Аналіз конструкції обладнання
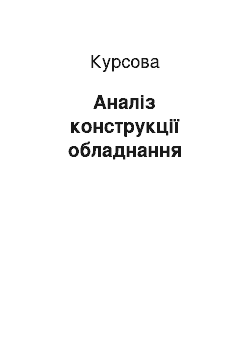
Молотковий барабан обертається в дробильній камері. Для відбору сухих подрібнених кормів є відсмоктуючий патрубок, а для відбору вологих кормів — замість решета вставляють викидну горловину прямокутного перерізу. При цьому відгвинчують дві смушкові (зі смушків) гайки і відкидають вниз кришку вивантажувального люка. До корпусу дробарки прикріплений улиткообразный кожух вентилятора. Його… Читати ще >
Аналіз конструкції обладнання (реферат, курсова, диплом, контрольна)
Вступ
У сільськогосподарських областях промисловості величезна увага приділяється процесу подрібнення (зерна, соковитих кормів, сіна). Дробильні машини є складовою ланкою у виробництві комбікормів та інших сполук та сумішей. На практиці, молоткова дробарка займає особливе положення серед іншого сільськогосподарського обладнання, так як подрібнення і дроблення зерна, кукурудзи, злаків і бобових потребує особливих апаратів. Саме для цих цілей у сільському господарстві застосовується молоткова дробарка зерна.
Молоткові дробарки мають ряд переваг:
· універсальність;
· можливість широкого регулювання ступеню подрібнення в межах від грубого помолу до тонкого:
· відсутність нагрівання продукту, що перероблюється;
· відсутність залипання робочих органів при переробці продуктів з підвищеною вологістю;
· наявність вентилятора, що забезпечує транспортування здрібненого продукту.
Промисловість випускає для подрібнення зерна декілька молоткових дробарок: КДМ — 2,0; КДМ — 3,0; КДУ — 2,0; ДБ-5 та інші.
Метою курсового проекту є аналіз конструкції обладнання, а саме молоткової дробарки КДУ-2.0; її призначення, технічна характеристика та розрахунок параметрів її складових.
1. Аналіз конструкції обладнання
1.1 Призначення і технічна характеристика
Кормодробарка універсальна КДУ — 2,0 призначена для подрібнення зерна, качанів кукурудзи, шроту, сіна та інших грубих кормів, а також для подрібнення зелених кормів, силосу та коренеплодів. Вона складається з силосорізки барабанного типу для попереднього грубого подрібнення несипких стеблових кормів та молоткової дробарки для перемелювання на борошно, дерть чи м’язгу.
1.2 Будова і принцип дії
Схема кормодробарки КДУ — 2,0 представлена на рис. 1.1.
Рис. 1.1. Універсальна дробарка кормів КДУ — 2,0: 1 — дробильний апарат; 2 — вентилятор; 3 — завантажувальний ківш; 4 — рукава; 5 — шлюзовий затвор; 6 — циклон; 7 — кормової трубопровід — 8 — повітряний трубопровід; 9 — фільтрувальний рукав; 10 — амперметр-індикатор; 11 — черв’ячний редуктор; 12 — ножовий барабан; 13 — важіль включення; 14 — подаючий транспортер; 15 — електродвигун; 16 — рама — 17 — підпресовуючий транспортер; 18 — редуктор.
Трибопроводи: прямий (нагнітальний) 7 і зворотній (відвідний) 8.
Крім того, дробарка обладнана барабаном 12, живильним 14 і пресуючим 17 транспортерами. Для підведення зернових матеріалів в дробильну камеру є завантажувальний бункер 3.
Всі вузли машин змонтовані на рамі 16. Привід робочих органів здійснюється від електродвигуна 15.
З машиною додатково постачають контрпривод для приводу машини від трактора.
Для попереднього подрібнення стеблових та інших несипучих кормів служить ножовий барабан 12 і протиріжуча пластина, для остаточного подрібнення — дробильний апарат. Зазор між ножем і протирізальною пластиною повинен бути 0,5…0,8 мм, який встановлюють двома регулювальними гвинтами.
