Виготовлення виробів з функціональної нанокераміки методом сухого ультразвукового та колекторного компактування
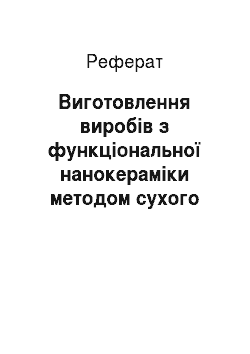
Різноманіття сфер застосування ультразвуку, при яких використовують різні його особливості, можна умовно розбити на три напрями. Перший пов’язано з отриманням інформації за допомогою ультразвукових хвиль, другий — з активним впливом на речовину і третій — з обробкою і передачею сигналів. При кожному конкретному застосуванні використовуються коливання певного частотного діапазону. У разі… Читати ще >
Виготовлення виробів з функціональної нанокераміки методом сухого ультразвукового та колекторного компактування (реферат, курсова, диплом, контрольна)
Різноманіття сфер застосування ультразвуку, при яких використовують різні його особливості, можна умовно розбити на три напрями. Перший пов’язано з отриманням інформації за допомогою ультразвукових хвиль, другий — з активним впливом на речовину і третій — з обробкою і передачею сигналів. При кожному конкретному застосуванні використовуються коливання певного частотного діапазону. У разі застосування ультразвукових коливань в практиці виробництва виробів з порошкових матеріалів можуть використовуватися всі перераховані напрями. Важливим питанням є вивчення впливу ультразвукового впливу на речовину в твердому стані. Головною причиною, що впливає на нерівномірний розподіл щільності за обсягом порошкового вироба, пресуючого в закритій жорсткої прес-формі, є процеси тертя. При компактуванні нанопорошків, що мають велику питому поверхню, ефекти тертя проявляються в значно більшому ступені, ніж для крупнодисперсних порошків. Рівномірність розподілу щільності уздовж осі пресування визначається в основному процесами пристінного тертя, а здатність порошку переміщатися в ортогональній осі пресування напрямку визначається коефіцієнтом гідростатичності ?, який, у свою чергу, залежить від пластичності часток порошку і процесів міжчастичного тертя. Домогтися задовільною рівномірностю розподілу щільності за обсягом утворюючого порошкового тіла можна, якщо виключити вплив процесів пристінного тертя.
Зазвичай це завдання вирішується шляхом пресування з пластифікаторами і зв’язками або в умовах пластичної течії при підвищених температурах, але в цих випадках необхідні стадії видалення домішкових компонентів у процесі спікання і використання додаткового обладнання та дорогих нетривких прес-форм для гарячого пресування. Для вирішення проблеми розробляються два методи компактування сухих політа нанодисперсних порошків, що дозволяють пресувати компакти складної форми з рівномірним розподілом щільності за обсягом: метод пресування під потужним УЗ-впливом (УЗВ — powerful ultrasound action, PUA) і метод «колекторного пресування» .
Знизити ступінь негативного впливу пристінного тертя без використання домішкових пластифікаторів можливо механічними УЗ-коливаннями формотворчих поверхонь прес-форми достатньої інтенсивності, коли в парі тертя «стінка-пресовка» виникатиме періодичний відрив поверхонь, і сили тертя будуть діяти тільки в моменти їхнього зіткнення.
Коефіцієнт пристінного тертя, таким чином, буде знижений пропорційно відношенню періодів часу відриву і контактування. За рахунок такого впливу можливо також зменшити сили тертя між НЧ, що важливо для підвищення щільності їх упаковки. Крім того, потужне УЗВ є способом деагломераціі і механоактивації наночастинок в процесі компактування безпосередньо перед спіканням.
Запропоновано і обґрунтовано метод сухого пресування керамічних НП під ультразвуковим впливом в квазірезонансних умовах. Метод полягає в тому, що коливальне зміщення частинок або агломератів нанопорошку під дією ультразвуку, здійснюваному в деякому діапазоні тисків пресування, близько до середніх розмірів цих частинок (агломератів). Для цієї мети підбирають відповідну амплітуду УЗ-коливань, що підводяться до прес-форми. Тим самим використовується розмірний фактор нанопорошків, коли навіть на досить великій глибині пресування коливальні зміщення наночастинок порошку від дії затухаючого ультразвуку будуть сумірні з їх малим розміром.
