Проектування ділянки термічної обробки різальних інструментів
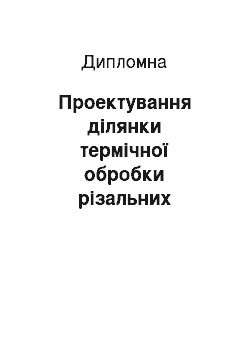
Різальні інструменти піддаються дії підвищеної напруги, частіше за все вигину і крученню. Максимальний вигинаючий або обертаючий момент виникає в ділянках, декілька віддалених від контактуючої поверхні, наприклад в основі зуба фрези, мітчика і так далі. У деяких інструментах може виникати розтягуюча напруга. Робота багатьох інструментів пов’язана з ударними навантаженнями або вібраціями… Читати ще >
Проектування ділянки термічної обробки різальних інструментів (реферат, курсова, диплом, контрольна)
Проектування ділянки термічної обробки різальних інструментів в умовах «ПАО «Луганськтепловоз»
Вступ різальний сталь технологічний безвольфрамовий
Термічна обробка набуває все більшого значення як для вдосконалення технологічних процесів виготовлення і обробки матеріалів з метою їх економного і раціонального використання, так і для отримання заготовок і інструментів із заданими властивостями. Нині можна вважати встановленим, що досвід, що є, і наукове обґрунтування технології термообробки дозволяють на окремих стадіях виробництва в усе зростаючому масштабі використовувати зміни температури (оскільки усі виготовлені із сталі вироби в процесі їх отримання і експлуатації піддаються дії температур, що багаторазово змінюються, з чим пов’язана і зміна властивостей металу) для цілеспрямованого впливу на технологічні і експлуатаційні властивості металу. Це означає, що область термообробки швидко розширюється, а само поняття повинне охоплювати усі термічні процеси, метою яких є зміна властивостей матеріалу.
Підвищення якості різальних інструментів — це по суті питання вдосконалення технології термічної обробки, важливість науково-технічного напряму, що передбачає створення нових і вдосконалення існуючих технологічних процесів термічної обробки. При цьому отримання високих і однорідних заданих властивостей повинно бути забезпечено автоматизованими термічними операціями у високопродуктивних агрегатах. Серед контрольних параметрів технологічного процесу термічної обробки останніми роками все більше застосовується швидкодіюча апаратура по контролю і регулюванню температурних, деформаційних і хімічних чинників, що визначають протікання і якість в цілому запланованого і реалізованого циклу термічної обробки різального інструменту.
Одним з основних чинників, що впливають на стійкість різального інструменту є термічна обробка. Правильне проведення процесу термічної обробки інструменту значною мірою визначає його подальшу поведінку в експлуатації. Окрім надання інструменту необхідної твердості у поєднанні з в’язкістю, зменшення деформації і забезпечення високої якості інструменту (воно досягається загартуванням і відпуском) термічна обробка вирішує і деякі допоміжні завдання, наприклад, попереднє поліпшення структури матеріалу інструменту.
Оскільки різальний інструмент працює при високих температурах і швидкостях різання, в тяжких умовах, отже, якість різального інструменту залежить не лише від правильного призначення і проведення термічної обробки, але і від якості сталі з якої виготовлений інструмент і від правильності його виготовлення.
Для отримання різального інструменту високої якості необхідно велику увагу приділяти зниженню трудомісткості заготівельних процесів, економії металу і скороченню вартості заготовки за рахунок її максимального наближення до форм і розмірів готової деталі, оскільки від якості інструменту залежить точність і працездатність деталей машин. Висока стійкість інструменту збільшує продуктивність механічної обробки, скорочує витрату інструментальної сталі і отже знижує собівартість виробів.
1. Технологічна частина
1.1 Виробнича програма термічної ділянки
Річна програма термічної ділянки різального інструменту розділена на три групи:
1) фреза дискова (пазова затилована) піддається повному відпалу, триступінчатому загартуванню і триразовому відпуску.
2) свердло піддається ізотермічному відпалу, загартуванню із ступінчастим нагрівом, високотемпературному триразовому відпуску — різальна частина, загартуванню і відпуску — хвостовик.
3) мітчик піддається режимам термічної обробки аналогічним для свердла.
Таблиця 1.1. Виробнича програма
Найменування послуг | Марка сталі | Розміри інструменту у планах, мм | Твердість HRC | Маса Інструменту, кг | Річна програма | Термообробка | ||
шт. | т | |||||||
Фреза дискова | 11М5Ф | 62−65 | 0,75 | 1,4 млн | Відпал, триступінчате загартування, двократний відпуск | |||
Свердло | Р6М5Ф3 | 6,8 — різальна частина; 9,4 — хвостова частина | Різальна частина 62-65 Хвостова частина 30-45 | 0,07 | 15 млн | Для різальної частини: відпал, загартування із ступінчастим нагрівом, триразовий відпуск; для хвостової частини: загартування і відпуск | ||
Мітчик | Р6М5 | М14×1,5-3 | Різальна частина 63−66 Хвостова частина 31-51 | 0,09 | 10 млн | Для різальної частини: відпал, загартування із ступінчастим нагрівом, триразовий відпуск; для хвостової частини: загартування і відпуск | ||
1.2 Аналіз умов роботи різального інструменту
Фрези дискові. Фреза використовується в якості різального інструменту для механічної обробки металу різанням, при якій різальний інструмент — фреза має обертальний (головний) рух, а оброблювана заготовка — поступальний хід (рух подачі), вона може бути спрямована як по напряму обертання фрези, так і проти.
Особливістю фрезерування є уривчастість процесу різання. Це обумовлено тим, що при обертанні фрези кожен зуб врізається в заготовку з ударом, а потім працює тільки на деякій частині обороту і виходить із зони різання. При подальшому русі зуб не торкається заготовки, що сприяє його охолодженню і обумовлює сприятливіші умови для роботи.
Врізання зубів фрези в заготівлю з ударами призводить до виникнення вібрації, що негативно позначається на точності і шорсткості обробки.
Робоча кромка інструменту випробовує теплові дії за рахунок тепла, що виділяється при різанні і терті. Температура досягає 400−600єС і може підвищуватися при подальшому підвищенні швидкості різання. Тепловий чинник впливає на властивості і поведінку інструментальних сталей. Кожен різальний зуб фрези має такі ж елементи як і будь-який різець або інший різальний інструмент, що врізаючись в метал, знімає стружку.
Тому найбільш важливі вимоги до дискової фрези наступні:
— висока твердість 63−65 HRC;
— висока міцність і опір пластичнії деформації;
— теплостійкість, при температурі різання 615−620°С;
— формоі розміростійкість.
Свердла. Свердло — різальний інструмент для обробки отворів в суцільному матеріалі, або для розсвердлювання отворів при двох рухах, що одночасно виконуються: обертання свердла навколо його осі і поступальної ходи подачі уздовж осі інструменту.
У промисловості застосовуються такі основні типи свердел: спіральні, пір'яні, кільцеві, центровочні. Свердла виготовляються зі швидкорізальних сталей, марок Р18, Р12, Р9, Р6М3, Р6М5, Р6М5К5. Основним типом свердел, що найширше застосовується в промисловості, є спіральне свердло. Воно застосовується при свердлінні і розсвердлюванні отворів діаметром до 80 мм. Такі свердла складаються з основних частин: різальної, напрямної, хвостовика. Різальна і напрямна частини складають робочу зону свердла, оснащену двома гвинтовими канавками.
Різальна частина свердла складається з двох (зубів), які в процесі свердління своїми різальними кромками врізаються в матеріал заготівлі і зрізують його у вигляді стружки.
Умови роботи свердла визначаються головним чином конструкцією різальної частини. Напрямна частина свердла потрібна для напряму свердла при роботі. Напрямна частина має допоміжні різальні кромки — кромки стрічки, що беруть участь у формуванні поверхні оброблюваного отвору. Хвостовик служить для кріплення свердла. У свердлах з конічним хвостовиком робоча частина виготовляється зі швидкорізальної сталі, а хвостовик із сталі 45.
Мітчики. Мітчик є загартованим гвинтом, на якому прорізається декілька прямих або гвинтових канавок, що утворюють різальні кромки інструменту. Канавки також забезпечують розміщення стружки, що утворюється при різанні; стружка може виводитися із зони різання.
Умови різання при знятті стружки мітчиком дуже важкі із-за скованого різання, великих сил різання і тертя, а також ускладнених умов видалення стружки. Крім того, мітчики мають знижену міцність із-за ослабленого поперечного перерізу. Особливо негативно це позначається при нарізанні різьблення у в’язких матеріалах мітчиками малих діаметрів, які часто виходять з ладу із-за поломок, викликаних пакетуванням стружки.
Тому матеріал для виготовлення мітчика повинен мати високу твердість (63−66 HRC) і зносостійкість, тобто здатність тривалий час зберігати різальні властивості кромки в умовах тертя.
1.3 Вибір матеріалу
Різальний інструмент працює в умовах тривалого контакту і тертя з оброблюваним металом. В процесі експлуатації повинні зберігатися незмінними конфігурації і властивості різальної кромки. Матеріал для виготовлення різального інструменту повинен мати високу твердість і зносостійкість, тобто здатність тривалий час зберігати різальні властивості кромки в умовах тертя.
Чим більше твердість оброблюваних матеріалів, товще стружка і вище швидкість різання, тим більше енергія, що витрачається на процес обробки різанням. Механічна енергія переходить в теплову. Тепло, що виділяється, нагріває різець, деталь, стружку і частково розсіюється. Тому основною вимогою, що пред’являється до інструментальних матеріалів, є висока теплостійкість, тобто здатність зберігати твердість і різальні властивості при тривалому нагріві в процесі роботи.
Різальні властивості інструменту погіршуються не лише під впливом високої температури, але і таких явищ, як адгезія, що викликає спаровування оброблюваного матеріалу з робочою поверхнею інструменту, прискорене вифарбовування і окислення поверхні, дифузія, абразивно-механічне зношування різальної кромки і поверхонь інструменту. Щоб уникнути передчасного руйнування різальної кромки необхідно, щоб інструментальний матеріал був досить міцним.
Робоча кромка інструменту знаходиться в умовах, близьких до нерівномірного усебічного стискування і переводячих метал в пластичніший стан внаслідок зростання долі дотичної напруги. При дуже великій напрузі може спостерігатися деформація і пластична течія тонкого поверхневого шару.
Різальні інструменти піддаються дії підвищеної напруги, частіше за все вигину і крученню. Максимальний вигинаючий або обертаючий момент виникає в ділянках, декілька віддалених від контактуючої поверхні, наприклад в основі зуба фрези, мітчика і так далі. У деяких інструментах може виникати розтягуюча напруга. Робота багатьох інструментів пов’язана з ударними навантаженнями або вібраціями, що не усуваються повністю в системі верстат — оброблювана деталь — інструмент або створюваними умовами різання, наприклад при наскрізному свердлінні, при роботі багатолезових інструментів (фрези, довбяки і так далі). Тому інструмент повинен мати високу твердість робочої частини, що перевищує твердість деталі. Інструмент з недостатньою твердістю не може різати: його форма і розміри швидко змінюються. Крім того інструмент має бути в’язким. При низькій в’язкості утворюються тріщини, відбувається вифарбовування і поломка інструменту.
В процесі роботи різального інструменту відбувається безперервне тертя — знос поверхні різальної кромки інструменту. Тому різальний інструмент повинен мати високу зносостійкість.
Матеріал для різального інструменту повинен відповідати не тільки основним експлуатаційним властивостям, переліченим вище, але і технологічним властивостям, які характеризують поведінку сталі при виготовленні інструменту і його термічній обробці: сталі для різального інструменту повинні мати високу загартовуваність і прожарюваність, стійкістю до деформації при термічній обробці, стійкістю проти гартівних тріщин, стійкість проти окислення і зневуглецювання, не мають бути забруднені неметалічними включеннями, що знижують якість інструменту.
Різальні властивості інструменту погіршуються під дією адгезії, що викликає зварювання оброблюваного матеріалу з робочою поверхнею інструменту, прискорене вифарбовування і окислення поверхні; дифузії, абразивно-механічного зношування різальної кромки і поверхні інструменту.
Сталь 11М5Ф є швидкорізальною безвольфрамовою і має наступний хімічний склад:
Таблиця 1.2. Хімічний склад сталі 11М5Ф (ТУ 14−1-2678−0)
C | Si | Mn | Cr | Ce | Mo | W | V | |
1.02−1.1 | до 0.5 | до 0.4 | 3.8 — 4.2 | до 0.15 | 5.2 — 5.8 | до 0.6 | 1.3 — 1.6 | |
При виготовленні різального інструменту особливий інтерес представляє використання безвольфрамової швидкорізальної сталі типу 11М5Ф, яка відноситься до сталей заевтектоїдного класу. Цю сталь, особливо модифіковану, в порівнянні із сталями чисто ледебуритного класу, відрізняє значно менша карбідна неоднорідність — об'ємна доля евтектичних карбідів не перевищує 1% при кристалізації металу в кокілі і 5% - в керамічній формі.
Важливо підкреслити, що надмірних карбідів дуже мало і після термічної обробки, що включає загартування від 1180 °C і триразовий відпуск при 560 °C, вони практично відсутні в структурі сталі. Як наслідок, після остаточної термічної обробки сталь марки 11М5Ф при усіх використовуваних способах литва значно перевершує сталь марки Р6М5 по ударній в’язкості. Завдяки тому, що вторинні карбіди більш повно розчиняються в аустеніті при нагріві під загартування, сталь марки 11М5Ф не поступається по твердості і теплостійкості сталі марки Р6М5.
Таблиця 1.3. Механічні властивості сталі 11М5Ф в стані постачання (після відпалу) (ТУ 14−1-2678−0)
у0,05 | у0,2 | уВ | д | ш | усж0,2 | усж | е | KCU | |
МПа | % | МПа | % | Дж/см2 | |||||
Ці властивості сталі 11М5Ф задовольняють вимогам для виготовлення фрези дискової.
Сталі з підвищеним вмістом вольфраму, ванадію, кобальту мають високу твердість, але у них сильно проявляється карбідна неоднорідність, яка негативно впливає на їх твердість, що призводить до вифарбовування різальних кромок. До цього менше схильні молібденовмісні сталі, які мають стабільні по усьому перерізу характеристики.
У наш час спостерігається тенденція до заміни швидкорізальних сталей з високим вмістом вольфраму на складнолеговані сталі з малим вмістом вольфраму. Найбільш типовими представниками таких сталей є сталі Р6М5 і Р6М5Ф3. Додавання молібдену дає можливість значно зменшити карбідну неоднорідність, що підвищує як міцність, так і стійкість різального інструменту. Тому в усіх випадках сталь Р18 можна замінювати сталлю Р6М5, особливо при виготовленні великогабаритних інструментів, коли особливо видно карбідна неоднорідність сталі Р18.
Підвищена стійкість, міцність і технологічність дали можливість сталі Р6М5 зайняти домінуюче місце серед сталей нормальної продуктивності. Її застосовують при виготовленні широкої гамми різальних інструментів.
Таблиця 1.4. Хімічний склад сталей Р6М5 і Р5М5Ф3 [ГОСТ 19 265−73]
Сталь | C | Cr | W | V | Mn | Si | Co | Mo | Ni | S | P | |
не більше | ||||||||||||
Р6М5 | 0,82−0,90 | 3,8-4,4 | 5,5-6,5 | 1,7-2,1 | 0,5 | 0,5 | 0,5 | 4,8-5,3 | 0,4 | 0,025 | 0,03 | |
Р5М5Ф3 | 0,95−1,05 | 3,8-4,3 | 5,7-6,7 | 2,3-2,7 | 0,5 | 0,5 | 0,5 | 4,8-5,3 | 0,6 | 0,025 | 0,03 | |
Вольфрамомолібденові сталі доцільно застосовувати для інструментів, від яких потрібні підвищена міцність і в’язкість. Сталь Р6М5 застосовується для усіх видів різального інструменту, працюючого при звичайних швидкостях різання, призначеного для різання вуглецевих і середньолегованих конструкційних сталей з уВ до 900−1000 МПа; зуборізного і різьборізного інструменту для обробки нержавіючих сталей. Стійкість інструментів із сталі Р6М5 рівна або дещо (приблизно на 20%) вища за стійкість інструментів із сталі Р18. Тому ці властивості сталі Р6М5 задовольняють вимогам для виготовлення мітчика.
Сталь Р6М5Ф3 застосовується для виготовлення різального інструменту (фасонні різці, розгортки, свердла, протягання та ін.), призначеного для обробки сталей і сплавів. Інструменти із сталі Р6М5Ф3 мають стійкість на 20% вище, ніж із сталі Р18. Тому ці властивості сталі Р6М5Ф3 задовольняють вимогам для виготовлення свердла.
Таблиця 1.5. Механічні властивості сталей Р6М5 і Р6М5Ф3 [ГОСТ 19 265−73]
Сталь | HRC | в при згинанні, МПа | Теплостійкість (HRC58), С | KCU кДж/см2 | |
Р6М5 | 63−65 | 320-360 | 5,2 | ||
Р6М5Ф3 | 63−66 | 320-360 | 5,0 | ||
Хвостова частина цих інструментів виготовлятиметься з конструкційної сталі 45. Структура стали, що містить менше 0,8% вуглецю складається з фериту і перліту. Збільшення вмісту вуглецю в сталі призводить до підвищення міцності і пониження пластичності. Істотний вплив вуглецю на в’язкі властивості. Збільшення вмісту вуглецю підвищує поріг холодноламкості і зменшує ударну в’язкість у в’язкій області (тобто при температурах вище за поріг холодноламкості).
Таблиця 1.6. Хімічний склад сталі 45 [ГОСТ 1050−74]
C Вуглець | Si Кремній | Mn Марганець | S Сірка | P Фосфор | Cr Хром | Fe Залізо | Ni Нікель | Cu Мідь | As Миш’як | |
від 0.42% до 0.5% | від 0.17% до 0.37% | від 0.5% до 0.8% | до 0.04% | до 0.035% | до 0.25% | від 97.425% до 98.91% | до 0.25% | до 0.25% | до 0.08% | |
Таблиця 1.7. Механічні властивості сталі 45 [ГОСТ 1050−74]
Загартування | Відпуск | 0,2 | в | 5, % | , % | KCU, кДж/см2 | НВ | |
МПа | ||||||||
850С | 550С | 185-210 | ||||||
1.4 Розробка маршрутної технології виготовлення різального інструменту
1. Отримання заготовки — поковки (ковальський цех).
2. Попередня пом’якшувальна термообробка — повний відпал (термічна ділянка ковальського цеху).
3. Контроль твердості (термічна ділянка ковальського цеху).
4. Попередня механічна обробка (механічний цех).
