Електрометалургія
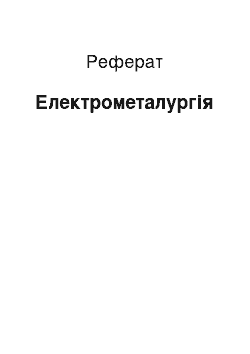
Электрододержатели служать для підвода струму до електродах й у затискача електродів. Голівки электрододер-жателей роблять із бронзи чи сталі та охолоджують водою, оскільки вони сильно нагріваються як теплом з печі, і контактними струмами. Электрододержатель повинен щільно затискати електрод і мати невеличке контактне опір. Найпоширенішим в час є пружинно-пневматический электрододержатель. Затиск… Читати ще >
Електрометалургія (реферат, курсова, диплом, контрольна)
Виробництво сталі в електричних печах.
У электоропечи можна одержувати легированную сталь з низьким змістом сірки і фосфору, неметалевих включень, у своїй втрати легуючих елементів значно менше. У процесі электроплавки не складно регулювати температуру металу та її склад, виплавляти сплави майже кожного состава.
Електричні печі мають суттєвими перевагами по порівнянню коїться з іншими сталеплавильными агрегатами, тому высоколегированные інструментальні сплави, нержавіючі шарикоподшипниковые, жаростойкие і жароміцні, і навіть багато конструкційні стали виплавляють лише у цих печах.
Потужні електропечі успішно застосовують щоб одержати низьколегованих і высокоуглеродистых сталей мартенівського сортаменту. З іншого боку, в електропечах одержують різноманітні феросплави, які становлять сплави заліза із елементами, які потрібно виводити в сталь для легування і раскисления.
Пристрій дугових электропечей.
Перша дуговая електропіч у Росії встановили 1910 р. на Обухівському заводі. Упродовж років п’ятирічок було побудовано сотні різних печей. Місткість найбільш великої печі у СРСР 200 т. Піч складається з залізного кожуха циліндричною форми зі сферичним днищем. Усередині кожух має огнеупорную футеровку. Плавильне простір печі закривається знімним склепінням. Піч має робоче вікно і випускне отвір зі зливним жолобом. Харчування печі здійснюється трифазним змінним струмом. Нагрівання і плавлення металу здійснюються електричними потужними дугами, палаючими між кінцями трьох електродів і металом, які у печі. Піч спирається на два опорних сектора, перекатывающихся по станині. Нахил печі убік випуску і робочого вікна здійснюється за допомогою реечного механізму. Перед загрузклй печі звід, підвішений на ланцюгах, піднімають до порталу, потім портал зі склепінням і електродами відвертається убік зливального жолоби і піч завантажують бадьей.
Механічне устаткування дугового печи.
Кожух печі повинен відповідати навантаження від безлічі вогнетривів і металу. Його роблять сварным з листового заліза завтовшки 16−50 мм залежно від розмірів печі. Форма кожуха визначає профіль робочого простору дугового електропечі. Найпоширенішим нині є кожух конічну форму. Нижня частина кожуха має форму циліндра, верхня часть—конусообразная з розширенням догори. Така форма кожуха полегшує заправку печі огнеупорным матеріалом, похилі стіни збільшують стійкість кладки, оскільки він далі розташована від електричних дуг. Використовують також кожухи циліндричною форми з водоохлаждаемыми панелями. Для збереження правильної циліндричною форми кожух посилюється ребрами і кільцями жорсткості. Днище кожуха зазвичай виконується сферичним, що забезпечує найбільшу міцність кожуха і мінімальну масу кладки. Днище виконують з немагнитной стали для установки під піччю електромагнітного перемешивающего устройства.
Згори піч закрита склепінням. Звід набирають з вогнетривкої цегли в металевому водоохлаждаемом сводовом кільці, яке витримує распирающие зусилля аркового сферичного зводу У частині кільця є виступ — ніж, що входить у піщаний затвор кожуха печі. У цегельною кладці зводу залишають три отвори для електродів. Діаметр отворів більше діаметра електрода, під час плавки в зазор кидаються гарячі гази, що руйнують електрод і виносять тепло з печі. Щоб запобігти цього зведенні встановлюють холодильники чи экономайзеры, службовці для ущільнення электродных отворів й у охолодження кладки зводу. Газодинамические экономайзеры забезпечують ущільнення з допомогою повітряної завіси навколо електрода. У зведенні є також отвір для отсоса запилених газів і отвір для кисневою фурмы.
