Проект механізації поточної технологічної лінії подрібнення коренебульбоплодів
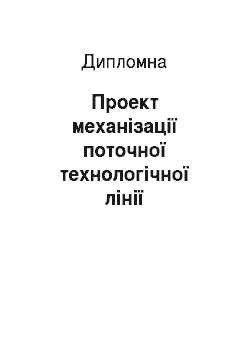
В кормоцеху і на території, яка прилягає, необхідно систематично прибирати відходи і залишки корму, проводити відповідні заходи по боротьбі з гризунами, а в літній час обробляти різними аерозольними препаратами проти мух. Необхідно проводити дезинфекцію силосних ям, складських приміщень. Для цього використовують 2% розчин хлораміну. Для дезинфекції бункерів, транспортерів, машин і обладнання… Читати ще >
Проект механізації поточної технологічної лінії подрібнення коренебульбоплодів (реферат, курсова, диплом, контрольна)
Вступ
Динамічний розвиток економіки сучасної України залежить від багатьох важливих факторів. В період становлення молодої незалежної України, розриву економічних зв’язків між республіками СНД — знизились темпи виробництва, як промислової так с/г продукції. Ці фактори призвели до зниження виробництва зерна, м’яса, молока, скорочення поголів'я худоби, птиці.
На сьогоднішній день постало питання, як подолати ці економічні негаразди, вийти з кризи, підняти на рівень світових стандартів випуск промислової продукції і продукції аграрного сектору.
Ці всі важливі питання знаходяться на контролі уряду України, Верховної Ради, міністерства сільського господарства. Відшуковуються резерви та шляхи покращення становища у виробництві продукції сільського господарства, а також продукції тваринництва.
В тваринництві на сучасному етапі ще не в повній мірі вирішені питання забезпечення галузі засобами механізації, матеріально-технологічного забезпечення матеріалами, запасними частинами, паливно-мастильними матеріалами.
В тваринництві низький рівень продуктивності праці, а якщо він і підвищується в певних галузях, то не в значній мірі.
Також не в повній мірі вирішені питання механізації невеликих поточних ліній на молочних фермах на 100−400 голів, а в свинарстві до тисячі голів, коли і надалі на таких фермах виробляється і буде вироблятися в найближчі роки значна кількість продукції. Ручна праця на даних фермах становить 60−70%. Виникає необхідність в прискореному і повному скорочені ручної праці на багатьох мало механізованих і допоміжних операціях. Крім цього, для досягнення високих надоїв молока і отримання кілограмових приростів в живій масі, необхідно тварин годувати збалансованими по поживності кормо сумішами. Однак відсутність високопродуктивних машин для подрібнення коренебульбоплодів стримує впровадження в виробництво годівлю тварин збалансованими кормовими сумішами. Тому темою дипломного проекту є «Проект механізації поточної технологічної лінії подрібнення коренебульбоплодів», яка передбачає розробку конструкції подрібнювача коренебульбоплодів згідно зоотехнічними вимогами.
1. Огляд сучасних технологій приготування кормів та кормоцехів
1.1 Способи підготовки кормів до згодовування
Процес приготування кормів може вимагати ряд технологічних заходів, різних за своєю природою та цілеспрямованістю (рис. 1).
Ефективність застосування того чи іншого технологічного заходу у процесі кормоприготування може проявитися різними шляхами і переслідувати як окремі цілі, так і їх комплекс. В основному вони зводяться до поступового покращення якості корму і підвищення його ефективної дії.
Розширюється і спрощується можливість використання тієї чи іншої сировини для годівлі і цим самим збільшується набір компонентів для різних видів тварин, зміцнюється кормова база галузі.
Після відповідної обробки (наприклад, подрібнення) в раціон свиней та птиці можна включати стеблові (сухі у вигляді сінного не трав’яного борошна, а зелені у вигляді дрібної січки), крупнокускові (макуха, коренеплоди, баштанні) та деякі інші корми.
Збільшується і покращується поїдання кормів. Наприклад, тварини погано поїдали непідготовлену солому (не більше 2−3 кг на голову ВРХ), а її втрати досягають 20−30%. Після відповідної підготовки (подрібнення, теплової або хімічної обробки) солома поїдається майже повністю і в більшій кількості. Прискорюється і підвищується перетравлення кормів. Так, зернові корми, що мають високий вміст поживних речовин та добрі смакові якості, у більшості випадків виявляються малоефективними, якщо їх згодовувати без попередньої перепідготовки. Ціле сухе зерно тварина погано розжовує, тому значна кількість поживних речовин залишається неперетравленою і виділяється з організму разом з калом. Істотно підвищується і перетравність соломи після її гідролізу.
При цьому попереднє подрібнення соломи прискорює процес хімічної обробки, підвищує її ефективність.
Скорочуються витрати енергії тварин на пережовування корму, запобігаються деякі захворювання тварин. Відомо, що на пережовування 1 кг соломи тварина витрачає 625−840 Дж. Отже, економія енергії на пережовування рівноцінна додатковій продуктивній дії корму.
Встановлено, що поживна цінність 100 кг подрібненої на січку соломи зростає на 0,8−1,2 кормових одиниць, а подрібненої на борошно на 1,6−2,0 порівняно з натуральною. Виявлено також зниження витрат енергії і на перетравлення інших подрібнених кормів. А згодовування цілого зерна чи несвіжих кормів може спричинити шлункові захворювання у тварин. Розширюється асортимент кормів, створюються умови для кормовиробництва та кормоприготування на промисловій основі і впровадження прогресивних технологій годівлі тварин. Відповідна обробка кормової сировини дозволяє готувати кормові суміші, комбіновані та повнораціонні корми. Перетравлення кормів в організмі тварин у значній мірі залежить від повноцінності і збалансованості годівлі. При надмірному, але погано збалансованому раціоні до 35−45% поживних речовин його не застосовуються. У той час приготування повноцінних кормів (сумішок) дозволяє значно зменшити витрати дорогих концентрованих і збільшити споживання відносно дешевих (грубі, відходи деяких виробництв) кормів, підвищити ефективність всіх компонентів раціону.
Поряд з традиційним використанням соковитих, грубих та концентрованих кормів в останні роки набули розповсюдження сінажно-концентровані типи годівлі, приготування вітамінного борошна, брикетування та гранулювань кормів.
