Очищення нафтопродуктів
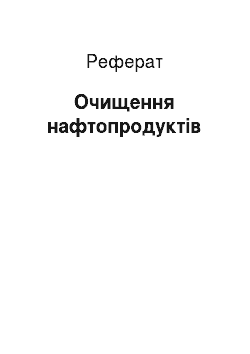
Технічні гази після устоновок прямої перегонки нафти, термічного і каталітичного крекінгу, коксування вміщують H2S у значній кількості. Особливо багато H2S у газах установок гідроочистки, де з органічних сірковміщуючих сполук створюється H2S. За вимогами технології і екологічної безпекивиробництв такі гази потребують очистки чи перед їх переробкою, чи перед викидом у атмосферу. Вміст H2Sу… Читати ще >
Очищення нафтопродуктів (реферат, курсова, диплом, контрольна)
Реферат на тему:
Очищення нафтопродуктів Для очищення нафтопродуктів (рідин та газів) використовують різні методи: хімічні, адсорбційні, абсорбційні, каталітичні та екстракційні.
Основні технологічні процеси:
— лугова промивка дистилятів первинної перегонки з метою очищення від кислих компонентів (нафтенові кислоти, H2S);
— очищення газів від S у вигляді H2S та RSH розчинами луги, різних поглотителей та за допомогою адсорбентів;
— очищення рідини від H2S та RSH методами лугового очищення з участю кисня, так називаєма окислювальна демеркаптанізація, чи за допомогою Н2-гідрогенізаційне очищення (гідроочищення);
— депарафінізація з метою виділення рідинних чи твердих парафінів;
— деасфальтизація-екстракційне очищення продуктів від асфальтенів;
— очищення продуктів від ароматичних сполук сірчанокислотними методами;
— очищення продуктів від ненасичених сполук хімічними та адсорційними методами.
У виробництві мастил використовують комбінований метод, який об'єднує екстракційний, адсорбційний та гідрогенізаційний засоби.
Очищення нафтопродуктів розчинами лугів Реакції лугового очищення Лугове очищення (залуговування) здійснюється з метою очищення дистилятних нафтопродуктів (бензин, керосин) від кислих продуктів, фенолів, сірководня та низших меркаптанів.
Кислоти, які вміщують нафтовий дистилят, реагують з лугою та дають солі, котрі майже повністю переходять у водяний розчин.
RCOOH + NaOH RCOONa + H2O.
Частина солей затримується у нафтопродукті, їх відділяють водяною промивкою, після промивки розчином луги.
Феноли перетворюються у феноляти, котрі також краще розчиняються у воді, ніж у нафтопродуктах.
ОН ONa.
R + NaOH R +H2O.
Обидві реакції рівноважні, в обмеженному напрямку йдуть реакції гідролізу. Ступень гідролізу залежить від температури-збільшується з підвищенням температури та зменшується з підвищенням концентрації луги. Тому очищення краще проводити при менших температурах, використовуючи концентріровані розчини луги. Але у таких умовах створюються стійкі емульсії типа «кисле масло у водяній лугі». Створенню емульсій сприяють продукти нейтралізації-солі нафтенових та сульфакислот, які є емульгаторами. Тому промивку проводять як раз навпаки-при високих температурах з низькоконценрованими розчинами луги.
Сірководень лугою реагують з створенням солей.
H2S + NaOH NaHS + H2O.
меркаптід.
H2S + 2NaOH Na2S + H2O.
Na2S + H2S 2NaHS.
Аналогічно реагують меркаптани. Н-бутілмеркаптан реагує на 35% гірше, ніж етилмеркаптан.
RSH + NaOH RSNa + H2O.
Інші сполуки сірки з лугами не реагують та залишаються без зміни.
Якщо є кисень меркаптіди перетворюються на дісульфіди.
2RSH + O2 RSSR + H2O2.
2RSH + H2O2 RSSR + 2H2O.
4RSH + O2 2RSSR + 2H2O.
Технологія залуговування рідинних нафтопродуктів Лугова промивка (залуговування). Процес проводять по різним схемамодноступов чи у два ступені з циркуліцією розчина луги.
Схема одноступового очищення.
Розчин луги вода очищенний продукт.
(бензин).
(бензин).
розчин промив.
луги відроботанний розчин розчин.
(рецикл).
Основні апарати-ежекторні сумісники та відстойники.
Очищення бензинових фракцій проводять при 40−50та концентрації NaOH до 15%- керосинових фракцій-60−70та 10−12%- дизельних фракцій 80−90та 10%.
В схемах використовують замість ежекторів апарати з мішалками.
