Исследование паровоздушной газифікації низькосортних вугілля Украины
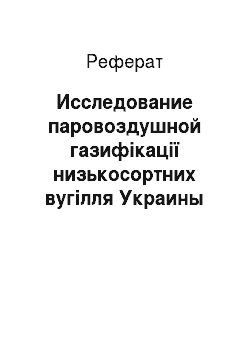
2.8) Поєднання всіх таких реакцій яких і визначає склад що утворюється газу, який змінюється за висотою газогенератора. Після окислительной і відновлювальної зон, званих разом зоною газифікації, виходять гарячі гази за нормальної температури 800—900 °З. Вони нагрівають вугілля, який піддається пиролизу в вышележащей зоні. Цю зону прийнято називати зоною піролізу, чи зоною полукоксования. Виходять… Читати ще >
Исследование паровоздушной газифікації низькосортних вугілля Украины (реферат, курсова, диплом, контрольна)
Міністерство освіти Украины украинский державний хіміко-технологічний университет.
кафедра хімічної технології топлива.
пояснювальну записку до дипломної работе.
на задану тему ________________________________________________________ ____________________________________________________________________________ _______________________________________________________.
Студент групи 5-ХТТ-17 Могутнов В. В. __________.
(шифр групи, прізвище, инициалы).
(подпись) Руководитель роботи доц. каф. Ковбык А. А. __________.
(посаду, прізвище, инициалы).
(подпись) Консультанты: Доц. Ковбык А.А.
__________.
(розділ роботи, посаду, прізвище, инициалы).
(підпис) охорона праці доц. Герасименко В. А __________.
экономическая частина ас. Гетьман О. А. __________.
Завідуючий кафедри Гулямов Ю. М. __________.
(прізвище, инициалы).
(подпись).
Дніпропетровськ 2003.
РЕФЕРАТ.
З. 57; табл.14; рис.4; библиогр. посилань 10; креслення. 1.
Вугілля, газифікація, генераторний газ, газогенератор
У загальній частини дипломної роботи було проведено літературний аналіз методів газифікації вугілля, вибір про обгрунтування принципової технологічної схеми отримання генераторного газу методом паровоздушной газифікації. Наведено параметри та описи процесу, зроблено економічний розрахунок ціни исследования.
З технічного аналізу за змістом баластових компонентів і летючих, вибрано сировину процесу газификации.
Вивчено вплив швидкості подачі окислювачів на ступінь конверсії вугілля. Обрані основні оптимальних показників процесу переробки низькосортного збагаченого концентрату: витрата повітря і кілька, температура.
У дипломної роботі наведено заходи для техніці безпеки, промислової санітарії і протипожежної техніки, під час проведення в випробувальною лабораторії. До того ж розраховані видатки проведенні дослідницької частини й визначено ціну исследования.
стр.
1. Літературний обзор
2. Фізико-хімічні основи процесу газификации.
3. Вибір, обгрунтування і опис технологічної схемы.
3.1 Принцип роботи лабораторної установки.
2. Технічна характеристика угля.
3. Вплив швидкості подачі газифікуючих агентов.
4. Аналіз отриманих данных.
4. Охорона труда.
1. Оцінка умов, у яких проводилася дослідницька работа.
2. Заходи з гарантуванню безпеки і здорових умов праці лабораторії 36.
3. Характеристика приміщення по пожароі взрывоопасностью.
4. Протипожежні заходи безопасности.
5. Економічна часть.
1. Визначення тривалості работы.
2. Грошові проведення исследования.
1. Розрахунок видатків сировини і материалы.
2. Розрахунок витрати на заробітну плату.
3. Розрахунок обсягу нарахування на зарплатню 51.
4. Розрахунок витрати на электроэнергию.
5. Амортизаційні отчисления.
6. Накладні расходы.
Стр.
5.3 Розрахунок ціни исследования.
6. Выводы.
український державний хіміко-технологічний университет.
Факультет ТВМС Кафедра ХТТ Специальность хімічна технологія палива й вуглецевих материалов.
УТВЕРЖДАЮ.
Зав. кафедри Гулямов Ю.М.
_____________________.
«_____» _______2003 г.
ЗАДАНИЕ.
на дипломну роботу студента.
Могутнова Віктора Викторовича.
1. Тема работы.
____________________________________________________________.
__________________________________________________________________________.
затверджений наказом інститутом від «____"______________2003 г.
№______________.
2.Время здачі студента готової работы.
_______________________________________________.
3. Вихідні дані до работе.
________________________________________________.
__________________________________________________________________________.
__________________________________________________________________________.
4. Зміст расчетно-пояснительной записки (перерахування питань, які мають решить).
__________________________________________________________________________.
_______________.
__________________________________________________________________________.
__________________________________________________________________________.
5. Перерахування графічного материала.
__________________________________________________________________________.
__________________________________________________________________________.
__________________________________________________________________________.
Бистре розвиток виробничих сил, пов’язані з великим витратою палива й вуглеводневої сировини, нерівномірність і складність видобутку горючих копалин супроводжується зростання цін і підвищення транспортних витрат і матеріальних затрат.
У хімічної індустрії найбільш нагальним завданням є переведення вугільної бази виробництва пов’язаного азоту, синтетичного метанолу. Цей переклад обіцяє зменшувати крупнотонажность хімічних підприємств від сезонних коливань у постачанні природного газу, звільнити з застосування значних кількостей жароупорных легованих сталей.
Перехід на тверде паливо має і ряд негативних явищ для промислового виробництва. Аналіз, підготовка виробництва та подолання труднощів є саме науки.
Фундаментальна обізнаність із твердим паливом в аппаратурно-техническом плані складніше, ніж з рідкими і газоподібними вуглеводнями. Видобуток і транспортування твердого палива, його сушінню, здрібнення, подання у газогенератор, видалення золи, очищення технологічного газу це вимагатиме допомоги механічних і технологічних пристосувань. З іншого боку, все технологічні операції вимагають енергетичних затрат.
Отже, перехід нові сировинну базу пов’язаний: зі зростанням питомих капітальних видатків, зменшення ККД процесу, збільшення витрати робочої сили тонну кінцевий продукт. Але з хоч би витратами ні пов’язаний такий перехід, його не можна розглядати, як альтернатива, це неминуча необхідність. І раніше буде розвинена підготовка до цього переходу, тим він пройде більш безболісно. Найважливішим ланкою при виконанні завданняпроблема газифікації твердих паливотримання генераторного газу [1].
1. ЛІТЕРАТУРНИЙ ОБЗОР.
