Електрошлакове зварювання
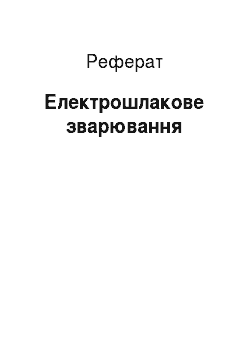
Щоб електродний метал надійно сплавлявся із головною, поверхню останнього мусить бути попередньо оплавлена плюс температуру, близьку до температурі плавлення. З іншого боку, поверхню металу повинна бути надійно захищена від окислення. При дугового зварюванні в нижньому становищі розплавляння крайок і заповнення розбирання металом відбувається, зазвичай, не одночасно. Метал з порожнини… Читати ще >
Електрошлакове зварювання (реферат, курсова, диплом, контрольна)
Міністерство загального характеру і професійної освіти Російської Федерации.
ОмГТУ.
Кафедра устаткування та технології зварювального производства.
Курсова работа.
По курсу «Інженерне творчество».
На тему: «Электрошлаковая сварка».
Выполнил:
Студент МСФ С-110.
Проверил:
Доцент к.т.н.
Шестель Л.А.
р. Омськ, 2000.
Электрошлаковая зварювання (ЭШС) знайшла широке застосування при виготовленні виробів металургійного, прокатного й енергетичного устаткування, в котло-, гідроі прессостроении, у будівництві т.д. З допомогою цього способу зварювання виконуються конструкції з вуглецевих і легованих сталей, титану, алюмінію, міді їх сплавів. Діапазон свариваемых толщин металу становить 20−2500 мм.
Сучасна оснащённость ЭШС така, що дозволяє вирішувати практично будь-які завдання промисловості у найвищому технічному рівні. До того ж, як засвідчило багаторічний досвід, ефективність застосування ЭШС значною мірою залежить від правильного вибору зварювального устаткування, і навіть раціонального вирішення питань техніки зварювання застосування відповідної технологічної оснастки.
Аннотация.
У цьому роботі мною розглянуто такий її різновид зварювання, як электрошлаковая зварювання. Був розглянутий процес зварювання, засоби зварювання і відповідно до їхніх використання у різних галузях промисловості, у цьому однині і машинобудування. Приведено таблиця класифікації різних способів зварювання. Розглянуто деякі технічні характеристики даного процесса.
1. Опис процесса.
2. Технологічні параметры.
2.2 Класифікація різновидів электрошлаковой сварки.
2.3Особенности електрошлакового процесса.
3. Область применения.
Заключение
.
Опис процесса.
Спосіб зварювання, заснований на виділенні тепла під час проходження електричного струму через розплавлений шлак, отримав назву электрошлаковой зварювання. У просторі, утвореному крайками свариваемых виробів і формуючими пристосуваннями, створюється ванна розплавленого шлаку, у якому занурюється металевий стрижень — електрод. Струм, проходячи між електродом і основним металом, нагріває розплав і підтримує у ньому високої температури і електропровідність. Температура шлаковой ванни повинна перевищувати температуру плавлення основного і електродного металу. Шлак плавить занурений до нього електрод і крайки вироби. Розплавлений основний метал разом із электродным проводить дні шлаковой ванни і утворить металеву ванну, яка, затвердевая, дає шов, який би з'єднав крайки вироби. Принаймні розплавлювання електрод подається вниз.
Найкращі умови для плавлення основного металу й у отримання глибокої шлаковой ванни створюються при вертикальному становищі осі шва. Тому электрошлаковая зварювання застосовується найчастіше разом із примусовим формуванням зварювальної ванни. Электрошлаковая зварювання в нижньому становищі менш зручна і не распространения.
Технологічні параметри процесу электрошлаковой зварювання (ЭШС).
Сущность методу примусового формування полягає у штучному охолодженні поверхні металевої ванны.
