Основи логістики
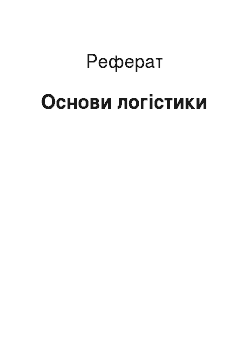
Як можна класифікувати склади промислового підприємства? ———————————- Англо-російський економічний словник/ під ред. А. В. Аникина.-М.: Російський мову, 1977, с. 365. В. К. Мюллер Англо-російський словарь.-М.: Російську мову, с. 441. William J. Stevenson Production/Operations Management.-4-th ed., IRWIN, INC., 1993, p.725. Логістика: Учеб. пособие / під ред. Б. А. Аникина.-М.:ИНФРА-М, 1997, с. 7… Читати ще >
Основи логістики (реферат, курсова, диплом, контрольна)
смотреть на реферати схожі на «Основи логістики «.
7. Основи логистики.
7.1. Поняття логистики.
У фундаменті економічної літературі зустрічаються різні визначення логістики. Наведемо деякі з них.
Логістика (Logistics) это:
1. Планування й забезпечення матеріально-технічного постачання, підготовки й пересування людського состава.
2. Організація служби тыла.
3. Матеріально-технічне забезпечення магазина[1].
4. Тил і постачання, матеріально-технічне постачання, робота тыла[2].
5. Рух матеріалів і запасов[3].
6. Наука про плануванні, організації, управлінні, постійному контролі й регулюванні руху потребує матеріальних та інформаційних потоків у просторі та у часі від своїх первинного джерела до кінцевого потребителя. 4].
Логістику також визначають як наукова дисципліна, що з пошуком нових можливостей підвищення ефективності матеріальних потоков.
Нині можна справити й ширший підхід до логістиці, який, крім вищезгаданого включає аналіз ринку постачальників і споживачів, координацію попиту й пропозиції над ринком товарів та послуг, а також гармонізацію інтересів учасників процесу руху товарів. У цьому вся разі багато функції маркетингу переходять до логистике. 5].
У ланцюзі через яку проходять матеріальний і інформаційний потоки від постачальника до споживача вирізняються такі ланки: постачання матеріалів, сировини, напівфабрикатів, зберігання продукції і на сировини, виробництво товарів, їх розподіл, споживання готової продукции.
У фундаменті економічної літературі логистическую систему ділять на макроі микрологистику. Макрологистика досліджує проблеми, пов’язані з аналізом ринку постачальників і споживачів, виробленням загальної концепції розподілу, розміщенням розподільних центрів, вибором найефективнішого виду транспорту, й т.д. Микрологистика розв’язує проблеми у межах окремих ланок логістики (наприклад, внутрипроизводственная логістика). Микрологистика забезпечує операції з планування, підготовці, реалізації і контролю за процесами переміщення товарів всередині промислових предприятий[6].
Поняття логістики спочатку з’явилося у військовій сфері, де охоплювало проблеми транспорту, постачання, переміщення військових підрозділів. Потім поняття та художні засоби логістики було перенесено у Громадянську сферу, де використовувались у управлінні матеріальними потоками у сфері обігу євро і виробництва. У цьому поняття і нові методи логістики стали застосовуватися у економіці порівняно недавно. Так на початок 1960;х років питанням оптимізації матеріальних потоків великої уваги не уделялось.
Перший етап (60-ті роки) характеризується інтеграцією складського господарства з транспортом, які починають функціонувати з єдиного графіку і з узгодженої технології. У цьому критерієм ефективності став бути мінімум загальних витрат за матеріальне розподіл, а чи не оцінка ефективності окремо складського господарства і транспорта.
Другий етап (80-ті роки) характеризується інтеграцією складського господарства і транспорту починаючи з виробництвом. Це дозволило б оперативно реагувати зміни довкілля, поліпшити використання устаткування і скоротити терміни виконання замовлень. Критерієм оптимальності стала мінімізація загальних витрат всіх вищезгаданих підрозділів. У цьому очевидно, що мінімізація загальних витрат можна досягти зниженням ефективності роботи окремих ланок підприємства. Спроби мінімізувати витрати будь-якого окремого виду можуть призвести до підвищенню всіх витрат з організацією матеріального потоку. Наприклад, зниження запасів може знизити витрати, пов’язані зі збереженням, але збільшити витрати, пов’язані з роботою транспорта.
Третій етап (час) характеризується інтеграцією всіх учасників логістичного процесса[7].
У країнах із ринковою економікою логістика охоплювала передусім товарні потоки у сфері звернення. У нашій країні вирішувалися завдання оптимізації передусім потоків продукції виробничо-технічного назначения.
Отже, метою дисципліни «Логістика» є формування в фахівців теоретичних і практичних навичок під управлінням матеріальним потоком.
У логістиці використовуються економічні, економіко-математичні і статистичні методи на вирішення різних теоретичних і практичних задач.
Важливе завдання на логістики є створення інтегрованої системи регулювання і функцію контролю матеріальних й інформаційних потоков.