Газифікація вугілля — виробництво пального (технологічного) газу при неповному окислюванні органічної маси вугілля, має давню історію з періодами бурхливого розвитку та спадами. Вперше горючий газ з вугілля отримав англієць Мердок в 1792 р. як попутний продукт під час виробництва «светильного олії «. До 50-му років в XIX ст. практично у всіх великих і середніх містах Європи й Америки діяли газові заводи для виробництва опалювального, побутового і светильного газу [2]. То справді був «золоте століття «газифікації вугілля. Починаючи з 1960;х років в XIX ст., дедалі більше серйозної конкуренції вугіллю починає надавати нафту. На початку 60-х років розробка родовищ дешевої нафти Близькому сході з’явилися й у Західному Сибіру привела практично до повної ліквідації цій галузі промисловості. Збереглися лише невеликі острівці в унікальних регіонах. Наприклад, до ПАР углепереработка (головним чином основі газифікації вугілля) стала великої промисловим сектором через ембарго про поставки нафти. Почалося тріумфальна хода нафти. Проте вже 1972 р. воно затьмарилося першим «енергетичну кризу », котрий за суті був спровокований на політичній основі країнами-учасниками ОПЕК. Світові нафтові ціни підскочили з 5−7 до 24 дол. США за барель (1 т сирої нафти сорти Brent? 8,06 барелей), і став ясно, що углепереработку списувати у комп’ютерний архів рано, позаяк у більшості розвинутих країн багато вугілля й мало або зовсім немає нафти. Цікаво відзначити, якби не цей перший «енергетичний криза », то крах соціалістичної системи міг наступити ще 1970;ті рр. Активний приплив «нафтодоларів «продовжив агонію СРСР. Цей криза підніс до цивілізованого світу дуже важливого уроку. По-перше, всі усвідомили, що запаси вуглеводневої сировини розподілено вкрай нерівномірний і незручно, й удругих, ці запаси — исчерпаемы. Запаси ж вугілля й інших твердих горючих копалин — нафтових сланців, бітумних пісків, торфу тощо. розподілені рівномірніше, і терміни їхнього вичерпання оцінюється багатьма сотнями років. Але найголовніший результат цей кризи залежить від активізації робіт з энергосбережению.
До прогнозам исчерпаемости природних ресурсів слід ставитися дуже обережно. Зазвичай, по них стоять політична кон’юнктура і вузько корпоративні інтереси. У 1970;1980 рр. наукова періодика була сповнена прогнозів, за якими сьогодні, 2002 р., ми мали добувати з надр залишки нафти і є. Передбачали, що під час 1995;2020 рр. розпочнеться другий «золоте століття» вугілля. Була популярна думка, що «нафту — це епізод за доби вугілля ». Панічні прогнози щодо перспектив нафтового ринку ініціювали створення нових технологічних процесів переробки вугілля, причому пріоритетним була оренда рідкого палива, як прямим ожижением вугілля, і непрямим, тобто. синтезом рідких вуглеводнів з «вугільного» синтез-газу. У, Великобританії, Німеччини, Японії, колишньому СРСР та інших країн при державну підтримку розпочато масштабні програми створення технологій углепереработки. Якоюсь мірою це на гонку кінця 1940;х самого початку 50-х років у галузі створення створення атомної бомби. У ній участь сотні фірм зі світовими іменами і до 1980;му років було споруджено десятки демонстраційних і пілотних установок для газифікації, ожижения та термічним переробки угля.
У 1980;х років інтерес до углепереработке почав згасати. причин кілька. По-перше, політикою «батога і «медяника «США встановили контроль над країнами — виробниками нафти. Найбільш амбіційних (Ірак, Іран) покарали на науку іншим. Через війну зростання нафтових цін уповільнився. Протягом 1980;х років нафтові ціни знизилися з 40 дол. США за барель (що він відповідає приблизно 65 дол. США за барель в сучасних цінах що з поправкою на інфляцію) до рівня 9,13 дол. США за барель у грудні 1998 р. й у даний час вагаються в «коридорі «17−27 дол. США за барель. По-друге, ефективно спрацювали державні програми енергозбереження, що в результаті до зниження темпу зростання споживання і газу. Із середини 70-х років енергоємність одиниці ВВП розвинених країн знизилася на 22%, а нефтеемкость на 38% [3].
По-третє, динамічний розвиток нафтогазової галузі й масштабні роботи з розвідки нових родовищ нафти і є показали, що запаси вуглеводневої сировини насправді значно більше, ніж передбачалося. Останні 20 років щорічний приріст розвіданих запасів нафти і є випереджає їх споживання, і прогнозні терміни вичерпання регулярно відсуваються. По досить авторитетним даним глобальну заміну нафти вугіллям можна очікувати після середини XXI в., а заміну газу вугіллям — наприкінці століття. Якщо, звісно, не станеться прориву у розвитку технології ядерного синтезу. По-четверте, жодна з розроблюваних технологій не дозволила підвищити рентабельність процесу набуття рідкого палива з на такої міри, щоб «синтетична нафту «могла конкурувати із природною нефтью.
У результаті «епоха вугілля» не настала тож до переробці вугілля зменшився. Більшість програм згорнули, а решта — радикально урізані. Більше десятки проектів було завершено на стадії 5-летней готовності, тобто. за зміни кон’юнктури ринку вуглеводневої сировини можна протягом 5 років з урахуванням демонстраційних установок продуктивністю 10−60 т/ч за вугілля розгорнути промислового виробництва. Якщо від комерційного використання технологій прямого і непрямого ожижения на кінці 80-х рр. поки що відмовилися, то інтерес до газифікації вугілля хоча і зменшився, але з припинився. Наприклад, у низці регіонів, де природного газу немає або мало (Північна Америка, Китаю і ін.), використання з вугілля для синтезу метанолу і аміаку економічно виправдано й побудований ряд промислових предприятий.
У 90-х роках бурхливий розвиток отримала внутрицикловая газифікація для електроенергії, тобто. використання бінарного циклу, при якому горючий газ утилізується у газовій турбіни, а продукти згоряння використовуються при генерації пара для паровий турбіни. Перша комерційна електростанція з внутрицикловой газифікацію — Cool Water, США, прим. Каліфорнія, потужністю 100 МВт (60 т/ч за вугілля) була побудована 1983 р. Використовувався газогенератор Texaco із подачею палива на вигляді водо-угольной суспензії. Після 1993 р. за кордоном впровадили експлуатацію 18 електростанцій з всередині циклової газифікацію твердих палив потужністю від 60 до 300 МВт. На мал.1 наведено дані про світовому виробництву газу з твердих палив з 1970 р., а табл. 1.2 — структура його потребления.
Рис. 1. Сумарна потужність газогенераторних установок [pic].
Динамика споживання газу з на мире.
Таблиця 1.2 |Цільове |Використання в |Частка |Запроваджується в |Річний | |використання |2001 р., МВт по |в |експлуатацію до |приріст | | |газу |2001 |кінця 2004 р., |потужності | | | |р., %|МВт за газ |2002;2004 | | | | | |рр., % | |Хімічне |18 000 |45 |5 000 |9,3 | |виробництво | | | | | |Внутрицикловая |12 000 |30 |11 200 |31 | |газифікація | | | | | |(виробництво | | | | | |електроенергії) | | | | | |Синтез по |10 000 |25 |0 |0 | |Фишеру-Тропшу | | | | | |УСЬОГО |40 000 |100 |17 200 |14,3 |.
Наведені дані наочно демонструють прискорення динаміки залучення газифікації на світову промисловість. Підвищений інтерес до внутрицикловой газифікації на розвинених країн пояснюється двома причинами. По-перше, ТЕС з внутрицикловой газифікацію екологічно менш небезпечна. Завдяки попередньої очищенні газу скорочуються викиди оксидів сірки, азоту та твердих частинок. По-друге, використання бінарного циклу дозволяє істотно збільшити ККД електростанції і, отже, скоротити питома витрата топлива.
У табл.1.2 наведено характерні величини питомих викидів і ККД на ТЕС з внутрицикловой газифікацію й у ТЕС із традиційною спалюванням угля.
