Взвешенная плавка нікелевого концентрату в Печі виваженої плавки (ПВП)
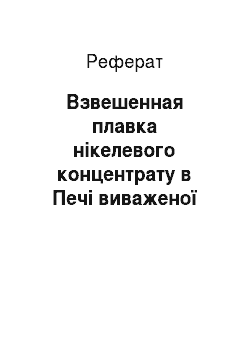
Розплавлені частки падають на поверхню ванни відстійника. У отстойной зоні печі відбувається сульфидно-силикатного розплаву на шлак і штейн. Задля підтримки заданої температури шлаку і штейну в отстойной зоні змонтовано 18 горілок газу. При виході з реакційної шахти собі напрямок руху газів змінюється на 90° — газовий потік проходить горизонтально над ванній в отстойной зоні печі. Потім собі… Читати ще >
Взвешенная плавка нікелевого концентрату в Печі виваженої плавки (ПВП) (реферат, курсова, диплом, контрольна)
року міністерство освіти Російської Федерации.
Норільський індустріальний институт.
Кафедра металлургии.
Курсова работа.
з дисципліни: «Металургія» на тему:
«ВЗВЕШАННАЯ ПЛАВКА НІКЕЛЕВОГО КОНЦЕНТРАТУ У ПЕЧІ ВЗВЕШАННОЙ ПЛАВКИ».
Выполнил: Бельтюков С. Перевірив: Рогова Л. И. Група: Экм-99-У ВО Підпис: _______________ Шифр: 60 800 Дата перевірки: Дата выполнения.
Норильськ, 2000 г.
1. Вибір технології производства…2.
2. Опис основного агрегата…3.
3. Фізико-хімічні основи процесса…5.
4. Техніко-економічні показатели…11.
5. Металургійний расчет…12.
Бібліографічний список.
1. ВИБІР ТЕХНОЛОГІЇ ПРОИЗВОДСТВА.
Плавка в підвішеному стані на підігрітому дуття було здійснено в промисловому масштабі фінської фірми «Оутокумпу» заводі «Харьявалта». У початковому варіанті для плавки застосовували повітряний дуття, підігріте до 400—500 °З. Починаючи з кінця 1960;х років, той процес за ліцензією фірми «Оутокумпу» стали широко застосовувати на металургійних заводах багатьох країн. Нині він впроваджений понад 30 підприємствах для переробки мідних, нікелевих і пиритных концентратів, зокрема. на Надеждинском металургійному заводі. Фінську плавку сьогодні можна вважати найпоширенішим у промисловості і найбільш технологічно і аппаратурно відпрацьованим автогенным процесом плавки сульфідних концентратов.
Особливостями виваженої плавки являются:
— висока продуктивність (питомий проплав 10−15 т/м2 в сутки);
— низький витрати — процес плавки сульфидного концентрату відбувається у режимі, близький до автогенному;
— можливості цілковитого автоматичного управління процесом плавки з допомогою системи «Проскон-103 «» ;
— можливість отримання штейну необхідного состава;
— утилізація сірки з висококонцентрованих сірчаних газов.
Конструкція ПВП і комплекс інших технічних рішень забезпечують отримання пара енергетичних параметрів високий ступінь утилізації сірки з відведених газів, що різко знижує викид двоокису сірки в навколишню середовище, й значно покращують умови праці обслуговуючого персонала.
У плавильному цеху НМЗ є дві печі виваженої плавки однаковою конструкції для плавки мідного і нікелевих концентратов.
Переділ виваженої плавки — структурне підрозділ плавильного цеху HMЗ.
2. ОПИС ОСНОВНОГО АГРЕГАТА.
Конструкція печі для плавки в підвішеному стані на підігрітому дуття досить складна — поєднує у собі дві вертикальні шахти (реакційну і газоход-аптейк) і горизонтальну камеру-отстойник.
