Звіт з практики на ВАТ Пластик
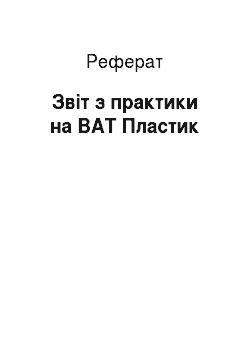
Таблиця 2.1 |№ |Найменування |Найменування технологічних показників — | |стадій і потоків| — | |реагентів — | — | |Температу|Давление |Количество|Прочие показники — | — |ра градусів — |загружаемы| — | — | — |x чи — | — | — | |поданих| — | — | — |компоненто| — | — | — |в — | |1 |2 |3 |4 |5 |6 — |1 |Водяної пар в — |3ч4,5 атм|не більш — | — |піч, поз. 201/1| — |40 т/час — | |2 |Паливний газ… Читати ще >
Звіт з практики на ВАТ Пластик (реферат, курсова, диплом, контрольна)
Содержание. Загальна характеристика підприємства ВАТ «пластик». 2 2 Апаратне оформлення процесу виробництва стиролу методом дегидрирования этилбензола. 5 2.1 Призначення цеху. 5 2.2 Фізико-хімічні основи процесу. 5 2.3 Технологічна схема відділення дегидрирования. 8 2.4 Опис реактора. 15 3 Характеристика загальнозаводського господарства. 18 3.1 Пароснабжение. 18 3.2 Електропостачання. 18 3.3 Водопостачання. 18 3.4 Каналізаційні споруди, очищення стічних вод мовби. 18 3.5 Ремонтно-механічна база. 18 3.6 Внутризаводской транспорт. 18 3.7 Складське господарство. 18 4 Безпека життєдіяльності. 19 4.1 Характеристика небезпеки виробництва 19 4.2 Характеристика вихідних речовин і продуктів. 22 4.3 Охорона навколишнього середовища. 24 Література. 27.
Загальна характеристика підприємства ВАТ «пластик».
Понад 35 років тому території Тульської області було організований Узловский хімічний завод, першої продукцією якого було текстолитовые каски.
У цей гримлячи Узловское товариство «Пластик «- це великий хімічний комплекс, до складу якого у собі 4 цеху синтезу полімерних матеріалів і п’яти цехів їхньої переробки зі своєю системою энергообеспечения.
До цехах синтезу належить цех із виробництва стиролу, який був став до ладу наприкінці 1975 года.
Потужність виробництва — 41 000 т/год.
Вихідний сировину — етилбензол. Основні постачальники є російські предприятия.
Що Виходить продукція відповідає ГОСТ 10 003–90.
Основні властивості стирола:
— безбарвна, легкозаймиста рідина із слабким специфічним запахом, нерозчинна в воде.
— температура запалення — 430С.
— температура кипіння — 145,20С.
— за рівнем на організм належить до третьої класу небезпеки — умеренно-опасные вещества.
Відмінною рисою нашого продукту є високий вміст основного речовини — 99,9%.
Цех оснащений автоматизованої системою управління процесом синтезу стиролу, розроблена вченими й впроваджена фахівцями нашого предприятия.
Є досвід експортування стиролу до Угорщини і Фінляндію через Союзхимэкспорт.
Цех із виробництва АБС-пластиков став до ладу в 1973 р. по технології, закупленої фірма «Асахі Кемікл «(Японія). Потужність виробництва — 23 000 т/год.
Основне вихідне сировину — стирол власного виробництва. Постачальники інших вихідних компонентів — російські предприятия.
Що Випускає АБС-пластик — міцний конструкционный матеріал 8-місячного марок, різних кольорів, відповідний ТУ 6−05−1587−84.
Основні свойства:
— ударна в’язкість по Изоду, щонайменше 20 — 25 кмб / см2.
— межа плинності при розтягненні щонайменше 390 кмб / см2 небезпеку здоров’я за безпосередньої контакту з ним.
Нині, починаючи з 1993 р., ведеться модернізацію устаткування з нарощування потужності. Роботи здійснюються досить важко конкурувати у умовах загального спаду производства.
Цех із виробництва емульсійної і суспензионного полістиролу був введений у правове експлуатацію у 1967 року. Потужність цехи з выпуску:
— суспензионного полістиролу — 5387 т/год.
— емульсійної полістиролу — 1580 т/год.
Вихідний сировину — стирол власного производства.
Суспензионный вспенивающийся полістирол призначений виготовлення спінених плит на будівництво і як тепло-, звукоизоляционного і пакувального материала.
Основні свойства:
— масова частка частинок основний фракції - щонайменше 89−95%.
— масова частка порообразователя — щонайменше 4,5−6% залежно від марки.
Відмінною рисою полістиролу ПСВ-С є спроможність до самозатуханию протягом 2−4 секунд.
Через відсутність споживачів емульсійної полістиролу фахівцями підприємства з урахуванням наявного устаткування розробили технологія отримання ударопрочного полістиролу УПС-М, випуск якого розпочато в 1993 р., потужність виробництва — 2320 т/год.
Ударопрочный полістирол УПС-М відповідає ТУ 6−00−1 023 832−12−94.
Основні характеристики:
— ударна в’язкість по Изоду — 9 кгс/см2.
— межа плинності при розтягненні - щонайменше 380 кгс/см2.
— теплостойкость по Віка — 95 °C.
— дозволено для контакту з харчовими продуктами.
З шести цехів переробки 3 цеху працюють на автомобилестроение.
Способи переробки пластмасс:
— лиття під давлением.
— прессование.
— экструзия.
У 1963 року пустили цех з випуску виробів методом прямого і трансферного пресування на пресах італійського провадження з зусиллям змикання від 40 до 400 т. з предпластификаторами. Є відділення підготовки сировини з усреднением його й таблетированием на роторних і гідравлічних таблетмашинах.
Потужність пресового устаткування — 1240 т/год.
Вихідний сировину — пресс-порошки, що їх підприємствами Росії, а також фенопласты власного виробництва марок У-1, У-2 (ГОСТ 5639−79).
Основна продукція цеху — деталі системи запалювання автомобілів, працюють у умовах високої напруги, корпусні деталі з термореактивных пластмас та інші, які мають опором ізоляції не менш 500 мОм за нормальної температури +100°С, високої ударної міцністю; вироби машиностроения.
У 1974 ж — 1975 рр. відпустили 1-ша до 2-га черги цехи з випуску деталей для Камського автозаводу методом лиття під давлением.
Потужність цеху — 3230 т/год.
Цех оснащений термопластавтоматами виробництва Німеччини, Італії, Польщі з обсягом виливки до 1500 см8 і питомим тиском до 2000 кг/см2.
Вихідний сировину: поліетилен, поліамід, поліпропілен й те, що їх російськими, підприємствами, і навіть АБС-пластики і ударопрочный полістирол власного производства.
Цех випускає вироби різної конструкційної складності, зокрема і з арматурой.
У 1970 р. до ладу вступив цех з випуску профильнопогонных виробів для Волжского автозавода.
