Добування вольфраму з оксид вольфраму
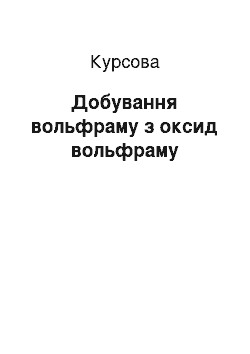
Рис. Петлева сушарка (в) і елемент сітчастої стрічки (б):1 — живильник вологого матеріалу; 2 — обігріваючі валки, для вдавлення матеріалу в сітку; 3 — нескінченна сітчаста стрічка; 4 — ланцюговий конвеєр для пересування петель сітчастої стрічки; 5 — ударний механізм; б — бункер зі шнеком У петлевих сушарках сушіння відбувається в шарі невеликої товщини (рівній товщині ланок стрічки, що становить… Читати ще >
Добування вольфраму з оксид вольфраму (реферат, курсова, диплом, контрольна)
ЗМІСТ
Вступ
1. Обгрунтування технології виробництва порошку вольфраму
1.1 Короткі відомості
1.2 Сировина для одержання вольфраму і методи його переробки
1.3 Розкладання вольфрамовмісних концентратів
1.4 Переробка розчинів вольфрамату натрію на вольфрамовий ангідрид
1.5 Відновлення вольфраму
2. Вибір і розрахунки обладнання
3. Аппаратурно-технологічне устаткування
4. Охорона праці
4.1 Загальна характеристика умов технологічного процесу
4.2 Характеристика речовин та матеріалів виробництва
4.3 Промислова санітарія
4.4.Пожежна безпека
5. Техніко-економічне обґрунтування
5.1 Розрахунок виробничої потужності проектованої дільниці
5.2 Розрахунок вартості і потреби сировини та матеріалів
5.3 Розрахунок амортизаційних відрахувань
5.4 Розрахунок витрат на оплату праці
5.5 Розрахунок річного фонду оплати праці керівників, спеціалістів, службовців і МОП
5.6 Розрахунок витрат по утриманню і експлуатації устаткування
5.7 Розрахунок загальновиробничих витрат
5.8 Калькуляція собівартості продукту
Висновок
Перелік використаних джерел
ВСТУП
Роль рідкісних металів в сучасній техніці усе більш зростає. Рідкісні метали значною мірою визначають розвиток таких важливих галузей промисловості, як виробництво спеціальних сталей, твердих і жароміцних сплавів, електротехніки, електровакуумної техніки і ряду галузей нової техніки. За останні десятиліття нові метали увійшли до орбіти промислового використання, зросли масштаби і розширилася номенклатура продуктів виробництв рідкісних металів.
Розсіяні рідкісні метали зустрічаються зазвичай у вигляді ізоморфних домішок в нікчемних концентраціях в кристалах інших мінералів. Тому рентабельне добування розсіяних рідкісних металів можливе тільки з відходів виробництв основних металів. Потрібно також враховувати і технологічні труднощі добування їх з сировини.
Роль в сучасній техніці вольфраму — самого тугоплавкого металу — дуже велика. Виробництво електронних та електроосвітлювальних приладів, легованих сталей, жароміцних сплавів для нових галузей техніки, зносостійких та інструментальних твердих сплавів — далеко не повний перелік областей його використання.
За останнє десятиліття в зв’язку з розширенням областей застосування та масштабів виробництва вольфраму, його сплавів і з'єднань, підвищенням вимог до якості виробів із цього металу виконані нові дослідження наукового і технологічного плану.
Метою даної роботи є розробка технології добування заданого об'єму виробництва вольфраму з триоксид вольфраму.
1. ОБГРУНТУВАННЯ ТЕХНОЛОГІЇ ВИРОБНИЦТВА ПОРОШКУ ВОЛЬФРАМУ
1.1 Короткі відомості
Вольфрам як елемент був відкритий в 1781 р., а через два роки з руди вперше була виділена вольфрамова кислота і отримано порошок вольфраму. З кінця XIX ст. вольфрам почали широко використовувати як легуючої добавки до вольфрамовим сталям.
З 1900 р. з моменту винаходу швидкорізальних сталей вольфрам став одним з найважливіших легуючих елементів, і його виробництво почало інтенсивно розвиватися. У 1900 р. російський винахідник А. Н. Лодигін запропонував і вперше здійснив застосування вольфраму для виготовлення ниток розжарювання в електричних лампочках. З 1927 р. вольфрам у вигляді карбіду почали використовувати в виробництві твердих сплавів, що грають важливу роль в сучасної техніки в якості матеріалу для виготовлення ріжучого інструменту.
Вольфрам в періодичній системі елементів Д. І. Менделєєва знаходиться в VI групі 6-го періоду під номером 74. Атомна маса вольфраму 183,92. Його щільність при кімнатній температурі 19 300 кг/м3.
Вольфрам є тугоплавким металом (tпл = 3395 + 15 ° С), поступаючись за цим параметром тільки вуглецю. Металл відрізняється дуже високою точкою кипіння (> 5500 ° С) і дуже малою швидкістю випаровування навіть при температурі 2000 ° С. Електропровідність вольфраму майже в три рази нижче електропровідності міді.
За зовнішнім виглядом компактний вольфрам схожий на сталь. Він є найбільш міцним з відомих металлов і зберігає свою міцність при високих температурах. Механічній обробці (куванні, прокатці і волочіння) вольфрам піддається тільки при нагріванні.
У звичайних умовах вольфрам дуже стійкий метал, але при нагріванні на повітрі до 400−500 °С окислюється з утворенням WO3, здатної з основними оксидами утворювати вольфрамати MeWO4. Крім WO3, відомі три інших оксиду: WO2 і проміжні WO2.72 і WO2.90.
Пари води інтенсивно окислюють вольфрам при температурі вище 600 °C з утворенням WO3 та WO2. З галоїдами при нагріванні він може з'єднуватися безпосередньо з утворенням сполук WCl6, WO2Cl2 та WOCl4. З воднем вольфрам не взаємодіє аж до температури плавлення.
У присутності повітря або інших окислювачів вольфрам розчиняється в розплавлених лугах, утворюючи вольфраматом, і роз'їдається гарячими водними розчинами лугів. Вольфрам слабо піддається дії кислот і царської горілки, але швидко розчиняється в суміші плавикової та азотної кислот.
В даний час вольфрам знаходить широке і багатоаспектне застосування в чистому вигляді і в ряді сплавів. У різних областях техніки використовують деякі хімічні сполуки вольфраму.
У чистому вигляді вольфрам у вигляді дроту, стрічки і різних деталей застосовують в електротехнічній і радіоелектронної промисловості, де використовують низьку пружність його парів при високих робочих температурах (2200−2500 ° С). Його застосовують для виготовлення ниток розжарювання в електролампа, катодів, підігрівачів і контактів в радіоелектронних приладах, рентгенівських і газорозрядних трубках. Вольфрамові нитки діаметром 0,018 мм внаслідок їх високої пружності є матеріалом для виготовлення підвісок рухомих котушок в гальванометра та інших подібних їм приладах.
Вольфрамові дріт, трубки і прутки використовують для виготовлення елементів опору в нагрівальних печах, що працюють в атмосфері водню, нейтрального газу або у вакуумі при температурах до 3000 ° С.
Ще ширше вольфрам застосовують у вигляді сплавів і в першу чергу при виробництві спеціальних сталей. На їх виготовлення витрачається до 50% вольфрамових концентратів.