Тонкоизмельченная шихта, попередньо висушена до змісту вологи менш 0,2%, подається у системі стрічкових конвеєрів і пневмотранспорта в бункер шихти. З бункера шихта двома скребковими транспортерами «Редлер «подається через звід реакційної камери з допомогою чотирьох спеціальних горілок. Основне призначення пальники — готування та підготовка шихтововоздушной суміші з метою прискорення процесу горіння сульфидов. Перемішування шихти з дутьем досягається разбиванием струменя шихти про конусрассекатель і подачею дуття через повітряний патрубок і розподільну грати. [pic].
Схема пальники печі завода.
1 — дуття; 2 — шихтовая воронка; 3 — завантажувальний патрубок;
4 — повітряний патрубок; 5 — конус-рассекатель;
6 — розподільна решітка; 7 — диффузор Вся піч виваженої плавки виконано вигляді кладки з магнезитового цегли. Підбійка реакційної й аптейка криється у металеві кожухи з листової сталі. У кладку всіх елементів печі закладено велике кількість водоохлаждаемых.
[pic].
Піч для плавки в підвішеному состоянии.
1 — горілка; 2 — реакційна камера; 3 — відстійна ванна; 4 — аптейк;
5 — котел-утилизатор; 6 — паровий воздухоподогреватель;
7 — паливний воздухоподогреватель элементов, що дозволяє значно подовжити термін їхньої служби агрегату. Аптейк безпосередньо сочленен з котлом-утилизатором тунельного типу. У бічний стіні отстойной камери встановлено дві мідні водоохлаждаемые плити з отворами для випуску шлаку, а передній торцевій стіні — чавунні шпури для випуску штейна.
Габарити печі визначено виходячи з технологічних розрахунків вироблених з допомогою ЕОМ, з проектної продуктивності печі і інших вихідних параметрів для проектирования.
У реакційної шахті, для окислення компонентів концентрату, використовується повітря збагачений киснем і підігрітий до 200 °C. Відповідно до теплового балансу — ступінь збагачення дуття киснем на ПВП нікелю становить 26% за середнього складі шихти, що дозволяє реакційної шахті працювати автогенно, не залучаючи додаткового палива Устаткування розраховане на максимальне збагачення киснем до 40%, коли з будь-яким причинам:
1. Теплопотребление шихти увеличится.
2. Збільшаться теплові втрати печи;
3. Підігрівши повітря уменьшится.
Якщо збагачення дуття киснем до 40% через перелічених вище чинників виявиться недостатнім, то тут для поповнення нестачі тепла в реакційної шахті, використовують природний газ.
Розплавлені частки падають на поверхню ванни відстійника. У отстойной зоні печі відбувається сульфидно-силикатного розплаву на шлак і штейн. Задля підтримки заданої температури шлаку і штейну в отстойной зоні змонтовано 18 горілок газу. При виході з реакційної шахти собі напрямок руху газів змінюється на 90° - газовий потік проходить горизонтально над ванній в отстойной зоні печі. Потім собі напрямок руху газу знову змінюється на 90° - газ піднімається по вертикальному аптейку печі вгору. У аптейк інжектується вугільна пил, де й відбувається відновлення сірчистого газу до елементарної сірки. Завдяки такий конструкції печі відбувається досить повне від'єднання сульфидносилікатних частинок, що перебувають у зваженому стані, від газового потока.
Пылевынос з печі виваженої плавки становить 12−15% ваги загружаемой шихты.
Після аптейка гази вступають у котел-утилизатор, де розладнуються з 1350 °C до 550 °C, та був після очищення в электрофильтрах від пилу, надходять в сірчаний цех для уловлювання з газів елементарної серы.
Піч виваженої плавки є головним агрегатом у ланцюзі переробки серосульфидных концентратів. Агрегат має високої інтенсивністю плавлення. У зв’язку з цим піч має складну і різноманітну систему охлаждения.
Агрегат повинен мати високої герметичностью. Порушення герметичності веде до подсосам, що порушує теплової баланс печі, разубоживает що відходять гази збільшує їх обсяги, збільшує витрата відновлювача. Перелічені вище причини негативно позначаються не подальшому опрацюванні газів у сірчаному цехе,.
