Розробка технологічного процесу механічної обробки чорнових заготовок з деревини
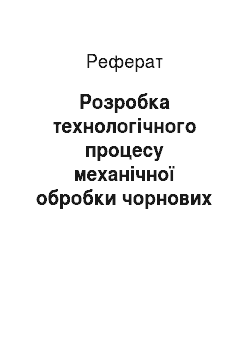
Зубчаті клейові з «єднання виготовляються відповідно до вимог ГОСТ 19 414. Точність формування зубчатих шипів повинна відповідати тринадцятому квалітетові за ГОСТ 6449.1. Параметр шорсткості поверхонь склеювання зубчатих шипів Rm max за ГОСТ 7016 не повинен перевищувати 200 мкм. Звичайна причина виникнення непрямолінійності ламелі при торцевому зрощуванні — неякісне фрезерування мікрошипів… Читати ще >
Розробка технологічного процесу механічної обробки чорнових заготовок з деревини (реферат, курсова, диплом, контрольна)
ДИПЛОМНА РОБОТА на тему:
Розробка технологічного процесу механічної обробки чорнових заготовок з деревини.
ЗМІСТ Вступ Розробка конструкцій виробу Опис виробу Конструкція і матеріали Розробка технологічного процесу Опис технологічного процесу Технологічна карта Заходи з охорони праці.
Список використаної літератури.
ВСТУП Деревина є одним з тих конструкційних матеріалів, який людство використовує з прадавніх часів і до наших днів. Накопичено величезний досвід виробів. Необхідних в промисловості, будівництва, сільському господарстві., транспорті, побуті тощо. Сьогодні деревину обробляють механічним, гідротермічним та хімічним способом. Механічний спосіб, який буде розглянуто далі, є найдавнішим і включає такі види оброблення, як різання, склеювання. гнуття, пресування, опорядження. З планом часу змінювався матеріал інструменту (комінний, бронзовий, сталевий, різання рідиною під тиском лазера) його вид (ручний пневматичний, електрифікований) обладнання (з ручним приводом, механічним, гідравлічним) вид деревного матеріалу (масивна деревина, фанера, деревиноволокнисті плити, деревностружкові плити, деревоволокнисті плити, гнуто клеєні блоки, деревноклейово композиція, плити MDF, OSB), вид інших матеріалів (клейових, лакофарбових, металевих виробів, фурнітура для виробництва м’яких меблів та інше), що приводило і до зміни технології виготовлення виробів з деревини. Технологія змінювалась також залежно від виду підприємства (індивідуальне, серійне, масове), регіональних традицій, досягнень науки та професійної освіти.
Пропонована праця складена програмою курсу «Основи технології виробів з деревини, який читається студентам нетехнологічних спеціальностей. Лісотехнічних навчальних закладів. Тут представлені розділи з організації виробів, та шість розділів, де розглянуто етапи технологічного процесу (розкрій, первинне машинне оброблення, отримання, криволінійних заготовок, склеювання та личкування, надання чистовій заготовці форми деталі та складання). В перспективі передбачається доповнити матеріал такими розділами: опорядження деревини, розрахунок обладнання та контроль якості, що логічно завершать поданий матеріал для вивчення курсу «Основи технології виготовлення виробів з деревини».
У даній роботі не розглядались питання конструювання виробів з деревини, опис конструкцій та принципи роботи обладнання, які розглядаються в інших конкурсах.
З причини розширення і насичення торговою ринку матеріалів, інструменту та обладнання в роботі не подані їх торгові марки, а вказуються лише загальні ознаки та принцип дії. Крім переліку операцій і рекомендованого обладнання, для більшості типів обладнання подана формула для визначення продуктивності і схеми організацій робочих місць. Наприкінці кожного розділу подано питання для самоконтролю та список літературних джерел, що допоможуть у підготовленні та окремі таблиці, які допомагають розкрити суть проблеми, що розглядається.
Виклад матеріалу побудовано таким чином. Що спочатку подається класифікація проведення тієї чи іншої операції (стану), а далі розкриваються способи її виконання. При переліку обладнання для виконання операції сторчаку виконується найпростіший тип, часто з ручною та спеціалізовані, що дає можливість, на думку автора, організувати технологічний процес обладнання деревини від найбільш простих цехів (початківцям до сучасних високопродуктивних за допомогою спеціалізованого обладнання.
2. РОЗРОБКА ТЕХНОЛОГІЧНОГО ПРОЦЕСУ СКЛЕЮВАННЯ БРУСІВ.
