Розробка пристосування для відновлення деталей типу хрестовина карданного шарніра
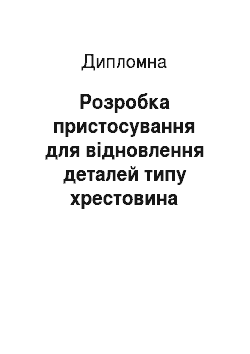
Електромеханічна обробка деталей Даний спосіб являється різновидом відновлення розмірів деталей тиском. Сутність його полягає в наступному. Деталь встановлюється в центри токарного станка. В супорті токарного станка закріплюють пружину державку, до якої кріплять твердосплавну пластину (рис 2.8). до деталі та державки підводять струм силою 300…800 А напругою 1…5 В. В зоні контакту пластини… Читати ще >
Розробка пристосування для відновлення деталей типу хрестовина карданного шарніра (реферат, курсова, диплом, контрольна)
Зміст
Антонація
Вступ
1.Технологія ремонту карданних передач
1.1 Основні несправності карданних передач
1.2 Технологія відновлення карданних передач
1.3 Збирання карданних передач
2.Відновлення розмірів, форми і механічних властивостей деталей за допомогою пластичної деформації
2.1 Характеристика процесу відновлення деталей пластичним деформуванням
2.2 Відновлення розмірів деталей в заданому напрямку
2.3 Електромеханічна обробка деталей
2.4 Відновлення форми деталі
2.5 Відновлення та покращення механічних властивостей деталей
2.6 Холодна правка під пресом
3.Конструктивна частина
3.1 Характеристика пристосування для відновлення деталей
3.2 Будова пристосування для відновлення хрестовин
3.3 Принцип роботи пристосування
3.4 Розрахунок пружини
3.5 Розрахунок потужності двигуна
3.6 Розрахунок шпонкового з'єднання
Висновки
Список використаної літератури
Додатки
Антонація
Дипломний проект на тему: «Розробка пристосування для відновлення деталей типу хрестовин карданного шарніра «присвячений проблемі удосконалення ремонтно-обслуговуючої бази з розробкою відповідного пристосування
В дипломному проекті приведено основні несправності та технологію ремонту хрестовин карданних передач, процес відновлення розмірів, форми і механічних властивостей деталей за допомогою пластичної деформації, показано необхідність провадження передових технологій, застосування енергоємних і метало ємних машин при виконанні ремонтних робіт у майстернях сільськогосподарських підприємств.
Розроблено конструктивну схему пристосування для відновлення хрестовин карданних передач, виконані необхідні креслення.
У графічній частині роботи було розроблено креслення загального вигляду пристосування, його складальне креслення та деталювання основних нестандартних деталей, які використовуються у даному пристрої, а також показано місця спрацювання спряжень карданного вала .
Дипломна робота містить 3 розділи розрахунково-пояснювальної записки та 5 листів графічної частини.
Вступ Приватизаційні процеси, які розпочалися в нашій країні згідно з прийнятими нормативно-правовими актами, торкнулись і агросервісної служби. В сільському господарстві масштаби її приватизації в значній мірі залежать від темпів реформування с.-г. підприємств. На інших рівнях 21% сервісних структур приватизації отже, накопичено певний досвід .
У зв’язку з цим виникла необхідність його узагальнення й аналіз позитивних і негативних тенденції з метою розробки пропозицій для нормального постприватизаційного розвитку реформованих аграрних структур .
Слід зазначити, що в агротехсервісній сфері до цього часу застосовуються різні способи приватизації сервісної служби КСП проводиться одночасно з основним виробництвом. Нині їх майно розподіляється (персоніфікується) безкоштовно між членами трудового колективу шляхом паювання. Стосовно інших рівнів, то тут 25 ремонтно-транспортних підприємств, 21 рай постач та завод, приватизовано через викуп майна трудовими колективами і перетворені у закриті акціонерні товариства, одна частина яких реформувалася через оренду з викупом, або товариства з обмеженою відповідальністю на яких реформувалось через відкритий продаж акцій .
Заміна форм власності зумовлює необхідність прискорення реструктуризацій них та інтеграційних процесів як в середині підприємства, так і на рівні агротехсервісної галузі і всього агропромислового комплексу. Основним напрямком їх здійснення має бути реформування існуючих агросервісних підприємств на всіх ієрархічних рівнях, створення відповідного конкурентного середовища та розгалуженої мережі посередницьких формувань, розвиток прямих між виробниками та споживачами технічних засобів.
В попередні роки в Україні була створена потужна Роб, яка налічувала 52,2 тисячі об'єктів. В них в господарствах 50,4 тисячі, в системі «Агропромсервісу» 1,8 тисячі, в тому числі 576 спеціальних ремонтних майстерень. На ремонтно-обслуговуючих роботах зайнято близько 0,5 мільйонів виконавчих робітників.
Для підтримання МТП на високому технічному рівні потрібно виконати значні обсяги ремонтно-обслуговуючих робіт, що складають більше 2,6 мільйонів сумових ремонтів.
З 1992 року спостерігається різке зниження обсягів виробництва на РТП. Технічне переоснащення ремонтно-обслуговуючих виробництв практично не проводиться тому, що не вистачає діагностичних, контрольно-вимірювальних, регулювальних та обслуговуваних засобів.
Для проведення переоснащення в спеціалізованих ремонтних майстернях необхідно залучити інвесторів, з цією метою Кабінет Міністрів Україниприйняв постанову № 1953 від 10 грудня 1998 року, згідно якої фінансова допомога надається сільським товаровиробникам, агропромсервісам та ремонтним підприємствам на закупівлю запасних частин і ремонтних иатеріалів, та оплату послуг ремонтних підприємств.
Система техсервісного обслуговування та ремонту техніки повинна орієнтуватись на створення в державі розгалуженої мережі техсервісних підприємств до якої повинні входити фірмові технічні центри підприємств виробників, техніка підприємтсва і база матеріального постачання «Укртехсервісу», РОБ господарств, приватні ТО інші технічні формування.
Дана мережа повинна підтримувати техніку в працездатному стані в гарантійні та післягарантійні періоди. Сільськогосподарський товаровиробник має можливість вільно вибирати виконавців техсервісних послуг залежно від їх якості, термінів виконання, вартості.
Також для своєчасного та якісного виконання ремонтних робіт господарства повинні бути оснащені сучасним обладнанням, ремонтними майстернями з достатньою виробничої площею і надійно діючими мийними установами.