5. Остаточна зміцнююча термообробка — загартування із ступінчастим нагрівом, високотемпературний триразовий відпуск (термічна ділянка механічного цеху).
6. Контроль твердості (термічна ділянка механічного цеху).
7. Остаточна механічна обробка (механічний цех).
8. Контроль якості готової деталі (механічний цех).
Розробка маршрутної технології виготовлення свердла із сталі Р6М5Ф3.
1. Отримання заготівлі - поковки (ковальський цех).
2. Попередня пом’якшувальна термообробка — ізотермічний відпал (термічна ділянка ковальського цеху).
3. Контроль твердості (термічна ділянка ковальського цеху).
4. Попередня механічна обробка (механічний цех)
5. Остаточна зміцнююча термообробка — загартування із ступінчастим нагрівом, високотемпературний триразовий відпуск; поліпшення хвостовика (термічна ділянка механічного цеху).
6. Контроль твердості (термічна ділянка механічного цеху).
7. Остаточна механічна обробка (механічний цех).
8. Контроль якості готової деталі (механічний цех).
Розробка маршрутної технології виготовлення різального інструменту мітчик із сталі Р6М5.
1. Отримання заготівлі - поковки (ковальський цех).
2. Попередня пом’якшувальна термообробка — ізотермічний відпал (термічна ділянка ковальського цеху).
3. Контроль твердості (термічна ділянка ковальського цеху).
4. Попередня механічна обробка (механічний цех)
5. Остаточна зміцнююча термообробка — загартування із ступінчастим нагрівом, високотемпературний триразовий відпуск; поліпшення хвостовика (термічна ділянка механічного цеху).
6. Контроль твердості (термічна ділянка механічного цеху).
7. Остаточна механічна обробка (механічний цех).
8. Контроль якості готової деталі (механічний цех).
1.5 Розробка технологічного процесу термічної обробки різального інструменту
Термічна обробка різальних інструментів (дискова фреза, свердло, мітчик) здійснюється на напівавтоматичній лінії з печей-ванн для інструментів. До складу лінії входять:
— соляна ванна 1 го підігріву;
— соляна ванна 2 го підігріву;
— ванна остаточного нагріву;
— селітрова ванна для загартування;
— камера охолодження;
— селітрова ванна для відпуску;
— ванна виварювання;
— ванна травління;
— ванна промивання;
— ванна нейтралізації;
— ванна пасивування.
Технологічний процес попередньої термічної обробки.
1) Попередня термічна обробка і призначення технологічних параметрів для фрези дискової (рис. 1.1).
— перший нагрів інструменту зробити в електрованні соляній електродній типу СВС 2.4.4/8,5 до температури 650°С. Тривалість нагріву 20-25 хв. Витримати при температурі нагріву 20-30 хв.
— другий нагрів інструменту зробити до температури 920°С. Тривалість нагріву 20-25 хв. Витримати при температурі нагріву 1 год.
— охолодити в печі до 500°С
— охолодити на повітрі до температури ділянки
— зробити контроль твердості 10% заготівель від партії за методом Бринеля Характерною особливістю відпалу безвольфрамової швидкорізальної сталі є утворення феррито-цементитної суміші з аустеніту при постійній температурі. При нагріві сталі 11М5Ф вище за критичну точку відбувається перехід перліту в аустеніт. Механізм процесу перетворення перліту в аустеніт полягає в зародженні зерен аустеніту і їх рості. Первинні зародки аустеніту при нагріві дещо вищому критичної точки А1 утворюються зсувним шляхом (б > г) при збереженні когерентності. При рості зародка когерентність б і г решіток порушується, зсувний механізм замінюється нормальним механізмом росту, і зерна аустеніту набувають рівноосної форми. Ізотермічна витримка потрібна для повного розпаду аустеніту і утворення перліту.
2) Попередня термічна обробка і призначення технологічних параметрів для свердла.
Різальна частина (рис. 1.2):
— нагрівати різальну частину інструменту в електрованні соляній електродній типу СВС 2.4.4/8,5 до температури 840-860°С. Тривалість нагріву ?5 хв. Витримати при температурі нагріву 10 хв.
— охолодити в печі до 720-730°С і витримати 2 год
— охолодити в печі до 600°С
— охолодити на повітрі до температури ділянки
— зробити контроль твердості за методом Бринеля
Хвостова частина (рис. 1.3):
— нагрівати хвостову частину інструменту в електрованні соляній електродній типу СВС 2.4.4/8,5 до температури 840°С±10°С. Витримати при температурі нагріву 20 хв.
— охолодити на повітрі до температури ділянки
— зробити контроль твердості за методом Бринеля
3) Попередня термічна обробка і призначення технологічних параметрів для мітчика.
Різальна частина (рис. 1.2):
— нагрівати різальну частину інструменту в електрованні соляній електродній типу СВС 2.4.4/8,5 до температури 840-860°С. Тривалість нагріву ?5 хв. Витримати при температурі нагріву 10 хв.
— охолодити в печі до 720-730°С і витримати 2 год
— охолодити в печі до 600°С
— охолодити на повітрі до температури ділянки
— зробити контроль твердості за методом Бринеля
Хвостова частина (рис. 1.3):
— нагрівати хвостову частину інструменту в електрованні соляній електродній типу СВС 2.4.4/8,5 до температури 840°С±10°С. Витримати при температурі нагріву 20 хв.
— охолодити на повітрі до температури ділянки
— зробити контроль твердості за методом Бринеля
Цілі відпалу:
1) зменшити карбідну неоднорідність литої і катаної сталі;
2) знизити твердість і забезпечити, таким чином, можливість обробки різанням;
3) підготувати структуру для загартування і попередити нафталіновий злам.
Для ізотермічного відпалу сталь нагрівають до температури, на 20−30°С вище А3 і після витримки швидко охолоджують до температури трохи нижче критичної точки А1 ?700 (С. При цій температурі сталь витримується до повного розпаду аустеніту і потім охолоджують на повітрі.
Перевагою ізотермічного відпалу в порівнянні із звичайним є значне скорочення часу відпалу і отримання одноріднішої структури. Температура ізотермічної витримки робить вплив отримувану на структуру і властивості. З пониженням температури ізотермічної витримки, тобто зі збільшенням міри переохолодження аустеніту зерна цементиту подрібнюються і утворюється дрібнозернистий перліт.
Відпал здійснюється в електрованні соляній електродній типу СВС 2.4.4/8,5, яка по своїй продуктивності забезпечує виконання виробничої програми і необхідний температурний інтервал режиму термообробки.
1.5.2 Технологічний процес остаточної термічної обробки.
Остаточна термічна обробка різальних інструментів полягає в триступінчатому загартуванні і триразовому відпуску.
Технологічний процес загартування інструменту.
1) Технологія загартування фрези дискової (рис. 1.1).
— перший підігрів інструменту зробити в електрованні соляній електродній типу СВС-3.8.4/8,5 до температури 500°С. Тривалість нагріву 35 хв
— другий підігрів зробити в соляній ванні СВС — 2,5.6.4/8,5 до температури 800-850°С. Тривалість нагріву 15 хв
— остаточний нагрів зробити у високотемпературній соляній ванні СВС-2.3.4/13 до температури 1210-1230°С. Тривалість нагріву і витримки 15 хв
— охолодити в маслі
— очистити інструмент.
Для сталі 11М5Ф проводять загартування з триступінчатим підігріванням до температури 1210−1230°С. Висока температура загартування проводиться для повнішого розчинення вторинних карбідів і отримання при нагріві аустеніту, високолегованого хромом, молібденом і ванадієм.
При триразовому підігріванні сталі 11М5Ф, забезпечується більше рівномірне прогрівання сталі і можливість запобігання утворенню тріщин.
Структура сталі 11М5Ф після загартування представляє собою високолегований мартенсит, що містить 0,3−0,4% нерозчинених-надмірних карбідів і залишкового аустеніту приблизно 28−34%. Залишковий аустеніт знижує різальні властивості сталі, і тому його присутність в готовому інструменті не допустима.
2) Технологія загартування свердла
Різальна частина (рис. 1.2):
— перший підігрів різальної частини інструменту зробити в електрованні соляній електродній типу СВС-3.8.4/8,5 до температури 500°С. Тривалість нагріву і витримки 30 хв.
— другий підігрів зробити в соляній ванні СВС — 2,5.6.4/8,5 до температури 800-850°С. Тривалість нагріву і витримки 10 хв.
— остаточний нагрів зробити у високотемпературній соляній ванні СВС-2.3.4/13 при температурі 1200-1230°С. Тривалість нагріву і витримки 8-9 хв
— охолодити в маслі
— очистити інструмент.
Хвостова частина (рис. 1.3):
— завантажити хвостову частину інструменту в електричну соляну ванну СВС — 2,5.6.4/8,5 нагріту до температури 820-840°С. Витримати при температурі нагріву 15 хв.
— охолодити в 5% водному розчині NaCl до 150-200°С.
— охолодити на повітрі.
3) Технологія загартування мітчика
Різальна частина (рис. 1.2):
— перший підігрів різальної частини інструменту зробити в електрованні соляній електродній типу СВС-3.8.4/8,5 до температури 500°С. Тривалість нагріву і витримки 30 хв.
— другий підігрів зробити в соляній ванні СВС — 2,5.6.4/8,5 до температури 800-850°С. Тривалість нагріву і витримки 10 хв.
— остаточний нагрів зробити у високотемпературній соляній ванні СВС-2.3.4/13 при температурі 1200-1230°С. Тривалість нагріву і витримки 8-9 хв
— охолодити в маслі
— очистити інструмент.
Хвостова частина (рис. 1.3):
— завантажити хвостову частину інструменту в електричну соляну ванну СВС — 2,5.6.4/8,5 нагріту до температури 820-840°С. Витримати при температурі нагріву 15 хв.
— охолодити в 5% водному розчині NaCl до 150-200°С.
— охолодити на повітрі.
Процес загартування полягає в повільному нагріві інструменту; для оберігання від виникнення значної внутрішньої напруги робиться два підігрівання. Перший робиться в електродній соляній ванні СВС-3.8.4/8,5 до температури 500°С і другий — у СВС — 2,5.6.4/8,5 до температури 850°С.
При підігріванні до 800-850°С з початкової структури перліт + карбіди утворюється структура аустеніт + карбіди. Але аустеніт при цій температурі малолегований, оскільки основна маса карбідів знаходиться поза твердим розчином. Для збільшення легованості аустеніту робиться остаточний нагрів до високої температури (загартування). Загартування робиться у високотемпературній соляній ванні СВС-2.3.4/13 до 1300°С. Необхідність швидкого нагріву пов’язана із здатністю швидкорізальної сталі легко окислюватися при високих температурах. Структура при 1000-1300°С — аустеніт + карбіди, тобто така ж як і при 850°С але у зв’язку з тим, що при нагріві в цьому температурному інтервалі відбувається розчинення карбідів, аустеніт при 1300°С виходить значно більше легованим.
Повного розчинення карбідів при нагріві до максимальної температури не відбувається і великі первинні карбіди залишаються поза розчином. Витримку при високій температурі роблять дуже незначну, тільки таку, яка потрібна для прогрівання робочого об'єму інструменту.
Охолодження нагрітої швидкорізальної сталі робиться в масляному гартівному баку. Охолодження в маслі робить інструмент стійкішим в роботі.
При охолодженні (загартуванні) відбувається розпад аустеніту з утворенням мартенсіту. Але не увесь аустеніт розпадається, а частина його (25-30%) зберігається у вигляді залишкового аустеніту. Тому структура після загартування є мартенсітом загартування + карбіди + залишковий аустеніт. Мартенсіт, що утворюється, настільки дрібно голчастий, що на вигляд структура загартованої швидкорізальної сталі здається такою, що складається тільки з аустеніту і карбідів. Утворення мартенсіту при загартуванні відбувається в певному температурному інтервалі. Температури початку (Мн) і кінця (Мк) мартенситного перетворення знижуються з підвищенням температури загартування. При загартуванні від температури вище 1100 °C точка Мк розташовується при температурах нижче нуля.
При нагріві інструментів треба вживати усі заходи проти зневуглецювання сталі, яке в даному випадку може бути дуже сильним із-за високої температури нагріву. Тому соляні ванни мають добре розкислювати.
Витримка при температурі загартування забезпечує розчинення в аустеніті часток карбідів в межах їх розчинності і прогрівання робочого об'єму інструментів. При витримці відбувається збільшення зерен аустеніту і збільшення кількості розчинених карбідів.
Охолодження проводиться в маслі, але перед цим потрібно підстудити на повітрі до температури 900−1000°С (жовтий колір каління) і після цього опустити в масло. При охолодженні в маслі без підстуджування можуть вийти гартівні тріщини. Охолодження в маслі здійснюється до температури 150−200°С, після чого загартований інструмент виймають з гартівного бака і дають остигнути на спокійному повітрі.
Технологічний процес відпуску інструменту.
1) Технологія відпуску фрези дискової (рис. 1.1):
— двократний нагрів зробити у ванні селітровій електричній до температури 580°С. Тривалість кожного відпуску 20 хв
— охолодити на повітрі.
Стандартний відпуск безвольфрамової швидкорізальної сталі двократний при температурі 520 °C по 1 годині. Проте використання багатократного відпуску з витримкою по 1 годині (плюс час, необхідний для прогрівання садіння) з обов’язковим охолодженням між відпусками до нормальної температури у виробничих умовах ускладнює цикл термообробки. З метою скорочення циклу рекомендується провести високотемпературний скорочений відпуск. Для сталі 11М5Ф вживаний двократний відпуск при температурі 580 °C і тривалість кожного відпуску 20 хв. При таких відпусках досягається вища вторинна твердість, опір вигину, покращується шліфуємість за рахунок меншої шорсткості поверхні в порівнянні з цими характеристиками після стандартних відпусків.
2) Технологія відпуску свердла.
Різальна частина (рис. 1.2):
— триразовий нагрів різальної частини інструменту зробити у ванні селітровій електричній до температури 540-560°С. Тривалість кожного відпуску 1-1, 5 год
— охолодити на повітрі.
Хвостова частина (рис. 1.3):
— нагрівати хвостову частину інструменту до температури 450-500°С у ванні селітровій електричній. Тривалість відпуску 30-40 хв
— охолодити на повітрі.
3) Технологія відпуску мітчика.
Різальна частина (рис. 1.2):
— триразовий нагрів різальної частини інструменту зробити у ванні селітровій електричній до температури 540-560°С. Тривалість кожного відпуску 1-1, 5 год
— охолодити на повітрі.
Хвостова частина (рис. 1.3):
— нагрівати хвостову частину інструменту до температури 450-500°С у ванні селітровій електричній. Тривалість відпуску 30-40 хв
— охолодити на повітрі.
Після загартування швидкорізальна сталь має бути обов’язково піддана відпуску. При нагріві до 100-200°С зменшується міра тетрагона мартенсіту. У інтервалі 300-400°С спостерігається зниження твердості, що пояснюється зняттям внутрішньої напруги, що виникла в процесі загартування.
При подальшому підвищенні температури відпуску твердість підвищується, досягаючи максимуму при 550°С.
В порівнянні з твердістю після загартування твердість після відпуску при 550°С виходить вищою. Ця максимально висока твердість здатна зберігатися при подальших нагрівах під час роботи інструменту і обумовлює його теплостійкість.
В результаті відпуску відбувається перетворення залишкового аустеніту на мартенсіт.
Характерною особливістю відпуску швидкорізальної сталі, є те, що отриманий в результаті загартування залишковий аустеніт перетворюється на мартенсіт не при нагріві і не при витримці при відпуску, а під час охолодження. Такий характер перетворення носить назву вторинного загартування швидкорізальної сталі. Мартенсіт відпуску (отриманий при розпаді залишкового аустеніту при відпуску) відрізняється від мартенсіту загартування тим, що в результаті розпаду залишкового аустеніту утворюється не первинний мартенсіт, а вторинний, крім того, у зв’язку зі збідненням залишкового аустеніту легуючими елементами, утворюваний мартенсіт буде також менш легований в порівнянні з мартенсітом загартування. У зв’язку з великою стійкістю залишкового аустеніту кращий результат відносно легшого і повнішого його розпаду з набуттям вищих різальних властивостей дає триразовий відпуск.
Рис. 1.1. Режим термічної обробки фрези зі сталі 11М5Ф Рис. 1.2. Режим термічної обробки різальних частин свердла зі сталі Р6М5Ф3 та мітчика зі сталі Р6М5
Рис. 1.3. Режим термічної обробки хвостових частин свердла зі сталі Р6М5Ф3 та мітчика зі сталі Р6М5
1.6 Контроль технологічних режимів і якості різального інструменту
Для точних вимірів температури застосовується прилад потенціометр. Суть методу потенціометричного виміру температури полягає в тому, що електрорушійна сила термопари урівноважується рівною їй за величиною, але протилежною до неї по знаку електрорушійною силою від постійного джерела струму. Такий прилад дає високу точність при вимірі температури.
Контроль і регуляція температури у ваннах здійснюється термопарою.
У термічному цеху прийняті наступні методи контролю якості виробів після термообробки:
а) зовнішній огляд, тобто неозброєним оком, для визначення таких дефектів як перепал, тріщини, деформація і ін.;
б) визначення твердості;
в) контроль мікроструктури після відпуску;
г) візуальний огляд після промивання і очищення інструменту.
Після відпалу робиться контроль твердості 10% заготовок від партії за методом Бринеля, заснованого на тому, що в плоску поверхню металу вдавлюється під постійним навантаженням сталева загартована кулька. Діаметр кульки і величина навантаження встановлюється залежно від твердості і товщини матеріалу.
Після відпуску перевіряють твердість усієї партії заготівель на різальній і хвостовій частині за методом Роквела. Цим способом твердість визначають по глибині втискування наконечника приладу в поверхню випробовуваного металу. Випробування здійснюється твердоміром ТК. Наконечником служить алмазний конус з кутом при вершині 120°.
2. Проектна частина
2.1 Визначення дійсного річного фонду часу роботи устаткування.
Режим роботи устаткування (кількість змін в добу) встановлюють залежно від типу виробництва (одиничне, серійне, масове), технології термообробки, типу устаткування та ін. В дрібносерійному виробництві раціональною є робота у дві зміни.
Для нормальних умов роботи при переривчастому графіку слід виходити з п’ятиденного робочого тижня тривалістю 41 година Тривалість однієї зміни:
ф=41:5=8,2 год.
Приймаємо режим роботи устаткування — 2-і зміни. Тоді номінальний фонд часу роботи складає:
Фн=(365−105−10)Ч2Ч8,2=4100 год.
Дійсний річний фонд часу роботи устаткування в умовах переривчастого робочого тижня складає:
де Р — витрати часу на ремонт устаткування%;
П — витрати часу на переналадку устаткування, %.
