Изучение теорії та технології виплавки шарикопідшипникової стали марки ШХ4
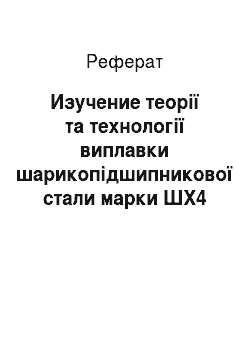
Марганець, як і хром, збільшує твердість і опірність стали истиранию. Але водночас він сприяє зростанню зерна при нагріванні, в результаті чого при термічній обробці може утворюватися грубозерниста структура перегрітої стали. Негативний вплив на в’язкість шарикопідшипникової стали надає кремній. Але марганець і кремній є раскислителями, і що вища їхня зміст, тим повнішим раскислена сталь, тому… Читати ще >
Изучение теорії та технології виплавки шарикопідшипникової стали марки ШХ4 (реферат, курсова, диплом, контрольна)
Міністерство освіти і науки Украины.
Запорізька державна інженерна академия.
Факультет М і ООС.
Кафедра МЧМ.
Курсова работа.
На тему: «Вивчення теорії та технології виплавки шарикопідшипникової стали марки ШХ4».
По курсу: «Технологія виробництва спеціальних сталей і сплавов».
Виконав: ст. грн. МЧ-2−98д.
Паламаренко А.Ю.
Перевірив: канд. тих. наук, доцент.
Воденников Сергей.
Анатолиевич.
Оцінка: ___________.
Запорожье.
Реферат.
Курсова робота містить 35 стор., 3 рис., 1 табл., 12 источников.
Мета роботи — поглиблення вивчення теорії та технології виплавки спеціальних сталей і сплавів з урахуванням аналізу та узагальнення науковотехнічної літератури та спеціалізованих журналів і изданий.
У цьому курсової роботі було розглянуто такі вопросы:
1. Сучасне стан і проблеми вітчизняної і закордонної металургійної промисловості, і навіть можливі шляхи подолання й подальшого розвитку отрасли.
2. Призначення, сферу застосування шарикопідшипникової стали марки ШХ4, і навіть сталей аналогічних марок, і навіть вимоги, які пред’являються ним.
3. Вплив легуючих елементів, шкідливих домішок, і навіть складу і виду неметалічних включень на властивості шарикоподшипниковых сталей.
4. Зроблено огляд існуючих методів виробництва шарикоподшипниковых сталей в Україні за кордоном, і навіть аналіз науково-технічної літератури, що стосується даного вопроса.
5. Розглянуто способи поліпшення існуючих технологій виробництва підшипникових сталей, і навіть напряму, і тенденції у створенні нових технологічних схем і процесів у вітчизняній й зарубіжної підшипниковому промышленности.
6. Розглянута аппаратурно-технологическая схема виробництва підшипниковому стали методом вакуумирования рідкої почав із одночасним рафинированием їх у стовпі шлаку, і навіть проаналізовано економічна ефективність впровадження даної технології на вітчизняних металургійних предприятиях.
ШАРИКОПОДШИПНИКОВАЯ СТАЛЬ, ШХ4, ВИРОБНИЦТВО, ОБРОБКА, СВОЙСТВА,.
ДОМІШКИ, ВАКУУМ-ШЛАКОВЫЙ ПЕРЕПЛАВ, ЕКОНОМІЧНИЙ ЭФФЕКТ.
Запровадження 1. Загальні відомості. 1. Призначення, види й сферу застосування шарикопідшипникової стали. 2. Щодо хімічного складу шарикоподшипниковых сталей. 3. Основні технологічні і експлуатаційні властивості, впливом геть них зовнішніх параметрів. 2. Аналіз способів виплавки шарикоподшипниковых сталей в Україні, з СНД за кордоном. 2.1 Загальна характеристика способів виплавки. 2.2 Виплавка в мартенівських печах. 2.3 Виплавка в электродуговых печах. 2.4 Спеціальні способи виплавки. 3. Аналітичний огляд літератури з питання технології, способів виплавки і розливання шарикопідшипникової стали останніми роками. 4. Вибір і з використання нових прогресивних розробок на технології виплавки шарикоподшипниковых сталей. Висновки. Перелік ссылок.
Експлуатаційні властивості більшості машин і творення механізмів (верстатів, автомобілів, авіаційних двигунів, прокатних станів, точних приладів та ін.) значною мірою залежить від точності, довговічності і надёжности підшипників качения — однієї з найважливіших і найбільш поширених елементів цих устройств.
Якість підшипників качения диктується їхнє конструкцією, технологією виготовлення й якістю використовуваного металу. У цьому роботі розглядаються питання, пов’язані із високою якістю металу — тобто. металургійні (способи виплавки і методи обробки тиском) і металловедческие аспекти технології отримання й опрацювання підшипникових сталей і сфери впливу цих факторів на експлуатаційні властивості підшипників качения. 1].
