Порошковая металургія й властивості металевих порошков
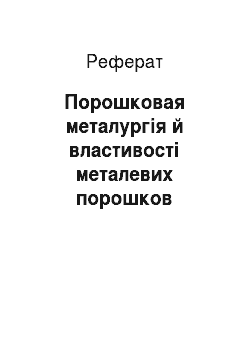
Пластичне руйнація. Граничне стан можна інтерпретувати як стан, попереднє руйнації. Пластична протягом десятиліть і крихке руйнація — називають станом пластичного руйнації. Експериментальне дослідження механічних властивостей пористих стисливих тіл. Схема «зсуву» при достатньої простоті реалізації дозволяє контролювати сумарну величину навантажень, прикладених до тіла, величину переміщень… Читати ще >
Порошковая металургія й властивості металевих порошков (реферат, курсова, диплом, контрольна)
1.Общая характеристика порошкової металургії й поліпшуючи властивості порошков.
Історія розвитку ЛМ у Росії. Основним стимулом зародження і розвитку ЛМ досі була потреба у нових матеріалах, неможливість їх отримання й опрацювання з допомогою традиційних методів. Основи сучасної ЛМ було закладено П. Р. Соболевськ в 1826—1827 гг..в зв’язку із необхідністю переробки порошку платини і відсутність можливостей його переплавлення. У НГТУ з урахуванням робіт, які з середини 60-х рр. була розпочато розробку нового напрями у порошкової металлургии-горячей обробки тиском пористих порошкових заготовок, істотно расширившей можливості цієї прогресивної галузі техніки. Створений університеті науковий заділ і матеріально-технічна база для, наявність висококваліфікованих кадрів, високою ефективністю виконаних робіт і широкі перспективи її подальшого розвитку послужили відкриттям в 1972 р. у складі проблемної науково-дослідної лабораторії динамічного гарячого пресування, довгі роки була країни провідною координуючої організацією у сфері динамічного гарячого пресування. З огляду на інтенсивна розбудова порошкової металургії в Ростовської області та на північному Кавказі, при кафедрі матеріалознавства і технології матеріалів було відкрито спеціальність «» Композиційні і порошкові матеріали, покриття «». Кафедра стала базової з організацією в НГТУ дисертаційного совета.
Основні області застосування ЛМ. Порошкові матеріали використовуються практично у галузі техніки, і обсяг їх застосування безупинно розширюється. Це як із дедалі більшою роллю, що виконують матеріали взагалі, і зі специфічними особливостями, властивими лише порошкове матеріалам. Так, розвиток електронної техніки було практично неможливо без розвитку напівпровідників, те ж сказати, у відношенні космічної техніки, ядерної энергетики.
Спеченные антифрикционные матеріали дозволили підвищити надійність і довговічність вузлів тертя, знизити втрати на тертя, замінити дорогі підшипники качения, на підшипники ковзання чи баббиты і бринзи на железографитовые псевдосплавы. Розробка матеріалів твердими мастилами уможливила їх використання у пристроях, де використання рідких мастил взагалі припустимо, наприклад, у харчової промисловості, при високих температурах.
Пористі порошкові матеріали широко використовують у вузлах тертя, фільтрах, теплових трубах, ущільненнях. Фрикційні порошкові матеріали є, сутнісно, композиційними і складаються з металевих і неметалевих компонентів. Вона має найбільш високі фрикційні властивості і дуже застосовуються. Електротехнічні матеріали — контакти, магнитомягкие і магнитотвердые матеріали, інструменти для электроэрозионной обробки, точкової і роликовой зварювання — знаходять дедалі ширше використання у електротехніці, енерго — і аппаратостроении, автоматиці і телемеханике, радіоелектроніки і інших галузях. Порошкові конструкційні матеріали є поширеної продукцією ЛМ. Потреба них становить близько 60% сумарною потреби у продукції ЛМ. Жароміцні, жаростойкие і композиційні матеріали визначають розвиток галузей сучасної техніки, де без забезпечення спеціальних властивостей неможлива експлуатація машин і агрегатів: авіаційної, ракетної техніки, космонавтики, хімічного машинобудування. Для їх потреб було створено тугоплавкі метали і сплави, тугоплавкі сполуки, одержувані в вона найчастіше лише методами ПМ.
Тугоплавкі і тверді бескислородные з'єднання та матеріали з їхньої основе-карбиды, бориды, нитриды, силициды та інші - знаходять застосування завдяки своїм унікальним властивостями у багатьох галузях промисловості, наприклад инструментальной.
Тверді сплави — найважливіші поширені порошкові матеріали, і при отриманні що у повною мірою реалізуються можливості ЛМ: отримання композиційних матеріалів з компонентів з різко різної температурою плавлення, досягнення унікального комплексу физико — механічних властивостей, безвідходна технологія. Застосовуються тверді сплави в інструментальної промисловості, бурової техніці, при обробці давлением.
Матеріали для сучасної атомної енергетики повинні витримувати экстримальные механічні і термічні навантаження з одночасним впливом фізичних чинників, їх використовують як поглинаючих і які уповільнюють елементів, а як і палива. Певну частина їх становлять порошкові материалы.
Эрозионностойкие матеріали повинні поєднувати різноманітні і незвичні властивості виробів забезпечуватиме їхню продуктивність на вельми важких умовах експлуатації. Прикладом можуть бути турбіни, у найбільш напруженої деталлю є сопловой вкладка, робоча температура на поверхні становить 3500−3600°С.
