Вплив шорсткості та стану поверхневого шару на експлуатаційні властивості деталей машин
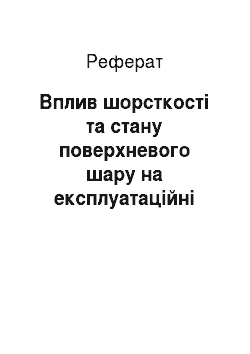
Втомлена міцність деталей суттєво залежить від величини, знака і глибини поширення залишкових напружень поверхневого шару. Численними дослідженнями встановлено, що за наявності у поверхневому шарі залишкових напружень стискання межа витривалості деталі підвищується, а за наявності залишкових напружень розтягування — знижується, причому залишкові напруження стискання суттєво підвищують межу… Читати ще >
Вплив шорсткості та стану поверхневого шару на експлуатаційні властивості деталей машин (реферат, курсова, диплом, контрольна)
Вплив шорсткості та стану поверхневого шару на експлуатаційні властивості деталей машин
1. Вплив шорсткості поверхні
Тертя та зношування деталей значно пов’язані з висотою та формою нерівностей і напрямком штрихів обробки. У початковий період роботи поверхонь, що труться, їх контакт відбувається по вершинах нерівностей. В результаті цього фактична поверхня зіткнення складає лише невеликий відсоток від розрахункової. Тому в місцях фактичного контакту по вершинах нерівностей виникають великі тиски, які часто перевищують межу текучості і навіть межу міцності металів, що труться.
Під дією тисків при нерухомих поверхнях в точках контакту відбувається пружне стикання і пластична деформація зминання нерівностей, а при взаємному переміщенні поверхонь — зрізання, відламування і пластичний зсув вершин нерівностей, що призводить до інтенсивного початкового зношування деталей, що труться, і до збільшення зазорів пари тертя.
Підвищеному початковому зношуванню в деяких випадках сприяють виникнення в точках контакту високих миттєвих температур і зрив окисної плівки, що покриває метали. Це супроводжується молекулярним зчепленням металів, що труться, і створенням вузлів схоплювання.
При роботі деталей в легких і середніх умовах висота нерівностей в період початкового зношування поверхонь, що труться, зменшується на 65−75%, що призводить до збільшення фактичної поверхні їх контакту, а отже, до зниження фактичного тиску.
Під час початкового зношування, що відбувається в період припрацювання, відбувається зміна розмірів і форми нерівностей, а також напрямку слідів обробки. При цьому висота нерівностей зменшується, чи збільшується до деякого оптимального значення, яке різне для різних умов тертя. Якщо для даних умов тертя вдається досягти оптимальної висоти нерівностей в процесі механічної обробки, то в процесі експлуатації вона не змінюється, а час припрацювання і зношування виявляється найменшим.
Графіки зношування (рис. 1) показують, що при оптимальній висоті нерівностей (точки О1 і О2) початкове зношування металу є найменшим. В більш важких умовах роботи крива 2 зношування зміщується вправо і вгору, а точки оптимальної шорсткості - вправо і вбік збільшення висоти нерівностей.
Рис. 1. Залежність зношування від висоти нерівностей поверхні
Збільшення висоти нерівностей проти оптимальної збільшує початкове зношування, а зменшення нерівностей проти оптимальної може призвести до молекулярного зчеплення пар тертя. Тому задачею конструктора, що проектує нові машини, є призначення оптимальної шорсткості, при якій зношування та коефіцієнт тертя за даних умов зношування був би мінімальним.
На рис. 2 показано, що через 160 000 подвійних ходів зношування поверхні з нерівностями великого кроку досягає 60 мкм, а зношування поверхні з тонкими нерівностями малого кроку було менше 40 мкм.
Вплив напрямку нерівностей на зносостійкість різний у різних умовах тертя і при різних розмірах нерівностей. При рідинному терті і малій висоті нерівностей напрямок штрихів значення немає, проте при збільшенні шорсткості більш вигідним виявляється паралельний напрямок штрихів і швидкості руху.
