Обґрунтування нормативів параметрів стендової перевірки автомобіля BMW 520i E28
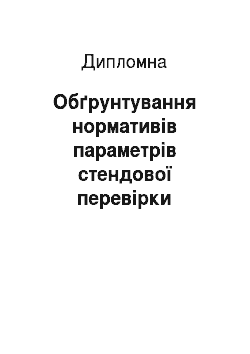
Вимога виконувати стендову перевірку гальм ДТЗ у стані повної маси виходить з обмежених можливостей більшості силових стендів по реалізації гальмівних сил (0,7…0,9 від діючого навантаження на колесо; у інерційних стендів це відношення трохи вище — q=1,0…1,2). Ця вимога занадто завищена; не випадково стандарт допускає для ДТЗ із пневмоприводом (тобто для більшості вантажних автомобілів і… Читати ще >
Обґрунтування нормативів параметрів стендової перевірки автомобіля BMW 520i E28 (реферат, курсова, диплом, контрольна)
ДИПЛОМНА РОБОТА Обґрунтування нормативів параметрів стендової перевірки автомобіля
BMW 520i E28
ЗМІСТ Вступ
1. Загальне діагностування автомобілів. Задачі дослідження
2. Чинні вимоги до гальм та силового агрегату
2.1 Показники працездатності гальмівної системи
2.2 Показники працездатності силового агрегату
3. Короткий опис і технічна характеристика
автомобіля BMW 520i E28
3.1 Короткий опис автомобіля
3.2 Загальний опис гальмівної системи
4. Тяговий баланс на стенді
5. Експериментальне визначення моменту інерції колеса
6. Експериментальне визначення моменту інерції трансмісії
7. Експериментальне визначення опорів обертанню коліс та роликів стенда
8. Розрахунок нормативів тягових властивостей
8.1 Визначення тягової сили на ведучих колесах
8.2 Побудова залежності тягової сили від швидкості
9. Розрахунок коефіцієнта розподілу гальмівних сил по осям
10. Розрахунок нормативів гальмівних параметрів
11. Безпека життєдіяльності і охорона праці
11.1 Законодавчі акти про охорону праці і безпеку життєдіяльності
11.2 Основні джерела виробничих шкідливостей
11.3 Загальні норми по охороні праці і БЖД на автотранспорті
11.4 Шляхи зниження забруднення навколишнього середовища
11.5 Вимоги пожежної безпеки
11.6 Техніка безпеки при діагностуванні автомобіля на стенді з біговими барабанами
11.7 Інструкція з охорони праці для операторів-діагностів легкових автомобілів Висновки і рекомендації
Перелік посилань
Вступ Більшість фахівців однією з основних причин аварійності на дорогах вважає помилки водіїв та пішоходів, забуваючи про технічну несправність транспортних засобів. У сполученні з різко зрослою інтенсивністю руху ця проблема придбала особливу гостроту. На підставі офіційних даних робиться помилковий висновок про необхідні заходи щодо забезпечення безпеки дорожнього руху, які повинні перебувати в площині сугубо адміністративної відповідальності за порушення правил дорожнього руху.
Це особливо актуально для України, де інтенсивність руху транспортних засобів (ТЗ) виросла в кілька разів і вже зараз досягла нормативних значень рівня розвитку автомобільної інфраструктури. Автомобільний парк країни перевищує 9 млн. од. і, поряд з динамічним ростом в останні 10 років, стає усе більш технічно й морально застарілим. Мало того, тепер рішенням Президента скасовані технічні огляди (може, то й вірно, бо вони давно перетворилися у формальність та джерело хабарів для інспекторів).
В 2005 р. частка експлуатованих ТЗ віком понад 5 років, вироблених у ближнім зарубіжжі (головним чином у Росії), перевищила 69%, що разом зі старими іномарками віком більше 10 років становить більше 81% автомобільного парку України.
При споконвічному невисокому рівні безпеки і якості виготовлення вітчизняних автомобілів число їхніх власників безупинно зростає. Все це разом зі зниженням якості й обсягів проведеного ТО, недотриманням відповідних приписань заводів-виготовлювачів створює критичну ситуацію на автомобільних дорогах країни. Вплив експлуатаційного зношування, матеріального й морального старіння на найважливіші властивості ТЗ здатний радикально їх погіршити в процесі технічної експлуатації, через що вони можуть стати причиною виникнення ДТП.
До причин виникнення аварійних ситуацій відноситься й невміле керування транспортними засобами, що перебувають в особистій власності, причому цей показник аварійності постійно росте.
Найвища ймовірність виникнення аварії спостерігається при експлуатації ТЗ з несправностями шин, освітлювальних і світлосигнальних приладів і гальмівних систем.
Таблиця 1 — Розподіл ДТП в Україні по видах несправностей транспортних засобів (1993 — 2006 р.р.)
Несправні елементи й системи | Частка ДТП, % | ||
Всі ТЗ | ТЗ індивідуальних власників | ||
Шини (розрив, зношування протектора) | 24,2−25,8 | 26,4−26,8 | |
Освітлювальні й світлосигнальні прилади | 23,1−24,9 | 25,3−25,9 | |
Робоча й стоянкова гальмівна системи | 17,5−16,5 | 14,3−14,7 | |
Рульове керування | 14,1−14,4 | 6,6−6,7 | |
Колеса (заклинювання, відрив) | 4,2−4,6 | 3,4−3,8 | |
Зчіпний пристрій | 1,2−1,6 | 0,7−1,0 | |
Інші | 7,0−6,8 | 6,6−7,0 | |
Таблиця 2 — Розподіл легкових автомобілів у Харківській області по марках
ВАЗ | 255 748 | 43,9% | |
ЗАЗ | 64 665 | 11,1% | |
ДЭУ | 21 555 | 3,7% | |
Опель | 156 729 | 2,7% | |
Фольксваген | 12 234 | 2,1% | |
Ауді | 9 903 | 1,7% | |
Інші | 193 998 | 34,8% | |
Разом | |||
Число ДТП за 8 місяців 2010 року по Харкову й області склало 8484, у т. ч. по технічній несправності 65; за 11 місяців 2009 — відповідно 10 096 та 59. Але кількість ДТП, у яких поганий технічний стан поглиблював важкість наслідків, значно більша. Зі сказаного можна зробити висновок, що одним з основних факторів, що впливають на безпеку дорожнього руху, є технічний стан ТЗ. Тому перевірка їхнього технічного стану засобами технічної діагностики є важливим і актуальним завданням.
