Анализ ні економічна оцінка технологій у кольорової металлургии
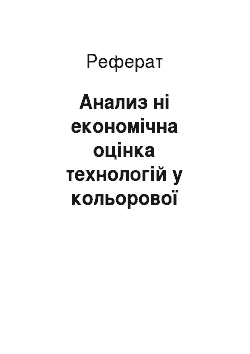
При виплавці высокоуглеродистой сталі та у випадках, коли зміст вуглецю в окисний період зменшується в металі нижче заданих меж, після видалення шлаку ванну науглероживают. Для науглероживания металу у піч завантажують електродний бій, кокс, а інших випадках чушковый чавун малим змістом шкідливих домішок — фосфору і сірки. У цьому загрузочное вікно щільно закривають щоб уникнути надходження кисню… Читати ще >
Анализ ні економічна оцінка технологій у кольорової металлургии (реферат, курсова, диплом, контрольна)
Міністерство освіти і науки Украины.
Східноукраїнський національний университет.
им. Даля.
РЕФЕРАТ.
на задану тему: «Аналіз ні економічна оцінка технологій у кольорової металлургии».
Выполнил: студент групи УП-211 Зарубін Е.А. Перевірив: Хаустова А.В.
Луганськ 2002 г.
План.
1. Роль і значення металу у економіці страны.
2. Пристрій і принцип роботи доменної печи.
3.Шихтовые матеріали та його підготовка до доменної плавке.
4. Види виплавленого чавуну та його назначение.
5. Суть доменного процесса.
6.Сырьё щоб одержати стали.
7. Пристрій і двухванных сталеплавильних аппаратов.
8. Пристрій і конверторов.
9. Установка і електричних печей для виплавки стали.
10. Технологія виплавки сталі у Мартенівської сети.
11. Технологія виплавки сталі у конверторе.
12. Технології виплавки сталі у Електричної печи.
13. Суть агломерації (призначення агломерації, сировину, процес агломерації, оборудование).
1. Роль і значення металу у економіці страны.
Як відомо, метали діляться на дві групи: чорні і кольорові. До чорним ставляться залізо та її сплави (чавун, сталь); інші метали — кольорові (зокрема і редкие).
Метали отримують двома шляхами: пирометаллургическим (вогняним) і гидрометаллургическим (мокрим). При металургійному способі метали не виплавляють, а выщелачивают в розчини, звідки потім виділяють електроліз чи іншими способами.
Особливе місце серед металів займають залізо та її сплави, складові на вагу 85—90% всього застосовуваного металу у СНД Галуззю, зайнятою виробництвом і які первинної обробкою заліза та її сплавів, є чорна металургія — основа розвитку сучасної в промисловості й технічного озброєння всього народного хозяйства.
Вироби з кольорових металів та його сплавів вживають переважно при опорядженні монументальних адміністративних і культурно-побутових будинків, і навіть при спорудженні споруд, які стосуються першому класу. Для цього використовують мідь, латунь, бронзу, алюміній і сплави з алюмінію та інших кольорових металів для художнього литья.
Найбільшого використання у сучасному будівництві знаходить алюміній. З нього виготовляють віконні і дверні коробки, віконні халепи і обрамлення скляних дверних полотен; з міцних алюмінієвих сплавів (дюралюміній та інших.) роблять легкі стеновые і перегородочные панелі, плити перекриттів, стропильные і мостові ферми тощо. п.
2. Пристрій і принцип роботи доменної печи.
У сучасному доменної печі є коксових бункера, розташованих над скиповой ямою, і трьох десятків бункерів для руди, агломерату, флюсів та інших материалов.
Під бункерами для коксу розташовані дискові гуркоту й терези. Доменна піч має скиповые підйомники на шляху подання матеріалів. Розвантаження матеріалів виробляють шляхом перекидання скиповой вагонетки в загрузочное пристрій печи.
Загрузочное пристрій і двох воронок, закритих двома конусами. З вагонетки шихту зсипають в верхню малу вирву на конус. Потім конус опускається і шихта падає в нижню вирву, на нижній конус. У цьому верхній конус піднімається, а нижній опускається і шихта надходить на колошник.
