Розробка технологічного процесу виготовлення металоконструкції «Балка прокольна»
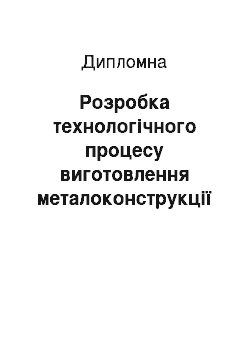
Немає такої області в якій не застосовувалися б зварювальні роботи. Особливе значення вони мають у будівництві та машинобудуванні. Виробництво зварювальних робіт проводиться там, де необхідно отримати міцне з'єднання будь-яких матеріалів. Не останню роль у цьому процесі відводиться фахівцям, які займаються зварювальними роботами. В даний час — розвиток високих технологій не залишилося осторонь і… Читати ще >
Розробка технологічного процесу виготовлення металоконструкції «Балка прокольна» (реферат, курсова, диплом, контрольна)
Дипломний проект Розробка технологічного процесу виготовлення металоконструкції «Балка прокольна»
Зміст Вступ
1. Загальна частина
1.1 Опис металоконструкції
1.2 Аналіз і розрахунок технологічності металоконструкції
1.3 Технічні умови на виготовлення металоконструкції
1.4 Властивості матеріалу виробу. Визначення групи зварюваності
1.5 Розрахунок на міцність зварних з'єднань
2. Технологічна частина
2.1 Обґрунтування укрупненої технології виготовлення деталей зварної конструкції
2.1.1 Технологічний процес виготовлення деталей зварної конструкції
2.1.2 Вибір заготівельного обладнання і його характеристика
2.1.3 Заходи щодо техніки безпеки і пожежної безпеки при заготівельних операціях
2.2 Обґрунтування вибору способу складання виробу
2.2.1 Вибір електродів для прихватки при зварюванні. Вибір роду зварювального струму
2.2.3 Вибір джерела живлення для ручної дугової прихватки, його характеристика й паспортні дані
2.2.4 Розробка або модернізація пристосування для складання, опис пристрою й принципу його дії
2.2.5 Технологічний процес складання виробу
2.2.6 Технологічний процес контролю якості складання
2.2.7 Технічне нормування процесів складання
2.2.8 Заходи щодо охорони праці та техніки безпеки при складанні металевої конструкції
2.3 Вибір способу зварювання вузла
2.3.1 Обґрунтування вибору способу зварювання вузла
2.3.2 Вибір зварювальних матеріалів і їхня характеристика. Вибір роду зварювального струму
2.3.3 Розрахунок режимів зварювання
2.3.4 Вибір устаткування для механізованого зварювання
2.3.5 Технологічний процес зварювання металоконструкції
2.3.6 Технологічний процес контролю якості зварювання
2.3.7 Технічне нормування процесів зварювання Висновки Перелік посилань деталь зварний балка прокольний Вступ Зварювання — це технологічний процес отримання нероз'ємного з'єднання.
Немає такої області в якій не застосовувалися б зварювальні роботи. Особливе значення вони мають у будівництві та машинобудуванні. Виробництво зварювальних робіт проводиться там, де необхідно отримати міцне з'єднання будь-яких матеріалів. Не останню роль у цьому процесі відводиться фахівцям, які займаються зварювальними роботами. В даний час — розвиток високих технологій не залишилося осторонь і зварювальний індустрія. Йде постійне поліпшення технології зварювальних робіт. Зараз виділяють безліч видів зварювання, до основних належать: електродугова, газова, лазерна, плазмова зварювання. Одним з широко застосовуваних технологічних процесів в машинобудуванні, є дугове зварювання в середовищі захисних газів.
Невід'ємною частиною секційним поїздів ПС-3,5−900 є поздовжня балка, розробка технологічного процесу якій, розглядається в даному дипломному проекті.
Поїзд Пс-3,5−900 виготовляється на ПАТ «Дружківський машинобудівний завод», тому тема дипломного проекту являється актуальною.
1. Загальна частина
1.1 Опис металоконструкції
Металоконструкция балка поздовжня входить до складу секційних поїздів ПС, які призначені для транспортування гірничої маси підземними гірничими виробками. Поїзди секційні ПС-3,5−900 відповідають вимогам КД.12.1.003. Складаються з секцій передній, кінцевий і проміжні. Комплектність поїзда секційного: секція передня — 1шт., секція кінцева — 1 шт., секції проміжні - не більше 28 шт. (за погодженням із замовником). Секції передня і кінцева оснащені автоматичними зчіпками.
Кожна секція поїзда секційного має одну колісну пару, з'єднану з рамою кузова через амортизатор. Другою точкою секція через спеціальне шарнірне пристрій з амортизацією спирається і з'єднується з попередньої секцією секційного поїзда.
Кожна секція поїзда секційного має відкриваються днища. Розвантажується поїзд секційний на ходу над ямою з розвантажувальними кривими. Технічні характеристики приведені у табл.1
Таблиця 1 — Технічні характеристики поїзда секційного ПС-3,5−900
Найменування параметра та розміру | Одиниця вимірювання | Норма для типу | |
ПС-3,5−900 | |||
Номінальна місткість, V | м3 | 3,5 | |
Максимальна вантажопідйомність | т | 6,0 | |
Колія, S | мм | ||
Довжина, L | мм | ||
Ширина | мм | ||
Висота від головки рейки | мм | ||
Жорстка база | мм | ||
Діаметр колеса по ободу катання | мм | ||
Висота зчіпки від осі до головки рейки | мм | ||
Маса не більше | кг | ||
1.2 Аналіз і розрахунок технологічності металоконструкції
До складальної одиниці «Балка прокольна» 2ПС3,5−900.01.01.020СБ входять п’ять позицій :
1 2ПС3,5900.01.01.021 — Кронштейн — 4 од.
2 2ПС3,5−900.01.01.022 — Кронштейн — 2од.
3 2ПС3,5−900.01.01.023 — Ребро — 2од.
4 2ПС3,5−900.01.01.051 — Балка — 1од.
5 1ПС3,5−900.01.01.054 — Ребро — 1од.
Балку продольну 2ПС3,5−900.01.01.020СБ зварюють за допомогою швів:
1 № 1 Т3-?5−40Z80 — таврове з'єднання з двобічним зварюванням, за шаховим розташуванням — 40 варимо 80 пропускаємо, за катетом шва 5 мм;
2 № 2 Т1-?5 — таврове з'єднання з одностороннім проваром, шов кутовий катетом шва 5 мм;
3 № 3 Т1-?10 — таврове з'єднання з одностороннім проваром, шов кутовий катетом шва 10 мм.
Розрахунок технологічності металоконструкції «Балка продольна» 2ПС3,5−900.01.01.020СБ розрахуємо по формулі :
(1)
Для шва № 1 Т3-?5−40Z80 :
Для шва № 2 Т1-?5 :
Для шва № 3 Т1-?10 :
Таблиця 2 — Маса наплавленого металу для швів металоконструкції
№ шва | Тип шва | ГОСТ | Довжина шва, мм | ||
Т3-?5−40Z80 | 5264−80 | 0,114 | 0,015 | ||
Т1-?5 | 5264−80 | 1,08 | 0,149 | ||
Т1-?10 | 5264−80 | 1,68 | 0,79 | ||
Розрахунок маси наплавленого металу виконується за формулою:
(2)
де: Fн — площа поперечного переріза шва; г — щільність металу шва, для сталі г=7,8; l — довжина шва.
