка, влагалище).
Рекомендується також АКВ для полоскання ротовій порожнині, слизової носа, зрошення гортані. Вона знімає запальним процесам, зміцнює тканини і кровоносні сосуды.
Оскільки АКВ задовольняє всі вимоги Держстандарту на питну воду, а також має різнобічними лечебно-оздоровительными діями, доцільно її використання у лікувальних учреждениях.
Глава II. Методи исследования.
2.1. Метод термічного анализа.
Термоаналитические методи служать на дослідження фізичних і хімічних перетворень в речовинах чи системах, які протікають під впливом тепла. Хімічні чи фізичні процеси, зміна стану речовини чи фази (плавлення, кристалізація, випаровування, горіння тощо.) супроводжується зміною внутрішнього теплосодержания системи. Процеси, що проходять із виділенням тепла, називаються экзотермическими, і з поглинанням теплаэндотермическими. Фізико-хімічні процеси часто супроводжуються зміною маси, що може бути визначено з допомогою термогравиметрического метода. 13] Сутність методу дифференциально-термического аналізу (ДТА) залежить від вимірі микротоков термопари, вміщеній в пробірку, яка нагріває з певної швидкістю. Термогравиметрия (TG) полягає в методі безперервного зважування досліджуваного речовини у процесі зміни температури. Метод диференціальної термогравиметрии (ДТG) грунтується на вимірі швидкості зміни маси навішення досліджуваного речовини при даної температурі. Поєднання методів ДТА, ТG, ДТG дозволяє визначити напрям і величину зміни теплового ефекту реакції (энтальпии), плинною в речовині під впливом температури, визначити характер структурних і фазових перетворень в речовині, визначити зміна маси речовини в залежність від температури, і навіть температури перетворень в речовині. Усі перелічені методи суміщені в дериватографе Q-1500. Принцип дії дериватографа Q-1500: Дериватографкомплексне термоаналитическое пристрій. Дериватограф Q- 1500 дає змогу виробляти вимірювати температуру (Т), зміна ваги (ТG), швидкості зміни ваги (ДТG) і журналістам зміну змісту теплоти (ДТА) досліджуваного речовини залежно від часу у діапазоні температур від 20 до 1500 З у звичайному режимі експлуатації і по 1000 З для квазиизометрических і изобарных досліджень. У окремих випадках склад довкілля істотно впливає на кінетику розкладання речовини. Тому важливо встановити, який вплив на процес розкладання надає власна газова атмосфера, що настає під час розпаду. І тому процес розкладання речовини проводять у спеціальному лабиринтном тиглі, який перешкоджає видалення газоподібних продуктів, проте зберігає практично 100% середу продуктів розпаду. такий режим експерименту називається квазиизобарныим. При квазиизотермическом режимі роботи у стадії експерименту температура зразка зростає зі великий швидкістю (2−5 С/мин), та був, починаючи з розпаду речовини, підтримується така температура, при якої розкладання приміром із постійної, дуже малій швидкістю. Прилад Q-1500 складається з п’ятьох основних блоков:
— блок термовесов;
— здвоєна піч з рамой;
— шестиканальний регістр з рамой;
— тиристорный блок управління регулювання программ;
— тиристорного блоку харчування регулювання программ.
Однією за складних завдань кінетики хімічних процесів є розрахунок енергії активації, тобто визначення надлишкового кількості енергії, яким має мати молекула в останній момент зіткнення, щоб почалася хімічна реакція. Для розрахунку енергії активації реакції використовують методи ДТА, ТG, ДТG. Енергія активації за дзвоновидною кривою ДТА то, можливо розрахована з уравнения:
Ln?t = з — E/(RT); (1) де? tзміна температури, відповідне глибині піка ДТА при заданої температурі вираженого в мм; Єенергія активації кДж/моль, тобто енергія яку потрібно повідомити молекулі, щоб він вступив у реакцію; Rуніверсальна газова стала Дж/мольК; зконстанта. По кривою ТG-анализа енергію активації расчитывают:
Lnm-2LnT=А-Е/RT; (2) де mзменшення маси речовини, визначається по ТG-кривой, в % чи мг;
А-постоянная величина. З кривою ДТG-анализа енергію можна визначити з рівняння: cV=B-E/RT; (3) де Vшвидкість зменшення маси речовини, мг/мин чи мг/ С;
Уконстанта;
Табсолютна температура, К.
Мал.1. Принципова схема дериватографа Q-1500 1- керамічна трубка; 2- власник проб; 3- піч; 4- включатель;
5,10,12- підсилювачі; 6- електромагніт; 7- котушка; 8- ваги; 9- диференціальний перетворювач сигналу; 11- регестрирующее устройство.
2.2.Определение коефіцієнта тертя і питомої износа.
Досліди проводилися на трибометре ПД-1А.
Він призначений випробування різних матеріалів (металів, сплавів, жорстких полімерів і кераміки) на тертя і износ.
Принцип дії устрою залежить від истирании пари тертя, що з нерухомого циліндричного зразка — пальця, прижимаемого торцевій поверхнею до площині обертового диска.
Пристрій трибометра.
Структурна схема трибометра містить випробувальний блок і пульт управління, щоб забезпечити можливість оцінки фрикционных властивостей блокових зразків та покрить широтою діапазону навантажень і скоростей.
Випробувальний блок включає у собі такі функціональні узлы:
1. Власники образцов;
2. Блок датчиків виміру характеристик і параметрів трения;
3. Прихід обертання нижнього образца;
4. Механізм навантаження образцов.
Зазначені вузли монтуються на загальної станині. Конструкція випробувального блоку забезпечує надійну виброизоляцию машини під час роботи за умов інтенсивних динамічних нагрузок.
Випробувальний блок електрично пов’язані з пультом управління, що містить :
1. Блок управління швидкістю обертання двигателя.
2. Вимірювач числа оберту і швидкості обертання вала.
3. Систему виміру сили трения.
4. Систему виміру лінійного износа.
5. Аналого-цифровий преобразователь.
6. Блок захисту від перегрузок.
2.3. Атомно-силовая мікроскопія (АСМ).
