Технология виробництва силікатного кирпича
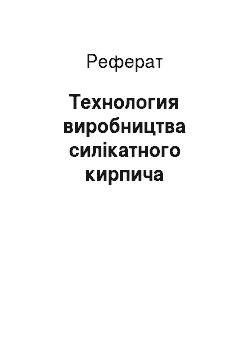
Силос є циліндричний посудину з листової сталі чи залізобетону; висота силосу 8 — 10 м, діаметр 3,5 — 4 м. У частині силос має конусоподібну форму. Силос розвантажується з допомогою тарельчатого питателя на стрічковий транспортер, у своїй відбувається большоё виділення пилу. При вылеживании в силосах маса часто утворює склепіння; причина цього — досить висока ступінь вологості маси, і навіть… Читати ще >
Технология виробництва силікатного кирпича (реферат, курсова, диплом, контрольна)
смотреть на реферати схожі на «Технологія виробництва силікатного цегли «.
Зміст. |Запровадження |2 | |1. Визначення проекту. |3 | |2. Технічна характеристика продукції. |4 | |3. Оцінка конкуренції, та ринків збуту. |9 | |4. Технологічна частина. | | |4.1 Сировину та її технологічна характеристика. |11 | |4.1.1 Пісок |11 | |4.1.2 Вапно |14 | |4.1.3 Вода |17 | |4.2 Опис технологічної схеми провадження з | | |обгрунтуванням технологічних процесів. | | |4.2.1 Підготовка силікатної маси. |18 | |4.2.2 Пресування сирцю |21 | |4.2.3 Процес автоклавной обробки |22 | |4.3 Вибір режиму роботи підприємства міста і план виробництва |25 | |продукції. | | |4.4 Розрахунок потреби сировини й матеріалів. |25 | |4.5 Вибір і розрахунок сировини й готової продукції |26 | |5. Механічна частина розрахунок основного технологічного | | |устаткування. | | | | | | | | | | | | | | | | | | | |.
Цегла є древнім будівельний матеріал. Хоча до сьогодення щонайширший поширення мав у багатьох країнах невипечений кирпич-сырец, часто з додаванням в глину різаної соломи, використання у будівництві обпаленого цегли також перегукується з глибокої давнини (будівлі в Єгипті, 3−2-е тисячоліття е.).
Нині більш 80% всього цегли виробляють підприємства цілорічного дії, серед які є великі механізовані заводи, продуктивністю понад 200млн.шт. в год.
Білгородська область є дуже перспективної для виробництва силікатного цегли, яке обгрунтовується як зручним розташуванням сировини, а й широкі можливості реалізації продукции.
Нині з’явилося багато спеціальних барвників для обробки фасадів, це дозволяє надати силикатному цеглині будь-який колір і відтінок. Широке поширення отримала оздоблення стін колотим силікатним кирпичом.
Різновидами силікатного цегли є известково-шлаковый і известково-зольный цегла. Відрізняються вони живуть від звичайного силікатного цегли меншою щільністю і найкращими теплоізоляційними властивостями. Для їх приготування замість кварцевого піску використовують шлаки чи золу.
У цьому курсової роботі виробництво силікатного цегли буде на прикладі Білгородського комбінату будівельних матеріалів (БКСМ) чи АТ «Будматеріали». Форму акціонерного товариства комбінат мав 1992 року. Основними видами продукції: цегла силікатний, вапно будівельна, крейда мелений, газо-силикатные блоки, газобетонні плити, мастика.
Основними цехами заводу є: силікатний цех, гірський цех, мелоизвестковый цех, цех технічного крейди, цех герметик. Як палива використовується природного газу, теплота згоряння якого дорівнює 7986 ккал/м3.
1.Определение проекта.
У цьому курсової роботі розглядається цех із виробництва силікатного цегли потужністю 100.000.000 прим. ум. кир. на рік. Силікатний цегла належить до групи автоклавных в’язких матеріалів. Силікатний цегла застосовують для кладки муру і стовпів у цивільному і промисловому будівництві, але не можна застосовувати для кладки фундаментів, печей, труб та інших частин конструкцій, що піддаються впливу високих температур, стічних та грунтових вод, містять активну углекислоту.
Силікатний цегла є екологічно чистим продуктом. По техникоекономічними показниками вона значно перевершує глиняний цегла. На його виробництво витрачається 15…18 годин, тоді як у виробництво глиняного цегли — 5…6 днів і більше. У двічі знижуються трудомісткість і витрати, а вартість — на 15…40%. Проте в силікатного цегли менше огнестойкость, хімічна стійкість, морозостійкість, водостойкость, трохи більше щільність і теплопровідність. У разі постійного зволоження міцність силікатного цегли знижується. Силікатний цегла виробляється кількох розмірів: o 250*120*65мм o 250*120*88мм, та інших видов.
Заради покращання якості і споживчих властивостей рекомендується виробляти, разом із стандартним известково-песчаным цеглою, известковозольний цегла, і навіть різні красители.
Известково-зольный цегла містить 20…25% винищити і 75…80% золи. Технологія виготовлення така сама, як і известково-песчаного цегли. Щільність — 1400…1600 кг/м3, теплопровідність — 0,6…0,7 Вт/(м З). Цегла використовують із будівництва малоповерхових будинків, і навіть для надбудови верхніх этажей.
Як засіб виробництва рекомендується силосний спосіб. По порівнянню з барабанним, цей спосіб економічніший, а технологія виробництва як проста. Далі в курсовому проекті буде докладніше обгрунтований силосний спосіб производства.
2.Техническая характеристика продукции.
Вимоги до технічним властивостями силікатного цегли змінюються в залежність від сфери його, зазвичай обумовленою будівельними нормами, неоднаковими у різних странах.
Міцність при стисканні і изгибе.
Залежно від краю міцності на стиснення силікатний цегла поділяють на марки 75, 100, 125, 150 і 200.
Марка цегли визначається її середнім межею міцності при стисканні, що становить зазвичай 7,5 — 35 МПа. У стандартах ряду розвинених країн (Росія, Канада, США), водночас, також регламентують межа міцності цегли на вигині. Пустотілі каміння середньої щільністю 1000 і 1200 кг/м3 можуть мати марки 50 і 25. У багатьох стандартів передбачено визначення міцності цегли в воздушно-сухом безпечному стані й лише англійському стандарті - в водонасыщенном.
У стандартах наведено середня міцність цегли даної марки і мінімальні значення краю міцності окремих цеглин проби, складові 75 — 80% середнього значения.
Водопоглощение — це з важливих показників якості силікатного цегли і є функцією його пористости, яка від зернового складу суміші, її формовочной вологості, питомої тиску при ущільнення. По ГОСТ 379– — 79 водопоглощение силікатного цегли має не меншим 6%.
При насиченні водою міцність силікатного цегли знижується по порівнянню з його міцністю в воздушно-сухом стані як і, як і в інших будівельних матеріалів, і це, зниження зумовлено тими самими причинами. Коефіцієнт розм’якання силікатного цегли у своїй залежить від його макроструктури, від мікроструктури цементуючого речовини і як звичайно менш 0,8.
Влагопроводность.
Вона характеризується коефіцієнтом влагопроводности [pic], який залежить середньої щільності цегли. При рср., приблизно рівної 1800 кг/м3, різноманітної вологості [pic] має такі значения:
Таблиця 1. |W, % |0,9 |2 |5 |8 |11 |14 |16,5 |18,5 | |[pic]*1|0 |3,6 |6,9 |8,7 |10,2 |14,5 |30 |73 | |0−5, | | | | | | | | | |кгм2 | | | | | | | | |.
Морозостойкость.
У нашій країні морозостійкість цегли, особливо лицьового, є поруч із міцністю найважливішим показником його довговічності. По ГОСТ «379 — 79 встановлено чотири марки цегли по морозостойкости. Морозостійкість пересічного цегли повинна бути щонайменше 15 циклів заморожування при температурі - 150С і відтаювання у питній воді за нормальної температури 15 — 200С, а лицьового — 25, 35, 50 циклів у залежність від кліматичного пояса, частин і категорій будинків, у його применяют.
Зниження міцності після випробування на морозостійкість проти водонасыщенными контрольними зразками на повинен перевищувати 20% для лицьового і 35% для пересічного цегли першої категорії і 15 і 20% для цегли вищої категорії качества.
Вимоги по морозостойкости до цеглині марок 150 і від пред’являються в тому разі, якщо його застосовують для обличкування будинків. У цьому цегла має відбутися 25 циклів випробувань без зниження міцності більш як на 20%. По польському стандарту силікатний цегла всіх видів повинен витримувати щонайменше 20 циклів заморожування і відтаювання без ознак руйнації. У стандартах Англії, навіть Канади для обличкування зовнішніх частин будинків, які піддаються зволоженню і заморожуванню, передбачається цегла підвищеної міцності (21 — 35 МПа), та його морозостійкість не нормируется.
Морозостійкість силікатного цегли залежить переважно від морозостойкости цементуючого речовини, що у своє чергу визначається її щільністю, микроструктурой і мінеральним складом новоутворень. За даними П. Р. Комохова, коефіцієнт морозостойкости цементного каменю з пресованого известково-кремнеземистого в’язальника автоклавной обробки коливається після 100 циклів від 0,86 до 0,94. У цьому зі збільшенням удільної поверхні кварцу з 1200 до 2500 см2/г коефіцієнт морозостойкости кілька зростає, а при подальшому збільшенні дисперсности кварцу він снижается.
Нині у зв’язку з застосуванням механічних захоплень для знімання і укладання в сировинну широту стали вводити значно більше кількість дисперсних фракцій підвищення його щільності та міцності. Внаслідок цього у структурі вироблюваного зараз силікатного цегли помітну роль грають вже микрокапилляры, у яких вода не замерзає, що значно підвищило б його морозостойкость.
Морозостійкість силікатних зразків залежить від виду гидросиликатов кальцію., цементуючих зерна піску (низкоосновных, высокоосновных чи його суміші). Після 100 циклів випробувань коефіцієнт морозостойкости зразків, попередньо минулих випробування на атмосферостойкость, дорівнював для низкоосновной зв’язки 0,81, высокоосновной — 1,26 й їхні суміші - 1,65.
Вивчалася також морозостійкість силікатних зразків, виготовлених на основі пісків різного мінерального складу. Були використані найбільш поширені піски: дрібний кварцовий, чистий і з додатком 10% каолинитовой чи монтмориллонитовой глини, полевошпатовый, суміш 50% полевошпатового і 50% дрібного кварцевого, великий кварцовий, у якому до 8% польових шпатов.