Загальна маса наплавленого металу для всієї металоконструкції, розраховується за формулою :
(3)
де: , , — маса наплавленого метала для різних типів зварних швів;
Показник долі наплавленого металу в загальній масі розраховується за формулою :
m =, (4)
де : — маса наплавленого металу;- маса зварної металоконструкції
m =
За розрахунками даної металоконструкції, показник долі наплавленого металу в загальній масі складає 0,9%
При m< 2% - металоконструкція вважається технологічною.
1.3 Технічні умови на виготовлення складальної одиниці
Основними вимогами до всіх зварних конструкцій є забезпечення їхньої надійності роботи в процесі експлуатації. До виробів, які підлягають зварюванню, пред’являються наступні основні вимоги:
1 Кромки, що зварюються, а також поверхні металу шириною не менш 20 мм, а також місця які прилягають до місць зварювання, перед зварюванням повинні бути зачищені до чистого металу;
2 Складання під зварювання доцільно виконувати в спеціальних складальних пристосуваннях. При складанні елементів, що зварюються, не допускається застосування примусової підготовки, що викликає наклеп або додаткові напруги в металі.
Взаємне закріплення деталей при складанні може виконуватись прихватками зі застосуванням електродного матеріалу, що забезпечує властивості металу прихватки відповідно до вимог до матеріалу шва. Прихватки повинні виконуватися без підрізів, пропалів і відкритих кратерів.
Технічні умови на заготівлю Технічні умови на заготівку включають вимоги на габаритні розміри заготівок, виконання вимог до площини й кривизни якість підготовки кромок.
Технічні умови на зварювання
1. Вироби не прийняті технічним контролем, на складання під зварювання не допускаються.
2. Кромки виробів, що підлягають зварюванню й прилягаючі до них поверхні повинні бути сухими й не мати корозії.
3. У серійному й масовому виробництві складання під зварювання повинна виконуватись на складальних плитах, стендах, стелажах, що забезпечують необхідне розташування деталей.
4. З'єднання при складанні сталевих конструкцій варто робити за допомогою прихваток, які накладаються в місцях розташування швів.
5. Розміри перетину прихваток повинні становити 0,7 розмірів перетину шва, але не більше 6 мм.
6. Прихватки необхідно виконувати тими ж матеріалами, що й зварний шов.
7. По закінченню зварювальних робіт шви прихваток і місця під зварювання повинні бути зачищені від шлаків і бризгів розплавленого металу.
8. Зібрана конструкція підлягає прийманню технічним контролем.
9. При складанні необхідно витримати розміри, зазначені на кресленні.
450±3,15; 850±2,8; 70±1,9; 71±1,9; 1700±5,5; 30±1; 95±2;
Технічні умови на зварювання Технічні умови на зварювання повинні включати: вимоги на зачищення кромок для зварювання, і з'єднання після зварювання, на дотримання режимів зварювання й допускаються відхилення, що до зовнішнього вигляду зварних швів.
Технологія зварювання метод, місце і час контролю якості повинні бути викладені в картах технологічного процесу. Допускається застосування в тому самому шві автоматичного та ручного зварювання. Якщо доля ручного зварювання не перевищує 15%, то такий шов вважається виконаним автоматичним зварюванням.
Зварні шви, повинні задовольняти наступним вимогам 6 мати гладку й мілко лускату поверхню (без напливів, пропалів, звужень і перерв) і плавний перехід до основного металу; наплавлений метал повинен бути щільним по всій довжині шва, не мати тріщин, поверхневих пір; підрізи допускається глибиною не більше 0,5 мм при товщині металу, що зварюється, 10 мм і не більше 1 мм при товщині металу понад 10 мм всі кратери повинні бути заварені.
Зварний шов не повинен мати внутрішніх тріщин, допускаються наступні внутрішні дефекти швів: не провари по перетину швів, виконаних двостороннім або однобічним зварюванням на підкладці, глибиною до 5% від товщини металу, але не більше 200 мм на 1 м шва; не провари в корні шва, виконаного однобічним зварюванням без підкладки, глибиною до 15% від товщини металу для товщини 20 мм і не понад 3 мм при товщині більше 20 мм.
Неприпустимі дефекти зварного шва повинні бути вилучені обробкою різанням, повітряно-дуговим струганням або іншими способами, за наступним зачищенням до чистого металу та заварені. Виправлення дефектів на тому самому місці допускаються не більше двох разів. При наступному виявленні дефектів вироби повинні бути роз'єднані і знову підготовлені для складання і зварювання.
Технічні умови на контроль якості
Контроль якості повинен здійснюватися систематично в течії усього виробничого циклу.
Порядок контролю якості вказується в карті технологічного процесу. Зібрана конструкція спочатку перевіряється виробничим майстром, а потім приймається контролем ВТК. Контроль якості зварних з'єднань здійснюється зовнішнім оглядом і вимірювальними інструментами. Зовнішньому огляду піддають 100% швів. Зовнішній огляд виявляє відхилення швів від заданої форми і розмірів, зовнішні тріщини, підрізи, пропали, пори, напливи.
Дефектні ділянки зварних швів видаляють механічним шляхом, газокисневим різанням або повітряно-дуговим струганням. Після виправлення шви піддають повторному контролю.
Технічні умови на основний метал Якість основного металу повинна відповідати вимогам сертифіката, що висилають заводу-виготовлювача; марку, хімічний склад сталі, профіль і розміри матеріалу, масу металу, номер партії, результати випробувань передбачених стандартом, номер стандарту на сталь даної марки. Вказують вимоги ГОСТ до поверхні металу й дефектам що припускаються на поверхні.
Технічні вимоги до електродів Розміри й загальні технічні вимоги до сталевих електродів для зварювання й наплавлення, регламентовані ДСТ 9466−75, тому ДСТ електроди виготовляють діаметром від 1.6 до 12(мм) і довжиною від 225 до 450(мм). Залежно від призначення електроди діляться на класи:
— електроди для дугового зварювання конструкційних сталей, для зварювання вуглецевих і легованих конструкційних сталей;
— для зварювання низьковуглецевих і низьколегованих сталей;
— для зварювання середньо вуглецевих і середньолегованих сталей;
— для зварювання легованих сталей із підвищеною міцністю.
Для кожного типу електрода розроблена одна або кілька марок покриття, що відрізняються складом, маркою зварювального дроту, властивостями наплавленого металу й призначенням.
Технічні вимогу до зварювального дроту Згідно із ГОСТ 2246–70 сталевий зварювальний дріт випускається від 0,3 до 12 мм. Цим же стандартом передбачається випуск 77 марок сталевого зварювального дроту різного хімічного складу й ділиться на 3 групи:
— низьковуглецеві дроти (6 марок);
— леговані дроти (30 марок);
— високолеговані дроти (41 марка).
Хімічний склад дроту дуже впливає на якість зварювального з'єднання. Тому марку зварювального дроту вибирають відповідно до хімічного складу зварюється сталі, ща, а також залежно від застосовуваного флюсу або захисного газу.
Вимоги до захисного газу У якості захисних газів застосовують інертні гази (аргон, гелій), активні гази (вуглекислий газ, азот). А так само суміші в різних пропорціях. Згідно із ГОСТ 8050–64 вуглекислий газ зріджений випускається двох сортів: чистий 99,5% і 99%. Вуглекислий газ першого сорту вибирають для зварювання конструкцій відповідального призначення.