Величины питомих викидів і ККД на ТЕС з внутрицикловой газифікацію і з традиційним спалюванням угля.
Таблиця 1.2 |Параметри |Традиційна |ТЕС з внутрицикловой | | |вугільна ТЕС |газифікацію | |Концентрація шкідливих веществ|130 |10 | |в димових газах |150 |30 | |(для вугільної ТЕС — согласно|16 |10 | |Євростандарту), мг/м3 | | | |- SOx | | | |- NOx | | | |- Тверді частки | | | |Електричний ККД, % |33−35 |42−46 |.
Слід зазначити, що удільні капітальні витрати при використанні внутрицикловой газифікації становить приблизно 1500 дол. США за 1кВт з перспективою зниження до 1000−1200 дол. США, тоді як традиційної вугільної ТЕС удільні капітальні витрати становить приблизно 800−900 дол. США за 1 кВт. Зрозуміло, що ТЕС з внутрицикловой газифікацію твердих палив привабливіша за наявності екологічними обмеженнями на місці розміщення й під час використання досить дорогого палива, оскільки витрати на 1 кВт скорочується. Ці умови притаманні розвинених країн. Нині використання внутрицикловой газифікації твердого палива вважають найбільш найперспективнішим напрямом в энергетике.
Для сучасної хімічної в промисловості й енергетики потрібні газогенераторы з одиничної потужністю за вугілля 100 т/ч і більше. На початку 1970; x років у промисловому масштабі було реалізовано три типу газогенераторов [4].
. Cлоевые газогенераторы. Свого часу діяло більш 800 газогенераторов, зокрема понад 34 газогенераторов «Лургі» з одиничної потужністю за вугілля до 45 т/ч. Після 1977 р. введено в експлуатацію ще 130 газогенераторов «Лурги».
. Газогенераторы Вінклера з бурхливим шаром. Було споруджено понад 40 кримінальних апаратів з одиничної потужністю до 35 т/ч по углю.
. Пылеугольные газогенераторы Копперса-Тотцека. На початку 70-х років експлуатувалося понад 50 відсотків апаратів з одиничної потужністю до 28 т/час по углю.
Невипадково все найпотужніші газогенераторы мали німецьке походження. Причина — в тому, що у Німеччини немає власної нафти, але є великі запаси вугілля. У 1920;1940 рр. у Німеччині реалізували безпрецедентна в масштабах програма углепереработки з виробництвом моторних палив, металургійного палива, газів різного призначення і широкого спектра продуктів вуглехімії, включаючи харчові продукти. Під час Другої світової війни з допомогою рідких продуктів піролізу, прямого і непрямого ожижения вугілля вироблялося до 5,5 млн. тонн на рік моторного палива. Саме німецькі розробки на той час визначили на багато десятиліття стратегію розвитку технологій углепереработки, зокрема газифікації топлива.
Коли проаналізувати конструктивні особливості і принцип дії сучасних промислових газогенераторов (на сьогодні до промислового масштабу доведено ще більше десятка конструкцій газогенераторов), можна назвати чотири основних інженерних рішення. 1. Створення Фріцем Винклером (концерн BASF) в 1926 р. газогенератора з бурхливим шаром. Ця технологія стала основою сучасних процесів HTW (Hoch-Temperatur Winkler) і KRW (Kellogg-Rust-Westinghouse) та інших. 2. Розробка фірмою «Лургі «в 1932 р. слоевого газогенератора, працюючого під тиском 3 МПа. Використання підвищеного тиску для інтенсифікації процесу газифікації реалізовано майже переважають у всіх сучасних промислових газогенераторах. 3. Розробка Генріхом Копперсом і Фрідріхом Тотцеком в 1944;45 рр. пиловугільного газогенератора з рідким шлакоудалением. Перший промисловий апарат цього було побудовано 1952 р. у Фінляндії. Пылеугольный принцип газифікації з рідким шлакоудалением реалізований у промислових апаратах Destec, Shell, Prenflo, розроблених з урахуванням газогенератора КопперсаТотцека, в апараті Texaco та інших. Видалення шлаку в рідкому вигляді реалізовано слоевом газогенераторе BGL (British Gas- Lurgy), розробленому з урахуванням газогенератора Лургі. 4. Розробка фірмою Texaco в 1950;ті роки газифікаторів на переробку важких нафтових залишків. Усього побудовано більше ніж 160 таких установок. У 1970;ті роки розробили модифікація апарату Texaco для газифікації водо-угольной суспензії. Принцип подачі на апарат як водо-угольной суспензії використаний й у газогенераторе Destec.
Були спроби використовувати й низку інших технічних рішень для створення нових газогенераторов: використання зовнішнього теплоносія, у цьому числі тепла ядерного реактора; газифікація в розплавах солей, заліза, шлаку; двох — триступенева газифікація; газифікація в плазмі; каталитическая газифікація і др.
У 1930;1950 рр. розробили теоретичні основи физикохімічних процесів горіння і газифікації вугілля, виконані фундаментальні дослідження, які втратили актуальності до нашого часу. У цьому напрямі незаперечно лідерство радянських учених: А. С. Предводителева, Л. Н. Хитрина, Я. Б. Зельдовича, Н. В. Лаврова, Д.А.Франк-Каменецкого, Б. В. Канторовича і др.
Газифікації можуть бути піддані будь-які види твердих палив від бурих вугілля до антрацитов.
Активність твердих палив і швидкість газифікації значною мірою залежить від мінеральних складових, які у ролі каталізаторів. Відносне каталітичне вплив мікроелементів вугілля при газифікації то, можливо представлено рядом:
Mn>Ba>>B, Pb, Be>>Y, Co>Ga>Cr>Ni>V>Cu.
До основними параметрами, що характеризує окремі процеси газифікації твердих палив, може бути отнесены:
— тип газифицирующего агента;
— температура і тиск процесса;
— спосіб освіти мінерального залишку та її удаление;
— спосіб подачі газифицирующего агента;
— спосіб підвода тепла в реакційну зону.
Всі ці параметри взаємопов'язані між собою — і багато чому визначаються конструктивними особливостями газогенераторов.
Зазвичай газифицирующими агентами служать повітря, кисень і водяний пар. При паро-воздушном дуття зайвими встановленні воздухоразделения, що здешевлює процес, але виходить газ низькокалорійний, оскільки сильно розведений азотом воздуха.
Температура газифікації залежно від обраної технології може коливатися в межах 850−2000 градусів. діапазон тисків газифікації від 0.1 до 10.0 МПа і від. Газифікація під тиском краща у разі отримання газу, використовуваного потім їх у синтезах, що проводяться при високих тисках (знижуються видатки стиснення синтез-газа).
У газогенераторах з рідким шлакоудалением процес проводять при температурах вище температури плавлення золи (зазвичай вищі 1300−1400 градусів). «Сухозольные» газогенераторы працюють за більш низьких температурах, і зола потім із нього виводиться в твердому вигляді [6].
По способу подачі газифицирующего агента й за становищем палива при газифікації розрізняють слоевые процеси, у яких шар кускового палива продувається по противоточной схемою газифицирующими агентами, і навіть об'ємні процеси, у яких здебільшого по прямоточной схемою паливна пил взаємодіє зі відповідному дутьем.