1. Загальне діагностування автомобілів. Задачі дослідження В економіці сучасної держави автомобільний транспорт відіграє величезну роль. Умовимося відносити до системи «автомобільний транспорт» рухомий склад, автотранспортні підприємства (АТП), авторемонтні і сервісні підприємства, водіїв і персонал цих підприємств, а також технічну службу ДАІ, що здійснює державний контроль за технічним станом транспортних засобів, які знаходяться в експлуатації, і органи екологічного контролю.
Процес функціонування цих складових включає в себе ряд контрольних і діагностичних функцій, необхідних для забезпечення і підтримки працездатного стану автотранспортних засобів (АТЗ). Найбільш повно і широко ці функції повинні виконуватися в підприємствах, що здійснюють підтримку технічного стану рухомого складу: в АТП і на станціях технічного обслуговування (СТО).
Сучасна система технічного обслуговування і ремонту (ТОР), звичайно називана «ОР-Д-УН» (тобто обов’язкові роботи, діагностика, усунення несправностей) функціонує за гнучким алгоритмом, що допускає різні технологічні маршрути АТЗ із виконанням більшого або меншого переліку робіт з ТОР і з гнучкою прив’язкою до напрацювання.
Функціонально контрольно-діагностичні операції можна розділити на три групи: контроль, діагностування і прогнозування.
Контроль, або загальне діагностування (ЗД) — це перевірка об'єкта на відповідність його вихідних параметрів вимогам експлуатаційних стандартів з метою визначення можливості дальшого використання об'єкта за призначенням і виявлення непрацездатного об'єкта. Діагностування, або поглиблене діагностування (ПД) — це комплекс операцій, які мають на меті виявлення технічних несправностей, що викликають непрацездатний стан об'єкта. Прогнозування — це передбачення майбутнього технічного стану об'єкта.
Найпоширенішою і найважливішою функцією є контроль — його належить виконувати в усіх підприємствах автотранспорту, в тому числі у ДАІ. ДАІ контролює лише системи, що впливають на безпеку руху: гальмівні системи, рульове керування, шини, амортизатори, фари і світлосигнальні пристрої. Органи екологічного контролю перевіряють вміст окису вуглецю та вуглеводнів у відпрацьованих газах автомобілів з бензиновими двигунами або димність вихлопу автомобілів з дизельними двигунами (хоча обов’язково треба перевіряти ще й вміст оксидів азоту). В АТП і на СТО перевіряють також встановлення керованих коліс (кути розвалу та сходження, поздовжнього та поперечного нахилу шворня) і силові агрегати за вихідними параметрами — тяговою силою або потужністю, витратою палива тощо.
Нормативи деяких параметрів встановлені нормативними документами або вказані у технічних характеристиках транспортних засобів, наприклад, вміст шкідливих речовин у відпрацьованих газах або контрольна витрата палива. Інші, хоча й регламентовані стандартами та правилами, суттєво залежать від методів та засобів діагностування. До цієї групи відносяться у першу чергу ті параметри, що їх визначають на діагностичних стендах з біговими барабанами. Їх треба перераховувати відповідно до особливостей цих стендів. Методами таких розрахунків не завжди володіють практичні робітники, їм доводиться звертатися до фахівців. Тому тема цієї дипломної роботи має практичне значення, а її результати можуть бути використані у ДАІ, в АТП і на СТО.
Отже, задачами дослідження у цій роботі є обґрунтування нормативних значень параметрів загального діагностування, які визначаються на стендах з біговими барабанами, а саме параметрів гальмівних систем і силового агрегату автомобіля BMW 520i.
2. Чинні вимоги до гальм та силового агрегату
2.1 Показники працездатності гальмівної системи Однією з найважливіших перевірок працездатності систем автомобіля, що впливають на безпеку дорожнього руху (СБДР), є перевірка гальм. Тому показники її працездатності, їхні припустимі значення й режими перевірки регламентуються нормативними документами, національними й міжнародними. Ці документи можна розділити на два види: одні висувають вимоги до продукції автомобільної промисловості, тобто до автомобілів, що випускаються із заводів, другі до автомобілів, що знаходяться в експлуатації. Розроблювачі автомобілів закладають у конструкцію гальмівних систем такі можливості, що гарантовано забезпечили б вимоги промислових стандартів. Останні досить високі, щоб створити запас на погіршення технічного стану гальм у процесі експлуатації. Міра цього погіршення обмежена експлуатаційними стандартами, на яких базуються вимоги правил дорожнього руху. Так, верхня межа усталеного уповільнення, закладена конструкторами, може складати для легкових автомобілів 10 м/с2, промисловий стандарт дає значення порядку 7 м/с2, а експлуатаційний стандарт — 5−6 м/с2. Останні вимоги і є тими, котрі використовують ДАІ і підприємства автотранспорту, що виконують обслуговування й контроль автомобілів.
В Україні з 1.01.99 введений у дію стандарт ДСТУ 3649−97 «Засоби транспортні дорожні. Експлуатаційні вимоги безпеки до технічного стану та методи контролю» замість чинного раніше міждержавного стандарту ГОСТ 25 478–95. Цим документом передбачені два види перевірки робочої гальмівної системи (РГС): дорожні і стендові випробування.
Дорожні випробування РГС виконуються з водієм і засобами вимірювань (у разі потреби і з оператором-випробувачем) при «холодних» гальмівних механізмах (РГС не використовувалася протягом 30−40 хв). Початкова швидкість гальмування V0 повинна знаходитися в межах від 35 до 45 км/год. Зусилля на гальмівній педалі (чи іншому органі керування) не повинне бути більш 490 Н для дорожньо-транспортних засобів (ДТЗ) категорій M1 і N1 і 686 Н для ДТЗ інших категорій. У процесі гальмування не допускається коректування водієм траєкторії руху ДТЗ, якщо це не потрібно для забезпечення безпеки руху. У випадку коректування траєкторії результат випробувань не зараховується.
Стан РГС оцінюється за фактичним значенням гальмівного шляху, що не повинний перевищувати норматив, зазначений у таблиці 2.1.
Таблиця 2.1 — Нормативні значення гальмівного шляху для дорожніх транспортних засобів, що знаходяться в експлуатації (за ДСТУ 3649−97)
Тип ДТЗ | Категорія ДТЗ (тягача) | Гальмівний шлях, м, не більш значень, розрахованих за формулами | |
Одиночні ДТЗ | М1 | V0? (0,10 + V0 / 150) | |
М2, М3, N1, N2, N3 | V0? (0,15 + V0 / 130) | ||
Автопоїзди | М1 | V0? (0,15 + V0 / 150) | |
М2, М3, N1, N2, N3 | V0? (0,18 + V0 / 130) | ||
де V0 — початкова швидкість гальмування, км/год.
