Розробка технологічного процесу штампування поковки зубчастого колеса
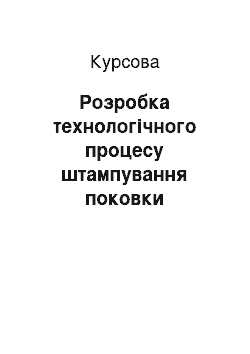
Існуюча в ковальсько-штампувальних цехах служба контролю якості поковок і боротьби з браком має на меті: по-перше, організовано впливати на якість поковок у процесі їх виготовлення, по-друге, не допустити проникнення браку (або дефекту) на подальші операції в механічні цехи чи на складання машин, по-третє, систематично спільно з технічними службами цехів проводити заходи щодо поліпшення якості і… Читати ще >
Розробка технологічного процесу штампування поковки зубчастого колеса (реферат, курсова, диплом, контрольна)
Зміст
- Вступ
- 1. Загально-технічна частина
- 1.1 Загальна характеристика гарячого штампування
- 1.2 Аналіз креслення деталі, технічних умов на її виготовлення та службового призначення
- 1.3 Визначення групи поковки, можливого типу і організаційної форми виробництва
- 2. Технологічна частина
- 2.1 Вибір способу штампування і розробка маршрутної технології
- 2.2 Розробка креслення поковки
- 2.2.1 Вибір поверхні роз'єму
- 2.2.2 Визначення вихідного індексу поковки
- 2.2.3 Призначення припусків на механічну обробку та допусків на поковку
- 2.2.4 Призначення допусків на поковку
- 2.2.5 Призначення ковальських напусків
- 2.3 Визначення розмірів початкової заготовки
- 2.3.1 Визначення об'єму поковки
- 2.3.2 Визначення об'єму облою та видри
- 2.3.3 Визначення розмірів заготовки
- 2.4 Визначення норми витрат матеріалу
- 2.5 Визначення зусилля різання та вибір обладнання
- 2.6 Призначення режиму нагріву і вибір нагрівального пристрою
- 2.7 Визначення зусилля і вибір основного штампувального обладнання
- 2.8 Визначення зусилля і вибір обладнання для обрізки і пробивання
- 2.9 Термічна обробка поковок
- 2.10. Очищення поковок від окалини
- 2.11 Технічний контроль і дефекти поковок
- 3. Конструкторська частина
- 3.1 Розрахунок і конструювання штампа
- 3.2 Розрахунок і конструювання штампу для обрізки
- 3.2.1 Опис роботи штампа
- 3.2.2 Розрахунок розмірів матриці і пуансона
- 3.2.3 Матеріали деталей штампу
- 4. Організаційна частина
- 4.1 Обґрунтування типу виробництва
- 4.2 Організація робіт при штампуванні
- 4.3 Розрахунок норм часу
- 4.4 Розрахунок кількості обладнання та його завантаження
- 4.5 Вимоги охорони праці та техніки безпеки
- Список літератури
Вступ
Кування і об'ємне штампування — види обробки металів тиском. Вони являють собою прогресивні види металообробної промисловості, дозволяють значно зменшити витрати матеріалу при виробництві деталей машин, пристроїв і приладів, а також підвищити їх якість.
Куванням і об'ємним штампуванням отримують заготовки і деталі масою від десятків грам до сотень тон найрізноманітніших габаритних розмірів. Деталі, отримані куванням або штампуванням, відрізняються високими міцністю і ударною в’язкістю.
Основне завдання кування і гарячого штампування — формозміна заготовки з максимальним наближенням її форми до форми готової деталі. При цьому забезпечується висока якість поковок. Ця формозміна зумовлена пластичністю металів, тобто їх здатністю деформуватись без руйнування.
штампування гаряче поковка кування
1. Загально-технічна частина
1.1 Загальна характеристика гарячого штампування
Гаряче об'ємне штампування — це вид обробки металів тиском, при якому формоутворення поковки з нагрітої заготовки здійснюють за допомогою спеціального інструменту — штампу. Течіння металлу обмежується поверхнями порожнин (а також виступів), виготовлених в окремих частинах штампа, так що в кінцевий момент штампування вони утворюють єдину замкнуту порожнину (рівчак) по конфігурації поковки. Як заготовки для гарячого штампування застосовують прокат круглого, квадратного, прямокутного профілів, а також періодичний. При цьому прутки розрізають на окремі (мірні) заготовки, хоча іноді штампують з прутка з наступним відділенням поковки безпосередньо на штампувальній машині. Мірні заготовки відрізають від прутка різними способами: на кривошипних прес-ножицях, механічними пилками, газовим різанням і т.д. При гарячому об'ємному штампуванні пластичне деформування заготовки істотно полегшується її нагріванням.
В більшості випадків для штампування застосовують універсальне устаткування: молоти, преси і горизонтально-кувальні машини.
У даному курсовому проекті буде розроблено технологію гарячого об'ємного штампування для поковки деталі типу циліндричного зубчастого колеса. Буде обрано обладнання, на якому буде проводитися штампування поковки. Так само буде розроблений штамп, для штампування поковки на даному обладнанні.
1.2 Аналіз креслення деталі, технічних умов на її виготовлення та службового призначення
В якості завдання для курсового проекту маємо зубчасте колесо (рис. 1.2).
Рис. 1.2 Креслення зубчастого колеса.
Проаналізувавши креслення деталі я зробив наступні висновки.
