Електрометалургія
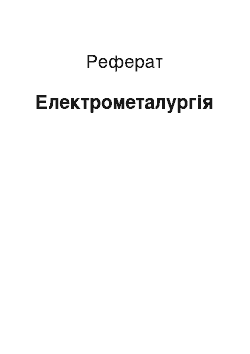
Більшість дугових печей має основну футеровку, що складається з матеріалів з урахуванням MgO. Підбійка печі створює ванну для металу і відіграє роль теп-лоизолирующего шару, уменьшающего втрати тепла. Основні частини футерівки — подина печі, стіни, звід. Температура у зоні електричних дуг сягає тисяч градусів. Хоча підбійка електропечі відділена дуг, вона все-таки повинна витримувати нагрівання… Читати ще >
Електрометалургія (реферат, курсова, диплом, контрольна)
Производство сталі у електричних печах.
У электоропечи можна одержувати легированную сталь з низьким змістом сірки і фосфору, неметалічних включень, у своїй втрати легуючих елементів значно меньше.
У процесі электроплавки не складно регулювати температуру металу та її склад, виплавляти сплави майже кожного состава.
Електричні печі мають суттєвими перевагами проти іншими сталеплавильными агрегатами, тому высоколегированные інструментальні сплави, нержавіючі шарикоподшипниковые, жаростойкие і жароміцні, і навіть багато конструкційні стали виплавляють лише у цих печах.
Потужні електропечі успішно застосовують щоб одержати низьколегованих і высокоуглеродистых сталей мартенівського сортаменту. З іншого боку, в електропечах одержують різноманітні феросплави, які становлять сплави заліза із елементами, які потрібно виводити в сталь для легування і раскисления.
Пристрій дугових электропечей.
Перша дуговая електропіч у Росії встановили 1910 р. на Обухівському заводі. Упродовж років п’ятирічок було побудовано сотні різних печей. Місткість найбільш великої печі у СРСР 200 т. Піч складається з залізного кожуха циліндричною форми зі сферичним днищем. Усередині кожух має огнеупорную футеровку. Плавильне простір печі закривається знімним сводом.
Піч має робоче вікно і випускне отвір зі зливним жолобом. Харчування печі здійснюється трифазним змінним струмом. Нагрівання і плавлення металу здійснюються електричними потужними дугами, палаючими між кінцями трьох електродів і металом, які у печі. Піч спирається на два опорних сектора, перекатывающихся по станині. Нахил печі убік випуску й робочого вікна здійснюється за допомогою реечного механізму. Перед загрузклй печі звід, підвішений на ланцюгах, піднімають до порталу, потім портал зі склепінням і електродами відвертається убік зливального жолоба і піч завантажують бадьей.
Механічне устаткування дугового печи.
Кожух печі повинен відповідати навантаження від безлічі вогнетривів і металу. Його роблять сварным з листового заліза завтовшки 16−50 мм залежно від розмірів печі. Форма кожуха визначає профіль робочого простору дугового електропечі. Найпоширенішим нині є кожух конічну форму. Нижня частина кожуха має форму циліндра, верхня часть—конусообразная з розширенням догори. Така форма кожуха полегшує заправку печі огнеупорным матеріалом, похилі стіни збільшують стійкість кладки, оскільки він далі розташована від електричних дуг. Використовують також кожухи циліндричною форми з водоохлаждаемыми панелями. Задля збереження правильної циліндричною форми кожух посилюється ребрами і кільцями жорсткості. Днище кожуха зазвичай виконується сферичним, що забезпечує найбільшу міцність кожуха і мінімальну масу кладки. Днище виконують з немагнитной стали для установки під піччю електромагнітного перемешивающего устрою.
Згори піч закрита склепінням. Звід набирають з вогнетривкої цегли в металевому водоохлаждаемом сводовом кільці, яке витримує распирающие зусилля аркового сферичного зводу У частині кільця є виступ — ніж, що входить у піщаний затвор кожуха печі. У цегельною кладці зводу залишають три отвори для електродів. Діаметр отворів більше діаметра електрода, під час плавки в зазор кидаються гарячі гази, що руйнують електрод і виносять тепло з печі. Щоб запобігти цього зведенні встановлюють холодильники чи экономайзеры, службовці для ущільнення электродных отворів й у охолодження кладки зводу. Газодинамические экономайзеры забезпечують ущільнення з допомогою повітряної завіси навколо електрода. У зведенні є також отвір для отсоса запилених газів і отвір для кисневою фурмы.
Для завантаження шихти в печі невеличкий ємності і подгрузки легуючих і флюсів в великі, печі скачування шлаку, огляду, заправки і ремонту печі є загрузочное вікно, й із литої рамою. До рамі кріпляться направляючі, якими ковзає заслінка. Заслінку футеруют огнеупорным цеглою. Для підйому заслінки використовують пневматичний, гідравлічний чи електромеханічний привод.
Із протилежного боку кожух має вікно для випуску сталі з печі. До вікна приварений зливальний жолоб. Отвір для випуску стали то, можливо круглим діаметром 120—150 мм чи квадратним 150 на 250 мм. Зливальний жолоб має корытообразное перетин і приварений до кожуху з точки 10—12° до горизонталі. Зсередини жолоб футеруют шамотным цеглою, довжина його становить 1—2 м.
