Пристрій фрезерний двохмісний, призначений для закріплення деталей типа «вал»
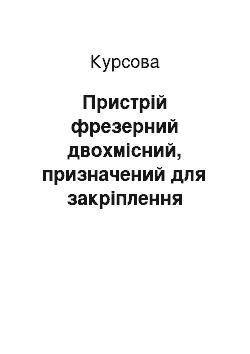
Безпека виробничого процесу — властивість виробничого процесу зберігати відповідність вимогам безпеки праці в умовах, установлених нормативно-технічною документацією. Це досягається комплексом конструкторських проектних та організаційних рішень, що полягають у відповідному виборі технологічних процесів, робочих операцій і впорядкування обслуговування обладнання, виробничих приміщень або зовнішніх… Читати ще >
Пристрій фрезерний двохмісний, призначений для закріплення деталей типа «вал» (реферат, курсова, диплом, контрольна)
Вступ Розвиток технології машинобудування, підвищення ефективності технологічних процесів — найважливіше завдання, що стоїть перед робітниками. Важливе значення для технології машинобудування мають комплексні показники металообробки. Успішне вирішення поставлених завдань можливе на основі спеціалізації, підвищення ефективності технологічного, технічного та ремонтного виробництва.
Ефективність металообробки враховує роль перспективного виготовлення та відновлення стальних штампів, прес-форм, виправлення браків та вплив якісного оснащення на продуктивність праці, економічність і зменшення металоємкості.
Технологія машинобудування неможлива без спеціалізації та впровадження групових і типових технологічних процесів з використанням уніфікованого оснащення та обладнання.
Основним завданням машинобудівного комплексу є дешеве і якісне виготовлення високопродуктивними методами машин та виробів різного призначення. Металорізальні верстати поряд з пресами-автоматами — це той вид обладнання, який лежить в основі виробництва усіх сучасних машин, приладів та інструментів.
Вартість механічної обробки деталей на металорізальних верстатах досить велика. Наприклад, в машинобудуванні вона складає 30−40% вартості готової деталі. Тому кожний процент підвищення продуктивності верстатів, внаслідок чого знижується собівартість деталей, має велике народногосподарське значення. Крім того, кількість металорізальних верстатів, їх технічний рівень і стан значною мірою характеризує виробничу потужність держави.
У наш час визначна роль у прискоренні технічного переоснащення машинобудування належить верстатобудівній промисловості. Одним із головних напрямів роботи по прискоренню науково-технічного прогресу є широка автоматизація технологічних процесів на основі використання автоматичних верстатів, машин, механізмі, уніфікованих модулів обладнання, робото технічних комплексів, обчислювальної техніки та ГВС.
Особиста увага приділяється прискореному розвитку комплексів, металообробного обладнання, створення гнучких виробничих систем, що базуються на оснащенні їх роботизованими комплексами, транспортними та складськими засобами з обчислювальною технікою.
Технологічне оснащення являє собою важливу частину в інтенсифікації виробництва, виготовленні деталей. Саме тому на підприємствах більше уваги приділяється питанням виготовлення та експлуатації пристроїв, їх застосування і проектування. Але головним питанням при конструюванні пристроїв є вирішення модернізації конструкції, зменшення часу на проектування та виготовлення верстатних пристроїв. Це обумовлено тим, що оснащення технологічних операцій механічної обробки заготовок верстатними пристроями потребує великих затрат.
Виникнення таких затрат і завдань прискорення темпів науково-технічного прогресу, підвищення якості машин і устаткування, зниження собівартості, удосконалення виробництва, підвищення якості продукції та зріст продуктивності праці залежить від:
колективної роботи на основі сучасних засобів виробництва втілення передових технологій виробництва втілення безвідходної технології виробництва з енергоємним прогресивним технологічним оснащенням.
У наш час розвиток верстатобудування йде у напрямку підвищення продуктивності, довговічності, надійності та точності обробки за рахунок використання автоматизованих процесів, робото-технічних комплексів і сучасного технологічного оснащення.
