Аналіз існуючих методів ресурсозбереження та енергозбереження на установках первинної переробки нафти
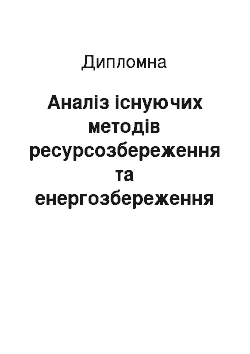
Бензин сьогодні використовується для автомобільних двигунів і для двигунів гвинтомоторних літаків (карбюраторних двигунів). Під час роботи такого двигуна горюча суміш парів бензину з повітрям надходить у циліндр двигуна, стискається у ньому поршнем і підпалюється від запалювальної свічки (іскри). Всередині циліндра продукти, що утворилися під час горіння парів бензину, розширюються і рухають… Читати ще >
Аналіз існуючих методів ресурсозбереження та енергозбереження на установках первинної переробки нафти (реферат, курсова, диплом, контрольна)
Вступ
переробка нафта октановий
Мета кваліфікаційної роботи — аналіз існуючих методів ресурсозбереження та енергозбереження на установках первинної переробки нафти.
Об'єкт дослідження — методи збереження ресурсів та енергоносіїв в первинній переробці нафти.
Предмет дослідження — збереження пари, води, теплоенергії, електроенергії.
Актуальність роботи — нафти у світі залишилося за підрахунками на тридцять років, тому актуальним питанням є покращення збереження ресурсів та енергоносіїв. У роботі розглянуті основні методи збереження нафти та нафтопродуктів, пари, води, теплота енергоресурсів.
Хімічний комплекс — один з провідних у структурі сучасної економіки. Від його розвитку, як і від розвитку машинобудування, значною мірою залежить науково-технічний прогрес. Комплекс хімічних виробництв виготовляє продукцію для всіх основних галузей промисловості, транспорту, сільського господарства, оборони, побутового обслуговування та інших сфер діяльності. Він істотно впливає на рівень і темпи розвитку економіки в цілому.
Хімічна і нафтохімічна промисловість займає важливе місце в сучасному промисловому потенціалі України. Її частка в ВВП складає 5,5%, в загальному товарообігу промислової продукції - 6,4%, експорті промислової продукції - 12,5%. Проте потенційні можливості галузі стосовно нарощування обсягів конкурентоспроможного товарного виробництва значно вищі. Діючі хімічні і нафтохімічні підприємства здатні (за умови створення сприятливих умов для розвитку імпортозаміщуючих виробництв) поставляти до 75% хімічної продукції споживчого і промислового призначення, яку споживає внутрішній товарний ринок. Однак, сьогодні ця доля складає лише 30%, а протягом останніх трьох років вона скоротилась на третину. Суттєве скорочення споживання хімічної продукції відбулось також і в проміжному промисловому споживанні - до 8%.
Стимулювання розвитку хімічної галузі здатне призвести до ланцюгової реакції для наростаючого розвитку багатьох споживаючих галузей промисловості через забезпечення їх сучасними матеріалами і сировиною. Галузь має один з найвищих рейтингів міжгалузевого споживання.
За час кризи відбулись значні структурні зміни в попиті. Традиційно місткі споживачі хімічної продукції значно знизили її споживання через падіння обсягів виробництва, низької покупної спроможності, що стало наслідком дефіциту оборотних коштів і недоступності кредитних ресурсів. Так, хімічна промисловість протягом останніх 10 років знизила частку проміжного споживання на 5,5%, машинобудування — на 7,3%, легка промисловість — на 4,5%, вся промисловість — на 8%, що свідчить про посилення ролі непромислового споживання з одночасним послабленням ролі пріоритетних галузей-споживачів, зокрема, легкої промисловості і машинобудування. Сприяти підвищенню попиту останніх на хімічну продукцію повинна державна підтримка розвитку пріоритетних галузей економіки.
Україна має великі потенційні можливості для розвитку хімічної промисловості. На початку 90-х років вона налічувала понад 80 великих підприємств. Особливістю галузі є те, що в структурі постачання сировини, матеріалів і напівфабрикатів близько 60— 70% їх обсягу становили поставки за зв’язками по кооперації з підприємствами республік колишнього Радянського Союзу. У цих же регіонах реалізовувалася значна частка виробленої продукції галузі.
Крім потужних підприємств, галузь характеризується наявністю суттєвого наукового потенціалу — великої кількості науково-дослідних і проектно-конструкторських організацій, серед яких і такі, що вели важливі розробки науково-технічних проблем хімічної технології в колишньому Радянському Союзі[1].
Обсяг первинної переробки нафти в Україні за січень-листопад 2012 р. у порівнянні з аналогічним періодом 2011 р. зменшився на 50% - до 4,1 млн т. Про це повідомляє Державна служба статистики (Держстат).
У листопаді обсяг первинної переробки склав 0,3 млн т, що на 6,6% більше, ніж місяцем раніше, і на 55,5% менше, ніж роком раніше.
Виробництво моторного бензину за 11 міс. знизилося на 41,2% - до 1 млн 512 тис. т. Виробництво дизельного палива скоротилося на 47% - до 1 млн 285 тис. т, мазуту — на 63,9%, до 710 тис. т.
Обсяг видобутку сирої нафти в Україні за 7 місяців 2012 р. зменшився на 5,1% - до 1,358 млн т. Видобуток сирої нафти в липні склав 195 тис. т, що на 4,5% більше, ніж місяцем раніше, і на 5% менше, ніж роком раніше.
Україна за перше півріччя 2012 р. зменшила первинну переробку нафти більш, ніж на 40%. Випуск бензину скоротився за 6 міс. на 31% - до 980,2 тис. т, дизпалива — на 42,1%, до 790,3 тис. т, мазуту — на 54,7%, до 490,3 тис. т. Видобуток нафти з газовим конденсатом в Україні в I півріччі 2012 р. скоротився на 2,9% - до 1,63 млн т[2].
Відзначимо, обсяг первинної переробки нафти в Україні в минулому році зменшився на 18,8% - до 6,7 млн?? т. Виробництво моторного бензину за цей період знизилося на 1,3% - до 2 835 000 т. Виробництво дизельного палива зменшилося на 28, 2% - до 2 664 000 т, мазуту — на 11%, до 2,148млн т. Обсяг видобутку сирої нафти в Україні за січень-грудень зменшився на 5,9% - до 2,424 млн т.
Первинна переробка нафти складається з двох етапів: підготовки нафти до переробки (знесолення та зневоднення на установках ЕЛОУ) та переробка на установках атмосферній трубчатці (АТ), атмосферно-вакуумній трубчатці (АВТ) і ректифікаційних колонах. При цьому отримують світлі нафтопродукти прямої перегонки (бензин, дизельне паливо та ін.), газ, мазут. Отримані світлі нафтопродукти не відповідають вимогам до високоякісних товарних нафтопродуктів і, як правило, підлягають подальшій переробці (каталітичному риформінгу, гідроочистці та ін.).