Найбільш важливими вольфрамсодержащімі сталями є швидкорізальні (8−20% W), інструментальні (1−6% W і 0,4−2% Сг), магнітні (5−9% W і 30 — 40% Со). Тверді сплави на основі карбіду вольфраму WC мають високу твердість, зносостійкість і тугоплавкостью. На основі карбіду створені найпродуктивніші інструментальні сплави (85−95% WC та 5 — 10% Со). Ряд твердих сплавів містить, окрім WC, карбіду титану, танталу і ніобію. Такі металокерамічні сплави отримують методами порошкової металургії.
Особливе значення тверді сплави на основі карбіду вольфраму придбали при виготовленні ріжучих і бурових інструментів і фільєр для волочіння дроту. Знаходять застосування також литі карбіди вольфраму.
До поширених жароміцним і зносостійким сплавів відносяться сплави вольфраму з кобальтом і хромом — стелліти. Їх застосовують головним чином для покриттів швидкозношуваних деталей, наприклад клапанів двигунів для літаків, лопатей турбін, штампів та ін.
Сплави вольфраму з міддю і сріблом використовують для виготовлення контактів в рубильниках, вимикачах і електродах точкового зварювання.
Рис. Структура шеєліта
1.2 Сировина для одержання вольфраму і методи його переробки
Відомо близько 15 мінералів вольфраму, що представляють, є солі вольфрамової кислоти. З них тільки Два — вольфраму (Ре, Мп) W04 і шеєліт CaWO4 — мають промислове значення. Вольфраму є ізоморфної сумішшю вольфраматів заліза і марганцю змінного складу. Найбільш багаті вольфрамові руди містять зазвичай 0,2−2% W. У рудах вольфраму часто супроводжують молібденіт MoS2, каситерит SnO2, пірит, халькопірит та інші мінерали. Найбільш часто вольфрамит зустрічається разом з касситеритом.
Вольфрамові руди обов’язково збагачують. При їх збагаченні виникають значні труднощі, обумовлені складністю і різноманітністю складу руд, низьким вмістом вольфраму, високими вимогами до складу концентратів і необхідністю комплексної переробки рудної сировини.
Для збагачення вольфрамових руд застосовують гравітацію і флотацію, магнітну і електростатичну сепарацію. Вольфраму флотірующій значно гірше шеєліту. З цієї причини основним способом збагачення воль-фрамітових руд є гравітація.
Відділення слабомагнітних вольфраміту від немагнітного каситериту успішно проводиться електромагнітної сепарацією. Основним методом збагачення руд є флотація шеелітових.
При збагаченні вольфрамових руд отримують концентрати з вмістом 55−65% WO3. Склад і якість таких концентратів регламентуються ГОСТ 213–2002, який передбачає утримання WO3 в концентратах 1-го сорту не нижче 65%. У вольфрамових концентратах обмежується вміст фосфору, сірки, миш’яку, олова, міді, сурми і вісмуту.
Для додаткового видалення домішок вольфрамові концентрати піддають доведенні шляхом окислювального випалювання або обробкою кислотами. При випаленні видаляють сірку і миш’як, а кислотної обробкою очищають від фосфору, молібдену, заліза та інших домішок.
Безпосередня переробка вольфрамових концентратів, крім виплавки ферровольфрама для потреб чорної металургії, закінчується отриманням трехокиси вольфраму WO3, яка служить вихідною сировиною для виробництва металевого вольфраму або його карбіду.
Всі використовувані в промисловості способи переробки вольфрамових концентратів включають такі основні технологічні стадії: 1) розтин (розкладання) концентратів; 2) вилуговування сплаву або спека; 3) очищення розчинів вольфрамату натрію від домішок; 4) отримання технічної вольфрамової кислоти; 5) очистку технічної вольфрамової кислоти; 6) отримання вольфрамового ангідриду (трехокиси вольфраму).
Реальні технологічні схеми отримання вольфрамового ангідриду WO3 відрізняються один від одного тільки способами отримання вольфрамової кислоти. В даний час для розтину вольфрамових концентратів в залежності від виду сировини та масштабів виробництва застосовують лужну або кислотну обробку. Найбільшого поширення в сучасній вольфрамової промисловості одержали лужні способи. Кислотне розкладання успішно застосовують тільки для розкладання шеелітових концентратів.
1.3 Розкладання вольфрамсодержащіх концентратів
Переробка вольфрамсодержащіх концентратів починається з їх розкладу. Найбільш поширене розкладання спіканням або сплавом з содою, засноване на реакціях утворення водорозчинних вольфраматів натрію.
При розкладанні вольфрамітових концентратів спека ням або сплавом з водою протікають такі основні реакції:
2FeWO4 + 2Na2CO3 + ½O2 = 2Na2W04 + Fe2O3 +2CO2;
3MnWO4 + 3Na2CO3 + ½O2 = 3Na2WO4 + Mn3O4 + 3C02.
Звичайні домішки в вольфрамітових концентраті при взаємодії з содою утворюють розчинні у воді натрієві солі Na2Si03, Na3P04, Na3As04 и Na2Mo04
Розкладання вольфрамітових концентратів проводять при 800−1000 °С. Залежно від температури реакційна маса являє собою полурасплавленную масу (спек) або рідкотекучий розплав (плав). Шихта для спікання вольфраміту включає концентрат, соду і іноді селітру. Соду вводять з надлишком 10−15% від теоретично необхідної кількості, що забезпечує розкладання вольфраміту на 98−95%. Добавка селітри в кількості 1−4% від маси концентрату дозволяє прискорити окислення заліза і марганцю.
Для спікання вольфрамітових концентратів в безперервному режимі використовують трубчасті обертові печі довжиною до 20 м і діаметром близько 2,2 м. Спек при виході з печі пропускають через валкові дробарки і потім подрібнюють в млинах мокрого розмелювання, пульпу яких направляють на вилуговування.
Для розкриття високосортних вольфрамітових концентратів (60−70% WO3) можна використовувати їх обробку розчинами їдкого натра, при якій утворюється вольфра-мат натрію і гидроксид заліза (II) і марганцю:
MeWO4 + 2NaОН = Na2WO4 + Ме (ОН)2.
Недоліки способу зводяться до отримання забруднених розчинів і труднофільтруемих опадів. Шеелітовие концентрати розчинами рідкого їдкого натра не розкладаються. Їх розкладання можна здійснити спіканням з содою, обробкою содовими розчинами в автоклавах або кислотним способом — обробкою соляною кислотою.
При спіканні шеелітових концентратів з содою поряд з вольфрамату натрію утворюються СаСОз або СаО. При подальшому вилуговуванні водою гідроксид кальцію здатний перекладати вольфрам у форму нерозчинного у воді вольфраміту кальцію за реакцією:
Na2WO4 + Са (ОН)2 — СаWO4 + 2NaОН.
Це значно знижує витяг вольфраму в розчин.
З метою запобігання утворення вільного оксиду кальцію в шихту спікання шеелітових концентратів вводять кварцовий пісок з метою переведення кальцію важкорозчиний силікат:
2СаWO4 + 2Na2С03 + SiO2 = 2Na2W04+Са2SiO4 + 2С02.
Процес спікання ведуть в трубчастих обертових пе чах зі значним надлишком соди (50−100%).
Автоклавної-содовий процес для розтину шеелітових концентратів був розроблений у Радянському. Цей спосіб полягає в обробці шеєліту содовим розчином при 225 -, 250 ° С і тиску 2,5−2,7 МПа в автоклавах з механічним перемішуванням і з перемішуванням парою. У розчин переходить 98−99% вольфраму. Розчини містять, г / л: 80−100 W03; 5−8 Mo; 80−90 Na2C03. При подальшій обробці таких розчинів виділяють вольфрамати натрію і молібденовий концентрат.
