Конспект лекцій і на екзаменаційні питання предмета Термічна Обработка
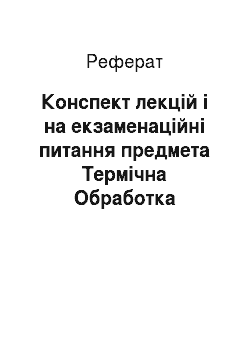
Відпустку стали. Стан загартованих деталей відрізняються дуже сильної неравновесностью структури. Це пов’язано з підвищеної концентрацією вуглецю в твердому розчині, високої щільністю дефектів кристалічного будівлі, і навіть внутрішніми напругами, будівлями і термическими. Через це загартована сталь хоч і мають міцні та непорушністю, одночасно з цією має практично нульової запас в’язкості. Ударні… Читати ще >
Конспект лекцій і на екзаменаційні питання предмета Термічна Обработка (реферат, курсова, диплом, контрольна)
Теорія термообробки. Термообработкой називається теплове вплив на метал із єдиною метою спрямованого зміни його структури та властивостей. Класифікація видів термообработки:
Відпал. Отжигом називають термообробку, спрямовану отримання в металах рівноважної структури. Будь-який відпал включає у собі нагрівання до певної температури, витримку нині певній температурі й наступне повільне охолодження. Мета отжига — зменшити внутрішні напруги в металі, зменшити прочностные властивості і збільшити пластичність. Відпал ділять на відпал 1 роду та 2 роду. Відпал 1 роду — це таке вид отжига, у якому немає структурних змін, що з фазовыми перетвореннями. Відпал 1 роду живуть у своє чергу поділяють на виборах 4 групи: 1. Гомогенізація — відпал, направлений замінити зменшення хімічної неоднорідності металів, образующейся внаслідок рекристалізації. У на відміну від чистих металів, все сплави після кристалізації характеризуються нерівновагової структурою, тобто. їх хімічний склад є змінним як у межах зерна, і у межах всього зливка. Хімічна неоднорідність обумовлена різної температурою плавлення вихідних компонентів. Чим менший ця різниця, тим паче помітна хімічна неоднорідність, получающаяся в зливку. Позбудеться від нього неможливо, можна лише зменшити. І тому застосовують високотемпературний відпал з тривалими витягами (від 2 до 48 годин). При високої температурі рухливість атомів в кристалічній решітці висока і з часом з допомогою процесів дифузії відбувається поступове вирівнювання хімічного складу. Проте усереднення хімічного складу відбувається у межах зерна, тобто. усувається переважно дендритная ізоляція. Щоб усунути зональну ликвацию (хімічну неоднорідність не більше частини зливка), необхідно витримувати зливки при даної температурі протягом кількох років. І це практично неможливо. У процесі отжига на гомогенизацию відбувається поступове розчинення нерівноважних интерметаллидных фаз, які можуть опинитися утворитися внаслідок кристалізації із швидкістю. При наступному повільному охолодженні після отжига такі неравновесные фази большє нє виділяються. Тому після гомогенізації метал має підвищеної пластичністю і легко піддається пластичної деформації. 2. Рекристаллизационный відпал. Холодна пластична деформація викликає на зміну структури металу та її властивостей. Сдвиговая деформація викликає збільшення щільності дефектів кристалічною грати, як-от вакансії, дислокації. Освіта ячеистой структури приміром із зміною форми зерен, вони сплющуються, витягуються у бік головною деформації. Усі ці процеси ведуть до того що, що міцність металу поступово збільшується, пластичність падає, тобто. виникає наклеп чи нагартовка. Подальша деформація такого металу неможлива, т.к. відбувається його руйнацію. Для зняття ефекту зміцнення застосовують рекристаллизационный відпал, тобто. нагрівання металу до температур вище початку кристалізації, витримку з наступним повільним охолодженням. Температура нагріву залежить від складу сплаву. Для чистих металів температура початку рекристалізації tp=0,4Тпл, еК, для звичайних сплавів порядку 0,6Тпл, для складних термопрочных сплавів 0,8Тпл. Тривалість такого отжига залежить від розмірів деталі загалом становить від 0,5 до 2 годин. У процесі рекристаллизационного отжига відбувається освіту зародків нових зерен і подальший зростання цих зародків. Поступово старі деформовані зерна зникають. Кількість недоліків у кристалічній решітці зменшується, наклеп усувається, і метал повертається у вихідне стан. Ступінь деформації визначає розмір зерна після отжига. Якщо вона близька до критичної ((кр=5−15%), то результаті, після отжига в металі виникають великі зерна, які зазвичай небажано. Тому перед рекристаллизационным отжигом деформацію металів виробляють зі ступенем 30−60%. Через війну виходить мелкозернистая однофазна структура, забезпечує хороше поєднання міці й пластичності. Збільшення ступеня деформації до 80−90% викликає появу у металі текстури деформації. Після рекристаллизационного отжига текстура деформації змінюється на текстуру рекристалізації. Зазвичай, це супроводжується різким спрямованим зростанням зерна. Збільшення розмірів зерна, тобто. зниження механічних властивостей, може викликати також надто велика температура отжига чи велика витримка. Тому, за призначенні режимів отжига необхідно використовувати діаграму рекристалізації. Рекристаллизационный відпал може застосовуватися як попередня, проміжна, і як остаточна термообробка. Як попередня термообробка його перед холодної деформацією, якщо вихідне стан металу неравновесное і має певний рівень зміцнення. Як проміжна операція рекристаллизационный відпал застосовується між операціями холодної деформації, якщо сумарна ступінь деформації занадто великою і запасів пластичності металу бракує. Як остаточний вид отжига його застосовують у тому випадку, якщо споживач вимагає поставки напівфабрикатів в максимально пластичном стані. У окремих випадках споживачеві потрібно напівфабрикат, який поєднає певний рівень міцності із необхідним запасом пластичності. І тут замість рекристаллизационного отжига користуються ним різновид — відпал на полигонизацию. Відпал на полигонизацию проводять за нормальної температури, яка нижче від температури початку рекристалізації. Відповідно за такої температурі відбувається лише часткове усунення наклепа з допомогою процесів повернення другого роду, тобто. відбувається зменшення щільності дефектів кристалічною грати, освіту ячеистой дислокационной структури без зміни форми зерен. Ступінь зменшення наклепа залежить, передусім, від температури. Чим ближче до температура до межі рекристалізації, тим менше наклеп, то більше вписувалося пластичність і навпаки. 3. Відпал зі зняттям внутрішніх напруг. Внутрішні напруги в металі можуть бути внаслідок різних видів обробки. Це може бути термічні напруги, які утворилися внаслідок нерівномірного нагріву, різної швидкості охолодження окремих частин деталі після гарячої деформації, лиття, зварювання, шліфовки і різання. Може бути структурними, тобто. які у результаті структурних перетворень, що відбуваються всередині деталі у різних куточках із швидкістю. Внутрішні напруги в металі можуть досягати великий розміру й, складаючись з робітниками, тобто. виникаючими під час роботи, можуть несподівано перевищувати межа міці й спричинить руйнації. Усунення внутрішніх напруг здійснюється з допомогою спеціальних видів отжига. Цей відпал проводиться при високих температурах нижче від температури рекристалізації: tотж=0,2−0,3Тпл є До. Підвищена температура полегшує ковзання дислокаций й під дією внутрішніх напруг, відбувається їх перерозподіл, тобто. з місць із підвищеним рівнем внутрішніх напруг дислокації переміщаються у сфері з зниженим рівнем. Відбувається хіба що розрядка внутрішніх напруг. При нормальної температурі той процес триватиме протягом кілька років. Збільшення температури різко збільшує швидкість розрядки, і тривалість такого отжига становить кілька годин. 4. Патентування. Дивитися термообробку стали. Відпал другого роду — термообробка, спрямовану отримання рівноважної структури в металах і сплавах, відчувають фазові перетворення. При отжиге другого роду нагрівання і наступне охолодження може викликати як часткову, і повну заміну вихідної структури. Повна заміна (((((() в результаті подвійний перекристалізації дозволяє кардинально змінити будова сплаву, зменшити розмір зерна, зняти наклеп, усунути внутрішні напруги, тобто. повністю змінити структуру й властивості деталі. Відпал другого роду то, можливо повний та неповним. Повний відпал супроводжується повної перекристаллизацией. При неповному отжиге структурні перетворення відбуваються в повному обсязі, з частковим збереженням вихідної фази. Неповний відпал застосовується у тому випадку, коли можна змінити будова другій фазі, зникаючої і знову що з’являється у своїй вигляді отжига. Гарт — це термообробка, спрямовану одержання сплаві максимально нерівновагової структури та відповідно аномального рівня властивостей. Будь-яка гарт включає у собі нагрівання до заданої температури, витримку і наступне швидке різке охолодження. Залежно від виду фазових перетворень, які у сплаві при загартуванню, розрізняють загартування з полиморфным перетворенням й гарт без полиморфного перетворення. Гарт з полиморфным перетворенням. Цей вид гарту застосовується для сплавів, де з компонентів має полиморфные перетворення. При загартуванню з полиморфным перетворенням нагрівання металу виробляється до температури, коли він відбувається зміна типу кристалічною грати в основному компоненті. Освіта високотемпературної полиморфной структури супроводжується збільшенням розчинності легуючих елементів. Наступне різке охолодження веде протилежного зміни типу кристалічною грати, однак через швидкого охолодження в твердому розчині залишається надлишкове зміст атомів інших компонентів, тому після цього охолодження утворюється нерівноважна структура. У металі зберігаються внутрішні напруги. Вони викликають різку зміну властивостей, збільшується міцність, зменшується пластичність. При швидкому охолодженні перебудова кристалічною грати відбувається поза рахунок одночасного усунення цілі груп атомів. Через війну замість звичайних зерен в металі з’являється игольчатая структура, що називається мартенситом. Неравновесное стан металу після цього типу гарту є термодинамічно хистким. Тому, аби перекласти метал у більш стійке стан, отримати необхідний рівень внутрішніх напруг, відповідно і необхідні механічні властивості, застосовують додаткову термообробку, яку називають відпал. Гарт без полиморфного перетворення. Застосовується для сплавів, які мають поліморфних перетворень, але мають обмежену розчинність одного компонента й інші. Якщо сплав, у якому вторинні фази, нагріти до температури вище лінії солидус, то збільшення розчинності призведе до розчинення вторинних фаз. Якщо нині такий твердий розчин швидко остудити, то виділення вторинних фаз утворитися не встигне, т.к. цього потрібно час пройти процесу дифузії, освіту інший кристалічною грати, кордонів розділу між фазами. Через війну, при нормальної температурі пересыщенный метастабільний твердий розчин містить надлишок другого компонента. Таке на зміну структури змінює властивості сплаву, міцність може, як збільшитися, і зменшитися, а пластичність, зазвичай, збільшується. Стан металу після такий гарту є термодинамічно хистким. Спонтанно або під впливом попереднього нагрівання метастабільний твердий розчин починає розпадатися із вторинної фази, тобто. ?м (?+?ІІ. Цей процес відбувається називається старінням. Отже, старіння — це термообробка, що здійснюється після гарту без полиморфного перетворення, спрямовану одержання сплаві більш рівноважної структури та рівня властивостей. Відпустку. Відпустку — термообробка, спрямовану зменшення внутрішніх напруг у сплавах після гарту з полиморфным перетворенням. Освіта вторинних фаз після гарту з полиморфным перетворенням завжди супроводжується різким збільшенням внутрішніх. Відповідно максимально збільшуються міцність і твердість, до мінімуму падає пластичність. Щоб самому отримати необхідне співвідношення міці й пластичності, такий сплав після гарту піддають додаткової термообработке: відпустці. Нагрівання викликає зменшення концентрації легуючих елементів в твердому розчині і виділення вторинних фаз. Після гарту без полиморфного перетворення сплав має структуру пересыщенного твердого розчину. Такий стан сплаву — нестабільне і з часом починає змінюватися. Пересыщенный твердий розчин розпадається із потім із нього дрібних включень вторинної фази. Цей процес відбувається на кілька стадій: У першій стадії в кристалічній решітці твердого розчину з’являються зони, збагачені атомами другого компонента. З часом ці зони збільшуються. У другий стадії концентрація атомів другого компонента сягає величини, відповідної за концентрацією виділення вторинної фази. Настає третя стадія, тобто. формування у тих зонах проміжної кристалічною грати, що відрізняється то грати твердого розчину і від грати вторинної фази. На четвертої стадії збільшення концентрації другого компонента призводить до освіті остаточної кристалічною грати вторинної фази і освіті кордону розділу між твердим розчином і вторинної фазою. Так як процес розпаду твердого розчину грунтується, передусім, на диффузионных процесах, він значною мірою заздрості від температури. Що температура, то швидше іде процес розпаду. Якщо температура нормальна, то процес розпаду називається природним старінням, і якщо температура підвищена, то — штучним старінням. У результаті, після старіння структура сплаву є зерна твердого розчину рівноважного хімічного складу, з рівномірно розподіленим за обсягом, величезною кількістю дрібних виділень вторинної фази. Ці виділення, розташовуючись на площинах ковзання, перешкоджають переміщенню дислокаций, вимагають збільшення скалывающего напруги. Відповідно, міцність і твердість сплаву увеличиваются.
