Технология термічної обработки
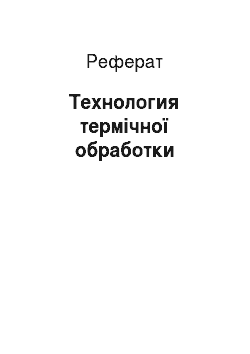
Температура цементації 930 °З. Як футерівки застосовують шамот і теплоізоляційні матеріали. Електричні нагрівачі мають на стінах шахти печі. СШЦМ для газової цементації дрібних деталей. Піч має жароупорный муфель, встановлений на підставку, обперту на футеровку пода печі. Підбійка виконана з шамотного вогнетривкої і теплоізоляційного матеріалів. Нагрівачі розташовані на півметровій стінках і поду… Читати ще >
Технология термічної обработки (реферат, курсова, диплом, контрольна)
смотреть на реферати схожі на «Технологія термічної обробки «.
Актуальними нині є питання підвищення надёжности і довговічності машин, приладів, установок, підвищення його якості і ефективності роботи, отже, питання економії металів, боротьби з корозією і зносом деталей машин. Роль них в довговічності машин і немає механізмів, приладів та інших особливо зросла час, так як розвиток більшості галузей промисловості (авіаційна, ракетна, теплоенергетика, атомна енергетика, радіоелектроніка та інших.) пов’язані з підвищенням навантажень, температур, агресивності середовищ, де працює деталь. Рішення всіх цих проблем передусім пов’язані з зміцненням поверхневих шарів изделий.
Змінити властивості поверхні можна в різний спосіб: нанесенням на поверхню нового матеріалу з необхідними властивостями; зміною складу поверхневого шару металла.
У другий випадок поверхневі шари металу піддають дифузійної химико-термической обробці (ХТО), у яких лежить на поверхні вироби утворюється новий, відрізняється від серцевини, сплав.
ХТО дозволяє їм отримати в поверхневому шарі вироби сплав практично будь-якого складу і, отже, забезпечити комплекс необхідних властивостей — фізичних, хімічних, механічних і других.
Однією з поширених методів ХТО є цементація. Процес цементації широко застосовують у промисловості завдяки одній його високої ефективності і доступності. Він дає змогу створювати на робочої поверхні деталі шар, у якого високої твёрдостью після гарту, зносостійкості, эрозионной стійкістю, контактної витривалістю і усталостной міцністю на вигині. Ці властивості забезпечуються при щодо м’якої іграшки і в’язкому серцевині, придающей деталі необхідну конструктивну прочность.
1. Опис деталі умов її работы.
Зубчасті колеса основними деталями більшості машин і творення механізмів. Вони служать передачі вращательных рухів між окремими елементами механизмов.
Обертання передається через зубцювате зачеплення. Відмова чи руйнація зубчастого колеса влечёт у себе припинення передачі крутящего моменту і відмова рухових агрегатів. Найбільш завантаженою частиною зубчастого колеса є зуб. На малюнку 1 показано схема зачеплення зубів. [pic].
Рис. 1 Схема зачеплення зубьев.
У процесі роботи зуби відчувають ударні навантаження, у результаті в них виникають контактні напруги. Поверхня зуба працює до зносу, в процесі роботи зуби нагріваються; для охолодження ними безупинно подається масло.
По конструкції дане зубцювате колесо є порожній циліндр. Зовні розташовані эвольвентные зуби, якими передається обертальне рух від ведучого зубчастого колеса. По внутрішньому діаметру даного зубчастого колеса виконані шлицы передачі крутящего моменту на ресори коробки агрегатів і далі ротору двигуна за його запуску, що забезпечує подачу палива на камеру сгорания.
У процесі роботи зубцювате колесо відчуває статичні, динамічні, знакопеременные і вібраційні навантаження величиною до 930 М. Деталь працює у олійною середовищі з робочої температурою до 300(С.
Рис. 2 Ескіз зубчастого колеса.
2. Технічні вимоги, які пред’являються матеріалу термічно обробленою детали.
Технічні вимоги матеріалу призначаються з умов роботи зубчастого колеса. З огляду на, що деталь працює у досить складних умовах, до неї пред’являються такі технічні требования:
— межа міцності [pic];
— умовний межа плинності [pic];
— ударна в’язкість [pic];
— твердість упрочнённой поверхні [pic];
— глибина упрочнённого шару [pic];
— твердість серцевини [pic].
3. Послідовність обробки детали.
Деталь від заготівлі до виготовлення проходить складний технологічний маршрут цехами підприємства (рис. 3):
З (КШ (Т1 (М1 (Т2 (М2 (Сб.
Рис. 3 Послідовність виготовлення зубчастого колеса.
З — заготівельний цех; різка прутка на заготівлі довжиною 85 мм, діаметром 65 мм;
КШ — кузнечно-штамповочный цех; штамповка методом гарячої штамповки;
Т1 — термічний цех; проведення попередньої термічної обробки поковок зі зняттям внутрішніх напруг після штампування й у підготовки структури до подальшої механічної обробці та термічної обработке;
М1 — механічний цех; проведення чорнової механічного оброблення, нарізування зубів та обробка зовнішніх поверхонь щоб надати деталі основних розмірів, відповідно до чертежу;
Т2 — термічний цех; остаточна термічна обробка для отримання необхідних свойств;
М2 — механічний цех; чистова механічна обробка (шліфування робочих поверхонь детали);
Рб — складальний цех; складання деталей в узел.
4. Вибір матеріалу для цієї деталі та обґрунтування выбора.
Для зубчастих коліс можна використовувати конструкційні цементуемые чи улучшаемые стали. З огляду на, що у технічним вимогам потрібні високі характеристики, варто звернутися до легированным сталям.
Дане зубцювате колесо приводу коробки агрегату авіаційного двигуна працює за нормальної температури до 300(С, для неї слід вибрати жодну з цементуемых теплостійких сталей із високим твёрдостью поверхні при достатньої твердості сердцевины.
Нині виготовлення відповідальних зубчастих коліс широко застосовуються теплостойкие стали перлитного класу, такі як 20Х3МВФ (ЭИ415), 12Х2Н4А і 12Х2НВФА (ЭИ712)[ ], для даного зубчастого колеса слід застосувати цементуемые стали. Цементуемые стали ділять втричі групи: углеродистые почав із неупрочняемой серцевиною; низколегированные зі слабко упрочняемой серцевиною; щодо высоколегированные почав із серцевиною, сильно упрочняемой при термічної обработке.
