Технология відновлення чавунних колінчастих валів двигунів ЗМЗ-53А
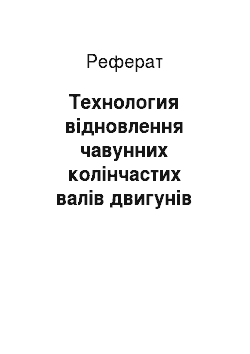
Найменування операції, переходу |Устаткування, — |Пер| |інструмент — |єхо| — | |так — | — | |5 Контроль — | |1 |Встановити колінчатий вал першою і п’ятої |Контрольна — | |корінними шейками на призми |плита — |2 |Перевірити биття третьої корінний шийки і |Призми, — | |при плині більш 0,2 мм фарбувати червоною |індикатор, — | |фарбою; такий вал підлягає виправленню на прессе|краска, пензель — |3… Читати ще >
Технология відновлення чавунних колінчастих валів двигунів ЗМЗ-53А (реферат, курсова, диплом, контрольна)
смотреть на реферати схожі на «Технологія відновлення чавунних колінчастих валів двигунів ЗМЗ-53А «.
У сучасному машинобудуванні застосовуються різні конструкційні матеріали. Але й до нашого часу чавун одна із основних конструкційних матеріалів. Наприклад, вагу чавунних виливків становить до 50% ваги машин. Це зумовлюється простотою і відносній дешевизною виготовлення чавунних деталей, хорошими ливарними властивостями чавуну, його високої зносостійкості, малої чутливістю до концентраторам напруг, здатністю гасити вібрацію тощо. д.
Однією з актуальних завдань завдань, які організаціями, експлуатують автомобільну і автотракторну техніку, є продовження терміну служби відпрацьованих деталей, зокрема і чавунних. Зварювання і наплавлення чавуну широко застосовується ремонту виведеного з ладу різного устаткування. Але вона пов’язане зі значними труднощами. Це з тим, що метал шва і околошовной зони дуже схильний до освіті твердих непластичных структур (ледебуриту, мартенситу) і тріщин внаслідок великих швидкостей охолодження під час зварювання і наплавленні, низькою міцності чавуну і майже повної відсутності пластичності. Це ускладнює рішення багатьох питань, пов’язаних із розробкою зварювальних матеріалів (електродів, дроту, флюсів та ін.) для зварювання чугуна.
Горьковський автомобільний завод широко застосовує в двигунах своїх автомобілів деталі з чавуну. Однією є колінчатий вал.
Метою дипломного проекту є розробка технологічного процесу відновлення чавунних колінчастих валів двигуна ЗМЗ — 53А що дозволяє уникнути названих вище недоліків із можливістю застосування у невеликих ремонтних підрозділах МШС РФ.
Велику роботу з вивчення процесів, що протікають під час зварювання і наплавленні чавуну, провели дослідники: Доценка Р. М., Доценка М. І., Луппиан Р. Еге. та інших. Роботи цих дослідників використані дипломному проекте.
1. Літературний огляд та обґрунтування теми дипломного проекта.
1. Опис вироби і технічні умови на: ремонт чавунного колінчатого вала.
Чавунні колінчасті вали в автомобільних двигунах почали застосовувати з 1960 року [3]. Высокопрочные чавуни по ГОСТ 7293–85 діляться на два класу: перлитные (ВЧ 45−0; ВЧ 50−1,5; ВЧ60−2) і ферритные (ВЧ 40−0; ВЧ 40−6). Велике застосування знайшли чавуни перлитного класу завдяки високої міці й износостойкости.
Чавунний колінчатий вал двигуна ЗМЗ-53А.
Рис. 1.1.
У табл. 1.1 наведено дані про прочностных властивості високоміцного, сірого, модифікованого, ковкого чавунів і вони 45 [1].
[pic].
З табл. 1.1. видно, основні механічні властивості перлитного високоміцного чавуну приблизно такі самі, як і в стали 45 і вище, ніж в інших чавунів. У цьому собівартість виливків з високоміцного чавуну в 2−2,5 рази менше проти собівартістю виливків з ковкого чавуну і поковок стали 45 [3].
Усталостная прочность.
Застосування високоміцного чавуну замість стали 45, виготовлення колінчастих валів став можливим завдяки його високої усталостной міцності. Співвідношення по усталостной міцності для сталевих і чавунних зразків гладких і колінчастих валів однаковою форми представлені у табл. 1.2 [2].
[pic].
За даними табл. 1.2. у зразків гладких валів, виготовлених із високоміцного чавуну, межа усталостной міцності на 18% менше, ніж в зразків виготовлених із стали 45; у колінчастих валів, виготовлених із тієї ж металів, ця різниця дорівнює лише чотири%. Пояснюється це тим, що усталостные тріщини викликають руйнації чавунних колінчастих валів, творяться у місцях концентрації напруг на галтелях, а високо-випробувальний чавун зберігає притаманну всім чавунів малу чутливість до концентрації напряжений.
Износостойкость.
Високу зносостійкість високоміцного чавуну з перлитной основою, не поступається за обсягом загартованою стали 45, більшість дослідників [4] пояснюють наявністю з його поверхні розкритих графітових включень, які є змазкою, а звільнені порожнини є накопичувачами додаткової мастила, необхідної під час пуску і зупинці двигателя.
При порівнянні сталевих і чавунних колінчастих валів в опублікованих роботах [5,7] вказується, що з твердості сталевих шийок HRC 56 їх зносостійкість дорівнює зносостійкості шийок чавунного колінчатого валу, при твердості шийок менш HRC 56 — менший прибуток і при твердості більш HRC 56 — більше зносостійкості шийок чавунного колінчатого вала.
Технічні умови на ремонт.
1. У колінчастих валів, вступників на складання, масляні канали і грязеуловители повинні бути старанно очищені від шлама.
2. Шатунные шийки повинен мати діаметр — 60,00−0,013 мм.
Корінні - 70,00−0,013 мм.
3. Овальність і конусность шийок колінчатого валу нічого не винні превышать.
0,01 мм.
4. Чистота поверхні шийок має відповідати 5 квалитету Ra 0,2;
0,4.
5. Довжина передній корінний шийки маєш бути у межах 30,45−30,90 мм.
Довжина шатунной шийки 52,0−52,2 мм.
6. Радіуси галтелей шатунных шийок повинні прагнути бути не більше 1,2−2,0 мм, корінних 1,2−2,5 мм.
7. При обертанні валу, встановленого в призми на крайні корінні шийки, биття на повинен перевищувати: а середньої корінний шийки — 0,02 мм. б) для шийки під розподільну шестірню — 0,03 мм. в) для шийки під маточину шкива вентилятора — 0,04 мм. р) для шийки під задній сальник — 0,04 мм. буд) фланца по торця — 0,04 мм.
8. Не паралельність осей шатунных і корінних шийок — трохи більше 0,012 мм на довжині кожної шейки.
2. Дефекти і несправності чавунного колінчатого вала.
Колінчатий вал є высоконагруженной деталлю двигуна. У процесі експлуатації двигун машини піддається різним навантажень, у цьому однині і несприятливим, це пуск двигуна по холодних умовах, не якісне мастильне олію, робота у запилених умовах тощо. д.
У результаті зазначених чинників труться колінчатого валу піддаються підвищеному зносу, що у своє чергу призводить до появи на цих поверхнях надиров, відколів, мікротріщин, раковин показаних на Рис. 1.2., які можуть призвести до поломки колінчатого валу і з експлуатації всього двигателя.
Дефекти чавунного колінчатого вала.
Рис. 1.2.
3. Сучасні технології відновлення чавунних колінчастих валов.
Нині чавунні колінчаті вали використовують у двигунах автомобілів горьковського автомобільного заводу, марки автомобілів ГАЗ-53А, ГАЗ-66, «Волга», «Газель». У деяких автохозяйствах парк цих машин становить до 80% від кількості машин. Перебудова народного господарства і структурні зміни у нашій країні сприяли разукрупнению автогосподарств, появі дрібних парків машин зі змішаною формою власності. Однією із завдань, вставшей перед цими автохозяйствами, стає підтримку машин робочому стані за обмежених фінансових ресурсів годі. У цій відновлення зношених деталей є нині актуальною задачей.
Є кілька технологій відновлення чавунних колінчастих валів [3]:
1. Шліфування під ремонтні размеры.
Одне з часто застосовуваних засобів відновлення працездатності колінчастих валів. Переваги цього способу у його технологічної простоті. З обладнання потрібно наявність кругло шлифовального верстати й типовий оснастки щодо нього. Але в цієї способу є і кілька недоліків. Втрата взаємозамінності деталей, потреба у деталях (вкладки) з ремонтними розмірами, наявність складських площ під них.
2. Вибродуговая наплавлення в жидкости.
У цьому способі якість наплавленного металу залежить багатьох факторів, і різко погіршується за зміни режимів наплавки та хімічного складу электродной дроту. Тому при добре налагодженому процесі відновлення на шийках чавунних колінчастих валів часто зустрічаються пори і тріщини. Кількість пір збільшується в глибині шару, тому відновлені чавунні колінчасті вали шліфують лише до третього ремонтного розміру, та був вибраковують. Усталостная міцність чавунних колінчастих валів, відновлених вибродуговой наплавкой в рідини, знижується на 35−40% [6]. Проте завдяки дворазовому запасу міцності в експлуатації спостерігається незначна кількість їх поломок. Але застосування цього способу наплавки на відновлення чавунних колінчастих валів двигунів вантажних автомобілів через значного зниження усталостной міцності ставати не приемлемым.
3. Вибродуговая наплавлення в водокислородной середовищі [9].
У цьому способі відновлення наплавленный метал має структуру троостита, що переходила в сорбитообразный перліт з твердістю шару HRC 42- 48. Такий метал по зносостійкості поступається высокопрочному чавуну, тим не менш, колінчасті вали відновлені у такий спосіб, забезпечують термін служби двигунів відповідний пробігу автомобіля 50−60 тис. км. Даних про усталостной міцності чавунних колінчастих валів, відновлених наплавкой в водокислородной середовищі, немає. У цілому нині експлуатаційні властивості таких валів вивчені недостатньо, а й через низькою тоді як высокопрочным чавуном зносостійкості наплавленного металу цей спосіб наплавки може бути рекомендований до повсюдному использованию.
4. Однослойная наплавлення під флюсом. Такий спосіб наплавки досліджувався в НИИАТе і КАЗНИПИАТе [3]. Для наплавки застосовували дріт різних марок, зокрема пружинну 2 класу ГОСТ 1071- 81, ОВС, НП-30ХГСА, Св-08, Св-10Х13, Св-12ГС ГОСТ 792–67 та інші. Наплавку виробляли під флюсами АН-348А, ОСЦ-45, АН-15, АН-20 ГОСТ 9087–81 без примешивания і з примешиванием до флюсу графіту, феррохрома, феромарганцю, ферромолибдена, алюмінієвого порошку та інших компонентів щоб одержати наплавленного металу мартенситной структури з твердістю HCR 56−62 без пір і тріщин. Наплавку виробляли при різному кроці, прямий і зворотної полярності, різних напруг дуги і індуктивності зварювальної ланцюга, швидкості подачі электродной дроту і обертання деталі. Усі різновиду однослойной наплавки під флюсом не дали позитивних результатів. Наплавленный метал мав неоднорідну структуру і твердість, містив пори, тріщини і шлакові включения.
5. Двухслойная наплавлення дротом Св-08 під легирующим шаром флюса.
Такий спосіб наплавки розроблений в НИИАТе [3]. Найкращі результати з численних варіантів двошарової наплавки виходять під час використання маловуглецевої дроту Св-08 діаметром 1,6 мм легирующего флюсу АН- 348А (2,5 частини графіту, 2 частини феррохрома № 6 і 0,25 частин рідкого скла). Метал першого шару має аустенитное будову та твердість HRC 35- 38. Другий шар має мартенситное будову та твердість HRC 56−62 і містить небагато пір. Недоліком цього способу наплавки є освіту великої кількості тріщин в наплавленном шарі, викликають підвищений знос пов’язаних вкладишів. Усталостная міцність чавунних колінчастих валів двигунів ЗМЗ 53-А, відновлених двошарової наплавкой під легирующим флюсом, знижується на 26- 28% тобто. менше, аніж за вибродуговой наплавленні в рідини. Наявність лежить на поверхні шийок великого кількості тріщин Демшевського не дозволяє рекомендувати цей спосіб для широкого применения.
6. Двухслойная наплавлення порошкової проволокой.
Схема процесу зварювання порошкової проволокой.
Рис. 1.3.
Такий спосіб розроблений в Казахському науково-дослідному інституті автомобільного транспорту в 1966 року [3]. Наплавленный метал другого шару має структуру мартенситу і твердість HRC 56−60. Суттєвим недоліком цього способу наплавки є освіту пір, раковин і тріщин в наплавленном шарі. Зносостійкість наплавленных шийок житлом становить не наплавленных. Усталостная міцність відновлених чавунних колінчастих валів знижується на 44%. У зв’язку з вище переліченими вадами цей спосіб відновлення чавунних колінчастих валів рекомендувати нельзя.
7. Наплавлення серед вуглекислого газа.
Схема наплавки серед вуглекислого газа.
Рис. 1.4.
Спосіб наплавки розроблений в НИИАТе [3]. Шийки чавунних колінчастих валів наплавлялись дротом різних марок, зокрема Нп-2Х13, ОВС, Св- 12ГС, Нп-30ХГСА, Св-08 та інші. В усіх випадках структура наплавленного металу була незадовільною, в шарі були пори й тріщини. Найкоротший кількість дефектів лежить на поверхні шийок виходить при наплавленні дротом Нп-2Х13, наплавленный метал у своїй має структуру аустеніту з карбідної сіткою і нерівномірну за довжиною твердість, коливну від HRC 51−60. Знос шийок чавунних колінчастих валів, наплавленных в вуглекислому газі дротом Нп-2Х13, були трохи більші не наплавленных шийок. Усталостная міцність у своїй способі знижується на 45−50%. Через зазначених недоліків таку наплавку застосовувати нецелесообразно.