Оптимальне квазірезонансне УЗВ всього обсягу пресування НП в ідеальному випадку припускає моно-дисперсність порошку і відсутність загасання коливань в порошковому середовищі. Реально порошок завжди полідисперсний, а амплітуда коливань, що передаються від стінки прес-форми в порошкове тіло, загасає в міру віддалення від стінок. Проте практично при будь-якій амплітуді УЗ-коливань знайдеться така область порошкового тіла, в якій діапазон розмірів частинок буде відповідати їх коливальному зміщенню. Оскільки в процесі пресування щільність порошкового тіла постійно змінюється, то змінюються і умови проходження УЗ-хвилі через пресування. Таким чином, ефективному квазірезонансному впливу на різних стадіях пресування будуть послідовно піддаватися всі області порошкового тіла.
Для ультразвукового впливу на керамічні порошкові матеріали і їх компактування з накладенням УЗ-коливань використовується як стандартне обладнання (ультразвуковий генератор, перетворювачі, гідравлічний прес), так і спеціально розроблена для цих цілей ультразвукові і пресові оснащення, що передає зусилля пресування і УЗ-коливання в зону компактування порошку.
Для перетворення електричних коливань в механічні використовують ультразвукові перетворювачі двох типів. П'єзоелектричні перетворювачі характеризуються високою добротністю, але їх застосування обмежене по потужності (до 1 кВт) і необхідністю використання при великих потужностях примусового повітряного охолодження. Використання перетворювачів магнітострикційного типу з водяним охолодженням практично не обмежена по потужності. Для передачі УЗ-коливань об'єкту впливу і узгодженого навантаження служать акустичні хвилеводи і узгоджуючі пристрої, основні методи розрахунку і конструювання яких викладені в Магнітострикційні перетворювачі не дозволяють отримувати на робочому кінці коливання високої інтенсивності (амплітуди коливального зсуву). Для підвищення величини амплітуди впливу використовують УЗ-концентратори (трансформатори швидкості), що представляють собою акустичні хвилеводи стрижневого типу змінного перерізу або змінної щільності, що приєднуються до перетворювача більш широким кінцем або частиною з більшою щільністю матеріалу. Принцип дії стрижневого концентратора заснований на збільшенні амплітуди коливального зміщення в стержні внаслідок зменшення його поперечного перерізу або щільності відповідно до закону збереження кількості руху. У кожному конкретному випадку доводиться вирішувати завдання акустичного узгодження УЗ-устаткування і оснащення, що містить об'єкт впливу в залежності від його габаритів, форми і стану. Загальні рекомендації щодо виконання акустичного узгодження висвітлені в роботі.
Для ущільнення порошкового матеріалу в закритих прес-формах, залежно від схеми і швидкості докладання навантаження використовують преси різного типу: універсальні і спеціалізовано гідравлічні, механічні та пресове обладнання спеціального призначення (гідроі газостати). Пресування здійснюють у прес-формах, матеріал і розміри яких визначаються рівнем тиску пресування схемою додатка навантаження, типом і станом порошкового матеріалу. Реалізація методу УЗ-пресування доступна для різних варіантів поєднання серійного ультразвукового та пресового устаткування. Так в описаних нижче експериментах по УЗ-компактування в якості джерела електричних коливань використовувався ультразвуковий генератор УЗГ-6.3 з частотним діапазоном 16−24 кГц і максимальної вихідної електричною потужністю 6,3 кВт, що працює на завантаження індуктивного типу. Для перетворення електричних коливань в механічні застосовували магнітострикційні перетворювачі типу ПМС-15 з номінальним значенням електричної потужності 3 кВт. Частота УЗВ визначалася резонансною частотою всій коливальної системи (перетворювачі - хвилеводи — прес-форма з порошковим тілом) і залишалася незмінною протягом однієї серії експериментів. Пресування порошкових матеріалів проводили на універсальному гідравлічному пресі WK-18 з максимальним зусиллям 100 тонн. У загальному випадку лабораторна установки для здійснення холодного статичного пресування порошкових матеріалів з накладенням УЗ-коливань (рис. 1.) складається з гідравлічного преса 1, ультразвукової прес-форми — хвилеводу 2 і магнітострикційних перетворювачів 3. Залежно від типу впливу обробка порошкового матеріалу здійснювалася з використанням спеціалізованої оснастки різного типу.
Підведення ультразвукових коливань можна здійснити двома способами. В одному з них напрямок коливального зміщення збігається з віссю пресування, в іншому — ультразвукові коливання спрямовані перпендикулярно осі пресування. У всіх випадках передача основної частини енергії УЗ-коливань порошковому тілу здійснюється через кордон розділу «стінка матриці прес-форми — бокова поверхня прессовки». Акустична розв’язка коливальної системи і деталей преса досягається застосуванням звукоізолюючих прокладок і відповідним дизайном УЗ-оснащення.