З огляду на високі вимогами з механічним властивостями, які пред’являються даному зубцюватому колесу, йому підходять стали третьої групи. Їх хімічний склад парламенту й механічні властивості наведено нижчий за таблице1 і таблице2. Щодо хімічного складу конструкційних цементуемых сталей ГОСТ 4543–71 Таблица1 |Марка |Зміст елементів, мас % | |стали |З |Cr |Ni |V |W |Mo |Si |Mn |P.S |P |Fe | |20Х3МВФА |0,15|2,80|(0,5|0,60|0,30|0,35|0,17|0,25|(0,02|(0,03|о | | |…0|…3| |…0|…0|…0|…0|…0|5 |0 |з | | |, 20 |, 30 | |, 85 |, 50 |, 55 |, 37 |, 50 | | | | |12Х2Н4А |0,10|1,25|3,25|____|____|____|0,17|0,3.|(0,02|(0,02|н | | |…0|…1|…3| | | |…0|. |5 |5 |про | | |, 15 |, 65 |, 65 | | | |, 37 |0,6 | | | | |12Х2НВФА |0,09|1,9.|0,8.|0,18|1,0.|____|0,17|0,3.|(0,02|(0,02|в | | |…0|. |. |… |. | |…0|. |5 |5 |а | | |, 16 |2,4 |1,2 |0,28|0,28| |, 37 |0,7 | | | |.
Механические властивості конструкційних цементуемых сталей.
Таблица2 |Марка |Термічна |[pic]|(0,2 |(|(|KCU |HRC | | | |(в | | | | | | |стали |обробка |МПа |МПа |% |% | |заговорили українською у. | | | | | | | | |МДж/м| |сердц| | | | | | | |(| |. | |20Х3МВФА |цементація | | | | | | | | | |920…950°С |(1070|(880 |(10 |(50 |(0,7 |(60 |(43 | | |выс. відпустку | | | | | | | | | |650…670°С | | | | | | | | | |гарт | | | | | | | | | |890…930°С | | | | | | | | | |низ. відпустку | | | | | | | | | |300…320°С | | | | | | | | |12Х2Н4А |цементація | | | | | | | | | |900…950°С |(980 |(785 |(12 |(55 |(0,1 |(58 |(30 | | |выс. відпустку | | | | | | | | | |650…670°С | | | | | | | | | |задо. у маслі | | | | | | | | | |780…800°С | | | | | | | | | |низ. відпустку | | | | | | | | | |150…170°С | | | | | | | | |12Х2НВФА |цементація | | | | | | | | | |900…925°С |(1050|(940 |(15 |(63 |(0,6 |(60 |(36 | | |выс. відпустку 650 | | | | | | | | | |±10°С | | | | | | | | | |гарт 880±10°С| | | | | | | | | | | | | | | | | | | |низ. відпустку | | | | | | | | | |160…250°С | | | | | | | |.
Сталь 20Х3МВФА — конструкційна теплостойкая високоякісна сталь. Вона належить до перлитному класу, і виплавляється у відкритих електричних печах, методами електрошлакового і вакуумного-дугового переплаву. Сталь добре деформується в гарячому стані. Сталь задовільно обробляється різанням. Ця сталь застосовується для виготовлення зубчастих коліс, втулок, пальців та інших деталей, працюючих до температури 350 °C. Застосування цієї стали для даного зубчастого колеса недоцільно, оскільки він не задовольняє технічним вимогам по пластичности.
Сталь 12Х2Н4А — високоякісна легована цементуемая сталь. У отожжённом стані є доэвтектоидной, а нормалізованому стані належить до перлитному класу. Застосовується виготовлення деталей зварних конструкцій, і навіть зубчастих коліс. Сталь добре деформується в гарячому стані; температурний інтервал деформації 1180−850°С. Ця сталь добре зварюється, має достатню прокаливаемость поверхневого шару. Після остаточної термічної обробки має велику твердість. Застосування цієї стали для цієї деталі не економічно: сталь містить багато дефіцитного нікелю і є дорогостоящей.
Сталь 12Х2НВФА — високоякісна легована конструкційна цементуемая сталь. У отожжённом стані є доэвтектоидной, а нормалізованому стані належить до перлитному класу. Застосовується для виготовлення важко навантажених деталей зварних конструкцій та вузлів, не піддається термічній обробці після зварювання. Застосовується також і деталей, працюючих при підвищених температурах до 500 °C. Ця сталь має високі прочностные характеристики, невисоку вартість. Її доцільно застосувати для даної детали.
5. Опис впливу легуючих елементів на структуру й поліпшуючи властивості обраного материала.
Вплив углерода.
Вуглець міститься у сталі у кількості 0,09…0,16%. Вона має: температуру плавлення 3500 °C; щільність 2,26 г/см (; кристалічну грати ГЦК з параметром a рівним 6,79(. Вуглець тяжко впливає властивості стали навіть за незначному зміні її змісту. Відомо, що відсотковий вміст вуглецю в стали приводить до підвищення міці й зниження пластичності. Ця сталь таки належить до третьої групи щодо високолегованих сталей з упрочняемой серцевиною. Серцевина в сталях має структуру малоуглеродистого мартенситу. А, щоб серцевина у своїй мала достатньої пластичністю і в’язкістю. Зміст вуглецю в сталях зазвичай обмежується нижньою межею менш 0,2% вуглецю [ ].
Вплив хрома.
Хром (Cr) міститься у сталі у кількості 1,9…2,4%. Має: температуру плавлення 1655 °C; щільність 7,1г/см (; кристалічну грати ОЦК з параметром a рівним 2,86(. Хром розчиняється в [pic] і [pic]. Максимальна розчинність в [pic]=0,5% при 20° С, в [pic]=12,8% при 510 °C. Хром належить до легирующим елементам, що підвищує критичні точки Ас3 і Ас1(рис.4). | | | | | | | | | | | | | | | | | | | | | | | | | | | | | | | | | | | | | | | | | | | | | | |Див. Мал.5 Вплив хрому |.
на твердість цементо;
Рис. 4 Частина діаграми ванного шару стану Cr-Fe.
Хром знижує температуру початку мартенситного перетворення (Мн) і збільшує зміст аустеніту залишкового. Хром є карбидообразующим елементом: при взаємодії з вуглецем утворюються карбиды Cr7C3; Cr26C3, растворяющиеся при нагріванні. Хром сильно збільшує прокаливаемость знижує критичну швидкість гарту. Хром збільшує міцність, при змісті більше однієї% знижує пластичність і ударну в’язкість. Хром підвищує твердість цементованного шару зі збільшенням її змісту до 2…3%. Подальше підвищення змісту хрому не приводить до підвищення твердості цементованного шару, у даної стали зміст хрому як разів і близько двох% (Див. Мал.5). Хром надає значний вплив на зміна концентрації вуглецю в цементованном шарі. При збільшенні змісту хрому концентрацію вуглецю слід підвищувати. На товщину цементованного шару величину зерна хром не влияет.
Вплив никеля.
Нікель (Ni) міститься у сталі у кількості 0,8…1,2%; має: температуру плавлення 1455 °C; щільність 8,91 г/см (; кристалічну грати ГЦК з параметром a рівним 3,51(. Нікель розчиняється в [pic] і [pic]. Максимальна розчинність в [pic]равна 80%, в [pic] нікель розчиняється необмежено, тобто є аустентообразователем. Нікель знижує критичні точки Ас3 і Ас1, підвищує критичну точку А4 (Див. Мал.6), знижує температуру початку мартенситного перетворення (Мн), збільшує кількість аустеніту зменшує схильність зерна аустеніту до зростання. | | | | | | | | | | | | | | | | | | | | | | | | | | | | | | | | | | | | | | | | | | | | | | | | | | | | | | | | | | | | | | | | | | | | | | | | | | | | | | | | | | | | | | | | |Див. Мал.7 Вплив | |Див. Мал.8 Вплив | | | | | | | |нікелю | |ніку- | | | | | | | | на твердість | |ля на | | | | | | | |цемен- | |твердість це- | | | | | | | |-тованного шару| |ментованного | | | | | | | |після | |шару |.
