Проектування та розрахунок редуктора для стрічкового транспортера
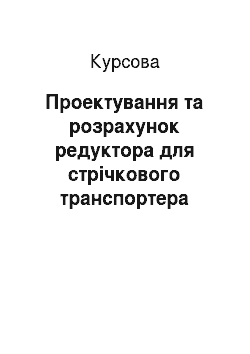
Змазування зубчастого зачеплення виробляється зануренням зубчастого колеса на проміжному валу в масло, що заливається усередину корпуса до рівня, що забезпечує занурення тихохідного колеса приблизно на 10 мм. Обсяг масляної ванни визначаємо з розрахунку 0.25 дм3 масла на 1кВт переданій потужності: V=0.25*11=2.75 дм3. По таблиці 10.8 установлюємо в’язкість масла. Для швидкохідного щабля при… Читати ще >
Проектування та розрахунок редуктора для стрічкового транспортера (реферат, курсова, диплом, контрольна)
Курсова робота:
Проектування та розрахунок редуктора для стрічкового транспортера
Зміст
Завдання на проект Введення Вибір електродвигуна й кінематичний розрахунок.
1.1 Коефіцієнт корисної дії привода
1.2 Вибір електродвигуна
1.3 Крутний моменти
2. Розрахунок зубчастих коліс
2.1 Вибір матеріалу
2.2 Розрахунок швидкохідного щабля двоступінчастого зубчастого редуктора.
2.2.1 Міжосьова відстань визначаємо по формулі
2.2.5 Діаметри ділильні
2.2.6 Діаметри вершин зубів
2.2.7 Ширина зуба
2.2.8 Коефіцієнт ширини шестірні по діаметру
2.2.9 Окружна швидкість коліс
2.2.10 Коефіцієнт навантаження
2.2.11 Перевіряємо контактні напруги по формулі
Сили, що діють у зачепленні
2.2.5 Перевірка зубів на витривалість по напругах вигину
2.3 Розрахунок тихохідного щабля двоступінчастого зубчастого редуктора.
2.3.1 Міжосьова відстань визначаємо по формулі
2.31 Нормальний модуль
2.3.2 Число зубів шестірні
2.3.2 Число зубів шестірні
2.3.4Число зубів колеса
2.3.5 Уточнюємо значення кута нахилу зубів
2.3.6 Діаметри ділильні
2.3.7 Діаметри вершин
.3.8 Ширина зуба
2.3.9 Коефіцієнт ширини шестірні по діаметрі
2.3.10 Окружна швидкість коліс
2.3.11 Коефіцієнт навантаження
2.3.12 Перевіряємо контактні напруги по формулі
2.3.13 Сили, що діють у зачепленні
2.3.14 Перевірка зубів на витривалість по напругах вигину
3. Попередній розрахунок валів редуктора
3.1 Провідний вал
3.2 Проміжний вал
3.3 Вихідний вал
4. Конструктивні розміри шестірні й колеса
5. Конструктивні розміри корпуса й кришки
6. Перевірка довговічності підшипників
6.1 Провідний вал
6.2 Проміжний вал
6.3 Ведений вал
7. Перевірка міцності шпонкових з'єднань
7.1 Провідний вал
7.2 Проміжний вал
7.3 Ведений вал
8. Уточнений розрахунок валів
8.1 Провідний вал8.2 Проміжний вал
8.3 Ведений вал
9. Вибір сорту масла
10. Посадки деталей редуктора
Cписок літератури
Завдання на проект
Спроектувати привод стрічкового транспортера
Варіант № 38.
Вихідні дані:
Термін служби: 7 років Потужність на вихідному валу Р3= 8 кВт Кутова швидкість на вихідному валу w3= 3.2? рад/с = 10 рад/с Рис. 1. — Вихідні дані
Введення
Ціль курсового проектування — систематизувати, закріпити, розширити теоретичні знання, а також розвити розрахунково-графічні навички студентів. Основні вимоги, пропоновані до створюваної машини: висока продуктивність, надійність, технологічність, мінімальні габарити й маса, зручність в експлуатації й економічність. У проектованому редукторі використовуються зубчасті передачі.