Значення Р залежать в основному від виду роботи, типу устаткування і складають 3−10%. Значення П вибирають в межах 0−5%, це залежить від частоти переналадок.
Для камерних печей приймаємо Р=4, П=2. Тоді дійсний річний фонд часу роботи устаткування в умовах переривчастого робочого тижня складає:
год.
2.2 Вибір і розрахунок необхідної кількості основного устаткування
Коротка характеристика основного устаткування
В якості основного устаткування для термообробки інструментів вибрана напівавтоматична лінія з печей-ванн для інструментів (рис. 2.1)
Рис. 2.1. Напівавтоматична лінія з печей-ванн для інструментів
1 — соляна ванна першого підігріву; 2 — соляна ванна другого підігріву; 3 — ванна остаточного нагріву; 4 — селітрова ванна для загартування; 5 — камера охолодження; 6 — селітрова ванна для відпуску; 7 — ванна виварювання; 8 — ванна травління; 9 — ванна промивання; 10 — ванна нейтралізації; 11 — ванна пасивування; 12 — ланцюговий конвеєр; 13 — стіл завантаження; I-III — шляхи автооператорів У цьому агрегаті (рис. 2.1, 2.2) з печами ваннами для дрібних інструментів є горизонтальні конвеєри, які рухаються із заздалегідь встановленою швидкістю і пересувають пристосування з інструментами у відповідних ваннах, і вертикальні, що піднімають пристосування з деталями з горизонтальних конвеєрів і передають їх від однієї ванни до іншої. Вертикальні конвеєри рухаються також із заздалегідь встановленою швидкістю, яку можна регулювати. Агрегат складається з трьох горизонтальних конвеєрів 1, 2 і 3, кожен з яких має свій привід і рухається з необхідною швидкістю. Це дозволяє давати різну витримку в окремих ваннах агрегату. Час проходження конвеєром 1 першої ванни можна регулювати впродовж 4-8 хв, конвеєром 2 — впродовж 10-30 хв і конвеєром 3 — в гартівному баку або ванні впродовж 1-8 хв. Вертикальні передавальні конвеєри 4, 5, 6 і 7 отримують рух також від незалежних приводів. Кожен з конвеєрів починає працювати, коли пристосування з деталями приходить до кінця шляху на горизонтальному конвеєрі в цій ванні, і включає автоматично відповідний контакт.
Рис. 2.2. Схема напівавтоматичної лінії з печей-ванн
а — схема агрегату; б — схема включення передавальних конвеєрів; 1-7 — конвеєри агрегату; 8 — мікровимикач; 9 — електродвигун; 10 — редуктор; 11 — магнітний пускач; 12 — зірочка; 13 — кулачок Електрична схема включення вертикальних транспортерів показана на рис. 2.2б. Завантаження нових пристосувань з деталями на конвеєр 4 (рис. 2.2а) робиться через 1-8 хв. Повне переміщення конвеєра 5 робиться впродовж регульованого інтервалу часу 4-30 сек, конвеєра 6, впродовж 4-20 сек і конвеєра 7 — від 0,5 до 2 хв. Пристосування з деталями переходять з одного конвеєра на інший автоматично. Перевагою цього агрегату є самостійні приводи і варіатори швидкостей 8 для кожного конвеєра, що дає можливість використовувати агрегат для найрізноманітніших режимів обробки. Такий агрегат можна застосовувати для звичайної термічної обробки (загартування і відпуск), а також для ізотермічної обробки, ціанування та ін. Продуктивність такого агрегата складає 280 кг/год.
У конструкції агрегату з печами-ваннами в якості транспортного пристрою використовується автооператор з програмним управлінням. Автооператор є зварним візком з штангою і траверсою і з двома електричними приводами горизонтального і вертикального переміщення. Внаслідок цього автооператор може здійснювати горизонтальні рухи по рейковому шляху, а також піднімати і опускати штангу з траверсою. Підвіска для транспортування інструментів в цій лінії має універсальний затиск і дозволяє захоплювати інструменти будь-якої форми перерізом від 10 до 100 мм. Підвіски можуть бути використані над усіма транспортуючими облаштуваннями цієї лінії - ланцюговим і штанговим конвеєрами, механізмом зворотно-поступального руху, автооператорами і підвісним конвеєром. За допомогою автооператора інструменти звільняються від затисків підвіски. Переміщення підвісок у ваннах відбувається за допомогою штангового конвеєра і пневмопривода. Перенесення з ванни у ванну робиться автооператорами.
Контрольно-вимірювальна апаратура і система автоматичного регулювання процесу і управління механізмами забезпечують виконання технологічного процесу термічної обробки за заданою програмою.
Технологічне устаткування лінії встановлене усередині металоконструкції, закритої кожухом і забезпеченою витяжною вентиляцією. На пульті управління лінії розташовані показуючі прилади-дублери, що дозволяють візуально контролювати температуру ванн. Схема автоматики синхронізує роботу трьох агрегатів, забезпечуючи задані технологічним процесом параметри.
Технічна характеристика [20]:
Продуктивність лінії, кг/ч…280
Темп видачі, хв…2,7−5
Число навантажених підвісок…54
Потужність приводів лінії, кВт…18
Потужність технологічного устаткування, кВт…495
Габаритні розміри лінії, мм…27 000Ч2800Ч4300
Маса лінії, т…20
Для попередньої термічної обробки інструменту вибрана електрованна соляна електродна СВС 2.4.4/8,5.
Рис. 2.3. Електрованна соляна електродна СВС-2.4.4/8,5:
1 — футерування; 2 — кришка; 3 — термопара; 4 — електрод; 5 — кожух; 6 — водоохолодження; 7 — вентиляційний кожух
На рис. 2.3 приведений загальний вигляд низькотемпературної соляної електрованни СВС-2.4.4/8,5, яка входить в напівавтоматичну лінію з печей ванн для інструментів. Нагрів виробів здійснюється в розплаві хлористих солей що знаходиться у футерованому тиглі. Вогнетривкий шар футерування викладений із спеціальних високоглиноземістих фасонних плит. Електрованна обладнана однофазною електродною групою. Електроди квадратного перерізу розташовані на одній стороні тигля ванни на близькій відстані один від одного, що забезпечує наявність робочого простору, вільного від протікання струму. Електродна група захищена керамічною плитою з боку робочого простору, чим запобігається коротке замикання електродів виробами, що нагріваються.
Інша частина електродної зони перекрита шамотною плитою для зменшення теплових втрат. Конструкція електродної групи дозволяє замінювати електроди без зливу солі. Матеріал робочої частини електродів — високохромиста сталь. Ванна живиться електроенергією через знижувальний трансформатор, на високій стороні якого є перемикач східців напруги, що дозволяє регулювати споживану потужність в залежності від режиму роботи. Ванна забезпечена рухливою футерованою кришкою, бортовим відсмоктувачем. На період пуску передбачена установка у ванну виймального блоку нагрівачів, що живиться від знижувального трансформатора ванни.
У однофазних соляних ваннах, що відрізняються достатньою стійкістю робочого режиму і підвищеною інтенсивністю руху розплаву, перепад температур в його межах не перевищує ±3,5 град.
Соляні електрованни нової серії почали виготовляти з одно-фазними електродними групами, електродами погружного типу, рухливою футерованою кришкою і трипозиційним регулюванням температури.
При виготовленні цих електродних ванн передбачені слідуючі технічні рішення:
— прямокутна форма робочого простору;
— застосування однофазних електродних груп, що складаються з двох електродів квадратного перерізу, що забезпечують електромагнітну циркуляцію розплавленої солі;
— перекриття електродної зони керамічними блоками в малих типорозмірах електрованн з керамічним тиглем;
— застосування в якості датчика температури радіаційного пірометра для електрованн до 1300 °C і термопари для электро-ванн до 1000 °C;
— можливість агрегатування електрованн різних температурних груп і вбудовування їх в потокові лінії;
— забезпечення техніки безпеки шляхом установки бортових відсмоктувачів, парасольок, кришок, застосування спеціальних пристроїв для розплавлення солі.
Нижче приведена технічна характеристика соляної ванни (у чисельнику — при робочій температурі 850 °C, в знаменнику — при робочій температурі 650°С) [18]:
Таблиця 2.1. Технологічні дані і характеристика соляної електрованни СВС 2.4.4/8,5
№ п/п | Найменування параметра | Норма | |
Встановлена потужність, кВт | |||
Максимальна робоча температура,°С | |||
Потужність холостого ходу, кВт | 16,5/10,5 | ||
Продуктивність, кг/год | 270/200 | ||
Напруга живлячої мережі, В | |||
Число фаз | |||
Тип знижувального трансформатора | ТО-35АЗ | ||
Кількість трансформаторів | |||
Напруга на електродах, В | |||
пускове | 20; 16,5 | ||
робоче | 14,1; 12,2 | ||
холостого ходу | 9,8; 8,1; 6,9 | ||
Число електродних груп | |||
Об'єм розплавленої солі, л | |||
Питома витрата електроенергії, кВт· год/кг | 0,113/0,152 | ||
Витрата охолоджувальної води, м3/год | 0,3 | ||
Розміри робочого простору, мм | |||
ширина | |||
довжина | |||
глибина | |||
Габаритні розміри | |||
ширина | |||
довжина | |||
висота | |||
Маса, т | |||
металоконструкцій | 0,6 | ||
запасних частин | 0,156 | ||
комплектуючого устаткування | 0,914 | ||
Загальна маса ванни (без солі), т | 1,8 | ||
Загальний вигляд високотемпературної соляної ванни СВС-2.3.4/13 призначеною для остаточної термічної обробки інструменту приведений на рис. 2.4, технічні дані вказані в таблиці. 2.2.
Рис. 2.4. Електрованна соляна електродна СВС-2.3.4/13:
1 — футерування; 2 — кришка; 3 — парасолька; 4 — пірометр; 5 — електрод; 6 — шинопровід від трансформатора; 7 — трансформатор; 8 — вентиляційний кожух
Таблиця 2.2. Технічні дані і характеристика устаткування для остаточної термообробки [18]
Найменування параметра | Норма | ||
Ванна соляна (I підігрів) | |||
1. | Максимальна робоча температура,°С | ||
2. | Потужність, кВт | ||
3. | Склад солі | 25% BaCl2+75% NaCl2 | |
4. | Об'єм солі, що розплавляється, л | ||
Ванна соляна (II підігрів) | |||
1. | Максимальна робоча температура,°С | ||
2. | Потужність, кВт | ||
3. | Склад солі | 25% BaCl2+75% NaCl2 | |
4. | Об'єм солі, що розплавляється, л | ||
Ванна соляна (остаточний нагрів) | |||
1. | Максимальна робоча температура,°С | ||
2. | Потужність, кВт | ||
3. | Склад солі | 100% BaCl2 | |
4. | Об'єм солі, що розплавляється, л | ||
Ванна селітрова електрична | |||
1. | Максимальна робоча температура,°С | ||
2. | Потужність, кВт | ||
3. | Склад солі | 100% KNO3 | |
4. | Об'єм солі, що розплавляється, л | ||
На рис. 2.5 приведений загальний вигляд електричної селітрової ванни для відпуску, технічні дані вказані в таблиці. 2.3.
Рис. 2.5. Ванна селітрова електрична для високого відпуску
1 — короб витяжний; 2 — тигель; 3 — каркас; 4 — кришка; 5 — ємність
Таблиця 2.3. Технологічні дані і характеристика ванни селітрової електричної [16]
№ п/п | Найменування параметра | Норма | |
Призначення ванни | високий відпуск | ||
Встановлена потужність, кВт | |||
Максимальна робоча температура,°С | |||
Робоча температура,°С | |||
Напруга живлення, В | |||
Кількість нагрівачів | |||
Діаметр дроту нагрівача, мм | |||
Тип нагрівачів | зигзагоподібні | ||
Регулювання температури | автоматичне | ||
Розміри робочого простору, мм | |||
діаметр | |||
висота | |||
Розрахунок необхідної кількості основного устаткування
При виборі устаткування необхідно враховувати такі чинники, як якість термообробки, екологічна безпека, мінімальна трудомісткість, низька собівартість та ін.
Початкові дані для розрахунку необхідної кількості основного устаткування так само, як додаткового і допоміжного, такі:
річна програма термічної обробки виробів цієї групи, Пi, кг, яка закріплена за цією операцією;
продуктивність вибраного устаткування для обробки деталей цієї групи, Рi, кг/рік;
вибраний режим роботи устаткування Ф°D, рік, тобто річний дійсний фонд часу роботи устаткування.
Для термічної обробки вибираємо напівавтоматичну лінію з печей ванн для інструментів, продуктивність якої складає 280 кг/ч.
Кількість одиниць устаткування можна визначити укрупнено, використовуючи продуктивність устаткування Рi.
Необхідна кількість годин Ei, для виконання цієї виробничої програми для термообробки інструменту «фреза дискова» визначаємо по формулі:
Розрахункова кількість устаткування, необхідного для виконання річної програми деталей цієї групи:
де Фд — річний фонд часу роботи устаткування, год Розрахункову кількість устаткування округлюємо до найближчого цілого числа і отримуємо прийняту кількість устаткування — Кпр=1
Коефіцієнт завантаження устаткування:
Необхідна кількість годин Ei, для виконання цієї виробничої програми для термообробки інструменту «свердло» визначаємо за формулою:
Розрахункова кількість устаткування, необхідного для виконання річної програми деталей цієї групи:
Коефіцієнт завантаження устаткування:
Необхідна кількість годин Ei, для виконання цієї виробничої програми для термообробки інструменту «мітчик» визначуваний по формулі:
Розрахункова кількість устаткування, необхідного для виконання річної програми деталей цієї групи:
Коефіцієнт завантаження устаткування:
Таблиця 2.4. Розрахунок кількості виробничого устаткування
Устаткування | Найменування деталі | Річна програма т | Необхідна кіль-ть годин роботи год | К-ть одиниць устаткування | Коефіцієнт завантаження устаткування | ||
розрах. | прийн. | ||||||
Напівавтоматична лінія з печей-ванн для інструментів | фреза дискова | 0,97 | 0,97 | ||||
Напівавтоматична лінія з печей-ванн для інструментів | свердло | 0,97 | 0,97 | ||||
Напівавтоматична лінія з печей-ванн для інструментів | мітчик | 0,84 | 0,84 | ||||
2.3 Підйомно-транспортні засоби
У термічних цехах широко застосовують різне підйомно-транспортне устаткування. Транспорт ділянки забезпечує завантаження і переміщення інструменту відповідно до технологічного процесу, потоковості виробництва; механізацію трудомістких процесів з повним використанням потужності підйомно-транспортних механізмів.
На термічній ділянці по виробництву різального інструменту для виконання підйомно-транспортних операцій використовуються 3 підвісні кран балки вантажопідйомністю 1 т., кожна переміщається паралельно один відносно одного уздовж ділянки по рейках укладених на підкранові балки. Для ремонтних робіт на термічній ділянці використовуються мостовий кран, який переміщається по усьому прольоту цеху.
2.4 Розрахунок і вибір необхідної кількості додаткового і допоміжного устаткування
На ділянці термічної обробки є наступне додаткове устаткування:
— прилад Бринеля для виміру твердості 10% заготівель за 2 зміни після відпалу. Продуктивність приладу 60 шт./год або 0,60 шт. за 2 зміни.
— після остаточного нагріву при загартуванні фрез, різальній і хвостовій частині свердел і мітчиків, інструмент необхідно охолодити. Таким чином для остаточного нагріву, після якого, необхідно охолодити інструмент в маслі використовується три ванни, тому потрібно три камери охолодження, які повинні розташовуватися навпроти гартівної ванни, на відстані 1,5-2 м. Камери охолодження призначені для регульованого охолодження металевих деталей і виробів після нагріву їх в термічних печах або агрегатах.
— прилад Роквела для виміру твердості 100% інструменту після відпуску. Знадобиться два прилади.
— ванни виварювання для очищення інструментів від окалини шляхом відновлення оксидів металів, по 1 ванні для кожного виду інструментів. В якості відновника застосовується гідрид натрію. Процес відновлення оксидів йде по наступних реакціях:
Fe3O4 + 4NaH = 3Fe + 4NaOH;
Fe2O3 + 3NaH = 2Fe + 3NaOH;
FeO + NaH = Fe + NaOH;
CrO3 + NaH = 2CrO + NaOH;
CuO + NaH = Cu + NaOH.
Гідрид натрію добре відновлює магнітний окисел заліза і більшість оксидів легованих елементів, які дуже важко піддаються травлінню в кислотах. В якості розчинника гідриду натрію використовується розплав їдкого лугу. Продуктами реакції є відновлений метал і їдкий луг (NaOH), який компенсує віднесення лугу з деталями. Для утворення розплаву лугу температура нагріву ванни підтримується рівною 370−400єС, а вміст гідриду натрію в розчині лугу 1,5−2%. Процес відновлення ведеться в електродних ваннах (рис. 2.6). Електроди розташовуються уздовж задньої бічної стінки ванни і відділяються від робочого простору останніми залізними гратами 2. Для зменшення втрат тепла доцільно зовнішні стінки ванни 6 ізолювати малотеплопровідним матеріалом.
Необхідний для відновлення гідрид натрію найчастіше отримують безпосередньо у ванні. З цією метою уздовж її передньої стінки згори встановлюють спеціальний генератор, який представляє залізну коробку 5, перевернуту вгору, краї її опущені в розплав лугу. Коробка вгорі має отвір, що герметично закривається 4, для завантаження металевого натрію і ряд трубок 3, по яких в розплав лугу подається водень. Металевий натрій внаслідок низької температури плавлення (близько 100°С) розплавляється і розтікається в генераторі по поверхні лугу. Водень, що підводиться по трубках, барботується через шар розплавленого лугу і вступає в реакцію з металевим натрієм, внаслідок чого утворюється гідрид натрію
Na + ½ H2 = NaH
Гідрид натрію розчиняється в розплавленому лузі і рівномірно розподіляється по ванні під впливом сильних конвекційних потоків, викликаних електромагнітним перемішуванням при електродному нагріві.