Під матеріальним потоком слід розуміти сировину, напівфабрикати, готові вироби, аналізовані у процесі додатку до ним різних логістичних операцій (розвантаження, укладка на піддони, переміщення, розпакування тощо.) і віднесені до якогось інтервалу времени.
Розмірність матеріального потоку визначається дробом, в чисельнику якої зазначена одиниця виміру вантажу (штуки, кілограми, тонни тощо.), а знаменникуодиниця виміру часу (добу, місяць, квартал і т.д.).
Наприклад, 1000 тонн/год.
Під інформаційним потоком розуміють сукупність які у логістичній системі, і навіть між цієї системою та довкіллям повідомлень, супроводжуючих матеріальний поток.
Інформація, належить матеріальним потокам можна розділити у часу втричі виду: випереджальна (попередня), що надходить разом з матеріальним потоком (наприклад, про кількісних і якісних його параметрах), яка надходить за матеріальним потоком (наприклад, різні підтвердження, претензії і т.п.).
Побудова інформаційної системи логістики має бути індивідуальним залежно кількості завдань і структури организации.
У цьому під інформаційної системою розуміють систему збору, зберігання, накопичення, пошуку істини та передачі, що застосовуються у процесі управління. Рекомендується всю логистическую систему розглядати, як сукупність функціонально обмежених підсистем, функціонування яких забезпечується інформацією рівні її ж таки інформаційних подсистем.
Логістика виробничих процессов.
У дослідженнях з логістики можна назвати два направления:
1. Підприємство сприймається як самостійна філософська одиниця й основна увагу приділяється операціям, що з входом і виходом матеріального потока.
2. Увага приділяється деталей проходження продукту всередині предприятия.
Організація матеріальних потоків всередині підприємства повинна залежати від проблеми реалізації продукції. У разі дефіциту, коли є повна впевненість, продукція буде реалізовано, багато уваги слід приділяти питанням високої завантаження устаткування (підвищення коефіцієнта змінності, коефіцієнтів використання устаткування за часом, потужності, обсягу роботи), збільшення виробничих серій, скорочення номенклатури своєї продукції, збільшення запасів. У умовах здійснюється випускати продукцію складу відповідно до розробленим для підприємства планом.
А в умовах коли першому плані виходить проблема реалізації і непередбачуваності попиту виробництво складу замінюється значною ступеня виробництвом на замовлення. Стає невигідним зміст великих запасів й те водночас не можна упускати можливість виконання виникаючих заказов[8]. Тому важливе значення має швидка адаптація системи (підприємства) до змін довкілля, що забезпечується можливістю її підсистем (закупівля, склади, запаси й ін.) швидко змінювати склад вихідного потока.
Управління матеріальними потоками у межах внутрішньовиробничих логістичних систем здійснюється з двох основних подходов.
Перший підхід є систему з «виштовхуванням» (Push system) вироби (рис.1).
Він передбачає, що виготовлення виробів починається з одного боку виробничої лінії, проходить через послідовний ряд технологічних операцій та закінчується обробкою іншому кінці виробничої ланцюжка. Матеріальний потік «виштовхується» одержувачу за командою, котра надходить на передавальне ланка з центральної системи управління виробництвом. У цьому після завершення обробки однією ділянці виріб передається наступного року незалежно від цього, чи готовий цю ділянку прийняти на обробку чи ні. Кожен ділянку має виробничий план. Проте створити «жорсткий» технологічний процес, всіх параметрів якого було б наперед точно розраховані, неможливо. Тому на згадуваній підприємствах завжди може бути певний виробничий запас, що грає роль буфера збільшує гнучкість системи. Що Штовхає системи за назвою «системи MRP"[9]. Вышеназванные системи значною мірою притаманні традиційних методів організації виробництва. Можливість їх застосування для логістичній організації виробництва з’явилася зв’язку із використанням ЕОМ, що дозволило гнучкість цієї системы.
Мал.1 Система з виштовхуванням вироби, запущеного в производство.
Скороченню виробничих запасів за збільшення гнучкості виробництва сприяє система поточного провадження з «витягуванням» виробів (Pull system) (рис.2).
Рис. 2 Система з витягуванням вироби, запущеного в производство.
Цю систему призів будуть по виробів з минулого ділянки по мері необхідності. Центральна систему управління не втручається у обмін матеріальними потоками між різними ділянками підприємства, не встановлює їм поточних виробничих завдань. На промислових підприємствах план має сенс тільки лінія остаточного складання і звідси інформацію про необхідності виробляти необхідні деталі надходить на попередні ділянки у вигляді спеціальних карток. План у тих ділянках формується щодня, як і забезпечує гнучкість системы[10].
До логистическим системам з витягуванням відносять систему КАН-БАН[11].
У цьому системі виділяють два виду карток: картки відбору, картки виробничого заказа.
У картці відбору вказується кількість деталей, що має бути взято на попередньому ділянці обработки.
У картці виробничого замовлення зазначено кількість деталей, що має бути виготовлено на попередньому участке.