закалки і отпуска.
Див. Мал.6 Частина діаграми стану Fe-Ni.
Сталь, легована нікелем, добре обробляється різанням, шліфується і зварюється. Нікель кілька зменшує товщину цементованного шару, сприяє подрібненню зерна серцевини. Зміна змісту нікелю від 0 до 2% не надає істотно на теплопрочность і твердість стали. При змісті 0,8…1,2% в стали 12Х2НВФА нікель забезпечує хороші механічні властивості. Нікель підвищує міцність і робить сталь менш чутливої до пластичної деформації. Нікель надає велике впливом геть структуру й поліпшуючи властивості цементованного шару (Див. Мал.7). Він утрудняє дифузію вуглецю, викликає зменшення глибини шару. У сталь не можна вводити дуже багато нікелю, оскільки зменшується твердість цементованного шару рахунок освіти залишкового аустеніту (Див. Мал.8). Нікель в комбінації коїться з іншими елементами, приміром, із хромом, сприяє збільшення міцності при підвищених температурах. Це єдиний елемент, який підвищуючи твердість і міцність, не знижує пластичність і вязкость.
Вплив вольфрама.
Вольфрам (W) міститься у сталі у кількості 1,0…1,4%. Має: температуру плавлення 3410 °C; щільність 19,3 г/см (; кристалічну грати ОЦК з параметром a рівним 3,16(. Вольфрам підвищує критичну точкуА1, тим самим він звужує [pic]- область і розширює [pic]- область (Рис.9).
| | | | | | | | | | | | | | | | | | | | | | | | | | | | | | | | | | | | | | | | | |.
Див. Мал.9 Частина діаграми стану Fe-W.
Присутність у стали вольфраму перешкоджає освіті грубої цементитной сітки, яка зумовлює крихкість поверхневого шару при збільшенні глибини шару цементації. Вольфрам сильніше хрому підвищує стійкість стали проти відпустки. Вольфрам негативно впливає тепопроводность стали. Отже вольфрам, у цій стали підвищує твердість цементованного слоя.
Вплив ванадію. | | | | | | | | | | | | | | | | | | | | | | | | | | | | | | | | | | | | | | | | | | | | | | | |.
Рис. 10 Частина діаграми стану Fe-V.
Ванадій є сильним карбидообразующим елементом, здатний зміцнювати твёрдый розчин. При взаємодії з вуглецем ванадій утворює карбід VC і тим самим підвищує твердість цементованного слоя.
6. Розробка технічного процесу термічної обробки детали.
Вибір операцій термічної оброблення і визначення режимів операций.
Цементация.
Цементація — процес насичення поверхневого шару стали вуглецем з з підвищення міцності, твердості і зносостійкості поверхового слоя.
За глибину цементованного шару приймають відстань від поверхні до перехідною зоны.
Розрізняють такі види цементації: цементація із застосуванням твердого карбюризатора; газова цементація із застосуванням рідкого чи газового карбюризатора. Найперспективнішим є газова цементація. У порівняні з цементацией в твердому карбюризаторе вона не має такі переваги: значно скорочується тривалість процесу завдяки швидкому нагріванню деталі; зростає пропускну здатність устаткування, що веде до підвищенню продуктивність праці; поліпшуються умови праці; з’являється можливість автоматизації процесса.
Газова цементація можна проводити із застосуванням рідкого і газового карбюризатора. Як рідкого карбюризатора, зазвичай, застосовується синтин, а ролі газового — эндогаз.
Синтин отримують з окису вуглецю і водню, які виникають при переробці твердого палива. Синтин — це безбарвна рідина, що містить 90% парафінових граничних вуглеводнів. Швидкість цементації при застосуванні синтина підвищується на 20% і 50% знижується виділення сажі і кокса.
У шахтних печах рідкий карбюризатор подається краплями, а наявний вентилятор створює рух газового потоку, і цементація протікає рівномірно. Для зменшення сажеобразования карбюризатор подають паливною насосом через форсунки в распылённом стані. Оптимальний витрата синтина становить 0,8л газу на 1 см (. Склад що утворюється газу: ЗІ 20…28%, Н2 55…75%, СН4 2…5%. Режим подачі синтина при насиченні визначають досвідченим путём.
Для легованих сталей температура цементації застосовується вище точки Ас3, коли стійкий аустенит, здатний розчинити багато вуглець. Для стали 12Х2НВФА має точку Ас3 рівної 840(С оптимальної температурою цементації є 960(С.
З використанням рідкого карбюризатора ефективно застосовувати комбінований цикл насичення щоб одержати лежить на поверхні цементованного шару змісту вуглецю не більше 0,8…1%. Після цементації структура цементованного шару приведено малюнку 11.
Рис. 11 Структура цементованного слоя.
Розрахунок часу нагріву і витримки при цементації. Загальне час перебування деталі в печі: [pic] [pic]- час нагріву; [pic]- час витримки; [pic]- час охолодження. Час нагріву розраховується за способу Смольникова [ ]: [pic] [pic]- сумарний фізичний чинник нагріву, залежить від температури нагріву, нагрівальною середовища проживання і матеріалу деталі, мин/см; [pic]- коефіцієнт рівномірності нагріву; [pic]- геометричний показник тіла рівний відношенню обсягу тіла V на площу поверхні F:
[pic].
Для цієї деталі, має форму пологого циліндра, геометричний показник тіла W равен:
[pic] D-наружный діаметр деталі, див; d-внутренний діаметр деталі, див; l-длина деталі, см.
Розміри цієї деталі такі: D=3,6 див, d= 1,2 див, l=6,9 див. Нагрівання деталі відбувається у газової атмосфері, тому коефіцієнт До приймаємо рівним [pic]=45 мин/см [ ], а при обраному розташуванні деталі [pic]=1,4, тогда:
[pic].
Отже, час нагріву деталі составляет:
[pic] | | | | | | | | | | | | | | | | | | | | | | | | | | | | | | | | | | | | | | | | | | | | | | | | | | | | | | | | | | | | | | | |.
Рис. 12 Графік режиму цементации.
Час витримки при цементації залежить від температури нагріву, виду карбюризатора, особливостей сталі та необхідної глибини шару. У разі цементацию проводять у газі, одержуваному при розкладанні синтина, при температурі 960 °C. Для отримання шару глибиною 1,0…1,6 мм час витримки має становити 5 годин [ ]:
[pic]ч.
Охолодження після цементації проводимо на воздухе.
Високий отпуск.
Відпустку — це операція термічної обробки стали, яка полягає в нагріванні стали до температури нижче Ас1, витримці при заданої певній температурі й наступному охолодженням з певній скоростью.