Кремнеземистая частина в’язальника складалася з тієї ж, але розмелених порід. Співвідношення між активної окисом кальцію і кремнеземом в вяжущем призначали виходячи з розрахунку отримання цементуючою зв’язки з величезним переважанням низькочи высокоосновных гидросиликатов кальцію чи його суміші. Кількість в’язальника у першій-ліпшій нагоді було постійним. Проте, морозостійкість силікатних зразків після 100 циклів заморожування і відтаювання залежить тільки від типу цементуючою зв’язки, а й від мінерального складу піску. Вплив мінерального складу піску особливо позначається за наявності зв’язки з низкоосновных гидросиликатов кальцію, як у суміш введено 10% каолинитовой чи монтмориллонитовой глини. Коефіцієнт морозостойкости при цьому падає до 0,82. При підвищенні основности зв’язки коефіцієнт морозостойкости складів, навпаки, підвищується до $ 1,5, що говорить про триваючої реакції між компонентами у процесі испытаний.
З даних видно, що добре виготовлений силікатний цегла необхідного складу є дуже морозостійким материалом.
Атмосферостойкость.
Під атмосферостойкостью зазвичай розуміють зміна властивостей матеріалу в результаті нею комплексу чинників: змінного зволоження і высушивания, карбонизации, заморожування і оттаивания.
М. М. Смирнов досліджував мікроструктуру свежеизготовленных і які пролежали в кладці 10 років зразків силікатного цегли Кореневського, Краснопресненського, Люберецкого і Мытищинского заводів. Він встановив, що у загальному разі лусочки новоутворень за 10 років частково заміщуються вторинним кальцитом внаслідок карбонизации гидросиликатов кальция.
Гаррісон і Бессі відчували багато років силікатний цегла різних класів міцності, заритий у ґрунт в цілому або наполовину, і навіть лежить у лотках з і на бетонних плитах, покладених на поверхню землі. Вони встановили, що зовнішній вигляд цеглин, які лежали 30 років у землі з дренирующим і дренирующим грунтом, мало змінився, та їх поверхню розм’якшилася, а й у цеглин, частково захованих у землю, відкрита частина залишилася без ушкоджень, хоч у випадках поверхню покрилася мхом.
Стан цеглин, що були 30 років на бетонних плитах, залежало від своїх класу, Так, виявилися без ушкоджень чи мали незначні ушкодження 95% цеглин класу 4 — 5 (28 — 35 МПа), 65% .цеглин класу 3 (21 МПа) і 25% цеглин класу 2 (14 МПа). Усі цеглини класу 1 (7 МПа) мали ушкодження вже 16 років. Усі цеглини, які лежали 30 років землі в лотках із жовтою водою, отримали ушкодження, і що нижче клас цегли, то раніше вони з’являлися: у цеглин класу 1 — через 8 років, класу 2 — через 19 років; класу 3 — через 22 року й для класів 4 — 5 — через 30 лет.
Міцність цеглин, які пролежали у землі 20 років, зменшилася приблизно, вдвічі. У цьому найбільше зниження міцності простежувалося в цеглин, які перебували у недренирующем глинистому грунті, а найменше — у цеглин, наполовину захованих у землю (стійма). За 20 років залежно та умовами перебування у грунті карбонизировалось 70 — 80% гидросиликатов кальцію, причому у основному коксування відбулася у перші 3 року. Отже, навіть за таких виключно жорстких випробуваннях силікатний цегла класів 3 і 4 виявилося досить стойким.
Загальновідомо, що міцність силікатного цегли після остигання підвищується. Саме тому за раніше що діяв ОСТ 5419 передбачалося визначати його міцність не раніше як за два тижні після виготовлення. Провели випробування цегли на зразках, відібраних від великого, числа партій (загалом 3 млн. прим.). По 10 цеглин з кожної проби розколювали навпіл, половинки різних цеглин складали попарно у певному послідовності і відчували відразу, а інші вкладали на стелажі і відчували у тій послідовності через 15 сут. У цьому було встановлено, що міцність цегли цей час зросла середньому становив 10,6%, вологість його зменшилася з 9,6 до 3,5%, а зміст вільної окису кальцію знизилося на 25% початкового. Таким чином, підвищення міцності силікатного цегли через 15 сут. після виготовлення можна пояснити спільним впливом його засихання і часткової карбонизации вільної извести.
Термографическими і рентгеноскопическими дослідженнями встановлено, що лише по випробування зразків у кліматичної камері помітних змін — у цементуючою зв’язці не відзначається, а після карбонизации гидросиликаты кальцію перетворюються на «карбонаты і гель кремнекислоты, є стійкими утвореннями, цементирующими зерна песка.
Отже, вважатимуться, що силікатний цегла, виготовлений із пісків різного мінерального складу з «використанням тонкомолотого известково-кремнеземистого в’язальника, є цілком атмосферостойким материалом.
Стійкість у воді й агресивних средах.
Стійкість силікатного цегли визначається ступенем взаємодії цементуючого його речовини з агресивними середовищами, оскільки кварцовий пісок стійкий до більшості середовищ. Розрізняють газові і рідкі середовища, у яких стійкість силікатного цегли залежить від своїх складу. З положень цих даних слід, що силікатний цегла нестійкий проти дії кислот, які розкладають гидросиликаты і карбонаты кальцію, цементуючі зерна піску, а також які у повітрі агресивних газів, парів і пилу при відносної вологості повітря більш 65%. Слід зазначити, що наведені орієнтовні дані ставляться до силикатному цеглині по ГОСТ 379– — 53, вимоги до якості якого значно нижчі від, ніж у ГОСТ 379– — 79.
Зразки силікатного цегли піддавали впливу проточній іпроточній дистильованої і артезіанської води протягом 2 років. У основному коефіцієнт стійкості зразків падає у перших 6 міс., та був залишається без зміни. Вищий коефіцієнт стійкості - у зразків, містять 5% меленого піску, причому більше низький — у зразків, до складу яких введено 5% меленої глини. Зразки, містять 1,5% меленого піску, займають проміжне становище: їх коефіцієнт стійкості становить приблизно 0,8, що треба визнати досить високою для пересічного силікатного кирпича.
Аналогічні зразки піддавали впливу сильно минерализованных грунтових вод, містять комплекс солей, і навіть 5%-ного розчину Na2SO4 і 2,5%-ного розчину MgSO4.
Кожні 3 міс. визначали міцність і коефіцієнт стійкості зразків, які перебували у різних розчинах. У розчині Na2SO4 міцність зразків знижується переважно у протягом 9 міс., а до 12 міс. вона стабілізується й у подальшому не змінюється. На відміну від надання цього міцність зразків, що були в розчині MgSO4, падає постійно, і вони починають інтенсивно руйнуватися вже з закінченні 15 мес.
Зазвичай, коефіцієнт стійкості зразків, містять 5% меленого піску, становить грунтових водах і розчині Na2SO4 приблизно 0,9, містять 1,5% меленого піску — 0,8, тоді як в зразків, у складі яких введено 5% меленої глини, в ґрунтовий води та 5%-ном розчині Na2SO4 він досягає 0,7. Отже, зразки з меленої глиною не можна визнати досить стійкими до впливу агресивних розчинів, і навіть м’якої іграшки і жорсткої воды.
Отже, силікатний цегла, до складу якої введено 5% меленого піску, має високої стійкістю до минерализованным грунтовою водам, крім розчинів MgSO4.
Жаростойкость.
До. Р. Дементьєв, нагревавший силікатний цегла при різної температурі протягом 6ч, встановив, щодо 200 «З його міцність збільшується, потім починає поступово згасати і при 600 «З сягає початкової. При 800 «З вона різко знижується внаслідок розкладання цементуючих цегла гидросиликатов кальция.
Підвищення міцності цегли за його прокаливании до 200 «З супроводжується збільшенням змісту розчинній SiO2, що говорить подальше протікання реакції між вапном і кремнеземом.
Базуючись на цих досліджень і досвіді експлуатації силікатного цегли в димарях і димових трубах дозволяється застосовувати силікатний цегла марки 150 для кладки димових каналів у, зокрема від газових приладів, для разделок, вогнезахисної ізоляції і обличкування; марки 150 з морозостойкостью Мрз35 — для кладки димарів вище горищного перекрытия.
Теплопроводность.
Теплопровідність сухих силікатних цеглин і каміння коштує від 0,35 до 0,7 Вт/(м «З) й у лінійної залежність від їх середньої щільності, мало залежачи від кількості і розташування пустот.
Випробування в кліматичної камері фрагментів стін, викладених з силікатних цеглин і каміння різної пустотности, показали, що теплопровідність стін залежить від щільності останніх. Теплоэффективные стіни виходять лише за використанні многопустотных силікатних цеглин і каміння щільністю не вище 1450 кг/м3 і акуратному віданні кладки (тонкий шар нежирного розчину щільністю трохи більше 1800 кг/м3, не що заповнює порожнечі в кирпиче).
3.Оценка конкуренції, та ринків збуту продукции.
Протягом кількох останніх років у Білгородської області намітилося стабільне підвищення попиту будівельні матеріали. Насамперед, це пов’язані з щодо сприятливим економічним кліматом області (місто Бєлгород зайняв чільне місце серед міст Росії у соціально-економічному аспекті). Завдяки цьому, підвищився попит на житло, що призвело до посиленому будівництва, як багатоквартирних будинків, так однієї сім'ї. До того ж, з різних чинників краще будівництво житлових приміщень саме з кирпича.
АТ «будматеріали» збувають силікатний цегла у всій Білгородської області, займаючи майже 1/3 ринку збуту силікатного цегли. Оскільки комбінат використовує для сировину бєлгородській області, транспортуючи його рейковим способом, знижуючи в такий спосіб питомі витрати і собівартість продукції, продукція заводу є попит. Ёмкость ринку зростає рахунок збільшення розширення будівництва у обласному центре.
Силікатний цегла з урахуванням золи ТЕС і порошкоподібної извести.
Питанням використання зол теплових станцій у виробництві силікатного цегли присвячено велика кількість досліджень. Проте найчастіше за все зола розглядали як компонент автоклавного в’язальника чи добавка (20 — 30%) в силикатную суміш. Золи застосовують у ролі кремнеземистого компонента в комірчаних бетонах, але донедавна мало використовувалися під час виготовлення силікатного кирпича.