Конструкція спроектованого пристосування дозволяє отримати потрібну точність обробки заготовок при забезпеченні високої продуктивності виробництва, забезпечення безпеки експлуатації та праці робітника.
Вирішення питання оптимізації конструкції оснащення пов’язано з аналізом різноманітних типових конструкцій деталей та вузлів, а також з методикою машинного проектування і використання традиційної методики.
Важливу роль у вирішенні питання відіграє техніко-економічній розрахунок, який виконується при проектуванні цього пристосування.
Для виконання заданої обробки деталі типу «вал» — фрезерування шпонкового пазу — необхідно спроектувати механізований верстатний пристрій. Вихідними даними для цього є річна програма випуску деталей та маршрутний технологічний процес, наведений в таблиці 1.
Таблиця 1 — Маршрутний технологічний процес деталі «Вісь паразитної шестерні»
№ операції | Найменування операції | Опис переходів | Облад-нання | Схеми базування | |
Фрезерно-центрувальна | Фрезерувати торці Свердлити центро-вочні отвори | МР-71 | |||
Токарна | Чорнове точіння поверхні 3 Напівчистове то-чіння поверхні 3 Чорнове точіння поверхні 4 Нпівчистове то-чіння поверхні 4 | 16К20 | |||
Токарна | Чорнове точіння поверхні 5 Напівчистове точіння поверхні 5 | 16К20 | |||
Токарна | 1.Чорнове точіння поверхні 6 2.Напівчистове точіння поверхні 6 | 16К20 | |||
Токарна | 1.Чистове точіння поверхні 5 2.Чистове точіння поверхні 6 3.Точити фаску 7 4.Точити фаску 8 | 16К20 | |||
Токарна | 1.Чистове точіння поверхні 4 2.Точіння канавки 10 3. Точіння фаски 9 | 16К20 | |||
Токарна | 1.Чистове точіння поверхні 3 2.Точіння канавки 11 3. Точіння фаски 12 | 16К20 | |||
Токарна | Точимо фаску 13 Точимо фаску 14 | 16К20 | |||
Різбонарізна | Накатуємо різьбу на поверхні 15 | ||||
Фрезерна | 1.Фрезерувати паз 16 | ||||
Свердлильна | Свердлити отвір 17 Ш9 Повторити перехід 2 рази | 2Н135 | |||
Фрезерна | 1.Фрезерувати лиску 18 | 6Н10 | |||
Термічна | Загартовуємо вал | ТВ4 | |||
Шліфувальна | 1. Шліфування поверхні 5 2. Шліфування поверхні 4 | 3153Е | |||
Слюсарна | 1. Зняття заусенець | Верс-так | |||
Миєчна | 1. Миємо вал | ||||
Контрольна | 1. Проконтролювати розміри | Стіл БТК | |||
1. Загальний розділ
1.1 Призначення, будова та принцип роботи спроекто-ваного пристосування Пристрій фрезерний, двохмісний призначений для закріплення деталей типа «вал». Установочними елементами є призми.
Для закріплення деталі типа «вал» нам потрібно повернути ручку розподільного крану. При цьому стиснене повітря із загальної повітряної мережі з тиском 0,5 МПа подається в безштокову порожнину і поршень зі штоком перемішується праворуч.
Шток має два скоси, якими рухаються ролики. Коли шток переміщується праворуч, він опускає нижній ролик, який знаходиться на тязі. До тяги через перехідну шпильку приєднаний притиск, який опускається з тягою і здійснюється затиск. Для розтиску деталі за допомогою розподільного крану стиснуте повітря подається в штокову порожнину і поршень зі штоком переміщуються ліворуч. Під дією пружини і верхнього ролика притиск з тягою приймають попереднє положення та здійснюють розтиск деталі.