Для завантаження шихти в печі невеличкий ємності і подгрузки легуючих і флюсів в великі, печі скачування шлаку, огляду, заправки і ремонту печі є загрузочное вікно, й із литої рамою. До рамі кріпляться направляючі, якими ковзає заслінка. Заслінку футеруют огнеупорным цеглою. Для підйому заслінки використовують пневматичний, гідравлічний чи електромеханічний привод.
Із протилежного боку кожух має вікно для випуску сталі з печі. До вікна приварений зливальний жолоб. Отвір для випуску стали то, можливо круглим діаметром 120—150 мм чи квадратним 150 на 250 мм. Зливальний жолоб має корытообразное перетин і приварений до кожуху з точки 10—12° до горизонталі. Зсередини жолоб футеруют шамотным цеглою, довжина його становить 1—2 м.
Электрододержатели служать для підвода струму до електродах й у затискача електродів. Голівки электрододер-жателей роблять із бронзи чи сталі та охолоджують водою, оскільки вони сильно нагріваються як теплом з печі, і контактними струмами. Электрододержатель повинен щільно затискати електрод і мати невеличке контактне опір. Найпоширенішим в час є пружинно-пневматический электрододержатель. Затиск електрода здійснюється за допомогою нерухомого кільця і зажимной плити, яка притискається до электроду пружиною. Ог-жатие плити від електрода і стиснення пружини відбуваються з допомогою стиснутого повітря. Электрододержатель кріпиться на металевому рукаві - консолі, який скріплюється з Робразною рухомий стійкою до однієї жорстку конструкцію. Стойка може переміщатися вгору чи вниз всередині нерухомій коробчатой стійки. Три нерухомі стійки жорстко пов’язані до однієї загальну конструкцію, яка спочиває на платформі опорною колиски печі. Переміщення рухливих телескопічних стійкий відбувається чи з допомогою системи тросів і противаг, наведених у рух електродвигунами, чи з допомогою гідравлічних пристроїв. Механізми переміщення електродів повинні забезпечити швидке піднесення електродів у разі обвалу шихти у процесі плавлення, і навіть плавне опускання електродів щоб уникнути їх занурення на метал чи ударів про нерасплавившиеся шматки шихти. Швидкість підйому електродів становить 2,5—6,0 м/мин, швидкість опускання 1,0— 2,0 м/мин.
Механізм нахилу печі повинен плавно нахиляти піч убік випускного отвори на кут 40—45° для випуску сталі та на кут 10—15 градусів убік робочого вікна для спуску шлаку. Житло печі, чи колиска, де встановлено корпус, спирається на два — чотири опорних сектора, які перекочуються по горизонтальним котрі спрямовують. У секторах є отвори, а направляють — зубці, з яких запобігається проскальзывание секторів при нахилі печі. Нахил печі здійснюється за допомогою рейки і зубчастого механізму, чи гідравлічною приводом. Два циліндра укріплені на нерухомих опорах фундаменту, а штоки шарнірно пов’язані з опорними секторами колиски печи.
Система завантаження печі буває два види: через завалочное вікно мульдозавалочной машиною і крізь гору з допомогою цебра. Завантаження з вікна застосовують лише з невеликих печах.
При завантаженні печі згори в один-два приєднання до протягом 5 хв менше охолоджується підбійка, скорочується час плавки; зменшується витрата електроенергії; ефективніше використовується обсяг печі. Для завантаження печі звід піднімають на 150—200 мм над кожухом печі і повертають убік разом з електродами, повністю відкриваючи робоче простір печі запровадження цебра з шихтою. Звід печі підвішений до рами. Вона з'єднана з нерухомими прилавками электрододержателей до однієї жорстку конструкцію, спочиваючу на поворотною консолі, яка укріплена на опорному подшипнике. Великі печі мають поворотну вежу, у якій зосереджено все механізми одворота зводу. Вежа обертається навколо шарніра на катках по дугообразному рейку. Баддя є сталевої циліндр, діаметр якого менше діаметра робочого простору печі. Знизу циліндра є рухливі гнучкі сектора, кінці яких стягуються через кільця тросом. Зважування і завантаження шихти виробляються на шихтовом дворі електросталеплавильного цеху. Баддя на візку подається до цеху, піднімається краном і опускається в піч. З допомогою допоміжного підйому крана трос висмикують з проушин секторів і за підйомі цебра сектора розкриваються і шихта вивалюється в піч у порядку, у якому вона була покладена в бадье.