Каталітичне лугове очищення бензинів та інших дистилятів (процес Мерокс) очищення топливних дистилятів від меркаптанів проводять у присутності кисня та каталізаторів. Таким чином проводять часткове очищення дистилятів від сірки, бо вдається зменшити вміст сірки за рахунок відділення H2S та нижчих меркаптанів, які дають летючі дісульфіди. Використовують гомогенний каталіз хелатнисполуки металів.
4RSNa + O2 2RSSR + 4NaOH.
Процес проводять у дві стадії. На першій стадії очищення у промивній тарільчатій колоні контактують каталітичний луговий розчин (розчин Мерокс) з сировиною без кисня. У колону другої стадії очистки крім продукту і каталітичного розчину подають повітря. Каталітичний розчин Мерокс знаходиться у циклі і у схемі передбачена його регенерація віддувкою летючих продуктів Процес Бендера використовують для очистки бензинів, реактивних палив від меркаптанів при їх концентрації не більше 0,8−1%.
Реакція з участю кисня йде на гетерогенному каталізаторі-сульфіді свинца при 70−125у присутності розчину луги.
к.
2RSNa + O2 2RSSR + Na OH.
Процес проводять у двох послідовних реакторах з твердим каталізатором. Похідна суміш сировини, розчина луги та повітря зміщується і спрямовується у реактори. Після реакторів реакційна суміш розділяється у газосепараторі і відстойнику.
Лугова очистка газових нафтопродуктів.
Для очистки нафтопродуктів використовують промивку розчином луги. Процес проводять у абсорбційних колонах. При абсорбції з лугою реагують: меркаптани RSH + NaOH RSNa + H2O.
діоксід CO2 + NaOH NaHCO3.
Умови абсорбції підбирають такі, щоб меркаптани перетворювались на 90−95%, а СО2-на 35−38%, бо для повного перетворення СО2 потрібна велика кількість луги.
Технологічні параметри в абсорбційній колоні:
швидкість газу (0,3−0,4м/с концентрація розчину NaOH-початкова 20%.
кінцева 1,5% (вміст соди до 7%).
кількість луги-7−8кратина кількість втрати луги- 1−2кг на 1000 м³.
t (можлива кристалізація) р=1МПа Цей метод можна використовувати при вмісті кислих газів (H2S+CO2)< 0,3%, якщо кислих компонентів більше, економічніші інші методи. У промисловості розчином луги проводять кінцеву очистку газів, наприклад на установках піролізу ЕП-250, ЕП-300.
Очистка технологічних газів від H2S.
Технічні гази після устоновок прямої перегонки нафти, термічного і каталітичного крекінгу, коксування вміщують H2S у значній кількості. Особливо багато H2S у газах установок гідроочистки, де з органічних сірковміщуючих сполук створюється H2S. За вимогами технології і екологічної безпекивиробництв такі гази потребують очистки чи перед їх переробкою, чи перед викидом у атмосферу. Вміст H2Sу технологічних газах установок переробки нафти, спрямовуємих на очистку від 0,1% до 30%.
Промисловий метод глибокої очистки газів від H2S це абсорбція розчинами алканоламінів. В основному, використовують моноетаноламіни (моноетаноламінова очистка-МЕА) чи діетаноламін.
Фізична абсорбція супроводжується хімічною реакцією.
2RNH2 + H2S (RNH3)2S.
(RNH3)2S +H2S 2RNH3HS.
де R-групаСН2СН2ОН Ці рівняння розглядають, як сумарну схему перетворення H2S в сульфіт та бісульфіт. Кінцеві сполуки при нормальних уиовах мають досить помітний тиск насиченого пару, який при нагріванні значно підвищується. Це дає можливість легко десорбирувати H2S і регенерувати розчин моноетаноламіна. В реакціях моноетаноламін реагує за рахунок аміно-групи. Наявність гідроксильної групи впливає на властивості сполук-як полярна група підвищує їх розчинність в воді і збільшує величину тиску насиченого пару.
За рахунок побочних реакцій моноетаноламіна з компонентами газової сімиші (CO2, O2 і інші) створюються побочні продукти, маючи високі температури кипіння. Наприклад, з H2S разом з О2 ствоюється тіосульфат, що не регенерується, як сульфіт та бісульфіт. Кількість побочних продуктів до 0,5% на розчин МЕА зумовлює витрати моноетаноламіна до 0,5 кг на 1 т сировини.
Макрокінетика процесу На швидкість реакції, глибину поглинання H2S, економічні показники процесу значно впливає концентрація розчину моноетаноламіна.