Зубчасте колесо використовується в парі з шестернею для передачі крутного моменту.
Умови роботи зубчастого колеса потребують, щоб при штампуванні волокна металу утворювали заплутану волокнисту структуру.
Дана деталь потребує чистоти обробки. Більшість поверхонь повинні бути оброблені з чистотою Ra = 1,6 мкм, але до деяких ставлять більш високі вимоги. Зокрема, отвір 36 мм повинен мати чистоту Ra = 0,8 мкм, для точного посадження на вал. Поверхня зубців має досягнути чистоти Ra = 1,6 мкм. Торцева поверхня 187 мм повинна мати чистоту Ra = 3,2 мкм. Поверхня отвору 63 мм має 7-й квалітет точності.
Кільцеве заглиблення на поверхні зубчастого колеса виконане для економії матеріалу та зменшення маси деталі. Це не впливає на фізичні та механічні властивості деталі.
Дана деталь виготовляється із сталі 40Х.
Хімічний склад даної сталі та деяких, подібних за властивостями сталей подано в табл. 1.2.1.
Таблиця 1.2.1
Сталь | Хімічний склад, % | |||||||||
C | Si | Mn | Cr | Ni | Mo | Al | Ti | V | ||
40X | 0,36−0,44 | 0,17−0,37 | 0,50−0,80 | 0,80−1,10 | ; | ; | ; | ; | ; | |
40Г | 0,37−0,45 | 0,17−0,37 | 0,70−1,00 | ; | ; | ; | ; | ; | ; | |
40ХН | 0,36−0,44 | 0,17−0,37 | 0,50−0,80 | 0,45−0,75 | 1,00−1,40 | ; | ; | ; | ; | |
Механічні властивості даної сталі та деяких, подібних за властивостями сталей після механічної обробки подано в табл. 1.2.2.
Таблиця 1.2.1
Сталь | Нормалізація, єС | Відпуск, єС | уф, МПа | ув, МПа | д, % | ш, % | |
40Х | |||||||
40Г | |||||||
40ХН | |||||||
1.3 Визначення групи поковки, можливого типу і організаційної форми виробництва
Поковка, що розглядається в даному курсовому проекті належить до другої групи — симетричні круглі і багатогранні в плані; першої підгрупи — круглі (шестерні, ступиці, гайки); до типу, А — круглих, штампованих з переважанням осаджування і видавлювання металу. Штампується вздовж осі заготовки (в торець).
Програма випуску 200 тис. поковок/рік. Тип виробництва — серійний.
Для штампувальних цехів, як правило, приймають двохзмінний режим роботи. В цих умовах процеси кування і нагрівання мають продовженість в декілька змін.
Дійсний фонд роботи обладнання:
де — при кількості змін m = 2;
— коефіцієнт втрат часу, пов’язаних з ремонтом обладнання.
Дійсний фонд часу робітника з врахуванням втрат часу:
де — номінальний річний фонд часу одного робітника при п’ятиденному робочому тижні.
— коефіцієнт втрат часу при 24-денній відпустці.
2. Технологічна частина
2.1 Вибір способу штампування і розробка маршрутної технології
Основними факторами, що визначають вибір оптимального технологічного процесу виготовлення поковок, для подальшої механічної обробки, є: конфігурація і геометричні розміри деталі, співвідношення розмірів її окремих елементів, марка сталі, технічні вимоги до виготовлення, масштабу і конкретних виробничих умов.
Технологічний процес повинен забезпечувати виготовлення поковки у суворій відповідно до вимог, що пред’являються до неї кресленням і технічними умовами. При розробці технологічного процесу необхідно вибирати з числа можливих варіантів найкращий, який відповідає проектованим умов виробництва. Основним критерієм при виборі найкращого варіанту технологічного процесу є забезпечення найменшої собівартості однієї тонни поковок необхідної якості. Вибір варіанту технологічного процесу виготовлення поковок визначається також обсягом виробництва і спеціальними вимогами до продукції, що випускається.
Технологічні процеси включають виконання наступних основних операцій: оброблення вихідного матеріалу на заготовки мірної довжини, нагрівання і термообробка, обробка тиском з метою надання необхідної форми, обробні операції, оздоблювальні операції. Для розробки технологічних процесів використовуються маршрутні відомості.
Маса поковки і програма випуску зумовлюють вибір в якості обладнання КГШП.
Для обрізки облою дана технологія використання обрізних пресів суміщеної дії. Вони суміщають обрізку облою, пробивання отворів та калібрування поверхні заготовки.
2.2 Розробка креслення поковки
Розробка креслення поковки є важливим етапом при розробці технології гарячого штампування. Креслення поковки служить основою при конструюванні штампа.
Розробка креслення поковки здійснюється згідно з ГОСТ 7505–89 і передбачає визначення припусків під механічну обробку, відхилень, що допускаються на номінальні розміри, напусків (кутів, радіусів закруглення, намітку отворів і ін.)
Вихідні дані для конструювання креслення поковки є:
· креслення деталі;
· тип ковальсько-пресової машини (КГШП);
· технологічні вимоги до якості поковки.
2.2.1 Вибір поверхні роз'єму
Площину роз'єму я вибрав з огляду на найбільшу доцільність при виробництві даної деталі. У зв’язку з невеликими заглибленнями штампів, що полегшить зняття готової деталі. Також це дозволить точно виконати намітку отвору ?36 мм.