Безпосереднє розкладання шеелітових концентратів кислотним способом полягає в обробці вихідного матеріалу концентрованої соляної кислотою з одержанням відразу технічної вольфрамової кислоти, що є найважливішою перевагою методу. Розкладання шеєліту за цим способом протікає практично по незворотною реакції CaW04 + 2HCl > H2W04 + CaCl2.
Процес ведуть в футерованих залізних чанах при 90−100 ° С протягом 6−8 год з надлишком кислоти 150 — 200% проти теоретично необхідного.
Спік або плав, що містить вольфрамати натрію, витравлюють гарячою водою (70−90 ° С) з метою переведення в розчин Na2W04. Вилуговування проводять у нагрітих чанах з механічним перемішуванням. Розчини відокремлюють від кеков фільтруванням.
1.4 Переробка розчинів вольфрамату натрію на вольфрамовий ангідрид
Кінцевою метою переробки розчинів вольфрамату натрію є отримання вольфрамового ангідриду W03 з сумарним вмістом домішок не більше 0,05−0,1%, придатного для виробництва металевого вольфраму або його карбід.
Отримання WO3 необхідної чистоти зазвичай здійснюється ється за складною многостадийной технології, що включає наступні процеси: 1) очищення розчинів вольфрамату натрію від домішок; 2) осадження вольфрамату кальцію (штучного шеєліту); 3) розкладання CaW04 кислотами з отриманням технічної вольфрамової кислоти; 4) розчинення вольфрамової кислоти в аміачної води; 5) виділення з розчину паравольфрамата амонію; 6) отримання W03 прожарюванням паравольфрамата амонію або вольфрамової кислоти.
Вихідні розчини вольфрамату натрію, отримані при вилуговування спек або плавів, а також автоклавно-содовим процесом, містять 80−150 г / л W03. Домішками вольфраматних розчинів є в основному розчинні натрієві солі кислот кремнію, фосфору, миш’яку, молібдену та сірки. Попереднє очищення розчинів від домішок дозволяє одержати вольфрамову кислоту достатньою мірою чистоти.
Очищення від кремнію заснована на осадженні кремнієвої кислоти при рН = 9−8 в результаті гідролізу силікату натрію по реакції:
Na2SiO3 + Н20 — H2Si03 + 2NaOH.
При кип’ятінні розчину кремнієва кислота коагулює і випадає в осад. Для нейтралізації лужних розчинів застосовують соляну кислоту. Осадження кремнієвої кислоти проводять у механічних мішалках з паровим обігрівом. Розчини після нейтралізації кип’ятять і тривало відстоюють. Освітлений розчин відокремлюють від осаду декантацією або фільтруванням.
Очищення від фосфору і миш’яку виробляють шляхом їх виділення з розчину у вигляді фосфатів і арсенатів магнію. Найбільшою ефективністю відрізняється амонійно-маг-ніевая очищення, спрямована на осадження з розчину малорозчинних солей, по реакціях:
Na2HP04 + MgCl2 + NH4OH = Mg (NH4)P04 + 2NaCl + H20;
Na2HAs04 + MgCl2 + NH4OH = Mg (NH4)As04 + 2NaCl +. H20.
Для зменшення розчинності утворюються солей і запобігання гідролізу вводять надлишок іонів Mg2+ та (NH4)+. Після тривалого відстоювання з розчинів випадає кристалічний осад амонійно-магнієвих солей.
Очищення від молібдену як самостійну стадію проводять тільки при його високому вмісті (> 0,3 г / л). Якщо молібдену в розчинах більше 8−10 г / л, то важливе значення набуває його виділення у вигляді сульфіду в молібденовий хімічний концентрат.
В основі очищення розчинів вольфрамату натрію від молібдену лежить відмінність умов утворення сульфосолей молібдену і вольфраму. При добавці строго обмеженої кількості сульфіду натрію в вольфраматний розчин і одночасному його підкисленні соляною кислотою переважно утворюється Nа2МоS4, який руйнується надалі з виділенням в осад малорозчинного сульфіду молібдену:
Nа2МоS4+НС1=МоS3+2NaCl +Н2S
Ступінь осадження молібдену не нижче 98%.
Очищений від домішок розчин вольфрамату натрію направляють на осадження кристалічної вольфрамової кислоти Н2WO4, яка може бути отримана безпосереднім осадженням або шляхом осадження вольфрамату кальцію з наступним його розкладанням.
Пряме осадження Н2WO4 є технологічно простішим способом. Необхідно тільки підкислити розчин вольфрамату натрію соляною кислотою, що викличе випадання в осад вольфрамової кислоти по реакції:
Na2WO4 + 2НС1 = 2NaС1 + Н2WО4.
Однак безпосереднє отримання вольфрамової кислоти пов’язано з утворенням труднофільтруемих колоїдних опадів.
Більш поширеним способом виділення вольфраму з розчинів є попереднє осадження вольфрамату кальцію СаW04, який внаслідок малої розчинності у воді дозволяє отримувати грубозернисті опади з досить високим витяганням вольфраму з розчину.
Вольфрамати кальцію (штучний шеєліт) зазвичай беруть в облогу водним розчином хлористого кальцію, який додається в розчин вольфрамату натрію. При цьому утворюється легко відстоює кристалічний осад шеєліту:
Na2WO4 + СаС12 = СаWO4 + 2NaС1.
Повнота осадження СаWO4 залежить від складу розчину. Рекомендується вести осадження з нагрітих до кипіння розчинів при вмісті в них 120−130 г/л WO3 і 0,3−0,7 г/л лугу. З розчину осідає 99 — 99,5% вольфраму. Відмитий гарячою водою осад вольфрамату кальцію у вигляді пасти або пульпи розкладають гарячої соляною кислотою:
СаWO4 + 2НСl > Н2WO4 + СаСl2.
Висока кислотність пульпи забезпечує додаткове очищення розчинів від фосфору, миш’яку і частково молібдену.
Розкладання СаWO4 проводять в сталевих реакторах, футерованих кислототривкої плиткою або гумованих гумою і забезпечених гумованої мішалкою. Обложену вольфрамову кислоту промивають на фільтрі. Відфільтрована і висушена вольфрамова кислота містить зазвичай 0,2−0,3% домішок.
Шеелітовие концентрати порівняно легко розкладаються концентрованими розчинами соляної кислоти при 90−100 ° С з отриманням відразу технічної вольфрамової кислоти, минаючи стадію перекладу вольфраму в розчин у вигляді вольфрамату натрію за вказаною вище реакції. Кислотний спосіб відрізняється від лужного меншим числом технологічних операцій. Однак його застосування стає найбільш ефективним при переробці багатих (до 75% W03) і чистих шеелітових концентратів. При кислотному розкладанні значно забруднених концентратів спосіб стає неекономічним через необхідність двоабо триразової перечісткі вольфрамової кислоти.
Кислотне розкладання природного шеєліту особливо цікаво для розкладання концентратів з високим вмістом молібдену. При достатньому надлишку соляної кислоти велика частина молібдену переходить в розчин, а вольфрамова кислота осаджується. Технічна вольфрамова кислота, особливо отримана кислотним способом, містить до 1,5−3% домішок у вигляді кремнієвої кислоти, солей натрію і кальцію, молібденової кислоти та ін.
