Накопители на гнучких магнітних дисках: що це таке вже й спосіб производства
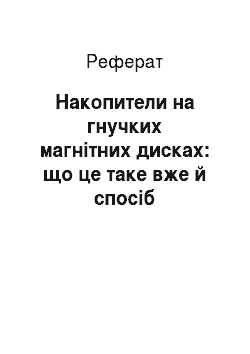
Іноді після всіх перелічених вище операцій із складанні і перевірці дисків деякі фірми як додаткової послуги також форматируют нагромаджувачі на гнучких магнітних дисках, тобто розбивають їх у доріжки й інформаційного секторів, щоб звільнити з цієї процедури користувача, проте останнє необов’язково, оскільки вимоги до форматування в різних користувачів часто відрізняються, тому солідні компанії… Читати ще >
Накопители на гнучких магнітних дисках: що це таке вже й спосіб производства (реферат, курсова, диплом, контрольна)
Технология виробництва накопичувачів на гнучких магнітних дисках.
Запис і зчитування інформації здійснюються з допомогою магнітних головок плаваючого типу. Вони кріпляться на важелі, які переміщаються по радіусу дисків з допомогою спеціального стежить привода.
Як матеріалу виготовлення магнітних дисків зазвичай застосовують алюмінієвий сплав Д16МП (МП — магнітна пам’ять). Цей сплав немагнитный, м’який, досить міцний, добре обробляється. Для зменшення кількості металургійних дефектів лежить на поверхні диска сплав піддають спеціальної очищенні. наприклад электрофлюсовому рафинированию з продувкой інертним газом.
Торцевые поверхні магнітних дисків покривають магнітним шаром. Гальваническое магнітне покриття має товщину до 1 мкм, а ферролаковое — до 5 мкм. Тільки торцевые поверхні крайніх дисків не йдуть на зберігання інформації. На робочої поверхні диска розміщуються 80 доріжок, 20 секторов.
Записи і зчитування інформації здійснюються з допомогою магнітних головок плаваючого типу. Вони кріпляться на важелі, які переміщаються по радіусу диска з допомогою спеціального стежить привода.
Щільність записи визначається величиною зазору між диском і магнітної голівкою, як від стабільності зазору залежить якість записи (зчитування). На підвищення щільності записи необхідно зменшити зазор, але значно підвищуються вимоги до робочої поверхні дисків. При малому зазорі і великих огріхах в макрогеометрии поверхні мають місце значні коливання амплітуди сигналу відтворення. Для надійної роботи нагромаджувача на гнучких магнітних дисках необхідно забезпечити шорсткість поверхні трохи більше Ra=0,22 мкм і мінімальні макрогеометрические відхилення. Торцевое биття диска при обертанні з чистотою 30 об/с на повинен перевищувати 0,3 мм, а питома неплоскостность 0,7 мкм на довжині 10 мм.
Виконання цих вимог представляє значні трудности.
Основними етапами технологічного процесу виготовлення магнітного диска є отримання заготівлі, підготовка поверхні, терморихтование, токарная обробка, нанесення магнітного покриття, зрівноважування, контроль.
Заготівлю дисків отримують з листового матеріалу. Різання аркушів на картки розміром 100×100 мм здійснюють на ножицях з похилими ножами і притиском матеріалу. З карток вирубкою на штампі чи токарському верстаті отримують диски.
При вирубування зона металу, прилегла поверхні зрізу, упрочняется. Товщина деформованого шару становить приблизно 0,3 товщини матеріалу. Додача наступну токарную обробку повинна перевищувати товщину деформованого слоя.
Розміри заготівлі для магнітного диска мають такі значення: зовнішнє діаметр становить 85,5 мм, а внутрішній — 24 мм.
Підготовка поверхні залежить від знежирюванні, промиванні в гарячої проточній воді (при t=60(З протягом 1 — 2 хв.) і сушінню. Вона складає спеціальних установках.
Диск, що у камері верстата отримує обертання зазнає дії обезжиривающего розчину, і навіть протирається обертовими щітками. Розчин подається з бачка насосом і розпорошується форсунками. Чиста вода для промивання постачається з крана. Обезжиривающий розчин з камери потрапляє через клапан знову на бачок для вторинного використання чи зливається. Диски сушать гарячим повітрям, циркуляція що його камері здійснюється вентилятором.
Терморихтование заготовок необхідне зняття внутрішніх напруг і забезпечення вимог щодо неплоскостности і осьового биттю. Цю операцію найдоцільніше виконувати в електричних печах опору, що забезпечують мінімальні перепади температур з усього робочому обсягу. Оптимальна температура рихтования для сплаву Д16МП становить 125— 215 З, а витримка нині температурі 3 год. Швидкість підйому температури становить 40(З за годину, а швидкість охолодження трохи більше — 20(З в час.