Рис. 2. Криві зношування (а) поверхонь з різною формою нерівностей (б) при однаковій висоті нерівностей Rz
При граничному терті поверхонь з малими значеннями Ra з паралельним напрямком нерівностей і вектором швидкості руху зношування та схоплювання, що виникають, виявляються більшими, ніж при поперечному напрямку нерівностей і руху подачі. Для поверхонь з великою шорсткістю, коли схоплювання не відбувається, паралельний напрямок штрихів дає найменше зношування.
Коефіцієнт тертя також пов’язаний з напрямком нерівностей та їх висотою. При сполученні поверхонь, що мають однаковий напрямок нерівностей, і при їх перпендикулярному напрямку до руху коефіцієнт тертя досягає найбільшого значення. При перпендикулярному напрямку нерівностей поверхонь, що труться, або при їх безладному розташуванні, що спостерігається при суперфінішуванні, коефіцієнт тертя мінімальний.
Точність сполучення, що встановлена кресленням і визначається зазором у з'єднанні, суттєво залежить від шорсткості сполучуваних поверхонь.
Раніше вказувалось, що в період початкового зношування висота нерівностей може зменшуватись на 65−75%. При малих розмірах деталей і шорсткості поверхонь з Rz= 3?10 мкм подвійна висота нерівностей 2Rz може бути співставленою з полем допуску на виготовлення деталі. Це означає, що в період початкового зношування поверхонь додатковий зазор в з'єднанні може досягнути значення допуску на виготовлення деталі, і точність з'єднання буде повністю порушена. Замість необхідного за кресленням з'єднання сьомого квалітету точності фактично виникає з'єднання восьмого або дев’ятого квалітету, порушується характер посадок тощо.
Для запобігання цього необхідно у всіх випадках відповідальних сполучень, від яких потрібне довготривале збереження встановленої конструктором точності, проводити обробку деталей при досягненні мінімальної шорсткості поверхонь, що труться.
При цьому рекомендується встановлювати необхідну висоту шорсткості в залежності від необхідної точності сполучення, що проектується, шляхом розрахунку за формулами:
при діаметрі сполучення понад 50 мм: Rz = (0,10?0,15)T;
при діаметрі сполучення від 18 до 50 мм: Rz = (0,15?0,20)T;
при діаметрі сполучення менше 18 мм: Rz = (0,20?0,25)T.
В цих формулах поле Т деталі і висота нерівностей Rz виражені в мкм.
Міцність пресованих з'єднань безпосередньо пов’язана з шорсткістю сполучуваних поверхонь. Зі збільшенням висоти нерівностей сполучуваних поверхонь міцність пресових з'єднань знижується. Наприклад, міцність пресового з'єднання маточини вагонного колеса з віссю при висоті нерівностей 36,5 мкм виявилась на 40% нижчою міцності такого ж з'єднання з висотою нерівностей 18 мкм (не дивлячись на те, що натяг у другому випадку був на 15% меншим).
Втомлена міцність деталей суттєво залежить від шорсткості їх поверхонь. Наявність на поверхні деталі, які працюють в умовах циклічного і знакозмінного навантаження, окремих дефектів і нерівностей сприяє концентрації напружень, які можуть перевищити межу міцності металу. В цьому випадку поверхневі дефекти і штрихи від обробки відіграють роль осередка виникнення субмікроскопічних порушень суцільного металу поверхневого шару і його розпушення, що є першопричиною створення втомлених тріщин.
Експериментальні графіки (рис. 3) показують, що при збільшенні параметра шорсткості відпаленої сталі 45 з Rz = 3,2 до Rz = 75 мкм межа її витривалості знижується з 285 до 200 МПа, тобто на 30%. Особливо різко знижується межа витривалості при збільшенні шорсткості найбільш гладких поверхонь.
