Комплексна організація виробництва морквяного соку
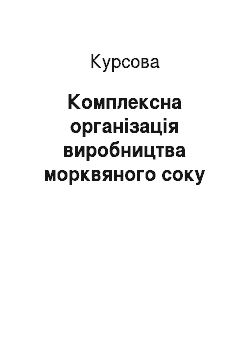
Далі морква потрапляє в дробарку, потім на шнековий бланшируватель, де проводять шпарення моркви. Після цього подрібнення пропарена маса потрапляє у здвоєну протиральну машину і випарний апарат, куди також подається цукровий сироп. Далі відбувається гомогенізація маси, в деаераторі видаляють повітря з маси і потім відбувається підігрів соку. В дозувально-наповнбвальному автоматі сок розливають… Читати ще >
Комплексна організація виробництва морквяного соку (реферат, курсова, диплом, контрольна)
Курсова робота
Комплексна організація виробництва морквяного соку
Вступ
Консервна промисловість, одна з важливіших галузей харчової промисловості України, що консервує харчові продукти, спеціалізуючись головним чином на виробництві плодоовочевих, м’ясних, рибних і молочних консервів. Консервна промисловість розвинулась на Україні вже в другій пол. 19 в., гол. на півдні, зокрема в Одесі (50% виробництва рибних консервів та понад 30% всього консервного виробництва України). В 1913 р. на Україні працювало 12 більших заводів, що разом з дрібнішими підприємствами випродукували 18 млн умовних банок овочевих і 15 млн м’ясних і рибних консервів, даючи до 90% виробництва цієї галузі.
Найбільше значення мас на Україні виробництво плодо-овочевих консервів (80% виробництва всієї К. п. України); в 1950;их рр. на Україні працювало 38 більших плодо-овочевих консервних заводів, та близько 215 дрібніших, розміщених переважно на півдні України. Найбільші з них працюють в таких містах, як Одеса, Херсон, Жданов, Симферопіль, Джанкой, Вінниця, Краматорське, Кам’янець — Подільський, Черкаси, Біла Церква, Ніжен.
В усьому світі соки традиційно користуються сталим попитом. Крім освіжаючої здатності, поживності, стимулюючої дії, гармонійного смаку, вони містять вітаміни та цілий комплекс біологічно активних речовин, необхідних людям для повноцінного і здорового харчування, особливо на стадії розвитку молодого організму. На жаль, середньостатистичний українець за рік вживає лише близько 8 літрів соків (для порівняння у 1996р.- 700 г, 1998р.- 2,5л), в той же час, як росіянин — 12, європеєць — 30, американець — 60 літрів.
Як свідчать результати маркетингових досліджень, основними споживачами соку є молоді люди віком 25−34 років, які проживають у містах. І хоча соки як продукт цінують однаковою мірою й чоловіки та жінки, проте за кількістю споживачів все ж таки переважають жінки.
Морквяний сік
Найбагатший з соків на природній бета-каротин, котрий перетворюється в організмі на вітамін А, що виконує важливу роль у процесі формування шкіри. Крім цього, вітамін, А є антиоксидантом, котрий оберігає шкіру від завчасного старіння. Морквяний сік містить також вітамін Е, який дбає про гарний вигляд шкіри, адже також є важливим антиоксидантом.
Примітка. Занадто велика кількість вітаміну, А призводить до пошкодження печінки, у котрій накопичується. Експерти радять випивати дві-три склянки морквяного соку на тиждень.
Український соковий ринок може скоротитись за підсумками 2011 року на 10% в натуральному вираженні. Такий прогноз озвучила Оксана Казанчук, директор по маркетингу групи компаній Т.В.Fruit, керівник проекту Galicia. «Ринок скорочується. За різними оцінками, падіння за підсумками 2011 року може становити близько 10%» , — сказала вона. В минулому році ринок соку в Україні скоротився майже на стільки ж.
Раніше на скорочення споживання соків в Україні звертав увагу Кестусіс Сліузас, генеральний директор «Тетра Пак Україна», яка виготовляє упаковку зокрема для даної категорії продуктів. «Зменшення об'ємів виробництва в більшій степені торкнулись категорії соків, оскільки сік не являється продуктом першої необхідності і люди скоротили витрати на його покупку» , — каже Кестусіс Сліузас.
Він відмітив, що в 2008 році споживання соків в Україні становило близько 14 літрів на душу населення, а в цьому році воно знизилось до 11 літрів: «Подальше зменшення споживання соків стало неприємним сюрпризом в цьому році. Можливо, до кінця року показник трохи зміниться, але росту ринку, на який всі сподівались, не відбулось». Він припустив, що зменшення попиту може бути пов’язано із ростом витрат населення, в тому числі й скороченням спрощеної системи оподаткування: «Ми прогнозуємо, що в наступному році споживання соків може поверутись на на рівень 2009 року, але це буде залежати від цілого ряду факторів» .
При цьому підкреслив, що об'єм споживання напоїв в Україні все ще відстає від європейського, де показник споживання на душу населення перевищує 20 літрів, і таким чином, у ринку є суттєвий потенціал росту.
1. Організація виробничого потоку по випуску нової продукції
1.1 Короткий опис технологічного процесу по виробництву морквяного соку
Моркву вигружають в лопатеву мийну машину, де проводиться первинна її мийка.
Після вторинної мийки в барабанній мийній машині, моркву сортують за якістю на інспекційному конвеєрі.Після цього морква потрапляє на ручну обрізку кінців та у карборундовую машину, де проводить очистка моркви від шкірки.Після цього морква піддається миттю в лопатевій мийній машині та інспектується на інспекційному конвеєрі.
Далі морква потрапляє в дробарку, потім на шнековий бланшируватель, де проводять шпарення моркви. Після цього подрібнення пропарена маса потрапляє у здвоєну протиральну машину і випарний апарат, куди також подається цукровий сироп. Далі відбувається гомогенізація маси, в деаераторі видаляють повітря з маси і потім відбувається підігрів соку. В дозувально-наповнбвальному автоматі сок розливають в заздалегідь підготовлену скляну тару 1−82−250.Герметизація проводять на закаточній машині і після цього банки подають в стерилізатор непреривної дії «Хунистор».
Простерилізовані банки миють в банкомийній машині та сушать в мийно-сушильному агрегаті.Потім банки обклеюють етикетками на етикетувальному автоматі.Укладку банок в короба і укладку коробів у штабеля здійснюють вручну. Транспортування готової продукції здійснюється за допомогою електропогрузчика.