У виробах зі високолегованих хромоникелевых сталей після цементації у структурі цементованного шару зберігається багато залишкового аустеніту. На його усунення проводять високий відпустку 650 °C протягом 2−10ч [ ]. За такої відпустці відбувається виділення дисперсних карбідів з залишкового аустеніту, твёрдый розчин збіднюється вуглецем і легирующими елементами, підвищуються температури початку й кінця мартенситного перетворення, що врешті-решт приводить до зменшення кількості залишкового аустеніту при наступної загартуванню. Такий відпустку необхідно застосувати і для даної стали[ ].
Розрахунок часу нагріву і витримки за високого отпуске.
[pic].
Час нагріву за відпускання залежить від температури, нагрівальною середовища, форми і середніх розмірів деталі. Для даного зубчастого колеса, має геометричний показник тіла W, рівний 0,5 мм. Час нагріву за відпускання з температурою 650 °C вираховується за формулою [ ]: | | | | | | | | | | | | | | | | | | | | | | | | | | | | | | | | | | | | | | | | | |.
Рис. 13 Графік режиму високого відпустки З огляду на знижену теплопровідність стали, збільшуємо час нагріву на 50%:
[pic].
Час витримки визначаємо з урахуванням структурних перетворень, які мають відбутися за високого відпустці цементованного вироби. Відповідно до літературних даних [pic] одно 2−4 год. Приймаємо [pic] рівним 3ч [ ]:
[pic]ч.
Закалка.
Гарт — це операція термічної обробки, яка полягає в нагріванні стали 30−50°С вище критичних точок Ас3 — для доэвтектоидных і Ас1 — для заэвтектоидных сталей і витримці нині температурі завершення фазових перетворень і наступному охолодженні зі швидкістю вище критичної. Сталь 12Х2НВФА є доэвтектойдной, критична точка Ас3 дорівнює 840(С, тому температура нагріву при загартуванню дорівнює [pic]. Оптимальною охолоджувальної середовищем при загартуванню для даної стали є олію, бо вона швидко відповідає сталь в інтервалі температур мінімальної стійкості аустеніту і загальмовано в інтервалі температур мартенситного перетворення, то є при охолодженні у маслі відбувається одночасне мартенситообразование в усій деталі, і знижується можливість освіти закалочных тріщин. У результаті гарту міцність і твердість збільшуються, а пластичність і в’язкість снижается.
Структура після гарту: лежить на поверхні мелкоигольчатый мартенсит, з рівномірно распределёнными карбидами і аустенит залишковий, в серцевині - малоуглеродистый мартенсит.
Розрахунок часу нагріву і витримки при загартуванню. Для гарту загальне час перебування деталі в печі розраховується наступним образом:
[pic] [pic]- час підігріву; [pic]- час витримки при підігріванні; [pic]- час остаточного нагріву; [pic]- час витримки при остаточному нагреве.
Час підігріву розраховується за способу Смольникова [ ]:
[pic] [pic]- сумарний фізичний чинник нагріву, залежить від температури нагріву, нагрівальною середовища проживання і матеріалу деталі, мин/см; [pic]- коефіцієнт рівномірності нагріву; [pic]- геометричний показник тіла. Коефіцієнт До приймаємо рівним [pic]=45 мин/см [ ], [pic]=1,3 мин/см[ ], W=0,51 см (див. раніше). Отже, час підігріву деталі составляет:
[pic].
Витяг при підігріванні необхідна вирівнювання температури по перерізу деталі. Час витримки зазвичай приймають рівним 25…30% від часу нагріву [pic]. Тоді: [pic].
Але такий значення часу витримки при підігріванні недостатньо, так як дана сталь є легованої і має знижену теплопровідність, тож слід збільшити час витримки, запровадивши поправочний коефіцієнт рівний 3, тогда:
[pic] Приймаємо час витримки при підігріванні рівним 30мин.
Далі деталь переносять до іншої піч з температурою 880 °C. Час остаточного підігріву розраховується аналогічно часу підігріву по способу Смольникова [ ]:
[pic].
За наявності попереднього підігріву расчётное час нагріву зменшують на 20−30% [ ], тоді: [pic] Приймаємо час остаточного нагріву рівним 20мин.
| | | | | | | | | | | | | | | | | | | | | | | | | | | | | | | | | | | | | | | | | | | | | | | | | | | | | | | | | | | | | | | | | | | | | | | | | | | | | | | | | | | | | | | | | | | | | | | | | | | |.
Рис. 14 Графік режиму закалки.
Приймаємо час остаточної витримки рівним 30мин. Загальне час: [pic].
Обробка холодом.
Обробка холодом залежить від охолодженні закалённой стали до температури нижче Км. Температура Км даної стали дорівнює -70(С, тому обробку холодом проводиться за нормальної температури — 50(С. | | | | | | | | | | | | | | | | | | | | | | | | | | | | | | | | | | | | | | | | | |.
Рис. 15 Графік обробки холодом.
Низький отпуск.
Низький відпустку — це операція термічної обробки, яка полягає в нагріванні закалённой стали до температури не вище температури у точці Ас1, витримці нині певній температурі й охолодженні надворі. Низький відпустку проводять зі зняттям внутрішніх напруг, які виникають за загартуванню і обробки холодом. Низький відпустку даної стали проводять із нагріванням до температури 250 °C [ ].
Розрахунок часу нагріву і витримки за низького отпуске.
Загальне час нагріву і витримки за низького отпуске:
[pic].
Час нагріву визначається залежність від геометричного показника, температури відпустки і нагрівальною середовища. По довідковим даним [ ] для цієї деталі, має W рівний 0,51 см, час нагріву для відпустки приймаємо 40мин.
Час витримки за низького відпустці визначається наступним образом:
| | | | | | | | | | | | | | | | | | | | | | | | | | | | | | | | | | | | | | | | | |.
Рис. 16 Графік режиму низького отпуска.
При низькому відпустці мартенсит гарту перетворюється на мартенсит отпуска.
2 Вибір устаткування всіх операцій технологічного процесса.
Визначення типу производства.
Тип виробництва визначається за коефіцієнтом закріплення операции:
[pic] [pic] - такт виробництва, хв; [pic] - час на обробку однієї садки, мин.
[pic] [pic]-действительный річний фонд часу, годину; [pic]-годовая програма випуску, шт.
Поштучна час розраховується за формуле:
[pic].
[pic] [pic] - основне оперативне час на обробку однієї садки, хв; [pic] - основне технологічне час, хв; [pic] - допоміжне не перекрываемое час, хв; [pic] - кількість деталей в садці, прим; [pic] - величезну кількість водночас обслуговуваних печей, од; [pic] - час на організаційне обслуговування робочого місця у % від оперативного; [pic] - час з технічного обслуговування робочого місця у % від оперативного; [pic] - час відпочивати та особисті потреби у % від оперативного.
Визначимо такт провадження у операції гарту. Для двозмінної роботи дійсний річний фонд часу дорівнює 4180ч, річна програма випуску дорівнює 200 000шт.
[pic] [pic] [pic]; [pic]; [pic][ ]; [pic][ ]; [pic][ ] [pic]; [pic] Виробництво з коефіцієнтом закріплення операції рівний 1,23 є крупносерийным (ГОСТ 31 108−74).