Основне призначення шлаків при эшс — перетворення електричної енергії в теплову. Тому основний характеристикою шлаків був частиною їхнього електропровідність і залежність її від температуры.
Якби існував шлак, не змінює своєї провідності в залежність від температури, його порівняно легко можна було б використовуватиме цілей зварювання. Завжди можна підібрати таку напругу, яке, будучи докладеним до постійному опору, викликає виділення у тому опір необхідної потужності і, отже, буде підтримувати у ньому необхідну температуру. Насправді провідність розплавлених шлаків різко підвищується зі зростанням температури, а нижче певній температури шлаки практично є непроводниками. Це обставина ускладнює стабілізацію процесса.
Деякі шлаки, містять двоокис титану, є хорошими провідниками навіть у твердому стані при кімнатної температурі. Такого роду шлаки мають електронної провідністю, на відміну іонній провідності шлаків, що у рідкому состоянии.
На відміну від дугового зварювання під флюсом при электрошлаковой зварюванні майже вся електрична потужність передається шлаковой ванній, як від неї электроду і основному металу. Умовою стабільності процесу є сталість температури шлаковой ванни, інакше кажучи, рівність одержуваного і отдаваемого тепла.
Однією з перешкод, які виникають за практичне застосування електрошлакового процесу, є можливість появи дугового розряду між електродом та вільної поверхнею шлаковой ванни або, переважно у глибині шлаковой ванни. Такий розряд буває дуже хистким, й поява його за электрошлаковой зварюванні можуть призвести до утворення дефектів шва. Щоб запобігти дугового розряду зварювання потрібно ведуть у умовах, протилежних умовам стабілізації дугового розряду: у глибокій шлаковой ванній, на перемінному струмі, за низького напрузі холостого ходу і з застосуванням шлаків з низьким стабілізуючими властивостями. Ці заходи ускладнюють поява дугового розряду і збільшують стійкість електрошлакового процесса.
Проте за надмірному погіршенні умови стійкості дугового розряду, трапляється так порушення стійкості електрошлакового процесу внаслідок, наприклад, випадкового витікання шлаковой ванни. Для відновлення шлаковой ванни потрібно б досить стійкий дугового розряд при дрібної ванні та швидке його стійкості при глибокої ванній. Цього досягти застосовуючи електрод малого діаметра, збільшуючи зазор між крайками чи змінюючи відповідним чином напруга холостого ходу зварювального трансформатора. Збільшення зазору економічно невыгодно.
Застосування шлаків з урахуванням фтористого кальцію, які мають великий електропровідністю, значно скорочує час, необхідне переходу від дугового процесу электрошлаковому.
Щоб електродний метал надійно сплавлявся із головною, поверхню останнього мусить бути попередньо оплавлена плюс температуру, близьку до температурі плавлення. З іншого боку, поверхню металу повинна бути надійно захищена від окислення. При дугового зварюванні в нижньому становищі розплавляння крайок і заповнення розбирання металом відбувається, зазвичай, не одночасно. Метал з порожнини, виплавленої дугою, відкидається тому, а порожнину заповнюється лише після відводу дуги. При зварюванні вертикальних швів це явище виражено ще більше чітко; метал крайок, оплавляемых дугою чи шлаком, стікає вниз, створюючи загальну ванну з электродным металом. Через війну оплавлення крайок над металевої ванній завжди утворюється незаповнена металом полость.
Там, коли крайки основного металу починають плавитися значно вища поверхні металевої ванни, крайки, які перебувають безпосередньо над ванній, може стати охлаждёнными нижче від температури плавлення. І тут можливо зване несплавление. Його не було варто плутати з непроваром крайок, що вони залишаються нерасплавленными. При несплавлении крайки виявляються оплавленими, але вони сплавляються з металом шва.