Метод АСМ застосовується для виміру топографії поверхні твердих тіл в нанометровом діапазоні та політичного аналізу особливостей її будівлі. Зображення поверхні в АСМ отримують з допомогою сканування зразка в горизонтальній площині з допомогою голки з радіусом кривизни шпичаки порядку десятков-сотен нанометрів, укріпленої на консолі (що хитається) з відомою жорсткістю. При скануванні вимірюється відхилення (зрушення резонансної частоти коливань) консолі під впливом сил між голкою і поверхнею. Отже, при реєстрації сил взаємодії (градієнта сил) проводять картографування поверхности. 15] Аналітичний вузол сканування АСМ є відкриту конструкцію до роботи надворі із гарним доступом за умови встановлення зразка і зміні сканирующего зонда. Огляд місця підвода шпичаки зонда до досліджуваної поверхні може забезпечуватися використанням длиннофокусного оптичного мікроскопа. Аналітичний зонд АСМ є ‘Г'-образную консольно закріплену балку з вістрям (радіус заокруглення -0,1мкм) на вільному кінці, виготовлену з вольфрамової дроту методом электро-химического травлення і полірування. Другим, довшим кінцем, бапка пов’язані з биморфным пьезокерамическим елементом (БД), який за подачі осцилюючих напруг від генератора частот (ГЧ) наводить їх у коливання зі своєю частотою (30−100кГц). Аби наблизитися зонда до зразка (Про) на відстань порядку кількох нанометрів, амплітуда коливань балки змінюється під впливом молекулярних сил (відштовхування) виникаючих між вістрям і поверхнею зразка. Рис. 2. Принципова схема АСМ.
Ззонд;
БМбиморфный элемент;
ГЧгенератор частот;
Прообразец;
ЛІлюминисцентный источник;
ВВоптичне волокно;
БЭблок электроники;
ПКперсональний компьютер;
ПД1,2,3,4- пьезоэлементы двигуна. Зміна амплітуди коливань зонда детектируется оптичної системою, в якої пучок світла від ЛІ йдучи ВВ, відбивається, по-перше, з його відколу край волокна подведенном з допомогою регульованого кронштейна на відстань 10мкм до? п'яті' зонда і, по-друге, від полірованого ділянки на поверхні балки. Різниця що проглядали оптичних сигналів реєструється і обробляється блоком електроніки (БЭ). По змін різниці сигналів судять про зміну амплітуди коливань зонда і, отже, про зміні відстані між сканирующим вістрям і досліджуваної поверхнею. З допомогою системи зворотний зв’язок з урахуванням управляючого комп’ютера (ПК) і блоку електроніки (БЭ) подаються відповідні управляючі напруги на Zділянку, пьезоэлементы двигуна (ПД). ПД, подовжуючи чи укорачиваясь, роблять переміщення шпичаки (чи зразка) вздовж осі Z і тим самим підтримують постійним відстань між вістрям зонда і поверхнею зразка під час сканування. Системи детектування і переміщень забезпечують чутливість по осі Z 0,1−0,2 нм, у площині ХОУдозвіл до 5−10 нм. Сканування шпичаки зонда над вимірюваною поверхнею здійснюється пьезодержателем ПД1. І тому відповідні квантові напруги на ХУділянки трубчастого елемента подають, що зумовлює їх вигину щодо осей ОХ і ЗУ і, отже, до скануванню у площині ХОУ. У залежність від стану системи цифровий процесор управляє становищем зонда. Комп’ютер реалізує растрову разветку пьезодвигателя. За цих вузлах растрової сітки проводять виміри положень. Дані накопичуються в ОЗУ компьтера.
Сканування. Підготовлений для досліджень на САМ зразок закріплюють на платформі власника в аналітичному вузлі в такий спосіб, що гаданий ділянку сканування розташовується під вістрям зонда. платформа встановлюється на направляючі. Після цього, здійснюється підвід зразка, вибір режиму і виробляється сканирование.
Обробка даних. Через війну експериментальних досліджень було отримані САМзображення, обробка виготовляють комп’ютері з допомогою оригінальних програм. Первинна обробка включає обчислення загальної площині нахилу зображення фільтрацію шумових компонентів. Потім методом многократной повторної фільтрації знаходять довгохвильові складові рельєфу. Для отриманих зображень виробляється статистичний аналіз висот топографії, кутів нахилу рельєфу і ориентационных кутів. З іншого боку, виконуються профільні поєднання зображень, які потім обробляються по спеціальної програмі визначення параметрів шероховатости.
2.4. Визначення ударної вязкости.
Ударне в’язкість у цій роботі визначалася на маятниковом копре RM- 201. Маятниковый копер призначений випробування пластмас на опір вигину під час удару, з їхньої довговічність і вязкость.
Маятниковий копер працює за принципом Шарпи. Маятник гойдається на осі, обертався в підшипниках, закріплених на вилкообразной чавунної стійці. У частині стійки є опори закріплення зразка. Відстань між опорами можна регулювати відповідно розмірам зразка. На напівкруглої шкалою, розташованої центрично з віссю маятника, є розподілу в відповідність до роботою удару різних маятників. У піднятий становищі маятник фіксують собачкою. Витягши собачку і вивільнивши цим маятник, нагромадження у ньому кінетична енергія звільняється і маятник у своїй найнижчому становищі вдаряє на встановлений на опорах зразок і ламає його. Частина енергії витратиться на руйнація зразка; що залишилося в маятник кінетична енергія змушує маятник злітати у протилежний бік. Виходить межі найнижчого становища маятник, зламавши зразок при допомоги ручки, насадженої з його вісь, переміщає зі свого вихідного становища фрикционную стрілку, що описує величину злету маятника. Шкала отградуирована з такою розрахунком, що дозволяє безпосередній відлік енергії, витраченої на излом.
2.5. Рентгеноструктурный анализ.
Рентгенівські дифрактометрыприлади, використовують ионизационные чи инсциляторные методи реєстрації дифракційних максимумов. 14] Сучасний дифрактометр є складною установкою, у якій здійснюється фокусування рентгенівських променів, що проглядали від зразка, і вимірюється інтенсивність дифракційних максимумів з допомогою лічильників. Установка оснащена електронної і інтегруючої схемами і автоматичної записом кривих інтенсивностей. У СНД серійно випускаються дифрактометры сімейства ДРОН (дифрактометр рентгенівський загального призначення) основу якої використовуються сама й той самий схема фокусування рентгенівських променів, названа на честь авторів — фокусування по Брэггу-Брентано. Дифракционная картина реєструється послідовно принаймні обертання зразка і лічильника. Тому необхідно, щоб інтенсивність випромінювання рентгенівської трубки був постійний, а геометрична зйомка мусить бути котра фокусує при порівняно великих обсягах зразка. Дифрактометры сімейства ДРОН складаються із джерела високої напруги, на якому розташовується оперативний стіл за реалізацією тій чи іншій схеми фокусування, що включає рентгенівську трубку, лічильник рентгенівських квантів. У окремих стійках (чи стійці, залежно від моделі) розміщуються блоки лінійного підсилювача, диференціального дискриминатора, пересчетного устрою, його секундоміра, пристрій виведення інформації, дифропечатающего устрою, самопишущего приладу, які забезпечують функціонування і можливість тій чи іншій завдання. РТрентгенівська трубка, Ддетектор, РГрегестрирующее пристрій, БФИблок формування імпульсу, ПСпересчетная схема, ИСПИвимірювач швидкості подачі імпульсів, ЕППелектронний що пише потенціометр, ПУвисоковольтна пристрій, Прообразец.
Рис. 3 Принципова схема дифрактометра.