Рис. 3. Залежність межі витривалості від висоти нерівностей
На рис. 4 показано вплив напрямку нерівностей на межу витривалості сталі при згинанні. Із діаграми видно, що при поздовжньому напрямку нерівностей циклічна міцність при згинанні сталі 2Х13 на 10−15% вища, ніж при поперечному розташуванні нерівностей. Ця закономірність проявляється при різних видах обробки.
Висота шорсткості, напрямок штрихів обробки, форма і крок нерівностей, розміри опорної поверхні та інші геометричні характеристики мікрорельєфу поверхні впливають й на інші важливі експлуатаційні властивості деталей машин і приладів, тобто зокрема і на їх міцність при ударному навантажені, контактну жорсткість, відбивну спроможність, коефіцієнт тепловіддачі, газову ерозію.
Рис. 4. Вплив напрямку штрихів обробки на межі витривалості зі сталі 2Х13: 1 — напрямок штрихів поперек деталі; 2 — напрямок штрихів вздовж деталі
шорсткість напруження зносостійкість наклеп метал
2. Вплив деформаційного зміцнення (наклепу) металу поверхневого шару
Зносостійкість деталей. Підвищенню зносостійкості деталей у більшості випадків сприяє попереднє зміцнення металу поверхневого шару, яке зменшує зминання і стирання поверхонь за наявності їх безпосереднього контакту, і взаємне проникнення поверхневих шарів, що виникає при їх механічній та молекулярній взаємодії: зміцнення збільшує дифузію кисню в метал поверхневого шару, створюючи в ньому тверді хімічні з'єднання FeO, Fe2O3, Fe3O4 характерні для окислювального зношування, що протікають з найменшою інтенсивністю, а також перешкоджають розвитку спільної пластичної деформації металів деталей, що труться, що викликає холодне зварювання схопленням, яке є найбільш інтенсивним видом зношування.
На рис. 5 показано зміну зношування валиків зі сталі У8А при їх терті - ковзанні з чавунними колодками зі змащенням в залежності від ступеня наклепу валиків після шліфування, вираженого мікротвердістю поверхневого шару. Графік ілюструє значне зменшення зношування зі збільшенням ступеня наклепу.
Позитивний вплив наклепу на зносостійкість поверхонь, що труться, проявляється тільки до певного ступеня початкового наклепу. Якщо при попередній обробці поверхні, що треться, ступінь пластичної деформації поверхневого шару перевищує певне для даного металу значення, то в металі починається процес його розпушення (розриви міжатомних зв’язків по площинах ковзання і субмікроскопічні порушення суцільності металу), що відбувається одночасно з процесом зміцнення, який продовжується. Це явище називається перенаклепом.
Рис. 5. Вплив наклепу на зношування стальних валиків
При подальшому збільшенні навантаження металу переміцнені і окрихчені зони металу відшаровуються від його основної маси; починається лущення і прискорене зношування металу. Таким чином, перенаклеп металу викликає різке падіння зносостійкості, а також знижує втомлену міцність деталей і деякі інші експлуатаційні властивості. У зв’язку з цим зміцнення металу поверхневого шару в процесі механічної обробки деталей при спеціальних зміцнюючих операціях (обкатка роликами і шариками, дрібоструминна обробка, тощо) слід провадити при суворо регламентованому наклепі що досягається, щоб запобігти виникненню перенаклепу.
Втомлена міцність деталей машин у значному ступеню залежить від зміцнення (наклепу) метала поверхневого шару. Зміцнення металу до певних меж зменшує амплітуду пластичної деформації і запобігає виникненню субмікроскопічних порушень суцільності (розпушення), що породжують розвиток втомлених тріщин.
Крім того, створення зміцненого наклепаного поверхневого шару перешкоджає зростанню існуючих і виникненню нових втомлених тріщин. Такий шар може значно нейтралізувати шкідливий вплив зовнішніх дефектів і шорсткості поверхні. Дослідження деталей з твердим зміцненим шаром після циклічних навантажень, через які в металі виникають напруження, що перевищують межу втомленості, показує, що втомлені тріщини зароджуються не у зміцненому шарі деталі, а у глибині її. Створення подібних тріщин під зміцненим шаром і їх подальше збільшення відбувається при більш високих напруженнях і їх більшому числі циклів навантаження, ніж в умовах відсутності наклепу. Вплив перелічених причин призводить до помітного підвищення втомної міцності деталей машин в результаті зміцнення металу їх поверхневого шару (рис. 6).