З метою скорочення матеріальних витрат на будівництво установок і експлуатаційних витрат у даний час широко використовуються комбіновані установки, які включають у себе електрознесолювальну установку, установку АВТ і установку для вторинної перегонки бензину.
1. Існуючі установки первинної переробки нафти
1.1 Установка електрознесолення нафти
Нафта, яка надходить на нафтопереробні заводи, як правило, містить воду і розчинені солі. При великому вмісті води в нафті збільшується тиск в апаратурі установок, знижується їх продуктивність, додатково витрачаються паливно-енергетичні ресурси. Наявність в нафті солей, особливо хлоридів, призводить до відкладення їх у трубах теплообмінників і печей, знижує коефіцієнт теплопередачі. Хлориди можуть гідролізуватися з утворенням хлоридної кислоти, що призводить до корозії обладнання.
Для видалення солей та води нафту перед переробкою піддають знесоленню і зневодненню на електрознесолювальних установках (ЕЛОУ) (рис. 1.1).
Рис. 1.1. Схема електрознесолювальної установки: 1, 12 — облікові пункти; 2, 3 — теплообмінники; 4 — нагрівник; 5 — електродегідратор І ступеня; 6, 8, 13, 15, 16, 19 — насоси; 7 — електродегідратор ІІ ступеня; 9, 11, 17 — ємності; 10 — нагрівник води; 18 — оглядовий ліхтар.І - сира нафта для електродегідрування; ІІ - очищена, знесолена нафта; ІІІ-м'ята пара; ІV — вода; V — луг; VІ - конденсат; VІІ - пара.
Для виділення солей з нафти використовують спосіб, який поєднує їх термічне відстоювання з обробкою в електричному полі. Головним апаратом електрознесолювальної установки є електродегідратор — ємність, забезпечена електродами, до яких підводиться змінний струм високої напруги. Напруга подається до електродів від двох підвищувальних трансформаторів і складає між електродами 15−33 Кв. Сировину вводять в електродегідратор через вертикально вмонтовану по осі апарата трубу, яка на половині висоти дегідратора закінчується розподільною головкою. Емульсія нафти і води подається у вигляді тонкого віялоподібного струменя. Оброблена нафта відводиться в центрі верхнього днища електродегідратора, а вода і солі - через нижнє днище.
Вода у нафті міститься у вигляді емульсій. Для руйнування емульсій використовують спеціальні деемульгатори, які послаблюють структурно-механічну міцність шарів, які обволікають краплі води.
При потраплянні нафтової емульсії в змінне електричне поле заряджені негативно частинки води починають пересуватися всередині краплі. При зміні полярності на електродах відбувається зміна конфігурації краплі, спостерігається рух окремих крапель до позитивно зарядженого електрода. Краплі зіштовхуються одна з одною, зливаються у більші й осаджуються. Солі, які є в нафті, разом з промивною водою відводять з установки. В табл.1.1 наведений матеріальний баланс електрознесолювальної установки.
Таблиця 1.1. Матеріальний баланс електрознесолювальної установки[3]
Статті балансу | І ступінь | ІІ ступінь | ||||
тис. т/рік | % (мас.) | тис. т/рік | % (мас.) | |||
Прихід | ||||||
Нафта | ||||||
Сира | 2050,0 | 95,0 | ||||
Знесолена з І ступеня | 2010,0 | 93,4 | ||||
Вода | 111,4 | 5,0 | 141,4 | 6,6 | ||
Продовження табл. 1.1 | ||||||
Разом | 2161,4 | 100,0 | 2151,4 | 100,0 | ||
Витрати | ||||||
Знесолена нафта | 2010,0 | 93,0 | 2000,0 | 92,97 | ||
Розчин солей | 141,4 | 6,54 | 141,4 | 6,57 | ||
Втрати | 10,0 | 0,46 | 10,0 | 0,46 | ||
Разом | 2161,4 | 100,0 | 2151,4 | 100,0 | ||
Примітка. Вміст води і солей в нафті: | ||||||
Вода, % (мас.) | Солі, мг/дм3 | Вода, % (мас.) | Солі, мг/дм3 | |||
Іступінь | ІІ ступінь | |||||
На вході | 2,0 | 5000,0 | На вході | 0,5 | 250,0 | |
На виході | 0,5 | 250,0 | На виході | 0,5 | 20,0 | |
На рис. 1.2. наведена схема утилізації теплоти стоків електрознесолювальної установки.
Рис. 1.2. Схема утилізації теплоти стоків електрознесолювальної установки до впровадження (а) та після нього (б):1, 2 — електродегідратори; 3 — теплообмінник.І, ІІ - сира нафта; ІІІ, ІV — стоки ЕЛОУ; V — вода для підігріву; VІ - нагріта вода.
1.2 Комбінована установка ЕЛОУ-АВТ-6
Комбінована атмосферно-вакуумна установка ЕЛОУ-АВТ-6 має такі блоки: знесолення нафти, атмосферну перегонку нафти, вакуумну перегонку мазуту та вторинну перегонку бензину.
Нафта І насосами 1, 2 (рис. 1.3) направляють двома потоками в теплообмінники 3 — 6, де її нагрівають за рахунок регенерації тепла верхнього і середнього циркулюючих зрошень колони 54 (К-10) і І і ІІ циркулюючих зрошень колони 20 (К-2). Нагріта до температури 150? С нафта надходить велектродегідраториІ ступені 7, 8 (Е-1−4/1) і потім ІІ ступені 9, 10 (Е-2−4/2).
Рис. 1.3. Принципова технологічна схема установки ЕЛОУ-АВТ-6: 1, 2, 17, 18, 26, 40, 41, 43, 53 — насоси; 3−6, 11−14, 24, 25, 28, 31, 37, 39, 52, 55, 58−65 — теплообмінники; 7−10 — електродегідратори; 15, 20−23, 36, 38, 50, 51, 54 — колони; 16, 19, 42, 57 — печі; 27, 30, 41, 46, 49 — повітряні конденсатори; 29, 32, 34, 45, 47, 48 — ємності; 33 — холодильник; 56 — паровий ежектор. І - сира нафта; ІІ - знесолена нафта в колону К-1; ІІІ - водяна пара; ІV — газова головка; V — фракція п.к.? 62? С; VІ - в атмосферу; VІІ - в колону К-2; VІІІ - фракція 350−500 ?С; ІХ — гудрон; Х — фракція 180−220 ?С; ХІ - фракція 220−280 ?С; ХІІ - фракція 280−350 ?С; ХІІІ - фракція 62−140 ?С; ХІV — фракція 140−180 ?С.
Зневоднена і знесолена нафта ІІ, після проходження через теплообмінники 11 — 14 з температурою 210? С надходить в колону 15 (К-1).