Нам у нашій роботі необхідно спроектувати редуктор для стрічкового транспортера, а також підібрати муфти, двигун. Редуктор складається з литого чавунного корпуса, у якому поміщені елементи передачі - 2 шестірні, 2 колеса, підшипники, вали та ін. Вхідний вал за допомогою муфти з'єднується із двигуном, вихідний також за допомогою муфти із транспортером.
1. Вибір електродвигуна й кінематичний розрахунок
Кінематичний аналіз схеми привода Привод складається з електродвигуна, двоступінчастого редуктора. При передачі потужності мають місце її втрати на подолання сил шкідливого опору. Такі опори мають місце й у нашім приводі: у зубчастій передачі, в опорах валів, у муфтах і в ременях з роликами. Через цього потужність на приводному валу буде менше потужності, що розвивається двигуном, на величину втрат.
1.1 Коефіцієнт корисної дії привода
По таблиці 1.1 коефіцієнт корисної дії пари циліндричних коліс ?з.к. = 0,98; коефіцієнт, що враховує втрати пари підшипників кочення, ?п = 0,99; коефіцієнт, що враховує втрати в муфті ?м = 0,98; коефіцієнт, що враховує втрати в ремені з роликами ?р = 0,9
0,98*0,99*0,98 = 0,95
0,95*0,98*0,99 = 0,92
0,92*0,99 = 0,91
Загальний КПД привода:
= 0,982 * 0,995 * 0,982*0,9 = 0,8
1.2 Вибір електродвигуна
Необхідна потужність електродвигуна:
Ртр=Р3/ =8/0,8=10 кВт,
Частота обертання барабана:
При виборі електродвигуна враховуємо можливість пуску транспортера з повним завантаженням.
Пускова необхідна потужність:
Рп=Ртр*1,3м=10*1,3=13 кВт
кВт
За ДСТ 19 523−81 по необхідній потужності
Ртр = 10 кВт вибираємо електродвигун трифазний асинхронний
короткозамкнений серії 4АН закритий, що обдувається із синхронною частотою
n = 1500 о/хв 4АН132М4 з параметрами Рдв = 11 кВт і ковзанням
S=2,8%, відношення Рп/Рн=2. Рпуск=2*11=22 кВт — потужність даного двигуна на пуску. Вона більше чим нам потрібно Рп= 13 кВт.
Номінальна частота обертання двигуна:
де: nдв — фактична частота обертання двигуна, хв-1;
n — частота обертання, хв-1;
s — ковзання, %;
Передатне відношення редуктора:
U=nдв/n3=1458/95,5=15,27
Передатне відношення першого щабля приймемо u1=5; відповідно до другому щаблю u2=u/u1=15,27/5=3,05
1.3 Крутний моменти
Момент на вхідному валу:
де: Ртр — необхідна потужність двигуна, кВт;
— кутова швидкість обертання двигуна, о/хв;
де: nдв — частота обертання двигуна, хв-1;
Момент на проміжному валу:
Т2 = Т1 * u1 * ?2
де: u1 — передатне відношення першого щабля;
?2 — КПД другі вали;
Т2 = 65,5*103 * 5*0,92 =301,3*103 Нмм
Кутова швидкість проміжного вала:
Момент на вихідному валу:
Т3 = Т2 * u2 * ?3
де: u2 — передатне відношення другого щабля;
?3 — КПД треті вали;
Т3 = 301,3*103 * 3,05 * 0,91 = 836,3*103 Нмм
Кутова швидкість вихідного вала:
Всі дані зводимо в таблицю 1:
Таблиця 1 — Вихідні дані
Швидкохідний вал | Проміжний вал | Тихохідний вал | ||
Частота обертання, о/хв | n1= 1458 | n2=291,3 | n3=95,5 | |
Кутова швидкість, рад/с | w1= 152,7 | w2 =30,5 | w3= 10 | |
Крутний момент, 103 Нмм | T1= 65,5 | T2= 301,3 | T3= 836,3 | |
2. Розрахунок зубчастих коліс
2.1 Вибір матеріалу
Вибираємо матеріал із середніми механічними характеристиками: для шестірні сталь 45, термічна обробка — поліпшення, твердість НВ 230; для колеса — сталь 45, термічна обробка — поліпшення, але на 30 одиниць нижче НВ 200.