пристрій фрезерний деталь заготовка
1.2 Перевірка умови позбавлення можливості переміщення заготовки у пристрої по шести ступеням свободи згідно ГОСТ 21 495–76
Аналіз креслення показує, що в якості технологічної бази, раціонально буде прийняти зовнішню циліндричну поверхню Ш40d6 і лівий торець.
Циліндрична поверхня Ш30d6 буде напрямною базою і позбавляє заготовку двох ступенів свободи (опорні точки 1 і 2). Циліндрична поверхня Ш40d6 також є напрямною базою і позбавляє заготовку двох ступенів свободи (опорні точки 3 і 4). Торець буде опорною базою і позбавляє заготовку однієї ступені свободи (опорна точка 5). Зусилля затиску позбавляє шостої ступені свободи (опорна точка 6).
Рисунок 1 — Схема базування заготовки Для забезпечення точної обробки необхідно правильно розташувати (зорієнтувати) її відповідно робочих органів верстату та в пристосуванні, забезпечити постійність контакту технологічних баз з опорами і повну нерухомість заготовки відносно пристосування в процесі обробки.
Рисунок 2 — Правило шести точок Опорна точка 1 позбавляє заготовку переміщення вздовж вісі Z.
Опорна точка 2 позбавляє заготовку обертання навколо вісі Y.
Опорна точка 3 позбавляє заготовку обертання навколо вісі Z.
Опорна точка 4 позбавляє заготовку переміщення вздовж вісі Y.
Опорна точка 5 позбавляє заготовку переміщення вздовж вісі Х.
Опорна точка 6 позбавляє заготовку обертання навколо вісі Х.
2. Розрахункова частина
2.1 Розрахунок похибки встановлення заготовки Похибка встановлення заготовки визначається за формулою [1]
Wв = 1,2 • (1)
де Wб — похибка базування заготовки
Wз — похибка закріплення заготовки
Wпр — похибка пристосування Похибка базування визначається за формулою
Wб = - 1 (2)
де Td — допуск на технологічну базу б — кут нахилу площини призми За таблицею допусків маємо Ш40 = мм Похибку закріплення приймаємо Wз = 0, тому що заготовка зміщується і не деформується під дією сили затиску.
Похибка пристрою складається з Wвиг, Wзн., Wвст. верстат.
Wвиг = 0, тому що призми шліфуються з однієї установки. Wзн. приймаємо рівну 0 тому, що вона не впливає на похибку пристрою. Що стосується призм Wвст. на верст. приймаємо 0,01 мм.
Похибка встановлення буде
Wв = 1,2 •
Так як Wв = 0,012 мм Т = 0,3 мм, то пристосування забезпечує задану точність обробки.
2.2 Розрахунок зусилля затиску заготовки в пристосуванні
Розрахунок зусилля затиску виконують при конструюванні нових пристосувань. Розрахунок зусилля затиску може бути зведений до задачі статики на рівновагу заготовки під дією прикладених до неї зовнішніх сил.
До оброблюваної заготовки прикладені сили, що виникають в процесі обробки, шукані сили закріплення і реакції опор. Під дією цих сил заготовка повинна знаходитися у рівновазі. Сила затиску Q повинна бути достатньою для попередження зміщення встановленої в пристосування заготовки.
Розраховуємо зусилля затиску.
Обробка деталі ведеться на фрезерному верстаті 6Т12, N = 7,5 кВт, = 0,75.
При фрезеруванні пазу 9 мм дисковою фрезою, виникає сила різання Рyz. Для зручності розрахунку цю силу розділяємо на складові:
Рn — горизонтальна складова, яка прагне змістити заготовку вздовж вісі Х, Рv — вертикальна складова, яка прагне повернути заготовку навколо точки О.
Рисунок 3 — Схема дії сил Складаємо рівняння рівноваги заготовки Мперекид — Мзатиск Мперекид = Pv •? + Pn • R1 (3)
Мзатиск = Q • ?2
KPv • ?1 + KPn • R1 — Q?2 = 0 (4)
де?1 — повна довжина деталі ?1 = 99 мм
R1 — плече дії сил різання
?2 — плече дії сил затиску ?2 = 37 мм
K — коефіцієнт запасу міцності К = 2,5
Розраховуємо сили різання.
