Виробництво плавленого периклазу з природного бруситу
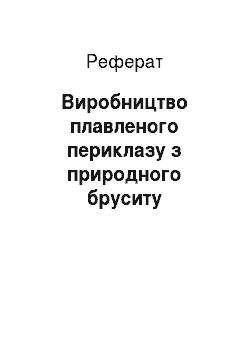
Номінальний хід розжига фіксується освітою микродуг між електродами і шматочками коксу, і навіть розігрівом коксового трикутника, поступовим збільшенням робочого струму і поступовим опусканням електродів щодо початкового становища. Розжиг печі виготовляють 1−3 щаблях пічного трансформатора. Вимірювання сили струму виробляється килоамперметром типу Э-377. Через 30 хв виробляється перша… Читати ще >
Виробництво плавленого периклазу з природного бруситу (реферат, курсова, диплом, контрольна)
I. СИРОВИНА І ДОПОМІЖНІ МАТЕРИАЛЫ…3.
II. ТЕХНОЛОГІЧНА СХЕМА ПРОИЗВОДСТВА…4.
III. ФІЗИКО-ХІМІЧНІ ОСНОВЫ ПРОИЗВОДСТВА…5.
IV. КОНТРОЛЬ ПРОИЗВОДСТВА…8.
V. АВТОМАТИЗАЦІЯ ПРОИЗВОДСТВА…9.
VI. БІБЛІОГРАФІЧНИЙ СПИСОК…11.
Вогнетриви підвищеної стійкості дозволяють розвивати високоефективні процеси в металургії, хімічної технології, виробництві будівельних матеріалів, енергетиці, приладобудуванні. Розвиток методів виплавки легованої стали, позапічної обробки вакуумом, інертними газами, синтетичними шлаками істотно змінили вимоги, запропоновані і до самим огнеупорам, і до технології їх виготовлення. Останніми роками в технології вогнетривів придбав важливе значення метод плавки і лиття, застосовуваний для вогнетривів з оксидів, відмінних стійкістю до дисоціації при високих температурах.
Початок промислового освоєння процесу набуття плавлених вогнетривких матеріалів належить до тридцятим років нинішнього століття. Одним із перших плавку в дугових сталеплавильних печах почали застосовувати США, Норвегія, Югославія й низку інших країн. У вперше провели плавку в 1934 року у Ленінграді. У тому ж року працівниками заводу «Магнезит «було випущено невеличка партія плавленого магнезита. 1939;го року заводу «Електросталь «було виплавлено 115 т плавленого магнезита, а вироби потім із нього відчули в зводах электропечей.
У 1959 року у Українському інституті вогнетривів було проведено роботи з плавленні магнезитового порошку в печі СКБ-514 потужністю 250 кВт. Починаючи з 1939 року, систематично на Саткинском вогнетривкому комбінаті виплавляють магнезит у двох однофазних печах ділянки «Пороги «потужністю 560 і 750 кВт. Нині плавлений вогнетривкий матеріал отримують на кількох спеціалізованих підприємствах: на комбінаті «Магнезит «в Сатке, на Богдановичском вогнетривкої заводі, заводі Северо-Ангарского рудника, на заводі «Казогнеупор ». Основні переваги цієї технологія полягають у високого рівня гомогенізації матеріалу при плавленні й одержанні після охолодження щільного в міцного тіла зі структурою, якої у певної ступеня можна управлять.
У технології вогнетривів плавленые матеріали займають особливу увагу. Плавлений периклаз знаходить усе більше застосування виготовлення вогнетривких виробів і порошків, і навіть як електроізоляційний матеріал в електротехнічній та інших галузях промисловості. Відмінною рисою плавленных матеріалів є їхньою висока щільність і значна коррозионная стойкость.