Химико-термическая обробка (ХТО). Це одночасне вплив на метал хімічної середовища, тепла із єдиною метою спрямованого зміни складу і властивостей поверхні деталі. Різні види ХТО спрямовані або для підвищення коррозионной стійкості, або міці й твердості, износостойких, антифрикційних властивостей. Змінюючи склад хімічної середовища, за одним і тієї ж деталях отримувати різні свойства.
Термомеханическая обробка. Це поєднання пластичної деформації, упрочняющей термообробки, причому утворюючись під час результаті деформації наклеп зберігається впливає фазові перетворення, що відбуваються під час термообробки. Таке комплексне вплив на метал дозволяє їм отримати рівень властивостей в металі вищий, чим можна отримати після деформації або ж після термообробки в отдельности.
Термообробка сталей. Критичні точки в діаграмі FE-C. Це температурні точки фазових перетворень. Їх заведено позначати літерами Ас і Аr. Ас — точка відповідає нагріванню, температура збільшується. Аr — точка відповідає охолодження, температура зменшується. 1) Крапка АС1 — перша критична точка (лінія PSK). Температура рівноважна, рівна 727 (З. І на цій лінії йде реакція переходу П (А. 2) Крапка АС2 =768 (З. Перехід заліза з магнітного в парамагнитное стан. 3) Крапка АС3 (лінія GS), залежно від хімічного складу, температура змінюється від 911 до 727 (З. Перетворення: Ф (А. 4) Крапка АС4 (лінія NY), температура 1400 (З повагою та вище. Перетворення: А (P.S -феррит. Вище цієї точки намагаються нагрівати. 5) Крапка Асm (лінія SE) А+Ц (((А.
Н агрівання і охолодження. Процес термообробки стали, у разі, включає у собі нагрівання і охолодження, у своїй відбуваються структурні і фазові перетворення. Ці перетворення прийнято розділяти чотирма основні види: 1. П (При підвищенні температури; 2. А (П при зменшенні температури; 3. А (М при загартуванню (температура значно зменшується, швидке охолодження); 4. М (П за відпускання (температура збільшується). По проходженні цих процесів при рідкісних варіантах термообробки залежить остаточна структура сталей отже, властивості деталей. Перше основне перетворення на стали:
П (А (температура збільшується) Перше основне перетворення відбувається, практично, попри всі видах отжига і гарту у процесі нагріву стали. Перетворення перліту в аустенит починається при нагріванні підросли першої критичної позначки АС1. У цьому зерна (Ф+Ц) в перлитном зерні взаємодіють між собою і злочини утворюється зародок зерна аустеніту: Ф+Ц (А Оскільки поверхні розділу між ферритом і цементитом в зерні перліту дуже багато, то початковий час виникає дуже багато зародків аустеніту. Початкова зерно аустеніту завжди дрібне. Збільшення температури нагріву викликає поступове зростання зерна аустеніту. Що температура, тим крупніша зерно. Поруч із зростанням зерна аустеніту відбувається розчинення великих включень цементита і вирівнювання змісту вуглецю в перетині деталей. Зростання зерна аустеніту у різних сталях йде по-різному. Якщо збільшення температури викликає повільний зростання зерна, що більше температура, тим більше зерно, то таку сталь називають спадково грубозернистої. Якщо саме нарощування температури зумовлює зростання зерна лише за нагріванні до температури 950−1000 (З, то таку сталь називають спадково мелкозернистой. Грубозерниста сталь — це нуртуюча, тобто. розпечена Mg і З. У структурі цієї стали немає жодних включень, стримуючих кордону зерен. Тому збіжжя у такий стали збільшується пропорційно зростанню температури. Спадково мелкозернистая сталь — це спокійна сталь, вона розпечена Al.
FeO + Al (Fe + Al2O3 Дрібне включення окису Al стримує кордону зерен від переміщення при нагріванні до температур до 950 (З, але подальше зростання температури викликає різке зростання збіжжя і її розмір навіть перевищити розмір збіжжя у грубозернистої стали. Щоб визначити, якого типу належить дана сталь, проводять випробування на стандартну пробу, тобто. нагрівають сталь до температури 930 (З повагою та тримають 8 годин. Якщо зерно збільшилося, то сталь грубозерниста, а то й збільшилося, то сталь мелкозернистая. Розмір зерна аустеніту є дуже важливою характеристикою. Що більше зерно аустеніту, тим відповідно буде крупніша зерно перліту чи мартенситу, які утворюються після отжига чи гарту. Велике ж зерно завжди небажано, т.к. знижує ударну в’язкість стали.
Второе основне превращение:
А (П (температура уменьшается).
Перетворення відбувається за повільному охолодженні стали, тобто. у процесі отжига. Починається воно освітою перших зародків цементита за українсько-словацьким кордоном зерна аустеніту при зниженні температури нижче точки А1.
Якщо зерно І було великим, відповідно великим буде підписаний і зерно П.
Якщо охолодження йде повільно, то дифузія вуглецю встигає пройти на більше відстань, відповідно утворюється зерно перліту і цементита великий толщины.
Якщо охолодження йде швидко, то дифузія пройти не встигає, образуются.
тонкі пластини Ф і Ц, структура перліту буде дрібнодисперсної, від якої заздрості твердість стали. Що більше перлитные пластини, тим менше твердість і навпаки. Тому, при повільному охолодженні твердість стали завжди вийде меньше.
Изотермическая діаграма распада.
Четвертое перетворення М (П. Структура загартованою стали, тобто М є т/д нестійкою. Це пояснюється, по-перше надмірним кількістю з в твердому розчині. Удругих, велику кількість внутрішніх дефектів кристалічного будівлі, по-третє наявністю залишкового аустеніту. Проте, спонтанно при нормальної температурі сталь неспроможна перейти на більш стійке стан, оскільки для перебудови структури потрібно додаткова енергія. Розпад нестійкою структури можливий лише за підвищенні температури. Така перебудова починається починаючи з невеликого нагрівання до 1000 і закінчується під час досягнення температурою т. А1 (тобто 7000). Умовно процес перебудови температури може бути розбитий втричі стадії: 1. При нагріванні до 2000С. У цьому вся інтервалі температур з М гарту виділяється надлишок вуглецю як дрібних виділень цементита Fe3C. У результат внутрішня напруга в мартенсите зменшується, і такий мартенсит називають мартенситом відпустки. Виділення з мартенситу цементита супроводжується зменшенням обсягу стали. 2. 200−4000С. За цих температурах триває перетворення мартенситу гарту в мартенсит відпустки при зменшенні обсягу й одночасно з цією залишковий аустенит, який в загартованою стали, перетворюється на мартенсит гарту. Цей процес відбувається йде зі збільшенням обсягу стали. Якщо залишкового аустеніту багато, це збільшення обсягу можна компенсувати. Зміна обсягу пов’язані з переходом мартенситу гарту в мартенсит відпустки. 3. 400−6000С. За цих температурах мартенсит відпустки розпадається на суміш феррита і цементита Мотп (Ф+Ц. Що температура, тим більше коштів розмір які утворилися зерен феррита і цементита. З іншого боку, змінюється від і форма цементитных включень. На відміну від пластинчастим форми, що утворюється під час розпаду аустеніту в останній момент переходу їх у перліт, при перетворення мартенситу в перліт частки цементита округлі, тобто сферичні. Таке зміни структури змінюється в’язкість стали. Чим дрібніший від частки цементита і вони більш круглі, то вище в’язкість. Розмір округлих включень цементита залежить від температури, що стоїть температура, тим включень більше, але водночас із збільшенням розміру включень зменшується і твердість і в’язкість стали.
Практика термообробки сталей.
При виготовленні деталей зміни структури та властивостей стали використовують різноманітні операції термообробки. До них відносять відпал, загартування і отпуск.
Відпал сталей. Відпал — це термообробка, спрямовану зменшення міці й твердості і підвищення пластичності стали. Температура отжига визначається його і від змісту вуглецю. Для доэвтектоидной і заэвтектоидной сталей використовують різноманітні види отжига. Це різним призначенням сталей.
Відпал доэвтектоидной стали. Для доэвтектоидной стали можна використовувати як відпал 1 роду, і відпал 2 роду. З отжигов 1 роду для стали застосовують відпал на рекристаллизацию (застосовують для маловуглецевої сталі, тобто змісті з менше 0,25%). Ця сталь варта холодної штампування. При деформації в нею постає зміцнення, тобто наклеп, що знімається отжигом на рекристаллизацию. 1. Рекристаллизационный відпал проходить при високих температурах 6800С, час отжига.
4−12 годин. 2. Відпал на зняття внутрішніх напруг. Цей вид отжига застосовується усунення внутрішніх напруг, які творяться у процесах різання, зварювання, шлифования. Зняття внутрішніх напруг відбувається поза рахунок процесів повернення. Тривалість і температура такого отжига залежить від виду напруг, від розмірів деталей, хімічного складу стали (до.
6000С), 2−12 годин. Більшість конструкційних деталей виготовляється з середньоі высокоуглеродистых сталей. Температура рекристаллизационного отжига таких сталей практично збігаються з температурою т. А1, тому більшість випадків зміни структури та властивостей стали застосовують відпал 2 рода.
Для доэвтектоидной сталі у основному застосовують повний відпал. За такої отжиге панує цілковите зміна структури стали, що дозволяє усунути всі дефекти, викликані холодної деформацією, зварюванням, різкій й дуже далее.
Відпал 2 роду для доэвтектоидной стали прийнято розділяти на виборах 4 вида:
1. повний отжиг.
2. ізотермічний отжиг.
3. нормализация.
4. патентирование.
