Зварювання металів
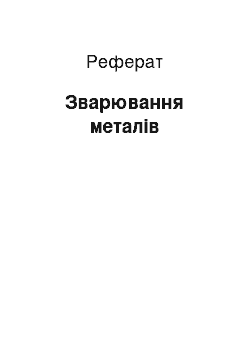
Газова зварювання застосовують у багатьох галузях промисловості при виготовленні і ремонті виробів із тонколистовий стали, зварюванні виробів із алюмінію та її сплавів, міді, латуні та інших кольорових металів та його сплавів. Різновидом газопламенной обробки є газотермическая різка, яка широко застосовується і під час заготівельних операцій при раскрое металу. Контактна зварювання посідає чільне… Читати ще >
Зварювання металів (реферат, курсова, диплом, контрольна)
1.
Введение
.
2. Призначення вироби, конструкция.
3. Вибір зварювального устаткування, пристосування, і инструменты.
4. Матеріали, застосовувані при сварке.
5. Вимоги до підготовки деталей під сварку.
6. Вибір орієнтованих режимів сварки.
7. Процес зварювання (технологія й техника).
8. Контроль якості зварювальних сполук (готових виробів і конструкций).
9. Техніка безпеки і пожежні заходи і під час зварювальних работ.
10. Використана литература.
1.
ВВЕДЕНИЕ
.
1) У разі науково-технічного прогресу особливо важливо розвиток які його областей науки, техніки і виробництва. Практично ні ні галузі машинобудування, приладобудування і питання будівництва, у застосовувалися б зварювання і різка металів. З допомогою зварювання отримують неразъемные сполуки майже всіх металів і сплавів різної товщини — від сотої частки міліметра за кілька метров.
У 1802 р. російський академік В. В. Петров у світі відкрив і описав явище електричної дуги, і навіть зазначив зокрема можливість використання її теплоти для розплавлювання металів. У 1882 р. російський академік М. М. Бенардос винайшов спосіб дугового зварювання із застосуванням вугільного електрода. У 1888 р. російський інженер-металург Н. Г. Славянов розробив металургійні основи дугового зварювання, створив перший автоматичний регулятор довжини зварювальної дуги і виготовив першим у світі зварювальний генератор.
За рівнем розвитку зварювального виробництва Росія головна країною у світі. У 1969 р. на борту космічного корабля «Союз-6» Валерій Кубасов з допомогою установки «Вулкан» провів автоматичну электроннопроменеву і дугову зварювання і різання металів у космосі; в 1984 р. на борту космічного корабля «Салют-7» Світланою Савицкой та архітектором Володимиром Джанибековым виконані ручна зварювання, різка, пайка і напилювання металів у відкритому космосе.
2) Зварюванням називається процес одержання неразъемных сполук через встановлення межатомных перетинів поміж свариваемыми частинами при їх нагріванні чи пластичному деформировании, чи спільному дії того чи іншого (ГОСТ 2601−84). Розрізняють два виду зварювання: зварювання плавленням і зварювання давлением.
Сутність зварювання у тому, що метал по крайкам свариваемых частин оплавляется під впливом теплоти джерела нагріву. Сутність зварювання тиском полягає у пластичному деформировании металу по крайкам свариваемых частин шляхом їх стискування під навантаженням за нормальної температури нижче температури плавления.
До зварюванні плавленням належить і газова зварювання, коли він для нагріву використовується тепло полум’я суміші газів, сжигаемой з допомогою пальники (ГОСТ 2601−84). Спосіб газової зварювання було розроблено на кінці минулого століття, коли почалося промислового виробництва кисню, водню і ацетилена.