Для зміни подачі ножовий барабан має дві змінні зірки з різною кількістю зубців (z1 -15 і z2 -20).
Для подачі стебельчатих та інших несипучих кормів до ножового барабана машина обладнана транспортерами: основним — живильним і допоміжним — пресуючим.
Пресування пухкої кормової маси забезпечується вагою пресуючого транспортера і тиском пружин. При цьому пресуючий транспортер притискається вниз до упору, встановленого на вертикальних стінках корита живильного транспортера.
Живильний і пресуючий транспортери примикають кінцями до завантажувального вікна кожуха ножового барабана і приводяться в дію від вала ножового барабана за допомогою передавального механізму.
Передавальний механізм складається з редуктора 4, закріпленого під рамою живильного транспортера. Конструкція редуктора забезпечує включення транспортерів в роботу, вимикання з неї і зворотну подачу матеріалу у випадках забивання завантажувальної горловини.
Дробильний апарат являє собою молоткову дробарку.
На одному кінці вала дробильного барабана закріплений шестилопатний вентилятор, на іншому — двоступінчастий багатострумковий шків для клинопасової передачі.
Молотковий барабан обертається в дробильній камері. Для відбору сухих подрібнених кормів є відсмоктуючий патрубок, а для відбору вологих кормів — замість решета вставляють викидну горловину прямокутного перерізу. При цьому відгвинчують дві смушкові (зі смушків) гайки і відкидають вниз кришку вивантажувального люка. До корпусу дробарки прикріплений улиткообразный кожух вентилятора. Його всмоктувальна горловина з'єднана з пиловідводним патрубком, а вихідний патрубок з'єднаний транспортуючим трубопроводом 8 (рис. 1.1) з циклоном 6. Циклон призначений для прийому подрібненого корму. Верхній патрубок циклону з'єднаний з верхнім кінцем повітропроводу 8.
Рис. 1.2. Схема дробарки КДУ — 2,0 (розріз): 1 — дробильний барабан; 2 — змінне решето; 3 — зарешітна камера; 4 — люк викиду; 5 — вставна викидна горловина; 6 — кришка дробильної камери; 7 — магнітний сепаратор; 8 — ківш-бункер для сипучих кормів; 9 — патрубок для води; 10 — ріжучий барабан; 11 — підпресовуючий транспортер; 12 — живильний (подаючий) транспортер; 13 — приймальний повітряний патрубок; 14 — рама; 15 — електродвигун; 16 — відсмоктуючий патрубок вентилятора; 17 — дека; 18 — протиріжуча пластина.
Повітряний потік, звільнений від розмеленого продукту, направляється з циклону по зворотному трубопроводу знову в дробарку, несучи з собою пилову фракцію. Частина зворотного повітряного потоку, проходячи через фільтрувальний рукав 9, встановлений перед дробаркою, відводиться назовні. Завдяки цьому в місцях надходження корму в дробильну камеру створюється розрідження і підсмоктування свіжого повітря. Це усуває запилювання і активізує надходження корму в дробильну камеру. У конусній частині циклону на діаметрально протилежних сторонах зроблені два вікна. Одне з них, закрите прозорою пластиною, служить для спостереження за потоком корму, інше, закрите металевою кришкою, служить для очищення циклону в разі його забивання подрібненим кормом. Нижньою частиною циклон з'єднаний зі шлюзовим затвором, який складається з порожнього корпуса з двома боковинами і ротора, що обертається усередині нього.
До вивантажувального патрубка шлюзового затвора прикріплені здвоєні набивні рукави з перекидною заслінкою і мішкодержачами.
Для подачі в дробильну камеру сипучого корму над верхньою живила горловиною змонтований завантажувальний ківш 8. Подача сипучої маси регулюється поворотною заслінкою з гвинтовим механізмом. У прорізах скатних стінок корпусу дробарки на шляху руху корму закріплені магнітні сепаратори: верхній і нижній, призначені для уловлювання залізних частинок, які випадково потрапили в корм. На валу електродвигуна встановлений восьмиструмковий двоступінчастий шків клинопасової передачі. Шість клиновидних ременів від одного ступеня шківа передають обертання дробильному барабану і вентилятору. Два ременя від другого ступеня шківа обертають ножовий барабан. Для полегшення запуску двигуна, зручності управління та контролю за ступенем його завантаження та інсталяції самої дробарки агрегат укомплектований магнітним пускачем з пусковою кнопкою, плавкими запобіжниками, пакетним перемикачем, автоматичної фрикційною муфтою відцентрової дії і амперметром-індикатором.