Электрододержатели служать для підвода струму до електродах й у затискача електродів. Голівки электрододер-жателей роблять із бронзи чи сталі та охолоджують водою, оскільки вони сильно нагріваються як теплом з печі, і контактними струмами. Электрододержатель повинен щільно затискати електрод плюс невеличке контактне опір. Найпоширенішим нині є пружинно-пневматический электрододержатель. Затиск електрода здійснюється за допомогою нерухомого кільця і зажимной плити, яка притискається до электроду пружиною. Ог-жатие плити від електрода і стиснення пружини відбуваються з допомогою стиснутого повітря. Электрододержатель кріпиться на металевому рукаві - консолі, який скріплюється з Г-образной рухомий стійкою до однієї жорстку конструкцію. Стойка може переміщатися вгору чи вниз всередині нерухомій коробчатой стійки. Три нерухомі стійки жорстко пов’язані до однієї загальну конструкцію, яка спочиває на платформі опорною колиски печі. Переміщення рухливих телескопічних стійкий відбувається чи з допомогою системи тросів та противаг, наведених у рух електродвигунами, чи з допомогою гідравлічних пристроїв. Механізми переміщення електродів має забезпечити швидке піднесення електродів у разі обвалу шихти у процесі плавлення, і навіть плавне опускання електродів щоб уникнути їх занурення на метал чи ударів про нерасплавившиеся шматки шихти. Швидкість підйому електродів становить 2,5—6,0 м/мин, швидкість опускання 1,0— 2,0 м/мин.
Механізм нахилу печі повинен плавно нахиляти піч убік випускного отвори на кут 40—45° для випуску сталі та на кут 10—15 градусів убік робочого вікна для спуску шлаку. Житло печі, чи колиска, де встановлено корпус, спирається на два — чотири опорних сектора, які перекочуються по горизонтальним котрі спрямовують. У секторах є отвори, а направляють — зубці, з яких запобігається проскальзывание секторів при нахилі печі. Нахил печі здійснюється за допомогою рейки і зубчастого механізму, чи гідравлічною приводом. Два циліндра укріплені на нерухомих опорах фундаменту, а штоки шарнірно пов’язані з опорними секторами колиски печи.
Система завантаження печі буває два види: через завалочное вікно мульдозавалочной машиною і крізь гору з допомогою цебра. Завантаження з вікна застосовують лише з невеликих печах.
При завантаженні печі згори в один-два приєднання до протягом 5 хв менше охолоджується підбійка, скорочується час плавки; зменшується витрати; ефективніше використовується обсяг печі. Для завантаження печі звід піднімають на 150—200 мм над кожухом печі і повертають убік разом із електродами, повністю відкриваючи робоче простір печі запровадження цебра з шихтою. Звід печі підвішений до рами. Вона з'єднана з нерухомими прилавками электрододержателей до однієї жорстку конструкцію, спочиваючу на поворотною консолі, яка укріплена на опорному подшипнике. Великі печі мають поворотну вежу, у якій зосереджено все механізми одворота зводу. Вежа обертається навколо шарніра на ковзанках по дугообразному рейку. Баддя є сталевої циліндр, діаметр якого менше діаметра робочого простору печі. Знизу циліндра є рухливі гнучкі сектора, кінці яких стягуються через кільця тросом. Зважування і завантаження шихти виробляються на шихтовом дворі електросталеплавильного цеху. Баддя на візку подається до цеху, піднімається краном і опускається в піч. З допомогою допоміжного підйому крана трос висмикують з проушин секторів і за підйомі цебра сектора розкриваються і шихта вивалюється в піч у порядку, у якому вона була покладена в бадді.
З використанням як шихти металлизован-ных котунів завантаження може здійснюватися безперервно за трубопроводу, який проходить отвір в зведенні печи.
Під час плавлення електроди прорізають в шихті три колодязя, дно якої яких накопичується рідкий метал. Для прискорення розплавлювання печі обладнуються поворотним пристроєм, яке повертає корпус в інший бік на кут в 80°. У цьому електроди прорізають в шихті вже дев’ять криниць. Для повороту корпусу піднімають звід, піднімають електроди вище рівня шихти і повертають корпус з допомогою зубчастого віденця, прикріпленого до корпусу, і шестерні. Корпус печі спирається на ролики.
Очищення відведених газов.
Сучасні великі сталеплавильні дугові печі під час роботи виділяють у повітря дуже багато запилених газів. Застосування кисню і порошкоподібних матеріалів ще більше сприяє цьому. Зміст пилу в газах электродуговых печей сягає 10 г/м3 і стає більше норми. Для уловлювання пилу виробляють отсос газів з робочого простору печей потужним вентилятором. І тому в зведенні печі роблять четверте отвір з патрубком для газоотсоса. Патрубок через зазор, дозволяє нахиляти чи крутити піч, наближається до стаціонарному трубопроводу. Дорогою гази розбавлено повітрям, необхідним дожигания ЗІ. Потім гази розладнуються водяними форсунками в теплообменнике і направляють у систему труб Вентури, у яких пил затримується внаслідок зволоження. Застосовують також тканинні фільтри, дезінтегратори і электрофильтры. Використовують системи газоочистки, які включають цілком усю електросталеплавильний цех, із установкою парасоль дымоотсоса під дахом цеху над электропечами.
Підбійка печей.
Більшість дугових печей має основну футеровку, що складається з матеріалів з урахуванням MgO. Підбійка печі створює ванну для металу і відіграє роль теп-лоизолирующего шару, уменьшающего втрати тепла. Основні частини футерівки — подина печі, стіни, звід. Температура у зоні електричних дуг сягає тисяч градусів. Хоча підбійка електропечі відділена дуг, вона все-таки повинна витримувати нагрівання до температури 1700 °C. У зв’язку з цим застосовувані для футерівки матеріали повинні мати високої огнеупорностью, механічної міцністю, термота хімічної сталістю. Подину сталеплавильної печі набирають у порядку. На сталевої кожух вкладають листовий азбест, на асбест—слой шамотного порошку, два шару шамотного цегли і основний шар із магнезитового цегли. На магнезитовой цегельною подине набивають робочий шар із магнезитового порошку зі смолою і пеком — продуктом нафтопереробки. Товщина набивного шару становить 200 мм. Загальна товщина подины дорівнює приблизно глибині ванни і може становити 1 м. для великих печей. Стіни печі викладають після відповідної прокладки азбесту і шамотного цегли з крупноразмерного безобжигового магнезитохромитового цегли довжиною до 430 мм. Кладка стін може виконуватися з цеглин в залізних касетах, які забезпечують зварювання цеглин до одного монолітний блок. Стійкість стін сягає 100—150 плавок. Стійкість подины становить рік-два. У складних умовах працює підбійка зводу печі. Вона витримує великі теплові навантаження від запалених дуг і тепла, відбиваного шлаком. Склепіння великих печей набирають з магнезитохромитового цегли. Набираючи зводу використовують нормальний і фасонный цегла. У поперечному сечении звід має форму арки, що забезпечує щільне зчеплення цеглин між собою. Стійкість зводу становить 50 — 100 плавок. Вона залежить від електричного режиму плавки, від тривалості перебування у печі рідкого металу, складу виплавлюваних стали, шлаку. Нині стала вельми поширеною отримують водоохлаждаемые склепіння і стеновые панелі. Ці елементи полегшують службу футеровки.