Усі частини печі виваженої плавки повинен мати високу герметичність, вимагають жорсткої підтримки заданих параметрів, що забезпечується роботою печі в автоматичному режимі з допомогою ЭВМ.
3. ФІЗИКО-ХІМІЧНІ ОСНОВЫ ПРОЦЕССА Процесс плавки сульфідних концентратів з утилізацією сірки з відведених газів дуже складний, на продуктивність печі, повноту перебігу окисних та відновлювальних реакцій впливають багато чинників, основними їх являются;
— розміри частинок та палестинці час перебування частинок в газовому потоке;
— час нагріву частиц;
— швидкість, напрям і послідовність окисних реакцій, вплив температури на кінцеве хімічне рівновагу; - мінералогічний склад концентратів; - вид відновлювача сірчистого ангідриду і вплив температури на кінцеве рівноважний стан відбудовних реакций.
Розміри частинок й розмір удільної поверхні компонентів шихтовых материалов.
Зазвичай руди подрібнюють перед флотацией не більше нижнього класу значущістю від 60% класу — 0,0605 мм до 90% класу -0,088 мм. Середньої величиною зерна флотационных концентратів вважатимуться від 0,07 мм до 0,03 мм.
Процеси нагрівання сульфідних частинок, дисоціації вищих сульфидов і взаємодії сульфидов з киснем пічний атмосфери під час виваженої плавки є типовими гетерогенными процесами, швидкість яких за інших, рівних умов лінійно залежить від величини поверхні розділу на кордоні тверде — газ.
Провівши нескладний розрахунок, можна переконатися що 1 кг матеріалу з питому вагу 4 г/см3 за середнього діаметрі зерна 0,04 мм, що він відповідає розміру зерен флотационных концентратів., має питому поверхню 59,5 м2/кг, Будучи узятим як компактного кулі, хоча б I кг матеріалу має поверхню всього 0,019 м². Отже, здрібнення матеріалу тягне у себе різке збільшення його удільної поверхні, Проте, зайве переизмельчение шихтовых матеріалів небажано, позаяк у цьому випадку зростає пылеунос,.
Рух частинок в газовому потоке.
Дуже важливим параметром процесу плавки в підвішеному стані є час перебування шихтовых частинок серед від часу надходження у простір реакційної шахти до зіткненні з поверхнею розплаву в отстойной зоні печи.
Поскольку і гази, й частки шихти рухаються лише у напрямі згори донизу, очевидно, що час перебування шихтовых частинок у польоті визначиться сумою швидкостей вільного падіння частинки й руху газового потік. У разі плавки сульфідних флотационных концентратів швидкість власного падіння найбільших зерен концентрату вбирається у I м/сек. Сульфидные частки, вдуваемые в реакційну шахту, незначно випереджають газовий потік і час, необхідне проходження частинок концентрату у всій висоті плавильної шахти, одно 0,8 — 0.9 часу проходження газом цього ж шляху, І якщо краще газ проходить шахту печі за 2,8 сік., то частки флотационного концентрату перебуватимуть в підвішеному стані приблизно 2,20 — 2,50 сек.
Нагрев частинок пилу і теплопередача В стадії завантаження шихти в реакційну шахту, шихта підігрівається з допомогою тепла, одержуваного нею при конвективном теплообмене з підігрітим до 200 З технологічним повітрям. Сприймалася часткою теплової потік описується рівнянням .
Q=(x P. S x ((T1-T2).
(- коэф-т передачі тепла конвекцией, ккал/м2/час.
P.S — сприймає теплової потік поверхню, м2.
(- час, час Тепла цього замало запалення сульфидного матеріалу, т.к. навіть сірка залежно від змісту кисню у газовій фазі воспламеняется в інтервалі температур від 260 до 360 °З. Сульфидные ж частки залежно від розміру зерен спалахують при високих температурах від 280 до 740 З. Опускаючись нижче, распыленная шихта потрапляє у зону високих температур, де за рахунок випромінювання від смолоскипа чи футерівки реакційної шахти нагрівається до температур запалення сульфидов.