1. Повний відпал Виробляється з нагріванням стали до температури, перевищує точку А3 з наступним повільним охолодженням разом із промовою. Повільне охолодження викликає повне рівноважний перетворення А (Ф + П. У результаті виходить максимально можлива пластичність, мінімальна твердість і міцність і повне зняття внутрішніх напруг. Якщо внутрішні напрями немає значення то після охолодження з піччю до 5000, подальше охолодження можна вестися повітрі. Повний відпал застосовують усунення дефектів структури, викликаних литтям, холодної деформацією, зварюванням. Основна хиба повного отжига — це її велика тривалість, можлива нерівномірність зеренного будівлі у центрі й лежить на поверхні великогабаритних виробів, викликана неоднаковою швидкістю охолодження. 2. Ізотермічний відпал. При изотермическом отжиге, заготівлі, нагріваються до температури вище т. А3 швидко охолоджують на 100є З нижче точки А1, потім вміщують у піч і за цієї температурі витримують до перетворення А (П. Оскільки перетворення А (П йде при постійної певній температурі й всього обсягу деталі одночасно, такий спосіб отжига дозволяє їм отри мати рівномірну структуру з усього обсягу деталі. Такий вид отжига застосовується для великогабаритних деталей відповідального призначення. 3. Нормалізація. Нормалізацією називають відпал з охолодженням деталі на вільному повітрі. Умови охолодження при нормалізації дозволяють отримати дрібне зерно, проти звичайним отжигом. Зменшення розміру зерна викликає збільшення міці й твердості, попри деякий зниженні пластичності. Особливо це на деталях, містять 0,3−0,6%С. Міцність і твердість таких сталей при нормалізації має проміжне значення між твердістю, отриманої після отжига та непорушністю, отриманої при загартуванню, тому нормалізація таких сталей є основними видами термообробки. Для малоуглеродистых сталей властивості після отжига і після нормалізації практично збігаються, для малоуглеродистых сталей відпал завжди заміняють нормалізацію. Нормалізацію застосовують як і остаточний вид термообробки як і проміжний, наприклад, між операціями холодної деформації зі зняттям наклепа чи перед обробкою різанням зменшення твердості. 4. Патентування. Це особливий вид отжига, що застосовується виготовлення високоміцною дроту. Низька температура перетворення дозволяє їм отримати рівномірну дрібну структуру. Така структура називається троостит. Після отжига сталь піддають холодної деформації, волочению. Через війну дрібної структури та наклепа дозволяють отримати метал міцністю 2000;5000 Мпа.
Відпал заэвтектоидной стали.
1. Відпал на сфероинизацию є неповним, тому при нагріванні повного розчинення цементитных включень немає. У процесі охолодження решта включень цементита під час розпаду аустеніту. Через війну форма включень цементита змінюється. З колишньої пластинчастим перетворюється на округлу сферичну. Тому такий відпал називається сфероинизирующим. Зміна форми включень цементита дозволяє підвищувати в’язкість стали; полегшує процес опрацювання різанням. Така структура стали є ідеальної перед загартованістю. Для прискорення процесу сфероинизации іноді застосовують відпал з циклированием температури на 20−30є З вище або нижчий від точки А1. Такий відпал називають маятниковым. При нагріванні стали відбувається розчинення країв цементитных пластин, при охолодженні ж цементит виділяється рівномірно на всю поверхню. Тому в такому вигляді отжиге процесі сфероинизации йде быстрее.
2. Нормалізація. Застосовується для заэвтектоидной почав із метою усунення виділень цементита на межі зерен. Суцільна цементитная сітка вкрай небажана. Вона утворюється під час повільному охолодженні з високих температур. Нагрівання сталей до температур вище точки Аст призводить до розчинення цементитной сітки по кордонів зерен. При прискореному охолодженні надворі вторинний цементит виділяється як окремих включень, не створюючи суцільний сітки по кордонів зерен. Через війну в’язкість стали восстанавливаются.
Гарт сталей. Загартованістю називають термообробку, що включає у собі нагрівання сталей до температур вище критичних та швидке, різке охолодження, для одержання високої міці й твердості. Розрізняють гарту об'ємну і поверхневу. При об'ємної загартуванню нагрівають і охолоджують обшир деталі, при поверхневою — лише поверхню. Залежно від температури нагріву гарт буває повної та неповної. При повної загартуванню сталь нагрівають вище точки А3. Повна гарт застосовується для доэвтектоидной стали. І тут при нагріванні вище точки А3 сталь має повністю аустенитную структуру і після різкого охолодження має повністю мартенситную структуру. При неповної загартуванню повного перетворення нічого очікувати, і залишився у структурі феррит дасть отримати високої твердості та міцності. Тож у доэвтектоидной стали неповну загартування не застосовують. Для заэвтектоидной стали застосовують лише неповну загартування. У цьому випадку вторинний цементит, який зберігається у стали, додатково підвищує твердість загартованих сталей. Якщо ж застосувати повну загартування, то вторинний цементит розчиняється в аустените. Це супроводжується різким збільшенням зерна. Після охолодження у такому стали відбудеться велика кількість залишкового аустеніту. Це додатково зменшить твердість стали, тому для заэвтектоидной стали повна гарт будь-коли застосовується. Витяг при загартуванню стали має бути таким, щоб встигли пройти все структурні і фазові перетворення. Але вона повинна бути надмірної, ніж викликати зростання аустенитного зерна. Зазвичай орієнтовно витримку деталі приймають з розрахунку 1 хвилину на 1 міліметр товщини для нагріву і + 1 хвилина на 1 міліметр товщини вирівнювання температури в перетині і проходження всіх структурах і фазових перетворень. Охолодження при загартуванню має бути різким, у тому, аби запобігти освіти перліту, але водночас — максимально повільним, аби знизити рівень внутрішніх напруг, які виникають докладно при різкому охолодженні. Внутрішні напруги повинні бути термічні і структурні. Термічні виникають через неоднаковою швидкості охолодження поверхні, і центрів масивних деталей, і навіть при неоднаковою швидкості охолодження і товстих перетинів деталі. Структурні напруги виникають через об'ємного ефекту (v ^) при переході А> М. Залежно від змісту вуглецю цей об'ємних ефект сягає 5−6%. Рівень внутрішніх напруг може бути настільки великий, у результаті відбувається знеформлення деталі чи його розтріскування. Охолодження при загартуванню можна вести в граничних середовищах (вода, олію мінеральну, водо-воздушные суміші). Від швидкості охолодження залежить структура, що у стали після гарту. Якщо швидкість недостатня, то отримує перлитная структура. Вони відрізняються одна від друга різним розміром частинок перліту і цементита. Якщо швидкість охолодження при загартуванню досить великий, у тому, ніж утворився перліт, але дуже мала для освіти мартенситу в сталях, з’явиться проміжна структура — бейнит. Зовні вона не має игольчатую структуру як мартенсит, однак самі голки є феррит, у якому виділяється частинки цементу. Якщо швидкість охолоджується стали перевищує критичну швидкість, то утворюється в мартенсит, який би максимальну твердість в загартованою стали. Найбільш ефективне охолодження забезпечує вода, та її недолік — занадто швидке охолодження в інтервалі мартенситного перетворення. У результаті виникають великі внутрішні напруги. Мінеральне олію навпаки дає малу швидкість охолодження у сфері мартенситного перетворення, але з досить швидку у сфері перлитного превращения.
Способи гарту. А, щоб забезпечити загартування сталей на мартенсит необхідно швидко охолоджувати їх у області перлитного перетворення. Але якщо такою ж швидкістю охолоджувати неї і далі у сфері мартенситного перетворення, то деталі виникають різкі закалочные напруги. Тому бажана проводити охолодження у сфері мартенситного перетворення наскільки можна повільніше, але середовища з перемінної швидкістю охолодження й не існує для різних деталей використовують різноманітні способи охолодження, щоб отримати загартоване стан із мінімум рівнем внутрішніх напруг. 1. Охолодження щодо одного охладителе (воді, олії). Недолік — дуже різкі внутрішні напруги. Щоб їх зменшити застосовують другий спосіб гарту. 2. Гарт у двох середовищах (із води в олію). У цій способу на початку деталь охолоджують у питній воді, до температури нижче перлитного перетворення, а потім перекидають до остаточного охолодження в олію. Такий спосіб складний і вимагає високій кваліфікації робочих, яких потрібно витримувати деталь певну кількість часу у воді. Якщо витримка буде мала, то, при подальшому охолодженні потрапляємо в перлитное перетворення, і гарту нічого очікувати, і якщо витримка дуже велика, то деталях виникають великі внутрішні напруги. 3. Ступінчаста гарт. При східчастої загартуванню нагріту деталь охолоджують швидко до заданої температурі в спеціально гарячої середовищі, як якої використовуються розплави металів чи солей. Час витримки у гарячій середовищі визначаються маркою сталі та то, можливо чітко визначено по секундоміру, після цього йде закінчення охолодження на воді чи олії. Витяг у гарячій середовищі дозволяє вирівняти температуру з усього перерізу деталей, тому при остаточному охолодженні у питній воді, чи олії перетворення аустеніту в мартенсит йде одночасно з усього обсягу деталі, що дозволяє різко знизити рівень внутрішніх напруг. Такий спосіб гарту застосовують для великогабаритних деталей складної форми, щоб до мінімуму знизити знеформлення. 4. Изотермическая гарт. Такий спосіб застосовується для великогабаритних деталей, які можна охолоджувати нас дуже швидко, через небезпеки руйнації. При изотермической загартуванню нагріті деталі вміщують у гарячу середу, нагріту до заданої температурою 350−400 градусів, у якій витримують до проходження перетворення аустеніту в троостит чи бейнит. Після повного перетворення деталь зазвичай охолоджується надворі. Додаткового відпустки після такий загартуванню непотрібен. Температура довкілля вибирається термообработкой, щоб отримати у деталі структуру, що забезпечує задану твердість. 5. Гарт з обробкою холодом. При загартуванню высокоуглеродистых сталей, містять нікель, молібден, вольфрам навіть по повного охолодження до нормальної температури перетворення аустеніту в мартенсит проходить не повністю. Залишковий аустенит має невисоку твердість і тому твердість деталі після гар ту буде недостатньою. Для усунення залишкового аустеніту загартовані деталі додатково охолоджують у сфері негативних температур 70−80 градусів, парами вуглекислоти чи рідкого азоту. Додаткове охолодження викликає перехід залишкового аустеніту в мартенсит і твердість загартованою стали підвищується. 6. Гарт з самоотпуском. Такий спосіб гарту застосовується для деталей, які повинні мати різну твердість у різних куточках. Щоб самому отримати зміну твердість, нагріту деталь вміщують у охолоджену середу лише робочої поверхнею, залишаючи гомілка від поверхні охолоджувальної середовища. Після повної охолодження поверхні деталь беруть із охолоджувальної середовища проживання і з допомогою тепла, збереглися в хвостовій частини, відбувається розігрів робочої поверхні і є її відпустку. Температуру розігріву поверхні контролюють за кольором побежалости.
Поверхнева гарт. Такий спосіб застосовується для виробів, які мають мусить бути поверхню й в’язка серцевина (шестерні, вали). При поверхневою загартуванню нагрівання проводиться не всієї деталі, лише її поверхні. Після нагріву відразу проводиться охолодження. Тому структурні виміру зачіпають лише поверхню. Залежно від способів нагріву розрізняють три «види поверхонь гарту: 1. Гарт зануренням — розігрів поверхні ведеться з допомогою короткочасного занурення деталі в гарячу середу. Після нагріву деталі охолоджують на воді чи олії. Товщина загартованого шару визначаються часом витримки у гарячій середовищі. Недолік — неможливість отримання тонкого загартованого шару. 2. Газопламенная гарт. Розігрів поверхні деталі проводиться з допомогою нагріву полум’ям газової пальники. Гідність способу у його універсальності, недолік — висока температура полум’я викликає перегрів поверхні, і як наслідок — велике зерно, вигоряння вуглецю, легуючих елементів, різкий температурою градієнт, можливо відшаровування загартованого шару. 3. Гарт ТВЧ — струмами високої частоти (индукционная гарт). Розігрів деталі виробляється з допомогою наведення у ній струмів високої частоти. Деталь поміщається всередину індуктора, підключеного до початків струмів високої частоти. Гідність способу — висока продуктивність недолік — потреба у складному устаткуванні, кожної деталі необхідний свій індуктор, наявність шкідливих електромагнітних полів. 4. Гарт з нагріванням поверхні лазером. У цьому способі гарту розігрів поверхні здійснюється з допомогою на неї высокоэнергетического пучка випромінювання. Інтенсивність енергії настільки велика, що поверхню протягом кількох часткою секунд то, можливо нагріта до розплавлювання. Охолодження поверхні після нагріву відбувається поза рахунок тепловідведення всередину деталі. Додаткове охолодження водою не потрібно. Переміщуючи промінь лазера поверхнею можна гартувати як окремі ділянки деталі, і всю її поверхню. В такий спосіб можна гартувати внутрішні поверхні деталі, не гартуючи її зовнішню поверхню. Глибина загартованого шару регулюється часом, висвітлюючи її лазером. За такої способі гарту вони можуть змінюватися і від кількох мікрон до десятків і сотень микрон.