У УралНИИстромпроекте проведено дослідження та розроблено технології виробництва известковозольного цегли. Сировинними компонентами є золошлаковая суміш Челябінської ТЭС-2 й пил газоочистки известеобжигательных печей Челябінського металургійного комбината.
Випробування проб пилу рукавных фільтрів і циклонів показали повне відповідність її вимогам стандарту до порошкоподібної будівельної вапна: зміст активних СаО+МgО — 60%, час і температура гасіння — відповідно 1,5−3 мін та 78−960С. Вапняна пил характеризується рівномірним зміною объема.
Зерновий і хімічний склади золошлаковой суміші, проби якої відбиралися з різних горизонтів золоотвала, представлені у табл. 2.
Таблиця 2. |Зміст зерен |Повні залишки (мас. %) на ситах, |Зміст частинок| |крупніша 5 мм |мм |менш 0,16 мм, | | | |мас. % | | |2,5 |1,25 |0,63 |0,315 |0,16 | | |3,7 — 5 |3 — |6 — 9 |11 — |22 — |58 — |40 — 42 | | |5 | |15 |27 |60 | |.
Насипна щільність золошлаковой суміші становить 760−1000 кг/м3, вологість 26 — 36%. По зерновому складу вона є среднезернистой, так як містить 73−78% зольной складової. Зразки зольной котра становила в суміші з портландцементом під час кипіння виявляють рівномірність зміни объема.
Залежність міцності известково-зольного сирцю і цегли від величини формовочной вологості і тиску пресування (табл. 3) аналогічна впливу зазначених чинників на властивості известково-песчаного цегли. Проте оптимальна формовочная вологість досліджуваної суміші становить 10 — 14 мас. %, що вдвічі перевищують величину, властиву традиційних сировинних материалов.
Таблиця 3. |Тиск пресування, |Межа міцності при стисканні, Мпа | |МПа | | | |Сирець |Цегла | | |При вологості суміші, мас. % | | |8 |10 |14 |16 |8 |10 |14 |16 | |20 |0,47 |0,46 |0,42 |0,3 |6,5 |7,9 |9 |8,6 | |25 |0,5 |0,54 |0,59 |0,41 |7,7 |10 |10,8 |9,9 | |30 |0,66 |0,69 |0,65 |0,44 |7,8 |12,4 |12,6 |12 |.
Міцність сирцю і цегли зростає паралельно зі збільшенням тиску пресування. Темпи зміцнення сирцю і зростання тиску пресування однакові. Міцність цегли в дослідженому діапазоні вологості суміші підвищується повільніше, ніж тиск прессования.
У известково-песчаных сумішей менш тісний залежність міцності сирцю від величини тиску пресування. Ці відмінності обумовлені, передусім, розвиненішою поверхнею частинок золошлаковой суміші, ніж в кварцевого піску однакового зернового складу. Розвинена поверхню визначає збільшити кількість контактів між частинками при ущільнення пов’язана з цим підвищення міцності зчеплення і механічного зачеплення. Частка їх у міцності сирцю з урахуванням кварцевого піску не перевищує 20 — 30%. Підвищення ролі названих чинників у формуванні міцності известково-песчаного сирцю і цегли характеризується збільшенні витрати в’язальника чи запровадження у сировинну суміш уплотняющих або укрупняющих добавок.
Наведені в табл. 3 дані отримані на известково-зольной суміші, що містить 5,6% СаО акт. Підвищення змісту винищити до 9,2% (СаО акт.) при вологості суміші 13,5% і тиску пресування 30 МПа сприяло зростанню міцності сирцю до 1,1 МПа і цегли до 16,3 МПа.
Вивчення кінетики автоклавного тверднення известково-зольного цегли показало, що він вимагає більш тривалому запаривании, ніж известковопіщаний цегла. Оптимальна тривалість изотермической витримки становила залежно від величини тиску пара в автоклаві: 8 — 9 год при 0,8 МПа., 6 — 8 год при 1 МПа, 4 — 6 год при 1,2 МПа.
Зразки цегли марок 100, 125 і 150 витримали комплексні випробування і мають такі характеристики: водопоглощение, мас. % … 18−22 марка по морозостойкости… F 25 зниження міцності при стисканні в водонасыщенном стані, % …18−20 щільність цегли, кг/м3… 1400- 1500 коефіцієнт теплопровідності, Вт/(м*К)…0,4−0,46 приріст теплопровідності на 1 мас. % вологості, Вт/(м До) … 0,015.
Цегла і сировинні компоненти успішно пройшли санітарно-гігієнічну экспертизу.
Зольний цегла є попит, що з поліпшеними споживчими властивостями (на 25−30% менша щільність тоді як традиційним силікатним цеглою і кращі теплозахисні властивості) і перевагу нижчої ціною цегли. Істотне зниження ефективного зольного цегли досягнуто як з допомогою використання дешевого техногенного сировини, а й завдяки відсутності дві такі енергоємних технологічних переділів, як випал винищити і помел вяжущего.
Перевагою даної технології є й екологічний ефект від участі застосування промислових відходів замість природних материалов.
У слідство без усього зазначеного такий цегла є найбільш ефективним та конкурентоспособным.
4.Технологическая часть.
4.1.Сырьё та її технологічна характеристика.
4.1.1Песок.
Основний компонент силікатного цегли (85 — 90% щодо маси) є пісок, тому заводи силікатного цегли розміщують, зазвичай, поблизу родовищ піску, і піщані кар'єри є частиною підприємств. Склад й поліпшуючи властивості піску визначають багато в чому характері і особливості технології силікатного кирпича.
Пісок — це недолуге скупчення зерен різного мінерального складу розміром 0,1 — 5 мм. За походженням піски поділяють на дві групи.- природні і штучні. Останні, своєю чергою, поділяють на відходи при роздрібненні гірських порід (хвости від збагачення руд, січка щебеневих кар'єрів тощо. п.), дробленые відходи від спалювання палива (пісок з паливних шлаків), дробленые відходи металургії (піски з доменних і ватержакетных шлаков).
За призначенням їх можна підрозділяти на піски для бетонних і залізобетонних виробів, кладочных і штукатурных розчинів, силікатного цегли. У даний курсової роботі висвітлюються лише даних про пісках для виробництва силікатного кирпича.
Форма і характеру поверхні зерен песка.
Ці чинники яких багато важать для формуемости силікатної суміші і міцності сирцю, і навіть впливають на швидкість реакції з вапном, що починається під час автоклавной обробки лежить на поверхні піщин. По даним У. П. Батурина, І. А. Преображенського і Твенхофелла, форма зерен піску то, можливо окатанной (близька до кулеподібної).; полуокатанной (більш хвилясті обриси); полуугловатой (неправильні обриси, гострі ребра і кути притуплені); незграбною (гострі ребра і кути). Поверхня піщин то, можливо гладкою, корродированной і регенерованої. Остання виходить при наростання на песчинках однорідної матеріалу, наприклад кварцу на кварцових зернах.
Класифікація песков.
У виробництві силікатного цегли класифікація пісків відіграє винятково важливу роль, оскільки він вирішальною мірою визначає формуемость сирцю з силікатних сумішей. Найкращою гранулометрией піску є, середні зерна розміщуються між великими, а дрібні - між середніми та великими зёрнами.
Більшість дослідників до пісках відносять зерна розміром 0,05 — 2 мм. В. В. Охотин виділяє у своїй дві фракції: піщані - 0,25 — 2 мм мелкопесчаные — 0,05 — 0,25 мм. П.І. Фадєєв поділяє пісок за величиною зерен п’ять груп: грубі (1 — 2 мм), великі (0,5 — 1 мм), середні (0,25 — 0,5 мм), дрібні (0,1 — 0,25 мм) і дуже малі (0,05 — 0,1 мм).
При змішанні однакових щодо маси трьох фракцій піску (великого, середнього та малого) з співвідношенням розмірів їх зерен 4:2:1 отримують суміш з високої пористість; при співвідношенні 16:4:1 пористість значно зменшується, при співвідношенні 64:8:1 — зменшується ще більше сильно, при співвідношенні 162:16:1 досягається найбільш щільна їх упаковка.
Встановлено, що оптимальна упаковка зерен силікатної суміші (з урахуванням наявності у ній тонкодисперсных зерен в’язальника) у межах співвідношень від 9:3:1 до 16:4:1.
Пористість песков.
Пористість рихло насипаних окатанных пісків зростає принаймні зменшення діаметра їх фракцій, а ущільненому вигляді вона однакова всім фракцій, крім дрібної. Пористість гострокутних пісків зростає у міру зниження їх розмірів, як і пухкому, і у ущільненому стані (табл. 4).
Таблиця 4. |Фракція, мм |Пористість пісків, %, може | | |пухкому |уплотнённом | | |окатанные |остроугольные|окатанные |гострокутні| |2 — 1 |36,06 |47,63 |33,4 |37,9 | |1 — 0,5 |36,3 |47,1 |33,63 |40,61 | |0,5 — 0,25 |39,6 |46,98 |33,42 |41,09 | |0,25 — 0,1 |44,8 |52,47 |34,35 |44,82 | |0,1 — 0,06 |44,53 |54,6 |39,6 |45,31 |.
З табл. 5 слід, що із зменшенням крупности пісків їх пористість зростає досить значно. Отже, здебільшого дрібні піски (крім добре окатанных) мають підвищену пористість як і пухкому, і у ущільненому стані, у зв’язку з аніж за використанні їх у виробництві силікатного цегли витрачають більше вяжущего.
Таблиця 5. |Пісок |Діаметр зерен, мм |Пористість, % | |Великий |2 — 1 |35 — 39 | |Середній |1 — 0,5 |40 | |Дрібний |0,5 — 0,25 |42 — 45 | |Пылеватый |0,25 — 0,05 |47 — 55 |.
Влажность.
У ґрунтах перебуває вода як пара, гігроскопічна, плівкова, капілярна, в твердому стані, кристаллизационная і хімічно пов’язана. Здатність грунту утримувати собі воду з допомогою молекулярних сил зчеплення називають молекулярної влагоемкостью, а вологість, відповідну максимальному смачиванию, — максимальної молекулярної влагоемкостью. Остання зростає у міру зменшення розміру фракцій піску, що це випливає з табл. 6.
Таблиця 6. |Матеріал |Фракція, мм |Максимальна | | | |молекулярна | | | |влагоёмкость | |Пісок: | | | |великий |1 — 0,5 |1,57 | |середній |0,5 — 0,25 |1,6 | |дрібний |0,25 — 0,1 |2,73 | | |[pic] |4,75 | |дуже дрібний |0,005 — 0 |10,18 | |Глина | |44,85 |.