Кількість переданого тепла з допомогою радіаційного нагріву описується рівнянням Стефана-Больцмана:
Q= P. S x K x (x (T1/100)4-(T2/100)4.
Тепло, отримане поверхнею частки, передається до її центру, Передача тепла вглиб частки, навіть якщо він і дуже мала, здійснюється з допомогою теплопровідності й у випадку кулястої частки підпорядковується уравнению:
qx = Q/(4Пх2 x t)= ((Тп-Тх)/r2(1/x-1/r).
З рівняння слід, що питома теплової потік до центра частки обернено пропорційна квадрату радіуса її. Це означає, що з малих розмірах частинок, які мають зерна флотационных концентратів, нагрівання матеріалу іде у частки секунды.
Реакції окислення сульфидов протікають з великим виділенням тепла. Оскільки для окислення сульфіду необхідний підвід кисню до зони реакції, тo стає зрозуміло, що це процеси можуть протікати лише з поверхні зерен. З цього випливає, що у деякому відрізку часу, починаючи з запалення, від поверхні сульфидной частки виникає додатковий теплової потік вглиб сульфидного зерна.
При запаленні сульфидной частки температура його поверхні стрибкоподібно зростає досягаючи в малі частки секунд 1500−1700°С. Процес окислення сульфидов набуває найвищу швидкість, позаяк у цей момент поверхню зерен максимальна, зміст кисню в газах ще високе та окисная плівка лежить на поверхні сульфидного зерна хіба що зароджується. Середня температура смолоскипа у цій зоні різко підвищується до 1400 °C і більше з допомогою тепла, выделяющегося при інтенсивному окислюванні всієї маси сульфідних зерен. У зоні максимальних температур виділяється основна частина тепла екзотермічних реакцій плавки, т.к. саме тут протікають з максимальними швидкостями більшість реакций.
В останньої зоні, званої зоною усереднення температур, швидкості всіх окисних процесів швидко падають, оскільки, по-перше, падає зміст кисню в газовому потоці і, по-друге, лежить на поверхні окисляющихся сульфідних зерен наростає плівка продуктів реакції, гальмуюча дифузію кисню вглиб зерна. Коли поверхні частки утворюється щільна кірка твердого окисла, позбавлена тріщин та інші дефектів, то дифузія кисню неї надзвичайно утруднена і процес окислення може припинитися, не дійшовши остаточно. Пухкі, трещиноватые плівки гальмують процес у меншою мірою, як і, як і рідкі окисные плівки, швидкість дифузії якими приблизно за три порядку вище, як за тверду плівку. У цілому нині процес окислення в реакційної шахті печі лімітується дифузією кисню через плівки продуктів реакції і зворотної дифузієюсірчистого ангідриду в ядро газового потока.
У гирло реакційної шахти окисні реакції повністю закінчуються. Про це свідчить результати аналізу газу на зміст вільного кисню: парціальний тиск кисню не вдома з реакційної шахти знижується до 10 мм рт.ст.
Диссоциация сульфидов при плавленні в підвішеному состоянии.
У складі концентратів присутні вищі сульфіди, які диссоциируют при нагріванні на нижчі сульфіди і на сірку. Нижче наведені реакції диссоциации.
FeS2(FeS+S.
Fe11S12(11FeS+S.
Fe7S8(7FeS+S.
3NiFeS2(3FeS+Ni3S2+½S2.
2CuFeS2(Cu2S+2FeS+S.
2CuS (Cu2S+S.
3NiS (Ni3S2+S.
2CuFe2S3(Cu2S+4FeS+S.
2Cu5FeS4(5Cu5S+2FeS+S.