З підвищенням рівня інтенсифікації тваринництва спостерігаються тенденції до переходу від багатокомпонентних раціонів на монокорми з додаванням необхідних добавок. Технологія приготування монокорму така.
Рис. 1.1 — Способи обробки кормів Рослини скошуються у стадії бутонізації - початку цвітіння трав або молочно-воскової стиглості зерна, тобто, коли вони мають найбільш високий вміст поживних речовин. Після цього висушуються в сушильному апараті і подрібнюються на борошно або січку, а потім збагачуються білковими, мінеральними та біологічно-активними речовинами і гранулюються чи брикетуються. Перехід від багатокомпонентних раціонів до ущільнених монокормів має такі переваги:
— дозволяє суміщати кормовиробництво і підготовку кормів до згодовування в одному процесі, здійснюючи заготівлю кормів у заздалегідь сплановані оптимальні строки і незалежно від погодних умов;
— забезпечує суттєве збільшення виходу поживних речовин з одиниці площі посіву і знижує їх витрати у процесі зберігання;
— спрощує рішення питань механізації та автоматизації приготування, зберігання і роздавання кормів: дозволяє на всьому шляху від поля до годівниці, тобто починаючи зі збирання і закінчуючи годівлею, механізувати всі процеси і операції;
— не потребує різнотипних сховищ та механічних засобів.
Таким чином, відносно до процесів кормоприготування можливі два підходи. Перший — коли відповідна підготовка є обов’язковою, щоб забезпечити саму можливість використання тієї чи іншої сировини як корму, тобто для перетворення потенційного корму на дієвий. Другий — коли підготовка доцільна в технічному та економічному відношеннях, оскільки сприяє раціонному і ефективному використанню кормів, супроводжуються збільшенням виходу продукції тваринництва при тих же запасах кормів.
Якщо враховувати масштаби розвитку тваринництва, а також той факт, що в сучасному виробництві тваринницької продукції відсоток затрат, пов’язаних з кормами, у загальному балансі собівартості цієї продукції перевищує 40−45% (молочнотоварне виробництво), а на промислових компонентах досягає 70−80% (наприклад, свинарство, птахівництво). Обидва названих підходи — розширення кормових ресурсів перевищення їх ефективності - є дуже важливим і постійно актуальним.
1.2 Технологічні схеми підготовки кормів до згодовування
Вибір технології кормоприготування обумовлюється наявними кормовими компонентами та їх якістю, видом та віком тварин, прийнятим типом годівлі. При цьому технологія кормоприготування в широкому розумінні цього визначення — це структура і послідовність способів та заходів обробки кормової сировини, мета яких одержати готові до згодовування корми.
Стосовно конкретних видів кормів багаторічним досвідом визначені раціональні технологічні заходи. Деякі з них є обов’язковими для більшості видів кормової сировини. Це очищення та подрібнення. Крім того, для реалізації найбільш доцільної технології годівлі тварин (кормовими сумішами) обов’язковим є також операції дозування та змішування.
На рисунку 2 зображені технологічні схеми підготовки до згодовування базових видів кормі, найпоширеніших у виробничій практиці.
Таким чином, процес кормоприготування полягає у виконанні технологічних операцій, спрямованих на подання сировини, що обробляється, нових властивостей. А машини, що виконують такі операції, називаються технологічним обладнанням. Крім технологічного обладнання, у процесі кормоприготування для переміщення об'єкту від машини до машини, чи його перевантаження використовується і допоміжне обладнання, яке забезпечує потік і безперервність, усуває ручну працю в процесі кормоприготування.
Рис. 1.2 — Технологічна схема підготовки до згодовування
2. Обґрунтування технологічних параметрів приготування кормів
2.1 Зоотехнічні вимоги до приготування кормів
При приготуванні кормів для ВРХ слід дотримуватися слідуючи зоотехнічних вимог:
— сіно повинно мити приємний запах, зеленуватий колір, в 1 кг має бути 0,42…0,46 кормові одиниці і 48…58 г перетравленого протеїну, 25…35 кг каротину;
— сінаж повинен мати приємний фруктовий запах, жовто-зелений колір, в 1 кг має бути 0,3…0,35 кормові одиниці, 30…60 г перетравленого протеїну, 40 мг каротину, 5 г кальцію, близько 1 г фосфору;
— силос повинен мати кислотність рН-3,5…4,6, не містити плісняви і оцінюватись на 11 балів за шкалою оцінки, мати приємний фруктовий або квашених овочів запах, і містити каротину в 1 кг — 15…25 мг;
— зерно кукурудзи, ячменю, вівса гороху та інших зернобобових культур перед згодовуванням тваринам розмелюють, подрібнюють, плющать. Для ВРХ краще його подрібнювати на частки розміром часток 1,5…3 мм, свиням 0,2…1 мм;
— консервоване зерно (вологість до 30…35%) плющать до мінімальної товщини 0,5 мм. Відхилення не повинне перевищувати ±20%. Кількість зерен з не пошкодженою поверхнею допускається до 1%.;
— коренеплоди мають бути чистими, без гнилі, плісняви, забруднення землею не повинно перевищувати 2…3% за масою, частки після подрібнення мають бути товщиною 10…15 мм;
— кормова суміш повинна бути однорідною (рівномірно вимішаною), без забруднення, мати температуру 12…250С, вологість 25…42%, зберігатися не більше 1,5 години, мати задану кормову поживність і необхідну кількість вітамінів.
2.2 Фізико — механічні властивості кормів
Корми поділяються на грубі, соковиті, вологі (рідкі), концентровані, мінеральні, синтетичні та відходи технічної промисловості.