8. Плазмова металлизация [10].
Схема плазмового напыления.
Рис. 1.5.
Серед нових технологічних процесів великий інтерес для процесу відновлення деталей автомобілів представляє способи нанесення металлопокрытий з допомогою плазмової струменя як джерело теплової енергії. Найперспективнішим способом відновлення деталей нанесенням износостойких металлопокрытий є плазменное напилювання з наступним оплавленням покриття. Причому у металі оплавленого покриття частка основного металу мінімальна. Покриття має високої зносостійкості, без пір і тріщин. Процес є високопродуктивним. Недоліком цього способу є високі початкові капіталовкладення устаткування. У нинішніх умови при відсутності оборотних засобів в підприємств цей недолік Демшевського не дозволяє рекомендувати спосіб до повсюдному использованию.
9. Лазерний спосіб восстановления[10].
Такий спосіб може бути рекомендований для використання цьому етапі з високу вартість устаткування й високої вимогливості до обслуговуючому персоналові й культурі производства.
10. Наплавлення під легирующим флюсом по оболонці [3].
Такий спосіб відновлення чавунних колінчастих валів розроблений в НИИАТе і дозволяє їм отримати наплавленный метал без пір і тріщин за більш високої, проти іншими засобами, усталостной міцності відновлених чавунних колінчастих валів. Перевагою цього способу є пір і тріщин, високі прочностные характеристики і просте, доступне за ціною, оборудование.
Сутність способу відновлення чавунного колінчатого валу з застосуванням захисних металевих оболочек:
Сутність способу ось у чому. Деталь обвертывают, металевої оболонкою з листової сталі, щільно притискають оболонку до поверхні деталі з допомогою спеціального пристосування, і зварюванням серед вуглекислого газу прихоплюють їх у стику. Після відходу пристосування виробляють автоматичну наплавку деталі під флюсом по металевої оболонці непосредственно.
Схема наплавки під флюсом по оболочке.
Рис. 1.6.
Відомо [12], що з усунення тріщин в наплавленном металі необхідно зменшити у ньому зміст вуглецю, кремнію, марганцю, сірки і фосфору. Оскільки високо-випробувальний чавун містить значну кількість цих елементів, при експериментах застосовували оболонку зі сталі 08 і дріт Св-08, містять в невеличкому количестве.
При наплавленні під флюсами АН-348А, ОСЦ-45, АН-15, АН-20 краще формування шару і менше дефектів вийшло при використанні флюсу АН-348А. Зі збільшенням товщини [3] оболонки глибина проплавления високоміцного чавуну зменшується (Рис. 1.6), відповідно зменшується вступ у наплавленный метал вуглецю, кремнію, марганцю і інші елементи. Тож отримання наплавленного металу мартенситной структури з твердістю HRC 56−62 у флюс додавали графіт і феррохром, забезпечуючи вміст у наплавленном металі вуглецю 0,6−0,8% і необхідну кількість хрома.
При товщині оболонки 0,8 мм тріщини і пори в наплавленном металі були відсутні, тоді як із звичайних засобах наплавки високоміцного чавуну при змісті вуглецю 0,6−0,8% тріщин і пір уникнути не удается.
Залежність глибини проплавления основного металу від товщини оболочки.
Рис. 1.7.
Роль оболонки в усуненні пір і трещин.
Зі збільшенням товщини оболонки зменшується глибина проплавления чавуну і кількість образующейся окису вуглецю, викликає освіту пір. При товщині оболонки 0,8 мм більш небагато окису вуглецю встигає виокремитися з розплавленого металу і пір у ньому не спостерігається. Усунення тріщин при наплавленні по оболонці сприяє два чинника: зменшення надходження у наплавленный шар кремнію, марганцю, магнію і зменшення розміру й швидкості наростання растягивающих напруг в наплавленном валику у його кристалізації завдяки зменшенню сил опору усадок валика з допомогою переміщення чи пластичної деформації оболонки. Доведено [13], що освіта гарячих тріщин відбувається у період перебування розплаву в твердожидком стані при певної величині і швидкості наростання внутрішніх напряжений.
Схема сил, що перешкоджають усадки наплавленного валика.
Рис. 1.8.
Процес усадки наплавленного металу відбувається так. При наплавленні частина металу, Т. Ж (Рис. 1.8), перебуває у твердожидком стані перебуває й при усадки зменшується в радіальному А, тангенциальном Б і осьовому напрямах. Усадки валика в радіальному напрямі А чавун не перешкоджає. Усадки в тангенциальном напрямі Б перешкоджає раніше наплавленный валик по контуру аб, чавун по контуру бвг і оболонка по контуру дд. При наплавленні по гвинтовій лінії в наплавленном металі в основному виникають кільцеві тріщини, тому розглядаємо процес усадки валика в осьовому напрямі У. Опір усадки валика в осьовому напрямі по контуру зи незначно, оскільки різниця у температурі на кордоні твердожидкого і твердого металу невелика та його усадка відбувається майже одночасно. Тому усадки валика у бік У перешкоджає лише чавун по контури вг і оболонка по контуру гд.
При усадки валика на початку відбувається пружна деформація оболонки, та чавуну. Оскільки чавун майже має пружними властивостями [1], швидкість наростання растягивающих напруг із боку оболонки у кілька разів менше, ніж із боку чавуну. Після досягнення краю плинності, відбувається пластична деформація оболонки, та чавуну, тому внутрішні напруги у яких не перевершать краю плинності т. е.
[pic],.
(1.1).
[pic],.
(1.2) де [pic], [pic] - напруги в оболонці і чугуне;
[pic], [pic] - межі плинності оболонки, та чугуна.
Інші напруги в валику дорівнюватимуть відношенню суми зусиль опору усадки із боку чавуну і оболонки на площу поперечного перерізу валика.
Для випадку з закріпленої оболонкою, напруги в валику можна висловити уравнением:
[pic], (1.3) де М — висота валика, мм;
[pic]- глибина проплавления чавуну при наплавленні без оболонки, мм;
[pic]- товщина оболонки, мм;
R — коефіцієнт, враховує різницю теплофизических властивостей чавуну і оболочки;
Отже, зменшення внутрішніх напруг у наплавленном шарі металу й у попередження освіти тріщин у ньому, необхідно застосовувати оболонки з низьким межею плинності і високої пластичністю. Такими властивості має малоуглеродистая сталь. При наплавленні по оболонці завтовшки 0,8−0,9 мм глибина проплавления чавуну зменшується з 2,4 мм до 1,0 мм [3]. Відповідно величина залишкових напруг зменшується приблизно в 2,4 раза.
Мартенситную структуру наплавленного металу можна отримати роботу шляхом: термообробки, охолодженням шару рідиною у процесі наплавки або шляхом запровадження наплавленный метал легуючих елементів, через флюс [14] чи дріт. Сутність останнього способу ось у чому. З збільшенням змісту вуглецю в стали, твердість утворить мартенситу зростає й сягає HRC 60−62 при 0,6−0,8% вуглецю [12]. Вуглець одночасно знижує точки початку й кінця мартенситних перетворень в область негативних температур. Тому, за збільшенні її змісту більш 0,8% твердість наплавленного металу знижується рахунок збільшення в ньому залишкового аустеніту. З збільшення змісту легуючих елементів, хрому чи марганцю, в наплавленном шарі криві перетворення зсуваються вправо, що зумовлює зменшенню критичної швидкості гарту при охолодженні деталі надворі. Стійкість освіченого мартенситу проти відпустки збільшується, тому при недостатній кількості легуючих елементів може відбутися відпустку раніше наплавленных валиків (швів) внаслідок значного нагріву шару у процесі наплавки. Крапки початку будівництва і кінця мартенситних перетворень знижуються до області негативних температур, тому надмірне збільшення легуючих елементів призводить до збільшення кількості залишкового аустеніту в наплавленном металі і зниження твердості останнього. Стійкість аустеніту у зоні мартенситних перетворень підвищується, тому при охолодженні наплавленного металу для перетворення аустеніту в мартенсит потрібно більше часу. При наплавленні це явище сприяє збільшення кількості залишкового аустеніту і зниження твердості наплавленного металла.
Відповідно до вище викладеним щоб одержати наплавленного металу мартенситной структури з твердістю порядку HRC 60−62 у ньому утримуватися 0,6−0,8% вуглецю і певний кількість легуючих елементів, залежить від термічного циклу наплавленного шару. У нашому разі доцільно застосовувати хром. Деякі інші легирующие елементи, наприклад марганець, сприяють освіті тріщин в наплавленном слое.
Досліди одержання металу з мартенситной структурою проводились наступному порядку [3]. Спочатку до флюсу домішували графіт для одержання в наплавленном металі 0,6−0,8% вуглецю, потім при цьому флюсу з знайденим кількістю графіту домішували феррохром щоб одержати мартенситной структури при охолодженні наплавленного металу на воздухе.
Вуглець і легирующие елементи в наплавленный метал можна вводити також застосуванням порошкової дротом, легирующего чи керамічного флюсу, легованої дроту і легованої оболочки.
За результатами дослідів у табл. 1.3 представлені дані експериментальних наплавок колінчастих валів двигунів ЗМЗ-53А.
[pic].
Як очевидно з табл. 1.3, найвища твердість металу зі структурою мартенситу виходить при наплавленні під легирующим флюсом, що містить 4% графіту і 3,5% феррохрома. У цьому наплавленный метал містить 0,8% вуглецю, 1,8% хрому, 1,79% марганцю, 0,65% кремнію й у незначній кількості інші элементы.
Експлуатаційні випробування на зносостійкість проводилися наступним чином [3]. Відчували чавунні колінчасті вали двигуна ЗМЗ-53А, у яких за дві шатунных і з дві корінних шийки були наплавлены під легирующим флюсом по оболонці. Частина шийок наплавляли під легирующим флюсом із меншим кількістю феррохрома, вони мали твердість HRC 50- 60, інші шийки мали твердість HRC 50−62. Наявність шийок з такою діапазоном твердості дозволило визначити залежність між твердістю і зносостійкості наплавленного металу щодо високоміцного чавуну. Чавунні колінчаті вали оброблялися у відповідність із механічними вимогами заводу і встановлювали на капітально відремонтовані двигатели.
Двигуни експлуатували у звичайних обставинах без розбірки до появи технічних несправностей, після що їхні знімали з автомобілів, розбирали і заміряли діаметри і товщини вкладышей.
У табл. 1.4 наведено дані про відносного зносу наплавленных шийок за дев’ятьма колінчатим валам яка відслужила вже, відповідним пробігу автомобіля 50−70 тис. км.
[pic].
З табл. 1.4 видно, що наплавленные шийки з твердістю більш HRC 56 зношуються менше, і з твердістю менш HRC 56 зношуються большє нє наплавленных чавунних шийок. Бо за оптимальному складі легирующего флюсу твердість наплавленного металу коливається не більше HRC 56−62, зносостійкість відновлених чавунних колінчастих валів виходить нижче новых.
Дані зносостійкості вкладишів з шийками тієї ж валів, див. табл. 1.4, наведені у табл. 1.5.
Як очевидно з табл. 1.5, знос вкладишів, пов’язаних із наплавленными шейками, менше, ніж із не наплавленными.
[pic].
Випробуванню на статичну міцність піддавали нові колінчаті вали і відновлені наплавкой. Результати наведені у табл. 1.6.
[pic].
Як очевидно з табл. 1.6, попри всі засобах наплавки відбувається зниження міцності відновлених чавунних колінчастих валов.
Випробуванню на усталостную міцність проводилися не машині УП-50 конструкції ЦНИИТМАШ на натуральних зразках. Машина УП-50 призначена для порушення та підтримки, заданих за величиною змінних изгибающих напруг. Результати випробувань на усталостную міцність наведені у табл. 1.7.
[pic].
Як очевидно з табл. 1.7, усталостная міцність незалежно від способі наплавки знижується. Найкоротший зниження усталостной міцності 10−15% відбувається за наплавленні під легирующим флюсом по оболонці. Найбільше зниження усталостной міцності при наплавленні в вуглекислому газі підтвердилося ламанням експериментального чавунного колінчатого валу в эксплуатации.
1.4. Тенденція розвитку ремонтної бази на стране.
Зарубіжний опыт.
З початку 1990 року у країні різко впали обсяги автомобільних вантажних перевезень. Відсутність фінансування державних підприємств, лібералізація цін економіці, зокрема і енергоресурси сприяли масовому падіння виробництва. Висока інфляція ліквідувала оборотні кошти автогосподарств, зміст великих автогосподарств, сталася на кілька сотень машин, стало економічно не выгодным.
Зарубіжний досвід показує [11], що у ринкової економіки найбільш ефективними стають фірми, котрі вибрали вузьку спеціалізацію. Це або автоперевезення, отже гараж на 5−20 машин, або авторемонтні роботи, підприємство з наявністю усього обладнання для ремонтних операцій. Кількість працівників цих фірмах вбирається у 25−50 людина. Багато країнах лише на рівні законодавства, через податків і економічні пільги, заохочується створення саме таких, підприємств. Такий фірмі легше пристосуватися до змін над ринком. Здорова між цими фірмами підштовхує їх для пошуку та впровадження нових технологій і надання великих услуг.
Нині країни дуже багато вантажних автомашин перебуває у приватних руках. Ремонт цих машин на великих авторемонтних майстерень стає вигідним у зв’язку з великими накладними видатками ремонтного підприємства. Тому наявність дрібних авторемонтних фірм з невисокими накладними видатками стає необходимостью.
5. Завдання дипломного проекта.