1.Технологія ремонту карданних передач
1.1 Основні несправності карданних передач В автомобілях і колісних тракторів з ведучими передніми мостами карданні передачі можуть мати наступні дефекти:
— спрацювання шийок і сальників хрестовин;
— спрацювання голчастих підшипників;
— спрацювання отворів у вилках;
— спрацювання шліців на валах і вилках;
— прогинання і скручування валів;
— спрацювання проміжних опор і їх підшипників.
В карданних передачах гусеничних тракторів типу Т-74, ДТ -75 зустрічаються наступні спрацювання:
— шліців;
— поверхонь під сальники і отворів під втулки у вилках кардана;
— резинових втулок;
— зламування карданних головок.
Основними дефектами карданного вала рисунок 1.1 являються спрацювання:
шліців проковзувальної вилки та карданного вала;
цапф хрестовини кардана та голчастих підшипників;
отворів у вилці;
отворів у фланці-вилці кардана в спряжені з голчастими підшипниками;
прогинання і вм’ятини;
порушення динамічного балансування.
Основними причинами підвищеного спрацювання деталей карданної передачі автомобілів і колісних тракторів — це пошкодження захисного резинового чохла і попадання бруду, пилу і інших абразивних частин в
А — отвори в ковзаючій вилці - підшипник голчастий (зовнішнє
кільце); Б — хрестовина — підшипник голчастий; В — ковзаюча вилка — вал карданний.
Рисунок 1.1 — Місця спрацювання спряжень карданного вала трактора К — 701шліцові з'єднання, відсутність мащення в підшипниках, порушення балансування карданної передачі. У гусеничних тракторів головною причиною передчасного спрацювання деталей карданної передачі являється порушення співвісності між двигуном і коробкою передач.
1.2 Відновлення карданних передач Спрацьовані шийки хрестовин хромують або проточують і запресовують термічно обробленні втулки, після чого шліфують їх до нормального розміру.
Вилки кардана з спрацьованими шліцами, а також спрацьовані підшипники і сальники замінюють новими. Якщо спрацьовані отвори вилок під стакани голчастих підшипників, то вушка вилок обтискають і зменшенні отвори обробляють під номінальний розмір. Іноді отвори наплавляють, а потім обробляють.
При спрацюванні шліців наконечника карданного вала його замінюють новим. Для цього проточують на токарному станку зварювальний шов кріплення наконечника до труби, випресовують вибракуваний наконечник, запресовують новий і приварюють його електричним зварюванням по окружності. Биття вала після зварювання не повинно перевищувати 1,0 мм. Відновлювати шліци наплавленням не рекомендується. Скручені вали замінюють новими.
Погнуту трубу карданного вала правлять під пресом в холодному стані. Прогинання в середній частині труби не повинно перевищувати 0,5 мм.
1 — конусна втулка; 2 — пуансон; 3 — резинова втулка; 4 — кришка.
Рисунок 1.2 а — Пристосування для запресування резинових втулок карданних головок тракторів Спрацьовані отвори під втулки у вилках карданної передачі гусеничних тракторів типу ДТ — 75 розвертають під втулки ремонтного розміру. Не перпендикулярність осей отворів відносно площин фланця вилки допускається не більше 0,25 мм на довжині 40 мм. Вилки з спрацюваннями шліців вище допустимого замінюють новими.
Спрацьовані резинові втулки карданних головок замінюють новими. Заміна втулок — процес трудомісткий, тому часто для запресування нових втулок застосовують різні пристосування по типу, запропонованого раціоналізатором Ф. В. Шлаітовим. Нову резинову втулку 3 (рис. 1.2 а) вставляють в конусну втулку 1 і через пуансон 2 запресовують її до упора в кришку 4. Потім кришку знімають, направляючий буртик конусної втулки 1 встановлюють в отвір карданної головки і запресовують резинову втулку в головку 5 кардана (рис. 1.3, б). Спрацьовані резинові втулки випалюють в горні або видаляють ножем.
1 — конусна втулка; 2 — пуансон; 3 — резинова втулка; 5 — карданна головка.
Рисунок 1.2б — Пристосування для запресування резинових втулок карданних головок тракторів Хрестовини кардана відновлюють вібродуговим наплавленням порошковою проволокою, а потім шліфують під номінальний розмір. Овальність і конусність шипів хрестовини після шліфування допускається не більше 0,01 мм, не перпендикулярність 0,1 мм на кінцях шипів хрестовини.
Спрацьовані отвори під зовнішні кільця голчастих підшипників розточують на токарному або розточувальному станкові і запресовують в розточенні отвори проміжні втулки.
Спрацьовані шліци ковзаючої вилки відновлюють обтисканням в матриці під пресом з послідуючим прошиванням протяжкою.
Шліци вала кардана можна відновлюють наплавленням.
Карданні вали після ремонту повинні підлягати динамічному балансуванню.
1.3 Збирання карданних передач При збиранні карданних передач автомобілів і колісних тракторів з ведучими передніми мостами вилки карданів слід розміщувати в одній площині, а маслянки всіх хрестовин — з однієї сторони. Необхідно слідкувати за правильним встановленням сальникових ущільнювачів і резинових чохлів.
В зібраному вигляді карданний вал підлягає динамічному балансуванню на спеціальному стенді. Карданні вали вантажних автомобілів типу ГАЗ та ЗІЛ балансують при 650 — 700 об/хв. Дисбаланс не повинен перевищувати 100 гс см. Зменшують дисбаланс приварюванням балансувальних пластин на обох кінцях труби карданного вала. Після балансування стрілки на валі і ковзаючій вилці кардана повинні співпадати. Якщо вони не співпадають або відсутні, їх необхідно нанести поновому.
технологія деталь ремонт кардан
2.Відновлення розмірів, форми і механічних властивостей деталей за допомогою пластичної деформації
2.1 Характеристика процесу відновлення деталей пластичною деформацією Способом пластичної деформації відновлюють розміри і форму різних деталей за рахунок перерозподілу метала під дією зовнішніх сил.
Даний спосіб застосовується також для відновлення початкових механічних властивостей деталей, зміцнення їх робочих поверхонь і чистового оброблення.
Деталі відновлюють як в холодному, так і в гарячому стані.
В холодному стані зазвичай відновлюють деталі із низьковуглицевих сталей, кольорових металів і їх сплаві, а в гарячому стані - із середньоі високовуглицевих сталей (температура нагрівання рівна 0,7…0,9 температури плавлення.
Спосіб відновлення деталей пластичним деформуванням базується на властивостях металів змінювати свою форму під дією внутрішнього навантаження за рахунок залишкової деформації.
Деталі, які відновлюються пластичним деформуванням, умовно можна розділити на дві групи:
— до першої із них відносяться деталі, які втратили правильну форму без спрацювання або незалежно від спрацювання яких-небудь їх елементів (деформація);
— до другої групи відносяться деталі, які втратили форму або розмір в результаті їх спрацювання по робочій поверхні.