У місці складування деталі занурюються у автонавантажувач у кількості, зазначеній у картках відбору (рис. 3). У цьому з ящиків знімаються прикріплені до них картки замовлення, які інформують про замовленні на виготовлення нових деталей у суворо певному кількості. План на ділянках формується щодня. Це забезпечує гнучкість системи. Якеабо переміщення виробів без карток неприпустимо. Зазвичай система КАН-БАН узгоджується з системою контролю за якістю. Цю систему не вимагає тотальної комп’ютеризації виробництва, проте вона не передбачає високу дисципліну постачання і високу відповідальність персоналу, як і обмежує її запровадження у різних странах.
7.2. Логістика запасов.
Як зазначалося вище, логістика вивчає матеріальні потоки. Запаси можна як форму існування матеріального потока.
Теорія управління запасами розробляє методи обчислення величини запасів, які забезпечують найбільш ощадливим шляхом задоволення майбутнього (який завжди певного) спроса.
Аналіз моделей управління запасами зводиться до встановлення послідовності процедур постачання і поповнення запасів, коли він забезпечуються мінімальні сумарні витрати, пов’язані з заготовки, зберіганням продукту і збитками через незадоволеного спроса.
Надмірно великий запас пов’язані з змертвінням капіталів, вимагає значних витрат за збереження і те що його. З іншого боку, недостатній запас викликає перебої у роботі виробництва, порушує взаємодії з іншими підприємствами і погрожує різними економічними санкциями.
Доцільний рівень запасів залежить від значної частини умов, пов’язаних і з самим виробництвом, і з зовнішніми стосовно нього факторами.
До внутрішнім умовам ставляться, наприклад, інтенсивність використання запасів у залежність від характеру виконуваного замовлення, можливості збереження і видатки зміст запасів у протягом тієї чи іншої проміжку времени.
Зовнішні чинники, що впливають вибір рівня запасів, визначаються коливаннями попиту продукцію підприємства, можливостями постачальників, оперативністю виконання замовлень, витратами перевезення. Сильним стимулом до створення зайвих запасів служить їх дефіцит. У цьому відзначається, що у ресурсоограниченной економіці усіх нормальних запасів частка запасів напівфабрикатів і матеріалів щодо більше частки нормальних запасів готової продукції, а спросоограниченной економіці - наоборот[12].
Деякі з вище перерахованих чинників можна заздалегідь врахувати, інші випадкові, статистичні закономірності яких підлягають определению.
Визначення доцільного рівня запасу найчастіше зводиться у виборі раціональних моментів замовлення (коли?) і раціональних обсягів поповнень (скільки, скільки?). І тут розглядаються дві альтернативи: або замовлення виробляються вони часто й малими партіями, або рідко й у великій объеме.
Іноді додаткову кількість матеріалів замовляється після визначення потреби з урахуванням вже укладеного договору. Недоліком цього найпростішого методу і те, що період від часу оформлення замовлення до отримання матеріалів можна дуже значним. Тому такий метод оформлення замовлення бажаний для дорогих деталей (ділянку На кривою АВС)[13] і деталей з дуже що хитається потребностью.
Інший підхід оформлення грунтується на ритмічності отримання замовлень. У цьому випадку застосовуються системи з фіксованою розміром замовлення (perpetual inventory system — стала система) і з фіксованою інтервалом часу між замовленнями (periodic system — періодична система).
Система з фіксованою розміром замовлення контролює рівень запасу. Коли рівень запасу падає нижчих за встановлений (точка замовлення), видається замовлення заповнення запасів. У цьому системі важливого значення набуває визначення економічно розумного (оптимального) розміру заказа.
Оптимальний розмір замовлення критерієм мінімізації сукупних витрат за збереження і повторення замовлення вираховується за формулою Вільсона (Wilson formula):
[pic][pic], де EOQ (ECONOMIC ORDER QUANTITY) — економічно розумний розмір заказа,.
D — річна потреба у заказываемом продукті, штук,.
O — видатки поставку одиниці заказываемого продукту, руб.,.
H — річні зберігання одиниці заказываемого продукту, руб./шт.
Наприклад, фірма збуває рівномірно протягом року (N = 12 місяців) в цілому D = 2400 штук виробів. Недоліки зберігання становлять H = 1,50 руб./шт. в одиницю часу (протягом місяця), витрати замовлення становлять O = 150 руб./заказ, тоді оптимальний обсяг поповнення запасів (величина замовлення) равен:
[pic]штук.
Графічне уявлення сумарних витрат у період часу (Т) (річні витрати) залежно від розміру партій поставки (Q) характеризує наступний графік (рис. 1):
[pic].
МС = Сп + Со,.
де МС — сумарні річні издержки,.
Сп — витрати з зберігання запасу на складе,.
З — витрати з оформленню заказа,.
МС = (Q/2)*H + (D/Q)*O.
У витрати з зберігання запасу складі (Сп) входят:
1. Постійна складова витрат із зберігання, котра від обсягу закладеного запасу: видатки зміст приміщень, амортизація складського устаткування, страхування складського господарства, оплата певній його частині податків на майно, висвітлення та опалення, поточний ремонт, видатки управлінський персонал,.
2. Змінна складова витрат за зберігання, прямо пропорційна обсягу закладеного запасу: втрати від омертвляння коштів, вкладених у купівлю складських запасів, витрати з страхуванню запасів, втрати причини збережених запасів, прямі видатки виробничий персонал.