2.1. Види склеювання виробів з деревини.
При виготовленні столярно-меблевих виробів застосовують різні способи з «єднання деталей у складальні одиниці і складальних одиниць у вироби. Водночас основним способом отримання не рознімних з «єднань є клейові з «єднання. Такі з «єднання забезпечують високу міцність. У ряді випадків міцність клейового з «єднання вища від міцності деревини й деревинних матеріалів. Крім цього, клейові з'єднання застосовуються не тільки для отримання складальних одиниць при виготовленні виробів, а й для підвищення фізико-механічних характеристик конструктивних елементів виробів раціонального використання малоцінних сировинних матеріалів застосування відходів виробництва для створення нових видів продукції тощо. В цілому у практиці столярно-меблевого виробництва застосовуються такі види склеювання:
а) склеювання заготовок пластями у блоки для отримання деталей більшого перерізу;
б) склеювання заготовок окрайками в щити для отримання деталей великої ширини;
в) склеювання заготовок торцями для одержання деталей потрібної довжини;
г) личкування деталей і складальних одиниць малоцінних деревинних порід личківками з деревини цінних порід або з синтетичних та інших матері.
д) склеювання тонких дерев «яних пластин у плані конструктивні елементи (фанеру) або склеювання одночасним гнуттям для отримання деталей криволінійної форми;
е) з «єднання деталей при їх складанні в складальні одиниці й вироби;
є) виготовлення ДСП, щитів і деталей з стружковим, рейковим, сотовим та іншими заповненнями.
Технологічний процес склеювання виконується в такій послідовності:
• підготовка до склеювання основи (брусків, щитів подрібненої деревини, тонких пластин тощо);
• добір і підготовка клею;
• нанесення клею на основу або змішування його з деревинними матеріалами і формування пакетів;
• запресування пакетів, що склеюються і витримка їх до схоплення клею;
• технологічна витримка склеєних пакетів (деталей).
Оскільки технологічний процес підготовки основи, а також способи й обладнання для запресування пакетів залежить від виду склеювання, їх слід розглянути при вивченні секретних видів склеювання.
2.2. Вимоги до заготовок.
Деревина є пористою структурою з наявністю переважно вузьких каналів у хвойних порід і великих пор і порожнин, що складають до 20% від обсягу деревини. В листяних порід. Унаслідок цього тверда речовина клею в ялини концентрується в дрібних поверхневих порах, а, наприклад, у бука мігрує усередину деревини. Тому виробники клеїв рекомендують для порід деревини з великими порами (дуб, ясен, горіх, в «яз, бук) застосовувати клеї з високим вмістом нелетких речовин і високою в «язкістю, що дозволяє зберегти клеючу речовину в ділянці шва. Сприяє цьому і двобічне нанесення клею.
• Вологість деревини. Набрякання й усадка деревини істотно залежать від її вологості і напрямку волокон. Ігнорування цих факторів може істотно вплинути на міцність шва і точність майбутнього виробу. При склеюванні по пласті деталі рекомендується з «єднувати «серцевину до серцевини, заболонь до заболоні». Через різну усадку проблемним є і склеювання деталей з різних порід дерева. Тому вологість кусків деревини, що склеюються, повинна відрізнятися не більше ніж на 2%. Варто враховувати, що при загальній вологості деревини менш 5% відбувається швидке зневоднювання клею, що призводить до «непроклеювання». Для запобігання цього необхідно збільшувати витрату клею і час пресування. При склеюванні деталей з вологістю більше 15%, навпаки, власна волога деревини збіднює клейовий шар. Вологість деталей, що склеюються, повинна контролюватися! Оптимальна для склеювання вологість деревини близька до 10%.
• Точність і обробка поверхонь деталей, що склеюються. Поверхня, що склеюється, не повинна бути «зализаною», покритою порохом, мати смолисті і жирові забруднення. З цього погляду бажано обробляти плоскі поверхні, що склеюються, не циліндричною, а торцевою фрезою (технологія КОТОІЕ5), тому що при торцевому фрезеруванні не закриваються мікропори, «Клей добре проникає в деревину, і у результаті, міцність з «єднання підвищується. Часовий розрив між фрезеруванням (фугуванням) поверхонь і склеюванням не повинен перевищувати дві години, інакше якість з «єднання погіршується. Особливо важливо це для хвойних порід через переміщення смол до поверхні. При склеюванні щита прямолінійність, площинність і, що дуже важливо, паралельність крайок рейок — половина успіху. Відхилення по товщині рейок повинно складати не більш ±0,2 мм; пласті, що склеюються по поверхні, повинні бути пригнані так, щоб товщина клейових швів не перевищувала 0,2 мм. При неможливості точного припасування і при склеюванні твердих листяних порід бажано застосовувати двобічне нанесення клею. Врахуйте: одна неякісна заготовка в наборі - і весь виріб буде неякісним!