В першому випадку застосовують правку, а в другому — осадження, роздавання, обтискання, розтягування.
2.2 Відновлення розмірів деталей в заданому напрямку Схеми способів відновлення деталей пластичною деформацією показані на рисунках.
Відновлення деталей осаджуванням (рис. 2.1) застосовують для збільшення або зменшення зовнішнього або внутрішнього діаметра палих деталей за рахунок їх скорочення. Цим способом відновлюють різні типи втулок при спрацюванні по зовнішньому або внутрішньому діаметру, цапфи валів, осі та інші. Для більшості втулок допускається зменшення довжини на 4%.
Рисунок 2.1 — Відновлення розмірів деталей осадженням Методом вдавлювання (рис. 2.2) відновлюють шліци валів та інші деталі. На рисунку 2.3 показано пристосування для відновлення шліців при спрацюванні їх по товщині. Ролики 2 і 3 виготовляють із спеціальних твердих сплавів або із інструментальної сталі і підлягають термообробці до твердості 55…58 НRC. Ролик 2 вдавлюючись, проводить перерозподіл метала, а ролики 3 формують профіль і розміри шліців. Відновлення шліців таким способом можна виконати, проводячи їх нагрівання за допомогою струму високої частоти.
Рисунок 2.2 — Відновлення розмірів деталі вдавлюванням
1 — корпус; 2 — ролик; 3 — колібруючий ролик; 4 — шліцевий вал.
Рисунок 2.3 — Схема пристосування для відновлення шліців вдавлюванням Відновлення роздаванням (рис. 2.4) застосовують для збільшення зовнішнього діаметра полих деталей за рахунок внутрішнього. Методом роздавання відновлюють поршневі пальці, бронзові втулки насосів гідросистеми, труби рульової колонки та інші. Роздавання частіше проводять в холодному стані, загартовані деталі попередньо відпускають або відпалюють. Операція виконується продавлюванням пуансона, шарика і тому подібне.
Рисунок 2.6 — Пристосування для обтискання втулок гідронасосів типа НШ Рисунок 2.4 — Відновлення розмірів деталі роздаванням Відновлення деталей обтисканням (рис. 2.5) проводять при необхідності зменшити внутрішній діаметр полих деталей за рахунок зміни зовнішнього діаметра. Даним методом відновлюють втулки із кольорових металів (рис. 2.6), проушини різних ричагів при спрацюванні гладеньких або шліцевих отворів і інше. Гарячим обтисканням відновлюють отвори проушин ланок гусениць тракторів класу 30 кН. Для цього після нагрівання до ковочної температури деталь встановлюють в матрицю штампа, вводять в неї пуансон і наносять по ньому удар пневматичним молотом або декілька ударів кувалдою. При цьому метал видавлюється в одних місцях і переміщується в інші. Так, відновлюють, наприклад, тарілки клапанів, спрацьовані по фаскам. Операція полягає в продавлюванні деталі через матрицю.
Рисунок 2.5 — Відновлення розмірів деталі обтисканням
1 — пуансон; 2 — матриця; 3 — вкладиш; 4 — втулка; 5 — палець; 6 — плита.
Відновлення деталей витягуванням (рис. 2.7) застосовують для збільшення довжини деталі за рахунок місцевого (на невеликій ділянці) звуження її поперечного перерізу. Цей метод використовується при ремонті тяг, штанг, робочих органів сільськогосподарських машин, наприклад лемешів та інших Накатування (рис. 2.7) застосовують для збільшення зовнішніх або внутрішніх розмірів деталей за рахунок перерозподілу металу на поверхні. Накатування зубчастим роликом проводять при відновленні посадочних поверхонь слабо завантажених валів та інших деталей.
Рисунок 2.7 — Відновлення розмірів деталі витягуванням і накатуванням
2.3 Електромеханічна обробка деталей Даний спосіб являється різновидом відновлення розмірів деталей тиском. Сутність його полягає в наступному. Деталь встановлюється в центри токарного станка. В супорті токарного станка закріплюють пружину державку, до якої кріплять твердосплавну пластину (рис 2.8). до деталі та державки підводять струм силою 300…800 А напругою 1…5 В. В зоні контакту пластини з деталлю виділяється велика кількість тепла, метал нагрівається до температури 800…900 градусів. При цьому твердосплавна пластина 1 вдавлюється в обертаючу деталь і проходить випучування металу. На поверхні її утворюється гвинтова канавка, і діаметр деталі збільшується з початкового D2 до діаметра D1. Після проходження згладжу вальної пластини 3 отримують кінцевий діаметр D0. Висаджувальні пластини виготовляють із сплаву Т15К6 з кутом при вершині 60 градусів. Згладжу вальна пластина повинна мати радіус заокруглення робочої грані 80…100 мм. Шороховатість робочої поверхні інструмента (пластини) повинна бути не більше, чим по Ra = 0,04 мм. Для підведення струму до деталі на патроні встановлюють мідне кільце і мідно-графітові щітки. Для живлення використовують звичайний зварювальний трансформатор, який має 3 — 4 витки незалежної додаткової обмотки проводом перерізом 120, цим же проводом підводять струм до деталі і державки. Режим електромеханічної обробки наведений у таблиці 2.1.
Таблиця 2.1 — Режими електромеханічної обробки
Режим роботи | Висаджування | Згладжування | |
Подача, мм/об | 1…2 | 1…1,5 | |
Тиск інструменту, Н | |||
для сирих сталей | 700…800 | 300…400 | |
для загартованих сталей | 900…1200 | 300…400 | |
Окружна швидкість деталі, м/хв. | 3…8 | 5…8 | |
Сила струму, А | 400…500 | 350…400 | |
Кількість проходів | 2…4 | 1…2 | |
Електромеханічний спосіб відновлення доцільно використовувати при необхідності збільшення діаметра деталі не більше чим на 0,15 мм. При великих величинах нарощування гвинтові канавки на поверхні деталі слід заповнювати композицією на основі епоксидних смол або електроімпульсним приварюванням проволоки.
Досить ефективним являється накладання ультразвуку на інструмент при проходах згладжування. Обробка проводиться без підведення до деталі струму.
Рисунок 2.8 — Схема висаджування і згладжування обертальної поверхні деталі при електромеханічній обробці
2.4 Відновлення форми деталі
Для відновлення правильної форми деталей, які мають згин, кручення, вм’ятини, застосовується спосіб, який зворотній пластичній деформації, — правка (рис. 2.9).
При правці без нагрівання у деталей залишаються значні внутрішні напруги, в результаті чого після правки вони поступово приймають початкову форму.