Для визначення складових Pv і Pn необхідно визначити силу Рyz [8]
деЕ — величина, що визначається за таблицею, Е = 0,17 [8]
V — швидкість м/хв, за таблицею приймаємо V = 105 м/хв [4]
z — число зубців, для фрези Ш50 приймаємо число зубців z = 14
bmax — максимальна ширина фрези, bmax = 9 мм К1 — коефіцієнт, який залежить від оброблювального матеріалу, К1 = 1,15
К2 — коефіцієнт, який залежить від типу фрези і швидкості різання, К2 = 1
Визначаємо потужність на шпинделі верстату Перевіряємо потужність верстату Потужність верстату достатня для виконання даної операції.
Визначаємо силу Рyz
При попутному фрезеруванні за таблицею співвідношення Pv і Pn до сили Рyz
Pv і Рyz = 0,7ч0,9Pn і Рyz = 0,8ч0,9
Приймаємо
Pn = 0,8 < Рyz = 0,8 • 1457 = 1165,8 Н
Pv = 0,7 < Рyz = 0,7 • 1457 = 1019,9 Н Визначаємо подачу на зуб за допомогою таблиці Szт = 0,10 мм/зуб.
Визначаємо подачу за формулою [8]
Sz = Szт • Ksz
Ksz = Kszс • Kszч • Kszт • Kszк = 1,1 • 0,66 • 1 = 0,66
Sz = 0,10 • 0,66 = 0,066 мм/зуб Визначаємо подачу на оберт
So = Sz • z = 0,066 • 14 = 0,924 мм/об Розраховуємо частоту обертання шпинделя Визначаємо дійсну частоту обертання nд = 630 об/хв.
Визначаємо дійсну швидкість різання Визначаємо основний час на операцію де L =? + y + ?
? = 2 мм
L = 2919,2 + 63 = 84,2
V3 = Sz • nд • z = 0,066 • 14 • 630 = 582,12 мм/хв Визначаємо зусилля затиску заготовки
2.3 Розрахунок основних параметрів затискного механізму Основним параметром затискного механізму є діаметр пневмоциліндру та зусилля на штоці.
Рисунок 4 — Схема клино-плунхерного механізму Знаходимо зусилля на штоці за формулою [1]
Звідси деб — кут нахилу площини клина, б = 160
ц1пр — приведений коефіцієнт кута тертя на похилій площині клина,
ц1пр = 2050ґ
ц2 = 5043ґ
tg ц2 = коефіцієнт тертя двохопорного плунжеру
d — діаметр вісі ролика
D — зовнішній діаметр ролика,
Q — зусилля затиску заготовки, Q = 9027,5 Н
Qзат = Q + Pпp
де Q — зусилля затиску Рпр — опір пружини, який визначаємо за формулою [6]
деd — діаметр проволоки, d = 2 мм
[ф] - допустиме напруження кручення в кг/мм2, за таблицею [ф] = 77
K — коефіцієнт, який враховує кривизну витка і вплив поперечної сили дес — індекс пружини, с = 2,5 мм
D — зовнішній діаметр проволоки, D = 18 мм
Qзат = 9027,5 + 86,6 = 9114,1 Н Визначаємо діаметр пневмоциліндру, коли стиснене повітря подається в безштокову порожнину деР — робочий тиск, приймаємо Р = 0,4 МПа
— ККД = 0,8
При штоковій робочій порожнині
деd — діаметр штоку Діаметр штоку визначаємо конструктивно
d = 0,3 • D = 0,3 • 0,123 = 0,03 м Приймаємо діаметр пневмоциліндру за ГОСТ 15 608–70 D = 160 мм, діаметр штоку d = 40 мм.