Робота засипного апарата і скіпового підйомника сблокирована і управляється автоматично з панельного щита.
Для зниження витрат коксу в доменну піч відцентровими воздуходувками подається гаряче повітря за нормальної температури 900—1100° З. Як приводу для повітродувок застосовують парові турбіни, працюючі при тиску до 30 am. Сучасні воздухонагреватели (рис. 1) здатні нагрівати повітря кількості 2000—2500 м3/мин до температури 900 — 1100° З. Збільшення кількості повітря і підвищення його температури досягаються з допомогою збільшення поверхні нагріву насадок до 16 000— 18 000 m2 і спалювання газів до 3600 ма/час і більше. Висота воздухонагревателя становить 46 м при.
3.Шихтовые матеріали та його підготовка до доменної плавке.
Вихідні матеріали, що подаються в доменну піч, — паливо, руда, агломерат, флюси, і навіть повітря перетерплюють фізичні і хімічні зміни. Відповідно з температурними зонами в печі відбуваються такі фізико-хімічні процеси: горіння палива, видалення вологи, розкладання карбонатів, відновлення заліза та інших елементів, коксування заліза, плавлення металу, освіту й плавлення шлаку і другие.
Завантажене в доменну піч паливо опускається рівня фурм і згоряє в струмені що надходить під тиском 1,5—2,0 am повітря, шгретого до 800— 1000° З повагою та вищої реакции.
4. Види виплавленого чавуну та його назначение.
Вуглець в чавуні може у вигляді механічної домішки р (графіту) і у вигляді хімічного з'єднання з залізом, званого карбідом чи цементитом железа.
Залежно від цього практично розрізняють два виду чавуну: чавун, у якому вільний графіт і що у зламі сірий чи темно-сірий колір і крупнозернистое будова. Такий чавун називають сірим чи ливарним чавуном його застосовують для отливок.
Чавун, яке у основному кількості вуглець як хімічного з'єднання з залізом FeC і має білий блискучий злам, називають білим граничним чавуном. Цей чавун переважно переробляється в сталь.
Одержання тієї чи іншої виду чавуну залежить кількості вуглецю, кремнію, марганцю, фосфору і сірки в шихті (табл. 2), які частково переходить до чавун, і навіть від процесу плавки в доменної печи.
5. Суть доменного процесса.
Найважливішими показниками роботи доменної печі є: 1) коефіцієнт використання корисного обсягу доменної печі; 2) витрати на т выплавленного чавуну. Коефіцієнт використання корисного обсягу доменної печі k є ставлення корисного обсягу печі до добової її производительности:
Доменна піч працює краще, що менше числове значення k зазвичай коефіцієнт k у межах від 0,45 до 1,35 і вкриваю його величину впливають такі чинники: а) вміст заліза в руді, б) підготовка шихтовых матеріалів до плавленні; в) сорт выплавленного чугуна.
При плавленні передільного чавуну k ~ 0,7—0,9,а що на деяких заводах k < 0,7; наприклад, на Череповецком металургійному заводі k = 0,45 м/т.
Витрата пального залежить від сорти виплавленого чавуну. Для виплавки 1 m передільного чавуну витрата коксу становить від 600 до 800 кг, бессемеровского чавуну від 800 до 1000 кг, ливарного чавуну від 800 до 1200 кг, спеціальних чавунів і феросплавів від 1750 до 2500 кг. Витрата шихти і рівень її використання є дуже важливими показниками, котрі характеризують економічність роботи доменної печі. Це визначається матеріальним балансом доменної плавки. Приблизний їх матеріальний баланс на 1 m виплавленого чавуну приведено у табл. 3.
[pic].
6.Сырьё щоб одержати стали.
Сталлю називають сплави заліза з вуглецем і другими.
елементами. Такі сплави мають пластичними властивостями як в.
нагрітому, і у холодному стані, і може піддаватися прокатке,.
волочению, куванню, штамповке.