Струм в плавильне простір печі подається через електроди, зібрані з секцій, кожна з яких є круглу заготівлю діаметром від 100 до 610 мм довжиною до 1500 мм. У малих електропечах використовують вугільні електроди, у крупних — графитированные. Графитированные електроди виготовляються з малозольных вуглецевих матеріалів: нафтового коксу, смоли, пеки. Электродную масу змішують і пресують, після чого сира заготівля обпікається в газових печах при 1300 градусах зазнає додатковому графитирующему випалу за нормальної температури 2600 — 2800 градусів електричних печах опору. У процесі експлуатацію у результаті окислення грубними газами і розпорошення при горінні дуги електроди згоряють. Принаймні укорочування електрод опускають в піч. У цьому электрододержатель наближається до склепіння. Однак настає час, коли електрод стає таким коротким, і що може підтримувати дугу, і його треба нарощувати. Для нарощування електродів в кінцях секцій зроблено отвори різьблені, куди угвинчується переходник-ниппель, з якого з'єднуються окремі секції. Витрата електродів становить 5—9 кг на тонну виплавленої стали.
Електрична дуга—один з видів електричного розряду, у якому струм проходить через іонізовані гази, пари металів. При короткочасному зближення електродів з шихтою чи друг з одним виникає коротке замикання. Йде струм великий сили. Кінці електродів розжарюються до краю. При раздвигании електродів з-поміж них виникає електрична дуга. Зі спекотного катода відбувається термоэлектронная емісія електронів, які, прямуючи до аноду, зіштовхуються з нейтральними молекулами газу та ионизируют їх. Негативні іони направляються до аноду, позитивні до катоду. Простір між анодом і катодом стає ионизированным, токопроводящим. Бомбардування анода електронами і іонами викликає сильний його розігрів. Температура анода може становити 4000 градусів. Дуга може горіти постійному і перемінному струмі. Электродуговые печі працюють на перемінному струмі. Останнім часом до ФРН побудована электродуговая піч постійному токе.
У перший половину періоду, коли катодом є електрод, дуга горить. При зміні полярності, коли катодом стає шихта — метал, дуга гасне, позаяк у початковий період плавки метал ще нагріте та її температура недостатня для емісії електронів. Тож у початковий період плавки дуга горить неспокійно, переривчасто. Коли ванна покривається шаром шлаку, дуга стабілізується і горить більш ровно.
Электрооборудование.
Робоча напруга электродуговых печей становить 100 — 800 У, а сила струму вимірюється десятками тисяч ампер. Потужність окремої установки може становити 50 — 140 МВ*А. До підстанції електросталеплавильного цеху подають струм напругою до 110 кВ. Високим напругою харчуються первинні обмотки пічних трансформаторів. На показано спрощена схема електричного харчування печі. У електричне устаткування дугового печі входять виробництва ремонтних робіт на печі. такі приборы:
1. Повітряний роз'єднувач, призначений для відключення всієї электропечной установки від лінії високої напруги у время.
2. Головний автоматичний вимикач, служить для відключення під навантаженням електричної ланцюга, через яку протікає струм високої напруги. При нещільної укладанні шихти в печі на початку плавки, коли шихта ще холодна, дуги горять хитливо, відбуваються обва лы шихти і виникають короткі замикання між електродами. У цьому сі ла струму різко зростає. Це спричиняє великим перевантажень трансформатора, котрі можуть вийти з експлуатації. Коли сила струму перевищить встановлений межа, вимикач авто матически відключає установку, навіщо є реле максимальної сили тока.
3. Пічний трансформатор необхідний перетворення високої напруги в низька (з 6—10 кВ до 100—800 У). Обмотки високої професійності і низького напруження і магнитопроводы, де вони можна побачити, вміщено у баці з олією, службовцям для охолодження обмоток. Охолодження створюється примусовим перекачуванням олії з трансформаторного кожуха в бак теплообмінника, у якому олію охолоджується водою. Трансформатор встановлюють поруч із электропечью у спеціальній приміщенні. Вона має пристрій, що дозволяє переключати обмотки сходами отже східчасто регулювати подаване в піч напруга. Приміром, трансформатор для 200-т вітчизняної печі потужністю 65 МВ*А має 23 щаблі напруги, які переключаються під навантаженням, без відключення печі.
Ділянка електричної мережі від трансформатора до електродів називається короткій мережею. Виходять з стіни трансформаторній підстанції фідери з допомогою гнучких, водоохлаждаемых кабелів подають напруга на электрододержатель. Довжина гнучкого ділянки повинна дозволяти виробляти потрібний нахил печі і відвертати звід для завантаження. Гнучкі кабелі поєднано з аналітичними мідними водоохлаждаемыми шинами, встановленими на рукавах электрододержателей. Трубошины безпосередньо приєднано до голівці электрододер-жателя, зажимающей електрод. Крім зазначених основних вузлів електричної мережі у ній входить різна вимірювальна апаратура, подсоединяемая до лініях струму через трансформатори струму чи напруги, і навіть прилади автоматичного регулювання процесу плавки.
Автоматичне регулирование.