Нині в виробничих підрозділах МШС РФ існує потреба у надійному і потребує високотехнологічного устаткування способі відновлення чавунних колінчастих валів ГАЗ — 53А. Досягнення цього вирішити такі задачи:
Потрібна розробити технологічний процес до складу якого в себя:
— Вибір устаткування й технологічної оснастки;
— Розрахунок і вибір режимів восстановления;
— Технічне нормування операций;
— Технологічну документацию;
— Проектування участка;
— Розробку і розрахунок приспособлений;
— Техніко-економічний расчет;
— Техніку безпеки під час проведення работ.
2. Проектування технологічного процесу відновлення чавунного колінчатого валу двигуна ЗМЗ-53А.
2.1. Розробка маршрутного технологічного процесса.
Для якісних наплавочных операцій потрібно зробити підготовку ремонтних поверхонь мийкою. Бруд, жирові і масляні плівки при зварювальних і наплавочных роботах призводять до утворення пір і тріщин. Часто які у ремонт вали через великі навантажень які долають під час експлуатації мають підвищену деформацію. Для виправлення цього дефекту потрібно передбачити операцію правки. Шліфування корінних шийок валу роблять у центрах верстата. Виконання технологічних вимог щодо биттю корінних шийок, кожен перехід шліфовки виробляють за одну установку в центрах верстата. І тому в технологічний процес введена операція правки центрових фасок. Захисні оболонки встановлюються на підготовлені поверхні шийок валу. Шийки валу повинен мати шорсткість не нижче Ra 1,25. І тому шийки валу шліфують на 1 мм менше останнього ремонтного розміру. Закріплення оболонок до шейкам валу виробляють зварюванням. Після закріплення оболонок потрібно наплавить галтели шийок і після цього наплавить шийки валу. Обробку шийок валу під ремонтні розміри виробляють протягом двох разу, чорновим і чистовим шлифованием. Обробка отворів олійних каналів виробляється перед чистовим шлифованием, щоб не зіпсувати номінальні розміри на слюсарних операціях. За необхідності готові колінчаті вали які пройшли операцію контролю у биттю корінних шийок правлять на пресі. І тому в технологічному процесі мусить бути передбачена повторна операція правки. Відновлення номінальних розмірів фланца маховика, шийки під шків вентилятора і різьби в отворі під храповик виробляють токарным і слюсарним способом. На виконання технічних вимог щодо шорсткості Ra 0,32 шийки колінчастих валів полірують. Для видалення жирових і масляних плівок, і навіть багна й стружки колінчасті вали миють. Щоб запобігти появи слідів іржі колінчаті вали консервують смазкой.
Технологія відновлення чавунних колінчастих валів двигуна ЗМЗ-53А автоматичної наплавкой під легирующим флюсом по оболонці приведено в табл. 2.1.
Таблиця 2.1. | |Технологія | | | | | | | |Відновлення чавунного колінчатого валу | | | |двигуна ЗМЗ-53А | | | |автоматичної наплавкой під легирующим | | | |флюсом по оболонці | | | |Матеріал — чавун магнієвий високо-випробувальний ВЧ | | | |- 50−1,5 | | | |Твердість НВ 196 — 203. Твердість шийок | | | |наплавки НRС 56 — 62. | | | | | | |№ |Найменування операції, переходу |Устаткування, | |Пер| |інструмент | |єхо| | | |так | | | | |1 Мийка | | | |Промити колінчатий вал в гарячому розчині |Мийна машина | | |каустичної соди | | | |2 Слюсарна | | |1 |Встановити колінчатий вал в лещата | | |2 |Відвернути пробки грязеуловителей |Верстак | | | |слюсарний | |3 |Зняти й перегорнути колінчатий вал |лещата, ключі | |4 |Повторити перехід 2 інших шатунных | | | |шийок | | |5 |Зняти деталь | | | |3 Очищення грязеуловителей | | |1 |Встановити колінчатий вал в лещата |Верстак | | | |слюсарний | |2 |Вибити бруд з цих двох грязеуловителей |лещата, ключі | |3 |Перегорнути колінчатий вал | | |4 |Вибити бруд з цих двох решти |Металевий | | |грязеуловителей |йорж | |5 |Зняти деталь | | |6 |Поставити колінчатий вал на установку для |Установка для | | |промивання грязеуловителей | | |7 |Промити грязеуловители |промивання | | | |грязеуловителей.| |8 |Зняти деталь | | | |4 Мийка | | | |Промити колінчатий вал в гарячому розчині |Мийна машина | | |каустичної соди | |.
|№ |Найменування операції, переходу |Устаткування, | |Пер| |інструмент | |єхо| | | |так | | | | |5 Контроль | | |1 |Встановити колінчатий вал першою і п’ятої |Контрольна | | |корінними шейками на призми |плита | |2 |Перевірити биття третьої корінний шийки і |Призми, | | |при плині більш 0,2 мм фарбувати червоною |індикатор, | | |фарбою; такий вал підлягає виправленню на прессе|краска, пензель | |3 |Зняти деталь | | | |6 Правка | | |1 |Встановити вал в електропіч і нагріти до |Електропіч | | |400 градусів З | | |2 |Вийняти вал з печі і час виявляють вал першої и|Призмы, | | |п'ятої корінними шийками на призми преса |індикатор | |3 |Перевірити биття третьої корінний шийки і |Пресс | | |виправити вал до биття не перевищує 0,2 | | | |мм | | |4 |Зняти деталь | | | |7 Центровка | | |1 |Встановити вал фланцем в патрон, а шийку под|Токарный верстат,| | |шестірню в люнет |патрон 3х | | | |кулачковый | |2 |Виставити вал, забезпечивши биття третьої |Люнет, індикатор| | |корінний шийки трохи більше 0,2 мм | | |3 |Перевірити різцем центровую фаску з точки |Різець ВК 8 | | |30 на глибину 3 мм | | |4 |Зняти деталь | | | |8 Шліфування шатунных шийок | | | |під наплавку | | |1 |Встановити вал в центросмесители про й 4 |Кругло-шлифоваль| | |шатунной шейкам |ный верстат | |2 |Шліфувати 1 і 4 шийки до діаметра 57,5 мм |Центросмесители | |3 |Повторити переходи 1 і 2 для 2 і трьох шатунных |Шліфувальний | | |шийок |коло | |4 |Зняти деталь |ЭСТ-25 (60) До | | |9 Шліфування корінних шийок під наплавку | | |1 |Встановити вал в центру верстата |Кругло-шлифоваль| | | |ный верстат | |2 |Шліфувати всі докорінні шийки до діаметра |Центру | | |67,5 мм | | |3 |Зняти деталь |Мікрометр 50−75 | | | |мм | | |10 Прихватка оболонок до корінним шейкам | | |1 |Зодягти оболонку на 1 шийку валу |Металева | |2 |Вставити вал з оболонкою в зажимные кільця |оболонка | | |стенда | | |3 |Виставити оболонку |Стенд для затискача| |4 |Опустити вал |Напівавтомат | | | |А547р | |5 |Включити пневмокамеру | | |6 |Прихопити оболонку | | |7 |Вимкнути пневмокамеру | | |8 |Підняти вал | | |9 |Повторити переходи 1 — 8 інших | | | |корінних шийок | | | |11 Контроль | | | |Легким постукуванням металевого стрижня |Металевий | | |перевірити | | | |щільність прилегания оболонок. При не |стрижень | | |щільному прилегании | | | |зубилом видалити оболонку та одягти нову. | | | |12 Заварка стику оболонки | | |1 |Покласти колінчатий вал до столу для прижатия|См. опер. 10 | | |оболонок | | |2 |Варити стики оболонок | | |№ |Найменування операції, переходу |Устаткування, | |Пер| |інструмент | |єхо| | | |так | | | | |13 Прихватка оболонок до шатунным шейкам | | | |Повторити все переходи операції 10 |Див. опер. 10 | | |14 Контроль | | | |Повторити переходи операції 11 |Див. опер. 11 | | |15 Заварка стику | | | |Повторити переходи операції 12 | | | |16 Слюсарна | | | |Завернути пробки в грязеуловители |Див. опер. 2 | | |17 Наплавлення галтелей корінних шийок в | | | |вуглекислому газі | | |1 |Встановити вал на верстат шийкою під шків |Установка для | | |вентилятора | | | |в патрон і отвором у фланці до центру |наплавки валів | | |задньої бабки | | |2 |Очистити шийки від багна й олії |Мундштук для | |3 |Наплавить ліві галтели всіх корінних шийок |наплавки валів | |4 |Повернути мундштук на 180 градусів |Патрон | |5 |Наплавить праві галтели всіх корінних шийок | | |6 |Зняти деталь | | | |18 Наплавлення галтелей шатунных шийок в | | | |вуглекислому газі | | |1 |Встановити вал в центросмесители |Центросмесители | |2 |Наплавить ліві галтели 1 і 4 шийки |Мундштук для | |3 |Повернути мундштук на 180 градусів |наплавки валів | |4 |Наплавить праві галтелей 1 і 4 шатунных |Установка для | | |шийок | | |5 |Повторити переходи 1,2,3,4 для 2 і трьох |наплавки валів | | |шатунных шийок | | |6 |Зняти деталь | | | |19 Наплавлення корінних шийок під флюсом | | | |Флюс АН 348 +3,5% феррохрома +4% графіту | | |1 |Встановити вал шийкою під шестірню в патрон |Установка для | | |і | | |2 |отвором у фланці до центру задньої бабки |наплавки валів | |3 |Очистити шийки від багна й іржі | | |4 |Зачистити місця прихваток і наплавки |Наждачное | | |галтелей |полотно | |5 |Пробити бородком оболонки над отворами | | | |олійних | | | |каналів |15% рідкого | | | |скла | |6 |Закрити отвори олійних каналів |85% графіту | | |графітової пастою | | |7 |Наплавить шийку до діаметра 72,9 -1,1 мм | | |8 |Повторити перехід 7 інших шийок | | |9 |Зняти деталь | | | |20 Наплавлення шатунных шийок | | |1 |Встановити колінчатий вал в центросмесители | | |2 |Очистити шийки від багна й іржі | | |3 |Зачистити місця прихваток і наплавки | | | |галтелей | | |4 |Пробити бородком оболонки над отворами | | | |олійних | | |5 |Закрити отвори олійних каналів |Див. опер.19 | | |графітової пастою | | |6 |Наплавить 1 шатунную шийку до діаметра | | | |62,9−1,1 мм | | |7 |Повторити перехід 6 для 4 шийки | | |8 |Повторити переходи 1−6 для 2 і трьох шатунных | | | |шийок | | |9 |Зняти деталь | |.
|№ |Найменування операції, переходу |Устаткування, | |Пер| |інструмент | |єхо| | | |так | | | | |21 Попереднє шліфування шатунных шийок | | |1 |Встановити колінчатий вал в центросмесители | | | |про й 4 | | | |шатунным шейкам | | |2 |Шліфувати 1 шатунную шийку до діаметра |Див. опер.8 | | |60,8−0,2 мм | | |3 |Повторити перехід 2 для 4 шатунной шийки | | |4 |Повторити перехід 1 і 2 для 2 і трьох шатунных | | | |шийок | | |5 |Зняти деталь | | | |22 Контроль | | | |Перевірити якість наплавленного шару; пори,| | | |раковини, | | | |тріщини і шлакові включення не допускаються;| | | |на | | | |бракованих шийках сошлифовать метал і | | | |наплавить | | | |новий під легирующим флюсом по оболонці | | | |23 Попереднє шліфування корінних шийок | | |1 |Встановити колінчатий вал до центру верстата | | |2 |Шліфувати корінні шийки до діаметра |Див. опер. 9 | | |70,8−0,2 мм | | |3 |Зняти деталь | | | |24 Контроль | | | |Перевірити якість наплавленного шару; пори,| | | |раковини, | | | |тріщини і шлакові включення не допускаються;| | | |на | | | |бракованих шийках сошлифовать метал і | | | |наплавить | | | |новий під легирующим флюсом по оболонці | | | |25 Обробка отворів олійних каналів | | |1 |Встановити колінчатий вал в корінні постели|Вертикально- | | |блоку | | | |двигуна ЗМЗ 53А на столі сверлильного |свердлильний | | |верстата |верстат | |2 |Якщо зенковать отвори олійних каналів на |Технологічний | | |всіх | | | |шатунных шийках |блок двигуна | |3 |Якщо зенковать отвори олійних каналів на |ЗМЗ-53А | | |всіх | | | |корінних шийках |Свердло діаметром| |4 |Продути отвори |14 мм | |5 |Зняти деталь | | | |26 Контроль | | | |Перевірити якість раззенковки олійних | | | |отворів | | | |27 Остаточне шліфування шатунных шийок | | |1 |Встановити колінчатий вал в центросмесители | | |2 |Шліфувати 1 шатунную шийку до діаметра | | | |60−0,013 мм | | |3 |Повторити перехід 2 для 4 шатунной шийки |Див. опер. 8 | |4 |Повторити переходы1,2,3 для 2 і трьох шатунных | | | |шийок | | |5 |Зняти деталь | | | |28 Остаточне шліфування корінних шийок | | |1 |Встановити колінчатий вал в центру | | | |кругло-шлифовального | | | |верстата |Див. опер. 9 | |2 |Шліфувати корінні шийки до діаметра | | | |70−0,013 мм | | |3 |Зняти деталь | |.