Для знімання внутрішніх напруг після холодної правки деталь необхідно стабілізувати, тобто витримати при температурі 250…300 градусів на протязі декількох годин.
Великі та сильно деформовані деталі правлять в нагрітому стані.
Рд — напрямок дії сил; - напрямок деформації; Мкр — крутний момент.
Рисунок 2.9 — Відновлення розмірів деталі правкою Правка місцевим поверхневим наклепом (рис. 2.10) не призводить до зниження втомлю вальної міцності, що важливо для цілого ряду деталей (колінчастих валів ті ін.). Принцип правки полягає в тому, що при нанесенні на поверхню деталі великої кількості місцевих ударів в поверхневому шарі виникають стискаючі зусилля, які направленні в ту сторону, куди наносились удари. Наклеп проводять ручним або пневматичним молотком з шаровою головкою.
Рисунок 2.10 — Схема правки вала місцевим поверхневим наклепом
2.5 Відновлення та покращення механічних властивостей деталей В ряді випадків стальні деталі, які загартовані з нагрівом струмом високої частоти, правлять місцевим поверхневим наклепом (рис. 2.11).
Пластичною деформацією — наклепом поверхневого шару деталі - можна відновити або підвищити поверхневу твердість, зносостійкість, підвищити втомлю вальну міцність деталі, її пружність.
Зміцнення поверхонь деталей наклепом проходить в результаті багато чисельних, які слідують один за одним, ударів по поверхні деталі шариків, стальної або чавунної дробі, бойків, накатуванням шариками, роликами та ін. Наклеп підвищує втомлю вальну міцність і твердість поверхні деталей. Наклеп слід використовувати для зварних швів і деталей, які працюють в умовах знакозмінних навантажень (колінчасті вали, поворотні муфти, ресори, зварні шви рам та ін.).
Рисунок 2.11 — Схема правки вала поверхневим наклепом Щоб усунути деформацію (короблення) чавунних деталей, наприклад блока, головки циліндрів, випускних колекторів, деформовані площини шліфують або фрезерують зі зніманням мінімального шару метала. Допускається також стругання площин.
Деталі, які втратили свою форму або розмір в результаті спрацювання, можуть бути відновленні пластичним переміщенням металу за рахунок його запасу. Природно, що збільшення одних розмірів проходить за рахунок зменшення інших.
Дрібоструменевий наклеп частіше всього здійснюють роторними установками механічної дії (ДУ — 1, БДУ — ЭГ і ін.). Стальна або чавунна дріб попадає на лопатки обертаючого ротора і, вилітаючи із установки зі швидкістю 30…90 м/с, вдаряється по поверхні деталі. В результаті обробки на деталі утворюється наклепаний шар глибиною 0,5…0,7 мм.
Дрібоструменевим наклепом відновлюють шестерні, листи ресор та інші.
Зміцнення чеканкою застосовують для місцевого наклепу ділянок поверхонь деталей з високою концентрацією напружень (галтелі, шліци, зварні шви та інші). Чеканка проводиться спеціальними бойками, роликами, шариками шляхом ударної дії на зміцнювальну поверхню.
Накатування шариками або роликами застосовують для збільшення поверхневої твердості шийок валів, поверхні отворів, для підвищення міцності валів, пружності пружин.
Хороші результати в отриманні наплавленого шару без пор і раковин і зміцненні його поверхні дає термомеханічна обробка. При цьому об'єднують процес наплавлення і зміцнення поверхні. Наплавлений шар безпосередньо за зварювальною ванною накатують роликом або ударами бойка, чим і досягається необхідний результат.
2.6 Холодна правка під пресом Холодна правка під пресом — найбільш простий спосіб виправлення деформованих стальних деталей. В залежності від величини деталі і необхідного для правки зусилля застосовують гвинтові, ричажні або гідравлічні преси. Деякі деталі, наприклад шатуни, правлять на спеціальних пристосуваннях, які представляють собою видозмінені ричажні преси.
Деякі крупні деталі, які мають великий переріз і які вимагають для правки великого зусилля (лонжерони, рами), правлять з нагрівом місць прогинання паяльними лампами або в горні. Для правлення зазвичай застосовують ланцюгові схватки і переносний гідравлічний або гвинтовий прес. Деталі, термічно обробленні при виготовленні, після гарячої правки підлягають термічній обробці.
Для правлення вал встановлюють на призми преса і навантажують між опорами. Під призми і шток преса кладуть прокладки із м’якого матеріалу, щоб захистити робочі поверхні вала.
При правці спостерігаються пружні деформації (деталь пружинить). Тому для усунення згину деталь вигинають в зворотну сторону на величину, значно більшу, чим стріла прогину, і витримують в даному положенні 1,5…2 хвилини. Величина, на яку слід вигнути деталь, щоб усунути згин, залежить від її відносних розмірів, конфігурації, від відстані між опорами і місцем прикладання навантаження, від матеріалу, термічної обробки. Наприклад, при правці колінчастих валів різних марок, укладенні на крайні корінні шийки, і прикладанні навантаження на середню корінну шийку величина, на яку прогинають вал, повинна перевищувати величину усуваючої стріли прогинання в 10 — 15 раз.
Точність правки деталі приведена в технічних умовах.
Стрілу прогину вала визначають індикатором. В не круглих деталях стрілу прогину вимірюють щупом, вводячи його в зазор між деталлю і накладену на неї лінійкою (в місці найбільшого зазору), або шаблоном. Деякі деталі, наприклад шатуни, перевіряють на спеціальних пристосуваннях по калібру з заміром величини згину або скручування щупом або індикатором.
Вали для перевірки встановлюють в центрах або укладають крайніми корінними шийками на призми.
При перевірці в центрах попередньо перевіряють стан центрових отворів в торцях вала. При забитих або пошкоджених центрових отворах спостерігається биття вала, яке не можна відносити за рахунок його згину. Згин вала перевіряють індикатором, підводячи його вимірювальний наконечник до середини вала або до середньої шийки багато опорних валів.
Холодна правка стальних деталей не дає стійких результатів.
При правці виникають внутрішні напруження в матеріалі, так як деталь починає виправлятися лише після того, як в її зовнішніх волокнах стискаючі і розтягуючі напруження перейдуть границю пружності.
На протязі часу залишкові напруження викликають нове (вторинне) скривлення виправленої деталі. Це виникає не тільки в період її експлуатації після ремонту, але і при зберіганні.
Для підвищення надійності холодної правки деталі зразу ж після правки підлягають термічній стабілізації. Для цього їх нагрівають до 400 — 450 градусів, витримують при даній температурі 0,5 — 1,5 години (в залежності від розмірів деталі) і дають поступово охолонути. В результаті залишкові напруження знімаються, тобто усувається причина, яка викликає зворотній згин деталі.