1.2 Формування раціональної структури виробничого процесу
морквяний сік виробничий потоковий На цьому етапі необхідно сформувати оптимальну структуру виробничого процесу. Для цього я провела класифікацію виробничих операцій у вигляді таблиці 2.1 і аналізувала раціональність структури виробничого процесу
Таблиця 2.1 — Структура технологічного процесу по виробництву морквяного соку
Назва виробничих операцій. | Коасифікація виробничих операцій. | ||
За призначенням. | За способом виконання. | ||
Загрузка моркви в миючу машину | Допоміжна | Машинна | |
Первинна мийка | Основна | Машинна | |
Інспекція | Допоміжна (контр-вимір) | Машинно — Ручна | |
Обрізка кінців моркви | Основна | Ручна | |
Механічна чистка | Основна | Машинна | |
Мийка моркви | Основна | Машинна | |
Подрібнення | Основна | Машинна | |
Шпарка | Основна | Машинна | |
Протирка | Основна | Машинна | |
Змішування | Основна | Машинна | |
Гомогенізація | Основна | Машинна | |
Деаерація | Основна | Машинна | |
Підігрів | Основна | Машинна | |
Фасування | Основна | Машинна | |
Герметизація | Основна | Машинна | |
Стерилізація | Основна | Машинна | |
Етикетування | Основна | Машинна | |
Укладка банок у короба | Допоміжна (трансп) | Ручна | |
Установка коробів на штабеля | Допоміжна (трансп) | Ручна | |
Транспортування гот. пробукції на склад. | Допоміжна (трансп) | Машинна | |
Проаналізуємо цю структуру і визначимо, чи є вона раціональною, використовуючи наступні коефіцієнти:
1. Питома вага основних операцій:
Пит.вага 1= к-ть осн. Опер/заг. к-ть опер*100 = 15/20*100=75%
2. Питома вага машинних та машинно-ручних операцій:
Пит.вага 2= к-ть маш +к-ть маш-ручн/заг к-ть опер= 16+1/20= 85%
Отже, структуру виробничого процесу можна вважати раціональною, оскільки:
1) Кількість основних операцій не менше, ніж 60% від всіх операцій;
2) Кількість машинних та машинно-ручних, наближено до 80%.
1.3 Розрахунок планового змінного виробничого завдання потокової лінії
На наступному етапі необхідно визначити планове змінне виробниче завдання потокової лінії.
(1.1)
де, Qр — плановий річний обсяг виробництва продукції, нат.од.;
Єр — ємність ринку даного продукту, нат.од.;
Х — ринкова частка підприємства, 10%
Qp = 40 000*10/100 = 4000 т
та перспективний річний обсяг виробництва продукції (Qр.пер.), нат.од.:
(1.2)
Qp.пер =4000(1+5/100) =4200т
Тоді планове виробниче завдання на зміну розраховую за формулою:
т готової продукції /зм (1.3)
де, Феф — ефективний річний фонд роботи потокової лінії, діб.
Кзм — кількість змін роботи потокової лінії на добу, зм.
Nл.зм = 4200/100*2 = 21 т/зм
1.4 Розрахунок планових змінних виробничих завдань кожному робочому місцю
Подальша робота по організації потоку неможлива без визначення планового змінного виробничого завдання кожному робочому місцю.
Виробниче завдання робочому місцю потоку являє собою кількість предметів праці, яка повинна бути оброблена на кожному робочому місці потоку за одиницю часу, щоб забезпечити виконання планового завдання потокової лінії.
Планові виробничі завдання кожному робочому місцю, як для машинних операцій, так і для ручних та машинно-ручних операцій встановлюють за можливим виробітком потокової лінії.
Можливу виробку потокової лінії за зміну знаходжу, виходячи з розрахованого у попередньому розділі змінного завдання потокової лінії за формулою:
(1.4)
де, Кн — плановий коефіцієнт напруженості змінного завдання, який наданий у «Завданні»
qл.зм. = 21/0,97 =21,649 т/зм
У «Завданні» по всіх операціях виробничого процесу наведено коефіцієнт а0, що враховує об'єктивні розбіжності між тією кількістю предметів праці, які надходять на дану операцію і виходом готової продукції. Коефіцієнт попередньо визначений по операціях на основі продуктового розрахунку і технологічних схем виробництва продукції.
Далі кожному робочому місцю визначається планове виробниче завдання, тобто така кількість предметів праці, яка повинна бути оброблена на даному робочому місці за прийняту одиницю часу (годину- Ni год, зміну- Nі зм).
Розрахунок роблю за формулами та заношу в таблицю 2.2
(1.5)
Nі.зм. = 21,649*0,58 = 12,556
(1.6)
Nі.год. = 12,556/8-0,25 = 1,62
Таблиця 2.2 — Розрахунок планових виробничих завдань робочим місцям
Назва операцій. | № оп. | а0 | Планове виробниче завданн по операціях за зміну, тзм. Ni зм. | Планове виробниче завдання по операціях за годину, тгод. Ni год. | |
Загрузка моркви в миючу машину | 0,58 | 12,556 | 1,620 | ||
Первинна мийка | 0,57 | 12,339 | 1,592 | ||
Інспекція | 0,56 | 12,123 | 1,564 | ||
Обрізка кінців моркви | 0,55 | 11,906 | 1,536 | ||
Механічна чистка | 0,53 | 11,473 | 1,480 | ||
Мийка моркви | 0,51 | 11,040 | 1,424 | ||
Подрібнення | 0,5 | 10,824 | 1,396 | ||
Шпарка | 0,49 | 10,608 | 1,368 | ||
Протирка | 0,48 | 10,391 | 1,340 | ||
Змішування | 0,47 | 10,175 | 1,312 | ||
Гомогенізація | 1,03 | 22,298 | 2,877 | ||
Деаерація | 1,02 | 22,081 | 2,849 | ||
Підігрів | 1,02 | 22,081 | 2,849 | ||
Фасування | 1,02 | 22,081 | 2,849 | ||
Герметизація | 1,01 | 21,865 | 2,821 | ||
Стерилізація | 1,01 | 21,865 | 2,821 | ||
Етикетування | 21,649 | 2,793 | |||
Укладка банок у короба | 21,649 | 2,793 | |||
Установка коробів на штабеля | 21,649 | 2,793 | |||
Транспортування гот. пробукції на склад. | 21,649 | 2,793 | |||
1.5 Розрахунок планової продуктивності та кількості обладнання по кожному робочому місцю
Розрахунок планового виробничого завдання кожному робочому місцю потоку дозволяє визначити по машинних операціях необхідну для його виконання кількість машин певної марки і продуктивності, а по ручних операціях — необхідну кількість робітників.
У «Завданні» наведені по кожній операції три варіанти можливих для придбання марок обладнання та норми їх продуктивності, що є вихідними даними для визначення планової технічної норми продуктивності і кількості машин та апаратів для виконання планового виробничого завдання на кожній машинній виробничій операції.
Кількість одиниць обладнання визначаю шляхом порівняння планового виробничого завдання з технічною нормою продуктивності машини:
Кількість машин по кожному варіанту визначаю за формулою:
(1.7)
де, Ni год — виробниче завдання і-му робочому місцю на годину; т/год;
Пт і — технічна норма продуктивності і-го обладнання, т/год
Кі.м = 1,62/0,8 = 2,025
Розраховану кількість машин довела до більшого цілого числа, це буде
кількість обладнання по розстановці ().