Глава III. Дослідження структури та властивостей полімерних матеріалів, модифікованих кремнийсодержащими добавками.
3.1. Результати рентгеноструктурного анализа.
3.1.1.Рентгеноструктурный аналіз кремня.
Аналізу піддавався кремній до термообробки, після термообробки при 1000С, 2000С, 3000С протягом одного часа.
Результати розрахунку рентгенограмм наведені у таблиці № 2. За основу складання цих таблиць прийнято значення межплоскостных відстаней, які розраховувалися за такою формулою d/n=(/2sin ((4) де (-довжина хвилі рентгенівського випромінювання, Е;
(-кут скольжения, 0.
Таблиця № 2 Результати розрахунку рентгенограмм кремнію |Реф-л|Кремень до |Після |Після |Після | |екс |Термообработ-ки|термо-обработки |термо-обработки |термо-обработки | |№ | |при 1000С |при 2000С |при 2000С | |Температура початку |900С |850С |950С |900С |900С | |плавлення | | | | | | |Температура max плавлення |1300С |1200С |1300С |1200С |1200С | |Температура закінчення |1600С |1600С |1500С |1550С |1700С | |плавлення | | | | | | |Температура початку |1800С |1850С |1900С |1900С |2000С | |окислення | | | | | | |Температура max окислення |2100С |2050С |2200С |2100С |2200С | |Температура закінчення |2600С |2400С |2700С |2600С |2550С | |окислення | | | | | | |Температура початку |2900С |3400С |3050С |3000С |3250С | |деструкції | | | | | | |Температура кінця |4600С |4600С |4700С |4600С |4600С | |деструкції | | | | | |.
[pic]Рис.7.
3.3. Ударне в’язкість полимера.
Ударне в’язкість зразків визначалася на маятниковом копре. Найбільшою ударної в’язкістю, з’ясувалося, має поліетилен з добавкою 1% кремнію. Зразки для дослідів застосовувалися прямокутного профілю площею 7(5 мм2. Результати досвіду наведено на рис.№ 9.
[pic]Рис.№ 9.
3.4. Триботехнические характеристики.
Триботехнические випробування проводилися на трибометре ПД-!А. Як випливало з результатів дослідження, найбільшим коефіцієнтом тертя має зразок із вмістом 3% кремнію, найменшим — із вмістом 0,1% і 0,5%[18,19,20].
Встановлено також, що зі збільшенням швидкості ковзання зразків збільшується коефіцієнт тертя і питома износ.
Результати досліджень наведено на рис№ 10, № 11.
Рис. 10.
[pic].
Рис. 11.
[pic].
Глава IY. Технологія виготовлення триботехнических матеріалів з урахуванням полимеров.
4.1. Принципи створення композиційних матеріалів з урахуванням полимеров.
Експлуатаційна довговічність машин і європейських механізмів часом визначається надійністю роботи вузлів тертя. Застосування фрикционных деталей з кольорових і спеціальних підшипникових сплавів вимагає виконання низки умов їхнього надійної роботи — мастила, спеціальних пристроїв, захищають вузли тертя від впливу абразивних частинок, забруднень, агресивних середовищ, механічних ушкоджень. Для малонагруженных і низкоскоростных вузлів тертя техніки різного призначення використання підшипників ковзання з металевих сплавів конструктивно необгрунтовано й економічно недоцільно. Сучасні композиційні матеріали на основі полімерів дозволяють вирішити завдання підвищення експлуатаційного ресурсу й надійності машин, забезпечивши у своїй значні матеріальні вигоди й економічна эффект.
Полімерні матеріали в чистому вигляді знайшли обмежений застосування при виготовленні деталей вузлів тертя унаслідок їх щодо невисоких експлуатаційних характеристик — високого коефіцієнта тертя, недостатньою термоі теплостойкости, низькою зносостійкості. Для підвищення службових характеристик полімеру використовують різні напрями: створення нових сполучних з необхідними характеристиками, модифікування многотоннажно випущених матеріалів функціональними добавками, обробку спеціальними методами.
Вибір напрямку створення полімерної композита обумовлений конкретними вимогами: економічними, конструктивними, технологічними, експлуатаційними та інших. Наприклад, застосування полімерних підшипників ковзання в автомобілях, сільськогосподарських машинах, випущених великими серіями, висувають першому плані економічні (вартість, доступність сировини) і технологічні (методи переробки на вироби, можливість регенерації технологічного шлюбу) аспекти. При використанні полімерних конструкцій в одиничних зразках техніки, особливо эксплуатирующейся в екстремальних умовах, природно, важливіше значення мають експлуатаційні і конструктивні вимоги — задані фізико-механічні властивості, термоі теплостойкость тощо. Вочевидь, що й інші методи модифікування полімерних матеріалів вибираються, з аналізу техніко-економічних вимог до конструкции.
Узагальнення вітчизняного й зарубіжного досвіду створення металлополимерных вузлів тертя дозволило виявити основні тенденції у цій області: розробку методів створення матеріалів із наперед заданими фрикционными властивостями й розробку методів управління поверхневими властивостями матеріалів у процесі фрикційного взаимодействия.
Дослідження механізму тертя і зношування полімерів по металам дає змогу стверджувати, що значний вплив на фрикційні характеристики надають: природа контактуючих матеріалів, нагрузочношвидкісні і теплові режими тертя, умови мастила, топографія поверхонь тертя. Робота вузла тертя, зокрема, великою мірою залежить від температури і складу довкілля, наявності абразиву, впливу агресивних і коррозионно-активных сред.
Для зниження коефіцієнта тертя і підвищення зносостійкості матеріалу у складі зв’язувальної зазвичай вводять від 0,1 до 40% мас. сухих мастил — графіту, сульфидов металів, солей вищих кислот, тальку, слюди та інших. Такі речовини у змозі утворювати на поверхнях тертя легкоподвижные верстви. Він модифікування знайшов найбільше застосування сшивающихся сполучних — фенолформальдегидных, эпоксидных, поліефірних смол.
Останніми роками стала вельми поширеною отримав метод підвищення фрикционных властивостей полімерних матеріалів шляхом введення до складу жидкофазных мастил і мастил. При запровадження рідких компонентів в межах, перевищують їх сумісність з полімерним сполучною, створюється можливість виділення надлишку рідини з матриці. Наявність у зоні тертя градієнта температур сприяє міграції мастильної рідини із підвищеною температурою. Отже, на поверхнях тертя безупинно генерується смазочная плівка. При зниженні температури у зоні тертя швидкість міграції мастила сповільнюється, що сприяє забезпечення ефекту самосмазывания в протягом тривалого времени.
