Прокатка
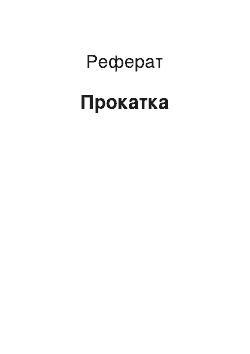
Сортові стани призначені для прокатки сортових і фасонных профілів. Калібрування валків сортових станів здійснюється з урахуванням найбільшого обжатия при кожному пропуску, щоб кількість перепусток була найменшою. На рис. 137 приведено калібрування валків для прокатки тавровой балки. Калібри пронумеровано гаразд послідовності обжатия заготівлі. У відповідність до розмірами прокату і діаметра… Читати ще >
Прокатка (реферат, курсова, диплом, контрольна)
ПРОКАТКА Прокатка. Прокатку виробляють на металургійних і машинобудівних заводах, у своїй отримують прокат — готові вироби чи заготівлі для наступної обробки куванням, штампуванням, пресуванням (видушуванням), волочінням чи різанням. У прокат переробляють близько 80% всієї виплавленої сталі й більшість кольорових металів і сплавів. Прокат використав будівництві, машинобудуванні й металлообработке.
Залежно від виду прокат ділять на сортовий, листовий, трубний, періодичний і спеціальний. На рис. 133 наведено види сортового прокату загального призначення: 1 — квадратний; 2 — круглий; 3 — смугової; 4 — кутовий; 5 — двутавровый; 6 — швеллерный; 9 — тавровый і пояснюються деякі види сортового прокату спеціального призначення — 7 і побачили 8-го — рейковий; 10 — узгоджений; 11 — смуга для черевиків гусениць тракторів; 12 — смуга для ободів коліс автомобилей.
Труби залежно від технології їх, виробництва ділять на безшовні зварні. До спеціальним видам прокату відносять дуже широке асортимент продукції: цельнокатаные колеса для вагонів, бандажі, осі, вали, кулі, зубчасті колеса, свердла й багато іншого. Для прокатки нагріті чи холодні заготівлі пропускають між обертовими валками прокатних станов.
[pic] рис. 133.
Існують три основні виду прокатки: поздовжня (для сортових і фасонных профілів), поперечна і поперечно-винтовая (для тіл вращения).
При подовжньої прокатці (рис. 134) валки обертаються врізнобіч, деформуючи заготівлю, товщина (висота) h0 якої зменшується, а довжина і ширина збільшуються. Найважливішою характеристикою при прокатці є обтиснення. Абсолютна обтиснення? h=h0-h1; відносне обтиснення? (%) обчислюють по формуле Относительное обтиснення за прохід залежить від кута захоплення чи становить 10 — 60%.
Шляхом найпростіших обчислень можна знайти, що? h = D (1-cos?), т. е. абсолютне обтиснення збільшується зі збільшенням діаметра валка D і кута ?. Кут захоплення? при прокатці в насеченных валках становить 27 — 34°, при прокатці сортового матеріалу 22 — 24°, при гарячої прокатці аркушів 15 — 22°, при холодної прокатці 3—8°.
Валки для прокатки виливають з вибіленого чавуну чи виковують з вуглецевої чи легованої стали. Їх роблять гладкими (применяют при прокатці аркушів), чи калиброванными з струмками (канавками) навкруг (для сортового і фасонного прокату). Профіль, складений суміжними струмками двох валків, називають калібром. Рис. 134.
При поперечної прокатці (рис. 135, а) валки 1 обертаються щодо одного напрямку і осі їх рівнобіжні, а заготівля 2 деформується ними під час обертання навколо своєї осі. Радіус заготівлі_ за цикл (полоборота заготівлі) зменшується на величину радіального обжатия? r.
Направление прокатки Виникаючі у своїй напруги у зовнішніх шарах заготівлі спрямовані тангенциально (?зв), а середині заготівлі - радіально, від центру периферії (?з), що може спричинити до появи отверстия.
?r=r-r'. з нерівній поверхнею у центральній її частки. Тому, якщо отримання отвори небажано, прокатку ведуть при невеликих обжатиях, коли? з < ?в.
Методом поперечної прокатки отримують, наприклад, зубчасті колеса і зірочки цепних передач на спеціальних верстатах з зубцюватими валками. Поперечно-винтовая (навкісна) прокатка широко застосовується під час виробництва безшовних труб з суцільний заготівлі (рис. 135, б). Валки 1 обертаються в одному напрямку, а осі їх розташовані під деяким кутом, тому заготівля 2 при обробці як обертається (vy), але й переміщається вздовж своєї оси (vx). Для отримання правильної форми і гладкій поверхні отвори труби (гільзи) у зоні освіти отвори встановлюється дерево 3. Отримані на прошивном стані гільзи розкочуються на трубопрокатних станах. Метод поперечно-винтовой прокатки застосовують також для куль, осей та інших виробів з допомогою спеціально каліброваних валків. Сталь для гарячої прокатки нагрівають до температури вище лінії 68К (див. рис. 132); мідь, алюміній та його сплави також прокочують в гарячому стані. З гарячекатаної заготівлі (лист завтовшки 1,25 мм) холодної прокаткою отримують тонкі вироби (до 0,1 мм менше), стрічки для пружин, листи, фольгу і прочее.
