Проект агрегатної дільниці вантажного автотранспортного підприємства
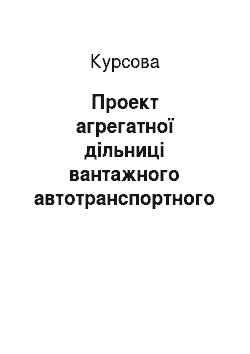
Залежно від умов експлуатації змінюються швидкісні і навантажувальні режими деталей, механізмів та агрегатів автомобілів і термін їхньої безвідмовної роботи. Наприклад, на коротких маршрутах частіше користуються зчепленням, гальмами, переключають передачі і зчеплення, внаслідок чого збільшується ймовірність їхніх відмов. При експлуатації автомобілів у важких дорожніх умовах збільшуються… Читати ще >
Проект агрегатної дільниці вантажного автотранспортного підприємства (реферат, курсова, диплом, контрольна)
Вступ
ремонт автомобіль технічний Технічне обслуговування і ремонт забезпечують справний технічний стан автомобільного транспорту. Одна з найважливіших проблем, яка стоїть перед автомобільним транспортом, є підвищення експлуатаційної надійності автомобілів, і зниження затрат на їх утримання. Вирішення цієї проблеми з однієї сторони, забезпечується автомобільною промисловістю за рахунок випуску автомобілів з великою надійністю і технічністю, з іншої сторони — вдосконалення методів технічної експлуатації автомобілів, підвищення продуктивності праці, зниженням трудомісткості робіт по технічному обслуговуванню і ремонту автомобілів, збільшення їх міжремонтних пробігів. Це потребує створення потрібної виробничої бази для підтримки рухомого складу в справному стані, широкого застосування засобів механізації і автоматизації виробничих процесів, збільшення будівництва і покращення станів доріг.
Вимоги до надійності транспортних засобів підвищується у зв’язку з швидким ростом і інтенсивністю руху, потужності, вантажопідйомності і в місткості автомобілів, а також технологічними і організаційними зв’язками автомобільного транспорту з обслуговуючими підприємствами та іншими видами транспорту.
Організація, методи і засоби збереження рухомого складу повинні забезпечувати його збереження в міжзмінний час і своєчасну підготовку для роботи на лінії.
Важливим завданням технічної експлуатації автомобілів є удосконалення методів проектування технічної бази АТП які забезпечують виконання всіх потреб по утриманню парку автомобілів.
Курсовій проект містить розробку прогресивної технології та організації робочих місць на виробничих ділянках.
1. Розробка агрегатної дільниці
1.1 Загальна будова та призначення коробки передач автомобіля
Коробка передач призначена для зміни крутного моменту за величиною та напрямком і довгочасного від`єднання двигуна від трансмісії.
Необхідність зміни крутного моменту виникає у зв`язку зі зміною умов руху. При рушанні з місця або при русі вгору до ведучих коліс повинно підводити більший крутний момент, ніж при рівномірному русі по горизонтальної ділянці дороги. Зміна крутного моменту досягається за допомогою зачеплення пар шестерень з різною кількістю зубів.
Передаточним числом називається відношення кількості зубів відомої шестірні до кількості зубів веденої шестірні, пари шестерень. Якщо в передачі приймає участь декілька пар шестерень, то передаточне число такої передачі визначається як добуток передаточних чисел пари шестерень.
Для отримання заднього ходу між ведучою і веденою шестернями вводиться проміжна, що змінює напрямок обертання веденої шестерні. Роз`єднання двох шестерень, що приймають участь у передачі веде до вимикання і від`єднання передачі і вимикання двигуна від трансмісії.
Основними частинами коробки є: картер, первинний вал з шестірнею і підшипниками, проміжний вал з шестірнями і підшипниками, вторинний вал з шестірнями і підшипниками, синхронізатор (синхронізатори), блок шестірень заднього ходу, механізм переключення передач.
Картер зверху закривається кришкою, а в бокових стінках маються люки для з`єднання з коробкою відбору потужності; при її відсутності - люки зачиняються кришками. Картер має пробку контрольно-заливного отвору, знизу є пробка (отвір) для зливу масла. Всі кришки картера ущільнюються спеціальною пастою, яка запобігає від потрапляння в картер води при подоланні броду та ін. Вентиляція картера здійснюється через трубку.
Кожний вал коробки встановлено на підшипниках. В кришках підшипників первинного і вторинного валів розташовані гумові сальники для запобігання течі масла з картера.
Синхронізатор слугує для безшумного переключення передач шляхом вирівнювання кутових швидкостей вмикаємих елементів. (В коробці передач автомобілів ЗІЛ 4545 — інерційні синхронізатори з блокуючими пальцями.). Принцип роботи синхронізаторів заснований на використанні сил тертя для вирівнювання кутових швидкостей вмикаємої шестірні і веденого вала. Вмикання передачі повинно проходити безшумно.
Блок шестірень заднього ходу встановлено на осі на двох роликових підшипниках. (Від передньої шестірні блока здійснюється відбір потужності при установці коробки відбору потужності). Шестірня блока, а також шестірня першої передачі і заднього ходу — прямозубі, решта всі шестірні коробки — косозубі.
Механізм переключення передач розташований в кришці коробки передач і складається із важеля, трьох штоків з вилками, трьох фіксаторів, замкового пристрою і запобіжника від випадкового вмикання передачі заднього ходу. Фіксатори запобігають можливість самовільного вмикання або вимикання передач. Замковий пристрій не допускає одночасного вмикання двох і більше передач.
Змащення коробки передач здійснюється розбризкуванням. В коробку передач ЗІЛ 4545 заправляється 5,1 л (с коробкою відбору потужності 6,7 л) масла.
Несправності та ТО коробки передач
Основними несправностей коробки передач:
— Ускладнене вмиканням передач;
— Самовільне їх вимикання на ходу автомобіля;
— Поломка зубців шестірень;
— Підвищений шум при роботі и сильний нагрів;
— Підтікання масла.
Ускладнене вмикання передач може бути із-за погнутості штоків і вилок, подряпин на зубцях шестірень і синхронізаторах, заїдання фіксаторів.
Самовільне вимикання передач можливо із-за зносу зубців шестірень і синхронізаторів, ослаблення кріплення вилок на штоках, несправності фіксаторів.
Поломка зубців може виникнути при різкому рушанні з місця завантаженого автомобіля або вмикання передач з несправним зчепленням.
Підвищений шум при роботі і сильний нагрів виникає внаслідок недостатньої кількості або малої в`язкості масла, більшого зносу або руйнування підшипників, поломки зубців шестірень, неправильного регулювання зчеплення.
Підтікання масла із картерів коробок може бути при ушкодженні прокладок, зносі сальників, із-за підвищеного тиску в картерах.
Усунення несправностей виробляється шляхом проведення поточного ремонту коробок з заміною зношених або пошкоджених деталей. При недостатньої кількості масла його рівень доводиться до норми.
1.2 Види робіт з технічного обслуговування, ремонту та відновлення коробки передач автомобіля
При КО перед виходом з парку на ходу автомобіля перевіряється робота коробки передач і роздавальної коробки, при цьому звертається увага на легкість і безшумність переключення передач; в цих агрегатах не повинно бути також стуків і самовільного вимикання передач. В путі перевіряється нагрів картерів; при цьому нагрів рахується нормальним, якщо він не викликає відчуття опіку долоні руки.