. Зі збільшенням связности частинок збільшуються видатки формування виробів, але зменшується ймовірність взаємодій матеріалу із зовнішнього середовищем і їхньої витрати з його захист. Порошок, є вихідним матеріалом для ЛМ, цьому плані займає проміжне становище між рідиною твердим тілом, володіючи савокупностью частинок плинністю, а обсязі кожної частки — деформируемостью. Металевим порошком — називається сукупність частинок металу, сплаву чи металлоподобного сполуки розмірами до міліметра, що у контакті і пов’язаних між собою. Лигатурами — називаються допоміжні сплави, застосовувані для жидкотекучести. Частка є індивідуальне тіло з невеликі розміри переважають у всіх трьох вимірах. Найчастіше розміри частинок, які у ЛМ, становлять 10−100 мкм. У зв’язку з цим вони теж мають розвинену поверхню, багато в чому визначальну поведінці при подальшого опрацювання і яка відрізняє його від звичайних матеріалів навіть ідентичної складу. Другий головною особливістю частки є куди більше зміст (відносне) у ній об'ємних дефектів — пір і включений.
Та фізика і хімія поверхні порошків. Поверхня твердого тіла є зоною, де межатомные зв’язку не компенсовані. Сорбція — поглинання речовини із довкілля твердими чи рідкими тілами. Поглинач називають сорбентом, що поглинається речовина — сорбатом. Абсорбція — поглинання сорбата всім обсягом сорбенту. Адсорбцыя — поглинання сорбата поверхнею сорбенту. Хемосорбцыя — поглинання сорбенту із заснуванням хімічних сполук, що супроводжується тепловим ефектом. Стан поверхні розділу між фазами Проте й У і навіть між частинками однієї фази можна охарактеризувати поверховим натягом. ПАР — це речовини, здатні адсорбироваться на поверхнях розділу фаз і знижувати величини. Поверхове натяг характеризує роботу переходу атомів із внутрішньої частини матеріалу на поверхню при освіті одиниці нової поверхні. Поверхнева энергия-избыток енергії поверхневого шару за українсько-словацьким кордоном двох стичних фаз, визначається різним характером межчастичного взаємодії обох фазах. При високої певній температурі й підвищеної дифузійної рухливості атомів площа поверхні може зберегтися, але коли його геометрична форма була неправильна чи порушена, вона змінюється. Збільшення поверхні розділу при подрібнюванні частинок пов’язані з енергетичними витратами, та її зменшення енергетично доцільно і може бути стимулом для перебігу певних процесів, наприклад при спекании або за температурному нагреве.
Мікроструктура поверхні. Ідеалізовані поверхні можна розділити втричі типу: сингулярні, вицинальные і диффузионные. Сингулярні поверхні розділу фаз від диффузионных кількістю атомних молекулярних верств, паралельних поверхні кристала, у яких здійснюється перехід від кристала до пару. Реальні поверхні містять звані поверхневі дефекти, тобто таких порушення у ідеальному розташуванні атомів, які мають велику протяжність у двох напрямах, і незначну — в третьем.
Об'ємні дефекти частинок порошків. Поруч із точковими лінійними і поверхневими, властиво структурі литих металів. Вона має розміри одного ладу у трьох вимірах і кілька порядків перевищують розміри точкових дефектів. До цього виду дефектів литих металів ставляться субмикропоры, є результатом изотропного зростання скупчень вакансій, субмикропузыри, сегрегації тощо. З зменшенням розмірів тіл (частинок) вплив цих факторів зростає, одночасно збільшується інтенсивність взаємодії з довкіллям, яка веде до підвищення газонасыщенности і окисленности металу. Усе це викликає збільшення кількості об'ємних недоліків у порошкових частинках проти литими і обробленими тиском металами. Неметалеві включенняце оксиди основного (заліза) і домішкових элементов. Поры у вихідних частинках можуть бути лише внутрішні, вони дрібні, виникають і при отриманні порошку з допомогою усадки, газообразования, механічного воздействия (трещины) і др.
Хімічні властивості порошків. До хімічним властивостями металевих порошків ставляться їх хімічний склад, газонасыщенность, пирофорность, токсичність, вибухонебезпечність. Щодо хімічного складу оцінюють змістом основних компонентів, домішок чи забруднень і газів. Залежить він від складу вихідних матеріалів і методу отримання порошків. Граничне зміст домішок в порошках визначається їхніми допустимим кількістю в готової продукції. Хімічний аналіз по методикам, прийнятим у загальне аналізу металів. Винятком є лише змісту кисню. Газонасыщенностьриса порошків. Є гази лежить на поверхні частинок (адсорбированные) і їх, потрапляючи в процесі виготовлення й при розкладанні добавок. Ухудшаются умови пресування (крихкість) і спечення (коробления).
Фізичні властивості. До фізичним властивостями порошків ставляться: форма частинок, їх розмір, питома поверхню, щільність, микротвердость. Фракція це сукупність частинок у певному діапазоні розмірів. Гранулометрический складзміст фракцій частинок (%) стосовно загальної кількості. Гранулометрический склад визначають ситовым, седиментационным, микроскопическим та інші методами. Ситовый аналіз проводять механічним поділом навішення порошку 100 г при насипний щільності більш 1,5 г/смі і 50 г при меншому значенні через необхідний набір сит, наявних одне над іншим. Порошок перед рассевом просушують. Частинки мають неправильне геометричну форму, їх взаимоориентировка випадкова, тому розмір до розрахунку призначають у одному якимабо напрямі, незалежно від своїх розташування. Питома поверхню є сумарну поверхню всіх частинок, складових одиницю їх маси чи обсягу. Щільність частки порошка-отношение її маси до займаному обсягу. Микротвердость дозволяє побічно оцінити здатність частинок порошку до деформированию, що не можна зробити, як звичайних матеріалів, по механічним властивостями, оскільки такі не визначаються для дискретних тел.
Адсорбционные методи діляться на статичні і динамічні. У перших виміру роблять за досягненні рівноваги газ — тверде тіло, у — других при невпинному бігові газу. Метод ртутній порометрии зазвичай використовується для виміру Ѕw коли ртуть не змочує досліджуваний порошок. Сутність методу полягає в вдавливании ртуті в пори за певного давлении,.