Таблиця 2.1 — Фізико-механічні властивості кормів
Назва корму | Об'ємна маса | Кут природного скосу ш | Коефіцієнт тертя по сталі f | |
Сіно | 95…140 | 50…65 | 0,25…0,30 | |
Подрібнена солома | 70…100 | 43…50 | 0,24…0,33 | |
Буряк кормовий | 560…620 | 30…45 | 0,48…0,50 | |
Бараболя | 600…650 | 25…35 | 0,45…0,50 | |
Горох | 800…820 | 14…20 | 0,20…0,30 | |
Кукурудза | 700…780 | 30…35 | 0,30…0,42 | |
Ячмінь | 560…710 | 35…38 | 0,35…0,47 | |
Силос | 600…750 | 65…70 | 0,66…0,70 | |
Сінаж | 500…600 | 65…70 | 0,60…0,65 | |
комбікорм | 600…750 | 35…40 | 0,35…0,40 | |
3. Розробка конструкції подрібнювача коренебульбоплодів
3.1 Необхідність розробки конструкції подрібнювача
Подрібнені коренеплоди є доброю добавкою до кормової суміші і охоче поїдається тваринами. В відповідності з вимогами розміри часток подрібнених коренеплодів для ВРХ мають розміри 5…12 мм. Практика показує, що подрібнювачі, які випускаються серійно, а саме ИКМ-5, ИКС-5М, ДИС-1М, Волгарь-5) не забезпечують такого рівня подрібнення, Окрім того, вони мають низьку експлуатаційну надійність, велику енергоємність і вагу, складну конструкцію, дорогі. При подрібненні кормового буряка даними машинами виділяється велика кількість соку, який розливається через отвори на підлогу кормоцеху. Скористатися з будь-яким з перекислених подрібнювачів в нашому кормоцеху буде нераціонально. Тому нам необхідно розробити таку конструкцію подрібнювача коренеплодів, яка б виконувала подрібнення з мінімальними затратами електроенергії, праці, із відповідними зоотехнічним вимогам розмірами часток.
Таким подрібнювач на мій погляд повинен бути подрібнювач з барабанним робочим органом з ножами, які мають ріжучу кромку, розміри часток подрібнених коренебульбоплодів будуть відповідати певному зазору між ножами і прорізами. Розроблений подрібнювач коренебульбоплодів повинен відповідати зоотехнічним вимогам.
3.2 Зоотехнічні вимоги до подрібнювача
Зоотехнічні вимоги подрібнювача зводяться до наступного:
1. Висока продуктивність.
2. Універсальність використання схожих операцій.
3. Змога регулювання ступеня подрібнення і продуктивності.
4. Машина не повинна загромаджувати проходи і затемняти приміщення.
5. Розміри подрібнювача повинні допускати його використання в типових тваринницьких приміщеннях.
6. Зручність очищення від залишків кормів.
7. Надійність в роботі і простота в керуванні.
8. Взаємозаміна робочих органів на випадок їх поломки.
9. Можливість використання засобів автоматики.
10. Простота будови і експлуатації.
11. Він повинен добре подрібнювати і не допускати лишніх витрат.
12. Мати мінімальні енерговитрати.
13. Володіти кращими техніко-економічними показниками.
3.3 Огляд існуючих подрібнювачів коренебульбоплодів
Подрібнювач «Волгарь-5». Складається з комбінованого робочого органу, живильного механізму, рами механізмів передачі і електроприводу. Робочий орган подрібнювача складається з двох ступіней подрібнення: барабанного типу і шнеково-ножового типу. Апарати першого і другого ступіней подрібнення приводять в дію клинопасовими передачами від шківа електродвигуна. Подрібнювальну масу подають вручну на горизонтальний траст портер, який транспортує до похилого транспортера. Той в свою чергу ущільнює шар маси і подає далі під ножі різального барабану. Подрібнена маса падає на шнек і транспортується до апарата другого ступеня, де подрібнюється вдруге до величини часток 2…10 мм і викидається через вивантажувальне вікно.
Регулювання машини: зазор між лезами барабана і притирізальної пластини, регулюють шляхом переміщення підшипників барабана і проти різальної пластини в межах 0,5−1,0 мм. Натяг полотна подавального транспортера регулюють натяжними гвинтами. Провисання нормально затягнутого полотна від прикладеного зусилля в 10 кгс повинно становити 20−25 мм.
Зусилля стискання пружин фрикційної муфти регулюють болтами. Нормальне зусилля повинно становити 120−180 кг. Натяг приводних ланцюгів регулюють натяжними зірочками, а приводних пасів натяжними роликами і електродвигуном. Ступінь подрібнення регулюють кутом становлення першого рухомого апарата другого ступеня подрібнення відносно кінця шнека. Подрібнювач «Волгарь-5» приведений на рисунку 3.1.
Рис. 3.1 — Схема технологічного процесу подрібнювача «Волгарь-5»: 1 — подавальний транспортер; 2 — прижимний транспортер; 3 — різальний барабан; 4 апарат другого ступеня подрібнення; 5 — електродвигун
Подрібнювач ИКС-5М. Призначений для миття і подрібнення коренебульбоплодів. Він відрізняється від подрібнювача ИКС-5 конструкцією робочого органа подрібнювального барабана. На роторі подрібнювача ИКС-5М встановлені молотки замість штифтів. Подрібнювач складається з наступних одиниць: бункера-ванни, шнекового транспортера, подрібнюючого апарату, насоса, насоса і системи циркуляції води.
Технологічний процес роботи: коренебульбоплоди завантажують в бункер, попадаючи в ванну, вони проходять перше очищення і миття. Потім вони захвачуються шнеком і подаються до подрібнювача. В процесі транспортування коренеплодів, вони додатково ополіскуються водою, яка подається через розпилювач, який розміщений в верхній частині шнека. Болото і камінці осідають в ванній. Подрібнення кормів здійснюється під дією молотків і проти різальної гребінки, а подрібнена маса направляється по поворотному лотку на транспортер чи в транспортний засіб.
Подрібнювач-каменевловлювач ИКМ-5. Складається з завантажувального бункера, живильного шнека, подрібнювального апарата дискового типу і скребкового каменевивантажувального транспортера. Подрібнювальний апарат складається з литого корпусу, нижнього і верхнього дисків, двох горизонтальних і чотирьох вертикальних ножів. Диски надіті на вал електродвигуна і зафіксовані. Скребковий транспортер призначений для вивантаження каміння, піску, болота з ванни подрібнювача. Вона являє собою місткість несучої зварної конструкції. Верхня частина ванни закрита листом, на якому кожух шнека.
Подрібнювач коренеплодів ИКМ-Ф10.Виконує функції аналогічні ИКМ-5 (рис. 3.2).
Рис. 3.2 — Технологічна схема ИКМ-Ф10: 1-бункер для коренебульбоплодів; 2-конус для видалення грязі; 3-транспортер; 4-шнек; 5-кожух шнека; 6-електродвигун шнека; 7-подрібнювач; 8-електродвигун подрібнювача
Він призначений для роботи в технологічних лініях кормоприготування на тваринницьких фермах. Відрізняється конструкцією шнека та на ньому використовується одно швидкісний електродвигун. Попереднє сухе очищення коренебульбоплодів на цій машини здійснюється барабаном діаметром 660 м і довжиною 950 м. Від обертається за допомогою електродвигуна з частотою 39 об/хв. На рис. 3.2 представлена конструктивна схема подрібнювача ИКФ-10.