При ЕТО виконується очистка зовнішньої поверхні коробок від бруду, пилу і снігу, їх мийка.
При ТО_1 перевіряється кріплення коробок, рівень масла в них, виробляється очистка сапунів (вентиляційних трубок).
При ТО_2 додатково доливають або замінюють масло в картерах.
При СО виробляється заміна масла в картерах у відповідності з майбутнім періодом експлуатації (крім все сезонних масел).
1.3 Коротка характеристика автотранспортного засобу
ЗІЛ 4545 — двохвісний вантажний автомобіль повнопривідний підвищеної прохідності, що випускається Автомобільним Заводом імені Лихачова (ЗІЛ). Автомобіль самоскид будівельний ЗІЛ 4545 призначений для перевезення і механізованого розвантаження будівельних і навалювальних вантажів.
Таблиця 1.1 — Коротка технічна характеристика автомобіля ЗІЛ 4545
Базове шасі | ЗІЛ -494 560 | |
Маса перевозимого вантажу, кг | ||
Єкологічний клас | Євро3 | |
Кабіна | двох дверна | |
Коробка передач | п’ятиступінчаста | |
Радіус повороту, м | 7,8 | |
Максимальна швидкість, км / год | ||
Колеса | 6,5Jх16Н2 | |
Місткість вантажної платформи, | 5,4 | |
Напрямок розвантаження | назад | |
Кут підйому вантажної платформи, град. | ||
Внутрішні розміри вантажної платформи, мм | 3050×2337×780 | |
Повна маса транспортного засобу, кг | ||
Габаритні розміри, мм | 6250×2500×2660 | |
Двигун | ||
Потужність двигуна, кВт (к.с.) | 98,7 (134) | |
Модель | ММЗ Д245.9 Е3 | |
Тип | дизельний | |
Робочий об'єм, л | 4,75 | |
Ступінь стиснення | ||
Потужність, кВт / к.с. при | 95,7/130 | |
Максимальний крутний момент, кгс. м / Н. м при | 45/446 | |
Підготовка вихідних даних до технологічного розрахунку на ПЕОМ
Таблиця 1.2 — Вихідні дані до технологічного розрахунку
Найменування нормативів | Позначення | Розмірність | Рухомий склад | |
ЗІЛ 4545 | ||||
Середньодобовий пробіг | lсд | км | ||
Нормативна періодичність ТО1 | км | |||
Нормативна періодичність ТО2 | км | |||
Нормативний пробіг до КР | км | |||
Нормативна трудомісткість ЩО | люд-г | 0.47 | ||
Нормативна трудомісткість ТО1 | люд-г | 13.20 | ||
Нормативна трудомісткість ТО2 | люд-г | 61.10 | ||
Нормативна трудомісткість ПР | люд_г/1000 км | 28.00 | ||
Кількість машин | Асп | од. | ||
Таблиця 1.3 — Таблиця значень коректувальних коефіцієнтів
Параметри | Значення коректувальних коефіцієнтів | ||||
Пробіг до КР | Періодичність ТО | Трудомісткість ТО | Трудомісткість ПР | ||
К1 | 1.10 | 1.10 | ; | 1,2 | |
К2 | 1.20 | ; | 1.20 | 1.20 | |
К3 | 0.90 | 0.90 | ; | 0.90 | |
К4 | ; | ; | ; | 1.06 | |
К4' | ; | ; | ; | 1.03 | |
К5 | ; | ; | 1.20 | 1.20 | |
Таблиця 1.4 — Коректування нормативних пробігів ТО та КР ЗІЛ 4545 бортовий
Найменування параметру | Нормативне значення, км | Значення корект. коеф. | Відкоректовані значення, км | Кратність | Кінцеві значення, км | |||
К1 | К2 | К3 | ||||||
lсд | ; | ; | ; | |||||
1.10 | ; | 0.90 | ||||||
1.10 | ; | 0.90 | ||||||
1.10 | 1.20 | 0.90 | ||||||
Таблиця 1.5 — Вихідні дані для розрахунку на ПЕОМ
№ | Форма підготовки даних | Пояснення | |
ЗІЛ 4545 | |||
1. | ЗКА101 Друмов К.I. ЗІЛ 4545 | Дані студента | |
2. | Кількість варіантів | ||
3. | lсд | ||
4. | LTO-1 | ||
5. | LTO-2 | ||
6. | LКР | ||
7. | Др.р | ||
8. | 0,55 | ДТО-ПР | |
9. | ДКР | ||
10. | АСП | ||
11. | 1.10 | К1 | |
12. | 1.20 | К2 | |
13. | 0.90 | К3 | |
14. | 1.06 | К4 | |
15. | 1.20 | К5 | |
16. | 1.03 | К4' | |
17. | 0.35 | КМ | |
18. | 0.47 | ||
19. | 13.20 | ||
20. | 61.10 | ||
21. | 28.00 | ||
22. | Тип рухомого складу | ||
Програма та об'єм робіт технічної служби підприємства
Роздруківка на ПЕОМ приведені в додатку. На його підставі складаємо зведену річну програму та обсяги робіт виробництва і представляємо у виді таблиці 1.6.
Таблиця 1.6 — Зведені дані розрахунків ПЕОМ
Параметри | ЗІЛ 4545 | ||
Річна програма, од. | |||
ЩО | |||
ТО1 | |||
ТО2 | |||
Д1 | 577.0 | ||
Д2 | 152.0 | ||
Добова програма, од. | |||
ЩО | 25.1 | ||
ТО1 | 1.3 | ||
ТО2 | 0.4 | ||
Д1 | 1.9 | ||
Д2 | 0.5 | ||
Продовження таблиці 1.6 | |||
Коефіцієнт технічної готовності | 0.835 | ||
Сумарний річний пробіг | |||
Результати розрахунку трудоємкості, люд.-год. | |||
ЩО | |||
ТО1 | |||
ТО2 | |||
ПР | |||
Підсумкова трудомісткість, люд.-год. | |||
Підсумок | |||
ТС | |||
Розподіл трудомісткості ТО за видами робіт, люд.-год. | |||
ТО1 | ТО2 | ||
Діагностичні | |||
Крипільні | |||
Регулювальні | |||
Мастильні | |||
Електротехнічні | |||
Система живлення | |||
Шинні | |||
Кузовні | |||
Прибиральні роботи | |||
Мийні роботи | |||
Розподіл трудомісткості ПР за видами робіт, люд.-год. | |||
Постові роботи | |||
Діагностичні | |||
Регулювальні | |||
Розбірно-складальні | |||
Зварювально-бляшані | |||
Малярні | |||
Закінчення таблиці 1.6 | |||
Дільничні роботи | |||
Агрегатні | |||
Слюсарно-механічні | |||
Електротехнічні | |||
Акумуляторні | |||
Система живлення | |||
Шиномонтажні | |||
Вулканізаційні | |||
Ковальсько-ресорні | |||
Мідницькі | |||
зварювальні | |||
Бляшані роботи | |||
Арматурні | |||
Деревообробні | |||
Оббивні | |||
Таблиця 1.7 — Річні обсяги трудомісткості робіт підрозділів АТП
№ | Найменування підрозділу | Річний об'єм робіт люд.-год | |
Виробничі зони: | |||
1. | Щоденне обслуговування ЩО | ||
2. | Технічне обслуговування ТО1 | ||
3. | Технічне обслуговування ТО2 | ||
4. | Діагностика Д1 | ||
5. | Поточного ремонту ПР | ||
Виробничі дільниці: | |||
1. | Агрегатна | ||
2. | Слюсарно-механічна | ||
3. | Електротехнічна | ||
4. | Системи живлення | ||
5. | Шиномонтажна | ||
6. | Теплова | ||
7. | Оббивна | ||
8. | Ковальсько-ресорна | ||
9. | Малярна | ||
10. | ВГМ | ||
Розрахунок чисельності виробничих робочих агрегатної дільниці
Розраховуємо технологічно необхідну РТ і штатну РШ кількість робітників.