Попри великі витрати енергії на плавку, застосування плавленных матеріалів перебувають у раді випадків економічно ви придатним, оскільки, уперших, поліпшуються властивості вогнетривів і збільшується термін їхньої служби; удругих, процес плавки матеріалу досить швидкий, тоді як керамічний синтез напівфабрикату вимагає досить хворого тимчасового інтервалу. При плавленні частина домішок возгоняется. Інші домішки переміщаються до периферії, звідки є підстави е подальшому віддалені. Отже, при плавленні відбувається хімічне збагачення матеріалу. Разом про те, плавленным матеріалам властиві й свої специфічні недоліки. Проте незаперечну перевагу плавленных вогнетривів зумовило їх перериване увеличение.
I. СИРОВИНА І ДОПОМІЖНІ МАТЕРИАЛЫ.
Для отримання плавленого периклаза використовується брусит Кульдурского родовища марок БРК-1 і БРК-2.
Основним минералом вихідного сировини є брусит. Домішки представлені магнезитом, доломитом, гидроксидами заліза, серпентинохлоритом і кварцем.
Хімічна формула брусита — Mg (OН)2. Вона складається на 64% з Mg O і 36% з H2О. У нинішньому вигляді ізоморфних домішок іноді присутні залізо (ферробрусит) і марганець (манганобрусит). Кристалічна структура типово шарувата. Колір брусита білий, зрідка зеленуватий чи бесцветный.
Сировину вступає у залізничних вагонах і розвантажується складі брусита. Кожна партія сировини перевіряється ОТК.
По зерновому й хімічному складам брусит повинен відповідати вимогам діючих технічних умов ТУ 14−8-392−827.
Склад сировини приведено у. табл.1.1.
Для підвода електричної енергії у робочий простір печі і горіння дуги служать електроди. Основними вимогами, яких мають задовольняти електроди, являются:
— хороша електропровідність, забезпечує номінальні втрати електроенергії при підводі струму до дуге;
Таблиця 1.1 Склад кульдурского брусита |Показники |Норма для | | |марок | | |БРК-1 |БРК-2 | |Масова частка, % | | | |MgO, щонайменше |65 |63 | |Fe2O3, трохи більше |0,15 |0,2 | |CaO, трохи більше |1,5 |2,5 | |SiO2, трохи більше |1,5 |2 | |Розмір шматків, мм, трохи більше |150 |150 | |Прохід через сітку № 5, не |10 |10 | |більш, % | | |.
— висока механічна міцність, предотвращающая обрив і поломку їх при роботі печи;
— висока температура окислення їх у повітрі й садити мінімальна окисляемость при горінні дуги, що дозволяє зменшити витрати електродів на плавку;
— мала вартість електродів, оскільки витрата електродів має важливе значення у балансі вартості виплавленого огнеупора.
Для плавки брусита застосовують графитированные електроди марки ЭГ-О, ЭГ-1А чи ЭГ-1, випущені по ГОСТ 4426–71. Електроди і з'єднувальні ниппели характеризуються такими показателями.
— удільне електричне опір 8,5−12 Ом· мм2/м;
— межа міцності при стискуванні 7−9 МПа; - межа міцності при розриві 3,5−5 МПа;
— питома витрата електродів 92 кг/т;
— максимальний струм електрода 12 500 А;
— число фаз- 3;
— частота струму 50 гц; - діаметр електрода 400 мм;
— діаметр розпаду електродів 700, 960 і 1180 мм;
— хід електрода 1400−1600 мм;
— швидкість переміщення електрода 1,6−1,8 м/мин.
Для розжига печі використовується кам’яновугільний кокс. Витрата коксу на плавку становить 120−130 кг.
II. ТЕХНОЛОГІЧНА СХЕМА ПРОИЗВОДСТВА.
Брусит Кульдурского родовища фракції 150 ми надходить, а залізничних вагонах і розвантажується складі брусита. Кожна партія сировини перевіряється ВТК. На складі брусит вантажиться в автосамосвалы і перевозиться на ділянку електропечей. З автосамосвала брусит висипається в прийомний бункер. Потім елеватором і транспортером подається в прийомні воронки над электропечью.