Далі розраховую сумарну технічну норму продуктивності для кожної операції для трьох варіантів за формулою:
(1.8)
УПmi = 0,8*3 = 2,4
Результати розрахунків поступово заношу в таблицю 2.3, таблиця заповнюється тільки для машинних операцій.
Таблиця 2.3 — Розрахунок продуктивності і кількості обладнання потокової лінії по всіх варіантах
Назва операції | №операції | Назва обладнання, тип, марка | Виробниче завдання по операціях за годину. Ni год. | Коефіціент а0 | Технічна норма продуктивності, тгод. Пmі | Кількість обладнання. | Сумарна технічна норма продуктивності, тгод. (у предметах праці Упmi.) | ||
За розрахунком Кі розр. | За розстановкою. Кі розст. | ||||||||
Загрузка моркви в миючу машину | Контейнероопро-кидувач. | 1,62 | 0,58 | 0,80 | 2,025 | 2,4 | |||
2,00 | 0,81 | ||||||||
5,00 | 0,324 | ||||||||
Первинна мийка | Миюча машина | 1,592 | 0,57 | 1,00 | 1,592 | ||||
2,50 | 0,6368 | 2,5 | |||||||
6,00 | 0,265 | ||||||||
Інспекція | 1,564 | 0,56 | |||||||
Обрізка кінців моркви | 1,536 | 0,55 | |||||||
Механічна чистка | Агрегат А9-КЧЯ | 1,48 | 0,53 | 0,40 | 3,7 | 1,6 | |||
2,00 | 0,74 | ||||||||
5,00 | 0,296 | ||||||||
Мийка моркви | Миюча машина | 1,424 | 0,51 | 0,70 | 2,034 | 2,1 | |||
1,50 | 0,949 | 1,5 | |||||||
4,00 | 0,356 | ||||||||
Подрібнення | Дробарка Д1 | 1,396 | 0,5 | 0,60 | 2,326 | 1,8 | |||
2,00 | 0,698 | ||||||||
5,00 | 0,279 | ||||||||
Шпарка | Шнековий бланширу-ватель | 1,368 | 0,49 | 0,50 | 2,736 | 1,5 | |||
1,80 | 0,76 | 1,8 | |||||||
3,00 | 0,456 | ||||||||
Протирка | Протира-льна машина Т1-КП4Д | 1,34 | 0,48 | 0,60 | 2,233 | 1,8 | |||
1,50 | 0,893 | 1,5 | |||||||
2,50 | 0,536 | 2,5 | |||||||
Змішування | Випарний апарат МЗС-320 | 1,312 | 0,47 | 0,30 | 4,373 | 1,5 | |||
1,50 | 0,874 | 1,5 | |||||||
4,00 | 0,328 | ||||||||
Гомогенізація | Гомогенізатор А1-ОГМ | 2,877 | 1,03 | 1,00 | 2,877 | ||||
2,50 | 1,15 | ||||||||
4,00 | 0,719 | ||||||||
Деаерація | Деаератор | 2,849 | 1,02 | 0,80 | 3,561 | 3,2 | |||
1,50 | 1,899 | ||||||||
3,50 | 0,814 | 3,5 | |||||||
Підігрів | Випарний апарат МЗС | 2,849 | 1,02 | 0,60 | 4,748 | ||||
2,00 | 1,424 | ||||||||
3,50 | 0,814 | 3,5 | |||||||
Фасування | Автомат дозувально-наповнювальний БЧ-КАД | 2,849 | 1,02 | 0,50 | 5,698 | ||||
1,70 | 1,675 | 3,4 | |||||||
4,00 | 0,712 | ||||||||
Герметизація | Закаточна машина Б4-КАД | 2,821 | 1,01 | 0,40 | 7,052 | 3,2 | |||
1,50 | 1,88 | ||||||||
3,50 | 0,806 | 3,5 | |||||||
Стерилізація | Стериліза-тор Хуністр | 2,821 | 1,01 | 0,60 | 4,701 | ||||
1,50 | 1,88 | ||||||||
3,50 | 0,806 | 3,5 | |||||||
Етикетування | Автомат Б4-КЕМ | 2,793 | 0,30 | 9,31 | |||||
1,00 | 2,793 | ||||||||
2,50 | 1,117 | 2,5 | |||||||
Далі вибираю один з трьох варіантів, запропонованих у «Завданні» та при цьому враховую наступне.
Підбираю так, щоб значення сумарної технічної норми продуктивності по кожній операції (УПті) якнайближче підходило до значення планового виробничого завдання на годину (Ni год) даному робочому місцю, при цьому бажано вибирати варіант з меншою кількістю машин.
В таблицю 2.4 заношу дані тільки для прийнятого варіанта: планову кількість обладнання та планову сумарну технічну норму продуктивності обладнання, виражену у предметах праці, які обробляються.
В таблиці розраховую планову приведену сумарну технічну норму продуктивності обладнання, т/год. готової продукції за формулою:
(1.9)
УПmі(пр) = 5 / 0,58 = 8,62
Таблиця 2.4 — Розрахунок планової приведеної сумарної технічної норми продуктивності обладнання
Назва операцій. | № оп. | Назва обладнання, тип, марка. | Планова к-ть обладнання. | Планова сумарна технічна норма продуктивності, т/год. | ||
Упmi у предметах праці. | Упmi.пр. приведена у ГП. | |||||
Загрузка моркви в миючу машину | Контейнероопро-кидувач. | 8,62 | ||||
Первинна мийка | Миюча машина | 10,52 | ||||
Інспекція | ||||||
Обрізка кінців моркви | ||||||
Механічна чистка | Агрегат А9-КЧЯ | 9,43 | ||||
Мийка моркви | Миюча машина | 7,84 | ||||
Подрібнення | Дробарка Д1 | |||||
Шпарка | Шнековий бланшируватель | 6,12 | ||||
Протирка | Протиральна машина Т1-КП4Д | 2,5 | 5,2 | |||
Змішування | Випарний апарат МЗС-320 | 8,51 | ||||
Гомогенізація | Гомогенізатор А1-ОГМ | 4,85 | ||||
Деаерація | Деаератор | 3,5 | 3,43 | |||
Підігрів | Випарний апарат МЗС | 3,92 | ||||
Фасування | Автомат дозувально-наповнювальний БЧ-КАД | 3,92 | ||||
Герметизація | Закаточна машина Б4-КАД | 3,5 | 3,46 | |||
Стерилізація | Стерилізатор Хуністр | 3,5 | 3,46 | |||
Етикетування | Автомат Б4-КЕМ | |||||
1.6 Розрахунок планової чисельності працівників на кожному робочому місці та розподіл робіт між виконавцями
Розрахунок чисельності робітників для кожної ручної та машинно-ручної операції проводиться за формулою:
Чрі = Ni год * Нічас (1.10)
де, Нічас. — це норма часу на виконання ручної або машинно-ручної операції, год/т готової продукції (наведені у «Завданні»)
Отже розраховую чисельність робітників для кожної ручної операції:
Чрі =1,564 * 2,92 = 4,566
Чисельність робітників для обслуговування машин на машинних операціях визначається відповідно до норм обслуговування (Нобсл), наведених у завданні д
Чмі = Нобсл.і * Кмірозст (1.11)
А тепер розрахую чисельність робітників для обслуговування машин:
Чмі = 1 * 1 = 1
Одержану розрахункову чисельність робітників довела до більшого цілого значення, це є чисельністю робітників по розстановці по операціях потокової лінії.