Технологічні властивості. Це кут природного укосу, насипну щільність, щільність утрясання, плинність, уплотняемость, прессуемость і формируемость. Формируемость порошку переважно залежить від форми, розміру й стану поверхні частинок. Аутогезия залежить від природи частинок, їх розмірів, стану поверхні, параметрів середовища, у якій перебувають. Кут природного укосу? утворюється поверхнею конуса вільно насипаного порошку і горизонтальній площиною у його. Таким чином, кут природного укосу? також і кутом тертя. Насипний обсяг — величина, зворотна насипний щільності. Щільність утрясання? ранків — цей показник порошку обсягу після утрясання його за певної програмі. Плинність порошку, тобто його здатність переміщатися під впливом сили тяжкості, оцінюється часом закінчення (?‚з) навішення 50 г через калиброванное отвір діаметром 2,5 мм. Уплотняемость порошків показує спроможність до зменшення займаного обсягу під впливом тиску, або вібрації. Прессуемость порошку оцінюють її спроможністю утворювати під тиском тіло, має задані розміри, форму і щільність. Формуемость порошку оцінюють його здатністю зберігати додану форму в заданому інтервалі значень пористости. Формуемость порошку переважно залежить від форми, розміру й стану поверхні частинок. Ефекти, які під час дії періодичних сил на дисперсную середу, можна поєднати у наступні группы:
1. Зміна поведінки нелінійних механічних систем: поява нових положень рівноваги і деяких видів руху, зміна характеру положень рівноваги, зміна власних частот малих коливань. 2. Ефекти переміщення і відведення: сепарація частинок матеріалу як, виникнення повільних потоків дисперсних середовищ, дрейф і локалізація частинок в неоднорідних полях періодичних зусиль і взаємні микросмещения. 3. Зміна під впливом періодичних сил реологічних властивостей дисперсних систем: удавані перетворення сухого тертя в в’язке, зниження коефіцієнта сухого тертя, удавані зміни коефіцієнта в’язкості і ще. 4. Виникнення інтенсивного механічного взаємодії між частинками та обсягами багатокомпонентних систем: розпушення дисперсною среды.
2.Метод отримання порошков.
Загальна характеристика методів отримання порошків та його класифікація. Порошкивихідне сировину ЛМє здебільшого матеріалами, зустрічаються у природі у вільному стані, а є вторинний продукт, на властивості якого впливає спосіб виготовлення, тому теоретичні основи їхньої отримання займають важливе місце у процесах ПМ.
Фізичні основи подрібнення матеріалів. Механічним подрібненням можна перетворити на порошок практично будь-який метал чи сплав. Воно широко використовують у ЛМ. Під подрібненням розуміють зменшення початкового розміру твердого тіла шляхом руйнації його передачі під дією зовнішніх зусиль, які переборюють внутрішні сили зчеплення. У час руйнації напруги в деформируемом тілі перевищує деяке граничне значення. Відповідно до теорії роздрібнення, запропонованої П. А. Ребиндером, робота ?ізм, затрачиваемая на здрібнення: у випадку яляется сумою двох енергій: енергії, затрачиваемой освіту нових поверхонь dWs і, расходуемой на деформацію обсягу dW?. При великому роздрібненні величина знову образующейся поверхні невелика.
Практика подрібнення, обробка різанням. Спеціальне отримання стружки чи тирси на подальше виготовлення їх виробів невигідно і тому практично його застосовують дуже рідко. Різання металу — складного процесу взаємодії ріжучого інструменту та заготівлі, що супроводжується поруч фізичних явищ. У срезаемом шарі виникають спочатку пружні, потім пластичні деформації, що призводять до зрушенню і руйнації, тобто скалыванию елементарного обсягу металу з точки? до подання подачі й освіті стружки. Тип стружки залежить від властивостей оброблюваного матеріалу. Після обробітку тендітних металів утворюється елементна стружка (надлому). На тип стружки впливає подача і швидкість різання. При різанні більшості вуглецевих і легованих сталей зі збільшенням швидкості різання стружка з елементної стає суглобної потім зливальний. Відразу після виготовлення деталей можна використовувати лише стружка надлому. Відомі приклади такого використання чавунної стружки. Спеціально для іноземних потреб ЛМ отримують стружку хімічно активних металів. Одержання магнієвого порошку на кратцмашинах царапанием компактного магнію сталевими щетками.
Здрібнення в кульових обертових, вібраційних і планетарних млинах. Здрібнення в кульових обертових млинах то, можливо самостійним способом перетворення матеріалу на порох чи додаткової операцією за інших засобах отримання порошків. У кульової млині матеріал стирається між внутрішньої поверхнею барабана і до зовнішньої - кульового сегмента, між кулями чи дробиться ударами. Здрібнення в кульових вібраційних млинах забезпечує швидке і тонке здрібнення таких матеріалів, як карбиды титану, вольфраму, кремнію, хрому, бору, ванадію. Здрібнення в вихрових млинах застосовується для пластичних металів. Воно відбувається поза рахунок ударних і истирающих зусиль, які виникають за зіткненні безпосередньо измельчаемых частинок. Струменеві млини різняться тим, що енергоносієм у яких є газ чи перегрітий пар що надходить з сопла з надзвуковою швидкістю. Млини забезпечують тонке здрібнення частинок до розмірів 1−5 мкм. Здрібнення в планетарних відцентрових млинах (ПЦМ) забезпечує тонке здрібнення трудноразмалываемых матеріалів ефективніше, ніж у млинах інших типів. У гироскопических млинах барабан обертається одночасно навколо горизонтальній і вертикальної осей, рух куль здійснюється аналогічно ПЦМ.
Здрібнення ультразвуком. Здрібнення ультразвуком роблять у середовищі, де поширюються пружні хвилі, які утворюються при періодичному чергуванні стискування і розрідження цього середовища із частотою понад 16 000 гц У рідкої середовищі виникає кавитация, тобто розриви зза дії на рідина растягивающих зусиль. Диспергирование ведуть у воді, спирті, ацетоні. Генерування ультразвукових коливань здійснюється з використанням магнитострикции й протилежного пьезокварцевого эффекта.
