Виробництво сталі
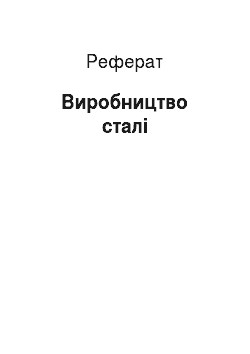
Обробка рідкого металу поза сталеплавильного агрегату. При позапічної обробці метал, виплавлений у звичайному сталеплавильному агрегаті (мартенівської печі, конвертере чи електропечі), піддається щодо впливу в сталеразливочном ковші. Основною метою позапічної обробки рідкої сталі у ковші стало зниження змісту розчинених у металі газів, неметалічних включень і сірки. Нині немає такої способу… Читати ще >
Виробництво сталі (реферат, курсова, диплом, контрольна)
НМетАУ.
Національна Металургійна Академія Украины.
Кафедра технологічного проектирования.
Курсова работа.
По дисципліни «Введення у спеціальність «.
На тему: «Виробництво сталі «.
Выполнил:
Студент групи ЛМ — 99.
Брез А. П.
Проверил:
Проф. Друян.
У. М.
. | |стор | |Запровадження |3 | |Виробництво сталі |3 | |Шлаки сталеплавильних процесів |3 | |Основні реакції сталеплавильних процесів |4 | |Окислювання вуглецю |4 | |Окислювання та своєчасне відновлення Mn |5 | |Окислювання та своєчасне відновлення Si |5 | |Окислювання та своєчасне відновлення P |5 | |Десульфация стали |5 | |Гази в стали |6 | |Розкислення стали |6 | |Виробництво сталі в конвертерах |7 | |Кислородно-конвертерное процес з верхньої продувкой |8 | |Кислородно-конвертерное процес з донної продувкой |10 | |Конвертерний процес з комбінованої продувкой |10 | |Виробництво сталі в мартенівських печах |11 | |Виробництво сталі в електропечах |12 | |Виплавка сталі у кислих электродуговых печах |13 | |Способи інтенсифікації виплавки сталі у великовантажних печах|13 | | |14 | |Плавка почав із рафинированием в ковші пічним шлаком |14 | |Плавка сталі у індукційною печі |15 | |Разливка стали |15 | |Разливка сталі у зливки |15 | |Шляхи підвищення якості стали |16 | |Обробка рідкого металу поза сталеплавильного агрегату |18 | |Виробництво сталі в вакуумних печах |18 | |Виробництво сталі в індукційних печах |19 | |Виробництво сталі в вакуумних дугових печах |20 | |Плазменно-дуговая плавка |21 | |Укладання |22 | |9. Список рекомендованої літератури | |.
Метали ставляться до найпоширеніших матеріалів, які людина використовує задля забезпечення всіх своїх потреб. Нині важко знайти таку область виробництва, науково-технічну діяльність людини чи навіть його від побуту, де метали не грали б чільну роль як конструкційного материала.
Метали поділяють сталася на кілька груп: чорні, кольорові і благородні. До групі чорних металів ставляться залізо та її сплави, марганець і хром. До кольоровим ставляться майже всі інші метали періодичної системи Д. І. Менделеева.
Залізо та її сплави є основою сучасної технологій і техніки. Серед конструкційних металів залізо слід за місці і поступиться ще й довгий час, як і раніше, що кольорові метали, полімерні і керамічні матеріали знаходять дедалі більше застосування. Залізо та її сплави перевищують 90% всіх металів, що застосовуються у сучасному производстве.
Найбільш найважливішим із сплавів заліза є його сплав з вуглецем. Вуглець надає міцність сплавів заліза. Ці сплави утворюють велику групу чавунів і сталей.
Сталями називають сплави заліза з вуглецем, зміст якого перевищує 2,14%. Сталь — найважливіший конструкционный матеріал для машинобудування, транспорту, й т. д.
Сталеплавильне виробництво — це отримання сталі з чавуну і сталевого брухту в сталеплавильних агрегатах металургійних заводів. Сталеплавильне виробництво є другим ланкою загалом виробничий цикл чорної металургії. У сучасному металургії основними способами виплавки стали є кислородно-конвертерный, мартенівський і електросталеплавильний процеси. Співвідношення між тими видами сталеплавильного виробництва меняется.
Сталеплавильный процес є окислительным процесом, оскільки сталь виходить внаслідок окислення і видалення більшу частину домішки чавуну — вуглецю, кремнію, марганцю і фосфору. Відмінною рисою сталеплавильних процесів служить наявність окислительной атмосфери. Окислювання домішок чавуну та інших шихтовых матеріалів здійснюється киснем, які мають газах, оксиди заліза і марганцю. Після окислення домішок, з металевого сплаву видаляють розчинений у ньому кисень, вводять легирующие елементи й отримують сталь заданого хімічного складу. [pic].
Виробництво стали.
Шлаки сталеплавильних процесів. Роль шлаків у процесі виробництва сталі виключно велика. Шлак режим, визначається кількістю і складами шлаку, надає велике впливом геть якість готової стали, стійкість футерівки і продуктивність сталеплавильного агрегату. Шлак утворюється внаслідок окислення складових частини шихти, з оксидів футерівки печі, флюсів та руди. По властивостями шлакоутворювальні компоненти можна розділити на кислотні (SiO2; P2O5; TiO2; V2O5 та інших.), основні (CaO; MgO; FeO; MnO та інших.) і амфотерные (Al2O3; Fe2O3; Cr2O3; V2O3 та інших.) оксиди. Найважливішими компонентами шлаку, які надають основне впливом геть його властивості, є оксиди SiO2 і CaO.