Під час плавлення в електродугову піч потрібно подавати різне кількість енергії. Змінювати подачу потужності можна зміною напруги чи сили струму дуги. Регулювання напруги виробляється перемиканням обмоток трансформатора. Регулювання сили струму здійснюється зміною відстані між електродом і шихтою шляхом підйому чи опускання електродів. У цьому напруга дуги не змінюється. Опускання чи підйом електродів виробляються автоматично з допомогою автоматичних регуляторів, встановлених з кожної фазі печі. У середовищі сучасних печах задана програма електричного режиму може бути встановлена весь період плавки.
Пристрій для електромагнітного перемішування металла.
Для перемішування металу у великих дугових печах, з метою прискорення і полегшення проведення технологічних операцій скачування шлаку під днищем печі в коробці встановлюється електрична обмотка, яка охолоджується водою чи стиснутим повітрям. Обмотки статора харчуються від двухфазного генератора струмом низькою частоти, що створює який біжить магнітне полі, яке захоплює ванну рідкого металу і рух нижніх верств металу вздовж подины печі у бік руху поля. Верхні верстви металу разом із прилеглим щодо нього шлаком рухаються у бік. Відтак можна направити рух або у бік робочого вікна, що полегшувати вихід шлаку з печі, або у бік зливального отвори, що сприяти рівномірному розподілу легуючих і розкислювачів і усреднению складу металу та її температури. Цей метод останнім часом має обмежений застосування, позаяк у надпотужних печах метал активно перемішується дугами.
Плавка сталі у основний дугового электропечи.
Сирі материалы.
Основним матеріалом для электроплавки є сталевої брухт. Лом ні бути надто окисленным, оскільки наявність великої кількості іржі вносить в сталь значну кількість водню. Залежно від хімічного складу брухт необхідно розсортувати на відповідні групи. Основне кількість брухту, призначене для плавки в електропечах, має бути компактним і великоваговим. При малої насипний масі брухту вся порція для плавки не міститься у піч. Доводиться переривати процес плавки і довантажувати шихту. Це збільшує тривалість плавки, призводить до підвищеному витраті електроенергії, знижує продуктивність електропечей. Останнім часом в електропечах використовують металлизованные котуни, отримані методом прямого відновлення. Перевагою цього виду сировини, що містить 85— 93% заліза, і те, що його не забруднене міддю та інші домішками. Котуни доцільно застосовувати для виплавки высо-копрочных конструкційних легованих сталей, електротехнічних, шарикоподшипниковых сталей.
Леговані відходи утворюються у электросталеплавильном цеху як недолитых зливків, литников; в обдирочном відділенні як стружки, в прокатних цехах як обрези і шлюби й т, буд.; ще багато легованого брухту йде від машинобудівних заводів. Використання легованих металлоотходов дозволяє заощаджувати цінні легирующие, підвищує економічну ефективність электроплавок.
М’яка залізо спеціально виплавляють в мартенівських печах і конвертерах і застосовують для регулювання змісту вуглецю у процесі электроплавки. У залозі міститься 0,01—0,15% З повагою та.
Підготовка матеріалів до плавке.
Усі присадки в дугові печі необхідно прожарювати видалення слідів оливи й вологи. Це запобігає насичення стали воднем. Феросплави підігрівають з прискорення їх проплавле-ния. Ад’ювантна легуючих, розкислювачів і шлакообразующих у сучасній печі багато в чому механізована. На бункерної естакаді з допомогою конвеєрів відбувається зважування й роздавання матеріалів по мульдам, які завантажуються в піч мульдовыми машинами. Сипучі для наведення шлаку вводять у електропечі бросательными машинами.
Технологія плавки.
Плавка в дугового печі починається з заправки печі. Жидкоподвижные нагріті шлаки сильно роз'їдають футеровку, яка то, можливо пошкоджена і за завантаженні. Якщо подина печі під час нічого очікувати закрита шаром рідкого металу і шлаку, вона то, можливо пошкоджена дугами. Тому до початку плавки виробляють ремонт — заправку подины. Перед заправкою із поверхні подины видаляють залишки шлаку і металу. На пошкоджені місця подины і укосів — місця переходу подины до печі - закидають сухий магнезитовый порошок, а разі великих ушкоджень — порошок з добавкою пеки чи смолы.
Заправку виробляють заправної машиною, що через. насадку з допомогою стиснутого повітря заправні матеріали, чи, разбрасывающей матеріали з приводу окружності з швидко обертового диска, який опускають відкрито піч сверху.
Завантаження печи.
Для найповнішого використання робочого простору печі в центральну значна її частина ближчі один до електродах завантажують великі шматки (40%), ближчі один до укосам середній брухт (45%), на подину і гору завантаження дрібний брухт (15%). Дрібні шматки повинні заповнювати проміжки між великими кусками.
Період плавления.
Розплавляння шихти в печі займає основне час плавки. Нині багато операцій легування і розкиснення металу переносять в ківш. Тому тривалість розплавлювання шихти переважно визначає продуктивність печі. Після закінчення завалки опускають електроди і включають струм. Метал під електродами розігрівається, плавиться і стікає вниз, збираючись у центральній частині подины. Електроди прорізають в шихті криниці, у яких ховаються електричні дуги. Під електроди закидають вапно задля наведення шлаку, який закриває оголений метал, оберігаючи його від окислення. Поступово озеро металу під електродами стає дедалі більше. Воно подплавляет шматки шихти, яке падає в рідкий метал і розплавляються у ньому. Рівень металу у печі підвищується, а електроди під впливом автоматичного регулятора піднімаються вгору. Тривалість періоду розплавлювання металу дорівнює 1—3 год залежно від розміру печі і встановленого трансформатора. У період расплавлени" трансформатор працює із повної навантаженням і і з 15% перевантаженням, допускаемой паспортом, самісінькому вищому щаблі напруги. У цей час потужні дуги безпечні для футерівки зводу і стін, оскільки вони закриті шихтою. Остигла під час завантаження підбійка може взяти дуже багато тепла без небезпеки її перегріву. Для прискорення розплавлювання шихти використовують різні методи. Найбільш ефективний застосування потужних трансформаторів. Так, на печах місткістю 100 т буде встановлено трансформатори потужністю 75,0 МВ-А, на 150-т печах трансформатори 90—125 МВ*А і від. Тривалість плавлення під час використання потужних трансформаторів зменшується до 1−1,5 год. З іншого боку, з метою прискорення розплавлювання застосовують паливні мазутні чи газові пальники, які вводять у піч або через робоче вікно, або через спеціальний електронний пристрій у. Застосування горілок прискорює нагрівання і розплавляння шихти, особливо у холодних зонах печі. Тривалість плавлення скорочується на 15—20 мин.