У прийомні воронки електропечей мостовим краном в кюбелях на місця збору осипу подається осип. Кокс привозиться автотранспортером, сгружается в кюбеля і подається у приймальну вирву заправного вузла. Подина стаціонарної ванни пічний вагонетки заправляється кіркою, осипом масою 700−1200 кг і вихідним сировиною на висоту 550−700 мм. На шкірки блоку чи осипу при необхідності подсыпка з глинозему, на підсипку з глинозему викладається трикутник завтовшки 120−160 мм (90−100 кг) з кам’яновугільного коксу фракції менше 20 мм електродного бою фракції 60−20 мм у відсотковому співвідношенні 1:1. Дозволяється застосування одного кам’яновугільного коксу фракції 60−20 мм.
Підготовлена до плавленні грубна вагонетка із порушенням установленої у ньому ванній подається під электродержатели печі. Мостовим краном, электротельфером чи спеціальним пристосуванням виробляється нарощування (перезаправка) електродів, установка нових ниппелей і електродів, перепускание електродів і затискачі их.
Перепуск електродів і відповідне нарощування їх виробляються після відключення печи.
Ниппельное гніздо нарощуваної секції, ніпель секції старанно обдуваются стиснутим повітрям. Забороняється затискати електроди в ниппельных соединениях.
Трансформатор печі встановлюється на першу щабель напруги. Вимірювання напруги виробляється вольтметром типу Ц-4202. Піч перекладається на автоматичне управління, і задатчики встановлюються на номінальний струм. Усі три електрода опускаються на коксовий трикутник до забезпечення надійного контролю. Становище електродів фіксується за розміткою стійки электродержателя. Піч включается.
Номінальний хід розжига фіксується освітою микродуг між електродами і шматочками коксу, і навіть розігрівом коксового трикутника, поступовим збільшенням робочого струму і поступовим опусканням електродів щодо початкового становища. Розжиг печі виготовляють 1−3 щаблях пічного трансформатора. Вимірювання сили струму виробляється килоамперметром типу Э-377. Через 30 хв виробляється перша завантаження ванни печі, Завантаження виробляється до того часу, поки дуга нічого очікувати закрита шаром шихти щонайменше 200 мм. Ознакою нормального ходу процесу режиму є опускання електродів на 150−250 мм щодо початкового становища. Закінченням розжига можна вважати зупинку і поступовий перехід електродів в режим стійкого підйому щодо крайнього нижнього становища при номінальному струмі печи.
Плавку здійснюють шляхом зміни введеної потужності з ходу процесса.
Автоматичне пристрій підтримки постійної потужності має бути відрегульовано для підтримки номінального струму для трансформатора.
Завантаження шихти під час плавки виробляється порційно. Плавку кожної порції здійснюють за підвищеної потужності 1,1−1,4 разу проти потужністю, введеної в піч до завантаження. Збільшення потужності здійснюють шляхом перемикання щаблів напруги пічного трансформатора від У до 1 чи підвищення номінальною токовой навантаження до 10−15%. Тривалість роботи печі на підвищених значеннях струму залежить від температури олії трансформатора, але з більш 0,5 часу циклу плавки.
Під час плавки виробляється штовхання з метою запобігти зависання шихти, ліквідації освіти кратерів та зниження теплових втрат. Штовхання шихти від стінок ванни до центра виробляється між загрузками і для кожної завантаженням із єдиною метою вирівнювання і трамбовки шару сировини. Ведення плавки без шуровки воспрещается.
У процесу плавки температура олії трансформатора має перевищувати 60 °З, а перевищення над температурою довкілля — не більш 60 °З. Після закінчення плавки піч відключається високовольтним выключателем.
Приводи піднесення та опускання електродів переключаються на ручне управління, і електроди піднімаються на висоту, що дозволить зробити выкатку візки із выплавленным у ванні печі блоком периклаза.
Після закінчення плавки поверхню блоку засипається шаром вихідного сировини і крізь 30 хв блок транспортується на електромагнітної сепарації на потоках чи лінії сепарации.