Згідно з ДСТУ допускається оцінювати працездатність РГС за критерієм значення усталеного уповільнення (jуст) ДТЗ, що повинне бути не менш 5,8 м/с2 для ДТЗ категорії M1 і 5,0 м/с2 для всіх інших (з урахуванням автопоїздів на базі ДТЗ категорії M1); при цьому необхідно контролювати час спрацьовування гальмівної системи, який для ДТЗ із гідроприводом повинен бути не більш 0,5 с і для ДТЗ із іншим приводом не більш 0,8 с.
Час спрацьовування гальмівної системи визначається стандартом України ДСТУ 2886−94 як проміжок часу від початку гальмування до моменту часу, у який уповільнення (гальмівна сила ДТЗ) приймає усталене значення.
При стендових випробуваннях критеріями технічного стану РГС є загальна питома гальмівна сила та час спрацьовування гальмівної системи (ГС) на стенді, а також осьовий коефіцієнт нерівномірності гальмівних сил для кожної осі. Загальна питома гальмівна сила (?г) повинна бути не менш 0,59 для одиночних ДТЗ категорії M1 і 0,51 для всіх інших. При цьому максимальне значення коефіцієнта нерівномірності будь-якої осі (Kн) не повинне перевищувати 20% у діапазоні гальмівних сил від 30% до 100% максимальних значень
(2.1)
де — максимальне значення гальмівної сили на i-ому колесі, Н;
Ma — споряджена маса автомобіля, кг;
g — прискорення вільного падіння, м/с2;
(2.2)
де , — значення гальмівної сили на лівому й правому колесі однієї осі, відповідно, Н;
— більше з двох указаних значень гальмівних сил, Н.
Час спрацьовування гальмівної системи на стенді () — це проміжок часу від початку гальмування до моменту часу, у який гальмівна сила колеса ДТЗ, яке знаходиться в найгірших умовах, досягає усталеного значення (ДСТУ 2886−94).
ДТЗ на стенді обов’язково випробують при повній масі. Допускається проводити випробування ДТЗ із пневматичним приводом у спорядженому стані. У цьому випадку максимальні гальмівні сили коліс і час спрацьовування повинні бути перераховані. Загальна питома гальмівна сила й час спрацьовування на стенді повинні визначатися як середнє арифметичне значення за результатами трьох випробувань, округлене до десятих часток. Якщо різниця між якими-небудь із цих значень і середнім більша 5%, випробування необхідно повторити. Як і на дорозі, випробування слід проводити при «холодних» гальмівних механізмах.
Вимога виконувати стендову перевірку гальм ДТЗ у стані повної маси виходить з обмежених можливостей більшості силових стендів по реалізації гальмівних сил (0,7…0,9 від діючого навантаження на колесо; у інерційних стендів це відношення трохи вище — q=1,0…1,2). Ця вимога занадто завищена; не випадково стандарт допускає для ДТЗ із пневмоприводом (тобто для більшості вантажних автомобілів і автобусів) випробування у спорядженому стані. Не виключено, що вона буде дотримуватися при державних техоглядах легкових автомобілів, де можна посадити в салон водія, інспектора і двох-трьох чоловік із черги. Але вже для мікроавтобусів, не говорячи про вантажні автомобілі й автобуси з гідроприводом гальм, це недосяжно. При регулярних же перевірках в експлуатації (на СТО і станціях діагностики АТП) ця вимога ніколи не буде дотримуватися. З цією метою можна використовувати штучне довантажування перевірюваних коліс, але стенди з довантажувачами масового поширення не одержали.
В усіх діючих стандартах для розрахунку нормативів використане спрощене представлення процесу гальмування. Дійсна гальмівна діаграма має досить складну конфігурацію. Один із прикладів запису уповільнення у функції від часу показаний на рисунку 2.1 (тонка зубцювата лінія). Справжню діаграму заміняють ідеалізованою (суцільна жирна лінія); саме так звичайно уявляють нормальну гальмівну діаграму, виділяючи на ній ділянку запізнювання тривалістю tЗ, ділянку наростання тривалістю tН (сума цих двох тривалостей називається часом спрацьовування tС) і ділянку усталеного гальмування (tУСТ). На ділянці запізнювання діє уповільнення вибігу jB, викликане силами опору котінню, опору повітря й тертя в підшипниках (а також силами тертя накладок об гальмівний барабан чи диск, якщо відсутні зазори через неправильне регулювання). На ділянці усталеного гальмування уповільнення вважають постійним — усталеним (jУСТ).
а — реальна; б — ідеалізована; в — спрощена Рисунок 2.1- Гальмівна діаграма Вважають, що уповільнення на ділянці наростання зростає лінійно. Щоб одержати криві швидкості і гальмівного шляху, досить проінтегрувати ідеалізовану залежність уповільнення від часу. Однак звичайно задачу спрощують ще більше: вважають уповільнення вибігу рівним нулю, а ділянку усталеного гальмування починають від моменту часу tСУ (умовимося називати цей момент умовним часом спрацьовування; деякі фахівці називають проміжок часу до цього моменту «утраченим часом»):
. (2.3)
Далі обчислюють гальмівний шлях
(2.4)
де A=tcy / 3,6=(tз + tн / 2)/ 3,6; B=2?3,62=25,92?26.
Таке спрощення незначно позначається на точності обчислення гальмівного шляху.
Стоянкова гальмівна система (СГС), згідно з ДСТУ 3649−97, перевіряється методом дорожніх чи стендових випробувань. СГС повинна утримувати ДТЗ повної маси категорій M і N у нерухомому стані не менш 5 хв на ділянці дороги з ухилом 16%; ДТЗ спорядженої маси категорії M на ухилі 23%; категорії N на ухилі 31%; причому випробування слід робити для двох положень ДТЗ на ухилі: передніми колесами нагору й униз. Зусилля на органі керування не повинне перевищувати 392 Н для категорії M1 і 588 Н для інших категорій. При випробуванні на стенді значення загальної питомої гальмівної сили повинне бути не менш 0,16 від повної ваги.
Перевірку допоміжної гальмівної системи (ДГС) стандарт передбачає тільки методом дорожніх випробувань. У діапазоні від 35 до 25 км/год за спідометром усталене уповільнення повинне бути не менш 0,5 м/с2 для ДТЗ повної маси; 0,8 м/с2 для ДТЗ у спорядженому стані.
Тут необхідно відзначити ряд недоліків діючої редакції стандарту, що роблять його вимоги суперечливими й несумісними.