З використанням як шихти металлизован-ных котунів завантаження може здійснюватися безперервно за трубопроводу, який проходить отвір в зведенні печи.
Під час плавлення електроди прорізають в шихті три колодязя, дно якої яких накопичується рідкий метал. Для прискорення розплавлювання печі обладнуються поворотним пристроєм, яке повертає корпус в інший бік на кут в 80°. У цьому електроди прорізають в шихті вже дев’ять криниць. Для повороту корпусу піднімають звід, піднімають електроди вище рівня шихти і повертають корпус з допомогою зубчастого віденця, прикріпленого до корпусу, і шестерні. Корпус печі спирається на ролики.
Очищення відведених газов.
Сучасні великі сталеплавильні дугові печі під час роботи виділяють у повітря дуже багато запилених газів. Застосування кисню і порошкоподібних матеріалів ще більше сприяє цьому. Зміст пилу в газах электродуговых печей сягає 10 г/м3 і значно стає більше норми. Для уловлювання пилу виробляють отсос газів з робочого простору печей потужним вентилятором. І тому в зведенні печі роблять четверте отвір з патрубком для газоотсоса. Патрубок через зазор, дозволяє нахиляти чи крутити піч, наближається до стаціонарному трубопроводу. Дорогою гази розбавлено повітрям, необхідним дожигания ЗІ. Потім гази розладнуються водяними форсунками в теплообменнике і направляють у систему труб Вентури, у яких пил затримується в результаті зволоження. Застосовують також тканинні фільтри, дезінтегратори і электрофильтры. Використовують системи газоочистки, які включають цілком усю електросталеплавильний цех, із установкою парасоль дымоотсоса під дахом цеху над электропечами.
Підбійка печей. Більшість дугових печей має основну футеровку, що складається з матеріалів з урахуванням MgO. Підбійка печі створює ванну для металу і відіграє роль теплоизолирующего шару, уменьшающего втрати тепла. Основні частини футерівки — подина печі, стіни, звід. Температура у зоні електричних дуг сягає тисяч градусів. Хоча підбійка електропечі відділена дуг, вона все-таки має витримувати нагрівання до температури 1700 °C. У зв’язку з цим застосовувані для футерівки матеріали повинні мати високої огнеупорностью, механічної міцністю, термота хімічної сталістю. Подину сталеплавильної печі набирають у порядку. На сталевої кожух вкладають листовий азбест, на асбест—слой шамотного порошку, два шару шамотного цегли і основний шар із магнезитового цегли. На магнезитовой цегельною подине набивають робочий шар із магнезитового порошку зі смолою і пеком — продуктом нафтопереробки. Товщина набивного шару становить 200 мм. Загальна товщина подины дорівнює приблизно глибині ванни і може становити 1 м значних печей. Стіни печі викладають після відповідної прокладки азбесту і шамотного цегли з крупноразмерного безобжигового магнезитохромитового цегли довжиною до 430 мм. Кладка стін може виконуватися з цеглин в залізних касетах, що забезпечують зварювання цеглин до одного монолітний блок. Стійкість стін сягає 100—150 плавок. Стійкість подины становить рік-два. У складних умовах працює підбійка зводу печі. Вона витримує великі теплові навантаження від запалених дуг і тепла, відбиваного шлаком. Склепіння великих печей набирають з магнезитохромитового цегли. Набираючи зводу використовують нормальний і фасонный цегла. У поперечному сечении звід має форму арки, що забезпечує щільне зчеплення цеглин між собою. Стійкість зводу становить 50 — 100 плавок. Вона залежить від електричного режиму плавки, від тривалості перебування у печі рідкого металу, складу виплавлюваних стали, шлаку. Нині стала вельми поширеною отримують водоохлаждаемые склепіння і стеновые панелі. Ці елементи полегшують службу футеровки.