|№ |Найменування операції, переходу |Устаткування, | |Пер| |інструмент | |єхо| | | |так | | | | |29 Контроль | | |1 |Встановити колінчатий вал 1 і п’яти корінними | | | |шейками на | | | |призми |Призми | |2 |Виробити поверховий огляд. Пори, тріщини, |Індикатор | | |мушлі та | | | |шлакові включення не допускаються |Скоби | |3 |Перевірити діаметри шийок | | |4 |Перевірити твердість на 1 коленчатом валі з | | | |партії | | | |Твердість мусить бути НRС 56−62 | | |5 |Перевірити биття 3 корінний шийки, шийки під| | | |розподільну шестірню, шийку під шків | | | |вентиля- | | | |тору, торцевое биття фланца. | | | |30 Правка | | |1 |Встановити колінчатий вал крайніми шейками |Пресс | | |на призми | | |2 |Перевірити биття 3 корінний шийки |Пристосування | |3 |Править колінчатий вал, биття трохи більше |для правки | | |0,05 мм | | |4 |Зняти деталь |Індикатор | | |31 Виправлення фланца кріплення | | | |маховика | | |1 |Торцевать торцеву поверхню фланца зі |Патрон 3х | | |боку |кулачковый | | |маховика і суто, забезпечивши биття торця |Люнет | | |не | | | |більш 0,04 мм |Індикатор | |2 |Перевірити різцем центровую фаску 60 градусов|Резец підрізною | | |на |ВК8 | | |глибину 2,5 мм |Різець прохідній | | | |ВК8 | |3 |Зняти фаску 3×45 по крайці фланца |Фаскомер | |4 |Зняти деталь | | | |32 Виправлення отвори у фланці під | | | |підшипник | | |1 |Закріпити шийку колінчатого валу під |Патрон 3х | | |розподільну |кулачковый | | |шестірню в патрон і п’яти шийку валу в люнет |Люнет | |2 |Зважити биття по середньої шийки. Пульс не | | | |має | | | |перевищувати 0,05 мм |Індикатор | |3 |Розточити отвір під ремонтну втулку до |Різець расточной | | |діаметра |ВК8 | | |44+0,05 на довжину 13 мм |Нутромер | |4 |Притупити гострі крайки |Шабер | |5 |Зняти деталь | | | |33 Слюсарна | | |1 |Закріпити колінчатий вал в лещата |Слюсарний | | | |верстак | |2 |Запрессовать ремонтну втулку з розмірами: |Альтанка, молоток| | |Зовнішнє діаметр 44,06 +0,02 мм |Лещата, мідні | | |Внутрішній діаметр 38,5 +0,5 |прокладки | | |Лінійний розмір 13 -0,3 мм | | |3 |Зняти деталь | | | |34 Розточення отвори | | |1 |Закріпити колінчатий вал за шийку під |Індикатор | | |маточину шкива в | | | |патрон і п’яти шийкою в люнет |Різець расточной | | | |ВК8 | |2 |Зважити биття по середньої шийки. Пульс не |Різець прохідній | | |має |ВК8 | | |перевищувати 0,05 мм |Нутромер | |3 |Розточити отвір у чопі під |Фаскомер | | |номінальний розмір | | | |до діаметра 40 -0,012,-0,028 мм | | |4 |Зняти фаску 2,5×60 градусів по крайці | | | |чопи | | |5 |Зняти вал | | |№ |Найменування операції, переходу |Устаткування, | |Пер| |інструмент | |єхо| | | |так | | | | |35 Відновлення шийки під шків вентилятора| | |1 |Встановити вал фланцем кріплення маховика в |Патрон 3х | | |патрон, 1 |кулачковый | | |корінний шийкою в люнет, мова підібрати |Люнет | | |центром | | |2 |Зважити биття по середньої шийки. Пульс не |Індикатор | | |має | | | |перевищувати 0,05 мм | | |3 |Виробити накатку зовнішньої поверхні |Накатка-рифление| | |шийки під шків | | | |вентилятора |пряме | |4 |Проточить шийку під маточину шкива |Різець прохідній | | |вентилятора до |ВК8 | | |номінального діаметра 38 +0,020, +0,003 мм |Скоба | |5 |Зняти деталь | | | |36 Прогонка різьби в отворі під храповик | | | |при зриві | | | |різьби до п’яти ниток | | |1 |Закріпити колінчатий вал в лещата |Верстак | | | |слюсарний | |2 |Прогнати різьблення М27×2 в отворі під |Лещата, мідні | | |храповик по всієї | | | |довжині |прокладки | |3 |Зняти колінчатий вал |Мітчик М27×2 | |4 |Перевірити якість прогонки різьби |Вороток | | |37 Нарізка ремонтної різьби в отворі під | | | |храповик | | | |при зриві різьби понад п’ять ниток | | |1 |Закріпити колінчатий вал фланцем в патрон і |Патрон 3х | | |1 шийкою |кулачковый | | |в люнет |Люнет | |2 |Зважити биття по середньої шийки. Пульс не |Індикатор | | |має | | | |перевищувати 0,05 мм | | |3 |Рассверлить отвір з зірваної різьбленням до|Сверло діаметром| | |діаметра | | | |27,7 +0,1 на довжину 38 мм |27,7 мм | |4 |Рассверлить отвір до діаметра 31 мм на |Свердло 31 мм | | |глибину 6 мм | | |5 |Нарізати ремонтну різьблення М30×2 на глибину |Мітчик М30×2 | | |29 мм | | |6 |Проточить фаску 3×30 градусів |Вороток | |7 |Зняти колінчатий вал |Різець расточной | | | |ВК8 | | |38 Контроль | | | |Перевірити різьблення М30×2 і фаску 3×30 |Пробка резьб. | | | |М30×2 | | |39 Полірування шийок | | |1 |Встановити колінчатий вал в центру верстата |Пристосування | |2 |Полірувати корінні і шатунные шийки валу |для полірування | | |40 Мийка | | | |Продути і промити колінчатий вал |Гас, | | | |Стиснутий повітря | | |41 Комплектація | | | |Змастити колінчатий вал, завернути в |Олія для АІ-20 | | |промаслену | | | |папір та відправити складу |Промаслена | | | |папір |.
2.2. Вибір устаткування й технологічної оснастки.
Приймаю для технологічного процесу відновлення чавунних колінчастих валів таке оборудование:
[pic].
2.3. Розрахунок і вибір режимів поновлення і механічної обработки.
2.3.1. Вибір та обґрунтування технологічного маршруту механічного оброблення корінних і шатунных шеек.
При чорновому шліфуванні виробляється великий з'їм металу, що неминуче призводить до появи внутрішніх напруг. Щоб уникнути деформацій валу обробку шийок колінчастих валів необхідно здійснювати в наступній последовательности:
1. Попереднє шліфування шатунных шеек;
2. Попереднє шліфування корінних шеек;
3. Зенкование отворів олійних каналов;
4. Остаточне шліфування шатунных шеек;
5. Остаточне шліфування корінних шеек;
6. Полірування шеек.
У іншому порядку шлифования вал деформується, і співвісність корінних шийок порушується, у зв’язку з цим доводиться вводити додаткову правку чавунного колінчатого вала.
2.3.2. Розрахунок проміжних розмірів, призначення припусков на механічну обработку.
Розмір припусков знайдено расчетно-аналитическим методом [15]. Розрахунок розпочато з перебування припуска на чистовое шліфування. Розрахунковий мінімальний припуск:
[pic] (2.1) де [pic]- висота мікро неровностей;
[pic]- товщина дефектного слоя;
[pic]- сумарне відхилення розташування оброблюваної поверхности.
[pic]- похибка установки. Після обробітку в центрах [pic]= 0.
[pic], (2.2) де [pic]- відхилення осі від прямолинейности;
[pic]- похибка центрирования;
[pic], (2.3) де [pic]- питома кривизна деталі. Для чистового шлифования прийнято [pic]=0,05 мм;
L — довжина заготівлі, мм. Прийнято L=710 мм.
[pic], (2.4) Усі дані для розрахунків (Rz, TD, h) взяті з [15 табл. 2,3 стор. 4].
[pic] мм;
[pic]мм;
[pic]мм;
[pic]мм;
Розрахункові мінімальні розміри визначено шляхом поповнення відповідного розрахункового припуска:
[pic], (2.5) де [pic]- мінімально припустимий діаметр корінний шийки на чистовий операції, [pic]= 69,987 мм;
[pic]-минимально припустимий розмір корінний шийки на чорнової операции.
[pic]мм;
Допуск на розмір даного переходу становить 0,2 мм, тому [pic] округляем до 70,6 мм;
[pic], (2.6).
[pic] мм;
Додача на черновое шлифование:
[pic] мм;
[pic]мм;
[pic] мм;
[pic] мм;
[pic] мм;
Допуск на розмір даного переходу становить 1,1 мм, тому [pic]округляем до 71,8 мм.
[pic] мм;
Отримані дані заносимо в табл. 2.3.
[pic].
Розрахунок припусков і проміжних розмірів для шатунных шийок чавунного колінчатого валу вироблено аналогічно корінним. Результати обчислень вносимо в табл. 2.4.
[pic].
Остаточно приймаємо розміри для наплавки:
Шатунных шийок — діаметр 62,9−1,1 мм;
Корінних шийок — діаметр 72,9−1,1 мм;
Для чорнового шлифования:
Шатунных шийок — діаметр 60,8- 0,2 мм;
Корінних шийок — діаметр 70,8−0,2 мм;
2.3.3. Розрахунок режимів різання при механічної обробці шийок чавунного колінчатого вала.
Черновое шліфування корінних шеек.
Необхідний діаметр: 70,8−0,2 мм;
Діаметр шлифуемой деталі: 72,9−1,1 мм;
Використовується кругло — шліфувальний верстат 3Б161.
Довжина оброблюваної шийки: Lш — 30,5 мм;
Кількість шийок — 5.
Вибрано шліфувальний коло — ЕСТ (25 — 60) К.
Діаметр кола Dк — 600 мм;
Ширина кола Вк — 20 мм;
Розрахункова швидкість обертання детали:
[pic], (2.7) де Dд — діаметр шлифуемой поверхні, мм;
Т — стійкість шлифовального кола. Прийнято Т=40 хв; t — глибина шлифования, мм.
Значення (Сv, k, m, t. x, [pic]) прийнято по [18, табл.36].
[pic] м/мин;
Розрахункова частота обертання детали:
[pic], (2.8).
[pic]об/мин.
[pic] - частота обертання деталі у межах паспортних даних станка.
Швидкість обертання шлифовального круга:
[pic], (2.9) де Dк — діаметр шлифовального кола, мм;
[pic]- частота обертання шлифовального кола. Прийнято по паспортним даним верстата [pic]- 1200 об/мин.
[pic] м/мин;
Швидкість переміщення стола:
[pic], (2.10) де Sпр — переміщення оброблюваної деталі вздовж її осі за оборот;
[pic], (2.11) де Вк — ширина шлифовального кола, мм;
[pic] - розрахунковий коефіцієнт шлифования. Для попередньої обробки [pic] = 0,35 [18 табл. 34].
[pic] мм/об;
[pic] мм/мин;
Отримане значення Vc = 0,35 мм/мин у межах швидкостей переміщення столу, вказаних у паспортні дані обраного станка.
Основна навантаження при шліфуванні посідає черновое шліфування. Потрібна потужність на обертання шлифовального круга:
Тангенциальная сила резания:
[pic], (2.12).
Значення (Порівн, u, x, у) взяті з [18 табл. 39].
[pic]Н;
Ефективна потужність на обертання шлифовального круга:
[pic], (2.13).
[pic] кВт;
Потрібна мощность:
[pic], (2.14) де [pic] - К.П.Д. шлифовального верстата. Прийнято [pic] = 0,75.
[pic] кВт;
Потужності обраного верстата достатньо чорнового шлифования на вибраних режимах.
Основне технологічне время:
[pic], (2.15) де L — довжина подовжнього ходу деталі, мм;
[pic], (2.16) де Lш — довжина оброблюваної поверхні, мм;
Вш — ширина кола, мм.
L = 30,5 — 20 = 10,5 мм; h — додача на обробку, мм; до — коефіцієнт, враховує точність шлифования і знос кола. За даними [18] при чорновому шліфуванні до = 1,3 — 1,4, прийнято до = 1,3; при чистовом шліфуванні до = 1,3 — 1,7, прийнято до = 1,5.
[pic] мин;
Час, витрачене п’ять шеек:
[pic] мин;
Розрахунок шатунных колінчастих шийок зроблено аналогічно. Отримані результати внесені до табл. 2.5.
[pic].
2.4. Технічне нормування операцій технологічного процесса.
Розрахунок норм часу зроблено по общемашиностроительным нормам [19, 20, 21, 22].
Тшт = Те + Тв + Тобс + Тф, (2.17) де Тшт — поштучна час, мин;
Те — основне (технічне) час, мин;
Тв — допоміжне час на встановлення та зняття деталі з устаткування, мин.
Тобс — час обслуговування робочого місця та устаткування, хв. Прийнято 5% від (Те + Тв).
Тф — час на фізичні потреби і відпочинок, хв. Прийнято 5% від (Те + Тв).
Розрахунок штучного часу для операцій № 23 чорнового шлифования корінних шеек:
По [21 карта № 3] час на встановлення та зняття деталі при обробці в центрах t = 1,5 мин.;
Тф = Тобс = [pic] мин;
Тш = 18+1,5+0,98+0,98 = 21,5 мин.