Для очищення технічної вольфрамової кислоти від домішок її розчиняють у воді аміачної з перекладом вольфрамату в розчин у формі вольфрамату амонію:
Na2W04 + 2NH4OH = (NH4)2W04 + 2Н20.
При цьому велика частина домішок залишається в осаді.
Розчинення технічної вольфрамової кислоти роблять у фарфорових або гумованих залізних чанах з мішалками. У чани подають 25%-ний розчин аміаку, що відповідає витраті 115 л аміаку щільністю 0,91 г/м3; на 100 кг W03.
Розчин (NH4) 2W04 після тривалого відстоювання (8−12 год) відокремлюють від осаду декантацією і направляють на виділення з неї вольфраму, який можна брати в облогу у вигляді чистої вольфрамової кислоти або паравольфрамата амонію. Осадження вольфрамової кислоти здійснюють аналогічно її виділення з розчинів вольфрамату натрію.
Для виділення з аміачних розчинів паравольфрамата, що забезпечує більш повне очищення від домішок, застосовують методи випарювання і нейтралізації.
При випаровуванні з розчину видаляється частина аміаку з скороченням об'єму розчину приблизно в п’ять разів. В результаті випаровування утворюється паравольфрамат амонію 5(NН4)20 Ч 12WO3 Ч 5Н20, пластинчасті кристали якого випадають при наступному охолодженні розчину. Кристали зневоднюють на фільтрі, потім на центрифузі, промивають водою і сушать.
При випаровуванні необхідно забезпечити переведення в па-равольфрамат не більше 80% вольфраму. Це запобігає його забруднення домішками; залишки вольфраму зі збагаченого домішками розчину беруть в облогу у вигляді Н2WO4 або СаWO4, які повертають в попередні переділи.
Випарювання проводять в апаратах періодичної або безперервної дії. Виділилися пари аміаку вловлюють в скрубері з отриманням аміачної води, що використовується для розчинення вольфрамової кислоти. Отримані в результаті дворазової аміачної обробки кислоти кристали паравольфрамата амонію містять сумарною близько 0,04% домішок.
При виділенні вольфраму нейтралізацією розчинів виділяються кристали паравольфрамата амонію голчастою модифікації (з 11 молекулами Н20) за сумарною реакції:
12(NH4)2WO4 +14НСl + 11Н2О = 5(NН4)2O * 12WO3 *11Н2О + 14NH4Cl.
Нейтралізацію проводять повільним обережним додаванням до вихідного холодного розчину соляної кислоти. Після довготривалого відстоювання (до 24 год) у вигляді кристалів паравольфрамата виділяється 85—90% W.
Спосіб нейтралізації не дозволяє регенерувати аміак і вимагає витрат чистої соляної кислоти.
Для виробництва металевого вольфраму або твердих сплавів на його основі потрібно вольфрамовий ангідрид WО3. Для його отримання вольфрамову кислоту або паравольфрамат амонію прожарюють в трубчастих обертових печах з електричним обігрівом при 500 — 850 ° С. Температуру вибирають залежно від виду прожарюємо матеріалу і необхідної крупності (зернистості) одержуваного ангідриду.
Процес прожарювання вольфрамової кислоти або па-равольфрамата амонію описується наступними реакціями:
H2WO4 > WO3 + H2O;
5(NH4)2O Ч 12WO3 Ч nH2O = 12WO3 + 10NH3 + (n+5)H2O.
Продукт прожарювання повинен містити не менш 99,9−99,95% WO3, склад якого регламентується технічними умовами.
1.5 Відновлення вольфраму
Відомі такі способи отримання вольфраму з його сполук: 1) відновлення трехокиси вольфраму воднем; 2) відновлення трехокиси вольфраму або вольфраматів (СаW04 тощо) вуглецем; 3) відновлення галогенідів (WF6, WCl6) воднем; 4) металотермічним відновлення оксидів або вольфраматів (магнієм, алюмінієм та ін); 5) термічна дисоціація карбонила вольфраму; 6) електролітичне отримання вольфраму в розплавлених середовищах.
Найбільш поширений в промисловій практиці спосіб відновлення WO3 воднем. Отримується в результаті відновлення порошкоподібний вольфрам використовують для виробництва компактного металу, отримання карбіду вольфраму і ряду сплавів. Порошок вольфраму, відновлені з вуглецем, непридатні для виробництва пластичного вольфраму, так як вони містять включення його карбідів, що призводить до крихкості і погіршення оброблюваності заготовок. Порошок вуглецевого відновлення іноді використовують у виробництві твердих сплавів (для отримання карбіду вольфраму), однак і в цій галузі вважають за краще застосовувати вольфрам водневого відновлення. Розроблено і починають застосовуватися методи отримання порошків вольфраму відновленням воднем парів галогенідів. Отримані при цьому порошки з різною крупністю частинок (тонкодисперсні або великі сферичні порошки) відрізняються високою чистотою, зокрема низьким вмістом кисню.
Метод термічної дисоціації карбоніла, а також відновлення галогенідів воднем використовуються для отримання вольфрамових покриттів на інших металах, графіті або виробах з кераміки. Металотермічним способи набули поширення переважно у виробництві ферровольфрама. Електролітичні способи одержання вольфраму неодноразово досліджувалися і продовжують вивчатися. Однак вони в даний час ще не знайшли практичного застосування.
Отримання компактного вольфраму плавкою внаслідок високої температури його плавлення представляло значні технічні труднощі і стало можливим тільки завдяки освоєнню сучасних методів вакуумної плавки (дугового, електронно-променевої, плазмової та ін.) До теперішнього часу вольфрам в основному отримують з його сполук у вигляді порошку, який потім перетворюють на компактний метал методом порошкової металургії.
Порошкоподібний вольфрам можна отримати відновленням його сполук, головним чином W03, різними відновниками. Найбільшого поширення в промисловій практиці отримав метод відновлення WО3 воднем. Відновлення вуглецем призводить до насичення WO3 карбідами, що надає металу крихкість і погіршує оброблюваність заготовок.
До якості виходять при відновленні вольфрамового ангідриду порошків, крім їхньої високої чистоти, пред’являються також вимоги до розміру і формі зерен і їх гранулометричним складом. Від цих характеристик порошків в значній мірі залежать результати подальшого їх перетворення в компактний метал.
Відновлення вольфрамового ангідриду воднем описується наступною сумарною реакцією:
WO3 + ЗН2 — W + 3H2O.
Фактично цей процес є багатоступеневим. Залежно від температури і вмісту в реакційному газі водню і відповідно парів води відновлення проходить в три або чотири стадії в такій послідовності:
WO3 > WO2,9 > WO2 > W;
WO3 > WO2,9 > WO2,72 > WO2 > W.
Чотирьохетапної відновлення має місце при температурах вище 585 °C, нижче якої WO2,9 відновлюється відразу до WO2.
При проведенні відновлення необхідно враховувати також розміри частинок виходять порошків, які при підвищенні температури укрупнюються. Для виробництва компактного металу методом порошкової металургії потрібні частинки різної крупності, що важливо при виборі умов відновлення. Укрупнення частинок порошку сприяють швидко наростаючі температури, вологість реакційного середовища і мала швидкість подачі водню.
Відновлення вольфрамового ангідриду воднем-складний гетерогенний процес, що включає наступні елементарні стадії: підведення відновника до реакційної твердої поверхні, сорбцію водню твердою часткою і дифузійне проникнення його всередину оксидної частинки, хімічна взаємодія водню з WO3, зустрічну дифузію водяної пари — продукту відновлення.