3.4 Принципи дії розроблювального подрібнювача та обґрунтування його параметрів
Запропонований подрібнювач складається з камери, яка має форму циліндра, в середині розміщений ротор. На внутрішній поверхні камери закріплені два протирізи. На ротору подрібнювача закріплено викидач подрібнених коренебульбоплодів. Ротор обертається на двою шарикових підшипниках, які змонтовані в одному стакані, який кріпиться до дна камери. На валу ротора напресований ведений шків (див додаток). Привід ротора здійснюється через клинопасову передачу від електродвигуна.
В верхній частині камери закріплено конусну завантажувальну горловину, а в нижній — вивантажувальне вікно. На конусній поверхні ротора виготовлені чотири пази, для проходу подрібнених частин, коренебульбоплодний викидач.
Чотири Z — подібних ножі закріплені над пазами при допомозі болтів і гайок. Камера спирається на три підпірки, виготовлені з швелера. До однієї з них кріпиться електродвигун.
Подрібнення коренебульбоплодів, які за допомогою транспортера ТК-5Б завантажуються в камеру, відбувається шляхом зрізання стружки ножами, закріпленими на роторі.
Зрізана стружка через порізані пази падає на дно камери і вигортається в вивантажувальну горловину. Щоб коренебульбоплоди в камері не рухалися разом з ротором, вони зупиняються протирізами.
Подрібнювач коренебульбоплодів для заданої продуктивності повинен мати продуктивність, яки визначаємо по формулі:
(3.1)
де G — максимальна добова норма коренебульбоплодів, G = 8500 кг;
Ку — коефіцієнт можливого збільшення продуктивності подрібнювача, Ку = 1,2;
КН - коефіцієнт можливих перевантажень подрібнювача, КН = 1,1;
ф — тривалість роботи кормоцеху протягом доби, ф = 3 год.
Таким чином, подрібнювач повинен забезпечити продуктивність не нижчу ніж 3090 кг/год. На рисунку 3.3 показана технологічна схема такого подрібнювача.
Рис. 3.3 — Технологічна схема подрібнювача: 1-завантажувальна горловина; 2-камера; 3-протиріз; 4-ротор; 5-ніж; 6-вигортач; 7-привід; 8-підпорки; 9-вивантажувальна горловина
Кутову швидкість обертання ротора знаходимо по формулі:
(3.2)
де п — частота обертання ротора,
(3.3)
де і — передаточне число пасової передачі, і = 1,5.
.
При конусному розміщені ножів на поверхні ротора швидкість кожної окремої точки буде різною. Мінімальна лінійна швидкість буде в верхній частині (точка А) і максимальна в нижній частині (точка В) (див. рис. 3.4).
Рис. 3.4 — Схема для визначення швидкості обертання ротора Лінійна швидкість точки, А буде:
А точки В буде:
Для розрахунків приймаємо середню лінійну швидкість:
(3.4)
Можна допустити, що такою швидкістю проходить процес різання коренебульбоплодів в нашому подрібнювачі. Знаходимо радіус обертання точки з середньою швидкістю:
(3.5)
Враховуючи ІІ-й закон Ньютона, знаходимо відцентрову силу:
(3.6)
де т — маса коренеплодів на роторі:
(3.7)
де V — об'єм частини камери між ротором і циліндром камери, м3;
с — об'ємна маса коренебульбоплодів, с = 540 кг м3;
ш — коефіцієнт, враховуючий заповнення камери, ш = 0,8.
Знаходимо об'єм:
(3.8)
Рис. 3.5 — Схема для знаходження об'єму частини камери (виділена частина)
Силу земного тяжіння РТ, з якою діють коренебульбоплоди на стінки ротора, знаходимо по формулі:
(3.9)
де т1 — маса коренеплодів, яка знаходиться в камері,
т1 = т + т11,(3.10)
де т11 — маса коренеплодів, яка знаходиться над ротором,
.(3.11)
Рис. 3.6 — Схема для знаходження кута нахилу твірної зрізаного конуса
(3.12)
,
.
Знаходимо бічну поверхню зрізаного конуса по формулі:
(3.13)
де l — твірна конуса,
(3.14)
.
За один оберт ротор своїми ножами зніме стружку з коренеплодів масою, яка рівна:
(3.15)
де Ни — висота ножа над поверхнею ротора, Ни = 0,010 м,
ш — коефіцієнт, який враховує заповнення камери в зоні обертання ротора з врахуванням відбивання коренебульбоплодів, ш0 = 0,20.
Z — кількість ножів на роторі, які беруть участь в подрібненні, Z = 2.
К0 — коефіцієнт, який враховує щільність прилягання коренебульбоплодів до поверхні ротора, К0 = 0,25.
.
При частоті обертання ротора подрібнювача и = 0,40 хв-1 і коефіцієнту нерівності подачі коренебульбоплодів в камеру о = 0,45, продуктивність Wn нашого подрібнювача буде рівною:
.(3.16)
.
Порівнюючи Wn i W ми маємо, що Wn > W (9136 > 3090). Це означає, що по продуктивності подрібнювач нас задовольняє.
3.5 Розрахунок кінематичних та енергетичних параметрів подрібнювача
Кінематична схема представлена на додатку графічної частини проекту. Із схеми видно, що передача крутячого моменту вала електродвигуна на ротор здійснюється клинопасовою передачею.
Враховуючи частоту обертання вибраного електродвигуна пдв = 1410 хв-1 і необхідну частоту обертання ротора п = 940 хв-1, знаходимо передаточне число клинопасової передачі:
(3.17)
.
Задаємося діаметром ведучого шківа, який закріплений на валу електродвигуна dв=100 мм.
Знаходимо необхідний діаметр веденого шківа dр, який закріплений на валу ротора подрібнювача.
.
Таким чином, для здійснення передачі крутячого моменту з валу електродвигуна на вал ротора необхідно мати dв=100 мм і dр = 150 мм, що забезпечує передаточне число і = 1,5.