Зубчаті клейові з «єднання виготовляються відповідно до вимог ГОСТ 19 414. Точність формування зубчатих шипів повинна відповідати тринадцятому квалітетові за ГОСТ 6449.1. Параметр шорсткості поверхонь склеювання зубчатих шипів Rm max за ГОСТ 7016 не повинен перевищувати 200 мкм. Звичайна причина виникнення непрямолінійності ламелі при торцевому зрощуванні - неякісне фрезерування мікрошипів (з вини інструмента або з вини верстата). Предметом суперечки часто є наявність зазорів по вершинах зубів при зрощуванні на мікрошип. Досвід показує: якісне зрощування можливе, якщо зазор по вершинах або поличках складеного, але ще не спресованого з «єднання, повинен бути не менше 0,3 мм і може лежати в межах 0,3…0…0,6 мм. Такий зазор буде обраний при пресуванні з рекомендованим нижче зусиллям. А взагалі ж, якщо невеликий видимий зазор, що залишається після пресування, істотно не впливає на якість вашого виробу, не боріться з ним.
2.3.Добір і підготовка клею й способи його нанесення Вибір клею і проектування клейових з «єднань повинно застосовуватися з урахуванням багатьох факторів. Це забезпечує складну міцність клейового з «єднання, стійкість проти дії зовнішнього середовища, гігієнічність тощо. Названі питання дають детального вивчення в комплексі, тобто вони повинні дати технологічним, експлуатаційним і санітарно-гігієнічним вимогам.
Для скорочення тексту при розгляді матеріалу введено позначення для клеїв різних марок.
Умовне позначення клеїв Глютиноні (калогенові) Гл Казеїнові Кз Карбомідоформальдегідні Мд Меламіноформальдегідні Мн Фенолформальдегідні Фн.
ІІолівінілапетатпі Пол.
ІІоліуретапові Пл Перхлорвінілові Пхв.
ІІоліакрплатпі Пт Ефіроцелюлозпі Еф Епоксидні Еп Клеї-розплаїш Кр Клеї на основі синтетичних каучуків Ск Клеї на основі натурального каучуку Нк Латексно-дпсперсіппі Лд Важливе значення при виборі марки клею мають експлуатації клеєних виробів. Адже умови експлуатації майна впливають на рівноважну вологість, а через неї на фізико-механічні властивості клейових з «єднань.
Таблиця 1.
Сфери застосування клеїв Матеріали, що склеюються з деревиною Рекомендовані клеї.
Деревина і деревинні матеріали (фанера, ДВП, ДСП) Мн, Мл, Фн, Пва, Гл, Кз, Лд, та їх модифікація Декоративні паперово-шаруваті пластики Мн, Пва, Мл, Лд модифіковані Пва, Ск Плівки на основі просоченого паперу Мн, Пва, Мл модифіковані наповнювачами, Лд Полімерні плівки й штучна шкіра Лд, Пва, Ск, Мл модифіковані.
Окрайковий пластик Кр Деталі і плівки з полівінілхлориду (ПХВ) Ск, Пхв, Пхв модифікований Ен Полістирол Ец, Пхв модифікований Еп Поліетилен Ск, Пу Поліуретан Пу, Ск, Пхв модифікований Ск Поліефіри Ск, Еу, Па Тканина Лд, Ец, Пва, Пхв, Ск, Кз, Гл Шкіра Лд, Ец, Пва, Ск Гума Ск, Нк Скло й кераміка Еу, Пу, Па Метали Ен, Ск, Фн, модифікований Ск і Пва.
Підготовка клею полягає в приготуванні робочого розчину. Робочий розчин готують відповідна до технологічного режиму.
Технологічним режимом передбачається:
— технічні вимоги до вихідних матеріалів, способи їх транспортування й зберігання, а також марки і вид обладнання, що застосовується;
— зміст технологічного режиму приготування клею і основні показники готового клею, умова його зберігання, кліматичні умови, за яких клей повинен готуватися й зберігатися;
— вимоги безпечності і виробничої санітарії в процесі приготування клею і його застосування.