При температурі 700−850 ° С і товщині шару WO3 близько 2−4 см, при яких проводять відновлення, найповільнішою стадією, що визначає кінцеву швидкість процесу, є видалення парів води від реакційної поверхні через шар матеріалу.
Для відновлення WO3 воднем використовують стаціонарні многотрубние печі з періодичним або безперервним пересуванням човників з вольфрамовим ангідридом вздовж труби або трубчасті обертові печі.
Найбільше поширення мають многотрубние печі, що мають — зазвичай 11 одночасно обігріваються електричним струмом труб з жароміцної сталі. Труби діаметром 50−70 мм і довжиною 5−7 м распо-ложени в два ряди (в нижньому ряду 6 труб, у верхньому 5). Вольфрамовий ангідрид поміщають в нікелеві човники (зі сферичним днищем), які обнародувано за допомогою штовхачів назустріч (частіше) току водню. Човник по отже проходить всі температурні зони (три або п’ять), просуваючись у бік більш високих температур і більше сухого водню. У розвантажувальному кінці труби човник охолоджується в холодильнику.
Відновлення можна вести в одній печі або в двох, послідовно розташованих. Спочатку оксиди нагрівають до 750 ° С, а потім до 900 ° С. Двустадійность відновлення більш громіздко і менш продуктивно, але дозволяє точніше регулювати крупність виходять вольфрамових порошків.
Продуктивність однієї одіннадцатітрубной печі складає для першої стадії відновлення близько 10,5, а для другої стадії приблизно 5,5 кг/ч WO3.
мал. Одинадцятитрубна піч для відновлення WO3:
1 — робочі труби; 2 — механічні штовхачі; 3 — відвод водню; 4 — труби для подачі водню; 5 — нагрівачі.
На сучасних заводах замість круглих труб застосовують труби-муфелі прямокутного перерізу (40 Ч 150 мм) з механізованим завантаженням і розвантаженням човників плоскою, форми. Продуктивність муфельній печі з чотирма муфеля становить близько 16 кг/ч.
Найбільш продуктивними і механізованими печами для відновлення вольфрамового ангідриду є безперервно діючі трубчасті обертові печі з електрообігрівом, розроблені в Радянському Союзі.
Електропіч безперервної дії має одну робочу обертову трубу діаметром 400 мм і довжиною 4 м. Всередині труби розміщені сталеві дірчасті диски (діафрагми) і Поздовжні ребра з уголковой сталі. Це пристрій запобігає швидке переміщення важкого порошку і сприяє поліпшенню його контакту з газами. Рух оксидів н водню в таких печах протівоточной.
Водень для виробництва чистого вольфрамового порошку отримують електролізом води в електролізерах із залізними і нікелевими електродами, розділеними перегородками. Електролітом служить розчин лугу. Катодний і анодний процеси при електролітичному розкладанні води описуються наступними електрохімічними реакціями:
4Н20 + 4е = 2Н2 + 40Н-;
4OH— - 4e = O2 + 2Н20.
Перегородки в електролізерах не забезпечують повного поділу водню і кисню; водень вимагає очищення. Для очищення від кисню газ пропускають через вертикальну піч, нагріту до 600−650 ° С і заповнену каталізатором з мідного стружки або суміші залізного і нікелевого порошку. На поверхні каталізатора кисень з'єднується з воднем з утворенням парів води, які видаляють пропусканням газу через осушувальну систему.
Відновлення WОз проводять при надлишку водню в 5−10 разів вище теоретично необхідного. Після виходу з печей його регенерують! шляхом видалення вологи в холодильнику і спеціальному осушувачі.
Іноді для відновлення вольфраму використовують вуглець у вигляді газової сажі. Цей більш простий і дешевий спосіб застосовується, коли споживачі не заперечують проти присутності домішки карбідів, наприклад при виробництві твердих сплавів.
Відновлення вольфрамового ангідриду з реакції WO3 + ЗС = W + ЗСО проводять при 1500 ° С в електричних трубчастих печах з трубою з графіту, яка служить одночасно нагрівачем. Шихту з вольфрамового ангідриду і відновника брикетуюче або завантажують в циліндричні патрони з графіту, які переміщують по розпеченій графітової трубі.
Для отримання порошків вольфраму, що використовуються при легуванні сталі або для виробництва вуглецевих технічних сплавів, можна використовувати пряме відновлення вольфраматів кальцію і натрію:
CaWO4 + ЗС = W + СаО + ЗСО;
Na2WO4 + 2С = W + Na2С03 + СО.
Соду від порошку відмивають водою, а оксид кальцію відокремлюють на концентраційних столах.
2. ВИБІР І РОЗРАХУНКИ ОБЛАДНАННЯ
мал.Технологічна схема процесу відновлення WO3.
kbiМ=2+2 М=2 М=18 М=184
WO3+3H2 = 3H2O + W
х1 кг. х2 кг. х3 кг. 800 кг.
х1==1008,6957 кг = «з втратами» = 1174,85
х2==26,086· 5=130,43 кг х3==234,783 кг · 0,92 = 216 кг
216 кг Н2О =› 12 кмолей
12 кмолей = 12· 22,4 м²
х = 541,2
Втрати :
Втрати на кожному технологічному етапі становлять: 2%, 8%, 5%, 0,2%, 0,5%
На основі проведених розрахунків та заданого обґєму виробництва порошку вольфрама, обираємо безперервно діючу трубчату обертову піч з електрообогрівом, яка задовольняє наші потреби завдяки своїй високій продуктивності.
Електропіч безперервної дії має одну робочу обертову трубу діаметром 400 мм і довжиною 4 м. Усередині труби розміщені сталеві дірчасті диски (діафрагми) і поздовжні ребра з кутикової сталі. Цей пристрій запобігає швидкому переміщенню важкого порошку і сприяє поліпшенню його контакту з газами. Рух оксидів і водню в таких печах противоточний.
Водень для виробництва чистого вольфрамового порошку отримують електролізом води в електролізерах із залізними і нікелевими електродами, розділеними перегородками. Електролітом служить розчин лугу. Катодний і анодний процеси при електролітичному розкладанні води описуються наступними електрохімічними реакціями:
4Н20 + 4е = 2Н2 + 40Н-;
4OH— - 4e = O2 + 2Н20.
вольфрам переробка технологічний мал. Технологічна схема отримання водню.
3. АППАРАТУРНО-ТЕХНОЛОГІЧНЕ УСТАТКУВАННЯ
Щокова дробарка
Рис. Щокова дробарка 1 — нерухома щока; 2 — рухлива щока; 3 — ось; 4 — колінчатий вал; 5 — вертикальний шатун; 6 — розпірні плити; 7 — пружина; 8 — тяга У щокових дробарках дроблення руди відбувається між нерухомою 1 і рухливою 2 щоками. Разом з боковими стінками щоки утворять робочий простір дробарки. Щока 2 підвішена на осі 3 й отримує хитання від колінчатого (ексцентрикового) вала 4, з'єднаного із щокою вертикальним шатуном 5 і розпірними плитами 6. Тиск щоки 2 підсилюється пружиною 7 через тягу 8.
При обертанні колінчатого вала нижній кінець шатуна рухається вниз і нагору. За рахунок руху шатуна нагору розпірна плита давить на рухливу щоку, наближаючи її до нерухомого. У цей момент відбувається роздавлювання матеріалу, розташованого між щоками. За рахунок руху шатуна вниз рухлива щока відходить вправо, утворюючи щілину. Цей цикл роботи дробарки характеризується розвантаженням роздавленого матеріалу й зсувом униз нової порції вихідної породи.