Шлак виконує кілька важливих функцій у процесі виплавки стали:
1. Пов’язує все оксиди (крім ЗІ), які утворюються у процесі окислення домішок чавуну. Видалення таких домішок, як кремній, фосфор і сірка, відбувається після їх окислення і обов’язкового переходу як оксидів з металу у шлак. У зв’язку з цим шлак має бути належним чином підготовлений для засвоєння й утримання оксидів домішок; 2. Багато сталеплавильних процесах служить передавачем кисню з пічний атмосфери до рідкому металу; 3. У мартенівських і дугових сталеплавильних печах через шлак відбувається передача тепла металу; 4. Захищає метал від насичення газами, які у атмосфері печи.
Змінюючи склад шлаку, можна чистьте метал від такого типу шкідливих домішок, як фосфор і сірка, і навіть регулювати у процесі плавки вміст у металі марганцю, хрому та інших елементів. А, щоб шлак міг успішно виконувати своїх функцій, він повинен на різні періоди сталеплавильного процесу мати певний хімічний склад парламенту й необхідну плинність (величина зворотна в’язкості). Ці умови досягаються використанням як шихтовых матеріалів плавки розрахункових кількостей шлакообразующих — вапняку, винищити, плавикового шпату, боксита і др.
[pic].
Основні реакції сталеплавильних процессов.
Сталь отримують з чавуну і брухту методом окисного рафінування (т. е. очищення). Кисень для окислення які у них домішок (вуглецю, марганцю, кремнію, фосфору та інших.) надходить або з атмосфери, або з залізної руди чи інших окислювачів, або за продувки ванни газоподібним углеродом.
Окислювання вуглецю. Особливість окислення вуглецю у тому, що продуктом цієї реакції є газоподібний ЗІ, який, виділяючись з металевої ванни як бульбашок, справляє враження киплячою рідини. Реакцію окислення вуглецю, розчиненої в металі написати в наступному вигляді: [З] + [O] = {CO}; K = [pic] де [З]; [O] - концентрації розчинених у металі вуглецю і кисню. Відповідно до рівняння для константи, при заданому значенні рсо твір концентрації вуглецю і розчиненої кисню є величина стала. Отже, від концентрації вуглецю залежить концентрація кисню в металі. Що зміст вуглецю в металі, тим нижче зміст кисню у ньому і наоборот.
Окислювання та своєчасне відновлення марганцю. Марганець елемент, у якого високим спорідненістю до кисню, легко окислюється як із кислому, і при основному процесах. Реакції окислення і відновлення марганцю можна уявити так: [Mn] + [O] [pic](MnO); [Mn] + (FeO) [pic](MnO) + [Fe].
Как показують розрахункові і експериментальні дані, на підвищення температури і основности шлаку концентрація марганцю в металі збільшується. Це зазначає, що реакція окислення марганцю сягає рівноваги, і окисний процес змінюється відбудовним. Оскільки майже всі стали містять марганець, його поновлення у процесах плавки — явище желательное.
Окислювання та своєчасне відновлення кремнію. Кремній має ще більшою спорідненістю до кисню, ніж марганець, і цілком окислюється вже під час плавлення. Окислювання кремнію іде за рахунок реакциям:
[Si] + 2[O] = (SiO2); [Si] + 2(FeO) = (SiO2) + 2 [Fe].
При плавленні під основним шлаком SiO2 пов’язується в міцний силікат кальцію (CaO)2•SiO2, що забезпечує майже повне окислювання кремнію, що міститься в шихті. При кислому процесі поведінки кремнію інше: при гарячому ході кислого процесу має місце інтенсивне відновлення кремния.
Окислювання та своєчасне відновлення фосфору. Фосфор в стали шкідлива домішкою, негативно впливає їхньому механічні властивості. Тому зміст фосфору в сталі у залежність від призначення обмежується межею 0,015 — 0,016%. Окислювання фосфору можна наступним образом:
2[P] + 5(FeO) = (P2O5) + 5[Fe]; (P2O5) + 3(FeO) = (FeO)3• P2O5; (FeO)3•P2O5 + 4(CaO) = (CaO)4•P2O5 + 3(FeO); 2P + 5(FeO) + 4(CaO) = (CaO)4•P2O5 + 5Fe.
Рівняння константи можна записати наступного виде:
K = [pic].
Звідки коефіцієнт розподілу фосфору між металом і шлаком:
L = (P2O5)/P2 = K[pic](FeO)5 [pic](CaO)4.
Десульфация стали. Сірка, як і фосфор, шкідлива домішкою в стали. Видалення сірки можна як реакции.
Feж + [P.S] +(CaO) = (CaS) + (FeO).
Рівняння для константи має вид:
До = [pic].
Коефіцієнт розподілу серы.
L = (S)/[S] = K (CaO)/(FeO).
З рівняння слід, що коли підвищення основности й відповідне зниження окисленности шлаку сприяє десульфации. Позитивну роль надає також підвищення металу й активна перемішування ванни. Зростанню ступеня видаленні сірки сприяють елементи, що утворюють сульфіди, більш міцні, ніж сульфід заліза. До таких елементам ставляться рідкісноземельні металлы.