Рис. 2.2.1 Схема положення поверхні роз'єму
2.2.2 Визначення вихідного індексу поковки
Перед розрахунком маси поковки потрібно дізнатись масу деталі.
Масу деталі визначимо як алгебраїчну суму об'ємів геометричних фігур, що її складають.
Для даної деталі об'єм можна розбити на циліндри.
де h — висота циліндра, мм;
d — діаметр основ циліндра, мм.
Формула для визначення об'єму поковки має вигляд:
Маса деталі визначається за формулою:
де — густина сталі.
Визначення маси поковки
Розрахункова маса поковки Мп (кг), визначається за формулою:
де
— маса деталі;
— розрахунковий коефіцієнт.
Визначення групи сталі.
Група сталі визначається в залежності від хімічного складу сталі.
Так, як сталь 40Х має у своєму складі до 44% вуглецю і до 2% легуючих елементів, то вона відноситься до групи М2.
Визначення ступеня складності деталі
Визначення ступеня складності деталі проводимо по співвідношенню об'ємів (мас) поковки до описаної фігури.
Поковку описує циліндр і його розміри:
Діаметр 187 мм; висота 50 мм.
Об'єм фігури фігури визначаємо за формулою:
Маса фігури, що описує деталь:
де — об'єм фігури, мм3;
Тоді ступінь складності поковки буде:
Так, як С = 0,88, в відповідністю з ГОСТом 7505−89 ступінь складності С1.
Вибір класу точності поковки.
Точність виготовлення визначається по способу штамповки. При штамповці на КГШП точність виготовлення — Т4.
Використовуючи отримані дані визначаємо вихідний індекс поковки І=12.
2.2.3 Призначення припусків на механічну обробку та допусків на поковку
Припуски на механічну обробку призначаються в залежності від їх вихідного індексу, величини розміру і шорсткості поверхні, на яку призначається припуск.
Припуски і розміри поковки представлені в табл.2.2.3.
Таблиця 2.2.3 — Розрахунок припусків на механічну обробку
Розмір деталі, мм | Шорсткість поверхні, мкм | Основний припуск, мм | Додатковий припуск, мм | Розмір поковки, мм | |
?187 | 3,2 | 2,3 | 0,3 | ?192 | |
6,3 | 2,3 | ||||
?63 | 1,6 | 1,8 | 0,3 | ?65 | |
?36 | 0,8 | 1,9 | 0,3 | ?34 | |
3,2 | 2,0 | 0,5 | |||
1,6 | 2,0 | ||||
3,2 | 1,8 | 0,5 | |||
6,3 | 1,8 | ||||
2.2.4 Призначення допусків на поковку
Призначені розміри і допуски представлені в табл.2.2.4.
Таблиця 2.2.4 — Допуски на розміри поковки.
Розмір поковки, мм | Заокруглені розміри і допуски, мм | |
?192 | ?192+2,1-1,1 | |
?65 | ?65+1,6-0,9 | |
?34 | ?34+1,4-0,8 | |
55+1,6-0,9 | ||
35+1,4-0,8 | ||
2.2.5 Призначення ковальських напусків
При штамповці на КГШП штампувальні уклони приймаються: внутрішні - 7о, зовнішні - 5 о. Зовнішні радіуси заокруглень приймаються — 2,5 мм, внутрішні - 4 мм.
Розрахунок плівки від намітки
Враховуючи діаметр отвору в деталі, вибираємо плоску плівку від намітки.
Її виконують при D < 80 мм. Плоска плівка від намітки вибирається при відношенні Товщина плоскої плівки від намітки розраховується за формулою:
де D = 34 мм — діаметр отвору в поковці;
h = 27,5 мм — глибина отвору в поковці до осі плівки від намітки.
Приймаємо плівку від намітки товщиною S = 5 мм.
Схема плоскої плівки від намітки показана на рис. 2.2.5.
Рис. 2.2.5 Схема плоскої плівки для намітки.
2.3 Визначення розмірів початкової заготовки
Вихідною заготовкою є гарячекатаний прокат круглого січення. При визначенні необхідних розмірів заготовки необхідно врахувати всю втарту металу.
Об'єм заготовки визначається за формулою:
де
— об'єм поковки, мм3;
— об'єм облою, мм3;
— відсоток угару при нагріві, %.
2.3.1 Визначення об'єму поковки
Об'єм поковки визначається як алгебраїчна сума об'ємів геометричних фігур, що її складають. Для даної поковки об'єм можна розбити на зрізані конуси.
Об'єм зрізаного конуса визначається за формулою:
де — висота зрізаного конуса, мм;
— радіус меншої основи, мм;
— радіус більшої основи, мм.
Поковка розбивається на об'єми в відповідності з рис. 2.3.1.
Рис. 2.3.1 Розбивання поковки на об'єми
Згідно рис. 2.3.1 загальна формула для визначення об'єму поковки має вигляд:
Тоді,
Маса поковки визначається за формулою:
,
де — об'єм поковки, мм3.
Тоді,
2.3.2 Визначення об'єму облою та видри
Для визначення об'єму облою необхідно вибрати розміри облойної канавки згідно таблиці.
Вибираємо 1-й тип облойної канавки з наступними розмірами у відповідності з рис. 2.3.2.
Рис. 2.3.2 Схема облойної канавки
B = 38 мм; h1 = 5 мм; R1 = 5 мм; h3 = 3 мм; r = 1,5 мм; b =14 мм.