Необхідно враховувати, що металургійна галузь, як України, і усього світу останні роки сидить над дуже серйозної проблемою — перевищенням потужностями, що роблять сталь, потужностей, які її можуть використовувати. У результаті багато металургійні підприємства змушені витрачати витрачати величезні кошти на дослідження і нових технологій, які у своє чергу розгортаються за трьом основним напрямам: зниження вже готової продукції, розробка технологій, дозволяють за незмінної ціни виробляти продукцію високої якості, й розробка абсолютно нових видів продукції, здатних витіснити вже наявні над ринком товари своїми унікальними свойствами.
Дуже серйозної проблемою для країн та України в частковості і те, що ціни на всі однотипні товари (готову сталь, прокат тощо.), виготовлені в розвинених капіталістичних країнах і потребує країнах третього світу, рознятся іноді у десятки раз. У результаті розвинені країни змушені закривати на своїх ринках від напливу дешевого металу через рубежу, що може спричинити закритися багатьох металургійних підприємств якщо не зміниться. Заводи України ж у цій ситуації змушені продавати метал досить високої якості за ціною дешевого металлолома.
Виходу із нинішньої ситуації багато в чому міг би посприяти уряд, приймаючи закони: — лобирующие інтереси великих промислових підприємств, як металургійних, і машинобудівних, оскільки найчастіше останні купують метал в тих самих іноземних підприємств, які скуповують її в вітчизняних металургійних гігантів. Необхідне відповідне стимулювати на законодавчому рівні звані угоди «на підтримку вітчизняного виробника», укладені без посередників безпосередньо між українськими підприємствами; - які захищають інтелектуальну власність як шляхом адміністративних стягнень, а й кримінальних покарань; - які б збільшення частки бюджету, расходуемой для наукових досліджень і розробки, і навіть на заохочення ученим і інженерам їх створив; - які роблять механізми патентування нових розробок доступнішими і менше розтягнутими як у часі, і за кількістю бюрократичних инстанций.
Своєчасне і знайти правильне запровадження у життя завдань може бути визначального чинника по дорозі розвитку лише металургійної галузі, але й української економіки загалом, оскільки металургія сьогоднішній день є одним із основних бюджетонаповнюючих галузей промисловості Украины.
1. Загальні сведения.
1. Призначення, види й сферу застосування шарикопідшипникової стали.
Як очевидно з назви, шарикоподшипниковую сталь застосовують головним чином заради виготовлення кульок, роликів і каблучок подшипников. 2] Але номенклатура марок стали цього виду досить широка. Це розмаїттям вимог до експлуатаційним властивостями підшипників зі боку традиційних, і навіть нових галузей в промисловості й сільського хозяйства.
Найбільш распространённые підшипникові высокоуглеродистые стали можна класифікувати наступним образом:
1. Стали для підшипників, що працюють у умовах (хромистая, хромистая з добавкою молібдену, хромомарганцевокремнистая, хромомарганцевая з добавкою молибдена).
2. Стали для підшипників, що працюють у агресивних середовищах і за підвищеної температурі (коррозионно-стойкая, теплостойкая). 1].
До перших належать стали марок ШХ15, ШХ15СГ, ШХ20СГ, ШХ4, ШХ6, ШХ9 і т.д. 3] Через війну проведеного 60 р. уніфікації два останніх марки було замінено сталлю ШХ15. Назви аналогічних марок інших країнах — 52 100, 100C6, SKF-24, SUJ2 і т.д.
До других відносять стали марок 95Х18-Ш (де літера «Ш» зазначає, що сталь выплавлена методом електрошлакового переплаву, а вакуумно-дуговой переплавку стали електрошлакового переплаву позначається «ШД»), 11Х18М-ШД, ЭИ760, ЭИ347 (8Х4В9Ф2), 8Х4М4ВФ1-Ш, 8DCV40, M50, Z80WDCV6, 80MoCrV4216 і др.
Крім названих широко застосовують низкоуглеродистые цементируемые сталі та обмежено — сплави із цілком особливими фізичними свойствами.
Вибір стали конкретної підшипника диктується його розмірами і умовами эксплуатации.
З хромистой і хромомарганцевокремнистой сталей виготовляють підшипники, працюють у інтервалі температур 60 — 3000С. Експлуатація підшипників за нормальної температури, перевищує 1000С, не потребує спеціальної термічної обробки деталей, які забезпечують стабільність розмірів, але сопровождающейся зниженням твердості, і навіть опору контактної втоми стали.