Розрахунок інших операцій зроблено аналогічно. Усі отримані дані наведені у табл. 2.6. | | | | | | | | | | Таблиця 2.6| |Назва |Оборудовани|№ |Основн|Вспом|Операти|Время |Время|Норма |Режими обробки | |операцій |е |опе|ое |огате|вное |на |на |по одній| | | | |рац|(техно|льное|время в|обслуж|отдых|го | | | | |ії |логиче|время|мин. |ивание|в |часів| | | | | |ское) |на | |рабоче|мин. |й у | | | | | |час |устан| |го |5% от|мин | | | | | |в |овку | |місця |Tе | | | | | | |хв. |і | |в | | | | | | | | |сняти| |мин.5%| | | | | | | | |е | |від Tе | | | | | | | | |детал| | | | | | | | | | |й у | | | | | | | | | | |хв. | | | | | | | | | |Те. |Тв. |Tе=To+T|Тоб. |Тф |Тшт. | | | | | | | |в | | | | | |Мийка |Мийна |1 |15 |2,2 |17,2 |0,86 |0,75 |18,81 |Температура 70−90 З Сода| | |машина | | | | | | | |каустична 10−15 грн. | | | | | | | | | | |на 10л. | | |Мийна |4 |15 |2,2 |17,2 |0,86 |0,75 |18,81 |Температура 70−90 З Сода| | |машина | | | | | | | |каустична 10−15 грн. | | | | | | | | | | |на 10л. | | |Ванна |40 |15 |2,2 |17,2 |0,86 |0,75 |18,81 |Гас | | |мийна | | | | | | | | | |Разом | | | | |51,6 | | |56,43 | | | | | | | | | | | | | |Слесарная|Верстак |2 |1,56 |0,00 |1,56 |0,08 |0,09 |1,73 | | | |Верстак |3 |1,18 |0,00 |1,18 |0,06 |0,07 |1,31 | | | |Пресс |6 |0,51 |0,00 |0,51 |0,03 |0,03 |0,56 | | | |Верстак |16 |0,55 |0,00 |0,55 |0,03 |0,03 |0,61 | | | |2H135Л |25 |1,24 |2,60 |3,84 |0,06 |0,07 |3,98 |S-200 обмин | | |Пресс |30 |0,51 |0,00 |0,51 |0,03 |0,03 |0,57 | | | |Верстак |33 |0,44 |0,00 |0,44 |0,02 |0,03 |0,49 | | | |Верстак |36 |0,90 |0,00 |0,90 |0,05 |0,05 |1,00 | | | |Верстак |41 |0,47 |0,00 |0,47 |0,02 |0,03 |0,52 | | |Разом | | | | |9,95 | | |10,76 | | | | | | | | | | | | | | | | | | | | | | | | | | | | | | | | | | | | | | | | | | | | | | | | | | | | | | | | | | | | | | | | | | | | | | | | | | | | | | | | | | | | | | | | | | | | | | | | | |Продо| | | | | | | | | | |лжени| | | | | | | | | | |е | | | | | | | | | | |табли| | | | | | | | | | |цы | | | | | | | | | | |2.6 | | | |Токарная |1К 62 |7 |0,60 |4,20 |4,80 |0,03 |0,04 |4,87 |P.S 200 обмин | | | |31 |3,50 |3,80 |7,30 |0,18 |0,21 |7,69 |P.S 280 об. мин V 0,16 | | | | | | | | | | |ммоб | | | |32 |1,75 |4,20 |5,95 |0,09 |0,11 |6,14 |P.S 220 об. мин V 0,1 ммоб| | | |34 |2,05 |4,20 |6,25 |0,10 |0,12 |6,48 |P.S 280 об. мин V 0,1 ммоб| | | |35 |5,85 |4,20 |10,05 |0,29 |0,35 |10,69 |Випуклість P. S 50 обмин V | | | | | | | | | | |0,2 ммоб | | | | | | | | | | |Проточка P. S 220 обмин V | | | | | | | | | | |0,16 ммоб | | | |37 |4,15 |3,80 |7,95 |0,21 |0,25 |8,41 |P.S 250 обмин V 0,2 ммоб| | | |39 |35,00 |4,20 |39,20 |1,75 |2,10 |43,05 |P.S 400 обмин | |Разом | | | | |81,50 | | |87,32 | | | | | | | | | | | | | |Шлифовани|3Б161 |8 |21,80 |4,20 |26,00 |1,30 |1,30 |28,60 |Частота обертання деталі | |е | | | | | | | | |nд 55обмин Швидкість | | | | | | | | | | |переміщення столу Vc | | | | | | | | | | |0,385 ммоб Швидкість | | | | | | | | | | |обертання шлифовального | | | | | | | | | | |кола Vк 754 ммин | | | |9 |12,50 |4,20 |16,70 |0,84 |0,84 |18,37 | | | | |21 |39,00 |4,20 |43,20 |2,16 |2,16 |47,52 | | | | |23 |18,00 |1,50 |19,50 |0,98 |0,98 |21,45 | | | | |27 |9,20 |4,20 |13,40 |0,67 |0,67 |14,74 | | | | |28 |7,00 |2,50 |9,50 |0,48 |0,48 |10,45 | | |Разом | | | | |128,30 | | |141,13| | | | | | | | | | | | | |Зварювання |Полуавтомат|10 |2,00 |16,50|18,50 |0,10 |0,12 |18,72 |Напруга 19−20 В Сила | | |А547р | | | | | | | |струму 120А Швидкість | | | | | | | | | | |обертання валу 2 обмин | | | | | | | | | | |Швидкість подачі | | | | | | | | | | |электродной дроту | | | | | | | | | | |1,4−1,6 ммин | | | |12 |1,80 |16,50|18,30 |0,09 |0,11 |18,50 | | | | |13 |1,60 |13,20|14,80 |0,08 |0,10 |14,98 | | | | |15 |1,50 |13,2 |14,70 |0,08 |0,09 |14,87 | | |Разом | | | | |66,30 | | |67,06 | | | | | | | | | | | | | |Наплавлення |Установка |17 |11,40 |3,8 |15,20 |0,57 |0,68 |16,45 |Напруга 20−22 В Сила | | |для | | | | | | | |струму 120−150А Швидкість | | |наплавки | | | | | | | |обертання валу 2,5−3 | | | | | | | | | | |обмин Крок наплавки 3,5 | | | | | | | | | | |ммоб Швидкість подачі | | | | | | | | | | |электродной дроту | | | | | | | | | | |1,4−1,6 ммин Зміщення | | | | | | | | | | |електрода з зеніту 8−10 | | | | | | | | | | |мм Виліт електрода 15−20| | | | | | | | | | |мм | | | |18 |8,80 |7,6 |16,40 |0,44 |0,53 |17,37 | | | | |19 |45,50 |6,6 |52,10 |2,28 |2,73 |57,11 | | | | |20 |56,40 |8,6 |65,00 |2,82 |3,38 |71,20 | | |Разом | | | | |148,70 | | |162,13| |.
2.5. Технологічна документація на технологічний процесс.
2.5.1. Маршрутна карта технологічного процесса.
Операции:
1. Мийка; 2. Слюсарна; 3. Слюсарна; 4. Мийка; 5. Контрольная;
7. Слюсарна; 7. Токарная; 8. Шлифовальная; 9. Шлифовальная;
10. Зварювальна; 11. Контрольна; 12. Зварювальна; 13. Сварочная;
14. Контрольна; 15. Зварювання; 16. Слюсарна; 17. Наплавочная;
18. Наплавочная; 19. Наплавочная; 20. Наплавочная;
21. Шлифовальная; 22. Контрольна; 23. Шлифовальная;
24. Контрольна; 25. Слюсарна; 26. Контрольна; 27. Шлифовальная;
28. Шлифовальная; 29. Контрольна; 30. Слюсарна; 31. Токарная;
32. Токарная; 33. Слюсарна; 34. Токарная; 35. Токарная;
36. Слюсарна; 37. Токарная; 38. Контрольна; 39. Токарная;
40. Мийка; 41. Комплектовочная.
2.5.2. Операційна карта механічного оброблення чорнового шлифования корінних шийок чавунного колінчатого вала.
Операційна карта приведено в табл. 2.7. | | | |Операцион| | | | | | | | | |нная | | | | | | | | | |карта на | | | | | | | | | |механичес| | | | | | | | | |кую | | | | | | | | | |обробку| | | | | | | | | |ГОСТ | | | | | | | | | |3.1404−86| | | | | | | | | |. | | | | | | | | | | | | | | | | | | | | | | | |Табли| | | | | | | | | |ца | | | | | | | | | |2.7 | | | |На| | |Твердість |Інструмент | |СОЖ |Режими обробки | | |їм| | |HRC | | | | | | |єп| | | | | | | | | |вв| | | | | | | | | |а| | | | | | | | | |не| | | | | | | | | |і | | | | | | | | | |мало| | | | | | | | | |рк| | | | | | | | | |а | | | | | | | | | |мало| | | | | | | | | |ті| | | | | | | | | |рі| | | | | | | | | |ав| | | | | | | | | |а | | | | | | | | | |Чу| | |56−62 |Робочий |Мерительный | | | | |гу| | | | | | | | | |зв | | | | | | | | | |мало| | | | | | | | | |пан| | | | | | | | | |не| | | | | | | | | |ви| | | | | | | | | |і | | | | | | | | | |ви| | | | | | | | | |зі| | | | | | | | | |до| | | | | | | | | |ін| | | | | | | | | |оч| | | | | | | | | |ны| | | | | | | | | |і | | | | | | | | | |ВЧ| | | | | | | | | |50| | | | | | | | | |- | | | | | | | | | |1,| | | | | | | | | |5 | | | | | | | | | |На| | |Те, хв. | | | | | | |їм| | | | | | | | | |єп| | | | | | | | | |вв| | | | | | | | | |а| | | | | | | | | |не| | | | | | | | | |про| | | | | | | | | |репетування| | | | | | | | | |задовільно| | | | | | | | | |вв| | | | | | | | | |а| | | | | | | | | |іє| | | | | | | | | |і | | | | | | | | | |ін| | | | | | | | | |ів| | | | | | | | | |по| | | | | | | | | |зі| | | | | | | | | |бл| | | | | | | | | |єп| | | | | | | | | |ий| | | | | | | | | |У розділі ст| | | | | | | | | |а| | | | | | | | | |прибл| | | | | | | | | |кр| | | | | | | | | |уг| | | | | | | | | |ло| | | | | | | | | |шл| | | | | | | | | |іф| | | | | | | | | |вв| | | | | | | | | |ав| | | | | | | | | |ьн| | | | | | | | | |ый| | | | | | | | | |3Б| | | | | | | | | |16| | | | | | | | | |1 | | | | | | | | | |Але| | | | | | | | | |ме| | | | | | | | | |р | | | | | | | | | |і | | | | | | | | | |зі| | | | | | | | | |де| | | | | | | | | |рж| | | | | | | | | |а| | | | | | | | | |не| | | | | | | | | |пе| | | | | | | | | |ре| | | | | | | | | |мо| | | | | | | | | |так| | | | | | | | | |23| | | | | | | | | |. | | | | | | | | | |Че| | | | | | | | | |рн| | | | | | | | | |вв| | | | | | | | | |ое| | | | | | | | | |шл| | | | | | | | | |іф| | | | | | | | | |вв| | | | | | | | | |а| | | | | | | | | |не| | | | | | | | | |до| | | | | | | | | |ре| | | | | | | | | |не| | | | | | | | | |ых| | | | | | | | | |ше| | | | | | | | | |ек| | | | | | | | | |. | | | | | | | | | |1 |Встановити | | |Верхонки | | | | | | |колінчатий вал | | | | | | | | | |в центру верстата| | | | | | | | |2 |Шліфувати | |16,5 |Коло шлифовальный|Микрометр МК |Rotak|Частота обертання | | | |корінні шийки | | |ЕСТ 25 (60) До |25 — 75 ГОСТ | |деталі nд 55обмин | | | |до діаметра | | |ГОСТ 2424−75, |6507−90 | |Швидкість | | | |61,1+0,1 мм Ra | | |центру наполегливі | | |переміщення столу | | | |0,63. | | |ГОСТ | | |Vc 0,385 ммоб | | | | | | |2575−79.Образцы | | |Швидкість обертання | | | | | | |шорсткості | | |шлифовального кола| | | | | | |ГОСТ 9378−75 | | |Vк 754 ммин | | |3 |Зняти деталь | | |Верхонки | | | |.
2.5.3. Карта ескізу чорнового шлифования корінних шийок чавунного колінчатого вала.
2.6. Укладання до технологічному процесові відновлення чавунних колінчастих валів двигуна ЗМЗ — 53А.
Цей технологічний процес забезпечує якісне відновлення чавунних колінчастих валів без змісту пір і тріщин. При всіх перевагах даної технології має і пояснюються деякі складності. Наприклад, і під час наплавочных робіт важко витримати розрахункові припуски на обробку. Притиснення захисної оболонки до шийки валу виробляється кожну шийку окремо. При доопрацюванні стенда можна зменшити час на складання валу і захисних оболонок. При малих обсягах виробів які підлягають відновленню вдасться повністю завантажити деякі робочі місця та доводиться шукати додаткову завантаження для рабочих.
2.7. Проектування ділянки на відновлення чавунних колінчастих валів двигуна ЗМЗ — 53А.
2.7.1 Розрахунок кількості обладнання та його загрузки.
Визначення кількості верстатів в обробці чавунних колінчастих валів вироблено по техніко-економічним показниками [16].
[pic], (2.18) де Ті - оперативне час витрачене дану операцію, мин;
Тт — такт виготовлення деталі, хв. Приймаю Тт — рівному максимальному оперативному часу витраченому на наплавочной операції Ті - 148,7 мин.
Необхідну кількість верстатів на токарной операции:
[pic];
На токарні операції приймаю 1 верстат. Решта кількість устаткування розраховане аналогічно і занесено в табл. 2.8.
2.7.2. Розрахунок кількості робітників і обслуговуючого персонала.
Розрахунок кількості робочих верстатників зроблено за кількістю прийнятого устаткування табл. 2.8.
[pic].
Деякі робочі буде завантажено в повному обсязі. Токар на 55%, слюсар на майже 7%, мийник на 35%, зварювальник на 45%. У разі ремонтного ділянки доцільно цих робочих доза вантажити роботою відповідно до їхнього профілю роботи. Наприклад, мийника можна використати в вхідний мийці машин вступників на ремонт.