У переліку вимог до стендів для перевірки гальм не обговорена швидкість перевірки. Це дозволяє використовувати будь-які стенди — і швидкохідні інерційні, де імітується будь-яка реальна швидкість, і тихохідні силові зі швидкостями 2,5…5 км/год. Тимчасом давно встановлено, що останні помітно завищують значення гальмівних сил у порівнянні з дорожніми випробуваннями.
Розглянемо принциповий недолік показника «питома загальна гальмівна сила»: він ніяк не відбиває фактичного розподілу гальмівних сил по осях ДТЗ, а тому можлива ситуація, коли автомобіль, маючи задовільне значення гф, на дорозі буде гальмувати з юзом, збільшеним гальмівним шляхом і заносом. Це може відбутися через надмірні гальмівні сили на задній осі (на візку тривісного автомобіля). Звичайно, у загальному стандарті складно регламентувати розподіл гальмівних сил по осях, який, строго говорячи, специфічний для кожної конкретної моделі ДТЗ. Однак можна було б дати ліберальні обмеження можливих діапазонів коефіцієнта розподілу гальмівних сил по осях ? для категорій ДТЗ і схем РГС, приблизно такого виду: для ДТЗ категорій M1 і N1 при гальмах однакового типу на всіх колесах -0,5, при дискових гальмах на передній осі і барабанних на задній -0,6; для категорії M2 -0,6; для двовісних ДТЗ категорій M3, N2 і N3 -0,3; для тривісних ДТЗ -0,25; (приведені значення дані винятково для ілюстрації, без глибокого обґрунтування і не повинні сприйматися як рекомендовані).
Не вільні від недоліків і інші вимоги ДСТУ 3649−97. Так, для дорожнього й стендового методів запропоноване проведення випробувань із «холодними» гальмівними механізмами (РГС не використовувалася протягом 30−40 хв). Однак, на дорозі показники обчислюються як середнє арифметичне за результатами двох гальмувань у протилежних напрямках, а для стенда — за результатами трьох випробувань. При цьому в стандарті не обговорено, чи поширюється умова про «холодні» гальма тільки на перше гальмування, чи на кожне. У першому випадку завжди буде спостерігатися істотна розбіжність між першим і другим (наступними) гальмуваннями. У другому між двома гальмуваннями повинно пройти 30−40 хв, а за цей час при дорожніх випробуваннях може помітно змінитися швидкість вітру; на стенді перевірка розтягнеться на 90−120 хв, що зовсім нереально й неприпустимо при масових перевірках в експлуатації. Далі, запропоновано перед проведенням контрольних випробувань на дорозі провести попередні гальмування з початкових швидкостей 20 і 30 км/год і не сказано, чи слід витримувати по 30−40 хв. перед кожним гальмуванням. Крім того, саме визначення стану «холодних» гальм означає в нашій кліматичній зоні початкову температуру від -35 до +35 °С в різні пори року, що може давати розбіжність початкових значень коефіцієнта тертя в гальмівному механізмі, наприклад, від 0,3 до 0,4. Варто ще пам’ятати, що залежності гальмівного моменту від коефіцієнта тертя мають нелінійний характер: зріст гальмівного моменту випереджає зріст коефіцієнта тертя. Наприклад, при збільшенні останнього в 1,5 рази момент на первинній колодці може зростати в 2 рази.
З цього погляду більш логічними є Правила 13 ЄЕК ООН: «…гальмо вважається холодним, якщо температура, виміряна на гальмівному диску чи з зовнішньої сторони гальмівного барабана, нижче 100 °С». Така вимога відповідає реальним умовам роботи гальмівного механізму і не викликає невиправданих утрат часу при випробуваннях — останнє особливо важливе при регулярних стендових перевірках, виконуваних в експлуатації.
При перевірці на стендах стоянкової гальмівної системи теж не все гаразд. При дорожньому методі випробувань СГС працює в статичному режимі, обертання колеса починається лише при недостатній ефективності стоянкового гальма. На силових стендах СГС перевіряють із тими ж швидкостями, що і РГС, на інерційних стендах — із початковою швидкістю близько 15 км/год. У кожному з цих випадків швидкість ковзання в тертьовій парі гальма відмінна від нуля, тому коефіцієнт тертя не такий, як у статиці. Правильно перевірити СГС на стенді можна лише в тому випадку, якщо він дозволяє імітувати статичне випробування гальм, тобто перевірку «на зрив». Це можливо на комбінованих тягово-гальмівних стендах із достатнім крутним моментом навантажувально-привідного пристрою у режимі двигуна, або на стенді будь-якого типу, якщо він обладнаний додатковим приводом (наприклад, ручним) для статичного випробування. Далі, ДСТУ не передбачає стендових випробувань допоміжної гальмівної системи. Однак сучасна стендова техніка дозволяє надійно імітувати її реальну роботу. ДГС можна перевіряти на будь-якому інерційному стенді, гальмівному чи тяговому (останнє справедливо лише для моторних і трансмісійних, але не для колісних гальм-уповільнювачів). Не поглиблюючись в зіставлення силового й інерційного методів стендової перевірки гальм, відзначимо лише, що ДСТУ 3649−97 має потребу у серйозному редагуванні, особливо щодо вимог до стендових випробувань. Тому варто приймати як вихідні ті значення параметрів гальмівної системи, що запропоновані для дорожніх випробувань, а нормативи стендових параметрів виводити з них на основі науково обґрунтованих методик або застосовувати такі методи і засоби стендових перевірок, що надійно імітували б реальну роботу конкретного гальмівного механізму на дорозі. Це й є однією з задач дослідження, виконуваного у цій дипломній роботі.
2.2 Показники працездатності силового агрегату Умовимося розуміти під терміном «силовий агрегат» (СА) двигун, трансмісію і ведучі колеса, тобто весь привід автомобіля. Діючі стандарти на автомобілі не вказують нормативних вимог до параметрів працездатності СА. Проте, ми повинні чітко уявляти собі, чого домагаємося від СА — він повинний: 1) давати необхідну тягову силу на ведучих колесах у необхідному діапазоні швидкостей; 2) витрачати на це не більше визначеної кількості пального; 3) викидати з відпрацьованими газами не більше припустимої кількості токсичних речовин.
Правда, існує стандарт ДСТ 26 899−86 «Стенди роликові для визначення параметрів тягово-швидкісних властивостей і паливної економічності автомобілів і колісних тракторів в умовах експлуатації», який говорить, що тягові стенди повинні в обов’язковому порядку вимірювати наступні діагностичні параметри: потужність на ведучих колесах, тягове зусилля на ведучих колесах, лінійну швидкість на окружності роликів, витрату палива. Це саме ті параметри, що ми перелічили.