1.4 Властивості матеріалу виробу. Визначення групи зварюваності
Металоконструкція Балка продольна 2ПС3,5900.01.01.020СБ виготовляється із сталі 20ХН ГОСТ 4543–71
Призначення — шестерні, чопи, пальці, деталі кріплення та інше. Деталі від яких потрібна підвищена в’язкість та помірна прокаливаємість.
Таблиця 3 — Хімічний склад сталі 20ХН, %
Хімічний елемент | % | |
Вуглець | 0,19 | |
Кремній | 0,17−0,37 | |
Мідь, не більш | 0,30 | |
Марганець | 0,40−0,70 | |
Нікель | 1,00−1,40 | |
Фосфор, не більш | 0,035 | |
Хром | 0,45−0,75 | |
Сіра, не більш | 0,035 | |
Таблиця 4 — Механічні властивості сталі 20ХН
Перетин, мм | МПА | МПА | % | КСU, ДЖ/ | |
Закалка 860 °C, масло. Отпуск 180°С | |||||
Для визначення групи зварювання, розрахуємо еквівалент вуглецю по формулі
(5)
де: C, Mn, Cr, Ni, Mo — вміст легованих елементів у сталі, %
Усі сталі поділяються що до зварювання на наступні групи:
1 Сталі, що добре зварюються Сэкв?0,25%
2 Сталі, що задовільно зварюються Сэкв=0,25−0,35%
3 Сталі, що обмежено зварюються Сэкв=0,35−0,45%
4 Сталі, що незадовільно зварюються Сэкв?0,45%
Еквівалент вуглецю складає 0,37%. Це означає, що сталь 20ХН відноситься до третьої групи зварювання, тому необхідно застосувати попередній підігрів, при температурі 120−200°C
1.5 Розрахунок на міцність зварних з'єднань Перевіримо на міцність зварне з'єднання Т1-?10, у якого, а довжина — 1680 мм. Тип з'єднання — таврове. На з'єднання діє сила Р=35КН.
Умова рівноміцності має наступний вигляд:
ф`? [ф`] (6)
Визначимо допущені напруження для основного металу:
(7)
де : — тимчасовий опір розриву (береться з таблиці марочника стелей);
n — коефіцієнт запасу міцності
Визначимо допущені напруження для металу шва:
[ф`] = 0,7[у], (8)
[ф`] = 0,7· 94,16 = 65,9 МПа Визначимо робоче напруження, яке виникло під час навантаження зварних швів:
(9)
де: Р =(3−4)k; k — катет шва Умова рівноміцності має наступний вигляд:
ф`? [ф`]
2,9?65,9
Запас міцності:
2. Технологічна частина
2.1 Обґрунтування укрупненої технології виготовлення деталей зварної конструкції
Укрупнена технологія має наступні переваги :
1. Понижується номенклатура деталей, які знаходяться у виробництві.
2. Зменшується обсяг документації.
3. Збільшується серійність виробництва, а отже й продуктивність.
4. Поліпшується якість заготівок, а отже якість складання і зварювання зварної конструкції.
2.1.1 Технологічний процес виготовлення деталей зварної конструкції
Вибір способів заготовки деталей виробів виконують виходячи з наступних вимог:
а) можливість мінімальної трудомісткості робіт;
б) максимальна продуктивність процесу заготівки;
в) максимальне використання заготівельного обладнання;
г) найменша кількість відходів матеріалів;
д) застосування сучасного заготівельного обладнання.
Технологічний процес виготовлення деталі поз.1 «Кронштейн»
2ПС3,5−900.01.01.021
Рисунок 1 — Ескіз деталі «Кронштейн» 2ПС3,5−900.01.01.021
Для виготовлення деталі поз.1 «Кронштейн» 4од. використовують прокат Карта розкрою метала для деталі «Кронштейн»
Вага деталі з креслення 2,16 кг Кількість деталей отриманих з листа:
19· 6 = 304 од.
Чиста вага деталей отриманих з листа:
2,16· 304 = 656,6 кг Чиста вага прокату :
140· 450·2·7,8 = 982 800 гр. = 982,7 кг Вагу усіх відходів визначимо, знаючи вагу всього листа 982,7 кг, отримаємо :
982,8−656,6 = 326,2 кг Визначаємо відсоток матеріалу за формулою:
Н/В ,
де: Н/В — норма відходу Н/В =
Отриманий відсоток відходу не відповідає нормам при виготовленні деталей з листового матеріалу у 4−8%, за рахунок складного обрису деталі.
Маршрутний технологічний процес виготовлення деталі «Кронштейн»
2ПС3,5−900.01.01.021
1. Транспортна Подати розміром 1400?4500 на ділянку заготовки.
Кран електромостовий Q = 5 т Строп АТ-475
2. Правильна Правити лист по площині витримавши площинність не більш 1 мм на 1 м довжини.
Багатоволкова листоправильна машина 9?360?2800
3. Термічне різання Різати лист згідно карти розкрою витримавши розміри 220?76.
КОМЕТА-М-К
4. Заточна Зачистка задирок деталей. Притупити гострі кромки.
Шліфувальний станок 3М636
5. Сверловка Висвердлити отвір діаметром 30 мм.
Радиально-свердлинний станок 2А554
6. Контрольна Контролювати розміри 86 мм, 230 мм, d=30мм, згідно креслення заготівки.
Вимірювальні інструменти Лінійка, штанген-циркуль Технологічний процес виготовлення деталі поз.2 «Кронштейн»
2ПС3,5−900.01.01.022
Для виготовлення деталі поз.2 «Кронштейн» 2 од. використовують прокат:
Карта розкрою для деталі «Кронштейн»
Вага виробу з креслення 2,05 кг.
Кількість деталей отриманих з листа:
19 · 16 = 304 од.
Чиста вага деталей отриманих з листа :
2,05 · 304 = 623,2 кг Чиста вага прокату:
140· 4502·7.8 = 982,800гр = 982,8 кг Вагу усіх відходів визначимо, знаючи вагу всього листа 982,8 кг, отримаємо:
982,8 — 623,2 = 359,6 кг Визначаємо відсоток матеріалу за формулою:
Н/В, (10)
де: Н/В — норма відходу Н/В =
Отриманий відсоток відходу не відповідає нормам при виготовленні деталей з листового матеріалу у 4−8%, за рахунок складного обрису деталі.
Маршрутно-технологічний процес виготовлення деталі «Кронштейн»
2ПС3,5−900.01.01.022
1. Транспортна
Подати розміром 1400?4500 на ділянку заготовки.
Кран електромостовий Q = 5 т Строп АТ-475
2. Правильна Правити лист по площині витримавши площинність не більш 1 мм на 1 м довжини.
Багатоволкова листоправильна машина 9?360?2800
3. Термічне різання Різати лист згідно карти розкрою витримавши розміри 220?76.
КОМЕТА-М-К
4. Правильна Правити лист по площині, витримавши площинність не більш 1 мм на 1 м довжини.
Прес фрикційний
5. Заточна Зачистка задирок деталей. Притупити гострі кромки.
Шліфувальний станок 3М636
6. Сверловка Висвердлити два отвори діаметром 30 мм.
Вертикально-свердлинний станок 2А-554
7. Контрольна Контролювати розміри 76 мм, 220 мм, d=30мм, згідно креслення заготівки.
Вимірювальні інструменти Лінійка, штанген-циркуль Технологічний процес виготовлення деталі поз.3 «Ребро»
2ПС3,5−900.01.01.023
Для виготовлення деталі поз.3 «Ребро» 2 од. використовують прокат Карта розкрою для деталі «Ребро»
Вага виробу з креслення 3,81 кг Кількість деталей отриманих зі смуги — 8 од.