Контактні напруги, що допускаються, по формулі (3.9 [1])
МПа де: ?Н lim b — межа контактної витривалості, МПа;
МПа для колеса: = 2*200 + 70 = 470 МПа для шестірні: = 2*230 + 70 = 530 Мпа КН — коефіцієнт довговічності
де: NHO — базове число циклів напруг;
NНЕ — число циклів зміни напруг;
Тому що, число навантаження кожного зуба колеса більше базового, то приймають КHL = 1.
[SH] - коефіцієнт безпеки, для коліс нормалізованої й поліпшеної сталі приймають [SH] = 1,1 1,2.
Для шестірні:
Для колеса:
Тоді розрахункова контактна напруга визначаємо по формулі (3.10 [1])
= 0.45(481+428)=410 МПа.
2.2 Розрахунок швидкохідного щабля двоступінчастого зубчастого редуктора.
2.2.1 Міжосьова відстань визначаємо по формулі
мм де: Ка — для косозубних коліс Ка = 43;
u1 — передатне відношення першого щабля;
Т2 — крутний момент другого вала, Нмм;
КН? — коефіцієнт, що враховує не рівномірність розподілу навантаження по ширині вінця.
При проектуванні зубчастих закритих передач редукторного типу приймають значення КН? по таблиці 3.1. КН?=1,25
[?H] - напруга, що допускається гранично;
?ba — коефіцієнт відносини зубчастого вінця до міжосьової відстані, для косозубної передачі ?ba = 0,25 0,40.
мм
Найближче значення міжосьової відстані за ДСТ 2185−66 аw = 160 мм (див. с. 36 [1]).
2.2.2 Нормальний модуль
mn = (0,01 0,02)*аw
де: аw — міжосьова відстань, мм;
mn = (0,01 0,02)*аw = (0,01 0,02)*160 = 1,6 3,2 мм Приймаємо за ДСТ 9563−60 mn = 3.
Попередньо приймемо кут нахилу зубів ?=10°.
2.2.3 Число зубів шестірні (формула 3.12 [1] )
де: аw — міжосьова відстань, мм;
? — кут нахилу зуба, °;
u1 — передатне відношення першого щабля;
mn — нормальний модуль, мм;
2.2.4 Число зубів колеса
z2 = z1 * u1 = 17*5=85
Уточнюємо значення кута нахилу зубів
де: z1 — число зубів шестірні;
z2 — число зубів колеса;
mn — нормальний модуль, мм;
аw — міжосьова відстань, мм;
? = 17°
2.2.5 Діаметри ділильні
Для шестірні:
Для колеса:
Перевірка:
2.2.6 Діаметри вершин зубів
Для шестірні: da1 =d1+2mn =53,3 + 2*3 = 59,3 мм Для колеса: da2 =d2+2mn = 266,7 + 2*3 = 272,7 мм
2.2.7 Ширина зуба
Для колеса: b2 = ?ba * aw = 0,4 * 160 = 64 мм Для шестірні: b1 = b2 + 5 = 64 + 5 = 69 мм
2.2.8 Коефіцієнт ширини шестірні по діаметру
де: b1 — ширина зуба для шестірні, мм;
d1 — ділильний діаметр шестірні, мм;
2.2.9 Окружна швидкість коліс
м/з
Ступінь точності передачі: для косозубних коліс при швидкості до 10 м/с варто прийняти 8-ю ступінь точності.
2.2.10 Коефіцієнт навантаження
По таблиці 3.5 при ?bd = 1,29, твердості НВ< 350 і несиметричному рас-положенні коліс коефіцієнт КН? = 1,17.
По таблиці 3.4 при? = 4,1 м/с і 8-й ступеня точності коефіцієнт КН?=1,07.
По таблиці 3.6 для косозубних коліс при швидкості менш 5 м/с КН? = 1.
= 1,17 * 1,07 * 1 = 1,252
2.2.11 Перевіряємо контактні напруги по формулі
МПа
де: аw — міжосьова відстань, мм;
Т2 — крутний момент другого вала, Нмм;
КН — коефіцієнт навантаження;
u1 — передатне відношення першого щабля;
b2 — ширина колеса, мм;
Умова міцності виконана.