Результати численних досліджень показують, що при наклепі металу поверхневого шару підвищення циклічної міцності деталей машин, що працюють в умовах нормальної кімнатної температури, може досягти 25−30%. При наклепі металу точінням і поліруванням межа витривалості підвищується на 20−25% за рахунок наклепу і на 12−15% зростає за рахунок зниження висоти шорсткості при переході від точіння до полірування.
Рис. 6. Вплив глибини (а) і ступеня (б) наклепу, створеного точінням, на межі витривалості сталі 45
Вплив наклепу на корозійну стійкість. Пластична деформація та наклеп поверхневого шару металу протікають в різно орієнтованих зернах неоднакового складу з різною інтенсивністю, феритні зерна деформуються інтенсивніше перлітних. Це викликає підвищення енергії та різну зміну електродного потенціалу. Більш наклепані феритні зерна стають анодами, а менш наклепані перлітні зерна — катодами. З тих же причин виявляються різними і викривлення атомної решітки в різних кристалічних зернах.
В результаті пластичної деформації полікристалічного металу в ньому створюються мікронеоднорідності, що сприяють виникненню великої кількості корозійних мікроелементів. Найбільш активними ділянками металу у взаємодії із зовнішнім середовищем є зони площин зсувів і місця виходів дислокацій на поверхню. В цих зонах прискорюється адсорбція та розвиваються корозійні і дифузні процеси. В результаті цього холоднодеформована м’яка сталь може поглинути у 100 разів більше водню, ніж відпалена.
Механічна обробка, що викликає наклеп поверхневого шару і зміну шорсткості поверхні, суттєво впливає на корозійну стійкість металу. За даними проведених досліджень коефіцієнт самодифузії нікелю жароміцної сталі після електрополірування, коли наклепаний шар повністю усунений, при 700 С складає 10-14 см2/с, а після шліфування — 13 010-14 см2/с. В табл. 7.3 наводяться дані про втрату в масі зразків внаслідок корозії за 30 діб перебування у воді.
Втрати в масі стальних зразків від корозії за 30 діб перебування у воді
Вид обробки зразка | Втрати в масі,? 10-5 г/см2 | ||
Сталь 20Х | Сталь У8А загартована | ||
Шліфування Точіння Силове точіння Обробка роликами | |||
Наклеп і залишкові напруження поверхневого шару можуть стати однією з причин корозійного розтріскування сталі при її довготривалому статистичному навантаженні в корозійних середовищах. Зняття наклепу відпалюванням усуває в цих випадках і корозійне розтріскування.
Необхідно однак відмітити, що за певних умов створення наклепу деталей накатуванням роликами або обдуванням дробом відбувається завальцьовування шляхів проникнення корозійних середовищ у середину металу через дефекти поверхні, які пластично деформуються феритом. Це може нейтралізувати розвиток корозійних процесів і розвиток втомної міцності деталей.
Наклеп поверхневого шару значно знижує магнітні властивості магнітом'яких матеріалів типу пермалой, альфенол тощо. У зв’язку з цим при їх механічній обробці наклеп неприпустимий.
При робочій температурі понад 700-800 С наклеп поверхневого шару в багатьох випадках виявляється шкідливим і знижує експлуатаційні якості деталей машин.
Це відбувається тому, що після пластичної деформації металу поверхневого шару при кімнатній температурі збільшується його питомий об'єм і зменшується щільність. Ця обставина сприяє більш швидкому протіканню дифузійних процесів при високій температурі та вигоранню легованих елементів, і тим самим прискорює процеси, що знижують опір металу відриву.
Тривала дія високої температури на наклепаний метал швидко призводить до інтенсивного розміцнення його, що знижує загальні експлуатаційні властивості деталей.