Несплавление стає можливим при занадто високу напругу зварювання, надмірно глибокої шлаковой ванні та під час використання шлаків, мало змінюють свою електропровідність і в’язкість з температурою. При нормальних характеристиках шлаків і вибраних режимах зварювання передчасному оплавлению перешкоджають теплоі электроизоляционная прошарок, утворена шлаком у холодних крайок вироби. Завдяки йому струм між електродом і металевої ванній проходить як у ізольованій трубці і нагрівання крайок навіть за великих межэлектродных проміжках починається біля самісінької поверхні металевої ванны.
Більшість тепла, выделяющегося в шлаку, переноситься ванну электродным металом. Майже вся теплова енергія передається основному металу через поверхню металевої ванны.
Якщо напруга зварювання тримати вище, ніж потрібно для розплавлювання електрода і крайок основного металу, то надлишок тепла в шлаковой ванній йде збільшення проплавления крайок. Якщо цього немає потреби, це тепло можна використати в плавлення присадочного матеріалу. Його можна подавати як дроту, як і і електрод, або окремими дрібними кусками.
З зменшенням діаметра електрода межэлектродный проміжок зменшується і небезпека несплавления різко знижується. Ще більший вплив на величину межэлектродного проміжку і характеру плавлення основного металу надають коливання електрода в горизонтальному направлении.
Рентгенографические дослідження та осциллографироваие процесу электрошлаковой зварювання в різних режимах показали, що метал переноситься з електрода в металеву ванну як крапель. Розміри крапель тим більше коштів, що менше зварювальний струм, вище напруга між електродами і металевої ванній та що більше глибина шлаковой ванни. Навпаки, зниження напруги зварювання, зменшення глибини ванни і підвищення струму сприяють мелкокапельному переносу електродного металу у зварювальну ванну.
При великих швидкостях подачі електрода, звичайних під час зварювання малоуглеродистых сталей, низькому напрузі чи малої глибині шлаковой ванни краплі металу можуть з'єднуватися з металевою ванній раніше, ніж відокремлюватися від електрода. Таке металеве з'єднання електрода з ванній є дуже короткий час; воно майже миттєво руйнується під дією електродинамічних зусиль, що виникають у провіднику і різко збільшуються зі зростанням щільності струму. Проте внаслідок великий частоти замикань середнє час проходження струму через метал може складати значну частину загального часу зварювання. Це не носить характеру короткого замикання. Загальна провідність зони зварювання в останній момент замикання зростає лише у 1,5 — 1,7 разу. Потужність, залежно від характеристики джерела харчування, змінюється незначно чи возрастает.
У такій напрямі змінюють характер електрошлакового процесу переміщення електрода в шлаку в горизонтальному напрямі. Зіштовхуючись із більш холодними объёмами шлаку, електрод плавиться великий глибині, і за певних режимах краплі не встигають відокремлюватися від кінця електрода до замикання з металевою ванной.
Электрошлаковый процес може протікати однаково стійко як у постійному, і на перемінному струмі. Рід зварювального струму надає значний вплив перебіг металургійних, які протікають в шлаковой ванній. При зварюванні постійному струмі помітно розвиваються явища электролиза.
Відомо, що з электродуговой зварюванні стійке горіння дуги можливе лише за порівняно великий щільності струму. Діапазон практично застосовуваних плотностей струму при ручний дугового зварюванні невеликий, але за зварюванні під флюсу він у межах від 20 до 200 а/мм2. На відміну від дугового зварювання электрошлаковый процес йде досить стійко при змінах щільності струму на досить широкому діапазоні від 0,2−0,3 а/мм2 (при зварюванні електродами великого перерізу) до 200−250 а/мм2 (під час зварювання дротом діаметром 3мм). Отже, характерною рисою електрошлакового процесу є висока стійкість його за низьких плотностях струму (в 100−200 раз менших, аніж за дугового сварке).
2.1. Класифікація різновидів электрошлаковой сварки.
Рис. 1. Класифікація різновидів эшс.