Диспергирование розплавів. Ці методи кваліфікуються за трьома ознаками.? вид енергії, використовуваної до створення розплаву: електрична дуга, плазма, лазерний, індукційний нагрівання.? вид силового на розплав: гравітація, енергія газових і водяних струменів, відцентрові сили, енергія газів і парів, які виділяються з розплаву, механічне, магнитогидродинамическое, ультразвукове.? середовище реалізації процесу плавлення і диспергирования: окислювальна, восстановительная, інертна, реакційна заданого складу, вакуум і другая.
Основи теорії, практика розпорошення — механічні, електричні методи, розпорошення газовим потоком і води. Механічні методи розпорошення — струмінь металу, яка з каліброваного отвори, руйнується обертовим диском. На підвищення ефективності диск то, можливо оснастили спеціальними виступами чи отворами. Основна складність — налипання металу на обертові деталі. Струмінь металу з плавильного агрегату потрапляє у обертався тигель з отворами в бічних стінах. Для отримання гранул однакового розміру розміри отворів збільшуються по мері видалення від дна тигля. Швидкість забезпечення високу швидкість, яка потрібна на розпорошення (до 18 000 хв? №), стримує застосування методу. Розпилення розплаву і гарт (кристалізація і придбання форми частинками) відбуваються у момент удару про водоохолоджувальну поліровану поверхню екрана, що забезпечує швидкість охолодження частинок. Високошвидкісне затвердіння з розплаву. Обертовим мідним диском беруться (экстрагируются) обмежені обсяги металу і практично миттєво затвердевают. Залежно від форми крайки диска можна одержувати частки лускатої, голчастою форми, волокна і др.
Електричні методи Электроимпульсный метод залежить від вплив електричного імпульсного струму на струмінь пульпи чи розплаву. Нагромаджувач енергії - конденсатор — заряджається джерела постійного чи змінного струму. За певного величині заряду пробивається проміжок, і весь нагромаджена під час? енергія виділиться під час ?0 у робочому проміжку і елементах ланцюга разрядного контуру. Электродуговое розпорошення здійснюється так. Пруток металу, що підлягає розпорошення, служить катодом. Анод виконується як водоохлаждаемого пологого циліндра. Використовуються також плазмові пальники з незалежної чи залежною дугою, коли анодом служить распиливаемый материал.
Розпилення газовим потоком. У інженерному відношенні можливо здійснення з трьох основних схем руйнації струменя: соосным потоком газу, потоком з точки, поперечним потоком. При розпорошення струменя розплаву можна виділити три структурні зони: не распавшуюся суцільну частина струменя; зону поділу струменя деякі волокна, пасма, нитки, краплі; зону формування частинок, інтенсивного перебігу теплообмінного та інших процессов.
Розпорошення рідинами. Висока щільність енергоносія, інтенсивне охолодження крапель розплаву, освіту значної кількості пара в зоні безпосереднього контакту рідини з расплавом. Як распыляющей рідини використовується вода чи олію. Распыляющий вузол форсунки має забезпечити зокрема можливість використання максимальної сили удару водяний струменя, пов’язане з довжиною її початкового ділянки, величина визначається вихідним діаметром насадки, тиском води перед насадкою мірою поджатия струи.
Технологія отримання порошків розпиленням розплавів. Водою можна розпорошувати низько — і высоколегированные сплави розпиленням отримують порошки быстрорежущих сталей. Одержання порошків титану, а його сплавів з низьким змістом кисню та азоту ввозяться основному відцентровим розпиленням в аргоні, гелії чи вакуумі. Одержання порошків алюмінію і магнію. Розпилення повітрям, азотом, інертними газами використовують инжекционные форсунки, у яких метал надходить з допомогою розрядження виникає у виходу з сопла при закінченні газу з кільцевої щілини під тиском 0,4 — 0,6 Мпа.
Физико-химические методи отримання металевих порошків. Сполуки галогениды металів, котрі реабілітуються або воднем, або активними металами (натрій і магній). Механізм відновлення більшості твердих сполук газоподібними восстановителями полягає в адсорбционно — автокаталитической теории.
Відновники, використовувані за відновлення порошків. Восстановителями служать гази (водень, оксид вуглецю, диссоциированный аміак, природний найконвертованіший, водяний, коксовий чи доменний гази, эндогаз), твердий вуглець (кокс, деревне вугілля, сажа) і метали. Вибір відновлювача залежить тільки від термодинамічних оцінок, а й від летючості, що має бути мінімальної, бо інакше процес потрібно вести при підвищеному тиску з допомогою аргону чи інших інертних газов.
Залізний порошок — основа многотоннажной ЛМ. Існують методи отримання порошків з FeCl2. Відновлений воднем залізний порошок має високий чистоту і вартість. Відновлення оксидом вуглецю проводиться при високих температурах вище 1000 єС з урахуванням адсорбционно — каталітичного механізму. Відновлення твердим вуглецем відбувається за 900−1000єС.
Содовий метод застосовується щоб одержати порошку підвищеної чистоти. У шихту додають 10 — 20% соди з якою за відновлення взаємодіють домішки, створюючи розчинні у питній воді натрієві алюминаты.
Металлотермия. Відновлення діоксиду титану кальцием.
Комбінований процес включає у собі відновлення на магній, а після відмивання — кальцієм, витрата якого знижується вдвічі. Відновлення гидридом кальцію отримують порошок титану, а його гідриду. Відновлення хлориду титану натрієм. Хлорид титану отримують хлоруванням концентрату руд, очищенням і фракційної дистиляцією. Відновлення хлориду титану на магній найбільш економічний спосіб. Реакція відбувається за 800 — 900єC. Сталевий герметичний апарат заповнюють злитками магнію, відкачують повітря, заповнюють аргоном, виплавляють магній, згори подають лімітовану кількість хлориду титану, щоб уникнути перегрева.