На промислових установках МЕА використовують розчини з концентраціями 13−20%, іноді більш розбавлені-до 10% чи концентровані-до30%. Відомо, що розчини з концентрацією менш, ніж 20% створюють умови швидкої корозії апаратури. Крім того при використанні концентрованного абсорбенту збільшуються витрати моноетаноламіна. При роботі з розчинами концентрацією 10−15% корозія стає не такою помітною, але зростають витрати на регенерацію і циркуляцію абсорбента.
Як оптимальна, рекомендується концентрація розчину моноетаноламіну 13−15%. Змінюють її в залежності від вмісту кислих компонентів у газі.
Для зворотньої реакції дуже важливо враховувати умови досягнення високого виходу. Розчини МЕА мають високу поглинаючу здібність, а за умовами підтримання парціального тиску кислих компонентів у газі 0,01−0,02МПа і мольному співвідношенні H2S: МЕА від 0,3 до 0,5. за цією вимогою розраховують необхідну кількість абсорбенту.
Процес абсорбції супроводжується значним екзотермічним тепловим ефектом-1905кДж/моль. Тепло абсорбції виводиться з робочої зони потоками газу і розчину МЕА. Температура абсорбенту, насиченого H2S на виході не повинна перевищувати 50за умовами рівноваги, температура абсорбенту на вході повинна перевищувати вхідну температуру газа 5−15 щоб з газу в абсорбері не конденсувались низькокип’ячи компоненти, це приведе до значного вспінювання і забруднення абсорбенту. Температурний режим абсорбера в інтервалі 20−40підтримують, змінюючи температури вхідних потоків.
Технологічна схема МЕА В схемах абсорбційної очистки газів від H2Sвикористовують тарільчаті чи насадочні абсорбційні колони. Абсорбери мають 22−24 тарілки (сітчасті, колпачкові, S-подібні) чи шар насадки (кільця Рашига) еквивалентний 4−5 теоретичним тарілкам. Абсорбцію проводять в одну-дві стадії в залежності від типу процесу-тонка, середня чигруба очистка (при тонкій залишок H2S не більш 2 г на 100 м³, при грубій-більш, ніж 100г/100м3.
Основні технологічні параметри процесу:
— тиск 1,3−1,6МПа;
— температура на тарілках 25−40.
— температура кубової рідини (насиченого розчину МЕА) не більш 50.
Контролюються і автоматично регулюються подачі газу та абсорбенту, температурний режим, температури вхідних потоків.
Регенерирують розчин у десорбері-колоні з 15−20тарілками чи насадкою (3−4 теоретичних терілки).для зменшення витрат моноетаноламіна 30−35% тарілок знаходяться вище тарілки подачі сировини. Низ колони відділено глухою тарілкою, з якої розчин МЕА спрямовують у кип’ятилбник, де він нагрівається до 130−150і повертається в колону під глуху тарілку. Температура в десорбері 116−122 тиск 0,06−0,09МПа, максимальний до 0,2МПа. Газ десорбції після десорбера вміщує значну кількість паров води, МЕА, тому його охолоджують і відокремлюють від рідини у газосепараторі.
Вхідний поток насиченого абсорбента після абсорбера треба нагрівати з 40−50до температури на вході в десорбер 80−90 Для цього використовують рекуперативні теплообмінювачі, де утилізують тепло регенерированого розчину МЕА, що йде з десорбера у абсорбер.
РЕКОМЕНДОВАНА ЛIТЕРАТУРА.
1.Технологические расчеты установок переработки нефти: Учебн. пособие для вузов / Танатаров М. А., Ахметшина М. И., Фасхутдинова Р. А. и др. / Под ред. М. А. Танатарова. -М.: Химия, 1987. -352 с.
2.Химия нефти и газа: Учебн. пособие для вузов / А. И. Богомолов, А. А. Гайле, В. В. Громова и др./Под ред. В. А. Проскурякова, А.Е. ДрабкинаЛ.: Химия, 1989.-424 с.
3.Альбом технологических схем процессов переработки нефти и газа./Под ред. Б. И. Бондаренко.-М.: Химия, 1983.-128 с.
4.Гуревич И. Л. Технология переработки нефти и газа.Ч.1.-М.:Химия, 1975.
5.Смидович Е. В. Технология переработки нефти.Ч.2.-М.:Химия, 1980.-328с.
6.Справочник нефтепеработчика. В 2-х томах./Под ред. С. К. Огородникова. -Л.:Химия, 1978.
7.Рудин М. Г. Карманный справочник нефтепереработчика.-Л.:Химия, 1989.
8.Расчеты основных процессов и аппаратов нефтепереработки. / Под ред. Е. Н. Судакова.- М.:Химия, 1979.
9.Сарданишвили А. Г., Львова А. И. Примеры и задачи по технологии переработки нефти и газа.-М.:Химия, 1980.-256 с.