З верху колони К-1 головний погон відводять в повітряний конденсатор 27 і потім в холодильник 28 і в ємність 29. Частину конденсату повертають в К-1 в якості гострого зрошення, а надлишок надходить в ємність 34. З низу К-1 нафту без бензину насосами 17, 18 подають через піч 19 (П-1). Із печі частинапотоку з температурою 360? С надходить в колону 20 (К-2), друга частина («гарячий струмінь») з температурою 340? С повертається в колону К-1.
З верху колони К-2 пари фракції 85−180 ?С та водяні пари відводять в повітряний конденсатор 30 і холодильник 31 та після конденсації для відстою води в ємність 32. Частину конденсату фракції 85−180 ?С подають на верх колони, а балансовий надлишок — в ємність 34.
Фракції 180−220 ?С, 220−280 ?С, 280−350 ?С, відводять як основні погони через відпарні колони 21 (К-6), 22 (К-7) та 23 (К-9), холодильники 24, 25 та 39 в резервуари проміжного парку. З низу колони К-2 мазут насосом 26 подають в піч 57 (П-3), звідки він з температурою 410? С надходить у вакуумну колону 54 (К-10). У нижню частину цієї колони подається перегріта пара з температурою 410? С, під тиском 1,0 МПа, який разом з газами розкладаннязверху надходить в поверхневий конденсатор 55, а водяна пара та невідконденсовані гази відсмоктують пароежекторними вакуумними насосами 56. Температуру в колоні К-10 підтримують за допомогою верхнього, середнього та нижнього циркулюючих зрошень. З колони К-10 у вигляді бокового погону відводять фракцію 350−500 ?С (VІІІ). Гудрон з низу колони К-10 забирають насосом і через ряд теплообмінників 61 та холодильник 63 відкачують з установки. Із колони К-2 фракцію п.к. — 180? С подають в колонустабілізатор 36 (К-8). З верху колони К-8 головного погону, а також гази С1 — С4 та Н2S надходять у конденсатор 33, потім в ємність 35. Частину конденсату головного погону у вигляді зрошення подають в колону К-8, невідконденсовані гази надходять з ємності 35 в паливну частину, а балансовий надлишок головного погону відводять у вигляді рідкої головки в резервуари проміжного парку.
З низу колони К-8 стабільна фракція п.к. — 180? С надходить в колону К-3. З верху колони К-3 пари фракції п.к. — 105? С відводять через конденсатор повітряного охолодження 44 в ємність 45, звідки частину фракції подають в колону К-3 у вигляді гострого зрошення, а балансовий надлишок — в колону К-4. З низу колони К-3 відводять фракцію 105−180 ?С та направляють в колону 51 (К-5).
З верху колони 50 (К-4) через повітряний конденсатор 45 пари фракції п.к. — 62? С відводять в ємність 47. З цієї ємності частину фракції п.к. — 62? С подають у вигляді гострого зрошення в колону К-4, і балансовий надлишок V надходить на залуговування і далі після відстоювання його виводять з установки.
З низу колони К-4 фракцію 62−105 ?С через повітряній холодильник 62і кінцевий холодильник 64 відводять з установки в резервуари проміжного парку.
Пари фракції 105−140 ?С з верху колони К-5 відводять в ємність 48 через повітряний конденсатор 49. Із ємності 48 частину фракції повертають у вигляді гострого зрошування в колону К-5, і балансовий надлишок після холодильника 52 направляють в резервуари проміжного парку в суміші з фракцією 62−105 ?С. Продукт із нижньої частини колони К-5 (фракція 140−180 ?С) через теплообмінник 66 направляють на залуговування і водне промивання. Теплота для процесу ректифікації в колонах К-3, К-4, К-5 та К-8 з'єднується потоками, циркулюючими через піч 42 (П-2)[4]. В табл. 1.2 приведені основні дані енергоспоживання установкою ЕЛОУ-АВТ-6.
Таблиця 1.2. Енергоспоживання на установці ЕЛОУ-АВТ-6
Енергоресурси | Витрати | ||||
Годинні | Річні | Питомі | |||
Паливо: | т | тис.т | тис.ту.п. | кг/у. п./т | |
рідке | 17,70 | 145,00 | 198,70 | 33,15 | |
газоподібне | 4,40 | 36,00 | 54,00 | 8,95 | |
Разом | 252,70 | 42,10 | |||
Теплоенергія | т | Тис.т | Тис.ГДж | кДж/т | |
Пара тиском 1,0 МПа, | 33,72 | 262,51 | 771,50 | 128,23 | |
у тому числі: | |||||
попередній евапоратор К-1 | 3,72 | 30,40 | 89,50 | ||
атмосферна колона К-2 | 11,70 | 95,64 | 281,00 | ||
відпарнаколона К-6 | 1,50 | 12,24 | 281,00 | ||
відпарнаколона К-7 | 0,46 | 3,75 | 10,90 | ||
відпарнаколона К-9 | 0,67 | 5,47 | 16,00 | ||
ежектор | 4,60 | 37,50 | 110,50 | ||
деаератор | 2,64 | 8,51 | 25,20 | ||
Пара тиском 0,3 МПа | 6,42 | 52,54 | 220,70 | 36,78 | |
у тому числі: | |||||
вакуумна колона К-10 | 5,68 | 46,50 | 185,30 | ||
відпарнаколона К-11 | 0,72 | 5,88 | 24,70 | ||
Інше | 0,02 | 0,16 | 0,70 | ||
Теплофікаційна вода 150−70 ?С | 21,80 | 3,99 | |||
Разом | |||||
Вироблення пари в котлахутилізаторах | 32,80 | 251,90 | |||
Електроенергія | кВт | тис.кВт•год | тис.ту.п | кВт•год/т | |
Електрод. насосів та апаратів повіт. охолод. | 10 358,00 | 47 448,00 | 7,90 | ||
Електродегідратори | 1200,00 | 5150,00 | 0,86 | ||
Освітлення | 180,00 | 615,00 | 0,10 | ||
Інше | 99,00 | 414,00 | 23,52 | 0,08 | |
Разом | 14 036,00 | 69 180,00 | 23,52 | ||
Хімічно очищена вода, тис. м3 | 314,50 | 2,50 | 0,43 | ||
Стисле повітря, тис. м3 | 1630,00 | 4,00 | 0,69 | ||
Всього енергоресурсів | 317,20 | 52,90 | |||
* В чисельнику теплоенергія в ГДж, в знаменнику — в тис.ту.п. | |||||
**В чисельнику теплоенергія в кДж, в знаменнику — в кг у.п. | |||||
***В чисельнику електроенергія в кВт•год, в знаменнику — в кг у.п. | |||||
Тис.т.у.п. — тисяч тонн умовного палива У технологічній схемі установки передбачена регенерація теплоти для нагрівання сирої нафти, яка подається на переробку, за рахунок теплоти нагрітих продуктових потоків (рис. 1.4)
Рис. 1.4. Графік нагрівання сирої нафти на установці ЕЛОУ-АВТ-6: t1 — сира нафта; t2-t6 — теплообмінники Т-2 — Т-6; t7 — до електродегідратора; t8 — після електродегідратора; t9, t10 — після теплообмінників Т-7 і Т-10.