У інтервалі температур від 550 З до 650 З першим диссоциирует пірит, тиск дисоціації якого за 631 °C до 0,1 атм. Найбільш стійкий борнит, роз'єднуючий в температур 8400−850°С. Усі реакції тривають від поглинанням тепла. Отщепляющаяся сірка воспламеняется, залежно від змісту кисню в дуття, в інтервалі температур 280 С-560 С.
Кінцевими продуктами дисоціації вищих сульфидов завжди є нижчі сульфіди які надалі частково окислюються, створюючи окисли відповідних металів переходять у шлак.
½S2+O2=SO2 (без катализатора).
½S2+3/2O2=SO3 (з катализатором).
Ni3S2+7/2O2=3NiO+2SO2(.
Cu2S+1,5O2=Cu2O+SO2(.
FeS+1,5O2=FeO+SO2(.
3FeS+5O2=Fe3O4+3SO2(.
Неокислившиеся нижчі сульфіди переходить до штейн. Окислювання сульфидов супроводжується освітою великих кількостей магнетита, особливо у поверхневих шарах частинок. Переокисление заліза до магнетита залежить також від рівня десульфуризации при плавленні. З зростанням ступеня десульфуризации та придбанням багатших штейнов дедалі більша частина заліза перетворюється на форму магнетита. До найважливіших елементарних стадій, які протікають в отстойной камері печі, ставляться: 1) сульфидирование які утворилися в смолоскипі оксидів коштовних металів; 2) розчинення тугоплавких складових (CaO, Si02, AI2О3, і MgO та інших.) в первинних залізистих шлаках процес формування шлаку кінцевого складу; 3) відновлення магнетита сульфидами; 4) формування штейну кінцевого складу і укрупнення дрібних сульфідних частинок; 5) поділ штейну і шлаку. 9NiO+7FeS=3Ni3S2+7FeO+SO2(Cu2O+FeS=Cu2S+FeO.
Образование фаялита.
2FeO+SiO2=(FeO)2SiO2 Розпад магнетита 3Fe3O4+FeS+5SiO2=5(FeO)2xSiO2+SO2(.
Плавкость сульфидов.
Порівняно з окислами сульфіди є як легкоплавкими сполуками. Температури плавлення основних сульфидов, входять до складу мідних і нікелевих штейнов:
Сульфід заліза 1171 С.
Халькозин — 1135 С.
Сульфід кобальту — 1140 С.
Хизлевудит — 788 С.
Эвтектические сплави, освічені двома різними сульфидами, а так ж эвтектики між сульфидом та її металом більш легкоплавки, ніж окремі компоненты.
Штейны при плавленні сульфідних компонентів завжди є многокомпонентными системами. Поїзди штейнов який завжди відповідають складам эвтектик, але з тих щонайменше, температури плавлення штейнов все-таки нижче, ніж температури плавлення які входять у них сульфидов. Зазвичай за нормальної температури 850- 900 °C штейны перебувають у жидкотекучем состоянии, Термодинамика окисних реакцій при плавленні в підвішеному стані Загалом вигляді основну реакцію, яка в реакційної шахті печі, можна уявити наступним уравнением:
MeS+1,5О2= MeO+SO2+Q Ця реакція экзотермическая і його парниковий ефект у часто, при умови нагріву матеріалу до температури запалення, забезпечує мимовільний хід процес без витрат тепла ззовні. Про інтенсивність перебігу тій чи іншій реакції прийнято судити з величині виміру изобарно-изотермического потенціалу системи, яка висловлює енергетичні перетворення на ході хімічного процесу. За всіх самовільних процесах величина (Z має негативний знак, що говорить про вивільненні енергії і віддачі її на систему набік, У цьому вся разі, ми спостерігаємо виділення тепла під час реакції. Чим більший числове значення (Z за негативної знаку, тим енергійніше й глибше протікає реакція. Отже, порівнюючи між собою величины (Z окремих реакцій, можна визначити преимущественность перебігу однієї реакції порівняно про інший. При позитивному значенні реакція неспроможна протікати спонтанно, оскільки на її скоєння необхідні енергетичні надходження ззовні, Величина зміни изобарно-изотермического потенциала.