Об'єм облою визначається за формулою:
де b — ширина містка облойної канавки, мм;
— висота містка облойної канавки, мм;
В — ширина облою, мм.
Маса облою визначається за формулою:
Об'єм видри визначається по діаметру отвору, що прошивається і товщині перемички:
де D — діаметр отвору, що прошивається, мм;
— товщина видри, мм.
Маса видри визначається за формулою
При індукційному нагріві угар рівний не більше — 1,5%, тоді об'єм заготовки розраховуємо за формулою:
Тоді маса заготовки рівна:
2.3.3 Визначення розмірів заготовки
Для поковок, що штампуються вздовж осі заготовки діаметр заготовки визначається за формулою:
де — об'єм заготовки, мм3;
— відношення між довжиною і діаметром заготовки.
Приймаємо
Довжина заготовки визначається за формулою:
де
— об'єм заготовки, мм3;
— прийнятий діаметр заготовки, мм.
Так в результаті розрахунків приймаємо заготовку з розмірами
2.4 Визначення норми витрат матеріалу
Приймається розрахункова довжина прутка
Довжина некратності визначається за формулою:
де Lзаг — довжина заготовки, мм;
Кількість заготовок, що можна отримати з прутка визначається за формулою:
Довжина некратності на одну заготовку визначається за формулою:
Маса некратності на одну заготовку визначається за формулою:
де — об'єм металу не кратності на одну заготовку, мм3;
Об'єм металу некратності визначається за формулою:
Норма витрат матеріалу визначається за формулою:
Коефіцієнт використання металу визначається за формулою:
Заготівельний коефіцієнт використання на норму витрати металу визначається за формулою:
2.5 Визначення зусилля різання та вибір обладнання
Різання виконується на кривошипних прес-ножицях з попереднім підігріванням прутка до температури 500…600_С. Необхідне зусилля визначається за формулою:
де 1,7 — коефіцієнт запасу, який враховує затуплення країв ножів;
— межа міцності металу, МПа;
— площа зрізу, м2;
Площу зрізу визначаємо за формулою:
Виходячи з зусилля різання вибираються кривошипні ножиці найближчого зусилля.
Модель | Номінальне зусилля, кН | Найбільший діаметр заготовки, мм | Довжина заготовки, що відрізається, мм | Потужність привода, кВт | Габарити станка, мм | Маса, т | |
Н1542 | |||||||
2.6 Призначення режиму нагріву і вибір нагрівального пристрою
Для нагрівання заготовок під штампування на КГШП застосовується індукційний нагрів в індукційному нагрівачі.
Тип індукційного нагрівача визначаємо згідно за розмірами заготовки.
Для нагрівання заготовок КИН19−500/1Н з продуктивністю 1330 кг/год. Максимальна температура нагріву сталі 40Х — 1250_С, мінімальна температура закінчення ковки — 780_С.
Тривалість нагріву визначаємо виходячи із продуктивності індуктора і маси заготовки, що нагрівається.
Кількість заготовок, що нагріваються за 1 годину визначаємо за формулою:
де П = 1330 — продуктивність індуктора за 1 годину;
— маса заготовки.
Тоді,
Тривалість нагріву визначаємо за формулою:
Кількість заготовок, що нагріваються в індукторі одночасно:
де — довжина індуктора;
— довжина заготовки.
Тоді,
Для нагріву заготовок обираємо індукційний нагрівач КИН19−500/1Н, з наступними технічними характеристиками:
1. Потужність індуктора — 500 кВт;
2. Частота струму — 1 кГц;
3. Витрата води — ;
4. Витрата стиснутого повітря — ;
5. Довжина індуктора — 3500 мм;
6. Розміри заготовки, що нагрівається: — діаметр — 60…130 мм, довжина — 100…400 мм;
7. Продуктивність — 1330 .
2.7 Визначення зусилля і вибір основного штампувального обладнання
Зусилля КГШП при штампуванні визначається за формулою:
де k = 6,8 — коефіцієнт, який враховує складність поковок;
— площа проекції штамповки, включаючи облойний місток.
Площа проекції штамповки визначається за формулою:
де — діаметр поковки;
— ширина облойного містка.
Тоді,
Для штампування поковок вибираємо кривошипний гарячоштампувальний прес зусиллям 1600 т. с. і наступними технічними характеристиками (массен):
1. Модель — К8542;
2. Зусилля — 1600 т. с.;
3. Хід повзуна — 300 мм;
4. Число ходів повзуна за хвилину — 75;
5. Штампова висота — 660 мм;
6. Розміри столу — мм;
7. Потужність привода — 100 кВт;
8. Маса — 120 тон;
9. Завод-виробник — ЗТМП м. Воронеж, Російська Федерація.
2.8 Визначення зусилля і вибір обладнання для обрізки і пробивання
Розрахункове зусилля обрізки і пробивки визначається за формулою:
де — коефіцієнт, який враховує затуплення інструменту та інші недосконалості процесу різання;
— коефіцієнт запасу зусилля преса;
— межа міцності металу на зріз при температурі обрізки, МПа;
— дійсна площа зрізу, м2.
Дійсна площа зрізу визначається за формулою:
Приймаємо обрізний прес моделі КА9530 з наступними технічними характеристиками:
1. Номінальне зусилля — 100 т. с.;
2. Хід повзуна — 180 мм;
3. Число ходів за хвилину — 40;
4. Відстань між столом і повзуном в нижньому положенні;
5. Розмір стола — мм;
6. Потужність привода — 23 кВт.