Технологічно необхідна кількість робітників, тобто тих, які безпосередньо забезпечують виконання річного об'єму робіт ТО і ТР в загальному, або за видами робіт розраховується за формулою:
(1.1)
де:
— річний об'єм робіт агрегатної дільниці, люд-год;
ФТ — явочний фонд часу, технологічно необхідний робітнику при однозмінній роботі, год. Явочний фонд часу становить 2070 год.
Штатна кількість виробничих робітників, тобто те, яке приймається підприємством з урахуванням втрат робочого часу на відпустки, хвороби і з інших причин, визначається за формулою:
(1.2)
де:
ФШ — фонд робочого часу штатного працюючого, год.
Фонд робочого часу штатного працюючого становить 1840 год.
1.4 Проектування виробничої зони, виробничої дільниці по технічному обслуговуванню і поточному ремонті
Призначення.
Агрегатна дільниця призначена для виконання робіт по поточному ремонту агрегатів і вузлів автотранспортних засобів.
До складу агрегатної дільниці входять: розбірно-мийне обладнання, обладнання ремонту агрегатів, обладнання ремонту і випробування гідромеханічної передачі.
Основні роботи, що виконуються на дільниці.
На дільниці виконуються розбірні, мийні, ремонтні роботи, збірка, контроль і випробування наступних агрегатів і вузлів: переднього і заднього моста, коробки передач, гідромеханічної передачі, зчеплення, карданної передачі, рульового управління, вузлів гальмівної системи.
Крім того, тут виконується розточування гальмівних барабанів, обточування гальмівних накладок і відновлення різьбових отворів в корпусних деталях.
Режим робіт і кількість працюючих.
Для виконання всього об'єму робіт на дільниці необхідно дев’ять чоловік. Режим роботи дільниці - однозмінний
Короткий опис технологічного процесу.
Агрегати і вузли автомобіля, що вимагають ремонту розбирають, миють і дефектують. При цьому деталі придатні до подальшої експлуатації ремонтують — та реставрують, а вибраковані складуються в скриню для відходів.
На робочих місцях відділення ремонту виробляється збірка агрегатів і вузлів на базі придатних, нових і таких, що реставруються деталей, доставлених з розбірно-мийного відділення і із складу.
Відремонтовані агрегати і вузли доставляються на пости зони поточного ремонту або на проміжний склад.
Оснащення дільниці технологічним устаткуванням.
Робоче місце слюсаря оснащене технологічним устаткуванням і оргтехоснасткою, необхідними для виконання заданого об'єму робіт.
Розбирання агрегатів і вузлів виробляється на столі. Для розбирання використовується пневматичний гайковерт і комплект інструменту.
Для деталей, що вимагають при митті вживання органічних миючих засобів, встановлена ванна.
Дефектація деталей виробляється на столі. Придатні деталі складуються на стелажі. Підставка використовується для агрегатів і вузлів, що чекають розбирання.
Ремонту агрегатів і вузлів.
Для виконання заданого об'єму робіт у відділенні передбачено чотири робочих місця. На одному з них здійснюється ремонт коробок передач.
Збірка коробок передач виконується на універсальному стенді з поворотним столом. Завдяки наявності змінних плит на нім можна виробляти збірку коробок передач різних модифікацій.
Збірка редуктора заднього моста виконується на стенді, який складається з двох стійок з підшипниками для установки поворотного столу під кріплення редуктора. Привід столу — ручний, черв’ячний. Установка, транспортування і зняття агрегатів із стендів виробляється за допомогою крану. Після ремонту агрегати складуються на стелажах.
Розточування гальмівних барабанів і обточування гальмівних накладок виконується на верстаті, до нижньої частини станини якого шарнірно сполучений з барабаном, до якого кріпиться гальмівна колодка. Зрізання накладок виробляється ножем, встановленим непорушно відносно барабана.
Переклепування фрикційних накладок гальмівних колодок і дисків зчеплення виконується на стенді, що має два універсальні пристосування: одне електромеханічне для свердління отворів в накладках, а інше — пневматичне — для клепки накладок і виготовлення заклепок.
Для збірки і регулювання зчеплення застосовується настільний пневматичний стенд.
Робочі місця оснащені інструментом.
Правила техніки безпеки при ремонті
Перед початком роботи:
1) Надіти і привести в порядок спецодяг.
2) Підготувати робоче місце. Прибрати сторонні предмети, звільнити проходи. Переконатися, що робоче місце добре освітлене. Інструмент і пристосування розкласти в зручному і безпечному для використання порядку, перевірити їх справність.
3) При виявленні несправного інструменту, пристосування, устаткування і електроосвітлення повідомити майстра.
Під час роботи:
1) Зняття, транспортування і постановку вузлів і агрегатів на стенди виробляти лише за допомогою підйомно-транспортних засобів.
2) Розбирання і збірку агрегатів виконувати лише на столі або стендах за допомогою знімачів, гайковертів і відповідних пристосувань.
3) При збірці і випробуванні агрегат на стенді надійно закріпити.
4) Несправні болти зрізати ножівкою або зрубати зубилом. При вирубуванні зубилом надівати захисні окуляри.
5) Зняття і установку пружин виробляти за допомогою спеціальних пристосувань.
6) Забороняється здувати металеву стружку з верстаків або з деталі стислим повітрям. Для видалення стружки користуватися щіткою.
7) Зняті деталі укладати на стелажі.
8) Забороняється зберігати в ящиках разом з інструментом металеві обрізання і дріт.
9) Забороняється застосовувати етилований бензин для миття вузлів і деталей.
10) Не допускати попадання змащувальних матеріалів на підлогу.
11) При здобутті травми на виробництві негайно звернутися за допомогою і повідомити майстра.
Після закінчення роботи:
1) Вимкнути устаткування і привести робоче місце в порядок. Прибрати інструмент, пристосування у відведене для цього місце.
2) Повідомити майстра про всі недоліки, виявлені під час роботи.
3) Забороняється мити руки в маслі, бензині, гасі і витирати їх дрантям, забрудненим тирсою і стружкою.
Спецодяг, захисні засоби.
Відповідно до «Типових галузевих норм безкоштовної видачі спецодягу, спецвзутті і запобіжних пристосувань робітником і службовцем автомобільного транспорту і шосейних доріг, слюсарюю по ремонту автомобілів видають: бавовняний комбінезон, комбіновані рукавиці, захисні окуляри.