Магнітний пускач забезпечений тепловим реле, що відключає електродвигун при тривалому перевантаженні.
Магнітний пускач, плавкі запобіжники і пакетний перемикач змонтовані в спеціальному виносному шафі, який встановлюють у приміщенні, де працює кормодробарка.
Амперметр-індикатор призначений для спостереження за завантаженням машини в процесі роботи і дозволяє краще її регулювати. Амперметр-індикатор і пускова кнопка магнітного пускача закріплені на пружинах спеціальної рамки, встановленої на корпусі дробарки. Рамка з приладами зроблена поворотною і забезпечує зручне спостереження за показами амперметра з робочого місця машини. Автоматично діюча фрикційна відцентрова муфта служить для полегшення пуску в роботу двигуна в агрегаті з дробаркою. Устрій її наступний. Усередині полого шківа, що обертається на валу електродвигуна в двох шарикопідшипниках, поміщені чотири фрикційні колодки, закріплені на плоских пружинах. Пружини пов’язані з хрестовиною, що сидить міцно на валу електродвигуна. Порожнистий шків з'єднаний клиноподібними ременями зі шківом молоткового (дробильного) барабана. При запуску електродвигуна в роботу шків, вільно посаджений на валу, стоїть на місці внаслідок гальмування приводними ременями. Потім, по мірі збільшення частоти обертання вала електродвигуна, фрикційні колодки під дією відцентрової сили долають пружну дію пружин і входять в зіткнення з шківом. Таким чином забезпечується автоматичне включення в роботу дробарки при досягненні валом двигуна певної частоти обертання.
Технологічний процес.
В завантажувальний ківш засипають сипучі корми при закритій поворотній заслінкці. Потім запускають машину в роботу і, стежачи за показниками амперметра-індикатора, поступово відкривають заслінку завантажувального копа. Перевантажувати машину не рекомендується. Подрібнений корм з-під дробильної камери відсмоктується вентилятором через відсмоктуючий патрубок і по нагнітальній трубі подається в циклон. З циклону подрібнення маса через шлюзовий затвор надходить з двох вивантажних рукавів у мішки або на транспортер, встановлений під вивантажувальними рукавами, щоб подати її до бункера або інші машини. Кукурудзяні качани, сіно та інші несипучі і стебельчаті корми направляють по живильному транспортеру до ножового барабана для попереднього подрібнення. Корм, подрібнений ножовим барабаном, надходить в дробильну камеру, де відбувається остаточне подрібнення. Ступінь подрібнення регулюється постановкою відповідного змінного сита (решета) з великим або меншим діаметром отворів. Для подрібнення вологих кормів машину переобладнують. Виймають решето, а замість нього встановлюють вивантажувальний патрубок. Потім відкривають кришку вивантажувального люка, а засллонку завантажувального ковша закривають.
2. Розрахункова частина
Вихідними даними для розрахунку дробарки являється її годинна продуктивність Q (кг/год). Розрахункова частина курсового проекту буде основана на підрахунках з годинною продуктивністю дробарки Q = 3100 кг/год.
Виходячи з цього, підраховується питома, тобто секундна продуктивність Qc (кг/с):
Qc = Q / 3600. (2.1)
Qc = 3100/3600 = 0,861 кг/с.
Розміри подрібнювальної камери знаходяться з рівняння питомого навантаження на одиницю площі проекції камери:
q' = Qc / L · D; (2.2)
де q' - питоме навантаження на одиницю площі проекції камери. Аналіз технічних показників сучасних молоткових дробарок показує, що при подрібненні фуражного зерна
q' = 2…5 кг / м? · с;
Qc — розрахункова продуктивність дробарки, кг/с;
L — ширина подрібнювальної камери, м;
D — діаметр подрібнювальної камери, м.