Гази в стали. Гази (кисень, водень і азот) утримуватися у будь-якій стали. Гази навіть за змісті в сотих і тисячних частках відсотка надають негативний вплив на властивості металу. Розчинність кисню в стали характеризується реакцією: [pic]. У готовому металі зміст кисню має бути мінімальним. Розчинність водню й азоту в металі починяется закону Стивенса:
[pic]; [pic], де pH і pN — парциальные тиску газів; KH і KN — розчинність водню та азоту при парциальном тиску відповідного газу рівному, 0,1 МПа. Зменшення розчинності під час переходу з рідкого в тверде стан при кристалізації стали викликає виділення газів з металу, що причиною освіти низки дефектів, наприклад, флокенов[1], пористости в зливках готової сталі та т. п. У присутності деяких елементів в металі можуть утворюватися їх з'єднання з азотом — нитриды. Наявність нитридов в кристалічною структурі багатьох сталей негативно впливає властивості металу. Азот і водень успішно видаляються з рідкої сталі у результаті реакції окислення вуглецю. Утворений у цій реакції ЗІ, збирається у бульбашки, які вириваються на поверхню металу, пробивають під металів шар рідкого шлаку виходять у повітря. Внаслідок цього складається враження кипіння рідкої ванни. Спливають бульбашки ЗІ захоплюють шляхом вгору певна кількість інших газів — H2 і N2 (рис. 1). Чим енергійніше протікає кипіння металу, тим менше зміст газів і краще якість металу. Для видалення H2 і N2 застосовують також вакуумну обробку, продувку ванни нейтральним газом (аргоном) і др.
Рис. 1 Схема видалення газів из.
рідкого металу у процесі кипіння Розкислення стали. Для зниження змісту кисню в стали проводять її розкислення. Це, зазвичай, остання, і відповідальна операція в процесі виплавки стали. Розкислення — це процес видалення кисню, розчиненої в стали, шляхом зв’язування їх у оксиди різних металів, мають більше спорідненість до кисню, ніж залізо. Найпоширенішими раскислителями є марганець і кремній, використовувані як феросплавів, і алюміній. Реакції розкиснення можна наступним образом:
[O] + [Mn] = (MnO) 2[O] + [Si] = (SiO2) 3[O] + 2[Al] = (Al2O3).
Залежно та умовами введення розкислювачів на метал розрізняють два методу розкиснення: глибинне (чи осаждающее) і диффузионное розкислення. При глибинному раскислении раскислители вводять у глибину металу. У цьому вся разі потрібен час у тому, щоб продукти розкиснення — оксиди кремнію, марганцю, алюмінію спливли в шлак. При диффузном раскилении раскислители в тонко здрібненому вигляді потрапляють у шлак, покриває метал. Спершу цьому випадку відбувається розкислення шлаку, а зниження вмісту кисню в металі відбувається поза рахунок переходу із металу у шлак, т. е. [O] ==> (O). При диффузионном раскислении немає забруднення металу неметаллическими включеннями — продуктами розкиснення. Для глибокого розкиснення застосовують обробку рідкого металу у вакуумі чи синтетичними шлаками. Залежно від рівня розкиснення розрізняють спокійну, киплячу і полуспокойную сталь. Спокійна сталь — це сталь, повністю раскисленная, т. е. завдяки введення великої кількості розкислювачів весь кисень в стали перебуває у що з элементом-раскислителем стані. При розливання такий стали гази не виділяються, і її застигає спокійно. Нуртуюча сталь — це сталь, частково раскисленная марганцем. При розливанні на злитки вона вирує (кипить) завдяки виділенню пухирців оксиду вуглецю, які виникають за реакцією: [З] + [O] = {CO}. Полуспокойная сталь — це сталь, за рівнем раскисленности що становить проміжне місце між киплячою та спокійною. Полуспокойную сталь ракисляют частково в печі (марганцем) і у ковші (кременем, алюмінієм). [pic].
Виробництво сталі в конвертерах.
Кислородно-конвертерный процес є одне із видів переділу рідкого чавуну в сталь без витрати палива шляхом продувки чавуну в конвертере технічно чистим киснем, подаваним через фурму, яка вводять у метал згори. Вперше кислородно-конвертерный процес у промисловому масштабі був здійснено Австрії у 1952 — 1953 рр. на заводах у містах Лінці і Донавице (там той процес отримав назву ЛД за першими літерами міст, нашій країні - киснево-конвертерного). Нині працюють конвертери ємністю від 20 до 450 т, тривалість плавки у яких становить 30 — 50 хв. Процес займає чільну роль серед існуючих способів виробництва стали. Такий успіх киснево-конвертерного способу залежить від можливості переробки чавуну практично будь-якого складу, використанням металобрухту від 10 до 30%, можливість виплавки широкого сортаменту сталей, включаючи леговані, високої продуктивністю, малим коштом для будівництва, великий гнучкістю і якістю продукции.
Кислородно-конвертерный процес з верхньої продувкой. Конвертер має грушоподібної форми з концентрической горловиною. Це забезпечує кращі економічні умови для входження у порожнину конвертера кисневою фурмы, відводу газів, заливання чавуну і завалки брухту і шлакообразующих матеріалів. Кожух конвертера виконують сварным з сталевих аркушів завтовшки від 20 до 100 мм. У центральній частині конвертера зміцнюють цапфы, з'єднані з побудовою для нахилу. Механізм повороту конвертера складається з системи передач, що пов’язують цапфы з приводом. Конвертер може повертатися навколо горизонтально осі на 360о зі швидкістю від 0,01 до 2 об./хв. Для більше важких конвертерів ємністю від 200 т застосовують двосторонній привід, наприклад, чотири двигуна дві кожну цапфу.