Ефективним методом є застосування газоподібного кисню. Кисень подають у піч ніби крізь сталеві футерованные трубки у вікно печі, і з допомогою фурмы, опускаемой в піч згори через отвір в зведенні. Завдяки экзотермическим реакцій окислення домішок і заліза виділяється додатково дуже багато тепла, яке нагріває шихту, прискорює її повне розплавляння. Використання кисню зменшує тривалість нагріву ванни. Період розплавлювання скорочується на 20—30 хв, а витрати на 60—70 кВт. год на 1 т стали.
Традиційна технологія электроплавки стали передбачає роботу з двом варіантів: 1) на свіжої шихті, тобто. з окисленням; 2) переплавку відходів. При плавленні за першим варіантом шихта складається з простих вуглецевих відходів, малоуглеродистого брухту, метал-лизованных котунів з добавкою науглероживателя. Надлишкове кількість вуглецю окисляют у процесі плавки. Метал легируют присадками феросплавів щоб одержати стали потрібного складу. У другому варіанті склад стали майже зовсім визначається складом відходів і легирующие додають лише деякою коригування складу. Окислення вуглецю не производят.
Плавка з окислением.
Розглянемо хід плавки з окисленням. Після закінчення періоду розплавлювання починається окисний період, завдання якого зводяться до чого: окислювання надлишкового вуглецю, окислювання і видалення фосфору; дегазація металу; видалення неметалевих включень, нагрівання стали.
Окисний період плавки починають присадкою залізної руди, яку дають на піч порціями. Через війну присадки руди відбувається насичення шлаку FeO і окислювання металу за реакцією: (FeO)=Fe+[O]. Розчинений кисень взаємодіє зі розчиненим у ванні вуглецем за реакцією [З] +[O]=CO. Відбувається бурхливе виділення бульбашок CO, які спінюють поверхню ванни, покритою шлаком. Бо у окисний період на металі наводять вапняний шлак із хорошою жидкоподвижностью, то шлак спінюється виділяються пухирями газу. Рівень шлаку стає вище порога робочого вікна і шлак випливає з печі. Вихід шлаку посилюють, нахиляючи піч убік робочого вікна на невеличкий кут. Шлак стікає в шлаковик), вартісну під робочої майданчиком цеху. Протягом часу окисного періоду окисляют 0,3—0,6% З з середньої швидкістю 0,3—0,5% С/ч. Для відновлення складу шлаку разом з рудою в піч додають вапно й невеличкі кількості плавикового шпату задля забезпечення жидкоподвижности шлака.
Безупинне окислювання ванни і скачування окисного вапняного шлаку є неодмінними умовами видалення зі сталі фосфору. Для перебігу реакції окислення фосфору 2[P]+5[O]=(P2O5); (Р2O5)+4(СаО)==(СаО)4*P2O5 необхідні високий вміст кисню в металі і шлаку, підвищений вміст CaO в шлаку і знижена температура.
У електропечі перші двоє умови повністю виконуються. Виконання останнього умови забезпечують наводкою свіжого шлаку й постійним оновленням шлаку, оскільки шлак, насичений (СаО)4*P2O5 скачивается з печі. Під час окисного періоду відбувається дегазація стали—удаление з її водню та азоту, що виділяються в бульки ЗІ, які відбуваються через металл.
Виділення пухирців ЗІ супроводжується ще й видаленням з металу неметалевих включень, які виносяться на поверхню потоками металу чи піднімаються нагору разом із бульбашками газу. Хороше кипіння ванни забезпечує перемішування металу, вирівнювання температури і состава.
Загальна тривалість окисного періоду становить від 1 до $ 1,5 год. Для інтенсифікації окисного періоду плавки, і навіть щоб одержати почав із низьким змістом вуглецю, наприклад хромонікелевої нержавіючої із вмістом вуглецю.
Окисний період закінчується, коли зміст вуглецю стає нижче заданого краю, зміст фосфору 0,010%, температура металу трохи вища температури випуску сталі з печі. Наприкінці окисного періоду шлак намагаються повністю прибирати з печі, скачивая його із поверхні металла.
Відновлювальний період плавки.
Після скачування окисного шлаку починається відбудовний період плавки. Завданнями відновного періоду плавки є: розкислення металу, видалення серы. коррек-тирование хімічного складу стали, регулювання температури ванни, підготовка жидкоподвижного добре раскисленного шлаку в обробці металу в час випуску з печі в ківш. Розкислення ванни, т. е. видалення розчиненої у ній кисню, здійснюють присадкою розкислювачів на метал і шлак. На початку відновного періоду метал покривається шаром шлаку. І тому в піч присаживают шлакоутворювальні суміші з урахуванням вапна з добавками плавикового шпату, шамотного бою, кварциту. Як розкислювачів зазвичай використовують феромарганець, феросиліцій, алюміній. При запровадження розкислювачів відбуваються такі реакции:
[Mn]+[O]=(MnO); [Si]+2 [Про] = (SiO2); 2[Al]+ 3[O]-(Al2O3).