Для знаходження потужності на поверхні коренеплодів використовуємо дослідження, проведені професором Резніком М.Є. Потужність на процес подрібнення коренеплодів він рекомендує знаходити по формулі:
(3.18)
де Р — сила різання коренеплодів;
Z — кількість ножів на роторі, Z = 4;
V — лінійна швидкість руху ножа, V = 16,7 м/хв.;
К0 — конструктивний коефіцієнт, К0 = 0,10.
Силу різання знаходимо по формулі:
(3.19)
де q0 — питомий тиск ножа на подрібнений матеріал, q0 = 1,5…20 кН/м;
lН — довжина леза ножа, lН = 0,24 м.
.
Підставляємо значення у формулу 4.18 і проводимо розрахунок:
.
Потужність електродвигуна, необхідного для приводу ротора подрібнювача, знаходимо за формулою:
(3.20)
де Кз — коефіцієнт запасу потужності, Кз = 1,1;
з — ККД передачі, з = 0,85.
.
По довіднику вибираємо тип електродвигуна 4АМ100S4 потужністю 3,0 кВт і частотою обертання пдв = 1410 хв-1.
3.6 Розрахунок клинопасової передачі
За допомогою клинопасової передачі проводиться передача обертання моменту від електродвигуна потужністю Nдв = 30 кВт і частотою обертання пдв = 1410 хв-1 на робочий орган подрібнювача коренеплодів. Передаточне число клинопасової передачі і = 1,5.
Рис. 3.7 — Схема для розрахунку клинопасової передачі
Визначаємо момент на швидкісному валу:
(3.21)
де щ1 — кутова швидкість обертання вала електродвигуна, розраховуємо по формул:
(3.22)
де пдв — частота обертання вала електродвигуна, пдв = 1410 хв-1.
.
При даному моменті рекомендують приймати паси з розмірами в = 13 мм, п = 8 мм, А1 = 81 мм2. Розрахунковий діаметр машинного шківа визначаємо по формулі:
(3.23)
.
Враховуючи стандартний ряд приймаємо dм = 100 мм.
Діаметр великого шківа повинен дорівнювати:
коренебульбоплід подрібнювач технологічний схема
(3.24)
Приймаємо dб 0 150 мм.
Визначаємо швидкість паса:
(3.25)
.
Визначаємо кутову швидкість ведучого шківа:
(3.26)
де е — відносна втрата швидкості, е = 0,02.
.
Визначаємо окружну силу:
(3.27)
.
Визначаємо оптимальні можливості відстані:
(3.28)
Приймаємо а = 200 мм.
Визначаємо довжину паса по формулі:
(4.28)
(3.29)
(3.30)
.
Приймаємо стандартну довжину L = 800 мм.
Визначаємо кут обхвату:
(3.31)
.
Визначаємо частоту пробігу паса:
.
З довідника вибираємо поправочні коефіцієнти: Ки = 1,11, С2 = 1,10, Ср = 0,8. Визначаємо корисну напругу:
(3.32)
.
Визначаємо допустиму корисну напругу:
(3.33)
.
Визначаємо необхідне число пасів:
(3.34)
.
Приймаємо Z = 3
Робочий коефіцієнт тяги:
.
Коефіцієнт:
.
Визначаємо сили, які діють в передачі:
.
Робочий натяг віток паса:
.
Натяг паса в спокої:
Визначаємо силу, яка діє на вали:
.
.
Отже, сила, що діє на вал рівна: Fa = 423 Н.
Виходячи з розрахунків ми приходимо до висновку, що для нашого подрібнювача досить два паса профілю А.
Вал ротора подрібнювача передає обертовий момент на носій. Вал встановлено вертикально. Частота обертання ротора п = 15,7 хв-1. Потужність електродвигуна Nдв = 3 кВт. Можливе перевантаження ротора 150%. Знаходимо діаметр вала, враховуючи тільки обертовий момент:
(3,35)
де Мк — обертовий момент, який діє на вал ротора, Нм;
[ф] — допустима напруга обертання вала, [ф] = 40 МПа.
(3.36)
де п — частота обертання вала, п = 940 хв-1;
Nдв - потужність електродвигуна, Nдв = 3000 Вт.
.
.
Рис. 3.8 — Схема до розрахунку міцності вала ротора Визначаємо реакції в точках, А і В.
Порівнюючи RA i RB бачимо, що RA > RB, а це означає, що найбільше напруження буде в точці А. Визначаємо максимальний знижений момент, а точці А.
.
Знаходимо напругу при зміні вала в перерізі (точка А):
.
Визначаємо напругу при скручуванні вала в точці А:
.
Перевірка на статичну міцність. При перевантажені в 150% коефіцієнт перевантаження Кп = 1,5. Вал виготовлений з сталі 40Х з характеристикою:
Нв = 200;ув = 730 МПа;уТ = 500 МПа;фТ = 280 МПа; у = 300 МПа;ф = 200 МПа;ш = 0,1;ш = 0,05.
Відношення При цьому відношення .
Перевіряємо вал в небезпечному перерізі:
Максимальна еквівалентна напруга :
.
Це означає, що міцність вала забезпечена. Враховуючи величини реакцій в точках, А і В, частоту обертання ротора і діаметр вала, приймаємо радіальні підшипники N180 308, внутрішній діаметр d = 40 мм, зовнішній діаметр d = 90 мм, ширина 23 мм.
Шпоночне з'єднання прийнято для з'єднання шківів з валом і диска з валом. В подрібнювачі застосовані три шпоночних з'єднання ведучого шківа з валом подрібнювача. Діаметр вала з місці з'єднання з шківом відповідає d = 30 мм, а розміри шпонок lр = 50 мм, b = 10 мм, h = 8 мм, t1 = 5 мм.
Міцність шпоночного з'єднання провіряємо за формулою:
(3.37)
де F — окружна сила, Н;
Асм - площа;
Мкр — крутячий момент, Мкр = 30,3 Нм;
d — діаметр вала під шпонку, d =30 мм;
h — висота шпонок, h = 8 мм;
t1 — глибина паза на валу, t1 = 5 мм;
lр — довжина розрахункової шпонки, lр = 40 мм;
[у] — допустиме навантаження, [у] = 80МПа.
.
Міцність шпоночного з'єднання забезпечена.