Відпустку стали. Стан загартованих деталей відрізняються дуже сильної неравновесностью структури. Це пов’язано з підвищеної концентрацією вуглецю в твердому розчині, високої щільністю дефектів кристалічного будівлі, і навіть внутрішніми напругами, будівлями і термическими. Через це загартована сталь хоч і мають міцні та непорушністю, одночасно з цією має практично нульової запас в’язкості. Ударні навантаження можуть викликати швидке руйнація деталей. З іншого боку, перехід нерівновагової структури загартованою сталі у більш стабільніша може статися з часом спонтанно під впливом оточуючої температури чи зовнішніх навантажень. Цей перехід пручається зміною обсягу і тому така ситуація неприпустима для високоточних деталей або заради вимірювального інструмента. Тому завжди загартовування деталі піддається додаткової термообработке — відпустці. Розрізняють 3 виду відпустки з температурі: низький, середній і високий. Низький відпустку 150−220 градусів Середній відпустку 350−450 градусів Високий відпустку 550−650 градусов Низкий відпустку застосовується для деталей, які повинні мати високу твердість і міцність. При низькому відпустці мартенсит гарту перетворюється на мартенсит відпустки. Мартенсит відпустки відрізняється від мартенситу гарту відсутністю внутрішніх напруг з допомогою виділення потім із нього надлишку вуглеводнів як дрібних карбідів. Твердість мартенситу відпустки така сама чи значно більше, ніж в мартенситу гарту (58 — 62 HRC). Середній відпустку проводиться для деталей, у яких потрібно максимальний межа пружності. При температурах середнього відпустки відбувається розпад залишкового аустеніту в мартенсит, і далі перехід мартенситу в троостит. Троостит є игольчатую структуру феррита, вздовж голок якого розташовані выделившиеся з твердого розчину дрібні карбиды. Така структура має малим запасом в’язкості, зате високим межею пружності. Тому такий її різновид відпустки застосовують виготовлення пружних деталей машин. Твердість 40 — 45НRС і дуже мала ударна в’язкість. Високий відпустку застосовується для деталей, у яких необхідно поєднання високої ударної в’язкості і з достатньою міцності - це деталі машин, хто з ударними і знакопеременными навантаженнями. У цьому утворюється сорбит. Сорбит є зерна феррита з безліччю точкових і округлих виділень карбідів, рівномірно розподілених за обсягом стали. Твердість 20 -25 НRС. Поєднання повної гарту й високого відпустки називається термічним поліпшенням стали. Такий термообработке зазвичай змушують проходити стали містять 0,3 = 0,6%З. Тому такі стали часто називають улучшаемыми.
Вибір тієї чи іншої виду відпустки залежить від призначення деталі. Якщо деталь повинна мати максимальної твердістю і зносостійкості, то відповідно твердість поверхні мусить бути максимальної й у такий деталі завжди застосовують загартування з низьким відпусткою. Якщо ж місце за технічними умовами виходить максимальна в’язкість, то застосовують загартування з великим відпусткою. Середній відпустку здебільшого використовують при виготовленні пружини. У окремих випадках при швидкому охолодженні деталей після гарячої деформації виникає ефект збільшення твердості з допомогою отримання нерівноважних структур типу троостит чи бейнит. Така сталь з працею піддається обробці різанням, для зниження твердості її піддають високому відпустці за нормальної температури 600−700є із повільним охолодженням. Найчастіше це высокоуглеродистая сталь чи сталь, що містить легирующие элементы.
Відпускна хрупкость.
Отпускной крихкістю називають зменшення в’язкості стали по відпустці в певному інтервалі температур. Відпускна крихкість поділяється на 2 виду: 1. Спостерігається по відпустці в температурному інтервалі 250−350є З — це відпускна крихкість I роду чи необоротна крихкість. 2. Спостерігається в інтервалі температур 500−600є З. Це відпускна крихкість II роду чи поправна. Крихкість I роду й у простих вуглецевих сталей, містять від 0,3−0,6%С. Вона проявляється за відпускання в температурному діапазоні 250−350є З. Причина її появи — виділення карбідів на межі зерен. Це викликає крихкість меж упорядкування і відповідно крихкість всієї деталі. Збільшення температури відпустки викликає розпад мартенситу з усього обсягу деталі відповідно вирівнювання структури, що викликає підвищене в’язкості. Отже, якщо сталь, розташовану за стані відпускної тендітності I роду, нагріти до високої температури, її в’язкість відновиться і повторний нагрівання після охолодження в температурному інтервалі 250−350є З відпускної тендітності большє нє викликає. Тому така відпускна крихкість називається необратимой.
Хрупкость II роду й у среднеуглеродистой стали, що містить легирующие елементи: Si; Мn; Сr. Причому виявляється ця відпускна крихкість лише за повільному охолодженні з температурою високого відпустки. Якщо деталі охолоджувати швидко надворі чи воді, то крихкість II роду не проявляється. Якщо сталь має вже відпускну крихкість II роду, то тут для її усунення потрібно знову нагріти деталь до температури відпустки і швидко остудити. В’язкість відновлюється, якщо знову нагріти поволі охолоджувати крихкість знову з’явиться. Тому така крихкість називається оборотного. Підвищує схильність сталей до відпускної тендітності II роду наявність домішок, особливо фосфору. Тому, аби зробити сталь нечутливою до відпускної тендітності II роду необхідно, по-перше, знижувати кількість шкідливих домішок, особливо фосфору, а по-друге, додавати в сталь молібден чи вольфрам. Відпускна крихкість I роду часто збігається по температурі із середнім відпусткою, тому пружини і ресори характеризуються мінімальним запасом вязкости.
Прокаливаемость сталей. Під прокаливаемостью розуміють здатність сталей темперамент на максимальну глибину. Для відповідальних деталей задля забезпечення максимальної надійності потрібно максимальна, а краще наскрізна прокаливаемость. Збільшення прокаливаемости можливо у різний спосіб, так підвищує прокаливаемость збільшення розмірів зерна аустеніту, підвищення нагріву під загартування, зменшення шкідливих домішок, підвищення хімічної однорідності. Але найсильніше збільшує прокаливаемость введення у сталь легуючих елементів. Більшість їх зрушують с-образные криві вправо. Збільшуючи стійкість аустеніту проти перлитного розпаду, легирующие елементи зменшують критичну швидкість охолодження, наближаючи її до швидкості охолодження серцевини. Сильнішими всіх у цьому напрямі діє хром, а також Ni, Mo, Mn. Найчастіше під час проектування деталі конструктор повинен знати величину критичного діаметра для даної марки стали. Критичний діаметр — це максимально можливий діаметр для даної марки стали, закаливающейся у цьому охладителе наскрізь. Найпростіший метод визначення критичного діаметра — спосіб пробної гарту. І тому від прутка відрізають шматок, нагрівають, гартують і вимірюють твердість по діаметру. Якщо твердість змінюється мало, то деталь прокаливается наскрізь. Найчастіше визначення критичного діаметра застосовується спосіб торцевій гарту. І тому з досліджуваної стали виготовляють циліндричний зразок із довжиною циліндра 100 мм діаметром 25. Зразок нагрівається в печі, та був охолоджується струменем води, спрямованої на торець. Після повної охолодження виробляється завмер твердості, починаючи з торця до того часу, поки твердість не перестане змінюватися. Кордон загартованою зони визначають за величиною закаливаемости стали. Закаливаемость — це здатність стали гартувати на максимальну твердість. Закаливаемость залежить передовсім від змісту вуглецю. Чим більший вуглецю, то вище твердість, то вище закаливаемость. До того ж від змісту карбидообразующих легуючих елементів. Різке падіння закаливаемости відбувається тоді, як у її структурі стає менш 50% мартенситу. Твердість полумартенситной зони залежить від змісту вуглецю. Отже, знаючи зміст вуглецю у цій стали, зі спеціального експериментальному побудованому графіку визначається твердість полумартенситной зони. Після цього експериментально отриманому графіці зміна твердості від торця отримуємо величину а. Після цього з спеціальної номограмме Блантера визначається критичний діаметр для даної марки стали. І тому величину, а відкладаємо верхній масштабної лінійці, і відпускаємо лінію вниз до перетину з лінією відповідностей індивідуальної швидкості охолодження. Від точки перетину відкладаємо горизонталь до використовуваної охолоджувальної середовища: вода, олію чи повітря. Знайшовши точку перетину опускаємо вниз на шкалу критичних диаметров.
Химико-термическая обробка (ХТО). ХТО — це поєднання впливів на деталь хімічної середовища проживання і теплового впливу із єдиною метою зміни хімічного складу і властивостей поверхні детали.
ХТО ділиться на:
1. ХТО з насиченням не металами (З, N, Si, B). 2. ХТО з насиченням металами (Cr, Ni, Ti, Zn). 3. Багатокомпонентна ХТО. Процес насичення поверхні деталі можна умовно розбити на 3 стадії: 1) Створення активних атомів. 2) Перенесення активних атомів до деталі взаємодія його з поверхнею. 3) Дифузія активних атомів вглиб металлов.
Всі ці 3 стадії процесу йдуть послідовно і тому загальна швидкість ХТО визначається швидкістю одній зі стадій, що йде найбільш медленно.
Зазвичай найменша швидкість — це швидкість дифузії в металі. Для прискорення дифузії збільшують температуру. Що температура, тим швидше плине дифузія, то швидше відбувається процес насичення поверхні деталі. Технологічний процес насичення поверхні деталі може відбуватися по-різному: 1) спосіб насичення з порошкових засыпок, тобто. деталь засинають порошками, що містять потрібні елементи. Спосіб самоуниверсальный, найдоступніший. Проте продуктивність його недостатня і потребу велику кількість порошку; 2) насичення з газової фази. Деталі вміщують у спеціальні печі з контрольованій газової атмосферою. Деталі на конвеєрі проходять через піч і після виходу відразу гартуються. Переваги: висока продуктивність, стабільне якість. Застосовується при масовому виготовленні. 3) Насичення з рідкої середовища. У цьому способі деталі вміщують у розплави солей, лугів, металів, містять потрібний елемент. 4) Насичення з пасти. Такий спосіб застосовується для місцевого насичення деталі легирующими елементами. 5) Насичення вакуумом. Деталь вміщують у вакуумну камеру, нагрівають і конденсируют її у атоми легуючих елементів. Застосовується для спеціальних деталей чи деталі, котрі мають окисляться.
Структура поверхневого шару докладно, які виникають при ХТО, залежить від типу взаємодії насыщающего елемента з металом, що є основним компонентом у цій детали.
Якщо насыщающий елемент утворює необмежений твердий розчин, то, при ХТО спостерігається плавне зміна концентрації та структуры.
Якщо ми відома необхідна товщина насиченого легирующим елементом поверхневого шару, то процеси ХТО ведуть до того часу перебувають у кордоні цього нічого очікувати досягнуто необхідна концентрація цього элемента.
[pic] Глибина насиченого шару визначається коефіцієнтом дифузії Д, t — час. Глибина дифузійного шару значною мірою залежить від коефіцієнта дифузії легирующего елемента і південь від часу насичення. Коефіцієнт дифузії визначається самим легирующим елементом, тобто. його природою. Чим більший температура, то більше вписувалося коефіцієнт дифузії, то швидше йде насичення. Товщина насиченого шару визначається, передусім, часом, але для здобуття права збільшити товщину шару вдвічі слід збільшити час обробки (насичення) вчетверо. Якщо взаємодія легирующего елемента з основним компонентом носить складніший характер, то структура шару буде складніша і буде відповідно відбивати фазовий склад, спостерігається з діаграми стану, що утворюється при взаємодії основного компонента з насыщающим элементом.