У витрати з оформленню замовлення (З) входят:
1. Постійна їх складова: витрати на організації замовлення, транспортні витрати, які пов’язані з обсягом партії поставки,.
2. Змінна складова на оформлення замовлення: транспортні витрати, залежать від величини партії поставки, витрати на погрузке-разгрузке.
Крива загальних річних витрат є дуже пологою поблизу точки мінімуму. Це говорить, що поблизу точки мінімуму розмір запасу може коливатися у деяких межах без істотного зміни загальних витрат (рис.1).
Система з фіксованою інтервалом часу між замовленнями передбачає розміщення замовлень на заповнення запасів із заданою періодичністю. Визначити інтервал часу між замовленнями з урахуванням оптимального розміру замовлення (EOQ). Для розрахунку інтервалу часу між замовленнями (час споживання замовлення) використовують формулу:
[pic], де N — кількість робочих днів (місяців) в году,.
D — потреба у заказываемом продукті, штук,.
EOQ — оптимальний розмір замовлення, штук.
За даними, наведених вище, визначимо час споживання запаса:
[pic] = 1 месяц.
Цей інтервал часу може бути скоригований з урахуванням експертних оцінок. У цьому системі момент замовлення не змінюється, тоді як розмір замовлення є змінюваного величиною. Розрахунок розміру замовлення (OQ) між замовленнями проводиться у разі формуле:
OQ= Максимальний бажаний замовлення — поточний замовлення + очікуване споживання під час поставки.
Наведені вище системи управління запасами розглядають одне із двох параметрів — розмір замовлення чи інтервал часу між замовленнями. Ці системи є ефективними для матеріалів з відносно невисокою вартістю умовах постійного споживання запасів. Набагато складніше визначати точку замовлення при неритмичном споживанні запасів. І тут слід вести стеження усіма відхиленнями, ніж перейти то кількість, що дозволяє продовжувати роботу до поповнення запасов.
За підсумками поєднання систем можна побудувати дуже багато їх різновидів, відповідальних різним требованиям.
Досить стала вельми поширеною практично має система з встановленої періодичністю поповнення запасів до встановленого рівня. Щоб уникнути завищення обсягів запасів чи його дефіцит, через постійні часові відтинки проводиться перевірка справжнього стану запасів, і коли після попередньої перевірки було реалізовано якесь кількість товарів, то подається замовлення. Розмір замовлення дорівнює різниці між максимальним рівнем, до якої відбувається поповнення запасів, і фактичним рівнем, у момент проверки[14].
Існує й систему управління запасами, звана системою «Минимум-максимум» (система з цими двома рівнями, чи Ss-система).
Вона зорієнтована на ситуацію, коли на облік запасів і витрати оформлення замовлення значні і порівнянні з утратами від нестачі запасів. Тож у аналізованої системі замовлення виробляються не через кожен поставлене інтервал часу, лише за умови, що запаси складі на той час виявилися рівними менше встановленого рівня. Що стосується видачі замовлення її розмір розраховується так, щоб постачання поповнила запаси до максимального бажаного рівня. Таким чином, дана система працює лише з цими двома рівнями запасів — мінімальним і максимальным[15].
Однією з найпростіших систем поповнення запасів є система «двох ящиків» (Two-bin system). І тут використовуються два контейнера для запасів. Коли одному з контейнерів запаси витрачені, відбувається їх пополнение.
У літературі наводяться рекомендації доцільність використання системам управління запасами залежно певних обстоятельств:
1. Якщо витрати управління запасами значні і можна обчислити, слід користуватися системою з фіксованою розміром заказа,.
2. Якщо витрати управління запасами незначні, то більш кращою виявляється система з їх постійним рівнем запасов,.
3. При замовленні товарів постачальник накладає обмеження на мінімальний розмір партії. І тут бажано використовувати систему з фіксованим розміром замовлення, оскільки легше одного разу скоригувати фіксований розмір партії, ніж безупинно регулювати його перемінний заказ,.
4. Проте, якщо накладаються обмеження, пов’язані з вантажністю транспортних засобів, то більш краще є система з постійним рівнем запасов,.
5. Система з їх постійним рівнем запасів більш краща у тому разі, коли постачання товарів відбувається у встановлені сроки,.
6. Система з їх постійним рівнем і системи з цими двома рівнями часто вибирається тоді, коли необхідно швидкого реагування зміну сбыта[16].
Різні види сировини й матеріалів і неоднакові умови для їхньої споживання та призначення у різних фірмах визначають необхідність використання різних методів розрахунку потреби у них.
Існують три методу розрахунку потреби у матеріалах: детермінований (певний), стохастический (імовірнісний, випадковий), эвристический.
Найпоширенішим і достовірним є детермінований метод чи метод прямого счета.
Потреба матеріалі визначається за такою формуле:[pic], де Hij — норма i-го матеріалу виробництва j-го вироби в натуральних одиницях измерения,.
Nj — програма виробництва j-ых виробів на плановому периоде.
На підприємствах, із многономенклатурным характером виробництва цей метод то, можливо громоздким.
Тому потреба у матеріалі визначають за групою однорідної продукції (так званим товарам-представителям).