Вимоги до приміщень.
Висота приміщень агрегатної ділянки має бути не менше 4,2 м.
Санітарно-технічна частина
У приміщеннях агрегатної дільниці передбачаються системи опалювання, вентиляції, внутрішнього водопроводу, гарячого водопостачання, каналізації і стислого повітря.
Опалювання.
Система опалювання виконується з умов забезпечення температури повітря в приміщеннях в холодний і перехідний періоди +16оС.
Вентиляція.
Для забезпечення нормованих параметрів повітряного середовища, встановлених санітарними і технологічними нормами, влаштовується припливно-витяжна вентиляція, розрахована на розбавлення шкідливого пару, що виділяється (пари бензину, гасу). Система вентиляції виконується з механічною і природною спонукою, місцева і загально-змінна.
Водопровід.
Для постачання водою технологічного устаткування в приміщенні розбірно-мийного відділення виконується водопровідна мережа.
Витрата води на технологічні потреби визначається характеристикою мийної машина.
Джерелом водопостачання служать внутрішньо-дворові мережі автотранспортного підприємства.
Гаряче водопостачання.
За відсутності в АТП пари в мийну машина подається гаряча вода (70.85оС) від теплової мережі або індивідуального водопідігрівача.
Каналізації.
Скидання стічних вод від мийної машини здійснюється в мережу господарчо-побутової каналізації. Для прийому стічних вод при митті підлоги і випадкових протоках в приміщеннях встановлюються трапи.
Стисле повітря.
Для забезпечення технологічного устаткування стислим повітрям на дільниці виконується система повітропостачання.
Джерелом повітропостачання на АТП — компресорна або пересувний компресор.
Електротехнічна частина
Силове електроустаткування.
По мірі надійності електропостачання всі споживачі електроенергії агрегатної дільниці відносяться до другої категорії.
Електропостачання здійснюється від місцевих електричних мереж напругою 380/220 В.
Захисне заземлення.
Всі корпуси електродвигунів розподільних пунктів, пускової апаратури, світильників мають бути заземлені. Як заземлюючі магістралі використовуються металеві конструкції будівлі, сталеві труби електропроводки.
Призначення та технологія виконання робіт агрегатної дільниці
Агрегатні роботи включають розбирально — збиральні, мийні, діагностичні та регулювальні операції по коробці передач, яка демонтована з автомобіля для поточного ремонту (ПР) в агрегатному відділенні.
В агрегатному відділенні встановлюється необхідне технологічне обладнання, яке забезпечує весь технологічний процес ремонту агрегатів.
Після діагностики технічного стану агрегат, знятий з автомобіля для ПР, встановивши на транспортний візок, транспортують в агрегатне відділення для зовнішнього миття. Попередньо з картерів агрегатів зливають масло.
Після зовнішнього миття агрегат направляється на спеціалізований стенд, який забезпечує вільний доступ до агрегату, а також поворот та нахил агрегату для зручності виконання ремонтних робіт. Розбирально — збиральні роботи різних вузлів проводяться в основному на верстаках із застосуванням універсального інструмента та спеціальних пристроїв, також використовують спеціальні пристрої, преси та відповідний інструмент.
Розібрані агрегати знежирюють в гарячому содовому розчині з подальшою промивкою в гарячій воді. Після закінчення ремонту механізмів, вузлів та деталей агрегат складають, після чого проводяться контрольно-регулювальні роботи.
В середньому орієнтовний розподіл загальних трудовитрат агрегатних робіт по коробок передач становить — 8%.
Оскільки у загальних трудовитратах агрегатних робіт значна доля (більше 50%) припадає на ремонт двигунів та їх систем, тому обслуговування і ремонт двигунів виконуються в окремому приміщенні (моторному відділенні).
В даному агрегатному відділенні встановлено необхідне технологічне обладнання, яке забезпечує весь технологічний процес ремонту агрегатів.
Агрегати і вузли потрапляючи в агрегатну дільницю поступають на зовнішнє миття і після на розбирання. Після розбирання агрегату чи вузла деталі поступають на миття у спеціальних ваннах, після чого виконується контроль і сортування. Справні деталі направляються на збирання вузлів і агрегатів. Браковані викидають в брухт. Деталі і складальні одиниці, що потребують ремонту, поступають в ремонт і після здійснення ремонтних операцій їх направляють на збирання або на зберігання в складі оборотних агрегатів.
Вибір технологічного обладнання для агрегатної дільниці
Таблиця 1.9 — Специфікація технологічного устаткування і оргтехоснастки
№ | Позначення | Найменування | Кільк. | Технічна характеристика | Площа, | |
1. | ПТ054 | Електротельфер | 4000*1500 | |||
2. | 2А125 | Верстат свердлильний | 500*1500 | 2,3 | ||
3. | ЦКБР114 | Стенд для зрізання гальмівних колодок | 1080*830 | |||
4. | Р304 | Стенд для заклепування колодок | 600*430 | 0,5 | ||
5. | Стенд для ремонту і обкатки редукторів ведучих мостів | 1020*780 | 0,8 | |||
6. | ЦКБ_Р207 | Стенд для збирання і розбирання зчеплення | 526*863 | 0,5 | ||
7. | АКТБ_25А | Стенд для збірки гідропідсилювача керма | 1020*780 | 0,8 | ||
8. | 2135−1М | Прес гідравлічний | 1520*840 | 2,6 | ||
9. | СТ-КПП1 | Стенд для розбирання-збирання коробок передач | 525*2000 | 1,1 | ||
10. | ОРГ_1468−05−230А | Стелажі | 6000*500 | |||
11. | ОМ_13 116 | Ванна для мийки деталей | 300*1400 | 0,5 | ||
12. | ОРГ_1468−07−090А | Ящик для піску | 1000*1000 | |||
13. | ОРГ_1468−07−090А | Ящик для дрантя | 300*1300 | 0,4 | ||
14. | ОРГ_1468−05−280 | Стіл для розбирання збірки металевий | 2000*500 | |||
15. | СД_3701−04 | Верстат слюсарний | 1500*1500 | 2,3 | ||
16. | ОРГ_1468−07−010А | Шафа для приладів та інструментів | 1200*500 | 0,6 | ||
Сумарна площа устаткування, | 31.4 | |||||
Розрахунок площі та планування агрегатної дільниці
Площа агрегатної дільниці визначається з урахуванням сумарної площі технологічного обладнання дільниці та коефіцієнта щільності розташування обладнання:
де:
fоб — сумарна площа технологічного обладнання дільниці;
КП — коефіцієнт щільності розташування обладнання. (КП = 4,5)
Для розрахунку сумарної площі технологічного обладнання використовуємо таблицю технологічного обладнання 1.8.
Виходячи з розрахунку сумарної площі технологічного обладнання дільниці маємо fоб = 31,4 м2. Отже площа агрегатної дільниці дорівнюється:
2. Розробка конструкції стенда
2.1 Призначення та принцип роботи стенда
Стенд призначений для розбирання та складання коробок передач вантажних автомобілів. Його компонувальна схема показана на рисунку 2.1.