Надходить нафта за температури 10? С, а потім її нагрівають до 135? С перед електродегідратором і до 213? С — перед колоною К-1. Теплоємність нафти збільшується від 6,76 до 212,1 ГДж/год перед електродегідраторами та до 348,6 ГДж/год перед колоною К-1.
У технологічній схемі установки ЕЛОУ-АВТ-6 значна кількість нафтопродуктів охолоджкється водою в теплообмінниках і повітрям в апаратах повітряного охолодження (табл.1.3).
Таблиця 1.3. Охолодження нафтопродуктів
Показники | Охолодження | ||
повітрям | водою | ||
Кількість охолоджуваних нафтопродуктів, т/год | 2398,3 | 510,4 | |
Витрати: | |||
повітря, тис. м3/год | 12 081,0 | ||
води, м3/год | 2190,7 | ||
теплове навантаження, ГДж/год | 446,2 | 82,3 | |
поверхня нагрівання, м2 | |||
Наприклад, в повітряному холодильнику 27 (рис. 1.5) охолоджують пари бензину від 105 до 60? С при тепловому навантаженні 89 ГДж/год, а в теплообміннику 30 відповідно з 103 до 54? С — при тепловому навантаженні 101,8 ГДж/год.
Теплоту конденсації бензинових парів можна використовувати для нагрівання теплофікаційної води.
Рис. 1.5. Схема теплообміну продуктових потоків установки первинної переробки нафти АВТ до реконструкції (а) та після неї (б):1 — теплообмінники; 2 — електродегідратори. І - гудрон; ІІ - мазут; ІІІ - перший вакуумний погон; ІV, V — другий вакуумний погон; VІ, VІІ - перше і друге циркулююче зрошення К-2; VІІІ, ІХ — перше і друге циркулююче зрошення К-5; Х, ХІ - дизпаливо; ХІІ - вакуумна фракція; ХІІІ - теплоносій; ХІV — сира нафта; ХV — нагріта нафта.
На багатьох нафтопереробних заводах для покращення регенерації теплоти проведена робота з переобв’язки теплообмінної апаратури, що дозволило підвищити температуру сировини, яка надходить в технологічну піч, і знизити витрати палива.
Реконструкціятеплообміну продуктових потоків установки первинної переробки нафти АВТ, призвела до того, що температура сировини перед піччю піднялася з 180 до 235? С, за рахунок чого зекономлено 17,6 тис. т у. п./рік.
На установці ЕЛОУ-АВТ-6 для нагрівання нафтопродуктів використовуються три технологічні печі, технічні дані яких наведені в табл.1.4.
Таблиця 1.4. Характеристика печей установки ЕЛОУ-АВТ-6
Показники | П-1 | П-2 | П-3 | Всього | ||
1секція | 2 і 5 секція | |||||
Теплопрод., ГДж/год | 105,0 | 159,6*2 | 21,9 | 121,8 | 627,9 | |
Витрати палива, т/год | 3,6 | 5,5 | 2,9 | 4,6 | 16,6 | |
Продукт | Гарячий струмінь | Відбензова-на нафта | Стабільний бензин, фракція 85−180 ?С | Мазут | ||
Продукту | 290,2 | 672,5 | 103,5 | 122,5 | 1188,7 | |
Водяного пару | 3,7 | 14,3 | 18,0 | |||
Температура, ?С | ||||||
На вході у піч | ||||||
На виході з печі | ||||||
Температура пару, ?С | ||||||
На вході у піч | ||||||
На виході з печі | ||||||
Темп. димових газів, ?С | ||||||
На перевалі | ||||||
На виході з конвекції | ||||||
Поверхня нагрів., м2, | ||||||
у тому числі секції: | ||||||
радіації | ||||||
конвекції | ||||||
паронагрівника | ||||||
Для утилізації теплоти відхідних газів за технологічними печами встановлено два котли-утилізатори КУ-125. Схема установки котлів-утилізаторів наведена на рис. 1.6.
Рис. 1.6. Схема компоновки котла-утилізатора КУ-125 для утилізації газів технологічних печей установки АВТ-6:1 — барабан; 2 — корпус котла; 3 — пароперегрівник; 4 — димосос; 5 — димова труба.
Загальні відомості з витрат паливно-енергетичних ресурсів на установках первинної переробки нафти наведені в табл.1.5.
Таблиця 1.5. Витрати паливно-енергетичних ресурсів на установках первинної переробки нафти (на 1 т нафти) [5]
Установка | Об'єм переробки нафти, тис. т | Норми витрат | ||||
Палива, кг у. п. | Тепло-енергії, тис. кДж | Електро-енергії, кВт•год | Всього, кг у. п. | |||
ЕЛОУ-10/6 | 2000,00 | 178,50 | 2,64 | 8,12 | ||
ЕЛОУ-АВТ-6 | ||||||
ЕЛОУ-АТ-6 | ||||||
Продовження табл. 1.5 | ||||||
ЛК-6у (секція 100) | ||||||
Вторинної перегонки бензину (22/4) | ||||||
Примітка. В чисельнику — теоретичні витрати, в знаменнику — досягнуті мінімальні фактичні витрати.
2. Фізико-хімічні властивості нафти
2.1 Склад і властивості нафти
Нафта — масляниста рідина, легша, ніж вода, що має забарвлення від жовтогарячого до темно-коричневого і майже чорного кольору. Нафта складається в основному з вуглецю (85−86%) і водню (12−14%), які зв’язані між собою у різноманітні хімічні сполуки — вуглеводні. Крім вуглеводнів нафта в невеликій кількості містить речовини, що у свою чергу, містять кисень, азот, сірку і механічні домішки.
Вуглеводнева частина нафти складається з парафінових (насичених) CnH2n+2, нафтенових (циклічні вуглеводні із загальною формулоюCnH2n) й ароматичних вуглеводнів. Ненасичених вуглеводнів CnH2n, як правило, у нафті немає, але вони є у продуктах їх переробки.
Парафінові вуглеводні від СН4 до С4Н10 — газоподібні. Вони присутні у нафті у розчиненому стані. Під час добування нафти, коли тиск її знижується, вони виділяються з неї у вигляді супутних газів. Рідкі парафінові вуглеводні від С5Н12 до С16Н34 становлять основну масу рідкої частини нафти і рідких фракцій, що одержують за її перероблення. Тверді парафінові вуглеводні від С16Н34 і вище розчинені у нафті і можуть бути виділені з неї. Нефтенові вуглеводні представлені у нафтах здебільшого похідними циклопентану і циклогексану.
Ароматичні вуглеводні містяться у нафті у відносно невеликих кількостях у вигляді бензолу і його гомологів — толуолу, ксилолів.
Класифікують нафти за вмістом вуглеводнів певних типів, які в них переважають. За таким принципом класифікації нафти поділяють на парафінові (найбагатші за бензиновими фракціями і містять твердий парафін); нафтено-парафінові; нафтено-ароматичні; парафіно-нафтено-ароматичні (асфальтові) — найважчі із нафт; ароматичні.