Після того, як визначили діаметр пневмоциліндру і діаметр штоку, визначаємо фактичне зусилля на штоці
При цьому фактичне зусилля затиску заготовки в пристрої буде Так як фактичне зусилля затиску більше розрахункового Qф = 14 893 Н > > Qр = 9027,5 Н, то умова надійності затиску заготовки забезпечена.
Уточнюємо похибку закріплення заготовки. Заготовка із сталі 45 діаметром 40+0,20 мм. Вимоги до обробки: Rz3 = 30; ?Rz3 = 20 мкм; н3 = 1,9; W3 = 8 мкм; ?W3 = 6 мкм. Призма з кутом 2б = 900 для фрезерування шпонкового пазу. Нормальна загрузка на опорі g = 2000 Н/мм,? g = 600 Н/см. Максимальний допустимий знос опорної поверхні призми п = 0,3 мм.
Rz0 = 3,5 мкм н0 = 2
Св, См — безвимірні розрахункові коефіцієнти, знаходяться по таблиці [9]
п — лінійний знос заготовки
2б — кут призми См = 0,2
К = 0,82
а = 0,695
К1 = 0,62
а1 = 0,55
Св = К (1+ W3) а = 0,82(1+8)0,695 = 3,8
См = К1(1+W3 + Rz0 + Rz3) а1 = 0,62(1+8+3,5+30)0,55
Rч = 0,22 • [2,28dч + (0,5ITd + 0,57ч)ctga] 2/4
Y=1/sinб{[См/10Кч]g+1,15Св/Кч0,4(g/d)0,2+1,07См/Кч•1/[5(н0+ н3)]•(g/d)1/
/[10(н0+ н3)]}
Y=1/sin450{[0,026/(10•1)]2000+1,15•3,8/10,4(2000/50)0,2+1,07•4,35•1/
/[5(5+1,9)]•(2000/50)1/[10(2+1,9)]}=18,4 мкм
J = 2000 • 2?: 18,4 • 106 = 219 • 106? Н/м
При довжині призми? = 4 мм
J = 145 • 106 • 4 = 580 • 106 Н/мм За таблицею приймаємо Rz0 = 1,1 мкм, н0 = 1,4.
ЕзІ = 0,1 • См: sinб • ?g
ЕзІ = 0,1 • 0,026: sin450 • 600 = 2,2 мкм ЕзІI = {1,1g1: [10(н0 + н3 + Rz0 + Ra3)1-a1]}
ЕзІI = {1,1 • 2000: [10(1,1 + 1,9)]0,62 • 20} = 2мкм ЕзІII = {0,87g • 0,2Ka: [sinбdon • (1 + W3)1-a]}?W3
ЕзІII = {0,87•20 000,2 • 0,82 •0,695: [sin450 • 500,2(1 + 8)1−0695]}6 = 5,9 мкм Езч = 0,1: sinб[0,4Смg: (1+Кч)2 + 3К (1+ W3) а /(1+Кч)0,4•(g:d)0,2](Кч-1)
Езч = 0,1: sin450 [0,4 • 0,025 • 2000: (1+4,5)2 + 3 • 0,82(1+8)0,695/ (1+4,5)0,4 • •(2000:50)0,2](4,5−1) = 6,25 мкм Похибка встановлення буде
Wв = 0,025 Т = 0,3. Це означає, що пристосування забезпечує задану міцність.
2.4 Розрахунок міцності двох деталей пристосування Розрахунок на міцність проводимо для більш навантажених деталей пристосування. До них відносяться шток, призма і тяга.
Шток — це довга деталь, яка може позбавлятися своєї стійкості. Розрахункова схема — брус жорстко защемлений з двох боків.
Рисунок 5 — Розрахункова схема брусу Розрахунок на міцність проводимо за формулою [7]
деQк — зусилля на штоці, Qк = 14 983 Н Азм — площина дії деформації, мм2
Розраховуємо граничну міцність при зминанні за формулою [7]
де[n] - запас міцності, приймаємо [n] = 1,5.