Газова зварювання застосовують у багатьох галузях промисловості при виготовленні і ремонті виробів із тонколистовий стали, зварюванні виробів із алюмінію та її сплавів, міді, латуні та інших кольорових металів та його сплавів. Різновидом газопламенной обробки є газотермическая різка, яка широко застосовується і під час заготівельних операцій при раскрое металу. Контактна зварювання посідає чільне місце серед механізованих способів зварювання. Особливість контактної зварювання — висока швидкість нагріву й одержання зварного шва, це дає умови застосування високопродуктивних потокових і автоматичних ліній складання вузлів автомобілів, опалювальних радіаторів, елементів приладів та радіосистем. Зварювання плавленням залежно від різних способів, характеру джерел нагріву і розплавлювання свариваемых крайок деталей можна умовно розділити ми такі основні виды:
— електрична дуговая, де джерелом теплоти є електрична дуга;
— електрична зварювання, де джерелом теплоти є розплавлений шлак, з якого протікає електричний ток;
— електронно-променеве, коли він нагрівання і розплавляння металу виробляється потоком электронов;
— лазерна, коли він нагрівання і розплавляння металу відбувається сфальцьованим потужним променем мікрочастинок — фотонов;
— газова, коли він нагрівання і розплавляння металу відбувається поза рахунок тепла полум’я газової горелки.
2. ПРИЗНАЧЕННЯ ВИРОБИ, КОНСТРУКЦИЯ.
Оболонка корпусу, що складається з днищевого, двох бортових і палубного перекриттів, підкріплюється зсередини поперечними і поздовжніми перебираннями і проміжними палубами і платформами, необхідність яких, і навіть їх кількість і місцезнаходження визначаються розмірами і призначенням судна.
Разом з краями і штевнями вони утворюють основний корпус і ставляться тож числу основних конструктивних елементів корпуса.
Зовнішня обшивка утворює непроникну оболонку, яка запобігає потрапляння води всередину судна згори (настил верхньої палуби), забезпечує плавучість судна (зовнішня обшивка) і непотоплюваність при ушкодженні зовнішньої обшивки днища (настил другого дна). З іншого боку, настил другого дна утворює междудонное пространство.
Зовнішня обшивка представляє ряд поясьев, які з окремих аркушів, розташованих довгою кромкою вздовж корпусу судна. Ширина поясьев — 1,5−2,5 м., але в великих судах — 3,0−3,2 м. Довжина аркушів — до 16 м.
Розбивка зовнішньої обшивки на поясья виготовляють кресленні розтяжки зовнішньої обшивки, що є зовнішньої обшивки одного борту на площину. Оскільки ширина розтяжки зовнішньої обшивки в краях менше, ніж у середині судна, поясья зовнішньої обшивки у районі оконечностей починають сужаться.
Щоб уникнути надмірного звуження у разі вводять втрати, тобто. поясья, у яких переходять два суміжних звужених пояса, заканчиваемы в одному сечении.
І тут виробляється завмер борту на судні 001 СБ.
Горизонтальний кіль у неповній середній частини судна роблять товщі прилеглих до нього поясьев днищевой обшивки. Ширстрек також утолщают.
Товщина аркушів зовнішньої обшивки в краях менше, ніж у середньої частини судна (крім судів льодового плавання). Для сполуки аркушів зовнішньої обшивки і настилів палуб та другого дна використовують зварювання. На судах, мають льодові підкріплення, бортова обшивка у районі ватерлінії робиться стовщена — це званий льодовий пояс. Крім нього, іноді утолщают листи, що примикають до великим вирізам в палубі (наприклад, у районі вантажних люків чи місцях з'єднання з поперечними перебираннями. Крайні що примикають до борта листи палубного настилу становлять палубний стрингер: його роблять товщі, ніж інші листи палубного настилу і мають вздовж судна. Як виняток іноді вдаються до плівці - на місці сполуки палубного стрингера з ширстреком, а за необхідності освіти так званих бар'єрних швів — у районі вилиці і з верхньої палубі. Бар'єрні шви, що йдуть вздовж судна, перешкоджають поширенню випадкових тріщин по всьому поперечному перерізу зовнішньої обшивки палубы.
При ремонті корпусів по Правилам регістру застосовуються стали нормальної міцності категорії А, У, Д, Є, врожаю та підвищеної міцності категорій А32, Д3, Е32, А36, Е36, А40, Д40, Е40.