2.4. Нанесення клею Клей на поверхні конструктивних елементів, що склеюються, наноситься ручним способом пензлем або зануренням, а також за допомогою різних механічних пристроїв. Одновальцьовий верстат для нанесення клею (рис. 1,а) складається з ванни, в якій знаходиться привідний валець і клей. Такий верстат застосовується для нанесення деталі малих розмірів, особливо бруски при їх склеюванні в щити і блоки. Ванна для клею може бути порожнистою. Використовуючи глютиновий клей, вона нагрівається гарячою водою; використовуючи смоляні клеї — охолоджується холодною водою.
Рис. 1. Схеми пристроїв для нанесення клею: а — одновальцьовий; б двовальцьовий з живленням від нижнього вальця; в — пристрій з підйомною перфорованою плитою; г — двовальцьовий з дозуючими валками; д — з донною щілиною Двовальцьовий верстат з живленням під нижнього вальця призначений для нанесення клею на два боки деталі (заготовки) рис. 1б. При цьому довжина заготовки повинна бути меншою від довжини кола верхнього пальця, а заготовки повинен подаватися з розривами. Пристрій з перфорованою плитою (рис. 1.в) використовується для нанесення клею на рейки (ділянки) при їх формуванні в щит. Цеп пристрій має видовжену вапну з клеєм, в якій знаходиться перфорована плита. яка зв «язана і важілем. Для нанесення клею оператор натискає ногою па важіль, піднімаючи цим перфоровану плиту з клею, і вона торкається поверхонь ділянок, змочуючи їх клеєм Двовальцьовий верстат з живленням обох вальній дозуючими вальцями е найдосконалішим. Він призначеним для нанесення клею на дві поверхні деталі будь-якої довжини (рис. 1 г). У даному випадку між вальцем, який наноси п. клен, і дозуючим вальцем утворюється ванночка для клею Зазор між вальцем, який наносить клей і дозуючим, регулюється і визначає кількість клею, що наноситься на поверхню. Використовуються верстати з донною щілиною (рис. 1.д). Для нанесення клею на профільні поверхні використовують розпилювання. Цей спосіб є універсальним.
2.5. Режими склеювання Режим склеювання, як і кожний технологічний режим виконання різних операцій, охоплює сукупність факторів, за яких виконується дана операція. Що стосується режиму склеювання, то він повинен охоплювати такі основні фактори: кількість клею, який наноситься на одиницю поверхні, тиск і температурні умови при пресуванні пакета, час витримування в пресі, температура деревини й приміщення, час витримування до запресовування тощо. Режим склеювання завжди необхідно добирати відповідно до властивостей даного виду клею. Розглянемо основні фактори режиму склеювання.
41. Кількість клею. Кількість клею який наноситься на одиницю площі, визначає товщину клеєного шару і його витрати. Якщо наносити на поверхню більш ніж потрібно клею, якість склеювання погіршується і зростають його витрати, якщо його менш ніж потрібно — товщина клейового шару може бути недостатньою для отримання якісного склеювання. Слід мати на увазі, що на оптимальну кількість клею впливає шорсткість поверхонь склеювання, вид клею та ін.
При склеюванні деревини і деревинних матеріалів витрата клею становить 110 — 350 г/м2 залежно від конкретних умов.
2.Тиск і час запресовування. Тиск при склеювання необхідний для щільного контакту поверхонь, що склеюються і змочування їх клейовим розчином по всій довжині і ширини склеювання. Під піском клей краще проникає у відкриті пори деревини. Цим підвищується площа склеювання. При наявності тиску надлишок нанесеного клею видавлюється і це не сприяє утворенню товстого і водночас неміцного клейового шару. Надлишковий тиск може сприяти видаленню клею й утворенню топких і неміцних плівок.
Рис. 2. Секційний гвинтовий прес: 1 — основа; 2 — нерухома плита; З — рухома плита: 4 — стояк: 5 — гвинт; 6 — верхня траверса Необхідний тиск при запресуванні залежить від виду клею, його в «язкості, якості підготовки поверхонь для склеювання, наявності покоробленості заготовок, що склеюються. Зусилля пресування при склеюванні становить 0,05…2,.5 МПа. Для створення тиску використовуються гвинтові, пневматичні і гідравлічні преси.
При склеюванні необхідно створити такий тиск пресування, який забезпечував би товщину клейового шару 0,1…0,15 мм. використовуючи гвинтові преси (рис.2), необхідно забезпечити відповідний питомий тиск пресування.
Як пристрої для створення потрібного тиску при склеюванні використовуються пневматичні преси. Тиск створюється повітрям, яке подається в пневматичну камеру.