Усередині зазначеного температурного інтервалу вибір хромистой чи хромомарганцевокремнистой стали визначається завтовшки стінок кілець чи діаметром тіл качения. Забезпечення наскрізний прокаливаемости кілець підшипників з товщиною стінки більш 10 мм і роликів діаметром більш 22 мм досягається заміною стали ШХ15 сталлю ШХ15СГ. Для кілець з товщиною стінки більш 30 мм у вітчизняній практиці використовують сталь ШХ20СГ, застосовується виготовлення деталей великогабаритних підшипників. Кордон розмірів деталей, вище за яку починається застосування стали ШХ20СГ чи її аналогів, в різних країнах різна. Очевидно, це пояснюється різної прокаливаемостью, зумовленої особливостями технології виплавки стали, а також різними схемами визначення товщини стінок колец. 1].
У зв’язку з впровадженням прогресивної технології термічної обробки деталей залізничних підшипників качения — поверхневою гарту при глибинному индукционном нагріванні - розроблена сталь ШХ4 з регламентованої прокаливаемостью. По складу вона відрізняється від стали ШХ15 зниженим змістом елементів, які впливають прокаливаемость стали, — марганцю, кремнію і хрома. 5].
Крім виготовлення деталей підшипників сталь ШХ15, наприклад, також застосовується також і виробництва голок розпилювачів форсунок, зворотних клапанів і подушок впрыскивающих систем, валиків паливні насоси, роликів, осей різних важелів та інших деталей, яких потрібно висока твердість і хороший опір износу. 4].
2. Щодо хімічного складу шарикоподшипниковых сталей.
По складу і властивостями цю сталь можна зарахувати до групі інструментальних сталей, але з застосуванню вона є конструкційної спеціального назначения. 2].
У таблиці 1 наводиться хімічний склад деяких марок шарикопідшипникової стали: хромистой, хромомарганцевокремнистой і коррозионностойкой; порівнювати також вказані марки деяких зарубіжних производителей.
Проблема недостатньою прокаливаемости і теплостойкости виробів із хромистой і хромомарганцевокремнистой сталей у низці країн вирішена шляхом створення їх модифікацій, містять невеликі добавки молібдену, ванадію (німецьких підприємствах сортамент виплавленої сталі містить марку X90CrMoV18, що містить деяке його кількість) і вольфрама.
У деяких країнах із метою економії імпортованого хрому розроблено кілька модифікацій підшипниковому стали, у його зниження компенсується невеликими добавками молібдену з підвищеним змістом марганца. 1].
Високий вміст вуглецю в шарикоподшипниковых сталях зумовлює їхню високу міцність після термічної обробітку грунту і стійкість проти истирания поверхнева твердість визначається концентрацією вуглецю в мартенсите, тому вона однакова всім шарикоподшипниковых сталей. [pic].
Твердість внутрішніх шарів металу залежить від глибини прокаливаемости, що у своє чергу залежить від змісту хрому. Хром уповільнює перетворення аустеніту в перліт і тим самим збільшує прокаливаемость стали, тому, що більший деталі підшипників, то з більшим змістом хрому (0,4−1,65%) застосовується сталь їхнього изготовления.
З іншого боку, висока твердість карбідів хрому підвищує зносостійкість стали. Хром збільшує стійкість мартенситу проти відпустки, зменшує схильність стали до перегріву і саме й надає їй мелкозернистую структуру. Але у дуже високому вмісті хрому (>1.65%) важко давалися однорідну структуру, тому зміст хрому в шарикоподшипниковых сталях звичайно перевищує 1.65%.
Марганець, як і хром, збільшує твердість і опірність стали истиранию. Але водночас він сприяє зростанню зерна при нагріванні, в результаті чого при термічній обробці може утворюватися грубозерниста структура перегрітої стали. Негативний вплив на в’язкість шарикопідшипникової стали надає кремній. Але марганець і кремній є раскислителями, і що вища їхня зміст, тим повнішим раскислена сталь, тому присутність цих елементів в шарикопідшипникової стали всіх марок бажано трохи більше 0,35%Si і 0,4%Mn. Виняток становлять стали для виготовлення деталей великих підшипників типу ШХ15СГ. Підвищений вміст марганцю і кремнію у цій стали пояснюється лише тим, що це елементи зменшують критичну швидкість гарту, знижуючи цим схильність стали до короблению і тещинообразованию при закалке.
Шкідливими домішками для шарикопідшипникової стали є фосфор, мідь і нікель. Фосфор збільшує схильність стали до утворення грубозернистої структури при нагріванні, підвищує тендітність і зменшує міцність на вигин, що у своє чергу збільшує чутливість стали до динамічним навантажень і схильність виробів до появи закалочных тріщин. У зв’язку з цим зміст фосфору в металі обмежують. Мідь, хоч і збільшує твердість, межа міці й прокаливаемость стали, є небажаної домішкою, оскільки на підвищення змісту міді при гарячої механічної обробці збільшується освіту поверхневих тріщин і надривів. Зміст нікелю обмежують у зв’язку з тим, що його знижує твердість стали.