2.2.12 Сили, що діють у зачепленні
У зачепленні діють три сили:
Окружна
Н
де: Т1 — крутний момент провідного вала, Нмм;
d1 - ділильний діаметр шестірні, мм;
Радіальна
Н
де:? — кут зачеплення, °;
? — кут нахилу зуба, °;
Осьова
Fa = Ft * tg ?, Н
Fa = Ft * tg? = 2457,8 * 0,3057 = 751,4 Н
2.2.13 Перевірка зубів на витривалість по напругах вигину
( см. формулу 3.25 [1] ).
МПа
де: Ft — окружна сила, Н;
Коефіцієнт навантаження КF = KF? * KF?
По таблиці 3.7 при ?bd = 1,34, твердості НВ ‹ 350 і несиметричному рас-положенні зубчастих коліс щодо опор коефіцієнт КF? = 1.36.
По таблиці 3.8 для косозубних коліс 8-й ступеня точності й швидкості 4,1 м/с коефіцієнт КF? = 1,1.
Таким чином, КF = 1,36 * 1,1 = 1,496.
Коефіцієнт, що враховує форму зуба, YF залежить від еквівалентного числа зубів z?
У шестірні
У колеса
Коефіцієнт YF1 = 3,85 і YF2 = 3,6 (див. стор. 42).
Визначаємо коефіцієнти Y? і КF?
де середні значення коефіцієнта торцевого перекриття ?? = 1,5; ступінь точності n = 8.
Допускаються напруги при перевірці на вигин, визначають по формулі 3.24 [1]:
МПа
По таблиці 3.9 для сталі 45 поліпшеної границя витривалості при циклу вигину = 1,8 НВ.
Для шестірні = 1,8 * 230 = 414 МПа
Для колеса = 1,8 * 200 = 360 МПа
Коефіцієнт безпеки
По таблиці 3.9 [SF]' = 1.75 для сталі 45 поліпшеної; [SF]" = 1 для кувань і штампувань.
Напруги, що допускаються:
Для шестірні
Для колеса
Перевірку на вигин варто проводити для того зубчастого колеса, для якого відношення менше. Знайдемо відносини:
Для шестірні
Для колеса
Перевірку на вигин проводимо для колеса:
Умова міцності виконана.
2.3 Розрахунок тихохідного щабля двоступінчастого зубчастого редуктора
2.3.1 Міжосьова відстань визначаємо по формулі
мм де: Ка = 43;
u3 — передатне відношення на виході;
Т3 — крутний момент на виході;
КН?=1.25
?ba = 0,25 0,40.
Найближче значення міжосьової відстані за ДСТ 2185−66 аw = 200 мм (див. с. 36 [1]).
2.3.2 Нормальний модуль
mn = (0,01 0,02)*аw = (0,01 0,02)*200 = 2 4 мм Приймаємо за ДСТ 9563−60 mn = 3 мм Попередньо приймемо кут нахилу зубів ?=10°.
2.3.3 Число зубів шестірні
2.3.4Число зубів колеса
Z4 = z3 * u2 = 32*3,05=97,6
2.3.5 Уточнюємо значення кута нахилу зубів
? = 12,83°=12o50/
2.3.6 Діаметри ділильні
Для шестірні:
Для колеса:
Перевірка:
2.3.7 Діаметри вершин зубів
Для шестірні: da3 =d3+2mn =98,5 + 2*3 = 104,5 мм Для колеса: da4 =d4+2mn = 301,5 + 2*3 = 307.5 мм
2.3.8 Ширина зуба
Для колеса: b4 = ?ba aw = 0,4 * 200 = 80 мм Для шестірні: b3 = b4 + 5 = 80 + 5 = 85 мм
2.3.9 Коефіцієнт ширини шестірні по діаметрі
2.3.10 Окружна швидкість коліс
м/с
Ступінь точності передачі: для косозубних коліс при швидкості до 10 м/с варто прийняти 8-ю ступінь точності.
2.3.11 Коефіцієнт навантаження
По таблиці 3.5 при ?bd = 0,93, твердості НВ< 350 і несиметричному рас-положенні коліс коефіцієнт КН? = 1,1.
По таблиці 3.4 при? = 1,5 м/с і 8-й ступеня точності коефіцієнт КН?=1,06.
По таблиці 3.6 для косозубних коліс при швидкості більше 1,5 м/с коефіцієнт КН? = 1.