Таблиця 1.5 — Розрахунок чисельності робітників
Назва операцій. | № оп. | Виробниче завдання по операціях, тонн за год. Ni год | Норма часу. т/годНічас | Норма обслуговування, чоловік. Нобсл.і | Кількість обладнання по розстановці. Км.і. Розст | Чисельність робітників, чол. | ||
За розрахунком. | За розстановкою. | |||||||
Загрузка моркви в миючу машину | 1,00 | |||||||
Первинна мийка | 0,5 | 0,50 | ||||||
Інспекція | 1,564 | 2,92 | 4,566 | |||||
Обрізка кінців моркви | 1,536 | 3,03 | 4,654 | |||||
Механічна чистка | 1,00 | |||||||
Мийка моркви | 1,00 | |||||||
Подрібнення | 1,00 | |||||||
Шпарка | 1,00 | |||||||
Протирка | 1,00 | |||||||
Змішування | 0,25 | 0,25 | ||||||
Гомогенізація | 0,5 | 1,00 | ||||||
Деаерація | 0,25 | 0,25 | ||||||
Підігрів | 0,25 | 0, 50 | ||||||
Фасування | 0,5 | 0,50 | ||||||
Герметизація | 0,5 | 0,50 | ||||||
Стерилізація | 0,5 | 0,50 | ||||||
Етикетування | 0,5 | 1,50 | ||||||
Укладка банок у короба | 2,793 | 2,11 | 5,893 | |||||
Установка коробів на штабеля | 2,793 | 1,95 | 5,446 | |||||
Транспортування гот. пробукції на склад. | 2,793 | 1,07 | 2,988 | |||||
Підсумовуючи чисельність робітників за розстановкою на всіх операціях я одержала явочну чисельність робітників на потоковій лінії у цілому (41 робітників).
1.7 Компонування робочих місць
Під компонуванням розуміють розміщення робочих місць та потокових ліній на виробничій площі. Методи компонування знаходяться у прямій залежності від технологічних особливостей виробництва та його типу. Основними вимогами, що пред’являються до компонування робочих місць, є:
— додержання потоковості виробничого процесу, досягнення найкоротшого шляху переміщення предмету праці у процесі його обробки;
— найбільш повне використання виробничої площі;
— додержання усіх правил техніки безпеки, охорони праці та промислової санітарії.
Оскільки при проектуванні потокової лінії на певній виробничій площі з багатьох варіантів, що повинні бути розглянуті з метою обрання найбільш оптимального і, який відповідає наведеним вище вимогам треба обрати варіант оптимальний, то для цього найбільш доцільно застосовувати комп’ютерну техніку. Якщо ж такі можливості відсутні, то компонування робочих місць проектують методом моделювання.
Висновок: При розрахунку чисельності, я скомпонувала робочі місця по 18,19 та 20 операціях.
2. Аналіз рівня організації виробничого процесу по випуску нової продукції
По закінченні проектування потокової лінії необхідно проаналізувати рівень організації основного виробництва та якщо необхідно, сформулювати пропозиції для його вдосконалення.
В даному розділі необхідно провести аналіз організації потокової лінії і оцінити рівень її раціональності, за такими показниками:
— перевірка можливості задоволення потреб ринку;
— ступінь використання виробничої потужності;
— узгодженість продуктивності машин на кожній операції з продуктивністю ведучої машини;
— рівень безперервності виробничого потоку;
— ступінь завантаження устаткування;
— рівень використовування устаткування в часі;
— рівень використовування робочого часу.
Для перевірки можливості задоволення потреб ринку я розраховую виробниче завдання потокової лінії та виробничу потужність, виходячи з запропонованого обладнання.
(1.12)
де, УПтпрmin - сумарна приведена норма продуктивності лімітуючої машини, т/год готової продукції;
N л.зм.' = 3 * (8−0,25) * 0,97 = 22,55 т
Кн — коефіцієнт напруженості змінного завдання.
Якщо N л зм' >= N л зм, то проектоване обладнання дозволяє задовольнити потреби ринку у даній продукції на перспективу, а якщо ні, то обладнання підібрано невірно та його треба замінити на більш продуктивне.
У моєму випадку N л зм' >= N л зм. Отже проектоване обладнання дозволяє задовольнити потреби ринку у даній продукції на перспективу.
Після цього необхідно визначити плановий фонд роботи лінії (Фпл), що дозволить виробити планований річний обсяг продукції.
(1.13)
Фпл = 4000 / 22,55 = 178 днів
Результат треба округлити до більшого цілого значення, що я і зробила.
Виробнича потужність потокової лінії визначається за ведучим обладнанням (яке вказане у «Завданні»).
Виробнича потужність потокової лінії за зміну
(1.14)
де, УПтвмпр- сумарна приведена технічна норма продуктивності ведучої машини, т/год готової продукції.
ВПл.зм = 8,51 * (8−0,25) = 65,952
Виробнича потужність потокової лінії за рік:
(1.15)
де, Феф — ефективний річний фонд роботи потокової лінії, який складається з двох складових: це робочий період потокової лінії, тобто кількість діб на рік, коли лінія працює (РП) та кількість змін на добу (Кзм) та надається у завданні.
ВПр = 65,952* 200 = 13 190,4
Феф = РП х Кзм
Феф = 100 * 2 = 200
При зміні попиту на продукцію можливо змінювати ту чи іншу складову, в результаті буде змінюватися випуск продукції.
Використання виробничої потужності оцінюють за наявністю резервів використання виробничої потужності та за коефіцієнтами використання потужності.
Інтегральний сумарний резерв використання виробничої потужності розраховую за формулою:
Rінтег = ВПр — Qр (1.16)
Rінтег = 13 190,4 - 4000 = 9190,4 т
Абсолютний резерв інтенсивного використання виробничої потужності
Rінт =(ВПл зм — Nл зм')*Феф (1.17)
Rінт = (65,952 - 22,25) * 200 = 8740,4 т
Абсолютний резерв есктенсивного використання виробничої потужності:
Rекс = (Феф — Фпл) *ВПл.зм (1.18)
Rекс = (200 - 178) * 65,952 = 1450,94 т
Ступінь використання виробничої потужності можливо оцінити шляхом розрахунку коефіцієнтів викоритання потужності.
Коефіцієнти використання потужності дорівнюють:
Кінтег = Qр / ВПр (1.19)
Кінтег =4000 / 13 190,4 = 0,303
Кінт = N л. зм' / ВП л. зм (1.20)
Кінт = 22,55 / 65,952 = 0,34
Кекс = Фпл /Феф (1.21)
Кекс = 178 / 200 = 0,89
Резерви використання виробничої потужності можливо задіяти, якщо збільшиться попит на продукцію та ємність ринку зросте. Наявність резервів свідчить про можливість збільшення обсягу виробництва продукції за потребами ринку та за рахунок яких факторів це можливо зробити.