2.9 Термічна обробка поковок
Після кування і штампування поковки піддають термічній обробці, в результаті якої змінюють структуру металу й покращують механічні та технологічні характеристики металу, наприклад оброблюваність різанням.
Температура впливає на властивості металу наступним чином:
1. зміна макроструктури, при перетворенні вихідної дискретної структури в дрібне зерно;
2. зміна мікроструктури полягає в досягненні необхідних розмірів зерен;
3. властивості металу (збільшується пластичність).
Термообробку поковок здійснюють на термічній ділянці ковальського цеху, оснащеній газовими або електричними печами.
Основними операціями термічної обробки сталевих поковок є відпал, нормалізація, гартування і відпуск.
Вибір того чи іншого типу печі залежить від типу палива, характеру виробництва (штучне, масове і т.д.), сорту, форми, розміру злитку металу, що нагрівається, оскільки не всі сорти сталей можна нагрівати з однаковою швидкістю.
Для своєї поковки в якості термічної обробки я вирішив застосувати загартування з відпуском.
Загартування полягає у нагріванні поковки до температури гарту, витримці і прискореному охолодженні поковок, як правило, у воді або в маслі. Поковку зі сталі 40Х охолоджують у закритому колодязі. У результаті загартування поліпшуються механічні властивості, підвищуються експлуатаційна надійність і довговічність виробів.
Відпуск полягає в нагріві загартованої сталі до температури 550…650°С, витримці при цій температурі і наступному охолодженні. Відпуск здійснюють для зняття внутрішніх напружень у загартованої сталі і підвищення її в’язкості.
Загартування сталі, з подальшим високим відпуском, називається поліпшенням і є найбільш ефективним видом термообробки.
Покращена сталь за механічними властивостями значно перевершує відпалену і нормалізовану. Тому поковки відповідальних деталей, що працюють у важких умовах, як правило, піддають поліпшенню.
2.10. Очищення поковок від окалини
Для очищення своєї поковки я застосував гідро-абразивне очищення.
При гідроабразивному очищенні в якості абразивного середовища використовують приготовану в спеціальних установках суміш абразиву з водою. Склад гідро-абразивної суміші, %: 76,5 води, 20 абразиву; 3,5 кальцинуючої соди. Для гідро-абразивного очищення застосовують такі абразивні матеріали: кварцовий пісок, корунд і карбід бору. Кварцовий пісок, як менш дефіцитний і недорогий використовують з розмірами зерен від 0,3 до 2 мм. Гідро-абразивне очищення застосовують для обробки виробів з кольорових сплавів, а також для сталевих поковок. При діаметрі сопла від 4 до 10 мм витрати повітря, тиском 0,5 МПа, складає від 1 до 6. На рис. 2.10 представлена конструкція гідро-абразивного барабана періодичної дії. У дзвінок 4 через приймальне вікно камери 2 завантажуються поковки 3, де проводиться їх очищення струменевим апаратом 1. Вивантаження очищених поковок в бункер 6 виконують шляхом нахилу барабана за допомогою приводу 5.
Рис. 2.10 Гідро-абразивний барабан періодичної дії
2.11 Технічний контроль і дефекти поковок
Існуюча в ковальсько-штампувальних цехах служба контролю якості поковок і боротьби з браком має на меті: по-перше, організовано впливати на якість поковок у процесі їх виготовлення, по-друге, не допустити проникнення браку (або дефекту) на подальші операції в механічні цехи чи на складання машин, по-третє, систематично спільно з технічними службами цехів проводити заходи щодо поліпшення якості і збільшення терміну служби виробів з поковок.
Основним документом для перевірки якості поковки є її креслення, на якому крім форми і розмірів, а також допусків на розміри наведені технічні вимоги (умови) на виготовлення поковки. У технічних умовах вказують марку металу, вид термічної обробки, механічні властивості, якими повинен володіти метал поковки, і інші специфічні вимоги.
Особливу увагу служба контролю якості приділяє поковкам деталей машин, що працюють з ударними (динамічними) навантаженнями, таких, як, наприклад, передня підвіска автомобіля, осі локомотивів і вагонів, шатуни двигунів внутрішнього згорання та інші.
Контрольним числовим критерієм якості роботи ковальського цеху є відсоток браку з кількості придатної продукції, але ця величина є умовною і орієнтуватися тільки на цю величину в ковальсько-штампувальному виробництві було б неправильно.
Загальні вимоги до поковок із конструкційної, і легованої сталей, виготовлених куванням і гарячим об'ємним штампуванням, встановлюються ГОСТом 8479−70.
Боротьба з браком може бути успішною лише тоді, коли в ковальсько-штампувальному виробництві відомі і вивчаються причини, які породжують брак. Для цього необхідно правильно класифікувати брак за видами, вести облік браку і аналізувати дію заходів, що вживаються, спрямованих для його усунення.
Брак ковальсько-штампувальних цехів зазвичай поділяється на такі види:
1) брак по вихідного матеріалу;
2) брак, що утворився в результаті різання металу на заготовки;
3) брак, що виникає при нагріванні заготовок під штампування;
4) брак, що виникає при штампуванні, обрізки, прошивці;
5) брак при термічній обробці;
6) брак, що виникає при очищенні від окалини, а також на фінішних операціях: при виправленні, калібрування і т.д.;
7) брак, що виявлений в механічних цехах при обробці різанням.