Стенд складається з опорної плити прикріплена до фундаменту чотирма болтами. Плита встановлюється на підставу рами 10. У середній частині стенду на стійці 5 встановлений поворотний стіл 14, який вручну може повертатися навколо осі стійки і фіксуватися механізмом 13 від педального приводу 11. Поворот столу здійснюється за допомогою кулькового підп'ятник 17, який встановлюється на опорну втулку, яка є опорою ковзання столу. Для забезпечення жорсткості столу всередині швелера приварені ребра жорсткості. Двулістний стенд одночасно забезпечує складання та розбирання двох коробок передач. На столі є два кронштейна 16, на які встановлюють коробки передач і закріплюють їх регульованими упорами 3.
Упор дозволяє регулювати розмір коробок по ширині при їх установці і кріплення болтами на кронштейні. Закріплення коробки здійснюється гідроциліндром 1 двох сторонньої дії. Гідроциліндри встановлюються в хомутики 2 і кріпляться з торцевого боку болтами.
Насос 19 призначений для нагнітання масла в гідроциліндри. Крутний момент насосу передається від електродвигуна 4. Насос і електродвигун встановлюються на столі і кріпляться болтами.
Для полегшення процесу відвернення болтів при знятті кришок коробок передач на центральній стійці, у верхній частині стенду кріпитися механічний гайковерт 20 за допомогою затискних болтів 8, використовуваний для відкручування і загортання болтів і гайок на коробці передач при розбиранні і збірці. Для забезпечення маневреності гайковерти він закріплюється на консолі складається з двох частин, з'єднаних один з одним за допомогою шворня 7 і двох шарикопідшипників.
Крутний момент на шпиндель 21 механічного гайковерти передається від електродвигуна 22 через ланцюгову передачу. У корпус шпинделя вбудована муфта вільного ходу, внутрішня частина якої пов’язана зі шпинделем, а зовнішня — з корпусом шпинделя.
Рисунок 2.1 — Загальний вигляд схеми стенда для ремонту коробок передач: 1_гидроцилиндр; 2_хомут; 3_упор; 4_електродвигун; 5_стійка; 6_шарикопідшипник; 7_шкворень; 8_затискной болт; 9_коробка передач; 10 — підстава рами; 11_педаль; 12_тяга; 13_фіксуючий механізм; 14_стіл поворотний; 15_гидробак; 16_кронштейн для кріплення коробки передач; 17 — кульковий підп'ятник; 18_болт; 19_насос для нагнітання масла; 20 — механічний гайковерт; 21_шпиндель; 22_електродвигун.
2.2 Розрахунок конструкції стенда
Розрахунок балки стола на вигин
Схема для розрахунку балки столу на вигин наведена на малюнку 2.2.
Рисунок 2.2 — Схема для розрахунку балки столу на вигин Вихідні дані для розрахунку:
1) вага коробки передач Р = 1200, Н;
2) плече сили l = 1, м.
Допустиме напруження на вигин:
Де Ми — згинальний момент, Н · м;
W — момент опору вигину, м.
Для сталі 3
Тоді
або
За величиною моменту опору W=6,4 см3, вибираємо швелер Швелер для якого Wy = 13,8 см3.
Розрахунок труби стойки на вигин
Схема для розрахунку труби стійки на вигин наведена на малюнку 2.3.
Рисунок 2.3 — Схема для розрахунку труби стійки на вигин Вихідні дані для розрахунку:
1) момент опору W=6,4 см3;
2) коефіцієнт б=0,9.
Момент опору вигину труби визначаються:
де D — зовнішній діаметр труби, см;
б — відношення внутрішнього діаметра до зовнішнього приймаємо
або
Товщина стінки труби
або
За довідником вибираємо трубу
Розрахунок зварних з'єднань
Схема для розрахунку зварювального з'єднання наведена на малюнку 2.4.
Рисунок 2.4 — Схема для розрахунку зварювального з'єднання Вихідні дані для розрахунку:
1) катет шва К = 6, мм;
2) зовнішній діаметр труби d = 120, мм.
Напруга в шві від згинального моменту:
Тоді або
Розрахунок зусилля затиску коробки передач
Схема для розрахунку зусилля затиску коробки передач наведена на рисунку 2.5.
Рисунок 2.5 — Схема для розрахунку зусилля затиску коробки передач Вихідні дані для розрахунку:
1) момент затягування болтів М = 55, Нм;
2) вага коробки Р = 1200, Н;
3) коефіцієнт тертя f = 0,16;
4) коефіцієнт запасу К = 2.
Нехтуючи реакцією опор і вагою заготовки, можна записати умову рівноваги як суму моментів відносно точки О:
де F1 — сила тертя між деталлю і штоком поршня, Н;
F2 — сила тертя між деталлю і опорою, Н.
В свою чергу:
де Q — зусилля на штоку гідроциліндра, Н;
Тоді
Зусилля на штоку:
Тоді
З урахуванням коефіцієнта запасу зусилля затиску:
Або
3. Розробка технологічного процесу
Розробка технологічного процесу
Догляд за коробкою передач полягає в підтяжці її кріплень до картера зчеплення і перевірці рівня оливи в її картері, доливання її і зміні відповідно до карти змащення.
Зливати оливу потрібно відразу після поїздки, поки вона гаряча. Якщо відпрацьована олива виявляється сильно забрудненою, коробку варто промити рідкою мінеральною оливою.
Перевірку рівня оливи роблять через заливний отвір на автомобілі, який розміщують на горизонтальній площині. Перевірку варто робити через якийсь час після поїздки, щоб дати можливість охолонути і стікти оливі зі стінок, а піні осісти.
У процесі експлуатації варто звертати особливу увагу на стан сапуна. Він служить для з'єднання внутрішньої порожнини коробки з атмосферою, і його забруднення приводить до підвищення тиску і виникненню течі оливи.
У початковий період експлуатації до приробляння сальників допускаються незначне (без каплепадіння) просочування оливи і поява масляного нальоту на днищі кузова.
Основні зовнішні дефекти коробок передач: підвищений шум і стуки під час роботи машини; погане включення або самовідключення шестерень внаслідок спрацювання підшипників та їх посадочних місць, спрацювання шестерень, шліцьових, шпонкових і різьбових з'єднань, а також тріщини і зломи в деталях.
Підвищене спрацювання підшипників кочення і зубів шестерень по товщині є причиною попадання абразивних частинок у мастило через нещільності.
Торцеві руйнування зубів шестерень з боку включення — результат неточного регулювання зчеплення і неправильного переключення передач.
Втомлювальне викришування робочих поверхонь зубів значно підвищується при неправильному зачепленні шестерень — збільшенні або зменшенні міжосьової відстані, неповному включенні, перекосі зчеплення, неправильному регулюванні конічного зачеплення.
Спрацювання шліців (по товщині) і шпонкових канавок — результат високих питомих тисків і ударних навантажень при збільшеному зазорі у шліцьовому або шпонковому з'єднанні.
Розбирання
Повністю коробки передач розбирають тільки при капітальному ремонті. При поточному ремонті або експлуатаційному ремонті автомобіля після зовнішнього і внутрішнього миття й часткового розбирання перевіряють технічний стан деталей коробки: вимірюють ступінь спрацювання зубів по довжині і товщині; по осьовому і радіальному переміщенню валів визначають ступінь спрацювання підшипників; ступінь спрацювання шліцьових і шпонкових з'єднань, а також міцність посадки вінців на втулках контролюють переміщенням шестерень. При потребі коробку направляють на капітальний ремонт.