Струм в плавильне простір печі подається через електроди, зібрані з секцій, кожна з яких є круглу заготівлю діаметром від 100 до 610 мм довжиною до 1500 мм. У малих електропечах використовують вугільні електроди, у крупних — графитированные. Графитированные електроди виготовляються з малозольных вуглецевих матеріалів: нафтового коксу, смоли, пеки. Электродную масу змішують і пресують, після чого сира заготівля обпікається в газових печах при 1300 градусах зазнає додатковому графитирующему випалу за нормальної температури 2600 — 2800 градусах в електричних печах опору. У процесі експлуатацію у результаті окислення грубними газами і розпорошення при горінні дуги електроди згоряють. Принаймні укорочування електрод опускають в піч. У цьому электрододержатель наближається до склепіння. Однак настає час, коли електрод стає таким коротким, і що може підтримувати дугу, і його треба нарощувати. Для нарощування електродів в кінцях секцій зроблено отвори різьблені, куди угвинчується переходник-ниппель, з якого з'єднуються окремі секції. Витрата електродів становить 5—9 кг на тонну виплавленої стали.
Електрична дуга—один з видів електричного розряду, у якому струм проходить через іонізовані гази, пари металів. При короткочасному зближення електродів з шихтою чи друг з одним виникає короткий замикання. Йде струм великий сили. Кінці електродів розжарюються до краю. При раздвигании електродів з-поміж них виникає електрична дуга. З розпеченого катода відбувається термоэлектронная емісія електронів, які, прямуючи до аноду, зіштовхуються з нейтральними молекулами газу та ионизируют їх. Негативні іони направляються до аноду, позитивні до катоду. Простір між анодом і катодом стає ионизированным, токопроводящим. Бомбардування анода електронами і іонами викликає сильний його розігрів. Температура анода може становити 4000 градусів. Дуга може горіти постійному і перемінному струмі. Электродуговые печі працюють на перемінному струмі. Останнім часом до ФРН побудована электродуговая піч на постійному токе.
У перший половину періоду, коли катодом є електрод, дуга горить. При зміні полярності, коли катодом стає шихта — метал, дуга гасне, позаяк у початковий період плавки метал ще нагріте та її температура недостатня для емісії електронів. Тож у початковий період плавки дуга горить неспокійно, переривчасто. Коли ванна покривається шаром шлаку, дуга стабілізується і горить більш ровно.
Электрооборудование.
Робоча напруга электродуговых печей становить 100 — 800 У, а сила струму вимірюється десятками тисяч ампер. Потужність окремої установки може досягати 50 — 140 МВ*А. До підстанції електросталеплавильного цеху подають струм напругою до 110 кВ. Високим напругою харчуються первинні обмотки пічних трансформаторів. На показано спрощена схема електричного харчування печі. У електричне устаткування дугового печі входять виробництва ремонтних робіт на печі. такі приборы:
1. Повітряний роз'єднувач, призначений для відключення всієї электропечной установки від лінії високої напруги у время.
2. Головний автоматичний вимикач, служить для відключення під навантаженням електричної ланцюга, через яку протікає струм високої напруги. При нещільної укладанні шихти в печі на початку плавки, коли шихта ще холодна, дуги горять хитливо, відбуваються обва лы шихти і виникають короткі замикання між електродами. У цьому сі ла струму різко зростає. Це спричиняє великим перевантажень трансформатора, котрі можуть вийти з ладу. Коли сила струму перевищить встановлений межа, вимикач авто матически відключає установку, навіщо є реле максимальної сили тока.
3. Пічний трансформатор необхідний перетворення високого напруги в низька (з 6—10 кВ до 100—800 У). Обмотки високої професійності і низького напруження і магнитопроводы, де вони можна побачити, містяться у баці з олією, службовцям для охолодження обмоток. Охолодження створюється примусовим перекачуванням олії з трансформаторного кожуха в бак теплообмінника, у якому олію охолоджується водою. Трансформатор встановлюють поруч із электропечью у спеціальній приміщенні. Вона має пристрій, що дозволяє переключати обмотки сходами отже східчасто регулювати подаване в піч напруга. Приміром, трансформатор для 200-т вітчизняної печі потужністю 65 МВ*А має 23 щаблі напруги, які переключаються під навантаженням, без відключення печи.