[pic].
Сталь містить до 2% вуглецю та деяка кількість марганцю, кремнію, і навіть шкідливі домішки (фосфор і на сірку). Крім цих домішок, в стали можуть утримуватися и.
[pic] легирующие елементи: хром, нікель, ванадій, титан і др.
Нині сталь виробляють переважно шляхом переділу чавуну, у якому з чавуну видаляється надлишок вуглецю, кремнію, марганцю, і навіть шкідливих домішок щоб надати їй необхідних властивостей. Вуглець та інші домішки за високої температури поєднано з аналітичними киснем набагато енергійніше, ніж залізо, і можна видалити при незначних втрати железа.
Вуглець чавуну, з'єднуючись з киснем, перетворюється на газ (окис вуглецю ЗІ) і улетучивается.
Інші домішки перетворюються на окисли SiO2, MnO і Р2О5, які внаслідок меншого проти металом частки спливають й утворюють шлак.
Нині у промисловості переважно застосовують конверторний і мартенівський методи отримання сталі; ще, сталь одержують у електричних дугових і індукційних печах.
7. Пристрій і двухванных сталеплавильних аппаратов.
Мартенівська піч має такі основні частини: робоче чи плавильне простір, голівки з вертикальними каналами, шлаковики, регенеративные камери з насадками, газодымовые кабани, воздушнодымовые кабани, перекладні устрою, загальний дымоходовой борів, підмурок і залізобетонні підвалини під робоче простір. Кожна піч має димову трубу.
Нижню частину робочого простору називають подом. Піч має передню стіну, у якій розташовані завалочные вікна, і задню стіну, у якій перебувають випускні отвори для стали. До торцевым стінах печі прилягають голівки, службовці для входження у робоче простір палива й повітря й у відводу продуктів горіння. Готування у вигляді вертикальних каналів з'єднуються за газовими і повітряними шлаковиками, які поєднано з аналітичними регенераторными камерами, мають цегельну кладку.
Унизу регенераторных камер перебувають поднасадочные канали, з'єднані газодымовыми і воздуходымовыми кабанами, якими відводяться продукти горіння, а на газ і повітря вступають у поднасадочные канали регенераторів. На газодымовых і воздуходымовых боровах встановлено перекладні устрою (клапани), службовці зміни напрями газу, повітря і продуктів горения.
Над робочим простором печі є звід. У середовищі сучасних мартенівських печах склепіння роблять підвісного типу. Мартенівська шихта через садочные вікна завантажується у робочий простір печі, а рідкий чавун заливається з ковшів. Необхідна для процесу тепло йде від смолоскипа, що утворюється від спалюваного у робочому просторі печі рідкого чи газоподібного топлива.
У печах, працівників газовому паливі, гази рухаються так. Газ й повітря надходять із правої боку, а продукти горіння з робочого простору йдуть із лівого боку. Тоді через правий газовий клапан надходить газ, який проходить під насадочное простір газового регенератора, а ще через правий повітряний клапан в під насадочное простір правого регенератора надходить повітря. Газ й повітря, піднімаючись вгору, обмивають насадку, нагріваються до температури 1000—1200° З, та був потрапляють у під насадочную частина регенератора. Звідси проходять через шлаковики піднімаються по вертикальним каналам до прольотам головок, якими потім вступають у робоче простір печі. При виході з головок нагріті до високої температури на газ і повітря змішуються й у робочому просторі утворюють факел, температура полум’я якого складають 1800—1900° С.
Продукти горіння разом із уносимой з робочого простору печі пилом утворюють димові гази, що йдуть через голівки. Менша частина газу іде газовим шляху, а велика — по повітряному шляху. По вертикальним каналам димові гази потрапляють у шлаковики, де частково осаджується уносимая газами пил. Гази, пройшовши шлаковики з температурою 1450—1500° З, вступають у регенераторы. Проходячи через регенеративную насадку, вони їй тепла і за нормальної температури 500—600° З йдуть із одна садочного простору в борів димовою труби. Коли температура насадки з боку знизиться, а температура насадки з боку підвищиться, відбувається перекидка клапанів зміни напрями потоку газу та повітря. Після цього знову нагрівається насадка правих регенераторів тощо. буд. мартенівських печей сприяє зниження питомої витрати палива, і навіть підвищенню продуктивності та стійкості печей. Повна автоматизація мартенівських печей передбачає автоматичне регулювання горіння палива на робочому просторі, перекидки клапанів, регулювання дешевих навантажень, подачі повітря і воды.