Повністю коробку розбирають на спеціальних або універсальних стендах, застосовуючи при цьому прості й універсальні знімачі і пристрої.
Рисунок 3.1 — Картер і кришка коробки передач
Технологічна карта процесу розбирання КПП ЗІЛ 4545
Обладнання та інструменти: знімач для гнізда картера підшипника первинного вала; мідна виколотка; молоток; плоскогубці; викрутка; торцевий ключ 14 мм; гайковерт; гайкові ключі, головки 10,12,14, та 32 мм.
Таблиця 3.1 — Технологічна карта процесу розбирання КПП
№ | Найменування операції та зміст переходу | Ескіз | Обладнання, пристрої, інструмент | Технічні умови | Норма часу, хв. | |
I. | Встановлення КПП на стенд | Для установки КПП на стенд відчинити та встановити кронштейн кріплення | ||||
II. | Розбирання КПП | Викрутка, гайковерт | Попередньо злити мастило. | |||
2.1 | Вивернути з картера болти кріплення до нього верхньої кришки. Зняти її в зборі з механізмом перемикання передач і прокладку. | Гайковерт, набір торцевих голівок | ||||
2.3 | Вивернути з картера болти кріплення кришки підшипника первинного вала до нього, зняти її прокладку. Знімачем випресовати з гнізда картера підшипник разом з первинним валом. | Знімач | ||||
2.4 | Роскернити гайку кріплення фланця вторинного вала, відвернути її, зняти шайбу і фланець. | Молоток | ||||
2.5 | Зняти з кінця вторинного валу провідну шестерню приводу спідометра. Випресовати з гнізда картера коробки підшипник вторинного валу разом з валом за допомогою оправи і молотка. Спресувати за допомогою пристосування підшипник вторинного валу. | Знімач, викрутка | Зняти з вала синхронізатор четвертої та п’ятої передач, шестерню першої передачі. | |||
2.6 | Витягти з картера вторинний вал разом з підшипником і затятим кільцем. Зняти з вала синхронізатор, шестерню третьої передачі з распорной втулкою, роспорну шайбу, шестерні другої та першої передачи. Вивернути з картера болти кріплення кришки заднього підшипника проміжного валу до нього, зняти її і прокладку. Подальшу розробку коробки передач не робити. | Виколотка і молоток | ||||
4. Основні види фізико-хімічного руйнування автомобілів
Основні види фізико-хімічного руйнування автомобіів
Основними видами руйнувань, що призводять до граничних (непрацездатних) станів деталей автотранспортних засобів, є статичне руйнування, втомленість, корозія, спрацювання та старіння.
Статичне руйнування — процес руйнування деталі під дією перевантаження, одноразового перевищення навантаженням міцнісних властивостей елементів автомобілів. Ознаками граничного стану є: крихке руйнування, крихкий злам, сколювання торців. Статичного руйнування зазнають зварні з'єднання, фасонні деталі, болти, валики, пальці та чавунні виливки.
Втомленість — процес руйнування деталі під впливом багаторазово повторюваних навантажень. Розрізняють втомленість малоі багатоциклову. Ознаки малоциклової втомленості - повзучість, в’язкий злам, заїдання. Малоциклової втомленості зазнають корпусні деталі, зубчасті колеса, вали, осі, пружини, посудини, підшипники ковзання. Ознаки багатоциклової втомленості - руйнування від втомлення, злам від втомлення, викришування, кавітація. Багатоциклової втомленості зазнають корпусні деталі, зубчасті колеса, підшипники кочення, вали, осі, пружини, шатуни, болти, зварні з'єднання.
Корозія — процес руйнування матеріалів унаслідок їхньої хімічної та електрохімічної взаємодії з навколишнім середовищем. Ознаки граничного стану — ерозія (газова, рідинна); корозія (атмосферна, при терті, в електролітах). Корозії зазнають елементи трубопроводів, робочі камери, кабіни, кузови, деталі насосів, латунні, дюралюмінієві, магнієві сплави та ін.
Основним видом руйнування механізмів автомобіля є спрацьовування
деталей — процес відокремлення матеріалу з поверхні твердого тіла і (або) збільшення його залишкової деформації при терті, яке проявляється в поступовій зміні розмірів і (або) форми тіла.
Спрацьовування, крім порушень механічних зв’язків між деталями, спричиняє порушення термодинаміки згоряння у двигуні, запалювання в електроустаткуванні, утворення суміші в системі живлення та ін. Спрацьовування деталей часто супроводжується деформаціями, нагромадженням напружень від втомлення тощо. Спрацьовування супроводжується також механічними й фізико-хімічними явищами, які ускладнюються тим, що на них істотно впливають проміжне середовище (мастильні матеріали, повітря) і фактори навколишнього середовища: температура, вологість і запиленість повітря, дія сонячного проміння та ін. Основною причиною спрацьовування деталей автомобіля є тертя.
Класифікація видів тертя наводиться нижче.
Тертя спокою — тертя двох тіл при мікрозміщеннях, без макрозміщення.
Тертя руху — тертя двох тіл, що рухаються одне відносно одного.
Тертя без мастильного матеріалу — тертя двох тіл, коли на поверхні тертя немає введеного мастильного матеріалу будь-якого виду.
Тертя з мастильним матеріалом — тертя двох тіл, коли на поверхні тертя є введений мастильний матеріал будь-якого виду.
Тертя ковзання — тертя руху, при якому швидкості тіл у точці стикання різні за значенням і (або) напрямом.
Тертя кочення — тертя руху, при якому швидкості стичних тіл однакові за значенням і напрямом принаймні в одній точці зони контакту.
Тертя кочення з проковзуванням — тертя руху двох стичних тіл при одночасному терті кочення і ковзання в зоні контакту.
Поверхні тертя мають мікронерівності, розміри яких залежать від точності обробки. При терті взаємодіють мікронерівності тертьових поверхонь між собою і з абразивними частинками, що потрапили в масло. Руйнування кількох шарів мікронерівностей призводить до макропошкоджень, тобто змін форми поверхні. Тертя ковзання в двигуні відбувається між поршневим кільцем і дзеркалом циліндра, між шийками колінчастого вала і підшипниками; тертя кочення — в шарико і роликопідшипниках.
У механізмах автомобіля можуть бути одночасно кілька видів тертя. Наприклад, робота шестерень коробки передач супроводжується тертям кочення і ковзання. Залежно від умов та режиму тертя, від якості тертьових поверхонь, мастильних матеріалів і дії зовнішнього середовища характер спрацьовування деталей механізмів може бути різним.
Оцінюючи явища і процеси при терті і спрацьовуванні, застосовують такі терміни: стрибкоподібний рух при терті, схоплювання при терті, перенесення матеріалу, заїдання, задирка, дряпання, відшаровування, викришування, припрацювання.
Стрибкоподібний рух при терті — явище чергування відносного ковзання і відносного спокою або чергування збільшення і зменшення відносної швидкості ковзання, яке виникає мимовільно при терті руху. Прикладом стрибкоподібного руху може бути рух, що виникає внаслідок автоколивань при зниженні коефіцієнта тертя зі збільшенням швидкості ковзання.