Різновидом методу прямого рахунки є так званий розрахунок потреби за аналогією. Він може застосовуватися тоді, коли налаштувалася на нові різновиду виробів ще розроблено норми расхода.
У разі, якщо мине певний такого роду продукцію виготовляється ні з жодного виду матеріалу, та якщо з кількох можна розраховувати потреби у них з рецептурного складу. З використанням розрахунку по рецептурному складу спочатку визначається потреба у продукції відповідність до виробничої програмою. Ця потреба встановлюється множенням чорнової маси одного вироби виробничу програму виготовлення виробів на плановому періоді. Потім визначається загальна кількість матеріалів, що має бути відпущено у виробництві з урахуванням втрат надходжень у технологічному процесі. Потреба кожному окремому матеріалі визначається шляхом множення отриманої величини частку цього матеріалу у складі суміші виготовлення виробів по рецепту.
При визначенні потреби стохастическим методом враховуються дані минулого періоду й з урахуванням прогнозу встановлюється очікувана потребность.
Найпростішим способом є метод динамічних коефіцієнтів. Для визначення потреби у матеріалі цим методом необхідно даних про фактичному витратах їх у минулому періоді помножити на коефіцієнт зміни програми випуску виробів чи обсягу робіт у плановому періоді і коефіцієнт, враховує економію матеріальних ресурсів у зв’язки й з впровадженням відповідних організаційно-технічних мероприятий.
Важливим методом стохастичних прогнозів є метод експоненційного сглаживания[17]. Цей метод у тому, що кілька динаміки згладжується з допомогою ковзної середньої, у якій ваги підпорядковуються експонентному закону.
Цю середню називають експоненційною середній і позначають St.
вона є характеристикою останніх значень низки динаміки, яким присвоюється найбільший вес.
Экспоненциальная середня обчислюється по рекуррентной формуле:
St = L* Yt + (1- L) St-1, де St — значення експоненційною середньої в останній момент t,.
St-1 — значення експоненційною середньої в останній момент (t — 1),.
Yt — значення експоненційного процесу у момент t,.
L — вагу t-ого значення низки динаміки (чи параметр сглаживания).
Послідовне застосування формули дає можливість обчислити экспоненциальную середню через значення всіх рівнів даного низки динамики.
Найважливішою характеристикою у цій моделі є L, за величиною якому здійснюється прогноз. Чим значення цієї параметра ближчі один до 1, тим більше коштів за прогнозу враховується вплив останніх рівнів низки динамики.
Якщо L близько до Про, то ваги, якими зважуються рівні низки динаміки убувають повільно, тобто. за прогнозу враховуються всі минулі рівні ряда.
У штатівській спеціальній літературі відзначається, які зазвичай практично значення L у межах від 0,1 до 0,3. Значення 0,5 що ніколи не превышается.
Експоненціальне згладжування застосовно, передусім, при постійному обсязі споживання (L = 0,1 — 0,3). За більш високих значеннях (0,3 — 0,5) метод підходить за зміни структури споживання, наприклад, з урахуванням сезонних колебаний[18].
Достовірність обумовленою потреби з урахуванням розглянутих вище методів значно підвищується, якщо наводяться з методом експертних оцінок. Сутність його у цьому, що динаміку зміни потреби встановлюється чи уточнюється з урахуванням опитування спеціалістів у галузі снабжения.
Для цього він розробляються спеціальні анкети, у яких формулюються питання, що стосуються факторів, і загальної потреби у матеріалах. Узагальнення обліку думок фахівців можуть зробити істотне впливом геть точність прогнозів. Надійність експертні оцінки визначається першу чергу добором фахівців-експертів, їх інформованістю в досліджуваних проблемах, і навіть можливостями обробки отриманої информации.
Для узагальнення оцінок експертів може застосовуватися метод Дельфы[19]. Особливість методу полягає у послідовному анонімному опитуванні експертів, яка виключає їх безпосередній контакт, направленому зменшення групового впливу, виникає при спільну роботу експертів і який перебуває в пристосуванні до думки большинства.
Багато в чому метод розрахунку потреби у матеріалах немає жодного необхідна точність розрахунку залежить від різних характеристик материалов.
Допоміжним засобом класифікації матеріалів служить АВСанализ.
Його зазвичай використовують із розподілу матеріалів залежність від кількості і цены (или якихось інших характеристик).
Його сукупно це дає побудова кривою Лоренца. Вона характеризує кумулятивне зростання величин двох взаємозалежних признаков (в % до підсумку), завдана на графік і ступінь концентрації окремих елементів по группам.
Для досліджуваних зазвичай співвідношень кількості і вартості цей аналіз призводить до наступним результатам: небагато найменувань деталей і матеріалів становить більшу частину вартості, для великої кількості найменувань ця частка вартості щодо мала (Рис.2).
[pic].
Рис. 2. Взаємозв'язок між кількістю і стоимостью.
Отже, 15% деталей становлять 80% вартості (група А), 35% - 15% (група У), 50% -5% (група С).
Тож деталей групи, А необхідно особливо точно розраховувати потреба, оптимальну величину замовлення, стан запасів слід старанно контролировать.
З допомогою аналізу XYZ асортимент деталей, що є складі розподіляють залежно від частоти потребления.
Деталі класу X характеризуються постійної величиною їх потребности.