По виду вихідних матеріалів розрізняють кілька радикальних способів плавки:
1. Плавка на твердому чавуні і металевому брухті, звана «скраппроцессом».
2. Плавка на рідкому чавуні, коли він для окислення домішок вводять руду; такий спосіб називають рудним процессом.
3. Плавка на рідкому чавуні, скрапе і руді, звана скрап-рудным процессом.
Рудний і скрапрудный процеси ведуть лише у основних печах, V позаяк у кислих печах під і стіни руйнуються закисью заліза, котра міститься в руде.
Плавку сталі у мартенівських печах ведуть скраппроцессом за тими / заводах, де немає доменних печей щоб одержати рідкого чугуна.
Для плавки стали скраппроцессом в мартенівську піч завантажують сталевої брухт (скрап), чушковой переробний чавун і вапно. Співвідношення сталевого брухту до чушковому чавуну приймають таке, щоб завантажена шихта мала таке зміст домішок: 2,4% З; 0,65% Si; до $ 1,5% Мп; до 0,13% Р і 0,05% P. S. Завантаження шихти ведуть прискорено, не допускаючи охолодження печі. Під час розплавлювання шихти майже зовсім окислюється кремній і лише частково окислюється вуглець, марганець і фосфор. Після розплавлювання зміст домішок в металі знижується і як: З — 1,0%, Si — сліди; Мп — 0,25%, Р — 0,05% і P. S — 0,040%.
Над розплавленим металом утворюється шар шлаку, багатий закисью заліза. Подальший процес окислення домішок протікає під шаром шлаку з допомогою растворяющейся закису заліза в металі, яка переходить з шлаку. Процес переходу закису заліза на метал протікає так. Закис заліза FeO окислюється лежить на поверхні шлаку з допомогою кисню полум’я до РезО4, которая, диффундируя через шар шлаку за українсько-словацьким кордоном рідкого металу, окисляє залізо по реакции:
Fe3O4 + Fe = 4FeO.
Які Утворюються скислы переходить до шлак. Кремнезем і пятиокись фосфору, переважно, пов’язуються з окисом кальцію, створюючи двукальциевый силикат.
SiO2 + 2СаО — 2 (СаО) — SiOa. і сіль фосфорної кислоты.
(FeO)3 • Р205 + 4СаО —> (СаО)4 • Р2О5 + 3FeO.
Для міцного сполуки пятиокиси фосфору в шлаку підтримується вільна окис кальцію. Утворений шлак з печі зливають у тому, ніж було відбудовано фосфору з шлаку на метал. За цей період плавки температура металу підвищується, і вуглець входить у реакцію з закисью железа.
З — FeO —> Fe + СО.
Під час окислення вуглецю ванна кипить, метал перемішується, залізо відновлюється з FeO, з металу видаляються сірка, неметалеві включення і газы.
Для знесірчення металу у ванну додають свежеобожженную вапно. По певній температурі й змісту вуглецю метал доводять до заданих технологічних меж відповідно до одержуваної маркою стали. Після кипіння в почали дедалі ще залишається певна кількість закису заліза, тому після закінчення плавки метал раскисляют шляхом введення розкислювачів: марганцю, кремнію чи алюминия.
Що стосується отримання легованої стали після розкиснення на метал вводять легирующие добавки у складі феросплавів (феррохрома, ферротитана та інших.) чи чисті метали (нікель, мідь та інших.). Готову сталь з печі випускають в ковші, які з допомогою кранів подають до дільниць розливання сталі. Вихід рідкої стали у своїй процесі плавки становить близько 96% ваги загружаемой металевої шихти в печь.