Ділянка електричної мережі від трансформатора до електродів називається короткій мережею. Виходять з стіни трансформаторній підстанції фідери при допомоги гнучких, водоохлаждаемых кабелів подають напруга на электрододержатель. Довжина гнучкого ділянки повинна дозволяти виробляти потрібний нахил печі і відвертати звід для завантаження. Гнучкі кабелі поєднано з аналітичними мідними водоохлаждаемыми шинами, встановленими на рукавах электрододержателей. Трубошины безпосередньо приєднано до голівці электрододер-жателя, зажимающей електрод. Крім зазначених основних вузлів електричної мережі у ній входить різна вимірювальна апаратура, подсоединяемая до лініях струму через трансформатори струму чи напруги, а також прилади автоматичного регулювання процесу плавки.
Автоматичне регулирование.
Під час плавлення в електродугову піч потрібно подавати різне кількість енергії. Змінювати подачу потужності можна зміною напруги чи сили струму дуги. Регулювання напруги виробляється переключенням обмоток трансформатора. Регулювання сили струму здійснюється зміною відстані між електродом і шихтою шляхом підйому чи опускання електродів. У цьому напруга дуги не змінюється. Опускання чи підйом електродів виробляються автоматично з допомогою автоматичних регуляторів, встановлених з кожної фазі печі. У середовищі сучасних печах задана програма електричного режиму може бути встановлена все період плавки.
Пристрій для електромагнітного перемішування металла.
Для перемішування металу у великих дугових печах, з метою прискорення і полегшення проведення технологічних операцій скачування шлаку під днищем печі в коробці встановлюється електрична обмотка, яка охолоджується водою чи стиснутим повітрям. Обмотки статора харчуються від двухфазного генератора струмом низькою частоти, що створює який біжить магнітне полі, яке захоплює ванну рідкого металу і рух нижніх верств металу вздовж подины печі у бік руху поля. Верхні верстви металу разом із прилеглим щодо нього шлаком рухаються у бік. Таким чином можна направити рух або у бік робочого вікна, що полегшувати вихід шлаку з печі, або у бік зливального отвори, що сприяти рівномірному розподілу легуючих і розкислювачів і усреднению складу металу та її температури. Цей метод останнім часом має обмежений застосування, позаяк у надпотужних печах метал активно перемішується дугами.
Плавка сталі у основний дугового электропечи.
Сирі материалы.
Основним матеріалом для электроплавки є сталевої брухт. Лом не може бути сильно окисленным, оскільки наявність великої кількості іржі вносить в сталь значну кількість водню. Залежно від хімічного складу брухт необхідно розсортувати на відповідні групи. Основне кількість брухту, призначене для плавки в електропечах, має бути компактним і великоваговим. При малої насипний масі брухту вся порція для плавки не міститься у піч. Доводиться переривати процес плавки і довантажувати шихту. Це збільшує тривалість плавки, призводить до підвищеному витраті електроенергії, знижує продуктивність електропечей. Останнім часом в електропечах використовують металлизованные котуни, отримані методом прямого відновлення. Перевагою цього виду сировини, що містить 85— 93% заліза, і те, що його не забруднене міддю та інші домішками. Котуни доцільно застосовувати для виплавки высо-копрочных конструкційних легованих сталей, електротехнічних, шарикоподшипниковых сталей.
Леговані відходи утворюються у электросталеплавильном цеху як недолитых зливків, литников; в обдирочном відділенні як стружки, в прокатних цехах як обрези і шлюби й т, буд.; ще багато легованого брухту йде від машинобудівних заводів. Використання легованих металлоотходов дозволяє заощаджувати цінні легирующие, підвищує економічну ефективність электроплавок.
М’яка залізо спеціально виплавляють в мартенівських печах і конвертерах і застосовують для регулювання змісту вуглецю у процесі электроплавки. У залозі міститься 0,01—0,15% З повагою та.