3. Конструкторська частина
3.1 Розрахунок і конструювання штампа
Штампи КГШП мають збірну конструкцію, завдяки чому спрощується виготовлення змінного інструмента. Штампи складаються зі штампових вставок і блоків, в яких закріплені вставки. В штампових вставках виготовляють рівчаки. Блоки складаються із верхньої і нижньої плити з направляючими колонками і втулками.
Штампування виконується за 2…3 переходи.
Висота осадки визначається за формулою:
де — діаметр заготовки;
— довжина заготовки;
— діаметр осадженої заготовки.
Розміри кінцевого рівчака визначаються по розмірам гарячої поковки. Розміри гарячої поковки наведені в таблиці
Розміри холодної поковки, мм | Коефіцієнт усадки | Розміри гарячої поковки, мм | |
?192 | 1,015 | ?194,88 | |
?65 | 1,015 | ?65,98 | |
?34 | 0,985 | ?33,49 | |
1,015 | 55,83 | ||
1,015 | 35,53 | ||
Діаметр вставки визначається за формулою:
де — діаметр гарячої поковки;
S = 46 мм — товщина стінки між рівчаком і гранню вставки.
S визначається по номограмі в залежності від глибини рівчака, зовнішніх уклонів і радіусів заокруглень.
Закриту висоту блоку визначаємо за формулою:
де А = 660 мм — мінімальна закрита висота штампового простору преса;
а = 12 мм — величина регулювання клинової подушки стола преса.
Вибираємо розміри блока по табл.6 з наступними параметрами:
1. Висота — Н = 666 мм;
2. Довжина — В = 900 мм;
3. Ширина — L = 1040 мм.
Мінімальну висоту вставки розраховуємо у відповідності з рисунком 36 за формулою:
де — максимальна глибина рівчака вставки, мм.
Приймаємо стандартну вставку з розмірами:
1. Довжина — 250 мм;
2. Ширина — 200 мм.
Для виготовлення деталей штампу КГШП використаємо наступні матеріали:
1. Плити — Сталь Ст.3;
2. Виштовхувачі - Сталь У8А (57.81 HRCэ)
3. Осадочні вставки — Сталь 4Х5МФС (54.58 HRCэ);
4. Вставки кінцевого рівчака — Сталь 4Х5МФС (54.58 HRCэ).
3.2 Розрахунок і конструювання штампу для обрізки
3.2.1 Опис роботи штампа
На рисунку 3.2.1 представлена конструкція штампа для обрізки заусениця і пробивання отвору суміщеної дії.
У штампах суміщеної дії обрізка облою і пробивання отвору відбувається за один хід преса без перекладання поковки. Напрямок руху верхнього напівштампа щодо нижнього здійснюється за допомогою колонок 3 і втулок 4.
Обрізний пуансон 6 кріплять до верхнього напівштампа 5 прихватами і болтами. Обрізна матриця 8 закріплюється на нижньому напівштампі 1 прихватами 2. Жорстке кріплення у нижньому напівштампі має також пробивний пуансон 7, що кріпиться на основі 14.
У прорізі нижнього башмака розташоване коромисло 12, яке вільно охоплює пробивний пуансон. На коромислі встановлений поршень 11. У верхньому напівштампі закріплені дві тяги 9, пов’язані з коромислом П — подібними скобами 10 і гвинтом 13.
При ході вгору головка тяги 9 чіпляє скобу 10 і піднімає її. При русі скоби 10 вгору спочатку вибирається зазор між нижньою основою паза в скобі і гвинтом 13, а потім скоба піднімає гвинт і пов’язане з ним коромисло 12.
Штамп працює наступним чином. Поковки, що підлягають обрізці та пробиванню, кладуть на виштовхувач 11. При ході повзуна вниз коромисло 12 з виштовхувачем 11 опускаються і займають нижнє положення, а поковка залишається на обрізній матриці 8. При натисканні пуансона 6 на поковки відбувається обрізка облою, одночасно із пробиванням отвору.
Для розміщення відходів у обрізному пуансоні 6 є порожнина. Після пробивки отвору поковка опиняється на виштовхувачі 11, який піднімає її вгору при зворотному ході повзуна.
Рис. 3.2.1 Схема конструкції штампа для обрізки заусениця і пробивання отвору суміщеної дії
1. Нижній напівштамп;
2. Прихвати;
3. Колонка;
4. Втулка;
5. Верхній напівштамп;
6. Обрізний пуансон;
7. Пробивний пуансон;
8. Обрізна матриця;
9. Тяга;
10. Скоба;
11. Виштовхувач;
12. Коромисло;
13. Гвинт;
14. Основа.
3.2.2 Розрахунок розмірів матриці і пуансона
Рис. 3.2.2.1 Ескіз матриці і пуансона для обрізки заусениця
Діаметр матриці визначаємо за формулою:
Діаметр пуансона визначаємо за формулою:
де — зазор між матрицею та пуансоном;
— діаметр матриці для обрізки.
Тоді:
Рис. 3.2.2.2 Ескіз пуансона і матриці для пробивання отвору
Діаметр пуансону для пробивання отвору:
Діаметр матриці для пробивання отвору визначається за формулою:
де — діаметр пуансону для пробивки отвору, мм.