(Z дозволяє визначити величину константи рівноваги реакції, що характеризує кінцеве стан системи, як у ній завершився мимовільний процес і встановилося рівновагу між вихідними і кінцевими складовими реакції. Ця зв’язок виражається уравнением:
Lq Kкр=-(Z/RT За величиною константи рівноваги можна будувати висновки про напрямку і глибині перебігу процесса.
Восстановление технологічних газів вугільної пылью.
Технологічні гази плавки в підвішеному стані до відновлення мають наступний состав:
SO2 — 12,6; H2O- 8,5; СО2- 5,5, O2- 0,7; N2- 72%; t= 1450°.
Процес відновлення сірчистих газів ввозяться аптейке печі виваженої плавки. Як відновного реагенту використовують подрібнений вугілля з мінімальним змістом летючих компонентів і золи. Оскільки леткі компоненти представлені вуглеводами, їх що у процесі відновлення технологічних газів, які ведуть освіті підвищених кількостей H2S, CS2 і CO, небажані. Підвищений вміст золи у вугіллі призводить до збільшення кількості пилу й шлаку, а, отже, знижує вилучення кольорових металів збільшує енерговитрати. До того ж зола вугілля є причиною освіти настылей в аптейке. По розрахунковим даним пылевынос печі виваженої плавки становить 12−15% від кількості загружаемой шихти, де на кількох частку золи доводиться значна частина. Оскільки вся пил вловлюється й повертається на процес, то збільшення зольності вугілля веде до пропорційного збільшення зворотному пыли.
Зола різних вугілля має різної температурою плавлення. При температурі 1350 °C зола перебуває у полурасплавленном стані, і за виході з аптейка за українсько-словацьким кордоном радіаційної частини котла-утилизатора при зіткненні зі стінками, буде налипать на поверхню футерівки (горловини) і утворювати прирощування. При видаленні настылей тим чи іншим способом, чи то обдмувши пором високого тиску, або повітрям, теж виключена можливість застосування буровзрывных робіт, але це пов’язано про відкриванням оглядових люків, отворів, що у своє чергу можуть призвести до розладу процесу вимушеним зупинкам печи.
Вуглець і леткі компоненти вугільної пилюки взаємодіють із сірчистим ангідридом, відновлюючи його елементарної серы.
Відновлення відбувається у загальної формі по уравнениям:
SO2+C=½S2+ CO2.
SO2 +2Н2=½S2+2H2O.
У цьому мають місце побічні реакції, що знижує вилучення сірки. При взаємодії сірчистого ангідриду з пылеуглем в інтервалі температур 1300−700°С частка які виникають компонентів H2S, CO, CO досить висока. Ступінь відновлення сірчистого ангідриду в елементарну сірку звичайно перевищує 20−25%, т.к. переважна більшість вугілля витрачається освіту побічних продуктов.
Коли газової фазі присутні водневі сполуки, зокрема і вода., кількість небажаних реакцій збільшується, що зумовлює зниження змісту елементарної сірки у газовій фазе.
Через війну відновлення виходить багатокомпонентний газ, і, з практичної погляду, особливої важливості у тому складі представляє сірчистий ангідрид і елементарна сірка. Відновлений газ з аптейка ПВП з температурою 1330 °C вступає у котел-утилизатор. У котле-утилизаторе газ охолоджується до температури 350 °C. Під час цієї температурі ЗІ і CO майже відсутні, а зміст елементарної сірки майже сягає максимума.
При охолодженні газу котле-утилизаторе протікають основні реакции:
CO+½ S2 = COS.
COS+H2O=CO2+H2S.
H2+½S2=H2S.
Из представлених реакцій перша реакція протікає швидко, а наступна реакція надто повільно й у повного перебігу реакції необхідний катализ.
При температурі 1330 °C в аптейке ПВП настає термодинамічне рівновагу між компонентами згаданими вище. Крім відновлення газу аптейке ПВП відбувається відновлення окислів пилу. Загалом вигляді реакцію відновлення компонентів пилу можна уравнением:
4МеО + 3S2 (4МеS + 2 SO2.