Вологість піску значною мірою впливає його обсяг, що необхідно враховувати під час перевезенні піску в залізничних вагонах чи баржах, і навіть при намыве його за карти. Найбільший обсяг піски займають при вологості приблизно 5%.
Видобуток та обробка песка.
Видобуток піску. Усі силікатні заводи розміщують зазвичай поблизу родовища основної сировини — піску. Для БКСМ пісок видобувається в Новоольшанском кар'єрі. Перш ніж розпочати видобутку піску, місце видобутку — кар'єр — необхідно попередньо підготувати на експлуатацію. І тому знімають розкривні породи, т. е. верхній шар, у якому землю, сторонні предмети, глину, органічні речовини тощо. п. Якщо товщина шару трохи більше 1 м, то верхній шар знімають бульдозером чи скрепером з наступним транспортуванням їх у відвал. Якщо ж розкривні породи мають велику висоту, відстань досхочу значне, то розкривні роботи виробляють екскаваторами і відвозять порожню породу рейковим чи автомобільним транспортом. Видобуток піску розпочинається після зняття дробильних порід і виробляється одноковшовыми екскаваторами, обладнаними прямий лопатою з різної ємністю ковша.
Транспортування піску від забою. Для перевезення піску від забою в виробниче приміщення, т. е. до пісковим бункерам, користуються різним транспортом, саме: рейковим, автотранспортом, ленточными транспортерами тощо. д.
На Білгородському комбінаті використовується рейковий транспорт для перевезення сировини з карьеров.
Для перевезення піску від забою до пісковим бункерам вагонетками вкладається вузкоколійний рейковий шлях. Рейкові шляху зі свого влаштуванню поділяються на постійні й переносні; при розгалуженні й у переїзду з однієї шляху в інший встановлюють стрілочні переклади. У залежність від прийнятої системи руху складів існують такі різновиду шляхів: однопутная тупикова чи кільцева. Кар'єрні шляху необхідно підтримувати завжди у справному состоянии.
Найвища вимога до стану шляху: баластовий шар повинен мати задану товщину і відкоси; все шпали повинні прагнути бути щільно підбито у запобігання просадки шляху під час руху складів; шлях може бути отрихтован виключно за прямій чи за дзвоновидною кривою даного радіуса без відхилень в сторону.
При рельсовом транспорті пісок вантажать екскаватором в великовантажні вагонетки Т-54 з опрокидывающимся кузовом, ємністю 2,5 — 3 м³.
З вагонеток в пісочний бункера пісок розвантажують, перекидаючи кузов. Ця трудомістка операція нині ряд заводів механизирована.
При невеличкому відстані від забою до піщаних бункерів для транспортування піску використовують стрічкові транспортери, які є нескінченну стрічку з багатошарової прогумованої тканини, надягнуту на два циліндричних барабана (приводний і натяжной). Якщо привести у обертання одне із барабанів — приводний, то стрічка починає рухатися і приводить у рух другий барабан — натяжной. Під стрічкою встановлюють підтримують ролики. Що ширшим транспортерная стрічка, тим більше матеріалу вони можуть перекинути за одиницю часу. Щоб матеріал не скидався з стрічки, встановлюється певна швидкість движения.
Обробка піску. Пісок, що надходить з забою до його вживання у виробництво, може бути відсіяний від сторонніх домішок — каменів, грудочок глини, гілок, металевих предметів тощо. п. Ці домішки у процесі виробництва викликають шлюб цегли і навіть поломки машин. Тому над пісковими бункерами на БКСМ встановлюють барабанні грохоты. 4.1.2Известь.
Вапно є другої складової частиною сировинної суміші, необхідної виготовлення силікатного кирпича.
Сырьём для винищити є карбонатні породи, містять щонайменше 95% вуглекислого кальцію CaCO3. До них належать вапняк щільний, вапняковий туф, известняк-ракушечник, крейда, мармур. Всі ці матеріали є осадочную гірську породу, утворену головним чином результаті відкладення дно якої морських басейнів продуктів життєдіяльності тварин організмів. На БКСМ використовується крейда, видобутий робити кар'єру «Зелена поляна».
Вапняк складається з вапняного шпату — кальцита — і деякого кількості різних домішок: вуглекислого магнію, солей заліза, глини і ін. Від цих домішок залежить забарвлення вапняку. Звичайно буває білим чи різних відтінків сірого і жовтого кольору. Якщо зміст глини в вапняках більш 20%, всі вони звуться мергелів. Вапняки з великим змістом вуглекислого магнію називаються доломитами.
Мергель є известково-глинистой породою, що містить від 30 до 65% глинистого речовини. Отже, наявність у ньому вуглекислого кальцію не перевищує 35 — 70%. Зрозуміло, що мергелі не придатні виготовлення їх винищити і тому застосовуються з цією цели.
Доломиты, як і вапняки, ставляться до карбонатним гірським породам, що складається з мінералу доломіту (СаСО3*МgСО3). Оскільки вміст у них вуглекислого кальцію менш 55%, то тут для випалу на вапно вони також непридатні. При випалюванні вапняку на вапно вживають тільки чисті вапняки, які містять великої кількості шкідливих домішок як глини, окису магнію і др.
За розмірами шматків вапняки для випалу на вапно діляться на великі, середні й дрібні. Розміри шматків вапняку наведені у табл. 7.
Таблиця 7. |Показники |Розміри шматків | | |Великі |Середні |Дрібні | |Граничний найбільший розмір шматків в мм |400 |200 |80 | |Граничний найменший розмір шматків в мм |200 |80 |30 | |Дозволене зміст шматків нижче |3 |3 |3 | |граничного найменшого розміру в % | | | |.
Чинним ГОСТ 5331– — 55 встановлено правила приймання вапняків і методи їхньої організації випробування. Розмір партії вапняку встановлено у 100 т, причому залишок понад 50 відсотків т вважається також партией.
Зміст дрібниці в вапняку визначають, просіваючи 1 т, породи через грохоты.
Основним в’язким матеріалом для силікатних виробів є будівельна повітряна вапно. По хімічним складом вапно складається з окису кальцію (СаО) з — домішкою певної кількості окису магнію (МgО).
Розрізняють два виду вапна: негашеную і гашену; на заводах силікатного цегли застосовується негашена вапно. Технічні умови на повітряну негашеную вапно регламентовані ГОСТ 9179– — 59, відповідно до якому вапно поділяється втричі сорти. Вимоги до якості винищити викладені у табл. 8.
Таблиця 8.
Технічні умови на негашёную комовую вапно. |Показники |Сорти | | |1 |2 |3 | |Зміст активних СаО+MgO, вважаючи на суху речовину,| | | | |в % (щонайменше) |85 |70 |60 | |Зміст непогасившихся зерен в % (трохи більше) | | | | |Швидкість гасіння на хв: |10 |20 |25 | |быстрогасящаяся (до) | | | | |медленногасящаяся (більш) |20 |20 |20 | | |20 |20 |20 |.
При випалюванні вапняк під впливом високої температури розкладається на вуглекислий на газ і окис кальцію і втрачає 44% свого початкового ваги. Після випалювання вапняку виходить вапно комовая (кипелка), має сірувато-білий, іноді жовтуватий цвет.
При взаємодії комовой винищити із жовтою водою відбуваються реакції гідратації СаО+ Н2О = Са (ОН)2; МgО+Н2О=Мg (ОН)2. Реакції гідратації окису кальцію і магнію тривають від виділенням тепла. Комовая вапно (кипелка) в процесі гідратації збільшується обсягом і утворить пухку, білого кольору, легку порошкообразную масу гідрату окису кальцію Са (ОН)2. Для повного гасіння вапна необхідно додавати до неї води щонайменше 69%, тобто. на кожен кілограм негашеним винищити близько 700 р води. Через війну виходить завершена суха гашене вапно (пушонка). Якщо гасити вапно з головою води, виходить вапняне тесто.
До вапна пред’являють такі основні требования:
1) вапно мусить бути быстрогасящаяся, т. е. час гасіння її повинна перевищувати 20 хв.; застосування медленногасящейся вапна знижує продуктивність гасительных установок;
2) сума активних окислів кальцію і магнію (СаО+МgО) в винищити повинна складати щонайменше 85%;
3) зміст окису магнію в винищити на повинен перевищувати 5%, оскільки магнезиальная вапно гаситься медленно;
4) зміст недожженной винищити на повинен перевищувати 7%, оскільки він не активна і впливає твердіння цегли при запаривании, а є баластом, яке підвищує витрата вапна і удорожающим собівартість готової продукции;
5) вапно повинна бути перепаленої, позаяк у такому вигляді вона повільно гаситься і розтріскування цегли в запарочных казанах (автоклавах).
Вапно треба лише у критих складських приміщеннях, предохраняющих її впливу вологи. Не рекомендується тривалий час зберігати вапно надворі, позаяк у ньому завжди міститься невеличке кількість вологи, яка гасить вапно. Зміст повітря вуглекислого газу призводить до карбонизации винищити, т. е. з'єднанню з вуглекислим газом і цим часткового зниження її активности.
Погасившаяся вапно можна використовувати для силікатного цегли. Проте через те, що вона після гасіння перетворюється на малий і дуже легкий порошок (пушонку), застосування її пов’язані з великими утрудненнями: збільшуються втрати, підвищується витрата вапна і собівартість. 4.1.3Вода.
За виробництва силікатного цегли воду застосовують усім стадіях виробництва: при гасінні вапна, приготуванні силікатної маси, пресуванні і запаривании цегли-сирцю, отриманні технологічного пара.
Природна вода не буває абсолютно чистою. Найбільш чистої є дощова вода, але вона містить різні домішки, хто у неї з повітря (розчинені гази, пил, мікроорганізми). Розчинених речовин у воді небагато, й тому вона називається м’якої. Вода, яка містить дуже багато вуглекислих солей кальцію і магнію (карбонатних), називається жорсткої. Застосовувати жорстку води промислових цілях, наприклад щоб одержати технологічного пара, без попереднього умягчения її не можна, інакше під час кипіння води на стінках промислових котлів утворюється накип, яка виводить з експлуатації. При постачанні котлів м’якої водою подовжується термін їхньої службы.
Боротьба накипом в парових казанах здійснюється двома шляхами: обробкою води умягчением до надходження їх у парові казани і внутрикотловой обработкой.