Чиста вага деталей отриманих з листа:
3,81· 8 = 30,6 кг Чиста вага прокату:
600· 6·1,2·7,8 = 33 696 гр = 33,7 кг Вагу усіх відходів визначимо, знаючи вагу всієї смуги 33,7 кг, отримаємо:
33,7−30,6 = 1,1 кг Визначаємо відсоток матеріалу за формулою:
Н/В ,
де: Н/В — норма відходу Н/В =
Отриманий відсоток відходу не відповідає нормам при виготовленні деталей з листового матеріалу у 4−8%. Тому отриманий відсоток відходу можна використати для виготовлення інших деталей.
Маршрутно-технологічний процес виготовлення деталі «Ребро»
2ПС3,5−900.01.01.023
1. Транспортна Подати розміром 6000?60 на ділянку заготовки.
Кран електромостовий Q = 5 т Строп АТ-475
2. Правильна Правити лист по площині витримавши площинність не більш 1 мм на 1 м довжини.
Багатоволкова листоправильна машина 9?360?2800
3. Різка Різати лист згідно карти розкрою витримавши розміри 1700±5,6; 850±2,8.
Ножиці листові Н3222
4. Правильна Правити смугу по площині, витримавши площинність не більш 1 мм на 1 м довжини.
Багатоволкова листоправильна машина 9?360?2800
5. Заточна Зачистка задирок деталей. Притупити гострі кромки.
Шліфувальна машина ИП-2203
6. Контрольна Контролювати розміри 680 мм, 54 мм, згідно креслення заготівки.
Вимірювальні інструменти
Технологічний процес виготовлення деталі поз.4 «Балка»
1ПС3,5−900.01.01.051
Для виготовлення деталі поз.4 «Балка» 1од. використовують прокат Вага виробу з креслення 80,63 кг Кількість деталей отриманих з листа
2· 5 = 10 од.
Чиста вага деталей отриманих з листа:
80,63· 10 = 806,3 кг Чиста вага прокату:
5500· 1600·14·7,8 = 960,96 кг Вагу всіх відходів визначимо, знаючи вагу всього листа 960,96 кг, отримаємо:
960,96−806,3 = 154,66 кг Визначаємо відсоток матеріалу за формулою:
Н/В ,
де: Н/В — норма відходу Н/В =
Отриманий відсоток відходу не відповідає нормам при виготовленні деталей з листового матеріалу у 4−8%. Тому отриманий відсоток відходу можна використати для виготовлення інших деталей.
Маршрутно-технологічний процес виготовлення деталі «Балка»
1ПС3,5−900.01.01.051
1. Транспортна Подати розміром 5500?1600 на ділянку заготовки.
Кран електромостовий Q = 5 т Строп АТ-475
2. Правильна Правити лист по площині витримавши площинність не більш 1 мм на 1 м довжини.
Багатоволкова листоправильна машина 9?360?2800
3. Різка Різати лист згідно карти розкрою витримавши розміри 1700±5,5; 450±3,15; 850±2,8 .
Ножиці листові Н3222
4. Правильна Правити лист по площині, витримавши площинність не більш 1 мм на 1 м довжини.
Багатоволкова листоправильна машина 9?360?2800
5. Заточна Зачистка задирок деталей. Притупити гострі кромки.
Шліфувальна машина ИП-2203
6. Гнуття Виробляємо гнуття над листом розмірами 5500?1600, товщиною 14 мм.
Листозгинальний прес И1330
7. Контрольна Контролювати розміри 2600 мм, 284 мм, згідно креслення заготівки.
Вимірювальні інструменти Лінійка Технологічний процес виготовлення деталі поз.5 «Ребро»
1ПС3,5−900.01.01.054
Для виготовлення деталі поз.5 «Ребро» 1 од. використовують прокат Карта розкрою для деталі «Ребро»
Вага виробу з креслення 0,39 кг Кількість деталей отриманих зі смуги
(6000−20)/70 = 85 од.
Чиста вага деталей отриманих з листа:
85· 0,39 = 33,15 кг Чиста вага прокату:
6000· 60·12·7,8 = 33,7 кг Вагу усіх відходів визначаємо, знаючи вагу всієї смуги 33,7 кг, отримаємо:
33,7−33,15 = 0,55 кг Визначаємо відсоток матеріалу за формулою:
Н/В ,
де: Н/В — норма відходу Н/В =
Отриманий відсоток відходу н відповідає нормам при виготовленні деталей з листового матеріалу у 4−8%.
Маршрутно-технологічний процес виготовлення деталі «Ребро»
1ПС3,5−900.01.01.054
1. Транспортна Подати розміром 6000?60 на ділянку заготовки.
Кран електромостовий Q = 5 т Строп АТ-475
2. Правильна
Правити смугу по площині витримавши площинність не більш 1 мм на 1 м довжини. Багатоволкова листоправильна машина 9?360?2800
3. Механічне різання Різати лист згідно карти розкрою витримавши розміри 1700±5,6; 850±2,8. Ножиці листові Н3222
4. Заточна Зачистка задирок деталей. Притупити гострі кромки по периметру деталі.
Галтувальний барабан ДМЗ
5. Контрольна Контролювати розміри 60 мм, 70 мм, згідно креслення заготівки.