Ширина і діаметр подрібнювальної камери знаходяться в заданому співвідношенні між собою:
K = D / L. (2.3)
Для дробарок з периферійною подачею маси рекомендується K = 1…1,7.
При розрахунку одночасно рівнянь (2.2) і (2.3) відносно діаметра (D, м) отримаємо:
D =. (2.4)
D = =0,32 м.
Ширина (L, м) подрібнювальної камери:
L = D / K. (2.5)
L = 0,32 / 1,3 = 0,25 м.
Діаметр (Dp) та довжину (Lp) подрібнювального ротора знаходять з урахуванням радіальних (ДR) та бічних (ДL) зазорів (рис. 2.1) за формулами:
Dp = D — 2ДR
Lp = L — 2ДL (2.6)
Рис. 2.1. Технологічна схема ротора
Величину радіальних зазорів доцільно приймати в зоні ДR = 2…3 мм, мінімально допустиму з конструктивних міркувань; в зоні решіт ДR = 8…12 мм.
При конструюванні дробильного ротора слід прагнути, щоб бічні зазори (між площиною крайніх молотків на осі підвісу і бічний камерою подрібнювача) були більше радіальних:
· в зоні дек: Dp = 0,32 — 2 · 0,003 = 0,314 м; Lp = 0,25 — 2· 0,003 = 0,244 м;
· в зоні решіт: Dp = 0,32 — 2 · 0,01 = 0,3 м; Lp = 0,25 — 2· 0,01 = 0,23 м.
Частота обертання дробильного ротора повинна бути на такому рівні, щоб забезпечити радіальну швидкість молотків м. Остання залежить від виду матеріалу, що переробляється, необхідної крупності продуктів подрібнення і конструктивних особливостей дробарки. У сучасних молоткових дробарках швидкість молотків знаходиться в межах м = 60…105 м / с:
— при подрібненні зерна: м = 60…80 м / с;
— при подрібненні сіна: м = 70…100 м / с.
Приймаємо м = 70 м / с.
Частота обертання дробарки ротора:
(2.7)
де м — швидкість молотків, м/с;
Dp — робочий діаметр ротора, м.
n = 70 / 3,14 • 0,314 = 70,99 с.
Відповідно до теорії ексцентричного удару зусилля не передаватиметься на вісь підвісу молотка при наступній умові:
; (2.8)
де l — відстань від вісі підвісу до кінця молотка, м;
Rn — радіус ротора дробарки по вісям підвісу молотків, м (рис. 2.2).
Рис. 2.2. Схема визначення параметрів молотка Тоді згідно з рис. 2.2:
l = 2 / 13 Dp = 0.15 Dp; (2.9)
l = 0,15 • 300 = 45 мм.
Rn = Rp — l = Dp/2 — l = 105 мм. (2.10)
Довжину (a) і ширину (b) молотків рекомендується знаходити, беручи до уваги такі співвідношення:
а = 1,5 • l = 1,5 •45= 67,5 мм; (2.11)
b = (0,4…0,45)•а = (0,4…0,45)•67,5 = (27…30,4) мм. (2.12)
Приймаємо: a = 67,5 мм; b = 29 мм.
Розміщувати молотки на дробильному роторі можна в шаховому порядку або по гвинтовій лінії. При цьому необхідно, щоб молотки забезпечували рівномірне перекриття по всій ширині камери подрібнення, сприяли рівномірному розподілу матеріалу по її ширині і зберігали умову рівноваги дробильного ротора.
Для розробки схеми розміщення молотків на дробильному роторі виконуємо наступні розрахунки. Залежно від товщини і густоти розміщення молотків визначаємо їх загальну кількість:
(2.13)
де K2 — коефіцієнт густоти розміщення молотків на роторі. При подрібненні сухого зерна і сухих стебел рекомендується приймати:
K2 = 0,5…1,0;
— товщина молотків, = 6 мм.
z = 1 •230 / 6 = 38 шт.