В загальному зусилля при запресуванні залежить від клею, склеюваних матеріалів і коливається в межах 0,5 … 2,5 МІІа.
Рис. 4. Принципова схема гідравлічного перса: 1 — бак для масла: 2- крап: 3 — робочий циліндр;
— плунжер робочого циліндра: 7 — рухома плита; 6 — нерухома плита; сформований пакет щитів: 8 — з «єднувальна труба: 9 — манометр; 10 — магнітний клапан: 11 — поршень насоса: 12 — циліндр насоса: 13 всмоктувальний клапан; 14 всмоктувальна труба.
Час витримування під пресом залежить від швидкості тверднення (схопленим) клею і тих напружень, які можуть виникнути її процесі склеювання. При утворенні внутрішніх напружень, наприклад, якщо склеювати з одночасним гнуттям час витримки під пресом повинен бути більшим. Час схоплення, або тверднення клею залежить від його виду, температури, за якої здійснюється запресовування (з підігріванням або без нього), вологості деревини і температури навколишнього середовища. Загалом, час витримування під тиском пакетів, що склеюються, знаходиться в межах 30 с … 6 год. залежно ні умов склеювання.
Температура деревини і) приміщення та час просочування клею. Температура деревини й приміщення та час витримування заготовок з нанесеним па них клеєм до запресовування зумовлені взаємопов «язаними факторами. Оскільки під час витримування заготовок нанесений на них клей підсихає, то відповідно він підвищує свою в «язкість і через певний час може втратити клеючі властивості. Через не робочий розчин клен слід готувати дещо меншої концентрації, тому що будучи нанесеним па деревину, він частково втрачає вологу, а враховуючи деякий час витримування, набуває потрібного.
Розрізняють два періоди витримування (просочування) заготовок з нанесеним клеєм: відкритий період, коли заготовки з клеєм залишають відкритими, і закритий, коли заготовки з нанесеним клеєм складають у пакети, тобто підготовляють ракети для завантаження в прес. Час відкритого і закритого просочування залежить від температури деревини й навколишнього середовища, а також марки клею. Як правило, температура деревини й приміщення, в якому відбувається процес склеювання, повинна знаходитися в межах 19 … 25 °C.
При склеюванні набуває чинності поняття про клеєснроможність клею. Вона визначається проміжком часу від нанесення клею на поверхню деревини до повної втрати клеючих властивостей. Деякі параметри режиму склеювання, клеєспроможність різних марок клеїв наведені в табл.1.
2.6. Інтенсифікація процесу склеювання.
Інтенсифікація процесу склеювання полягає в прискоренні тверднення кленової плівки, яка нанесена на поверхні заготовок, що склеюються. Процес тверднення клею прискорюється двома способами: хімічним і тепловим.
Хімічний спосіб полягає в додаванні до клейового розчину прискорювачів, при дії яких клей полімеризується, тобто переходить у твердий етап. Прикладом прискорення процесів Вклеювання хімічним способом може бути додавання до вихідного матеріалу для клею хлористого амонію, щавелевої кислоти, молочної кислоти, гасового контакту Петрова (нафтової сульфокислоти), параформу тощо. При гарячому склеюванні карбомідоформальдегідними клеями до них перед використанням додають водний розчин хлористого амонію, а при холодному — розчин щавелевої кислоти.
Інтенсифікацію процесу склеювання тепловим способом можна поділити на три види:
— нагрівання клейоного шару за рахунок тепла попередньо накопиченого (акумульованого) в заготовках до склеювання;
— нагрівання клейового шару через деревину в процесу склеювання;
— безпосереднє підведення теплоти до клейового шару.
Нагрівання клейового шару акумульованою теплотою може бути одностороннім і двостороннім. Цей процес полягає в короткочасному нагріванні заготовок до нанесення на них клею потім нанесення клею і швидке змикання поверхонь. Частіш, застосовується одностороннє нанесення клею. При цьому клей наносять на поверхню ненагрітої заготовки, а потім з «єднуючі. її з нагрітою до температури 150 … 200 °C і швидко запресовують. Тепло передається від нагрітої заготовки до клею і він швидше твердіє. Інші два види нагрівання клейового шару можна здійснити: струмом високої і нормальної частоти, нагріванням плит, між якими знаходяться запресовані заготовки. Останній спосіб широко застосовується на практиці Перспективними в інтенсифікації процесу склеювання І використання струмів високої і низької частот. Розглянемо їх детальніше.