[pic].
Малюнок 2 Конвертер ємністю 300 т з двостороннім приводом механізму поворота.
У шлемной частини конвертера є льотка для випуску стали. Випуск стали через льотку виключає можливості влучення шлаку на метал. Льотка закривається вогнетривкої глиною, замішаної на воде.
[pic].
Малюнок 3 Технологічна схема виробництва сталі в кисневому конвертере.
Хід процесу. Процес виробництва сталі в кисневому конвертере полягає з таких основних періодів (рис 3); завантаження металобрухту, заливання чавуну, продувки киснем, завантаження шлакообразующих, зливу сталі та шлака.
Завантаження конвертера починається з завалки сталевого брухту. Лом завантажують в нахилений конвертер через горловину з допомогою завалочних машин яткового типу. Потім із допомогою заливальних кранів заливають рідкий чавун, конвертер встановлюють в вертикальне становище, вводять фурму і включають подачу кисню з чистотою щонайменше 99,5% О2. Поруч із початком продувки завантажують першу порцію шлакообразующих і залізною руди (40 — 60% від загальної кількості). Решту сипучих матеріалів подають у конвертер в процесі продувки одна чи кілька порціями, найчастіше 5 — 7 хвилин від початку продувки. На процес рафінування значний вплив надають становище фурмы (відстань від кінця фурмы до поверхні ванни) і тиск подаваного кисню. Зазвичай висота фурмы підтримується не більше 1,0 — 3,0 м, тиск кисню 0,9 — 1,4 МПа. Правильно організований режим продувки забезпечує хорошу циркуляцію металу та її перемішування зі шлаком. Останнє своє чергу сприяє підвищенню швидкості окислення які у чавуні З, Si, Mn, P. Важливим в технології киснево-конвертерного процесу є шлакообразование. Шлакообразование значною мірою визначає хід видалення фосфору, сірки та інших домішок, впливає якість виплавленої стали, вихід придатного і якість футерівки. Основна мета стадії плавки залежить від швидкому формуванні шлаку з необхідними властивостями (основностью, жидкоподвижностью тощо. буд.). Складність виконання це завдання пов’язані з високої швидкістю процесу (тривалість продувки 14 — 24 хвилини). Формування шлаку необхідної основности і заданими властивостями залежить від швидкості розчинення винищити в шлаку. На швидкість розчинення винищити в шлаку впливають такі чинники, як склад шлаку, його окисленность, умови змочування шлаком поверхні вапна, перемішування ванни, температурного режиму, склад чавуну тощо. буд. Раннього формуванню основного шлаку сприяє наявність первинної реакційної зони (поверхню дотику струменя кисню з металом) з температурою до 2500о. У цьому зоні вапно піддається одночасному впливу високої температури і шлаку з підвищеним змістом оксидів заліза. Кількість введеної на плавку винищити визначається розрахунком і від складу чавуну і змісту SiO2 руді, боксите, вапна та інших. Загальний витрата винищити становить 5 — 8% від безлічі плавки, витрата боксита 0,5 — 2,0%, плавикового штампа 0,15 — 1,0%. Основность кінцевого шлаку мусить бути щонайменше 2,5. Окислювання всіх домішок чавуну починається від початку продувки. При цьому найінтенсивніше на початку продувки окислюється кремній і марганець. Це високим спорідненістю цих елементів до кисню при порівняно низьких температурах (1450 — 1500о З повагою та менш). Окислювання вуглецю в кислородно-конвертерном процесі має важливе значення, т. до. впливає температурного режиму плавки, процес шлакообразования і рафінування металу від фосфору, сірки, газів і неметалічних включень. Характерною ознакою киснево-конвертерного виробництва є нерівномірність окислення вуглецю як у обсягу ванни, і у перебігу продувки. З перших хвилин продувки разом з окисленням вуглецю починається процес дефосфорации — видалення фосфору. Найбільш інтенсивне видалення фосфору іде у першій половині продувки при порівняно низькою температури металу, дуже високому вмісті в шлаку (FeO); основность шлаку та її кількість швидко зростає. Кислородно-конвертерный процес дозволяє отримати < 0,02% Р в готової стали. Умови видалення сірки при кислородно-конвертерном процесі не можна вважати настільки ж сприятливим, як видалення фосфору. Причина у тому, що шлак містить значну кількість (FeO) і висока основность шлаку (> 2,5) досягається лише у другій половині продувки. Ступінь десульфурации при кислородно-конвертерном процесі у межах 30 — 50% і змістом сірки в готової стали становить 0,02 — 0,04%. Після досягнення заданого змісту вуглецю дуті відключають, фурму піднімають, конвертер нахиляють і метал через льотку (зменшення перемішування металу і шлаку) виливають в ковш.