Відновлення з розчинів, газоподібних сполук й у плазмі. З розчинів сполук? й, Cu, Co метали витісняють воднем в автоклавах. Зрушувати потенціал водню в негативний бік можна, підвищуючи pH чи збільшуючи тиск водню. Ощадливіше змінювати pH, підвищення якого на одиницю еквівалентно зміни тиску водню в 100 раз. Термічні розрахунки доводять, зазначені меаллы можна осадити вже за часів 25єC і 0,1Мпа. Відновлення газоподібних сполук воднем ввозяться киплячому шарі з галогенидов вольфраму, ренію, молібдену, ніобію і титану. Одержання високодисперсних порошків в плазмі перспективне для металів, карбідів, нитридов та інших. Відновники — водень чи продукти плазмової конверсії з високої температурою і окислювачів. Оксид нікелю відновлюють в струмені Ar — H2 чи Ar — CO, причому зміст водню близько до стехиометрическому, а теплообмін і плазмообразование відбуваються з допомогою аргону. Реакція лімітується дисоціацією NiO, повне її відновлення характеризується 7000єC.
Физико — хімічні основи отримання порошків електроліз. Процес є своєрідне відновлення: передача електронів до металу з одночасної перебудовою структури відбувається з допомогою відновлювачів, а й за рахунок електрической енергії. Спосіб універсальний, забезпечує високу чистоту порошків. Електроліз — одне із найбільш складних физико — хімічних процесів виробництва порошків. Процес залежить від розкладанні водних розчинів сполук який виділяється матеріалу. Наявність хлору чи фтору на аноді змушує вживати заходів профілактики його взаємодії з електролітом і порошком. Електроліт від порошків відокремлюється відгоном нагріванням чи центрифугированием і відмиванням. Електроліз водних розчинів. Спосіб щоб одержати порошків міді, срібла, заліза, нікелю, кобальту, олова та інших. Нікель, цинк, кобальт утворюють рівномірні щільні дрібнозернисті опади незалежно від природи електроліту. Срібло чи кадмій зростають у вигляді окремо сильно разветвляющихся кристалів при електролізі простих солей, з розчину ціанистих солей вирізняються як рівного рівного слоя.
Одержання мідного, нікелевого, залізного порошку. Мідний порошок отримують з розчину сернокислой міді, вона має високу чистоту і регульовану дисперсність. Нікелевий порошок отримують элетролизом аміачних розчинів хлорно — кислого нікелю. Особливості отримання залізного порошку пов’язані про те, що у ряду напруг залізо залізо розташовується лівіше водню, тому останній виділяється разом із воднем, погіршуючи вихід по току і забезпечення якості порошка.
Одержання порошку танталу суміш фторида і хлориду калію покращує легкоплавкость, жидкотекучесть і електропровідність електроліту. Одержання порошку титану розчинну анод виконують з сбрикетированных титаносодержащих матеріалів. Одержання порошку цирконію. На його отримання необхідно використовувати фтороцирконат калію і хлористий калій високого якості, проводити процес серед чистого аргону. Одержання заліза элктролизом хлоридных розплавів забезпечує отримання порошку дуже високою чистоти. Одержання порошків методами термодиффузионного насичення, випаровування — конденсації. Метод застосовується щоб одержати сталей і сплавів, легованих елементами, оксиди яких трудновосстановимы. Одержання порошків містять три і більше металевих компонентів, можна робити спільним відновленням суміші оксидів з наступним насиченням трудновосстановимыми компонентами з точкових джерел. Перенесення здійснюється через газову фазу як хлоридів, иодидов чи бромидов, які виникають під час нагріву при взаємодії металів з продуктами розкладання галоидных солей амонію. Випари — конденсація. Сутність методу залежить від перекладі металу у парообразное стан і наступного конденсації парів на поверхнях, температура котрих значно менша точки плавлення осаждаемого металла.
Корозія металів — їх зруйнування вследствии хімічного чи електрохімічного взаємодії із зовнішнього середовищем. Одержання порошків металлоподобных сполук методами прямого синтезу з елементів, відновлення, високотемпературного синтезу. Металлоподобные сполуки мають, зазвичай, високу твердість і температуру плавлення, мають складної зв’язком, у якій поєднуються металева, іонна і ковалентная складові. Для отримання порошків застосовують прямий синтез з елементів, відбудовні процеси, електроліз розплавлених і метод самораспростроняющегося високотемпературного синтезу (СВС). Відбудовні процеси використовують із отримання карбідів, боридов, нитридов і силіцидів шляхом відновлення оксидів вуглецем чи углесодержащим газом.
3. Формування порошкових материалов.
Поняття формование. Формование (надання порошкової масі певної форми) металевого порошку є технологічну операцію, у яких металевий порошок утворює порошковую формовку, тобто тіло із заданою формою, розмірами і плотностью.
Елементи механіки і реологии деформируемого тіла. Елементи механіки і реологии деформируемого тіла можливість феноменологічного описи багатьох закономірностей пресування і спечення, але важливим є і мікроскопічний підхід до цих процесам, заснований на концепціях твердого тіла. Загальні інформацію про механізмах процесу массопереноса. Зміна щільності при пресуванні і спекании зумовлено багатьма процесами, різними по своїй — природі: взаємним ковзанням елементів структури щодо друг друга, пластичної деформацією, в’язким течією, диффузионными явищами. Більшість цих процесів має термоактивационный характер, а пластична деформація, ще, і граничний. Переважним механізмом дифузії твердих тілах вважається вакансионный, і енергія активації представляється що з доданків, залежать від параметрів освіти і рух вакансій. У процесах спечення і гарячого пресування є протягом речовини — повзучість. При нагріванні грузького тіла, зокрема і порошкового, відбуваються і рекрестализационные процеси, пов’язані переходити мкроструктуры на більш стабільне состояние.