Этот процес йде з поглинанням тепла, що знижує температуру відведених газів, Відновлена зворотний пил містить у собі такі сполуки: NiS, CuS, FeS, CoS, ZnS, PbS, As2S2, Cu2Se, SiO2, Аl2O3, CaO, MqO, інші і вільний углерод.
При порівнянні компонентів окисленої і відновленої пылей видно, у процесі відновлення відбувається поглинання сірки і виділення вільного кисню для зв’язування якого вимагають додаткова витрата вуглецю. Отже, можна дійти невтішного висновку, що зниження пылевыноса у процесі плавки вигідно, як з економічної погляду по витраті вугілля, і з погляду зниження безповоротних втрат кольорових металлов.
4. ТЕХНІКО-ЕКОНОМІЧНІ ПОКАЗНИКИ ПРОЦЕССА.
|Показатель |Значення | |Продуктивність печі, т на добу |445,44 | |Питома проплав, т/(м2 x сут) |10−15 | |Зміст О2 в дуття, % |26 | |Температура дуття, З |25−40 | |Зміст Ni, %: | | |У штейне |34,9 | |У шлаку |1,4 | |Пылеунос, % |10−15 |.
5. Металургійний расчёт.
Исходные дані для розрахунку: зміст Ni в концентраті - 8%; cодержание Сu в концентраті - 4%;
Расчёт виробляємо на 100 кг концентрату. Щодо хімічного складу концентрату: Cu — 4%; Ni — 8%; Fe — 46%; P. S — 30%; SiO2 — 3,5%; CaO — 2,3%; MgO — 2%; Al2O3 — 1,38%; інші - 2,82%. По мінералогічному складу орієнтовно 60% міді перебуває у кубаните, 40% в халькопирите, нікель перебуває у пентландите.
Склад концентрата.
Таблиця № 1 |Ni |6,9 |33,48 | |Cu |3,41 |16,55 | |P.S |4,88 |23,7 | |O2 |0,41 |2 | |Fe |5,01 |24,3 | |Разом |20,61 |100 |.
Перейде в шлак заліза: 43−5,01=37,99 кг Флюсы:
Для отримання кондиційних відвальних шлаків й у з великим змістом Fe в вихідному сировину у шихту вводяться флюсующие присадки. Основним флюсующим компонентом в шихті служить песчаник.
Приймемо наступний склад песчаника:
SiO2 — 80%, MgO — 1,5%, Al2O3 — 8,7%.
CaO — 1,3%, FeO — 2,5%,.
Розрахунок ведемо отримання шлаку, що містить 30% SiO2. Приймемо, що Х — загальна маса шлаку, кг; У — маса загружаемого піщанику, кг. Складові піщанику переходить до шлак повністю. Тоді загальна маса шлаку буде, кг:
Х=У+37,99×71,85/55,85+5,88+6,65= У+61,4.
37,99×71,85/55,85 — кількість FeO, яка утворювалася з заліза концентрату, перейшов у шлак. 6,65 — кількість SiO2 в концентраті 5,88 — кількість CaO, MgO, Al2O3.
Второе рівняння отримуємо з балансу: 0,30 Х=6,65+0,8У Решая систему рівнянь получаем:
У=23,54 (піщаник) Х = 84,94 (шлак) Результат перевіряємо підрахунком кількості і складу шлака:
|FeO |48,87+23,54×0,025=49,46 |58,23 | |SiO2 |6,65+23,54×0,8=25,48 |30,00 | |Al2O3 |1,52+23,54*, 087=3,57 |4,19 | |CaO |2,35+23,54×0,013=2,66 |3,12 | |MgO |2,02+23,54×0,015=2,37 |2,79 | |Інші |1,42 |1,67 | |Разом |84,94 |100 |.