Рис. 3.9 — Схема для розрахунку шпоночного з'єднання Визначаємо міцність шпон очного з'єднання по формулі:
(3.38)
4. Екологія і безпека життєдіяльності
4.1 Вплив механічної підготовки кормосуміші на підвищення екології і безпеки життєдіяльності
Вдосконалення с/г виробництва, переведення тваринництва на промислову основу, будівництво, експлуатація великих тваринницьких комплексів ставлять перед багатьма спеціалістами (ветеринарної, санітарно-епідемічної служби, проектувальниками, господарниками і іншими) нові задачі по профілактиці інфекційних захворювань і охорони навколишнього середовища.
Охорона навколишнього середовища — це система державних заходів, що забезпечують зберігання природного середовища, здатного для нормального проживання сьогоднішніх і майбутніх поколінь.
Тваринництво на промисловій основі екологічно найбільш ефективно і дає змогу забезпечити населення м’ясними і молочними продуктами харчування.
Але розвиток тваринництва на промисловій основі поставило ряд складних проблем, пов’язаних з охороною навколишнього середовища. В дійсності, концентрація поголів'я на малих площах, накопичення великої кількості рідкого гною, який негативно діє на навколишнє середовище, впливає на здоров’я тварин, рослинництво, санітарно-побутові умови населення. Утилізація відходів і охорона навколишнього середовища сьогодні набуває ще більшого значення.
Основними забрудниками атмосфери с с/г техніка, відходи тваринництва.
Екологічну проблему в кормоцеху складають пил, шум, стічні води і шкідливі гази, які виділяються з кормів при неправильному їх зберіганні. Повна електрифікація технологічного процесу включила використання для приводу кормоприготувальних машин ДВС. А це виключило можливість забруднення приміщень і атмосфери вихлопними газами, що містять велику кількість токсичних речовин.
Велику проблему для кормоцехів складає очищення стічних вод (миття коренеплодів). Використання відстійників не дозволяє повністю очистити воду для подальшого циклу миття коренеплодів, а це потребує більшої кількості чистої води, забруднену воду виливають за межі кормоцеху.
При подрібнені грубих кормів виділяється велика кількість пилу, який забруднює як приміщення, так і територію. Особливо шкідливо діє цей пил на обслуговуючий персонал, забруднює деталі, що приводять до сильного зношування і збільшення витрат електроенергії на привід машини. Для ліквідації цього явища за подрібнювачем необхідно встановити циклон, в якому і буде осідати пил.
Основною задачею кормоприготування є своєчасна подача кормів без попадання паливно-мастильних матеріалів і інших сумішей. При заготівлі кормів для тварин, с/г машини повинні пройти технологічне миття і очищення робочих органів.
Випадання радіоактивних речовин, надмірне внесення міндобрив, пестицидів, не обеззараженого гною, димові викиди в атмосферу сірки, азоту і інших важких металів приведе до забруднення рослинного світу, який є основним кормом для тварин. Попадання в організм тварин таких речовин суттєво впливає на їх здоров’я, продуктивність і якість продукції. Тому, корми при вирощуванні, заготівлі, зберіганні і транспортуванні необхідно піддати різним видам обробки для уникнення захворювань при згодовуванні їх в забрудненому вигляді.
При завантажені транспортера ТК-5Б слідкують, щоб коренеплоди не мали сторонніх механічних домішок, щоб вони не були гнилі і плісняві. Перед згодовуванням коренеплоди піддати хіміко-аналітичному випробовуванню проб на вміст нітратів, а також радіоактивному визначенню забрудненості. Перед згодовуванням їх миють і подрібнюють в кількості не більше ніж на одну годівлю, тому що подрібнені вони швидко псуються, чорніють і забруднюються.
Солома при закладці в скирту також повинна піддаватися аналізу на вміст нітратів і радіоактивного забруднення. Вміст їх добовому раціоні не повинні перевищувати ГДК. При виявлені в соломі доз вищих за допустимі норми, її згодовують тваринам разом з доброякісними кормами. При розрахунку об'єму годівлі кормів добова доза нітратів в раціоні повинна бути не вищою 0,2 кг ваги тварини.
Перед згодовуванням силосу слідкують, щоб не було гнилого, ураженого грибком і іншими токсинами, з високим вмістом вільного окису азоту і аміаку. При приготуванні концентровані корми повинні провірятися на вміст отруйних і токсичних речовин, грибків, паразитів. Вони очищаються від сторонніх предметів просіюванням через сито з подальшим перепусканням через електромагнітну установку.
В кормоцеху і на території, яка прилягає, необхідно систематично прибирати відходи і залишки корму, проводити відповідні заходи по боротьбі з гризунами, а в літній час обробляти різними аерозольними препаратами проти мух. Необхідно проводити дезинфекцію силосних ям, складських приміщень. Для цього використовують 2% розчин хлораміну. Для дезинфекції бункерів, транспортерів, машин і обладнання приготування кормової суміші використовують 0,5% розчин хлораміну або гарячий розчин дезмолу в такій же концентрації по мірі забрудненості але не менше одного разу в місяць. Тому дотримання всіх вищесказаних вимог до кормів і обладнання дасть змогу виробляти екологічно чисту продукцію.
4.2 Аналіз небезпечних і шкідливих факторів при виконанні виробничих процесів в кормоцеху
Міри по охороні праці на с/г підприємствах проводяться відповідно з «Положенням про працю по охороні та техніці безпеки в колгоспах на підприємствах, в організаціях системи агропромислового комплексу України».
За охорону праці і техніку безпеки в господарстві відповідає керівник підприємства, інженер з техніки безпеки, головний зоотехнік, завідуючий фермою.
Небезпечні та шкідливі фактори поділяються по їх природі впливу на організм людини, на фізичні, хімічні та психофізіологічні фактори (по ГОСТ 120.003−74).
До фізичних факторів відносяться машини і механізми, що знаходяться в русі, рухомі частини виробничого обладнання, матеріали, що перебувають в русі, підвищена чи понижена температура поверховостей обладнання, матеріалів, робочої зони, вологості повітря, швидкості руху повітря (особливо це буває в цехах при приготуванні кормових сумішей), підвищення напруги в електричному колі, що являється однією з причин нещасних випадків. Також одними з фізичних факторів є відсутність або недостатність освітлення або різкий контраст освітлення робочої зони. До травм також приводять гострі частини обладнання, машин.
Під час приготування кормів в кормоцеху, при завантажені концкормів, грубих кормів, соломи, сіна і подальшій їх переробці та змішувані виділяється велика кількість пилу, що шкідливо діє на організм людини. Також це має місце при вивантаженні готової кормосуміші в кормороздавач КТУ-10А.