Як еквівалентних для зазначених категорій стали ГОСТ 5521 передбачає такі марки:
— для стали категорії А — сталь Ст3 сп2, Ст3 сп3, Ст3 пс2, Ст3.
Гпс2;
— для В-сталь марок Ст3 сп4, Ст3 пс4, Ст3 Гпс4;
— для Д-сталь марки С;
— для, А 32, Д32, Є 32 — сталь марок 09Г2 і 09Г2С;
— для А36, Д36, Е36 — сталь марки 10Г2 С1Д;
— для Д40 і Е40-сталь марки 10 ХСНД (СХЛ-4).
У цьому конструкції використовується листовий метал марки ВСт3 сп.
Сталь марки Ст3 то, можливо киплячій, спокійною й полуспокойной. Сталь групи У за способом виробництва ділиться на мартенівську і конвеерную. Попереду марки стали ставиться позначення групи стали У і загальнодосяжний спосіб виробництва (М чи До). У сталях, виділені на зварних конструкцій, особливо точно регламентується зміст хімічних елементів, оскільки навіть незначне збільшення змісту вуглецю сірки і фосфору негативно впливає свариваемость ВСт3ст4.
Вуглець — 0,14−0,22.
Марганець — 0,40−0,65.
Кремній — 0,12−0,30.
Сірка — 0,055.
Фосфор — 0,045.
Ця сталь належить до добре свариваемым. Також ця сталь добре рубають гільйотиною і добре ріжеться газом.
3. ВИБІР ЗВАРЮВАЛЬНОГО УСТАТКУВАННЯ, ПРИСТОСУВАННЯ І ИНСТРУМЕНТЫ.
Щоб виготовити лист бортовий обшивки застосовуємо таке оборудование:
Тельфер — це невеличке підйомний кран, які перебувають всередині цеху, використовуваний для переміщення деталей по цеху.
Турбинка — це електрична машинка зі зняттям крайок і видалення проміжків зачистки металу. Вона складається з електричного двигуна і наждакового диска.
Гільйотина — варта рубки металу завтовшки від 5 мм выше.
Зварювальний перетворювач ПСО-500 — служить для перетворення змінного струму постійно струм, використовуваний для харчування зварювальної дуги. Перетворювач має генератор зварювального струму і електродвигун, що у загальному корпусі. Якір генератора електродвигуна розташований однією валу, підшипники якого прописані у кришках корпусу. На вал електродвигуна насаджений вентилятор, готовий до охолодження агрегату під час роботи. Для регулювання зварювального струму користуються маховичком реостату. При обертанні маховичка по годинниковий стрілці струм збільшується, а під час обертання проти годинниковий стрілки — зменшується. Величина зварювального струму вимірюється амперметром.
Для запалювання електрода і підвода щодо нього зварювального струму служить электродержатель. Відповідно до ГОСТ 14 651–69 электродержатели випускаються трьох типів залежно від сили зварювального струму: I типу — для струму 125 А; II типу — для струму 125−315 А; III типу — 315−500 А.
Щитки і маски виготовляються по ГОСТ 1361–69. матеріалом служить чорна волокнина чи пластмаса з матовій поверхнею. Маса щитка має перевищувати 0,48 кг, маски — 0,50 кг.
Для зачистки металу і зварного шва використовують: молотокшлакоотделитель (кіра), і металева щетка.
4. МАТЕРІАЛИ, ЗАСТОСОВУВАНІ ПРИ СВАРКЕ.
Електроди: через великого розмаїття застосовуваних покриттів діляться на типи за складу покриттів, а, по призначенню електродів і механічним властивостями (міці й пластичності) металу шва (наплавленного металу) і зварного сполуки, одержуваних під час зварювання електродами такого типу. Електроди Э42 свідчать, що електрод призначений для зварювання конструкційних сталей і відданість забезпечує межа міцності при стисканні 42 кгс/мм кв.