Недоліком антифрикційних матеріалів, містять рідкі мастила, є обмеженість ресурсу роботи вузла тертя. Це з відносно невеликим кількістю рідкої мастила, що можна вводити на полімерний матеріал без істотного ускладнення технології виготовлення й переробки, і навіть без зниження і подібних фізико-механічних характеристик полімерної зв’язувальної. Частково дані недоліки усуваються під час використання спеціальних поглиначів рідкої мастила, які можуть опинитися адсорбировать значні обсяги рідини при невеликих власних обсягах. Отже, з’являється можливість переробляти композиції, містять до приблизно 40−50% про. рідкої мастила, на стандартному технологічному устаткуванні. Як поглиначів (адсорбентів) мастила використовують порошки металів, оксидів, графіту, полімерів, силікатів та інших. веществ.
Експлуатаційний діапазон застосування полімерних антифрикційних матеріалів часто визначається теплостойкостью полімерної зв’язувальної, теплопроводностью композиції. Так, при стрибкоподібному зміні нагрузочношвидкісних режимів експлуатації, викликану екстремальними ситуаціями, основною причиною відмови металлополимерного вузла тертя є теплове руйнація подшипника.
Цікавий метод підвищення зносостійкості вузлів тертя, що полягає у запровадженні в полімерне сполучне добавок, талановитими в полімеризації, — трибополимеров. Освіта трибополимерной плівки у зоні тертя забезпечує зниження зносу вузла. Дефіцитність трибополимеризующих присадок і обмежений діапазон прояви цього ефекту стримують розвитку цього направления.
Перспективним напрямом підвищення зносостійкості полімерних матеріалів і композитів з їхньої основі є диффузионное насичення поверхневих верств деталей тертя цільовими добавками. Це дозволяє досягти значного експлуатаційного ефекту при відносно невеликих економічних витратах на модифікацію изделий.
Останніми роками активний розвиток отримав трибохимический принцип створення металлополимерных вузлів тертя. Суть развиваемого принципу полягає в направленому використанні фізико-хімічних процесів у зоні непорозуміння з метою забезпечення сприятливого режиму експлуатації узла.
Продукти трибохимических реакцій деяких випадках можуть виконувати роль противоизносных добавок, про інгібіторів зношування. Тому найважливішим завданням триботехнического матеріалознавства є створення трибосистем, у яких розвиваються фізико-хімічні процеси освіти інгібіторів зношування. У зв’язку з цим на стадії проектування вузла тертя необхідно врахувати трибохимические аспекти його експлуатації. Це сприятиме підвищенню надійності і довговічності, забезпечення необхідного ресурсу роботи техніки. Реалізація трибохимического принципу створення металлополимерных вузлів тертя дозволила розробити групу самосмазывающихся матеріалів і методів підвищення зносостійкості вузлів трения.
4.2. Виготовлення виробів методом контактного формования.
Метод контактного формування не вимагає складного устаткування, і й тому він широко застосовується під час виготовлення об'ємних і пласких деталей з склопластиків у будівництві, машино-, приборо-, автомобіліі суднобудуванні. При контактному формовании отверждение матеріалу відбувається, зазвичай, при кімнатної температурі, проте до прискорення процесу можна застосовувати обогреваемые форми власності чи проводити отверждение при підвищених температурах (60−1000С).
Контактне формование виробів із склопластику ведуть у формах, виготовлених дерев’янний, гіпсу, склопластику, металу тощо. Робочу поверхню шаблону чи форми обезжиривают зазвичай бензином чи ацетоном, контролюючи чистоту, гладкість, відсутність задиров та інших дефектів поверхности.
На підготовлену оснастку (форму, шаблон) наноситься пласкою пензлем, тампоном чи розпилювачем розділовий шар — адгезионная змащування, яку треба просушити за нормальної температури 18 — 20 градусів до зникнення липкости.
До антиадгезионному засобу пред’являється ряд специфічних вимог: забезпечення легкого знімання отвержденного вироби з форми, швидке висихання, нетоксичність, неприлипание до виробу, і навіть можливість отримання виробів із глянсовою чи матовій поверхностью.
Як антиадгезионных коштів використовують полімерні пленкообразующие матеріали, зокрема водні і водно-спиртовые розчини поливинилового спирту, розчин ацетату целюлози в ацетоні, каучуку. Їх завдають на поверхню форм пласкими пензлями чи распылением.
Найширше застосовують водно-спиртовые розчини поливинилового спирту, швидкість засихання яких регулюється зміною співвідношення води і етилового спирта.
На підвищення стабільності розчину поливинилового спирту за склад розчину вводиться мыло[5,6].
У промисловості при переробці поліефірних склопластиків з використанням дерев’яних шаблонів і форм застосовують мастило наступного состава.
Таблиця № 5.
Склад мастила при переробці поліефірних стеклопластиков.
|Уайт-спирит |100 мас. год. | |Церезин М-80 | 17,1 мас. год. | |Віск буроугольный | 17,1 мас. год. | |Поліетиленовий віск ПВ-300 | 4,29 мас. год. | |Поліетиленовий віск окислений |4,29 мас. год. |.
Мастило забезпечує до 15−25 съемов виробів. Її готують шляхом розчинення суміші сухих компонентів в уайт-спирите протягом 3−4 годин при 80−90 градусів на водяній бані. На підвищення ефективності мастила рекомендується у складі її вводити прискорювачі отверждения.
Після засихання розподільного шару робочу поверхню оснастки покривають рівномірним шаром формовочного складу, що включає полиэфирную смолу, барвники, згущувачі, добавки, які знижуватимуть ингибирующее дію кисню повітря, тощо. Потім вкладають стеклоткань за довжиною (ширині) столу, шаблону. Стики полотнищ стеклоткани шириною щонайменше 20 мм, необхідно рівномірно зміщувати за довжиною (ширині) формовочной оснастки у запобігання стовщень готових изделий.
Выклейку заготівлі шар стеклоткани можна робити різними способами, у своїй тканину іноді просочують заздалегідь, у просочувальних машинах чи кистю вручну на спеціальних рамках, які можна змонтовані в установці касетного типа.
При виготовленні деталей зі складними контурами застосовувати заздалегідь просочену стеклоткань незручно. Тому суху стеклоткань прикріплюють до столу, перший шар просочують формовочным складом, після чого покривають стеклоткань наступним шаром сухий стеклоткани і пригладжують пензлем без зв’язувальної до його лежить на поверхні тканини. Ущільнення верств виробляють валиками. Потім на стеклоткань додатково завдають сполучне до її просочення, після чого вкладають наступний шар тканини. Процес повторюють до отримання потрібної товщини вироби. Зазвичай, при виготовленні виробів із склопластиків використовують три «види стеклоткани підвищення прочностных характеристик.
Для отримання певної кількості зв’язувальної в стеклопластике необхідно контролювати його витрати при пропитке. Він залежить від типу стеклоткани.
Просякнута стеклоткань отверждается безпосередньо на оснастці при температурі не нижче 180 З повагою та вологості трохи більше 65% протягом 30−60 хв з наступним доотверждением при 60−700. З протягом 2−3 годин. Готові склопластикові вироби знімають із оснастки через 72−96 годині і обрізають до необхідного розміру алмазними колами. Такий метод широко використовується під час виготовлення корпусів судів, човнів, кузовних частин автомобілів, резервуарів та інших великогабаритних деталей[10].