Узгодженість продуктивності машин на кожній операції з продуктивністю ведучої машини визначається таким показником, як коефіцієнт узгодженості (Кузі).
Коефіцієнт узгодженості (пропорційності) Кузі — визначають відношенням сумарної приведеної продуктивності устаткування на i— тій операції (Піпр) до сумарної приведеної продуктивності ведучої машини (Пвмпр). Дані для розрахунку беру з таблиці 2.3.
(1.22)
Кузі = 8,62 / 1,88 = 4,585
Якщо значення коефіцієнта узгодженості на операціях виробничого процесу відрізняється від одиниці більше (менше), ніж на 5,0%, то виробничий потік можна вважати безперервним.
Крім того, якщо коефіцієнт узгодженості на операції буде менший за одиницю, то ця операція називається «вузьким місцем» потоку, обладнання на такій операції необхідно замінити на більш продуктивне.
Далі перевіряю ступінь завантаженості обладнання. Перевірка ведеться шляхом визначення коефіцієнта завантаження обладнання та коефіцієнта його використання в часі по кожному виду обладнання окремо.
Коефіцієнт завантаження Кзі — це відношення розрахункової необхідної кількості машин (Км.ірозр) до прийнятої для установки на потоковій лінії проектованої кількості машин (Км.і розст). Дані для розрахунку беру з таблиці 2.4.
(1.23)
Кзі = 0,4212 / 1 = 0,4212
Коефіцієнт використання обладнання у часі (Квикоб.і) знаходжу як відношення розрахункового часу роботи машини (обладнання) до номінального часу за зміну, добу.
(1.24)
Квикі = (11,05 / 8,62) * (1 / 7,75) = 0,165
Тобто чим ближче ці коефіцієнти до одиниці, тим краще використовується обладнання і чим ближчі між собою значення коефіцієнтів по окремих видах машин (обладнання) потокової лінії, тим краще підібране обладнання.
Необхідно також зробити висновки про рівень організації праці і виробництва на організованому виробничому потоці.
Співвідношення розрахункової чисельності робітників на операціях виробничого процесу Чрозрі реальної по розстановці Чрозстi, яка враховує можливості робітника суміщати операції і виконувати розширений об'єм робіт, дозволяє.визначити коефіцієнт використання робочого часу на окремих операціях (Квик.час i):
(1.25)
Квик.часі = 2 / 2 = 1
Значення коефіцієнтів використання робочого часу близьке до одиниці свідчить про високий рівень використання робочого часу і рівень організації праці на потоковій лінії.
Таблиця 2.6 — Аналіз рівня організації виробничого процесу по випуску нової продукції
№ операції | Назва операції | Приведена сумарна технічна норма продуктивності, т/год | Коефіцієнт узгодженості | Розрахунковий час роботи обладнання, годин | Коефіцієнт використання обладнання у часі | Кількість обладнання | Коефіцієнт завантаження | Чисельність робітників | Коефіцієнт використання робочого часу | |||
за розрахунком | за розстановкою | за розрахунком | за розстановкою | |||||||||
Загрузка моркви в миючу машину | 8,62 | 1,012 | 7,75 | 0,337 | 0,324 | 0,324 | 1,00 | |||||
Первинна мийка | 10,52 | 1,236 | 7,75 | 0,276 | 0,265 | 0,265 | 0,50 | 0,5 | ||||
Інспекція | 4,566 | 0,9132 | ||||||||||
Обрізка кінців моркви | 4,654 | 0,9308 | ||||||||||
Механічна чистка | 9,43 | 1,108 | 7,75 | 0,308 | 0,296 | 0,296 | 1,00 | |||||
Мийка моркви | 7,84 | 0,921 | 7,75 | 0,371 | 0,356 | 0,356 | 1,00 | |||||
Подрібнення | 1,175 | 7,75 | 0,290 | 0,279 | 0,279 | 1,00 | ||||||
Шпарка | 6,12 | 0,719 | 7,75 | 0,475 | 0,456 | 0,456 | 1,00 | |||||
Протирка | 5,2 | 0,611 | 7,75 | 0,559 | 0,536 | 0,536 | 1,00 | |||||
Змішування | 8,51 | 7,75 | 0,341 | 0,328 | 0,328 | 0,25 | 0,25 | |||||
Гомогенізація | 4,85 | 0,569 | 7,75 | 0,599 | 1,15 | 2,3 | 1,00 | |||||
Деаерація | 3,43 | 0,403 | 7,75 | 0,848 | 0,814 | 0,814 | 0,25 | 0,25 | ||||
Підігрів | 3,92 | 0,460 | 7,75 | 0,742 | 1,424 | 1,4 | 0, 50 | 0,5 | ||||
Фасування | 3,92 | 0,460 | 7,75 | 0,742 | 0,712 | 0,712 | 0,50 | 0,5 | ||||
Герметизація | 3,46 | 0,406 | 7,75 | 0,840 | 0,806 | 0,806 | 0,50 | 0,5 | ||||
Стерилізація | 3,46 | 0,406 | 7,75 | 0,840 | 0,806 | 0,806 | 0,50 | 0,5 | ||||
Етикетування | 0,352 | 7,75 | 0,969 | 2,793 | 1,07 | 1,50 | 0,75 | |||||
Укладка банок у короба | 5,893 | 0,9821 | ||||||||||
Установка коробів на штабеля | 5,446 | 0,9076 | ||||||||||
Тр г/п на склад | 2,988 | 0,996 | ||||||||||
11,345 | 10,748 | 34,547 | 15,4797 | |||||||||
Виходячи з даних таблиці 6, можна зробити наступні висновки:
1) Виробничий потік є перервним, оскільки коеф. узгодження відрізняється від одиниці більше ніж на 5%, також обладнання на операціях 2,5,6,7,8,9,11,12,13,14,15,16 є «вузьким місцем» і його треба замінити.
2) Навантаженість обладнання коливається в межах від 20% до 84%. Це свідчить про те, що обладнання не буде вистачати.
3) Обладнання використовують не на 100% ефективно, це може бути частково пов’язано з особливостями технологічного процесу.
4) Значення коеф. використаного робочого часу близьке до одиниці і це свідчить про високий рівень використаного робочого часу і рівень організації праці на потоковій лінії.
3. Організація технічного обслуговування і ремонтів потокової лінії
Завдання ремонтного обслуговування виробництва полягає в тому, щоб забезпечити безперервну і якісну роботу устаткування, зведення до мінімуму випадків аварійних зупинок виробництва.
Ремонтне обслуговування необхідно здійснювати таким чином, щоб попередити поломки устаткування і непередбачені зупинки, зниження якості роботи устаткування.
Це можна забезпечити за допомогою системи планового технічного обслуговування і ремонту (ПТОР), яка здійснюється відповідно до плану.