У пристосуванні закріплення дисків при терморихтовании заготівлі дисків поміщають між алюмінієвими плитами. У кожному шарі перебувають розслідування щодо 10 заготовок. Становище заготівлі на плиті визначається трьома штифтами, які фіксують заготівлю з діаметру. Вони є також і фіксації вкладення наступній плити. Підстава і вантажна плита виконані з чавуну. Вантажна плита забезпечує необхідну тиск, яке верхньої заготівлі становить 0,02— 0,04 Мпа. Стойка має вушко, з допомогою якого пристосування завантажують у електричну шахтну піч. Температура робочого простору й пристосування контролюється термопарами, встановленими іззовні і всередині приспособления.
Контроль торцевих поверхонь дисків після терморихтования здійснюють обабіч безконтактним (емкостным) методом. Заготівлі дисків встановлюють на площину маточини і закріплюють через кільце притиском з допомогою гайки.
Осьове биття вимірюють при рівномірному обертанні із частотою 0,2 об/c при фіксованому становищі датчика одній із концентричних окружностей. Непараллельность переміщення датчика по площині має перевищувати 0,001.
Токарную обробку дисків проводять на верстатах підвищеної точності в вакуумному патроне.
Основними частинами патрона є планшайба і корпус зі змінним кільцем. Через отвори його порожнину з'єднана з канавками, які перебувають на торцевій поверхні планшайбы. Різниця атмосферного тиску повітря і тиску всередині планшайбы притискає заготівлю диска до виступам, утримуючи диск на планшайбе з допомогою сил тертя. Для знімання диска порожнину планшайбы з'єднують із навколишньою атмосферою. Величина розрядження становить 0,05 — 0,07 Па. Поворот зовнішнього й внутрішнього діаметрів, і навіть фасок здійснюється за частоті обертання шпинделі від 700 до 900 про/ мін та подачі до 0,1 мм/об.
Підготовка поверхні диска перед нанесенням покриття залежить від очищенні її миючим розчином за нормальної температури 55 — 65(З. Як подслоя застосовують мідь, яку завдають гальванічним способом.
Магнітне покриття, завдана по мідному підшару, забезпечує малий струм записи, високу амплітуду зчитуваного сигналу та практично бездефектне покриття. Товщина мідного подслоя становить приблизно 5 мкм. Чистота поверхні після нанесення мідного подслоя погіршується, і її відновленні застосовується полірування, у якому товщина подслоя зменшується на 0,5 мкм.
Подслой і магнітне покриття завдають електролітичним способом в пристосуванні, що забезпечує підвід струму і обертання диска в гальванічної ванній. Обертання диска забезпечує рівномірність осадження покрытия.
Пристосування складається з текстолитовой плити, де встановлено двигун, і знижуючі редуктори. На валу редуктора насаджена дерево з диском. Струм до диска подається від дроту й чопи до оправі. Диск занурююється у ванну наполовину діаметра. Для отримання рівномірного магнітного поля встановлюють латунний екран. Занурення диска в ванну, підвищення і перенесення його з однієї ванни до іншої здійснюється з допомогою тяг.
Статична зрівноважування дисків виробляється після покриття міддю. Диск, щільно надягнутий на оправлення встановлюють на раму-весы, яка призмами спирається на стійку. Терези врівноважуються з допомогою вантажів. Раму стопорят на стійці штифом, який після установки диска виймають. При наявності неврівноваженості рама збочує з горизонтального становища, що фіксується стрілкою на шкалою. У цьому всі перелічені вище операції виконуються автоматически.
Остаточне полірування складає верстаті з вертикальним шпинделем. Опрацьований диск закріплюють у вакуумній планшайбе. У цьому він притискається до точної поверхні планшайбы. Як інструмент застосовують полировальник, шарнирное кріплення якого забезпечує його самоустановку щодо поверхні диска.
Для запобігання магнітного носія від механічних і кліматичних впливів на торцевые поверхні дисків можуть наносити захисне покриття. Раніше цією роллю виконував хром, зараз використовується тифлон. Останній дозволяє: зробити диск абсолютно не чутливим до будь-якого роду загрязнениям: жир, вода, пыль.
Довільно обрані диски піддають випробувань на сохраняемость записаній інформації при тривалої роботі у режимі зчитування. Контрольні виміру параметрів відтворювальних сигналів здійснюють з допомогою осциллографа.
Кліматичні випробування проводять за підвищеної (+50(З) і зниженою (— 50(З) температурах, а механічні при вібраційних і ударних нагрузках.
Після кожного випробування диски піддають візуальному огляду з перевіркою параметрів считываемой информации.
Взаємозамінність вибраних НГМД перевіряють на кількох нагромаджувачах, куди послідовно встановлюють і той ж диск. У цьому інформація, записана на дискетах, повинна без збоїв відтворюється усім накопителях.
Іноді після всіх перелічених вище операцій із складанні і перевірці дисків деякі фірми як додаткової послуги також форматируют нагромаджувачі на гнучких магнітних дисках, тобто розбивають їх у доріжки й інформаційного секторів, щоб звільнити з цієї процедури користувача, проте останнє необов’язково, оскільки вимоги до форматування в різних користувачів часто відрізняються, тому солідні компанії воліють надавати вибір способу форматування покупцю, а чи не проводять його заранее.