Вибір основного оборудования.
У крупносерийном виробництві застосовуються печі періодичного і безперервного дії. З огляду на специфіку термічної обробки даної деталі вибираємо печі періодичної дії. Серед печей періодичного дії найбільшого поширення отримали камерні і шахтні електричні печі опору. Для цієї деталі, має форму пологого циліндра, доцільно вибрати шахтні печі всім видів термічної обработки.
Шахтні печі має низку переваг: відносна простота конструкції; компактність; завантаження і вивантаження деталей механізована для чого застосовуються электротельферы, мостові крани; печі легко герметизируются з допомогою піщаних затворів. З урахуванням розмірів деталі річний програми випуску вибираємо такі марки печей: — для цементації - шахтну муфельну електропіч опору типу СШЦМ 6.12/9; - для високого відпустки — шахтну електропіч опору типу СШЗ 6.12/7; - для гарту — шахтну електропіч опору типу СШО 6.12/10; - для низького відпустки — шахтну електропіч опору типу СШЗ 6.12/7; - в обробці холодом — холодильна установка КТХ.
Технічні характеристики наведені у таблице3.
Технічні характеристики шахтних печей Таблица3 |Характеристики |М, а р до і п е год е і | | |СШЦМ 6.12/9 |СШЗ 6.12/7 |СШО 6.12/10 | |Встановлена потужність, |105 |75 |105 | |кВт | | | | |Встановлена |900 |700 |1000 | |температура,°С | | | | |Маса завантаження, кг |800 |900 |1001 | |Висота, мм |3645 |4130 |3790 | |Довжина, мм |2720 |2600 |2000 | |Діаметр, мм |2580 |2380 |2470 |.
[pic].
Електропіч опору для цементации.
Шахтні муфельные електропечі призначені для химико-термической обробки деталей і світлого отжига дроту і стрічки із чорного і кольорових металів в бунтах. Муфели і пристосування виготовляють з хромонікелевої стали чи сплаву. Матеріалом для нагрівачів служить ніхром Х20Н80 чи безникелевые сплави типу Х27Ю5Т.
Рис. 17 Шахтна муфельная електропіч типу СШЦМ.
Температура цементації 930 °З. Як футерівки застосовують шамот і теплоізоляційні матеріали. Електричні нагрівачі мають на стінах шахти печі. СШЦМ для газової цементації дрібних деталей. Піч має жароупорный муфель, встановлений на підставку, обперту на футеровку пода печі. Підбійка виконана з шамотного вогнетривкої і теплоізоляційного матеріалів. Нагрівачі розташовані на півметровій стінках і поду шахти печі. Спеціальні пристосування з жароміцних сталей, встановлювані в муфель, мають знімні днища з отворами для проходження газа-карбюризатора. Піч закривається кришкою. Кришка має механізм підйому і повороту. У кришці є отвори на шляху подання в муфель газукарбюризатора і відводу відпрацьованою атмосфери. Центром кришки встановлено вентилятор для перемішування атмосфери в муфеле щоб одержати стабільних результатів за глибиною насичення вуглецем оброблюваних деталей. Вентилятор включається після завантаження партії деталей в муфель і у протягом всієї химико-термической обробки. Для рівномірного нагріву муфеля, отже, і оброблюваних деталей піч за висотою розділена на дві самостійні температурні зони. Верхня частина печі втрачає більше теплоти в навколишнє простір, ніж нижня частина, тому верхня зона споживає більше електричної енергії. У шахтної печі з муфелем виключається взаємодія електричних нагрівачів з цементующей атмосферою. Умови роботи нагрівачів в печах з муфелем та звичних печах з повітряної атмосферою аналогічні. Шахтні печі виготовляють різної мощности.
Електропіч опору для високого, низького відпустки і гарту. [pic] Рис. 18 Шахтна електропіч типу СШО, СШЗ.
На малюнку 18 показано шахтна електропіч типу СШО, СШЗ з температурою нагріву до 700 °З. Піч працює із окислительной чи захисної атмосферою і становить каркас, футерованный вогнетривкими і теплоізоляційними матеріалами. Згори піч перекривається поворотною кришкою з механізмом піднесення та повороту. Вентилятор розташований внизу печі. Нагрівачі розміщені бічних стінках печі. Між нагревателями і обрабатываемыми деталями чи виробами є екран з напрямними для запобігання його від ушкоджень за мінімального завантаження виробів (наприклад, як бунтів). Задля більшої рівномірності нагріву піч розбита за висотою на три температурні зони I-III. Температуру вимірюють термопарами. Розняття між піччю і кришкою ущільнюють з допомогою піскового затвора.
Закалочный бак.
До устаткуванню, призначеному для охолодження при загартуванню, відносять немеханизированные і механізовані закалочные баки, у яких деталі розладнуються у вільному стані, закалочные преси, закалочные і гибозакалочные машини, у яких деталі (шестерні, вали, листи, ресори) гартуються в затиснутому стані. Рис. 19 Закалочный бак з механізована ным переміщенням столу [pic] Немеханизированный заклочный бак є ёмкость циліндричною чи прямокутної форми. Бак зварюють з листовий низьковуглецевої сталі завтовшки 4—6 мм. У термічних цехах застосовують невеликі закалочные баки для гарту малих і середніх деталей. Розміри баків у плані (в мм): 60×700, 700×1200. Глибина баків близько 1000 мм. У немеханизированных баках все процеси з приводу передачі деталей в бак, переміщенню в баку і видачі їх із бака виконують вручну. Орієнтовний обсяг закалочной рідини в баці становить 15 л на 1 кг охлаждаемых деталей. Для великих деталей (штампи, вали тощо. п.) розміри закалочных баків можуть сягати кількох метров.
При визначенні обсягу закалочного бака та її розмірів слід враховувати, що з забезпечення: рівномірних умов охолодження деталей над ними під ними може бути шар закалочной рідини завтовшки щонайменше 100 мм. З іншого боку, рівень закалочной рідини може бути, від краю бака на відстані щонайменше, ніж 100—150 мм.
Для гарту деталей, застосовують баки (рис.19) з механізованим переміщенням закалочного столу, який встановлюється піддон з нагрітими деталями. З допомогою пневматичного підйомника стіл може опускатися і підніматися в баке.
Установка в обробці холодом. [pic].
Для охолодження небагатьох окремих деталей, наприклад, ріжучого інструмента, калібрів та інших виробів із високолегованої сталі застосовують камери корисним обсягом 0,1—1,0 м³. Камера шкафная (КТХ) обладнана компресорної установкою, які забезпечують охолодження до —100°С, і электронагревателями, що дозволяє нагрівати камеру до 155 °C. На рис. 20 показаний розріз камери КТХ. Машинне відділення лежить у частині камери. Електричні нагрівачі розташовані під робочою простором камери. Проноситись Рис. 20 Камера шкафная.
[pic] вентилятора, вращаемая електродвигуном, спрямовує потік повітря на воздухоохладитель, у якому розмістили змійовик, послідовно соединённый зі змійовиком випарника, припаяним до внутрішнього корпусу камери. Через вікно у двері можна за включеному осветительном приладі оглядати внутрішнє простір камеры.