Якщо не можна нагрівати деталі до вказаної температури (остання термічна обробка при виготовленні проведена при більш низькій температурі), теплову стабілізацію ведуть при температурі 200 — 250 градусів. В даному випадку залишкові напруження знижуються на 50 — 60%.
3.Конструктивна частина
3.1 Характеристика пристосування для відновлення деталей Пристосування, яке має станину, встановлену на ній шпиндельну головку з дорном, приводи обертання дорна і осьового переміщення шпиндельної головки, а також механізм фіксації оброблювальної деталі, виконанні у вигляді призми з чотирма взаємно перпендикулярними пазами, один із яких співпадає із віссю шпиндельної головки, і вертикально-рухомого привідного притискача, розташованого над призмою, відрізняється тим, що, з метою розширення номенклатури відновлювальних деталей, підвищення надійності і якості відновлення, і покращення умов знімання відновлювальних деталей, воно обладнане штоком з механізмом його піднімання і провертання на 90 градусів, при цьому в призмі механізму фіксації виконано центральний отвір, а шток розміщений в вказаному отворі призми.
Пристосування відрізняється тим, що шток виконаний з гвинтовою канавкою на його боковій поверхні, а механізм піднімання і провертання штоку виконаний у вигляді встановленої співвісно отвору призми з можливістю обертання в одну сторону відносно своєї осі втулки зі штифтом, який входить в гвинтову канавку штока, і пневмоциліндра, який розташований співісно штоку і пов’язаного з ним.
Пристосування може бути використане при відновленні спрацьованих деталей типу хрестовин карданного шарніра.
Відоме пристосування для відновлення спрацьованих деталей типу хрестовина карданного шарніра, яка містить шпиндельну головку з закріпленими на її кінці дорном, привід осьового переміщення головки, індуктор струму високої частоти і механізм фіксації відновлювальної деталі.
Однак в даному пристосуванні після роздавання наряду із збільшенням діаметра шипів хрестовин спостерігається їх скорочення по довжині на 1,5 — 2 мм, у зв’язку з чим необхідна додаткова операція по нарощуванню торців шипівхрестовин електродуговим наплавленням з наступною їх механічною обробкою. Це призводить до різкого зниження якості і продуктивності процесу і не дозволяє здійснити масове відновлення деталей.
Найбільш близьким по технічній суті і досягнутому ефекті є пристосування для відновлення деталей типу хрестовина карданного шарніру, яке містить станину встановлену на ній шпиндельну головку з дорном, приводи обертання дорна і осьового переміщення шпиндельної головки, а також механізм фіксації оброблювальної деталі, виконанні у вигляді призми з чотирма взаємно перпендикулярними пазами, один із яких співпадає із віссю шпиндельної головки, і вертикально-рухомого привідного притискача, розташованого над призмою.
Нагрівання шипа до пластичного стану тільки в зоні роздачі, в різниці від суцільного попереднього нагріву його, одночасно з роздаванням забезпечує подовження тіла шипа на 0,3 — 0,6 мм, що дозволяє виключити трудомісткі операції по наплавленню шипів торців шипів з метою їх подовження і механічної обробки після наплавлення.
Однак відоме пристосування не забезпечує відновлення певних типів хрестовин, так як в деяких типах хрестовин необхідно відновлювати сальникові шийки шипів. Вказані хрестовини не можуть бути відновленні за допомогою вказаного пристосування, так як при роздаванні хоча б однієї із сальникових шийок проходить перекіс хрестовини відносно фіксуючої призми. На практиці це призводить до зламування деформуючих твердосплавних дорнів.
Крім того, утруднене видалення відновлювальної хрестовини із призми, що не дозволяє використовувати пристосування в автоматичних лініях.
Метою даної розробки є розширення номенклатури відновлювальних деталей, підвищення надійності і якості відновлення, і покращення умов знімання відновлювальних деталей.
Вказана мета досягається тим, що пристосування для відновлення деталей типу хрестовина карданного шарніру, яке має станину, встановлену на ній шпиндельну головку з дорном, приводи обертання дорна і осьового переміщення шпиндельної головки, а також механізм фіксації оброблювальної деталі, виконанні у вигляді призми з чотирма взаємно перпендикулярними пазами, один із яких співпадає із віссю шпиндельної головки, і вертикально-рухомого привідного притискача, розташованого над призмою, обладнане штоком з механізмом його піднімання і провертання на 90 градусів, при цьому в призмі механізму фіксації виконано центральний отвір, а шток розміщений в вказаному отворі призми.
Шток пристосування виконаний з гвинтовою канавкою на його боковій поверхні, а механізм піднімання і провертання штоку виконаний у вигляді встановленої співвісно отвору призми з можливістю обертання в одну сторону відносно своєї осі втулки зі штифтом, який входить в гвинтову канавку штока, і пневмоциліндра, який розташований співісно штоку і пов’язаного з ним.
3.2 Будова пристосування для відновлення хрестовин Пристосування для відновлення деталей типу хрестовин карданних шарнірів складається (рис. 3.1) із станини 1, на верхній горизонтальній плиті якої встановлена головка 2 з висувним шпинделем 3. На передньому кінці шпинделя змонтований патрон 4 із закріпленим в ньому дорном 5, який виконаний із твердого сплаву. На задньому кінці шпинделя встановлений упорний підшипник 6, який запобігає передачі крутного моменту на шток пневмоциліндра 7 осьового переміщення шпинделя 3. Привід обертання шпинделя 3 здійснюється від електродвигуна 8, який розташований в нижній
1 — станина; 2 — головка; 3 — шпиндель; 4 — патрон; 5 — дорн; 6 — підшипник; 7 — пневмоциліндр; 8 — електродвигун; 9 — пасова передача; 10 — притискач; 11 — пневмоциліндр; 12 — призма; 13 — шток; 17 — пневмоциліндр; 20 — підставка; 21 — пульт; 22 — пневмопанель; 23 — пружина.
Рисунок 3.1 — Пристосування для відновлення хрестовин частині станини, через пасову передачу 9. Механізм фіксації відновлювальної деталі виконаний у вигляді притискача 10, розташованого на кінці штока пневмоциліндра 11 над призмою 12, який містить чотири направляючих паза, вісь симетрії одного із яких співпадає з віссю шпиндельної головки.
Механізм піднімання і провертання відновлювальної деталі на 90 градусів (рис. 3.2) відносно пазів призми містить шток 13, який розташований в центральному отворі призми 12, яка обертає навколо своєї осі втулку 14, яка встановлена співвісно з отвором призми і яка обладнана розташованим на її внутрішній поверхні штифтом 15, який взаємодіє з гвинтовою канавкою 16 циліндричної поверхні штока 13, який переміщується в осьовому напрямку в середині втулки і отвору призми способом пневмоциліндра 17, зусилля якого менше зусилля, яке створює пневмоциліндр 11, і постійно напраленого до верху. Втулка 14 (рис. 3.3) обладнана виступами 18 і фіксатором 19 від зворотнього провертання штоку 13.