Якщо взаємодія утворюється на кілька фаз (твердих розчинів чи хімічних сполук), то ми все ці фази створюватимуться в поверхневому шарі у порядку спаду концентрацій. Кожен із верств буде відповідати окремої фазі [pic]. Причому зміна концентрації у тому шарі відповідатиме зміни концентрації з діаграми стану нині температурі. Двухфазные верстви можуть утворюватися при ХТО лише у випадках, коли під час охолодження одне з фаз внаслідок якийабо реакції розпадається на суміш кількох фаз.
Зміна структури поверхні при ХТО становить спрямовану дифузію легирующего елемента. На початку лежить на поверхні утворюється зародки нових фаз, потім вони живуть вглиб деталі, створюючи лежить на поверхні характерну столбчатую структуру.
У кількох випадках після ХТО проводять додаткову обробку, включаючи у собі загартування відпустку у тому, щоб отримати необхідну структуру лежить на поверхні потрібні свойства.
Насичення металів неметаллами.
Основні види ХТО розробити й подати застосовуються для сталевих деталей. У залежність від основного насиченого компонента ці види називають: 1. Цементація — насичення вуглецем. 2. Азотування — насичення азотом. 3. Сульфатирование — насичення сірої. 4. Силицирование — насичення кремнієм. 5. Борирование — насичення бором. Можливе також багатокомпонентне насичення. Насичення З повагою та N — нитроцементация N-S — сульфоазатирование.
1. Цементація стали Цементація викликає процес насичення поверхонь деталей вуглецем з з підвищення твердості і зносостійкості. Цементацию застосовують для деталей, у яких твердість поверхні повинна поєднуватися з в’язкому серцевиною, добре витримує ударну навантаження. Цементації піддають стали, у яких вміст вуглецю вбирається у 0,1−0,25% З. Цементацию насиченням З проводять або з твердої середовища, або у спеціальних газових печах, куди вводяться граничні вуглеводні, містять велике кількість З, тверда середовище складається з вугілля З = 80%, вуглекислої солі Ca Co3. Для активного проходження насиченості вуглецем необхідно забезпечити перенесення З від твердого карбюратора на поверхню деталі. Цей перенесення здійснюється з допомогою існування газової фази, що містить окис вуглецю ЗІ. У печах зацементация відбувається поза рахунок насичення безгазового фази, доставка З лежить на поверхні деталі здійснюється за розпаді граничних вуглеводнів. Процес цементації ведеться при високих температурах порядку 900 — 9500С. Така температура необхідна для переходу структури в аустенитное стан. Температура цементації має бути досить високої, щоб забезпечити аустенитную структуру і ніж викликати зростання зерна. Тривалість процесу цементації визначається необхідної глибиною насыщаемого шару і визначається з швидкості насичення 0,1 мм/час. Загальна тривалість 8−10 годин. Після закінчення процесу цементації деталь охолоджується, у своїй відбувається зміна її структури. Якщо деталь містить 0,1−0,25% З, то що виходить структура була Ф+П. Після цементації структура поверхневого шару відповідає зміною структури з діаграми Fe-C. У цьому лежить на поверхні деталі виникає несприятлива структура, як суцільний сітки вторинного цементита по кордоні зерен. Попри найвищу твердість цементитная сітка сильно охрупчивает метал і може викликати выкрашивание поверхности.
Для виправлення структури та отримання потрібних властивостей деталі після цементації в обов’язковому порядку піддають додаткової термообработке. Вона містить у собі одинарну чи подвійну загартування і подальший низький відпустку. Якщо деталь немає відповідального призначення, то після цементації застосовують одну загартування. Нагрівають до 880−9000С і охолоджують у маслі. Гарт з такою температурою викликає часткове розчинення цементи тной сітки. У результаті замість суцільних виділень вторинного цементита на межі утворюються окремі дрібні включення з усього обсягу металу. Але гарт з такий температурою зберігає крупнозернистое будова стали. Тому в’язкість буде знижена. Відпустку за нормальної температури 160−180є З дозволяє зменшити закалочные напруги без зменшення твердости.
Для відповідальних деталей, які піддаються ударним навантажень застосовують складну ТЕ, що складається із трьох операцій. 1. Високотемпературна гарт 860−880є З, яка для великогабаритних деталей то, можливо замінено нормалізацію. Ця операція термообробки спрямовано усунення цементитной сітки. 2. Гарт 760−780є З (обов'язкова). Повторна гарт дозволяє подрібнити збіжжя у сталі та відповідно підвищити її в’язкість. 3. Низький відпустку (1−2 години). Мета — зняття закалочных напруг. Додаткова обробка після цементації дозволяє перевести перлитную структуру в мартенситную. Це забезпечує збільшення міці й твердості поверхні. Остаточні властивості деталі виходять після цементації при термообработке, поверхню матиме 700−750 НВ (кг/мм2), (58−62 НRО), середина свої властивості не змінює: 180−200 НВ, (120−140 НRв).
Азотирование.
Это насичення поверхні деталі азотом. Азотування проводять у спеціальних газових печах, куди поміщають деталі, а далі подається диссоциированный аміак, тобто. проходить розпад аміаку. Дисоціація аміаку відбувається на спеціальних автоклапанах у присутності каталізатора. Це треба задля здобуття права в піч надходили атоми азоту. Температура азотування 520−550є З, тобто. вона висока, оскільки розчинність азоту в феррите цілком достатня. Тому азотування робити після закінчень термообробки, наприклад, після гарту й високого відпустки. Це дозволяє піддавати азотированию вже готові деталі, минулі обробку різанням, шлифованием, тобто. непотрібен залишати припуски на остаточну обробку як із цементації. Низька температура азотирования Демшевського не дозволяє отримати глибокого насичення поверхонь. Тому звичайна товщина азотированного шару 0,3 — 0,5 мм, а тривалість процесу у 2−3 разу перевищує тривалість цементації. На підвищення ефекту зносостійкості стали подвергаемые азотированию зазвичай містять Cr, Al, Mo. Ці елементи, взаємодіючи з азотом, утворюють власні інгредієнти, які додатково підвищують твердість і зносостійкість поверхности.
38Х2МЮА — нитролоид. У порівняні з цементацией азотування має перевагу й недостатки.
Переваги: 1) Проводиться після остаточної термообробки, тому потребує додаткових припусков. 2) Вища твердість і зносостійкість. 3) Вища стійка міцність деталей. 4) Вища коррозионная стійкість. 5) Вища робоча температура 400−450є С.
Недоліки: 1) Більше тонкий шар. 2) Більше тривалий процес, вимагає складного устаткування, продуктивність меньше.
Нитроцементация.
Це ХТО, коли він деталь насичується одночасно вуглецем і азотом. Вона спрямовано отримання властивостей, які включають гідності й цементації і азотирования одночасно. Якщо насичення З повагою та N відбувається з газової фази, цей процес називається нитроцементацией, якщо процес йде з рідкої середовища (розплавлених ціанистих солей), цей процес називають цианированием.
Процес нитроцементации відбувається за температурі, лежачої нижче температури цементації, але вище температури азотирования (830−880є З). Чим вище температура, тим енергійніше іде процес насичення вуглецем і, відповідно, результати виходять ближчі один до цементації. Чим нижчий температура, то більше вписувалося насичення N й поліпшуючи властивості деталі ближчі один до азотированию.
Спільне насичення N і З дозволяє скоротити тривалість процесу, причому більше низькі температури неможливо засвоюватися зерну, тому сталь зберігає своє в’язке стан. Застосування нитроцементации більш прогресивно, ніж чиста цементація. Після нитроцементации деталь піддають загартуванню і низькому відпустці, причому гарт зазвичай проводиться відразу по закінченні ХТО без додаткового нагрева.
Сульфатирование Після сульфоазотирования деталі легше прирабатываются друг до друга, знижуються втрати енергії, затрачиваемой на обертання деталі. Сульфаазотирование частіше проводять з газової фази, рідше з порошкової засипки. Глибина насиченого шару 0,1−0,2 мм.
Силицирование. Застосовують для деталей, працюючих при підвищених температурах. Впровадження Si в поверхню дозволяє підвищити жаростійкість, тобто. опір поверхні окислювання при високих температур. Після силицирования поверхні утворюється окисли кремнію, або подвійні окисли Fe Si2 O4 — шпилеты. Температура процесу 1100−1200є З. Глибина шару сягає 0,8 мм, але тривалість близько діб. Якщо випробувати газову фазу, то ролі газової фази використовують SiH4 — моносилан.
Силицирование частіше проводять разом з насиченням деталі Al, цей процес називають алюмосилицированием. У результаті поверхні утворюється FeAl интерметаллидная фаза і Al2O3.
FeAl2O4. Це дозволяє додатково підвищити жаростійкість детали.
Борирование.
Застосовують для інструмента гарячого деформованого металу. При насичення сталевих деталей бором лежить на поверхні утворюються бориды: FeB, Ke2B, Fe4B, які збільшують твердість і жаростійкість за нормальної температури 800−1000є З, твердість до 700є З не змінюється зовсім. Борирование проводиться з порошкових засыпок за температур 1000−1100є З. Глибина шару після борирования до 80−200 мкм, але стійкість висока. Недолік — крихкість поверхні. При ударному вплив можливо освіту мікротріщин і скалывание повторного слоя.
Насичення металів металами (диффузионная металлизация). При насиченні поверхні деталі металами відбувається освіту твердих ресурсів на кшталт заміщення, тобто. атоми основного компонента заміщуються в кристалічній решітці атомами легирующего елемента. Процес дифузії по типу заміщення набагато повільніше, ніж у механізму впровадження. Тому процес дифузійної металізації потребує більше високих температур і тривалих витягів. Найчастіше застосовують насичення поверхні Al, Cr, Ti, Zn.
Аллитирование. Застосовують для сталевих і нікелевих деталей з метою підвищення жаростійкості поверхні, утворюються Al2O3. Аллитирование робити двома способами: 1) Аллитирование з порошкової суміші І тут беруть порошок FeAl. Нагрівають до температури 1050−1150є З повагою та витримують від двох до двадцяти годин. Хлор взаємодіє зі Al (ALCL3) і з допомогою освіти цього хлористого Al відбувається перенесення Аl на поверхню з порошку. 2) Занурення деталі в розплав Аl, витримка у ванні і далі нагрівання до робочої температури аллитирования.
Хлорування. Хлорування застосовують з різними цілями: 1) Для малоуглеродистых сталей із вмістом З 0,41% - посередньо чи високо вуглецева сталь. І тут хромування застосовують підвищення твердості і зносостійкості поверхности.
Збільшення твердості відбувається поза рахунок утворення в сталях карбідів хрому, що й підвищують службові властивості деталей: Сч23С6.
На відміну від гальваники, ХТО називають твердим хромированием.
Беруть порошок FeСr, додають Al2O3 і NH4Cl. При хромировании можна отримати товщину до 0,2 мм. М’яка хромування використовується підвищення коррозионной стійкості труб, фланцев.
Титанирование. Насичення Ti підвищує коррозионную стійкість і підвищує кавитационную стійкість. Насичення Ti проводять з порошкових сумішей FeTi.
Цинкование. Захищає від корозії. Насичення Zn проводять зануренням деталі в розплав. Температура розплавленого цинку у ванні 350−550є З. Час перебування у розплавленою ванній 1−10 хвилин. Товщина цинкового покриття 10−30 микрон.
Термомеханическая обработка.
(ТМО). Це поєднання пластичної деформації і термообробки, до чого наклеп, що виник при деформації впливає фазові перетворення під час термообробки. Розрізняють ТМО сталі та старіючих сплавов.
ТМО Сталей. Застосовують 2 виду ТМО: ВТМО і НТМО.