Схоплювання при терті — явище місцевого з'єднання двох твердих тіл, що настає внаслідок дії молекулярних сил при терті.
Перенесення матеріалу — явище при терті твердих тіл, яке полягає в тому, що матеріал одного тіла з'єднується з іншим і, відриваючись від першого, залишається на поверхні другого.
Заїдання — процес виникнення і розвитку пошкоджень поверхонь тертя внаслідок схоплювання і перенесення матеріалу. Заїдання може завершуватися припиненням відносного руху.
Задирка — пошкодження поверхні тертя у вигляді широких і глибоких борозен у напрямі ковзання.
Дряпання — утворення заглиблень на поверхні тертя в напрямі ковзання при дії виступів твердого тіла або твердих частинок.
Відшаровування — відокремлення з поверхні тертя матеріалу у формі лусочок при спрацьовуванні від втомлення.
Викришування — утворення ямок на поверхні тертя в результаті відокремлення частинок матеріалу при спрацьовуванні від втомлення.
Припрацювання — процес зміни геометрії поверхонь тертя і фізико-хімічних властивостей поверхневих шарів матеріалу в початковий період тертя, який звичайно проявляється за постійних зовнішніх умов у зменшенні сили тертя, температури й інтенсивності спрацювання.
Спрацювання — результат спрацьовування, який визначається в установлених одиницях. Значення спрацювання може виражатися в одиницях довжини, об'єму, маси та ін.
З метою виявлення основного процесу руйнування поверхні і керування ним розроблено класифікацію видів спрацьовування.
Механічне спрацьовування — спрацьовування в результаті механічних дій. Воно визначається різанням, виламуванням частинок, пластичним деформуванням та ін. Найпоширеніше механічне спрацьовування — це абразивне.
Абразивне — механічне спрацьовування матеріалу в результаті ріжучої або дряпаючої дії твердих тіл чи твердих частинок, які мають різну форму й по-різному орієнтовані своїми гострими ребрами щодо спрацьованої поверхні. Одні з них мають різальну дію, інші пластично деформують м’який матеріал, залишаючи сліди у вигляді видавлених рисок. У результаті багаторазового переміщення частинок поверхневий шар деталі поступово руйнується. Абразивні частинки можуть потрапляти на тертьові поверхні разом із повітрям, паливом, мастильними матеріалами тощо. Абразивного спрацьовування в поєднанні з іншими видами зазнають практично всі тертьові деталі автомобіля.
Гідроабразивне (газоабразивне) — абразивне спрацьовування в результаті дії твердих тіл або твердих частинок, захоплених потоком рідини (газу).
Гідроерозійне (газоерозійне) — спрацьовування поверхні в результаті дії потоку рідини (газу). Цей вид спрацьовування характерний для паливної апаратури дизельних двигунів, жиклерів карбюраторів, випускних клапанів двигуна.
Кавітаційне — механічне спрацьовування при русі твердого тіла відносно рідини, при якому пухирці газу захлопуються поблизу поверхні, що створює місцевий ударний тиск або високу температуру. Кавітаційне руйнування іноді буває у водяних насосах, на зовнішніх поверхнях мокрих гільз циліндрів та в інших деталях автомобіля.
Спрацьовування від втомлення — механічне спрацьовування в результаті руйнування від втомлення при повторному деформуванні мікрооб'ємів матеріалу поверхневого шару. Спрацьовування від втомлення може відбуватись як при терті кочення, так і при терті ковзання.
При фретинзі — механічне спрацьовування стичних тіл при коливальному відносному мікрозміщенні.
При заїданні — спрацьовування в результаті схоплювання, глибинного виривання матеріалу, перенесення його з однієї поверхні тертя на іншу та дії утворених нерівностей на спряжену поверхню. Схоплювання металу і перенесення його з однієї деталі на іншу, виривання частинок із поверхні однієї деталі і налипання на інші, заїдання спряжених деталей внаслідок виникнення молекулярного зчеплення між тертьовими поверхнями бувають у підшипниках ковзання, втулках валів, поршнях та інших деталях, особливо в процесі припрацювання механізмів. При інтенсивному схоплюванні металів відбувається процес наволікання шару менш міцного металу на поверхню міцнішого.
Корозійно-механічне спрацьовування — спрацьовування в результаті механічної дії, що супроводжується хімічною та (або) електричною взаємодією матеріалу з середовищем (киснем, газами, кислотами, лугом). Взаємодія середовища з поверхневими шарами металу призводить до утворення нових хімічних сполук, які різко змінюють властивості тертьових активних шарів металу.
При цьому тертьові поверхні спрацьовуються внаслідок періодичного утворення і руйнування менш міцного шару. Корозійно-механічного спрацьовування зазнають циліндри двигуна, вкладиші підшипників, шийки колінчастого вала та інші деталі внаслідок дії сірчаної, сірчистої та органічних кислот.
Окислювальне — корозійно-механічне спрацьовування, при якому переважає хімічна реакція матеріалу з киснем або окислювальним навколишнім середовищем.
При фретинг-корозїї — корозійно-механічне спрацьовування стичних тіл при малих коливальних відносних переміщеннях.
Електроерозійне — ерозійне спрацьовування поверхні в результаті дії розрядів при проходженні електричного струму.
Залежно від умов роботи одна й та сама деталь може зазнавати одночасно дії кількох видів спрацьовування.
Наприклад, верхня частина циліндра двигуна зазнає водночас механічного і корозійно-механічного спрацьовування.
Процес наростання спрацьовування поверхневих шарів має певні закономірності (рисунок 4.1).
Спрацьовування у підвищується протягом усього пробігу L автомобіля до певного стану деталі, але інтенсивність спрацьовування різна на різних етапах роботи.
Рисунок 4.1 — Залежність спрацювання та інтенсивності спрацьовування деталі автомобіля від його пробігу (для усталених умов експлуатації)
У початковий період роботи (припрацювання) деталі спрацьовуються дуже інтенсивно (ділянка ОА) до якогось значення, характерного для цих умов роботи, потім процес переходить у зону усталеного спрацьовування (ділянка АВ), різко зростає і переходить в аварійне спрацьовування. У міру припрацювання знижується інтенсивність спрацьовування внаслідок збільшення площі поверхонь за рахунок спрацьовування, а також зміни мікрогеометрії тертьових поверхонь деталей і тиску.
Спрацьовування на ділянці АВ називається нормальним (природним). Воно характеризується сталістю умов роботи тертя і швидкості спрацьовування цього спряження. Після точки В спрацьовування різко зростає внаслідок збільшення зазору між тертьовими поверхнями, зростання динамічних навантажень, погіршення режиму мащення та ін. Отже, збільшення зазорів між деталями має бути обмеженим.
Якщо працююче спряження розібрати, то після складання інтенсивність спрацьовування збільшується порівняно з початковим за рахунок нового припрацювання його деталей. Таким чином, розбирати автомобіль і його елементи можна тільки в разі крайньої потреби.