Вимірювальні інструменти Лінійка
2.1.2 Вибір заготівельного обладнання і його характеристика Для термічного різання деталі позиції 1 «Кронштейн» та позиції 2 «Кронштейн», що виготовляється з листа товщиною 20 мм. Застосовується машина для різання «Комета М-К», технічна характеристика якої наведена в табл.3
Таблиця 3 — Технічна характеристика машини «Комета М-К»
Параметри | Комета М-К | |
Ширина оброблюваного листа, мм | ||
Найбільша товщина розрізаємого листа, мм | ||
Параметри | Комета М-К | |
Для чотирьох різаків | ||
Швидкість обробки контуру, мм/хв | 50−8000 | |
Загальна потужність, кВт | ||
Габаритні розміри, мм | 6540?3390?2330 | |
Маса, кг | ||
Для різання листового прокату застосовую ножиці листові з похилим ножем Н3222, технічна характеристика якої наведена в табл.4
Таблиця 4 — Технічна характеристика ножиців листових з похилим ножем Н3222
Параметри | Н3222 | |
Найбільша товщина листа, що розрізається, мм | ||
Найбільша ширина, що розрізається, мм | ||
Число ходів ножа в хвилину | ||
Потужність електродвигуна, кВт | 16,5 | |
Габаритні розміри, мм | 5650?2500?2375 | |
Маса, т | 18,5 | |
Для правки листового прокату застосовую багатоволкову листоправильну машину, розміром 9?360?2800., технічна характеристика якої наведена в табл.5
Таблиця 5 — Технічна характеристика багатоволкової листоправильної машини розміром 9?360?2800
Параметри | 9?360?2800 | |
Розміри випрямляючого листа, мм: товщина найбільша ширина | 6−16 | |
Кількість правильних валків | ||
Діаметр правильних валків, мм | ||
Швидкість правки, м/с | 0,17 | |
Потужність електродвигунів, кВт : привода обертання валків привода підйому-опускання верхніх валків привода підйому направляючих валків | 2,8?2 | |
Габаритні розміри, мм | 11 823?4905?6368 | |
Маса, т | 218,2 | |
Для зачистки гострих кутів поз.1 «Кронштейн», поз. 2 «Кронштейн», застосовую шліфувальний станок 3М636, технічна характеристика якого наведена в табл.6
Таблиця 6 — Технічна характеристика шліфувального станку 3М636
Параметри | 3М636 | |
Діаметр шліфувального круга, мм | ||
Ширина шліфувального круга, мм | ||
Відстань між центрами шліфувальних кругів, мм | ||
Швидкість шліфувальних кругів, об/хв | 955−1425 | |
Потужність головного приводу, кВт | ||
Параметри | 3М636 | |
Габарити станка, мм | 1275?750?1350 | |
Маса станка, кг | ||
Для зачистки гострих кутів позиції 3 «Ребро», позиції 4 «Балка», позиції 5 «Ребро», застосовую шліфувальну машину ИП-2203, технічна характеристика якої наведена в табл.7
Таблиця 7 — Технічна характеристика шліфувальної машини ИП-2203
Параметри | ИП-2203 | |
Потужність, кВт | 1,3 | |
Діаметр абразивного круга, мм | ||
Посадковий діаметр круга, мм | ||
Тиск стисненого повітря, МПа | 0,63 | |
Частота обертання шпинделя на холостому ході, об/хв | ||
Робоча швидкість круга, м/с | ||
Габаритні розміри, мм | 285?210?205 | |
Маса, кг | 3,8 | |
Для висвердлювання отворів позиції 1 «Кронштейн», позиції 2 «Кронштейн», застосовую вертикально-свердлинний станок 2А554, технічна характеристика якого наведена в табл.8
Таблиця 8 — Технічна характеристика вертикально-свердлинного станка 2А554
Параметри | 2А554 | |
Діаметр свердлення у сталі, мм | ||
Потужність головного двигуна, кВт | 5,5 | |
Переміщення головки по рукаву, мм | ||
Переміщення рукава по колоні, мм | ||
Частота обертання шпинделя, об/хв. | 18−2000 | |
Кількість подач шпинделя | ||
Габаритні розміри, мм | 2665?1030?3430 | |
Маса, кг | ||
Для гнуття поз. 4 «Балка» застосовую листозгинальний прес И1330, технічна характеристика якої наведена в табл.9
Таблиця 9 — Технічна характеристика листозгинального пресу И1330
Параметри | И1330 | |
Номінальне зусилля преса, кН | ||
Довжина столу і повзуна, мм | ||
Ширина стола, мм | ||
Відстань між стійками станини в світлі, мм | ||
Відстань між столом і повзуном, мм | ||
Кількість безперервних ходів, хв | 40; 10 | |
Хід повзуна, мм | ||
Система управління | релійна | |
Габаритні розміри верстата, мм | 3000?1820?2950 | |
Маса верстата, кг | ||
2.1.3 Заходи щодо техніки безпеки і пожежної безпеки при заготівельних операціях Перед початком роботи на проектованій ділянці необхідно перевірити справність устаткування, пристосувань і інструмента, огорож, захисного заземлення, вентиляції. Під час роботи необхідно виконувати всі правила використання технологічного устаткування дотримуватися правила безпечної експлуатації транспортних засобів, тари та вантажо-підіймальних механізмів, дотримуватися вказівки про безпечне утримання робочого місця. В аварійних ситуаціях необхідно неухильно виконувати всі правила. Що регламентують поведінку персоналу при виникненні аварій і ситуацій, які можуть провести до аварій і нещасних випадків. По закінченні роботи повинно бути вимкнено все електро устаткування, проведена прибирання відходів виробництва та інші заходи, що забезпечують безпеку на ділянці. Ділянка має бути оснащена необхідними попереджувальними плакатами, обладнання повинно мати відповідне забарвлення, повинна бути виконана розмітка проїжджої частини, проїздів. Сама ділянка повинна бути спланований згідно з вимог техніки безпеки, а самедотримання: ширинипроходів, проїздів, мінімальна відстань між обладнанням. Всі ці відстані повинні бути не менше припустимих.
Щоб запобігти негативному впливу виявлених небезпечних та шкідливих виробничих факторів на здоров’я працівників, попередити виникнення виробничого травматизму при виконані технологічного процессу виготовлення деталі передбачаємо проведення наступних заходів загального характеру: раціональна організація робочих місць; регулярний контроль правильності всіх прийомів праці при виконанні операцій технологічного процесу; своєчасне проведення планово попереджувальних ремонтів виробничого обладнання та інструменту; підтримування проїздів та проходів в належному порядку; раціональні режими виконання всіх основних та допоміжних операцій технологічного процесу; ефективне використання засобів індивідуального захисту, своєчасний контроль їх стану, дотримання потрібної (встановленої нормами) періодичності їхньої заміни; використання сучасних запобіжних пристроїв і огородження робочих зон; проведення систематичного контролю стану обладнання та допоміжнихпристроїв та інших.
2.2 Обґрунтування вибору способу складання виробу Після формоутворення та підготовки поверхонь, деталі надходять на складання, що є однією з найбільш відповідальних операцій у виготовленні зварних і паяних виробів.
Аналізуючи конструкцію «Балка продольна» можна зробити висновок, що дана металоконструкція буде збиратися схемою повного складання конструкції з наступним зварюванням.
Рисунок 10 — Схема повного складання конструкції з наступним зварюванням Цю схему зазвичай використовують для порівняно простих виробів або виробів середньої складності, що складаються з невеликого числа деталей з легкодоступним для виконання з'єднаннями. За цією схемою конструкцію спочатку повністю збирають, закріплюючи елементи струбцинами, фіксаторами, прихваточними з'єднаннями і т.п., після чого зібрану конструкцію передають на зварювальну ділянку для виконання зварювання всіх з'єднань. Фронт робіт при цьому розширюється, цикл складальних робіт зменшується. Схема використовується при різних типах виробництва. Технологічний процес складання і зварювання залежно від програми випуску, маси й конфігурації виробів може бути механізований або повністю автоматизований.
2.2.1 Вибір електродів для прихватки при зварюванні. Вибір роду зварювального струму Після вибору схеми складання вибираю зварювальні матеріали для виконання прихваток.
Для виконання прихваток застосовую ручне дугове зварювання, внаслідок її малої продуктивності. Сталь 20ХН — низьколегована вуглецева сталь, тому необхідно застосовувати постійний струм зворотної полярності, тому що електрод для прихваток буде застосовуватися, що плавиться. Для прихваток необхідно застосовувати електрод хімічний склад, що дає і механічні властивості наплавленого металу близькі до основного металу.
Таким є електрод типу Е-ХМФ-Ф, марки ЦЛ-20−63.
Для виконання прихваток застосовуємо електрод типу Е-ХМФ-Ф марки ЦЛ-20−63.