8. Пристрій і конверторов.
Сутність конверторного способу отримання сталі у тому, що за рідкий чавун, залитий в конвертор, родувается повітря, кисень якого окисляє вуглець та інші примеси.
Наведено загальний, вид звичайного конвертора грушоподібної форми, звареного з товстого листової сталі та футерованного всередині вогнетривкими матеріалами. Зовні у неповній середній частини конверторів є циліндричних виступу, званих цапфами" які є для опори і повороту конвертора. Один із цапф робиться порожнистої і сполучається з воздуховодом; від цапфы до днища через трубу і повітряну коробку підводиться повітря. У днище конвертора є отвори — фурмы, якими під тиском 2,0— 0,5 am.
[pic].
Малюнок 2. Конвертор: 1-Механизм для повороту конвертора, 2- вогнетривка кладка,.
3-шлак, 4-металл, 5- канали на шляху подання воздуха.
У конверторах застосовують кислу основну футерівки. Тепло, необхідне нагріву рідкої стали до високих температур, у тих процесах виходить з допомогою хімічних реакцій окислення домішок чугуна.
У цьому домішки можуть окисляться елементарним киснем і киснем закису заліза, яка розчиняється в металі. При окислюванні домішок киснем виділяється значну кількість тепла.
Домішки окислюються елементарним киснем за такими реакциям:
Si + О2 —> SiO2 •+ О;
При окислюванні елементів найбільше тепла виділяють кремній, фосфор і марганець. Ці елементи використовуються при продувке чавуну як джерело тепла (кремній в кислому, а фосфор переважно конверторе). Недостатня кількість тепла від реакцій компенсується температурою рідкого чугуна.
Для отримання сталі методом продувки застосовують два сорти чавунів: марки Б1 і Б2 — для кислого і Т1 —для основного процессов.
Чавун марки Б1 і Б2 містить мінімум фосфору (0,07%) і сірки (0,06%), чавун марки Т1 містить фосфору 1,6—2,0%, інколи ж до 2,5%.
9. Установка і електричних печей для виплавки стали.
Дугові електричні печі ємністю від 1,5 до 250 т побудовано у за принципом використання тепла від електричної дуги, образующейся між графітовими чи вугільними електродами і металевої ванній, розвиваючими температуру до 3500 °C і від, Піч (рис. 3) складається з циліндричного кожуха зі сферичним днищем Ці частини зсередини футеруются теплоизоляционной і вогнетривкої кладкою отже утворюється робоче простір печі. Звід печі робиться знімним; він викладається з динасового чи хромомагнезитового цегли в залізному каркасе-кольце.
Останнім часом збільшення терміну їхніх служби що на деяких заводах застосовують водоохлаждаемые склепіння як металевих конструкцій з теплоизолирующей прошарком з вогнетривких матеріалів. Піч має загрузочное вікно і випускне отвір для випуску металу. Загрузочное вікно закривається футерованной дверкой що піднімається і опускається з допомогою механізму. Піч встановлено на два опорних сегмента на направляють фундаменту задля підтримання та нахилу з допомогою механізму як і бік випуску металу, і у бік завантажувального вікна. У зведенні печі влаштовують три отвори для електродів. Електроди закріплюють в электрододержателях. Піднесення і опускання электрододержателей з електродами у процесі плавки здійснюються автоматичної блокуванням. Для харчування електричний струм подається від понижувального трансформатора по гнучкому кабелю і мідним шинам до електродах. Первинна обмотка трансформатора харчується струмом високої напруги 6000—30 000 в, який перетворюється на струм низького напруги кількох щаблів від 90 до 280 в. Потужність трансформатора переважно визначається ємністю печи.