Тут приведено схема різних застосувань електрошлакового процесу. Розрізняють дві основні групи прийомів электрошлаковой зварювання: 1) зі вільним формуванням зварювальної ванни і 2) з примусовим формуванням її. З іншого боку, можливо розподіл на інших ознаками: у зв’язку зі струму, характеристиці джерела харчування, ступеня механізації тощо показателям.
Электрошлаковая зварювання з примусовим формуванням може виконуватися різними приёмами, залежать від типу електродів, способу запровадження їх в розбирання і підвода до них зварювального струму. У тому числі на цей час застосовуються: зварювання дротом, зварювання електродом великого перерізу, зварювання плавящимся мундштуком і стыковая электрошлаковая зварювання (контактношлаковая).
Для зварювання металу великий товщини электроду слід надавати коливальні руху на напрямі товщини металу або збільшувати число електродів чи змінювати їх перетин. Найчастіше застосовується поєднання цих приёмов.
При зварюванні з коливаннями число електродів звичайно перевищує трьох, щоб уникнути надмірного ускладнення апаратури. При порівняно коротких швах мундштуки можна вводити в розбирання не збоку, а згори. І тут число електродів то, можливо значно більшою трьох. У обох випадках мундштуки разом із подає механізмом рухаються вгору зі швидкістю освіти шва.
Поруч із електродами суцільного перерізу при описаних вище схемах електрошлакового процесу можна застосовувати так звана порошкова дріт чи трубчастий електрод з додаткового легування металу шва.
Якщо мундштуки зробити щось із тієї самої (приблизно) матеріалу, як і электродные дроту, і хто подає механізм під час зварювання не піднімати, то мундштуки при підході до них шлаковой ванни будуть плавитися і переходити в шов. Цей прийом электрошлаковой зварювання називається зварюванням плавящимся мундштуком.
При зварюванні трьома пластичними електродами, мундштуки відсутні, а механізм вертикального переміщення з нерухомо закріпленим у ньому електродом рухається вниз назустріч шву.
Електроди великого перерізу може мати найрізноманітнішу форму поперечного перерізу: прямокутну, кільцеподібну (для зварювання циліндричних деталей) чи фасонну. Для ущільнення зливків, виливки, переплавлення та інших видів робіт з велику кількість переплавляемого металу можна застосовувати електроди з брикетированной стружки та інших відходів. У окремих випадках для регулювання проплавления крайок можуть застосовуватися порожнисті електроди, заповнені металевої крупкой.
Стыковая электрошлаковая зварювання, чи, як її називають, контактношлаковая, особливий тим, що з ній відсутня присадочный метал; струм пропускається між свариваемыми частинами. Під час цієї схемою свариваемые поверхні займають горизонтальне становище; шлаковая ванна перебуває між нижньої деталлю і верхньої. При пропущенні струму через шлак свариваемые поверхні оплавляються, а над нижньої поверхнею утворюється ванна розплавленого металу. Після цього свариваемые частини зближуються; шлак витісняється з простору з-поміж них, розплавлений метал твердне і деталі виявляються звареними між собою. Момент вимикання струму може іноді передувати осаді свариваемых деталей.
Зварювання дротом нині широко застосовується у промисловості. Вона дає можливість отримувати шви різної форми з досить рівномірним проваром заданої ширини. Дротом можна зварити метал завтовшки від 20 до 500−600 мм за будь-якої довжині шва.
Пластинчастими електродами зварюють прямолінійні шви будь-який товщини і порівняно невеличкий довжини (до1−1,5 м). Що стосується коротким швах зварювання пластинами зручніше зварювання дротами з коливаннями, оскільки апаратура неї простіше й надёжнее. З іншого боку, під час зварювання пластинами не потрібно вільного місця перед стиком. Важлива перевага цього способу є зокрема можливість використання як електродів таких матеріалів, як чавун, з яких не можна чи важко виготовити проволоку.