Деталі класу Y характеризуються заздалегідь відомими тенденціями визначення потреби у них (наприклад, сезонностью).
Деталі класу Z споживаються нерегулярно, будь-які тенденції споживання отсутствуют.
Іноді задля розподілення матеріалів на групи X, Y, Z використовують коефіцієнти варіації, зумовлені по формуле:[pic][pic], де [pic] - середнє абсолютне відхилення, що дорівнює середньої арифметичній з абсолютних відхилень (модулів) значень ознаки всіх одиниць сукупності середньої арифметичній ([pic]): [pic].
У цьому виділяють такі кордону класів: |Клас |Кордони зміни коефіцієнта варіації, в % | |Х |0 -10 | |У |10 — 25 | |Z |25 — [pic] |.
Використання технології штрихових кодов.
Для управління логістичній системою необхідна за будь-який час мати повну інформацію матеріальне потоці. Це завдання то, можливо успішно вирішена за умови використання спеціальної мікропроцесорної техніки, здатної ідентифікувати кожну вантажну одиницю. З цією метою використовуються звані штрихові коды.
Штрихові коди (Ваr codes) — модель чорних ліній і «білих просторів, які зчитуються сканирующим пристроєм, що містить різну информацию.
Вперше штрихові коди було застосовано в 60-ті роки американськими залізничниками для маркування вагонів. На 1973 року у США запроваджено універсальний товарний код (UPC — universal product code) (Рис.1):
Мал.1. Універсальний товарний код[20].
Нуль, розташований зліва, ототожнює номенклатурну позицію, п’ять цифр ідентифікують виготовлювача (14 800), останні п’ять (23 208) — ідентифікують особливості изделия.
Цей код особливе поширення одержав у в промисловості й сфері услуг.
Він спрощує процеси виробництва та контролю запасів, сортування, упаковки. Застосовується для маркування комплектуючих, напівфабрикатів, готових изделий.
У сфері ж звернення більшого поширення має система EAN, що з’явилася у Європі на 1977 року. Є алфавіт коду EAN, у якому кожної цифрі відповідає певний набір штрихів і прогалин. На етапі запуску товару у виробництві йому присвоюється тринадцатизначный цифровий код, що у вигляді штрихів і прогалин наноситься цей товар. Перші дві і три роки цифри означають код країни-виробника, такі 4 цифр позначають предприятие-изготовитель. Інші цифри — закодоване найменування товару, його вага й розміри. Остання цифра — зазвичай, нуль — є контрольної і використовується для перевірки зчитування цифр сканером. Вона розраховується за спеціальному алгоритму.
Так, спочатку складають все цифри, які стоять на парних місцях, і множать їх суму в 3. До одержаному твору додають суму цифр, що стоять на непарних місцях, крім останньої, що є контрольної. Від підсумкового числа відкидають десятки і з десяти віднімають отриману останню цифру підсумкового числа. Отриманий результат відповідає контрольної цифре.
У тому 1991 р. ми мали створена асоціація ЮНИСКАН, що спеціалізується у сфері автоматичної ідентифікації. Російські підприємства мають можливість, зареєструвавши в асоціації, придбати індивідуальний код.
За суттю, штрихової кодспосіб запровадження інформацією ЕОМ. Зображення штрихового коду наноситься щодо, що є об'єктом управління у системі. Для реєстрації цього здійснюють операцію сканування. Світлове пляма рухається по штриховому коду. Варіації отриманого сигналу залежить від варіації відображеного світла. Розшифрувавши електричний сигнал, ЕОМ перетворює їх у цифровий код.
Цей код є адресою осередки пам’яті в ЕОМ, що містить повну інформацію про товаре.
Застосування технології штрихового кодування дозволяє у виробництві створити систему обліку й контролю руху виробів та її частин кожній ділянці, і навіть ознайомитися з станом логістичного процесу на підприємстві цілому, скоротити кількість допоміжного персоналу, спростити звітність і виключити їх помилки. У складському господарстві цю систему дозволяє автоматизувати облік контроль над рухом матеріального потоку, автоматизувати процес інвентаризації запасів, і навіть скоротити час на логістичні операции[21].
Логістика складирования.
Ефективність логістичній системи залежить тільки від вдосконалення промислового виробництва, а й складського хозяйства.
Рух матеріального потоку через склад збільшує вартість продукції. У цьому витрати з складуванню стають дуже помітними в загальної ланцюжку освіти вартості з виробництва, що робить актуальним вивчення проблем, що з функціонуванням складського хозяйства.
Сучасне складське господарство є комплексом высокомеханизированных складів, спеціалізованих за видами матеріальних ресурсів з огляду на вимоги по оптимізації умов його збереження і складської переработки.
Склад — будинку, споруди, устрою, призначені для приймання, концентрації та зберігання різних тих матеріальних цінностей, підготовки їх до виробничому споживання і ритмічного відпустці потребителям[22].
Склади промислових підприємств класифікуються наступним образом:
1. За характером діяльності чи з призначенню: матеріальні (постачальницькі) склади, внутрипроизводственные (межцеховые і внутрицеховые), сбытовые.
2. По вигляду й характеру збережених матеріалів: універсальні і специализированные.