Воду умягчают двома шляхами: термічним і хімічним. Термічний спосіб грунтується на розкладанні карбонатної жорсткості нагріванням води до 85 — 1100, у своїй утворюються труднорастворимые які в осад карбонат кальцію і гидроокись магнію. Такий спосіб зазвичай застосовується у поєднані із хімічним методом. Реагентами у своїй є їдкий натр і кальцинована сода.
Внутрикотловая обробка залежить від розчиненні накипу соляної кислотою (5 — 7-відсотковим розчином), навіщо через парові казани прокачивают розчин. Тривалість промивання залежить від рівня забруднення (але з більше — 10 — 20 годину.). Після закінчення кислотною промивання і після видалення кислоти казани промивають слабким розчином щелочи.
Вода при нагріванні перетворюється на пар; якщо воду нагрівати участь у закритому посудині, наприклад, у казанах, вона випаровуватиметься із поверхні і пар накопичуватиметься у просторі від поверхні води до того часу, поки між водою і що утворюється з її пором не встановиться динамічний рівновагу, щоб у одиницю часу стільки ж молекул води випаровується, як і переходить знову на рідина. Пара, що у рівновазі з рідиною, з якій він утворився, називається насиченим. У виробництві силікатного цегли гасіння силікатної є і для запарювання цегли-сирцю застосовується насичений пар, який в котельных.
4.2.Описание технологічної схеми провадження з обгрунтуванням технологічних процесів. 4.2.1Подготовка силікатної массы.
Дозування компонентов.
Для отримання сировинної суміші (силікатної маси) необхідного якості необхідно правильно дозувати их.
Дозу вапна в силікатної масі визначають за кількості винищити в ній, а, по змісту тій її активній частині, що братиме участь в реакції тверднення, т. е. окису кальцію. Тому норму вапна встановлюють насамперед залежно від неї активности.
На кожному заводі зазвичай її встановлюють дослідним шляхом. Середнє зміст активної вапна в силікатної масі одно 6 — 8%. При вживанні свежеобожженной винищити без сторонніх домішок і недожога кількість її можуть бути зменшено; Якщо ж в вапна міститься велика кількість недожженного каменю й сторонніх домішок, і навіть якщо вапно довго зберігалася надворі, норма їх у суміші слід збільшити. Як недостатнє, і зайве кількість вапна в силікатної масі тягне у себе небажані наслідки: недостатнє зміст винищити знижує міцність цегли, підвищений вміст робить дорожчою собівартість, але водночас не надає позитивної дії на якість. Активність вапна, що надходить виробництво часто змінюється; тому щоб одержати маси, зі заданої активністю потрібно часто змінювати у ній кількість винищити. На БКСМ використовується вапно активністю 70 — 85%.
Практично з виробництва користуються заздалегідь укладеними таблицями, що дозволяє визначати дозування вапна в кг на одиницю продукції (1 м3 силікатної маси чи 1000 прим. цегли) — таблиця 9.
Таблиця 9. |Активність |Активність силікатної маси, % | |вапна, % | | | |6 |6,5 |7 |7,5 |8 |8,5 | |60 |378 |409 |440 |472 |504 |535 | |65 |349 |378 |407 |437 |466 |495 | |70 |324 |351 |378 |405 |432 |459 | |75 |303 |328 |353 |378 |403 |428 | |80 |283 |306 |330 |353 |378 |400 | |85 |267 |289 |300 |333 |356 |378 |.
Необхідна кількість піску отмеривается за обсягом, а вапно на вагу з допомогою бункерних весов.
Крім вапна і піску, складовою силікатної маси є вода, необхідна до повного гасіння винищити. Вода також надає масі пластичність, необхідну пресування цегли-сирцю, і це створює сприятливе середовище для перебігу хімічної реакції тверднення цегли при його запаривании.
Кількість води має точно відповідати нормі. Недолік води призводить до неповного гасіння винищити; надлишок води, хоч і забезпечує повне гасіння, але створює який завжди допустиму вологість силікатної маси. Волога частково надходить із піском, кар'єрна вологість якого коливається залежно від кліматичних умов. Кількість води, необхідне доведення вологості силікатної маси до потрібної величини, практично також можна заздалегідь розрахувати залежно від кар'єрної вологості що надходить у виробництві піску та таблицю визначення витрати води на одиницю продукції (1000 прим. цегли чи 1 м³ силікатної маси). Кількість води (в л), потрібне для доувлажнения силікатної маси (на 1000 прим. цегли), залежно від вологості піску, наведено в табл. .
Таблиця 10. |Вологість |Потрібна вологість силікатної маси, % | |піску, % | | | |5 |5,5 |6 |6,5 |7 | |3 |74 |92 |111 |130 |148 | |3,5 |55 |74 |92 |111 |130 | |4 |37 |55 |74 |92 |111 | |4,5 |18 |37 |55 |74 |92 | |5 |— |18 |37 |55 |74 | |6 |— |— |— |18 |37 |.
Загальний витрата води щоб одержати силікатної маси необхідного якості становить близько 14% (ваги маси) і розподіляється так (в%): на гасіння извести…2,5 на випаровування при гашении…3,5 на зволоження массы…7,0.
Хімічна реакція гасіння винищити протікає по формуле:
СаО+Н2О=Са (ОН)2.
Іноді підвищення міцності цегли в силикатную масу вводять різні добавки як меленого піску, глини і др.
Щоб досягти правильного співвідношення складових компонентів, застосовують спеціальні дозировочные пристосування. Через те що приготування силікатної маси необхідного якості є одним із найважливіших операцій на технологічному процесі виробництва силікатного цегли, обов’язково регулярно перевіряти в лабораторіями її свойства.
Визначення швидкості гасіння винищити слід щонайменше двох разів у зміну; у разі подовження часу гасіння вапна необхідно негайно змінити режим гасіння шляхом подовження циклу приготування силікатної массы.
Визначення активності вапна (зміст СаО+МgО) необхідно проводити також двічі на зміну і з активністю вапна змінювати дозування її щоб одержати нормальної силікатної массы.
Активність і вологість силікатної маси слід перевіряти через кожні 1 — 1,5 часу й у разі відхилення одержуваних показників від заданих негайно змінювати дозування вапна і воды.
Приготування силікатної массы.
Известково-песчаную суміш готують двома шляхами: барабанним і силосным. На Білгородському комбінаті застосовується силосний спосіб, і це цілком обосновано.
Силосний спосіб приготування маси має значних економічних переваги перед барабанним, бо за силосовании маси на гасіння винищити не витрачається пар. З іншого боку, технологія силосного способу виробництва значно простіше технології барабанного способу. Підготовлені вапно і пісок безупинно подаються живильниками в заданому співвідношенні в одновальную мішалку безперервного дії і воложаться. Перемішана і зволожена маса вступає у силосы, де витримується від 4 до 10 годину., протягом яких вапно гасится.
Силос є циліндричний посудину з листової сталі чи залізобетону; висота силосу 8 — 10 м, діаметр 3,5 — 4 м. У частині силос має конусоподібну форму. Силос розвантажується з допомогою тарельчатого питателя на стрічковий транспортер, у своїй відбувається большоё виділення пилу. При вылеживании в силосах маса часто утворює склепіння; причина цього — досить висока ступінь вологості маси, і навіть ущільнення і часткове твердіння її за вылеживании. Найчастіше склепіння утворюються у нижніх шарах маси, біля підніжжя силосу. Для кращої розвантаження силосу необхідно зберегти можливо меншу вологість маси. З досвіду роботи аналізованого заводу встановлено, що силосы розвантажуються задовільно лише за вологості маси 2 — 3%. Силосна маса при розвантаження більш порошить, ніж маса, отримана по барабанному способу; звідси важчі умови до роботи обслуговуючого персонала.
Перераховані вище негативні моменти в повному обсязі, але у якийсь мері усуваються механізацією разгрузки.
Робота силосу протікає так. Усередині силос розділений перегородками втричі секції. Маса засипається однієї із секцій протягом 2,5 годину., стільки потрібно й у розвантаження секції. На момент заповнення силосу нижній шар встигає вылежаться протягом тієї самої часу, тобто. близько 2,5 годину. Потім секція выстаивается 2,5 години, і після цього розвантажують. Отже, нижній шар гаситься майже п’ять годину. Оскільки розвантаження силосів відбувається знизу, а проміжок між разгрузками становить 2,5 години, те й всі наступні верстви також витримують в протягом 5 годину. в безупинно діючих силосах. Що стосується освіти зводу при розвантаженні силосу і припинення надходження маси на стрічковий транспортер категорично забороняється робочим перебувати у силосе.
Для полегшення розвантаження періодично включають вібратор, укріплений на стінці силосу; і вже цим зменшують прилипання маси до стінок. За більш серйозних зависаниях маси силосах її шурують ломами через розвантажувальні окна.
На БКСМ розвантаження маси з бункерів механізована. Розподільні щітки на транспортерної стрічці піднімають механічним пневмоподъемником. Над транспортерної стрічкою, яка подає силикатную масу, встановлено розподільні щітки, котрі переміщалися вертикально по рамі. Опускання і підйом щіток над стрічкою здійснюється з пульту управління, який оснащений світловий сигналізацією і пристроєм, регулюючим подачу повітря на пневмоцилиндры. 4.2.2.Прессование сырца.
На якість цегли в основному з його міцність найістотніше впливає тиск, якому піддається силікатна маса під час пресування. Через війну пресування відбувається ущільнення силікатної маси. Старанно ущільнити сирець — отже довести до мінімуму вільне простір між частинками піску, зблизивши їх настільки, що вони поділялися друг від друга лише найтоншим шаром в’язальника речовини. Таке зближення зерен піску при подальшої водо-тепловой обробці цегли-сирцю в автоклаві забезпечує отримання щільного і міцного конгломерата.
На Білгородському комбінаті будівельних матеріалів 9 пресів РМ — 816 і два преса СМЗ — 152, які працюють під тиском 20 Мпа. Продуктивність преса — 2680 штук умовного цегли за 1 час.
У час пресування силікатної маси виникають сили опору стиску із боку зерен піску, що перешкоджають максимальному зближенню зерен. Сила тертя маси про стінки форми і зерен друг про друга долається шляхом застосування тиску. Тому тиск має розподілятися рівномірно у всій площі прессуемого вироби. Пресування необхідно вести лише до певної межі, бо за збільшенні тиску вище граничного у своїй з’являються пружні деформації, які зникають після зняття тиску призводять до руйнації сирцю. Отож не можна підвищувати тиск до появи деформаций.