Як усякий вихідний параметр, три перераховані показники (тягова сила, витрата палива, вміст токсичних речовин) складаються в результаті складної й суперечливої взаємодії різних факторів. Так, тягова сила визначається, з одного боку, вихідним крутним моментом двигуна, з іншого боку — механічними утратами в трансмісії. У свою чергу, момент визначається досконалістю процесу згоряння, повнотою використання енергії продуктів згоряння, механічними утратами в самому двигуні. На досконалість процесу згоряння впливає правильність роботи систем живлення, запалювання, газорозподілу й охолодження. Енергія продуктів згоряння використовується добре, якщо немає утрат тиску в циліндрі через неправильне регулювання клапанів і надмірного прориву газів через компресійні кільця.
Стандарти задають норматив тільки на викид шкідливих речовин. На потужність і витрату палива стандартних вимог немає. Як же визначити, що таке працездатний стан, а що ні? Зауважимо спочатку, що потужність і витрата палива — показники в першу чергу економічні. Далі відзначимо, що повний знос ЦПГ викликає падіння потужності двигуна усього на 2…3%, якщо інші системи відрегульовані правильно. Отже, ми можемо чекати від двигуна, щоб його крутний момент складав не менше 95% від номінального.
Номінальний крутний момент наводиться у характеристиках двигуна без навісного обладнання (компресора, насоса гідропідсилювача тощо). У першому наближенні будемо вважати, що фактичний момент на 10% менше. Тоді виходить, що припустиме падіння моменту від зазначеного в характеристиці складає 10…15%. Це має перевіряти оператор при діагностуванні. Але ми можемо вимірити, не знімаючи двигун з автомобіля, не момент, а лише тягову силу на ведучих колесах, що пропорційна моменту. Звичайно, доведеться враховувати, що на різних обертах двигуна момент різний. Ми візьмемо зовнішню швидкісну характеристику (ЗШХ) двигуна, перерахуємо оберти колінчатого валу у швидкість і по виведеній формулі побудуємо графік припустимої тягової сили від швидкості.
Щодо витрати палива теж немає стандартних вимог. В характеристиці автомобіля приводиться так звана контрольна витрата палива, що обчислюється в літрах на 100 км при характерній швидкості руху автомобіля чи в характерному режимі - так, за стандартом ЄЕК, для легкових автомобілів на швидкостях 90 і 120 км/год і у міському циклі, за новішим стандартом ЄС — у міському, позаміському та змішаному циклах. Це — норма для нового, ідеально відрегульованого автомобіля. Є також експлуатаційні норми, що враховують і погіршення технічного стану, і різні умови експлуатації, і різне завантаження. Напевно, не буде помилкою сказати, що норма для вихідного параметра «витрата палива» повинна лежати десь між першим і другим числом.
Що ж робити діагносту, який повинен вирішити, у нормі тягова сила й витрата палива, чи не в нормі? Можна заміряти ці параметри на декількох добре відрегульованих автомобілях і разом із головним інженером затвердити власні нормативи. Вони можуть бути різними для двигунів із різним пробігом. Зміст такого підходу очевидний: нам хочеться мати потужність побільше, витрати поменше, але вимоги повинні бути реальними, тобто здійсненними для нашого рухомого складу з урахуванням його віку і для наших умов експлуатації.
Викид токсичних речовин істотно залежить від режиму роботи двигуна. Чадний газ, чи монооксид (окис) вуглецю CO, є продуктом неповного згоряння вуглецю і виникає переважно при недостачі кисню, тобто малому коефіцієнті надлишку повітря. Те ж можна сказати про незгорілі вуглеводні CnHm. Ці шкідливі речовини викидаються при роботі двигуна на режимі холостого ходу чи близькому до нього, коли практично немає зовнішнього навантаження. Відповідно, їх і перевіряють на таких режимах. З іншого боку, набагато токсичніші оксиди азоту (загальне позначення — NOx) утворюються тільки при високих температурах, тобто при роботі двигуна в реальних режимах із середнім і високим навантаженням. Відповідно, і перевіряти їхній викид потрібно під навантаженням.
Отже, для перевірки працездатності СА потрібно виміряти найбільшу тягову силу, витрату палива й викид токсичних речовин у визначених швидкісних і навантажувальних режимах. Це можна зробити методами дорожніх і стендових випробувань.
Дорожні випробування тягових властивостей зараз в експлуатації не проводять. Вимірювання витрати палива при дорожніх випробуваннях раніше виконували регулярно. Робили його на горизонтальній ділянці дороги з твердим покриттям, за два виміри — у прямому й зворотному напрямках. Зрозуміло, при цьому двигун працює не на повному дроселі, витрата істотно відрізняється від ефективної за ЗШХ. Швидкість контролюють по спідометру. Витрату вимірюють об'ємну, у л/100 км, за допомогою мірної посудини, установленої на кабіні зовні, щоб посудина була видна водію. Потім такі випробування заборонили — великий ризик пожежі при роботі з негерметичною мірною посудиною. Тепер, коли з’явилися витратоміри, що їх включають у паливопровід і герметизують, такого ризику немає.
Уповільнення вибігу характеризує суму зовнішніх опорів плюс сили тертя в підшипниках маточин та у роз'єднаній трансмісії. Для оцінки технічного стану автомобіля найцікавіша саме остання складова. Виділити її на тлі суми зовнішніх опорів непросто: вона порівняно невелика. Більш помітна вона на малих швидкостях, коли опір повітря, пропорційний квадрату швидкості, сильно падає, але на малих швидкостях дуже велика похибка спідометра. Підвищені утрати на тертя можуть служити симптомом ряду несправностей: перетягнені підшипники маточин; немає мастила в агрегатах і тертьових парах трансмісії і ходової частини; надмірні зноси в зубчастих парах, через що виникає заклинювання; немає зазорів в одному чи декількох гальмівних механізмах, через що накладки постійно затирають по барабану (диску). Остання несправність може привести до серйозного ушкодження автомобіля.
Стендові випробування дозволяють виконати всі потрібні перевірки і деякі крім того. Так, якщо стенд обладнаний навантажувальним пристроєм, можна виміряти максимальну тягову силу в усталеному режимі. Перевірки за вибігом можна проводити, у залежності від конструкції стенда, не тільки по кожній осі, але і по кожному колесу — для діагностування, особливо поглибленого діагностування, це набагато зручніше. Перевірку витрати палива можна виконувати з використанням мірної посудини не тільки об'ємним, але і масовим (ваговим) способом, який точніше, ризик пожежі при цьому набагато менший, ніж на дорозі, тому що мірна посудина знаходиться на окремому столі.