3. На кшталт конструкції: закриті, напівзакриті, відкриті, специальные.
4. За місцем розташування: станційні чи портові, прирельсовые, глубинные.
У складської системі взаємодіють матеріальні потоки, які засновані на функціях транспортування і збереження. Функція транспортування визначає рух матеріалів, а функції зберігання реалізують, крім складування, різні види вирівнювання збережених запасів. Наприклад, вирівнювання за часом необхідна за тому випадку, якщо періодичність попиту відповідає часу виготовлення, вирівнювання за кількістю належить до підприємств, у яких серійне виробництво, вирівнювання обсягів пов’язано із доставкою вантажів транспортними засобами (для скорочення транспортних витрат склад може об'єднувати партії вантажів до завантаження транспортний засіб), вирівнювання асортименту необхідне підприємств, які виробляють різноманітний асортимент продукції, требующийся в різні періоди времени.
Ефективне функціонування складського господарства має враховувати такі вопросы[23]: вибір між власним складом чи складом загального користування, кількість складів і розміщення складської мережі, величину і місце розташування складу, вибір системи складирования.
Функції складів реалізуються у процесі здійснення окремих логістичних операцій. Вирізняють наступний комплекс складських операцій: розвантаження транспорту, приймання товарів, складування і збереження, отборка товарів з місць зберігання, комплектування (комиссионирование) й упаковки товарів, навантаження, внутрискладское перемещение[24].
На етапі розвантаження і приймання вантажів здійснюється розвантаження (звільнення) транспортних засобів тягаря, контроль документального і фізичного відповідності замовлень поставки, документальне оформлення прибулого вантажу, формування складської вантажний единицы.
Вантажна одиниця — певна кількість вантажів, які занурюють, транспортують, вивантажують і зберігають як єдину масу. Характеристиками вантажний одиниці є її розміри, спроможність до збереженню цілісності і початковою геометричній форми у процесі різних логістичних операцій. У цьому важливого значення набуває визначення її оптимального виду та розмірів, дозволяють мінімізувати кількість операцій із переробці вантажів. Розміри вантажних одиниць би мало бути сполученими з устаткуванням для навантаження, розвантаження, транспортування і збереження. Процес складування залежить від розміщення і укладанні вантажу за зберігання. Важливе значення під час проведення складування набуває ефективне використання зона зберігання. Це забезпечується оптимальним вибором системи складирования.
Розрізняють такі різновиду складування: одиничне зберігання, лінійне зберігання, блокове зберігання. Одиничне зберігання притаманно великих деталей і машин. Лінійне зберігання забезпечує прямий доступ для різних деталей. У цьому вироби можуть зберігатися безпосередньо на підлозі чи полках-стеллажах. Можуть також застосовуватися пересувні стелажіетажерки. У висотних складах відбірник у спеціальній підйомнику пересувається вздовж осередків і відбирає потрібні вироби. Такі склади називаються статичними. У висотних динамічних складах підйомник автоматично подається до осередку із необхідним вантажем і вантаж транспортується до робочого місцеві добирача. Тут необхідну кількість вантажу відбирається, решта подається знову на місце хранения[25].
Збереження складованих об'єктів в блоках характеризується щільним (без просвітів) розташуванням штабелируемых одиниць. І тут то, можливо досягнуто хороше використання обсягу складу, та заодно відсутня прямий доступом до збереженим об'єктах. Що стосується блокового складування переміщатися і зберігатися можуть використовуватися лише комплектні единицы.
У середовищі сучасних складах найчастіше використовують комбінації різних видів складирования.
Выводы.
1. Логістика — наука про плануванні, організації, управлінні, контролі і регулювання руху матеріальних й інформаційних потоків в просторі та у часі від своїх первинного джерела до кінцевого потребителя.
2. Під матеріальним потоком слід розуміти сировину, напівфабрикати, готові вироби, аналізовані у процесі додатку до ним різних логістичних операцій (розвантаження, укладка на піддони, пересування та т.п.) і віднесені до якогось інтервалу времени.
3. Під інформаційним потоком розуміють сукупність які у логістичній системі, і навіть між цієї системою та довкіллям повідомлень, супроводжуючих матеріальний поток.
4. Визначення доцільного рівня запасу найчастіше зводиться до вибору раціональних моментів замовлення (коли?) і раціональних обсягів поповнень (скільки, скільки?). І тут розглядаються дві альтернативи: або замовлення виробляються вони часто й малими партіями, або рідко й у великому объеме.
5. Додаткове кількість матеріалів, може заказываться після визначення потреби з урахуванням вже укладеного договору. Інший підхід грунтується на ритмічності отримання замовлень. І тут застосовуються системи з фіксованою розміром замовлення (perpetual inventory system — стала система) і з фіксованою інтервалом часу між замовленнями (periodic system — періодична система).
6. Існують три методу розрахунку потреби у матеріалах: детермінований (певний), стохастический (імовірнісний) і эвристический.
7. Управління матеріальними потоками у межах внутрішньовиробничих логістичних систем здійснюється з двох основних підходів: перший підхід є систему з «виштовхуванням» (Push system) вироби, другий — систему з «витягуванням» виробів (Pull system).