Рис. 2.6. Ванна для відновлення окалини гідридом натрію
— травильні ванни для очищення від окалини та іржі, по 1 ванні для кожного виду інструментів. Травління, крім того, виявляє поверхневі дефекти на деталях (тріщини, волосовини і т.д.). У інструментальних термічних цехах застосовують електролітичне травління. Цей спосіб повністю унеможливлює перетруювання і допускає очищення деталей з дрібним різьбленням. Електролітичне травління полягає в обробці деталей в електроліті певного складу, причому деталі є одним з електродів (анодом або катодом). При тому, що анодному, що труїть, при недотриманні режиму, може вийти перетруювання, що виключається при тому, що катодному, що труїть. Зразковий склад і режим роботи ванни того, що труїть: сірчана кислота — 50 г./л, соляна кислота — 20 г./л, хлористий натрій — 22 г./л, температура ванни — 60-70єC, щільність струму — 7-10 а/дм3, тривалість процесу — 10-15 хв. Ванна травління є баком прямокутного перерізу (рис. 2.7), звареним з листової сталі завтовшки 6−8 мм. Для видалення шкідливої пари ванна забезпечується вентиляцією з двостороннім відсмоктувачем. Окрім вентиляції до ванни монтують трубопроводи холодної і гарячої води і каналізації.
Рис. 2.7. Ванна для електролітичного травління Ванна забезпечується підвісним конвеєром для пересування підвісок або кошиків з деталями і для перенесення з однієї ванни в іншу. Такі агрегати використовують в чистових термічних цехах для очищення деталей від окалини замість дробеструменевих апаратів.
— ванни промивання, по 1 ванні для кожного виду інструментів. У цій ванні деталі промивають гарячим содовим розчином з подальшим охолодженням водою. Внутрішня частина зварного корпусу ванни розділена перегородкою на дві секції. У першій секції на деталі згори і знизу подається гарячий розчин через розподільники з розбризкувачами, в другій секції деталі охолоджуються проточною водою. Конвеєрна стрічка натягнута на два гладкі барабани. Вал провідного барабана приводиться в обертання електродвигуном змінного струму через триступінчатий шків. Содовий розчин, що подається насосом з бака через фільтр в розподільник з розбризкувачами, промиває деталі і повертається у бак. Розігрівання розчину і підтримання його температури забезпечується подачею пари. Згори ванна закрита знімною кришкою.
— ванни нейтралізації, по 1 ванні для кожного виду інструментів.
— ванни пасивування, по 1 ванні для кожного виду інструментів. Ванна (рис. 2.8) складається з корпусу 1, трьох штанг 4 для навішування деталей, бортових відсмоктувачів, двох скоб для транспортування ванни. Футерування ванни робиться винипластом листовим або пластикатом. Ванна встановлюється на опорах 2. Перед футеруванням ванни корпус перевіряється на герметичність, знежирюється бензином-розчинником і покривається кислотостійким лаком. Перед пасивуванням поверхня деталі знежирюється електрохімічним способом, промивається у воді, протравлюється, знову промивається у воді і потім пасивується в розчині 5−10% нітрату натрію. Використання ванни покращує якість поверхні інструменту.
Рис. 2.8. Ванна пасивування В якості допоміжного устаткування на ділянці використовується:
— для контролю температури і часу режиму на кожній ванні встановлений потенціометр, перетворювач і годинник.
— ланцюгові конвеєри (рис. 2.9) для пересування пристосування з деталями у відповідних ваннах і передачі їх від однієї ванни до іншої. Рух конвеєрів відбувається по замкнутій трасі. Тяговим пристроєм є ланцюг, що огинає, веде і направляє зірочки. Ланцюг має ходові ролики, які котяться по нижній полиці двотаврової балки. До осей роликів прикріплені підвіски з гачками, на які вішаються пристосування з деталями. Приводна станція конвеєра складається з електродвигуна і передатного механізму з варіатором, що служить для зміни швидкості руху конвеєра.
Рис. 2.9. Схема ланцюгового конвеєра
1 — підвісна рейка; 2 — тяговий ланцюг; 3 — робоча каретка; 4 — холоста каретка; 5 — пристосування з деталями; 6 — сітчасте обгороджування Таблиця 2.5. Звідна відомість устаткування
Устаткування | Модель | Призначення | Характеристика | Кіль-ть шт. | Потужність кВт | |
Основне устаткування | ||||||
Ванна соляна | СВС-2.4.4/8,5 | відпал | Робоча температура 650-920С | |||
Ванна соляна | СВС-3.8.4/8,5 | загартування I підігрів | Робоча температура 500С | |||
Ванна соляна | СВС — 2,5.6.4/8,5 | загартування II підігрів | Робоча температура 800-850С | |||
Ванна соляна високотемп. | СВС-2.3.4/13 | загартування III підігрів | Робоча температура 1200-1230С | |||
Ванна селітрова електрична | 9978.1817 | відпуск | Робоча температура 550-580С | |||
Додаткове устаткування | ||||||
Прилад Бринеля | ТШ | вимір | навантаження 1000 кг | |||
Прилад Роквела | ТК | вимір | навантаження 150 кг | |||
Камера охолодження | охолодження | |||||
Ванна виварювання | очищення | Робоча температура 370-400єС | ||||
Ванна травління | очищення | Робоча температура 60-70єC | ||||
Ванна промивання | МКП | промивання | ||||
Ванна нейтралізації | нейтралізація | |||||
Ванна пасивування | пасивування | |||||
Допоміжне устаткування | ||||||
Потенціометр, перетворювач, годинник | КСП3, ТХА-0806 16 р | контроль температури і часу режимів | ||||
Кран балка | КБ-1 | перевезення | Q=1т | 7,5 | ||
Монорейка з тельфером | Т — 0,25 | перевезення | Q=0,25т | 3,5 | ||
Конвеєр ланцюговий | пересування у ваннах | |||||
2.5 Розрахунок енергії ділянки
Визначаємо потребу цеху в різних видах енергії. Споживана енергія розраховується по формулі, кВт:
де Ni — потужність кожного струмоприймача з паспортних даних устаткування, кВт:
— напівавтоматична лінія з печей-ванн для інструментів (3) — 495 кВт;
— кран балка (1) — 7,5 кВт;
— тельфер (1) — 3,5 кВт.
Kc — коефіцієнт попиту, застосовується рівним 1,05.
Річна витрата електроенергії визначається за формулою, кВт.
де Ф°D — дійсний річний фонд часу роботи устаткування;
л — коефіцієнт завантаження устаткування (0,93).
Розрахунок витрати води
Вода розходиться на виробничі потреби і на очищення інструментів. Розраховуємо витрату води мийної машина:
— витрата води складає 0,06 м3/ч
— ;
— .
0,06 · 0,93 · 3854 =215 м3/рік
3. Спеціальна частина
3.1 Порівняння технологічних властивостей швидкорізальних сталей та безвольфрамових швидкорізальних сталей
Історія розвитку швидкорізальних сталей налічує більше 80 років. Усі ці роки учені різних країн наполегливо працювали над проблемою зниження в них кількості вольфраму.
Швидкорізальні сталі є основними матеріалами у виробництві металорізальних інструментів. Вони відрізняються поєднанням великих значень твердості (64−65 HRC) і теплостійкості (620−630°С), а також міцності (ув изг~3000−3500 МПа) і ударної в’язкості (КС~0,3−0,4 МДж/м2). Ці властивості забезпечуються, по-перше, великою кількістю дорогих і дефіцитних легуючих компонентів швидкорізальної сталі (W, Mo, V, Co та ін.) і, по-друге, виділенням при відпуску швидкорізальних сталей з їх основи (мартенсіту) безлічі дрібних (дисперсних) карбідів цих компонентів.
В той же час, недолік усіх широко відомих швидкорізальних сталей полягає в тому, що вони відносяться до класу евтектичних сталей і, по суті, є білими чавунами. Численні і масивні карбіди евтектики, по-перше, знижують, як і в чавунах, запас пластичності сталі і, по-друге, не розчиняючись при нагріві до гартівних температур, виключають участь в зміцненні швидкорізальної сталі до 50% усіх її легуючих компонентів.
У наш час розробляються швидкорізальні сталі нового покоління, а саме економнолеговані швидкорізальні сталі заевтектоїдного класу.
Економнолеговані швидкорізальні сталі. У зв’язку із зростаючою дефіцитністю вольфраму і молібдену — основних легуючих елементів, використовуваних при виробництві швидкорізальних сталей, все більше застосування знаходять сталі з низьким вмістом вказаних елементів або що не містять вольфрам, які називають економнолегованими. Серед сталей цього типу найбільше застосування отримала сталь 11Р3М3Ф2, яка має досить високі показники по твердості (НRC 63−64), міцності (ув=3,4 ГПа) і теплостійкості (до 620°С).
У структурі цих сталей практично відсутня евтектика і усі їх легуючі компоненти зосереджені в карбідах, розчинних при гартівних температурах, і тому практично повністю задіяні в зміцненні сталі в процесі відпуску. На цій основі розроблена швидкорізальна сталь 11М5Ф, яка не поступається відомим сталям Р6М5 і Р18 по твердості і теплостійкості і перевершує їх по запасу пластичності при істотно меншому вмісті легуючих компонентів.
Низьколегована безвольфрамова сталь 11М5Ф (1,06% З; 5,5% Мо; 4,0% Сr; 1,5% V) належить до нового класу заевтектоїдних сталей, на відміну від традиційних ледебуритних сталей. Нагрів під загартування дозволяє розчинити усі карбіди типу Ме6С (що неможливе для ледебуритних сталей), що забезпечує легованість і властивості сталі 11М5Ф приблизно на рівні відповідних показників сталі Р6М5.
В той же час, швидкорізальна сталь 11М5Ф відрізняється широкою універсальністю: після відповідної термічної обробки вона з успіхом використовується для виробництва металорізальних і штампових інструментів для холодної і напівгарячої деформації, а також для інструментів, вироблюваних литвом. Через свою універсальність сталь 11М5Ф особливо придатна для малих і середніх виробництв. Сталь 11М5Ф пройшла успішні заводські випробування більш ніж на 50 підприємствах.
Нині на тій же основі розроблені заевтектоїдні швидкорізальні сталі 11М7Ф і 11М7ФЮС, які по твердості (67−68 HRC) і теплостійкості (635−640°С) перевершують сталі евтектичного класу, у тому числі з підвищеним вмістом кобальту (до 8%).
Крім того, склад цих сталей, на відміну від існуючих, дозволяє застосовувати їх цілеспрямовано для виробництва інструментів з плазмовими покриттями, а також для тих, що піддаються хіміко-термічній обробці.
До теперішнього часу досягнуті значні успіхи. Проте робіт із створення швидкорізальних сталей без вольфраму було виконано порівняно мало. Вони відносилися, в основному, до 40-х років минулого століття і особливого успіху в промисловості не мали. Багато що залежало від методів визначення твердості і зносостійкості сталі при кімнатній температурі, що застосовувалися у той час, а також виборі режимів термічної обробки.
3.2 Вплив різних чинників на структуру і властивості безвольфрамової швидкорізальної сталі
Фазовий склад
Фазовий склад швидкорізальних сталей після відпалу, що виконується в промислових умовах на низьку твердість, не є повністю рівноважним. Приблизно його можна охарактеризувати для безвольфрамовых сталей — по діаграмі Fe — Mo — C (рис. 3.1). Зміна вмісту молібдену від 5 до 12% не впливає на фазовий склад, змінюється лише кількісне співвідношення фаз. Ванадій знаходиться в карбіді Мe6С і також не змінює фазового складу. Розглянемо основні фази при 20 °C.
Рис. 3.1. Переріз діаграми стану системи Fe — Mo — C при 20єC
1. Альфа-фаза містить 50 — 70% хрому, наявного в сталі, невелику кількість молібдену і ванадію.
2. Карбід Мe6С, в якому є присутніми основна кількість молібдену, ванадію і частина хрому. Кількість карбідів залежить від складу сталі і змінюється в межах від 10 до 30% (по масі).
3. Окрім вказаних на діаграмі, є присутніми: карбід Мe23С6 кількість якого в різних швидкорізальних сталях майже однаково, в цьому карбіді міститься також частина ванадію і трохи молібдену; карбід МeС; карбід Мe3С в окремих ділянках внаслідок ліквації, кількість його може бути більша: у відпущеній сталі, в якій Мe3С — проміжна фаза, він утворюється також при збільшенні вмісту вуглецю без відповідного підвищення кількості молібдену і ванадію; карбід Мe2С в якості проміжної фази після відпуску в сталі з високим вмістом вуглецю — в литому стані.
Структура литої, деформованої і відпаленої сталі
Для литого стану характерна найбільш значна неоднорідність структури. Вона обумовлена наступними перетвореннями.
Перитектичне перетворення. Твердіння розпочинається з виділення кристалів (д-раствора, що містять менше вуглецю, ніж рідини. При пониженні температури (д-кристали взаємодіють з рідиною по перитектичній реакції: д + рідина + рідина.
Перетворення, як перитектичне, відбувається на поверхні розділу фаз. Тому нова г-фаза утворюється спочатку в поверхневих шарах д-кристалів і перериває контакт між серцевиною д-кристалів і рідиною, що залишилася, збагаченою вуглецем. Подальше протікання перитектичної реакції і насичення серцевини д-кристалів може розвиватися лише в результаті дифузії вуглецю і легуючих елементів з рідини через г-фазу і д-кристали. Цей процес навіть в умовах уповільненого охолодження протікає лише частково; у структурі зберігається деяка кількість д-фази. Міра перетворення і величина менш легованих ділянок д-фази, що залишається, залежать, таким чином, від швидкості охолодження.
При подальшому охолодженні відбувається евтектоїдний розпад — фази з утворенням — евтектоїда — дисперсної суміші аустеніту і карбідів, частина яких цементитні; - евтектоїд із-за великої подрібненості сильно травиться, здається темним і погано відрізнимим в мікроскопі від перліту.
Ця неоднорідність будови спостерігається більше при швидкому охолодженні, коли перитектичне перетворення мало розвивається, тобто у невеликих відливках.
Твердість невеликих відливок 60 HRC; зовнішній шар зерна виконує роль каркаса і забезпечує високий опір втискуванню.
Неоднорідність будови, що створюється перитектичним перетворенням, усувається термічною обробкою; для цієї мети потрібна головним чином дифузія вуглецю. Тому відпал литої сталі вирівнює структуру, що дозволяє отримати однорідну мікротвердість металевої основи при подальшому загартуванні.
Вплив нагріву на структуру сталі
Відмінності у будові відпаленої сталі мало впливають на перетворення при нагріві для відпуску.
При 1000−1150°С розчиняються в першу чергу дрібні карбіди, у тому числі і розташовані орієнтовано по межах зерен, а при нагріві вище 1150 °C — більші карбіди.
З підвищенням легованості твердого розчину знижуються температури мартенситного перетворення і зростає кількість аустеніту. Воно збільшується майже пропорційно підвищенню температури загартування і при нагріві на дрібне зерно (балу 11−10) досягає 22−28%.
Зерно сталі. Для швидкорізальних сталей, що мають багато надмірних карбідів, характерне збереження дрібного зерна навіть при високому нагріві, що перевищує температури загартування заевтектоїдних сталей.
Дуже дрібне зерно (балу 12−11) зберігається при температурах, при яких вже досягається значне насичення аустеніту (1190−1220°С).
Підвищення нагріву додатково на 25−30°С вже викликає помітніший ріст зерна: до балу 10−9. Істотно, що такому нагріву відповідає насичення аустеніту вуглецем і легуючими елементами, близьке до граничного.
У сталі з великою карбідною неоднорідністю (бал 7−9) утворюється зерно неоднакової величини. У ділянках, збіднених карбідами, ріст зерна починається при температурах, на 10−15°С нижчих, ніж в сталі з дрібними і рівномірно розподіленими карбідами.
Ще більше підвищення температури на 10−20°С, при якому зберігаються дрібні карбіди, викликає помітні якісні зміни структури. Спостерігається стрибкоподібний ріст зерна до балу 8−7 і утворення карбідної сітки, що виникає при охолодженні. Легований аустеніт стає сильно перенасиченим при нижчих температурах (1000 — 700°С), тобто, в температурній області, в якій ще інтенсивно протікають дифузійні процеси. Тому навіть при швидкому охолодженні з аустеніту устигає виділитися частина карбідів, розчинених при високому нагріві. Ці карбіди із-за впливу меж зерен виділяються, головним чином, в пограничних шарах.
Злам сталі. Сталь з дрібним зерном має фарфоровидний матовий злам. Ріст зерна до балу 9−8 супроводжується утворенням грубішого зламу. По виду зламу можна таким чином визначати температури загартування, що не викликають зайвого росту зерна: до балу 9.
Вплив нагріву на властивості сталі
Зміна складу твердого розчину і структури, що виникають в процесі загартування, неоднаково впливають на різні властивості швидкорізальної сталі.
Теплостійкість, оскільки вона визначається тільки складом твердого розчину, зростає з підвищенням температури загартування спочатку значно, коли розчиняється велика частина вторинних карбідів і ще зберігається дрібне зерно (бал 10). При подальшому підвищенні температури нагріву теплостійкість збільшується менше, але це супроводжується значним ростом зерна.
Зміна механічних властивостей характеризується кривою з максимумом. При нагріві до відносно низьких температур вони зростають, а потім після вищого нагріву знижуються. Температура цього максимуму різна для сталей різного складу і для деяких механічних властивостей.
Твердість загартованої сталі зростає до 64−65 HRC після нагріву, що зберігає зерно балу 10 і знижується до 62−63 HRC після загартування з вищих температур. Її зниження викликане ростом кількості аустеніту. Після відпуску, що викликав дисперсне твердіння, ця відмінність змінюється; сталь, що загартована з високого нагріву і отримала більш легований розчин, має більшу твердість і опір пластичнії деформації, ніж сталь, загартована з нижчої температури.
Міцність загартованої сталі знижується з підвищенням температури загартування через зростання зерна і напруги. Проте у відпущеній сталі з підвищенням температури загартування, що ще зберігає дрібне зерно (балу 12−11), вона зростає, завдяки зміцнюючому впливу дисперсних карбідів, що виділяються при відпуску.
В’язкість при загартуванні з невисоких температур трохи зростає завдяки розчиненню карбідів, присутніх по межах зерен. Проте подальший нагрів викликає різке зниження в’язкості, що настає після загартування з нижчих температур, ніж зниження міцності; це викликано великою чутливістю в’язкості до росту зерна.
Щільність сталі і лінійні розміри зразків з підвищенням температури загартування спочатку збільшуються, а потім зменшуються, внаслідок впливу зростаючої кількості залишкового аустеніту.
Перетворення після високого нагріву (для загартування)
Переохолоджений аустеніт має високу стійкість. Для усіх теплостійких сталей характерно, що перлітовому перетворенню передує виділення деякої кількості карбідів. Аустеніт, насичений вуглецем і легуючими елементами при високому нагріві, стає перенасиченим і здатним до виділення карбідів вже в результаті невеликої витримки при нижчих температурах (1000−550єС). Карбіди, що виділяються, розташовуються переважно по межах зерен, міцність знижується. Тому швидкорізальні сталі недоцільно гартувати на повітрі. Для попередження виділення карбідів потрібне прискорене охолодження в ділянці надкритичних температур, а також в області перлітового перетворення.