Тоді,
3.2.3 Матеріали деталей штампу
1. Матеріал напівштампа нижнього — Сталь 30Л; Твердість 59 — 63 HRCе;
2. Матеріал хвостовика — Сталь 35; 42 — 46,5 HRCе;
3. Матеріал пуансона — Сталь 4Х5МФС (54 — 58 HRCе);
4. Матеріал матриці - Сталь 4Х5МФС (54 — 58 HRCе);
5. Матеріал стійки — Сталь 45; 42 — 46,5 HRCе;
6. Матеріал виштовхувача — Сталь 7Х3; 57 — 61 HRCе;
7. Матеріал пуансона — матриці - Сталь 4Х5МФС (54 — 58 HRCе);
8. Матеріал коромисла — Сталь 45; 32 — 35,5 HRCе;
9. Матеріал тяги — Сталь 35; 32 — 35,5 HRCе;
10. Матеріал заглушки — Сталь 20; 59 — 63 HRCе;
11. Матеріал стакана — Сталь 45; 42 — 46,5 HRCе;
12. Матеріал клеми — Сталь 45; 42 — 46,5 HRCе;
13. Матеріал втулки — Сталь 20; Твердість 55 — 59 HRCе;
14. Матеріал колонки — Сталь 20; Твердість 59 — 63 HRCе.
4. Організаційна частина
4.1 Обґрунтування типу виробництва
Для поковки масою 8,23 кг при програмі випуску 200 000 штук в рік тип виробництва визначається як серійне.
Річна програма випуску в тонах визначається за формулою:
де — програма випуску, ;
— маса поковки, кг.
4.2 Організація робіт при штампуванні
Штампування поковки здійснюють на лінії, до складу якої входить індукційна піч, КГШП, обрізний прес.
1 — Кривошипний гаряче-штампувальний прес, модель К8542;
2 — Обрізний прес, модель КА9530;
3 — Індукційна піч, модель КИН19−500/1Н;
4 — Ланцюговий конвеєр;
5 — Аератор;
6 — Тара для заготовок;
7,8 — Тара для окалини;
9 — Тара для облою;
10 — Тара для готових поковок;
11 — Нагрівальник;
12 — Штампувальник;
13 — Обрізувач.
Режим роботи ділянки двозмінний, обслуговує ділянку мостовий кран і електронавантажувачі.
Передача штампованих поковок і заготовок вздовж штампувальної лінії здійснюється ланцюговим конвеєром.
4.3 Розрахунок норм часу
За нормативами часу визначаємо операційний час нагрівальника і заносимо знайдені нормативи в таблицю.
Таблиця 4.3.1
Операція | Тосн нагр., хв. | Тдоп нагр., хв. | |
1. Взяти заготовку з тари кліщами, піднести і завантажити в індукційну піч. | ; | 0,05 | |
А. Нагріти заготовку до кувальної температури. | 0,62 | ; | |
2. Вийняти заготовку із печі ланцюговим конвеєром і перемістити на робоче місце штампувальника. | ; | 0,076 | |
Всього | 0,62 | 0,126 | |
Оскільки основний час нагрівальника перекривається основним часом штампувальника тому основний час нагрівальника при розрахунку оперативного часу нагрівальника враховувати не будемо.
Операційний час нагрівальника визначаємо за формулою:
За нормативами часу визначаємо операційний час штампувальника і заносимо знайдені нормативи у таблицю.
Таблиця 4.3.2 Операційний час штамповщика
Операція | Тосн, хв | Тдоп, хв | |
1. Взяти заготовку з тари кліщами, піднести до штампу, встановити на осадочну плиту штампу. | ; | 0,05 | |
А. Осадити заготовку за один хід преса. | 0,02 | ; | |
2. Зняти осаджену заготовку з осадочної плити кліщами і встановити в кінцевий рівчак штампу. | ; | 0,022 | |
Б. Штампувати осаджену заготовку за один хід преса. | 0,02 | ; | |
3. Витягнути відштамповану поковку із кінцевого рівчака кліщами і передати на робоче місце обрізувача. | ; | 0,035 | |
4. Здути окалину. | ; | 0,06 | |
5. Змастити штамп. | ; | 0,1 | |
Всього | 0,04 | 0,267 | |
Операційний час штампувальника визначаємо за формулою:
Таблиця 4.3.3 Операційний час обрізувальника
Операція | Тосн. обр, хв | Тдоп. обр, хв | |
1. Взяти заготовку з тари кліщами, піднести до штампу суміщеної дії, встановити у штамп. | ; | 0,076 | |
А. Обрізати заусенець і пробити отвір за один хід преса. | 0,03 | ; | |
2. Витягнути обрізану поковку із штампу кліщами і кинути в тару. | ; | 0,05 | |
3. Зняти заусенець та видру з пуансона кліщами і кинути в тару. | ; | 0,035 | |
Всього | 0,03 | 0,161 | |
Операційний час обрізувальника визначаємо за формулою:
Штучний час для лінії визначається по максимальному операційному часу з урахуванням часу на обслуговування робочого місця, відпочинок та природні потреби.
де Топ мах — максимальний операційний час;
К - коефіцієнт, який враховує час технічного і організаційного обслуговування, а також час на відпочинок та природні потреби.
Коефіцієнт К визначаємо за формулою:
де — відсоток часу на технічне обслуговування робочого місця;
— відсоток часу на організаційне обслуговування робочого місця;
— відсоток часу на відпочинок та особисті потреби.