Зварювання плавящимся мундштуком може застосовуватися для металу будь-який товщини при довжині шва до 3 м, а разі потреби — і більше. Вона, як і зварювання пластиною, не вимагає вільного місця збоку стику та, крім того, допускає обмеження місця над стиком. Характерною ознакою її є можливість зварювання швів складного криволинейного профілю. Апаратура для зварювання плавящимся мундштуком складається з одного подає механізму переносного типу, установлюваного, зазвичай, безпосередньо на виріб. Це її зручною для зварювання дрібних швів, котрим інші способи невыгодны.
2.2.Особенности електрошлакового процесса.
Электрошлаковая зварювання з примусовим формуванням відрізняється від дугового зварювання як ручний, і автоматичної, поруч особливостей, які треба враховувати і використовувати при застосуванні цього способа.
Під час проходження електричного струму через шлак немає такого інтенсивного виділення газів, супроводжуваного розбризкуванням шлаку, як при дугового зварюванні. При що встановилася электрошлаковом процесі разбрызгивания шлаку немає зовсім. Це дозволяє вести зварювання з відкритої поверхнею шлаковой ванни. Подача шлаку в ванну обмежується дуже малим кількістю, рівним кількості отлагающейся лежить на поверхні шва шлаковой палітурки завтовшки 1−1,5 мм. Це з вазі не перевищує 0,2−0,3 кг на погонний метр шва, незалежно від товщини металла.
Завдяки малій кількості расплавляемого флюсу що електрична енергія добре використовується для плавлення електрода і основного металла.
У результаті інтенсивного перемішування шлаку плавлення крайок відбувається більшому відстані від електрода чому це можливо, за дугового сварке.
Практичними наслідками цих особливостей є: малий витрата шлаку, що становить загалом, з урахуванням втрат на розсипання, 5% ваги наплавленного металу, тобто. удвадцятеро менший, аніж за дугового зварюванні під флюсом, малий витрата електричної енергії на 1 кг наплавленного металу, в 1,5−2 менший, аніж за дугового зварюванні під флюсом й у 4 менший, під час зварювання відкритої дугою. Ще важливішим практичним результатом цих особливостей є можливість здійснення однопрохідний зварювання металу завтовшки до 150−200 мм однією електрод, а при більшій кількості електродів — практично необмеженої товщини. Саме ця властивість відкриває найширші перспективи застосування электрошлаковой зварювання в промисловості, насамперед в тяжкому машиностроении.
Серед інших особливостей электрошлаковой зварювання найбільше значення мають следующие.
У результаті порівняно малого витрати флюсу і, отже, незначного поповнення шлаковой ванни новими порціями флюсу, забезпечується більш постійний, аніж за дугового зварюванні, хімічний склад металу шва.
Завдяки вертикальному становищу осі шва значно полегшується спливання газових міхурів і частинок шлаку і видалення їх із металу. Поліпшується заповнення металом междендритных порожнин. Якщо газовий пузырёк чи неметаллическое включення затримається за українсько-словацьким кордоном метал — шлак, всі вони переміщуватимуть разом із цією кордоном, тоді як із зварюванні в нижньому становищі вони було б захоплено кристаллизующимися металом. Тому схильність до утворення пір та інших неплотностей при электрошлаковой зварюванні в багато разів нижче, аніж за дугового зварюванні в нижньому становищі; менше чутливість до вологості шлаку, іржі і забруднення кромок.
У результаті сприятливого напрями зростання кристалів в швах, виконаних электрошлаковым способом в вертикальному становищі, відсутня так звану зону слабини, що спостерігається в швах великого перерізу, зварених в нижньому становищі. Це ж обставина істотно знижує схильність швів до утворення кристаллизационных тріщин. Температурні умови для околошовной зони також сприятливі, що і великий погонной енергією по порівнянню з окремим шаром багатошарової зварювання, і попереднім, створюваним шлаковой ванній. Нагрівання крайок починається лише на рівні поверхні шлаковой ванни, а плавиться вони починають в безпосередній близькості до металевої ванни. Між початком підігріву крайок основного металу та його плавленням проходить 2−3 і хвилин, унаслідок чого знижується як швидкість нагріву, і швидкість наступного охлаждения.