При нижчих температурах (625−400єС) аустеніт дуже стійкий. Навіть тривала витримка не викликає помітного перетворення, що використовують при ступінчастому загартуванні. Температури витримки краще вибирати в нижній зоні 500−400єС, щоб повністю попередити виділення карбідів. Структура сталі, загартованої з такою витримкою, не відрізняється від отримуваної при безперервному охолодженні в олії.
Стійкість аустеніту у бейнітній області (400−200єС) менша, ніж в перлітовій. Це пов’язано з невеликою концентрацією вуглецю в розчині. Коротка витримка в цій області викликає стабілізацію переохолоджуваного аустеніту, що сприяє збереженню в загартованій сталі більшої кількості залишкового аустеніту.
При збільшенні кількості аустеніту знижується напруга, збільшується міцність і зменшуються об'ємні зміни, деформація і чутливість до тріщин. Подальший відпуск перетворює залишковий аустеніт так само повно, як і в сталі, що піддавалась безперервному загартуванню.
Ізотермічне загартування з тривалою витримкою при 270−220єС викликає утворення тонкоголчастих продуктів проміжного перетворення — бейніту. Кількість бейніту складає 20−30% після витримки 1 год і досягає 50% після витримки 6 год.
В результаті тривалої витримки значно збільшується кількість аустеніту (до 40%), знижується твердість, але підвищується міцність загартованої сталі.
Подальший відпуск викликає такі ж перетворення, як і в сталі з меншою кількістю аустеніту; структура сталі, що піддається ізотермічному загартуванню, не відрізняється після відпуску від отримуваної після звичайного загартування і відпуску.
Таким чином, повне ізотермічне загартування не створює технологічних переваг.
Температури початку і кінця мартенситного перетворення сильно залежать від легованості аустеніту, а отже, від температури загартування і від умов охолодження.
Уповільнене охолодження при температурах > 625єС підвищує температури мартенситного перетворення.
У сталі, що нагрівалася до високих температур і охолоджувалася в маслі або за способом ступінчастого загартування, мартенситне перетворення починається при 200−150єС і не закінчується при +20єС.
Стабілізація аустеніту викликається витримкою впродовж більше 60 хв при 20єС.
Подальший відпуск, знижуючи напругу, надає більшості сталей такі ж структуру і властивості.
Структура сталі, загартованої з температур, що забезпечують високу теплостійкість, і охолодженої в олії або за способом ступінчастого загартування: мартенсіт (60−65%), карбіди (5−20%) і залишковий аустеніт (15−30%).
Структура і властивості відпущеної сталі
Відпуск, правильно виконаний, створює вторинну твердість на 3 — 8 HRC більше, ніж після нагріву на 350єС, підвищує опір пластичної деформації, міцність і теплопровідність.
Зміни в структурі спостерігаються тільки після відпуску при температурі >500єС; у ній виявляються мартенсіт і карбіди без помітних ділянок аустеніту.
Вибір оптимальної температури для ТО сталі 11М5Ф
Для вибору режиму попередньої термічної обробки були розглянуті вплив швидкості нагріву, витримки при температурі аустенізації і швидкості охолодження в широкому діапазоні температур і витримки.
Швидкість нагріву і охолодження при відпалі визначалися на зразках після кування без відпалу таким чином. Зразки завантажували в холодну піч і нагрівали до 900єС зі швидкостями 100, 25 і 15 єС/год до 675єС. Для отримання надійних результатів нагрівання і охолодження з кожною швидкістю повторювали тричі.
Якщо судити по значеннях твердості, то можна зробити висновок, що нагрів зі швидкостями 25 — 100єС/год забезпечує практично однаковий структурний стан зразків в усьому температурному інтервалі. Тому для вибору оптимальних режимів відпалу була прийнята швидкість 100єС/год.
Дослідження показали, що найбільш інтенсивне розміцнення матриці при швидкостях нагріву 100, 50 і 25 єС/год відбувається при температурі вище 650єС, про що свідчить різке збільшення інтенсивності лінії б-фази в процесі високотемпературного аналізу.
При охолодженні вплив швидкості на властивості сталі істотніше. При охолодженні із швидкістю 25 і 15 єС/год сталь отримує практично однакову низьку твердість 20 — 21 HRC. Дослідження (таблиця. 3.1) показують, що підвищення твердості обумовлене головним чином розмірами карбідів, які більше коагулюють при охолодженні із швидкістю 25 і 15 єС/год.
Таблиця 3.1. Вплив швидкості охолодження на властивості безвольфрамової швидкорізальної сталі
Температура, єС | HRC | Сx10,6, Oм м | Нс, А/М | |
Швидкість охолодження 50єС/год | ||||
0,630 | ||||
0,581 | ||||
0,552 | ||||
0,526 | ||||
0,454 | ||||
0,373 | ||||
Швидкість охолодження 25єС/год | ||||
0,629 | ||||
0,596 | ||||
0,591 | ||||
0,548 | ||||
0,542 | ||||
0,532 | ||||
0,503 | ||||
0,503 | ||||
0,437 | ||||
0,370 | ||||
Швидкість охолодження 15єС/год | ||||
0,623 | ||||
0,592 | ||||
0,583 | ||||
0,567 | ||||
0,561 | ||||
0,557 | ||||
0,537 | ||||
0,532 | ||||
0,512 | ||||
На підставі досліджень за швидкість охолодження при відпалі сталі 11М5Ф узяли 25єС/год.
Вибір оптимальних температур аустенізації при відпалі проводили з використанням методу симплексних решіток. Температуру аустенізації призначали в межах від 820 до 940єС, через кожні 30єС. Тривалість витримки складала 2, 4, 6, 8 і 10 год при 820єС і 15 хв при 940єС. Умови нагріву і охолодження до температури аустенізації були однакові.
Нагрів до 650єС робили по потужності печі, потім із швидкістю 100єС/год до температури аустенізації. Охолодження з температури аустенізації проводили із швидкістю 25єС/год до 675єС, далі з піччю до 20єС.
Результати досліджень, наведені в таблиці 3.1, показують, що твердість безпосередньо після відпалу мало залежить від температури аустенізації і витримки при ній. Міцність і плинність при цьому змінюються помітніше.
Таблиця 3.2. Вплив режиму відпалу на властивості безвольфрамової швидкорізальної сталі
№ досліду | Режим відпалу | ув, МПа | у0,2 МПа | ц, % | д % | НВ | ||
Темп., єС | Витримка, хв. | |||||||
16,5 | ||||||||
16,7 | ||||||||
20,9 | ||||||||
Зразки, піддані відпалу при різних температурах, гартували при однаковій температурі - 1210єС в маслі. Загартовані зразки піддавали триразовому відпуску при 580єС з витримкою по 20 хв і охолодженням на повітрі.
Високий комплекс властивостей після загартування з відпуском в даному випадку можна пояснити тим, що безпосередньо після загартування сталь мала дрібнозернисту структуру (бал 10−11) і досить високий рівень легованості твердого розчину.
Таким чином, для сталі 11М5Ф найбільш оптимальним є наступний режим відпалу. Нагрів по потужності печі до 650єС, витримка до повного нагріву заготовок, потім нагрів зі швидкістю не більше 100єС/год до 900−920єС, витримка при цій температурі, охолодження з піччю до 500єС, далі допускається охолодження на повітрі.
4. Охорона праці та безпека у надзвичайних ситуаціях
4.1 Охорона праці
Одним з найважливіших державних завдань є турбота про поліпшення умов праці і безпеки праці на виробництві.
Основним законодавчим актом є Закон України «Про охорону праці» від 14 жовтня 1992 р.
Відповідно до Закону України «Про охорону праці» умови праці на робочому місці, безпека технологічних процесів, устаткування і інших засобів виробництва, використовуваних працівником, а також санітарно побутові умови повинні відповідати вимогам нормативних актів про охорону праці.
Особливо важливим є дотримання правил техніки безпеки при термічній обробці, оскільки при її виконанні виникають чинники, що здійснюють шкідливий вплив на людський організм, такі як загазованість, високі температури, електромагнітне випромінювання і так далі.
Подальше зниження виробничого травматизму не може бути досягнуте тільки за рахунок технічних, санітарно-гігієнічних і економічних заходів, без вдосконалення методів роботи з охорони праці, підвищення рівня знань питань техніки безпеки і охорони праці керівних і інженерно-технічних працівників.
Мета розділу — поліпшення умов праці працівників, попередження виробничого травматизму, профзахворювань, пожеж, аварій та ін. на виробничих дільницях, технологічному обладнанні, в приміщеннях та на робочих місцях ділянки термічної обробки лезових інструментів.
Аналіз шкідливих і небезпечних виробничих чинників
Небезпечні і шкідливі виробничі чинники, що виникають при термічній і хіміко-термічній обробці, підрозділяються на фізичні, хімічні, біологічні і психофізіологічні. До фізичних чинників відносяться: підвищена температура повітря робочої зони, підвищена запиленість і загазованість повітря робочої зони, підвищена або знижена вологість і рухливість повітря, небезпечний рівень напруги в електромережі, підвищений рівень електромагнітного випромінювання, шуму або вібрації на робочому місці, машини, що рухаються, і механізми, переміщувані вироби і матеріали.
До хімічних чинників відносяться загальнотоксичні, подразнюючі, канцерогенні.
Біологічні небезпечні і шкідливі виробничі чинники — бактерії, віруси, гриби і тому подібне, скупчуються в місцях, важкодоступних для проведення прибирання і можуть спричинити різні по тяжкості захворювання.
Психофізіологічні чинники включають фізичні і нервово-психологічні перевантаження.
З перерахованих фізичних чинників перші чотири здійснюють вплив на формування метеорологічних умов в робочій зоні і в цеху в цілому. Робочою зоною слід вважати простір заввишки до двох метрів над рівнем підлоги або майданчики, на яких знаходяться робочі місця. Якщо обслуговування процесів виробництва здійснюється в різних місцях робочої зони, постійним робочим місцем є уся робоча зона.
Склад і температура атмосфери термічного цеху значною мірою залежать від видів використовуваних технологічних процесів, типів устаткування. Важливе значення має справність і належний режим роботи загальної і місцевої вентиляційних систем.
При термічній і хіміко-термічній обробці металів можлива дія на працівників різних небезпечних і шкідливих виробничих чинників, у тому числі: незахищені рухливі елементи виробничого устаткування; заготовки, готові вироби або деталі, що пересуваються; транспортні засоби, що рухаються; аерозолі фіброгенної дії (пил); несприятливий мікроклімат робочої зони; підвищена температура поверхонь устаткування і матеріалів; знижена температура при обробці деталей холодом; небезпечний рівень напруги в електричній мережі; підвищений рівень електромагнітного випромінювання (ультрафіолетового, видимого, інфрачервоного, лазерного, мікрохвильового, радіочастотного); підвищена напруженість магнітного поля; підвищений рівень шуму на робочому місці; знижена освітленість робочого місця; пожежоі вибухонебезпечність; хімічні чинники загальнотоксичної, подразнюючої, канцерогенної дії на організм працівника; тяжкість і напруженість праці.
Усім цим чинникам необхідно приділяти постійну увагу.
Аналіз стану повітря робочої зони
Шкідливі речовини (пил, пари металоорганічних сполук) проникають в організм людини через дихальні шляхи, через шкіру і чинять подразливу дію на слизову оболонку очей, дихальні шляхи, шкіру. В організмі людини пил викликає подразнення дихальних шляхів, призводить до появи специфічних захворювань.
Системи опалювання, вентиляції і кондиціонування при проведенні основних і ремонтно-допоміжних робіт повинні забезпечувати оптимальні або допустимі мікрокліматичні умови в робочій зоні відповідно до вимог Санітарних норм мікроклімату виробничих приміщень, затверджених постановою головного державного санітарного лікаря України від 01.12.99 № 42 (ДСН 3.3.6.042−99), а також зниження змісту в повітрі шкідливих речовин до значень, що не перевищують гранично допустимі концентрації (ГДК), що регламентовані ГОСТ 12.1.005−88 «Система стандартів безпеки праці. Загальні санітарно-гігієнічні вимоги до повітря робочої зони».
Вентиляційні системи повинні відповідати вимогам ГОСТ 12.4.021−75 «Система стандартів безпеки праці. Системи вентиляційні. Загальні вимоги».
На термічній ділянці вміст шкідливих речовин до проведення заходів був наступним:
Таблиця 4.1. Аналіз концентрації шкідливих речовин у повітрі термічної ділянки [21]
Параметр | Фактична концентрація, мг/м2 | ГДК, мг/м2 | |
Оксид азоту (N2O) | |||
Хлорид барію (BaCl2) | 1,8 | 0,3 | |
Гідрооксид калію (KOH) | 2,2 | 0,5 | |
Нітрат калію (KNO3) | |||
Масла індустріальні (И-12А, И-20А) | |||
На організм людини найбільш впливає мікроклімат приміщення.
У цеху мають бути сприятливі метеорологічні умови праці відповідно до ГОСТ 12.1.005−88, значення температури, відносної вологості і швидкості руху повітря встановлюються для робочої зони виробничих приміщень залежно від категорії тяжкості виконуваної роботи, величини надлишків явного, такого, що виділяється в приміщенні, тепла і періоду року. Оптимальні норми температури, відносної вологості і швидкості повітря в робочій зоні виробничого приміщення показані в таблиці 4.2.
Таблиця 4.2. Оптимальні норми температури, відносної вологості і швидкості повітря в робочій зоні виробничого приміщення
Сезон року | Категорії робіт* | Температура, єС | Відносна вологість, % | Швидкість повітря, м/с, не більше | |
Холодний і перехідний період (температура зовнішнього повітря <10єС) | Середньої тяжкості | 17 — 19 | 60 — 40 | 0,3 | |
Теплий період (температура зовнішнього повітря >10єС) | Середньої тяжкості | 20 — 22 | 60 — 40 | 0,4 | |
Аналіз небезпеки дії випромінювань
Робітники-термісти при виконанні різних операцій термічної обробки, знаходячись поблизу відкритих завантажувально-розвантажувальних вікон печей, піддаються дії теплових випромінювань. В умовах нормального проведення технологічного процесу це не чинить негативного впливу на здоров’я працюючих. При поганій теплоізоляції завантажувальних вікон, незадовільній вентиляції, високій температурі довкілля, порушенні технології можливе перегрівання організму. Цьому сприяє висока вологість повітря, щільний одяг, оскільки усе це утрудняє випар через шкірний покрив, а отже, охолодження тіла.
Сильне перегрівання може привести до теплового удару, при якому порушується механізм терморегуляції в організмі, що швидко призводить до розладу діяльності центральної нервової системи.
При перегріванні з’являється наростаюча слабкість, головний біль, сонливість, почервоніння лиця. Надалі, при тривалій дії чинників, що викликають перегрівання, до цих явищ приєднується запаморочення, шум у вухах, болі в спині і кінцівках, підвищення температури тіла до 40єC.
Згідно ГОСТ 12.1.005−88, інтенсивність теплового опромінення працюючих від нагрітих поверхонь технологічного устаткування, освітлювальних приладів, інсоляції на постійних і непостійних робітниках місцях не повинна перевищувати 35 Вт/мІ при опроміненні 50% поверхонь тіла і більше, 70 Вт/мІ - при величині опромінюваної поверхні від 25 до 50% і 100 Вт/мІ - при опроміненні не більше 25% поверхні тіла.
Інтенсивність теплового опромінення працюючих від відкритих джерел (нагрітий метал, скло, «відкрите» полум’я та ін.) не повинна перевищувати 140 Вт/мІ, при цьому опроміненню не повинне піддаватися більше 25% поверхні тіла і обов’язковим є використання засобів індивідуального захисту, у тому числі засобів захисту лиця і очей.
За наявності теплового опромінення температура повітря на постійних робітничих місцях не повинна перевищувати вказані в таблиці Х.2 верхні межі оптимальних значень для теплого періоду року.
Аналіз небезпеки ураження електричним струмом
При обслуговуванні електроустановок (ванна соляна СВС) з напругою 380 В виникає небезпека ураження електричним струмом.
Головні причини нещасних випадків від дії електричного струму:
— випадковий дотик або наближення на небезпечну відстань до струмопровідних частин, що знаходяться під напругою;
— поява напруги на металевих частинах верстатів в результаті ушкодження ізоляції.
Ураження електричним струмом відбувається в результаті дотику людини до струмопровідних частин, що знаходилися під напругою. Величина струму, що проходить через тіло людини, залежить від режиму нейтралі мережі, активного і ємнісного опору між фазними дротами і землею, а також схеми включення людини в ланцюг струму.
Ступінь ураження людини електричним струмом визначається силою струму, що пройшов через тіло людини, і є визначальним чинником при дії на організм людини.
Залежно від класу приміщень по небезпеці ураження електричним струмом встановлюються величини безпечної напруги, що не вимагають спеціальних заходів захисту.
Для звичайних приміщень Uбез.=36 В, для особливо небезпечних приміщень вологість 75% і t 25С Uбез.=12 В.
Згідно ПУЭ-2009, проектована ділянка термічної обробки лезових інструментів належить до категорії приміщень «Без підвищеної небезпеки».
До чинників електробезпеки в трифазних електричних мережах відносяться: хороша електрична ізоляція електричної мережі від «землі» і навколишніх предметів, а також застосування захисного заземлення корпусів устаткування.
Для захисту від ураження електричним струмом усі робочі місця, пов’язані з використанням електроенергії, повинні відповідати вимогам електробезпеки по ГОСТ 12.1.030−82.
У проектованому виробничому цеху для запобігання ураженню електричним струмом передбачені: захисне заземлення, аварійне відключення, плавкі запобіжники.
Аналіз пожежної небезпеки
Джерела займання у виробничих умовах різноманітні за природою свого виникнення і по запасу енергії, яку вони можуть передати. У ряді випадків причиною займання горючих речовин можуть бути джерела тепла, необхідні для проведення технологічного процесу. У термічному цеху це — нагрівальні печі і установки, розжарені деталі і так далі. Разом з цим причиною виникнення пожеж у виробничих умовах можуть бути несправності технологічного устаткування нагрівальних печей, ванн, гартівних баків, установок ТВЧ і контрольно-вимірювальних приладів, а також несправності в електроустановках.
Будь-яка горюча речовина може загорітися, але для цього потрібні певні джерела займання. У тому випадку, коли температура джерела тепла буде нижча температури самозаймання горючого середовища або кількість теплової енергії джерела займання виявиться недостатньою для процесу горіння, займання не станеться. Наприклад, гартівне масло, що має кімнатну температуру, не можна запалити іскрою або сірником, оскільки теплова енергія виявиться при цьому недостатньою для створення горючьої концентрації пари масла в повітрі. Таким чином, горить не саме масло (як, втім і будь-яка інша горюча рідина), а пари досягши їх концентрації в повітрі певної величини. Аналогічний процес відбувається при горінні твердих речовин: полум’ям горять не самі по собі тверді речовини, а газоподібні і пароподібні продукти, що виділяються при розкладанні цих речовин в умовах нагріву.