При ВТМО сталь нагрівають до аустенитного стану, потім охолоджують в область високотемпературної стійкості аустеніту, проводять гарячу дифузію, потім відразу роблять загартування і після неї низький відпустку. Під час гарячої деформації аустеніту утворений наклеп частково знімається з допомогою процесів динамічної полигонизации. Ступінь дифузії вибирається такий, аби запобігти повного зняття наклепа з допомогою динамічної рекристалізації, т. е. після гарячої деформації утворюється полигонизованная структура аустеніту з великим кількістю малоугловых кордонів. При загартуванню утворюється мелкоигольчатая структура мартенситу, яка зберігає підвищену щільність дефектів кристалічного будівлі аустеніту. Відтак після ВТМО вдається підвищити міцність стали 20- 30% зі збереженням в’язкості проти звичайній закалкой.
При НТМО гаряча деформація проводиться у сфері низькотемпературної стійкості аустеніту, т. до. температура дифузії невисока, то практично весь наклеп зберігається наслідується в сталях після гарту. НТМО дозволяє різко збільшити дефективность кристалічною грати та за рахунок цієї підвищити міцність майже 2 разу. Однак цьому знижується пластичність і в’язкість приблизно на 15- 20%. Проведення гарячої деформації при низької температури, вимагає дуже потужно го устаткування. Тому НТМО частіше застосовують при прокатці аркушів, профілів чи труб.
А, щоб проводити ТМО необхідно мати достатній інтервал стійкості аустеніту. Тому ТМО проводять, зазвичай, для легованих сталей. Леговані елементи зміщують вправо с-образные криві, збільшуючи цим область стійкості аустенита.
ТМО старіючих сплавов.
Для старіючих сплавів можна застосувати НТМО, ВТМО, ВНТМО і ПТМО. [pic]1. НТМО — низькотемпературна термообробка застосовується частіше всего (80%). При НТМО спочатку проводиться гарт, потім холодна пластична деформація й наступні старіння. При холодної деформації загартованого сплаву виникає наклеп, тобто. підвищується щільність дефектів кристалічного будівлі. При наступному старіння розпад пересыщенного твердого розчину починається зародженням і появою зміцнюючих фаз на дефектах кристалічного будівлі, тобто. відбувається блокування дислокаций интерметаллидными фазами та їх усунення потрібно додаткове зусилля. Отже, міцність сплаву увеличивается.
2. ВТМО — при ВТМО гаряча деформація поєднується з нагріванням під загартування, проте ступінь дифузії має бути таким, ніж викликати зняття наклепа, з допомогою проходження динамічною рекристалізації. Після дифузії в сплаві утворюється полигонизованная структура, яка зберігається після дифузії і після наступного старіння. При ВТМО ефект збільшення міцності сягає 10- 15% за збереження в’язкості. ВТМО можливе тільки у випадках, коли температура нагріву під гарячу деформацію й під загартування совпадают.
3. ВНТМО: поєднання ВТМО і НТМО.
4. ПТМО — попередня ТМО. При ПТМО деформація (гаряча чи холодна) проводяться до гарту, тому основне завдання гарту — це провидіння нагріву і охолодження буде настільки швидким, щоб, недопущення зняття наклепа, т. до. зробити це важко, то ПТМО застосовується дуже редко.
Леговані і спеціальні стали. Легованими чи спеціальними називають такі стали, які у своєму складі крім вуглецю містять додаткові добавки, запроваджене склад із єдиною метою спрямованого зміни її властивостей. Такі добавки називаються легирующими елементами (добавками). Основне відмінність легуючих елементів від домішок у тому, що їхня кількість визначається необхідної мірою зміни властивостей стали, тоді як домішок кількість визначає допустиму міру погіршення властивостей. Одні говорили і самі елементи можуть зайняти позицію домішок чи роль легуючих елементів, але домішки потрапляють у сталь випадково, чи з шихтою, тоді як легирующие елементи вводяться спеціально. До основним легирующим елементам відносять: Cr, Ni, Mo, V, Mn, Si, Al. Кількість впроваджуються легуючих елементів може змінюватися від часткою відсотка до десятків відсотків. Вплив легуючих елементів проявляється у зміні структури та, відповідно, властивостей стали.
Вплив легуючих елементів на полиморфное перетворення на сталях. Більшість легуючих елементів, під час введення в сталь, змінюють температуру початку й кінця поліморфних перетворень. 1. Перша група легуючих елементів особливий тим, що знижує точку А3 і підвищує точку А4. До групи входять Ni, Mn, Pt. Запровадження легуючих елементів, які знижує точку А3 і водночас підвищує точку А4, розширюючи область існування аустеніту, називають аустенизаторами. При змісті легуючих елементів більше Скр, структура буде аустенитная, без поліморфних перетворень. 2. Друга ж група легуючих елементів особливий тим, що підвищує точку А3 і знижує точку А4. До групи входять Si, Ti, V, Mo. Запровадження легуючих елементів підвищує точку А3 і водночас знижує точку А4. І тут відбувається замикання області існування аустеніту і за змісті легуючих елементів більше СКР, поліморфних перетворень в стали нічого очікувати. Такі легирующие елементи, які стабілізують Феррит, називаються ферритизаторами. Якщо сталь вводять легирующие елементи з різними впливом на полиморфные перетворення, то остаточна структура стали то, можливо різної, залежно від співвідношення легуючих елементів і температурного впливу, тобто. сталь може бути з ферритной, феррит + аустенит, аустенитной структурой.
Взаємодія легуючих елементів з залізом і вуглецем. По взаємодії з залізом, легирующие елементи діляться втричі групи: 1. Легирующие елементи, відмінні слабким взаємодією з залізом. Такі легирующие елементи або взагалі взаємодіють із залізом, або утворюють тверді розчини дуже малих концентрацій. Наприклад, Pb, K, P. S. Такі легирующие елементи розташовуються, зазвичай, на межі зерен, погіршуючи цим зв’язок з-поміж них. Через війну прочностные властивості падають, але поліпшується оброблюваність різанням (автоматна сталь). 2. Легирующие елементи, відмінні освітою з залізом твердих розчинів. Зазвичай, збільшується міцність і твердість, але з цим одночасно знижується пластичність і в’язкість. Освіта твердих розчинів може бути на кшталт заміщення чи впровадження. Розчини заміщення утворюють легирующие елементи — метали, а тверді розчини впровадження утворюють легирующие елементи — неметаллы (B, N). Освіта твердих розчинів впровадження надто збільшує твердість і знижує пластичність. Лише легуючий елемент збільшує міцність, пластичність, в’язкість і водночас знижує поріг хладноломкости — це Ni. 3. Освіта интерметаллидов. При освіті легирующими елементами хімічних сполук з залізом, утворюються интерметаллидные фази: FeCr, FeAl. Це спричиняє різкого збільшення міці й твердості, але одночасно знижує в’язкість і пластичність. По взаємодії з вуглецем, легирующие елементи діляться на дві групи: Карбидообразующие. До них відносять Cr, W, Ti, Mo. До не карбидообразующим відносять Ni, Al, Cu, Si, Mn. Карбиды ставляться до фазам впровадження, тому їх появу у сталях викликає різке збільшення міці й твердості, з одночасним зниженням в’язкості і пластичності. Легирующие елементи впливають на становище критичних точок в сталях і основних ліній з діаграми Fe-C. Запровадження карбидообразующих елементів підвищує точки А1 і А3, т.к. карбиды легуючих елементів стійкіші і розчиняються в залозі за більш високих температур, ніж звичайний цементит. Тому запровадження легуючих елементів, їхнім виокремленням карбиды, зумовлює необхідність підвищення температур отжига і гарту. Запровадження карбидообразующих елементів зміщує вліво точки P. S і E з діаграми Fe-C, тому, що більше легуючих елементів, тим менше зміст вуглецю в перлите. Зміщення точки Є вліво може спричинить з того що при змісті вуглецю 1,3−1,5% у структурі можуть спостерігатися виділення эвтектики — ледебуриту. У звичайних вуглецевих сплавах ледебурит присутній в чугуне.
Вплив легуючих елементів на фазові перетворення під час термообробки. Запровадження легуючих елементів змінює становище З — образних кривих на діаграмі изотермического перетворення аустеніту. Практично всі легирующие елементи зміщують З — образні криві вправо, а точки Mn і Mk вниз. І тільки один елемент виняток, діє навпаки — це Co. Через усунення З — образних кривих вправо, змінюється критична швидкість охолодження при загартуванню. При змісті легуючих елементів більш 15−20%, інтервал перлитного перетворення зміщується вправо настільки, що з охолодженні надворі перетворення не настає зовсім. Початок і поклала край мартенситного перетворення зміщується до області негативних температур. Через війну Аустенитная структура стали зберігається за будь-яких температурах. Таку сталь називають сталлю Аустенитного класу. Наявність легуючих елементів в стали робить стабільнішим загартоване стан, тобто. мартенсит зберігається при нагріванні у процесі відпустки до вищих температур. Тож якщо у звичайній углеродистой стали мартенсит перетворюється на троостит вже за часів нагріванні до 250є З, то легованих сталях мартенсит може зберігатися до температур 450−550є З. Це дозволяє використовувати таку сталь під час роботи, наприклад, з вищими швидкостями різання, чи ролі інструмент гарячої штамповки.
Зміна твердості легованої стали за відпускання. Збереження твердості легованої стали високої температури відпустки пояснюється підвищеної сталістю мартенситу, і навіть виділенням потім із нього за відпускання величезної кількості дрібних карбідів легуючих елементів: Cr, W, Ti. Цей ефект називається дисперсионным чи вторинним твердением.
Маркування легованої стали. Для маркування легованої стали прийнята буквенно-цифровая форма, в якої кожному легирующему елементу привласнити своя літера, а цифра, яка слід цю буквою показує середнє зміст цього елемента у відсотках. Якщо зміст елемента близько до одиниці, то ніякої цифри не ставиться. Умовно будь-яку марку модно уявити, як чотири частини. 1. Вона може або же не бути, зазвичай літери. Перша частина показує призначення стали: А — автоматна, Ш — шарикоподшипниковая, Р — ріжучий (быстрорежущая). 2. Тут завжди перебувають цифри, що дають вміст у стали углерода.
10, 20, 40 — в сотих частках відсотка (будь-яка сталь, крім інструментальної). Якщо стоїть одна цифра 2−9, це зміст вуглецю в десятих частках відсотка. Якщо ні цифри, той зміст приблизно%. 3. Позначення легуючих елементів і кількість. А — азот (N), Б — ніобій (Nb), У — вольфрам (W), Р — марганець (Mn), Д — мідь (Cu), Є - селен Se), До — кобальт (Co), М — молібден (Mo), М — нікель (Ni), П — фосфор
(P), Р — бір (B), З — кремній (Si), Т — титан (Ti), Х — хром (Cr), Ф — ванадій (V). Якщо цифри немає, той зміст легуючих елементів 1%. Будь-яка цифра дорівнює числу відсотків. Винятки У — 0,003%, N — 0,02−0,05%, Se — 0,3%. Іноді в маркуванню з’являється цифра 1: 15Х1МФ — зміст Cr більше 1%, але вже менше 2%. 4. Літерна частина. Букви наприкінці марки показують якість стали чи метод очищення: А — вищу якість, тобто. занижений вміст шкідливих домішок (30ХГСА) Ш — шлак переплавку, тобто. додаткова очищення продувкой шлаком. СШ — синтетичним шлаком. ВД — вакуумно-дуговой переплав.
Винятки (маркірування для службового користування). 1. Шарикоподшипниковые стали: ШХ6, ШХ9, ШХ15. Цифра показує зміст хрому над цілих, а десятих частках відсотка. 2. Ріжучі стали: Р9, Р18, Р6М5. Цифра після літери Р показує зміст не вуглецю, а вольфраму у цілих відсотках. Вуглецю в сталях однакову кількість — 1,2%. 3. Марки для службового користування. Ці марки не розшифровують хімічний склад, а показують на завод-виготовлювач (Еге — електросталь, Д — дніпроспецсталь). Друга літера може або же не бути: І - дослідницька, П — пробная.