Процес газифікації вугілля першого покоління: Лурьги, Вінклера і Копперс-Тотцека, досить добре вивчені і застосовують у промисловості, у деяких країнах щоб одержати переважно синтез-газу і замінника природного газа.
Більшість великих газогенераторов на твердому паливі працюють за прямому процесу із газифікацією палива на движущемся шарі. У цьому рух палива й дуття відбувається назустріч одна одній. За цією схемою подаване в газогенератор дутьё відбувається після шлковую зону, де вона кілька підігрівається, і далі вступає у зону горіння палива при нестачі кисню. Кисень дуття входить у реакції з вуглецем створюючи оксид і діоксид вуглецю одновременно.
Основними вадами процесу Лурьги є порівняно невеличка швидкість розкладання водяної пари дуття, необхідність використання водяної пари як охолоджуючого теплоносія, що внеможливить сплавления і спечення золи, і навіть вмісту у газі вищих вуглеводнів і фенолів [9].
Підвищення температури реалізовано процесі БГЛ з рідким шлакоудалением, розробленому фірмою «British gas «з урахуванням процесу Лурьги. В такий спосіб можна переробляти малореакционные і коксующие вугілля широкого гранулометрического складу. Виділені з газу смоли й пил повертають в газогенератор, причому кількість повернення може становити близько 15% вугілля. Процес перевірений на установки потужністю за вугілля 350 т на добу. У Ухтфильде. Процес вважається перспективним до застосування США, де роботи з його вдосконаленню [10].
Процес Вінклера грунтується на використанні псевдоожиженного шару палива. Принцип газифікації мелкозернистого палива на киплячому шарі у тому, що з певної швидкості дуття і крупности палива, лежачої на грати шар палива входить у движение.
Процес Вінклера забезпечує високу продуктивність, можливість переробки різних вугілля і що складом кінцевих продуктів. Але цього процесі великі втрати непрореагированного вугілля 20−30% (мас.), що виноситься з реактора, що веде до втрати виробництва тепла й зниження енергетичної ефективності процесу. Псевдоожиженный шар відрізняється великий чутливістю зміну режиму процесу, а низька тиск лімітується продуктивність газогенераторов [5].
За методом Вінклера за кордоном працюють 16 заводів (Іспанії, Японії, Німеччини, Кореї та інші). Газогенератор типу Вінклера має діаметр 5,5 м; висоту 23 метрів і максимальна одинична потужність діючих газогенераторов цього нині становить 33 тис. м3 газу годину [6].
У розроблений процес газифікації на апараті із наступною агломерацією золитак званий процесс-V, готовий до виробництва низкокалорийного газу, що може бути використаний у ролі сировини щоб одержати водню, аміаку чи метанолу, і навіть як палива. Газифікацію проводять у присутності кисню і водяної пари в псевдоожиженном шарі при тиску 5,7−7 МПа і температурі 980−1100 градусів. Вугільний пил відокремлюється в циклонах, причому із зовнішнього циклону пил повертається у газогенератор. Газ зовсім позбавлений рідких продуктів, що полегшує його очищення [6].
У результаті високої температури процесу задля газифікації може бути використані вугілля будь-якого типу включаючи спекающиеся, а отриманий газ бідний метаном і містить конденсирующиеся вуглеводнів, що полегшує його наступну очищення. До вад процесу можна віднести низька тиск, підвищений витрата кисню, необхідність тонкого розмелювання палива [5].
Перший промисловий газогенератор цього продуктивністю 4 тис. м3 за годину синтез газу, було створено 1954 року. За методом Коппер-Тотцека у світі працюють 16 заводів (Японія, Греція та інші). Газогенератор КопперТотцека з цими двома форсунками має діаметр 3−3,5 м; довжину 7,5 метрів і обсяг 28 м³ за годину [6].
Відомі невдалі спроби здійснити прямоточную факельную газифікацію за умов сухого золоудаления. Нині газифікацію вугільної пилюки проводять із рідким шлакоудалением. З цією метою отримали поширення газогенераторы вертикального типу, близькі по конструктивного оформленню до котельням агрегатам з пылеугольным спалюванням (Бабкок-Вилькокс) і газогенераторы із горизонтальним камерою газифікації (Копперс-Тотцек).
Великі робота зі створення газогенераторов для газифікації пылевидных палив під високим тиском із рідким шлакоудолением проводить американська фірма «Тексако», що є першопрохідником при застосуванні для газифікації водо-угольных суспензий. У газогенератор подають водну суспензію вугілля з концентрацією до70% (мас.), що спрощує рішення багатьох технічних запитань і дозволяє автоматизувати процес [5]. У 1984 року японської фірмою «Убе Индастриз» пущений найбільший у світі газогенератор Тексако потужністю за вугілля 1500 т дизпалива на добу, вырабатывающий газ для синтезу аміаку [7]. На заводі Aioi (Японія) 1987 року була споруджена пілотна установка продуктивністю 6 тонн на добу вугілля для газифікації водо-угольных су суспензії із процесу Тексако, як найбільш прогресивному. По проектним даним процес здійснюється під тиском 1,96−2,94 МПа за нормальної температури 1400 градусів із отриманням суміші газів з оксиду вуглецю, діоксиду вуглецю і водню, до 1991 року проводили науководослідження що з «Tokyo Electric Power Co» і це перероблено 533 тонни вугілля. Ступінь конверсії вуглецю досягала 100%. У синтез-газе утримувалося до 52,3% оксиду вуглецю, 33,2% водню, 12,7% діоксиду вуглецю. На повітряному дуття при підігріванні суспензії до 150 градусів ступінь конверсії досягала 72% [8].
Недоліком цього способу подачі вугілля є значний витрата тепла на випаровування води в газогенераторе, але вугілля не вимагає попередньої сушіння і виключається подача пара в газогенератор. Процес Тексако характеризується також підвищеною питомим витратою кисню 400- 450 м³ на 1000 м³ синтез-газу. Співвідношення вугілля: вода в суспензії коливається у різних межах від 70:30 до 45:55. Водо-угольные суспензії використовуються також і газифікації під тиском 10 МПа в газогенераторе Би-2эс. З іншого боку, при експлуатації устаткування газогенераторних станцій, у яких використовуються водо-угольные суспензії, виявлено труднощі для запобігання корозії циркуляційних насосів і инжекционных клапанів. Але ці недоліки здешевлюють хліборобські значимості, оскільки процес высокоэффективен [9].
Виробництво газу з твердих горючих копалин може здійснюватися з урахуванням двох технологічних прийомів: в газогенераторах наземного типу, і під землею (підземна газифікація угля).
Підземну газифікацію вугілля як засіб фізико-хімічного перетворення на горючий газ безпосередньо дома залягання вугільних пластів вперше почали реалізовувати у колишньому Совєтському Союзі у 1933 року. На початку 1960;х років експлуатували п’ять дослідно-промислових станцій «Подземгаз», в тому числі у Україні під час кам’яних вугілліЛисичанську в Донбассе.
Основні стадії процесу підземної газифікації вугіллябуріння з землі на вугільний пласт свердловин, поєднання цих свердловин каналами по вугільному пласту, і, нарешті, нагнітання один свердловини повітряного чи кисневого дуття й витягування з деяких інших свердловин що утворився газу. Газообразование в каналі відбувається поза рахунок хімічного взаємодії вільного і пов’язаного кисню з вуглецем і термічного розкладання угля.