12 — призма; 13 — шток; 14 — втулка; 15 — штифт; 16 — гвинтова канавка; 19 — фіксатор; 20 — підставка.
Рисунок 3.2 — Механізм піднімання провертання відновлювальної деталі
На верхньому кінці штока 13 розташована підставка 20, яка орієнтує хрестовину відносно пазів призми 12.
Управління технологічним циклом відновлення проводиться за допомогою пульта 21. На пневмопанелі 22 розташовані блок очищення повітря і пневморозподільники.
13 — шток; 14 — втулка; 18 — виступи; 19 — фіксатор.
Рисунок 3.3 — Розріз механізму піднімання провертання відновлювальної деталі
3.3 Принцип роботи пристосування
Підготовка до роботи даного пристосування включає наступні операції: встановлення відновлювальної хрестовини на підставку 20, вмикання електродвигуна 8 приводу обертання шпинделя, а також підведення стиснутого повітря до пневмопанелі 22.
Після проведення підготовлю вальних операцій робота на пристосуванні здійснюється в напівавтоматичному режимі.
Після натискання кнопки «Прижим» пневмоциліндр 11, пересилюючи дію пневмоциліндра 17, фіксує способом притискача 10 відновлювальну хрестовину в пазах призми так, що вісь одного із шипів її співпадає з віссю шпинделя.
При переміщенні вниз гвинтова канавка 16 штока 13, затиснутого з двох кінців пневмоциліндрами 11 і 17, повертає штифт 16, а з ним і втулку 14, на 90 градусів. При цьому в кінці ходу штока 13 вниз один із чотирьох виступів 18 втулки 14 фіксується фіксатором 19 пристосування.
4 — патрон; 5 — дорн; 10 — притискач; 11 — пневмоциліндр; 12 — призма; 20 — підставка.
Рисунок 3.4 — Процес відновлення хрестовини Після встановлення (рис. 3.4) хрестовини в призму вмикається пневмоциліндр 7 подачі обертаючого дорна 5 в бік деталі. При доторканні кінця дорна з торцем хрестовини за рахунок стискання пружини 23 інструмент закінчує осьове переміщення і зусилля пневмоциліндра 7 повністю передається дорну 5. При цьому в результаті тертя дорна об шип проходить нагрівання останнього до пластичного стану, після чого дорн 5 заходить в отвір шипа і роздає хрестовину, тобто збільшує зовнішній діаметр шипа хрестовини. Після закінчення процесу роздавання шпиндель відводиться в попереднє положення. Притискач 10 звільняє хрестовину, а пневмоциліндр 17 піднімає шток в верхнє положення. При цьому гвинтова канавка 16 штока 13 взаємодіє зі штифтом 15 втулки 14, в результаті чого шток, піднімаючись до верху, провертається на 90 градусів і повертає деталь так, що вісь наступного шипа хрестовини встановлюється паралельно осі шпиндельної головки.
По вказаному циклу проходить послідовне роздавання наступних шипів хрестовини. Після закінчення роздавання останнього четвертого шипа шпиндель із дорном і притискач 10 автоматично відводиться в попереднє положення, а пневмоциліндр 17 витягує деталь із призми. Деталь видаляється з підставкою 20 і встановлюється нова. В подальшому цикл повторюється.
В порівнянні із відомим використання запропонованого пристосування дозволяє розширити номенклатуру відновлювальних деталей, підвищити надійність роботи пристосування для відновлення і якість відновлювальних деталей, а також покращити умови їх знімання.
3.4 Розрахунок пружини Дано: пружина стиску,;; мм; = 25…35 мм; 10 м/с. [16]
Незалежно від заданої витримки на основі формули можна переконатись, що при значеннях менше 0,25, всі одножильні пружини, навантажені зі швидкістю більше 9,4 м/с, відносяться до класу ІІІ.
З врахуванням діапазону значень для пружини класу ІІІ від 0,1 до 0,4 знаходимо силу :
Н (3.1)
Підставивши значення, отримаємо:
Н Для вказаного інтервалу в ГОСТ 13 774– — 86 є витки з наступними силами: 300; 375; 335.
Виходячи з заданих розмірів діаметру і найменших габаритів вузла
= 300 Н, = 1,4 мм, = 3,1 мм, мм, = 50,93 Н/мм, = 5,9 мм.
Згідно ГОСТ 13 764– — 86 для пружини класу 3 = 0,6. Використовуючи ГОСТ 9389– — 75, визначимо напруження для знайденого діаметру дроту [16]:
(3.2)
МПа Належність до класу перевіряємо шляхом визначення величини відношення, для чого знаходимо і критичну швидкість по формулам b [16]:
(3.3)
Підставивши значення отримаємо:
м/с (3.4)
Тоді
м/с Перевіримо, чи дійсно дана пружина відноситься до 3 класу:
Знайдена нерівність свідчить про можливість дотику витків, і те що пружина відноситься до 3 класу.
Визначення інших параметрів проводимо по формулам [16]:
Жорсткість пружини визначаємо по формулі:
Н/мм (3.5)
Підставивши дані у дану формулу отримаємо:
Н/мм Кількість робочих витків пружини визначаємо за формулою:
(3.6)
Отримаємо Після чого уточнюємо жорсткість нашої пружини:
(3.7)
Повну кількість витків знаходять по формулі:
(3.8)
Середній діаметр пружини визначаємо по формулі:
мм (3.9)
мм Деформації, довжини й крок пружини знаходять за формулами [16]:
мм (3.10)
мм (3.11)
мм (3.12)
Підставивши дані отримаємо:
мм, мм, мм
(3.13)
мм (3.14)
мм
мм (3.15)
мм
мм (3.16)
мм
мм (3.17)
мм
мм (3.18)
мм
3.5 Розрахунок потужності електродвигуна
(3.19)
де — ККД механізму підйому [14]
кВт
Вибираємо електродвигун з потужністю
Двигун типу MTF111−6,кВт при ПВ-60% [14]
хв-1, вага 76 кг, мм.