Отриманий метал містить підвищений вміст кисню, тому заключній операцією плавки є розкислення металу, яке проводять у сталеразливном ковші. З цією метою одночасно з зливом стали зі спеціального поворотному жолобу в ківш потрапляють раскислители і легирующие добавки. Шлак з конвертера зливають через горловину в шлак ківш, встановлений на шлаковозе під конвертером. Перебіг киснево-конвертерного процесу обумовлюється температурним режимом і регулюється зміною кількості дуття і введенням у конвертер охолоджувачів — металобрухту, залізної руди, вапняку. Температура металу під час випуску з конвертера близько 1600о З. Під час продувки чавуну в конвертере утворюється значну кількість відведених газів. Для використання тепла відведених газів і отчистки їхню відмінність від пилу кожним конвертером обладнані котел-утилизатор і установка для очищення газів. Управління конвертерним процесом здійснюється з допомогою сучасних потужних комп’ютерів, у яких вводиться інформацію про вихідних матеріалах (склад парламенту й кількість чавуну, брухту, винищити), і навіть про показниках процесу (кількість і склад кисню, відведених газів, температура тощо. п.).
Кислородно-конвертерный процес з донної продувкой. У 1960;х років дослідами по вдуванию струменя кисню, оточеній шаром вуглеводнів, було показано можливість через днище без руйнації вогнетривів. Нині у світі працюють кілька десятків конвертерів з донної продувкой садкой до 250 т. Кожна десята тонна конвертерной стали, виплавленої у світі, посідає той процес. Основне відмінність конвертерів з донної продувкой від конвертерів з верхнім дутьем у тому, що вони теж мають менший питомий обсяг, т. е. обсяг що припадає на тонну продуваемого чавуну. У днище встановлюють від 7 до 21 фурм залежно від ємності конвертера. Розміщення фурм в днище може бути різним. Зазвичай їх мають лише у половині днища те щоб при нахилі конвертера вони були вище рівня рідкого металу. Перед установкою конвертера в вертикальне становище через фурмы пускається дуття. У разі донної продувки поліпшуються умови перемішування ванни, збільшується поверхню металл-зарождения і виділення пухирців ЗІ. Таким чином, швидкість обезуглероживания при донної продувке вищою, порівняно з верхньої. Одержання металу із вмістом вуглецю менш 0,05% не представляє труднощів. Умови видалення сірки при донної продувке сприятливіші, аніж за верхньої. І це пов’язане з не меншою окисленностью шлаку та розширенням поверхні контакту газ — метал. Остання обставина сприяє видалення частини сірки в газову фазу як SO2. Переваги процесу з донної продувкой перебувають у підвищенні виходу придатного металу на 1 — 2%, скороченні тривалості продувки, прискоренні плавлення брухту, меншою висоті будинку цехи і т. буд. Це певний інтерес, передусім, для можливої заміни мартенівських печей без корінний реконструкції будинків мартенівських цехов.
Конвертерний процес з комбінованої продувкой. Ретельний аналіз переваг і повним вад способів виплавки сталі у конвертерах з верхньої та нижньої продувкой привів до створення процесу, в якому метал продувається згори киснем і знизу — киснем в захисної сорочці чи аргоном (азотом). Використання конвертера з комбінованої продувкой проти продувкой лише зверху дозволяє підвищити вихід металу, дозволяють збільшити частку брухту, знизити витрата феросплавів, зменшити витрати кисню, підвищити якість стали з допомогою зниження змісту газів при продувке інертним газом наприкінці операции.
[pic].
Виробництво сталі в мартенівських печах.
Сутність мартенівського процесу полягає у переробці чавуну і брухту на упаду отражательной печі. У мартенівському процесі згорання у на відміну від конвертерного недостатньо тепла хімічних реакцій і фізичного тепла шихтовых матеріалів. Для плавлення твердих шихтовых матеріалів, покриття значних теплових втрат перезимувало і нагріву стали до необхідних температурах піч подводиться додаткове тепло, одержуване шляхом спалювання у робочому просторі палива на струмені повітря, нагрітого до високих температур. Для забезпечення максимального використання подаваного в піч палива необхідно, щоб процес горіння палива закінчувався цілком у робочому просторі. У зв’язку з цим у піч повітря подається у кількості, перевищує теоретично необхідне. Це створює у атмосфері печі надлишок кисню. Тут також присутній кисень, утворюючись під час результаті розкладання при високих температур вуглекислого газу й води. Отже, газова атмосфера печі має окисний характер, т. е. у ній міститься надлишок кисню. Завдяки цьому метал у мартенівської печі протягом усієї плавки піддається прямому чи непрямому впливу окислительной атмосфери. Для інтенсифікації горіння палива на робочому просторі частина повітря йде на горіння, може замінюватись киснем. Газоподібний кисень може також подаватися у ванну (аналогічно продувке металу в конвертере). Внаслідок цього під час плавки відбувається окислювання заліза та інших елементів, які у шихті. Які Утворюються у своїй оксиди металів FeO, Fe2O3, MnO, CaO, P2O5, SiO2 та інших. Разом із часточками поступово разрушаемой футерівки, домішками, внесеними шихтою, утворюють шлак. Шлак легше металу, й тому він покриває метал в усі періоди плавки. Шихтові матеріали основного мартенівського процесу складаються, як і за інших сталеплавильних процесах, з металевої частини (чавун, металевий брухт, раскислители, легирующие) і неметаллической частини (залізна руда, мартенівський агломерат, вапняк, вапно, боксит). Чугун може застосовується в рідкому вигляді чи пацях. Співвідношення кількості чавуну і сталевого брухту в шихті не завжди однаковий залежно від процесу, виплавлюваних марок сталі та економічних умов. [pic].