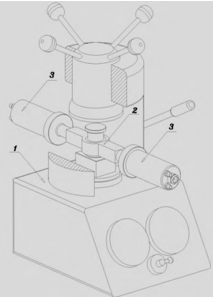
Рис. 1. Схема лабораторної установки для компактування порошкових матеріалів з накладенням ультразвукових коливань Для експериментів по здійсненню УЗВ на пресований матеріал були розроблені і виготовлені різні конструкції ультразвукових прес-форм, деякі варіанти виконання яких наведено на рис. 2.7−2.10.
Для пресування виробів середніх габаритів циліндричної форми була розроблена і виготовлена УЗ-прес-форма з можливістю приєднання двох магнітострикційних перетворювачів (рис. 2.). Матриця-хвилевід (1, 2) здійснює передачу УЗ-коливань від магнітострикційних перетворювачів до пресування. Хвилевід резонансної довжини 1 виконаний з м’якої сталі з низьким значенням акустичного опору. Для забезпечення гарного акустичного контакту матриця 2 із загартованої інструментальної сталі сполучається з хвилеводом 1 напруженої посадкою. У прес-формі здійснюється одностороннє пресування порошкового матеріалу з радіальним підбиттям коливань в зону пресування від двох синфазно працюючих перетворювачів.
Для ультразвукового пресування малогабаритних виробів циліндричної форми була розроблена і виготовлена ультразвукова прес-форма з стрижневим експоненціальним концентратором 1 (рис. 3.).
Матриця 2 сполучена з концентратором по гарячій посадці. У прес-формі здійснювалося одновісне двостороннє пресування порошку з радіальним підбиттям ультразвукових коливань від одного перетворювача. Для досліджень впливу ультразвукових коливань, напрямок коливального зміщення якого збігається з напрямком пресування, була розроблена ультразвукова прес-форма з двухстержневою системою хвилеводів (рис. 4.). У цій системі здійснюється перетворення радіально підведених коливань від двох перетворювачів в коливання, коливальний зміщення яких паралельно осі пресування. Зона ущільнення порошку розташована в місцях максимальної амплітуди коливального зсуву на кінці другого стрижня — хвилеводу. Для УЗВ на порошкове тіло в стані насипної щільності може бути використана трьохстержнева коливальна система з двома закриваючими порожнинами П для завантаження порошку (рис. 5.). Для оцінки рівня УЗВ використовують параметр амплітуди коливального зсуву. Як датчики амплітуди ультразвукових коливань використовують п'єзоперетворювачі та індуктивні голівки. Однак застосування перших обмежено їх поганий стійкістю до потужним коливанням, а використання другого неефективно в силу їх високої температурної чутливості.
Способи безконтактного вимірювання амплітуди (оптичні, лазерні досить дорогі і придатні тільки для контролю поверхонь з відкритим доступом. Однак для пошуку і оптимізації режимів УЗВ технологічного процесу цілком достатньо контролювати і оцінювати їх за значенням вихідної електричної потужності ультразвукового генератора або навіть за рівнем електричної напруги, що подається до перетворювача.
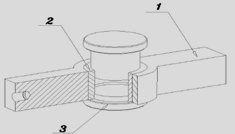
Рис. 2. Прес-форма для ультразвукового компактування виробів циліндричної форми з великим відношенням радіального до осьового розмірів.
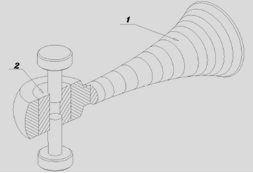
Рис. 3. Ультразвукова прес-форма з радіальним підбиттям коливань через стрижневий експонентний концентратор.
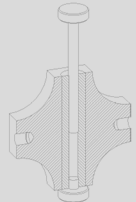
Рис. 4. Ультразвукова прес-форма для дослідження впливу коливань, спрямованих паралельно осі пресування.
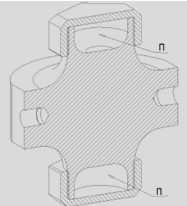
Рис. 5. УЗоснащення для активації і диспергування сухих порошків в порожнині акустичного стрижня Загальні операції при проведенні експериментів з ультразвукового компактування і обробці порошків полягають у наступному. 80 В експериментах по УЗ-компактуванню фіксована навіска досліджуваного порошку 4 завантажується в порожнину матриці 1 ультразвукової прес-форми. Для збереження вихідної чистоти порошків пластифікатори і мастила не застосовуються. Здійснюється плавна передача зусилля пресування P порошковому тілу 4 з одночасною передачею в зону пресування УЗ коливань від магнітострикційного перетворювача 6 через концентратор 5. Поточний тиск оцінюється за шкалою манометра преса з певною точністю і кроком реєстрації. Величина тиску в поршні преса перераховується в значення тиску пресування. По закінченні пресування проводиться плавне зниження тиску, розбирання прес-форми й витяг отриманого компакта.