Через війну процесів розкиснення більшість розчиненої кисню пов’язується в оксиди і видаляється з ванної як нерозчинних в металі неметалічних включень. Процес протікає досить швидко і тривалість відновного періоду переважно визначається часом, необхідним освіти рухомого шлаку. У малих та середніх печах при виплавці відповідальних марок сталей продовжують застосовувати метод диффузионного розкиснення стали через шлак, коли раскислители як меленого електродного бою, порошку феросиліцію присаживают на шлак. Зміст кисню в шлаку знижується і згідно до закону розподілу кисень з металу перетворюється на шлак. Метод цей, хоча й залишає в металі оксидних неметалевих включень, потребує значно більших витрат часу. У відбудовний період плавки, і навіть під час випуску стали під шаром шлаку, коли відбувається хороше перемішування металу зі шлаком, активно відбувається десульфурация металу. Цьому сприяє хороше розкислення сталі та шлаку, високий вміст винищити в шлаку та висока температура. У результаті відновного періоду вводять легирующие — ферротитан, феррохром та інших., і деякі, наприклад нікель, присаживают разом із шихтою. Нікель не окислюється і втрачається за плавленні. Добавки тугоплавких ферровольфрама, феррониобия роблять у початку рафінування, оскільки потрібно чимало часу їхнього розплавлювання. Нині більшість операцій відновного періоду переносять з печі в ківш. Наприклад, в кіш вводять порції легуючих чи дають їх у струмінь стали, що з печі у її нахилі. Присаживают у процесі випуску раскислители. Метою відновного періоду є забезпечення нагріву стали до заданої температури й створення шлаку, десульфурирующая здатність якого використовується за спільної випуску з печі разом із сталью.
Одношлаковый процесс.
У зв’язку з інтенсифікацією процесу электроплавки останніми роками отримав велике поширення метод плавки в дугового печі під шлаком. Сутність цього ось у чому: дефосфорация металу поєднується з періодом розплавлювання. Під час розплавлювання з печі скачують шлак і виробляють добавки винищити. У окисний період випалюють вуглець. Після досягнення в металі.
Переплавку отходов.
На заводах спеціальних сталей кількість які виникають відходів сягає 25—40% від виплавленої сталі. Частина відходів надходить із машинобудівних заводів, у электросталеплавильных цехах 50% легованих сталей виплавляють з шихти, яка перебуває тільки з них. Раціональне використання відходів дає зекономити чимало легуючих, електроенергії, підвищує продуктивність електропечей. У леговані відходи поділяють на 82 групи. При розрахунку шихти прагнуть використовувати якомога більше відходів даної марки стали чи найближчих марок.
Шихту складають із таким розрахунком, аби вміст вуглецю у ванні по расплавлении було в 0,05— 0,10% нижче заданого маркою стали. Необхідні легирующие, неокисляющиеся добавки Ni Cu, Mo, W завантажують разом із шихтою, а інші - V, Тi, Cr, Mn, Al, Si, Nb — прагнуть вводити якнайпізніше різних стадіях плавки, зокрема і під час випуску ківш. Метал заданого складу одержують у процесі рафинировки чи ковші. Під час плавки наводять вы-сокоосновной, жидкоподвижный шлак, який частково скачують з печі. Це дозволяє видалити до 30% фосфору. Якщо склад металу близький до розрахунковому, то ми не скачивая шлаку, розпочинають раскислению шлаку молотим коксом, ферросилицием і алюмінієм. У цьому легирующие елементи відновлюються з шлаку і переходить до метал, наприклад так відновлюється оксид хрому: 2(Cr2O3)+3 (Si)=3(SiO2)+4 [Cr]. Тривалість відновного періоду у тому варіанті технології така сама, як й у плавках з окисленням. Плавка на відходах значно коротші (приблизно за 1 год) проти плавкою на свіжої шихті з допомогою окисного періоду. Це збільшує продуктивність електропечей на 15—20% і скорочує витрати на 15%.
Методи інтенсифікації електросталеплавильного процесса.
Застосування кисню. Використання газоподібного кисню в окисний період плавки й у периодрасплавления дозволяє значно інтенсифікувати процеси розплавлювання і окислення углерода.
Застосування синтетичного шлака.
Цей метод передбачає перенесення рафінування металу з електропечі в розливальний ківш. Для рафінування металу виплавляють синтетичний шлак з урахуванням винищити (52−55%) і глинозему (40%) у спеціальній электродуговой печі із вугільною футеровкой. Порцію, рідкого, гарячого, активного шлаку (4−5% від безлічі стали, виплавленої в електропечі) наливають в основний сталеразливочный ківш. Ківш подають до печі у неї випускають сталь. Струмінь стали, падаючи з великою висоти, вдаряється про поверхню рідкого шлаку, розбивається на дрібні краплі і вспенивает шлак. Відбувається перемішування стали зі шлаком. Це активному перебігові обмінних процесів між металом і синтетичним шлаком. Передусім протікають процеси видалення сірки завдяки низькому змісту FeO в шлаку і кисню в металі; підвищеної концентрації вапна в шлаку, високої певній температурі й перемішуванню стали зі шлаком. Концентрація сірки то, можливо знижена до 0,001%. У цьому відбувається значне видалення оксидних неметалевих включень зі сталі завдяки асиміляції, поглинання цих включень синтетичним шлаком і перерозподілу кисню між металом і шлаком.
Обробка металу аргоном.
Після випуску сталі з печі через обсяг металу у ковші продувают аргон, що подають або через пористі пробки, зафутеро-ванные в днище, або через шви кладки подины ковша. Продування сталі у ковші аргоном дозволяє вирівняти температуру і хімічний склад стали, понизити зміст водню, видалити неметалеві включення, що в результаті дає можливість підвищити механічні і експлуатаційні властивості стали.
Застосування порошкоподібних материалов.
Продування сталі у дугового електропечі порошкообразными матеріалами в струмі газаносителя (аргону чи кисню) дозволяє прискорити найважливіші процеси рафінування сталі: обезуглероживание, дефосфорацию, десульфурацию, розкислення металла.