Таблиця 10 — Зварювально-технологічні властивості електроду марки ЦЛ-20−63
Стійкість дуги | Задовільна | |
Розбризкування | Мале, втрати близько 2% | |
Формування шва | Задовільне | |
Віддільність жужільної кірки | Задовільна | |
Типовий коефіцієнт наплавлення | 10,3 г/А· ч | |
Витрата електродів на 1 кг наплавленого металу | 1,6 кг | |
Таблиця 11 — Типовий хімічний склад наплавленого металу, електрода типу Е-ХМФ-Ф %
Зміст | C | Si | Mn | Cr | Mo | V | S | P | |
ГОСТ ЦЛ-20−63 | 0,08−0,13 0,10 | 0,15−0,45 0,25 | 0,5−0,9 0,75 | 0,8−1,2 1,00 | 0,40−0,70 0,55 | 0,10−0,35 0,20 | ?0,04 <0,04 | ?0,04 <0.04 | |
Таблиця 12 — Типові механічні властивості наплавленого металу, електрода типу Е-ХМФ-Ф
Значення | кгс/ | кгс/ | д, % | |
ГОСТ : при 20°C | ; | ? 50 | ?16 | |
ЦЛ-20−63 при 20°C при 540°C | 17,4 | |||
2.2.2 Розрахунок режиму ручної дугової прихватки Як правило ручне дугове зварювання у серійному, багатосерійному і масовому виробництві використовується в основному для виконання прихваток, внаслідок малої продуктивності. Основними вихідними даними для розрахунку режиму зварювання є: катет прихватки, марка та діаметр електрода.
1. Сила зварювального струму розраховується за формулою :
(11)
де: d — діаметр електрода прийнятий; i — припустима щільність струму Приймаємо
Таблиця 13 — Припустима щільність струму (А/) у електроді при ручному дуговому зварюванні
Вид покриття | Діаметр стрижня електрода, мм | ||||
Кисле, рутилове | 14−20 | 11,5−16 | 10−13,5 | 9,5−12,5 | |
Основне | 13−18,5 | 10−14,5 | 9−12,5 | 8,5−12,0 | |
Напруга на дузі при ручному дуговому зварюванні змінюється у межах
20−36 В і не регламентується.
Швидкість зварювання розраховується за формулою:
(12)
де: — швидкість зварювання; - коефіцієнт наплавлення по паспорту;
— сила зварювального струму; г=7,8 — щільність наплавленого металу;
— площа наплавленого металу за 1 прохід
2.2.3 Вибір джерела живлення для ручної дугової прихватки, його характеристика й паспортні дані
Виконання прихваток, під час складання «Кронштейна», виконується на постійному струмі зворотної полярності. Спосіб зварювання для виконання прихваток ручне дугове зварювання. Тому необхідно застосувати джерело живлення постійного струму з крутопадаючою зовнішньою характеристикою. Можна використати однопостове та багатопостове джерело живлення. Однопостове джерело живлення краще використовувати при дрібносерійному та серійному виробництві. При багатосерійному та масовому виробництві краще використовувати багато постову ситсему живлення зварювальних постів зварювальним струмом. Це дає можливість розвантажити робочі місця від обладнання, з економити виробничу площу і кошти. Тому для зварювання пропонується багатопостове джерело живлення постійного струму із жорсткою зовнішньою характеристикою, крутопадаюча характеристика на кожному робочому місці забезпечується баластовим опором. Зварювальний струм одного поста становить 240 А .
Багатопостові джерела живлення застосовуються в умовах багатосерійне й масового виробництва, дозволяють заощаджувати виробничу площу, кошти й електроенергію, підвищують культуру виробництва, за рахунок розвантаження робітників місць від зварювального устаткування. При чому джерела живлення забезпечують незалежну роботу зварювальних постів і незначне спадання напруги у шинодроту. Тому для одночасного живлення декількох постів постійним струмом застосуємо багато постовий випрямляч ВДМ-1001. Дане джерело живлення зможе одночасно забезпечувати зварювальним струмом 240А постів, де: Iзв— номінальний зварювальний струм одного поста;
Iд.ж.— номінальний зварювальний струм багато постового джерела живлення, А Ці джерела мають падаючу зовнішню характеристику на вході кожного зварювального поста, що забезпечується включенням баластового опору (РБ-201, РБ-301). Для ручного дугового зварювання і автоматичного зварювання під флюсом вітчизняна промисловість випускає багатопостові випрямлячі типу ВДМ. Основними елементами випрямляча типу ВДМ є трифазний трансформатор Т, випрямний блок В, шинопровод з баластовими опорами.
Ці джерела мають падаючу зовнішню характеристику на вході кожного зварювального поста, що забезпечується включенням баластового опору. Для ручного дугового зварювання й автоматичного зварювання під флюсом вітчизняна промисловість випускає багатопостові випрямлячі типу ВДМ Основними елементами багатопостового випрямляча типу ВДМ є трифазний трансформатор Т, випрямний блок В, шинопровод з баластовими опорами.
Рисунок 11 — Електрична схема багатопостового випрямляча ВДМ.
Первинна обмотка трифазного трансформатора Т включається. за схемою «трикутник» і має відводи в кожній фазі, які призначені для стабілізації вихідної напруги мережі в діапазоні ±5%Uном
Вторинна обмотка має дві секції, які включені за схемою «зірка», а їх ЕДС зрушені на кут. Причому нейтраль першої секції цієї обмотки утворить негативний вивід, а нейтраль другої секції - позитивний вивід випрямляча. Початку секцій вторинної обмотки підключені до напівпровідникових кремнієвих діодів VI — V6 випрямного блоку В. Число діодів у кожній фазі визначається струмом навантаження. При необхідності збільшення числа діодів на кожній фазі їх поєднують у блоки.
Випрямляч типу ВДМ має швидкодіючий тепловий захист відповідно від короткочасного й тривалого перевантаження. Вихідна напруга випрямляча надходить на 1-й зварювальний пост через шинопроводи і баластові опори Rб.
Таблиця 14 — Технічна характеристика випрямляча ВДМ-1601
Параметри | ВДМ-1601 | |
Номінальний зварювальний струм випрямляча, кА | 1,6 | |
Номінальний зварювальний струм поста, А | ||
Діапазон регулювання зварювального струму, А | 12−3,15 | |
Напруга, В : холостого ходу номінальне робоче | ||
Число зварювальних постів | ||
Тип балансового опору | РБ-301 | |
Споживна потужність, кВт | ||
Габаритні розміри, мм | 1100?700?900 | |
Маса, кг | ||
2.2.4 Розробка або модернізація пристосування для складання, опис пристрою й принципу його дії
До пристосування для складання металоконструкції «Балка продольна» 2ПС3,5−900.01.01.020 СБ, входять дев’ять позицій:
1 Основа — 1од.
2 Упор — 3од.
3 Відкідний прижим — 2 од.
4 Шаблон — 1од.
5 Упор — 1од.
6 Фальшвал — 3 од.
8,9 — Стандартні вироби (болт М10, шайба) Пристосування працює таким чином:
Відкидні притиски знаходяться у вихідному положенні. Спочатку в пристосування з постійним упорів встановлюється поз.4 «Балка» 2ПС3,5−900.01.01.051 і гвинтовими притисками притискають поз.3 «Ребро» 2ПС3,5−900.01.01.023.
Потім в пристосування встановлюється поз.2 «Кронштейн» 2ПС3,5−900.01.01.022 в кількості 2 штук по «Упорам» поз.5 і за «Фальшвалом» поз.6,7. «Кронштейн» 2ПС3.5−900.01.01.021 поз.1 — 4 од. встановлюється за «Упорів» поз.2, «Фальшвалу» поз.7 і «Шаблоном» поз.4. «Ребро»
2ПС3,5−900.01.01.023 поз.3 і «Ребро» 1ПС3,5−900.01.01.054 поз.5 встановлюється за «Упорів» поз.2 і поз.5.