Для магнітної - сепарації порошки в кюбелях пофракционно подаються мостовим краном в прийомні воронки над сепараторами. Сепарація виготовляють барабанному сепараторе ЛБСЦ-83−50 з діаметром барабана 600 мм. Подача матеріалу на який досі живить лоток сепаратора регулюється з допомогою шибера і повинна бути 900−1400 кг/ч. Частота обертання барабана 75 об./хв. Вона відповідає найбільшому вилучення заліза в магнітний продукт. Після сепарації порошки засипають за фракціями в кюбеля, які стоять на переду точних візках, чи м’які контейнера подаються на отгрузку.
Порошки з плавленого периклаза, призначені виготовлення виробів, в кюбелях пофракционно чи скільки завгодно автотранспортом подаються у цех магнезіальних виробів № 2.
Збереження всіх порошків складі готової продукції виробляється у кюбелях, мішках і резинокордовых контейнерах.
III. ФІЗИКО-ХІМІЧНІ ОСНОВЫ ПРОИЗВОДСТВА.
У процесі плавки вихідний матеріал відчуває складні фізико-хімічні перетворення. Зростання кристалів периклаза ввозяться різних ділянках блоку за п’ятьма основним механізмам (рис. 3.1).
У результаті неоднорідного температурного режиму, різночасного зростання кристалів різноманітні механізмам і впливу гравітації при плавленні периклаза відбувається помітна диференціація компонентів розплаву, і окремі зони блоку збагачуються оксидом магнію, тоді як домішки накопичуються в шкірки, центральної зони і плавильної пилу. Найбільшому перерозподілу у блоці піддаються оксид кальцію і кремнезем й у меншою мірою — оксиди заліза і алюминия.
Виплавлений блок неоднорідний за хімічним складом, щільності, макроі микроструктуре. Неоднорідність обумовлена його зональным будовою, визначальним ступенем розплавлювання матеріалу, умовами кристалізації в різних ділянках, міграцією домішкових оксидів та інші чинниками. Блок то, можливо умовно подразделен п’ять зон (рис. 3.2): центральну шириною 400−500 мм, периферійну — 250−300 мм, освіти монокристалів іноді столбчатого будівлі, розташовану між внутрішньою частиною блоки і зовнішнім шаром, — 100−200 мм, бічну скоринку — 250−350 мм, нижню скоринку — близько 200 мм.
Рис. 3.I. Схема зростання кристалів периклаза при электродуговой плавке:
I — областьспрямованої кристалізації з розплаву; II — область об'ємної кристалізації з розплаву; IIIгалузь освіти пара і парофазных перетворень; IVобласть кристалізації із парів; V — область збірною перекристаллизации;
1 — графітовий електрод; 2 — електродна дуга; 3 — пари оксиду магнію і продуктів його дисоціації; 4 — дзеркало розплаву; 5 — розплав; 6 — зона монокристалів; 7 — напрям тепловідведення при спрямованої кристалізації з розплаву; 8 — кристали периклаза; 9 -напрям тепловідведення при об'ємної кристалізації розплаву; 10 — кірка; 11 — нитковидні, кісткові і изометричные кристали периклаза, що утворилися з парів; 12 — осип; 13 -напрям міграції внутрикристаллических пір; 14 — собі напрямок руху внутрикристаллических легкоплавких включень; 15 — напрям термокапиллярного перенесення легкоплавких примесей.
На поверхні блоку залишається недоплав (осип) біла маса, що є суміш порошку, близького за складом до каустическому магнезиту, і шматків частково разложившегося брусита.
Рис. 3.2. Схема зонального будівлі блока;
1 — центральна зона; 2 — периферійна зона; 3 — зона монокристалів; 4 — бічна кірка; 5 — нижня кірка; 6 — осип (недоплав).