В процесі приготування кормосуміші виникає багато шуму і вібрації, що також шкідливо для здоров’я людини. Особливо велике число травм відбувається в процесі завантаження, транспортування і розвантаження кормів, якщо ці роботи виконуються вручну. Основні умови безпечної роботи — це правильна організація робіт, а також дотримання вимог техніки безпеки.
Також однією з причин травм в процесі кормоприготування в цеху є те, що площадки робочих місць знаходиться на деякій висоті, що і є одним із небезпечних факторів, що приводять до травм. Також можна виділити і можливий захват одягу відкритими передачами, які приводять в рух машини. Щоб уникнути травм на виробництві потрібно дотримуватися слідуючи правил:
— передачі повинні мати захисні кожухи;
— обслуговуючий персонал, що працює в цеху, повинен мати спец одяг;
— робочі місця повинні бути обладнані, сухі і справні;
Хімічні фактори по характеру дії на організм людини поділяються на:
— загальнотоксичні (отруєння всього організму);
— роздратовуючі і ті, що викликають подразнення дихального тракту і слизистих оболонок.
По шляху проникнення в організм людини ці фактори поділяються на проникаючі через органи дихання; харчовий канал; шкірне покриття та слизисту оболонку. Для того, щоб дія цих факторів була якомога меншою обслуговуючому персоналу видається спеціальний одяг, який повинен дезінфікуватися. Для вентиляції кормоцеху повинен постійно працювати вентилятори системи витяжної вентиляції.
До роботи в кормоцеху допускаються особи віком не молодші 17 років, ознайомлені з даним обладнанням і машинами, які знають правила техніки безпеки і проінструктовані на робочому місці.
Хронічно професійні отруєння — це результат тривалої дії шкідливих факторів виробництва. Тривале вдихання повітря з підвищеним вмістом пилу викликає хронічне захворювання верхніх дихальних шляхів або легенів. Для зменшення дії цих факторів, робітники кормоцеху застосовують респіратори. Тривала дія вібрації на організм людини в сполучені з переохолодженням приводять до віброхвороби. Санітарно-гігієнічні причини нещасних випадків — це результат порушення гігієни праці, санітарних норм і правил, незадовільне освітлення, підвищена вологість повітря, інтенсивний шум, загазованість і запиленість повітря.
Одним з найбільш небезпечних факторів при виконанні виробничих процесів може бути пожежа. Причини виникнення пожежі:
— неправильне планове розміщення споруд, складів без вираховування необхідних розривів, направлення вітрів і розміщення категорії виробництва по пожежній небезпеці технологічного процесу;
— неправильний монтаж електричної сітки, обладнання, освітлювальних пристроїв, електродвигунів і порушення правил їх експлуатації;
— самозапалювання сіна, соломи, трав’яної маси внаслідок неправильного їх зберігання і невчасної переробки;
— не дотримування правил пожежної безпеки при користуванні відкритим вогнем, а також при курінні;
— попадання блискавки при грозі.
Для захисту від шкідливих і небезпечних дій обслуговуючого персоналу кормоцеху, видають індивідуальні захисні засоби.
Робочі органи приймальних механізмів мають властивість забиватися, для цього кормоцехи забезпечують механізмами автоматичного виключення або запобіжними засобами (муфти) і автоматичною сигналізацією (звуковою і світловою). При попаданні в апарат сторонніх предметів, спрацьовує замковий пристрій, який заблоковує кінцеве включення. Крім запобіжних заходів привід приймальних механізмів повинен бути забезпечений реверсом.
Для передбачення опіків обслуговуючого персоналу, всі роботи по запарюванню грубих кормів та іншому використанню пари виконують в спеціальному одязі і окулярах.
5. Техніко-економічне обґрунтування
Для забезпечення високого ступеня надійності подрібнювача передбачено проведення його технічного обслуговування № 1 і ТО 2. Періодичне ТО виконується 2 рази в рік (при переходах на зимовий і літній періоди). ТО № 1 потрібно виконувати через 75−90 год технологічного наробітку (1−2 рази на місяць), залежно від марки машини, характеру її використання завантаження та умов праці. ТО 2 через 270−300 годин технологічного наробітку, що може збігатися з сезонним технічним обслуговуванням. При щоденному ТО необхідно вичищати подрібнювач від залишків корму, болота і пилу (при виключеному електродвигуну).
При ТО 1, крім операцій при щоденному ТО, необхідно проводити перевірку змазки в підшипниках. Перевіряти і ліквідувати можливі поломки в електричному обладнані, проводити регулювання клинопасової передачі.
При ТО 2, крім операцій проведених ТО і ТО 1, необхідно проводити очищення скребків з ціллю ліквідації прилиплого шару корму, проводити заміну змазки в підшипниках, окраси місця оголені від фарби. При періодичному ТО крім операцій передбачених щоденним ТО, ТО 1 і ТО 2 необхідно виконувати розбирання подрібнювача, ліквідувати виявлені дефекти, при необхідності замінити підшипники і паси. Провірити опір заземлюю чого контуру і стан пускового приладу.
Для подрібнювача коренеплодів визначаємо слідуючи показники: витрати на виготовлення або модернізацію машини, річну економію від зниження собівартості продукції за рахунок впровадження удосконалення машини, строк окупності, економію витрат праці.
Витрати на виготовлення або удосконалення машини визначають по формулі:
(5.1)
де Сс — вартість виготовлення станини, грн.;
Сдм — витрати на виготовлення деталей на металоріжучих станках, грн.;
Спц — ціна покупних виробів по прейскуранту, грн.;
Ссб — заробітна плата працівників на збиранні конструкції, грн.;
Сцм — цехові накладні витрати на виготовлення або удосконалення машини, грн.
Вартість виготовлення станин визначається по формулі:
(5.2)
де Qс — маса матеріалу, витрачена на виготовлення станини, грн.;
Ссд — середня вартість 1 кг готових деталей, грн.
Маса матеріалу визначається по формулі:
(5.3)
де Qg — чиста маса деталі, Qg = 28 кг;
А і п — коефіцієнти, які залежать від виду матеріалу деталі, способу її виготовлення, наявність механічної обробки і іншого.