Потужність цеху — 4249 т/год.
Виробництво оснащено экструдерами діаметром до 63 мм фірм Італії, Німеччини, Франции.
Вихідний сировину: ПВХ різних марок, поліетилен, поліамід, що їх російськими, підприємствами, і навіть власне сировину з урахуванням отримання ПВХпластиката.
Що Виходить продукція — трубки і шланги діаметром від 1,8 до 48 мм різного призначення: електроізоляційні, бензо-, антифризостойкие, харчові; профілі складної конфігурації, ущільнювачі і другое.
У цеху є відділення металізації лавсановій плівки завтовшки від 12 до 50 мікрон, шириною 1500 мм отримання поливинилхлоридного пластикату в гранулах з урахуванням смол ПВХ. Металізована лавсановая плівка використовується виготовлення профілів обробки автомобилей.
У 1985 р. пустили до ладу цех із виробництва шпалер, оснащений італійським, австрійським оборудованием.
Потужність провадження у випуску шпалер -32 619 млн. м2 /год.
Цех дбає про вітчизняного сировину, випускає шпалери методом глибокої друку, паперові і моющиеся, із елементами рельєфу з урахуванням спінених паст ПВХ.
Пізніше освоєно виробництво плівки ПВХ, дубльованої і декорованою під дерево й «чорною плівки завтовшки 400 мікрон, шириною 1200 мм, використовуваної для обробки меблів, і тілі-, радиоаппаратуры.
Потужність цехи з випуску плівки — 5 млн.136 тис. м2/год.
Цех виготовляє вали для глибокої друку до 1600 мм діаметром до 700 мм, і навіть шаблони для круглоі плоскотрафаретной печати.
На наявному устаткуванні підприємство випускає товари масового спроса:
— поліетиленової плівку завтовшки від 50 до 200 мікрон і завширшки до 2800 мм, і навіть вироби з неї (скатертини, мішки, сумки-пакеты).
— каски захисні для нафтовиків, газовиків і строителей.
— вироби побутових-побутової-господарсько-побутового призначення і дитячі игрушки.
Підприємство забезпечене власним енергетичним комплексом: цехами по поділу повітря і водопідготовки, котельнями, электроподстанциями, системою біологічного очищення стічних вод.
2 Апаратне оформлення процесу виробництва стиролу методом дегидрирования этилбензола.
2.1 Призначення цеха.
Цех призначений для стиролу методом дегидрирования этилбензола.
Характеристика цеху: 1. Рік входження у експлуатацію — IV квартал 1975 р. 2. потужність виробництва: проектируемая — 40 000 т/рік досягнута — 41 000 т/рік 3. Кількість технічних ліній — одна 4. Метод виробництва — безперервний 5. Генеральний проектувальник — ОНПО «Пластполимер» 6. проектувальник технологічної частини — Воронезький філія Гипрокаучук.
(АТ «Синтезкаучукпроект»).
Розробник технологічного процесу — ВНИИСК, р. Воронеж (НИИСК).
Організації виконали робочі креслення — Воронезький филиал.
Гипрокаучук (АТ «Синтезкаучукпроект»), Московський Гипрокаучук. 7. Категорія провадження у його із техніко-економічного рівню — перша 8. Виробництво розширенню та реконструкції не подвергалось.
2.2 Фізико-хімічні основи процесса.
Стірол отримують каталітичним дегидрированием этилбензола з наступної ректифікацією продуктів дегидрирования виділення стиролу з змістом основного речовини щонайменше 99,8%.
Дегидрирование этилбензола ввозяться присутності водяної пари на катализаторе марки К-28У, що містить оксид заліза і небагато сполук калію, рубідію, цирконію. Водяної пар вводиться зниження парциального тиску процесу, що сприяє зрушенню рівноваги реакції убік освіти стиролу, скорочення побічних реакцій лежить на поверхні катализатора.
Реакція дегидрирования этилбензола виробляється у двухступенчатом адиабатическом реакторі з проміжним підведенням тепла через межступенчатый підігрівник. Зміст стиролу після першому місці - щонайменше 23%, після Другої - щонайменше 47%.
Температура процесу 550−6400С, співвідношення етилбензол: пар одно 1:3ч3,5, тиск над шаром каталізатора трохи більше 1 атм.
Основна реакція дегидрирования:
[pic].
Побічні реакции:
[pic].
Изопропилбензол, який міститься у этилбензоле, у процесі дегидрирования перетворюється на L-метилстирол:
[pic].
Дивинилбензол полимеризуется із заснуванням нерозчинних полімерів в колонах ректификации.
Наявність бензолу призводить до утворення дивинила:
[pic].
Одночасно йдуть реакції дегидроконденсации із отриманням полициклических сполук — двухзамещенных стильбенов, фенантренов, нафталинов.
Вуглець, утворений при поділі вуглеводнів, видаляється з каталізатора водяником паром:
[pic].
Щоб запобігти полімеризації стиролу у його отримання використовуються також інгібітори: парахинондиоксим (ДОХНУВ), 4-нитрофенол — відхід (ПХФ), 2,6-дитретбутил-4-диметиламинометилфенол (підставу Манниха).
Норми технологічного режима.