Електроди: СМ-11 дозволяють зварювати шви у кожному просторовому становищі й забезпечують отримання поплавленного металу без тріщин, з високої пластичністю, ударна в’язкість поплавленного металу під час зварювання цими електродами 14−16 кгс/мм куб. Можна вживати такі типи по ГОСТ (67−60 ЭЛУР-10, Э34, Э42, Э46 — для зварювання низьколегованих і низьковуглецевих сталей). Э45А, Э50, Э50А, Э55 — для зварювання среднелегированных і низьковуглецевих сталей. Э60, Э60А, Э70, Э85, Э100, Э125, Э145 — для зварювання среднеуглеродистых і низьколегованих сталей, які стосуються маркам ОМА-2, ОЗЦ-1, ОММ-5, ЦМ-7, АНО-1, ОЗС-3, МР-3, ОЗС-4, ОЗС-2, УОНИ-13/45, УОНИ-13/55, УОНИ-13/65,.
Зварювальна дріт використовують за Держстандарту 2246−40 і бывает:
— низкоуглеродистая — марки Св-08, Св-08А, Св-08АА тощо. у цій конструкції використовуємо електроди типу Э45А марки УОНИ-13/45.
УОНИ-13.
Електроди УОНИ-13 дають добре раскисленный щільний спрямований метал, у якому кілька більша кількість марганцю і кремнію і у якого високими механічними властивостями. Метал, спрямований електродами УОНИ-13, має високої щільністю, значної ударної в’язкістю, сягаючої 25−30 кгс/см2 для УОНИ-13/45 УОНИ-13/55 зазвичай, в металі, направленому електродами УОНИ-13, не утворюється тріщин. Тому електроди з покриттям УОНИ-13 начебто одні з найкращих і застосовуються для зварювання особливо відповідальних конструкцій, котрі мають ударні навантаження і вібрації, і навіть дію підвищених і знижених температур.
Оскільки покриття УОНИ-13 зовсім позбавлений органічних сполук (наприклад крохмалю) вони витримують тривале депотріскування (до 350−400°С), що полегшує їх просушку і робить менш сприйнятливими до влаге.
Зварювання електродами УОНИ-13 на перемінному струм необхідно включити в ланцюг осциллятор, який би стійке горіння дуги.
5. ВИМОГИ До ПІДГОТОВЦІ ДЕТАЛЕЙ ПІД СВАРКУ.
Заменяемая частина обшивки корабля готується в цеховому приміщенні з листового металу. На рівну поверхню вкладається лист металу, де виробляється розмітка, різка ацетилено-кислородным різаком чи рубання тванню і розбирання кромок.
Лінії контуру вирізу наскільки можна слід поєднувати зі своїми подстроечными зварними сполуками. У цьому в кожного кінця вирізу такі зварні сполуки повинні розпускатися на довжині, рівної 20 толщинам, але з більше 300 мм.
Слід уникати скупченості зварних швів, перетину їх під гострим кутом, і навіть близького розташування паралельних стиків швів і кутових зі стыковыми.
Відстань між паралельними зварними швами незалежно від своїх напрями має не менее:
— 200 мм — між паралельними стыковыми швами;
— 75 мм — між паралельними кутовим і стыковым швами;
— 50 мм — між паралельними кутовим і стыковым швами на довжині трохи більше 2 м.
Кут між двома стыковыми швами може бути щонайменше 60°.
Монтажні стики (пази) аркушів обшивки і настилів повинні розташовуватися від паралельних їм перегородок, палуб, настилу другого дна, рамних зв’язків і ін. з відривом щонайменше 200 мм.
Стикові зварні сполуки (лінія реза) обшивки і набору допускається поєднувати лише у плоскости.
При заміні зовнішньої обшивки зі збереженням набору вирізку аркушів роблять за кордоні замінного ділянки за розміткою, як від набору відокремлюють розтинаючи лист обшивки лінією притыкания набору, сплавляючи одночасно зварні шви. Далі за крайкам набору сплавляються залишки зварних швів, вириви наплавляются і зачищаются під зварювання до чистого металу абразивним инструментом.