В даному розділі курсової роботи необхідно спланувати об'єм ремонтних робіт і чисельність ремонтного персоналу, (у тому числі по професіях) для ремонтного обслуговування, відповідно до системи ПТОР організованого виробничого потоку.
Використовуючи галузеве «Положення про систему технічного обслуговування і ремонту технологічного устаткування» в «Завданні» вибрана і надана вся необхідна інформація для планування робіт по техобслуговуванню і ремонту устаткування.
Для визначення структури ремонтного циклу необхідно розрахувати число всіх видів ремонтів і технічних обслуговувань.
Кількість середніх ремонтів я розраховую за формулою:
(1.26)
де Кс — число середніх ремонтів в одному ремонтному циклі;
Трц — тривалість ремонтного циклу;
Пс — період часу між двома середніми ремонтами;
1 — число капітальних ремонтів в одному ремонтному циклі.
Кс = 36 /12 — 1 = 2
Кількість поточних ремонтів розраховую за формулою:
(1.27)
де Кп — число поточних ремонтів в одному ремонтному циклі;
Пп — період часу між двома поточними ремонтами.
Кп = 36 / 6 — (2 + 1) = 3
Кількість технічних обслуговувань розраховую за формулою:
(2.28)
де Кто — число оглядів в одному ремонтному циклі;
Пто — період часу між двома технічними обслуговуваннями.
Кто = 36 / 2 — (2 + 3 + 1) = 12
Результати розрахунків представляю у вигляді таблиці 2.7.
Таблиця 2.7 — Розрахунок кількості ремонтів в одному ремонтному циклі
Найменування устаткування | Період між ремон-тами. К С П ТО | Кількість ремонтів в одному ремонтному циклі | |||
Середніх | Поточних | Технічних обслуговувань | |||
Контейнероопрокидувач. | |||||
; | |||||
Миюча машина | |||||
Агрегат А9-КЧЯ | |||||
; | |||||
Миюча машина | |||||
Дробарка Д1 | |||||
; | |||||
Шнековий бланшируватель | |||||
Протиральна машина Т1-КП4Д | |||||
; | |||||
Випарний апарат МЗС-320 | |||||
Гомогенізатор А1-ОГМ | |||||
; | |||||
Деаератор | |||||
Випарний апарат МЗС | |||||
Автомат дозувально-наповнювальний БЧ-КАД | |||||
Закаточна машина Б4-КАД | |||||
; | |||||
Стерилізатор Хуністр | |||||
; | |||||
Автомат Б4-КЕМ | |||||
За даними таблиці по кожному виду обладнання будують структуру ремонтного циклу в аналітичному вигляді.
Назва обладнання, тип, марка. | Структура ремонтного циклу в аналітичному вигляді | |
Контейнероопрокидувач. | К-ТО1-ТО2-ТО3-ТО4-ТО5-ТО6-ТО7-ТО8-ТО9ТО10-ТО11-П-ТО12-ТО13-ТО14-ТО15-ТО16-ТО17-ТО18-ТО19-ТО20-ТО21-ТО22-К | |
Миюча машина | К-ТО1-ТО2-П1-ТО3-ТО4-С1-ТО5-ТО6-П2-ТО7-ТО8-С2-ТО9-ТО10-П3-ТО11-ТО12-К | |
Агрегат А9-КЧЯ | К-ТО1-П1-ТО2-П2-ТО3-П3-ТО4-П4-ТО5-П5-ТО6-П6-ТО7-П7-ТО8-П8-ТО9-П9-ТО10-П10-ТО11-П11-ТО12-П12-К | |
Миюча машина | К-ТО1-ТО2-П1-ТО3-ТО4-С1-ТО5-ТО6-П2-ТО7-ТО8-С2-ТО9-ТО10-П3-ТО11-ТО12-К | |
Дробарка Д1 | К-ТО1-ТО2-П1-ТО3-ТО4-П2-ТО5-ТО6-П3-ТО7-ТО8-К | |
Шнековий бланшируватель | К-ТО1-П1-ТО2-П2-ТО3-С1-ТО4-П3-ТО5-П4-ТО6-С2-ТО7-П5-ТО8-П6-ТО9-К | |
Протиральна машина Т1-КП4Д | К-ТО1-ТО2-ТО3-П1-ТО4-ТО5-ТО6-П2-ТО7-ТО8-ТО9-П3-ТО10-ТО11-ТО12-П4-ТО13-ТО14-ТО15-П5-ТО16-ТО17-ТО18-П6-ТО19-ТО20-ТО21-П7-ТО22-ТО23-ТО24-П8-ТО25-ТО26-ТО27-К | |
Випарний апарат МЗС-320 | К-ТО1-П1-ТО2-П2-ТО3-С1-ТО4-П3-ТО5-П4-ТО6-С2-ТО7-П5-ТО8-П6-ТО9-К | |
Гомогенізатор А1-ОГМ | К-ТО1-ТО2-ТО3-П1-ТО4-ТО5-ТО6-П2-ТО7-ТО8-ТО9-П3-ТО10-ТО11-ТО12-П4-ТО13-ТО14-ТО15-П5-ТО16-ТО17-ТО18-П6-ТО19-ТО20-ТО21-П7-ТО22-ТО23-ТО24-П8-ТО25-ТО26-ТО27-К | |
Деаератор | К-ТО1-ТО2-ТО3-П1-ТО4-ТО5-ТО6-С1-ТО7-ТО8-ТО9-П2-ТО10-ТО11-ТО12-С2-ТО13-ТО14-ТО15-П3-ТО16-ТО17-ТО18-К | |
Випарний апарат МЗС | К-ТО1-П1-ТО2-П2-ТО3-С1-ТО4-П3-ТО5-П4-ТО6-С2-ТО7-П5-ТО8-П6-ТО9-К | |
Автомат дозувально-наповнювальний БЧ-КАД | К-ТО1-П1-ТО2-С1-ТО3-П2-ТО4-С2-ТО5-П3-ТО6-К | |
Закаточна машина Б4-КАД | К-ТО1-П1-ТО2-П2-ТО3-П3-ТО4-П4-ТО5-П5-ТО6-К | |
Стерилізатор Хуністр | К-ТО1-ТО2-ТО3-П1-ТО4-ТО5-ТО6-П2-ТО7-ТО8-ТО9-П3-ТО10-ТО11-ТО12-П4-ТО13-ТО14-ТО15-П5-ТО16-ТО17-ТО18-П6-ТО19-ТО20-ТО21-П7-ТО22-ТО23-ТО24-П8-ТО25-ТО26-ТО27-К | |
Автомат Б4-КЕМ | К-ТО1-ТО2-П1-ТО3-ТО4-С1-ТО5-ТО6-П2-ТО7-ТО8-С2-ТО9-ТО10-П3-ТО11-ТО12-К | |
Планування ремонтів здійснюється шляхом складання графіка виведення устаткування в ремонт. Графік складається на основі ремонтного циклу для всіх одиниць устаткування. Графік необхідно розробити на плановий рік за місяцями.