Рисунок 4.
За характером шихтовых матеріалів основний мартенівський процес ділитися сталася на кілька різновидів, найбільшого поширення у тому числі отримали скрап-рудный і скрап-процессы. При скрап-рудном процесі основну масу металевої шихти (від 55 до 75%) становить рідкий чавун. Цей процес відбувається широко застосовується на заводах з повним металургійним циклом. При скрап-процессе основну масу металевої маси шихти (від 55 до 75%) становить металевий брухт. Чавун (25 — 45%), зазвичай, застосовується у твердому вигляді. Таким процесом працюють заводи, у яких немає доменного производства.
[pic].
Малюнок 5 Схема двухванной сталеплавильної печи:
1 — топливно-кислородные фурмы;
2 — фурмы для вдмухування твердих матеріалів; 3 — звід печі; 4 — вертикальні каналы;
5 — шлаковики; 6 — подины печей.
[pic].
Виробництво сталі в электропечах.
Електросталеплавильне виробництво — це отримання якісних і високоякісних сталей в електричних печах, які мають суттєвими перевагами проти іншими сталеплавильными агрегатами. Виплавка сталі у електропечах полягає в використанні електроенергії для нагріву металу. Тепло в електропечах виділяється внаслідок перетворення електроенергії у теплову при горінні електричної дуги або у спеціальних нагрівальних елементах, або з допомогою порушення вихрових струмів. На відміну від конвертерного і мартенівського процесів виділення тепла в електропечах не пов’язане зі споживанням окислювача. Тому электроплавку може бути у будь-якій середовищі - окислительной, відновлювальної, нейтральній і широтою діапазону тисків — у вакуумі, атмосферного чи надлишкового тиску. Електросталь, призначену задля її подальшого переділу, виплавляють, головним чином дугових печах провідною футеровкой й у індукційних печах.
[pic].
Малюнок 6 Схема робочого простору дугового электропечи:
1 — куполообразный звід; 2 — стінки; 3 — желоб;
4 — сталевыпускное отвір; 5 — електрична дуга; 6 — сферичний під; 7 — робоче вікно; 8 — заслінка; 9 — электроды.
Дугові печі бувають різну місткість (до 250 т) і з трансформаторами потужністю до 125 тисяч кіловат. Джерелом тепла в дугового печі є електрична дуга, що виникає між електродами і рідким металом чи шихтою при додатку до електродах електричного струму необхідної сили. Дуга є потік електронів, іонізованих газів і парів металу і шлаку. Температура електричної дуги перевищує 3000о З. Дуга, як відомо, може постати при постійному і постійному струмі. Дугові печі працюють на перемінному струмі. При горінні дуги між електродом і металевої шихтою у період плавки, коли катодом є електрод, дуга горить, т. до. простір між електродом і шихтою іонізується з допомогою випущення електронів з нагрітого кінця електрода. При зміні полярності, коли катодом стає шихта — метал, дуга гасне, т. до. на початку плавки метал ще нагріте та її температура недостатня для емісії електронів. При наступної зміні полярності дуга знову виникає, у початковий період плавки дуга горить переривчасто, неспокійно. 1 — електрод 2 — голівка электродержателя 3 — звід 4 — підвіска зводу 5 — сводное кільце 6 — цилиндричекий кожух 7 — робочий майданчик 8 — механізм нахилу печі 9 — жолоб для зливу сталей [pic].
Рисунок 7 Дуговая сталеплавиль-ная печь.
Після расплавлении шихти, коли ванна покриває рівним шаром шлаку, дуга стабілізується і горить ровно.
Виплавка сталі у кислих электродуговых печах Электродуговые печі із кислою футеровкой зазвичай використовуються при виплавці стали для фасонного лиття. Ємність яких становить від 0,5 до 6,0−10 т. Кисла підбійка більш термостійка і дозволяє експлуатувати піч з урахуванням умов прерывной роботи багатьох ливарних цехів машинобудівних заводів. Основним недоліком печей із кислою футеровкой і те, що під час плавки з металу не видаляються сірка і фосфор. Звідси, дуже високі вимоги до якості застосовуваної шихти за цих домішок. Плавлення у кислому печі триває приблизно таке ж, як і основний печі (50- 70 хв). У окисний період підуть менше вуглецю (0,1 — 0,2%) і через підвищеного змісту FeO в шлаку метал кипить без присадок залізної руди. Зміст SiO2 в шлаку до кінця окисного періоду підвищується до 55 — 65%. Коли метал нагріте, починається відновлення кремнію за реакцією: (SiO2) + 2[C] = [Si] + 2COгаз.
Наприкінці окисного процесу зміст Si в металі збільшується до 0,2 — 0,4%. Розкислення стали перед випуском можна проводити як і печі, і у конце.
Способи інтенсифікації виплавки сталі у великовантажних печах. Одношлаковый процес. Технологія виплавки стали під шлаком без відновного періоду застосовується для виплавки мартенівського сортаменту сталей. Після закінчення проведення окислите1льного періоду присаживают силікомарганець і феррохром у необхідному кількості для отримання необхідного хімічного складу даної марки стали, покращують шлак добавкою винищити, флюсів. Потім сталь випускають в ківш, де проводять остаточне розкислення і легування. [pic].
Рисунок 8 Технологічна схема виробництва сталі в дугового сталеплавильної печи.