Невуглеводнева частина нафт складається із сірчистих, кисневих і азотистих сполук.
За вмістом сполук сірки нафти поділяють на малосірчисті із вмістом сірки до 0,5%, сірчисті (0,5−2%) і високосірчисті, в яких сірки більше 2%.
Кисневі сполуки — це нафтенові кислоти, феноли, смолисті речовини. Останні додають нафті темного забарвлення, розкладаються і коксуються під час нагрівання.
Мінеральні домішкице механічні домішки, вода, мінеральні солі, зола.
Механічні домішки — це тверді часточки піску, глини, що виносяться з надр землі потоком нафти, яка добувається. Вода в нафті перебуває у двох станах: відокремлена від нафти при відстоюванні й у вигляді стійких емульсій, які можуть бути зруйнованими тільки спеціальними методами. Мінеральні солі, наприклад хлорид кальцію і магнію, розчинені у воді, що міститься у нафті. Зола становить у нафті соті і навіть тисячні частки відсотка.
Склад нафти визначає її фізичні властивості, зокрема колір, густину, температури за яких вона загоряється і застигає, та ін.
Густина більшості нафт за 20? С — 0,83−0,97 г/см3. В’язкість нафти неоднакова і значно зменшується з підвищенням температури. Температура застигання коливається в широких межах — від 10 до -20 ?С. Вона характеризує умови, за яких нафта втрачає плинність. Теплота згоряння нафти змінюється в межах 39 800−44 000 кДж/кг.
2.2 Продукти перероблення нафти
Продукти нафтоперероблення можна поділити на такі: палива рідкі і газоподібні, розчинники, змащувальні оливи, консистентні мастила, тверді і напівтверді суміші вуглеводнів (парафіни, церезин, вазелін та ін.), нафтові бітуми та пек, нафтові кислоти і їх похідні (милонафти, сульфокислоти, жирні кислоти та ін.), індивідуальні вуглеводні (газоподібні і рідкі - етилен, пропилен, метан, бензол, толуол, ксилол), які є сировиною для нафтохімічної промисловості.
Нафтове рідке паливо поділяють на моторні бензини, тракторне паливо, дизельне паливо, котельне паливо, паливо для реактивних і турбореактивних двигунів.
Рідке паливо споживається у величезній кількості, особливо моторні бензини, які застосовуються у поршневих карбюраторних двигунах із запаленням від іскри. Моторне паливо не може містити сірчистих сполук, органічних кислот та інших речовин, які спричинюють корозію металів, що використовуються для виготовлення двигунів і тари. Вони повинні бути стабільні при зберіганні.
Бензин може мати певний фракційний склад, який характеризує початок і закінчення кипіння фракцій, що одержуються з розгорненням бензину в інтервалі температур 25−200 ?С. Тиск насиченої пари бензину, тобто тиск пари, який може бути над рідким бензином за певних умов, не повинен бути вищим установленої межі.
Важлива властивість бензину — його антидетонаційні якості, або детонаційна стійкість.
Бензин сьогодні використовується для автомобільних двигунів і для двигунів гвинтомоторних літаків (карбюраторних двигунів). Під час роботи такого двигуна горюча суміш парів бензину з повітрям надходить у циліндр двигуна, стискається у ньому поршнем і підпалюється від запалювальної свічки (іскри). Всередині циліндра продукти, що утворилися під час горіння парів бензину, розширюються і рухають поршень; рух поршня передається в ходову частину машину. Чим сильніше стискається суміш у циліндрі двигуна або, скажімо, чим вищий ступінь її стиснення, тим економічніший двигун. Зі збільшенням ступеня стиснення настає такий момент, коли замість спокійного горіння суміші починає різко збільшуватись швидкість поширення полум’я у циліндрі двигуна. Цей процес, подібний до вибуху, називається детонацією; він супроводжується різким стуком у циліндрі, появою чорного диму на вихлопі машини. Усе це приводить до підвищення витрати палива, зниження потужності двигуна й передчасного його зношення.
Схильність бензинів до детонації характеризується октановим числом. Чим вище октанове число бензину, тим менша схильність його до детонації, тобто краща якість. Октанове число — величина умовна. Ізооктан (2, 2, 4-триметилпентан)проявляє малу схильність до горіння з детонацією, і для нього прийняте октанове число, що дорівнює 100; октанове число н-гептану, надзвичайно схильного до детонації беруть за 0. Октанове число суміші ізооктану з н-гептаном залежно від вмісту в ній масової частки ізооктану змінюватиметься від 0 до 100%. Октанове число суміші беруть рівним вмісту в ній ізооктану. Наприклад, якщо суміш складається з 70% ізооктану і 30% н-гептану, то її октанове число становить 70. Для визначення октанового числа бензину порівнюють у певних умовах детонаційні властивості його і сумішей ізооктану з н-гептаном. Бензин матиме октанове число, відповідне вмісту ізооктану в суміші, в якої однакові з ним детонаційні властивості. Наприклад, октанове число автомобільного бензину 78 означає, що він має так само детонаційні властивості, що й суміш, яка складається з 78% ізооктану і 22% н-гептану.
Виробляють авіаційний бензин з октановим числом 100 і вище. Чим вище октанове число авіаційного бензину, тим менше його буде потрібно для польоту, і, отже, можна збільшити корисне навантаження літака. Октанове число моторного палива підвищується зі збільшенням вмісту в ньому ізопарафінів та ароматичних сполук.
Для підвищення октанового числа моторного палива застосовують суміш бензину з високооктановими компонентами — ізооктаном, ізопентаном, етилбензолом та ін. — або додають до бензину антидетонатори. Як антидетонатор раніше застосовували тетраетил-свинецьPb (C2H5)4 у суміші з бромистим етилом і монохлорнафталіном (етилова рідина), який нині заборонений.
Тракторне паливо — звичайно гас; якість його характеризується тими самими показниками, що і якість бензину.
Дизельне паливо — гас, газойль, соляровий дистилят; використовується для поршневих двигунів внутрішнього згоряння.
Котельне паливо — мазут та інші нафтові залишки.
Паливо для реактивних двигунів є фракцією гасу, яку використовують для повітряно-реактивних двигунів.
До газоподібного нафтового палива відносять попутні гази і гази, що одержуються під час перероблення нафти і нафтопродуктів.
Змащувальні оливи розділяють на такі групи залежно від сфери іх застосування: індустріальні - веретенне, машинне тощо; для двигунів внутрішнього згоряння — автотракторне (автоли), авіаційні оливи та ін.; трансмісійні; турбінні; компресорні; для парових машин — циліндрові; оливи спеціального призначення. Якість олив характеризується змащувальною здатністю, в’язкістю, температурами застигання і спалаху, густиною, вмістом води, кислотністю, коксивністю, зольністю, стабільністю[7].