Электрошлаковая зварювання завжди виробляється у один прохід, тому лінійна швидкість зварювання товстого металу значно нижчі від, аніж за дугового багатошарової зварюванні. Завдяки цьому швидкості нагріву і наступного охолодження околошовной зони дуже малі, а схильність до утворення околошовных тріщин під час зварювання закаливающихся сталей порівняно невелика.
Оскільки электрошлаковая зварювання виробляється у один прохід, повністю ліквідується найбільш поширений дефект багатошарової зварювання — шлакові макроскопічні включення. Вони можуть з’являтися лише при грубе порушення технології сварки.
Зварювання металу будь-який товщини виробляється без розбирання крайок. Крайки, підлягають зварюванні, немає фасок: вони хочуть з зазором, що створює свого роду розбирання крайок. Це кілька разів зменшує трудоёмкость і вартість підготовки крайок під сварку.
Завдяки симетричності розбирання й положення у ній електродів при электрошлаковой зварюванні, зазвичай, відсутні кутові деформації. Вони можуть бути лише за зварюванні деяких спеціальних типів зварних соединений.
При товщині свариваемого металу менше 40−50 мм трудоёмкость і вартість зварних сполук при электрошлаковой зварюванні більше, аніж за дугового зварюванні під флюсом. Проте якщо з зростанням товщини продуктивність і економічність электрошлаковой зварювання швидко й зростають при толщинах понад 100 мм бувають в багато разів вище, аніж за дугового сварке.
3. Область применения.
Найважливішою проблемою сучасного машинобудування є ощадливе використання металів, зниження металлоёмкости конструкцій, підвищення його надёжности і довговічності. Відомо, що у зварних машинобудівних конструкціях видатки матеріали перевищують 50%. Тому найбільший народногосподарський ефект від участі впровадження заходів, сприяють економії металу, реалізується у в таких галузях машинобудування, які виробляють крупногабаритное толстостенное устаткування, як газо-нефтехимическая і энергетическая.
Першим призначенням електрошлакового процесу була зварювання вертикальних монтажних швів виробів, шви які неможливо експортувати зручне для дугового зварювання нижнє положение.
Однак, висока ефективність електрошлакового процесу вивела його з межі монтажній зварювання, зробивши її основним способом зварювання металу великий товщини, та був і поза межі власне зварювального виробництва. Зараз электрошлаковый процес застосовується як під час зварювання і наплавленні, а й також отримання виливків і зливків спеціального призначення й у ущільнення звичайних зливків і отливок.
Электрошлаковая зварювання застосовується у виробництві барабанів парових котлів та інших судин високого тиску, де вже цілком витиснула яку використовували раніше багатошарову автоматичну зварювання, під час виготовлення станин великих механічних пресів, траверс, архитравов і циліндрів гідравлічних пресів, валів великих гідротурбін і гідрогенераторів, станин прокатних станів, суднових корпусів, ахтерштевней, форштевней і інших суднових деталей, корпусів великих электромашин, паровозних і тепловозних рам, стійкий мартенівських печей, колінчастих валів, великих фланців і багатьох інших деталей. Широке поширення отримала электрошлаковая зварювання стиків арматури. Попри порівняно невеличке перетин зварних сполук, цей спосіб виявився ефективніше других.
Нерідко застосування зварних конструкцій дозволяє заощадити дуже багато металу. Так для зварних валів Варваринской ГЕС вагу зливків становив 59 т вместо100 т для цельнокованых; зварена кобура механічного ковочно-штамповочного преса тиском 4000 т важить на 24 т менше, ніж литом варіанті. З застосуванням зварювання під час виготовлення стійкий мартенівських печей на Дніпропетровському заводі металоконструкцій отримана велика економія товстого прокату рахунок ліквідації отходов.