Щодо хімічного складу периклаза по зонам показує, що чисті різниці перебувають у монокристальной і периферійної зонах. При плавленні брусита у тих зонах міститься менше оксидів заліза, аніж за плавленні магнезита, однак цьому разі центральної зоні значно більше кремнезему і СаО. У зовнішніх зонах блоку (бічний та нижньої кірках) міститься значну кількість СаО, Al2O3, внаслідок міграції домішок, зумовленої градієнтом температури. Ця міграція, мабуть, обумовлена ще й гравітаційними силами. У нижню скоринку міграція домішок найбільша. Мікроструктура різних зон різний. У внутрішньої частини блоку як і периферійної, і центральної зонах силікати представлені переважно мервинитом.
ЗСаО — МgО · 2SiО2, що характеризується полисинтетическими двійниками і показниками заломлення Ng = 1,724, Np= 1,706. Багато силікатів, особливо у центральної зоні, у якій утворюють значні скупчення як у кордоні кристалів, і всередині них. Спостерігається спрямованість міграції силікатів по градієнту температур.
Бічна кірка також має дуже багато силікатів. Силікати представлені мервинитом, зміст якого сягає 10−15%. У зоні монокристалів присутній менш 1% 2СаО· SiО2. Розмір кристалів надає помітне впливом геть коефіцієнт лінійного термічного розширення периклаза (табл.3.1).
Таблиця 3.1. Термічне розширення плавленого периклаза |Зона |Середній |Коефіцієнт лінійного| | |розмір |термічного | | |кристалів, |розширення ?•108 | | |мм |град-1 в інтервалі | | | |20−1450 °З | |Центральна |0,2−0,3 |10,4−12,0 | |Периферійна |0,6−0,9 |13,8−15,5 |.
Периферійна зона блоку з великим розміром кристалів периклаза має більший коефіцієнт лінійного термічного расширения.
Встановлено, що структура блоку, характер зональности і кількість домішок в периклазе можна регулювати харчуванням печі шихтою, швидкостями плавлення і охолодження. Збільшення тривалості плавки позитивно б'є по товщині зони монокристалів і розмірі кристалів периклаза. Збільшення швидкості плавки дає підстави отримувати плавлений периклаз досить високої якості. Разом про те, розмір кристалів й розмір їх удільної поверхні залежить від чистоти вихідного сырья.
Плавка периклаза відбувається в відновлювальної середовищі, що пов’язаний із згорянням коксу при розжиге і електродів. Вплив відновлювальної середовища обумовлює поява периклаза металевих включень і включень вуглецевого речовини. Виявлені в кристалах периклаза із окремих ділянок блоків тонкодисперсные включення металевого магнію засвідчують відхиленні складу периклаза від стехиометрического за температур, близьких до температур його кристалізації. Кількість включень різних типів залежить від чистоти вихідного сырья.
Примесные оксиди в плавленом периклазе виявляються вигляді форстерита, монтичеллита, мервинита, двохі трехкальциевых силікатів, твердих розчинів магнезиоферрита і магнезиовюстита. Можливо обмежений розчинення в периклазе оксиду кальцію. Силікати, що утворюють плівки на межкристаллических межах периклаза, мають певної просторової протяжністю, тісно що з удільної поверхнею кристалів периклаза. Величина удільної поверхні силікатів, як більше легкоплавкой фази, істотно впливає на прочностные і електричні властивості периклаза.
Здрібнення периклаза супроводжується великим намолом заліза, що викликає необхідність наступної магнітної - сепарації. Встановлено, що залізо витягається як металевих включенні природи і магнезиоферрита. Виявлено також, що при подрібнюванні периклаза з його зернах утворюються «примазки «заліза, і усе веде до незначному потрапляння частинок периклаза в видобуту магнітну фракцію. Разом про те, спостерігається часткове вилучення в магнітну фракцію немагнітних оксидів (SiO2 і СаO) як силікатів, що з наявністю у яких частинок металевого заліза. Отже, магнітна сепарація як очищає периклаз від заліза, але знижує зміст силікатних примесей.