Таблиця 2.1 |№ |Найменування |Найменування технологічних показників | | |стадій і потоків| | | |реагентів | | | | |Температу|Давление |Количество|Прочие показники | | | |ра градусів | |загружаемы| | | | | | |x чи | | | | | | |поданих| | | | | | |компоненто| | | | | | |в | | |1 |2 |3 |4 |5 |6 | |1 |Водяної пар в | |3ч4,5 атм|не більш | | | |піч, поз. 201/1| | |40 т/час | | |2 |Паливний газ | |0,3ч1,1 | | | | |перед пальниками | |атм | | | | |печі, поз. | | | | | | |201/1−2 | | | | | |3 |Перегрітий пар |трохи більше | | | | | |виході з |750 | | | | | |печі, поз. 201/1| | | | | |4 |Перегрітий пар |трохи більше | | | | | |виході з |750 | | | | | |печі, поз. 201/2| | | | | |5 |Розрядження в | |3ч15 мм | | | | |радиантных | |вод. ст. | | | | |камерах печі | | | | | |6 |Контактний газ | |трохи більше | | | | |над шаром, поз. | |1,0 атм | | | | |202/1 | | | | | |7 |Контактний газ | |трохи більше | |Зміст стиролу| | |під шаром, поз. | |0,6 атм | |щонайменше 23% | | |202/1 | | | | | |8 |Контактний газ | |трохи більше | | | | |над шаром, поз. | |0,6 атм | | | | |202/2 | | | | | |9 |Контактний газ | |трохи більше | |Зміст стиролу| | |під шаром, поз. | |0,2 атм | |не менее50% | | |202/2 | | | | | |10 |Водяної пар на | |3ч4,5 атм| |10ч15% вагових від | | |змочування в | |перед | |кількості ЭБШ | | |випаровувач, поз.| |регулятор| | | | |204 | |ом | | | | | | |витрати | | | |11 |Подача ЭБШ в |70ч80 | |трохи більше |Склад ЭБШ: | | |випаровувач поз. | | |12 т/час |этилбензола не | | |204 | | | |менш 99%, рівень| | | | | | |в поз. 204 не | | | | | | |понад десять% | |12 |Пароэтилбензольн|150ч160 | | | | | |на шихта на | | | | | | |виході з поз. | | | | | | |204 | | | | | |13 |Контактний газ |трохи більше |трохи більше | | | | |виході з |180 |0,2 атм | | | | |поз. 205/1−2 | | | | | |14 |Паровий | | | |Рівень 50ч70%, | | |конденсат в | | | |загальна лужність | | |казанах поз. | | | |трохи більше 12 | | |205/1−2 | | | |мг экв/кг | |15 |Вторинний пар з | |3ч4,5 атм| | | | |котлів поз. | | | | | | |205/1−2 | | | | | |16 |Контактний газ |трохи більше | | | | | |виході з |120 | | | | | |поз. 209 | | | | | |17 |Водоуглеводородн|40ч65 | | | | | |ый конденсат на | | | | | | |виході з поз. | | | | | | |217 | | | | | |18 |Контактний газ |трохи більше | | | | | |виході з |450 | | | | | |поз. 211 | | | | | |19 |Контактний газ | |100ч400 | | | | |на всасе | |мм вод. | | | | |компресорів, | |ст. | | | | |поз. 213/1−4 | | | | | |20 |Контактний газ |трохи більше |трохи більше | | | | |на нагнітання, |150 |2 атм | | | | |поз. 213/2−4 | | | | | |20а|Контактный газ |трохи більше |трохи більше | | | | |на нагнітання, |170 |2 атм | | | | |поз. 213/1 | | | | | |1 |2 |3 |4 |5 |6 | |21 |Абгаз на поз. |1ч8 | | | | | |216/1−2 | | | | | |22 |УВК в ємності | | | |Рівень трохи більше | | |поз. 219 | | | |80% | |23 |Водний конденсат| | | |Рівень 40ч80% | | |в ємності поз. | | | | | | |221 | | | | | |24 |Стоки в Х.З.К. |трохи більше | | |Зміст | | |після |40 | | |вуглеводнів не | | |теплообмінника | | | |понад сто мг/л | | |поз. 231 | | | | | |25 |Некондиційний | | | |Рівень 30ч80% | | |продукт в | | | | | | |ємності поз. 235| | | | | |26 |Паровий | | | |Рівень 30ч70% | | |конденсат в | | | | | | |ємності поз. | | | | | | |240/1−2 | | | | | |27 |Паровий |трохи більше | | | | | |конденсат на |40 | | | | | |скиданні в | | | | | | |каналізацію, | | | | | | |поз. 240 | | | | | |28 |Зливові стоки в| | | |Рівень трохи більше | | |ємності поз. | | | |80%, зміст | | |260/3 | | | |вуглеводнів не | | | | | | |понад сто мг/л | |29 |Паровий | | | |Загальна жорсткість не| | |конденсат від | | | |більш 20 мкг | | |насоса поз. | | | |экв/кг, | | |241/1−2 на | | | |прозорість по | | |харчування котлів | | | |шрифту щонайменше 40| | |поз. 205/1−2 і | | | |див. | | |повернення у | | | | | | |котельну | | | | | | | | | | | |.
2.3 Технологічна схема відділення дегидрирования.
Этилбензольная шихта (ЭБШ) — суміш свіжого этилбензола з заводського складу ЛВЖ і поворотного этилбензола з ємності, відділення промпродуктов, насосами подається в випаровувач поз. 204 з регулюванням витрати через кожухотрубчатый теплообмінник поз. 209, де підігрівається до 70−95 градусів водним конденсатом, які пройшли по трубному пространству.
Частина ЭБШ постійно подається на промисловий хроматограф зі скиданням на всос насосов.
У поз. 204 (кожухотрубчатый теплообмінник) ЭБШ нагрівається до температури кипіння, випаровується і лише частково перегревается.
Для зниження температури кипіння ЭБШ випаровування ведуть у струмі водяного пара.
Витрата пара на змішання в трубному просторі поз. 204 підтримується регулятором у кількості 10−15% від подачі ЭБШ.
Випаровування здійснюється з допомогою тепла конденсації водяної пари, подаваного в межтрубное простір испарителя.
Пари ЭБШ з температурою 150−160 градусів, регульованої витратою пара на випаровування, надходять із випарника в трубне простір перегревателя поз.203, де нагріваються з допомогою тепла перегрітого водяної пари, що надходить з межступенчатого подогревателя.
Перегріті пари ЗБШ з поз. 203 вступають у смесительную камеру реактора поз. 202, де змішуються з перегрітою водяником пором (трохи більше 750°С) у відсотковому співвідношенні I : — 3,5, що надходять з печі поз. 201/11, яка перебуває з цих двох радиантных камер та однієї конвекционной камери, об'єднаних до одного блок.
Реактор поз. 202 — вертикальний циліндричний апарат, що з двох щаблів, з проміжним підведенням тепла в межступенчатом подогревателе.
У кожній щаблі реактора перебуває шар каталізатора із вмістом оксиду заліза, невеликої кількості сполук калію, рубідію, цирконію. Для рівномірного розподілу пароэтилбензольной суміші перед верствами каталізатора передбачені розподільні устройства.
У реакторі відбувається каталітичний процес адиабатического двухступенчатого дегидрирования этилбензола в стирол в струмі водяної пари з проміжним підігрівом контактного газа.
Тиск на вході у I щабель — трохи більше I ати, виході з I щаблі - трохи більше 0,6 ати. При завищенні тиску до I ати включається звукова і світлова сигнализация.
Температура пароэтилбензольной суміші на вході у 1 щабель реактора 550- 6400С з допомогою эндотермической реакції і тепловтрат температура виходить із реактора поз. 202/1 контактного газу понижается.
Далі контактний газ підігрівається в межступенчатом подогревателе до температури 550−6300 з водяникам парою й надходить на 2 щабель реактора поз. 202/2, де триває дегидрирование під час проходження газу через шар катализатора.
Контактний газ з реактора вступає у котел-утилизатор поз. 205/1−2, де його тепло використовується щоб одержати вторинного водяного пари тиском 3−4,5 ати. Про відхиленнях рівня казанах від меж 50−70% подається звуковий і світловий сигнали на ЦПУ.
При завищенні тиску контактний газ перед апаратом поз. 209 більш 0,2 ати подається звуковий і світловий сигнали, спрацьовує блокування і закриваються отсечные клапани на трубопроводах подачі пара і паливного газу в піч поз. 201, ЭБШ — в випаровувач поз.204, і відкривається отсечной клапан на трубопроводі контактного газу від сепаратора поз. 212 в гидрозатвор поз. 234.
Далі контактний газ, охолоджене до температури трохи більше 1800С подається в пінний апарат позиція 209, де проходить через шар вспененного конденсату, подаваного на сітчасті тарілки апарату, охолоджується до температури трохи більше 1200С, очищається від катализаторной пилу й дістає вуглеводні з водного конденсату. Виробляється додаткове отпаривание вуглеводнів гострим пором з рідкої фази до виходу ХЗК з пінного апарату поз. 209.