Недоліки традиційної технології підземної газифікації вугіллянизька теплота згоряння одержуваного газу, з допомогою здійснення процесу на повітряному дуття, недостатня стабільність і керованість процесу, недостатня екологічна чистота підприємств підземної газифікації вугілля, насамперед через неповного уловлювання відповідних продуктів, великий обсяг бурових і підготовчих робіт, сягаючої в собівартості газу 30−35%; попри це традиційна підземна газифікація є надійної базою його подальшого совершенствования.
У найбільш інтенсивні роботи з підземної газифікації вугілля були розпочаті 1972 року. У перебігу 1972;1989 рр. було проведено більш тридцяти експериментів у різних гірничо-геологічних умовах. Якщо перші польові роботи проводили на повітряному дуття із отриманням низкокалорийного газу, то основне більшість наступних випробувань здійснювали на парокислородном дуття із отриманням среднекалорийного газу. Найкращі результати зі США можуть досягнуто при направленому підводі дуття до реакційної поверхні вугільного пласта, що підтверджує результати раніше проведених експериментів в нас у стране.
Нині найбільш детальне і кваліфіковане дослідження можливостей підземної газифікації на США здійснює компанія «Енерджі Интернейшинал». У доповіді її президента О.Г. Сінглтона проаналізовані результати підземної газифікації на навіть сформульовані деякі аспекты.
Основні висновки досліджень підземної газифікації вугілля следующие:
1) Експлуатаційні видатки виробництво генераторного газу при підземної газифікації вугілля менше, аніж за надземної газифікації угля.
2) Капітальні витрати, при близьких за величиною підприємств, набагато менш як при підземної газифікації угля.
3) Екологічні показники технології підземної газифікації вугілля виходять максимум за більш низьку продуктивність предприятия.
4) Синтез-газ при підземної газифікації вугілля досить успішно конкурує під аналогічною продуктом, одержуваним при паровим риформінгу природного газа.
Широкомасштабне промислове впровадження підземної газифікації на нашій країні можливе лише за умови підвищення ступеня керованості процесу, одночасному зниженні питомих витрат і збільшенні використанні вугільного пласта.
Основні резерви підвищення ефективності підземної газифікації угля.
— вдосконалення схеми газифікації до конструкції підземного газогенератора із єдиною метою активного і спрямованого взаємодії окислювача з реакційної поверхні вогневого забою, попри выгазовывания вугільного пласта.
— Зниження непродуктивних втрат тепла.
— Великі перспективи відкриваються перед підземної газифікації вугілля під час переходу великі глибини 700 метрів і более.
Американські дослідники провели техніко-економічне порівняння різних варіантів використання генераторного газу, отриманого при надземної газифікації вугілля й підземної газифікації вугілля. Відповідно до цих даним, застосування підземної газифікації вугілля дозволяє знизити експлуатаційні витрати з порівнянню з наземної газифікацію вугілля при виробництві генераторного газу. Практично більш 78% запасів кам’яних і майже 34% бурих вугілля України можна використовувати для підземної газифікації угля.
З узагальнення літературних і з урахуванням реальних умов втілення території України нами обрано схема паровоздушная газифікації на стаціонарному слое.
2.ФИЗИКО-ХИМИЧЕСКИЕ ОСНОВЫ ПРОЦЕССА.
Газифікацією називають високотемпературні процеси взаємодії органічної маси твердих чи рідких горючих копалин чи продуктів їх термічної переробки з повітрям, киснем, водяником пором, диоксидом вуглецю чи його сумішами, у яких органічна частина палива звертається до горючі газы.
Єдиним твердим залишком при газифікації повинна з’явитися негорючая частина вугілля — зола. Насправді вдасться повністю перевести органічну масу на газ, й у шлаку залишається частина займистою маси топлива.
Загальні принципи роботи апаратів для газифікації — газогенераторов—можно розглянути з прикладу найпростішого газогенератора, зображеного на рис 2.
Рис. 2. Схема роботи слоевого газогенератора: А — пристрій газогенератора 1 — затвор, 2 — корпус газогенератора, 3 — колосниковая решітка; 4 — чаша це про людське золы;
Б — зміна складу газу висоті газогенератора (паровоздушное дуття, збагачене киснем) — 1 — кисень, 2 — водяну пару, 3 — діоксид вуглецю, 4 — монооксид вуглецю, 5 — водень, 6 — метан і пари смоли; У — розподіл температур за висотою газогенератора.
Газогенератор подібного типу є вертикальну шахту з листової сталі, футерованной огнеупорным цеглою. У верхню частину його є завантажувальний люк, обладнаний затвором 1. У частині газогенератора встановлено колосниковая решітка 3, якою в шахту безупинно подається газифицирующий агент. Згори безупинно надходить вугілля. При подачі в газогенератор повітря на зоні, розташованої безпосередньо в колосникової грати (окислювальна зона, чи зона горіння), відбувається горіння твердого пального викопного із заснуванням ЗІ і СО2 по реакциям;
2С + О2 = 2СО + 218,8 МДж/кмоль углерода.
(2.1).
З + О2 = СО2 + 394,4 МДж/кмоль углерода.
(2.2).
Утворений діоксид вуглецю в відновлювальної зоні відновлюється новими порціями вуглецю в оксид углерода:
СО2 + З = 2СО— 175,6 МДж/кмоль углерода.
(2.3).
Якщо разом із повітрям в генератор подають також водяну пару, то відновлювальної зоні додатково протікають реакции:
З + Н2О = ЗІ + Н2 — 132,57 МДж/кмоль вуглецю (2.4).
З + 2Н2О = СО2 + 2Н2 — 89,5 МДж/кмоль вуглецю (2.5).
І тут утворений газ містить два горючих компонента: оксид вуглецю і водород.
У газової фазі можуть протікати та інші реакції. Так, можлива реакція між оксидом вуглецю і водяником паром:
ЗІ + Н2О=СО2 + Н2 + 43,1 МДж/кмоль.
(2.6).
При взаємодії ЗІ і Н2 може утворитися метан:
ЗІ + ЗН2 =СН4 + Н2О + 203,7 МДж/кмоль.
(2.7) адже за умов процесу піддається термическому распаду.
СН4 —> З + 2Н2 —71,1 МДж/кмоль.
(2.8) Поєднання всіх таких реакцій яких і визначає склад що утворюється газу, який змінюється за висотою газогенератора. Після окислительной і відновлювальної зон, званих разом зоною газифікації, виходять гарячі гази за нормальної температури 800—900 °З. Вони нагрівають вугілля, який піддається пиролизу в вышележащей зоні. Цю зону прийнято називати зоною піролізу, чи зоною полукоксования. Виходять з цього зони гази підігрівають вугілля у зоні сушіння. Разом ці дві зони утворюють зону підготовки палива. Отже, при слоевой газифікації поєднується термічна переробка палива й власне газифікація напівкоксу чи коксу, отриманого у зоні підготовки палива. Тому газ, отводимый з апарату, містить як компоненти, які утворилися у процесі газифікації, а й продукти піролізу вихідного твердого пального викопного (газ піролізу, пари смоли, водяну пару). При охолодженні відведеного з газогенератора газу відбувається конденсація смоли і води, які далі треба очистити і піддати переработке.