Основи процесу ущільнення порошкоподібних матеріалів. Аналізований клас матеріалів, як і всі тверді тіла, залежно та умовами навантаження і деформації може виявляти пружні, пластичні і грузлі властивості. Пластичне руйнація виникає у тілі під час досягнення у ньому граничного стану. Пластична деформація тіл, супроводжується їх тендітним руйнацією, може бути розглянута як процес, лежить у основі механізму ущільнення порошкового матеріалу. Отже, можна укласти, що кінетика процесу ущільнення повністю визначається умовами пластичної деформації стисливого пористого тіла, механічні властивості якого залежить від технологічних властивостей вихідного порошкового матеріалу та її щільності в певний момент времени.
Пластичне руйнація. Граничне стан можна інтерпретувати як стан, попереднє руйнації. Пластична протягом десятиліть і крихке руйнація — називають станом пластичного руйнації. Експериментальне дослідження механічних властивостей пористих стисливих тіл. Схема «зсуву» при достатньої простоті реалізації дозволяє контролювати сумарну величину навантажень, прикладених до тіла, величину переміщень сдвигаемых обсягів брикетів у двох взаємно перпендикулярних напрямах. Установки трехосного навантаження, попри наявність деякого розподілу за обсягом тіла, дають точніші значення напруг. Мета експерименту полягало у визначенні величин стискають і сдвигающих зусиль, поєднання яких призводить до пластичному руйнації зразка і виявлення умов переходу деформації тендітного руйнації в розвинене пластичне протягом матеріалу, коли повинна мати місце відповідна зрушенню деформація стискування матеріалу і підвищення його щільності. Без пластичної деформації матеріалу неможливо його ущільнення; Розвиток в стисливому тілі пластичних деформацій потребує певного поєднання дотичних і стисливих напруг на поверхнях ковзання. Збільшення щільності пористої середовища як залежить від величини стискають навантажень та його зміни, а є функцією отриманої тілом пластичної деформації. Пресування є формование металевого порошку в прес — формі під впливом тиску. При насыпании порошку до форми поверхневі шари частинок сприймають контактну навантаження. Енергія пресування витрачається подолання тертя між частинками, зовнішнього тертя і деформування частинок. Усі види пресування мають власний механізм ущільнення, підпорядковуються різним закономірностям, але всім них однією з важливих питань є з’ясування залежності щільності порошкового тіла тиску. Складність фізичних процесів, можна побачити протягом ущільнення порошкових матеріалів закритих прес — формах, не дозволила досі побудувати загальну физико — математичну теорію пресування. Тому досі немає аналітичного висловлювання, який би універсальним для пресування різних матеріалів і широкого інтервалу тисків. Спільним недоліком майже всіх рівнянь пресування і те, що де вони враховуються реальної граничной щільності, досяжною у цьому порошку. У НГТУ використаний енергетичний підхід до проблеми ущільнення пористого тіла при динамічному і статичному гарячому прессовании.
Бічне тиск при пресуванні. При додатку тиску деформація порошкової маси може статися з допомогою нормальної деформації контактів частинок та його відносного зсуву. При збільшенні тиску пресування відбувається зростання майданчиків взаємних контактів. Важливою характеристикою пресування є коефіцієнт бічного тиску ?, що становить собою ставлення бічного тиску до тиску пресування? і здатні якісно що характеризує пластичність уплотняемого материала.
Розподіл щільності в спресованих брикетах. Зовнішнє тертя прессуемого порошку про стінки прес — форми визначає зусилля, необхідне для виштовхування брикта саме його пресування і зване тиском виштовхування. Тиск виштовхування завжди менше втрат тиску тертя порошку про стінки прес — форми, що пов’язана зі зміною обсягу спресованого брикета після зняття тиску. Розрив контактів між частинками з великої протязі може викликати руйнація цілісності прессовок, зване расслоем.
Структурні проблеми при пресуванні. Структурні проблеми в брикетах при пресуванні визначаються двома групами чинників: зменшенням приросту і перетвореннями у структурі матеріалу частинок. Можна припустити що пресування зрештою здійснюється з допомогою зниження загального запасу енергії порошкової системи. У традиційних поняттях все властивості порошкових матеріалів є функцією контактного перерізу, а площа цього перерізу визначається значенням нормального щодо нього стискає напряжения.
4.Спекание порошкових материалов.
Визначення спечення. Збирання порошків є третьою способом отримання полікристалічних тіл самої різної хімічної природи: металів та їхніх з'єднань, оксидів, ковалентних кристалів. Збирання є нагрівання і витримка порошкової формовки за нормальної температури нижче точки плавлення основного компонента з метою забезпечення заданих механічних і физико-химических свойств.
Властивості твердих тіл і зв’язок його з дисперсностью. Під час вивчення механізму і кінетики процесів, які у спекающемся пористом тілі, необхідно пам’ятати особливості фазового рівноваги, оскільки «фаза речовини «і «фаза порожнечі «мають такі розміри, коли ефекти, зумовлені искривленностью кордони між сосуществующими фазами, може стати значними. Основною причиною відмінності властивостей дисперсних і макроскопічних об'єктів є підвищена кривизна поверхонь перших, яка веде до появи тисків за українсько-словацьким кордоном розділу твердих дисперсних фаз, розбіжності тисків парів металів над поверхнями з різною кривизною і відповідних плотностей вакансий.
Непороговая і порогова повзучість. Агломерація пористого тіла супроводжується ползучестью речовини. За інших рівних умов кінетика ущільнення залежить від механізму повзучості, т. е. здібності матеріалу повільно й безупинно деформуватися під впливом постійної навантаження. При температурі досить високої щоб термічно активируемое диффузионное переміщення атомів мало належної швидкістю, слід розрізняти непороговые механізми, які можуть опинитися визначати деформування при малих напругах ?, і порогові, виявляються при напругах, переважаючих деяке граничне значення ?*. Спільним ознакою всіх механізмів непороговой повзучості (НП) є спрямовані потік вакансій під впливом різниці їх хімічного потенціалу. Розмір порогового напруги ?* визначається конкретними механізмами гальмування, розмноження і рух дислокаций.