Контактний газ з пінного апарату іде на 3-х ступінчасту конденсацию:
1-ша щабель конденсації - охолодження контактного газу — виробляється до температури 40−650С в конденсаторах повітряного охолодження поз. 210.
Конденсатор складається з 6-и горизонтально розташованих секцій, складених із оребренных біметалевих труб, обдуваемых потоком повітря, нагнетаемого осьовим вентилятором.
У разі потреби подається знесолена вода на зволоження повітря, охолоджуючого повітряні конденсатори (в літнє время).
Можлива циркуляція знесоленої води за схемою: через каплеотбойник поз. 211, охлаждаемый зворотної водою. Конденсатор є кожухотрубный теплообмінник; по трубному простору надходить що охолоджує зворотна вода, по межтрубному — контактний газ. З поз. 211 несконденсированный газ надходить послідовно через каплеотбойник поз. 212 (вертикальний, обсягом 5 м3) в конденсатор-холодильник поз. 216/1, охлаждаемый розчином этиленгликоля чи минаючи його, потім у розширювач поз. 212а.
Конденсат з поз. 211, 212, 212"а", 216/1 самопливом зливається в ємність поз. 218.
Для скидання надлишкового тиску газу (понад 500 мм вод. ст.) на всасывающем трубопроводі компресорів поз. 213/1−4 встановлено гидрозатворы поз. 234, звільнення поз. 234 виробляється у поз. 235. Гази після каплеотбойника поз. 212а направляються в усмоктувальний трубопровід компресорів поз. 213/1−4, де стискуються до тиску трохи більше 2,0 кгс/см2, нагрівається у своїй до температури трохи більше 1500С, потім охолоджується зворотної водою не в холодильнику поз. 214 і надходить у каплеотбойник поз. 215.
Конденсат з каплеотбойника поз. 215 і холодильника поз. 214 періодично виводиться в ємність поз. 230, звідки із накопиченням відкачують в ємність насосом поз. 218.
При завищенні тиску газу на нагнітанні компресорів більш 2 ати спрацьовує блокування і компресора зупиняються з одночасної подачею звукового і світлового сигналов.
Аналогічна блокування передбачена при відхиленні тиску всасе компресорів від меж 0,01−0,04 ати.
Схемою передбачено: подача знесоленої води (в літній час) в сорочки на охолодження компресорів із конкретним висновком в ємність поз. 260/3.
Передбачено регулювання тиску контактного газу лінії всаса компресорів поз. 213/1−4 перебросом надлишкового тиску з лінії нагнітання в лінію всаса.
III щабель конденсації - газ вступає у межтрубное простір конденсаторів поз. 216/2,1 з майданом охолодження 468 м², де охолоджується до 1ч80С розчином этиленгликоля (антифриз марки «40 »), що надходить з заводський сети.
Регулювання температури газу виході з поз. 216/1−2, (абгаза) здійснюється автоматично зміною витрати розчину этиленгликоля на конденсатор поз. 216.
З конденсатора поз. 216/1−2 несконденсированный газ вступає у сепаратор поз. 224, обсягом I м3, звільняється з уносимых крапель рідини, проходячи через каплеотбойное пристрій тарельчатого типу, і направляють у теплообмінник поз. 200.
Конденсат з конденсатора поз. 216/1−2 і сепаратора поз. 224 вступають у ємність поз. 218. Для запобігання проскока газу ємність поз. 218 у збірнику поз. 216/1−2 здійснюється регулювання сталості рівня. Несконденсированный газ (абгаз), що з метану, водню, вуглекислого газу, парів вуглеводнів та води, підігрівається в кожухотрубном теплообменнике поз. 200 з допомогою тепла парового конденсату, що надходить з межтрубного простору випарника поз. 204. Далі абгаз змішується з паливною газом і подається на спалювання в пароперегревательную піч поз. 201/2.
При пуск виробництва передбачене подання абгаза на воздушку. Водноуглеводородный конденсат, що з стиролу, этилбензола, бензолу, толуолу і конденсату водяної пари після поз. 212, 212 «а », 217 самопливом вступає у ємність поз. 218 обсягом 96 м³ з сітчастою перегородкою, де відбувається його відстій і расслоение.
Верхній шар із ємності поз. 216 — углеводородный конденсат (УВК) самопливом вступає у проміжний збірник поз. 219 обсягом 5 м³. Рівень в поз. 219 регулюються безупинної відкачуванням УВК відцентровими насосами поз. 220/1−2 у відділення промпродуктов в ємності поз. 401/1−2 обсягом 100 м³.
Повне звільнення ємності поз. 216 від вуглеводнів під час зупинки проводиться у разі трубопроводу з верхньої точки (люк) через оглядової ліхтар на всасе насоса поз. 200 і ємність поз. 219.
При зупинці робочого насоса автоматично включається резервний насос поз. 220.
Нижній шар — водний конденсат з поз. 218 вступає у ємність поз. 221, обсягом 8 м³. Рівень в ємності поз. 221 регулюється безупинної відкачуванням водного конденсату відцентровим насосом поз. 222/1−2, подається в пінний апарат поз. 220, обсягом 37,8 м³. Химзагрязненный конденсат після насоса поз. 222 поділяється на 3 потоку: частково на циркуляцію через змеевики для обігріву статей на відділенні дегидрирования з поверненням в трубопровід після регулюючого клапана (в зимовий період). Частково на циркуляцію в ємність поз. 246, звідки насосом поз. 247 за рівнем в поз. 246 і змійовик для обігріву статей на відділенні ректифікації і складу з поверненням в трубопровід всаса насоса поз. 222. У пінний апарат поз. 200 (весь потік) для отпаривания углеводородов.
У період насосом поз. 247 виробляється циркуляція для захолаживания знесоленої воды.
Водний конденсат з пінного апарату поз. 209 самопливом вступає у ємність 100, звідки насосом 100/1−2 через фільтр 101/1−2 і теплообмінник 229, 230 іде на установку екстракції і перегонки химзагрязненного конденсата.
Через калорифери повітряних конденсаторів поз. 210 чи в ємність поз. 218 подається насосом поз.301. Конденсат з ПЭУ відділення ректифікації через ємність поз. 301 обсягом 3,98 м³, водну шар із відділення промпродуктов з ємності віз. 420 обсягом 5,4 м³ і поз. 235 обсягом 2,2 м³ відділення дегидрирования. Ємність поз.236 служить для звільнення насосів і апаратів відділення дегидрирования.
Відпрацьований каталізатор з реактора поз. 201/1−2 під час капремонту з допомогою вакууму, створюваного компресором поз. 237, продуктивністю 1600 м3/час, вивантажується в бункер поз. 236 обсягом 48,5 м³ і вивозиться в спеціально відведений місце. Отсасываемый компресором поз.237 повітря очищається від катализаторной пилу на фільтрі поз.239 і скидається в атмосферу.