У процесі змінюється і склад твердої фази. До зони газифікації, як вище, надходить не вугілля, а кокс, та якщо з окислительной зони виводиться розпечений шлак, який охолоджується в чаші 4 із жовтою водою, яка виконує одночасно функції гідравлічного затвора, та був виводиться з апарату. З викладеного вище варто, що газифікація є складне поєднання гетерогенних і гомогенних процесів. Можливо, і послідовне, і паралельне перебіг цих реакцій. Механізм цих процесів досі до кінця не з’ясований. Тож якщо першої стадією взаємодії кисню і вуглецю у зоні горіння вважають освіту поверхового вуглецькисневого адсорбционного комплексу, то питання, що первинним продуктом взаємодії водяної пари з розпеченим коксом, предмет дискуссий.
У газогенераторе протікає ряд екзотермічних і эндотермических реакцій. Равновесия реакцій (2.1) і (2.2) зміщено убік освіти ЗІ і СО2. Рівновага эндотермических реакцій (2.3) — (2.5) у разі підвищення температури зміщено убік освіти відповідно ЗІ і Н2, але вихід зазначених продуктів (рівноважний) зменшується у разі підвищення давления.
Рівновага экзотермической реакції (2.6) зрушено убік освіти вихідних продуктів при високих температурах вище 1000 °З повагою та залежить від давления.
Освіта метану за реакцією (2.7) імовірніше у разі підвищення тиску газификации.
Термодинамические розрахунки дозволяють визначити равновесные склади газів залежно від температури і тиску газифікації. Проте скористатися результатами цих розрахунків для передбачення реального складу газів важко через значних відмінностей у швидкостях реакцій і сфери впливу на процес низки технологічних факторов.
Швидкість реакцій газифікації лімітується швидкістю хімічних перетворень у газовій фазі і поверхні твердої фази, і навіть швидкістю дифузії. При температурах 700—800 °З процес газифікації гальмується переважно хімічної реакцією, а при високих температурах вище 900 °З — переважно дифузією. У реальних умов сумарний процес газифікації відбувається у проміжної області, і його залежить від кінетичних і диффузионных факторов.
Процеси газифікації інтенсифікують шляхом значного підвищення температури, збільшення тиску газифікації (що дозволяє значно збільшити парциальные тиску реагують речовин), і навіть збільшення швидкості дуття, концентрації кисню в дуття чи розвитку реакційної поверхности.
Для наближення процесу газифікації до кінетичної області використовують тонкоизмельченный вугілля й ведуть процес при високих швидкостях газових потоков.
Вихід газу, його склад парламенту й теплота згоряння змінюються залежно від те, що використовують у ролі дуття. Назви газів, одержуваних при використанні різних видів дуття, наведено ниже:
Дуття Назва Сухий повітря Повітряний газ Смесь повітря і водяної пари Полуводяной газ Водяной пар (при зовнішньому підводі тепла) Водяної газ.
Суміш кисню і водяного пара.
Оксиводяной газ (газ.
парокислородного дутья).
Для зіставлення потягів і властивостей цих газів потрібно зробити такі припущення: газова суміш полягає з горючих компонентів (єдиний можливий баласт — азот повітря); газифікується чистий вуглець; не враховуються втрати тепла. Гази, відповідальні цим допущенням, називають ідеальними генераторными газами.
Одержувані практично генераторные гази відрізняються щодо виходу й складу від ідеальних. По-перше, вугілля не вважається чистим вуглецем, тому вихід горючих компонентів для 1 кг органічної маси вугілля завжди значно менше. Передусім це стосується молодим вугілля, який вирізняється містило велику кількість кисню, а тим паче до торфу.
По-друге, в генераторных газах завжди міститься помітне кількість СО2. Хімічне рівновагу в газогенераторах не досягається, тому зміст СО2 завжди перевищує рівноважну концентрацию.
По-третє, у зоні підготовки вугілля утворюються пари води та леткі продукти термічного розкладання, які входять у склад газа.
У кожному газі міститься більше чи менше азоту, що знижує реальну теплоту згоряння газу, бо за спалюванні газу частина тепла витрачається нагрівання балластного азоту. У реальних умов газифікації внаслідок нерівномірний розподіл зон і змішання потоків частина горючих газів згоряє із заснуванням водяного пара і СО2. З іншого боку, за умов газифікації неминучі різні теплові втрати (в довкілля, з палкими газами, зі шлаком і уносимым паливом). Тому фактичні значення термічних коефіцієнтів корисної дії значно менше величин, розрахованих для ідеальних умов. Процеси газифікації можна класифікувати за такими признакам:
1) по теплоту згоряння одержуваних газів (в МДж/м3): отримання газів з низькою (4,18—6,70), середньої (6,70—18,80) і високої (31—40) теплотою сгорания;
2) за призначенням газів: для енергетичних (безпосереднього спалювання) і технологічних (синтези, виробництво водню, технічного вуглецю) целей;
3) за величиною частинок використовуваного палива: газифікація крупнозернистых, мелкозернистых і пылевидных топлив;
4) на кшталт дуття: повітряний, паровоздушное, кисневе, парокислородное, паровое;
5) за способом видалення мінеральних домішок: мокре і сухе золовидалення, рідке шлакоудаление; 6) щодо тиску газифікації: при атмосферному (0,1 — 0,13 МПа), середньому (до 2—3 МПа) і високому тиску (вище 2—3 МПа);
7) характером руху газифицируемого палива: в псевдостационарном опускающемся шарі, в псевдоожиженном (киплячому) шарі, в движущемся потоці пылевидных частиц;
8) по температурі газифікації: низькотемпературна (до 800 °З), среднетемпературная (800—1300 °З) і високотемпературна (вище 1300 °С);
9) за балансом тепла у процесі газифікації: автотермический (стабільна температура підтримується з допомогою внутрішніх джерел тепла у системі) і аллотермические, т. е. що потребують підводі тепла із боку для підтримки процесу газифікації. Зовнішній підвід тепла можна проводити з допомогою твердих, рідких і газоподібних теплоносіїв [10].
3. ВИБІР, ОБГРУНТУВАННЯ І ОПИС ТЕХНОЛОГІЧНОЇ СХЕМЫ.
У цьому нами роботі прийнято метод паровоздушной газифікації на нерухомому (стаціонарному) шарі, дозволяють застосовувати вугілля майже всіх марок і реально отримувати хімічні продукти з мінімальним кількістю стадій. Застосовуючи паровоздушную газифікацію вугілля дозволяє здешевити отримання генераторного газу, причому процес йде при атмосферному давлении.
Узятий процес має низку істотних достоїнств над іншими способами газифікації вуглецю твердого топлива:
— можливість побудови агрегатів великий одиничної мощности;
— універсальність методу, що дозволяє застосовувати всі види вугілля, і навіть перехід із паро-воздушного дуття на кисневе і парокислородное дутье;
— невеличка металлоемкость;
— невелика кількість стадій на підготовку угля.
Основні параметри обраного процесу газифікації представлені у таблиці 3.1.
Основні параметри обраного процесу газификации.
Таблиця 3.1 |Показник |Процес газифікації | |Крупность вугілля, мм |1…3 | |Температури, градусів | | |- паровоздушная суміш |400 | |- газогенератор |950 | |Маса загружаемого вугілля, грн |50 |.
3.1. Принцип роботи лабораторної установки.