4.3. Виготовлення виробів методами вільного і відцентрового литья.
Широке застосування метод вільного лиття знайшов при переробці ненасичених поліефірних смол у виробництві деталей радіотехнічного призначення, електричного устаткування кабельних муфт, наливних статей, листових і стрижневих заготовок щоб одержати гудзиків, пряжок і біжутерії і т.д.
До заливочным композиціям пред’являється такі вимоги: вони повинен мати невисоку в’язкість, помірну усадку, невеличкий экзотермический ефект при отверждении, а отвержденном стані підвищену ударну міцність та низці випадків високі показники электроизоляционных властивостей, поліпшену прозорість, теплопровідність, зносостійкість і хімічну стойкость.
Заливання у відчинені й закриті форми здійснюють, зазвичай, після запровадження отверждающей системи не залучаючи зовнішнього тиску, а часом використовують найпростіші пристосування для заливання під тиском стиснутого повітря 0,02−0,2 МПа[10].
Необхідна час гелеобразования і отверждения забезпечується співвідношенням і пишатися кількістю компонентів отверждающей системи. Для прискорення отверждения виробів форми нагрівають, причому температура нагріву залежить від застосовуваної системи отверждения.
Прискорення процесу отверждения можна досягнути шляхом обробки смоли струмами високої частоти. У цьому досягається підвищення твердості на 10−22% та подальше зниження абразивного зносу на 11−18%. Вільну відливку можна провадити у формах з поліетилену, пропилену, застосування яких немає вимагає нанесення антиадгезионной мастила на робочу поверхню форм.
З іншого боку, застосовують також форми з силіконовою гуми, особливо в виготовленні декоративних виробів: деталей меблів, багетів, для обрамлення картин, статуеток, прикрас, гудзиків, пряжок і др.
Виготовлення еластичних форм входять такі процеси: виготовлення моделі, форми для виливки силіконовою матриці, кріплення моделі у формі, приготування силіконового компаунда і заливання до форми, вулканізація, вилучення матриці з форми, термообробка матриці, виготовлення копій моделі у матриці, розмноження силіконових матриць. Модель-оригинал розробляється і виготовляється із будь-якої матеріалу: пластика, дерева, металу, воску, пластиліну тощо. Силіконовий компаунд відтворює дрібні деталі малюнка моделі, тому допускаються будь-які дефекти, зокрема відбитки пальцев.
Після підготовки моделі виріб обезжиривают і закріплюють до форми. Форма для виливки силіконових матриць виготовляється як циліндра чи рамки зі знімним дном. Для кращого вилучення силіконовою матриці з форми, стінки обробляють антиадгезионным складом з урахуванням воску, парафіну. Допускається застосування вазеліну і мінерального олії. Закріплення моделі у формі виробляється у вигляді липкою стрічки, клею і будь-якою іншою способом, але з огляду на те, що модель повинна щільно прилягати на дно форми у запобігання подтекания силікону під модель.
Після змішання компонентів силіконову композицію дегазируют в вакуумі видалення повітряних бульбашок, захопленого у процесі змішання. У цьому обсяг суміші збільшується в 2−3 разу, тому ємність мусить бути заповнена лише на 1/3 обсягу. Коли вспученная композиція повертається до початкового обсягу, дегазацію припиняють. Коли поверхні моделі є складний малюнок, та над заливанням її покривають тонким шаром силіконовою композиції, у якому запроваджено каталізатор вулканизации.
Вулканізація силіконовою форми триває 6−24ч при 20−250 З. Коли композиція у процесі вулканізації втратить липкість і набере твердість, силіконову матрицю беруть із форми і відділяють від моделі. На підвищення її довговічності потрібно термообробка за нормальної температури 140−1600 З. У процесі термообробки відбувається довулканизация, видаляються леткі продукти реакції, стабілізуються властивості. Щоб не відбулася деформація матриці через швидкого нагріву, температуру необхідно підвищувати, починаючи з 800С зі швидкістю 10−200С/час.
Після термообробки в матриці з полиэфирной смоли відливається необхідну кількість копій моделі, якими виробляється розмноження силіконових матриць. Для виготовлення виробів вільної заливанням використовуються композиції з урахуванням смол ПН-1 і ПН-12.
Кількість компонентів отверждающей системи (прискорювача і ініціатора) підбирається експериментально, щоб забезпечити час гелеобразования 13−16 хв (протягом якого смола зберігає плинність). Цього часу достатньо заливання 20−25 форм. Стірол чи 3% розчин парафіну в стиролі вводять у композицію при литві виробів на еластичних силіконових формах з метою зниження поверхневою липкости.
Поліефірна композиція заливається тонкої струменем в силіконові форми, нагріті до температури 100−1200С. Після заливання рекомендується помістити їх в сикатив термошкаф з температурою 110(100С, через 10−20 хв форму беруться заготівлі виробів і матриця без промивання готова наступної заливке.
У разі мелкосерийного виробництва виготовлення виробів із ненасичених поліефірних смол методом вільної заливання може бути використані установки типу УОС-2−1 з продуктивністю переробки полиэфирной композиції 50−70 кг/час. Принцип роботи установок полягає у наступному: композиція з прискорювачем заливається до однієї ємність, і з ініціатором до іншої, потім композиції шнековыми насосами подаються у змішувач проточного типу, де перемішуються. З змішувача композиція, здатна швидкого отверждению, подається до форми. На установці можлива одночасна заливання двох форм.
4.4. Технологічний регламент виготовлення композиційних матеріалів з урахуванням ненасичених поліефірних смол.
Технологічний регламент виготовлення композиційних матеріалів на основі ненасичених поліефірних смол розроблений з урахуванням результатів науково-дослідницьких робіт передбачає використання композиційних матеріалів під час виробництва абразивного инструмента.
Технологічний процес виготовлення шліфувальних кіл гнучкою зв’язці складається з таких стадій: підготовка сировини й форм; приготування формотворної суміші; виготовлення і збереження кіл; розбирання форм і виїмка кругов.
1.Подготовка сировини й форм.
1. Сировину перевірити щодо відповідності Держстандартам, ОСТам, ТУ.
2. Приготування мастила для форм.
3. Підготовка форм.
Форми оглянути. Раковини, подряпини, бруд на формообразующих поверхнях форм не допускаются.
Форми встановити робочому столі. Стару мастило видалити і пензлем завдати тонкий і рівномірне шар мастила на формотворну поверхні форм.
Для отримання рівномірного шару необхідно мастило попередньо розмішати до однорідної массы.
Температура повітря робочого приміщення мусить бути не ниже.
+200С.
2.Приготовление формотворної массы.
Приготування маси провадити у металевої ємності при перемішуванні на лопастном смесителе.