Перегрів водяного пара.
Перегрів водяного вару ввозяться пароперегревательной печі поз. 201/1−2, складається з двох радиантных камер та однієї конвекционной камери, об'єднаних до одного блок.
Пароперегревательная піч має 24 подові пальники, у яких спалюються природного газу і абгаз.
Водяної пар тиском 3−4,6 атм., отримуваний дросселированием що надходить з заводський мережі пара із тиском 10−12 атм., через сепаратор поз.199, і навіть отримуваний в котлах-утилизаторах поз. 205/1−2, надходить послідовний у конвекционную частина, й радиантную частина печі поз.201/1. При досягненні максимального рівні в сепараторе поз. 199−200 мм, подається світловий і звуковий сигнал і відкривається клапан на трубопроводі конденсату з сепаратора поз. 199 через холодильник поз. 245а в каналізацію. Перегрітий до температури трохи більше 7500С, пар вступає у межступенчатый перегреватель, де віддає тепло контактному газу, що виходить з першого щаблі реактора поз. 202/1, після чого вступає у перегреватель поз. 203, де віддає тепло пароэтилбензольной суміші і робить на повторний перегрів в піч поз. 201/1. Перегрітий до температури трохи більше 7500С, водяну пару з печі поз. 201/2 подається в смесительную камеру реактора поз. 202/1,2, де змішується з парами ЭБШ у відсотковому співвідношенні ЭБШ: пар = I: 3 +3,5. Передбачено можливість подачі перегрітого пара від проміжного колектора печі поз. 201/1 видалення полімеру з оборудования.
Блокування по пароперегревательной печи.
При зниженні витрати пара після регулятора нижче 15 т/ч автоматично припиняються: подача паливного газу на піч 201/1 і ЭБШ в випаровувач 204.
При зниженні тиску паливного газу до 0,8 атм. після регулятора автоматично припиняються: подача ЭБШ в випаровувач поз. 204 і є в піч поз. 201/1,2, про спрацьовуванні блокування подаються звуковий і світловий сигнали на ЦПУ. При спрацьовуванні блокування водяну пару продовжує вступати у піч поз. 201/1 по відвідної лінії Ф 57 повз отсечного клапана.
Паровий конденсат.
Чистий паровий конденсат відділення промпродуктов і з апаратів відділень дегидрирования і ректифікації вступає у збірник парового конденсату поз. 240/1−2, обсягом 10 м³. При відхиленнях від рівня 30−70% подаються звуковий і світловий сигналы.
Охолодження парового конденсату виробляється з допомогою конденсації парів вторинного скипання в конденсаторах поз.242, кожухотрубный теплообмінник з поверхнею нагріву 74,8 м², поз. 243, кожухотрубный теплообмінник з поверхнею нагріву 29,2 м², звідки конденсат самопливом зливається в збірники поз. 240/1−2.
Конденсація в конденсаторі поз. 243 здійснюється зворотному водою, в конденсаторі поз. 242 антифризом в зимовий період і зворотному водою (летом).
Паровий конденсат в зимовий період для підігріву антифризу проходить через межтрубное простір конденсатора поз. 242 і далі вступає у збірники поз. 240/1−2.
Кількість парового конденсату який струменіє через конденсатор поз. 242 (температура антифризу на вході з поз. 242) регулюється вручну арматурою на трубопроводі, конденсату з відділення дегидрирования на збірки поз. 240/1−2.
З збірника поз. 240/1−2 паровий конденсат відцентровими насосами поз. 241/1−2 подається харчування котлів-утилізаторів поз. 205/1−2 з регулюванням витрати за рівнем в котлах-утилизаторах надлишок конденсату тим самим насосом відкачують в заводську мережу парового конденсату з регулюванням витрати за рівнем в поз. 240/1−2. Паровий конденсат у запобігання зустрічі з киснем повітря перебуває під паровий подушкой.
При зупинці робочого насоса поз. 241 автоматично включається резервный.
Насосом поз. 241 конденсат подається на зволоження пара що надходить испарители ректифікаційних колон і роторно-пленочные аппараты.
Паровий конденсат від поз. 204 (200) виводиться в колектор відділення ректифікації (після регулятора тиску) й у збірники поз. 240/1−2 (в зимовий період — через поз. 242 в поз. 240/1−2). Арматура на трубопроводі конденсату від поз. 204 (200) до збірника поз. 240/1−2 повністю для запобігання запору конденсату від поз. 204 (200) при припинення подачі пара в кип’ятильники відділення ректификации.
При переповненні конденсатных збірок поз. 240/1−2 аварійний скидання конденсату здійснюється через гидрозатвор з охолодженням сбрасываемого в каналізацію конденсату з допомогою автоматичного перемішування холодної (зворотному) воды.
Періодичні відбори проб конденсату виробляються через охолоджувач проб поз. 244, обсягом 0,014 м³, охлаждаемый зворотному водой.
Без парового конденсату передбачена підживлення ємностей поз. 240/1−2 знесоленої водою з заводський мережі, а на виході з ладу насосів поз. 241/1−2 можна подавати обессоленную воду у котлы-утилизаторы поз. 205/1−2.
Для охолодження теплообмінників поз. 230, 214, конденсатора поз. 211 і сорочок компресорів поз. 213/1−4, 237 подається зворотний вода тиском щонайменше 2,5 атм. від заводський мережі по підземному трубопроводу. Введення заповнені у приміщенні компресорної так і безпосередньо у теплообмінника поз. 230.
2.4 Опис реактора.
Реактор призначений щоб одержати стиролу дегидрированием этилбензола у присутності водяної пари на катализаторе за нормальної температури 600−6300С.
Реактор складається з циліндричною обечайки Ш 4500 мм з верхнім і нижнім приварными полушаровыми днищами. Усередині реактора розміщений підігрівник контактного газу Ш 1600 мм, в межтрубное простір якого подається перегрітий водяну пару при тиску 2,3 кг/см2 і температурі 7000С, а, по трубах Ш 25Ч2 мм проходить контактний газ, що необхідно подогревать.
Реактор всередині футерован шамотным цеглою і минераловатными матами.
У верхньої та нижньої частинах апарату розміщений каталізатор, у якому відбувається перетворення этилбензола в стирол при високих температурах.
У верхню частину реактора перебуває змішувач, у якому этилбензольная шихта змішується з перегрітою водяником паром.
Реактор у робочому режимі працює наступним образом:
У штуцер, А подається перегрітий водяну пару за нормальної температури рівної 630ч6400С із тиском 1 атм., який після змішувача змішується з парами этилбензола, які надходять з штуцера М (t=5500C, p=1,1 атм.).
Потім суміш водяної пари з парами этилбензола за нормальної температури 6000С і тиску 0,9 атм через розподільне пристрій надходить перший шар каталізатора, у якому відбувається реакція дегидрирования этилбензола в стирол.
за рахунок эндотермической реакції температура суміші падає до 560−5650С.