Класифікація легованої стали. Однією загальноприйнятої класифікації легованої стали, на справжній момент, не існує, і тому прийнято розділяти леговані стали з кількох признакам:
1. Класифікація структурою в равновесном стані (після повільного охолодження). Поділяють на виборах 4 группы:
1). Рівноважний состояние.
Доэвтектоидная.
Эвтектоидная.
Заэвтектоидная.
Ледебуритная (карбидная).
2). За структурою в нормалізованому стані (після охолодження на воздухе).
2. Класифікація за якістю (за змістом шкідливих примесей).
1. Звичайного якості (P.S — 0,03%, Р — 0,04%).
2. Якісна сталь (P.S — 0,025%).
3. Високоякісна сталь (P.S — 0,015%).
4. Особливо високоякісна сталь.
Якість впливає міцність, стійкість проти разрушения.
3. Класифікація за змістом легуючих элементов.
Малолегированная сталь — до 2,5% легуючих элементов.
Среднелегированная сталь — 2,5−10% легуючих элементов.
Высоколегированная сталь — понад десять% легуючих элементов.
Якщо вміст заліза щонайменше 45%, то — це сталь. Якщо менше, то -сплав.
4. Класифікація по назначению.
Конструкційні стали: деталі машин, конструкції, вузли, механизмы.
Інструментальні стали.
Стали і сплави зі спеціальними свойствами.
Конструкційні стали. Поняття конструкційної міцності Під конструкційної міцністю розуміють здатність всієї конструкції тривалий час надійно працювати у різних умовах експлуатації без катастрофічних руйнацій. Конструкційна міцність — це інтегральна характеристика, що об'єднує у собі кілька груп чинників. 1. Металургійні чинники (природа матеріалу). Сюди відносять хімічний склад, мікроструктуру, кристалічну грати, наявність дефектів, поліморфних перетворень тощо. 2. Конструктивно-силовые чинники. Сюди відносять конструкцію, напруженосилове стан, масштабний чинник, чинник форми тощо. 3. Зовнішні чинники. Сюди відносять наявність агресивних середовищ, електромагнітних полів, абразивного зносу, температуру. А, щоб успішно протистояти всім що руйнує чинникам під час виборів матеріалу до тієї чи іншого деталі, необхідно враховувати низку параметров.
Вибір стали для деталей конструкційного призначення. 1. Міцність. Першої характеристикою, через яку здійснюють вибір стали до тієї чи інший деталі, є міцність. Проте міцність конструкції розраховується іноді ні з краю міцності ?У, а з краю плинності ?0,2, т.к. величина 0,2 — це ?=0,2%, тобто. максимально допустима деформація. Якщо деформація буде більше, то знеформлення деталі призведе до відмови механізму результаті заклинювання чи руйнації. Тому, за виборі стали під той чи інший деталь міцність оцінюється по межі плинності. 2. Критичний діаметр. Більшість конструкційних деталей під час виготовлення піддається упрочняющей термообработке, у своїй властивості стали після термообробки в значною мірою залежить від того, прокалилась чи деталь наскрізь чи ні. Якщо деталь масивна і містить легуючих елементів, то після гарту серцевина залишиться незагартованої. Такі деталі будуть погано працювати на розтягнення, і особливо погано протистоятимуть знакопеременным навантажень, тобто. опиратися втоми. Тож деталей, працівників удар чи на втома, завжди ставляться вимоги наскрізний прокаливаемости. Прокаливаемость стали оцінюється по критичного діаметру. Критичний діаметр — максимальний діаметр, котрі можуть загартуватися наскрізь в заданому охладителе. Отже, під час виборів марки стали максимальний розмір деталі в сечении може бути менше, або дорівнює критичного диаметру.
Для зручності вибору тій чи іншій марки стали для деталей різного розміру, застосовуються спеціальні таблиці, де всі стали розставлено з двох параметрів — краю плинності після термічного поліпшення і критичного діаметра. Табл. 3. Хладноломкость. 4. Ударне в’язкість. Якщо деталі призначені до роботи при негативних температурах, а як і умовах ударного навантаження, тобто. динамічних навантажень, то такими параметрами, якими проводиться вибір стали, є температура полухрупкости Т50, а як і ударна в’язкість аn чи в’язкість руйнації К1С. Температура полухрупкости показує температуру, коли він 50% зламу носить в’язкий характер, 50% - тендітний. Тобто якщо це кордону хладноломкости деталі. Знаючи робочу температуру, завжди потрібно вибирати таку сталь, щоб кордон хладноломкости панувала 20−40є З нижче робочої. Для зниження хладноломкости вводять Ni, Mo. В’язкість стали залежить від розмірів зерна: чим дрібніші зерно, тим більша в’язкість. Для підвищення в’язкості вводять Ni, Mo, Mn, W. 5. Додаткові чинники. Якщо з умов праці деталі піддаються додатковим видам зносу (абразивний знос поверхні, окислювання поверхні в агресивних середовищах, вплив підвищених температур), то крім типових чинників під час виборів марки стали враховуються й додаткові, і підбираються відповідних заходів для протидії що руйнує чинникам (поверхнева гарт, ХТО, поверховий наклеп, обдувка дробом, песком).
Низкоуглеродистые цементуемые стали. Ця група сталей варта виготовлення деталей, які мають підвищеної твердістю, міцністю, зносостійкості поверхні і є одночасно в’язкому серцевиною. Кількість вуглецю у тих сталях 0,1- 0,25%. Запровадження додаткових легуючих елементів необхідно, колись всього, підвищення міцності серцевини. Шар цементації 0,6−1,2 мм, температура цементації 950−980є З, витримка, з швидкості цементації, 0,1мм/час. При масовому виробництві цементацию проводять у газових печах, при штучному чи мелкосерийном виробництві - у твердій середовищі (засинають вугіллям). Якщо цементація проводиться у газовій печі, то гарт виробляється безпосередньо на виході з печі, тобто. без додаткового нагріву. Після цементації всі деталі піддаються упрочняющей термообработке, для відповідальних деталей — подвійна гарт (перша гарт — 850−870є З, друга гарт — 760−780є З) + низький відпустку (180−200є З), для неответственных деталей — одна гарт з цементационным нагріванням (930−950є З) + низький відпустку (180−200є З). Іноді замість першої гарту застосовують нормалізацію (здрібнення зерна, усунення цементитной сітки). Цементируемая сталь містить Cr, W, Ti — карбидообразующие, Ni, Si, Cu — не карбидообразующие. Карбидообразующие елементи підвищують твердість поверхні. 1. Стали з не упрочняемой серцевиною — ст. 10, 15, 20 (прості углеродистые). 2. Стали зі слабко упрочняемой серцевиною — ст. 15Х, 15ХР, 15ХГР. 3. Стали із дуже упрочняемой серцевиною — ст. 12ХН3А, 20Х2Н4А, 18ХНВА, 18ХГТ, 25ХГТ.
Среднеуглеродистые цементуемые стали. Деталі відповідального призначення працюють, зазвичай, за умов знакопеременных, ударних навантажень і тому вимагають застосування сталей, сочетающих такі характеристики як висока міцність, в’язкість, а як і опір усталостному руйнації. Такі характеристики можна отримати роботу в среднеуглеродистой стали, тобто. що містить 0,25−0,55% вуглецю. 1. Якщо до такої стали застосувати повну загартування і неприйнятно низький відпустку, можна отримати дуже високий межа міцності, та заодно дуже маленький запас в’язкості. Тому найчастіше після гарту таку сталь піддають високому відпустці. У цьому межа міцності кілька знижується, зате вдається отримати максимально високу в’язкість, тобто. отримати максимально високу конструкционную міцність. Поєднання повна гарт (820−850є З) + високий відпустку (550−650є З) застосовується для улучшаемых сталей. Структура після такий гарту — сорбит. Кордонів зерен немає. Максимально висока усталостная міцність досягається лише за умови однорідної структури, у цьому випадку деталі повинен мати наскрізну прокаливаемость. Якщо після гарту у центрі деталі структура буде перлитная, така деталь буде непереливки опиратися втоми. 2. Для забезпечення наскрізний прокаливаемости потрібно мати максимально високий критичний діаметр, тобто. максимально можливий діаметр, який прокаливается деталь у цьому охладителе. Критичний діаметр, тобто. прокаливаемость, залежить від багатьох чинників. Але головне з них наявність легуючих елементів (крім кобальту, легирующие елементи зміщують зобразні криві вправо, збільшують стійкість аустеніту, зменшуючи тим самим критичну швидкість охолодження). Через війну при загартуванню швидкість охолодження навіть масивних деталей стає вище критичної, і деталь гартується наскрізь, тобто. основним механізмом впливу легуючих елементів цю сталь є збільшення прокаливаемости стали. 3. Багато деталей з улучшаемой стали працюють у умовах поверхового зносу (за умов тертя). Опір зносу забезпечує висока твердість, тільки після високого відпустки твердість стали становить 23−25 HRC і її замало. Тому і додатковий варіант упрочняющей термообробки для таких деталей застосовують поверхневу загартування чи ХТО (азотування). Добавки V, Ti утворюють дуже стійкі карбиды, які розчиняються при нагріванні під загартування, тому стримують зростання аустеніту. У результаті сталь виходить мелкозернистой і має високий в’язкість. Mo і W вводять у сталь зменшення відпускної тендітності 2 роду. Буква На кінці означає зменшене зміст шкідливих домішок P. S і P. Вибір тій чи іншій марки сталі з цієї групи проводиться, передусім, по межі міці й по критичного діаметру. І тому користуються таблицею, де всі стали розміщені за категоріями міці й критичного діаметру. По критичного діаметру улучшаемые стали поділяють п’ять груп: 1. Критичний діаметр до 20 мм при охолодженні у питній воді. У цю групу входять все прості углеродистые стали 30, 35, 40, 45, тобто. практично нелегированные (найдешевші і легкодоступні). 2. Критичний діаметр 20−40 мм при охолодженні у маслі. У цю групу входять стали 35Х, 40Х, 45Х. 3. Критичний діаметр 40−60 мм. У цю групу входять стали 38ХС, 25ХГСА, 30ХГСА, 35ХГСА, 40Г2, 40ХГР, тобто. стали, містять добавки Cr, Mn, Si. 4. Критичний діаметр до 100 мм. У цю групу входять стали 30ХН3А, 35ХМ, 40ХН, тобто. стали, містять Cr, Ni. 5. Критичний діаметр понад 100 мм (до 1000 мм). У цю групу входять стали 38Х2Н2МА, 35ХН3МА, 40ХНМА.
Высокоуглеродистые пружинні, ресорні стали. 1. Основну вимогу до пружинно-рессорной стали — це той максимальний межа пружності. Розмір краю пружності залежить переважно кількості вуглецю в стали: ніж його прізвища більше, то вище межа пружності. 2. Друге вимога — висока релаксационная стійкість (проти зниження краю пружності). 3. Стійкість при усталостном нагружении. Потрібна високу якість поверхні, додаткова обробка наклепом (дріб, пісок), ніж виникли тріщини втоми. Термообробка пружинних сталей. При виготовленні пружин користуються як гарячої, і холодної деформацією. Гаряча деформація використовується під час виготовлення великогабаритних пружин великого перерізу. Після гарячої навивки застосовують загартування і середній відпустку, структура — троостит. Він є мелкопластинчатую структуру, яка має мінімальним запасом в’язкості, але, оскільки пружини мають працювати лише з пружність, то в’язкість перестав бути обмеженням. При виготовленні пружин невеликого поперечного перерізу можна використовувати патентування, тобто. ізотермічний відпал із наступною холодної деформацією. Після виготовлення й термообробки пружини піддають ретельної обробці поверхні (шліфовка, поліровка, фарбування), щоб усунути концентратори напруг на подальше усунення усталостных тріщин. Підвищити усталостную стійкість можна також ознайомитися обробкою, що створює поверховий наклеп.