Залежно від числа осей підвісу на роторі визначаємо кількість встановлюваних на одній осі молотків:
(2.14)
де — число вісей подвісу, приймаємо = 4;
Для забезпечення необхідних відстаней між молотками на осях підвісу визначаємо крок гвинтової лінії :
(2.15)
і відстань між сусідніми слідами молотків х:
(2.16)
де — загальна товщина несучих дисків і кронштейнів ротора, які перекриваються молотками. Приймаємо = 20 мм. Товщина решета залежно від виду матеріалу, що переробляється приймається = 2…6 мм.
Продукти подрібнення видаляються з камери через гратчасту поверхню. Тому, чим більше площа останньої, тим вище може бути її пропускна здатність.
Крупність часток, що проходять через отвори решіт, завжди менше їх діаметру. Ставлення розміру часток ц до діаметру отворів решіт do називається коефіцієнтом проходу решіт:
(2.17)
де = 10…20 мм, приймаємо = 14 мм.
На рисунку 2.3 показана схема для визначення діаметра отвору в решеті.
Рисунок 2.3 — Схема визначення діаметра отвору в решеті.
Якщо прийняти дуги аb і bс за прямі лінії, то можна записати наступні рівняння:
(2.18)
(2.19)
де — кут польоту частинок, який залежить від її швидкості, = 40…60, приймаємо = 60.
Діаметр отвору в решеті дорівнює:
(2.20)
Приймаємо .
Сучасні дробарки зазвичай бувають обладнані системою транспортування продуктів подрібнення пневматичним транспортером. До елементів цієї системи належать: вентилятор зі всмоктувальним і нагнітальним трубопроводами, циклон, шлюзовий затвор і зворотний повітропровід.
Розрахунок їх ведеться по витраті повітря, котрий дорівнює:
(2.21)
де — щільність повітря при нормальних умовах, = 1,29 кг/м3;
— коефіцієнт вагової концентрації суміші, який в поживних установках низького і середнього тиску дорівнює: = 0,5…1,0.
м?/с.
Для пневмотранспортування кормових матеріалів застосовують звичайно відцентрові вентилятори. По витраті повітря підбираємо вентилятор № 3 продуктивністю 1552 м3 / ч, ЦП-7−40, ККД = 0,5; = 2840 об / хв.
Діаметр всмоктуючого і нагнітає трубопроводів визначаємо з рівняння:
(2.22)
де — швидкість повітря в трубопроводі, м / с.
Швидкість повітря визначається з умови вилітання часток корму і приймається більше критичної, такою, при якій ще не відбувається завал трубопроводу транспортуються матеріалом:
(2.23)
можна приймати з літератури про аеродинамічні властивості продуктів подрібнення або визначити за емпіричною формулою:
(2.24)
де — середній розмір часток продуктів подрібнення, = 3…5 мм;
— довжина часток = 14 мм;
— вологість продукту, = 30%.
м/с, м/с.
Приймаємо = 6,5 м/с.
.
Нагнітальний трубопровід з'єднується з циклоном за допомогою дифузора, що забезпечує деяке зниження швидкості. Встановлено, що з умов поділу потоку, швидкість повітря на вході в циклон не повинна перевищувати 10…15 м/с. Тому перетин дифузора кілька більше перетину нагнітального трубопроводу:
(2.25)
де — діаметр перетину стінок дифузора у місці приєднання до циклону.
При цьому:
м/с. (2.26)
Приймаємо = 14 м/с.
Якщо прийняти, то
м, м. (2.27)
В циклоні за рахунок розширення швидкість падає і складає 30…40% від. Тоді м/с. Приймаємо =5 м/с.
Діаметр внутрішньої труби циклону визначається:
(2.28)
На рисунку 2.4 зображена схема розрахунку розмірів циклона.
Мінімально допустимі розміри циклона:
(2.29)
(2.30)
(2.31)
(2.32)
(2.33)
(2.34)
Діаметр зворотнього повітропроводу приймаємо рівним діаметру внутрішньої труби циклону Д = 276 мм.
Рисунок 2.4 — Схема до підрахунку розмірів циклона.
Потужність, необхідна для приводу дробарки, визначається з рівняння енергетичного балансу:
(2.35)
де — потужність, споживана завантажувальним пристроєм, Вт;
— потужність на подрібнення матеріалу, Вт;
— потужність на транспортування продуктів подрібнення, Вт;
— потужність приводу шлюзового затвора, Вт.