Істотне значення має тут швидкість, з якою виробляється тиск. Приміром, ударне швидке додаток зусилля викликає не ущільнення, а руйнація структури вироби. Тож подолання внутрішніх сил тертя тиск має прикладатися плавно із збільшенням. Робоча тиск у пресах застосовується рівним 150 — 200 кг/см2.
На нормальну роботу преса, отже, отримання цегли хорошої якості великий вплив надає зміст вологи в силікатної масі. У оптимальних умовах пресування цегли вологість маси повинна складати б — 7% ваги сухого речовини і постійно контролюватися. Збільшення вологості вище оптимальної дає можливості спресувати сирець, зняти його з столу пресу КПРС і вкласти на вагонетку; зменшення вологості призводить до того, що спресований сирець важко зняти з столу преса: він розламується під впливом власної ваги. З іншого боку, недостатнє зміст вологи в сирці позбавляє вапно необхідної пластичності, які забезпечують зв’язок між окремими зернами песка.
Процес пресування цегли складається з таких основних операцій: наповнення пресових коробок масою, пресування сирцю, виштовхування сирцю на поверхню столу, зняття сирцю зі столу, укладання сирцю на запарочные вагонетки.
Силікатна маса, приготовлений в силосах, передається з допомогою транспортерної стрічки в бункер над пресс-мешалкой преса. Подача маси пресс-мешалку повинна так регулюватися, щоб він займала приблизно ¾ обсягу пресс-мешалки. Якщо що надходить маса має як низьку вологість, ніж потрібно, доувлажнение її виробляється у пресс-мешалке, навколо стінок якої вкладається трубопровід із дрібними отворами з її довжині, спрямованими вниз.
Сила струменя котра надходить по трубці води регулюється прессовщиком при допомоги вентиля. Зволожена маса ножами пресс-мешалки під час обертання їх подається в пресові коробки через отвори в дні пресс-мешалки. При повороті столу преса коробки, наповнені масою, переміщаються на певний куток і займають становище між прессующим поршнем і верхньої стороною плитки контрштампа. Під тиском поршень поступово піднімається і виробляється пресування сырца.
У час пресування стіл преса зупиняється, а ножі пресс-мешалки обертаються і заповнюють масою таку пару пресових коробок. Після пресування стіл преса повертається те щоб штампи преса разом із сирцем підійшли до выталкивающему поршневі. Сирець виштовхується поршнем в вертикальному напрямі; верхня пластина штампа при виштовхуванні виходить з пресових коробок на 3 — 5 мм вище рівня столу. Потім выталкивающий поршень опускається вниз початкове становище. Після зняття пари цеглин двома съемщиками-прессовщиками стіл повертається і штампи підбиваються під механічну щітку для очистки.
Верхні пластини очищаються від налиплої маси, штампи опускаються на величину наповнення пресових коробок та циклу починається снова.
Силікатний цегла за величиною повинен відповідати вимогам ГОСТ 379– — 53; у разі відхилення від встановлених розмірів сирець вважається браком.
Щільність пресування сирцю досягається виключно зміною величини наповнення пресових коробок: що більше висота наповнення, тим вище щільність сирцю і, навпаки, що менше висота наповнення коробок, тим нижче щільність сирцю. Під час пресування треба пильнувати те, щоб сирець виходив однаковою щільності; цього потрібно підтримувати висоту наповнення пресових коробок однаковою. Ножі пресс-мешалки мали бути зацікавленими закріплені від дна і стінок на однаковому расстоянии.
Після пресування отримані цеглини автоматом-укладчиком вкладаються на вагонетки, які транспортуються в автоклави, де проводять тепловолога обробка цегли. 4.2.3.Процесс автоклавной обработки.
Щоб надати необхідної міцності силикатному цеглині його обробляють насиченим пором; у своїй температурное вплив узгоджується з обов’язковим наявністю в кирпиче-сырце водного середовища, яка сприяє перебігові реакції освіти цементуючих речовин з максимальної інтенсивністю. Насичений пар використовується з температурою 1750 за відповідного такий температурі тиску у вісім атм.
Автоклав є трубу довжиною 19 м і з діаметром 2 м, місткістю 12 вагонеток (V=5965 м3). Режим роботи автоклава: o 1,5 годину. — підйом пара, o 5−6 годину. — витримка, o 1−1,5 годину. — спуск пара.
У процесі автоклавной обробки, т. е. запарювання цегли-сирцю, розрізняють три стадии.
Перша стадія починається з впуску пара в автоклав і закінчується в разі настання рівності температур теплоносія (пара) і оброблюваних изделий.
Друга стадія характеризується сталістю температури і тиску в автоклаві. Саме тоді отримують максимальне розвиток всі ті физикохімічні процеси, що сприяють освіті гидросиликата кальцію, отже, і твердению оброблюваних изделий.
Третя стадія починається із припинення доступу пара в автоклав і включає час остигання виробів на автоклаві досі вивантаження потім із нього готового кирпича.
У першій стадії запарювання насичений пар з температурою 1750 під тиском 8 атм. впускають в автоклав з сирцем. У цьому пар починає псуватися і конденсуватися на кирпиче-сырце і стінках автоклава. Після підйому тиску пар починає проникати у дрібні пори цегли і перетворюється на воду. Отже, до води, введеної під час виготовлення силікатної маси, приєднується вода від конденсації пара. Утворений порах конденсат розчиняє присутній у сирці гідрат окису кальцію і інші розчинні речовини, що входять до сирець. Відомо, що пружність пара розчинів нижче пружності пара чистих розчинників. Тому припливаючий в автоклав водяну пару буде конденсуватися над розчинами вапна, прагнучи понизити їх концентрацію; це додатково зволожує сирець в процесі запарювання. І третьої причиною конденсації пара в порах сирцю є капілярні властивості материала.
Роль пара при запаривании зводиться лише збереженню води в сирці в умовах високих температур. За відсутності пара відбувалося б негайне випаровування. води, отже, висихання матеріалу і повний припинення реакції освіти цементуючого речовини — гидросиликата.
З моменту, як і автоклаві буде досягнуто найвища температура, т. е. 170 — 2000, настає друга стадія запарювання. У той час максимальне розвиток отримують хімічні і обов’язкові фізичні реакції, які ведуть до утворення моноліту. На той час пори сирцю заповнені водним розчином гідрату окису кальцію Са (ОН)2, безпосередньо соприщо стосується з кремнеземом SiO2 песка,.
Наявність водного середовища і високої температури викликає лежить на поверхні піщин деяке розчинення кремнезему, зчинений розчин вступає в хімічну реакцію з утвореними протягом першого стадії запарювання водним розчином гідрату окису кальцію і цього виходять нові речовини — гидросиликаты кальция:
[pic].
Спочатку гидросиликаты перебувають у коллоидальном (желеобразном) стані, але поступово викристалізовуються і, перетворюючись на тверді кристали, зрощують піщини між собою. З іншого боку, з насиченого водного розчину гідрат окису кальцію також випадає як кристалів і своїм процесом кристалізації бере участь у зрощування песчинок.
Отже, на другий стадії запарювання освіту гидросиликатов кальцію і перекристалізація їх і гідрату окису кальцію викликають поступове твердіння кирпича-сырца.
Третя стадія запарювання протікає із припинення доступу пара в автоклав, т. е. починається падіння температури в автоклаві, швидке чи повільне залежно від ізоляції стінок автоклава і наявність перепуску пара. Відбувається зниження температури вироби і збіднення його водою, т. е. вода випаровується і підвищується концентрація розчину, що у порах. З підвищенням концентрації гідрату окису кальцію і зниженням температури цементуючого речовини силікати кальцію стають більш основними, і це триває до того часу, поки цегла нічого очікувати вивантажений з автоклава. У результаті посилюється твердіння гидросиликатов кальцію і, отже, підвищується міцність силікатного цегли. Одночасно плівки цементуючого речовини сильніше збагачуються випадаючого з розчину гидратом окису кальция.
Механічна міцність силікатного цегли, выгруженного з автоклава, нижче тієї, яку він одержує при наступному выдерживании його за повітрі. Це що відбувається карбонизацией гідрату окису кальцію з допомогою вуглекислоти повітря по формуле.
Са (ОН)2+СаСО2=СаСО3+Н2О.
Отже, повний технологічний цикл запарювання цегли в автоклаві складається з операцій очищення завантаження автоклава, закривання і закріплення кришок, перепуску пара; впуску гострого пара, витримки під тиском, другого перепуску, випуску пара у повітря, відкривання кришок і вивантаження автоклава. Сукупність усіх перелічених операцій становить цикл роботи автоклава, що дорівнює 10 — 13 час.
Запаривание цегли в автоклавах вимагає суворого дотримання температурного режиму: рівномірного нагрівання, витримки під тиском і такої ж рівномірного охолодження. Порушення температурного режиму наводить до браку.
Для контролю над режимом запарювання на автоклавах встановлено манометри і самопишущие дифманометры, забезпечені годинниковим механізмом, записуючим на барограмме повний цикл запарювання кирпича.
З автоклава силікатний цегла надходить на склад.
4.3 Вибір режиму роботи підприємства міста і план виробництва продукции.
Режим роботи підприємства визначається характером перебігу виробничих процесів. Підприємство із виробництва силікатного цегли характеризується безперервним виробничим процесом. Отже, при виборі режиму роботи підприємства необхідно керуються такими параметрами: o ефективний фонд часу (Тэф.) становить 365 днів o число годин роботи у зміну (Пмм.) приймають 8 o проектна річна потужність підприємства рівна 100 000 000 шт.усл. кирпича.
Необхідна кількість змін у добу можна розрахувати по формуле:
[pic],.
Q — проектна потужність підприємства, q — годинна продуктивність производства.
Годинна продуктивність равна:
[pic].
Отже, кількість змін у добу составит:
[pic].
Річний план виробництва визначається проектної потужністю підприємства, а випуск її в ринок збуту протягом року то, можливо распределён поквартально, що зручне силікатного цегли. Намічений обсяг випуску продукції показаний в таблиці 11.
Таблиця 11.
Намічений обсяг випуску продукції. |Виробництво і |Розподіл обсягу випуску продукції з | |розподіл |кварталами, | | |прим. ум. цегли | | |I |II |III |IV | |Обсяг виробництва |25 000 000 |25 000 000 |25 000 000 |25 000 000 | |Випуск товару над ринком |16 666 667 |16 666 667 |16 666 667 |16 666 667 | |До того ж запаси |8 333 333 |8 333 333 |8 333 333 |8 333 333 |.