Передаточне число привода [14]:
(3.20)
3.6 Розрахунок шпонкового з'єднання
Вихідні дані:
діаметр вала D=36 мм;
обертаючий момент Т3=74.3 Нм;
частота обертання вала n3=57.7 хв-1;
Для діаметра вала D=36 мм за (табл.5.9) вибираємо шпонку 10x8x55 ГОСТ 8787–78. [14]
Перевіряємо шпонку на зминання (МПа) за формулою:
(3.21)
де Т3 — обертаючий момент,;
d — діаметр вала, мм;
h — висота шпонки, мм;
l — довжина шпонки, мм;
[узм] - допустиме навантаження зминання, [узм]=100…130 МПа. [14]
Умову міцності виконано зм<[зм].
Перевіримо напруги зрізу (МПа) за формулою [14]:
(3.22)
де b — ширина шпонки, мм;
[фзр] - допустимі напруги зрізу, [фзр]=60…100 МПа.
Умову міцності виконано зр<[зр].
Висновки
Дана установка дозволяє відновлювати отвори хрестовин за допомогою пластичного деформування, а саме використовувати при відновленні даних деталей методу роздавання.
Метою даної розробки є розширення номенклатури відновлювальних деталей, підвищення надійності і якості відновлення, і покращення умов знімання відновлювальних деталей.
Вказана мета досягається тим, що пристосування для відновлення деталей типу хрестовина карданного шарніру, яке має станину, встановлену на ній шпиндельну головку з дорном, приводи обертання дорна і осьового переміщення шпиндельної головки, а також механізм фіксації оброблювальної деталі, виконанні у вигляді призми з чотирма взаємно перпендикулярними пазами, один із яких співпадає із віссю шпиндельної головки, і вертикально-рухомого привідного притискача, розташованого над призмою, обладнане штоком з механізмом його піднімання і провертання на 90 градусів, при цьому в призмі механізму фіксації виконано центральний отвір, а шток розміщений в вказаному отворі призми.
Отже, дане пристосування для відновлення хрестовин можна з успіхом використовувати на будь-яких ремонтних сільськогосподарських підприємствах і отримувати після ремонту надійні і якісно відремонтовані хрестовини, які не будуть ні в чому відрізнятись, мається на увазі у довговічності роботи, від нових.
Список використаної літератури
1. Комплексная система технического обслуживания и ремонта машин в сельском хозяйстве. — М.: ГОСНИТИ, 1985. — 143 с.
2. Практикум з ремонту машин / О.І. Сідашенко, О. А. Науменко, А.Я.
Поліський та ін.; За ред. О.І. Сідашенка, О. А. Науменка. — К.: Урожай,
1995. — 224 с.
3. Ремонт машин / О.І. Сідашенко, О. А. Науменко, А.Я. Поліський та ін.;
За ред. О.І. Сідашенка, А.Я. Поліського. — К.: Урожай, 1994. — 400 с.
4. Курсовое и дипломное проэктирование по надежности и ремонту машин / И. С. Серый, А. П. Смелов, В. Е. Черкун. — М.: Агропромиздат, 1991. — 184 с.
5. Водолазов Н. К. Курсовое и дипломное проектирование по механизации сельского хозяйства. — М.: Агропромиздат, 1991. — 335 с.
6. Ремонт машин / И. Е. Ульман, Г. А. Тонн, И. М. Герштейн и др.; Под общ. ред. И. Е. Ульмана. — 3 — е изд., перераб. и доп. — М.: Колос, 1982. — 446 с., ил. — (Учебники и учеб. пособия для с.- х. Техникумов.
7. Селиванов А. И. Cправочная книга по организации ремонта машин в сельском хозяйстве. — М.: Колос, 1989.
8. Справочник по единой системе конструкторской документации / В. П. Градиль, А. К. Моргун, Р. А. Егошин. Под ред. А. Ф. Раба. — Х.: Прапор, 1998. — 255 с.
9. ТК 70.0001.081 — 86. Дизели Д-240, Д — 240Л, Д — 241, Д — 241Л, Д — 242, Д — 242Л. Технические требования на капитальный ремонт. — М.: ГОСНИТИ, 1987. — 108 с.
10. Молодык Н. В., Зенин А. С. Востановление деталей машин: Справочник. — М.: Машиностроение, 1989. — 256 с.
11. Воловик Е. Л. Справочник по востановлению деталей. — М.: Колос, 1981. — 361 с.
12. Ремонт дизельних двигунів: Довідник / За ред. Л.С. Єрмолова — К.: Урожай, 1991. — 248 с.
13. Обладнання ремонтних підприємств / М.І. Черновол, М. В. Власенко, В. М. Наливайко, В. С. Кухаренко. — К.: Урожай, 1996. — 272 с.
14. Шейнблит А. Е. Курсовое проектирование деталей машин. — М.: Высшая школа, 1991. — 432 с.
15. Денежный П. М., Стискин Г. М., Тхор И. Е. Токарное дело. — М.: Высшая школа, 1986. — 240 с.
16. Анурьев В. И. Справочник конструктора машиностроителя: В 3-х т. Т.1- М.: Машиностроение, 1979. — 728 с.
17. Комплексная система технического обслуживания и ремонта машин в сельском хозяйстве — М.: Логос. — 1985.