Залежно від призначення молоткової дробарки її завантажувальний пристрій може бути виконано у вигляді самоточного бункера і у вигляді живильного транспортера. Потужність на привід живильного транспортера розраховуємо за формулою:
(2.36)
де — продуктивність дробарки, т/ч;
— довжина наружної сатини транспортера, =1,5 м;
— висота підйому груза, =6 м;
— коефіцієнт опору руху стрічки транспортера, =0,35;
— вага погонного метру транспортера, = 14 кг/м = 140 Н/м;
— швидкість транспортера, = 1,6 м/с;
— швидкість зерна, яке подаєтся на транспортер, м/с.
З урахування ККД передачі: .
Потужність, споживана на подрібнення матеріалу, що переробляється:
(2.37)
де — питома робота подрібнення, Дж/кг;
(2.38)
де — коефіцієнт, =1,3 Дж/кг;
— ступінь подрібнення, =20.
Дж/кг,
кВт/ч.
3. Монтаж і експлуатація обладнання
Загальні вказівки щодо зберігання і монтажу.
Дробарка надходить до замовника розібраною на вузли, законсервовані й запаковані загальною або місцевою упаковкою на заводі.
Консервація вузлів і деталей дробарки гарантує збереження виробу протягом 12 місяців з дня відвантаження з заводу при умовному зберігання упакованих вузлів і деталей в складських приміщеннях і під навісом.
Монтаж дробарки повинен проводитися кваліфікованими фахівцями, ознайомленими з цією інструкцією.
Знання інструкції персоналом, монтуючими дробарку повинно бути перевірено комісією, призначеною керівником механослужби підприємства, що експлуатує дробарку. Документ, що підтверджує перевірку знань персоналу, монтуючого дробарку, повинен зберігатися у справі машини.
З постачальником можна укласти договір на технічне керівництво монтажем дробарки кваліфікованим шеф-інженером.
За умови дотримання цієї інструкції, а також правил приймання, зберігання та переконсервації вузлів і деталей дробарки на складі, завод протягом гарантійного строку, безоплатно замінює або ремонтує вишедші з ладу деталі, крім броні, а також поставлених з дробаркою в якості запасних частин втулок ексцентрика, і шестерні приводного валу.
Перед монтажем дробарки необхідно ретельно оглянути всі вузли, зняти з них консерваційне покриття, переконатися, що всі сполучені поверхні і різьби не отримали ушкоджень у дорозі, а якщо такі пошкодження є, усунути їх, перевірити міцність кріплення нерухомих з'єднань.
Рухливі з'єднання, такі як підшипники приводного вала, сферичний підп'ятник, диски підп'ятника ексцентрика слід обов’язково розібрати, особливо ретельно очистити від консерваційного покриттів, оглянути тертьові поверхні та усунути пошкодження, одержувані при реконсервації і транспортуванні.
При складанні вузлів перед монтажем необхідно рухомі поверхні змастити рідким мастилом, а нерухомі сполучені поверхні - консистентним мастилом. Всі отвори повинні бути ретельно очищені і продути стисненим повітрям. Під час складання ретельно стежити, щоб на поверхні, що труться та посадкові поверхні не потрапив пил або бруд, не застосовувати брудні обтиральні матеріали та матеріали, що залишають ворсинки, нитки, шматки на робочих поверхнях.
Для змащення користуватися тільки чистими маслами і консистентними мастилами. Небезпечні щодо забруднення місця перекривати щитами або брезентами навіть при тривалих зупинках монтажних робіт.
Кожна дробарка проходить на заводі контрольну збірку і випробування на холостому ходу. Тому, як правило, при кваліфікованому монтажі ніяких додаткових припасувань деталей не потрібно.
Необхідно лише простежити, щоб всі регулювальні прокладки, на яких дробарка проходив обкатку, були встановлені при монтажі. Регулювальні прокладки передбачені під нижнім диском підп'ятника ексцентрика і між патрубком станини і фланцем корпусу приводного валу.