Вивчення процесу паровоздушной газифікації низькосортного Павлоградського вугілля проводили на лабораторної установці періодичного дії з газогенератором стаціонарного типу рис .
Газогенератор мав висоту 0.5 м, внутрішній діаметр 0.04 м. Обсяг реакційної зони становив 0.05 м.
Повітря компресором (1) направляють у парообразователь (5), де змішується з пором, що утворюються в парообразователе під час подачі води з резервуара (3). Отримана паровоздушная суміш заданої температури надходила в газогенератор (6), на грати до яку попередньо завантажувалася навішення вугілля. Температурний режим в реакторі підтримувався электронагревателем (7). Виходить з газогенератора газ охолоджувався в холодильнику (8), проходив сепаратор (9), фильтр-смолоотделитель (10) і далі іде на хроматографический аналіз (12). Контрольновимірювальна апаратура забезпечує облік витрати повітря, пара, виходу газу, завмер температур.
[pic].
Рис. 1. Схема лабораторної установки по газифікації вугілля. На схеме:
1-компрессор; 2-расходомер; 3-резервуар для води; 4-гидрозатвор; 5-парообразователь з пароперегревателем; 6-реактор (газогенератор (РР)); 7-электронагреватель для РР; 8-холодильник; 9-сепаратор; 10-фильтр; 11-газовый лічильник; 12-блок анализа.
3.2. Технічна характеристика угля.
Для експерименту застосовували збагачений концентрат Павлоградської ЦЗФ ш. Сташкова. Оцінка палива як сировини для газифікації проводилася підставі даних технічного аналізу. Для аналізу були взятий рядовий вугілля марки ДГ ш. Дніпровська і збагачений концентрат Павлоградської ЦЗФ марки ДГ ш. Сташкова.
Технічний аналіз вугілля виконували відповідно до ГОСТами 6379−59, 6383−52, 6382−53.
Вологість вугілля визначався за такою формулою W=((a-b)/a)*100%, де анавішення вугілля сушіння, р; внавішення вугілля після нього, г.
Зольність Аа=(в*100)/а ,% де увологість зольного залишку, г.
Вихід летючих речовин Va=((b*100)/a)-W ,%.
Отримані результати наведені у табл 3.1.
|Уголь |Технічний аналіз | | |Зольність |Вологість |Выхолд летючих речовин | |Рядовий |20.5 |6.7 |32.5 | |Збагачений концентрат |5.1 |9.8 |38.2 |.
Отже, внаслідок проводити дослідження встановлено, що дані вугілля відповідають трабованиям, висунутій до сировини для газифікації. Для проведення экспериментных досліджень процесу газифікації нами був обраний за змістом баластових компонентів, виходу летючих речовин збагачений концентрат Павлоградської ЦЗФ ш. Сташкова, фракційного состава.
3.3. Вплив швидкості подачі газифікуючих агентов.
Досліджувалося вплив швидкості подачі окислювачів на ступінь конверсії на умовах даної лабораторної установки. Серію дослідів проводили при постійному співвідношенні воздух/пар = 7:1 і температурі в газогенераторе 950 градусів. Тривалість процесу становила 75 хв. Отримані результати представлені на рис. 3.1 .
Оскільки швидкість газового потоку визначає час контакту окислювача з паливом, то встановлено, що з однаковою тривалості процесу, низька інтенсивність дуття не забезпечує достатньої конверсії вугілля. У водночас при перевищенні оптимальної швидкості подачі, реагують речовини не встигають взаємодіяти повністю. Через війну отримуваний газ містить більше негорючих компонентів у собі і рівень перетворення вугілля зменшується. З іншого боку, значно зростає ймовірність уноса.
Рис. 3.1. Вплив швидкості подачі газифікуючих агентів на ступінь перетворення угля.
З урахуванням вище викладеного, було обрано швидкість подачі газифікуючих агентів 1,7 мл/мин.
3.4. Аналіз отриманих данных.
Щоб вибрати собі оптимальний витрата показників газифікуючих агентів був проведена серія экспериментов.
Як вхідних змінних використовували витрата повітря і витрати пара.
Температура в реакційної зоні становила 950 градусів, газу виході з реактора 700 градусів. Швидкість зростання температури в газогенераторе 15 0С/мин. Паровоздушная дутьевая суміш підігрівалася до 400 0С.
У приведённой табл. 3.2 видно, що й збільшити витрати пара в дуття із 0,4 до до 0,6 кг на 1 кг робочого палива, ступінь розкладання пара зменшується. У цьому не вдома спостерігається зростання концентрації водню й відповідне зниження оксиду углерода.
Концентрація діоксиду вуглецю в газі зростає, т.к. реакція його освіти є джерелом теплоти реалізації эндотермических реакцій розкладання водяної пари, що зумовлює деякого зниження теплоти згоряння газу, і це частково компенсується рахунок збільшення змісту водню. З іншого боку, збільшується вихід газу. Також збільшення пара в дуття призводить до гальмування процесів піролізу, обумовлених спекаемостью вихідного вугілля. Це має передусім велике технологічне значення, т.к. підвищує стійкість роботи установки.
При збільшенні витрати повітря теплота згоряння одержуваного газу зменшується, хоча вихід його досить високий. У складі газу спостерігається вищу зміст азоту, діоксиду вуглецю, залишкового кислорода.
Отже, за браку окислювачів спостерігається низький рівень конверсії вугілля, а надлишок компонентів дуття веде для отримання більшого кількості газу, але низкокалорийного. Тому, необхідно зробити серію експериментів по газифікації визначення оптимальних умов. У сфері витрат, на яку припадало для повітря і кілька 2,5−3,5 м³ і 0,4−0,5 кг, соответственно.
Порівняльні результати дослідів газифікації збагаченого концентрату марки ДГ.
Таблиця 3.1 |№ |Показники |Досвід | | | |1 |2 |3 |4 |5 |6 |7 |8 |9 | |1 |Витрата дуття: | | | | | | | | | | | |повітря, м3/кг |2,5 |2,5 |2,5 |3,5 |3,5 |4,5 |4,5 |4,5 |3,5 | | |пара, кг/кг |0,4 |0,5 |0,6 |0,4 |0,6 |0,4 |0,5 |0,6 |0,5 | |2 |Склад сухого газу, %про.: | | | | | | | | | | | |CO2 |9,0 |9,7 |10,4 |12,8 |13,8 |17,8 |18,0 |18,2 |13,3 | | |H2 |12,5 |13,3 |14,2 |9,5 |10,7 |6,2 |6,4 |6,5 |10,1 | | |CO |21,5 |20,6 |19,7 |14,8 |13,7 |5,8 |5,6 |5,4 |14,2 | | |CH4 |2,3 |2,3 |2,2 |1,9 |1,8 |1,7 |1,7 |1,7 |1,9 | | |O2 |0,3 |0,3 |0,3 |0,4 |0,4 |0,8 |0,8 |0,8 |0,4 | | |N2 |54,4 |53,8 |53,2 |60,6 |59,6 |67,7 |67,5 |67,4 |60,1 | |3 |Вихід сухого газу, м3/кг |3,60 |3,65 |3,69 |4,57 |4,63 |5,23 |5,25 |5,27 |4,60 | |4 |Теплота згоряння газу, Qн МДж/м3 |4,90 |4,87 |4,82 |3,59 |3,54 |2,02 |2,01 |2,00 |3,57 | |5 |Вологість газу, г/м3 |49,17 |70,03 |87,54 |63,60 |98,67 |69,31 |87,04 |104,36 |81,17 | |6 |Ступінь конверсії вугілля, % |82,6 |83,9 |85,1 |88,7 |89,9 |91,1 |86,4 |87,8 |89,0 | |7 |Ступінь розкладання пара, % |54,38 |46,12 |44,85 |30,67 |27,47 |12,3 |11,74 |11,64 |28,73 | |8 |к.п.д. газифікації, % |63,72 |64,21 |64,30 |59,27 |59,21 |38,17 |38,12 |38,08 |59,32 |.