Інженерно-технічний персонал розрахований у вигляді 11−12% від кількості робочих [16]. Прийнято 1 майстер. Інший обслуга приймається по зі штатним розкладом ремонтного цеха.
2.7.3. Розрахунок виробничих площадей.
Розрахунок площ ділянки відновлення чавунних колінчастих валів зроблено за нормами технологічного проектування підприємств машинобудування [23] і занесли у табл. 2.9.
[pic], (2.19) де [pic] - загальна площа, зайнята устаткуванням; до — коефіцієнт проходів та створення робочих зон. Прийнято до = 4,5 [16].
[pic].
[pic] [pic],.
2.7.4. Розробка та обґрунтування схем планування оборудования.
Ширина прольоту ділянки прийнята У = 18 м.
Довжина зайнята участком:
[pic], (2.20).
[pic] м;
Норми ширини проїзду прийнято з урахуванням оргоснастки виходячи з типових проектів організації робочих місць й виконання вимог ГОСТ 12.3.020 — 80 [23].
Ширина проїзду — 3 м;
Відстань від верстата до проїзду — 2 м;
Відстань між верстатами: між тильними сторонами — 1 м; між бічними сторонами — 1,3 м; між фронтом — 2,6 м;
Відстань від муру і колон до: фронту — 1,6 м; тильного боку — 1,5 м; бічний боку — 0,9 м;
По рекомендаціям [23], прийнято розташування наплавочного, зварювального посади під стінами ділянки в ізольованому приміщенні. Шліфувальний і мийний посади як і маю в ізольованому помещении.
Схема ділянки відновлення чавунних колінчастих валов.
3. Конструювання стенда для прихватки металевої захисної оболочки.
3.1. Опис деталі, технічні умови їхньому изготовление.
Ескіз металевої оболочки.
Рис 3.1.
D — внутрішній діаметр кольца.
Для шатунных шийок D = 57,5 мм;
Для корінних шийок D = 67,5 мм;
P.S — товщина кільця 0,8 — 0,9 мм.
Технічні умови на виготовлення: 1. 1. Матеріал — лист 0,8−0,9 мм, сталь 08 кп (ГОСТ 8075 — 81); 2. 2. Ризики, вм’ятини, подряпини глибиною більш 0,2 мм не допускаются;
3. Краї кільця притупити колом фаской 0,2×45; 3. 4. Разностенность деталі має перевищувати 0,1 мм.
Схоплена, до шейкам чавунного колінчатого валу, оболонка повинна щільно прилягати до шийки, у місцях неплотного прилегания відбувається несплавление шару із головною металом, утворюються пори і трещины.
Експериментальна перевірка різноманітних пристосувань для притиснення оболонок до шейкам під час прихватки дозволила вибрати найбільш просте та надійне їх — разъемное металеве кільце, облицьоване всередині гумою завтовшки 5 — 6,5 мм [3]. З допомогою разъемного кільця можна притискати оболонки до шейкам валу вручну, використовуючи кліщі (Рис. 3.2) [3] і слюсарну струбцину.
Ескіз кліщів для притискання оболонки до шейкам вала.
Рис. 3.2.
2. Вибір та обґрунтування принципової схеми стенда.
Розроблюваний стенд повинен відповідати кільком требованиям:
1. Зручність у роботі і обслуживании.
2. Малі габаритні размеры.
3. Низька ціна комплектующих.
4. Пристосування має забезпечити повне усунення всіх геометричних похибок штампувальних операцій повним обжатием оболонки поверхнею шийки вала.
Для зручності роботи з зварювальних операціях доцільно застосувати верхню завантаження чавунного колінчатого валу в приспособление.
Із трьох найпоширеніших видів приводів: електричного, гідравлічного і пневматичного найменші габаритні розміри має пневмопривод. Перевагою пневма і гідроприводів проти електричним є можливість відтворення поступального руху без будь-яких передатних механизмов.
У порівняні з гідравлічними пневматичні приводи мають такими перевагами: їх виконавчі устрою мають нижчу вартість, поворотні лінії значно коротші, оскільки повітря то, можливо видалено у повітря з точки системи. Наявність необмеженого запасу повітря на якості робітника тіла також сприяє широкому поширенню пневмоустройств. Разом про те пневматичні приводи при рівних габаритів з гідравлічними розвивають менше зусилля, що вищим тиском рідини в гідравлічних приводах [25].
Виходячи з розуміння, що з якості притиснення оболонок до чавунному колінчатому валу залежить якість наплавочных робіт, соціальній та цілях механізації процесів обжатия оболонок у цьому дипломному проекті вирішується завдання розробки стенда для обжатия і наступного прихватки захисної металевої оболонки до колінчатому валу. Однією з варіантів розв’язання проблеми то, можливо застосування важільною схеми стенда.
Остаточно приймаю стенд з верхньої завантаженням чавунного колінчатого валу, важільною схеми передачі зусилля стискування, з допомогою пневмапривода.
Послідовність роботи стенда:
У розкриті півкільця 1 з забитої в них гумової прокладанням 4 встановлюють оболонки 5, вал 6 вкладають на оболонки, та виставляють так, щоб краю півкілець і оболонки збігалися. Потім опускають колінчатий вал з зажимными кільцями вниз, включають подачу повітря на пневматичну камеру 8. Шток пневматичною камери, й сама камера виробляє тиск на важелі 2 який кріпляться на рамі 7 у вигляді кронштейнів 3. Після цього прихоплюють оболонки впритул полуавтоматом у двох точках з відривом 5 мм від галтели. Після прихваток випускають повітря з пневматичній камери, піднімають вал вгору й за знімають його з стенда.
Принципова схема стенда.
1. Півкільця; 2. Важелі; 3. Кронштейни; 4. Гумова прокладка; 5.
Оболонка; 6. Колінчатий вал; 7. Рама; 8. Пневматична камера.
Рис. 3.3.
3.. Розрахунок основних параметрів стенда.
Для якісного прилегания захисної металевої оболонки до чавунному колінчатому валу потрібно зусилля, стискаюче гумову прокладку, облегающую оболонку, на 1 мм [3].
Зусилля стискування отримано на закон Гука:
[pic], (3.1) де [pic] - переміщення (стиснення) гуми. Прийнято [pic]= 0,001 м.
L — товщина гуми. Прийнято L = 0,006 м.
Є - модуль пружності гуми. Прийнято для СКС — 30 Є = 8,4 МПа [26 стор. 166].
[pic] - зусилля стискування, Н.
А — площа гуми, [pic].
[pic], (3.2) де [pic] - діаметр шатунной шийки чавунного коленчатого[pic] вала.
Прийнято [pic] = 0,0675 м;
[pic]- товщина металевої оболонки. Прийнято [pic]= 0,0009 м;
[pic]- ширина шатунной шийки з відрахуванням галтелей. Прийнято [pic]= 0,048 м;
[pic][pic];
[pic], (3.3).
[pic]Н;
Остаточно приймаємо стискаюче зусилля [pic] = 15 кН.
Ескіз полуколец.
Рис. 3.4.
Внутрішній діаметр півкілець отримано з формулы:
[pic], (3.4) де [pic] - діаметр шийки чавунного колінчатого валу, м.
[pic]- товщина оболонки. Прийнято [pic]= 0,9 мм;
[pic]- товщина гуми. Прийнято [pic]= 6 мм;
Для шатунных шеек:
[pic] мм;
Прийнято [pic]= 80,5 мм;
Для корінних шеек:
[pic] мм;
Прийнято [pic]= 70,5 мм;
Ширина півкілець отримана з формулы:
[pic], (3.5) де [pic]- довжина шийки чавунного колінчатого вала;
R — радіус галтелей;
Для корінних шеек:
[pic]мм;
Для шатунных шеек:
[pic]мм;
Схема докладання сил.
Рис. 3.5.
Розміри L2, L3, L4, L5 — прийнято конструктивно:
L2, L3 — 40 мм, L4 — 50 мм, L5 — 30 мм.
Зусилля стискування механізму стенда [pic] - 15 кН.
[pic], (3.6).
[pic]кН;
По рекомендаціям [8] прийнято зусилля на штоку пневмапривода [pic]=6 кН.
[pic], (3.7).
[pic] кН;
Відстань L1 з знайдених усилий.
Розрахункова схема перебування L1.
Рис. 3.6.
[pic] кН;
[pic]; (3.8).
[pic] м;
3.3.1. Розрахунок привода.
Остаточно прийняте зусилля на штоку пневматичній камери [pic]= 6 кН.
Надлишкове тиск у магістралі рм. Прийнято рм = 0,6 МПа.
Діаметр мембрани, при толкающем зусиллі [8]:
[pic], (3.9) де [pic]- зусилля на штоке;
[pic]- коефіцієнт [pic];
[pic]- діаметр опорного диска;
[pic]- діаметр мембраны;
По рекомендаціям [8] приймаю рм — 0,6 МПа, [pic] - 0,6;
[pic]м;
Рекомендований максимальний хід поршня [8].
[pic], (3.10).
[pic]м;
Приймаю хід поршня P. S — 0.03 м;
По прийнятому зусиллю на штоку, з [8] приймаю мембранную камеру КПЦ — 600 ГОСТ 15 608–70 з характеристиками:
Максимально дозволене тиск магістралі рм — 0,6 МПа;
Діаметр мембрани (в заделке) Dм — 140 мм;
Діаметр штока Dшт — 16 мм;
Хід поршня P. S — 30 мм;
Максимальне зусилля на штоку Ршт — 6 кН;
Ще Одне зусилля Рм — 60 Н;
Жорсткість пружини З — 660 Н/м;
Схема пневмапривода принципиальная.
МК — мембранная камера;
Р — пневмораспределитель двухпозиционный, трехлинейный;
КР — клапан редукционный;
Ф — фильтр;
МН — манометр;
ВН — вентиль;
Рис. 3.7.
Принцип роботи пневмапривода:
Відкриття вентиля ВН повітря з пневмомагистрали направляють у фільтр очищення від багна й пилу. Манометр МН показує фактичне тиск у лінії. Після очищення, повітря проходить через клапан редукційний КР для стабільну роботу приводу при перегонах тиску в основний магістралі, де тиск повітря знижується до 0,6 МПа. Після клапана редукционного повітря потрапляє у пневмораспределитель двухпозиционный, трехлинейный ручного дії. У першому крайньому становищі, повітря направляють у мембранную камеру, де виробляє роботу руху поршня. У другому становищі основна магістраль перекрита, а робоча порожнину мембранної камери сполучається з атмосферою й під дією поворотній пружини шток мембранної камери повертається у вихідне положение.
По рекомендаціям [8] розрахована ефективна площа перерізу трубопровода.
[pic], (3.11) де P. S — хід поршня;
Ршт — зусилля на штоке;
Рм — тиск у магистрали;
Uу — безмірний коефіцієнт [8 Рис. 7.7];
Для визначення Uу потрібно визначити 1/x і Хпр.
1/x — безрозмірний коефіцієнт площі мембраны;
Хпр — безрозмірна жорсткість пружины;
[pic], (3.12) де F — площа мембраны;
[pic], (3.13) де D — діаметр мембраны;
[pic] [pic];
[pic];
Безрозмірна жорсткість пружины:
[pic], (3.14) де З — жорсткість пружины;
[pic];
По [8 Рис. 7.7] знаходимо Uу — 6,3;
[pic] мм;
За даними [8] прийнято трубопровід металевий з зовнішнім діаметром 8 мм завтовшки стінки 1,6 мм, труба бесшовная холоднодеформированная з коррозионно-стойкой стали ГОСТ 9941–72. Довжина еквівалентного трубопроводу Lэ = 2,1 м.
За даними [26] принимаю:
Пневмораспределитель В71 — 22А ТУ 2−053−1787−86, діаметр проходу Dу — 6 мм, максимальне тиск Рmax = 1МПа;
Фільтр повітряний ФВ6−03 ТУ 25.280 666−80, робочий тиск Р = 0,3 — 0,9 МПа;
Пневмоклапан редукційний БВ57−3 ГОСТ 18 468–79, діаметр проходу Dу — 6 мм, максимальне робочий тиск Р = 1 МПа;
Вентиль ПОВ-1 ТУ 25−02.380 516−80;
Манометр надлишкового тиску МП ТУ 25.02.180 315−78, діаметр корпусу Dк — 100 мм, верхній межа Р = 1 МПа;
4.. Прочностной розрахунок деталей.
По заданим силам і знайденим плечам розрахований шарнір Проте й важіль Т.
Розрахункова схема шарніра Проте й важеля Т.
Рис. 3.8.
[pic]; [pic];
(3.15).
[pic]; при [pic]= 0;
[pic]; при [pic]= 0,04;
Небезпечна перетин у шарніра А. Попередньо призначаю важіль з перерізом У = 25 мм, h = 25 мм, матеріал сталь 45 з розрахунковим опором по межі плинності R = 360 МПа. Діаметр шарніра — 12 мм.
[pic], (3.16).
Для прямоугольника:
[pic], (3.17).
Для круга:
[pic], (3.18).
Для важеля полностью:
[pic], (3.19).
[pic][pic] ;
[pic] Па ;
[pic];
Обраний перетин важеля забезпечує прочность.
Шарнір, А перевіряємо на зусилля зрізу і смятия.
Схема докладання їхніх зусиль до шарниру А.
Рис. 3.9.
Умова міцності по срезу:
[pic], (3.20) де Р — зусилля зрізу; d — діаметр шарніра; до — число зрізів, до = 2;
Rср — розрахункове опір срезу.
Для стали 45 прийнято Rср = 150 МПа;
Приймаю зусилля зрізу Р = 10,5 кН, з розрахункової схеми Рис. 3.8.
Діаметр шарнира:
[pic], (3.21).
[pic]м ;
Умова міцності по смятию:
[pic], (3.22) де Rсм — розрахункове опір при смятии.