Для збільшення виходу стиролу контактну суміш потрібно знову підігріти до температури 600ч6300С. Це відбувається у подогревателе. Контактний газ (t=560ч5650C, p=0,6 атм) вступає у трубне простір; в межтрубное простір через штуцер У надходить перегрітий водяну пару з температурою 7000С і тиском 2,3 атм.
Пара з штуцера Р виходить із температурою 6000С і тиском 2,2 атм, а контактний газ з температурою 600ч6300С і тиском 0,6 атм надходить на другий каталізатора, де відбувається подальше дегидрирование этилбензола в стирол.
З температурою 560ч6000С і тиском 0,2 атм контактний газ виходить через штуцер Б на охолодження і конденсацию.
При регенерації реактор працює наступним образом:
Через штуцер, А надходить теж кількість пара з температурою 600ч6500С і тиском 1 атм, а ще через штуцер М надходить паровоздушная суміш (t=500ч6000C, p=1,1 атм), котрі після змішування надходять на шар катализатора.
При температурі 600ч6500С, вугілля, отложившийся під час роботи реактора выгорает.
Потім суміш з температурою 6500С вступає у трубне простір подогревателя, де охолоджується до температури 550ч6000С.
У межтрубное простір через штуцер У подається водяну пару з температурою 450ч5000С і тиском 2,3 атм, який, прохолоджуючи паровоздушную суміш, нагрівається до температури 5500С і виходить через штуцер Г.
Потім паровоздушная суміш надходить другого шар каталізатора, де також йде вигоряння углерода.
Суміш газів регенераций і водяної пари з температурою 6500С виходить через штуцер Б на охолодження і конденсацию.
Встановлюється реактор на циліндричну опору.
Обсяг реактора V=193 м3.
Маса апарату становить 84 000 кг. До того ж стали Х17Н1342Т 18 900 кг, стали Х18Н10 Т 24 900 кг.
Габарити: 23 550Ч7780Ч5400.
Характеристика загальнозаводського хозяйства.
3.1 Пароснабжение.
Пароснабжение і теплопостачання здійснює цех № 22, який містить 2 котельные.
3.2 Электроснабжение.
Електроенергія підводиться до підприємства двома кабелями (6 кВТ): резервним і робочим. На підприємстві є система підстанцій і розподільних щитов.
3.3 Водоснабжение.
Водопостачання займається цех № 21, який подає питну і річкову воду. Є цех водопідготовки, який подає обессоленную воду. На території підприємства є артезіанські скважины.
3.4 Каналізаційні споруди, очищення стічних вод.
Цех № 32 проводить очищення всіх стоків заводу і города.
Біологічні очисні споруди повністю уведено підрозділи до експлуатацію у 1976 року загальної потужністю 50 тис. м3/добу. Попри скрутне становище в економіці, підприємство намітило в 1995 р. провести реконструциию частини загальної технологічного ланцюжка з метою поліпшення біохімічного окислення стоков.
Пропускна здатність очисних сооружений:
— по хозпитьевой воді - 1 млн. 600 тис. м3/год.
— по річковий воді - 3 млн. 685 тис. м3/год.
3.5 Ремонтно-механічна база.
Цех № 22 проводить поточний, плановий і капітальний ремонти. Цех № 29 виробляє ремонт оборудования.
3.6 Внутризаводской транспорт.
Транспортний цех № 31 містить близько сорока одиниць різної транспортної техніки. Також виробляється наймання транспорту для далеких перевозок.
3.7 Складське хозяйство.
На території підприємства перебувають 20 складів: центральні, спеціальні склади (горючі вибухонебезпечні соединения).
4 Безпека жизнедеятельности.
Експлуатація цеху стиролу пов’язані з застосуванням горючих і токсичних рідин і газоподібних продуктов.
Наявність великої кількості апаратів, насосів, компресорів, трубопроводів і запірної арматури створює умови для перепусток та витоків газів і вуглеводнів, що може спричинити до загазованості приміщень, територій й виникнення пожеж, вибухів, і навіть отруєнню чи травмування обслуговуючого персонала.
Стірол, етилбензол, бензол ставляться до легковоспламеняющимся жидкостям.
Основний особливістю провадження з погляду вибухонебезпечності продуктів є нижні межі взрываемости продуктів в суміші з повітрям. У результаті при неплотностях апаратів і комунікацій чи при аваріях помешкань цеху порівняно швидко можуть утворитися загальні чи місцеві вибухонебезпечні концентрации.
До основним на небезпеки в цеху относятся:
1. Отруєння парами углеводородов.
2. Термічний опік пором, гарячої водой.
3. механічне травмування у разі порушення правил обслуговування оборудования.
4. Поразка електрострумом з обслуговування электрооборудования.
5. Поразка від вибуху парів стиролу, этилбензола та інших легкозаймистих жидкостей.
6. Ядуха з обслуговування криниць, приямков, траншей, ємностей і апаратів у слідстві порушення правил техніки безпеки під час роботи з інертними газами (азотом).
4.1 Характеристика небезпеки производства.
Таблиця 4.1 |Наименов|Класс|Температура, градусів |Концентрацио|характеристика |Предельн| |ание | | |нный межа |токсичності |про | |сировини, |Опасн| |воспламенени|(воздействия на|допустим| |полупрод|ости | |я |організм |на | |уктов, |ГОCT | | |людини) |концентр| |готового|12. | | | |ация в | |продукта|I.007| | | |повітрі | |, |-76 | | | |робочої | |відходів | | | | |зони | |производ| | | | |производ| |ства | | | | |ственных| | | | | | |помещени| | | | | | |і. | | | |Вищий ґатунок |Перший сорт | |1 |2 |3 |4 | |1 |Зовнішній вид |Прозора однорідна рідина без | | | |механічних домішок і | | | |розчиненої вологи | |2 |Масова частка стиролу, % щонайменше |99,80 |99,60 | |3 |Масова частка фенилацетилена, % не |0,01 |0,02 | | |більш | | | |4 |Масова частка дивинилбензола, % не |0,0005 |0,0005 | | |більш | | | |5 |Масова частка карбонильных |0,01 |0,01 | | |сполук, у перерахунку | | | | |бензальдегид, % трохи більше | | | |6 |Масова частка перекисных соединений|0,0005 |0,0005 | | |враховуючи активний кисень, %| | | | |трохи більше | | | |7 |Масова частка полімеру, % трохи більше |0,001 |0,001 | |8 |Кольоровість по платиновокобальтовой |10 |10 | | |шкалою, од. Хазена трохи більше | | | |9 |Масова частка стабілізатора |0,0005−0,0010 |0,0005−0,0010 | | |пара-трет-бутилпирокатехина, % | | |.
Основні фізико-хімічні властивості і константи стирола.