Опірність стали выкрошиванию зменшують домішки таких кольорових металів, як олово, свинець, миш’як. Негативне вплив на властивості стали багатодітній родині і гази: кисень утворює неметалеві включення, водень збільшує поражённость флокенами, а азот знижує опірність выкрошиванию.
Вплив сірки на властивості шарикопідшипникової стали неоднозначно. Негативний вплив відбилося у зниженні стійкості проти истирания і усталостном руйнуванні при на робочу поверхню сульфидов. Проте освіту сульфидной оболонки навколо сульфідних включень при достатньому змісті сірки зменшує вплив цих включень на концентрацію напруг і як наслідок підвищує опір втоми. Зі збільшенням відносини концентрацій S/O до 3−5 стійкість підшипників зростає. Цьому сприяють та поліпшення якості поверхні через те, що сірка покращує оброблюваність стали. 2].
1.3 Основні технологічні і експлуатаційні властивості, впливом геть них зовнішніх параметров.
Найчастіше підшипники качения працюють при малих динамічних навантаженнях, що дозволяє виготовляти їх із порівняно тендітних высокоуглеродистых сталей після наскрізний гарту й низького відпустки. У деяких сферах застосування підшипників їм потрібно підвищена динамічна міцність, що змушує застосовувати высокоотпущенные почав із поверхневою загартованістю чи цементируемые стали.
Навантаження, сприйнята подшипником качения, передається через тіла качения — кульки чи ролики, розділені сепаратором. У точках дотику тіл качения з кільцями виникають контактні напруги, викликають локальні деформації, у яких утворюються контактні майданчики, у випадку мають форму еліпса, у приватних ж випадках — це коло чи смужка. Тиску на контактної майданчику, перенесені деталями підшипника під час роботи, дуже великі й доходять зазвичай до 200Мпа, а й у тяжелонагруженных підшипників — до 4000Мпа. [1].
Дуже велика впливом геть майбутні властивості готових виробів на підшипниковому промисловості надає якість заготовок.
Залежно від призначення підшипникова сталь приходить у вигляді гарячекатаних прутків круглого і квадратного (великих розмірів) перетинів, в вигляді гарячекатаної смуги, гарячекатаних і холоднокатаных труб і великогабаритних паковок, і навіть холоднотянутой дроту в мотках і прутках.
Технічні вимоги до якісних показниками сортового прокату з сталей типу ШХ15 і ШХ15СГ (в т. год. і ШХ4), норми й фізичні методи контролю основних якостей її зазначені у ГОСТ 801–68, труб в ГОСТ 800–78, дроту в ГОСТ 4727–67; до стали ШХ15ШД вакуумного-дугового переплавлення — в ГОСТ 21 022–75.
З іншого боку, є ще низку технічних умов, містять додаткових вимог до якості напівфабрикатів зі сталі цих марок, отриманих іншими методами рафинирующих переплавов чи що відбивають особливості нових технологічних процесів отримання заготовок.
Вимоги, які пред’являються стану поверхні прутків, труб, дроту підшипниковому стали, передбачають відсутність грубих дефектів типу порушення сплошности чи обмежують допустимість менш небезпечних дефектів незначною глибини. На поверхні прутків не допускаються розкуті і раскатанные забруднення, бульки, тріщини, кірочки, заходи сонця, полони та інші дефекти, які під час переділі зливка чи проміжної заготовки.
Попри ретельний контроль на металургійних підприємствах, шлюб за цими дефектів становить найбільший відсотку кількості стали, рекламованої подшипниковыми заводами. Особливо великий цей відсоток для калиброванной стали.
Не виявлені при контроль у прутках і трубах поверхневі дефекти розкриваються у процесі подальшої механічного оброблення, пластичної деформації, термічної обробки чи процесі експлуатації подшипников.
До допустимим дефектів лежить на поверхні прутків і труб ставляться дрібні відбитки, рябизна, подряпини. Глибина залягання таких недоліків у стандартах диференціюється залежно від діаметра прутків і зажадав від стану поставки. 1].
Підвищення суми легуючих до 5% і від можна виправдати лише у випадках особливих експлуатаційних умов (коррозионная середовище, підвищені робочі температури та інших.), бо вона призводить до збільшення витрат на оброблюваність та зниження довговічності (малюнок 1) проти тими ж показниками традиційних підшипникових сталей.
[pic].
Малюнок 1 — Вплив сумарного змісту легуючих елементів на довговічність підшипникових сталей.