З допомогою комплексні методи дослідження було вивчено будова кристалів периклаза. Процес кристалізації периклаза при охолодженні розплаву супроводжується освітою недоліків у кристалах. Ці дефекти обумовлені внутрішніми напругами, виникаючими в кристалах периклаза при охолодженні і приводящими до пластичної, пружною й тендітної деформаціям, і навіть впливом домішок, їхнім виокремленням кристалічні, склоподібні чи газові включення до кристаллах.
Дефекти кристалів в плавленом периклазе може бути підрозділені на дві группы:
— дефекти першого роду, зумовлені внутрішніми напругами; до них ставляться сліди механічної деформації, лінії ковзання, механічні двійники, блокове мозаїчне будова, тріщини спайности і микротрещины;
— дефекти другого роду, зумовлені наявністю примесей:
Дефекти в кристалах підвищує електропровідність та здатність до поглинання вологи, полегшує руйнація під впливом шлакових і агресивних середовищ і т.д.
Напрям блоку ведуть поступово, повільно піднімаючи температуру підйомом електродів з печі принаймні розплавлювання матеріалу. Піч для плавки не футеруют, оскільки футеровкой служить шар непроплавленой шихти, який завше залишається між корпусом і расплавом. У поперечному сечении блок плавленого матеріалу утворює трикутник, решта пічного простору циліндричною печі представлена непроплавленой шихтою як спеченной палітурки і осыпи.
Кристалізація розплаву у блоці починається у процесі плавки знизу і з боков.
Основний двигуном міграції домішок в периферії блоку є зворотна сегрегація, діюча за горизонталлю блоку, основу якої лежать явища розвитку всередині затверділого розплаву капілярного тиску, возникавшего внаслідок різниці міжфазних натяжений за українсько-словацьким кордоном з твердої фазою розплаву середнього складу і розплаву, збагаченого домішками. Останній процесі кристалізації мігрує в периферійну частина блоку. Зворотний ликвацию створюють переривчастим ходом плавки периклазовой шихти, тобто. чергуванням інтенсивної плавки і витримкою розплаву за нормальної температури плавлення шляхом зміни потужності, введеної в піч. Процес перетворення брусита в периклаз складається з послідовних эндотермических стадій розкладу і плавлення до экзотермической стадії кристалізації расплава.
При температурі 410 °З сирої брусит дегитратирует, перетворюючись на MgO в вигляді периклаза.
[pic].
Кордон палітурки з дегитратированным бруситом відповідає температурі кристалізації монтичеллита, тобто. 1490 °C.
Повнота міграції домішок в скоринку і центральну частина блоку визначається особливостями охолодження і кристалізації розплаву. Температури кристалізації фаз розплаву принципово різняться, визначають лад і характер кристалізації. Першим кристалізується з розплаву периклаз з освітою зони монокристалів високої чистоти за українсько-словацьким кордоном з кіркою, яка надає каталітичне впливом геть кристалізацію. Наявність градієнта температури цій межі, висока пористість палітурки і достатня концентрація MgО в розплаві обумовлюють зростання монокристалів і значну міграцію силікатів в скоринку. При освіті зони монокристалів шляху міграції силікатів в скоринку найбільш прямолінійні і короткі. Верхня межа темпера тури розплаву обмежується точкою його кипіння, мало відрізнялася від температури плавлення MgО, тому існування необхідного градієнта температури за українсько-словацьким кордоном рідкої і твердої, фаз визначається інтенсивністю тепловідведення. При видаленні фронту кристалізації від палітурки і прогріві шихти зменшуються теплоотвод від розплаву і градієнт температури, і отже, припиняється спрямований зростання кристалів. У результаті подальшого наплавления обсяг рідкої фази збільшується, концентрація домішок у ній зменшується. Після закінчення плавки відключення печі починається інтенсивна тепловіддача, наплавленный обсяг переохлаждается й відбувається об'ємна кристалізація із заснуванням щільною і пористої зон, сложенных переважно равноосными кристалами периклаза неправильної і частково дендритной форм. Після відключення печі подэлектродные кратери верхню частину блоку закривають шихтою. Киплячий в зонах горіння дуг розплав MgО швидко віддає тепло шихті, і верхні верстви його кристалізуються, що утрудняє вихід газів з обсягів розплаву. Внаслідок цього у верхній частини блоку утворюється значний обсяг раковистой зони, що з плавленого матеріалу як «тарілок », які чергуються з газовими порожнинами, периклаз цієї зони через високе пористости не застосовується для плит.