1. Підготовка сипучих компонентов.
2. Підготовка связующего.
3. Змішування сипучих компонентів зі связующим.
3.Изготавление і збереження кругов.
1. Після перемішування, масу із робітничого ємності перелити в розливальний ковш.
2. З ковша суміш заливати в форми, роблячи кругові руху за периметром форм і кладучи один шар послідовно в інший до заповнення форм массой.
3. Вивільнені робочу ємність і ківш разливочной машини очистити від залишків формотворної маси, використовуючи серветки обтирочные, змочені ацетоном.
4. Відразу після заливання форм починається полімеризація кіл, що відбувається із тепла.
5. Через 15−20 хв ножем видалити з форми надлишки формотворної массы.
6. Кола зберігати в сухому приміщенні за температури понад +100С.
Кола складувати рядами чи підвішеному стані на штырях.
4.Контроль качества.
1. Кожне виріб озирається візуально. Не допускається наявність тріщин і сколов.
4.5. Механічна обробка поліефірних материалов.
Матеріали з урахуванням поліефірних смол можуть піддаватися всіх видах механічного оброблення, це пов’язане з певними труднощами. Механічне перенесення закономірностей процесу різання металів і рекомендацій на окремі види їх опрацювання на процес різання пластмас, засвідчує практика, неможливий, оскільки пластмаси — особлива по порівнянню із металами група матеріалів, має специфічні властивості, які обумовлюють особливості процесу їх різання. Деталі з поліефірних матеріалів під час виготовлення пресуванням, литтям, формованием змінюють свої розміри і форми внаслідок усадки при отверждении і остиганні, тому обробка різанням є необхідною, панівною і важливішої операцією загалом технологічному процесі виготовлення виробів із цих материалов[11,12,17].
Поліефірні матеріали, зазвичай, містять пігменти, наповнювачі дисперсні і волокнисті, зокрема скловолокно, що викликає швидкий знос інструмента. Цьому сприяє низька теплопровідність полиэфирной смолы.
При механічної обробці поліефірних матеріалів краще застосовувати різці з твердих сплавів групи ВК порівняно з сплавами груп ТК і ТТК.
Для твердих сплавів групи ВК з різним вмістом кобальту (ВК-3, ВК-4, ВК-6, ВК-8, ВК-10) найбільша стійкість відзначено під час використання різців, оснащених платівками з ВК-6, що як вчетверо перевищує термін їхньої служби твердосплавних різців з ВК-8. Стійкість різців, оснащених платівками з мелкозернистых твердих сплавів ВК6М і ВК60М, в 7−9 раз перевершує стійкість інструмента з ВК-8. Стійкість різців з швидкорізальної сталі Р18 в 2−3 рази менше, ніж із ВК-8 і вольфрамових сплавів КНТ-20 і ТН-20.
Стійкість різців з швидкорізальної сталі можна підвищити нитроцементацией, нанесенням тонкого поверхневого шару карбонитридов на установках ‘Булат'.
При розрізуванні аркушів, труб і стрижнів з склопластиків завтовшки до 30 мм найбільша продуктивність обробки відзначено під час використання діамантових кіл, оснащених синтетичними діамантами АСВ і АСК зернистостью 400/315 чи 250/200. Рекомендована швидкість різання V=60−65 м/с, подача S=6 000−7 000 мм/мин.
Стійкість діамантових кіл становить близько 50 год, і з застосуванням охолоджувальної середовища вона збільшується приблизно 2 раза.
Для шлифования пластмас найбільш придатні карборундовые кола середньої твердості на керамічної чи бакелитовой поєднанні з розміром зерна абразиву 0,8−0,5 мм для чорнової обробітку грунту і 0,25−0,16 мм для чистовий. Часто застосовують також шлифовальную шкурку з тими самими розмірами зерен абразиву. Остаточну обробку поверхні перед поліруванням виробляють шкурками із найбільш дрібними абразивными зернами № М-20, М-40.
Розроблено спеціальні абразивні кола, що дозволяють підвищити продуктивність шлифования пластмас. Як абразивного матеріалу в них використано роздрібнене (віконне, тарне) скло, а ролі зв’язки — бакелітова смола. Абразивні кола з скляних зерен здатні самозатачиваться у процесі шлифования. Пояснюється це тим, що зерна з скла мають гірші механічні характеристики, ніж электрокорунд і карбід кремнію, і легко руйнуються внаслідок откалывания від зерен невеликих частинок і выкрашивания затупившихся зерен. Натомість у роботу вступають нові обнажившиеся зерна, і ріжучі властивості кола підтримуються на протязі період стойкости.
Впровадження скляних абразивних кіл виробництво показало, що вони за стійкості перевершують металообробні в 10−20 разів, і дають більш низьку шорсткість поверхні. Для отримання поверхонь особливо високого якості чи надання їм стійкості до навколишньому середовищі, застосовують полірування, яке надає виробу товарний вигляд. Полірування виробляють на полировальных колах чи барабанах діаметром 500−700 мм, причому використовують м’які і тверді кола. Працюючи з твердими колами з повсті і фетру виправляють глибокі дефекти —- ризики, подряпини, штрихи і т.п. Складаються ці кола з цих двох прокладкових дисків на щотри робочих диска, які товщина дорівнює 60−100 мм.
Працюючи з м’якими полировальными колами, деталі піддають остаточному полированию.
Робітники поверхні кіл покривають полировальными композиціями, основною частиною яких є абразивні матеріали — пемза, наждак, карборунд, крейда, глина, оксид хрому та інших. Полірувальні пасти випускають з абразивами чотирьох градацій по дисперсности (чотирьох квітів). Найстрашніше грубе полірування отримано під час використання пасти з абразивом дисперсностью 60- 65 мкм (паста червоного кольору), жовта паста містить абразив розміром 40−45 мкм, зелена — 30−35мкм сіре паста, найтонша, — 20−25 мкм. У таблиці № 6 наведено склад, мас %, найчастіше застосовуваної шлифовальнополировальной пасти (пасти ГОИ).
Таблиця № 6 Склад шлифовально-полировальной пасти ГОЇВ | |Груба |Середня |Тонка | |Окис хрому |81 |76 |74 | |Стеарин |10 |10 |10 | |Розщеплений жир |5 |10 |10 | |Силикагель |2 |2 |1,8 | |Гас |2 |2 |2 | |Сода двууглекислая |— |— |0,2 |.
Якщо після полірування лежить на поверхні виробів залишається жирна плівка, необхідно застосовувати склади видалення полировальных паст. Поїзди містять водні розчини і емульсії з м’яким абразивом, розчинники, поверхнево-активні речовини і др.
Під час упорядкування рецептур полировальных паст необхідно враховувати, що при полировании светлоокрашенных виробів на пасту вводяться лише світлі компоненти, які слідів на оброблюваної поверхні, а відновлення початкового кольору ще на місцях обробки можна використовувати кольорові пасти. Мінімальний додача на полірування 0,12−0,30 мм.