Зміна змісту складових сталь легуючих елементів надає різноманітний вплив на властивості підшипників. Добавка молібдену надає позитивний вплив на довговічність подшипников.
У Японії було випробувано підшипникові стали типу ШХ15 із вмістом 1- 1.5% Si. Довговічність підшипників з цих сталей підвищувалася, але вони не отримали застосування через поганий обрабатываемости.
Запропонована заміна стали ШХ15 на сталь зі зниженим вмістом хрому (85Cr1Mo) була здійснена, попри більш короткий час отжига, зза зниженою (8 мм) прокаливаемости. Цю сталь доцільно застосовувати там, де потрібно поліпшена деформируемость в холодному состоянии.
Багатьма авторами було доведено сприятливо впливає підвищеного змісту сірки (до 0,15%) на довговічність і оброблюваність підшипникових сталей, хоча почав із таким змістом сірки доки применяются.
У підшипникових сталях, отриманих звичайною технології, міститься близько 0,005% О2, 0,01−0,02% N2, 0,0001−0,0005% Н2. Кисень перебуває у вигляді окислів та її кількість залежить від технології розкиснення. При вакуумировании зміст кисню зменшується до 0,002%, а при ВДП — до 0,001%.
Водень негативно впливає якість стали зважаючи на те, що зниження розчинності його за зниженні температури металу викликає підвищені локальні тиску в металі, що призводять до утворення флокенов.
При дослідженні підшипникових сталей вітчизняних і зарубіжних фірм було встановлено негативний вплив підвищених змістів азоту NO та суми азоту та кисню на довговічність подшипников.
Микропористость може призводити до утворення питтинга та зниження довговічності подшипника.
Неметалеві включення до підшипникових сталях є концентраторами напруг і може деяких випадках бути причиною появи мікротріщин, які виникають від підвищеної концентрації мозаїчних напруг, різкого охолодження при загартуванню і др. 6] а загалом разі намагаються, щоб неметалеві включення мали глобулярную форму. Найбільш згубне вплив на якість підшипників надають включення оксидів і нитридов алюминия.
Нині найповніше задовольняють вимогам по змісту шкідливих включень стали, виготовлені методами ЭШП і ВДП. Однак це метал надто дорогою та, крім того і не встановлено економічно доцільні вимогами з чистоті металла.
2. Аналіз способів виплавки шарикоподшипниковых сталей в Україні, в.
СНД і поза рубежом.
2.1 Загальна характеристика способів выплавки.
Найбільш распространёнными способами виробництва шарикоподшипниковых сталей є: основний мартенівський, кислий мартенівський і электродуговой. Останній, за даними С. С. Штейнберга, визнано найбільш досконалим. Вважали, що у електропечі то, можливо виплавлено першосортний метал навіть у щодо загрязнённых сірою економікою та фосфором матеріалів. Тому на згадуваній заводах, у яких вихідні матеріали забруднені сірою економікою та фосфором вище норми, єдиним агрегатом для виплавки першосортної стали було визнано электропечь.
Саме там, де можливо отримання чистих по сірці і фосфору чавунів, рівноцінним агрегатом було визнано кисле мартенівська печь.
Нині країн СНД майже 90% підшипниковому стали масового призначення виплавляється в электродуговых печах і майже 10% в кислих мартенівських печах.
Як у разі виплавки в електропечі, і у разі мартенівської плавки можливо застосування обробки металу у ковші синтетичними известково-глинозёмистыми шлаками.
Іншим напрямом, яким удосконалювалося якість вітчизняної підшипниковому стали, була технологія рафинирующих переплавов — вакуумного-дугового, електрошлакового, плазмового і электроннолучевого. Рафинирующие переплавы є дуже ефективними: завдяки принциповому зміни процесу кристалізації стали збільшилася щільність зливка, знизилося загальний вміст газів, домішок, неметалічних включень і зменшилися розміри їх у слитке.
Новим напрямом, развиваемым останніми роками у вітчизняній промисловості при виплавкою сталі у відкритих дугових електропечах, стало внепечное вакуумирование в ковші, в установках циркуляційного чи порційного вакуумирования, вакуум-шлаковой обробки (УВСШ).
У світі вдосконалення процесу виробництва сталі для підшипників масового і лише частково, спеціального застосування пішло шляхом внепечного вакуумирования. Сталь для особливо відповідальних підшипників виплавляють методами вакуумної індукційною виплавки, вакуумного-дугового переплаву, электроннолучевой плавки, плазмового і електрошлакового переплава.
2.2 Виплавка в мартенівських печах.