Плавка з рафинированием в ковші пічним шлаком. Застосовується на печах ємністю 100 — 200 т. Після закінчення окисного періоду й розкиснення металу наводять новий шлак із високим вмістом СаО. Протягом 40 — 60 хв шлак раскисляют молотим коксом і ферросилицием. Перед випуском в шлак дають CaF2. Високе (10 — 20%) зміст CaF2 забезпечує високу рафинирующую здатність шлаку. При випуску з печі спочатку випускають в ківш рідкий шлак і далі потужної струменем метал. Перемішування металу зі шлаком забезпечує високий рівень рафінування від домішок (від сірки) і неметалевих включень. Однією форму рафінування сталі в ковші вважатимуться технологію синтетичних шлаків з урахуванням СаО — Al2O3. І тут потрібні додаткові витрати для плавлення шлака.
Плавка сталі у індукційною печі. У індукційних печах для виплавки металу використовується тепло, яке виділяється в металі з допомогою порушення у ньому електричного струму змінним магнітним полем. Джерелом магнітного поля була в індукційною печі служить індуктор. Проводить електричний струм шихта, вміщена в тигель печі, піддається впливу змінного магнітного поля, виникає від індуктора, нагрівається у результаті теплового впливу вихрових токов.
У порівняні з дуговими на електропечі індукційні печі випливає низка переваг: відсутність електродів і електричних дуг дає змогу отримувати сталі та сплави з низьким змістом вуглецю і газів; плавка характеризується низьким чадом легуючих елементів, високим технічним ККД і можливість точного регулювання температури металла.
[pic].
Малюнок 9 Схема індукційною печи.
1 — каркас; 2 — подовая плита; 3 — водоохлаждаемый індуктор; 4 — ізоляційний шар; 5 — тигель; 6 — абсоцементная плита; 7 — зливальний носок;
8 — комір; 9 — гнучкий токоподвод; 10 — опорні брусья.
Индукционная піч складається з вогнетривкої тигля, вміщеного в індуктор. Індуктор є соленоид, зроблений із мідної водоохлаждаемой трубки. Струм до индуктору подається гнучкими кабелями. Воду для охолодження підводять гумовими шлангами. Уся піч криється у металевий кожух. Згори тигель закривається склепінням. Для зливу металу піч може нахилятися убік зливального шкарпетки. Тигель печі виготовляється набиванням чи викладається цеглою. Для набивки використовують мелені вогнетривкі матеріали — основні (магнезит) чи кислі (кварцит). Оскільки плавка в індукційною печі відбувається дуже швидко, шихта для неї використовується, зазвичай, з високоякісної металобрухту відомого складу. Перед плавкою відбувається точний розрахунок шихти по змісту вуглецю, сірки і фосфору, і навіть легуючих елементів. Шихту завантажують в тигель в такий спосіб, щоб він щільно заповнювала обшир тигля. Після завантаження шихти включають струм на повну потужність. Принаймні проплавления шихти завантажують решту. Потім на поверхню металу завантажують шлакообразующую суміш, що складається з винищити, магнезитового порошку і плавикового шпату. У процесі плавки шлак раскисляют добавками порошку коксу і меленого раскислителя. Під час плавлення додають легирующие матеріали. Метал раскисляют кусковыми феросплавами і наприкінці плавки алюмінієм. У індукційних печах виплавляють, зазвичай, сталі та сплави складного хімічного состава.
[pic].
Разливка стали.
Разливка сталі у зливки. З сталеплавильного агрегату сталь випускається в сталеразливочный ківш, готовий до короткочасного збереження і розливання сталі. Сталеразливочный ківш (рис) має форму усіченого конуса з великим підставою вгорі. Ківш має зварної кожух, зсередини футеруется огнеупорным шамотным цеглою. Переміщають ківш з допомогою мостового крана чи спеціальної залізничної візку. Сталь з ковша розливають через одну чи дві склянки, розміщених у днище ковша. Отвір закривають чи відкривають зсередини вогнетривкої корком з допомогою стопора. Ємність сталеразливочных ковшів сягає 480 т. У сталеплавильних цехах сталь з ковша розливають або у изложницы, або машинами безупинної разливки.
[pic].
Малюнок 10 Загальний вид сталеразливочного ковша:
1 — цапфа; 2 — шкарпетку для зливу шлаку 3 — стопор; 4 — скоба для кантования ковша.
[pic].
Малюнок 11 Схема розливання сталі по изложницам.
A — разливка згори: 1 — сталеразливочный ківш; 2 — плісень; 3 — піддон; Б — разливка сифоном: 1 — сталеразливочный ківш; 2 — центрова трубка; 3.
— прибуткова надставка; 4 — плісень; 5 — піддон; 6 — сифонные трубки.
Шляхи підвищення якості стали.
Безупинне розвиток техніки представляє дедалі більше високі вимоги до якості стали. Численні засоби одержання металів високої якості може бути умовно розділені втричі группы:
. Обробка рідкого металу поза сталеплавильного агрегата.
. Виплавка сталі у вакууме.
. Спеціальні способи электроплавки металлов.