Для стали 45 прийнято Rсм = 610 МПа;
Р — зусилля смятия. Прийнято Р = 10,5 МПа;
Асм — площа поверхні смятия, [pic].
[pic], (3.23) де d — діаметр шарніра. Прийнято d = 12 мм;
[pic] - сума мінімальних толщин аркушів направлених ним у одну бік. Прийнято [pic]= 16 мм.
[pic] [pic];
[pic];
[pic];
Аналогічно розраховуємо шарнір В.
Зусилля зрізу для шарніра У одно Р =6 кН.
Діаметр шарнира:
[pic];
Зусилля смятия для шарніра У одно Р = 6 кН.
[pic] прийнято 10 мм, Рис 3.10.
[pic];
[pic];
[pic];
Схема докладання їхніх зусиль до шарниру В.
Рис. 3.10.
3.5. Проектування штампа.
Процес виготовлення захисних металевих оболонок складається з наступних операцій: очищення знежирення аркуша, розрізування його за смуги, вирубування з смуг заготовок для оболонок Рис. 3.11, гнучка країв оболонок Рис. 3.12, гнучка середині оболонок Рис. 3. 13.
Ескіз штампа для вирубки оболочек.
Рис. 3. 11.
Розмір оболонок визначено розрахунковим шляхом з таких зависимостей:
Довжина оболочки:
[pic], (3.24) де [pic]- діаметр шийки чавунного колінчатого валу, мм;
[pic]- товщина оболонки, мм;
Ширина оболочки:
[pic], (3.25) де [pic]- ширина шийки чавунного колінчатого валу, мм; r — радіус галтели, мм;
Отримані розміри занесені в табл. 3.1.
[pic].
Ескіз штампа для гнучкі країв оболочки.
Рис. 3. 12.
Діяльність [3] приведено схема штампа для гнучкі країв оболонок до чавунному валу двигуна ГАЗ — 21. За підсумками цієї схеми й рекомендацій [28 Т.2] призначаю розміри У, в, R, r і заношу в табл. 3.2.
[pic].
Решта розміри призначаю з конструкції штампа.
Ескіз штампа для гнучкі середині оболочки.
Рис. 3.13.
Розміри для штампа гнучкі середині оболонки призначаю аналогічно штампу для гнучкі країв, і заношу в табл. 3.3.
[pic].
3.6. Правила та інструкції технічної експлуатації штампа.
Спеціальні вимоги безпеки [29].
Перед початком работы:
1. Привести до ладу робочий одяг: застебнути всі ґудзики, заправити одяг те щоб був майоріючих на вітрі кінців, прибрати волосся під головного убору. Перед операцією вирубки з смуги, яку подають вручну чи заправляють в автоматичну подачу, надіти наладонники.
2. Роботу починати за тими пресах, які вивчені робітникам і до що їх допущен.
3. Перевірити й переконатися справними: всіх частин пресу КПРС і правильності їх взаємодії; дії остановочно-пусковых пристосувань (важелів, пускових кнопок, педалей тощо. буд.); дії гальма і муфти зчеплення; заземляющего дроту й контактів його сполуки. В правильності установки штампа при штампування деталей на провал; І тут в плиті столу преса має бути отвір для виходу деталей і отходов.
4. Перевірити наявність захисних огороджень на обертових механізмах, особливо звернувши увагу до наявність огороджень небезпечної зони преса чи штампа.
5. Перевірити роботу преса на холостому ходу.
Під час работы:
1. Бути уважними під час роботи, не відволікатися сам і не відволікати інших. Приступати на роботу лише з справному прессе.
2. При застревании деталі в штампі вимкнути прес й повідомити звідси майстру чи наладчику.
3. Не переключати самостійно роботу преса з встановленого наладчиком режима.
4. Не проводити самостійну налагодження й будь-які виправлення у преса чи штампа.
5. При отлучке з робочого місця зупинити прес і вимкнути электромотор.
Після закінчення работ:
1. Вимкнути електромотор. Привести до ладу робоче місце і його зміннику чи мастеру.
2. Повідомити своєму зміннику і майстру про всіх помічених під час роботи неисправностях.
4. Економічна часть.
4.1. Техніко-економічні показники відновлення чавунних колінчастих валов.
Собівартість відновлених чавунних колінчастих валів двигуна ЗМЗ- 53А визначено розрахунком, наведеному в таблиці 4.1 Дані собівартості колінчастих валів відремонтованих шлифованием взято у бухгалтерії ВАТ НЗХК. Дані відновлення наплавкой взято [3].
Таблиця 4.1.
[pic].
Найнижча вартість мають чавунні колінчасті вали, відремонтовані шлифованием під ремонтні розміри, тому при відновленні необхідно прагнути, щоб наплавленный метал забезпечував зокрема можливість використання всіх ремонтних размеров.
Крім собівартості відновлених чавунних колінчастих валів необхідно враховуватиме й інші показники, зокрема зносостійкість і можливість використання шляхом шлифования під ремонтні размеры.
За її методикою Єфремова Е.Е. [24] кожен спосіб відновлення характеризується з допомогою вартісного вимірника, що висловила видатки деталь в рублях на 1000 км пробігу автомобиля.
[pic], (4.1) де, Sр — вартість витрат за відновлення детали;
Х — коефіцієнт відносної зносостійкості деталі після його восстановления;
Lнх — пробіг автомобілі з відремонтованої деталью.
Lн — пробіг автомобілі з нової деталью;
Зносостійкість чавунних колінчастих валів двигунів ЗМЗ-53А нових, відновлених шлифованием. Вибродуговой наплавкой. Наплавкой удвічі шару під легирующим флюсом й у два шару порошкової дротом, під легирующим флюсом по оболонці перебуває одному рівні, тому коефіцієнт зносостійкості прийнято рівним одиниці. Нові й відновлені чавунні колінчаті вали використовують багаторазово. Зважаючи на це, вартісної вимірювач буде равен:
[pic][pic], (4.2) де Sр1-себестоимость восстановления;
Sр2- собівартість ремонту шлифованием під ремонтні размеры;
L1-пробег автомобілі з відновлених чавунним колінчатим валом;
L2-пробег автомобілі з чавунним колінчатим валом після ремонту шлифованием; n-количество використовуваних ремонтних размеров;
Середній пробіг автомобілі з капітально відремонтованим двигуном становить 65 тис. км [3], після цього пробігу значної частини колінчастих валів має невеликі износы і з них придатні для експлуатації. Проте за авторемонтних заводах все колінчаті вали ремонтують шлифованием під найближчі ремонтні розміри, тому автомобілі з відновленими чавунними колінчатими валами мають і той середній пробіг 65 тис. км, після чого колінчасті вали або ремонтують, або выбраковывают.
Колінчаті вали, відновлені вибродуговой наплавкой, внаслідок збільшення кількості пір за глибиною шару використовують лише до третього ремонтного розміру включно і далі вибраковують, тобто. n=3. Нові чавунні колінчасті вали, наплавленные під шаром флюсу по оболонці і під флюсом удвічі шару внаслідок деформації під час експлуатації і нерівномірного зносу окремих шийок, ремонтують трохи більше 5 раз, тобто. n=5. Отже, загальний пробіг автомобілі з чавунним колінчатим валом, відновлених вибродуговой наплавкой становить 65+65*3=260 тис. км, а інших чавунних колінчастих валів 65+65*5=390 тис. км пробігу автомобиля.
Розрахунки з визначення витрат у рублях на 1000 км пробігу автомобіля, початку відновлення до вибраковки колінчатого валу, наведені у таблиці 4.2.
[pic].
Як очевидно з табл. 4.2 всі засоби наплавки економічно доцільні, але, оскільки техніко-економічний коефіцієнт критерію вибору раціонального способу при наплавленні під легирующим флюсом по оболонці найменший, отже, цей спосіб вважатимуться більш прийнятним порівняно з другими.
5. Охорона труда.
5.1. Стан умов праці при працях з восстановлению.
чавунних колінчастих валов.
Технологічний відновлення чавунних колінчастих валів включає у собі ряд несприятливих, для виконавців робіт, чинників. Небезпеки, які відбуваються на робочих місць, поділяються на імпульсні і аккумулятивные.
Джерелами імпульсних небезпек є рухливі маси, потоки повітря, газів і рідин, незаземленные джерела електричної енергії, неправильне розміщення устаткування робоче місце. Імпульсна небезпека, яка веде до травмі, миттєво реалізується у випадкові моменти часу й то, можливо представлена дискретної, випадкової функцією виробничого процесса.
Джерелами аккумулятивных небезпек є: підвищений шум, вібрація, забрудненість повітряної середовища газами і парами. Через війну дії цих факторів організм людини перевтомлюється, порушується координація рухів, притупляється реакція організму на зовнішні подразники. Аккумулятивная небезпека реалізується протягом усього виробничого процесу, представляючи його безперервну функцію, і призводить до підвищеному стомленню і заболеваниям.
На робочих місць зварювання і наплавки присутні такі шкідливі чинники як ультрафіолетове випромінювання, виділення шкідливі речовини процесу згоряння, надлишкове виділення теплоты.
На робоче місце шлифовщика присутній підвищений вміст абразивною суспензії повітря, шум при обробці изделий.
На робоче місце токаря і слюсаря присутній підвищений шум, є небезпека отримати травму від обертових частин устаткування. До травмі можуть призвести як і потрапляння стружки в глаза.
На робоче місце мийника робочим тілом є вода, температура яких становить 90 градусів. Існує можливість отримання ожогов.
У зв’язку з тим, що технологічний відновлення чавунних колінчастих валів призначений для не великих ділянок ремонтних підрозділів МШС переважно розміщених в старих приміщеннях, часто мають не достатньо висвітлення, соціальній та зв’язку з, що однією з найбільш об'ємної зусиль для відновленню чавунних колінчастих валів є операції шлифования, зроблено розрахунок штучного висвітлення робочому місці шлифовщика.
5.2. Аналіз шкідливих і найнебезпечніших чинників шлифовального отделения.
.
| | | | | | |Таблиця 5.1 | |Робоча |Небезпечні й |Характеристика небезпечних і шкідливих чинників | |місце |шкідливі | | | |чинники | | |Круглошл|Шум |Шум як фізіологічне явище представляє| |ифовальн| |собою несприятливий чинник зовнішнього середовища й| |ый | |окреслюється звуковий процес, | |верстат | |несприятливий до і заважає | |3Б161 | |роботи і відпочинку. По фізичну природу шум, | | | |створюваний оборудованнием, обумовлений | | | |процесами механічного впливу | | | |деталей. | | |Освітленість |Світло природно умовою | | | |життєдіяльності чоловіки й грає велику | | | |роль збереженні здоров’я дитини і високої | | | |працездатності. Недостатня | | | |освітленість вимагає як постійного | | | |напруги очей, що зумовлює | | | |перевтомі та зниження працездатності, | | | |але й можуть призвести до того що, що буде | | | |незамечены окремі огріхи в | | | |виготовленні. | | |Небезпека |Працюючи верстата обертовою його частиною | | |травмування |є шліфувальний коло і оброблювана | | |обертовими |деталь, тому є велика небезпека | | |частинами. |травмування обертовими частинами при | | | |роботі. | | |Небезпека |Працюючи колінчаті вали подаються до | | |травмування |робочому місцю кран-балкою, тому може | | |під час роботи з |виникнути аварійна ситуація внаслідок | | |підйомними |обриву троса, неправильного кріплення вантажу | | |механізмами |та інші чинниками, пов’язані з | | | |експлуатацією підйомно-транспортного | | | |устаткування. | | |Пожароопасност| На робоче місце шлифовщика є | | |и |мастильні матеріали, які можна | | | |розлиті і за недбалому ставлення до заходам | | | |пожежної безпеки може виникнути | | | |пожежа. | | |Небезпека |У його устрої шліфувальний верстат має| | |поразки |електрообладнання, необхідне його | | |електричним |функціонування, тому наявність | | |струмом |електроустаткування і токоведущих частин при| | | |неправильної експлуатації і недотриманні | | | |правил техніки безпеки електроустановок| | | |можуть призвести з ураженням обслуговуючого | | | |персоналу електричним струмом. |.
5.3. Вимоги нормативно-технічної документації з охорони труда.
Таблиця 5.2 |Вимоги |Нормативний | | |документ | |Робоча місце, його обладнання та оснащение,|ГОСТ 12.2.061−81. | |застосовувані відповідно до характером |Устаткування | |роботи, повинні гарантувати безпеку, | | |охорону здоров’я та перемоги працездатність | | |працюючих | | |Шум робочому місці ні перевищувати 80 |ГОСТ 12.1.003−83. | |дБА. |Шум. Загальні | | |вимоги | | |безпеки. | |Виробниче обладнання має мати |ГОСТ 12.2.003−74. | |убудоване пристрій видалення | | |що виділяються своєю практикою шкідливих | | |речовин безпосередньо від місця їх | | |освіти і скупчення. | | |Штучне висвітлення виробничих |СНиП II-4−79 | |приміщеннях має устаиваться з лампами | | |розжарювання чи люмінесцентними лампами в | | |вигляді загального освітлення з рівномірним чи | | |локалізованим розміщенням світильників і | | |комбінованого (спільного освітнього і місцевого). | | |Застосування одного місцевого висвітлення не | | |допускається. Норма освітленості робочого | | |місця повинна бути при загальному висвітленні | | |300 лк. | | |Приводні частини устаткування, і навіть |ГОСТ 12.2.002−80. | |передачі, яких може бути доступ людей, |Огорожі. Загальні | |повинні прагнути бути обгороджені. |вимоги. | |Рухомі і обертові елементи |ГОСТ 12.2.027−80. | |устаткування, яких може бути доступ |Устаткування | |обслуговуючого персоналу, мали бути зацікавленими |гаражне і | |обгороджені зусебіч і по довжині, |авторемонтне. | |незалежно від висоти розташування швидкості| | |руху. | | |Органи управління, пов’язані з певною |ГОСТ 12.2.064−81. | |послідовністю їх застосування, повинні |Органи управління | |групуватися в такий спосіб, щоб действия|производственным | |працюючого здійснювалися зліва праворуч і |устаткуванням. | |згори донизу. | | |У конструкціях органів управління, |ГОСТ 12.2.027−80. | |виділені на включення устаткування, | | |мають бути передбачені засоби захисту від| | |випадкового включення. | | |Електрична схема устаткування повинна |ГОСТ 12.2.007−75. | |виключати можливість його мимовільна |Вироби | |умикання/вимикання. |електротехнічні. | | |Загальні вимоги. |.