Залежно від ємності печі електроди застосовують різних діаметрів. Графітові електроди проти вугільними мають вищу міцність і менше опір електричному струму. З практичних даних встановлено, що зі збільшенням ємності печі витрати зменшується і як від 600 до | | |1000 квт-ч на 1 т стали. Витрата електродів | | | | |залежить також від Л характеру перероблюваної | | | | |шихти. Працюючи на твердої шихті на 1 т стали| | | | |витрачається 12—18 кг вугільних електродів і південь від 5| | | | |до 8 кг графітових; під час роботи на рідкої шихті| | | | |витрата їх скорочується приблизно тричі. | | |Рис.3 Электродуговая піч: 1-| | Тривалість процесу плавки збільшується| | |кожух, 2-днище, 3-под, 4-свод,| |на підвищення ємності печі і як при | | |5-электроды | |переробці рідкої шихти 1,5—4 год і 4—8 год | |.
— твердої шихты.
Чад металу становить 1—3% під час роботи на рідкої шихті і 5—8% на твердой.
Кількість плавок на добу сягає 3—4 при твердою і 6—8 при рідкої шихті. Електричні дугові печі ємністю понад 10 m зазвичай використовують на металургійних заводах, а печі з не меншою ємністю — в сталеливарних цехах щоб одержати фасонных сталевих отливок.
Складовими шихти при плавленні сталі у електричних печах є сталевої брухт, чавун, залізна руда, флюси, раскислители і феросплави, що використовують запровадження легуючих добавок в сталь.
Плавку стали ведуть основним і кислим процесами. Для плавки стали основним процесом під і стіни печі футеруют основними матеріалами (магнезитовым цеглою), а плавки кислим процесом — кислими матеріалами (динасовым кирпичом).
10. Технологія виплавки сталі у Мартенівської сети.
Плавка сталі у основних мартенівських печах рудним процессом.
Плавку сталі у мартенівських печах ведуть рудним процесом на таких металургійних заводах, які у собі мають доменні печі, але мають прокатно-кузнечного производства.
При рудній процесі на сталь переробляють рідкий чавун, отримуваний в доменних печах. Для прискорення окислення домішок чавуну в завалку додають чисту залізну руду в.
які виникають окислів завантажують вапняк. Рудний процес плавки стали відрізняється від скраппроцесса тим, що ні потрібно витрат тепла і часу на розплавляння металу і процеси окисления.
11. Технології виплавки сталі у конверторе.
Для заливання рідкого чавуну конвертор повертають з вертикального положення у горизонтальне. Після заливання чавуну пускають дуття і конвертор повертають днищем вниз. Шар металу становить від 1/5 до 1/3 висоти циліндричною частини конвертора. Ємність сучасних конверторів, працівників повітряному дуття" сягає 40 т.
У конверторах застосовують кислу основну футерівки. Тепло, необхідне нагріву рідкої стали до високих температур, у тих процесах виходить з допомогою хімічних реакцій окислення домішок чугуна.
У цьому домішки можуть окисляться елементарним киснем і киснем закису заліза, яка розчиняється в металі. При окислюванні домішок киснем виділяється значну кількість тепла.
При окислюванні елементів найбільше тепла виділяють кремній, фосфор і марганець. Ці елементи використовуються при продувке чавуну як джерело тепла (кремній в кислому, а фосфор переважно конверторе).
Недостатня кількість тепла від реакцій компенсується температурою рідкого чугуна.
Для отримання сталі методом продувки застосовують два сорти чавунів: марки Б1 і Б2 — для кислого і Т1 —для основного процессов.
Чугун марки Б1 і Б2 містить мінімум фосфору (0,07%) і сірки (0,06%), чавун марки Т1 містить фосфору 1,6—2,0%, інколи ж до.
2,5%.
Останнім часом для продувки чавуну замість повітря застосовують технічний кисень, що дозволяє підвищити швидкість плавки, вихід придатної стали рахунок збільшення добавки твердої шихти і зменшення хімічних домішок в чавуні, які піддаються окислению.
Конвертор, працюючий на кисневому дуття, за конструкцією відрізняється від тим, що є суцільне днище і кисні нього під час процесу плавки подається згори, оскільки подача кисню через донні фурмы призводить до швидкого їх разрушению.
12. Технології виплавки сталі у Електричної печи.