У струмені аргону чи кисню в ванну вдуваются порошки з урахуванням вапна, плавикового шпату. Для рас-кисления металу використовують порошкоподібний феросиліцій. Для окислення ванни й у прискорення удаленияуглерода і фосфору додають оксиди заліза. Мел-кораспыленные тверді матеріали, потрапляючи в ванну металу, мають велику поверхню контакту з металом, в багато разів перевищує площа контакту ванни зі жужільним шаром. У цьому происходитинтенсивное перемішування металу з твердими частинками. Усе це сприяє прискоренню реакцій рафінування сталі. З іншого боку, порошкообразные флюси можна використовувати до швидшого наведення шлака.
Плавка у кислому электропечи.
Кислі електропечі футеруют вогнетривкими матеріалами з урахуванням кремнезему. Ці печі мають глибші ванни й у з цим менший діаметр кожуха, менші теплові втрата часу та витрати. Стійкість футерівки зводу і стін кислої печі значно вища, ніж в основний. Це малої тривалістю плавки. Печі із кислою футеровкой місткістю 1—3 т застосовують у ливарних цехах для сталевого лиття і виливків з ковкого чавуну. Вони допускають періодичність у роботі, т. е. роботи з перервами. Відомо, основна підбійка швидко зношується при частому охолодженні. Витрата вогнетривів на 1 т сталі у кислої печі нижче. Кислі вогнетриви дешевше, ніж основні. У кислих печах швидше розігрівають метал до високої температури, що необхідне лиття. Недоліки кислих печей пов’язані насамперед із характером шлаку. У цих печах шлак кислий, яке складається переважно з кремнезему. Тому такий шлак Демшевського не дозволяє видаляти зі сталі фосфор і на сірку. Щоб мати цих домішок у припустимих межах, необхідно підбирати спеціальні шихтові матеріали, чисті за фосфором і з сірці. З іншого боку, кисле сталь має зниженими пластичними властивостями проти основний сталлю внаслідок присутності металі высококремнистых неметалічних включений. Технология плавки у кислому електропечі має такі особливості. Окисний період плавки нетривалий, кипіння металу йде слабко, оскільки кремнезем пов’язує РеО в шлаку і тим самим швидкість переходу кисню на метал для окислення вуглецю знижується. Кислый шлак більш в’язкий, він утрудняє кипіння. Шлак наводять присадками піску, використаної формовочной землі. Вапно присаживают до вмісту у шлаку трохи більше 6—8% СаО. Розкислення кислої стали проводять, зазвичай, присадкою кускового феросиліцію. Частково сталь раскисляется кремнієм, який відновлюється з шлаку або з футерівки по реакцій: (SiO2)+2Fe=2(FeO)+[Si]; (SiO2)+2[C]=2CO+[Si]. На відміну від основного процесу при кислому феромарганець присаживают наприкінці плавки в роздробленому вигляді у ківш. За такої способі засвоюється до 90% марганцю. Кінцеве розкислення проводять алюминием.
Одержання низьковуглецевої коррозионностойкой стали (процеси AOD і VOD).
Широке поширюються методи виробництва низьковуглецевої коррозионностойкой стали поза электропечи.
Метод AOD. У електропечі виплавляють основу нержавіючої стали, що містить заданий кількість хрому і нікелю, з допомогою недорогих, высокоуглеродистых феросплавів. Потім сталь разом із пічним шлаком заливають в конвертер, профіль якого представлений рис. 81. Підбійка конвертера виготовлено з магнезитохромитового цегли. Стійкість футерівки до 200 плавок. У нижньої зоні футерівки, у третій ряду цегельною кладки від днища конвертера. Фурмы є конструкцію з мідної внутрішньої труби і зовнішньої труб із нержавіючої стали, внутрішній діаметр фурмы 12—15 мм. Початкова зміст вуглецю в стали то, можливо для ферритных хромистых сталей 2,0—2,5%, а аустенитных сталей 1,3—1,7%. У перші 35 хв сталь продувают сумішшю кисню і аргону у відсотковому співвідношенні 3: 1. Щоб уникнути перегріву металу у про, конвертер присаживают брухт — даної марки стали, феррохром тощо. п. Потім протягом 9 хв сталь продувают сумішшю кисню і аргону у відсотковому співвідношенні 1:1. Саме тоді концентрація вуглецю знижується до 0,18%. У третьому періоді в продувочном газі ще більше зменшують ставлення кисню до аргону до 1:2, продувку продовжують ще 15 хв. Упродовж цього терміну зміст вуглецю знижується до 0,035%. Температура підвищується до 1720 °C. Наприкінці продувки присаживают вапно і феросиліцій на відновлення хрому з шлаку. Після поновлення шлак, у якому 1% Cr2O3, скачивается і після наведення нового шлаку проводять остаточну продувку аргоном. Причому у шлак переходить сірка, неї давав в металі знижується до 0,010%.
Через війну процесу AOD отримують високоякісну нержавіючу сталь з низьким змістом вуглецю, сірки, азоту, кисню, сульфідних і оксидних неметалічних включень, з високими механічними властивостями. На підвищення економічності процесу аргон частково заміняють азотом. Середня тривалість продувки становить 60—120 хв, витрата аргону становить 10—23 м3/т, кисню 23 м3/т. На рис. 82 представлено зміна температури і складу металу. Ступінь вилучення хрому становить 98%.
Метод VOD. Цей метод вакуумно-кислородного обезуглероживания з продувкой аргоном. У основі методу лежить здійснення реакції [C]+[O]=CO, рівновагу якої у вакуумі зсувається в праву бік. Чим нижчий парціальний тиск ЗІ, тим нижче мусить бути залишкова концентрація вуглецю в стали. У цьому складаються сприятливі умови на відновлення оксиду хрому вуглецем, що дає змогу провадити процес обезуглероживания не мають відчутних втрат хрому зі шлаком. Коррозионностойкую сталь виплавляють в електропечі з досить високою змістом вуглецю (0,3—0,5%); сталь випускають у спеціальний ківш з хромомагнезитовой футеровкой, у яких в днище фурму на шляху подання аргону. Ківш встановлюють в вакуумну камеру, відкачують повітря і починають продувку киснем згори через водоохолоджувальну фурму, яку вводять у камеру через кришку. Одночасно виробляється продування аргоном через дно ковша. Після закінчення продувки проводять присадку розкислювачів і легуючих для коригування складу. Витрата аргону у тому способі значно нижчі від ніж у AOD (всього 0,2 м3/т). Одержуваний сталь містить дуже низькі концентрації вуглецю (0,01%) за низького вмісту азоту. Окислювання хрому незначне. Для видалення сірки в ківш завантажують вапно, що дозволяє після розкиснення і короткочасного перемішування аргоном знизити концентрацію сірки в металі до необхідних меж. У порівняні з процесом AOD його складніший вживається для сталей відповідального призначення за низьким змістом вуглецю. До переваг те й інше процесу треба віднести економію дорогого низкоуглеродистого феррохрома, зазвичай який використовувався і при отриманні нержавіючої сталі у дугових печах, і навіть досягнення низьких змістів вуглецю без великих втрат хрома.