Геометрія контактної області. Суворе розгляд завдання про геометрії контактної області навіть у найпростіших випадках контакту між двома сферами і сферою і площиною пов’язане з великими труднощами в в зв’язку зі необхідністю обліку перерозподілу речовини. Геометрична активність у певному просторовому розподілі вакансій в контактної зоні, залежить від початкового сплющивания при пресуванні, при спекании зменшується й переважно радіусом кривизни поверхні контакта.
Рушійні сили спечення термодинамическая доцільність перенесення речовини у сфері контактного перешийка обумовлена зменшенням загальної поверхні і є поверхневою енергії системи. Тиск пара над вигнутій поверхнею можна визначити з допомогою рівняння Лапласа. Друга сила пов’язані з наявністю залежності між концентрацією вакансій і кривизною. Поблизу ізольованій пори концентрація вакансій вище рівноважної зростає із зменшенням пір. Концентрація вакансій в решітці поблизу межзерных кордонів, які перебувають під напругою? , відрізняється від равновесной.
Непороговые механізми формування контакту при припекании однойменних твердих тіл. У обдасти високих температур, коли диффузионная рухливість атомів і пружність парів велика, преобладабт термоактивируемые процеси. При спекании центри частинок можуть залишатися дома чи зближуватися. Зближення центрів при перенесення маси непороговыми механізмами зокрема у разі, якщо стік атомів лежить у обсязі частинок, а чи не з їхньої поверхні. Механізм грузького течії є у разі аморфних тіл. Коефіцієнт в’язкості, визначальний швидкості цього процесу, з коефіцієнтом об'ємної самодиффузии. Вследствии спрямованого переміщення атомів з обсягу частинок до контактному перешийка збільшується площа контакту і зближуються центри. Процес відбувається під впливом поверхового натяжения.
Інтеграція реальних частинок. Релаксація напруги вздовж контактної поверхні може статися з допомогою повороту частки, у якому зменшується межфазная енергія. Рушійна сила цього процесу залежить від кута дезорієнтації між гратами контактуючих частинок. Поворот частки передбачає не зміна обсягу речовини в контактної зоні, яке перерозподіл, що може здійснюватися диффузионным і дислокационным механізмами. При дислокационном механізмі взаємне розштовхування гвинтових дислокаций, що у граничной площині, приводить до зменшення їх щільності і повороту частки. У реальних випадках типовими може бути контакти між частинками довільній форми: конічними голками, вершиною двугранного кута і площиною, голкою і площиною. Справжня структура контакту визначається геометрією елементів шорсткості, що з локальної кривизною елементів поверхні перешейки.
Порогові механізми формування контакту при припекании однойменних твердих тіл. Напруга у зоні контакту між частинками чи часткою і площиною перебувають у сложнонапряженном стані, що визначається як зовнішньої стосовно частинкам силою P прижимающих, і силою капілярного тиску Pk, обумовлений тенденцією до зменшення вільної поверхневою енергії частинок. Наочним свідченням пластичності у зоні контакту є освіту скупчень дислокаций, котре купує у разі правильної геометрії контакту симетричні обриси — «розетки спечення «.
Електричні ефекти у зоні контакту. При формуванні контакту в режимі імпульсного пропускання струму проявляється два ефекту: енерговиділення і підвищення дислокаций «електронним вітром «. Дислокационный механізм формування контакту реальний для металів, які мають високої температуропроводностью.
Ефекти самоидентирования і самопрессования. У процесі формування контакту під впливом Pk здійснюється пружне і пластичне деформування. Пластичність може виявляти себе у пластичному деформировании. Для прояви ефекту самоидентирования контактують повинен бути досягнуть рівень напруг, які його смятие.
Припекание різнорідних тіл. Процес складніше, аніж за припекании однорідних тіл, оскільки проходить додаткове вирівнювання концентрації. Можлива об'ємна, поверхнева дифузія і дифузія через газову фазу. Зароджується розвивається диффузионная пористість. Граничні випадки: повна нерозчинність і необмежена розчинність, коли ускладнення, пов’язані з формуванням фаз в дифузійної зоні, не рассматриваются.
Взаємно розчинні і нерозчинні тіла. Повна взаємна нерозчинність реалізується у разі великий різниці в температурах і дифузійної рухливості атомів. Форма тугоплавкой частки не изменяется.
Гомогенізація напруг і вакансій. Оцінка показує, що гомогенне зародження життєздатного зародка пори передбачає флуктуационное об'єднання N вакансій. При більшому тому числі ймовірність такого такого події зникаюча мала, тому зародки може лише тріщини і микрополости. Завдання дифузійної гомогенізації в сферичних зразках можна розв’язувати стосовно двом граничним умовам: за наявності джерела кінцевої чи безкінечною мощностью.
Джерело безкінечною потужності. Усього сорти А, диффундируя по поверхні частинок B, методично їх обволікати, покриваючи шаром, з яких відбувається потік На B. Так потужність потоку убуває, настане час, починаючи від якого шар На поверхні B стане досить товстим, щоб бути фазою і, отже, джерелом безкінечною мощности.
Джерело кінцевої потужності зосереджений в шарі завтовшки h < < R з концентрацією C0 на сфері. Згодом отжига концентрація в шарі убуває. Після закінчення гомогенізації у сфері утворюється однорідний розчин з концентрацией.
Припекание взаємно розчинних тіл. При припекании однойменних речовин двигуном процесу є градієнт термодинамічної потенціалу, обумовлений градієнтом концентрації вакансій, що виникає на вигнутих поверхнях. У процесі припекания частинок з однорідних сплавів збагачення однією з компонентів може статися з допомогою механізму поверхневою дифузії чи механізму перенесення речовини через газову фазу внаслідок різних парциальных тисків пружності парів компонентов.