Інтенсифікація склеювання за допомогою струмів високої частоти (СВЧ). Процес нагрівання кленового шару струмами високої частоти грунтується на використанні діелектричних властивостей клею. Для нагрівання клейового шару цим способом заготовки, що склеюються, розміщують між двома металічними пластинами — електродами, на які подається змінний струм високої частоти. Електроди й затиснені між ними заготовки, що склеюються (рис. 7.5). утворюють прообраз конденсатора, в якому пакет, що склеюється є діелектриком, а електроди — обкладками конденсатора. Якщо подавати струм і па обкладки конденсатора, виникає поле, частота якого змінюється аналогічно до зміни електричних зарядів, тобто рівнозначно до частоти. Під дією змінного електричного поля в діелектрику, тобто в клейовому шарі склеюваного пакета, відбувається деформація і коливання молекул, на які затрачується частина енергії, що підводиться до конденсатора. Коливні рухи молекул викликають міжмолекулярне тертя і нагрівання клейового шару, за рахунок чого відбувається його тверднення. Таким чином, електрична енергія витрачається при цьому на переборення сил міжмолекулярного тертя. Для того щоб викликати швидке й інтенсивне нагрівання клею, необхідна висока частота зміни зарядів на обкладках конденсатора. Вона повинна становити 10…30 МГц.
Рис 5. Схема розміщення клейового шару відносно силових Ліній СВЧ: а — паралельне; 6 — перпендикулярне; в — її розсіяному полі.
Інтенсифікація склеюваним струмами нормальної (промислової) частоти. Виділену при проходженні струму теплоту можна підводити до клейового шару різними способами попереднім нагріванням поверхонь, що склеюються (акумульованою теплотою), виділенням теплоти провідником, що знаходиться в клейовому шві, прогріванням клейового шару за рахунок проходження через нього струму, прогріванням кондуктивним і радіаційним способами.
Названі способи забезпечують різну ефективність. Так, при використанні способу акумульованої теплоти поверхні, що склеюються, попередньо нагріваються контактом з електронагрівачем. Оптимальна температура нагрівача становить 200 °C. час прогрівання — 6 хв. За температур, вищих від оптимальних, поверхня деревини підгоряє. На нагріті таким способом поверхні заготовок швидко наноситься клей і вони з'єднуються під пресом. Можна нагрівати тільки одну з поверхонь, що склеюються. При цьому уникається небезпеки передчасного загусання нанесеного клею.
Нагрівання клею електричним провідником полягає втому, на нанесену поверхню заготовки клейового шару накладають електропровідну металеву сітку. Поверхні заготовок стискаються і склеюваний блок запресовується. Металева сітка виступаючими кінцями з «єднується з джерелом струму промислової частоти.
Аналогічним процесом можна прискорювати процес клейового шару, якщо його зробити електропровідним. Для цього до клею додають сажу, яка робить його електропровідним. Слід зазначити, що додавання до клею які дещо знижує його клеючі властивості. Надмірна кількість іржі призводить до повної втрати клеєм клеючих властивостей. розглянутий спосіб інтенсифікації склеювання безпосереднім нагріванням клейового шару застосовується при виготовленні склєнних ферм, балок, арок тощо.
За кондуктивного (електроконтактного) нагрівання теплота від нагрівача до клейового шару передається через деревину. Такий спосіб ефективний при склеюванні тонких шарів деревини, особливо при личкуванні. У цьому випадку нагрівник являє собою топку металеву пластину, по якій проходить струм. Якщо цю пластину контактувати, зокрема з личкуванням, то вона нагрівається і через неї передається лота до клейового шару.
Клейовий шар радіаційним способом нагрівається тенами через деревину або деревинні матеріали.
Оскільки інтенсифікація процесів склеювання за рахунок перетворення електричної енергії в теплову відбувається з відповідними втратами, то відсоток використання цієї теплоти буде різним: при використанні СВЧ — 40%, опором в клейовому шарі — 10%, кондуктивним способом — 20% і радіацією ТЕН — 25%.
Використовуючи різні способи інтенсифікації процесів склеювання, необхідно дотримуватися відповідних правил техніки безпеки. Особливо це стосується використання струми високої частоти. З метою безпечної роботи при використання кондуктивного способу нагрівання вихідна робоча установки не повідна перевищувати 12 В.