Дуже обмежений обсяг виробництва кислих мартенівських сталей типу ШХ15 (зокрема. і ШХ4) з СНД за кордоном пояснюється особливостями її виробництва: паливо і шихтові матеріали при кислому процесі повинен мати низький вміст сірки і фосфору, тому що ці елементи при виплавці не видаляються з стали.
За відсутності чистих руд можливий варіант, коли спочатку виплавляють спеціальну заготівлю в основних мартенівських печах, та був переплавляють їх у кислих. Попри високі експлуатаційні властивості одержуваної стали, що є економічно не выгодным.
У кислої печі шарикоподшипниковую сталь можна виплавляти активним чи кремневосстановительным процесом. Якщо з мері розплавлювання в піч не вводять ніяких добавок, то мірі збільшення температури металу шлак насичується кремнезёмом внаслідок окислення кремнію, восстанавливающегося з подины. В’язкість шлаку збільшується, а швидкість переходу кисню з атмосфери печі через шлак знижується. На певній стадії плавки починає превалювати відновлення кремнію, збільшується його концентрація в металі. Цей процес відбувається називають кремневосстановительным. У такий спосіб виробляють подшипниковую сталь на заводах фірми SKF в Хеллефорсе. Виплавку ведуть у кислих мартенівських печах ёмкостью 30−120т. Футеровку цих печей виконують з чистих силікатних матеріалів, містять близько 97% SiO2. шихту створюють із рідкого чавуну (50%), губчастого заліза (30%), і відходів підшипниковому стали (20%). Зміст сірки і фосфору в сталевої ванній після розплавлювання низька, що, передусім, дуже високою чистотою цієї залізної руди, з якої виготовляються губчатий залізо і чавун. Окислювання здійснюється киснем. Ні на піч до випуску, ні з ківш під час випуску не додаються ні силикокальций, ні алюминий.
У СНД виплавку шарикоподшипниковых сталей в кислих мартенівських електропечах здійснюють активним процесом в печах ёмкостью 90 т.
Активний процес характеризується тим, що руду, вапно (чи вапняк) вводять у процесі плавки. Це підвищує жидкоподвижность шлаку, обмежує відновлення кремнію збільшує його окислительную здатність. Відбувається інтенсивний кипіння, зміст кремнію не перевищує 0,10−0,12%. Як шихтовых матеріалів використовуються чистий по сірці і фосфору чавун, спеціальна шихтовая болванка і по 10% від садки власні відходи кульковою стали.
Спеціальна болванка виплавляється в основних мартенівських печах. У матеріалі її міститься до 0,015%S і по 0,017%P.
Остаточне розкислення поводять в печі силикокальцием (1,26кг/т) і кусковым алюмінієм (0,4 кг/т), присадку розкислювачів закінчують до появи шлака.
Останніми роками застосовується також активний процес з наступної обробкою металу у ковші синтетичним известковоглинозёмистым шлаком наступного складу: 52−55% CaO, 38−42% Al2O3, до 3% SiO2, до 0.5% FeO, до 1.5% TiO2.
2.3 Виплавка в электродуговых печах.
Подшипниковую сталь виплавляють з двох технологічним схемами — з обробкою пічним шлаком і з обробкою металу у ковші высокоглинозёмистым синтетичним шлаком, одержуваним в окремої печи.
Залежно відрізняється від застосовуваної шихти за обома технологічним варіантів виплавка може здійснюватися методом переплаву чи свіжої шихті. При виплавкою сталі методом переплаву з обробкою пічним шлаком використовуються від 70 до 100% відходів підшипникових сталей. Остаточне розкислення проводять пічним кусковым алюмінієм шляхом присадки їх у піч за 5 хвилин до випуску (0,5 кт/т стали). При виплавці на свіжої шихті з обробкою пічним шлаком використовують вуглеродний брухт (74−77%), чавун (18−21%), і відходи підшипниковому стали (4,5%). Остаточне розкислення металу виробляють первинним алюмінієм у кількості 0,5 кг/т в ківш і 0,5 кг/т в ковш.
Высокоглинозёмистым синтетичним шлаком може оброблятися сталь, виплавлена як у свіжої шихті, і методом переплаву. Физикохімічні процеси, які у ковші при взаємодії рідкої почав із рідкими известково-глинозёмистыми синтетичними шлаками, переважно зводяться до того що, що з зливі рідкого металу з досить великий висоти в ківш відбувається їх інтенсивне перемішування і взаємна эмульгирование. Поверхня контакту металу і шлаку за її взаємній эмульгировании надзвичайно збільшена проти звичайним способом рафінування металу в печи.
Останніми роками дослідження на зниження основности рафинировочного шлаку. Застосування шлаків зниженою основности, полукислых і кислих шлаків продиктовано прагненням наблизити склад включень в основний электродуговой стали до складу в кислої мартенівської чи кислої індукційною сталях.