Выводы.
Так, технологію виготовлення матеріалів з урахуванням ненасичених поліефірних смол і виробів із них входять такі операції: підготовку сипучих вихідних компонентів; підготовку зв’язувальної; змішання сипучих компонентів зі сполучною; дегазацію композиційної матеріалу; заливання композиційної матеріалу в форми; формування изделия.
Вироби можна одержувати методом прямого чи литьевого пресування при мінімальному тиску пресування, оскільки композиції мають високої плинністю. Використовуючи композицію, можна виготовляти армовані вироби шляхом просочення поліамідних, бавовняних, скляних та інших тканин, що дозволяє їм отримати особливо міцні конструкції за збереження високих антифрикційних властивостей. Вироби антифрикционного призначення, мають циліндричну форму, особливо великогабаритні, доцільно виготовляти методом відцентрового лиття при швидкості обертання форми 120 — 400 хв -1.
Для прискорення процесу формування виробів форму рекомендується підігріти до 40 — 800С, навіщо можна використовувати гарячої води чи термошкаф. Час отверждения композиційних матеріалів можна змінювати в межах. Процес отверждения йде із тепла, що можна враховувати в виготовленні великогабаритних виробів у запобігання їх коробления і растрескивания.
Композиційні матеріали з урахуванням ненасичених поліефірних смол допускають обробку будь-якими видами ріжучого інструмента, що дозволяє виготовляти вироби з точністю котрі оформляють розмірів. Перевагою композиційних матеріалів подібного типу є можливість використання відходів у технологічному циклі. Розроблено метод регенерації відходів композицій з урахуванням ненасичених поліефірних смол шляхом збільшення тривалості гумоподібної стану з наступним подрібненням їх у вальцах. Подрібнене активовані відходи можна використовувати в ролі наповнювача композиційних матеріалів, що дозволяє в 3 — 5 раз знизити витрата зв’язувальної й у значною мірою розв’язує проблеми утилізації промислових полімерних отходов.
Глава Y. Вимоги техніки безпеки під час роботи з полиэфирными смолами і инициирующими добавками.
5.1. Збереження поліефірних смол і ініціюючих добавок.
Поліефірні смоли бережуть у бочках чи бідонах зі сталі, алюмінію чи оцинкованої сталі у закритих приміщеннях за нормальної температури не вище 200С, захищаючи від дії сонячних променів і вологи. Гарантійний термін зберігання становить зазвичай 4−6 місяців, та якщо після закінчення цього строку смола відповідає вимогам НТД, яку можна вважати придатної до переработке.
Пожежна небезпека поліефірних смол визначається природою мономера, входить у до їхнього складу. Стірол, є компонентом багатьох смол, легко воспламеняется (температура спалахи 310С, температура самовоспламенения 4900С)[29].
Щоб запобігти пожежі необхідно зберігати смоли в щільно закупореної тарі; висвітлення та електрообладнання складських приміщень має зроблено у вибухонебезпечному виконанні. Не допускаються наявність джерел відкритого вогню й искрообразование. Приміщення би мало бути обладнані засобами пожежогасіння — пінними і углекислотными вогнегасниками, піском і т.п.
Перекисные і гидроперекисные ініціатори, є вибухі вогненебезпечними речовинами, бережуть у ізольованих провітрюваних приміщеннях за нормальної температури не вище 250С. У сухому стані можуть розкладатися зі вибухом при ударах, растирании, нагріванні, поєднанні з сильними кислотами і восстановителями. Гипериз, перекису метилэтилкетона, циклогексанона необхідно зберігати щодо тари з поліетилену чи темного скла. У цьому забороняється використовувати гумові і притертые скляні пробки, натомість застосовують завинчивающиеся кришки з поліетилену чи корковые пробки з прокладанням з поліетиленової пленки[7].
Перекис бензоила поставляють і бережуть у увлажненном стані (вологість щонайменше 25%) в скляних і керамічних ємностях (банки, пляшки) з дерев’яними чи поліетиленовими пробками і кришками. Заморожена зволожена перекис бензоила також вибухонебезпечна, як і суха, у зимовий період необхідно воложити її водою, а етиловим спиртом.
Не допускається зберігання перекисів і гидроперекисей поруч із джерелами тепла, і навіть на сонячному світу. Складське приміщення мусить відповідати вимогам, що ставляться до приміщенням для зберігання вогніі вибухонебезпечних речовин. Джерела електричного висвітлення розташовуються поза приміщенням. Приміщення має бути чистим, у разі виникнення пожежі треба використовувати води і песок.
У лабораторіях наукових і виробничих приміщеннях дозволяється зберігати лише небагато ініціатора. Тара, вивільнювана з-під перекисів і гидроперекисей, має бути старанно промываться ацетоном, водою, содовим розчином чи 3%-ным розчином луги, після цього тару можна використовувати повторно. Категорично забороняється зберігати непромытую тару.
Застосовуваний як прискорювача диметиланилин приходить у скляних пляшках, прискорювач НКв алюмінієвих бідонах і скляних суліях. Прискорювачі через їх горючести і токсичності бережуть у окремих приміщеннях за умов, аналогічних умовам зберігання поліефірних смол.
5.2. Переробка поліефірних смол.
Ненасичені поліефірні смоли — пожароопасные і токсичні матеріали. Токсичність стиролсодержащих поліефірних смол обумовлена вмістом у них стиролу (25−40 мас %), пари якого надають наркотичне і дуже дражливе дію, і навіть впливають на нервову систему, кров, і кровотворні органи. Потрапляння стиролу чи стиролсодержащих смол на шкіру може викликати й дерматити. Гранично припустиму концентрацію в робочої зоні 30 мг/м3, в виробничих приміщеннях -5, в приземному прошарку промислового майданчика — 1,5, а житловий зоні - 0,003 мг/м3, у питній воді водних об'єктів господарсько-питного і культурно-побутового водоиспользования -0,1 мг/л. До складу поліефірних композицій входить ряд компонентів, які мають високу токсичность[25,26,28].
Роботи з полиэфирными смолами слід здійснювати помешканнях із припливно-витяжної вентиляцією. Досягнення повітря ГДК стиролу 5 мг/м3 під час роботи зі стиролсодержащими смолами необхідно подавати повітря 2 000 м3/ч на 1 м² поверхні формуемого матеріалу, проте створити такий повітрообмін за умов складно. З іншого боку, зі збільшенням швидкості потоку повітря сильно підвищується швидкість випаровування стирола.
Для розрахунку вентиляції повітрообмін L (м3/ч) при виділенні органічних розчинників з розчину полімерів визначають по формуле.
L=G (K2 — K1) (7) де G — кількість що виділяються розчинників, г/ч;
К2 — граничне зміст розчинників в удаляемом повітрі, г/м3;
К1 — зміст розчинників в приточном повітрі, г/м3.