Петлева сушарка
Рис. Петлева сушарка (в) і елемент сітчастої стрічки (б):1 — живильник вологого матеріалу; 2 — обігріваючі валки, для вдавлення матеріалу в сітку; 3 — нескінченна сітчаста стрічка; 4 — ланцюговий конвеєр для пересування петель сітчастої стрічки; 5 — ударний механізм; б — бункер зі шнеком У петлевих сушарках сушіння відбувається в шарі невеликої товщини (рівній товщині ланок стрічки, що становить 5 — 20 мм) при двостороннім омиванні стрічки гарячим повітрям і прогріві запресованого матеріалу металевим каркасом (сіткою), нагрітим вальцями. Це забезпечує більшу швидкість сушіння в порівнянні з камерними сушарками. Слід зазначити, що петлеві сушарки відрізняються складністю конструкції й вимагають значних експлуатаційних витрат.
Піч
Рис. Трубчаста обертова піч для відновлення WO3:
1 — стальна робоча труба; 2 — корпус пічі з підігрівачєм; 3 — сталеві дірчасті диски; 4 — завантажувальний бункер; 5 — привід; 6 — розвантажувальний бункер; 7 — камера подачі водню.
Електропіч безперервної дії має одну робочу обертову трубу діаметром 400 мм і довжиною 4 м. Всередині труби розміщені сталеві дірчасті диски (діафрагми) і Поздовжні ребра з уголковой сталі. Це пристрій запобігає швидке переміщення важкого порошку і сприяє поліпшенню його контакту з газами. Рух оксидів н водню в таких печах протівоточной.
4. ОХОРОНА ПРАЦІ
4.1 Загальна характеристика умов здійснення технологічного процесу
Охорона праці - це система правових, соціально-економічних, організаційно-технічних, санітарно-гігієнічних, лікувально-профілактичних заходів та засобів, направлених на збереження життя, здоров’я, працездатності людини в процесі трудової діяльності /1/. Метою охорони праці є зведення до мінімуму числа нещасних випадків та профзахворювань з одночасним забезпеченням нормальних та здорових умов праці при її максимальній продуктивності.
Аналіз небезпечних та шкідливих виробничих факторів, які є наявними в умовах технологічного процесу, наведені у таблиці 4.1.
Таблиця 4 1 — Перелік шкідливих та небезпечних факторів та їх джерела
Небезпечний (шкідливий) виробничий фактор ГОСТ 12.0.003−74*/3/ | Нормативно-технічний документ, що регламентує вимоги безпеки | Джерело виникнення | Дія фактора на організм людини | Нормативний показник та його значення | |
Висока електрична напруга, 380 В | ПУЕ-87/3/, ГОСТ 12.1.030−81*/4/ | Щит Управління | Термічна, біологічна, електролітична та механічна дія | Постійний Перемінний струм | |
І.Пороговий відчутний 5−7 мА/0.6−1.6мА | |||||
2.Пороговий невідпускаючий | |||||
50−80 мА/10- 15мА 3.Фібріляційний 300 мА/>50−100 мА 4.Верхнямежа фібріляційного струму 5А | |||||
Запиленість | ГОСТ 12.1.005−88 /5/, ГОСТ 12.1.007−88 /6/ | Завантаження WO3 | Табл.4 2 | ГДК в повітрі робочої зони, мг/м3 (табл.4 2) | |
Шум | ГОСТ 12.1.003−83* /7/, ДСН 3.3.6.037−99 /8/ | Вентиляційна установка | Психологічна та фізіологічна дія, пошкодження органів слуху. Шумова хвороба. | Рівень шуму La, дБА LA=80 дБА. Рівень звукового тиску Lp, дБ. | |
Вибухова та пожежна небезпека (Н2 та ін.) | ГОСТ 12.1.004−91* /9/, ГОСТ 12.1.044−89* /10/ | Піч | Опіки верхніх та нижніх дихальних шляхів та інших частин тіла, вибух | Див. табл.4 3 | |
Вібрація | ДСТУ 12.1.012*2008 /11/, ДСН 3.3.6.039−99 /12/ | Вентиляційна установка | Постійна дія загальної та локальної вібрації викликає вібраційна хворобу, діє на центральну нервову систему. | Віброшвидкість V, м/с віброприскорення а, м/с2 або їх логарифмічні рівні LV, LA, дБ LV=92 дБ | |
Шкідливі Речовини WO3 H2 W | ГОСТ | Див. табл. 4 2 | ГДК в повітрі | ||
12.1.005−88 | Піч | робочої зони, | |||
/5/, ГОСТ 12.1.007−88 /6/ | мг/м3 Див. табл. 4 2 | ||||
Несприятливий | ГОСТ | Порушення | Оптимальна | ||
мікроклімат | 12.1.005−88 | терморегуляції | припустима | ||
(підвищена | /5/, ДСН | організму | температура t, | ||
температура | 3.3.6.042−99 | людини | °С, відносна | ||
поверхні | /13/ | Піч | вологість ц%, | ||
обладнання | швидкість руху | ||||
та | повітря V, м/с | ||||
матеріалів, | (табл. 4.4) | ||||
відносна вологість) | |||||
4.2 Характеристика речовин та матеріалів виробництва
Токсикологічні характеристика речовин та матеріалів, які є в проектованому виробництві, наведена в таблиці 4 2.
Таблиця 4.2- Характеристика речовин та матеріалів виробництва.
Назва | Клас | ГДК в повітрі | Характер дії | Перша | |
речовини | небезпеки | робочої | речовини на | допомога та | |
ГОСТ | зони, мг/м3 | організм | міри безпеки | ||
12.1.007−88 | ГОСТ | людини | |||
/6/ | 12.1.005−88 /5/ | ||||
Вольфрам WO3 | Подразнення слизових оболонок верхніх та глибоких верхніх дихальних шляхів. Слабкість. | Спецодяг, распиратор ШБ-1 «Пелюстка», «Астра-2», окуляри, вентиляція. | |||
Водень | ; | При дуже високій концентрації викликає удушення, в наслідок зменшення нормального тиску кисню. | Свіже повітря. Спокій, укрити для запобігання переохолодження. Протигаз ізолюючий. | ||
Характеристика пожежновибухової та пожежної небезпеки речовини та матеріалів, а також категорія й група вибухонебезпечних сумішей наведена в таблиці 4.3.
Таблиця 4. 3 — Характеристика пожежновибухової та пожежної небезпеки речовини та матеріалів.
Найменування речовини | Характеристика пожежної та вибухової небезпеки | Показники пожежної та вибухової небезпеки ГОСТ 12.1.044−89*/10/ | Категорія та група вибухонебезпечної суміші ГОСТ 12.1.011−78* /20/ | ||||
^СП/ °С | ^см.см °С | НКМР, % об. | НКМР, % об. | ||||
Водень Н2 | ГГ | ; | 4,09 | 80,0 | ІІС, Т2 | ||
Відповідно до НАПБ Б.03.002−2007 /21/ приміщення цеху по вибуховопожежній та пожежній небезпеки відноситься до приміщення класу, А завдяки тому, що в технологічному процесі виділяється горючий газ — водень. Ступень вогнестійкості будови відповідно до ДБН В.1.1−7-2002 /22/- І, Н.
Клас зон в приміщенні відповідно до НПАОП 40.1−1.32−01 /23/-2. По ступеню небезпеки ураження електричним струмом приміщення цеху відповідно ПУЕ — 87 /3/ відноситься до особливо небезпечних, завдяки тому, що на дільниці присутні хімічно-активні речовини, які руйнують струмопровідні частини обладнання.