Особливу увагу слід приділити регулюванню прокладок під ексцентрик, на яких не допускається загини, пом’ятості та інші дефекти поверхні, що з’явилися при транспортуванні. Установка прокладок з дефектами поверхні викличе перекіс ексцентрикового вузла і його неправильну роботу.
4. Охорона праці
4.1 Загальні положення
Мета впровадження системи управління охороною праці (УОП) — це всебічне сприяння виконанню вимог, які повністю ліквідують, нейтралізують або знижують до допустимих норм вплив на працюючих небезпечних та шкідливих факторів виробничого середовища, забезпечують усунення джерел небезпеки, ізолювання від них персоналу, використання засобів, що усувають небезпечні ситуації та підвищують технічну безпеку, створюють надійні санітарно-гігієнічні та ергономічні умови. УОП передбачає встановлення конкретних кількісних показників діяльності виробничих підрозділів, підтримування котрих в заданих межах забезпечує досягнення основної мети щодо організації безпечних та нешкідливих умов праці.
Власник зобов’язаний створити в кожному структурному підрозділі і на робочому місці умови праці відповідно до вимог нормативних актів, а також забезпечити дотримання прав працівників, гарантованих законодавством про охорону праці.
З цією метою власник забезпечує функціонування системи управління охороною праці, для чого:
* створює відповідні служби і призначає посадових осіб, які забезпечують вирішення конкретних питань охорони праці, затверджує інструкції про їх обов’язки, права та відповідальність за виконання покладених на них функцій;
* розробляє за участю профспілок і реалізує комплексні заходи для досягнення встановлених нормативів з охорони праці, впроваджує професійні технології, досягнення науки і техніки, засоби механізації та автоматизації виробництва, вимоги ергономіки, позитивний досвід з охорони праці, тощо;
* забезпечує усунення причин, що призводять до нещасних випадків, професійних захворювань і виконання профілактичних заходів, визначених комісіями за підсумками розслідування цих причин;
* організовує проведення лабораторних досліджень умов праці, атестації робочих місць на відповідність нормативним актам про охорону праці в порядку і строки, що встановлюються законодавством, вживає за їх підсумками заходів щодо усунення небезпечних і шкідливих для здоров’я виробничих факторів;
* розробляє і затверджує положення, інструкції, інші нормативні акти про охорону праці, що діють у межах підприємства та встановлюють правила виконання робіт і поведінки працівників на території підприємства, у виробничих приміщеннях, на будівельних майданчиках, робочих місцях відповідно до державних міжгалузевих та галузевих нормативних актів про охорону праці, забезпечує безкоштовно працівників нормативними актами про охорону праці;
* здійснює постійний контроль за дотриманням працівниками технологічних процесів, правил поводження з машинами, механізмами, устаткуванням та іншими засобами виробництва, використанням засобів колективного та індивідуального захисту, виконанням робіт відповідно до вимог щодо охорони праці;
* організовує пропаганду безпечних методів праці та співробітництво з працівниками в галузі, охорони праці.
У випадку відсутності в нормативних актах про охорону праці вимог, які необхідно виконати для забезпечення безпечних і нешкідливих умов праці на певних роботах, власник зобов’язаний вжити погоджених з органами державного нагляду заходів, що забезпечують безпеку працівників.
У разі виникнення на підприємстві надзвичайних ситуацій і нещасних випадків власник зобов’язаний ужити термінових заходів для допомоги потерпілим, залучити при необхідності аварійно-рятувальні формування.
Система цілей УОП — багаторівневий комплекс, який, у свою чергу, визначає цілі для різних рівнів управління охороною праці з врахуванням стадій виробничого циклу.
На рівні галузі встановлюються цілі стратегічного характеру щодо прийняття довготермінових планів наукового, технічного, економічного та соціального розвитку об'єктів (умов та безпеки праці) на підставі довготривалих прогнозів і програм розвитку.
На рівні виробничих об'єднань та підприємств визначаються цілі тактичного характеру: установлення складу та структури підрозділів, методів взаємодії, аналіз рівня безпеки праці стимулювання. З переходом на госпрозрахунок та самофінансування виробничі об'єднання та підприємства повинні ставити стратегічні цілі.