Таблиця 4.3 |№ |фізико-хімічні властивості і константи стиролу |Значення і | | | |розмірність | |1 |Молекулярний вагу |104,15 | |2 |Щільність при 20 градусів |906,0 кг/м3 | |3 |Температура кипіння |145,2 градусів | |4 |Температура плавлення |-30,63 градусів | |5 |Показник заломлення |1,5462 | |6 |Критична температура |358 градусів | |7 |Критичний тиск |46,1 атм | |8 |Теплоємність при 20 градусів |43,64 кал/моль градусів | |9 |Теплота випаровування при 145,2 градусів |8,9 ккал/моль | |10|Теплота плавлення |25,9 ккал/кг | |11|Вязкость при 25 градусів |0,771 | |12|Давление насичених парів при 20 градусів |4,9 мм рт. У розділі ст. | |13|Удельное об'ємне електричне опір |10−11 ом/м | |14|Диэлектрическая проникність |2,431 |.
Характеристика вихідного сировини, матеріалів і полупродуктов.
Таблиця 4.4 |№ |Найменування |Государственны|Показатели, |Регламентируемые| | |сировини, |і чи |обов'язкові для |показники з | | |матеріалів, |галузевої |перевірки |допускаемыми | | |напівпродуктів |стандарт, | |відхиленнями | | | |технічні | | | | | |умови, | | | | | |регламент чи | | | | | |методика по | | | | | |підготовці | | | | | |сировини | | | |1 |2 |3 |4 |5 | |1 |Етилбензол |ГОСТ 9385−77 |зовнішній вигляд |Прозора, | | |технічний |вищого гатунку | |однорідна, | | | | | |безбарвна | | | | |реакція водної витяжки |рідина | | | | |щільність при 20 градусів, |Нейтральна | | | | |г/см3 |0,866−0,870 | | | | |масова частка |99,8 | | | | |этилбензола, % щонайменше| | | | | | |0,01 | | | | |масова частка | | | | | |изопропилбензола і | | | | | |вищих вуглеводнів, %|0,0005 | | | | |трохи більше | | | | | |масова частка хлору, % | | | | | |трохи більше | | |2 |Каталізатор |ТУ |Зовнішній вид |Гранули | | |К-28У |38.403 227−89 | |красно-коричнево| | | | | |го кольору | |3 |Парахинондиокс|ТУ 6−2 945−84 |Зовнішній вид |Мелкокристалличе| | |їм | | |ський комкающийся| | | | | |порошок від | | | | | |світло-сірого | | | | | |чи | | | | |Масова частка летючих |серовато-коричне| | | | |домішок, % трохи більше |вого до | | | | | |темно-сірого | | | | | |кольору | | | | | | | | | | | |20 | |4 |2,6 |ТУ 38−10 330−81|Внешний вид |Особливою чистоти, | | |-дитретбутил-4| | |вищого гатунку — | | |-диметиламином| | |кристалічний | | |етилфенол | | |порошок від | | | | | |ясно-жовтого | | | | |Масова частка летючих |до помаранчевого | | | | |речовин, % трохи більше |кольору | | | | | | | | | | | |0,2 | |5 |4-нитрофенол |ТУ 6−14−0876 |Зовнішній вид |Паста від | | |відхід | | |ясно-жовтого | | | | | |до коричневого | | | | |Зміст води, % не |кольору | | | | |більш |10,0 | |6 |Паратретичный |Імпорт |Зовнішній вид |Від білого до | | |бутилпирокатех| | |світло-сірого | | |ін | | |кольору |.
4.3 Охорона навколишнього среды.
Викиди в атмосферу.
Таблиця 4.5 |Найменування |Коли|Сумма|Периодичн|Характеристика выброса|Допустимое | |викидів, |чест|рный |ость | |кількість | |відділення, |у |обсяг| | |нормувальних| |апарат, диаметр|исто|отход| | |компонентів| |і висота |чник|ящих | | |шкідливих | |викиду. |вв |газів| | |речовин | | | |, | | |сбрасываемы| | | |м3/ча| | |x в | | | |з | | |атмосферу, | | | | | | |кг/час | | | | | |Темпера|Состав | | | | | | |туру | | | |1 |2 |3 |4 |5 |6 |7 | |Воздушник |1 |5,75 |постоянно|17 |Стірол — 625, |0,0036 | |апарату поз. | | | | |етилбензол — |0,0019 | |235, діаметр | | | | |330 | | |0,057 м, висота | | | | | | | |10 м. | | | | | | | |Воздушник |1 |14,04|постоянно|17 |Стірол — 1629,|0,0229 | |апарату поз. | | | | |етилбензол — |0,0024 | |260/3, діаметр | | | | |169 | | |0,069 м, висота | | | | | | | |5 м. | | | | | | | |Вентиляційна |1 |21 000|постоянно|18 |Стірол — 2,4, |0,0504 | |шахта в/с 13−2, | |0 | | |етилбензол — | | |діаметр 0,6 м, | | | | |6,6 | | |довжина 20 м. | | | | | | | |Вентиляційна |1 |8000 |постоянно|18 |Стірол — 6,0, |0,0400 | |шахта в/с В-12, | | | | |етилбензол — |0,0552 | |діаметр 0,4 м, | | | | |6,9 | | |довжина 16,2 м. | | | | | | | |Вентиляційна |1 |8100 |постоянно|18 |Стірол — 1,0, |0,0154 | |шахта в/с В-11, | | | | |етилбензол — 8|0,0648 | |діаметр 0,4 м, | | | | | | | |довжина 16,2 м. | | | | | | | |Воздушник |1 |115 |при |20 |Стірол |- | |апарату поз. | | |аварійних| | | | |234, діаметр | | |ситуаціях| | | | |0,273 м, висота | | | | | | | |15 м | | | | | | | |Воздушник |1 |5,75 |постоянно|16 |Стірол — 3444,|0,0198 | |апарату поз. | | | | |етилбензол — |0,0007 | |376а, діаметр | | | | |122 | | |0,057 м, висота | | | | | | | |23 м | | | | | | | |Воздушник |1 |15,5 |постоянно|16 |Стірол — |0,3478 | |апарату поз. | | | | |22 436, |0,0036 | |377, діаметр | | | | |етилбензол — | | |0,057 м, висота | | | | |234 | | |3 м | | | | | | | |Воздушник |1 |5,75 |постоянно|16 |Стірол — 3000,|0,0201 | |апарату поз. | | | | |етилбензол — |0,0016 | |378а, діаметр | | | | |275 | | |0,057 м, висота | | | | | | | |23 м | | | | | | | |Воздушник |1 |5,75 |постоянно|16 |Стірол — 4110,|0,0230 | |апарату поз. | | | | |етилбензол — |0,0025 | |380, діаметр | | | | |434 | | |0,057 м, висота | | | | | | | |23 м | | | | | | | |Воздушник |1 |5,75 |постоянно|16 |Стірол — 3555,|0,0204 | |апарату поз. | | | | |етилбензол — |0,0030 | |380, діаметр | | | | |520 | | |0,057 м, висота | | | | | | | |23 м | | | | | | | |Воздушник |1 |5,75 |постоянно|18 |Стірол — 2445,|0,0141 | |апарату поз. | | | | |етилбензол — |0,0013 | |370, діаметр | | | | |22 | | |0,057 м, висота | | | | | | | |12 м | | | | | | | |Воздушник |1 |14,04|постоянно|17 |Стірол — 2444,|0,0343 | |апарату поз. | | | | |етилбензол — |0,0022 | |360/1, діаметр | | | | |157 | | |0,089 м, висота | | | | | | | |5 м | | | | | | | |Воздушник |1 |14,04|постоянно|17 |Стірол — 1388,|0,0195 | |апарату поз. | | | | |етилбензол — |0,0013 | |360/2, діаметр | | | | |96 | | |0,089 м, висота | | | | | | | |5 м | | | | | | | |Воздушник |1 |5,75 |постоянно|17 |Стірол — |0,0604 | |апарату поз. | | | | |10 500, | | |377а, діаметр | | | | |етилбензол — | | |0,057 м, висота | | | | |394 | | |25 м | | | | | | | |Воздушник |1 |15,5 |постоянно|16 |Стірол — |0,1672 | |апарату поз. | | | | |10 786, |0,0196 | |375, діаметр | | | | |етилбензол — | | |0,057 м, висота | | | | |1267 | | |3 м | | | | | | | |Воздушник |1 |62,0 |постоянно|16 |Стірол — 3446,|0,2136 | |апарату поз. | | | | |етилбензол — |0,0282 | |378, діаметр | | | | |455 | | |0,0057 м, висота| | | | | | | |3 м | | | | | | | |Воздушник |1 |62,0 |постоянно|16 |Стірол — 1933,|0,1198 | |апарату поз. | | | | |етилбензол — |0,0065 | |380, діаметр | | | | |105 | | |0,057 | | | | | | | |1 |2 |3 |4 |5 |6 |7 | |м, висота 3 м | | | | | | | |Воздушник |1 |15,5 |постоянно|16 |Стірол — |0,3478 | |апарату поз. | | | | |22 436, |0,0036 | |379, діаметр | | | | |етилбензол — | | |0,057 м, висота | | | | |234 | | |3 м | | | | | | |.