Старіння — процес поступової і неперервної зміни експлуатаційних властивостей, що спричиняється дією механічних, електричних, теплових та інших навантажень, наявність яких визначається режимом роботи й умовами експлуатації автомобіля. Ознаки граничного стану старіння — необоротна зміна фізико-хімічних властивостей матеріалів деталей (втрата пружності та ін.). Старіння зазнають елементи і деталі з металів, полімери, гумотехнічні вироби, ущільнення, напівпровідники.
Вплив основних факторів на зміну технічного стану автомобілів
На технічний стан автомобіля впливають конструктивні, технологічні, експлуатаційні та інші фактори.
Конструктивні фактори визначаються формами й розмірами деталей (від них залежать тиск на поверхню деталі, концентрація напружень, ударна міцність і міцність від втомлення металу); жорсткістю конструкції, тобто властивістю деталей, особливо базових та основних, трохи деформуватися під дією навантажень, що сприймаються; точністю взаємного розміщення поверхонь та осей спільно працюючих деталей; правильним вибором посадок, які забезпечують надійну роботу спряжень та ін.
Технологічні фактори залежать від якості матеріалів, що використовуються для виготовлення деталей, застосування відповідної термічної обробки їх та складальних робіт (центрування, співвісності, регулювання зазорів, якості кріплення) та ін.
Експлуатаційні фактори залежать від дорожніх, транспортних і кліматичних умов. Вони найбільше впливають на технічний стан автомобілів. Дорожні умови характеризуються типом, станом і міцністю покриттів, поздовжнім профілем дороги, режимом руху, видимістю тощо. Кліматичні умови в різні періоди року визначаються температурою і вологістю повітря, атмосферним тиском, кількістю опадів, силою і напрямком вітру, тривалістю снігового покриву та ін. Транспортні умови охоплюють обсяг і відстань перевезень, умови вантаження і розвантаження, особливості організації перевезень, умови зберігання, обслуговування та ремонту автомобілів.
Залежно від умов експлуатації змінюються швидкісні і навантажувальні режими деталей, механізмів та агрегатів автомобілів і термін їхньої безвідмовної роботи. Наприклад, на коротких маршрутах частіше користуються зчепленням, гальмами, переключають передачі і зчеплення, внаслідок чого збільшується ймовірність їхніх відмов. При експлуатації автомобілів у важких дорожніх умовах збільшуються навантаження на деталі автомобіля, в результаті чого деталі швидше спрацьовуються, настає втомлення металу, порушується стабільність кріплень і регулювань, а в деяких випадках трапляються поломки деталей трансмісії, ходової частини і рульового керування. Різні дорожні умови впливають на зміну характеру дії навантажень. Вібрація рами внаслідок нерівностей дороги ослаблює заклепкові з'єднання, порушує співвісність двигуна і коробки передач, спричиняє додаткові навантаження у корпусах. Вібрація автомобіля прискорює спрацьовування і призводить до поломки кріпильних деталей карданної передачі, радіатора і підвіски.
Зниження температури навколишнього повітря, погіршення стану дороги внаслідок снігових заметів або бездоріжжя спричиняють додаткове передчасне спрацьовування або поломки деталей автомобіля (спрацьовування шліців, шипів і підшипників хрестовини, зрізування шпильок кріплення підвісної опори та ін.).
Щоб зменшити вплив кліматичних умов на робочі процеси автомобіля, створені спеціальні мастильні матеріали. Робота автомобіля на вологих дорогах, а також в умовах вологого клімату спричиняє корозію деталей підвіски, рами, кузова, крил, кабіни та ін.
На термін служби силових передач автомобіля істотно впливає їхній тепловий режим. Він визначається температурою навколишнього повітря, ступенем завантаження автомобіля, його швидкістю й залежить від довжини маршруту, тривалості простою під вантаженням і вивантаженням, якості ТО та інших показників.
У процесі роботи і зберігання автомобіля деякі його агрегати і деталі перебувають у постійній взаємодії з експлуатаційними матеріалами. Властивості цих матеріалів та умови їхнього застосування позначаються на процесі спрацьовування і корозії деталей, витрачанні мастильних матеріалів, продуктивності автомобіля. Експлуатаційні матеріали повинні відповідати конструктивним і технологічним особливостям агрегатів автомобіля, їхньому технічному стану й умовам експлуатації.
Значно впливає на технічний стан автомобіля якість його водіння, від якого залежать динамічні навантаження в деталях трансмісії автомобіля. Найбільш дієвими є режими рушання з місця в разі застрявання автомобіля. При різкому включенні зчеплення крутний момент, що прикладається до трансмісії, може значно перевищити максимальний крутний момент двигуна з урахуванням коефіцієнта запасу. Цим пояснюються поломки в трансмісії автомобіля, який працює в умовах поганих доріг.
Висновки
У ході виконання даної дипломної роботи була спроектована агрегатна дільниця та підібране технологічне устаткування.
Була розрахована річна виробнича програма, річний обсяг робіт технічного обслуговування та поточного ремонту, розрахована чисельність виробничих робітників, підібрано обладнання і оснащення, визначено спосіб управління виробництвом, складена технологічна карта процесу ремонту КПП.
Були закріплені, вдосконалені і поповнені знання та навички, отримані в процесі навчання з організації виробництва і технології технічного обслуговування і ремонту автомобілів, поглиблені знання з наукової організації праці та проектування автотранспортних підприємств, вивчені передові методи виробництва і отримані навички з організації агрегатного відділення та проаналізовано матеріали технологічного та конструктивного характеру.
Список літератури
1. Напольский Г. М. Технологическое проектирование автотранспортных предприятий и станций технического обслуживания. — М.: Транспорт, 1985 — 231 с.
2. Лудченко А. А. Сова И.Л. Техническое обслуживание и ремонт автомобилей. К.: Выща школа. Головное изд-во, 1983. — 384 с.
3. Б. Н. Суханов и др. Техническое обслуживание и ремонт автомобилей. Пособие по курсовому дипломному проектированию. — М.:Транспорт, 1985.
4. Техническая эксплуатация автомобилей / Под ред. Г. В. Крамаренко. — М.: Транспорт, 1983. — 488 с.
5. О. А. Крупин, С. А. Кармолин Руководство по эксплуатации РЕ 5 808 600 2006 — 110 с.
6. Лудченко АА. Основы технического обслуживания автомобилей. — К.: Выща школа. Головное изд-во, 1987. — 400 с.
7. Автомобили КамАЗ: Техническое обслуживание и ремонт/ В. Н. Барун, Р. А. Азаматов, ЕА. Машков и др. — М.: Транспорт, 1988. — 352 с.
Говорущенко Н. Я. Автомобильное топливо. Как его экономить. — Харьков: Выща шк.: Изд-во при Харьк. ун-те, 1989. — 143 с.
8. Говорущенко НЛ. Техническая зксплуатация автомобилей. — Харьков: Выща шк.: Изд-во при Харьк. ун-те, 1984. — 312 с.
9. Жегалин О. И., Лупачев ГІД. Снижение токсичности автомобильных двигателей. М.: Транспорт, 1985. — 120 с.
10. Канарчук В. Е., Чигринец АД. Бесконтактная тепловая диагностика машин. — М.: Машиностроение, 1987. — 160 с.
11. Канарчук В.Є., Дудченко О А. Система забезпечення роботоздатності автотранспортних засобів: Навч. посіб. — К.: НМК БО, 1991. — 216 с.