= 1,1 * 1,06 * 1 = 1,15
2.3.12 Перевіряємо контактні напруги по формулі
Умова міцності виконана
2.3.13 Сили, що діють у зачепленні
У зачепленні діють три сили:
Окружна
Радіальна
Осьова
Fa = Ft * tg ?=6117,8*0.228=1394,9 Н
2.3.14 Перевірка зубів на витривалість по напругах вигину
Коефіцієнт навантаження КF = KF? * KF? (см. стр. 42 [1])
По таблиці 3.7 при ?bd = 0,863, твердості НВ ‹ 350 і несиметричному розташуванні зубчастих коліс щодо опор коефіцієнт КF? = 1.2.
По таблиці 3.8 для косозубних коліс 8-й ступеня точності й швидкості 1,5м/с коефіцієнт КF? = 1,1.
Таким чином, КF = 1,2 * 1,1 = 1,32.
Коефіцієнт, що враховує форму зуба, YF залежить від еквівалентного числа зубів z?
У шестірні
У колеса
Коефіцієнт YF1 = 3,62 і YF2 = 3,6 (див. стор. 42).
Визначаємо коефіцієнти Y? і КF?
де середні значення коефіцієнта торцевого перекриття ?? = 1,5; ступінь точності n = 8.
Допускаються напругу при перевірці на вигин визначають по формулі 3.24 [1]:
По таблиці 3.9 для сталі 45 поліпшеної границя витривалості при циклі вигину = 1,8 НВ.
Для шестірні = 1,8 * 230 = 414 МПа
Для колеса = 1,8 * 200 = 360 МПа
Коефіцієнт безпеки
По таблиці 3.9 [SF]' = 1.75 для сталі 45 поліпшеної; [SF]" = 1 для кувань і штампувань.
Напруги, що допускаються:
Для шестірні
Для колеса
Перевірку на вигин варто проводити для того зубчастого колеса, для якого відношення менше. Знайдемо відносини:
Для шестірні
Для колеса
Перевірку на вигин проводимо для колеса
Умова міцності виконана
3. Попередній розрахунок валів редуктора
Матеріал той же що й шестірня Сталь 45 поліпшена.
3.1 Провідний вал
Діаметр вихідного кінця, Н/мм2.
мм [1]
де: Т-Крутний момент, Нмм;
— допускається навантаження Н/мм2;
мм Тому що вал редуктора з'єднаний з валом двигуна муфтою, то необхідно погодити діаметри ротора dдв і вала dв1. Муфти УВП можуть з'єднувати вали зі співвідношенням dв1:dдв 0,75, але напівмуфти повинні при цьому мати однакові зовнішні діаметри. У підібраного електродвигуна dдв=32 мм. Вибираємо МУВП за ДСТ 21 425−93 з розточеннями напівмуфт під dдв=32 мм і dв1=25 мм.
Приймемо під підшипник dп1=30 мм.
Шестірню виконаємо за одне ціле з валом.
3.2 Проміжний вал
Матеріал той же що й шестірня Сталь 45 поліпшена.
Діаметр під підшипник допускається Н/мм2.
мм Приймемо діаметр під підшипник dП2=30 мм.
Діаметр під зубчастим колесом dзк=35 мм.
Шестірню виконаємо за одне з валом.
3.3 Вихідний вал
Матеріал той же що й шестірня Сталь 45 поліпшена.
Діаметр вихідного кінця Н/мм2.
мм Вибираємо муфту МУВП за ДСТ 21 424−75 з розточенням напівмуфт під dв3=46мм.
Діаметр під підшипник приймемо dП3=50 мм.
Діаметр під колесо dзк=55 мм.
4. Конструктивні розміри шестірні й колеса
Розміри коліс визначаються з наступних формул:
Діаметр западин зубів: df=d1-2.5mn, мм Діаметр маточини:, мм довжина маточини:, мм товщина обода:, мм., але не менш 8 мм.