Роль рідкої та газовій вази при спекании. Рідка фаза може з’являтися або за температурі плавлення легкоплавкого компонента або за більш низької температури внаслідок контактного плавлення. Якщо обсяг легкоплавкого компонента малий, в контактної області між однойменними тугоплавкими частинками з’являється прошарок розплаву, у якій частково чи цілком розчиняється тугоплавкое вещество.
Роль газової фази у процесі припекании різнорідних металів велика, якщо велика пружність парів однієї з металів. Ефект перенесення через газову фазу аналогічний що спостерігається при поверхневою диффузии.
Характеристики ізольованій пори в твердому тілі. Форма пори залежить від стану, у якому вона. Рівноважний — коли час заповнена нерастворимым в речовині матриці газом, що під тиском, рівним поверхневому тиску. Розподіл напруг навколо ізольованій пори та його величина визначають і механізм, і кінетику перенесення маси, супутнього залечиванию пори. Розподіл вакансій навколо ізольованій сферичної пори в кристалі зумовлено нескомпенсированностью тисків — лапласовского зовнішнього й газового. Воно неоднорідне, що викликає поява диффузионного потоку, змінює обсяг поры.
Непороговые механізми залечивания ізольованій пори. Процес залечивания завжди супроводжується зниженням енергії системи, зумовленої або наявністю пори, або дією зовнішніх сил. Процес залечивания ізольованій пори в однорідної ізотропного середовищі розглядається під впливом лапласовского і докладеної ззовні тисків, явно недостатніх для емісії дислокационных петель з його обсягу. Деформація відбувається за малих напругах, і його швидкість пропорційна першої їх ступеня напруг. При непороговом залечивании важливі диффузионные потоки в обсязі матриці. Потоки поверхневою дифузії вздовж поверхні пори можуть лише змінити її форму, не змінюючи обсягу. Якщо час огранена атомно — гладенькими поверхнями, залечивание ускладнюється. Осідання атомів ними може бути «пороговою «. У цьому вся разі випаровування вакансій може початися вже з трехграничной вершини пори, при цьому освіту зародка не предпологается, і механізм стає непороговым.
Порогові механізми залечивания ізольованій пори. Кінетика процесу залечивания пори пороговыми механізмами то, можливо описана як у межах феноменологічного підходу, не який передбачає використання конкретних модельних поглядів на механізмі перенесення маси, і з допомогою поглядів на дислокационных механізмах массопереноса. При граничних механізмах поставки речовини в залечивающуюся пору структура матриці навколо неї може відчувати істотні зміни, що, своєю чергою, може спотворити і механізм, і кінетику її залечивания.
Ансамбль пір у реальному кристалічному тілі. У ансабле сферичних пір зменшення вільної поверхневою енергії може бути реалізований у двох процесах: залечивание пір (зовнішнє агломерація) і коалесценция, коли пикнометрическая щільність незмінна (внутрішнє збирання). Локальні напруги в ансабле частинок, спотворюють їх вихідну локалізацію, можуть виникнути внаслідок розбіжності у розмірах і втрачає, отже, величин усадки відповідних контактах. Істотних змін щодо в геометрії ансамблю може викликати частковими перекриттями полів напруг у області близько розташованих контактів. Існуюча особливість усадки на контакт у тому, що агломерація просторових ланцюгів (ниток) залежить від цього, виявляється ця нитку закріпленої з однієї чи двох концов.
Активований збирання — це збирання порошкової формовки при вплив хімічних і фізичних чинників, викликають інтенсифікацію спечення. Активність порошків неспроможна визначатися термічно нестабільними спотвореннями, снимающимися при низьких температурах (надлишкова енергія, усунення атомів зі стану рівноваги, микронапряжения, локализующиеся не більше блоків, фрагментів). У процесі механічного подрібнення, поряд зі збільшенням поверхні, можна цілеспрямовано змінювати форму, шорсткість і пористість порошків. Кількість дислокаций, які можуть опинитися адсорбировать вакансії, збільшується не пропорційно збільшення щільності дислокаций. При деформационном упрочнении знижується прессуемость. Термічна активація і більше термін перебування у області температур інтенсивного спечення зумовлюють сильнішу усадку на початку процесу зі збільшенням температури або зменшення швидкості нагрева.
Фізичні методи — опромінення (нейтронне, ультразвукове), кристалографічні перетворення, високі тиску. Опромінення може активізувати порошок, створюючи надлишкові точкові дефекти, і навіть активувати процес, викликаючи генерування точкових дефектів і несталі стану кордонів. Зі збільшенням тиску коефіцієнт дифузії знижується. До хімічним методам активирования порошків можна віднести всі засоби, щоб забезпечити отримання дисперсних частинок, наприклад осадження з розчинів, відновлення сумішей солей, выпаренных з розчинів, синтез в плазмі, синтез нестехиометрических сполук, а до хімічним методам активирования процесу спечення — легування металами та сполуками, вплив газових середовищ, сублімацію. Розрізняють три виду спечення: з високої швидкістю усадки, перемінної малой.
Сверхпластичность пористої структури. Сверхпластичность здатність матеріалу до великим рівномірним пластичним деформаціям без порушення внутрішньої сплошности, з’являється при високих гомологічних температурах під впливом низьких, сильно залежать від швидкості деформації напряжений.
Вплив технологічних чинників на збирання. Температура інтеграція — основний чинник, і залежно від нього процес спечення формовок з однокомпонентных порошків можна розділити втричі етапу. Ультрадисперсные порошки внутрішнє збирання їм може супроводжуватися появою монокристала, розміри якого значно переважають розміри частки. Механічне легування — освіту суперсплава якщо спільному змішуванні і механічному подрібнюванні його компонентов.