4.4 Розрахунок потреби сировини й материалов.
Потреба сировини й матеріалів розраховується з таких параметров:
Вихідна активність вапна = 70%. Зміст вапна в вяжущем = 80%. І тут, активність отриманого в’язальника составит:
[pic].
На 1 т сухий известково-песчаной суміші щоб одержати її активності слід узяти 80*0,56 = 44,8 кг ІПВ і 955,2 кг песка.
Потреба сировини на 1000 прим. ум. кирпича.
1. Потреба песка:
0,9552*4,3 = 4,1 т.
З урахуванням 5%-ной кар'єрної вологості потреба піску составит:
4,1*1,05= 4,305 т.
2. ИПВ:
0,384*4,3= 1,6512 їх: -вапна 1,6512*0,8=1,32 096 т.
— піску 1,6512*0,2=0,33 024 т.
Отже, загальна кількість піску составит:
4,305+0,33 024=4,63 524 т.
З урахуванням 3% втрат суміші у процесі виробництва кількість компонентів составит:
. Пісок — 4,63 524*1,03=4,8 т.
. Вапна — 1,3296*1,03=1,4 т.
При проектній потужності 100 млн. прим. ум. цегли потреба сировини составит:
. Пісок — 4,8*100=480 тис. тонн на год;
. Вапно — 1,4*100=140 тис. тонн на год.
Таблиця 12. |№ |Сировинні |Процен|Норма |Витрата з урахуванням втрат | |п/|компоненты,|т |витрати | | |п |од. |потерь|на | | | |виміру | |одиницю | | | | | |продукції| | | | | | |рік |місяць |добу |зміна |годину | |1 |Пісок, тыс.|3% |0,0048 |480 |40 |1,7 |0,57 |0,071 | | |т | | | | | | | | |2 |Вапно, |3% |0,0014 |140 |11,7 |0,5 |0,17 |0,021 | | |тис. т | | | | | | | |.
4.5 Вибір і розрахунок складів сировини й готової продукции.
1. Слад песка.
Тип складу відкритий. З урахуванням місячного запасу сировини, висоти шару складування і насипний щільності, загальна площа складу составит:
[pic].
2. Склад извести.
Вапно зберігається в названих бункерах V=6 м3. Насипна щільність комовой вапна = 1600 кг/м3. Отже, розрахуємо необхідне кількість бункеров:
[pic].
3. Склад кирпича.
Цегла зберігається пакетами (клітинами). Склад вміщує зберігання готової продукції протягом 1 тижня від місячного обсягу виробництва. Тоді запас продукції составит:
8 333 333:3=2 777 778 прим. ум. кирпича.
У першому штабелі 672 цегли, і вона обіймає 1,8 м². Отже, всього штабелів понадобится:
2 777 778:672=4134 штабелей.
З даних, можна розрахувати площа складу кирпича:
[pic].
5. Механічна часть.
Розрахунок основного технологічного оборудования.
Основою розрахунку технологічного устаткування є проектна потужність підприємства (100 млн.шт.усл.кир.), режим його роботи (безперервний), тривалість технологічного циклу і годинна продуктивність агрегата.
Розрахунок потрібної кількості одиниць (n) устаткування роблять за формуле:
[pic], Рn — необхідна годинна продуктивність підприємства, Рч — годинна продуктивність обраного агрегату, До — нормативний коефіцієнт використання устаткування в часу (0,8).
Розрахунок потрібної кількості одиниць оборудования:
1. Кульові мельницы.
[pic].
2. Силосы.
[pic].
3. Прессы.
[pic].
4. Автоклавы.
[pic].
Дані про технологічному устаткуванні зведені в таблиці 13.
Таблиця 13.
Перелік технологічного устаткування. |№ |Наимено|Тип, марка |Производитель|Мощность |Маса, |Стоимос|Колич| |п/|вание | |ность |двигуна |габарит |ть |ество| |п | | | | | | | | |1 |Мельниц|СМ-146 |5000 кг/ч |130 |10,7*31 |16,4 |3 | | |а | | | | | | | |2 |Силосы |СМ-152, 246|1670 кг/ч |25 |2,5*1,5 |5,2 |9 | |3 |Преса |СМ-816, 152|2680 прим. усл.|35 |4,75*3,35 |37,5 |6 | | | | |к/ч | | | | | |4 |Автокла| | |39,5 |2,2*2,7 |68,8 |13 | | |ви | | | | | | |.
6.Контроль виробничого процесу якості готової продукции.
Дроблення винищити. Перевіряють раз на зміну шляхом рассева проби дробленої винищити на ситах з отворами 5, 10, 20 і 30 мм. При подрібнюванні в молотковій дробарці вся вапно має відбуватися крізь сито з отворами 10 мм, а залишок на ситі з отворами 5 мм ні перевищувати 25%. Коли заводі використовують щековые дробарки, то вся дробленая вапно має відбуватися крізь сито з отворами 30 мм, а залишки інших ситах мали бути зацікавленими відповідно трохи більше 50, 30 і 20%.
Шихтовка пісків. Цю операцію контролюють на початку кожної зміни. У тому випадку, якщо крупность пісків відрізняється лише втричі, їх шихтовку слід припинити, бо за цьому пористість пісків збільшиться, що сприятиме перевитрати вяжущего.
При грубої шихтовке пісків робити кар'єру перевіряють, як і пропорції завантажують вагонетки чи автосамосвалы пісками різної крупности у кожному забої. За наявності кількох прийомних бункерів до різних фракцій піску необхідно перевіряти задану пропорцію пісків в шихті за кількістю живильників однаковою продуктивності, одночасно выгружающих піски різної крупности. Якщо ж подача різних пісків відбувається лише з двох бункерів, то. у разі перевіряють кількість піску, що його видають кожним питателем, загальновідомими прийомами за швидкістю руху стрічки питателя й площі перерізу лежачого у ньому піску з урахуванням її насипний плотности.
Відсів включень з піску. На початку кожної зміни перевіряють стан сит на грохотах, бо за розриві сит великі включення можуть потраплятимуть у просіяний пісок, а при замазывании — пісок може вступати у отсев.
Дозування компонентів в’язальника. Перевіряють ежесменно становище шиберов чи відсікають ножів під час використання об'ємних живильників і показання які реєструють приладів під час використання вагових дозаторів. Не рідше рази на тиждень виробляють контрольні зважування порцій компонентів, видавали живильниками і дозаторами за певний проміжок часу (наприклад, за 15 — 20 с).
Тонкість помелу в’язальника. Контролюють не менше десь у зміну шляхом просева проби на механічному приладі для просіювання цементу. Залишок на ситі з сіткою № 021 ні перевищувати 2%, але в ситі з сіткою № 008 — 10%. Питома поверхню в’язальника мусить бути щонайменше 4000 см2/г.
Дозування компонентів силікатної суміші. Цю операцію перевіряють в початку кожної зміни аналогічно контролю дозування компонентів вяжущего.
Приготування суміші. Контролюють зволоження компонентів, їх пароподогрев (у разі застосування) і змістом активної окису кальцію в суміші не рідше ніж тричі на зміну. Однорідність суміші визначають раз на тиждень шляхом послідовного відбору за 10 з в скляні бюкси з притертими кришками щонайменше 15 проб суміші, котра виходить з змішувача, і визначення в них вмісту вологи і необхідність активної окису кальцію. Для визначення активності слід брати навішення суміші 7 р, оскільки, у своїй виходять найбільш правильні результати. Потім відомими способами підраховують коефіцієнт варіації вологості і активності суміші, який може бути не вище 0,1. У випадку перевищення необхідна ретельна регулювання роботи дозаторів, перевірка справжнього стану лопатей змішувачів і частоти обертання їх валов.
Гасіння суміші. Перевіряють температуру що надходить у силосы чи реактори і котра виходить з них суміші тричі на зміну і рівень погашенности винищити раз на зміну. Ступінь погашенности визначають по пробі масою 100 р, вміщеній у судину Дьюара, безпосередньо дома відбору, порівнюючи криву остигання проби з тарировочной кривою остигання судини Дьюара при однаковою їх початковій температурі. У разі, коли крива остигання проби розташована вище тарировочной кривою, слід збільшити терміни гасіння смеси.
Обробка гашеної суміші. Перевіряють не рідше ніж тричі на зміну зерновий склад парламенту й вологість гашеної суміші доі після обробки, Візуально під бинокулярной лупою визначають раз на зміну, із чого складаються отсеянные грудочки: з скупчень частинок винищити, глини, дисперсного кремнезему або ж з котунів добре промешанной однорідної суміші компонентів. За наявності суміші окремих грудочок вапна, глини та інших дисперсних матеріалів слід перевірити правильність і рівномірність харчування стрижневих змішувачів, а разі обробітку грунту і доувлажнения суміші в лопастных смесителях — також стан лопатей і частоту їх вращения.
Формование і укладка сирцю на вагонетки. Не треба менше десь у зміну визначати на циферблатных терезах масу сирцю, сформованного в різних гніздах столу кожного преса, зовнішній вигляд і міцність сирцю, наявність у ньому дефектів, які виникають за формовании і укладанні автоматами на запарочные вагонетки, і навіть стан поверхні платформ вагонеток.
Транспортування сирцю і завантаження їх у автоклави. Слід ежесменно перевіряти стан откаточных колій та стиків, забрудненість рейок просыпью, плавність заталкивания запарочных вагонеток в автоклави, заплющення кришок прохідних автоклавів з выгрузочного кінця відразу після викочування складу запаренного цегли щоб уникнути охолодження і подсушки загружаемого сырца.
Автоклавная обробка. Ежесменно контролюють правильність проведення заданого режиму запарювання сирцю по диаграммам на контрольних приладах або ж за наявності програмних регуляторів з їхньої записів. Одночасно перевіряють запис тиску пара в магістральному паропроводі, які мають перевищувати по крайнього заходу на 0,05 МПа заданий тиск у автоклавах. Необхідно регулярно ознайомитися з випуском повітря з автоклавів на початку запаривания.
Контроль якості готової продукції. Якість запаренного силікатного цегли і каміння визначається по ГОСТ 379–79 кожної партії виробів, рівної місткості одного автоклава, по зовнішнім виглядом, розміром (250*120*88мм), випробуванню на міцність на вигині і стискуванні, причому останні випробування допомагає визначити марку цегли. Силікатний цегла також випробовується на водопоглощение і морозостійкість (25 циклов).