Стічні воды.
Таблиця 4.6 |Найменування |Куди |Количе|Периодичность|Характеристика скидання | |стоку, відділення, |сбрасы|ство |скидання | | |апарат. |вается|стоков| | | | | | | |Склад |Дозволене | | | | | |скидання, |кількість | | | | | |мг/л (по |сбрасываемы| | | | | |компонентам|х шкідливих | | | | | |) |речовин, | | | | | | |кг/сутки | |Стічні води з |Очистн|150 |1 разів у месяц|Стирол — |0,5 | |апаратів поз. |ые |т/меся| |70, | | |260/1−3 | |ц | |етилбензол | | |(атмосферні води | | | |- 30 | | |з відкритих | | | | | | |майданчиків, | | | | | | |конденсат після | | | | | | |пропаривания | | | | | | |апаратів) | | | | | |.
Для зменшення забруднення атмосфери азот з парами вуглеводнів з ліній азотного дихання апаратів поз. 396/1, 2, 390/1,2, 398/1, 2, 272/1, 2, 320, 301 скеровуються в конденсатор поз. 345, охлаждаемыq розчином этиленгликоля, сконденсовані вуглеводні зливаються в ємність поз. 370, азот викидається в атмосферу.
Азот з парами вуглеводнів з ліній азотного дихання ємностей поз. 413/1, 2, 411/1−3 скеровуються в конденсацію на конденсатор поз. 417, з ліній азотного дихання ємностей 401/1, 2, 405/l, 2, 409/l, 2, 425 на конденсатор поз. 429.
Вуглеводні з конденсаторів зливаються в ємність поз. 420, азот викидається і атмосферу.
Несконденсированные гази від ПЭУ відділення ректифікації скеровуються в додаткові конденсатори поз. 375/11,12 для конденсації углеводородов.
.Химзагрязненные води утворюються з водного конденсату відділення дегидрирования, конденсату з ПЭУ відділення ректифікації, відстійних вод відділення промпродуктов, періодично сюди додаються води від промивання апаратів під час підготовки їх до ремонту. Очищення всієї химзагрязненной води від органіки виробляється шляхом отпарки в пінному аппарате.
Загальна кількість химзагрязненных вод цеху 6,0−8,0 м3/1 тн стирола.
Водноуглеводородный конденсат з конденсаторів поз. 210, 211, 216, 224 відділення дегидрирования вступає у ємність поз. 218.
У відділенні ректифікації джерелом химзагрязненных стічних вод мовби є пароэжекционные установки, призначені до створення вакууму в колонах ректифікації. Конденсат з барометрических ящиків поз. 376а, 378а, 379а, 380а, через ємності поз. 301, 360 вступає у ємність поз. 218.
Водний конденсат відділення промпродуктов містить ароматні вуглеводні (бензол, толуолу, етилбензол, стирол) не більше розчинності і направляють у ємність поз. 218.
У ємності поз. 218 відбувається і відстій, потім химзагрязненные води отпариваются від вуглеводнів в пінному апараті поз. 209 і скеровуються в установку очищення химзагрязненного конденсату (в разі скидання в химзагрязненную каналізацію охолоджується в теплообменнике поз. 231 до температури не вище 400С).
Скидання очищених стоків в водойми ввозяться відповідність до вимогами «правил охорони поверхневих вод від забруднення стічними водами «і величинами ГДК (дивіться таблицу).
ГДК речовин, які у виробництві стиролу, встановлені для водойм санітарно-побутового водоиспользования і рибогосподарського значения.
Таблиця 4.7 |№ |Найменування |ГДК |Водойми |Водойми | |пп |речовин |очистных|санитарно-бытового |рибогосподарського | | | |сооружен|водоиспользования |значення | | | |ий | | | | | | |ПДК,|Лимитирующий |ПДК,|Лимитирующий | | | | |мг/л|показатель |мг/л|показатель | | | | | |шкідливості | |шкідливості | |1 |Стірол |100ч300 |0,1 |Органолептичес|0,1 |Органолептическ| | | | | |київ | |ий | |2 |Етилбензол |140 |0,01|Органолептичес|0,01|Органолептическ| | | | | |київ | |ий | |3 |Толуолу |200 |0,5 |Органолептичес|0,5 |Органолептическ| | | | | |київ | |ий | |4 |Бензол |100 |0,5 |Санитарнотокси|0,06|Органолептическ| | | | | |логічний | |ий |.
Щоб не допустити влучення в зливну каналізацію продуктів виробництва з атмосферними водами, стекающими з відкритих майданчиків, скидання їх виробляється у залежність від аналізу, у химзагрязненную каналізацію чи незабруднені виробничі стоки через збірні підземні ємності поз. 260/1−3; при змісті вуглеводнів в ємностях поз. 260/1−3, понад сто мг/л виробляється відкачка їх у ємність поз. 218.
У аварійних випадках (при руйнуванні апаратів, трубопроводів) продукти провадження з зовнішніх майданчиків по міткам збираються в підземні ємності поз. 260/1−3, і тупиковий криницю, звідки повертається у виробництво через ємність поз. 218.
1. постійний технологічний регламент виробництва стиролу метдом дегидрирования этилбензола цеху 04-№ 1−04. Узловское ВАТ «пластик».