Значення электрошлаковой зварювання не вичерпується її економічним ефектом. Широке її застосування докорінно змінює характер розвитку важкого машиностроения.
Чинниками, обмежують розміри елементів, може бути: потужність ковальсько-пресового устаткування, розміри нагрівальних і термічних печей, розміри металообробних верстатів. Окремо слід подивитися на обмеження, внесені труднощами перевезення негабаритних вантажів цього разу місце їх монтажа.
Зростання ж розмірів та ваги елементів може відбуватися лише з урахуванням пропорційного зростання перелічених вище виробничих потужностей. Проте якщо з застосуванням электрошлаковой зварювання така пропорційність може зберігатися ні в всіх случаях.
Передусім зайвими зростання потужностей, що з зростанням развеса зливка, оскільки электрошлаковая зварювання дозволяє зварювати між собою виливки в блоки розмірів і майже будь-який форми. Электрошлаковая зварювання, здебільшого, дає можливість з'єднувати поковки те щоб у разі потреби обійтися порівняно легкими прессами.
Нині электрошлаковая зварювання дозволяє виготовити на заводах зі порівняно малопотужним станочным і ковальсько-пресовим устаткуванням заготівлі розмірів. Подальше зростання розмірів окремих деталей обмежений можливістю транспортировки.
Великі можливості відкриваються до застосування електрошлакового процесу при наплавочных роботах. Электрошлаковая наплавлення може успішно виконуватися електродами великого перерізу, наприклад під час виготовлення біметалевих виробів, при облицюванні робочих поверхонь товстостінних судин тощо. Найчастіше наплавляемые поверхні мають вертикально чи похило: у разі электрошлаковый процес ведеться як і при сварке.
Электрошлаковым способом успішно зварюються стали різних класів і марок. Поруч із малоі среднеуглеродистыми сталями вдається зварювати ферритные нержавіючі стали, хромоникелевые аустенитные стали, жароміцні сплави на нікелевій основі, зварюють титан та її сплави. Крім прямолінійних і кільцевих швів великий довжини, можна зварювати короткі шви товстого металла.
При зварюванні вертикальних монтажних швів электрошлаковая зварювання може виявитися вигідніше ручний зварювання вже за часів товщині металу 16−20 мм.
Доцільність застосування зазначеного виду зварювання великою мірою залежить від кількості швів, які підлягають зварюванні. Що він більше, тим нижче межа товщини, від якого вигідно застосовувати электрошлаковую сварку.
Заключение
.
Электрошлаковая зварювання застосовується для зварювання великих толщин, різних сплавів, і типів швів. Є економічним і якісним способом зварювання, порівняно з зварюванням відкритої дугою. Цей процес знайшов широке використання у тяжкому машинобудуванні й ряді інших галузей промышленности.
1. Хакимов О. Н. Электрошлаковая зварювання з регулюванням термічних циклів. — М.: Машинобудування, 1984.
2. Электрошлаковая зварювання. — М.: Державне науково — технічне видавництво машинобудівної літератури, 1959. Під редакцією Патона Б.Е.
3. Сизов В. С. Электрошлаковая зварювання сталей великих толщин. — Л.: ЛДНТП, 1972. ———————————;
Электрошлаковый процесс.
Вільне формирование.
Примусове формирование.
Проволока.
Електрод великого сечения.
Зварювання проволокой.
Зварювання плавящимся мундштуком.
Зварювання элек-тродом боль-шого сечения.
Стыковая элек-трошлаковая сварка.
Без коле-баний.
З коле-баниями.
Пластина.
Стрижневі, кільцеві, фасонные.
Сверху.
Сбоку.
Заварка дефектов.
Уплот-нение.
Наплав-ка.
Довгі прямі швы.
Зварювання компактних деталей.
Короткі прямі шви (>500.
Короткі прямі шви (.