Технологічні вирізи їх необхідно виконувати відповідно до кресленням і ТІ 02−00- 247. У цьому лінії реза обшивки і набору може бути суміщені чи рознесені. Набір, зазвичай, слід розрізати під деяким кутом до обшивке.
Перед вирізкою, за необхідності, по крайкам вирізу слід встановлювати якими планки, скоби тощо., предохраняющие вырезаемую конструкцію падінням, з приваркой обухів для строповки і демонтажу краном.
Слабодеформированные ділянки шпангоутів стрингеров у районі заміни обшивки выправляются з нагріванням дома, а значні деформації замінюються або ж після вирізки выправляются під пресом із наступною вваркой, якщо знос їх перевищує допустимих значений.
Після вирізки дефектних ділянок зовнішньої обшивки наявні гофрування по крайкам решти аркушів повинні поліпшуватися з нагріванням з допомогою виделки, домкратів і вручну ударами кувалдою на ширину 150−200 мм для можливості стикування нових листов.
При установці нових аркушів зовнішньої обшивки рекомендується для стикових швів застосовувати зварне з'єднання С45 по ГОСТ 5264–90. У цьому розбирання крайок і зварювання основного шва передбачати зсередини корпусу, а зовні воздушно-духовую строжку кореня шва із наступною заваркой.
Допускається одночасне виробництво сборочно-сварочных робіт з корпусу в районах, якщо де вони викликають у цілому негативне впливом геть посадку корпусу на кільовий доріжці і клітинах дока; не порушують подовжню міцність судна, знаходиться в плаву.
Приварку до конструкціям корпусу гребінок, скоб, планок, обухів тощо. мусить бути зведена до мінімуму. Виконання прихваток і приварку кріпильних деталей повинна перевірятися складальними матеріалами тих категорій, які потрібні для зварювання конструкцій. У прихватках неприпустимі пори, підрізи, прожоги, тріщини і заварені кратеры.
Видалення приваренных гребінок та інших тимчасових кріплень на конструкціях з вуглецевих і низьколегованих сталей виробляється шляхом руйнації прихваток вигином на шов.
Прихватки, решта на основному металі, після видалення тимчасових кріплень мали бути зацікавленими зачищені на зовнішньої обшивці снаружи.
На всіх стадіях виробництва зварних конструкцій має здійснюватися систематичний пооперационный контроль до зварювання. Перед зварюванням перевіряються: правильність складання сполук і вироби загалом. Особливе увагу слід звернути на правильність підготовки крайок, величину проміжків, збігів крайок, отчистку крайок й прилеглих до них ділянок основного металу, слід перевірити величину і якість прихваток, і навіть дотримання герметичних размеров.
Товщина металу аркуша" й борту — 10 мм.
Зазор між бортом і листом — 3 мм.
Розміри аркуша бортовий обшивки — 1400×800 мм.
6. ВИБІР ОРІЄНТОВАНИХ РЕЖИМІВ СВАРКИ.
Вибір режиму ручний дугового зварювання часто зводиться до визначення діаметра електрода і зварювального струму. Швидкість зварювання і непередбачуване напруження на дузі встановлюються самим зварником залежно від виду зварного сполуки, марки сталі та електрода, становища шва у просторі і т.д.
Діаметр електрода вибирається залежно від товщини металу, типу зварного сполуки, типу шва та інших. Струм вибирають залежно від діаметра електрода. Для вибору струму можна скористатися зависимостью:
I = Kd, де K = 25−60 А/мм d — діаметр електрода, мм.
Щодо малий зварювальний струм веде до хитливому горінню дуги, непровару й малої продуктивності. Надмірно великий струм веде до сильному нагріванню електрода під час зварювання, збільшення швидкості плавлення електрода і непровару, підвищеному разбрызгиванию електродного матеріалу і погіршення формування шва.