товщина диска:, мм діаметр отворів:, мм Do=df-2 мм фаска: n=0.5mn x 45o
Всі розрахунки зводимо в таблицю 2:
Таблиця 2 — Розрахунки
z | mn | b, мм | d, мм | da, мм | df, мм | dст, мм | Lст, мм | мм | З, мм | |||
1) щабель | шестірня | 53,3 | 59,34 | 45,8 | ; | ; | ; | ; | ||||
колесо | 266,7 | 272,7 | 259,2 | 67,5 | ||||||||
2) щабель | шестірня | 98,5 | 104,5 | ; | ; | ; | ; | |||||
колесо | 301,5 | 307,5 | 97,5 | |||||||||
5. Конструктивні розміри корпуса й кришки
Розрахунок проведемо по формулах (табл. 10.2, 10.3[1]):
Товщина стінки корпуса: мм.
Товщина стінки кришки редуктора: мм.
Товщина верхнього пояса (фланця) корпуса: мм.
Товщина нижнього пояса (фланця) кришки корпуса: мм.
Товщина нижнього пояса корпуса: мм., приймемо р=23 мм.
Товщина ребер підстави корпуса: мм., приймемо m=9 мм.
Товщина ребер кришки корпуса: мм., приймемо m=8 мм.
Діаметри болтів:
— фундаментальних: мм., приймаємо болти з різьбленням М20;
— які кріплять кришку до корпуса в підшипників: мм., приймаємо болти з різьбленням М16;
— які кріплять кришку з корпусом: мм., приймаємо болти з різьбленням М12;
Гніздо під підшипник:
— Діаметр отвору в гнізді приймаємо рівним зовнішньому діаметру підшипника: Dп1=30 мм, Dп2=60 мм.
— Діаметр гнізда: Dk=D2+(2−5) мм., D2 — Діаметр фланця кришки підшипника, на 1 і 2 валах D2= 77 мм, на 3 валу D2= 105 мм. Тоді Dk1=D2+(2−5)= 80 мм, Dk2=D2+(2−5)= 110 мм.
Розміри радіальних шарикопідшипників однорядних середньої серії наведені в таблиці 3:
Таблиця 3 — Розміри радіальних шарикопідшипників однорядних середньої серії
Умовна позначка підшипника | d | D | B | Вантажопідйомність, кН | ||
Розміри, мм | С | З | ||||
N306 | 28,1 | 14,6 | ||||
N310 | 65,8 | |||||
Розміри штифта:
— Діаметр мм.
— Довжина мм.
З табл. 10.5[1] приймаємо штифт конічний ДЕРЖСТАНДАРТ 3129−70
мм, мм.
Зазор між торцем шестірні з однієї сторони й маточини з інший, і внутрішньою стінкою корпуса А1=1,2 =1,2*10=12 мм.
Зазор від окружності вершин зубів колеса до внутрішньої стінки корпуса, а також відстань між зовнішнім кільцем підшипника провідного вала й внутрішньою стінкою корпуса А= =10 мм.
Для запобігання витікання змащення підшипників усередину корпуса й вимивання пластичного матеріалу, що змазує, рідким маслом із зони зачеплення встановлюємо кільця, їхню ширину визначає розмір y=8−12 мм. Ми приймаємо y=10 мм.
6. Перевірка довговічності підшипників
6.1 Провідний вал
Реакції опор:
у площині XZ:
Перевірка:
— 388,2−2457,8+2108,7+737,3=0
у площині YZ:
Перевірка:
— 542,5+935,4−392,9=0
Сумарні реакції:
Підбираємо підшипник по більш навантаженій опорі № 2
Умовна позначка підшипника | d | D | B | Вантажопідйомність, кН | ||
Розміри, мм | С | З | ||||
N306 | 28,1 | 14,6 | ||||
Відношення
Цій величині по таблиці 9.18[1] відповідає e=0,21
Відношення X=0.56, Y=2.05
Еквівалентне навантаження по формулі:
H
де V= 1-обертається внутрішнє кільце підшипника;
коефіцієнт безпеки по таблиці 9.19[1] КБ=1;
температурний коефіцієнт по таблиці 9.20[1] КТ=1,0.
H
Розрахункова довговічність, млн. про по формулі:
Розрахункова довговічність, год по формулі :
год Фактичний час роботи редуктора Термін служби 7 років, при двозмінній роботі:
365днів*16ч.КгодКсут=365*16*0,7*0,3=1226,4 год.