Отже, деталь витримує деформацію зминання і при цьому не втрачає своєї робочої властивості.
Розрахунок на стійкість і стискання.
Коефіцієнт приведення довжини приймаємо = 0,5. Визначаємо робочу гнучкість деталі за формулою де? пр — приведена довжина стержня, мм
?пр =? •
де? — довжина деталі,? = 195 мм
іmin — найменший радіус інерції повздовжнього перерізу стержня.
деd — діаметр штока, d = 40 мм
?пр = 0,5 • 95 = 97,5 мм Для сталей л0 = 60 та лгран = 100.
У даному випадку л0 лгран, тому деталь стійкості не втрачає та розраховується на міцність при стисканні.
Розрахунок міцності при стисканні проводимо за формулою деF — сила на штоці, Н, А — площина перерізу, мм2
деd — діаметр штоку.
Граничну міцність розраховуємо за формулою детч — границя текучості, Н/мм2
[n] - запас міцності, приймаємо [n] = 1,5
ст = 11,9 Н/мм2 [ст] = 222,7 Н/мм2
Таким чином, деталь витримує деформацію стискання, не втрачаючи своїх робочих властивостей.
Розраховуємо на міцність деталь типу тяга. Ця деталь піддається деформації розтягнення. Деталь типа брусу, має різні площини перерізу.
Рисунок 6 — Схема дії сил на тягу На рисунку 6 видно, що найнебезпечніший переріз буде А2.
Перевіряючи розрахунок на міцність для цього перерізу маємо вид деNz — максимальна прокольна сила, діюча на важіль при навантаженні,
Nz = Q = 6028,84 H
A2 — площина найнебезпечнішого перерізу.
Розраховуємо допустиме напруження за формулою детч — границя текучості, для сталі 45 тч = 1040 МПа
[n] - коефіцієнт запасу міцності, для сталі 45 [n] = 2,5
Визначаємо площину поперечного перерізу А2 = А1 — А3
А2 = 1760 — 1040 = 720 мм³
Рисунок 7 — Небезпечний переріз
2.5 Аналіз конструкції спроектованого пристосування При розгляді конструкції спроектованого пристосування можна встановити, що тип пристрою фрезерний; затискний механізм клино-плунжерного типу з двома роликами. Його призначення — базування, закріплення заготовки при фрезеруванні шпонок, лисок, валів. Пристрій двохмісний, установочними елементами є призми.
Затискним механізмом є сполучення вбудованого пневматичного циліндру, клино-плунжерного механізму з двома роликами і тягою. Пристрій є переналагоджуваним і складається із змінної частини, постійної частини — корпус, вбудований пневмоциліндр, клино-плунжерний механізм, повітряно-розподільний кран та тяги з роликом.
Пристрій механізований за допомогою пневмоприводу, двохмісний для обробки двох заготовок.
Управління пристроєм ручне за допомогою розподільного крану.
2.6 Основи техніки безпеки. Безпечність технологічних процесів та устаткування Виробничий процес — складна соціально-технічна система. Під час виконання різноманітних виробничих операцій людина може стикатися з виробничою небезпекою.
Виробнича небезпека — можливість дії на працюючих небезпечних і шкідливих виробничих факторів.
Безпека праці - стан умов праці, при якому виключається дія на працюючих небезпечних і шкідливих виробничих факторів.
Техніка безпеки — система організаційних заходів і технічних засобів, які запобігають дії на працюючих небезпечних виробничих факторів. Небезпека обладнання та виробничих процесів, яка виявляється під час експлуатації, закладається ще в процесі проектування та конструювання. Тому дуже велике значення має дотримання вимог безпеки вже під час їх розробки.
Виробничі процеси та експлуатація обладнання повинні відбуватися відповідно до вимог правил техніки безпеки, в яких закладаються заходи щодо усунення небезпеки як узагальненого характеру, так і стосовно конкретного обладнання. Ретельне виконання вимог цих правил запобігає нещасним випадкам.