Мийна машина. Рис. 21 Схема малогабаритній мийною машини У термічному виробництві використовують мийні машини різних типів. На малюнку 21 показано малогабаритна мийна машина з роликовым подом конструкції ЗІЛ. На зварної рамі встановлено мийна камера, вхід у якому закритий гумової заслінкою. Контейнер з вимощеними деталями встановлюють на роликовий під. У процесі промивання контейнер робить возвратнопоступательные переміщення в мийної камері зі швидкістю 2,9 м/мин.
Установка для струйно-абразивной обробки деталей. [pic].
Рис. 22 Установка для струйно-абразивной обробки деталей.
Струйно-абразивная обробка деталей є процеси, при яких робочий матеріал (металевий пісок, дріб) вводять у струмінь газу чи рідини і направляється на очищаемую поверхню. І тут кінетична енергія, повідомлена абразиву, витрачається видалення забруднень із поверхні оброблюваної деталі. Оскільки струйно-абразивная обробка полягає в суто механічному дії абразиву, ефективність обробки збільшується зі збільшенням твердості абразиву і швидкості його переміщення. На малюнку 22 приведено схема напівавтоматичного установки для струйно-абразивной обробки дрібних деталей. Установка складається з корпусу, барабана, надсопельного бункера, основного бункера, приводу, сопла і электрошкафа. У корпусі і барабані є двері для завантаження деталей. У верхню частину установки поміщається вытяжная вентиляція. Внутрішня порожнину барабана в обробці деталей облицьована гумою. Обертання барабан одержує вигоду від електродвигуна через редуктор і ланцюгову передачу.
Робота установки здійснюється так: в барабан завантажуються очищаемые деталі, в бункер — металева дріб. Завантажувальні двері щільно закриваються і включається привід обертання барабана. При обертанні барабана дріб захоплюється ковшами, прикріпленими до торцям барабана, і завантажується в надсопельные бункера, звідки дріб самопливом вступає у сопла. Струмінь стиснутого повітря з дробом спрямована в бункер на детали.
Великі металеві частки через отвори в барабані потрапляють у бункер, а дрібні — отсасываются витяжною вентиляцією. Через 15—20 хв привід автоматично вимикається, барабан зупиняється і очищені деталі вивантажуються. У апаратах для струйно-абразивной обробки найбільш зношуються сопла, яких із великий швидкістю викидаються частки робочого материала.
Розрахунок кількості устаткування. Визначення потрібного кількості печей кожної операции:
[pic]; [pic]- потрібне час печі, печи-час; [pic]- дійсний річний фонд часу, ч;
[pic]печи-час; [pic]- оперативне час на термообробку однієї садки, год; [pic]- кількість садок в річний программе;
[pic] [pic]- річна програма випуску, шт;
[pic] Визначимо кількість устаткування всіх операцій. Вихідні дані: [pic]=200 000шт, [pic]=4180ч 1. Для цементації: 2. Для високого отпуска:
3. Для гарту: [pic]; [pic]; [pic]; [pic]п/ч; [pic] п/ч; [pic] п/ч; [pic]; [pic]; [pic]; [pic]; [pic]; [pic]; [pic]. [pic]. [pic]. 4. Для обробки холодом: 5. Для низького відпустки: [pic]; [pic]; [pic]п/ч; [pic] п/ч; [pic]; [pic]; [pic]; [pic];
[pic] [pic]. [pic].
3 Вибір пристосування Рис. 23 Этажерка.
Вибір устаткування залежить від технології термічної обробки, застосовуваного устаткування, матеріалів і габаритів вироби. Оскільки пристосування відчуває постійний перепад температур. Термін їхнє служіння обмежений. У шахтних печах застосовуються пристосування типу етажерка (рис.23). етажерки виготовляються з жаропрочной стали марки 36Х18Н25С2. На етажерку при цементації розміщається порядком 70шт.
Вибір методів контроля.
Контроль параметрів технологічного процесса.
Контроль температуры.
Контроль і регулювання температури в печах здійснюється з допомогою потенциометров. Нині найбільш досконалим приладом є електронний автоматичний потенціометр КСП-4. Первинним прибором-датчиком є термопара, тип термопари вибирається залежно від робочої температури печі. Марки і технічні характеристики термопар наведені у таблиці 4.
Марки і характеристики застосовуваних термопар ГОСТ 6616–74.
Таблица4 |Операция|Темпер|Тип |Граду|Материал|Предел |Межа | | |атура,|термопар|ировк|электрод|измерения при|измерения при | | |(З |и |а |вв |тривалої |короткочасною| | | | | | |роботі |роботі | |цементац|960 | | |хромель-| | | | |іє |650 |ТХА |ПХЕ | |50 |1000 |1300 | |выс.отпу|880 | | |алюмель | | | | |ск | | | | | | | | |гарт | | | | | | | | |обработк|- 50 |термомет|_____|________|______|______|_______________| |а | |р | |_ | | |__ | |холодом | | | | | | | | |низ.отпу|250 |ТХК |ХК |хромель-|50 |600 |800 | |ск | | | | | | | | | | | | |копель | | | |.
Контроль синтина.
Контроль витрати синтина здійснюється з допомогою ротаметра і має складати 6,5…7,2мл/мин чи 160…180капель/мин.
Контроль якості термічно опрацьованих деталей.
Контроль якості після термічної обробки проходить за ОСТ 10 002- 78, група контролю 2ц.
Контроль зовнішнього вида.
Проводиться зовнішній огляд готових деталей на коробление і журналістам зміну розмірів. Контроль зовнішнього вигляду проводиться на 100%.
Контроль твердості термічно опрацьованих деталей.
Твердість є одним із характеристик якості цементації. Твердість вимірюється після цементації, гарту й низького відпустки. Контроль твердості проходить за методу Роквелла (ГОСТ 9013−59) на приладі ТК-2 шляхом удавлення в спустошену поверхню алмазного конуса при навантаженні Р=1470Н. Свідчення приладу знімають за шкалою «З» — чорного цвета.
Контроль глибини цементованного слоя.
Для контролю глибини цементованного шару використовують прес Бринеля. Цей метод полягає в вдавливании в спустошену поверхню закалённого кульки діаметром 2,5 мм при навантаженні рівної Р=187,5Н.
Контроль микроструктуры.
Мікроструктуру досліджують на мікроскопах, вирізані з цементованных і закалённых зразках з допомогою спеціальних шкал, розроблених для даної стали. Зміст вуглецю визначається послойным хімічним чи спектральним анализом.
7. Можливі види шлюби й методи його устранения.
Дефекти які під час цементации.
1. Трооститная сітка — утворюється під час внутрішньому окислюванні. Внутрішнє окислювання зменшує зміст легуючих елементів в твердому розчині, підвищує критичну швидкість гарту. При загартуванню у маслі призводить до не мартенситному перетворенню аустеніту. Для усунення трооститной сітки за 5…10мин до закінчення процесу у грубну атмосферу вводять аміак 2,5…10%. довговічність деталей можна підвищити, усуваючи зони внутрішнього окислення наступної механічної обработкой.