Ширина санітарно-захисної зони відповідно до ДНАОП 0.03−3.01−71 [14]-50м.
4.3 Промислова санітарія
Метеорологічні умови обрані відповідно до ГОСТ 12.1.005−88 /5/ та ДСН 3.3.6.042−99 /13/ з урахуванням категорії робіт та період року, наведені в таблиці 4.4.
Таблиця 4.4- Припустимі параметри метеорологічних умов
Категорія робіт по енерговитратам | Період року | Температура, °С | Відносна вологість, не більше, % | Швидкість повітря, не більше, м/с | |
Середньої важкості II б | теплий | 16−27 | 70 при 25 °С | 0,2−0,5 | |
холодний | 15−21 | 0,4 | |||
Для нормалізації параметрів мікроклімату в цеху передбачені наступні заходи:
1) відповідно до СНІП 2.04.05−91* /25/ застосовуються вентиляції та опалення у холодний період року;
2) застосування засобів індивідуального захисту (спецодяг, гумові чоботи та рукавиці, окуляри);
3) Механізація процесів завантаження та розвантаження матеріалів.
4) Теплоізоляція печі
Характеристика виробничого освітлення приведена в таблиці 4.5
Таблиця 4.5 — Характеристика виробничого освітлення (ДБН В.2.5−28−2006 /16/)
Характеристика зорової роботи | Розмір об'єкта розрізнення, мм | Розряд та підрозряд зорових робіт | Природ не освітлення | Штучне освітлення | ||||
Вид | Єн,% | Вид | Ещіп, лк | Джерело світла, тип світильника | ||||
Середньої | 0,5−1 | IV в | 0,9 | ф І | Люміне | |||
точності | (фонсередній, контраст; | суміщене | пз со о X ю § о 2Ј | сцентна лампа ЛД80−4, НОГЛ- 80 | ||||
середній) | загальне | |||||||
Завдяки тому, що приміщення цеху знаходиться в IV поясі світлового клімату, то еN = eN-mN
де т — коефіцієнт світлового клімату, дорівнює 0,9 (вікна на північ);
N — номер групи забезпеченості природнім світлом (табл. 4.(16)).
е2 = 0,9−0,9 = 0,81%
4.4 Пожежна безпека
Причини пожежі:
1) Порушення технологічного режиму;
2) Несправність електроустаткування — іскри, що утворюються при коротких замиканнях, і нагрівання ділянок електромереж та електрообладнання, що виникають при їх перевантаженнях або при появі великих перехідних опорів;
3) Самозаймання речовин на інших матеріалів — тепло, виділяється при хімічній взаємодії деяких речовин і матеріалів, наприклад, лужних металів з водою, окислювачів з пальними речовинами, а також при самозайманні речовин, наприклад, промасленого обтирального дрантя або спецодягу
4) Порушення правил пожежної безпеки, процесу.
Згідно НПАОП А.01.001−2004 /17/, ГОСТ 12.1.004.-91* /9/, ДСТУ 2272:2006 /18/ пожежна безпека в цеху забезпечується системами попередження пожежі, протипожежного захисту, вибухонебезпека-системою заходів згідно з рекомендаціями ГОСТ 12.1.010−76* /19/, організаційнотехнічними заходами.
Заходи системи протипожежного захисту:
— наявність автоматичних відключень апаратів і комунікацій
— наявність засобів повідомлення про пожежу (електрична пожежа сигналізація, телефонний зв’язок, радіозв'язок);
— застосування засобів пожежегасіння (зовнішній та внутрішній водопровід; автоматичні засоби пожежотушіння — спринклерні, первинні засоби пожежотушіння) (табл.4 6);
Таблиця 4 6- Перелік первинних засобів на дільниці цинщування
Приміщення | Площа, м2 | Первинні | К-сть, шт. | Вогнегасячий | |
(споруда, | засоби | ефект | |||
обладнання) | пожежотушіння | ||||
(найменування, | |||||
тип) | |||||
Вогнегасники | Зниження | ||||
вуглекислотні | концентрацій | ||||
ВВК-5 | кисня в зоні | ||||
горіння та | |||||
охолодження | |||||
об'єкту що | |||||
горить | |||||
Гальванічна | Вогнегасник | Піна | |||
ділянка. | 400−500 | повітрянно; | нанесена на | ||
Категорія А | пінний ВВП-10 | поверхню | |||
твердих | |||||
матеріалів, | |||||
що горять, | |||||
або рідин, | |||||
ізолює зону | |||||
горіння, що | |||||
приводить до | |||||
припинення горінню*. | |||||
Шухляда з піском | Ізолює зону горіння | ||||
Войлок | Ізолює зону горіння | ||||
Висновок: наведені вище заходи дозволяють забезпечити безпечні та нешкідливі умови праці на дільниці, яка проектується.
5. ТЕХНІКО-ЕКОНОМІЧНЕ ОБГРУНТУВАННЯ
5.1 Розрахунок виробничої потужності проектованої дільниці
Виробничу програму дільниці розраховано по ведучому устаткуванню, тобто по пічі, відповідно до формули (5.1):
G = А · П · Феф. (5.1)
деG — програма дільниці, м3/рік;
А — кількість однотипного ведучого устаткування, яка дорівнює 1 шт.;
П — продуктивність одиниці ведучого устаткування, дорівнює 281,6т/год;
Феф. — ефективний фонд часу роботи одиниці ведучого устаткування, год/рік.
Річний фонд часу роботи устаткування залежить від режиму роботи дільниці. Ефективний фонд часу розраховано відповідно до формули (5.2):
Феф. = Д · С · r · ДО1 · ДО2 — Р · С · r, (5.2)
деД — кількість робочих днів у році;
С — кількість змін за добу;
r — тривалість зміни, год;
ДО1 — коефіцієнт зупинки на ремонт устаткування;
ДО2 — коефіцієнт на переустаткування (переоснащення);
Р — кількість днів ремонту, дорівнює 20 днів.
Феф. = 365 · 3 · 8 · 0,99 · 0,98 — 20 · 3 · 8 = 8019 год/рік,
G = 1 · 0,0322· 8019 = 258,2 тис. т/рік
5.2 Розрахунок вартості і потреби сировини та матеріалів
Розрахунок потреби в матеріальних ресурсах на виробничу програму дільниці визначено за кожним видом сировини і розраховано відповідно до формули (5.3):
Р = Н · G (5.3)
деР — річна потреба сировини та матеріалів;
Н — норма використання сировини і матеріалу на продукт, т/т;
G — вироблення продукту відповідно до проекту, т/рік.
Потреба у сировині й матеріалах для виробництва представлена у табл. 5.1.
Таблиця 5.1 — Потреба у сировині й матеріалах
Сировина й матеріали | Питомі норми витрат, т/т | Об'єм виробництва, т | Річна потреба, т | |
WO3 | 1174,85 | 258,2 | 303 346,27 | |
H2 | 130,43 | 33 677,026 | ||
Всього | 1305,28 | 337 023,296 | ||
Розрахунок вартості сировини та матеріалів представлено у табл. 5.2.
Таблиця 5.2 — Вартість сировини та матеріалів
Сировина й матеріали | Ціна, грн/т | Витрата, т | Вартість, грн | |||
На 1 т продукту | На річну програму | На 1 т продукту | На річну програму | |||
WO3 | 1174,85 | 303 346,27 | 361 853,8 | 93 430 651,16 | ||
H2 | 130,43 | 33 677,026 | 18 260,2 | 4 714 783,64 | ||
Всього | 1305,28 | 337 023,296 | 25 231,6 | 98 145 434,8 | ||
5.3 Розрахунок амортизаційних відрахувань
Початкова вартість основного технологічного устаткування приведена табл. 5.3.