Основні параметри контролю зведені в таблиці 11.
Таблиця 11.
Контроль виробництва та якості силікатного цегли. |Найменування |Параметри контролю |Періодичність |Нормативна | |технологическ| |контролю |документація, в | |ой операції | | |відповідність до | | | | |якої | | | | |здійснюється | | | | |контроль | |Помел |тонкість помелу: залишок |1 разів у зміну |ГОСТ 379−79 | |в'язальника |на ситі | | | | |з сіткою № 021 — до 2%, | | | | |№ 008 — 10% | | | |Приготовление|коэффициент варіації |1 разів на тиждень| | |суміші |вологості і активності | | | | |суміші - до 0,1 | | | |Формование і |дефекти сирцю; |1 разів у зміну | | |укладка сырца|прочность сирцю | | | |на вагонетки | | | | |Автоклавная |тиск пара |щомісяця | | |обробка | | | | |Готова |розмір цегли ([pic]) |кожної | | |продукція |міцність на вигині і |партії виробів| | | |стисканні | | | | |водопоглощение (щонайменше 6| | | | |%) | | | | |морозостійкість (25 | | | | |циклів) | | |.
7.Мероприятия з охорони навколишнього среды.
Однією з чинників, які впливають на морально-психологічне стан людей, стала останнім часом радіоекологія довкілля, в тому однині і будівельних об'єктів промислового й громадянського призначення. Кожен житель нашої країни у середньому отримує щорічно дозу майже п’ять мЗв (1Зв=100 бер) попри всі тіло з допомогою природної радіації та медичної диагностики.
Ефективні еквівалентні радіаційні дози опромінення, одержувані населенням від будівельних матеріалів і конструкцій, найвищі і становлять 56 — 65%, зокрема: гамма-випромінювання (30 — 35%) і радіоактивні гази (26 — 30%).
З огляду на нерівномірність розподілу природних радіонуклідів (від 7 до 4700 Бк/кг) в гірських породах і мінералах, що використовуються виробництва будівельних матеріалів, виникла потреба регіонального дослідження на радіоактивність будівельних матеріалів, виробів і конструкцій і складання чіткої й повної картини про внесок в ефективну еквівалентну дозу облучения.
У районах з природним радіаційним тлом основний внесок в радіоактивність будівельних матеріалів і виробів вносять природні джерела та насамперед природні радіонукліди — 238,235U, 40K, 226Ra і 232Th .
Звісно ж актуальним створення ефективну систему радіаційного контролю та прийняття невідкладних заходів зі забезпечення радіаційній безпеці людини з урахуванням зниження ризику у разі виникнення порушень дейстующих норм всіх етапах технологічного процесу виробництва — від кар'єра до випуску готової продукції. Щойно мінеральну сировину вилучено у надрах і пущено в технологічний процес, джерело випромінювання з природного перетворюється на антропогенный.
Силікатний цегла, відповідний ГОСТ 379– — 95 «Цегла і камені силікатні», одна із основних видів будівельних матеріалів житлове будівництво. У зв’язку з цим проведено дослідження радіаційної безпеки представницьких проб на основних технологічних переділах виробництва полнотелого утолщенного силікатного цегли марки 150, виробництва найбільшого Білгородської області АТ «Стройматериалы».
Загальну радіоактивність і питому ефективну активність радиоизотопов торію, радію, калію і цезію визначали гамма-спектрометрическим методом як в вихідному сировину, і на основних технологічних переділах, включаючи готової продукції. Виміри проводили в акредитованої в Держстандарті РФ лабораторії радіаційного контролю («Спектр») при Бел ГТАСМ.
Більше 50% заводів силікатного цегли країни мають власними известково-обжигательными цехами, сировиною котрим служать карбонатні породи. АТ «Будматеріали» як карбонатного сировини використовує крейда Білгородського родовища. Крейдяні породи Білгородського родовища ставляться до верхнемеловому віку. У геологічному будову родовища беруть участь крейдяні, палеогенные і четвертинні відкладення. Формений склад крейди — це коколиты, фораминеферы, призми иноцерамов і порошковий кальцит. Мел відрізняється підвищеною ступенем чистоти. У крейдової породі зустрічаються лише окремі плями, забарвлені гидроокислами заліза. Високе якість крейди підтверджується його хімічним складом, що про переважному змісті кальцита СаСО3.
Присутні у кількості карбонаты магнію утворюють розсіяні в основному крейди кристали магнезиального кальцита, доломіту і сидерита. Некарбонатная частина представлена глинистыми мінералами, силикатами, окислами заліза, калію, титану, сполуками марганцю і фосфора.
На малюнку 1 приведено технологічна карта радіаційного моніторингу виробництва винищити і силікатного кирпича.
Малюнок 1.
Технологічна карта радіаційного моніторингу виробництва силікатного кирпича.(.
Знання закономірностей розподілу радіонуклідів в крейдових осадах i піску необхідно як з метою оцінки геохімічного поведінки в природі, а й дуже важливо задля забезпечення радіаційної і екологічну безпеку під час виробництва винищити і силікатного кирпича.
Аналіз змісту радіонуклідів і обший удільної ефективної активності показує, що відносний внесок радионуклида АК в сумарну гамма-активність піску, крейди, вапна і готового силікатного цегли становить відповідно 47; 0,6; 17 і 26%.
Природний крейда мало сорбує 232Th, але він міститься у готовому виробі (силикатном цеглі) з допомогою запровадження піску, у якому активність по торию становить 5 Бк/кг. При декантировании піску водою зміст торію у ньому різко снижается.
По технологічного циклу під час виробництва вапна пилюка з пылеосадительной камери повертається у обертову піч. Це спричиняє збільшення активності 226Ra в силикатном цеглі. У зв’язку з тим, що радій є джерелом виділення радіоактивного газу радону за його розпаді, виникає запитання доцільність повернення пилу у обертову піч з пылеосадительной камеры.
Отримані системні аналізи на радіаційне якість кар'єрних матеріалів, винищити і готового силікатного цегли відповідно до вимозі ГОСТ 30 108– — 94 «Матеріали й вироби будівельні. Визначення удільної ефективної активності природних радіонуклідів» свідчать, що крейдяні відкладення Білгородського родовища, і навіть пісок НижнеОльшанського родовища, вапно і силікатний цегла ставляться до низкорадиоактивным об'єктах та відповідають першому класу радіаційної безпеки, придатні в усіх проявах будівництва. Однак у сформованій практиці радіаційний моніторинг за умов чинного виробництва забезпечено лише на стадіях 1; 3 і 9-те (див. малюнок 1).
Виконання комплексного і системного радіаційного моніторингу гірського сировини, і навіть усім технологічних стадіях виробництва вапна і силікатного цегли, ухвалення низки технічних рішень щодо використанню пылевидных вапняних фракцій дозволять істотно знизити — радіаційний рівень силікатного цегли, отже, і спільного радіаційного фону в житлових й управління промислових будинках і сооружениях.
Заключение
.
На закінчення, про виконану роботу можна достеменно сказати, що запропонований спосіб виробництва — силосний — силікатного цегли, був обраний цілком обгрунтовано і є нині найбільш эффективным.
Силосний спосіб має значних економічних переваги, оскільки при силосовании маси на ослаблення не витрачається пар. З іншого боку, технологія силосного способу виробництва значно простіше технології барабанного способу. Підготовлені вапно і пісок безупинно подаються живильниками в заданому співвідношенні в одновальную мішалку безперервного дії і воложаться. Отже, відбувається зменшення як фінансових витрат, і тимчасових. В своє чергу неминуче тягнуть у себе економію коштів. З іншого боку, збільшується продуктивність завода.
Білгородський ринок є дуже перспективною для силікатного цегли. Зараз створюються проекти будівництва нових житлових районів, які зажадають великої кількості будівельних матеріалів. З іншого боку, вже нині ведеться велике будівництво як і цілком нові райони міста, і у вже обжитых.
Проте чи лише білгородські підприємства є споживачами силікатного цегли. Цегла може успішно збуватися у всій области.
Але річ у достатню кількість споживачів. Виробництво силікатного цегли в Білгородської області є доцільним з місця зору розташування сировини. Чи по кишені цього чинника значною мірою знижуються витрати, пов’язані з транспортуванням і доставкою сырья.
Отже, досягається економія на одиницю продукции.
Понад те ефективно виробляти известково-зольный силікатний кирпич.
Цей цегла має низку переваг. Істотне зниження собівартості ефективного зольного цегли досягнуто як з допомогою використання дешевого техногенного сировини, а й завдяки відсутності двох таких енергоємних технологічних переділів, як випал вапна і помел вяжущего.
Перевагою даної технології є й екологічний ефект від участі застосування промислових відходів замість природних материалов.
З погляду социально-этического маркетингу, силікатний цегла є прогресивним будівельний матеріал. При використанні запропонованого способу виробництва, знижуються як економічні витрати, а й зростають його социально-этические властивості, такі як який досягається екологічний ефект і полегшення праці рабочих.
Застосування даної технології дозволить розширити ринки збуту силікатного цегли, підвищивши, в такий спосіб, рентабельність производства.
Список літератури. 1. Боженов П.І. Технологія автоклавных матеріалів. — С.-П., 1978. 2. Вахнин М. П., А.А. Аніщенка Виробництво силікатного цегли. — М., 1989 3. Воробьёв В. А. Будівельні матеріали. — М., 1979 4. Воронін В.П., Заровнятных В. А. Ефективний силікатний цегла з урахуванням золи ТЕС і порошкоподібної винищити/ Будівельні матеріали, № 8 — М.,.
2000. 5. Гвоздарев І.П. Виробництво силікатного цегли — М., 1951. 6. Митрохина М. М., Хвостенков С.І. Використання відходів ТЕС у виробництві силікатного цегли. — М., !977. 7. Павленко В.І., Тушева І.С. Радіаційний моніторинг виробництва вапна і силікатного цегли/ Будівельні матеріали, № 4 — М., 2001. 8. Хавкін Л. Технологія силікатного цегли. — М., 1982.
(Цифри вказують ділянки радіаційних замеров.
———————————;
Карьер 1.
Сито-бурат.
Смеситель.
Пресс.
Сито-бурат.
Мельница.
Цегла 9.
Автоклав.
Силоса.
Кар'єр 3.
Дробилка.
Обертова печь.
Пылеосадительная камера.
Циклоны.
Электрофильтры 12.
Виробництво извести.
Мел.
Известь.
Песок Пар (вода).