Стали для холодної штампування. До цих сталям відносять, передусім, малоуглеродистые почав із змістом З =0,05 — 0,2%. Основні требования:
1. Висока штампуемость, тобто. здатність приймати об'ємну форму з пласкою заготовки.
2. Високе якість поверхні деталі після холодної штампування. Ці вимоги обеспечиваются:
1. Механічними свойствами.
2. Хімічним составом.
3. Структурой.
Вимоги по механічним свойствам:
1. Мінімальна твердість (HRB) < 45 одиниць (55 одиниць — для легованих сталей).
2. Високий межа міцності ?У, низький? Т ([pic]).
[pic]- число текучести.
3. Висока пластичность.
Вимоги з хімічної составу:
1. Зміст З 1400−1500 мПа. Найміцніші досягають? в=3000 мПа. Також мають високим межею плинності ?т > 1350−1400 мПа, тобто. стали — высокопластичные. Высокопрочные стали застосовують у авіації і ракетної техніці, т.к. вказують при заданої міцності знизити вагу конструкції. Щоб самому отримати високу міцність необхідно провести відповідне легування, забезпечити високу чистоту металу, отримати структуру з допомогою термообробки, яка забезпечувала б задані характеристики. Високу міцність, твердість можна отримати й у звичайних вуглецевих сталях після гарту й низького відпустки, та заодно така сталь має високої крихкістю, тобто. неспроможна опиратися ударним навантажень. Тому такі стали зарахувати до высокопрочным можна лише умовно. До высокопрочным сталям відносять почали, які мають високим опором до тендітному руйнації К1С = 200−300 кДж/мІ. На підвищення в’язкості стали, у ній зазвичай вводять дуже багато Ni, Mo, Mn. На підвищення прокаливаемости сталь повинна містити Cr, Si. Для освіти зміцнюючих интерметаллидных фаз додають Ti, Al, W. Незважаючи те що, що З — найсильніший упрочнитель, підвищення його концентрації веде до їх зниження в’язкості. Тому зміст З Тзак. Якщо це основна умова не виконується, то наклеп, утворений при деформації, буде знято з допомогою рекристалізації. І тут необхідно змінити схему процесу. Деформація проводиться не відразу після нагріву, а після витримки й невеликого подстуживания до температури нижче від температури рекристалізації. Технологічно втмо проводять при гарячої прокатці чи гарячому пресуванні. І тут устаткування дозволяє за невеликий відтинок часу продеформировать метал з досить великою деформації. І відразу після цього є можливість швидкого охолодження. Вперше втмо була виявлено випадково при гарячому пресуванні сплавів системи Al — Mg — Si. У час застосовують структурне зміцнення. Сприяє появі прес — ефекту гомогенізація сплавів, а як і запровадження труднорастворимых легуючих елементів (Ti, Zr, Sc).
НТМО. При нтмо холодна деформація проводиться відразу після гарту на початок старіння. Загартована сплав має структуру пересыщенного твердого розчину. І попри збільшення міцності зберігає високу пластичність, тому після гарту може бути піддавати холодного деформированию зі ступенем 15- 20%. Що Виникає наклеп дозволяє міцність рахунок збільшення дефектів кристалічного будівлі. При наступному старінні виділення вторинних фаз блокує дефекти, збільшуючи опір деформації, підвищуючи цим міцність. Холодна деформація проводиться як у прокатному стані, і розтяганням. Розтягнення дозволяє одночасно виправити знеформлення напівфабрикатів, отриману при закалке.
Сплави алюмінію. Алюміній виробляється як хімічно чистий, і технічно чистий. Хімічно чистий позначається А. Далі йдуть цифри, що дають його чистоту Технічно чистий алюміній маркується А. Далі йде цифра, показує зміст алюмінію. Деформируемый алюміній. АТ Основними легирующими елементами, які вводять у склад сплаву, є Si, Cu, Mg, Mn, Zn, Li. Їхню кількість може змінюватися від 0,5 до 12%. Крім цих елементів як микродобавок можуть вводити Ti, Cr, Fe, Zr, Sc. У ролі маркування використовують 3 схеми: 1. Деформируемый алюміній. АМц (N) — Al — Mn. АМg (N) — Al — Mg. АВ, АТ — Al — Mg — Si. Д1, Д16 — Al — Cu — Mg. Литейний алюміній. АЛ (N).
2. Цифрова схема для деформируемых сплавів. Усього 4 цифри: 1 цифра — основа (Al — 1) 2 цифра — система легування (0 — чистий алюміній, 1 — Al — Cu — Mg, 2 — Al — Cu — Mn, 3 — Al — Mg — Si, 4 — Al — Mg, 5 — Al — Mg, 9 — Al — Zn — Mg). 3 і 4 цифра — номер сплава.
3. Ливарні сплави. Аналогічна маркуванню стали. А — Al (основа). 2 місце — легирующие елементи: До — Si, М — Cu, Мг — Mg, Мц — Mn, М — Ni, Ц — Zn. Після кожної літери, відповідної легирующему елементу, стоїть цифра, показує його вміст у цілих відсотках. Якщо цифри немає, то кількість легирующего елемента одно 1%. Залежно від технології виробництва випускаються напівфабрикати з алюмінієвих сплавів після різних варіантів термообробки. І тут до основний маркуванню наприкінці додаються букви і цифри, що дають стан поставки: А — плакировка. Б — технологічна плакировка. М — отожженный. П — полунагартованный. М — нагартованный. Т — твердий (гарт + природне старіння). Т1 — гарт + штучне старіння. ТН — загартований, нагартованный і, природно состаренный. Т1Н — загартований, нагартованный і штучно состаренный. Т1Н1 — загартований, посилено нагартован і штучно состаренный.
Сплави, не упрочняемые термообработкой. До цій групі ставляться технічний алюміній, деформируемый алюміній, сплави Al з Mn (АМц), Al з Mg (АМг).
Сплави Al з Mn (АМц). Mn утворює з Al интерметаллидную фазу AlMn6, що дає эвтектику при температурі 658є З при змісті Mn 1,95%. Кількість Mn, що може перейти у тверде розчин, становить 0,5% при 500є З. Попри обмежену розчинність Mn в Al, ефект від участі упрочняющей термообробки настільки невеликий, що це сплави вважаються не упрочняемыми термообработкой. Mn підвищує міцність Al, у своїй зберігається пластичність, висока коррозионная стійкість, свариваемость. Тому з цього сплаву роблять листи, стрічки для холодної штампування. Термообробка: рекристаллизационный відпал 500є З — 1 годину. Збільшення температури або часі витримки можуть призвести до крупнозернистости. Для подрібнення зерна вводять Ti. Підвищити міцність можна тільки наклепом.
Сплави Al з Mg (АМг). Mg, розчиняючись в Al, сильно збільшує її міцність. Кожен відсоток Mg збільшує міцність на 30 мПа. Проте міцність збільшується з допомогою ефекту растворного зміцнення. Виділення вторинної фази після гарту й старіння дає помітний ефект зміцнення лише за змісті Mg в сплаві 8%. Сплави для холодної деформації містять трохи більше 6% Mg. Ці сплави також вважаються не упрочняемыми. АМг1 — 1,1% Mg. АМг2 — 2,5% Mg. АМг3 — 3,2% Mg. АМг5 — 5,5% Mg. АМг6 — 6,5% Mg. Перші три сплаву йдуть на виготовлення аркушів обшивки. АМг5 і АМг6 використав важко навантажених деталях, добре зварюються. Основний вид термообробки: відпал 450−470є З, тривалість 0,5−3 години. Сплави АМг можна зміцнювати деформацией.
Сплави, деформируемые і упрочняемые термообработкой.
Сплави Al — Cu — Mg. Дюралями називають сплави Al з Cu, яких додатково додають Mg і Mn. Упрочняются ці сплави з допомогою гарту без полиморфного перетворення і наступного старіння. Виділення зміцнюючих вторинних фаз дозволяє блокувати дислокації і опір деформації. Особливістю термообробки дюралі є дуже вузьке інтервал закалочных температур. Якщо сплав недогреть, то ми не відбувається розчинення вторинних фаз і ефекту гарту нічого очікувати. Якщо сплав перегріти, то кордонів зерен з’являється рідка фаза, відбувається усадка, утворюється микропористость і різко знижуються міцність і пластичність. Після нагріву і витримки перенесення деталей з печі в закалочный бак має проводитися нас дуже швидко (трохи більше 30 сек). Тож гарту алюмінієвих сплавів будують спеціальну піч. Після гарту проводять старіння. Для жароміцних дюралей застосовують штучне старіння (120−160є З) від 4 до 12 годин. 1. Дюралі середньої міцності Д1, Д6. 2. Дюралі підвищеної міцності Д16. 3. Дюралі жароміцні Д19, ВАД1. 4. Дюралі підвищеної пластичності Д18. Великим недоліком є погана коррозионная стійкість. На підвищення коррозионной стійкості проводять плакировку. Стали груп 2 і трьох підлягають загартуванню і штучному старению.
Сплави Al — Si — Mn. Основні стали групи: АВ, АД31, АД33, АД35. Дані сплави використовують із виготовлення обшивки літаків. Термообробка: гарт 540−560є З (охолодження надворі чи олії) + штучне старіння 160−180є З. Сплави ставляться до среднепрочным.
Сплави Al — Zn — Mg — Cu. Основні стали групи: В93, В95, В96, В96ц. Щодо хімічного складу: 6−8,5% Zn, 2−2,5% Mg, 1−2% Cu. Сплави цієї групи мають підвищену міцністю. Термообробка: гарт 450−470є З (охолодження в киплячій воді) + штучне старіння 175є З. Якщо потрібно максимальна в’язкість, то сплав піддають перестариванию (Т2). Высокопрочные сплави використовують із важко навантажених елементів каркаса літаків. Недолік даних сплавів — погана коррозионная стійкість, хрупкость.
Сплави Al — Cu — Mn. Основні стали групи: Д20. Дані сплави є жаропрочными. Робітники температури від -250є З до 250є З. Упрочняются термообработкой, добре зварюються, мають хорошу коррозионную стойкость.
Сплави Al — Zn — Mg. Основні стали групи: 1915, 1925. Понижено кількість Zn. Дані стали розроблено для заміни АМг6. Стали добре зварюються, мають хорошу коррозионную стійкість. Упрочняются термообработкой (гарт + старіння). Сплави ставляться до среднепрочным.
Сплави АК. Основні стали групи: АК4, АК41, АК6, АК8, АК10, АК12. Ці сплави для гарячої штампування. Сплави ставляться до групи високоміцних. Вони упрочняются термообработкой (гарт + старіння), не піддаються зварюванні. Добавки Fe і Ni дозволяють отримати у сплаві труднорастворимые упрочняющие фази. Тому деталі не втрачають міцності за нормальної температури 300є З. Разом про те при нормальної температурі міцність і пластичність менше, ніж в дюралей.
Сплави Al — Li — Cu, Al — Li — Mg. Li має хорошу розчинність і упрочняет сплав. Запровадження Li підвищує пружність і жорсткість конструкції. Сплави мають погану технологічність і сильно окисляются.
Спеціальні алюмінієві сплавы.
Основные стали групи: САП1, САП2, САП3. Після прокатки отримують або листи, або профілі. У цьому основа сплаву — чистий алюміній. На ролі упрочняющей фази виступає глинозем, в яку вкриті частки порошку. При гарячої деформації окисная плівка дробиться, подрібнюється і рівномірно розподіляється з усього обсягу напівфабрикату. У процесі нагрівання така окисная плівка не розчиняється до розплавлювання, що дозволяє зберегти міцність при робочих температурах до 350є З. Ці сплави є найбільш жаропрочными. При нормальної температурі міцність і пластичність гірше, ніж в дюралей. А максимальна жаропрочность залежить від кількості окислів всередині металу. Якщо ролі вихідних матеріалів брати дрібніший порошок, то об'ємна частка окислів збільшується, відповідно збільшується опір деформації. Тому, змінюючи розмір порошку, змінюють кількість окислов.