6.2 Проміжний вал
Реакції опор:
у площині XZ:
Перевірка:
3176−6117,8+484+2457,8=0
у площині YZ:
Перевірка:
1,6+2283,8−935,4−1350=0
Сумарні реакції:
Підбираємо підшипник по більш навантаженій опорі № 1
Умовна позначка підшипника | d | D | B | Вантажопідйомність, кН | ||
Розміри, мм | С | З | ||||
N306 | 28,1 | 14,6 | ||||
Відношення
Цій величині по таблиці 9.18[1] відповідає e=0,21
Відношення X=1, Y=0
Еквівалентне навантаження по формулі:
H
Розрахункова довговічність, млн. про по формулі:
Розрахункова довговічність, год. по формулі:
год.
6.3 Ведений вал
Реакції опор:
у площині XZ:
Перевірка:
— 5325,8+6117,8+1043,3−1835,3=0
у площині YZ:
Перевірка:
— 254,6−2283,8+2538,4=0
Сумарні реакції:
Підбираємо підшипник по більше навантаженій опорі № 1
Умовна позначка підшипника | d | D | B | Вантажопідйомність, кН | ||
Розміри, мм | С | З | ||||
N310 | 65,8 | |||||
Відношення
Цій величині по таблиці 9.18[1] відповідає e=0,195
Відношення X=0.56, Y=2.2
Еквівалентне навантаження по формулі:
H
Розрахункова довговічність, млн. про по формулі:
Розрахункова довговічність, год по формулі:
год
7. Перевірка міцності шпонкових з'єднань
Застосовуються шпонки призматичні з округленими торцями по
ДЕРЖСТАНДАРТ 23 360−78. Матеріал шпонок — сталь 45 нормалізована.
Таблиця 1 — Шпонкові з'єднання
Діаметр вала d, мм | Ширина шпонки b, мм | Висота шпонки h, мм | Довжина шпонки l, мм | Глибина паза t1, мм | |
Напруги зминання й умова міцності по формулі:
Напруги зминання, що допускаються, при сталевій маточині =100…120 Мпа
7.1 Провідний вал
При d=25 мм;; t1=4 мм; довжині шпонки l=30 мм; крутний момент Т1=65,5 Нм
7.2 Проміжний вал
При d=35 мм;; t1=5 мм; довжині шпонки l=32 мм; крутний момент Т2=301,3 Нм
7.3 Ведений вал
При d=55 мм;; t1=6 мм; довжині шпонки l=55 мм; крутний момент Т3=314 Нм
При d=46 мм;; t1=5 мм; довжині шпонки l=65 мм
8. Уточнений розрахунок валів
8.1 Провідний вал
Уточнений розрахунок складається у визначенні коефіцієнтів запасу міцності s для небезпечних перерізів і порівнянні їх з значеннями, що допускаються s. Міцність дотримана при .
Матеріал вала — сталь 45 поліпшена. По таблиці 3.3[1]
Границі витривалості:
Рис. 1 — Перетин А-А
Концентрація напруг обумовлена наявністю шпонкового паза
Коефіцієнт запасу міцності по нормальних напругах вигину
Коефіцієнт запасу міцності по дотичних напруженнях
По таблиці 8.5[1] приймаємо ;
По таблиці 8.8[1] приймаємо ;
Момент опору крутінню по таблиці 8.5[1]:
при d=25 мм; b=8 мм; t1=4 мм
Момент опору вигину:
При d=25 мм; b=8 мм; t1=6 мм
Згинальний момент у перетині А-А
My=0;
MА-А=МX
Амплітуда й середнє значення циклу:
Амплітуда нормальних напруг:
Перемінна постійних напруг:
Тоді
Результуючий коефіцієнт запасу міцності по формулі (8.17 [ 1 ])
Умова міцності виконана.
Перетин В-В
приймаємо
. Момент опору крутінню при d=40.3 мм:
Момент опору вигину:
Згинальний момент у перетині B-B
Амплітуда й середнє значення циклу:
Амплітуда нормальних напруг:
величина дуже маленька тому неї враховувати не будемо Тоді
Результуючий коефіцієнт запасу міцності по формулі (8.17 [ 1 ])
Умова міцності виконана.