3. Технологічна схема первинної переробки нафти
3.1 Підготовка нафти
Необхідність підготовки нафти до перероблення пояснюється такими причинами. Фонтани нафти, що виходять із свердловини, захоплюють за собою пісок, глину, воду та інші речовини, що трапляються на їх шляху. У нафті є розчинені гази, вода, солі. Все це має бути видалено з нафти, оскільки їх наявність призводить до порушення технологічних процесів переробки нафти.
Підготовка нафти до перероблення починається на нафтових промислах. Нафта зі свердловин по трубах надходить в уловлювачі (трапи), в яких відбувається виділення розчинених газів (супутних газів), а потім потрапляє у відстійники. На дні відстійників осідають пісок та інші тверді домішки, а також накопичується вода, оскільки вона важча за нафту. З відстійників нафта надходить у резервуари, з яких по трубопроводах або в цистернах її доставляють на нафтопереробні заводи.
На заводах проводиться остаточне зневоднення нафти, видалення з неї розчинених солей, механічних домішок, і лише після цього нафта надходить на перероблення.
3.2 Методи перероблення нафти й основні апарати
Методи перероблення нафти можна поділити на дві групи: фізичні й хімічні.
Фізичні методи перероблення нафти засновані на використанні відмінностей у фізичних властивостях речовин, що входять до складу нафти. Наприклад, одні з них тверднуть або кристалізуються за вищих, інші за нижчих температур, одні розчиняються в яких-небудь розчинниках краще, ніж інші, та ін. Якщо нагрівати нафту, то в міру підвищення температури з неї випаровуватимуться ті продукти, які закипають і випаровуються за нижчих температур, ніж ті, які киплять за вищих температур. Такий процес називається перегонкою нафти, і серед фізичних методів він набув найбільшого поширення. Хімічні реакції під час застосування фізичних методів перероблення нафти не відбуваються.
Хімічні методи перероблення засновані на тому, що під впливом температури, тиску, каталізаторів вуглеводні, що містяться у нафті і нафтопродуктах, зазнають якнайглибших хімічних перетворень. У цих процесах відбувається безліч хімічних реакцій, у результаті яких утворюються нові сполуки, нові продукти.
Отже, природа фізичних і хімічних процесів принципово різна, проте у практичному їх здійсненні є схожість: ці процеси складаються з двох основних операцій — нагрівання перероблюваної сировини до високої температури і розділення продуктів виходу.
Трубчаста піч (рис. 3.1) складається з металевого каркаса, укріпленого на фундаменті. Стінки печі викладені з вогнетривкої цегли. У середині печі у двох камерах укріплені труби, сполучені послідовно.
Рис. 3.1. Трубчаста піч: 1 — форсунка; 2, 3 — радіантні труби; 4 — конвективна камера.
По цих трубах швидко рухається нафта, що нагрівається, або нафтопродукт. У трубчастих печах для обігрівання використовується рідке або газоподібне паливо. Для спалювання рідкого палива в печі встановлена форсунка 1. Димові гази, що утворюються під час спалювання палива, шлях проходження яких на рис. 3.1 зображений стрілками, заповнюють труби, віддають їм тепло і надходять у димар. Продукти перероблення надходять у трубки, розміщені в конвективній камері 4, потім проходять по подових радіантних трубах 3 лівої камери печі, стельованихрадіантних трубах 2 і після подових радіантних труб 3 правої камери, маючи високу температуру, виводяться з печі.
Довжина трубок досягає в цілому близько 1 км, і під час руху по них нафта нагрівається у процесі перегонки приблизно до 320−350 ?С, а із застосуванням хімічних методів перероблення — і до вищої температури. За високої температури велика частина нафти перетворюється на пару. Пара і частина нафти, що не випарувалася, для виділення з них окремих продуктів надходять у колони ректифікації.
Одна з конструкцій тарілок колони ректифікації зображена на рис. 3.2
Рис. 3.2. Тарілки колони ректифікації: 1 — патрубки; 2 — переливні трубки; 3 — барботажні ковпаки.
Колона ректифікації для розділення нафтопродуктів є сталевим циліндром заввишки до 40 м і діаметром до 3,5−4 м. Усередині колони встановлено кілька десятків горизонтальних полиць, або тарілок. На цій тарілці у центрі колони є направлена вгору трубка (патрубок) 1, закрита зверху ковпаком 3 з щербинами. Через патрубки і ковпаки проходять пари нафти, що піднімаються в колоні знизу вгору. Зверху колона зрошується холодною рідиною, наприклад бензином, і через ті переливні труби 2 (зливні стакани), що є на тарілці, рідина перетікає з тарілки на тарілку. Завдяки тому, що зливні стакани підносяться над рівнем тарілки, на ній завжди є шар рідини, через який барботують пари, які піднімаються вгору. Є й інші конструкції колон ректифікацій, проте принцип їх дії не відрізняється від зображеного на рис. 3.2.
Суміш пари і рідина, що відходить із трубчастої печі, надходять у нижню частину колони. Пари піднімаються вгору і, оскільки температура по висоті колони знижується, рухаючись із тарілки на тарілку, поступово конденсуються, віддаючи своє тепло стікаючій рідині. За рахунок цього тепла з рідини випаровуються найбільш легкокиплячі продукти. Таким чином, рідина, що стікає з тарілки на тарілку, збагачується більш висококиплячимипродуктами, а пари, навпаки, ?легко киплячими.
3.3 Перегонка нафти
Як уже наголошувалося, перегонка — один із поширених методів перероблення нафти. Процес перегонки нафти схематично зображений на рис. 3.3.
Рис. 3.3. Схема перегонки нафти: 1 — трубчаста піч; 2 — колона ректифікації; 3 — теплообмінники; 4 — холодильник.
Нафта, що подається у трубчасту піч 1, спочатку проходить через теплообмінники 3, в яких вона підігрівається до 180? С бензином і мазутом, що відходять з колони ректифікації 2. У трубчастій печі відбувається подальше нагрівання нафти до 320−350 ?С, і при цьому утворюється суміш парів і рідини, яка надходить у колону ректифікації 2. Знизу в колону підводиться пара, й у ній відбувається розділення нафти на фракції, або дистиляти, які відбираються по висоті колони.
Зверху з колони виводяться пари бензину, які спочатку охолоджуються нафтою у теплообміннику 4, а потім — водою у холодильнику 4. При охолодженні пари бензину конденсуються, перетворюються у рідкий бензин, який частково надходить у сховище, а частково подається на зрошування колони. Вихід бензину при перегонці нафти становить від 3 до 15% маси перероблюваної нафти. Решта продуктів перегонки нафти — лігроїн, гас, солярове масло — виводяться з колони, охолоджуються в холодильниках (на рис. 3.3 не показані) і перекачуються у сховища. Знизу колони відбирається найважчий продукт — мазут, тепло якого використовується у теплообміннику 3 для нагрівання нафти. На установці, абсолютно аналогічній зображеній на рис. 3.3, але що працює під розрідженням, можна проводити розгін мазуту на фракції, одержуючи змащувальні оливи, необхідні для змащування частин машин і механізмів, що труться. Залишок після розгону мазуту називається гудроном; його використовують, наприклад, у дорожньому будівництві.