Вибір між дорожніми й стендовими випробуваннями найчастіше визначається економічними факторами: у цілому сумарні витрати на випробування парку автомобілів дорожнім методом протягом якогось періоду часу завжди будуть вище, але придбання й монтаж стенда з будівництвом і устаткуванням поста пов’язане з великими початковими витратами. Відзначимо ще одне міркування: для дорожніх випробувань потрібна зручна ділянка дороги — гарне покриття, відсутність обмежень швидкості, слабка інтенсивність руху (щоб не довелося на мірній ділянці робити обгони чи маневрувати якось інакше) і, нарешті, достатня довжина, щоб можна було вийти на режим, виконати розгін, а потім вибіг, а це не завжди доступно. З іншого боку, є випадки, коли стендові випробування неспроможні. Наприклад, при перевірці якості й ефективності обтічників і регулюванні їхнього кріплення на кабіні - в АТП це можна зробити лише на дорозі, по прискоренню в режимі розгону, по уповільненню в режимі вибігу чи по витраті палива в усталеному режимі при характерних швидкостях руху.
При стендових випробуваннях легше оцінити утрати в трансмісії і маточинах коліс: кожне колесо чи хоча б кожна вісь перевіряється окремо і немає опору повітря. Крім того, можна за допомогою домкратів знизити навантаження на колеса, що перевіряються, до мінімального значення — аби колеса й ролики оберталися без прослизання — і тим різко зменшити опір котінню, тертя в підшипниках коліс і бігових барабанів стенда. Тоді цікаві для нас симптоми несправностей будуть складати не одиниці відсотків від сумарних опорів, а, наприклад, 20…30, а то й 50% (коли затирають накладки), тобто ймовірність їхнього виявлення набагато вища.
3. Технічна характеристика автомобіля BMW 520i E28
3.1 Короткий опис автомобіля Автомобіль BMW 520i E28 — це легковий автомобіль середнього класу, який випускався у 1981;1994 роках.
Автомобіль задньопривідний, і його компонувальна схема характеризується переднім подовжнім розташуванням силового агрегату.
Я мав відносно вільний доступ до автомобіля BMW520i з чотирьохдвірним кузовом седан, двигуном робочим об'ємом 2 л потужністю 92 кВт і механічною п’ятиступеневою коробкою передач. На цьому автомобілі я виконував експерименти, для нього ж була виконана більшість розрахунків.
Рисунок 3.1. — Автомобіль BMW520i
На автомобілях BMW520i застосовувався чотиритактний, чотирициліндровий бензиновий двигун, встановлений вздовж осі автомобіля. Розподільний механізм — клапанний, з одним розподільним валом верхнього розташування. Система живлення — впорскування. Основні технічні дані автомобіля наведені у таблиці 3.1.
Таблиця 3.1 — Основні технічні дані експериментального автомобіля BMW520i Е28
Показник | Значення | |
Колісна формула | 4?2 | |
Повна маса, кг | ||
Споряджена маса, кг | ||
Маса при проведені експерименту, кг | ||
Шини Радіус статичний, мм | 195/65R15 82T Cordiant Sport | |
Максимальна швидкість автомобіля, км/год | ||
Двигун | M20 | |
Система сумішоутворення | K-Jetronic | |
Діаметр циліндра і хід поршня, мм | 80?66 | |
Робочий об'єм, см3 | ||
Ступінь стиснення | 9,8 | |
Номінальна потужність «нетто», кВт / при частоті обертання, хв-1: | 92/ 5800 | |
Максимальний крутний момент, Н? м / при частоті обертання, хв-1 | 165 / 3400 | |
Витрата палива, л/100 км: при 90 км/год / 120 / міський цикл | 7.6 / 10.2 / 12.7 | |
Максимальна швидкість автомобіля, км/год | ||
Передаточне число коробки передач | ||
I | 3,674 | |
II | 3,325 | |
III | 1,612 | |
IV | 1,229 | |
V | 1,0 | |
Задній хід | 3,91 | |
Головна передача | 4,063 | |
3.2 Загальний опис гальмівної системи
На автомобілі застосована робоча гальмівна система з двома контурами, що значно підвищує безпеку водіння. Один контур гідроприводу забезпечує роботу передніх і задніх гальмівних механізмів, інший — тільки передніх. У нормальному стані обидва контури працюють рівномірно, однак при відмові одного з контурів робочої гальмівної системи використовується другий контур, і сила гальмування все одно буде діяти на два колеса, забезпечуючи при цьому зупинку автомобіля з достатньою ефективністю.
Стоянкова гальмівна система тросового типу з механічним приводом, діє на гальмівні механізми задніх коліс.
Схема гальмівної системи показана на рисунку 3.2. Загальна технічна характеристика гальмівної системи приведена в таблиці 3.2.
Таблиця 3.2 — Технічна характеристика гальмівної системи автомобіля BMW520i
Передні гальмівні механізми | дискові | |
Число робочих циліндрів гальмівного механізму на одному колесі | ||
Діаметр робочих циліндрів, мм великих малих | 42,85 33,96 | |
Задні гальмівні механізми | барабанні | |
Число робочих циліндрів гальмівного механізму на одному колесі | ||
Кількість поршнів в одному циліндрі | ||
Діаметр циліндра, мм | 20,6 | |
Діаметр барабана, мм | ||
Гідравлічний привід гальмівних механізмів | роздільний, оснащений сигнальним пристроєм і регулятором тиску задніх гальм | |
Головний гальмівний циліндр | двохкамерний, типу `тандем' | |
Діаметр головного циліндра, мм | 23,81 | |
Регулятор тиску | гідравлічний з навантажувальною пружиною | |
Підсилювач | вакуумний, механічний | |
Рисунок 3.2. — Барабанні гальма задніх коліс
Рисунок 3.2. — Схема гальмівної системи автомобіля BMW 520i E28
1 — гальмівний механізм переднього колеса; 2 — трубопровід контуру «ліве переднє - праве заднє гальма»; 3 — головний циліндр гідроприводу гальм; 4 — трубопровід контуру «праве переднє - ліве заднє гальма»; 5 — бачок головного циліндра; 6 — вакуумний підсилювач; 7 — гальмівний механізм заднього колеса; 8 -регулятори тиску у приводах лівого та правого задніх гальм; 9 -гальмівна педаль; А — гнучкий шланг переднього гальма; В — гнучкий шланг заднього гальма
4. Тяговий баланс на стенді
Для перевірки на стенді працездатності силового агрегату потрібно вимірювати значення найбільшої тягової сили, витрати палива й вмісту токсичних речовин у реальних швидкісних і навантажувальних режимах. Конкретизуємо ці вимоги, переводячи їх у показники стенда.