Для проведення капітального ремонту будь-якого обладнання здійснюється зупинка у роботі всієї потокової лінії - річна зупинка, тому необхідно вибрати місяць і у цей період планувати проведення капітальних ремонтів всього обладнання потокової лінії. Тому спочатку розробляють нормативний плановий графік ремонту, а потім його корегують таким чином, щоб капітальні ремонти всіх видів обладнання проводились одночасно. При цьому враховують наступне:
— річна зупинка проводиться у тому місяці, коли лінія не працює (для сезонного виробництва) або коли випуск продукції найменший;
— ремонтні роботи носять профілактичний характер, тому капітальний ремонт краще робити в строк чи раніш за нормативний термін.
Розрахуємо план-графік ремонтних робіт на лінії по виробництву, починаючи з 1 вересня по грудень.
№ | вересень | жовтень | листопад | грудень | |
ТО1 | П1 | ТО2 | П3 | ||
; | ТО1 | ; | ТО2 | ||
; | ; | ; | ; | ||
; | ; | ; | ; | ||
ТО1 | ТО2 | ТО3 | ТО4 | ||
; | ТО1 | ; | ТО2 | ||
; | ТО1 | ; | ТО2 | ||
; | ТО1 | ; | ТО2 | ||
ТО1 | П1 | ТО3 | С1 | ||
; | ТО1 | ; | ТО2 | ||
ТО1 | ТО2 | ТО3 | ТО4 | ||
ТО1 | ТО2 | ТО3 | ТО4 | ||
; | ТО1 | ; | ТО2 | ||
; | ТО1 | ; | ТО2 | ||
; | ТО1 | ; | ТО2 | ||
ТО1 | ТО2 | П2 | ТО3 | ||
; | ТО1 | ; | ТО2 | ||
На основі даних річного графіка планових ремонтів розраховую планову трудомісткість ремонтних робіт по кожній одиниці устаткування. При цьому необхідно пам’ятати, що співвідношення між нормами трудомісткості капітального, середнього, поточного ремонту і планового технічного обслуговування складають К: С: П: ТО = 1: 0,6: 0,2: 0,03
Трудомісткість капітального ремонту устаткування першої категорії ремонтоскладності (машини-еталона) складає 35 чол.-год. Таким чином, трудомісткість усіх ремонтних робіт по і-ой машині складає:
Тплi =35* [Кк.р.(рік) + 0,6 Кc.(рік) + 0,2 Кп.(рік) + 0,03 Кт.о.(рік) ] *КРСі*nмi (2.29)
де, Тплi — трудомісткість ремонтних робіт i-ої машини в плановому періоді, чол.-год.;
КРСі - категорія ремонтоскладності машини;
nмi — кількість однотипних машин в потоковій лінії, од.
Тплi =35*(0 + 0,6 * 1 + 0,2 * 1 + 0,03 * 4) * 2,4 * 2 = 154,56 год.
Результати розрахунків вношу в таблицю 2.9.
Таблиця 2.9 — Розрахунок планової трудомісткості ремонтних робіт всього обладнання
Найменування устаткування, тип, марка | Кількість одиниць обладнання | Карегорія ремонтоскладності | Кількість ремонтів за плановий період | Планова трудомісткість ремонтних робіт, год | ||||
К | С | П | ТО | |||||
1.Контейнероопро-кидувач. | 37,1 | |||||||
2.Миюча машина | 2,4 | 154,56 | ||||||
3.Агрегат А9-КЧЯ | 4,2 | 202,86 | ||||||
4.Миюча машина | 2,4 | 77,28 | ||||||
5.Дробарка Д1 | 2,1 | 51,45 | ||||||
6.Шнековий бланшируватель | 4,9 | 186,935 | ||||||
7.Протиральна машина Т1-КП4Д | 1,8 | 109,62 | ||||||
8.Випарний апарат МЗС-320 | 3,6 | 137,34 | ||||||
9.Гомогенізатор А1-ОГМ | 4,5 | 137,025 | ||||||
10.Деаератор | 5,8 | 515,62 | ||||||
11.Випарний апарат МЗС | 3,6 | 137,34 | ||||||
12.Автомат дозувально-наповнювальний БЧ-КАД | ||||||||
13.Закаточна машина Б4-КАД | 241,5 | |||||||
14.Стерилізатор Хуністр | 25,3 | 1540,77 | ||||||
15.Автомат Б4-КЕМ | 5,8 | 186,76 | ||||||
4479,16 | ||||||||
Планова чисельність ремонтного персоналу знаходиться, виходячи з трудомісткості ремонтних робіт. Для обліку різного роду непередбачених робіт при ремонтному обслуговуванні потокової лінії, розраховану загальну трудомісткість ремонтних робіт необхідно збільшити на 10%.
Тоді планова чисельність ремонтного персоналу (Чрем.) для обслуговування потокової лінії складе:
(1.30)
де, Кн.р. — коефіцієнт непередбачених робіт (1,1−1,2);
Фр — річний фонд робочого часу 1 робітника, год.;
Кв.н. — коефіцієнт виконання норми виробітки (1,05−1,2)
Чрем = 4479,16 * 1,1 / 800 * 1,1 = 5,59 = 6 чол.
Кожен вид ремонтних робіт передбачає виконання:
слюсарних робіт — 72,5% від загальної трудомісткості;
Чрем = 3247,4 * 1,1 / 800 * 1,1 = 4,04 = 4 чол.
верстатних робіт — 20% від загальної трудомісткості;
Чрем = 895,8 * 1,1 / 800 * 1,1 = 1,1 = 1 чол.
інших (малярних, зварювальних, жерстяних і т.п.) — 7,5% від загальної трудомісткості.
Чрем = 335,9 * 1,1 / 800 * 1,1 = 0,4 = 1 чол.
Висновок: Ми спланували об'єм ремонтних робіт і чисельність ремонтного персоналу для ремонтного обслуговування. Виходячи з цього співвідношення я визначила чисельність ремонтних робітників за професіями (слюсарі, верстатники, інші):
— 4 робітники на виконання слюсарних робіт
— 1 робітник на виконання верстатних робіт.
— 1 робітник на виконання інших робіт.
4. Організація системи матеріального обслуговування нового виробництва
Для того, щоб забезпечити підприємство необхідними матеріалами відповідно до виявленої потреби, організовується матеріально-технічне постачання підприємства. Його завдання полягає у визначенні потреби підприємства у матеріалах і технічних ресурсах, дослідженні можливостей покриття цієї потреби, організації зберігання матеріалів і видачі їх у цехи, а також в проведенні контролю за використанням матеріально-технічних ресурсів і сприяння їх економії.
Вирішуючи цю задачу, працівники органів постачання повинні вивчати і враховувати попит і пропозицію на всі споживані підприємством матеріальні ресурси, рівень і зміну цін на них, на послуги посередницьких організацій, вибрати найбільш оптимальну форму руху товару, оптимізувати запаси, знижувати транспортно-заготівельні і складські витрати.