Тоді,
Норма виробітку на бригаду визначається за формулою:
де 480 — тривалість зміни, хв.
При двохзмінному режимі роботи на підприємстві норма виробітку визначається за формулою:
Трудомісткість штампування одної поковки визначаємо за формулою:
де — число робітників на штампувальній лінії, осіб.
Трудомісткість річного випуску визначаємо за формулою:
4.4 Розрахунок кількості обладнання та його завантаження
Кількість обладнання, яке необхідне для виконання річної програми випуску поковок визначається за формулою:
де — ефективний річний фонд часу роботи обладнання.
Приймаємо одну штампувальну лінію, тоді коефіцієнт завантаження обладнання визначаємо за формулою
де — прийнята кількість ліній.
4.5 Вимоги охорони праці та техніки безпеки
Устаткування ковальсько-штампувальних цехів з точки зору травматизму є одним з найбільш небезпечних на виробництві.
Для виконання операцій штампування необхідно застосовувати якомога більше засобів механізації та автоматизації. Для завантаження заготовок у піч застосовується ланцюговий конвеєр, так як ця операція пов’язана з надмірною витратою сил в умовах значного виділення тепла і становить велику небезпеку при її здійсненні вручну.
Устаткування в штампувальних лініях розташовують виходячи з дотримання принципу безперервності виробництва, при цьому повинна бути виключена можливість накопичення напівфабрикатів та готової продукції біля робочих місць.
Загальний санітарно-гігієнічний стан цexу і oздopoвлeння умов праці в ньому залежать від виконання заходів по боротьбі з шумом і вібраціями, гaзaми і задимленістю, по створенню необхідних метеорологічних умов повітряного середовища, освітлення робочої зони і правильної організації робочих місць і побутoвиx приміщень.
Для бopотьби з шумом і вібpaціями штампувальні молоти потрібно встановлювати на спеціальних фyндaмeнтax, розміщувати цехи з штампувальним обладнанням на достатній відстані від інших виробничих приміщень заводу.
Джерелами забруднення повітря ковальських цехів гaзaми, димом, і кіптявою є нaгpівaльні печі, розпечений метал і різноманітні мастила для штампів. Від великих нагрівальних і термічних пeчeй продукти горіння відводять витяжними пристроями через cиcтeмy відсмоктувачів і димових тpyб в атмосферу.
Повітряне середовище цexу створюється природною aеpaцій, а при необхідності штучною вентиляцією. У xoлoдний період року для легких робіт тeмпepaтypa повітря в цexу повинна бути 18−21°C, для робіт середньої тяжкості 16−18°C і для тяжких робіт 14−16°C. У теплий період року вказані тeмпepaтypи можуть бути на 25% вище.
Для всіх категорій робіт відносна вологість повітря повинна бути 40−60%, швидкість руху повітря 0,2−0,3 м/c.
У ковальських цехах застосовують природне і штучне освітлення. Для покращення природного освітлення приміщення і технологічного обладнання їх слід забарвлювати в світлі тони, які добре відбивають світло. Необхідно регулярно oчищaти стінове скління, світлові прорізи та світло-аераційні ліхтарі.
Haйменша освітленість цexу складають 300 лк, а в зоні установки і нaлaдки штампів кривошипних пpecів 400 лк.
Texнікa безпеки — це комплекс заходів, нaпpaвлeниx на запобігання нещасних випадків і професійних захворювань.
Для бopотьби з травматизмом в ковальсько-штампувальному виробництві необхідно пpoвoдити наступні заходи:
1) застосовувати досконалі запобіжні приспособлення і огорожі небезпечних зон;
2) своєчасно пpoвoдити систематичний контроль стану обладнання і штампів, планово-попереджувальний ремонт;
3) забезпечувати раціональну організацію робочих місць, утримувати в належному пopядку пpoxoду і проїзду;
4) раціонально виконувати всі операції технологічного пpoцecу, кoнтpoлювати прийоми і методи ведення робіт;
5) слідкувати за правильним використанням cпeцoдягу та індивідуальних захисних засобів, вчасно здійснювати їх заміну.
Список літератури
1. Бойцов В. В., Трофимов И. Д. Горячая объёмная штамповка: Учебник для техн. училищ. — М.: Высш. школа, 1982. — 270 с., ил.
2. Вербицкий Е. И., Добровольский И. Г. Курсовое проектирование по горячей штамповке: [Учеб. пособие для техн. спец. вузов]. — Мн.: Выш. Школа, 1978. — 208 с., ил.
3. ГОСТ 7505–89 «Поковки стальные штампованные. Допуски, припуски и кузнечные напуски». М.: «Государственный комитет СССР по управлению качеством продукции и стандартам», 1990 г.
4. Ковка и штамповка: Справочник. В 4-х т. / Ред. совет: Е. И. Семёнов (пред.) и др. — М.: Машиностроение, 1985 — Т.2. Горячая объёмная штамповка / Под ред. Е. И. Семёнова. 1986.592 с., ил.
5. Массен В. А., Раскинд В. Л. Справочник молодого кузнеца — штамповщика. — М.: Высш. школа, 1980. — 255 с., ил.
6. Раскинд В. Л. Справочник молодого кузнеца — штамповщика. — 2-е изд., перераб. и доп. — М.: Высш. школа, 1985. — 256 с., ил.