При таких процесах має знижуватися число великих глобулярных включень, але підвищуватися число сульфідних і, можливо, силікатних включень. При рафинировании стали кислими шлаками превалюючим виглядом кисневих включень стають тонкі рядки дрібних зерен корунда.
2.4 Спеціальні способи выплавки.
Виплавка змішанням в ковші рідких расплавов.
Особливістю тієї технології є одночасне комплексне використання трьох металургійних агрегатів: основний мартенівської печі, у якій виплавляють железоуглеродистый напівпродукт; дугового електропечі для виплавки рідкої лигатуры; шлакоплавильной електропечі для виплавки синтетичного шлака.
Одержання стали здійснюється шляхом змішання в сталеразливочном ковші железоуглеродистого напівфабрикату і переробки рідкої лигатуры у процесі рафінування розплавів синтетичним шлаком і продувкой аргоном.
Передумови підвищення якості і експлуатаційних властивостей стали, отриманої за технологією змішання з продувкой металу у ковші аргоном по порівнянню зі звичайною электросталью, засновані наступних теоретичних положеннях і експериментально встановлених фактах: а) поліпшуються умови розкиснення і легування сталі у ковші; б) у процесі розкиснення беруть участь як алюміній і кремній, а й вуглець, утворює газоподібні продукти реакцій і у якого при обраної технології змішання раскислительной здатністю значно вище кремнію; в) рівномірно розподілені легирующие елементи обсягом ковша; р) як об'єкт розкиснення використаний железоуглеродистый розплав необхідної і легко регульованої окисленности.
Вакуумна плавка, переплавку і вакуумна дегазація стали.
Застосовується кілька різновидів вакуумної обробки підшипниковому стали.
1) Виплавка в вакуумних індукційних печах на свіжої шихте.
2) Виплавка в электродуговых печах із наступною позапічної вакуумної обробкою в ковші чи спеціальних установках, той процес називають вакуумированием чи вакуумної дегазацией.
3) Переплавку електродів в вакуумних дугових печах. Електродами є прокатанные заготівлі, попередньо отримані в электродуговых чи электрошлаковых печах.
Загальні особливості вакуумної обробки зводяться до чого: рідкий метал охороняється від окисного впливу атмосферного кисню; внаслідок зниження тиску або в печі зменшується розчинність азоту та водню, вирізняються з рідкого металу і откачиваются; внаслідок підвищення раскислительной здібності вуглецю зменшується зміст кисню в металі як наслідок, знижується зміст неметалічних включень внаслідок відновлення їх вуглецем і частково результаті термічної дисоціації; також знижується зміст домішок деяких кольорових металів (олово, миш’як, свинець, вісмут та інших.), які мають високої пружністю пара; підвищується хімічна однорідність стали.
Для внепечного вакуумирования підшипниковому стали всіх марок в основному застосовують такі найбільш продуктивні способи: — циркуляційний (RH) — продуктивність однієї установки близько 400 тис. тонн на рік; - порційний (DH) — продуктивність близько 200 тис. тонн на рік; - вакуумирование в ковше-печи ASEA-SKF (з дуговим підігрівом і електромагнітним перемішуванням) — продуктивність близько 200 тис. тонн на год.
Усі перелічені установки можуть працювати у комплексі із будь-якими сталеплавильными агрегатами — электродуговой, мартенівської, конверторной печами. Вакуум створюється високопродуктивними пароэжекторными насосами.
Разливка стали попри всі зазначених засобах виробляється у зливки чи на установках безперервного розливу стали.
Электрошлаковый переплав.
Підшипникова сталь стала однією з перших об'єктів, у яких була випробувана, та був успішно впроваджено технологію ЭШП. Під час проходження електричного струму через шар рідкого шлаку у ньому виділяється тепло, оплавляющее кінець електрода, зануреного в шлак. Склад шлаку підбирають в такий спосіб, що він мав високим рафинирующим дією і високим электросопротивлением. Розплавлений метал, проходячи через шлак, рафинируется, у ньому знижується зміст кисневих включень і сірки. Потрапляючи в водоохлаждаемый кристаллизатор очищений метал швидко і цілеспрямовано кристалізується, що запобігає освіту дефектів слитка.
Особливостями зливків електрошлакового переплаву є висока щільність, відсутність великих неметалевих включень, рівномірний розподіл дрібних включень, відсутність внутрішніх та поверхневих раскатанных забруднень, усадочных дефектів, підвищена пластичність при гарячої механічної обработке.
При ЭШП ступінь десульфурации становить 80%. Зміст сульфідних і оксидних включень зменшується в 1,5−2 раза. 1] Цей процес відбувається є досить дорогим, тому сталь, виплавлену в такий спосіб доцільно використовувати лише у випадках, коли вироблені підшипники використовують у особливо відповідальних виробах і агрегатах (літаки, атомні реактори і т.п.).