На рівні цехів і дільниць встановлюються цілі оперативного характеру: послідовність оперативного виконання окремих функцій тощо.
Окремі виконавці, що впливають на умови праці, організаційно та технічно забезпечують їх оптимізацію і цілі безпеки праці.
Основні завдання, вирішення яких забезпечує досягнення цілей УОП на різних рівнях управління і стадіях організаційно-виробничої діяльності, полягають у виконанні комплексу послідовних взаємопов'язаних дій щодо попередження травматизму та виробниче зумовлених захворювань.
Вирішення задач управління охороною праці має бути забезпечене взаємодією усіх структурних підрозділів, служб і фахівців, які визначаються керівником підприємства. Функції структурних підрозділів і служб, посадові обов’язки керівних та інженерно-технічних працівників щодо виконання задач управління охороною праці встановлюються на місцях на всіх рівнях, виходячи з структури, штатів і конкретних умов діяльності установи (підприємства).
4.2 Безпека експлуатації обладнання
Для безпечної експлуатації дробарок слід дотримуватись правил, описаних в пункті 3 — «Монтаж та експлуатація обладнання», а також своєчасно проводити технічне обслуговування, дотримуючись таких правил, як:
1. Технічне обслуговування дробарки проводиться тільки підготовленим обслуговуючим персоналом.
2. Технічне обслуговування дробарки полягає в регулярному спостереженні за її роботою, періодичній заміні швидкозношуваних деталей (молотків), періодичної заміни (добавці) мастила в підшипниковому вузлі.
3. При технічному обслуговуванні необхідно перевіряти стан кріпильних вузлів. Це досягається шляхом огляду, підтягування ослаблених з'єднань і встановлення нових кріпильних деталей замість пришедших у непридатність.
4. Підшипникові вузли при огляді за зовнішнім виглядом, шуму, температурі нагріву, зміні кольору мастила, визначають стан самих підшипників, а також посадок їх кілець. При необхідності проводиться заміна підшипників та їх змазка.
5. Роботу дробарки можна продовжувати до повного зносу і виходу з ладу окремих вузлів.
6. Необхідність заміни молотків дробарки визначається за крупності дробленого матеріалу. Показником зносу (абразивного стирання) молотків є збільшення крупності подробленного матеріалу.
7. Технічне обслуговування електрообладнання дробарки повинен здійснювати електротехнічний персонал. Обслуговування повинно виконуватися в строгій відповідності з «Правилами улаштування електроустановок», «Правилами технічної експлуатації електроустановок споживачів» і «Правилами техніки безпеки при експлуатації електроустановок споживачів».
Висновки
кормодробарка обладнання технічний
Сільськогосподарські переробні виробництва є важливою ланкою народного господарства, які забезпечують своєчасну переробку рослинної і тваринної продукції безпосередньо на місцях їх одержання, тобто в умовах виробника. Швидкими темпами мають впроваджуватися та використовуватися найновіші науково-технічні розробки.
Одним із важливих механічних процесів є процес подрібнення. Подрібнення — процес руйнування твердого матеріалу під дією зовнішніх сил. Процеси подрібнення широко використовуються в цукровому, борошно-круп`яному, хлібопекарському, м`ясопереробному, спиртовому, пивоварному та інших виробництвах.
У переробних виробництвах застосовують молоткові дробарки з шарнірно підвішеними молотками. Такі дробарки призначені для подрібнення зерна та інших сухих крихких матеріалів.
Курсовий проект було розраховано з урахування годинної продуктивності дробарки 3,1 т.
Використані джерела
1. Гулий І.С., Пушанко Н. Н. Обладнання виробництв переробної та харчової промисловості. Вінниця, «Нова книга». 2001.-486 с.
2. І.Ф. Малежик, П. С. Циганко. Процеси і апарати харчових виробництв.-К.:НУХТ, 2003.-400 с.
3. Антіпов С.Т., Крєтов І.Т. Машини та апарати харчових виробництв. Кн1 — М.: Вища школа, 2001 — 680 с.
4. Кавецький Г. Д., Процеси та апарати харчової технології. М.: Колос, 2000 — 551 с.