Безпека виробничого процесу — властивість виробничого процесу зберігати відповідність вимогам безпеки праці в умовах, установлених нормативно-технічною документацією. Це досягається комплексом конструкторських проектних та організаційних рішень, що полягають у відповідному виборі технологічних процесів, робочих операцій і впорядкування обслуговування обладнання, виробничих приміщень або зовнішніх майданчиків, виробничого обладнання та умов його розміщення, засобів захисту працюючих, умов зберігання й транспортування виробництва. Велике значення має правильний розподіл функцій між людиною та складовими частинами виробничого процесу.
Виробничі процеси не повинні бути пожежота вибухонебезпечними, не повинні забруднювати навколишнє середовище викидами небезпечних і шкідливих речовин понад допустимі норми.
Машини, апарати та інше обладнання, які застосовуються в різних галузях промисловості, різноманітні за принципом дії, конструкцією, типажем і розмірами. Однак, існують деякі загальні вимоги, дотримання яких на стадії користування виробничого обладнання дозволяє забезпечити безпечність при його експлуатації.
Для досягнення безпечності праці будь-яке виробниче устаткування в процесі проектування та виготовлення дослідних зразків має забезпечуватись необхідними спеціальними технічними засобами безпеки:
загороджувальними та запобіжними пристроями гальмівними та блокуючими пристроями і сигналізаторами безпеки спеціальними засобами електробезпеки, пожежота вибухобезпеки вирішенням ергономічних вимог, а також іншими засобами, залежно від його специфічних особливостей та умов експлуатації.
При проектуванні обладнання доцільно враховувати умови його експлуатації, якщо при дії вологості, високих та низьких температур і тисків, сонячної радіації, механічних коливань, агресивних речовин, мікроорганізмів, грибків, вітрових навантажень та ін., обладнання не було небезпечним.
Забезпечення потрібної міцності, а значить безпечності машини, повинно досягатись ще на етапі проектування та виготовлення не лише в серійному виробництві. Про це слід пам’ятати на етапі модернізації та інтенсифікації роботи обладнання, з чим пов’язана постійна діяльність інженерно-технічних працівників. Ці заходи мають не лише підвищувати продуктивність машин та механізмів, але й не знижувати їх міцність.
Перелік використаної літератури
1. Шманев В. А., Шулепов А. П., Анипченко Л. А. «Приспособления для производства деталей летательных аппаратов». М.: Машиностроение, 1990.
2. Данилевский В. В. «Технология машиностроения». М.: Высшая школа, 1984.
3. Белоусов А. П. «Проектирование станочных приспособлений». М.: Высшая школа, 1980.
4. Справочник технолога машиностроителя / Под ред. А. Г. Косиловой и Р. К. Мещерякова. М.: Машиностроение, 1985. Том 2.
5. Кузнецов Ю. И. «Технологическая оснастка для станков с ЧПУ и промышленных роботов».
6. Горошкин А. К. «Приспособления для металлорежущих станков». Справочник. М.: Машиностроение, 1979.
7. Гельфгат Ю. Г. «Сборник задач и уравнений по технологии машиностроения». М.: Высшая школа, 1986.
8. Справочник «Режимы резания металлов» / Под ред. Ю. В. Барановского. М.: Машиностроение, 1972.
9. «Станочные приспособления». Справочник / Под ред. Б. Н. Вардашкина. М.: Машиностроение, 1984.
10. Методичний посібник «Розрахунок деталей верстатних пристосувань на міцність» ТРКМ ДНУ, 2001.
11. Анурьев В. И, Комашничков Ф. Ф., Маслеников И. М. «Справочник конструктора-машиностроителя». М.: Машиностроение, 1963.
12. Справочник технолога машиностроителя / Под ред. А. Г. Косиловой и Р. К. Мещерякова. М.: Машиностроение, 1985. Том 1.
13. ГОСТ 2.105−95 «Общие требования к текстовым документам». К.: Киев, Госстандарт Украины, 1996.