2.7. Склеювання брусів При виготовленні столярно-меблевих виробів широко застосовується склеювання брусків у блоки по товщині, ширині, довжині. Це зумовлено необхідністю переробки і раціонального використання низькосортної та тонкомірної пилопродукції. Оскільки в столярно-меблевих виробах, зокрема, у віконних, дверних блоках, стільцях та інших виробах, які через значні розміри, в ряді випадків, неможливо виготовити з цільної деревини, то застосовується склеювання. Склеювання тонким короткомірних матеріалів дає можливість одержати заготовки погрібних розмірів, з кращими фізико-механічними властивостями і, головне, більш раціонально використати деревину.
Основними технологічними операціями при склеюванні брусків с добирання матеріалу, формування чорнових заготовок, формування чистових заготовок за розмірами, шорсткість поверхонь і розміщенням річних кілець, нанесення клейового розчину на одну або дві склеювані поверхні, формування пакетів пресування з витримкою до схоплення клею й технологічна витримка.
До заготовок, що готуються до склеювання, ставляться відповідні вимоги. Вони особливо високі для заготовок, які використовуються для виготовлення несучих конструктивних елементів виробів. Це здійснюється відповідно до діючих стандартів. Вимоги до якості деревини в різних шарах клеєних конструкцій. Ці стандарти передбачають три категорії якості деревини, що застосовується в розтягненій і стисненій зонах склеєних конструкцій.
Межа міцності деревини, що застосовується при виготовленні несучих клеєних конструкцій, повинна бути не меншою ніж, МПа:
— розтяг — 55,.
згин — 50,.
стиск — 30,.
— сколювання —4.
300 мкм.
У технології виробництва необхідно також враховувати забезпечення потрібної якості клеєних конструкцій, зокрема належну їх формостійкість. Зокрема для попередження можливої зміни форми склеєних щитів їх виготовляють з брусків шириною 15 … 70 мм. При використанні в клеєних інструкціях деревини різних порід можлива також поява симетричних внутрішніх напружень. Тому пропонується склеювані поверхні щільної деревини робити більш шорсткими порівняно з поверхнями м «яких порід деревини. Встановлено, що шорсткіша поверхня, будучи склеєною, стає податливішою знижує внутрішні напруження.
Бруски склеюються в блоки по товщині й ширині за допомогою спеціальних пристосувань (струбцин, хомутів та ін.) пресів гвинтових, пневматичних і гідравлічних.
При склеюванні заготовок з щільної деревини по пластах окрайках і торцях застосовується обладнання безперервної або періодичної дії. Технологічний процес склеювання заготовок по пластях (товщині) складається з обробки їх по товщині, нанесенні на склеювані поверхні клею, формуванні пакетів пресуванні і технологічній витримці після склеювання.
Склеюють бруски у блоки по довжині, як правило на зубчастий тип. Так, з «єднання за міцністю поділяються на дві категорії: міцністю не менше як 75% і понад 60% порівняно з масивною деревиною. Зусилля при склеюванні зубчастого типа повинно бути: для хвойних порід Р = 20 і, Мпа, а листяних — на 20% більше ніж хвойних де t — крок шипа, мм. Для забезпечення самогальмування шипів при складанні нахил їх повинен бути не меншим за 1:8. а необхідний час пресування при складанні не меншим за 2 с. Склеюючи на зубчастий шин торцьове зусилля складання можна здійснювати за двом, схемами:
— при виготовленні безперервної стрічки з «єднаних заготовок у момент їх стискування проходить затискання — спеціальним гальмом попередньої заготовки і силова подача наступної за нею;
— швидке переміщення з достатнім зусиллям заготовок на початку входу в склеюючий пристрій і сповільнення їх переміщення на виході з пристрою.
У лініях безперервного склеювання заготовок по довжині виходить блок нескінченної довжини. Його по виході з липи ріжуть на мірні відрізки. Отримані мірні відрізки калібрують на поздовжньо-фрезерувальних верстатах і, якщо необхідно повторно склеюють по окрайці в щит. Прикладом безперервного склеювання заготовок по довжині на зубчастий шип може бути схема лінії, показана на рис. 6.
Рис. 6. Схема лінії склеювання заготовок по довжині на зубчастий шин: 1 — пульт: 2,3 — формування зубчастих шипів; 4 — з «єднання шипів; 5 — запресування; б — торцювання по довжині; 7 — приймальний роликовий стіл.
Для склеювання брусків по крайках використовуються різні щитоскладальні пристрої безперервної дії. Щитоскладальні верстати безперервної дії поділяються на два типи: за характером набору заготовок у щиті і напрямом переміщення їх відносно склеюваних поверхонь. Підготовка заготовок до склеювання полягає в обробці окрайків. У випадку використання заготовок, які за товщиною значно різняться між собою, необхідна також обробка по товщині.