Деталі прихоплюються ручним дуговим зварюванням. Після прихваток зібрана конструкція розкріплюється, місця прихваток зачищаються від шлаку і бризок розплавленого металу. Після очищення зібрана конструкція знімається з пристосування і укладається на місце складування, за допомогою крана консольно-поворотного вантажопідйомністю 0,25 т. Пристосування дозволяє витримати розміри 50?2690 і вага пристосування 185 кг. Кріплення «Упорів» поз.2 і «Відкидного упора» поз. 3, до основи пристосування, здійснюється за допомогою болтів М10.
2.2.5 Технологічний процес складання виробу Складання Випрямляч ВДМ-1001
Пристосування для складання КП.ЗВ.ВЗК.01.13.000 СК
1. Подати на робоче місце складальника деталь позиції 1 — 4 од.,
позицію 2- 2 од., позицію 3 — 2 од., позицію 4 — 1 од., позицію 5 — 1 од., за допомогою крана поворотного Q=0,25 т Строп АТ-475
2. Зачистити крайки деталей, що підлягають зварюванню та поверхні, що прилягають до них на ширині не менш 20 мм.
Щітка сталева РСТУ1554−90
3. У пристосування для складання встановити позицію 1 — 4 од., позицію 2−2 од., позицію 3 — 2 од., позицію 4 — 1од., позицію 5 — 1 од. Притиснути гвинтовим притискачем та прихватити ручним дуговим зварюванням, кількість прихваток
62 од. Довжина прихваток 30 мм, кількість 62 од., довжина шва 18,6 м, катет шва 4 мм. При складані витримати розмір 450±3.15; 850±2,8; 1700±5,6; 71±1,9; 70±1,9. Електродотримач ЕД-201 ГОСТ 14 651–90
Щиток РНП-Е105У1 ГОСТ 124 035–78
Електроди діаметром 4 мм, типу Е-ХМФ-Ф марки ЦЛ-20−63 ГОСТ 9466–60
Режими зварювання: ;
4. Зачистити прихватки й біля шовну зону від шлаків і бризгів.
2810−0203 зубило Н12ХР ГОСТ 7211–86
7850−0118 молоток Ц15ХР ГОСТ 2310–77
5. Таврувати вузол.
654−034 клеймо
7850−0118 молоток Ц15ХР ГОСТ 2310–77
2.2.6 Технологічний процес контролю якості складання Контроль (складання)
1. Перевірити якість прихваток і зачистити зовнішнім оглядом.
2. Контролювати розміри прихваток 30 мм, катет 5 мм і розміри креслення 850±2,8; 1700±5,5; 450±3,5
Катетомер, штангенциркуль ШЦ-125 ГОСТ 166–70
3. Таврувати вузол.
654−034 клеймо,
7850−0118 молоток Ц15ХР ГОСТ 2310–77 .
2.2.7 Технічне нормування процесів складання Норма штучного часу на складання металоконструкції в цілому визначається як сума витрат часу на встановлення, кріплення та установку прихваток.
Норма часу на складання вузла металоконструкції визначається за формулою:
(13)
де:, , — штучний час на виконання окремих слюсарно-складальних операцій; - підготовчо-заключний час, виражений у відсотках від штучного часу на виконання слюсарно-складальних операцій; - сумарний коефіцієнт, що враховує умови виконання роботи, який розраховується за формулою:
(14)
де: — коефіцієнт, залежний від зручності виконання роботи;
— коефіцієнт, залежний від наявності застосування механізованих чи універсальних складальних пристроїв; - коефіцієнт, залежний від марки металу, що застосовується для складання вузла; - коефіцієнт, залежний від кількості вузлів (виробів) у партії.
Таблиця 15 — Специфікація виробу
Позиція | Найменування | Кількість | Маса, кг | Прим. | |
Кронштейн L=0,22 м | 2,16 | ||||
Кронштейн L=0,22 м | 2,05 | ||||
Ребро L=0,68 м | 3,81 | ||||
Балка L=2,6 м | 80,63 | Базова деталь | |||
Ребро L=0,07 м | 0,39 | ||||
За умови, що базову деталь «Балка» поз.4, довжиною 2.6 м та масою 80,63 кг необхідно встановити на плиту підйомним краном для подальшого складання. Штучний час на її встановлення складає: хв За умови встановлення деталі «Кронштейн» поз.1, довжиною 0,22 м та масою 2,16 кг, штучний час її встановлення складає:
хв За умови встановлення деталі «Кронштейн» поз.2, довжиною 0,22 м та масою 2,05 кг, штучний час її встановлення складає:
За умови встановлення деталі «Ребро» поз.3, довжиною 0,68 м та масою 3,81 кг, штучний час її встановлення складає :
За умови встановлення деталі «Ребро» поз.5, довжиною 0,07 м та масою 0,39 кг, штучний час її встановлення складає
За умови, що складність виконувати роботи проста. Підготовчо-заключний час становить:
За умови, що складання виробів виконується у зручних умовах на плиті із вуглецевої сталі, коефіцієнти, що враховують умови виконання роботи, становлять:
— коефіцієнт, залежний від зручності виконання роботи
— коефіцієнт, залежний від наявності застосування механізованих чи універсальних складальних пристроїв
— коефіцієнт, залежний від марки металу, що застосовується для складання вузла
— коефіцієнт, залежний від кількості вузлів (виробів) у партії
Таким чином сумарний коефіцієнт, що враховує умови виконання роботи, становить:
Норма часу на складання виробу становить:
2.2.8 Заходи щодо охорони праці та техніки безпеки при складанні металевої конструкції
Виготовлення металоконструкцій пов’язане із застосуванням великої кількості верстатів різних видів, що мають частини, які швидко обертаються (шпинделі, вали, планшайби, маховики, шестерні тощо), а також частини, які створюють значний тиск (ножиці, преси), працюють від електроприводу. Порушення правил техніки безпеки при експлуатації верстатів може спричинити нещасні випадки або викликати аварію. Для запобігання виробничому травматизму персонал, який обслуговує верстати та механізми, управляє ними, повинен досконально знати і постійно застосовувати правила охорони праці при роботі на них і під час виконання робіт, пов’язаних з ними.
Основне технологічне обладнання повинне знаходитись поза траєкторіями руху вантажопідйомних засобів з вантажами. Біля робочих місць слід передбачити майданчики для складання матеріалів, деталей та металоконструкцій до і після обробки, складання або зварювання. Габарити цих майданчиків треба покрасити фарбою. Складувати матеріали, деталі або металоконструкції можна тільки у відведених для цього місцях на майданчиках. На підлозі робочого місця не повинно бути клоччя та відходів виробництва.
Матеріали, деталі та металоконструкції необхідно складати так, щоб вони не заставляли робоче місце і не могли розсипатися або впасти.
Всі машини, верстати, апарати, пристрої, установки та небезпечні зони повинні бути надійно загороджені. Під небезпечною зоною мається на увазі простір, в якому постійно діють або періодично виникають фактори, небезпечні для життя та здоров’я людини. Небезпечна зона може бути обмеженою або постійною. Наприклад, зона між набігаючою віткою привідного ременя та шківом. Іноді розміщення небезпечної зони в просторі та її габарити безперервно змінюються (так, при сучасних режимах фрезерування сталей зона дії потоку стружок переміщується).
Верстати фарбують у світлі тони. Загородження на верстатах і машинах мають колір самого устаткування. Місця, які треба закривати, фарбують у червоний колір, який добре видно, коли загородження знято.