Прокатні стани розрізняють за призначенням, кількості валків в клети, кількості клетей і схемою їх расположения.
За призначенням прокатні стани діляться на обтискні (блюминги і слябинги), заготовочные, сортові, листові і спеціальні. Спочатку зливок прокочують на обтискному стані, потім на заготовочном і, нарешті, на сортовом, листовому чи специальном.
За кількістю валків та його розташуванню стани подовжньої прокатки ділять двома-, трьох-чотирьохі многовалковые, і навіть універсальні. Двухвалковые стани (рис. 136, а) бувають реверсивные (прокатка заготовок ведеться у обидва боки) і нереверсивные.
[pic] рис. 135 [pic].
[pic].
рис. 136.
(прокатка ведеться до однієї бік, для повторних перепусток заготівля повертається через верхній валок).
Прокатка заготовок на трехвалковых станах (рис. 136, б) ведеться в один бік між нижнім та середнім валками, до іншої - між середнім і верхнім; напрям обертання валків постійне. У півфіналі чотирьохі шестивалковых верстатах (рис. 136, в, р) верхні і нижні валки є опорними, вони перешкоджають прогибу середніх робочих валків; цю схему застосовується для листових станов.
У клетях з 12 (рис. 136, буд) і 20 валками забезпечується ще більше жорсткість робочих валків; у яких виробляють холодну прокатку стрічки завтовшки до 0,001 мм.
Універсальні стани (рис. 136, е) мають горизонтальні і вертикальні валки і забезпечують обтиснення чотирьох сторон.
Сортові стани призначені для прокатки сортових і фасонных профілів. Калібрування валків сортових станів здійснюється з урахуванням найбільшого обжатия при кожному пропуску, щоб кількість перепусток була найменшою. На рис. 137 приведено калібрування валків для прокатки тавровой балки. Калібри пронумеровано гаразд послідовності обжатия заготівлі. У відповідність до розмірами прокату і діаметра валків сортові стани ділять на крупносортные (діаметр валків D= 500:750 мм), среднесортные (D= 350:500 мм) і мелкосортные (D= 250:350 мм). У сортових станів жодна, а кілька робочих клетей.
У вже створені і впроваджено у виробництво поперечно-винтовые стани для прокатки валів, гайкових ключів, вагонних осей, тарою, труб з високими поперечними ребрами для теплообменной апаратури, зубчастих коліс, гвинтів з великим кроком різьби, червячных фрез, свердел та інших виробів. Нові прогресивні методи прокатки значно заощаджують метал з допомогою зменшення чи усунення відходів у стружку при механічної опрацюванні та різко підвищують продуктивність труда.
Пресування (витискання). При пресуванні метал видавлюють__ з замкнутої порожнини через отвір, у результаті отримують виріб з перерізом у вигляді отверстия.
Пресують мідь, свинець, алюміній, цинк, магній та його сплави, і навіть сталь з мірних заготовок, нарізних з стільникового проката.
Рис. 137.
Все метали і сплави, крім свинцевих, пресують гарячими. Існують два виду пресування — пряме і обратное.
При прямому пресуванні (рис. 138, а) заготівлю 2 закладають в контейнер 3, укріплений на рамі 1 гідравлічного преса; туди закладають пресс-шайбу 4. На плунжере 6 преса укріплений відштампувати 5, який тисне на пресс-шайбу, у результаті метал заготівлі випливає через отвір матриці 7 як прутка. Тиск пресування сягає 100 МН. При зворотному пресуванні (рис. 138, б) заготівля перебуває у глухому контейнері і залишається при пресуванні нерухомій, а прессуемый метал при русі матриці випливає назустріч їй. Протилежне, пресування вимагає менших зусиль і залишок металу у контейнері менша, аніж за прямому пресуванні, проте на меншою деформації пресований пруток зберігає сліди структури литого металу. Дротики суцільного перерізу одержують, як прямим, і зворотним пресуванням. Пресування труб (рис. 138, в) виробляють лише прямим методом, у своїй закладений контейнер 9 зливок 10 попередньо обжимается пресс-шайбой 11, та був прошивається дорном 8, кінець якого сягає отвори матриці 12. При пресуванні метал випливає з кольцеобразного калібру, складеного отвором матриці і дорном, у результаті утворюється труба.
Пресуванням отримують вироби різного профілю (рис. 139) з розміром перерізу до 400 мм. Пресовані вироби точніше отриманих прокаткою, крім того, ряд профілів можна лише пресуванням, тому вона широко використовують у металлообработке.
_.
[pic]рис.138 рис. 138.