Мазут часто називають котельним паливом, тому що його спалюють у топках парових котлів і різних печей. Проте це не єдине його застосування. Як уже вказувалося, мазут використовується для одержання змащувальних олив; крім того, за хімічного перероблення з мазуту одержують бензин, а також газоподібні вуглеводні, що є сировиною хімічного синтезу.
4. Ресурсозбереження в первинній переробці нафти
Ресурсозбереження — це сукупність науково-методологічних, технологічних, інженерно-технічних, організаційно-технічних, економічних і організаційно-господарських заходів, спрямованих при виробництві продуктів на збереження і раціональне використовування природних ресурсів; на значне збільшення ступеню перероблення і різке скорочення втрат матеріальних ресурсів, найбільш повну рекуперацію вторинних матеріальних ресурсів та відходів, що призводить до значного росту економічної ефективності промислового виробництва і запобігає його шкідливій дії на навколишнє середовище. Ресурсозбереження в хімічній, нафтохімічній, нафтопереробній, металургійній і металообробній промисловості є важливим фактором справжнього переходу до стійкого розвитку.
Ресурсозбереження дозволяє не тільки зберегти природні і матеріальні ресурси для майбутніх поколінь, розтягнути на значно триваліші терміни їх раціональне використання і забезпечити охорону навколишнього середовища, але також відкриває великі можливості для збільшення об'єму виробництва високоякісної продукції при тих самих чи навіть менших затрат суспільної праці і економії капітальних вкладів.
Основними способами економії пари на НПЗ є: мінімізація кількості пари для процесів відпарювання і розділення продуктів; ліквідація витоку пари через з'єднання в паропроводах; зменшення втрат пари в конденсатовідвідниках; збирання конденсату і його використання в якості живильної води котлів; оптимізація параметрів промислової і побутової теплофікації; покращення ізоляції трубопроводів, а також арматури. Встановлено, що мінімальна кількість пари, яка потрібна для відпарювання легких нафтопродуктів складає 31,5 кг на 1 т та 65 кг на 1 т для важких нафтопродуктів. Для вимірювання і оптимізації витрат пари на парових лініях для відпарювання слід встановлювати лічильники та індикатори.
До скорочення кількості води, яка йде на охолодження, призводить до зниження витрат паливно-енергетичних ресурсів, а також заміна водяного охолодження повітряним. Широке використання повітряного охолодження скоротить потребу в охолоджуючій воді на 60−75%, а кількість стічних вод зменшиться на 25−45%. Відповідно скоротяться втрати нафти та нафтопродуктів, зменшаться витрати на водопостачання та каналізацію.
Пінч-методи проектування оптимальних рекуперативних теплообмінних систем і систем ректифікації багатокомпонентних сумішей. Задача модернізації теплообмінних систем діючих хімічних підприємств є достатньо складною, якщо використовувати тільки термодинамічні методи (пінч-метод) і евристичні методи, винайдені в кінці 1980;х років. Коли застосовують термодинамічні методи для модернізації діючих технологічних систем, задача розглядають як задачу псевдо проектування технологічної системи. Виявляють недоліки проекту діючої технологічної системи у порівнянні з новим ідеальним проектом. Такий підхід не враховує особливостей структури існуючої теплообмінної системи. Один із методів, запропонованих для подолання цього недоліку, називається системним пінч-методом. В рамках цього систематичного пінч-методу за допомогою простих термодинамічних методів спочатку визначають теплообмінники, які є вузьким місцем в діючій технологічній системі. Для використання системного пінч-методу вимагається модифікація структури існуючої технологічної системи. Такою модифікацією може бути зміна теплового навантаження, додавання нових теплообмінників, розділення технологічних потоків. Виявлення найбільш підходящого варіанту модифікації висхідної структури технологічної системи не є достатньо очевидною і простою задачею. На цьому етапі можна використовувати методи нелінійного програмування для знаходження найбільш вигідних змін структури, але при цьому обов’язково необхідно керуватися термодинамічними міркуваннями. Цей метод дозволяє модернізувати діючі технологічні системи одним прийомом, який дає можливість проектувальнику контролювати, приймати або заперечувати варіанти на кожному етапі розробки проекту модернізації технологічної системи.
У наш час розроблені методи проектування енергозберігаючих систем ректифікації багатокомпонентних сумішей, колонних комплексів, в структурі яких використовуються різні складні колони, а також колони для розділення азеотропних сумішей. Були запропоновані евристичні і математичні методи, які розробляють ряд ефективних варіантів систем ректифікації. Ці методи засновані на одночасній оптимізації структури колон, послідовності колон в системі, оптимізації тиску і виборі внутрішніх енергоносіїв для забезпечення теплових навантажень куба і конденсатора.
Поряд з боротьбою з втратами нафтосировини на нафтопереробних заводах не менш важливим фактором у справі поліпшення техніко-економічних показників нафтопереробної промисловості є також боротьба за скорочення витрат води, палива та електроенергії. Це стане цілком зрозуміло, якщо врахувати, що процеси переробки нафти, як правило, пов’язані з витратою великої кількості тепла.
Достатньо сказати, що в наш час витрати палива нафтозаводами складає в середньому 12−14% від кількості нафти, яка переробляється.
Основною причиною таких значних енергетичних затрат є недостатньо повне здійснення регенерації тепла гарячих потоків. Навіть на сучасних наших нафтозаводах ступінь використання тепла шляхом регенерації не перевищує в кращому випадку 20−25%.
Таке положення пояснюється, головним чином, недостатньо високою ефективністю існуючих систем регенерації тепла, недосконалістю теплообмінної апаратури, а також наявністю зайвої багатоступінчастості технологічних процесів, які призводять до неминучого багаторазового нагрівання і охолодження сировинних потоків.
В наш час цілий ряд проектних і науково-дослідницьких організацій ведуть роботи щодо усунення цих недоліків — розробляються нові, більш ефективні процеси переробки нафти та газу, створюються проекти комбінованих установок, де поєднується ряд технологічних процесів, більш успішно вирішується питання регенерації тепла, в тому числі і тепла від згоряння коксових відкладень на каталізаторах, а також розробляється ряд інших заходів, направлених на скорочення енергетичних витрат.
5. Енергозбереження в первинній переробці нафти
Атмосферна перегонка нафти здійснюється при температурі 320−360 ?С, і для нагрівання сировини необхідно витрачати велику кількість теплоти, яка підводиться в систему рекуперативного теплообміну, в трубчатих печах і з парою. Теоретична (мінімальна) робота розділення нафти на фракції складає 15−20 кДж/кг, тобто незначна в порівнянні з кількістю підведеного тепла. Частково тепло рекуперується, а більше половини марно відводиться в водяних або повітряних холодильниках. Витрати технологічного палива на діючих трубчатках атмосферної (АТ) і атмосферно-вакуумної (АВТ) залежить в основному від ступені рекуперації тепла нафтопродуктів і ККД печей. Під ступенем рекуперації розуміється відношення кількості теплоти, рекупероване в системі попереднього нагрівання нафти, Qрек до загально підведеної в процесі кількості тепла:
(5.1)
де Qрек, Qп, Qпар — відповідно кількість теплоти, підведеної в систему рекуперації, в печі і з парою[14]. Витрата технологічного палива є в основному функцією ступені рекуперації тепла і ККД печей (рис. 5.1).