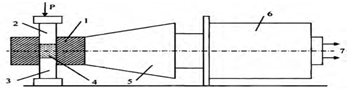
Рис. 6. Установка для сухого пресування порошків під УЗ-впливом: 1 — матриця з пуансонами (2,3), 4 — порошок, 5 -УЗ-концентратор, 6 — магнітострикційний перетворювач з резонансною частотою 21 кГц, з'єднаний з 7 — УЗ генератором УЗВ здійснюється протягом усього процесу ущільнення. Рівень УЗВ контролюється вимірюванням електричної потужності W, підводиться до УЗ-перетворювача. Контрольні зразки пресування (W = 0 кВт) виготовляються в тих же умовах і оснащенні. Для визначення оптимальних режимів УЗ-компактування на наступних стадіях експериментів досліджуються експлуатаційні характеристики виробів. Стандартними методами визначаються щільність виробу і розподіл пор за розмірами, зернистість, міцнісні характеристики, мікротвердість і тріщиностійкість, кристалічна структура і фазовий склад. Ультразвуковий вплив на пресовані сухі порошки ефективно знижує сили внутрішнього (міжчастичного) тертя і при оптимальній амплітуді УЗ-хвилі сприяють рівномірному ущільненню наноі полідисперсних порошків у відсутності будь-яких пластифікаторів Крім того, встановлено, що УЗ-вплив на стадії компактування метастабільних нанопорошків впливає на кристалічну структуру і фазовий склад спеченої кераміки. Тому метод сухого компактування нанопорошків під УЗ-впливом перспективних для виготовлення оптично прозорих керамік оскільки дозволяє виключити застосування домішкових пластифікаторів та зв’язок (властивих шлікерного литтю) при забезпеченні рівномірної щільності в компакті, а також дозволяє впливати на кристалічну структуру спечених керамік, щоб сприяти формуванню матеріалу з кубічної структури.
Так при отриманні оптично прозорих керамік Nd3 + Y2O3 найбільш прозорими були зразки, отримані при таких оптимальних технологічних режимах:
- * тиск пресування — 240 МПа;
- * потужність УЗВ — 3 кВт;
- * температура нагріву — 2000 ° С;
- * час витримки — 30 годин.
Товщина зразків після спікання склала 2,6 мм, діаметр — 10 мм. При таких технологічних параметрах у зазначених зразках оптично прозорих керамік пропускання становило 60%.
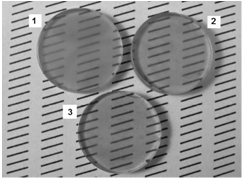
Рис. 7. Зразки оптично прозорих керамік Nd-Y2O3: 1) — звичайне пресування; 2), 3) — сухе ультразвукове пресування Метод УЗ-пресування порошків не виключає одне тимчасового застосування інших способів корисного впливу на процес компактування. Про ефективне використання УЗ-впливу в процесах шликерного лиття було сказано раніше. Також ефективний спосіб пресування порошкових матеріалів, який дозволяє перерозподіляти сили пристінного тертя таким чином, що перепади щільності в порошковому тілі уздовж осі пресування залишаються мінімальними (коллекторне пресування), запропонований і реалізований спільно з УЗ пресуванням авторами. На малюнку 8. представлені фотографії та моделі керамічних виробів, технологія виробництва яких з використанням ультразвукового та колекторного пресування були розроблені в НОІЦ «Наноматеріали і нанотехнології» ТПУ.
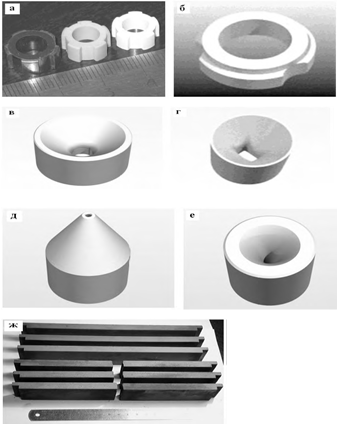
Рис. 8. Зразки керамічних виробів, технологія виробництва яких з використанням методів ультразвукового та колекторного пресування розроблена в ТПУ: а — турбинки бензонасоса (Y-TZP-нанокераміка); б — торцеві ущільнення для гідронасосів (Y-TZP-нанокераміка); в — фильера для волочіння проводів (Y-TZPнанокераміка); г — калібр для ізолювання обмотувальних проводів (Y-TZP-нанокераміка); д — дорн для телефонних проводів (Y-TZPнанокераміка); е — матриця для накладення гумової ізоляції на кабель (Y-TZP — нанокераміка); ж — мішень з ZrB2 — кераміки для магнетронного розпилення.