При зварюванні з вертикальними і горизонтальними швами струм може бути зменшений проти прийнятого для зварювання в нижньому становищі приблизно за 5−10%, а стельових на 10−15% про те, щоб рідкий метал не випливав із зварювальної ванны.
7. ПРОЦЕС ЗВАРЮВАННЯ (ТЕХНОЛОГІЯ І ТЕХНИКА).
Існує дві способу запалювання дуги покритими електродами — прямим відривом і відривом за дзвоновидною кривою. Перший спосіб називають запалюванням впритул. Другий нагадує йому рух при запалюванні сірники і тому її називають чирканьем.
Після запалювання дуги починається плавлення основного і електродного металів. На виробі утворюється ванна розплавленого металу. Зварювальник мав надавати електрод в дугу зі швидкістю, рівної швидкості плавлення електрода. Нормальною вважають довжину дуги, рівну 0,5−1,1 діаметра стрижня электрода.
Збільшення довжини дуги знижує стійке її горіння, глибину проплавления основного металу, підвищує втрати на чад і розбризкування електрода, викликає освіту шва з нерівній поверхнею та підсилюють шкідливий вплив оточуючої атмосфери на розплавлений металл.
Нахил електрода під час зварювання залежить від становища зварювальника в просторі, товщини і складу свариваемого металу, діаметра електрода, виду та товщини покрытия.
Для отримання щільного і рівного шва під час зварювання в нижньому становищі на горизонтальній площині кут нахилу електрода може бути 15° від вертикалі убік ведення шва.
Для отримання валика потрібної ширини виробляють поперечні коливальні руху електрода. Найчастіше застосовують шви шириною від 1,5 до запланованих 4 діаметрів електрода, отримані з допомогою поперечних коливальних рухів электрода.
8. КОНТРОЛЬ ЯКОСТІ ЗВАРЮВАЛЬНИХ ИЗДЕЛИЙ (ГОТОВИХ ИЗДЕЛИЙ І КОНСТРУКЦИЙ).
Усі види контролю за якістю зварювання можна розділити на дві основні группы:
I) неруйнівні види контроля.
II) руйнують види контроля.
Неруйнівні види контролю призначені виявлення як зовнішніх, і внутрішніх дефектів. Зазвичай зовнішні дефекти виявляються зовнішнім оглядом з допомогою міряльного інструмента, а внутрішні визначаються фізичними методи дослідження — просвічуванням рентгенівськими і гамма-излучением, ультразвуком, магнітним й найбільш простим і дешевим методом — гасова проба. Неразрушающий контроль залежить від тому, що зварної зразок чи виріб піддається дії відповідних импульсов.
Руйнують види контролю призначені визначення характеру, місця розташування розмірів дефектів та їх на працездатність зварних сполук. Руйнівний контроль здійснюється сверлением, технологічної пробою, механічними випробуваннями на розтягнення, вигин, зріз, удар, твердість, іноді гідравлічною чи пневматичним випробуванням зварних виробів з руйнацією їх. Надійним і дуже що застосовуються у справжнє час є радіаційний контроль просвічуванням зварних сполук рентгенівським і гамма-излучением. Дефекти виявляються як чорних плям на світлому тлі хорошого шва.
Ультразвукової спосіб виявлення дефектів зварювання грунтується на відображенні спрямованого імпульсу високочастотної звуковий хвилі. Ультразвукової контроль має такі основні преимущества:
— висока чутливість (1−2%), що дозволяє виявляти, визначати місцезнаходження і вимірювати невеликі дефекты.
(площею більш як 2 мм2);
— велика яка проникає здатність звукових хвиль, що дозволяє контролювати товсті матеріали (для стали до 2 м);
— можливість контролю тільки з одного поверхні зварного соединения.
Проте ультразвукової контроль має ще й недолік, що обмежує її застосування чи що ускладнює перевірку якості зварних швів; він виявляється у складності розшифровки дефектів шва через вплив внутрішньої структури (велике зерно, тонкодисперсные включення); складної конфігурації і орієнтації дефекту і найскладнішого виду зварного изделия.