Додатки
Форм | Зона | Поз. | Позначення | Назва | Кільк | Примітка | |
06−14.ДП.09.С-23.04.20.000 | Підставка | ||||||
06−14.ДП.09.С-23.04.21.000 | Пульт | ||||||
06−14.ДП.09.С-23.04.22.000 | Пневмопанель | ||||||
06−14.ДП.09.С-23.04.23.000 | Пружина | ||||||
06−14.ДП.09.С-23.04.00.000СК | т | ||||||
Зм. | Лист | № докум. | Підпис | Дата | |||
Форм | Зона | Поз. | Позначення | Назва | Кільк. | Примітка | ||
Документація | ||||||||
А1 | 06−14.ДП.09.С-23.04.00.000СК | Складальне креслення | ||||||
Деталі | ||||||||
06−14.ДП.09.С-23.04.01.000 | Станина | |||||||
06−14.ДП.09.С-23.04.02.000 | Головка | |||||||
06−14.ДП.09.С-23.04.03.000 | Шпиндель | |||||||
06−14.ДП.09.С-23.04.04.000 | Патрон | |||||||
06−14.ДП.09.С-23.04.05.000 | Дорн | |||||||
06−14.ДП.09.С-23.04.06.000 | Підшипник | |||||||
06−14.ДП.09.С-23.04.07.000 | Пневмоциліндр | |||||||
06−14.ДП.09.С-23.04.08.000 | Електродвигун | |||||||
06−14.ДП.09.С-23.04.09.000 | Пасова передача | |||||||
06−14.ДП.09.С-23.04.10.000 | Притискач | |||||||
06−14.ДП.09.С-23.04.11.000 | Пневмоциліндр | |||||||
06−14.ДП.09.С-23.04.12.000 | Призма | |||||||
06−14.ДП.09.С-23.04.13.000 | Шток | |||||||
06−14.ДП.09.С-23.04.14.000 | Втулка | |||||||
06−14.ДП.09.С-23.04.15.000 | Штифт | |||||||
06−14.ДП.09.С-23.04.16.000 | Гвинтова канавка | |||||||
06−14.ДП.09.С-23.04.17.000 | Пневмоцилідр | |||||||
06−14.ДП.09.С-23.04.18.000 | Виступи | |||||||
06−14.ДП.09.С-23.04.19.000 | Фіксатор | |||||||
06−14.ДП.09.С-23.04.00.000СК | ||||||||
Зм. | Лист | № докум. | Підпис | Дата | ||||
Розробив | Зарецький В. | Пристосування для відновлення карданних передач Складальне креслення | Літера | Лист | Листів | |||
Керівник | Анісімов В. Ф, | У | ||||||
ВДАУ, гр. 41 -М | ||||||||
Н. контр | Островський | |||||||
Затв. | Анісімов В. Ф | |||||||
Форм | Зона | Поз. | Позначення | Назва | Кільк. | Примітка | ||
Документація | ||||||||
А1 | 06−14.ДП.09.С-22.03.00.000ВЗ | Вигляд загальний | ||||||
Складальні одиниці | ||||||||
06−14.ДП.09.С-23.03.01.000 | Станина | |||||||
06−14.ДП.09.С-23.03.02.000 | Головка | |||||||
06−14.ДП.09.С-23.03.03.000 | Шпиндель | |||||||
06−14.ДП.09.С-23.03.04.000 | Патрон | |||||||
06−14.ДП.09.С-23.03.05.000 | Дорн | |||||||
06−14.ДП.09.С-23.03.06.000 | Підшипник | |||||||
06−14.ДП.09.С-23.03.07.000 | Пневмоциліндр | |||||||
06−14.ДП.09.С-23.03.08.000 | Електродвигун | |||||||
06−14.ДП.09.С-23.03.09.000 | Пасова передача | |||||||
06−14.ДП.09.С-23.03.10.000 | Притискач | |||||||
06−14.ДП.09.С-23.03.11.000 | Пневмоциліндр | |||||||
06−14.ДП.09.С-23.03.12.000 | Призма | |||||||
06−14.ДП.09.С-23.03.13.000 | Шток | |||||||
06−14.ДП.09.С-23.03.17.000 | Пневмоцилідр | |||||||
06−14.ДП.09.С-23.03.20.000 | Підставка | |||||||
06−14.ДП.09.С-23.03.21.000 | Пульт | |||||||
06−14.ДП.09.С-23.03.22.000 | Пневмопанель | |||||||
06−14.ДП.09.С-23.03.23.000 | Пружина | |||||||
06−14.ДП.09.С-23.03.00.000ВЗ | ||||||||
Зм. | Лист | № докум. | Підпис | Дата | ||||
Розробив | Зарецький В. | Пристосування для відновлення карданних передач Вигляд загальний | Літера | Лист | Листів | |||
Керівник | Анісімов В. Ф, | У | ||||||
ВДАУ, гр. 41-М | ||||||||
Н. контр | Островський | |||||||
Затв. | Анісімов В. Ф | |||||||
Форм | Зона | Поз. | Позначення | Назва | Кільк. | Примітка | ||
Документація | ||||||||
А4 | 06−14.ДП.09.С-23.00.00.000ПЗ | Пояснювальна записка | ||||||
06−14.ДП.09.С-23.00.00.000 ПЗ | ||||||||
Зм. | Лист | № докум. | Підпис | Дата | ||||
Розробив | Зарецький В. | Пристосування для відновлення карданних передач | Літера | Лист | Листів | |||
Керівник | Анісімов В. Ф, | У | ||||||
ВДАУ, гр.41 -М | ||||||||
Н. контр | Островський | |||||||
Затв. | Анісімов В. Ф | |||||||
Рецензія на дипломний проект студента 4-го курсу ФМСГ ВДАУ
Зарецького
на тему: « Розробка пристосування для відновлення деталей типу
хрестовина карданного шарніра"
Даний дипломний проект відповідає вимогам і стандартам, що встановленні до дипломного проектування для вищих навчальних закладів. Дипломний проект представлена на 5 листах графічної частини формату А1 та сторінках пояснювальної записки. Пояснювальна записка містить три розділи та пояснення пропонованих рішень, таблиці та рисунки.
Тема дипломної роботи актуальна, пов’язана із розширенням номенклатури відновлювальних деталей, підвищення надійності і якості відновлення, і покращення умов знімання відновлювальних деталей. В роботі зроблено аналіз основних несправностей хрестовин карданних передач, описано основні способи та методи відновлення хрестовин карданних передач пластичним деформуванням, а також запропонована конструкція пристрою для їх відновлення.
Графічна частина проекту і розрахунково-пояснювальної записки виконанні з дотриманням вимог ЄСТД і ЄСКД.
По суті до роботи суттєвих зауважень не маю, окрім наступних:
— відсутні деякі посилання на літературні джерела;
— бажано б було навести конструкції існуючих пристосувань для відновлення деталей методом заливання рідким металом Проте в цілому дана розробка заслуговує впровадження на спеціалізованих ремонтних підприємствах, може бути оцінена на «відмінно», а студент Зарецький заслуговує присвоєння освітньо-кваліфікаційного рівня «бакалавр» з механізації сільськогосподарського виробництва.
Рецензент, доцент Спірін А. В.
Відгук на дипломний проект студента четвертого курсу факультету
механізації сільського господарства денної форми навчання
Зарецького
на тему: « Розробка пристосування для відновлення деталей типу
хрестовина карданного шарніра «
Дане пристосування для відновлення карданних хрестовин можна з успіхом використовувати на будь-яких ремонтних сільськогосподарських підприємствах і отримувати після ремонту надійні і якісно відремонтовані хрестовини карданних передач, які не будуть ні в чому відрізнятись, мається на увазі у довговічності роботи, від нових.
За період виконання дипломного проекту студент Зарецький В. Ю. показав достатньо високий рівень знань із загальноосвітніх та спеціальних дисциплін, вміння користуватися довідковою та нормативною документацією, самостійно вирішувати складні інженерні завдання.
Вважаю, що дипломний проект виконаний на достатньо високому рівні, за структурою, змістом та обсягом відповідає завданню та вимогам, що висуваються до дипломних проектів. Виконана робота може бути подана для захисту перед ДЕК, а студент Зарецький заслуговує присвоєння йому освітньо-кваліфікаційного рівня «бакалавр» з механізації сільськогосподарського виробництва Керівник дипломного проекту, проф. Анісімов В. Ф.