Крім загальної необхідно встановлювати місцеву вентиляцію у місцях найбільшої концентрації токсичних летючих речовин (преси, сушильные шафи, ділянки для контактного формування, вільної заливання тощо.). У цьому рекомендується відсмоктувати стирол у нижній частині робочого приміщення, оскільки його пари важче воздуха.
Працюючи з полиэфирными смолами слід користуватися спецодягом (халати, комбінезони, фартухи та інших.), гумовими, поліетиленовими чи поливинилхлоридными рукавичками чи спеціальними захисними мастилами на основі поливинилового спирту чи казеїну. Рекомендується застосовувати для захисту шкірних покровів пасти, мазі, креми (типу мазі Селинского і ИЭР-1).
Пасту завдають на руки, витримують кілька хвилин до засихання, після чого на шкірі утворюється захисна плівка. Після закінчення роботи її змивають водою. Влучаючи смоли на незахищені ділянки шкіри необхідно видалити її тампоном, та був промити цю ділянку шкіри теплою водою з милом чи 5%- ным розчином соди і змазати кремом. Перекису надають різке дражливе дію на шкіру слизову оболонку і може викликати опіки, тому вражена місце слід обробляти спирт або сильної струменем води. При потраплянні перекису правді в очі, їх промивають водою і 5%-ным розчином соди і звертатися до врачу.
Цех із переробки поліефірних смол повинен відповідати вимогам, що ставляться до взрывоі пожароопасным приміщенням: їх постачають засобами пожежогасіння, взрывобезопасными електроустаткуванням і освітлювальної апаратурою. Забороняється роботу з інструментом, котрі можуть викликати іскріння під час удару, не можна попередньо змішувати ініціатор і прискорювач щоб уникнути загоряння й Великого вибуху. Приміщення, у яких готуються й обробляються поліефірні композиції, мають клас ПУЭ У- 1а, а механічна обробка виробляється у приміщеннях класу П-2а.
При механічної обробці гранично припустиму концентрацію пилу в виробничому приміщенні має перевищувати 2 мг/м3. Після роботи необхідно мити обличчя і руки лише гарячою водою, спочатку без мила, щоб пил не утиралася в шкіру, та був з милом. Вхідний пристрій пневмоотсоса необхідно встановлювати в такий спосіб, щоб у нього потрапляли пилюку і стружка. Інакше вони розсіюються повітря і забруднюють його. Іноді при механічної обробці пластмас стружку й пил вилучають із допомогою мастильно-охолодної жидкости.
1. Звіт на тему ‘Розробити склад парламенту й технології виготовлення абразивного матеріалу в обробці деталей складної геометричній форми'. Наук. рук.: Струк В. А., — Гродно, 1996.
2. Довідник по композиційним матеріалам. Під ред. Дж. Любика т1, т2. — М.: Машинобудування, 1988.
3. Струк В. А. Антифрикционные матеріали з урахуванням полімерних сполучних. — Гродно, 1996.
4. Композиційні матеріали. Довідник під загальним ред. В. В. Васильева, Ю. М. Тарнопольского. — М.: Машинобудування, 1990.
5. Сєдов Л. Н. Склад і їхні властивості поліефірних сполучних для пресскомпозиций. — М., 1975.
6. Моїсєєва І.П., Верин С. П., Семенова Н.І. Тиксотропные антикоррозионные грунтовки за захистом надводних поверхонь судів. -1975.
7. Сировина й напівпродукти для лакофарбових матеріалів. Довідкове посібник. Під ред. М. М. Гольдберга.- М., 1978.
8. Сєдов Л. Н., Михайлова З. В. Ненасичені полиэфиры.- М., 1977.
9. Довідник по пластмас. Під ред. В. М. Катаева, В. А. Попова, Б. И. Сажина. — М., 1975.
10. Азаров В.І., Цвєтков В.Є. Технологія сполучних і полімерних матеріалів. — М.: Лісова промисловість, 1985.
11. Нові матеріали у техніці та науку.- М., Наука, 1976.
12. Коляго РР., Струк В. А. Матеріали з урахуванням ненасичених полиэфиров. — Мінськ: Навука і тэхнiка, 1990.
13. Костін В.П. Фізико-механічні випробування металів, сплавів і неметалевих матеріалів. — М.: Машинобудування, 1990, — 256 с.
14. Вегман Е. Ф., Руфанов Ю. Г., Федорченко І.Н. Кристалографія, мінералогія і рентгенографія. — М.: Металургія, 1990, — 262с.
15. Струк В. А., Минюк Г. Е. Лабораторний практикум по курсу"Физика і хімія полімерів". — Гродно: ГрГУ, 1995, — 64с.
16. Феномен кременю: реальність, і перспективи. Збірник праць першого Республіканського науково-практичного семінару. — Мінськ, 1993.-126с.
17. Стугін В.Є., Акутин М. С. Основи переробки пластмас.- М.: Хімія, 1985. 400 с.
18. Охлопкова А. А. Триботехнические і механічні характеристики модифікованого политетрафторэтилена // Тертя і износ.-№ 4. — Т.17. — 1996. — З. 550−553.
19. Миронов В. С. Технологічне управління триботехническими характеристиками шаруватих полімерних композицій // Тертя і знос. — № 3. Т.16. -1995. -С.527−536.
20. Ольшевський О. З. Дослідження триботехнических характеристик композиційних матеріалів з урахуванням ПЭНД // Фізика конденсованих середовищ: Тези доповідей YI Республіканської науковій конференції у студентів і аспірантів /Під ред. Лиопо В.А.- Гродно: ГрГУ, 1998. — С.147.
21. Кузнєцов В.М. Суміші полімерів.- М.: Хімія, 1979. — 304с.
22.Менсон Дж., Сперлинг Л. Полімерні суміші і композити / Під ред. Ю. К. Годовского. — М.: Хімія, 1979. -440с.
23. Тупов І.І., Кострикина Г.І. Хімія і фізика полімерів.- М.: Хімія, 1989. 432 с.
24. Портной К. И., Солибенов С.Є., Светлов И. Л., Чубаков В. М. Структура й поліпшуючи властивості композиційних матеріалів. — М.: Машинобудування, 1979. — 255с.
25. Полімерні суміші / Під ред.Д.Пола, С.Ньюмака. — М.:Мир, 1981. 455с.
26. Гольдадэ В. А., Струк В. А., Песецкий С. С. Інгібітори зношування металлополимерных систем.- М.:Химия, 1993. — 240с.
27. Струк В. А. Лабораторний практикум за курсом «Матеріалознавство «для інженерних спеціальностей. — Гродно: ГрГУ, 1991. — 66с.
28. Бортників В. Г. Основи технології переробки пластичних мас.- Л.: Хімія, 1985.-304 с.
29. Стугін В.Є., Кузнєцов В. М. Структура і механічні властивості полімеру. — М.: Вищу школу, 1979. — 352с.