Крім звичайного зональної структури блоку, всередині кожної зони виявлено значна хімічна промисловість та структурна неоднорідність периклаза у різних ділянках подовжнього і поперечного перетинів блоку. Так було в ділянках об'ємної кристалізації домішкових оксидів більше, ніж у ділянках спрямованої кристаллизации.
IV. КОНТРОЛЬ ПРОИЗВОДСТВА.
Якість вогнетривів визначається технологією їх виробництва, і залежать стану контроль над дотриманням технології. Контроль виробництва периклазовых плавленных порошків складається з контролю сировини, контролю технологічного процесу, контролю готової продукции.
Технічний контроль виробництва здійснюється відділом технічного контролю (ВТК), правничий та обов’язки, якого визначаються типовим становищем. ВТК являє собою самостійну структурне підрозділ комбінату. Основний обов’язком ВТК є здійснення контролю за якістю своєї продукції, суворого відповідності її стандартам і технічних умов, ВТК контролює дотримання встановленої технології усім стадіях виробництва, і навіть якість поступаемого до цеху сировини, палива, материалов.
Лабораторні роботи з контролю технологічного процесу покладаються на цехову лабораторію. Контроль якості сировини й правильність його складування є першою і дуже важливою операцією у спільній схемою контролю виробництва. Технічні умови сировини залежно з його виду регламентують хімічний склад, вологість, водопоглощение, і навіть показники загального виду — крупность шматків тощо. Результати лабораторних аналізів та клінічних випробувань заносять у спеціальний журнал.
Контроль технологічного процесу — поточний контроль виробництва — предусматривает:
— дотримання технології процесса;
— попередження причин, що призводять до шлюбу продукции;
У цеху розробки схем контролю виробництва регламентують: точки контролю, частоту контролю, персонал, здійснює контроль чи відбір проб; зміст контролю; методи контролю та т.д.
На всі з відбору спроб і здійсненню контролю становлять лабораторні інструкції. За результатами поточного контролю над місяць працівники ВТК становлять звіт за якістю продукції, який обговорюється нараді по качеству.
Вихідний контроль — контроль якості готової продукции.
З цеху може бути отгружены ті порошки, властивості яких цілком відповідають вимогам відповідних стандартов:
Порошки однієї марки комплектують у Комуністичній партії. На кожну партію готової продукції становлять паспорт (сертификат).
Вхідний контроль, сировини й матеріалів. Вступники матеріали підлягають вхідному контролю якості. На матеріали, які на відповідають вимогам ГОСТ чи ТУ, становлять рекламацію і викликають представника поставщика.
Схема контролю виробництва представленій у табл.4.1.
Таблиця 4.1 Контроль виробництва плавленных периклазовых порошків |Найменування |Контрольований параметр |Місце |Частота відбору| |контрольованого | |відбору |проб | |параметра (матеріалу) | |проб | | |Брусит |Масові частки оксиду кальция,|Бункера|На кожну | | |діоксиду кремнію, оксиду |над |плавку | | |магнію, оксиду заліза, |печами | | | |зміна маси при | | | | |прокаливании | | | |Плавлений периклаз |Масові частки оксиду магнію, |Кюбеля |З кожної | |фракції 40−0 |діоксиду кремнію, оксиду |після |блоку | | |кальцію, оксиду заліза, |щековой| | | |зміна маси при |дробилк| | | |прокаливании |і | | |Плавлений периклаз по |Масові частки оксиду магнію, |Кюбель |Середня проба | |фракціям: 2−0,5; 1−0; |оксиду кальцію, діоксиду | |від кожної | |0,5−0; 3−1; 0,063−0 мм |кремнію, оксиду заліза | |блоку, бункера| | | | |чи кюбеля |.