Індукційні печі і плавка в них.
Нині індукційні печі знаходять широке використання у металургії і машинобудуванні. У лабораторіях використовують високочастотні печі ємністю і від кількох грам до 100 кг, в ливарних цехах низькоі среднечастотные печі до 2—6 т; найбільші печі мають ємність до 60 т. У порівняні з дуговими на електропечі в індукційних печах відсутність електродів і електричних дуг дає можливість отримувати почали і сплави з низьким змістом вуглецю і газів. Плавка характеризується невеликим чадом легуючих елементів, високим електричним до. п. буд" точним регулюванням температури металла.
Недоліком печей є холодний, погано перемешиваемый шлак, яка дозволяє як і інтенсивно, як і дугових печах, проводити процеси рафінування. Стійкість футерівки в печах невысокая.
Основний тип сучасних високочастотних чи індукційних печей — це печі без сердечника. Така піч складається з индуктора-катушки, навитой з мідної трубки з водяникам охолодженням. Всередину індуктора вставляється або готовий вогнетривкий тигель, або тигель набивається порошкообразным огнеупорным матеріалом. При накладення на індуктор змінного електричного струму частотою від 50 до 400 кГц утворюється змінне магнітне силове полі, пронизуюче простір всередині індуктора. Це магнітне полі наводить в металевої садці вихрові токи.
Пристрій індукційних печей.
У центрі печі поміщений індуктор. Вона має вид соленоида і виготовлений із профилированной мідної труби. По трубі йде вода на її охолодження. Усередині індуктора набитий вогнетривкий тигель. Струм подається по гнучким кабелям. Піч криється у металевий кожух. Згори тигель закривається склепінням. Поворот печі для зливу металу здійснюється навколо осі, розташованої у зливального шкарпетки. Поворотні цапфы печі почивають на опорних підшипниках станин. Нахил печі проводиться з допомогою реечного механізму через рухливі шарниры-цапфы чи гідроприводом. Невеликі печі похиляють з допомогою тали.
Підбійка печей то, можливо кислої чи основний, набивної або цегляної. Для набивки використовують вогнетривкі матеріали різної крупности від часткою міліметра до 2—4 мм. Для основний футерівки застосовують порошок магнезита з добавками хромомагнезита і борної кислоти для зв’язки. Кислі суміші готують з урахуванням меленого кварциту. Набивання тигля ведуть пошарово навколо металевого шаблону, форма якого відповідає профілю тигля.
Після закінчення набивки футеровку спекают і ліплять. У залізний шаблон завантажують чавун, включають струм, метал поступово розігрівається і нагріває футеровку. Потім метал доводять до плавлення. У першій плавленні розплавляють м’яке залізо, що дозволяє досягти високої температури для випалу футерівки. Великі печі футеруют фасонным огнеупорным кирпичом.
Електричне оборудование.
Індукційні печі живить струм високої частоти від лампових генераторів чи струмом середньої частоти (2500 гц) від машинних перетворювачів. Великі печі працюють на струмі промислової низькою частоти (50 Гц від мережі). Ці печі часто служать як міксерів рідкого металу у ливарних цехах.
У схему входять машинний генератор, батарея конденсаторів і автоматичний регулятор, плавильний контур. Преосвітній агрегат складається з асинхронного електродвигуна, обертаючого генератор і динамо-машину, що дає струм в обмотки порушення генератора.
Для компенсації реактивної потужності і шляхом створення електричного резонансу встановлюють батарею конденсаторів. Частина конденсаторів то, можливо відключена зміни емкостной складової. Резонанс буває за умови? L=1/?C (L-коэффициент самоиндукции печі, З — ємність конденсатора,? — кутова частота). Підбираючи зміну ємність, можна працювати за умов, близьких до резонансу, тобто. підтримувати co? близька до одиниці. Автоматичний регулятор електричного режиму підтримує оптимальну електричну потужність взаємозалежним регулюванням co?, напруження і сили тока.
Технологія плавки сталі у індукційною печи.
Плавку проводять на високоякісному брухті зі зниженим вмістом фосфору і сірки. Великі й малі шматки так вкладають в тигель чи баддю, з допомогою якої завантажують великі печі, що вони щільно заповнювали обсяг тигля. Тугоплавкі феросплави вкладають на дно тигля. Після завантаження включають струм на повну потужність. Принаймні проплавления і осідання скрапу подгружают шихту, не увійшла відразу в тигель. Коли останні шматки шихти зануряться в рідкий метал, на поверхню металу закидають шлакоутворювальні матеріали: вапно, магнезитовый порошок, плавиковый шпат. Шлак захищає метал від контакту з атмосферою, запобігає теплові втрати. Під час плавлення шлак раскисляют добавками порошку коксу, меленого феросиліцію. Метал раскисляют кусковыми феросплавами і наприкінці алюмінієм. Під час плавлення дають добавки легуючих. Оскільки чаду легуючих мало відбувається, то індукційних печах можна виплавляти сплави складного состава.
Список використаної литературы.
Металургія чорних металів; Б. В. Линчевский, О. Л. Соболевський, А. А. Кальменев.