Для перевірки силового агрегату потрібно реалізувати сили зчеплення, помітно менші, ніж при гальмуванні (q?0,5), але в тривалому усталеному режимі, а також мати плавне регулювання навантаження і високу точність його вимірювання. Загалом тут вимоги значно м’якші, ніж при перевірці гальм.
Щоб знайти шлях виконання цих вимог, розглянемо закономірності, що зв’язують між собою обертання бігових барабанів стенда й колеса, що спирається на них. Рух системи колеса-барабани буває усталеним і неусталеним. Розрізняють обкатний і навантажувальний усталені режими.
Обкатний режим — це рівномірний рух барабанів стенда й коліс, що опираються на них, із приводом від двигуна стенда. На діагностичних стендах обкатні режими використовують, наприклад, для перевірки легкості обертання коліс. На обкатних стендах заводів такі режими використовують для холодного обкатування нового чи відремонтованого автомобіля, яке виконують для попереднього припрацьовування сполучених деталей.
Навантажувальний режим — це рівномірний рух барабанів і коліс із приводом від двигуна автомобіля. На діагностичних стендах навантажувальні режими використовують для перевірки тягових властивостей і витрати палива, на обкатних — для гарячого обкатування автомобіля при працюючому двигуні і різнім зовнішнім навантаженні.
Тривалість усталеного режиму досить велика і на обкатних стендах може складати десятки хвилин і навіть годин, а на діагностичних набагато коротшазвичайно одиниці чи десятки секунд. Це залежить від темпу стабілізації режиму, наприклад, прогріву перевірюваної системи чи вузла автомобіля, від швидкодії системи вимірювань й реєстрації параметрів і від необхідності участі людини в стабілізації режиму й зчитуванні показань вимірювальних приладів. У будь-якому режимі повне ковзання колеса по барабанах неприпустиме, воно викликає місцевий перегрів і знос шини, спотворює картину процесу й результати вимірювань.
В обкатному режимі опір руху створюють власні втрати в приводі, сили тертя в передачі від двигуна стенда до робочих барабанів, в опорах барабанів, у силовому зв’язку між барабанами, опір котінню колеса по барабанах, утрати в підшипниках колеса й сили тертя всіх обертових об'єктів об повітря (так названі «вентиляторні» втрати). Це постійні опори, вони діють завжди, незалежно від характеру перевірок. Якщо на стенд установлені ведучі колеса, у число постійних опорів входять також сили тертя у зв’язаних з колесом обертових частинах автомобіля, наприклад, у роз'єднаній трансмісії.
При окремих діагностичних операціях можуть додаватися опори в інших частинах автомобіля. Так, при поглибленому діагностуванні двигуна іноді перевіряють суму механічних утрат і втрат на компресування повітря в циліндрах, які, природно, додаються до опорів. При перевірці гальмівних властивостей додаються сили тертя в гальмах. Умовимося називати опори останньої групи «корисними». У загальному виді силовий баланс для обкатного режиму запишеться так [5]:
(4.1)
де Мтрк — момент сил тертя в колесі та постійно зв’язаних з ним обертових частинах автомобіля, Н? м;
Мтрс — момент сил тертя в стенді, Н? м;
Мкот — момент від опорів котінню, Н? м;
Мп — момент від опору повітря, Н? м;
Мкор — момент від «корисних опорів», Н? м.
Усі зазначені моменти повинні бути приведені до однієї осі, краще усього до осі приводного барабана чи колеса. При аналізі зручніше користуватися не моментами й іншими характеристиками обертального руху, а силами й характеристиками поступального руху — вони звичніші й наочніші. Якщо всі перераховані моменти приведені, наприклад, до осі колеса, то, розділивши їх на радіус колеса Rк, можна перейти від моментів M до сил F у контакті колеса з барабаном:
. (4.2)
Тут Rк — це динамічний радіус, або ж радіус котіння без проковзування; у першому наближенні його можна вважати рівним статичному радіусу на дорозі; за більш точними даними В.О. Зуєва, він трохи більший від статичного радіусу — десь на 1,5…3%.
Утрати на тертя в підшипниках стенда й колеса підкоряються загальним закономірностям і можуть бути розраховані звичайними способами:
(4.3)
де — радіальне навантаження на пари підшипників, Н; векторна сума всіх зовнішніх навантажень (наприклад, дійсного радіального зусилля притиснення колеса до барабана N) і власної ваги елемента, що спирається на цю пару підшипників;
— коефіцієнт опору котінню кульок (роликів) по кільцях для даного типу підшипників;
— радіус, на якому діє рівнодіюча сил опору котінню кульок (роликів) по кільцях; можна приймати його рівним середньому радіусу підшипника, м;
R — радіус поверхні, до якої приводяться сили (радіус бігового барабана стенда чи радіус колеса), м.
Утрати на котіння колеса по барабанах
(4.4)
де N1, N2 — радіальні зусилля притиснення колеса до переднього (першого) і заднього (другого) барабана, Н;
— коефіцієнти опору котінню шини по передньому (першому) і задньому (другому) барабану відповідно.
Зусилля N1 та N2 істотно залежать від дійсного навантаження на колесо в даному режимі Gк, від діючих подовжніх сил і від геометрії барабанного блока, зокрема, кута між центрами барабанів і колеса й відстані між осями переднього і заднього барабанів по горизонталі і вертикалі. Значення коефіцієнта опору котінню сильно залежить від співвідношення радіусів колеса й барабанів, слабкіше від зусилля притиснення колеса до барабана, а також від швидкості і від тривалості режиму. За даними О.В. Сєрова, коефіцієнт опору котінню зв’язаний з відношенням радіуса барабана до радіуса колеса зворотною залежністю (див. рисунок 4.1). Він досить близький до дорожнього (на негладкій дорозі) при співвідношенні радіусів 0,4…0,5. Так рекомендують вибирати радіус барабанів, особливо для тягових стендів.
Опір повітря обертанню колеса на стенді не вивчено.
Коли діють значні корисні опори, частка постійних опорів у загальному балансі сил невелика. У першому наближенні їх можна оцінити за вертикальним навантаженням на колесо й коефіцієнтом сумарних постійних опорів
. (4.5)
Рисунок 4.1 — Вплив радіуса бігового барабана на коефіцієнт опору котінню Значення становлять 0,025…0,040, менші значення відносяться до шин високого тиску (вантажні автомобілі й автобуси — 0,025…0,030), більші - до шин низького тиску (легкові автомобілі, мікроавтобуси — 0,030…0,040). За даними 8, істотно залежить від швидкості.
Однак всі ці дослідження проводилися на старих діагональних шинах. Зараз же на легкових автомобілях застосовуються тільки радіальні шини, опір коченню яких по роликах не вивчено.