V. АВТОМАТИЗАЦІЯ ПРОИЗВОДСТВА.
Автоматизовані системи управління технологічним процесом дугових електричних печей поділяються на програмні і адаптивные.
Програмні АСУТП підрозділяється втричі группы:
— з програмуванням електричного режими з ходу плавки;
— те електричного і теплового;
— те електричного, теплового і технологічного режимов.
У першому випадку АСУТП включає у собі автоматичний регулятор потужності АРМ, запрограмоване пристрій, регистрирующее і сигнализирующее пристрої і перемикач щаблів напруги ПСН пічного трансформатора ПТ. Зміна програми здійснює оператор, безупинно чи періодично контролюючий стан та перебіг процесу з показанням датчиков.
АСУТП з програмуванням електричного і теплового ре жимов складніше, оскільки, крім регулятора АРМ, в схему запроваджено регулятор теплового режиму АРТ. Управління електричним режимом здійснюється автоматами, котрі за вихідної інформації та заданим алгоритмам виробляють сигнали, пропорційні електричної потужності. Ці сигнали вступають у вигляді управляючих команд для приводу дроселі ПД, перемикача щаблів напруги ПСН, переміщення електродів РПЭ, і навіть високовольтного разъединителя ПВР, пов’язаних між собою відповідно до функціональної схеме.
Адаптивні АСУТП дугових електропечей створюються з урахуванням використання ЕОМ і локальних систем управления.
Технологічний процес плавки в дугового електропечі, як та інших плавильних агрегатах, характеризується цикличностью.
Цикл плавки включає очищення і заправку печі, завантаження шихти, періоди плавлення, охлаждения.
Очищення і заправка печі. Перед плавкою піч очищають: вилучають із подины і укосів непроплавленный матеріал. На подине викладається коксовий трикутник з допомогою спеціального шаблона.
Завантаження шихти. Завантаження шихти виробляється через приймальню вирву як электропечью з ручним шиберным затвором. Шихта складається з природного брусита.
Період плавлення. Основне завдання цього періоду — нагріти сировинної матеріал до температури плавлення, підтримувати цю температуру до розплавлювання сировини й забезпечити необхідний перегрів ванны.
Період плавлення становить зазвичай понад половина тривалості всієї плавки, у своїй витрачається 60−80% загальної кількості електроенергії, споживаної за плавку. На початку періоду плавлення дуги горять між електродами та міцної холодної шихтою. Електричний режим тим часом хисткий. Короткі дуги горять неспокійно, перекидаються з однієї шматка брусита в інший, часто обриваються, викликаючи необхідність короткого замикання для повторного запалювання. У невеликий обсяг під електродами виділяється величезна потужність. У результаті шихті утворюється розплав. Автоматичний регулятор потужності переміщає електроди вгору до того часу, доки встановиться номінальний струм. Чим більший площа дотику розплаву з електродом, то більше вписувалося сила тока.
БІБЛІОГРАФІЧНИЙ СПИСОК.
1. Байсоголов В. Г., Механічне і транспортне устаткування вогнетривкої промисловості. М.: Металургія, 1981. 294 с.
2. Брон В. А., Раєва І.С. та інших. Вплив термообробки на структуру і властивості плавленого периклаза // Вогнетриви, 1982. № 10. С.46−50.
3. Глинков Г. М., Маяковський В. А. АСУШ в агломераційних і сталеплавильних цехах, М: Металургія, 1981. 293 с.
4. Попов О. Н., Рибалкін Д.Г., Соколов В. А. та інших. Виробництво і застосування плавленолитых вогнетривів. М.: Металургія, 1985. 256 с.
5. Симонов К. В. Деякі закономірності формування блоку при плавленні брусита в рудно-термическая печі ОКБ-955 Я // Вогнетриви. 1984, # 9″ З. 36- 39.
6. Симонов К. В., Гапонов Я. Г. та інших. Вплив режиму плавки брусита на якість периклаза // Вогнетриви. 1982. № 4> С.15−23.