Зі збільшенням ступеня і глибини наклепу жароміцних сплавів їх втомлена міцність при роботі в середовищі з високою температурою знижується (рис. 7). При глибині наклепу 190 мкм, що виникає при чорновому точінні, число циклів N до зруйнування сплаву при 700 С виявляється приблизно у двічі нижчим, ніж після електрополірування, яке не викликає наклепу.
Рис. 7. Вплив, глибини наклепу при різних методах обробки жароміцного сплаву на число циклів N до його зруйнування при високих температурах: 1 — електрополірування; 2 — полірування після шліфування; 3 — шліфування; 4 — полірування після точіння; 5 — чистове точіння; 6 — полірування; 7 — чорнове точіння
Різними експериментами було показане суттєве зменшення тривалої міцності жароміцного сплаву в залежності від глибини наклепу, що виникає при різних видах обробки. З даних досліджень видно, що при значному наклепі, створюваному дробовоструминною обробкою та обкаткою роликами, тривала міцність при стогодинних дослідженнях знижується при 700 С на 11,5−27%, а при 800 С — на 15−45%. Навіть при чистовому точінні наклеп поверхневого шару зменшує тривалу міцність майже на 10%.
Ще сильніше проявляється шкідливий вплив наклепу (як поверхневого, так і суцільного) на міцність жароміцних сплавів при циклічних нагріваннях (термовтомленість). Як показує діаграма на рис. 8, при 700 С час Т до руйнування зразків, наклепаних обдуванням дробом і обкаткою роликами, відповідно у два і шість разів меншим, ніж у зразків без наклепу (оброблених електрополіруванням).
Рис. 8. Вплив наклепу при різних методах обробки жароміцного сплаву на час до його зруйнування при випробовуванні з циклічним нагріванням: 1 — електрополірування; 2 — шліфування; 3 — полірування після шліфування; 4 — полірування після точіння; 5 — точіння; 6 — обдування дрібом; 7 — обкатування роликом
При дослідженнях деяких структурно-стійких сталей при температурі 600−700 С не спостерігалося шкідливого впливу наклепу, а в деяких випадках навіть була виявлена позитивна дія наклепу на міцнісні характеристики цих сталей. Отже, питання про вплив наклепу при помірних робочих температурах потребує в окремих випадках додаткових уточнень. Проте, в цілому вплив наклепу на міцність деталей машин, що працюють при високих робочих температурах, є шкідливим.
3. Вплив залишкових напружень
Зношування. При терті деталей в металі поверхневого шару відбуваються значні пластичні деформації, що викликають інтенсивний наклеп і великі залишкові напруження стискання.
На самому початку процесу тертя деталей залишкові напруження, які створені в їх поверхневому шарі попередньою обробкою та є за своєю природою пружними, знімаються під дією пластичних деформацій, що протікають, не встигнувши істотно якось вплинути на процес зношування.
Одночасно у поверхневому шарі в результаті тертя виникають залишкові напруження стискання, які залежать від умов тертя і пластичних властивостей металів, що труться, і не залежать від величини і знака залишкових напружень, створених попередньою обробкою та існуючих у поверхневому шарі до початку тертя.
У зв’язку з цим величина і знак залишкових напружень поверхневого шару, створених попередньою обробкою, не впливають на швидкість та величину зношування при терті ковзання.
Цей висновок відноситься тільки до залишкових напружень поверхневого шару і нормальних умов тертя ковзання в режимі окислювального зношування.
Напружений стан всього перерізу деталі (наприклад, розтягуючі внутрішні напруження в стінках втулки, що напресована на іншу деталь; розтягуючі внутрішні напруження у пружновигнутій пластині) може впливати на характер та інтенсивність зношування. Можливим є і вплив напруженого стану при зношуванні в умовах пітінга, при якому значення мають явища втоми металу.