2. Обезуглероживание поверхні цементованного шару — відбувається за подстуживании надворі за відсутності автоматичного регулювання вуглецевого потенціалу у другому періоді насичення. Для усунення обезуглероживания передбачається остудити деталі серед опрацьованих газов.
3. Нерівномірна глибина цементованного шару — є наслідком рівномірності температури у робочому просторі чи поганий циркуляції пічний атмосфери, у разі порушення подачі карбюризатора, зниження температури, недостатньою выдержке.
Дефекти при закалке.
1.Недогрев — виникає у тому випадку, якщо сталь була нагріта до температури нижче критичної. Частина сорбита не перетворюється на аустените, в результаті гарту виходить структура має низьку твердість. Цей дефект можна виправити навіщо недогретую сталь отжигают, та був проводять нормальну закалку.
2.Перегрев — виходить, якщо сталь була нагріта до температури набагато вища критичної або за оптимальної температурі було дано занадто велика витримка. При перегрів йде зростання зерна аустеніту, мартенсит стає хрупкостойким. Виправляється отжигом, загартованістю Плавлення — виходить у разі, якщо сталь була недогрета до температури близька до температурі плавлення. Плавлення характеризується оплавленням й у цьому сенсі окисленням металу на межі зерен, тому сталь стає дуже тендітній. Пережого є невиправним шлюбом. Закалочные тріщини — творяться у результаті різкого охолодження чи нагріву, перегріву, нерівномірного охолодження, його присутність серед деталях гострих кутів, рисок і п.т. Плямиста гарт — виникає якби поверхні деталі окалина, забруднення, нерівномірна структура. У деяких зонах замість мартенситу то, можливо троостит чи сорбит. Цей шлюб усувається шляхом очищення деталей і для загартованістю проводять контроль стали однородность.
Дефекти які під час отпуске.
1. Недоотпуск — виходить за нормальної температури відпустки нижче нормальної в результаті сталь на сягає необхідних властивостей. Виправити недоотпуск можна додатковим отпуском.
2. Переотпуск — виходить за нормальної температури відпустки вище нормальною або зміні тривалості відпустки. Через війну переотпуска сталь не сягає необхідних властивостей. Сталь має знижену твердість і прочность.
8. Охорона труда.
Під час проведення операції термічної обробки дільниці виникають небезпечні й шкідливі виробничі чинники, які мають негативне вплив для здоров’я і працездатність людини. Елементи формують ці чинники наведені у таблице5.
Небезпечні чинники технологічного процесса.
Таблиця 5 |№ |Наименовани|Оборудование, |Материалы,|Производственная|Окружающая | |п/|е |приспособление|сырьё |середовище |середовище | |п |операції |, інструмент | | | | |1 |Цементація |СШЦМ 6.12/9 |12Х2НВФА |Висока |Виділення | | | |етажерка |синтин |температура, |тепла, | | | | | |продукти |забруднення | | | | | |розкладання |стічні води | | | | | |синтина, | | | | | | |підвищену | | | | | | |напруга | | | | | | |токоведущих | | | | | | |частин | | |2 |Високий і |СШЗ 6.12/7 |12Х2НВФА |Висока |Виділення | | |низький |етажерка | |температура, |тепла, | | |відпустку | | |продукти |забруднення | | | | | |розкладання |стічних вод мовби | | | | | |синтина, | | | | | | |підвищену | | | | | | |напруга | | | | | | |токоведущих | | | | | | |частин | | |3 |Гарт |СШО 6.12/10 |12Х2НВФА |Небезпека |Виділення | | | |закалочный бак|масло |загоряння |тепла, | | | | | |олії, висока |забруднення | | | | | |температура, |стічні води | | | | | |продукти | | | | | | |розкладання | | | | | | |синтина, | | | | | | |підвищену | | | | | | |напруга | | | | | | |токоведущих | | | | | | |частин | | |4 |Промивання |мийна машина|12Х2НВФА |Підвищена |Забруднення | | | | |10% водный|влажность, |стічних вод мовби | | | |ММТ кошик |розчин |шкідливі | | | | | |Na2CO3 |випаровування | | |5 |Обдувка |гидропескостру| | | | | | |йная машина | | | | |6 |Зачистка |верстат | |Шум, |Забруднення | | | | | |пылевыделения |стічних вод мовби | |7 |Контроль |твердомер |12Х2НВФА |Недостатня |_____________| | |твердості |2090ТР | |освещённость |_ | |8 |Контроль |мікроскоп, |12Х2НВФА |Шкідливі |Забруднення | | |глибини |полірувальний |травители,|испарения, шум, |стічні води, | | |шару |коло, вытяжной|полироваль|недостаточная |шкідливі | | | |шафу |ная |освещённость, |випаровування в | | | | |рідина |потрапляння |атмосферу | | | | | |травителя на | | | | | | |руки | |.
1 Заходи з техніці безопасности.
До заходів із техніці безпеки при експлуатації установок і приладів контролю параметрів технологічних процесів ставляться такі: при контролі температури — проходи до первинним перетворювачів температури встановленим у важкодоступних місцях, повинні забезпечуватися оглядовими майданчиками і східцями. Усі прилади, яких підводиться електроживлення мали бути зацікавленими заземлені; при контролі витрати кількості та підвищення рівня — при експлуатації витратомірів змінного перепаду тиску необхідно забезпечувати скидання продуктів продувки в дренажні чи каналізаційні лінії задля унеможливлення забруднення повітря. Усі прилади, яких підводиться електроживлення, би мало бути заземлені. Всім лічильників, приладів, установок розміщених у важкодоступних місцях, мають бути передбачені майданчики чи криниці із добре освещёнными проходами.
Працюючи на электротермическом устаткуванні з контрольованими атмосферами заборонена змішування горючих газів застосовуваних при приготуванні контрольованих атмосфер з повітрям, у уникнення освіти вибухової суміші. Суворе дотримання правил зупинки печей заміна контрольованій атмосфери. Перед запровадження у піч атмосфери з неї необхідно попередньо видалити повітря. Для продувки печей необхідно застосовувати інертні гази. Видалення газів які мають різким запахом із робітничого зони проводиться місцевими вентиляторами з отсосами. Щоб запобігти отруєння, у трубопроводах і апаратах слід передбачити надійні з'єднувачі і прокладки.
2 Заходи з охорони навколишнього среды.
Термічна обробка металу і експлуатація електроустаткування у тому чи іншою мірою надає шкідливі на довкілля, оскільки супроводжується освітою великої кількості шкідливих газів, пилу, загрязнённых вод. Тому, за експлуатації э.т.о. і виборі середовища при термічній обробці необхідно враховувати ступінь негативного впливу цих факторів на навколишню среду.