Тому ультразвукової контроль часто застосовують тільки попереднім в поєднані із наступним просвічуванням швів рентгенівським чи гамавипромінюванням. За всіх випадках ультразвукової контроль швів повинен виконуватися висококваліфікованими і досвідченими операторами.
Магнітний вид контролю металу грунтується у тому, що з проходженні магнітних силових ліній по випробуваному матеріалу у місцях дефектів виникають поля розсіювання. Коли поверхні металу завдати ферромагнитный порошок, то над розташуванням дефекту буде створено скупчення порошку як правильно орієнтованого магнітного спектра.
Існують два способу контролю з допомогою магнітного порошку: сухою й мокрий. У першому випадку магнітний порошок (вохра, сурик, залізні тирсу, окалина тощо.) перебуває у сухому вигляді; у другий випадок магнітний порошок перебуває в підвішеному стані рідини (гасі, мильному розчині, воді). Сухим чином можна знайти як поверхневі, і глибинні дефекти; мокрим способом краще виявляються поверхневі дефекты.
Гидравлическому випробуванню піддаються різні судини, казани і трубопроводи, працюючі під тиском. Гідравлічною випробуванням контролюється як щільність зварних сполук, але й відносна міцність всієї зварної конструкції. При гідравлічному випробуванні посудину наповнюється водою; для виходу повітря на верхню частину одне отвір залишають відкритим. Це отвір закривається лише після наповнення водою всього судини. Потім у посудині гідравлічною пресом створюється тиск, однакову робочому тиску. Якщо дефектів не можна знайти, тиск збільшується до Рисп = 1,25 Рраб для судин і Рисп = 1,5 Рраб для трубопроводів. Під цим тиском посудину чи трубопровід витримують 5 хв, потім тиск знижують до Рраб і обстукивают сполуки молотком зі сферичної голівкою з відривом 15−20 мм від крайки шва. Після цього шви оглядають. При випробуванні на морозі замість води застосовують антифриз.
Пневматичне випробування проводять із метою контролю щільності зварних сполук. І тому на замкнене посудину нагнітають повітря до робочого тиску. Зовні все шви змочуються мильним розчином. Стиснутий повітря місцях неплотностей утворює мильні бульбашки. Залежно кількості і інтенсивності виділення мильних бульбашок можна будувати висновки про характері й величині дефекту. Пневматичний вид контролю зварних сполук набув широкого застосування під час випробування судин малої ємності, як найзручніший і доступний в заводських умовах з масовим виробництвом. І тут випробовуваний посудину поринає у ванну з і неплотности визначаються виділенням повітряних бульбашок. Для судин дуже великої обсягу застосовувати випробування стиснутим повітрям слід дуже обережно, бо за наявності недоліків у швах може відбутися розрив всього сосуда.
Випробування гасом. Гас може проникати через малі неплотности: тріщини, пори і наскрізні непровары металу. Для контролю шви із боку розкриття забарвлюють крейдою, розведеним на воді з додаванням клею, а із боку кореня сполуки змочують гасом. Гас, проходячи через неплотности, утворює на висохлій крейдової фарбі темні плями, якими можна будувати висновки про характері неплотности і піднятому місці її розташування. Якщо недоїмку протягом 30−60 хв такі плями не з’являться, то шви вважаються задовільними. Швидкість проходження гасу через метал визначатиметься завтовшки зварного з'єднання заліза і характером розташування недоліків у металі. Для відповідальних виробів час витримки під гасом встановлюють до 12 год за нормальної температури навколишнього повітря вище 0° і по 24 год за нормальної температури нижче 0°.
Гасова проба еквівалентна 3−4 ат гідравлічного тиску, застосовуваного для зварних судин закритого типа.
9. ТЕХНІКА БЕЗПЕКИ І ПОЖЕЖНІ ЗАХОДИ ПРИ ВЫПОЛНЕНИИ.
ЗВАРЮВАЛЬНИХ РАБОТ.