Усі передачі (ремінні, канатні, ланцюгові, шарнірні та ін.) повинні мати міцні запобіжні загородження, а гайки, болти та інші елементи обертових частин машин та механізмів, що перебувають на висоті 2,5 м й нижче від підлоги, — надійні загорожі. Оброблювані предмети, які рухаються, а також виступають за габарити устаткування, треба також загороджувати запобіжними пристосуваннями. Пристрої для зупинки обладнання або механізму слід розміщувати таким чином, щоб ними можна було зручно користуватися з робочого місця і самі вони в жодному разі не могли ввімкнутися. Пускові пристрої повинні забезпечувати швидкість і плавність вмикання устаткування, а також зручність користування ним.
Розміщення органів управління (ручок, маховичків, кнопок) повинно бути зручним і безпечним при користуванні і гарантувати для обслуговуючого персоналу мінімум переходів навколо устаткування та механізму. Наявність кількох місць пуску, як правило, забороняється Виняток можна зробити тільки для великого устаткування. Для управління цим устаткуванням слід опрацювати спеціальну інструкцію. Якщо устаткування обслуговує бригада робітників, віддати наказ про пускможе тільки бригадир. При кнопковому вмиканні устаткування або механізму кнопки заглиблюють на 3—5 мм у внутрішню стінку пускової коробки, контакти кнопок захищають від потрапляння пилу та стружки, а також від дії емульсій, мастил та інших речовин, які вживаються під час роботи. Кнопки зупинки мають червоний колір, напис «Стоп» і виступають над панеллю на 3 мм. Пускові деталі устаткування повинні мати надійні загородження або запобіжні пристрої, які виключають можливість мимовільного вмикання устаткування через, наприклад, падіння предмета або випадкове натискування. Пускові педалі повинні виступати над рівнем підлоги не більше ніж на 120 мм, а опускатися нижче положення натискування (вмикання) вони можуть не більше ніж на 60 мм. Зусилля при натискуванні на педаль, потрібне для пуску устаткування при положенні робітника сидячи, не може перевищувати 26,5 Н, стоячи — 34,3 Н.
Для обслуговування устаткування, на якому обробляються важкі деталі (масою більше 20 кг), треба передбачати відповідні підйомні пристрої або пристрої, за допомогою яких можна встановлювати і знімати деталі (крани, стріли, рухомі роликові столи тощо). Затискні пристрої (задній центр, патрон і т.п.) повинні забезпечувати швидкий і надійний захват деталі.
2.3 Вибір способу зварювання вузла
2.3.1 Обґрунтування вибору способу зварювання вузла Для даної металоконструкції обираємо електродугове напівавтоматичне зварювання у середовищі захисних газів. Переваги:
а) підвищення продуктивності в порівнянні з ручним зварювання в 1,2−1,5 рази. А при зварюванні порошковим дротом в 1,6−2,0 рази;
б) можливість зварювання у будь-якому положенні;
в) можливість і доцільність зварювання малокаліберних швів і виробів малої товщини;
г) висока маневреність і мобільність у порівнянні з автоматичним зварюванням;
д) можливість індивідуального контролю за напрямком дуги по шву.
Недоліки:
а) сильне розбризкування металу при зварюванні на струмах 200−400 А та необхідність видалення бризів з поверхні виробу. Цей недолік не відноситься до зварювання порошковим дротом;
б) низька продуктивність праці (якщо багато часу затрачається на видалення бризів);
в) зовнішній (товарний) вид швів гірше. Ніж при зварюванні під флюсом.
Галузь раціонального застосування:
а) у одиничному, дрібносерійному, рідше у серійному виробництві;
б) переважно для зварювання малокаліберних швів у будь-якому просторовому положенні.
2.3.2 Вибір зварювальних матеріалів і їхня характеристика Вибір роду зварювального струму Для одержання зварних швів необхідного хімічного складу та механічних властивостей, необхідно застосувати зварювальні матеріали які б забезпечували наплавлений метал близький по хімічному складу та механічним властивостям до основного металу Для зварювання у середовищі вуглекислого газу, застосовуємо вуглекислий газ першого сорту СТУ 14 175:2004 та зварювальний дріт марки Св-18ХГСА ГОСТ 8050–64. Хімічний склад наведено у табл. 16
Таблиця 16 — Хімічний склад Св-18ХГСА
С | Cr | Mn | Si | N | |
0,18% | 1% | 1% | 1% | 1% | |
2.3.3 Розрахунок режимів зварювання Розрахунок напівавтоматичного зварювання у середовищі захисних газів:
1. Катет шва 5 мм, тому для даної металоконструкції обираємо діаметр дроту 1,6 мм.
2. Виліт електрода:
(15)
де: — діаметр електродного дроту
3. Сила зварювального струму:
(16)
4. Швидкість подачі електродного дроту:
(17)
де: — коефіцієнт розплавлювання електродного дроту і визначається по формулі:
(18)
5. Швидкість зварювання:
(19)
де : — швидкість зварювання; - площа наплавленого металу
6. Коефіцієнт наплавлення:
(20)
де: — коефіцієнт розплавлення; - втрати електродного матеріалу в наслідку окислювання, випари та розбризкування,, для розрахунків приймається 10%
7. Напруга на дузі:
(21)
2.3.4 Вибір устаткування для механізованого зварювання Згідно обраного способу зварювання, необхідно обрати устаткування, яке буде забезпечувати прийняті режими зварювання: м/ч;; л/хв. Для механізованого зварювання застосовуємо випрямляч ВДГМ-1602−1 та полуавтомат ПДГ-508, технічні характеристики яких приведені у табл. 16, табл. 17
Таблиця 16 — Технічна характеристика випрямляча ВДГМ-1602−1
Номінальний зварювальний струм випрямляча, кА Номінальний зварювальний струм поста, А Діапазон регулювання зварювального струму поста, А Напруга, В: холостого ходу номінальне робоче Число зварювальних постів Тип баластового опору Споживана потужність, кВ· А Габаритні розміри, мм Маса, кг | 1,6 200−400 РБГ-401 1150?900?1850 | |
Таблиця 17 — Технічні характеристики напівавтомату ПДГ-508
Параметри | ПДГ-508 | |
Номінальна напруга мережі, В | ||
Частота живильної мережі, Гц | ||
Номінальний зварювальний струм, А | ||
Рід струму | постійний | |
Межі регулювання зварювального струму, А | 100−500 | |
Діаметр електродного дроту, мм | 0,2−2 | |
Швидкість подачі електродного дроту, м/ч | 0,2−2 | |
Маса електродного дроту, м/ч | 108−932 | |
Маса електродного дроту у касеті, кг | ||
Витрата газу, л/хв | 8−20 | |
Габаритні розміри довжина ширина висота | 445±10 316±10 370±10 | |
Маса напівавтомату, кг | ||
2.3.5 Технологічний процес зварювання металоконструкції
Зварювання Випрямляч ВДГМ-1602−1
Напівавтомат ПДГ-508
Кран консольно-поворотній Q=0,25т
1. Подати на робоче місце зварника складальну одиницю за допомогою крана консольно-поворотнього Q=0,25 т Строп АТ-475
2. Зачистити місця, які підлягають зварюванню та прилягають до них поверхні на ширині не менш 20 мм Щітка сталева ГОСТ 1454–91
3. Покрити біля шовні зони розчином сульфітно-спиртової барди КБЖ Кисть ГОСТ 10 597–91
4. Заварити складальну одиницю суцільними швами за один прохід, застосувавши 4 контування на 90°, 2 кантування на 180°, 6 контувань на 45°.