Перевірка гальм силовим способом — це окремий випадок усталеного обкатного режиму з корисними опорами. Баланс сил описується тим же рівнянням (4.2), де корисним опором Fкор виступає гальмівна сила на перевірюваному колесі Fг. Про неї судять за вимірюваною датчиком силою Fд, причому показувальний прилад проградуйований у значеннях Fг з урахуванням перевідного коефіцієнта, що враховує радіус барабана r, відстані L від осі привода до осі датчика сили і передаточного числа iр редуктора, якщо реактивний момент вимірюють на двигуні стенда
. (4.6)
У цьому випадку можна виключити з балансу сил член Fтрк, тому що ці сили при гальмуванні і на стенді, і на дорозі додаються до сил, створюваних гальмівним механізмом, і входять у цікаву для діагноста величину. Можна також через малу швидкість виключити опір повітря Fп; тоді
. (4.7)
При перевірці гальм проковзування барабанів по шині (юз) абсолютно неприпустиме: при юзі діє вже не гальмівна сила, а сума сил зчеплення шини з барабанами, яка ніяк не пов’язана з фактичною гальмівною силою і різко обмежує можливості стенда по її реалізації. Для запобігання юзу робочу поверхню барабанів на силових стендах роблять негладкою, а це різко підвищує опір котінню. Редуктор також збільшує втрати на тертя в приводі. Значення в цьому випадку приблизно вдвічі більше, ніж на гладких барабанах швидкохідного стенда без редуктора: 0,05…0,08. Вимірювані гальмівні сили на силовому стенді складають 0,6…0,9 від навантаження на колесо. Отже, постійні опори вносять у вимірювану величину помилку порядку 5,5…13%. Можна установити нуль у вимірювальній системі по режиму прокручування стенда без автомобіля чи з автомобілем без гальмування. Це зменшить систематичну помилку, але не виключить її цілком.
У навантажувальному режимі двигун установленої на стенді машини переборює опір у трансмісії, «постійні» опори і додатковий опір, створюваний навантажувальним пристроєм стенда («навантаження»). Силовий баланс для навантажувального режиму запишеться так:
(4.8)
де Fтрк — тягова сила на ведучих колесах, Н;
Fнав — навантаження стенда, Н.
У неусталених режимах кутові швидкості елементів системи колеса-барабани і, відповідно, окружні швидкості на поверхнях котіння колеса й барабанів непостійні і міняються від V1 до V2. Розрізняють два типи неусталених режимів: вибіг (V1 > V2) і розгін (V1 < V2). Розгін — це рух із позитивним прискоренням, вибіг — із негативним прискоренням (уповільненням j).
Вільним називають вибіг без додаткового гальмування автомобілем чи стендом, коли уповільнення створюється тільки постійними опорами. Розгін також може відбуватися без додаткових опорів чи з ними. Будемо називати останні два режими «вільний розгін» і «утруднений розгін».
Рівняння балансу сил для неусталених режимів зводяться до загального вигляду
(4.9)
де — сума приведених до розглянутої осі моментів інерції тіл, що беруть участь у русі, кг? м2;
— кутове прискорення елемента, до осі якого приведений рух, с-2.
Якщо використовувати поняття «приведена маса», то замість балансу моментів можна записати баланс сил (у ньютонах)
(4.10)
де — сума приведених мас тіл, що беруть участь у русі, кг;
a — лінійне прискорення на поверхні котіння, м/с2.
У режимі вибігу створювана приводом сила Fпр менша від суми сил у правій частині без інерційного члена. Режим вибігу використовують при діагностуванні для визначення тих чи інших сил, найчастіше — сил тертя в колесі й у роз'єднаній трансмісії Fтрк. Вимірюють уповільнення і по його значенню обчислюють суму сил, що діють у даному режимі:
. (4.11)
Існуючий критерій вибору інерційної маси стенда по еквівалентності масі автомобіля важко застосувати до стендів для пересувних діагностичних станцій ПДС. Зменшення інерційної маси також обмежують два критерії. Перший — повний час гальмування на стенді повинний завжди перевищувати час спрацьовування приводу, другий — забезпечення реального температурного режиму гальм при стендовій перевірці. При виконанні другого критерію автоматично виконується і перший. Однак при цьому можна прийняти практично будь-яку масу.
Тому для обґрунтування вибору оптимальної приведеної інерційної маси запропонований критерій, який можна сформулювати так: приведена інерційна маса стенда повинна бути настільки великою, щоб сумарна помилка визначення гальмівної сили, яка викликана похибкою вимірювальної системи і неточним знанням стендової приведеної маси, не перевищувала величини, припустимої стандартами.
Похибку приведеної маси стенда можна обчислити по формулі
(4.12)
де , — припустимі похибки визначення на стенді відповідно гальмівної сили та сповільнення.
Згідно з існуючими вимогами %. Похибка виміру сповільнення визначається конструкцією вимірювальної системи. На стендах ХАДІ, відповідно до результатів метрологічної атестації, %. З огляду на це, припустиме значення похибки визначення приведеної маси стенда складає - .
Оскільки ця похибка є відносною, вона може бути визначена по формулі
(4.13)
де , — абсолютні значення похибок виміру приведених мас відповідно стенда і коліс, кг;
— дійсні значення приведених мас відповідно стенда і коліс, кг.
Похибка є систематичною, тому що визначається при проведенні періодичних перевірок з високою точністю (методом падаючого вантажу чи біфілярного підвісу). Тому з формули (4.13) її можна вилучити. Тоді запропонований критерій вибору приведеної інерційної маси стенда можна записати так:
. (4.14)
Отже, для того щоб ми змогли зробити усі необхідні перевірки і правильно визначити параметри, ми повинні знати приведену масу стенда, трансмісії і ведучих коліс автомобіля. В літературі про це сказано мало і через це була поставлена задача експериментально визначити приведену масу стенда, трансмісії і ведучих коліс автомобіля. Приведена маса стенда визначається конструкторами; наприклад, у випадку стенда ПДС-Л, для якого ми будемо розраховувати нормативи, вона дорівнює приблизно 200 кг.
Для кількісної оцінки запропонованого критерію вибору приведеної інерційної маси стенда (формула 4.14) досліджена можлива варіація приведеної маси колеса. Вона може варіювати внаслідок зносу протектора шини і металевих деталей гальмівних механізмів, неякісного виготовлення шини, зміни тиску і т.д. Найбільший вплив на величину інерційної маси колеса робить знос протектора (момент інерції шару, що зношується, складає близько 30% від загального моменту інерції колеса).