Ліси, підмостки і трапи на судні повинні прагнути бути надійними, виготовленими за затвердженими кресленням і прийнятими представниками відділу техніки безпеки. Ліси повинен мати бортові дошки заввишки 150 мм, щоб виключити падіння вниз інструментів чи інших предметів. На лісах обов’язково встановлюють 2−3 ярусу лееров. Трапи чи сходні мали бути зацікавленими міцно закріплені та мати бильця по обидва боки. Не допускається перевантаження лісів понаднормово. Необхідно стежити, щоб за однієї вертикалі на лісах і майданчиках не працювало кілька человек.
Забороняється працювати на мокрих, слизьких і зледенілих палубах судна і настилах лісів. Крига треба сколоть, а мокрі місця посипати піском, тирсою і т.п.
Усі робочі місця у цеху і судні мали бути зацікавленими обладнані засобами гасіння пожеж. У спеку року дерев’яні настили лісів періодично поливають водою. Усі горючі і быстровоспламеняющиеся матеріали бережуть у спеціальних закритих приміщеннях і спеціальної тарі. З використанням вогненебезпечних матеріалів потрібно суворо дотримуватися инструкций.
У разі пожежі в цеху на судні необхідно терміново викликати пожежну команду заводу, та її прибуття вжити заходів із гасінню пожежі (скористатися вогнегасником, піском і води) й відчуття міри по гарантуванню безпеки покупців, безліч порятунку майна від огня.
Слід пам’ятати, що олію, нафту можна гасити пінними вогнегасниками чи піском. Гарячу електропроводку і електричні машини, які під напругою, не можна гасити водою і пінними вогнегасниками, оскільки це можуть призвести з ураженням людей електричним струмом. У разі потрібно негайно знеструмити проводку і машини та після цього розпочати гасінню вогню. У разі пожежі дуже важливо зберегти спокій, дисципліну і беззаперечно виконувати розпорядження керівника, відповідального за гасіння пожара.
Відповідальність за організацію та влитися стан техніки безпеки на підприємствах несе адміністрація підприємств, у якої є спеціальні відділи технічно безпеки, чи інженери технічно безопасности.
Усі робочі, перед допуском на роботу, мали бути зацікавленими проінструктовані стосовно безпечного ведення робіт у разі необхідності здати відповідне випробування за правилами техніки безопасности.
Шкідливе вплив випромінювання електричної дуги, невидимі ультрафіолетові промені, використовувані зварювальної дугою, шкідливо діє сітківку і рогову оболонку очей. Якщо незахищеними очима на світло дуги протягом 5−10 хвилин, то через 1−2 години після цього, з’являється біль у очах, спазми століття, сльозотеча, світлобоязнь і запалення очей. У такому випадку потрібно звернутися до врачу.
Для захисту зору служать щитки і маски з захисними скельцями. Скла не пропускають ультрафіолетового проміння, а інфрачервоне проміння пропускають тільки у межах від 0,1 до 3% від загального количества.
Для запобігання дії променів зварювальної дуги, людей, працюючих поруч з місцями зварювання, захищають светонепроникающими щитами, ширмами чи кабінами з дикту й брезентом заввишки 1,8 м. Заради покращання вентиляції всередині кабіни, стінки не доводять до статі на 25−30 див. щоб зменшити різницю у яскравості світла, стінки кабін забарвлюють в матові світлі тону (сірий, блакитний, жовтий) і збільшують штучну освітленість робочого места.
Поразка електричним струмом. Граничне напруга холостого ходу під час зварювання на повинен перевищувати, зазвичай, 70 У. Особливо небезпечно поразка струмом під час зварювання всередині резервуарів, де зварювальник зтикається з металевими поверхнями, які перебувають під напругою стосовно электродержателю.
ВИКОРИСТАНА ЛИТЕРАТУРА.
1. Фрід О.Г. «Пристрій судна».
2. Рибаков В. М. «Дуговая і газова сварка».
3. Рибаков В. М. «Зварювання і різка металлов».