Рис. 5.1. Залежність питомої витрати палива (Q = 44 000 кДж/кг) від ступеня рекуперації та ККД печі.
Енергосировинний ККД установок залежить від трьох основних факторів: витрати палива, споживання теплової енергії, втрат нафтопродуктів. Всі інші фактори є складовими трьох основних або незначні. На рис. 5.2 наведена залежність енергоресурсного ККД зер технологічної установки від витрати енергії (1 кг умовного палива на 1 т нафти, яка переробляється) і втрат нафтопродуктів.
Рис. 5.2. Залежність енергоресурсного ККД установки від витрати енергії і втрат нафтопродуктів: 1 — втрати 0%; 2 — 1%; 3 — 3%.
Термодинамічний аналіз показав, щозастосовувані при атмосферній перегонці нафти складні колони з відпарними секціями мають достатньо високу ефективність розділення: енергоресурсний ККД їх перевищує 30%. В типових схемах установок АТ і АВТ застосовують і менш ефективне обладнання, наприклад, колону попереднього відбензинювання нафти, ККД якої близько 3%. Але застосування цієї колони дає можливість відбирати тепло на більшій кількості температурних рівнів. Даний приклад показує, що схеми нафтопереробки ще не оптимізовані і є істотні резерви економії. До цього часу розроблено кілька варіантів високо економічних ректифікаційних систем, які складаються із комплексу високоефективних колон зі зв’язаними матеріальним і тепловим потоками. Впровадження таких систем для процесів первинної перегонки нафти, вторинного розділення нафтових фракцій та продуктів хімічних перетворень призводить до значного скорочення витрат енергії на розділення.
У даний час на типових установках АТ і АВТ пари верхніх продуктів колон, які мають температуру 90−170 ?С, конденсуються у водяних або повітряних холодильниках; тепло зазвичай не використовується, хоча навіть часткове його використання призводить до суттєвої економії палива.
Для нормальної роботи атмосферної колони кількість тепла, яке відводиться, повинне бути майже постійним, і тому тепло може відводитися не повітрям, а продуктовим потоком, наприклад, сирою нафтою. Повітряний холодильник залишається тільки в якості додаткового кінцевого. Використання тепла конденсації верхнього продукту для первинного нагрівання сирої нафти та в інших цілях за кордоном використовують достатньо широко. Повітряний холодильник може підключатися через триходовий кран, який встановлюється так, щоб кількість подаваного на зрошення нафтопродукту, який проходить через повітряний холодильник, було достатнім тільки для підтримання потрібної температури зрошення. Отже, кількість тепла, яке сприймає теплообмінник може змінюватися в дуже широких межах без впливу на тепловий баланс колони.
Утилізацію тепла верхнього продукту можна здійснити за схемою зображеною на рис. 5.3.
Рис. 5.3. Схема використовування тепла верхнього продукту колони: 1 — ректифікаційна колона; 2 — насос; 3 — теплообмінник; 4 — сепаратор; 5 — компресор; 6 — теплообмінник.
Для підвищення температури утилізованого тепла можна збільшити температуру верха колони і здійснювати двоступеневу конденсацію парів. Другу ємність використовують тільки для збору парів продукту, які сконденсувалися, а зрошення подають з першої ємності. Така схема дозволяє утилізовувати до 80% тепла, але використовуватися вона може тільки при широкому фракційному складі верхнього продукту.
Пари верхнього продукту атмосферної колони 1 подаються в компресор 5 безпосередньо або через теплообмінник для регулювання температури на всмоктуванні. Після стиснення пари віддають тепло сирої нафти в теплообміннику 3 і дроселюються в сепаратор. Газ виходить з сепаратора під необхідним тиском і може бути легко використаний для будь-яких цілей. Це є важливою перевагою даної системи. Далі рідина дроселюється в наступний сепаратор і звідти подається на зрошення колони. Колона може працювати і при відключеному компресорі, що значно підвищує надійність схеми.
У нафтопереробці давно використовуються колони з проміжним циркуляційним зрошенням, яке надає незначний вплив на розділення, проте має велике значення для утилізації тепла, так як воно в проміжному конденсаторі відводиться на більш високому температурному рівні і використовується для нагрівання сирої нафти.
Великий вклад в економію енерговитрат можуть внести вдосконалення і оптимізація системи рекуперативного підігрівання нафти за рахунок тепла продуктів і циркуляційних зрошень. Ступінь підігрівання нафти лімітується температурою і витратами гріючих потоків; теоретично може бути рекуперована певна кількість тепла. Для кожного ступеня нагрівання температура нафти лімітується температурою і витратами гріючих потоків і розраховується за тепловим балансом:
(5.2)
де — відповідно витрати (маса) нафти та газу, кг; - теплоємність газу та нафти відповідно, Дж/кг; Т1 і Т2— температура граючого потоку і нафти, К.
Практично завжди витрати нафти перевищують витрати гріючих потоків. Для цього випадку в межах, тобто при нескінченно великій поверхні нагрівання, температура гріючого потоку буде приймати значення температури нафти на вході в теплообмінник і максимально досягнута температура нафти
. (5.3)
З рівняння слідує, що для досягнення максимально можливої температури на наступному ступені нагрівання потрібне максимальне нагрівання на попередньому ступені. При аналізі системи потрібно розраховувати теоретично можливий ступінь рекуперації тепла. Для багатьох схем він лежить в області втеор? 0,6.
Оптимізація системи теплообміну дає можливість підвищити температуру нагрівання максимум до 270? С. Така температура являється практично межею нагрівання нафти в системі рекуперації. Необхідність роботи системи підігрівання нафти в оптимальному режимі зумовила розробку системи управління комплексу теплообмінних апаратів. Здійснюється управління температурою блоку знесолення, забезпечується мінімально допустима швидкість потоку нафти в кожному теплообміннику і максимально можлива температура нагрівання нафти при поступовому забрудненню теплообмінників. При цьому всі параметри підтримуються в допустимих межах. Робота в системі управління базується на спрощеній, але достатньо хорошій моделі об'єкта, застосуванні мікропроцесорної техніки, ієрархічного управління.
Основним шляхом зниження енергозатрат при первинній перегонці нафти являється розробка високоефективних технологічних схем.
Аналіз роботи типової установки АТ-6 продуктивністю з нафти 6 млн. т/рік (секція 100 ЛК-6у) показав, що затрати енергії мають наступне значення: технологічного палива — 876МДж/т, теплової енергії - 210МДж/т, електроенергії - 40МДж/т, всього — 1126МДж/т.