А = 1,49п = 0,95
Витрати на виготовлення деталей на метало ріжучих станках розраховуємо по формулі:
(5.4)
де Км — коефіцієнт, враховуючий масштаб виробництва, Км = 2,2;
Коб — коефіцієнт, враховуючий найбільшу точність обробітку деталей, Коб = 1,2;
К1 — коефіцієнт, враховуючий найбільший клас чистоти поверхні,
К1 = 0,95;
п — число однотипних деталей, п = 1;
G — погодинна зарплата працівників, нарахована по середньому розряду, G = 1,6 грн;
tв — середня трудомісткість виготовлення деталей, tв = 2 год;
С1 — ціна 1 кг матеріалу заготовки, С1 = 6,5 грн.
Заробітну плату працівників зайнятих на збирані машин вираховуємо по формулі:
(5.5)
де К — коефіцієнт, враховуючий витрати до основної заробітної плати, К = 1,03;
Кс — коефіцієнт, враховуючий оцінку між повним і оперативним збиранням, Кс = 1,08;
tсб — трудоємкість збирання окремих елементів конструкції, tсб = 6,8;
R — коефіцієнт, враховуючий конструктивні особливості виробу і його елементи, R = 1,5.
Цехові накладні витрати на виготовлення або удосконалення машини розраховуються по формулі:
(5.6)
де С1прр - заробітна праця виробничих працівників з розрахунком додаткової доплати Сдо і нарахувань по державному страхуванню Ссп; грн.
R — загальногосподарські накладні витрати підприємства, R = 28%.
Заробітну плату виробничих працівників визначаємо за формулою:
(5.7)
де Спр — основна заробітна плата виробничих працівників, Основна заробітна плата визначається по формулі:
(5.8)
де См — заробітна плата виробничих працівників, зайнятих на метало ріжучих станках, грн.;
Ссб — ЗП виробничих працівників, зайнятих на збиранні машин, грн.;
Визначаємо вартість покупних запчастин по фермі:
(5.9)
де Спод — вартість двох підшипників, Спод = 8,80 грн.
Селен.дв — вартість електродвигуна, Селен.дв = 120 грн.
Спас — вартість пасів, Спас = 24 грн.
Сболт — вартість болтів, Сболт = 4,4 грн.
Таким чином, щоб виготовити подрібнювач коренеплодів в металі (в умовах господарства) необхідно затратити 669 грн.
Література
1. Брагинец Н. В., Палишкин Д. А. Курсовое и дипломное проектирование по механизации животноводства. — М.: Колос, 1984. — 164 с.
2. Колесник А. А., Шаманский В. Г. Курсовое и дипломное проектирование. — М.: Колос, 1983.
3. Мельников С. В. Механизация и автоматизация животноводческих ферм и комплексов.- Л.: Колос, 1978.
4. Погорелый Л. В., Рожков В. Г. Мечта Н.П. Снижение затрат ручного труда в животноводстве.- К.: Урожай, 1987. 195 с.
5. Трончук И. С., Фесина Б. Е., Почерняева Г. М. и др. Кормление свиней. — М.: Агропромиздат, 1990. — 175 с.
6. Козловский В. Г. Организация и технология производства свинины. — М.: Колос, 1978.
7. Хохрин С. Н. Кормление свиней.- М.: Колос, 1982. — 104 с.
8. Козловский В. Г., Ладан П. Е. и др. Свиноводство.- М.: Колос, 1984.
9. Коваленко В. Ф., Кисельов Є.П. Відтворення поголів'я у промисловому свинарстві. — К.: Урожай, 1979. 136 с.
10. Зайцев В. П., Свердлов М. С. Охрана труда в животноводстве. — М.: Колос, 1984.
11. Арзуманян Е. А. Животноводство. — М.: Агропромиздат, 1985. — 448 с.
12. Вольтов М. М. и др. Охрана труда в сельском хозяйстве. Справочник. — М.: Колос, 1985.
13. Гайовий О.Є. Куксенюк П. Н., Шевченко В.І. Охорона праці у сільському господарстві. Збірник нормативних актів. — К.: Видавництво «Варта», 1996. — 590 с.
14. Канарев Ф. М. и др. Охрана труда. — М.: Колос, 1982.
15. Карташов Л. П. Механизация и электрификация животноводства. — М.:
Агропромиздат, 1987.
16. Кукта Г. М. и др. Механизация и автоматизация животноводства. — Киев: Вища школа, 1990.
17. Ревенко І.І. Посібник-практикум з механізації виробництва продукції тваринництва. — Київ: Урожай, 1994.
18. Анурьев В. И. Справочник конструктора-машиностроителя. Т.3. — М.: Машиностроение, 1982.
19. Кузьмин А. В. Расчеты деталей машин. — Минск: Вышейшая школа, 1986.
Головин В.Т., Скворцов Е. А., Никитин Е. А. Методические указания по экономическому обоснованию конструктивных разработок машин, узлов и агрегатов. — Луганск: ЛНАУ, 2004. — 10 с.
20. Кириченко В. Е., Брагинец Н. В., Вольвак С. Ф., Пермигин М. Ф., Фесенко А. В. Методические рекомендации по оформлению курсовых и дипломных проектов (работ) по специальности 8.91 902 «Механизация сельского хозяйства».- Луганск: Издательство ЛНАУ, 2005. 43 с.
21. Троянов М. М. Механізація технологічних процесів у тваринництві. — Харків.: Прапор, 1993.-140 с.
22. Теорія та розрахунок машин для тваринництва / І.Г. Бойко, В.І. Грідасов, А.І. Дзюба та ін.; За ред. І.Г. Бойко. — Х.: НМЦ ХНТУСГ, 2002. — 216 с.
23. Практикум по машинах і обладнанню для тваринництва / І.Г. Бойко, В.І. Грідасов, А.І. Дзюба та ін.; За ред. О. П. Скорик, О.І. Фісячекнко. — Х.: НМЦ ХНТУСГ, 2004. — 275 с.
24. Курсове та дипломне проектування по механізації тваринницьких ферм / І.Г. Бойко, В.І. Грідасов, А.І. Дзюба та ін.; За ред. О. В. Нанки. — Х.: НМЦ ХНТУСГ, 2003. — 356 с.
25. Машини та обладнання для тваринництва /І.Г. Бойко, В.І. Грідасов, А.І. Дзюба та ін.; За ред. І.Г. Бойко. — Х.: НМЦ ХНТУСГ, 2006. — 625 с.