У термічних цехах пожежі можуть бути викликані спалахом масла в гартівному баку в результаті його перегрівання; витоком горючого газу з газопроводів або печей, що призводить до утворення вибухоі пожежо-небезпечної суміші газу і повітря; викидом розплавлених солей і лугів з печей-ванн при попаданні в них вологи і займання предметів, на які потрапляють бризки розплаву. Самозайманням пилу і порошків деяких матеріалів (титану, алюмінію, вугілля та ін.), що супроводжується вибухом; застосуванням відкритого вогню, наприклад при зварюванні без дотримання належних заходів обережності; займання дрантя і інших матеріалів в результаті порушення правил складування гарячих деталей; іскрою і електричною дугою, що виникли в несправних електроустановках; загорянням ізоляції внаслідок короткого замикання дротів, в яких порушений ізоляційний шар; іскрою від розряду статичної електрики, що утворюється при русі рідини по трубах або місткості; несправністю устаткування і контрольно-вимірювальних приладів. Наприклад, порушення герметизації в печах з контрольованою атмосферою може привести до утворення вибухонебезпечної суміші газу і повітря, зрив шланга з патрубка для подання рідкого карбюризатора — до його розтікання по гарячій печі і в результаті до займання.
Застосування легко займистих рідин для миття підлог і стін в умовах термічного цеху також може привести до їх займання.
Безпека будівель, споруд і приміщень забезпечується дотриманням чинних нормативних документів при проектуванні, будівництві і експлуатації відповідно до вимог ГОСТ 12.1.004−91 «Система стандартів безпеки праці. Пожежна безпека. Загальні вимоги», ГОСТ 12.1.010−76 «Система стандартів безпеки праці. Вибухобезпечність. Загальні вимоги», СНиП 2.09.02−85, СНиП 2.11.01−85 «Складські будівлі», ДБН В. 1.1.7−2002 Захист від пожежі. Пожежна безпека об'єктів будівництва, затвердженому наказом Держбуду України від 03.12.2002 № 88 (зі змінами), СНиП 2.04.05−91 «Опалювання, вентиляція і кондиціонування».
Категорія пожежонебезпечності виробництва: Г — виробництва, пов’язані з обробкою речовин, що не згорають, і матеріалів в гарячому, розжареному або розплавленому станах, що супроводжуються виділенням променистого тепла, систематичним виділенням іскр і полум’я, а також виробництва, пов’язані із спалюванням твердого, рідкого і газоподібного палива.
Категорія вибухонебезпеки виробничого приміщення: B-Iб — аналогічні зонам класу В-Ia (вибухонебезпечні суміші горючих газів або пари легкозаймистих рідин з повітрям можуть утворюватися тільки у разі аварій), але відрізняються рядом особливостей, основні з яких — високі значення нижньої концентраційної межі займання газоповітряних або пароповітряних сумішей (15% і більше), що утворюються, а також невелика кількість вибухонебезпечних сумішей — не більше 5% вільного об'єму приміщень.
Для проектованого виробничого цеху обираємо водопінний вогнегасник типу ВВП-12.
Заходи з поліпшення умов праці
Заходи з поліпшення умов праці можна поділити на:
1) Організаційні - визначення прав і обов’язків в області охорони праці усіх працівників в посадових інструкціях; створення системи управління охороною праці; затвердження положення про службу охорони праці; організація навчання і інструктажів; організація кабінету і куточків по охороні праці; забезпечення працівників засобами індивідуального захисту (ЗІЗ) і аптечками; організація контролю параметрів шкідливих і небезпечних чинників.
2) Санітарно-гігієнічні - введення в експлуатацію нових або розширення існуючих приміщень, гардеробних, душових, умивальних, кімнат відпочинку, приміщень для обігріву працівників, стаціонарних або пересувних їдалень, кімнат по чищенню і ремонту ЗІЗ, сушарок, теплових переходів, тамбурів, лазень і тому подібне; організація медичних оглядів; впровадження оптимальних режимів праці і відпочинку; впровадження виробничої гімнастики; організацію питного постачання; устаткування будинків і баз відпочинку, поліклінік при організації.
3) Інженерно-технічні - модернізація устаткування; впровадження систем сигналізації і захисту від дії шкідливих і небезпечних чинників; впровадження систем автоматичного, напівавтоматичного і дистанційного управління технологічними процесами, систем автоматичного управління технологічними режимами; заходи по зниженню рівнів небезпечних і шкідливих чинників; перепланування розміщення виробничого устаткування; облаштування нових дверних отворів, перегородок, тамбурів і тому подібне; механізація складування, транспортування сировини, продукції і тому подібне.
Заходи щодо оздоровлення повітряного середовища
Для досягнення нормативних значень вмісту шкідливих речовин необхідно застосовувати місцеві відсмоктувачі повітря. Місцеві відсмоктувачі мають бути розташовані так, щоб повітря, що відсмоктується, не проходило через зону дихання працівника. В якості місцевих відсмоктувачів можна застосовувати бортові відсмоктувачі. Круглі ванни і шахтні термічні печі рекомендується обладнати кільцевими відсмоктувачами. Не допускається об'єднувати повітропроводи витяжних систем від термічних печей і від гартівних масляних баків і ванн (із-за можливого займання масла).
Ефективною мірою з попередження захворювань, викликаних тривалим вдиханням виробничого пилу і шкідливих речовин, являється комплексна автоматизація праці, при якій управління устаткуванням відбувається з дистанційних пультів і щитів, винесених в окремі приміщення із сприятливими умовами праці.
Заходи щодо небезпеки дії випромінювань
Основним шляхом оздоровлення праці в термічних цехах, де теплове випромінювання — основний компонент мікроклімату, являється зміна технологічних процесів у напрямі обмеження джерел тепловиділень і зменшенні часу контакту працюючих з ними. Дистанційне керування процесом збільшує відстань між робітником і джерелом тепла і випромінювання, що знижує інтенсивність радіації, що впливає на людину. Важливе значення мають теплоізоляція поверхні устаткування; облаштування захисних, покритих теплоізоляційними матеріалами екранів, що захищають робітників від променистого і конвекційного тепла, водяні і повітряні завіси; укриття поверхні нагрівальних печей порожнистими екранами з циркулюючою в них проточною водою знижує температуру повітря на робочому місці і повністю усуває теплове випромінювання.
Заходи, що виключають ураження електричним струмом
Захист людей від ураження електричним струмом в умовах виробництва досягається наступним: наявність ізоляції, обгороджувань, розташуванням на недоступній висоті, блокуваннями, наявністю захисних заземлень і автоматичного відключення, облаштуванням ізолюючих підлог, а також постійним інструктажем по техніці безпеки працівників.
Для запобігання нещасним випадкам устаткування необхідно забезпечувати спеціальними огородженнями, захисними і запобіжними пристроями.
Для заземлення електроустановок різних призначень і напруги у більшості випадків роблять одне загальне заземлення, що забезпечує найменший опір.
За наявності заземлення внаслідок стікання струму на землю напруга дотику зменшується і, отже, струм, що проходить через людину, виявляється менше, ніж в незаземленій установці. Щоб напруга на заземленому корпусі устаткування була мінімальною, обмежують опір заземлення. Для електроустановок напругою до 1000 В при ізольованій нейтралі трансформатора, генератора опір захисного заземлення має бути не більше 4 Ом.
Заходи щодо забезпечення пожежної безпеки Основне завдання попередження пожеж полягає в тому, щоб виключити хоч би один з чинників, необхідних і достатніх для розвитку некерованого процесу горіння — пожежі. Це завдання вирішується учбово-виховною, роз’яснювальною роботою серед робітників-термістів і службовців; будівельними протипожежними заходами; режимними заходами при експлуатації будівель, споруд, технологічного устаткування.
Для запобігання виникненню пожеж в термічному цеху необхідно: в пожежонебезпечних приміщеннях включити припливно-витяжну вентиляцію, дотримуватися правил спільного зберігання речовин і матеріалів і норми їх одноразової потреби, застосовувати переносні низьковольтні світильники, обладнані захисними скляними ковпаками і сітками. Не допускається: порушення схеми розставляння устаткування і тари; забруднення устаткування і робочих місць відходами виробництва; застосування для захисту електромереж вставок, що не калібруються; установка електронагрівальних приладів і печей на складах; миття підлог і стін легко займистими рідинами.
Проектний розрахунок штучного освітлення ділянки ТО лезових інструментів
1) Розподіляємо світильники на плані приміщення (рис. 4.1).
Знаходимо висоту підвісу світильників над робочою поверхнею h [25]:
h = Н — hР - hС = 6−1-0,2 = 4,8 м, де Н — висота приміщення, м;
hР — висота робочої поверхні, м;
hС — висота звісу світильника, м.
Вибір оптимальної відстані між рядами світильників залежить від типу КСС (крива розподілу світлосил), до якого відноситься вибраний тип світильника, а також висоти підвісу світильників над робочою поверхнею h; для визначення оптимальної відстані Lопт між світильниками використовують коефіцієнт, який залежить від кута, на якому досягається середнє значення сили світла I (кд) в цьому типі КСС [25], причому:
отже м.
Для розподілу світильників на плані приміщення також необхідно врахувати, що відстань від стіни до найближчого світильника, l має бути рівним Ѕ L. Тому L необхідно підібрати так, щоб воно було максимально близьке до Lопт, а розміри приміщення (А, В) ділилися без залишку на відстань між світильниками L.
Обираємо L=6 м.
2) Визначаємо кількість і тип світильників в цьому приміщенні.
Кількість світильників визначається залежно від вибраної відстані між світильниками і розмірів приміщення [25]:
шт.
Рис. 4.1. Схема розподілення світильників на плані приміщення
Стельовий світильник з двома прямими трубчастими люмінесцентними лампами потужністю по 60 Вт — ЛСП 01 2*(58) 60−226. Кліматичне виконання УХЛ 4. Тип джерела світла — пряма трубчаста люмінесцентна лампа Т8 діаметром 32 мм.
3) Визначаємо норму освітленості Енорм, (лк) на робочому місці по ДБН В.2.5−28−2006. Нормативна величина освітленості на робочому місці залежить від розряду і підрозряду зорових робіт, а також системи освітлення (цей розрахунок виконуємо для системи загального освітлення).
Визначаємо Енорм = 400 лк, розряд і підрозряд зорових робіт — А-2 ([26], стор. 4).
4) Визначаємо потужність кожної лампи (Вт) для забезпечення в приміщенні нормованої освітленості за методом-ватт:
Pл = PS/N = 80,4*360/20=1447 Вт, де Pл — потужність однієї лампи, Вт;
Р — питома потужність, Вт/м2;
Питома потужність залежить від величини нормативної освітленості, площі і висоти приміщення, типу і розміщення світильника і коефіцієнта запасу. Її значення наводяться в таблицях. Визначаємо P=20,1 Вт/м2 для Енорм = 100 лк; отже для Енорм = 400 лк, P=20,1*4=80,4 Вт/м2
S — площа приміщення, м2;
N — кількість ламп в освітлювальній установці.
Проектний розрахунок місцевої вентиляції соляної ванни загартування
Розрахунок кількості повітря, що видаляється однобортовими і двобортовими відсмоктувачами робиться за наступною методикою [28]:
Кількість повітря, що видаляється бортовим відсмоктувачем:
де a = 750 м3/год — питома витрата повітря, яка приймається за табл. 4.3 на стор. 107, залежить від ширини ванни b і висоти спектру шкідливостей hшк;
b = 1,4 м — ширина ванни СВС-2.3.4/13, необхідна для визначення а;
hшк = 80 мм — висота спектру шкідливостей, необхідна для визначення а, приймається за табл. 4.2 на стор. 102 в залежності від типу соляної ванни;
tр = 1200 єС — температура рідини у ванні;
tп = 20 єС — температура повітря у приміщенні;
х = 1,1 — поправочний коефіцієнт на глибину рівня рідини, приймається за табл. 4.4 на стор. 107 в залежності від ширини ванни b;
s = 1 — поправочний коефіцієнт на рухливість повітря в приміщенні, приймається за табл. 4.5 на стор. 108 в залежності від швидкості руху повітря в приміщенні хв та висоти спектру шкідливостей hшк;
хв = 0,4 м/с — швидкість руху повітря в приміщенні, необхідна для визначення s;
l = 1.1 м — довжина соляної ванни.
Висновки. У частині «Охорона праці» розділу дипломного проекту проведено аналіз шкідливих і небезпечних виробничих чинників на виробничих дільницях, технологічному обладнанні, в приміщеннях і на робочих місцях ділянки термічної обробки лезових інструментів та запропоновані заходи щодо поліпшення умов праці з розрахунком штучного освітлення проектованої ділянки та розрахунком місцевої вентиляції соляної ванни загартування.
4.2 Безпека у надзвичайних ситуаціях
Безпека у надзвичайних ситуаціях (НС) — це стан захищеності населення, об'єктів господарювання та довкілля від небезпек у НС.
Надзвичайна ситуація техногенного та природного характеру — порушення нормальних умов життя та діяльності людей на окремій території чи об'єкті на ній або на водному об'єкті, спричинене аварією, катастрофою, стихійним лихом чи іншою небезпечною подією, зокрема епідемією, епізоотією, епіфітотією, пожежею, яке призвело (може призвести) до неможливості проживання населення на території чи об'єкті, ведення там господарської діяльності, загибелі людей та/або значних матеріальних втрат.
Захист населення і територій від НС техногенного та природного характеру — система організаційних, технічних, медико-біологічних, фінансово економічних та інших заходів щодо запобігання та реагування на НС техногенного та природного характеру і ліквідації їх наслідків, що реалізуються центральними і місцевими органами виконавчої влади, органами місцевого самоврядування, відповідними силами та засобами підприємств, установ та організацій, незалежно від форм власності й господарювання, добровільними формуваннями і спрямовані на захист населення і територій, а також матеріальних і культурних цінностей та довкілля.
Цивільна оборона України є державною системою органів управління, сил і засобів, які створені для організації і забезпечення захисту населення від наслідків надзвичайних ситуацій техногенного, екологічного, природного та військового характеру.
Цивільна оборона є складовою частиною загальнодержавних заходів з попередження надзвичайних ситуацій та у справах захисту населення від їх наслідків.
Оцінка стійкості напівавтоматичної лінії з печей-ванн для термічної обробки інструментів до впливу ударної хвилі вибуху газо-повітряної суміші
Для споруд і устаткування, швидко обтічних ударною хвилею (трансформатори, верстати, антени, димові труби, опори і т. п.), найбільшу небезпеку представляє швидкісний напір повітря, рухомий за фронтом ударної хвилі. Тиск швидкісного напору ДPск залежить від надлишкового тиску ДPф.
При дії швидкісного напору на об'єкт виникає зміщуюча сила Рзм, яка може викликати: зсув обладнання щодо заснування (фундаменту) або його відкидання; перекидання обладнання; ударні перевантаження, тобто миттєве інерційне руйнування елементів обладнання.
Зсув обладнання
Зсув обладнання, що викликається дією ударної хвилі, може призвести до слабких, а в ряді випадків і середніх руйнувань. Ступінь руйнування обладнання різко підвищується, якщо воно відкидається на якусь відстань, супроводжується ударами з іншими предметами і викликає додаткові руйнування.
Вихідні дані:
Під час вибуху ємності з газом пропан Q=5т, утворюється ударна хвиля вибуху газоповітряної суміші ДPф = 30кПа.
1. Довжина лінії l = 27 000 мм;
2. Ширина b = 2800 мм;
3. Висота h = 4300 мм;
4. Маса m = 20 000 кг.
Визначити граничне значення надлишкового тиску, що не викликає зміщення лінії, щодо бетонної основи ДPф lim зм
Рішення:
1. Визначаємо граничне значення швидкісного напору, що не призводить до зміщення верстата, за формулою По таблиці визначаємо коефіцієнт тертя чавунної підстави лінії по бетону f = 0,35, а за таблицею — коефіцієнт аеродинамічного опору Cx = 1,3, тоді:
2. За величиною ДPск = 4,4кПа з графіка знаходимо ДPф lim см = 35 кПа.
Висновок: при ДPф = 30кПа ударна хвиля не викличе зміщення лінії з печей-ванн.
Перекидання обладнання
Високі елементи обладнання при дії ударної хвилі можуть перекидатися (звалюватися) і сильно руйнуватися.
Вихідні дані:
Під час вибуху ємності з газом пропан Q=5т, утворюється ударна хвиля вибуху газоповітряної суміші ДPф = 30кПа.
1. Довжина лінії l = 27 000 мм;
2. Ширина b = 2800 мм;
3. Висота h = 4300 мм;
4. Маса m = 20 000 кг.
Знайти граничне значення швидкісного тиску напору ДPск lim пер, при якому лінія ще не перекидається.
Рішення:
1. Визначаємо граничне значення швидкісного напору ДPск lim пер, при якому лінія ще не перекидається, за формулою:
2. За величиною ДPск lim пер = 78,6кПа знаходимо ДPф lim пер = 85кПа.
Висновок: при надмірному тиску ДPф lim пер = 85кПа, ударна хвиля не викличе перекидання лінія з печей-ванн, тому що очікуваний надмірний тиск ДPф = 30кПа.
Висновки
Інженерно-технічні заходи по підвищенню стійкості напівавтоматичної лінії з печей-ванн для інструментів проводити недоцільно, оскільки очікуваний надмірний ДPф = 30кПа тиск значно менше ДPф lim на зміщення і перекидання, що говорить про стійкість устаткування.
5. Промислова екологія
5.1 Аналіз підприємства як джерела забруднення довкілля
З великого об'єму промислових викидів, що потрапляють в довкілля, на машинобудування доводиться лише незначна його частина — 1−2%. Проте на машинобудівних підприємствах є основні і забезпечуючі технологічні процеси і виробництва з дуже високим рівнем забруднення довкілля. До них відносяться:
— внутрішньозаводське енергетичне виробництво і інші процеси, пов’язані із спалюванням палива;
— ливарне виробництво;
— металообробка конструкцій і окремих деталей;
— зварювальне виробництво;
— термічна обробка деталей;
— гальванічне виробництво;
— лакофарбне виробництво.
Тверді відходи машинобудівного виробництва містять амортизаційний лом (модернізація устаткування, оснащення, інструменту), стружки і тирсу металів, деревини, пластмас і т. п., шлаки, золи, шлами, опади і пил (відходи систем очищення повітря та ін.).