Основний процес плавки стали Плавку стали основним процесом ведуть із повний та частковим окисленням і окислення примесей.
Плавку які з окисленням домішок проводять у тому випадку, коли потрібно переробити шихтові матеріали з підвищеним змістом фосфору і сірки й одержати сталь з мінімальним кількістю цих елементів. Після розплавлювання шихти в піч додають руду. Окисли заліза руди окисляют що у металі домішки Si, Mn,.P і З, в результа ті чого утворюється залозистий шлак із вмістом (FeO)sP206, сприяє видалення фосфору з металу. Для освіти тривкішого сполуки ангідриду фосфору в шлак додають свежеобожженную вапно щоб одержати фосфорно-кальциевой солі у складі шлаку по реакции:
(FeO)3 • Р20б + 4СаО -* (СаО)4. Р2О5 + 3FeO + О.
Ця реакція протікає успішно, оскільки метал не нагріте до вы-I сокой температури. У цей час зазвичай спостерігається кипіння ванни f з допомогою часткового окислення вуглецю і безперервної освіти газу. Отриманий шлак з наявністю фосфору сливают.
При виплавці высокоуглеродистой сталі та у випадках, коли зміст вуглецю в окисний період зменшується в металі нижче заданих меж, після видалення шлаку ванну науглероживают. Для науглероживания металу у піч завантажують електродний бій, кокс, а інших випадках чушковый чавун малим змістом шкідливих домішок — фосфору і сірки. У цьому загрузочное вікно щільно закривають щоб уникнути надходження кисню повітря з атмосфери у просторі печі. Після закінчення науглероживания наводять новий шлак. Для освіти шлаку в піч завантажують флюсующую суміш у кількості до запланованих 4% ваги металу, що складається з 80% свежеобожженной винищити і 20% плавикового шпата.
У знову нинішньому шлаку зазвичай, у початковий період зміст окислів як закису заліза FeO і закису марганцю МпО становить 5 — 8%. Для зменшення утримання цих окислів в шлак додають раскисл ительную суміш, що складається з винищити, меленого феросиліцію і коксу. Під впливом раскислительной суміші в шлаку зменшується зміст FeO до 1,0% і Мп до 0,4%. Шлак такого складу активним десульфуратором металу. Обробка металу раскисл ительным шлаком також забезпечує розкислення металу. Такий метал доводять до заданого складу, до нього вводять необхідні добавки, а потреби і легирующие елементи. V Остаточне розкислення стали виробляють алюмінієм. Такий процес називається плавкою під білим шлаком.
13. Суть агломерації права (призначення агломерації, сировину, процес агломерації, оборудование).
Залізна руда на 60−90% є минералом, інше — порожня порода. Рудний матеріал складається з оксидів і карбонатів магния.
Перед завантаженням шихти в Д.П. в рудних матеріалах підвищують зміст Fe, тобто. залізну руду піддають обробці: дробленню, збагаченню, усреднению, використання дрібних фракцій, агломерації (термічної обробці при t0 1200−1900). При агломерації видаляється 90% P. S і Fe2O3 перетворюється на Fe3O4.
Агломерационная шихта включає: рудну частина (5−6 мм), паливо (кокс) — 3 мм, флюс (добавка вапняку — 3 мм), вугілля (3−6%).
Процес агломерації відбувається у агломераційних машинах, у яких основний вузол — агломерац. горн.
Список використаної литературы.
1. Баринов Н. А. Технологія металів. Металлургиздат.1963 2. Сидоров І.А. Основи технології найважливіших галузей промышленности,.
Москва, «вища школа», 1971 3. Ковано В. М. (та інших.) Основи технології машинобудування «Машиностроение»,.
1965 4. Никіфоров В.М. (та інших.) Технологія найважливіших галузей промисловості, ч.1, вид. ВПШ при цк кпрс, 1959 5. Данилевський В. В. Технологія машиностроения.
«Вищу школу», 1965.
Якщо Вам знадобився мій реферат, повідомте мені звідси, буду Вам дуже признателен!
My Е-mail: [email protected].
———————————- [pic].