Втомлена міцність деталей суттєво залежить від величини, знака і глибини поширення залишкових напружень поверхневого шару. Численними дослідженнями встановлено, що за наявності у поверхневому шарі залишкових напружень стискання межа витривалості деталі підвищується, а за наявності залишкових напружень розтягування — знижується, причому залишкові напруження стискання суттєво підвищують межу витривалості, ніж знижують його такі ж за величиною залишкові напруження розтягування. Для сталей підвищеної твердості підвищення межі втомленості завдяки дії стискальних напружень досягає 50%, а зниження його під дією розтягальних напружень — 30%. Вплив залишкових напружень на межу витривалості сталі особливо суттєвий, коли різниця в міцності сталі при розтягуванні та стисканні велика. У зв’язку з цим межа витривалості твердих сталей залежить від величини і знака залишкових напружень особливо сильно, в той час як у м’яких і пластичних сталей ця залежність проявляється менше.
Рис. 9. Вплив залишкових напружень на втомлену міцність деталей зі сплаву ВТЗ-1
Графік залежності межі витривалості металів і сплавів ВТ3-від величини і знака залишкових напружень, утворених при шліфуванні, показаний на рис. 9 і свідчить про те, що між межею витривалості та залишковими напруженнями поверхневого шару існує прямий зв’язок, який може бути виражений співвідношенням виду:
у-1 = A — Bузал,
де у-1 — межа витривалості металу після його шліфування;
узал — залишкові напруження поверхневого шару, що виникли в результаті шліфування, із врахуванням їх знака;
А і В — постійні величини.
Аналогічні співвідношення були отримані й для інших матеріалів і видів обробки. При цьому експерименти проводилися при кімнатних температурах, тому висновки не можуть відноситись до умов роботи деталей в зоні високих температур. При нагріванні деталей, що мають в поверхневому шарі залишкові напруження, відбувається релаксація напружень і їх вплив на межу витривалості послаблюється.
4. Вплив структурних змін металу поверхневого шару
Теплота, що виділяється в зоні різання при різних методах механічної обробки в певних умовах (напружені режими різання, притуплення різального інструмента і засалювання круга надто високої твердості, недостатнє охолодження тощо), викликає структурні зміни металу поверхневого шару.
При обробці металів, що піддаються загартовуванню, може відбутись часткове загартування металу поверхневого шару, а при обробці загартованих металів — відпущення різного ступеня.
Структурні зміни металу при його механічній обробці і, зокрема, припали поверхні, що шліфується, є серйозною причиною зниження довговічності деталей машин.
Ділянки м’якого відпущеного металу мають знижену зносостійкість. На рис. 10 показано, що деталі із загартованої сталі 40Х, яка має підпал поверхневого шару, зношуються значно інтенсивніше аналогічних деталей без підпалу.
Рис. 10. Вплив шліфувального припалу на зношування стальних зразків: 1 — з припалом 2 — без припалу
Звичайно в зонах відпущеного металу, що має менший питомий об'єм, розвиваються залишкові напруження розтягування, які знижують втомлену міцність деталей. При цьому на границях ділянок зміненої структури часто утворюються шліфувальні тріщини, які є осередками втомлених руйнувань деталей.
Межа витривалості зразків з підпалинами (рис. 11) значно нижча за межу витривалості зразків, виготовлених із загартованої сталі 40Х без підпалин.
Рис. 11. Вплив шліфувального припалу на межу витривалості сталі 40Х: 1 — без припалу 2 — з припалом
Використана література
1. Бондаренко С. Г. Розмірні розрахунки механоскладального виробництва. — К. 1993. — 544 с.
2. Маталин А. А. Технология машиностроения. — Л. — М., 1985. — 496 с.
3 Основы технологии машиностроения / Под ред. В. С. Корсакова — М., 1977. — 416 с.
4. Справочник технолога-машиностроителя / Под. ред. А. Г. Косиловой, О. К Мищерякова. Т. 1. — М. 1985. — 655 с.
5. Руденко П. А., Шуба В. А и др. Отделочные операции в машиностроении. — К.: Техника, 1990. — 150 с.