Розміри відходів металу у виробництві залежать від кількості металів і сплавів, що підлягають переробці і встановленого коефіцієнта відходів. В основному машинобудівні підприємства утворюють відходи від виробництва прокату (кінці, обрізки, обдирна стружка, тирса, окалина та ін.); виробництва литва (ливники, сплески, шлаки і знімання, сміття та ін.); механічної обробки (висікання, обрізки, стружка, тирса та ін.). На підприємствах машинобудування відходи складають до 260 кг на 1 т металу, іноді ці відходи складають 50% мас оброблюваних заготівель (при листовому штампуванні втрати металу досягають 60%). Основними джерелами утворення відходів легованих сталей є металообробка (84%) і амортизаційний лом (16%).
Шлами з відстійників очисних споруд і прокатних цехів містять велику кількість твердих матеріалів, концентрація яких складає від 20 до 300 г./л. Після знешкодження і сушки шлами використовують як добавку до агломераційної шихти і видаляють у відвали. Шлами термічних, ливарних і інших цехів містять токсичні з'єднання свинцю, хрому, міді, цинку, а також ціаніди, хлорофос та ін.
Найбільш екологічно небезпечні забрудники при металообробці - індустріальні масла, металевий пил та ін.
Джерелами матеріальних забруднень біосфери в термічних цехах є паливні печі, печі-ванни, гартівні пристрої, миючі машини, травильні баки, дробеструйні і дробеметні апарати.
Паливні газові печі виділяють в повітря вуглекислий газ, що створює в атмосфері землі парниковий ефект, скупчуючись в приямках, тунелях цеху і боровах печей, двоокис вуглецю діє на організм людини як наркотик і задушливий газ.
При ціануванні в печах-ваннах виділяються оксиди азоту, ціаністий водень і солі синільної кислоти. Оксиди азоту негативно діють на організм людини, інші речовини, що виділяються, — найсильніші отрути. При термічній обробці з нагрівом (охолодженням) в розплавах солей, лугів і металів неминуче виділення в атмосферу отруйних випарів, міра шкідливості яких залежить від складу розплаву.
Застосування мінеральних масел в якості гартівних середовищ призводить до забруднення атмосфери масляними аерозолями і продуктами згорання масла.
Травильні баки термічних цехів і ділянок металургійних заводів при знятті окалини з термічно оброблених виробів виділяють в повітря аерозолі кислот — соляної, азотної і сірчаної. Відпрацьовані травильні і миючі розчини — це шкідливі стоки.
Таким чином, машинобудівний комплекс є потенційним забрудником довкілля:
— повітряного простору (викиди газу, пароподібних речовин, димів, аерозолів, пилу і тому подібне);
— поверхневих вододжерел (стічні води, витік рідких продуктів або напівфабрикатів і тому подібне);
— ґрунти (накопичення твердих відходів, випадання токсичних речовин із забрудненого повітря, стічних вод).
5.2 Визначення викидів забруднюючих речовин на ділянці термічної обробки, що розробляється
Розрахунок викиду забруднюючої речовини робиться за формулою [32]:
де q — питоме виділення речовини на одиницю продукції, приймається за таблицею 5.1;
П — розрахункова продуктивність агрегату (т/год);
в — поправочний коефіцієнт для обліку умов плавки;
з — ефективність засобів по зниженню викидів в долях одиниці;
г — річний час роботи агрегату Таблиця 5.1. Виділення забруднюючих речовин в термічних цехах
Соляні ванни | |||
Тип устаткування, технологічний процес | Речовина | Кількість | |
Нагрів під загартування в розплавах хлористого барію, натрію і калію | Аерозолі | 0,35 г./кг металу | |
Хлористий водень | 0,12 г./кг металу | ||
Охолодження і відпуск сталевих деталей в сумішах з вуглекислого натрію, хлористого натрію і вуглекислого калію | Аерозолі | 0,25 г./кг металу | |
1)
2)
3)
5.3 Гігієнічна оцінка впливу викидів шкідливих речовин від ділянки на стан атмосферного повітря
Початкові дані
Таблиця 5.2. Параметри джерела викидів
Н, м | D, м | м/с | Тг, оС | То, оС | Найменування забрудника | F | Вміст в газах, що викидаються, C, г/м3 | |
0,4 | Аерозолі Хлористий водень | 0,6 0,12 | ||||||
Розрахунок
1. Визначення максимальних приземних концентрацій шкідливих речовин
1. Визначимо об'єм газів, що викидаються в атмосферу за 1 с:
де D — діаметр гирла джерела викиду, м;
— середня швидкість виходу газів з гирла джерела викиду, м/с.
2. Визначимо масу шкідливої речовини, що викидається в атмосферу (окремо для кожного забрудника) за 1 с:
г/с,
1)
2)
де C — вміст забрудника в газах, що викидаються, г/м3.
3. Визначимо різницю температур газів, що викидаються, і навколишнього атмосферного повітря:
оС, де Тг — температура газів, що викидаються, оС;
То — середня температура зовнішнього повітря о 13 годині найбільш жаркого місяця року оС.
4. Вичислимо спеціальний параметр f:
м/(оС· с2),
де Н — висота джерела викиду над рівнем землі, м.
5. Викиди вважаємо нагрітими, оскільки різниця температур Т>0, а також f<100.
6. Вичислимо параметр м для нагрітих викидів:
7. Залежно від величини параметра м, згідно з таблицею 5.3, визначимо значення коефіцієнта n:
Таблиця 5.3. Алгоритм визначення коефіцієнта n
м 0,5 | n = 4,4м | |
0,5 м 2 | n = 0,532−2,13+3,13 | |
м > 2 | n = 1 | |
Отже, n = 0,532· 1,762-2,13·1,76+3,13=1,03
8. Для нагрітих викидів визначимо коефіцієнт m і максимальну приземну концентрацію шкідливої речовини См (для кожного забрудника):
1)мг/м3
2)мг/м3
9. Виберемо з таблиці 5.4 розрахункову формулу і вичислимо значення безрозмірного параметра d.
Таблиця 5.4. Формули для обчислення параметра d
Значення vм | Нагріті викиди | Холодні викиди | |
м? 0,5 | d = 5,7 | ||
м? <0,5 2 | d = 11,4м | ||
м? > 2 | |||
10. Визначимо відстань від джерела викиду до точки з максимальною концентрацією шкідливої речовини в приземному шарі:
11. Порівняємо отримані значення максимальних приземних концентрацій з гранично допустимими концентраціями шкідливих речовин в атмосферному повітрі (ГДК) відповідних речовин і зробимо висновок про якість розсіювання забруднень.
Для аерозолів ГДК=0,5 мг/м3, для хлористого водню ГДК=5 мг/м3; отримані значення максимальної приземної концентрації дорівнюють См=0,2 мг/м3 і См=0,04 мг/м3 відповідно. Виходячи з цього можна зробити висновок про задовільну якість розсіювання забруднень.
2. Визначення гранично допустимих викидів шкідливих речовин
12. Вичислимо значення ГДВ для нагрітих викидів:
1)г/с,
2)г/с, де ГДК — гранично допустимі концентрації шкідливих речовин в атмосферному повітрі, мг/м3.
13. Вичислимо максимальні концентрації шкідливих речовин у викиді біля гирла джерела:
1)г/м3
2)г/м3
14. Оскільки М<�ГДВ, то визначення необхідної міри очищення не потрібно.
5.4 Розрахунок економічного збитку від забруднення атмосфери
Під економічним збитком від забруднення довкілля розуміється грошова оцінка фактичних і можливих збитків (втрат), обумовлених дією забруднення.
Укрупнена оцінка збитку від забруднення атмосферного повітря викидами підприємств базується на використанні величини питомого збитку від забруднення і визначається за формулою [32]:
де — питомий збиток від викиду в атмосферу умовної тонни забруднюючих речовин, = 14,4 (грн/ум. т);
у — безрозмірний коефіцієнт, що враховує відносну небезпеку забруднення атмосферного повітря над територіями різних типів (у=4 для територій промислових підприємств);
fi — безрозмірна поправка, що враховує характер розсіювання домішків;
Мпрi — приведена маса річного викиду домішки i-го виду з джерела, ум. т/рік;
n — загальна кількість видів домішок у викиді;
Кінд — коефіцієнт індексації.
Приведена маса річного викиду домішків визначається за формулою:
де Аi — показник відносної агресивності, ум. т/т;
Мфi — фактична маса річного викиду i-ої забруднюючої речовини, т/рік
1)
2)
Величина безрозмірної поправки f, що враховує характер розсіювання забруднень в атмосферному повітрі, визначається залежно від швидкості осідання.
Для газоподібних і дрібнодисперсних домішок із швидкістю осідання 1 см/с величина безрозмірної поправки f визначається за формулою:
де j — безмірна поправка, що враховує тепловий підйом факела в атмосферу
;
ДT — середньорічна різниця температур в гирлі джерела викиду забруднюючих речовин і в навколишній атмосфері, оС;
Н — висота джерела викиду, м;
u — середньорічне значення швидкості вітру на рівні флюгера, м/с, за відсутності даних приймається u = 3,0 м/с.
Отже:
Визначення розмірів платежів за забруднення атмосфери
Суми збору, що стягується за викиди стаціонарними джерелами забруднення ПВС, обчислюються платниками самостійно на підставі затверджених лімітів, виходячи з фактичних об'ємів викидів, нормативів збору і коригуючих коефіцієнтів, за формулою:
де МЛі — об'єм викиду i-ої забруднюючої речовини в межах ліміту, т;
Мni — об'єм понадлімітного викиду (різниця між об'ємом фактичного викиду і ліміту) i-ої забруднюючої речовини, т;
Hуi — норматив збору за тонну i-ої забруднюючої речовини, грн/т; приведений у в таблиці 3.1, 3.2, 3.3 на стор. 6;
Кнас — коригуючий коефіцієнт, що враховує чисельність жителів населеного пункту, приведений у в таблиці 3.4 на стор. 7;
Кф — коригуючий коефіцієнт, що враховує народногосподарське значення населеного пункту, приведений у в таблиці 3.5 на стор. 8;
Кn — коефіцієнт кратності збору за понадлімітний викид в атмосферу забруднюючих речовин — 5.
5.5 Розробка заходів по зменшенню викидів, скидань і утворення відходів
Екологічна безпека атмосфери, мінімізація викидів забруднюючих речовин може бути забезпечена застосуванням методів знешкодження (видалення) забрудників або використанням безвідходних технологій. До цих методів відносять наступні (залежно від середовища або комбінації середовищ):
Відстоювання. Засновано на розділенні системи «Повітря або рідина — тверді частки» під впливом сили тяжіння. Застосовується для відділення зважених грубо — чи дрібнодисперсних домішок. Метод використовується також для очищення стічних вод від зважених часток.
Фільтрування. Засновано на розділенні системи газ — тверді частки або газ — рідка фаза з поміссю пористого матеріалу (пористі, тканинні, зернисті фільтри). Метод використовується також для очищення води від твердих і рідких забрудників.
Коагуляція. Процес заснований на розділенні системи газ — тверді частки шляхом укрупнення дисперсних забрудників, що виділяються, і видалення їх фізичними або механічними методами. В якості коагулянтів можуть бути солі заліза, алюмінію, магнію і тому подібне. Метод використовується також для очищення стічних вод від твердих і рідких дрібнодисперсних часток.
Магнітний метод. Суть методу полягає в тому, що дисперсна система з певною швидкістю пропускається через апарат, в якому створюється магнітне поле; під дією поля змінюються траєкторія руху часток, їх орієнтація і створюються умови для їх відділення від середовища, що очищається. Застосовується також для очищення води від зважених домішок.
Ультразвуковий метод. Заснований на дії звукових коливань певних частот на дисперсні системи (дим, пил, туман і тому подібне), внаслідок цього протікає швидка коагуляція аерозолів і суспензій з утворенням опадів. Застосовується для обробки стічних вод.
Адсорбція. Заснована на поглинанні забруднюючих домішок адсорбентом, має широке поширення для очищення газів (повітря). Найбільш ефективним адсорбентом є активоване вугілля. Широко застосовується в промисловості також для регенерації розчинників, очищення стічних вод.
Абсорбція. Метод заснований на поглинанні газів рідкими поглиначами. У промисловості широко застосовується для очищення технологічних газів від кислих і побічних продуктів, розділення газових сумішей.
Нейтралізація. Деструктивний метод переробки відходів. Він здійснюється змішенням лужних і кислих потоків, фільтруванням кислих газів через нейтралізуючі матеріали, застосуванням нейтралізуючих реагентів, промиванням газів водними нейтралізуючими розчинниками (хімічна адсорбація). Використовується також для обробки стічних вод (один з етапів комплексної переробки).
Відновлення. Метод заснований на відновленні неорганічних і органічних з'єднань зі зміною їх валентності або структури. Наприклад, для очищення повітряного середовища від оксидів азоту в промисловій практиці використовують в якості відновників СН, CO, NH, Н, отримуючи продукти відновлення: азот, воду і вуглекислоту. Метод використовується також при очищенні стічних вод від нітросполук.
6. Економічна частина
6.1 Капітальні вкладення в технологічне обладнання
Балансова вартість одиниці обладнання розраховується за формулою:
грн, де Куст — балансова вартість одиниці обладнання, грн.;
Цопт. — оптова ціна одиниці обладнання, грн.;
Зб — витрати на будівельні роботи і обладнання фундаменту устаткування, грн.;
Зм — витрати на монтаж обладнання, грн.;
Зтр.-з. — транспортно-заготовчі роботи, грн.
Оптову ціну обладнання визначаємо за діючими за таблицею Д 1, додаток, А [35]: 1 800 000 грн Решту складових формули розраховуємо за наступними орієнтовними нормативами (у відсотках до оптової ціни).
Транспортно-заготовчі витрати у наближених розрахунках для більшої ваги можуть бути прийняті у розмірі 5−10% від оптової ціни обладнання. Приймаємо: 90 000 грн.
Витрати на спорудження фундаменту залежать від ваги і складності і складають зазвичай 2−8% від їх оптової ціни. Приймаємо: 36 000 грн.
Витрати на монтажні роботи визначаються за цінником на монтаж устаткування. У наближених розрахунках величину цих витрат можна прийняти у розмірі 4−6% від оптової ціни обладнання. Приймаємо: 72 000 грн.
6.2 Капітальні вкладення в підйомно-транспортне і інше допоміжне обладнання
Капітальні вкладення в підйомно-транспортне і інше допоміжне обладнання визначаються аналогічно до капітальних вкладення у технологічне обладнання в підйомно-транспортне і інше допоміжне обладнання можуть і бути взяті у розмірі 10−15% вкладень в технологічне обладнання.
Приймаємо капітальні вкладення в підйомно-транспортне та інше допоміжне обладнання у розмірі 324 000 грн.
Складаємо титульний список устаткування, в який включається усе основне і допоміжне устаткування, підйомно-транспортне і енергетичне устаткування.
Таблиця 6.1. Титульний список устаткування
Найменування устаткування | Кількість одиниць | Встановлена потужність, кВт | Вартість одиниці, грн | Вартість усього устаткування | ||||
одиниці | всього | одиниці | Транс/монтаж / фундам | всього | ||||
Основне | ||||||||
Напівавтоматична лінія з печей-ванн для інструментів | ||||||||
Допоміжне | ||||||||
Прилад Бринелля | ||||||||
Прилад Роквелла | ||||||||
Потенціометр, перетворювач, годинник | ||||||||
Кран балка | 7,5 | |||||||
Монорейка з тельфером | 3,5 | 3,5 | ||||||
Конвеєр ланцюговий | ||||||||
Підсумок | ||||||||
; | 1646,5 | |||||||
На підставі даних таблиці 6.1., заповнюємо звідну відомість основних засобів в таблиці 6.2.
Таблиця 6.2. Звідна відомість устаткування
Група устаткування | Площа одиниці устаткування, м2 | Кількість устаткування | Загальна площа | |
Напівавтоматична лінія з печей-ванн для інструментів | 75,6 | 226,8 | ||
Прилад Бринелля | 1,5 | 1,5 | ||
Прилад Роквелла | 1,5 | 1,5 | ||
Загальна площа | ; | ; | 229,8 | |
Потреба в побутових приміщеннях визначається з розрахунку 7 м2 на одного робітника. Висота приміщення 6 м. Будівельні витрати на 1 м2 із залізобетонною несною конструкцією приймаємо 150 грн, а для побутових приміщень 180 грн. Визначаємо потребу в побутових приміщеннях:
7 • 31 =217 м2
271•6=1626 м2
Вартість побутових приміщень розраховується: 1626 •180 = 292 680 грн.
Вартість будівлі 351 000 грн Загальна вартість будівлі і побутових приміщень складає 643 680 грн.
Вартість інших складових основних засобів визначається укрупнено по нормативах. Витрати на енергетичне устаткування складають 5 грн на 1 кВт встановленій потужності; відповідно 1647•5=8235 грн.
Вартість дорогого і довго служачого інструменту 89 280 грн. (13% від вартості технологічного обладнання).
Вартість виробничого та господарського інвентарю 13 300 грн., (1% від вартості обладнання і площ).
Структура основних виробничих фондів і величина річної суми зносу фондів визначається: 1) будівлі з нормою амортизації 5% - 18 040 грн., 2) господарський інвентар з нормою амортизації 25% - 1920 грн., 3) технологічне та підйомно-транспортне обладнання, інструмент, пристосування і виробничий інвентар з нормою амортизації становить 9783 грн.
Річна сума зносу складає: 117 790 грн.
Амортизацію розраховуємо для кожного кварталу окремо і заносимо в табл. 6.3.
Таблиця 6.3. Амортизація
Сума амортизації | ||
1 квартал | ||
2 квартал | ||
3 квартал | ||
4 квартал | ||
Всього | ||
6.3 Визначення вартості оборотних фондів
Крім основних засобів для нормальної роботи підприємства необхідні оборотні фонди підприємства. До оборотних виробничих фондів відносяться частина засобів виробництва, речовинні елементи які в процесі праці витрачаються в кожному виробничому циклі, і їх вартість переноситься повністю на виготовлений продукт. На частку припадає понад 70% всіх оборотних коштів підприємства.
6.4 Розрахунок витрат на паливо та енергію для технічних цілей
Витрати на електроенергію для термічної обробки визначаються за формулою:
Эт = Спр • Фд • Nу • Кз • Кс • Цэ = 3 • 3854 • 495 • 0,75 = 4 292 392,5 грн, де Спр — прийнята кількість установок для т / о;
Кс — коефіцієнт попиту (0,8);
Nу — встановлена потужність одного агрегату 495 кВт;
Цэ — ціна одного кВт електроенергії - приймаємо 75 коп.
6.5 Визначення потреби в трудових ресурсах
Трудові ресурси підприємства є найважливішим елементом виробничих сил, визначають темпи зростання виробництва, продуктивності праці і якості продукції.