Для розрахунку складу і кількість відведених газів приймемо, що все кисень, необхідний здійснення реакцій, надходить із підігрітим дутьем. У цьому необхідно враховувати, що у практиці є неорганізовані подсосы холодного повітря, кількість якого не може коливатися від 2% до 6%.
Вологість шихти 0,2%, отже в піч надійде ее.
(100+23,54)х0,002=0,25 кг.
З урахуванням змісту сірки в штейне і шлаку її піде на газы:
28,28 — 4,88- 0,67=22,73 кг.
32S-64 SO2.
22,73 P. S — X SO2, що становить 45,46 кг SO2.
На окислювання заліза, переходить у шлак, витрата кисню становитиме 48,87−37,99=10,88 кг.
Загальна потреба кисню на плавку 100 кг концентрату буде, кг:
— На окислювання сірки — 22,73.
— На окислювання заліза — 10,88.
— Переходить в штейн — 0,41.
Итого:34,02 кг.
Разом з киснем в піч надійде азота.
34,02/0,23×0,77=113,8 кг Из практики роботи відомо, що з шлаком втрачається: Cu — 2%, Ni — 4,5% Cu= 3,75×0,02= 0,075 Ni= 7,58×0,045=0,34 P. S в шлак = 28,28- (4,88+22,73)=0,67.
В технічні гази відходить: Cu: 3,75-(3,41+0,08)= 0,26 Ni: 7,58-(6,9+0,34)=0,34.
|Статьи |Усього | До того ж | |балансу | | |.
| |Cu |Ni |Fe |P.S |SiO2 |CaO |MgO |Al2O3 |O2 |N2 |H2O |інші | |.
Завантажене: | | | | | | | | | | | | | | |Шихти |100,22 |3,75 |7,58 |43,00 |28,28 |6,65 |2,35 |2,02 |1,52 |- |- |0,20 |4,87 | |Песчаника.
|21,59 | | | | |18,83 |0,31 |0,35 |2,05 |- |- |0,05 | | |Воздуха.
|147,82 | | | | | | | | |34,02 |113,80 | | | | Усього: |269,63.
|3,75 |7,58 |43,00 |28,28 |25,48 |2,66 |2,37 |3,57 |34,02 |113,80 |0,25 |4,87 | | | | | | | | | | | | | | | | | Отримано: | | | | | | | | | | | | | | | | | | | | | | | | | | | | | |Штейна |20,61 |3,41 |6,90 |5,01 |4,88 | - | - | - | - |0,41 | |.
| - | |Шлаків |88,91 |0,08 |0,34 |37,99 |0,67 |25,48 |2,66 |2,37 |3,57 |10,88 | | |4,87 | |Технічні гази |160,11 |0,26 |0,34 | |22,73 | | | | |22,73 |113,80 |0,25 | | | Усього: |269,63 |3,75 |7,58 |43,00 |28,28 |25,48 |2,66 |2,37 |3,57 |34,02 |113,80 |0,25 |4,87 | |Матеріальний баланс плавки концентрату в печи.
Виваженої Плавки нікелевої линии.
Бібліографічний список.
1. И. А. Стригин та інших. «Основи металлургии», т.1 Загальні вопросы.
Металургії, Москва, Металургія, 1975 г.
2. И. А. Стригин та інших. «Основи металлургии», т.2 Важкі метали, Москва,.
Металургія, 1975 г.
3. И. А. Стригин та інших. «Основи металлургии», т.7 Технологічне устаткування підприємств кольорової металлургиии, Москва, Металлургия,.
1975 г.
4. Н. В. Гудима «Технологічні розрахунки в металургії важких кольорових металів», Москва, Металургія, 1977 г.
5. Ф. М. Лоскутов, А. А. Цейдлер «Розрахунки по металургії важких кольорових металів», Москва, Металлургиздат, 1963 г.
6. Технологічна інструкція № 0401−3.1.109−34−80.
7. А. В. Ванюков, Н.І. Уткін «Комплексна переробка мідного і нікелевого сировини», Челябінськ, Металлургия, 1988 г.