У термічному виробництві до основним чинникам надають шкідливе впливом геть довкілля относятся:
1. виділення тепла в біосферу — майже вся електроенергія, споживана печами, перетворюється на тепла і розсіюється в біосфері як втрат чи при охолодженні нагрітих деталей. Чим міцніше електропечі, то істотніші цього чинника. Для зменшення непотрібного розсіювання тепла доцільно: поліпшення теплоізоляції і зменшення всіх видів втрат, використання тепла відведених газів і охолоджувальної води для технологічних чи комунальних цілей; виділення у повітря шкідливих газів — в термічних цехах при нагріванні в контрольованих атмосферах, сушінню та інших операціях виділяються шкідливі гази. Для зменшення забруднення атмосфери проводяться такі заходи: застосування систем газоулавливания і газоочистки, заміна технологічних процесів з великим газовыделением інші більш скоєні; забруднення водоёмов виробничими стічними водами — в термічних цехах в стічні води потрапляють розчини кислот, лугів і солей, застосовувані для травлення деталей; вода використовувана для гарту й промивання виробів і охолодження пічних пристроїв. Для знешкодження стічних вод мовби проводяться такі заходи: стічні води повинні перед скиданням проходити різні методи очищення, щоб забезпечити ГДК шкідливих речовин у воді; після обробки, відстоювання і фільтрування стічні води скидаються у побутову каналізацію; використання водних ресурсів — электротермическое устаткування є великим споживачем води, расходуемой на охолодження елементів печей і устойств. До неї пред’являються високі вимоги: зменшення паркана води із джерел і забезпечення її якості необхідно застосовувати системи обігового водоснабжения.
6 Заходи з протипожежної безопасности.
При обслуговуванні електропечей мають бути дотримані такі вимоги безпеки: все токоведущие частини електропечей, із якими можливо зіткнення обслуговуючого персоналу, повинні прагнути бути ізольовані чи обгороджені; і прилади контролю, яких підводиться електроживлення, повинні бути заземлені; електричні печі повинен мати блокування для автоматичного відключення нагрівальних елементів при відкриванні дверцята печі. при експлуатації электротермического устаткування потрібно використовувати ізоляційні кошти індивідуальної захисту: рукавиці, діелектричні калоші, килимки і т.п.
5. з обслуговування электротермического устаткування Правилами експлуатації електроустановок передбачені спеціальні заходи для безпеки за захистом обслуговуючого персоналу від впливу високих температур і теплового випромінювання. Усі механізми управління і обслуговування печей повинні бути те щоб робочий не зазнавав впливу високих температур і шкідливих газів. Різниця температур лежить на поверхні печей і навколишнього повітря має перевищувати 45…60(С.
Нормативне забезпечення проекта.
ГОСТ 9012–59 Метали. Методи випробування. Вимірювання твердості по Бринелю.
ГОСТ 4543–71 Сталь легована конструкційна. Марки і технічні требования.
ГОСТ 1913;59 Метали. Методи випробування. Вимірювання твердості по.
Роквеллу. Шкали А, У, С.
ГОСТ 12.0.004−79 «ССБТ. Організація навчання працюючих безпеки праці. Загальні положения.».
ГОСТ 12.1.005−88 «ССБТ. Загальні санітарно-гігієнічні вимоги до повітрю робочої зоны».
ГОСТ 12.4.011−89 «ССБТ. Засоби захисту що працюють у ливарних і термічних цехах».
ГОСТ 12.0.002−80 «ССБТ. Безпека виробничого оборудования.
Загальні требования".
ГОСТ 12.4.011−89 «ССБТ. Засоби захисту працюючих. Классификация».
ГОСТ 12.3.004−75 «ССБТ. Термічна обробка металів. Загальні вимоги безопасности».
ГОСТ 12.1.004−85 «ССБТ. Пожежна безпеку. Загальні требования».
ГОСТ 12.1.010−76 «ССБТ. Взрывобезопасность. Загальні требования».
1. Сучасні технології у виробництві газотурбінних двигунів під редакцією А. Г. Братухина, Г. К. Язова, Б. Е. Карасева.
М.: Машинобудування, 1997 р. 410с.
2. А. А. Гарькавый, «Виробництво деталей авіаційних двигателей».
М.: Машинобудування, 1977 г.
3. Гуляєв О.П., «Металловедение».
М.: Машинобудування, 1988 г.
4. Долотов Г. П., Кондаков Е. А., «Устаткування термічних цехів і лабараторий випробування металлов».
М.: Машинобудування, 1988 р. 336с.
5. Электротермическое оборудование:
Довідник під редакцією А. П. Альтгаузена.
М.: Енергія, 1980 г. 416с.
6. Авіаційні матеріали. Довідник, тои I під редакцією Туманова А. Т.,.
ОНТИ, 1975.
7. Парфеновская Н. Г., Самоходский А.І. «технологія термічної обробки металлов».
8. Филлипов С. А., Фиргер І.А. «Довідник термиста».
М.: Машинобудування, 1975 г.
9. Башнин Ю. О., Ушаков Б. К., Секей О. Г. «Технологія термічної обробки стали».
М.: Металургія, 1986. 424с.
———————————- Вольфрам утворює карбід W2C, який за нагріванні легко розчиняється в аустените. За наявності вольфраму критична швидкість гарту знижується, а прокаливаемость підвищується. Зменшується схильність до зростання зерна аустеніту, підвищується ударна в’язкість. Вольфрам набагато збільшує твердість цементованного шару, зменшує чутливість до перегріву. Вольфрам змаліє структуру сталі та збільшує зміст вуглецю в поверхневому слое.
Ванадий (V) міститься у сталі у кількості 0,18…0,28%. Має: температуру плавлення 1710 °C; щільність 5,96 г/смі; кристалічну грати ОЦК з параметром a рівний 3,03(. Ванадій підвищує критичні точки А1 і А3 і знижує критичну точку початку мартенситного перетворення (Рис.10). ванадій затримує зростання зерна аустеніту при високих температур гарту. Ванадій незначно підвищує концентрацію вуглецю в цементованном шарі. При дуже високому вмісті ванадію глибина цементованного шару уменьшается.
Ця сталь є високолегованої, має знижену теплопровідність, тому її нагрівання відбувається повільніше. Слід збільшити час нагріву на 30%:
[pic] Потрібен час на нагрівання пристосування, тому отримана значення [pic] слід збільшити ще на 30%:
[pic] Приймаємо [pic] рівним 1 час.
[pic] Умовна товщина дорівнює фактичної товщині деталей помноженою на коефіцієнт форми, який приймаємо рівним 2 [ ]:
[pic] Фактична товщина дорівнює: [pic] Отже, час нагріву равно:
[pic].
Знайдемо час остаточної витримки. Для звичайних сталей:
[pic].
[pic] Однак у цьому стали при загартуванню повинні відбутися диффузионные процеси розчинення фаз в аустените. У легованих сталях диффузионные процеси уповільнені, для завершення структурних перетворень така витримка недостатня тому вводимо поправочний коефіцієнт рівний 3: [pic].
Понижение температури до температури нижче точки кінця мартенситного перетворення Км викликає перетворення аустеніту в мартенсит, що підвищує твердість стали. Проте, одночасно зростають внутрішні напруги, тому деталь охолоджують повільно й відразу після обробки холодом проводять низький відпустку. По довідковим даним [ ] час витримки для структурних перетворень приймаємо 2 ч.
[pic] Фактична товщина дорівнює: [pic].
[pic] Отже, час витримки равно:
[pic]ч[pic]ч25мин.
[pic].