Всі працівники підприємства залежно від ступеня їх участі у виробничій діяльності поділяються на промислово-виробничий і непромисловий персонал, не пов’язаний з основною виробничою діяльністю.
Кількість працюючих у цеху розраховується за категоріями: основні і допоміжні робітники, службовці, в тому числі: керівники, фахівці, інші службовці.
Таблиця 6.4. Розрахунок чисельності допоміжних робітників, зайнятих обслуговуванням устаткування
Група обладнання | Кількість одиниць обладнання | Норма обслуговування | Розряд робочого | Кількість осіб | Змінність | Явочний склад | |
Прилад Бринелля Прилад Роквелла | 1,5 | 0,5 | |||||
Всього | |||||||
Чисельність допоміжних робітників, зайнятих обслуговуванням всього цеху визначається по нормам. Результати відображені в табл. 6.5.
Таблиця 6.5. Розрахунок чисельності допоміжних робітників, зайнятих обслуговуванням цеху
Професія | Розряд робочого | Норма обслуговування | Кількість у зміну | Змінність | Явочний склад | |
Наладчик Слюсар-ремонтник Слюсар з рем-ту обл. Слюсар з контр. вим. Кранівник | 0,1 0,5 0,3 0,5 0,7 | |||||
За підсумками розрахунків складаємо зведену відомість працюючих в цеху (табл. 6.6).
Таблиця 6.6. Зведена відомість працюючих в цеху
Категорія працюючих | Всього | 1 зміна | 2 зміна | |
Основні робочі | ||||
Допоміжні робітники | ||||
Разом виробничих робітників | ||||
Службовці: в т. ч. керівники та фахівці | ||||
Інші службовці | ||||
Разом | ||||
6.6 Розрахунок фонду оплати праці
В економічній практиці існують такі фонди оплати праці як: фонд основної заробітної плати, фонд додаткової оплати праці, інші заохочення та компенсаційні виплати.
Фонд оплати праці розраховується окремо для відрядників, погодинників і службовців. Основна зарплата відрядників визначається перемножуванням розцінок на кількість продукції.
Додаткова заробітна плата визначається у відсотках до основної заробітної плати. Величина цього відсотка в середньому приймається 50%. Фонд оплати праці отримуємо складанням основної та додаткової заробітної плати.
Відрахування на соціальне страхування, складають 37,8% від фонду оплати праці.
Таблиця 6.7. Розрахунок фонду оплати праці працюючих відрядників
Професія | Чисельність за річним планом | Кількість норм | Розряд робочого | Годинна тарифна ставка грн. | Фонд відрядної з/п т.грн. | Фонд додаткової з/п т.грн. | Разом ФОП т.грн. | Відрахування на соц. страх. | |
Терміст | 20,01 | ||||||||
Для визначення фонду прямої заробітної плати робітників погодинників необхідно аналогічним способом визначити всі параметри як і для відрядників, відмінність полягає в додатковій заробітній платі, яка становить 40% від основної.
Таблиця 6.8. Розрахунок оплати праці робітників-погодинників
Проф-я | Чисел-ть за річ. планом | Дійсний річний фонд часу | Середній розряд роб-го | Годинна тарифна ставка | Фонд з/п по тарифу, грн | Додаткова з/п, грн. | Разом ФОП | Відрахування на соц. страх. | ||
одного | всіх | |||||||||
Наладчик | 20,01 | |||||||||
Слюсар-ремонтник | 20,01 | |||||||||
Кран-к | 20,01 | |||||||||
Всього | ; | ; | ; | ; | ||||||
Таблиця 6.9. Розрахунок фонду оплати праці службовців
Посада | Кіль-ть шт.-их од-ць | Оклад в міс., грн | Додаткова з/п, грн. | Річний ФОП, т.грн. | Відрахування на соц. страх. | |
Ст. майстер | ||||||
Майстер | ||||||
Ст. інженер тех-ог | ||||||
Інженер тех-г | ||||||
Інженер з інст-у | ||||||
Технік — тех-г | ||||||
Ст. диспетчер | ||||||
Диспетчер | ||||||
Нормувальник | ||||||
Інженер з НОТ і У | ||||||
Економіст | ||||||
Механік | ||||||
Ст. бухгалтер | ||||||
Табельник | ||||||
Прибиральник приміщення | ||||||
РАЗОМ | ||||||
Результати розрахунку фонду заробітної плати по всім категоріям працюючих зводяться до відомості (табл. 6.10), де середня заробітна плата підраховується як відношення загального річного фонду до явочної чисельності.
Таблиця 6.10. Зведена відомість річного фонду заробітної плати
Категорія робочих | Кількість | ФОП, тис. грн. | Середній рівень з/п, грн. | |
Основні | ||||
Допоміжні | ||||
Службовці | ||||
Підсумок по цеху | ||||
6.7 Витрати на утримання і експлуатацію устаткування
Номенклатура статей витрат їх зміст і порядок визначення наведені в табл. 6.11.
Таблиця 6.11. Витрати на утримання і експлуатацію устаткування
Стаття витрат і її зміст | Сума, грн. | Норматив або спосіб визначення витрат | |
1. Витрати на повне відновлення і капітальний ремонт ОПФ | |||
1.1. Амортизація | |||
Обладнання | |||
Транспортних засобів | |||
Інструментів і пристосувань | |||
Виробничого інвентарю | |||
2. Витрати на експлуатацію обладнання | |||
2.1 Вартість допоміжних матеріалів для підтримки устаткування в робочому стані | 40−50 грн. на одиницю обладнання | ||
2.2. Витрати на оплату праці (з нарахуваннями) роб. обслуговування устаткування (наладчиків, ремонтників) | За розрахунком фонду оплати праці робітників погодинників | ||
2.3. Вартість використання палива, електроенергії, води, пари, стисненого повітря та інших видів енергії | |||
3. Витрати на проведення поточного ремонту обладнання і транспортних засобів | 5% від початкової вартості облад-я, транспор. зас-в | ||
4. Витрати на внутрішньозаводське транспортування вантажів | 20% від первісної вартості автотранспорту | ||
4.1. Витрати на оплату праці робітників, зайнятих переміщенням вантажів, підвезення матеріалів на робоче місце і склад | За розрахунком фонду оплати праці допоміжних робітників | ||
4.2. Вартість допоміжних матеріалів для експлуатації транспортних засобів (авто-і електрокари) | 20% від первісної вартості авто-і електрокарів | ||
5. Знос малоцінних і швидкозношуваних інструментів та пристроїв (не цільового призначення) | 20% від вартості інструментів | ||
6. Інші витрати | 5% від ФОП осн. роб. | ||
РАЗОМ | |||
6.8 Визначення загальновиробничих витрат
Номенклатура статей загальновиробничих витрат, їх зміст і порядок проведення визначені в табл. 6.12.
Таблиця 6.12
Загальновиробничі витрати
Стаття витрат і її зміст | Сума, т.грн. | Норматив або спосіб визначення | |
1. Витрати, пов’язані з управління пр-вом | |||
1.1. Витрати на оплату праці працівників апарату управління цеху з нарахуваннями на з/п | Розрахунок фонду оплати праці | ||
2. Витрати пов’язані з оплатою службових відряджень | |||
3. Амортизаційні відрахування | 841,989 | ||
3.1. Амортизація виробничих і побутових приміщень | Табл. расчета амортизации | ||
3.2. Амортизація господарського інвентарю цеху | |||
3.3. Знос нематеріальних активів | |||
4. Витрати на обслуговування виробничого процесу | |||
4.1. Витрати на оплату праці цехового персоналу (з нарахуваннями): фахівців, службовців, молодшого персоналу та інших працівників, що не відносяться до управлінського персоналу | Розрахунок фонду оплати праці | ||
4.2. Витрати на проведення поточного ремонту і утримання будівель | 3% від первісної вартості будівлі | ||
4.3. Витрати, пов’язані із забезпеченням техніки безпеки праці, санітарно-гігієнічних та інших спеціальних вимог | 3% від ФОП основних і допоміжних робітників | ||
5. Інші витрати (витрати по раціоналізації, пожежної і сторожової охорони, нестачі, канцелярські витрати) | 5% від ФОТ усіх робочих | ||
РАЗОМ | |||
6.9 Формування складу витрат за статтями витрат
Виражені в грошовій формі поточні витрати підприємства на виробництво утворюють виробничу собівартість продукції. Перелік включених до собівартості поточних витрат наведено в табл. 6.13.
При цьому для отримання калькуляції собівартості одиниці виробу необхідно ділити отримані значення на річну програму, щоб отримати величину витрат на одиницю виробу.
Таблиця 6.13. Калькуляція собівартості виробу
Шифр рядків | Найменування статей калькуляції | Сума за одиницю, грн. | Структура витрат, % | |
Сировина та матеріали | 1,56 | |||
Зворотні відходи | 0,02 | |||
Разом матеріали за вирахуванням відходів | 1,54 | |||
Паливо та енергія на технологічні цілі | 10,64 | |||
Основна заробітна плата | 0,19 | |||
Додаткова заробітна плата | 0,09 | |||
Відрахування на соціальне страхування | 0,1 | |||
Витрати, пов’язані з підготовкою та освоєнням виробництва | 0,08 | |||
Відшкодування зносу спеціальних інструментів цільового призначення | 0,02 | |||
Витрати на утримання і експлуатацію устаткування | 0,03 | |||
Загальновиробничі витрати | 0,27 | |||
Адміністративні витрати | 0,16 | |||
Втрати внаслідок технічного неминучого браку | 4418,8 | 0,005 | ||
Інші витрати виробництва | ; | 0,15 | ||
Разом виробнича собівартість | ; | 14,86 | ||
Витрати на збут | ; | 0,3 | ||
Разом повна собівартість | ; | 15,16 | ||
6.10 Визначення фінансових результатів підприємства
Кінцевим результатом господарської діяльності підприємства є прибуток. В кінцевому підсумку вона відображає всі сторони виробничої і господарської діяльності підприємства.
Основою для розрахунку прибутку є повна собівартість, рентабельність, ціна виробу, а також обсяг виробничої програми.
Оптова ціна виробу, плановий рівень рентабельності (30%):
Ц = Сп• (Р+ р/100),
де Р — рівень рентабельності (30%);
Сп — повна собівартість виробу;
Ц = 15,16 • (1+ 30/100) = 19,71 грн Розрахункова відпускна ціна:
Цо = Ц+ПДВ, де ПДВ — податок на додану вартість.
Цо = 19,71+3,94 =24 грн Повна собівартість річного обсягу товарної продукції:
Стп = Сп • А, Стп = 15,16 •2 640 000 = 12 523 524 грн Вартість річного обсягу продукції (без податку на додану вартість):
Qт =Ц • А,
Qт = 19,71 • 2 640 000 = 16 282 233 грн Балансовий прибуток по товарному випуску планового періоду (рік):
Пб = Qт — Стп, грн Пб = 16 282 233 — 12 523 524 = 3 758 709 грн Розрахунковий (чистий) прибуток, що залишається в розпорядженні підприємства:
Пр = Пб-Н, де Н — загальна сума податків і виплат з балансового прибутку (податок на прибуток -25%)
Пр = 3 758 709 — 939 677 = 2 819 032 грн Розрахункову норму рентабельності проектованого підприємства можна розрахувати за формулою:
Р = Пб • 100/(Фо+Фос),
де Фо — вартість основних виробничих фондів, грн;
Фос — обсяг оборотних коштів, грн.
Вартість оборотних коштів укрупнено можна визначити з умови, що витрати на основні матеріали в їх структурі становлять 30%.
Фос = (М • 100)/(30 • п) = (4 295 669 • 100)/ (30 • 3) = 4 742 766 грн Р = 3 758 709 • 100/(114 057+4772966) = 45%
Термін окупності вкладень в основні виробничі фонди:
То = Фо/Пб = 114 057/3758709 = 0,3 років
Основні техніко-економічні показники зведені в табл. 6.17.
Таблиця 6.14. Основні техніко-економічні показники
Найменування показника | Одиниця виміру | Чисельне значення | |
Випуск виробу на рік Фреза Свердло Мітчик | шт. | 1,4 млн 15 млн 10 млн | |
Товарна продукція без ПДВ | грн. | ||
Випуск продукції на 1 роб. | грн | ||
Випуск продукції на 1 м2 вироб. площі | грн. | ||
Усього працюючих: в т. ч. | чол. | ||
Основних робочих | чол. | ||
Допоміжних робітників | чол. | ||
Коеф. завантаження обладнання | 0,93 | ||
Трудомісткість виготовлення виробів Фреза Свердло Мітчик | нормо-год | ||
Собівартість виробів | грн. | 15,16 | |
Термін окупності кап. вкладень у вироб. фонди | рік | 0,3 | |
Ціна виробу (оптова) | грн | 19,71 | |
Прибуток розрахунковий | грн. | ||
Рентабельність підприємства | % | ||
Заключна частина
У цьому дипломному проекті розроблена маршрутна технологія виготовлення різального інструменту: фрези, свердла та мітчика. Виконано розрахунок трудомісткості термообробки і дійсного річного фонду часу роботи устаткування; вибір і розрахунок необхідної кількості основного, додаткового і допоміжного устаткування; розрахунок енергетики ділянки. Розглянуті і досліджені причини виникнення браку різального інструменту при термообробці і в процесі експлуатації і методи їх усунення. Розроблені заходи за безпечними умовами праці робітників ділянки термічної обробки згідно вимог промислової екології, охорони праці і цивільної оборони.
Розроблені унікальні швидкорізальні сталі заевтектоїдного класу, які при істотно меншому вмісті легуючих компонентів і нижчої вартості значно перевершують за властивостями сталі аналогічного призначення. Перспектива розвитку проекту залежить від результатів досліджень організацій, зацікавлених в його реалізації.
Список використаних джерел
1. Смохоцкий А. И. Парфеновская Н.Г. Технология термической обработки металлов — М.: Машиностроение, 1976 — 311 с.
2. Сорокин В. Г. Волосникова А.В. Вяткин С. А. и др. Марочник сталей и сплавов — М.: машиностроение, 1989 — 640 с.
3. Гуляев А. П. Инструментальные стали. Справочник. М.: Машиностроение, 1975 — 272 с.
4. Райцес В. Б. Термическая обработка. М.: Машиностроение, 1980 — 208 с.
5. Карташова Л. И. Материаловедение для машиностроителей в задачах. К.: ИСДО, 1996 — 200 с.
6. Каменичный И. С. Краткий справочник термиста. М.: Машиздат, 1959 -280 с.
7. Лахтин Ю. М. Металловедение и термическая обработка металлов. М.: Металлургия, 1984 — 360 с.
8. Башнин Ю. А., Ушаков Б. К., Секей А. Г. Технология термической обработки стали. Учебник для вузов. М.: Металлургия, 1986 — 424 с.
9. Бартель Г. П. Прогрессивная технология инструментального производства в тяжелом и транспортном машиностроении. Тематический сборник научных трудов-Краматорск, 1988 — 266 с.
10. Сергейчев И. И. Печковский А.М. Термическая обработка режущего и измерительного инструмента. М.: МАШГИЗ, 1960 — 308 с.
11. Лахтин Ю. М. Рахштадт А.Г. Термическая обработка в машиностроении. Справочник. М.: Машиностроение, 1980 — 783 с.
12. Технология термической обработки стали / Под ред. Бернштейна М. Л. — М.: Металлургия, 1981 — 608 с.
13. Геллер Ю. А. Инструментальные стали. М.: Металлургиздат, 1955 — 548 с.
14. Соколов К. Н. Оборудование термических цехов. Киев-Донецк: Вища школа, 1984 — 328 с.
15. Никифоров В. М. Технология металлов и конструкционные материалы. Л.: Машиностроение, 1986 — 363 с.
16. Справочник. Соляные ванны для термической обработки изделий / Под ред. Геллера Ю. А. — МАШГИЗ, 1963 — 124 с.
17. Долотов Г. П. Кондаков Е.А. Оборудование термических цехов и лабораторий. Испытания металлов. М.: Машиностроение, 1988 — 336 с.
18. Сатановский Л. Г. Мирский Ю.А. Нагревательные и термические печи в машиностроении. М.: Металлургия, 1971 — 384 с.
19. Шмыков А. А. Справочник термиста. МАШГИЗ, 1961 — 392 с.
20. Рустем С. Л. Оборудование и проектирование термических цехов. М.: МАШГИЗ, 1962 — 588 с.
21. Березуцький В. В. Основи охорони праці. Х.: Факт, 2007. — 480 с.
22. ГОСТ 12.1.005−88 «Система стандартів безпеки праці. Загальні санітарно-гігієнічні вимоги до повітря робочої зони»
23. ПУЭ-2009 (Украина)
24. Наказ Міністерства України з питань надзвичайних ситуацій та у справах захисту населення від наслідків Чорнобильської катастрофи від 02.04.2004 № 151 «Про затвердження Типових норм належності вогнегасників»
25. Методичні вказівки до виконання практичної роботи «Проектний розрахунок штучного освітлення виробничих приміщень за коефіцієнтом використання світлового потоку»
26. ДБН В.2.5−28−2006
27. Расчёт электрического освещения методом удельной мощности: http://elektroas.ru/raschyot-elektricheskogo-osveshheniya-metodom-udelnoj-moshhnosti-prodolzhenie
28. Волков О. Д. Проектирование вентиляции промышленного здания. Учебное пособие. Х.: Высш. шк. ХГУ, 1989. -240 с., ил.
29. Райцес В. Б., Литвин В. М. Техника безопасности в термических цехах. — К.: Тэхника, 1988. — 160 с.
30. Гражданская оборона /Под ред. Шубина Е. П. — М.: Просвещение, 1991 — 223 с.
31. Гражданская оборона /Под ред. Алтунина А. Т. — М.: Воениздат, 1980 — 192 с.
32. Методичні вказівки до виконання розділу дипломного проекту «Промислова екологія»
33. Дикань В. Л., Дейнека А. Г., Позднякова Л. А., Михайлов И. Д., Каграманян А. А. Основы экологии и природопользования. Учебное пособие — Харьков: ООО «Олант», 2002. — 384 с.
34. А. С. Быстров, В. В. Варанкин, М. А. Виленский и др. Временная типовая методика определения экономической эффективности осуществления природоохранных мероприятий и оценки экономического ущерба, причиняемого народному хозяйству загрязнением окружающей среды. — М.: Экономика, 1986. — 96 с.
35. Методичні вказівки до виконання розділу дипломного проекту «Економічна частина» (для студентів денної та заочної форми навчання за спеціальністю 705 040 301 «Прикладне матеріалознавство». /Укладач: В. М. Дубасов. Луганськ: Вид-во СНУ ім. В. Даля, 2011 — 28 с.