Обробка рідкого металу поза сталеплавильного агрегату. При позапічної обробці метал, виплавлений у звичайному сталеплавильному агрегаті (мартенівської печі, конвертере чи електропечі), піддається щодо впливу в сталеразливочном ковші. Основною метою позапічної обробки рідкої сталі у ковші стало зниження змісту розчинених у металі газів, неметалічних включень і сірки. Нині немає такої способу обробки рідкої сталі у ковші, який дозволило б одночасно значно знизити в металі зміст неметалевих включень, сірки і газів. Тому залежно від поставленого завдання застосовується той чи інший спосіб позапічної обробки металів. Обробка металів в ковші синтетичним шлаком призводить до зниження стали сірки, неметалічних включень і кисню. Сутність методу у тому, що метал випускають із печі в ківш, частково заповнений рідким шлаком (4 — 5% від безлічі металу), який попередньо виплавляють у спеціальній агрегаті. Рідкий шлак і метал інтенсивно перемішуються. Сірка, кисень і неметалеві включення переходять із металу у шлак. Після обробітку металу синтетичним шлаком є його склад парламенту й фізико-хімічні властивості. Шлак повинен мати низькі температуру плавлення і в’язкість, і навіть мати високої основностью і низької окисленностью. Цим вимогам відповідають известковоглиноземистые шлаки, містять 50 — 55% СаО, 38 — 42% Al2O3, 1,5 — 4% SiO2, 0,15 — 0,5% FeO. Шлаки такого складу мають високої рафинирующей здатністю. Підвищення якості стали, обробленою синтетичним шлаком, компенсують витрати, пов’язані з выплавкой такого шлаку. Продування металу у ковші порошкообразными матеріалами одна із сучасних способів підвищення якості сталі та продуктивності сталеплавильних агрегатів. Рідкий метал у потоці інертного газу (аргону) через фурму вводять подрібнені десульфураторы і раскислители. У результаті обробки можна отримати роботу метал із вмістом сірки і кисню менш 0,005% каждого.
Обробка рідкої стали аргоном в ковші є найпростішим способом підвищення якості металу. Аргон вдувають в рідку сталь через пористі і вогнетривкі пробки, які в днище ковша. Аргон не розчиняється в рідкої стали, тому при продувке металу аргоном обсягом рідкої стали утворюється велика кількість бульбашок, які інтенсивно перемішують метал і виносять з його поверхню неметалеві включення. З іншого боку, водень і азот, розчинені в стали, переходить до бульки аргону разом із ним залишають рідкий метал, т. е. відбувається дегазація стали. Позапічна обробка рідкої стали вакуумом з промисловою масштабах стала застосовується спочатку 1950;х років. Існує велика кількість методів вакуумної обробки стали. Деякі принципові схеми наведено ниже:
[pic].
Малюнок 12.
Найпростішим способом є вакуумирование сталі у ковші (а). У цьому випадку ківш з рідким металом вміщують у герметичну камеру, з якої відкачують повітря. При зниженні тиску в камері метал закипає внаслідок бурхливого виділення з металів газів. Після дегазації металу камеру разгерметизируют, а ківш з вакуумированной відправляють на разливку. Ковшевое вакуумирование неефективно при обробці повністю раскисленной сталі та великих мас металу. І тут внаслідок слабкого розвитку реакції З + O = CO метал кипить мляво. Для поліпшенні дегазації стали вакуумну обробку металів в ковші поєднують з продувкой його аргоном і електромагнітним перемішуванням. Зазвичай дегазацію металу у ковші проводять протягом 10 — 15 хв. Більше тривала обробка призводить до значному зниження температури металу. Парционное і циркуляционное вакуумирование стали (рис б й у) застосовують при дегазації великих мас металу. При парционном вакуумировании футурованная вакуумна камера не великого обсягу поміщається над ковшем з рідким металом. Патрубок камери, футерованный зсередини і зовні, повантажений у рідкий метал. Під впливом атмосферного тиску порція металу (10 — 15% загальної маси) піднімається до камери і дегазируется. При русі ковша униз чи камери вгору метал випливає, а при зворотному русі знову до камери, для повної дегазації стали необхідно провести від 30 до 60 циклів вакуумної обробки. При циркуляционном способі вакуумирования стали застосовують вакуумну камеру з цими двома патрубками. Рідкий метал з ковша піднімається до камери по одному патрубку, дегазируется і випливає знову на ківш за другим патрубку. Відбувається безперервна циркуляція металу через вакуумну камеру. Підйом рідкої сталі у камеру відбувається поза рахунок эжектирующего дії аргону, що подають у вхідний патрубок. Струйное вакуумирование металу застосовується у основному литві великих зливків (рис р). цей спосіб є досконалим, т. до. усувається вторинне окислювання при розливанні вакуумированного металу з ковша в изложницы. При литві зливків в вакуумі струмінь металу, переливаемого з ковша, а изложницу, встановлену у вакуумній камері, розривається виділяються газами силою-силенною дрібних крапель металу. Поверхня металу різко зростає, що призводить глибокої дегазації стали. З іншого боку, сталь також дегазируется в изложницы. Останнім часом щоб одержати почав із дуже низьким змістом вуглецю обробку металу у вакуумі поєднують з продувкой його кисню чи сумішшю аргону і кислорода.
Виробництво сталі в вакуумних печах. Застосування вакууму при виплавки стали дає змогу отримувати метал практично будь-якого хімічного складу з низьким змістом газів, неметалевих включень, домішок кольорових металів. Як зазначалося, реакції дегазації і розкиснення металу вуглецем в вакуумі протікають повніше. З іншого боку при плавки металу у глибокому вакуумі (.