8. Штрихові коди (Bar codes) — модель чорних ліній і «білих просторів, які зчитуються сканирующим пристроєм, що містить різну информацию.
9. Склад — будинку, споруди, устрою, призначені для приймання, концентрації та зберігання різних тих матеріальних цінностей, підготовки їх до виробничому споживання і ритмічного відпустці потребителям.
Питання для повторения.
1. Що слід розуміти під логистикой?
2. Що таке матеріальний і інформаційний потоки?
3. Наведіть основні відомостей про історії логистики.
4. Які питання вирішуються на теорії управління запасами?
5. Які чинники впливають на доцільний рівень запасов?
6. У чому суть системи з фіксованою розміром заказа?
7. У чому суть системи з фіксованою інтервалом времени?
8. Як визначається потреба у материалах?
9. Яка практична значимість АВС — аналізу та ХУZанализа?
10. У чому особливості систем з «виштовхуванням» і «витягуванням» виробів, запущених в производство?
11. Що таке штрихові коди і що складаються переваги їх применения?
12. Як можна класифікувати склади промислового підприємства? ———————————- [1] Англо-російський економічний словник/ під ред. А. В. Аникина.-М.: Російський мову, 1977, с. 365. [2] В. К. Мюллер Англо-російський словарь.-М.: Російську мову, с. 441. [3] William J. Stevenson Production/Operations Management.-4-th ed., IRWIN, INC., 1993, p.725. [4] Логістика: Учеб. пособие / під ред. Б. А. Аникина.-М.:ИНФРА-М, 1997, с. 7. [5] Саме там, с. 10. [6] Саме там, с. 14. [7] У фундаменті економічної літературі виділяють і дещо інші етапи розвитку логістики: наприклад, дологистический період (до 1950;х років), період класичної логістики (60-ті роки), період неологистики (початку 80-х років). Див., наприклад, Логістика /під ред. Б. А. Аникина.-М.: ИНФРАМ, 1997, с.31−37. [8] Виробництво на замовлення може застосовуватися й за умов дефіциту, коли виробляється складна й дорога продукція. У умовах доцільно почекати, поки споживач точно б не викладе власні вимоги. Наприклад, будувати судна чи электротурбины складу немає звичаю. Колії самих або арматурную сталь виробляють складу. Це ж характерне й для продукції, має безліч модифікацій (Див.: Янош Корнаи Дефіцит.- М.: Наука, 1990, с.137). [9] MRP — material requirement planning [10] Вперше цю систему була випробувана в 1972 року на автомобільної фірмі «Тайота». Автор системи Т. Оно використовував принцип «останнього ланки», застосовуваний у супермаркетах, для промислового виробництва. У супермаркетах покупець є інформаційним джерелом необхідного кількості, асортименту тощо. Імпульс для функціонування системи служить попит, визначається покупцем. [11] У літературі є вказівку, що фонетично точнішим є термін «камбан». См., например, Статистичні методи підвищення якості /Під ред. Хитоси Кумэ.- М.: Фінанси і статистика, 1990, з. 274. [12] Янош Корнаи Дефицит.-М.: Наука, 1990, с. 139. [13] Cм. Рис. 2. [14] Докладніше звідси див.: Неруш Ю. М. Коммерческая логістика /підручник.- М.: ЮНИТИ, 1997, с. 141. [15] Докладніше звідси див.: Логистика: Учеб. пособие / Під ред. Б. А. Аникина.- М.:ИНФРА-М, 1997, с.237−246. [16] Неруш Ю. М. Комерційна логістика/ підручник, М.: ЮНИТИ, 1997, с. 143. [17]Подробнее звідси: Статистичне моделювання та прогнозування /під ред. А. Г. Гранберга.-М.: Фінанси і статистика, 1990, с.184−189. [18] Промислова логістика / перекл. А. В Проскуряков, Н. К. Моисеева, Н. Т. Севруков, А. Н. Пилищенко.- Санкт-Петербург, Політехніка, 1994, с.78−83. [19] Метод Дельфи отримав назву від міста Дельфи, що є відомим зза віщунів — оракулів, мешканців ньому й котрі пророкують майбутнє. Пророцтва оприлюднювалися після ретельного обговорення раді дельфийских мудреців. [20] Докладніше про UPC див.: William J. Stevenson Production/Operfnions Management.-4th ed.-RICHARD D. IRWIN, INC., 1993, р.589. [21] Гаджинский А. М. Основи логистики.-М.:ИВЦ «Маркетинг», 1996, с. 105. [22] Неруш Ю. М. Комерційна логістика/ учебник.-М.: ЮНИТИ, 1997, с. 165 [23] Логістика /навчальних посібників під ред. Б. А. Аникина.-М.: ИНФРА-М. 1997, з. 254. [24] Гаджинский А. М. Основи логістики (2-ге издание).-М.: ИВЦ «Маркетинг», 1996, с. 82. [25] Саме там, с. 86.
———————————;
Замовлення покупателя.
Планування потреби у матеріалах, деталях, полуфабрикатах.
Сборка.
Склад.
Цех.
Поставщик.
Замовлення покупателя.
Заказ.
Заказ.
Поставщик.
Цех.
Сборка.