8.2 Проміжний вал
Матеріал вала — сталь 45 поліпшена. По таблиці 3.3[1]
Границі витривалості:
Рис. 2 — Перетин А-А
Концентрація напруг обумовлена посадкою підшипника з гарантованим натягом
приймаємо
Момент опору крутінню при d=30 мм:
Момент опору вигину:
Згинальний момент у перетині А-А
Амплітуда й середнє значення циклу:
Амплітуда нормальних напруг:
величина дуже маленька тому її враховувати не будемо
Тоді
Результуючий коефіцієнт запасу міцності по формулі (8.17 [ 1 ])
Умова міцності виконана.
Перетин В-В.
Концентрація напруг обумовлена наявністю шпонкового паза
приймаємо
Момент опору крутінню при d=35 мм; b=10 мм; t1=5 мм
Момент опору вигину:
Згинальний момент у перетині B-B
ё
Амплітуда й середнє значення циклу:
Амплітуда нормальних напруг:
величина дуже маленька тому неї враховувати не будемо Тоді
Результуючий коефіцієнт запасу міцності по формулі
Умова міцності виконана.
8.3 Ведений вал
Матеріал вала — сталь 45 поліпшена. По таблиці 3.3[1]
Границі витривалості:
Рис. 3 — Перетин А-А
Концентрація напруг обумовлена наявністю шпонкового паза
приймаємо
Момент опору крутіння при d=55 мм; b=16 мм; t1=6 мм
Момент опору вигину:
Згинальний момент у перетині А-А
Амплітуда й середнє значення циклу:
Амплітуда нормальних напруг:
величина дуже маленька тому її враховувати не будемо
Тоді
Результуючий коефіцієнт запасу міцності по формулі (8.17 [ 1 ])
Умова міцності виконана.
Перетин В-В
Концентрація напруг обумовлена наявністю шпонкового паза
приймаємо
Момент опору крутінню при d=42 мм; b=12 мм; t1=5 мм
Момент опору вигину:
Згинальний момент у перетині B-B
Амплітуда й середнє значення циклу:
Амплітуда нормальних напруг:
величина дуже маленька тому її враховувати не будемо Тоді
Результуючий коефіцієнт запасу міцності по формулі (8.17 [ 1 ])
Умова міцності виконана.
9. Вибір сорту масла
Змазування зубчастого зачеплення виробляється зануренням зубчастого колеса на проміжному валу в масло, що заливається усередину корпуса до рівня, що забезпечує занурення тихохідного колеса приблизно на 10 мм. Обсяг масляної ванни визначаємо з розрахунку 0.25 дм3 масла на 1кВт переданій потужності: V=0.25*11=2.75 дм3. По таблиці 10.8[1] установлюємо в’язкість масла. Для швидкохідного щабля при контактних напругах 401,7 МПа й швидкості v=2,8 м/с рекомендується в’язкість, що, масла повинна бути приблизно дорівнює 28*10-6 м2/с. Для тихохідного щабля при контактних напругах 400,7 МПа й швидкості v=1,05м/с рекомендується в’язкість, що, масла повинна бути приблизно дорівнює 34*10-6 м2/с.
Середня в’язкість масла
По таблиці 10.10[1] приймаємо масло індустріальне І-30А (за ДСТ 20 799−75).
Камери підшипників заповнюємо пластичним мастильним матеріалом УТ-1, періодично поповнюємо його шприцом через прес-маслянки.
10. Посадки деталей редуктора
Посадки призначаємо відповідно до вказівок, які є в табл. 10.13.
Посадка зубчастого колеса на вал H7/p6 за ДСТ 25 347−82.
Шейки валів під підшипники виконуємо з відхиленням вала k6.
Відхилення отворів у корпусі під зовнішні кільця по H7.
Інші посадки призначаємо, користуючись даними табл. 10.13[1].
Cписок літератури
Чернавський С. О. Курсове проектування деталей машин: Навчальний посібник для технікумів .- К., 2004
Шейнблит А. Е. Курсове проектування деталей машин: Навчальний посібник для технікумів. — К., 2003
Палей М. А. Допуски й посадки: Довідник: В 2ч. Ч.1. — К., 2005
В.И.Анурьєв Довідник конструктора-машинобудівника: т.1,2,3. — К., 2004
Єремєєв В.К., Горен Ю. Н. Курсове проектування деталей машин: Методичний посібник і завдання до проектів для студентів заочної форми навчання всіх технічних спеціальностей. — К., 2004.