Складальні верстати періодичної дії (рис. 6.) мають пневматичний притискний механізм з зусиллям до 20 кН.
За схемою (рис.6а) заготовки 1 з нанесеним на склеювані поверхні клеєм вкладаються на стіл одна до одної так, щоб їх торці в суміжних смугах були на різному рівні. Вкладені заготовки базують притискним валиком 2 і подають запресовуючим пристроєм 3 до електродів СВЧ 4, де відбувається прискорене склеювання. Після склеювання щит подається до пилки 5 і розрізається впоперек па мірні відрізки. Готові щити обробляються по товщині на рейсмусових або на широкострічкових шліфувальних верстатах.
Виготовлення щитів за схемою (рис. 7б) здійснюється таким чином. Заготовки 1, проходячи клеєвий пристрій 2 полаються до упора кінцевого вимикача 4 і пилкою торцюються на потрібний розмір. Далі заготовки подаються до затискного пристрою З і притискних шин 5, де сповільнюється їх рух, забезпечується потрібний тиск пресування і базування. При поступовому русі сформованого щита він потрапляє в зону дії СВЧ 6, склеюється, а пилкою 7 розрізається вздовж волоком па мірні відрізки.
а б Рис. 7. Принципові схеми пристроїв для склеювання заготовок по окрайках и щити: а — склеювання паралельно переміщенню: 1 заготовка; 2 — притискні валики; З — механізм подачі і стискання; 4 — поле СВЧ; 5 — пилка, 6 — склеєний щит; б — склеювання перпендикулярно переміщенню: 1 — заготовка; 2 — механізм подачі і нанесення клею; 3 — механізм стискання; 4 — кінцевий вимикач; 5 — затискний пристрій; 6 — поле СВЧ, 7 — пилка.
Бруски склеюються в боки по товщині, ширині і довжині з використанням різних способів інтенсифікації тверднення клею або без них. При цьому необхідно дотримуватися норм відкритого і закритого просочування клею.
При виготовленні будівельних конструкцій вихідні заготовки спочатку склеюють по довжині, а потім по товщині; в меблевому виробництві, через менші поперечні розміри заготовок, склеювання проводять по довжині.
В столярному виробництві щити використовуються для виготовлення дверей, щитового паркету, паркетних дощок тощо.
2.8. Сучасне обладнання для склеювання брусків (рейок) в щити.
Прохідні клеїльні преси моделі Dimter ProfiPress L 2500 НF, які недавно появилися на ринку, користуються винятковим попитом. Мова йде про сучасні надійні установки, які забезпечують високу рентабельність при виготовленні щитових заготовок навіть малими партіями. Високопродуктивна і гнучка технологія пресування із застосуванням струмів високої частоти (СВЧ) для затвердіння клею дуже популярна нині у виробництві клеєних щитів з масиву, Надії на те, що нова техніка може поліпшити якість продукції, в остаточному підсумку виправдалися сповна. Виробники щитів особливо задоволені бездоганною міцністю клейових швів, якої вдається досягти лише при затвердінні клею в полі СВЧ. І якщо колись саме розбіжність по швах була основною причиною повернення проданих щитів, то тепер про дорогі рекламації на підприємстві практично забули.
Переналаштування на інші розміри щита — щоб уникнути невиправданих літрах дорогої сировини зводяться до найпростішого регулювання преса на потрібну товщину матеріалу. На всі пов «язані з цим дії ще приблизно 60 секунд, тоді як колись вони займали цілих 8 хвилин. При зміні ширини щита жодного втручання оператора не потрібно: підрівнювання рейок відбувається автоматично, по пересувному подовжньому упорі. Завдяки цьому навіть виробництво одиничних виробів стало рентабельним.
З упровадженням моделі ProfiPress L 2500 НF помітно підвищилася і якість рейкових щитів. Цьому зокрема сприяє використання пневматичних притисків, що забезпечують рівномірний розподіл тиску — як верхнього, так і бічного — по всій поверхні щита. У такий спосіб унеможливлюється зсув рейок у пакеті, а отже, зменшуються витрати на наступне калібрування щитів, надійніше дотримуються допуски.
Нині лінія ProfiPress L, на підприємстві НВS випускає за зміну до 400 кв. м щитових заготовок, виготовлених малими партіями. Це стало можливим завдяки істотному зменшенню обсягу підготовчо-заключних робіт і витрат на шліфування, а також більш швидкому затвердінню клею.