Порівняльні результати паровоздушной газифікації у вибраній області витрат окислителей.
Таблиця 3.2 |№ |Показники |Досвід | | | |1 |2 |3 |4 |5 |6 |7 |8 | |1 |Витрата дуття: | | | | | | | | | | |повітря, м3/кг |2,7 |2,7 |2,9 |2,9 |3,1 |3,1 |3,3 |3,3 | | |пара, кг/кг |0,4 |0,5 |0,4 |0,5 |0,4 |0,5 |0,4 |0,5 | |2 |Склад сухого газу, %про.: | | | | | | | | | | |CO2 |8,1 |9,0 |9,2 |9,9 |10,5 |11,1 |11,7 |12,2 | | |H2 |13,3 |14,1 |12,3 |13,2 |11,3 |12,0 |10,4 |11,0 | | |CO |22,3 |21,2 |20,9 |19,9 |18,8 |17,9 |16,8 |16,1 | | |CH4 |2,3 |2,3 |2,3 |2,3 |2,2 |2,2 |2,0 |2,0 | | |O2 |0,3 |0,2 |0,2 |0,1 |0,3 |0,3 |0,4 |0,4 | | |N2 |53,7 |53,2 |55,1 |54,6 |56,9 |56,5 |58,7 |58,3 | |3 |Вихід сухого газу, м3/кг |3,90 |3,94 |4,16 |4,20 |4,30 |4,34 |4,45 |4,48 | |4 |Теплота згоряння газу, Qн МДж/м3 |5,09 |5,04 |4,81 |4,78 |4,40 |4,37 |3,97 |3,95 | |5 |Вологість газу, г/м3 |52,63 |70,33 |54,55 |72,39 |58,52 |75,64 |61,05 |78,30 | |6 |Ступінь конверсії вугілля, % |89,4 |90,4 |93,1 |94,2 |92,0 |93,1 |90,2 |91,6 | |7 |Ступінь розкладання пара, % |49,47 |45,56 |45,9 |42,1 |40,02 |37,67 |35,44 |33,29 | |8 |к.п.д. газифікації, % |71,72 |71,73 |72,29 |72,53 |68,35 |68,51 |63,82 |63,93 |.
4.ОХРАНА ТРУДА.
4.1. Оцінка умов, у яких проводилася дослідницька работа.
Даним роботою передбачалося дослідження твердих горючих копалин зокрема вугілля, у дослідницькій лабораторії кафедри хімічної технології палива й вуглецевих матеріалів УДХТУ.
До групи физически-вредных промислових чинників під час проведення робіт у дослідницької лабораторії относят:
— підвищена температура 9500С поверхні устаткування, то, можливо отримані опік руки;
— підвищений рівень шуму 20 дБ, у слідстві роботи лабораторних установок, можуть призвести до їх зниження слуху, поразка центральної нервової системи, органів травлення і др.;
— небезпечний рівень напруги в електричної ланцюга устаткування (380.
У), замикання може відбутися через тіло людини, це дуже небезпечно, можливі смертельні случаи;
— підвищений рівень вібрації з посади лабораторних установок, негативно діє нервову систему, призводить до порушення координації руху чоловіка, можливі виброзаболевания.
Під час дослідження, у повітря приміщення може потрапляти газоподібні речовини: водень, оксид і діоксид вуглецю, метан.
Вдихуваний багато оксид вуглецю вступає у кров, зменшує приплив кисню до тканинам, підвищує кількість цукру на крові, послаблює подачу кисню до серця. У здорових людей цей ефект проявляється у зменшенні здібності виносити фізичні навантаження. Люди із хронічними хворобами серця може впливати протягом усього життєдіяльність организма.
За ступенем впливу на організм людини шкідливі речовини визначаються чотирма класу небезпеки. Клас небезпеки шкідливі речовини визначається залежність від ГДК шкідливих речовин у повітрі робочої зоны.
Оксид вуглецю: ГДК= 20 мг/м3, клас небезпеки — 4-й — речовина малоопасное.
Бензин: ПДК=100 мг/м3, клас небезпеки — 4-йречовина малоопасное.
4.2. Заходи з гарантуванню безпеки і здорових умов праці лаборатории.
Електричне устаткування у дослідницькій лабораторії харчується змінним струмом напругою 380/220 У, частотою 50 гц. За рівнем электроопасности лабораторія ставитися до категорії приміщень із підвищеної небезпекою, тому що має токопроводящий залізобетонний пол.
Основним способом по освіті електричної безпеки до лабораторій при застосуванні електричного устаткування це заземление.
Для заземлення устаткування передбачається трубчасте заземлення, розташоване по контуру будівлі, де знаходиться лаборатория.
Для штучного заземлення застосовують вертикальні електроди. Як вертикальних електродів застосовують сталеві труби завдовжки 2,5 м, діаметром 3 см.
Опір розтікання струму одного вертикального електрода визначають за такою формулою 2.1:
Re=[pic] (4.1).
Де pудільне опір грунту на місці розміщення заземления,.
100Ом*м, lдовжина трубчастого електрода, 2,5 м; dдіаметр трубчастого електрода, 0.03 м; tглибина розміщення середини електрода від землі, t=t0+l/2=2 м t0- відстань від верхньої точки трубчастого заземлення до землі, 0.75 м;
Re=[pic] Ом.
Оскільки Re>Rдоп, тобто. 36,73 Ом > 4 Ом, визначаємо кількість заземлений не враховуючи з'єднувального проводника:
n'=Re/Rдоп (4.2) де Rдоп — дозволене опір заземляющего устрою, 4 Ом. За формулою (2.2): n'=36.73/4[pic]10 Визначаємо кількість вертикальних електродів: n =n'/[pic]e ,.
(4.3) де [pic][pic]e — коефіцієнт використання вертикальних електродів, що враховує обопільне екранізування, [pic]e =0.55 (заземлення розміщено по контуру). За формулою (4.3):
n =10/0.55[pic]18 Визначаємо довжину сполучної смуги: z =a*n*l де аставлення відстані між електродами до довжині, 1, z=1*18*2.5=45 м.
Опір розтікання струму сполучної смуги, не враховуючи екранізування визначається за такою формулою :
Rш=[pic] (4.4).
где bширена сполучної смуги, 0.03 м, За формулою (4.4):
Rш=[pic] Ом.
Загальне опір заземляющего устрою визначається по формуле.
R з=[pic] (4.5) де [pic]шкоефіцієнт використання сполучної штанги, [pic]ш= 0.27 (заземлення розміщено по контуру). За формулою (4.5):
Rз=[pic] Oм Таким чином Rз.