На рівні підприємства запаси належать до об'єктів, які потребують великих капіталовкладень є одним з чинників, що визначає політику підприємства, впливає на рівень управління ресурсами. Проте багато підприємств не приділяють цьому належної уваги і недооцінюють свої потреби у наявних запасах. В результаті цього їм доводиться вкладати в запаси більший капітал, чим передбачалося.
Товарно-матеріальні запаси забезпечують безпеку системи матеріально-технічного постачання, її гнучке функціонування.
Існує три види товарно-матеріальних запасів:
1. сировинні матеріали (комплектуючі вироби та паливо);
2. товари, що знаходяться на стадії виробництва;
3. готова продукція.
Залежно від їх цільового призначення вони підрозділяються на наступні категорії:
— технологічні (перехідні) запаси, які рухаються з однієї частини системи в іншу;
— поточні (циклічні) запаси, що створюються протягом середньостатистичного виробничого періоду, або запаси обсягом у одну партію товарів; резервні (страхові або «буферні»); іноді їх називають «запасами для компенсації випадкових коливань попиту» (до цієї категорії відносяться спекулятивні запаси, що створюються на випадок очікуваних змін попиту або пропозиції на ту або іншу продукцію.
Існують певні обмеження на розмір товарно-матеріальних запасів. Обмеженнями виступають витрати на їх зберігання. Тому виникає необхідність досягнення балансу між перевагами і недоліками: з одного боку — витрати на замовлення, а з іншого — витрати на зберігання товарів. Цей баланс досягається вибором оптимального обсягу партій замовлених товарів, або визначенням економічного (оптимального) розміру замовлення (economic order quantity), який обчислюється за формулою Вілсона:
де S — річний (сезонний) обсяг потреби у ресурсі, т;
С0 - витрати на організацію однієї заявки, од/од; Сu — витрати на зберігання одиниці ресурсу, грн/т.
Ропт = v2*40000*107/2,9 = 1718,05
У курсовій роботі для двох видів сировинних ресурсів або матеріалів (допоміжна сировина, тара, упаковка), потрібно визначити оптимальний розмір замовлення, обсяг гарантованого запасу, пороговий рівень запасу, максимально бажаний запасу, кількість постачань ресурсу на рік, за отриманими даними побудувати графік руху запасів у системі управління запасами з фіксованим розміром замовлення.
Розрахунки параметрів системи управління запасами з фіксованим розміром запасу заношу в таблицю 1.10
Таблиця 2.10. Параметри управління запасами
№ п/п | Показник | Порядок розрахунку | Розрахунок | |
Потреба, т | ||||
Оптимальний розмір замовлення, т | Формула Вілсона | 1718,05 | ||
Час постачання, дні | 4,00 | |||
Можлива затримка постачання, дні | 2,00 | |||
Очікуване денне споживання т/день | [1]: [к-ть роб. днів] | 23,81 | ||
Термін витрачання замовлення, дні | [2]: [5] | 72,15=73 | ||
Очікуване споживання за день постачання, т | [3]*[5] | 95,24 | ||
Максимальне споживання за час постачання, т | ([3]+[4])*[5] | 142,86 | ||
Гарантійний запас, т | [8]-[7] | 47,62 | ||
Пороговий рівень запасу, т | [9]+[7] | 142,86 | ||
Максимально бажаний запас, т | [9]+[2] | 590,92 | ||
Термін витрачання запасу до порогового рівня, дні | ([11]-[10]):[5] | 18,82=19 | ||
Кількість постачання на рік | [1]: [2] | 23,28 = 24 | ||
Виходячи з даних, побудуємо графік руху запасів у системі управління запасами з фіксованим розміром запасу.
Висновок: У цьому розділі, для сировинного ресурсу ми визначили оптимальний розмір замовлення — 1718,05 т.; обсяг гарантійного запасу — 47,62 т.; порогів рівень запасу — 142,86 т.; максимально бажаний запас — 590,92 т.; та кількість постачань ресурсів на рік — 24.
Висновок
В даній курсовій роботі мені необхідно було організувати виробництво нової продукції та забезпечити обслуговування потокової лінії. Провівши розрахунки, я дійшла таких висновків:
—- Структура виробничого процесу виявилась раціональною, тому мені не довелося її раціоналізовувати;
—- Перспективний річний обсяг виробництва дорівнює 2000 т.;
—- Планове виробниче завдання потокової лінії дорівнює 27,3 т/зм.;
—- Обладнання використовують не на 100% ефективно, це може бути частково пов’язано з особливостями технологічного процесу;
—- Значення коеф. використаного робочого часу близьке до одиниці і це свідчить про високий рівень використаного робочого часу і рівень організації праці на потоковій лінії;
—- Ремонтні роботи будуть проводитися протягом вересня, жовтня, листопада та грудня. Їх будуть проводити 6 робітників;
—- Оптимальний розмір замовлення — 1718,05 т.; обсяг гарантійного запасу — 47,62 т.; порогів рівень запасу — 142,86 т.; максимально бажаний запас — 590,92 т.; та кількість постачань ресурсів на рік — 24.
Список літературних джерел
1. Богатирьов А. М., Приходько К. П., Савенко І.І. Організація виробництва на підприємствах консервної промисловості. Навчальний посібник. Одеса: «Аспект», 1997, — 200 с.
2. Васильков В. Г. Організація виробництва: Навч. посібник. -К.:КНЕУ, 2003.-524 с.
3. Гибсон Дж.Л., Иванцевич Д. М., Доннелли Д. Х. Организации: поведение, структура, процессы: Пер. с англ…-8-е изд. -М.:ИНФА-М, 2000.-662 с.
4. 3еваков А.М., Пертов В. В. Логистика производственных запасов. Учебник. — СПб.: Изд-во Михайлова В.A. 2002 г.- 320c.
5. Курочкин А. С. Организация производства: Учебн. Пособие. -К: МАУП, 2001,-1216 с.
6. Курочкин А. С. Операционный менеджмент: Учебн. Пособие. -К:
7. Логистика: Учебник / Под ред. Б. А. Аникина, — 3-е изд., перераб. и доп. — М.:ИНФРА-М, 2003. 368 с.
8. Мороз В. С., Тельнова А. С. Організація виробництва (Текст).: учеб. Кишинев.:Картя Молдовеняско, 1984. -387 с.
9. Організація виробництва: Навч. Посіб. / В. О. Онищенко, О.В.Редкін, А.С.Старовірець, В. Я. Чевганова. — К: Лібра, 2005. 336с.
10. Организация производства на предприятиях общественного питания (Текст).: Учеб. пособие. Ростов н/д.: Фенікс, 2000. -320 с
11. Пасічник В.Г., Акіліна О.В. Організація виробництва (Текст).: навч. метод. посіб. К.: Центр навч. л-ри, 2005.-248 с.
12. Петрович П. М., Захарчин Г. М. Організація виробництва: підручник. -Львів: «Магнолія плюс», 2005,-400 с.
13. Практикум по логистике. Учеб. пособие / Под ред. Б. А. Аникина.-М.:ИНФРА-М, 1999.-270с.