Таблиця 5.3 — Вартість устаткування
Устаткування | Кількість одиниць | Ціна устаткування, грн | Ціна всього устаткування, грн | 30% монтаж та транспортування, грн | Вартість устаткування, грн | |
Піч | ||||||
Всього | ||||||
Силові машини і обладнання (7 — 8% від вартості облад-нання) | ; | ; | ; | ; | ||
Невраховане облад-нання (10−12% від всього врахованого) | ; | ; | ; | ; | ||
Транспортування (5%від графи 4) | ; | ; | ; | ; | ||
Монтаж (20% від графи 4) | ; | ; | ; | ; | ||
Спецроботи (8% від графи 4) | ; | ; | ; | ; | ||
Всього | ||||||
Тоді амортизація дорівнює:
0,15 · 563 100 = 84 465 грн/рік.
Розрахунок кошторисної вартості будівництва наведено у табл. 5.4.
Таблиця 5.4 — Кошторисна вартість будівництва
Найменування будівель | Обсяг, м3 | Вартість будівельних робіт, грн | Вартість санітарно-будівельних робіт, грн | Разом загальна вартість санітарно-технічних робіт, грн | Повна кошторисна вартість будівлі будинків, грн | |||||
За 1 м³ | Загальна вартість, грн | Опалення та вентиляція (5%) | Водопровід та каналізація (10%) | Освітлення (5%) | Інші роботи (6%) | |||||
Дільниця | ||||||||||
Адміністративний корпус | ||||||||||
Всього | ||||||||||
Тоді амортизація будівництва дорівнює:
0,1 · 1 673 280 = 167 328 грн/рік.
5.4 Розрахунок витрат на оплату праці
Річний фонд оплати праці складається з фонду основної заробітної плати та фонду додаткової оплати праці.
Розрахунок балансу робочого часу одного робітника наведений у табл. 5.5.
Коефіцієнт переходу від явочної чисельності робітників до облікової розраховано за формулою (5.4):
(5.4)
Де Кпер. — коефіцієнт переходу від явочної чисельності робітників до облікової;
Феф. — ефективний фонд часу роботи одиниці ведучого устаткування, год/рік;
Фр.м. — корисний фонд робочого часу одного робітника;
С — кількість змін за добу.
Таблиця 5.5 — Баланс робочого часу одного робітника
Показники | Робочи | ||
Основні | Допоміжні | ||
Календарний фонд часу, дні | |||
Неробочі дні, всього в тому числі: | |||
— свята | |||
— вихідні | |||
Номінальний фонд робочого часу | |||
Невиходи на роботу, дні: | |||
— основні та додаткові відпустки | |||
— відпустка учням | |||
— відпустка по вагітності й пологам | |||
— по хворобі | |||
Корисний фонд робочого часу, дні | |||
Середня тривалість робочого дня, год | |||
Корисний фонд робочого часу в рік, год | |||
Коефіцієнт переходу | 1,54 | 1,54 | |
Розрахунок чисельності робітників приведений у табл. 5.6, а розрахунок ФОП основних та допоміжних робітників — у табл. 5.7.
Таблиця 5.6 — Розрахунок чисельності робітників
Назва професії | Чисельність робітників у зміну | Кількість змін за добу | Явочна чисель-ність | Коефіцієнт облікового складу | Облікова чисельність робочих | |
Основні робітники: | ||||||
1 Апаратник АТ1 | 1,54 | |||||
2 Апаратник АТ2 | ||||||
3 Апаратник КСО1 | ||||||
4 Апаратник КСО2 | ||||||
5 Апаратник ЗВ | ||||||
Всього | ||||||
Допоміжні робітники: | ||||||
1 Електрик | 1,54 | |||||
2 Механік | ||||||
3 Сантехнік | ||||||
Всього | ||||||
Таблиця 5.7 — Розрахунок ФОП основних та допоміжних робітників
Професія | Облікове число | Тарифний розряд | Ставка, грн/год | Ефективний фонд часу 1 робітника, год/рік | Тариф, грн | Доплата і надбавки (30%), грн | Фонд ОЗП, грн | Додаткова оплата праці (20%), грн | Річний фонд оплати праці, грн | |
Основні робітники: | ||||||||||
1 Апаратник АТ1 | V | 8,39 | 74 503,2 | 22 350,96 | 96 854,16 | 19 370,83 | 116 224,99 | |||
2 Апаратник АТ2 | V | 8,39 | 74 503,2 | 22 350,96 | 96 854,16 | 19 370,83 | 116 224,99 | |||
3 Апаратник КСО1 | VI | 9,27 | 82 317,6 | 24 695,28 | 107 012,88 | 21 402,58 | 128 415,46 | |||
4 Апаратник КСО2 | VI | 9,27 | 65 854,08 | 19 756,22 | 85 610,3 | 17 122,06 | 102 732,36 | |||
5 Апаратник ЗВ | IV | 7,56 | 53 706,24 | 16 111,87 | 69 818,11 | 13 963,62 | 83 781,73 | |||
Всього | 350 884,32 | 105 265,29 | 456 149,61 | 91 229,92 | 547 379,53 | |||||
Допоміжні робітники: | ||||||||||
1 Електрик | IV | 7,56 | 66 830,4 | 13 010,19 | 79 840,59 | 15 968,12 | 95 808,71 | |||
2 Механік | IV | 7,56 | 66 830,4 | 13 010,19 | 79 840,59 | 15 968,12 | 95 808,71 | |||
3 Сантехнік | IV | 7,56 | 53 464,32 | 16 039,29 | 69 503,61 | 13 900,72 | 83 404,33 | |||
Всього | 187 125,12 | 42 059,67 | 229 184,79 | 45 836,96 | 275 021,75 | |||||
5.5 Розрахунок річного фонду оплати праці керівників, спеціалістів, службовців і МОП
Основою розрахунку ГРОФ вказаних категорій робітників є штатні оклади, які встановлюються на рівні діючих на підприємстві, або згідно єдиної тарифної сітки для робітників або службовців по спеціальним професіям. Розрахунок ГРОФ керівників, спеціалістів, службовців наведено у табл. 5.8.
Таблиця 5.8 — Розрахунок ГРОФ керівників, спеціалістів, службовців
Категорія працівників | Чисельність | Оклад за місяць, грн | Кількість місяців | Основний фонд ЗП, грн | Додаткова оплата праці, грн (45%) | Річний фонд оплати праці | |
Начальник дільниці | |||||||
Інженер-технолог | |||||||
Інженер-механік | |||||||
Начальник зміни | |||||||
Нормувальник | |||||||
Лаборант | |||||||
Прибиральник | |||||||
Всього | ; | ; | |||||
5.6 Розрахунок витрат по утриманню і експлуатації устаткування.
Розрахунок витрат по утриманню і експлуатації устаткування проведено у вигляді таблиці і наведено у табл. 5.9.
Таблиця 5.9 — Розрахунок витрат по утриманню і експлуатації устаткування
Найменування статей | Величина витрат, грн | Примітка | |
1 Витрати на оплату праці: | |||
1.1 основна ЗП допоміжних робітників | 275 021,75 | Табл. 5.7 | |
1.2 відрахування на оплату праці | 208 168,44 | 38,03% від озп | |
2 Матеріальні витрати: | |||
2.1 на проведення технічного обслуговування |