5.4. Заходи з захисту робочих від небезпечних і шкідливих факторов.
Щоб зменшити чи виключити взагалі, вплив небезпечних і шкідливих чинників на людини необхідний ціле пасмо заходів для охорони труда.
Методи боротьби з шумом:
Однією з методів боротьби із гамом є застосування звукопоглинальних матеріалів для обличкування стін, стель та статі виробничих помещений.
Як оперативного способу профілактики шкідливого впливу шуму на працюючих доцільно використовувати наявні кошти індивідуальної захисту, зокрема потивошумные навушники. Навушники знижують рівень звукового тиску від 3 до 36 дБ.
Пристрій освещения:
Під час проведення шліфувальних робіт є раціональне висвітлення, що дозволяє ознайомитися з об'єктом, над роботою оборудования.
Вихідні данные:
Розміри приміщення: довжина 7,5 м, ширина 5,2 м, висота 6 м.
У приміщенні виробляється обробка металу шлифованием. Параметри середовища — нормальні, стелю — бетонний, брудний, стіни — брудні, підлогу — темный.
Приймаю нормируемые параметри освітленості відповідно до (п 11.1 табл. 2.2.1 [30] і пп. 4.12 і 4.15 [31]) і заношу в табл. 5.3.
[pic].
Согласно (п 11.1 табл. 2.2.1[30]) приймаю систему загального освітлення. Приміщення шліфовки чавунних колінчастих валів, ділянки відновлення, не містить і обробляє матеріали здатні утворити вибухонебезпечні суміші. Приміщення не вибухонебезпечне. Приміщення шлифовального відділення не пожежонебезпечна П — 111 ([32] табл. П.3). З (табл. П. 3 [32]) для газорозрядних ламп і класу пожароопасности П — 111 потрібно ступінь захисту 1Р23. Приймаю тип КСС з ([32] табл. П.7), тип кривою сили світла Р. Приймаю по ([32] табл. П.9) тип світильника рівня захисту 1Р23, кривою сили світла Р, класу светораспределения П, табл. 5.4.
[pic].
Для розрахунку приміщення шлифовального відділення використаний метод світлового потока.
Индекс помещения:
[pic], (5.1) де, а — довжина приміщення; в — ширина помещения;
[pic]- розрахункова висота освітлювального приладу над робочої поверхнею. Прийнято [pic]= 6 м.
[pic] Коефіцієнт використання світлового потока:
[pic], (5.2) де [pic]- ККД світильника. По (табл. П. 8 — П. 10 [32]) прийнято 0,7;
[pic]- ККД приміщення. По (табл. П. 12 [32]) прийнято при:
[pic]- коефіцієнт відображення стелі (П. 13 [32]) прийнято [pic]= 50%;
[pic]- коефіцієнт відображення світла кольоровими поверхнями. По (табл. ПП.14 [32]) приймаю [pic]= 0,41%; Приймаю [pic]= 0,41.
[pic]; Потрібне кількість светильников:
[pic], (5.3) де n — число рядів світильників; m — число світильників в ряду;
[pic], (5.4) де [pic]- відстань між сусідніми светильниками.
[pic], (5.5).
[pic], (5.6) де [pic]- коефіцієнт [pic] для типу КСС, прийнято з (табл. П. 15 [32]) [pic]=1,1.
[pic] м ;
[pic];
[pic]; Приймаю m = 1, n = 1;
[pic]шт; Необхідний світловий потік светильника:
[pic], (5.7) де [pic]- нормативна мінімальна освітленість розрахункової поверхні, лк;
P.S — площа приміщення, [pic], прийнято P. S = 38,8 [pic];
Z — коефіцієнт [pic], прийнято при точковому розташуванням світильників рівним 1,15 [32];
[pic]- коефіцієнт запасу, приймаю по (табл. 1.1 [30]) [pic]= 1,8;
[pic]лм; Приймаю по (табл. П. 16 — П. 20 [32]) для розрахункової поверхні лампи: РСП05 потужністю 700 Вт, напругою 140 У, світловим потоком 40 000 лм. Для необхідного світлового потоку Ф = 83 954 лм беру два світильника загальним світловим потоком Ф = 80 000 лм. Світловий потік у межах допуску — 10% + 20%.
5.5. Техніка безопасности.
.
5.5.1. Загальні требования.
Верстат може бути заземлен.
Не допускаються до управління верстата особи, які пройшли навчання й не атестовані за фахом шліфувальник, і навіть особи, до 18-ти лет.
Забороняється робота на несправному устаткуванням, при несправному захисному кожухе.
Працюючи на верстаті обов’язково користуватися захисним экраном.
5.5.2. Вимоги до початку работы.
Перед початком роботи робочий зобов’язаний оглянути і перевірити технічне стан вузлів і деталей верстати й переконатися у їх исправности.
Перевірці на справність і надійність подлежат:
— і захисні кожухи обертових вузлів верстата, і навіть їх крепление;
— заземлення верстата, (визуально);
— висвітлення робочого места;
— систему управління стендом.
Працювати на верстаті, що має несправності, забороняється. Необхідно переконатися у на робоче місце коштів індивідуальної захисту, коштів пожежогасіння й коштів надання першої медичної помощи.
5.5.3. Вимоги під час работы.
За появи під час роботи верстата сторонніх шумів, стукотів тощо. верстат необхідно відключити і перевірити, звідки виходять дані ознаки неисправности.
Під час роботи запрещается:
— позбуватися виконання прямих обязанностей;
— виходити із приміщення при що працює оборудовании;
— передавати управління верстатом особам, які мають цього разрешение.
При припинення подачі електроенергії робітник повинен відключити верстат від сети.
5.5.4. Вимоги після закінчення работ.
Після закінчення робіт робочий обязан:
— вимкнути верстат і започаткувати його уборку;
— зробити необхідні запис у журналі приймання і здавання смены.
5.5.5. Вимоги в аварійної ситуации.
У разі аварійної ситуації робочий зобов’язаний відключити стенд від сіті й повідомити звідси своєму безпосередньому руководителю.
Заключение
.
З виконаної роботи можна зробити такі выводы:
Запропонована технологія автоматичної наплавки високоміцного чавуну під флюсом по оболонці дозволяє значною мірою підвищити працездатність відновлених колінчастих валів завдяки усуненню в наплавленном металі дефектів (пір і тріщин) і підвищення усталостной прочности.
Технологічний процес складається з чотирьох етапів восстановления:
— Підготовка шийок валу до б складальним операциям;
— Складання шийок валу і захисних оболочек;
— Наплавочные операции;
— Механічна обробка шийок валу під номінальні размеры.
Технологія відновлення содержит:
— Розрахунок і вибір оборудования;
— Технологічне нормування операцій;
— Розрахунок виробничого участка.
— Вибір технологічної оснастки;
Конструкція розробленого стенда для прихватки захисної оболонки до шейкам валу дозволяє частково механізувати операцію зварювання, що дозволить знизити трудовитрати з цього операцію і применшити виробничий травматизм.
У цьому дипломному проекті є і не вирішені задачи.
— Необхідний пошук рішень щодо підвищенню відсотка завантаження слюсарних, мийних, токарних операций.
— Потрібна експериментальна перевірка працездатності технологічного процесу відновлення чавунних колінчастих валов.
1. Клочнев М. І. Високо-випробувальний чавун з кулястим графітом. М.,.
Машгиз., 1963. 2. Кудрявцев І. У. Конструкційна міцність чавуну з кулястим графитом.
М., Машгиз., 1957. 3. Доценка Р. М. Відновлення чавунних колінчастих валів автоматичної наплавкой. М., Транспорт., 1970. 56 з. 4. Марковський Є .А. Зносостійкість чавунів з кулястим графітом //.
Високо-випробувальний чавун. Київ, 1964. 5. Краснощеков М. М., Пахомов Б. П., Марковський Є. А. Дослідження зносостійкості колінчастих валів методом радіоактивних ізотопів //.
Трактори і сільгоспмашини. 1962. № 2. 6. Доценка Р. М. Зносостійкість і усталостная міцність чавунних колінчастих валів ГАЗ — 21, нові й відремонтованих. // Автомобільна промисловість. 1969. № 2. 7. Середенко Б. М. Зносостійкість високоміцного чавуну, які у тракторостроении. // Наукові праці ин-т машиноведения і переробка сільськогосподарської механізації. Київ, 1958. Т. 4. 8. Герц Є. У., Крейнин Р. У. Розрахунок пневмоприводов. М., 1975. 271 з. 9. Луппиан Р. Еге., Симонятов У. Р. Відновлення вибродуговой наплавкой в кисні чавунних колінчастих валів М — 21. // Автоматична наплавка.
1968. № 4. 10. Спиридонов М. У. Плазмові і лазерні методи зміцнення деталей машин. Мінськ, 1988. 155 з. 11. Хасуи А. Наплавлення і напилювання. М., 1985. 239 з. 12. Гуляєв А. П. металознавство. М., 1966. 13. Лебедєв Б. І. Усадка железно-углеродистых сплавів пов’язана з ній явище — освіту гарячих тріщин. // Автореферат канд. дисертації. /.
Л., 1956. 14. Доценка М. І. Відновлення колінчастих валів автоматичної наплавкой. М., 1965. 15. Полиновский Л. А. Розрахунок припусков на механічну обработку.
Визначення точності обробки. Методичні вказівки до виконання лабораторних і практичних робіт. Новосиб., СГУПС. 1988. 12 з. 16. Єгоров М. Є. Основи проектування машинобудівних заводів. М.,.
1969. 17. ОНТП-14 — 86. Норми технологічного проектування підприємств машинобудування. М., 1987. 96 з. 18. Розрахунок режимів різання при механічної обробці металів і сплавов.
Методичне посібник. Хабаровськ. 1997. 83 з. 19. Общемашиностроительные нормативи часу на слюсарну обробку деталей і слесарно-сборочные роботи з складанні машин і приладів у умовах масової, крупносерійного і среднесерийного типів виробництва. М.,.
1991. 158 з. 20. Общемашиностроительные нормативи часу для технічного нормування робіт на металорізальних верстатах, дрібносерійне і одиничне производство.
Ч. 1. М., 1967. 315 з. 21. Общемашиностроительные нормативи часу для технічного нормування робіт на шліфувальних і доводочных верстатах (укрупнені). М., 1974. 112 з. 22. Нормативи для технічного нормування робіт, за автоматичної электродуговой зварюванні під шаром флюсу. М., 1954. 142 з. 23. ОНТП-14 — 90. Норми технологічного проектування підприємств машинобудування. М., 1991. 115 з. 24. Єфремов У. У. Ремонт автомобілів. М., 1965. 25. Бежанов Б. М. Пневматичні механізми. М., 1957.251 з. 26. Герц Є. У. Пневматичні пристрої і системи у машинобудуванні. М.,.
1981. 27. Гідравлічне і пневматичне устаткування загального призначення, изготавливаемое з СНД, Литві, Латвії. М., 1982. 123 з. 28. Кування і штамповка. Довідник. В. 4-х т. М., 1985. Т. 2. 29. Збірник типових інструкцій технічно безпеки. М., 1994. 432 з. 30. ОСТ 32 — 9 — 81 ССБТ. Норми штучного висвітлення об'єктів залізничного транспорту. М., 1982. 40 з. 31. СНиП 11 — 4 — 79. Природний і штучне висвітлення. М., 1980. 48 з. 32. Розрахунок і проектування штучного висвітлення виробничих приміщень та відкритих майданчиків. Методичні вказівки до вирішення задач.
Новосибірськ. 1989. 30 с.
Рецензія на дипломний проект студента СГУПСа Ббббббб Олександра Олеговича на задану тему: «Технологічний відновлення колінчастих валов».
Дипломний проект представлений расчетно-пояснительной запискою обсягом 92 сек. і 8 кресленнями формату А1.
Дипломний проект присвячений актуальною проблемою відновленню чавунних колінчастих валів автотракторних двигунів. За основу автором взятий спосіб відновлення наплавкой по захисної металевої оболонці. Технологічний процес за складом операцій, прийнятому устаткуванню і з технологічної оснастці можна зараховувати до категорії легко реалізованих, тому цю роботу то, можливо впроваджена ремонтних дорожніх майстерень. Технологічний процес пропрацьований досить глибоко, прийняті рішення обгрунтовані розрахунками. Розроблений стенд для обтиску сталевої оболонки дозволяє значною мірою механізувати операції складання перед наплавкой.
У місці про те треба сказати деякі недоліки проекта:
— Запропонований ділянку на відновлення чавунних колінчастих валів не прив’язаний до конкретного предприятию;
— Робітники місця на операціях складальної і слюсарної завантажені недостатньо 3% і 4% соответственно.
— Конструкцію стенда бажано було спроектувати многопозиционным, що дуже скоротило б оперативне время.
Не дивлячись на зазначені недоліки дипломний проект, заслуговує відмінній оцінки, а студент дипломник Ббббббб Олександр Олегович присвоєння кваліфікації інженера механика.
Начальник ділянки № 2 цеху 10.
ВАТ Рррррр А.И.
16.06.99.