3. Аналітичний огляд літератури з питання технології, способів виплавки і розливання шарикопідшипникової стали протягом останніх годы.
Підшипникові стали виплавляють і з початку 20-го століття (першої була сталь шх15, широко яку також і нині), за це час у цієї Одеській області було вироблено безліч досліджень, і експериментів, спрямованих як у пошук закономірностей впливу хімічного складу, забезпечення і типу неметалічних включень, мікроі макроструктури, і на виявлення залежності якості готових підшипників від способу їх производства.
Серед металургів і працівників підшипниковому промисловості немає єдиної думки про пайовому вплив технологічних, конструктивних і металургійних чинників на довговічність підшипників, що у більшості досліджень питання підвищення якості підшипниковому стали вирішувалися переважно з погляду задоволення вимог існуючих стандартів без достатньої перевірки зв’язок між цими вимогами і довговічністю підшипників. Розбіжність у думках пояснюється лише тим, що випробування підшипників — це багатофакторний експеримент і дуже важко виділити вплив однієї з діючих чинників. [8].
Різні дослідники по-різному оцінюють рівень впливу різних гілок чинників на якість подшипников.
Приміром, у роботі Першого державного підшипникового заводу (ПГПЗ) і запорізького машинобудівного інституту було встановлено, що довговічність L90 підшипників типу 76 210 шведської фірми СКФ в 6 разів перевищує аналогічний показник вітчизняних, австрійських і італійських подшипников.
У той самий час спільними дослідженнями ВНИШ і УкрНИИспецстали по випробуванню підшипників, виготовлених із металу шведської фірми СКФ і вітчизняних за наявною на підшипникових заводах технології, встановлено, що довговічність (L90) підшипників типу 76 210 з шведської підросли, ніж із вітчизняної (заводу «Дніпроспецсталь»), всього на 30−45%.
Дослідження підшипників після стендових випробувань дозволило зробити висновок, і що якість металу вітчизняного виробництва й шведської фірми СКФ за багатьма показниками одинаково.
Аналіз результатів випробувань підшипників дозволив дійти невтішного висновку, що вплив конструктивних параметрів і технологічних чинників (чистота поверхні, точність складання, гранность тіл качения тощо.) значно вище, ніж вплив металургійного якості металу, зокрема природи й кількості неметалевих включень. Висловлене становище то, можливо також підтверджено результатами випробувань довговічності різних типів підшипників, наведених В. П. Жевтуновым (ВНИПП) на Всесоюзній конференції по подшипниковым сталям м. Запоріжжі (1974г.). [8].
На думку А. Кравчика (Польща), основним критерієм оцінки якості матеріалу підшипників є усталостная контактна міцність, яка відбиває стійкість матеріалу проти виникнення поверхового выкрошивания «питтинг» на робочих поверхнях підшипників. Механізм виникнення цих выкрошиваний предмет суперечливих гіпотез. Питання ж ідеться про причинах, викликають наступ усталостного зносу в разі втоми качения, як і інших видах усталостной міцності, шкідливий вплив надають різноманітних неоднорідності і несплошности матеріалу, які, виконуючи роль концентраторів напруг, викликають їх нерівномірний розподіл у сусідніх микрообластях, що веде до прискореному руйнації матеріалу. [9] Тобто. важливішим вважає якість металу, із якого виготовлена подшипник.
Поруч із технологією виплавки однією з найважливіших чинників, впливають на макроструктуру і рівень чистоти стали, є маса зливка. Разливку изложницы виробляють лише сифонным способом. Маса зливка сталей ШХ15 і ШХ4 коштує від 0,6 до 5,2 т, а сталей типу ШХ15СГ — от0,6 до3,8 т. По даним інших джерел, в усіх країнах використовують зливки масою 2−5 т. Збільшення зливків до 5−6 т, викликане прагненням інтенсифікувати процес розливання зі збільшенням ёмкости печей, погіршує макроструктуру стали, ступінь її забруднення. Дуже мала маса зливка (0,5−1,0 т) не дозволяє цілком усунути дендритную ликвацию і вирівняти хімічну неоднорідність внаслідок недостатнього обжатия і при отриманні великих заготовок. 1].
Дуже найперспективнішим напрямом у плані є машин безперервного лиття заготовок. І тут, особливо в використанні методу «плавка на плавку», тобто. у разі, якщо сталеплавильні агрегати мають велику ёмкость і продуктивність, для підприємства очікується істотного збільшення продуктивності, особливо рахунок зменшення втрат з литниками і зменшення кількості недоліків у заготовках.
Суттєвого поліпшення техніко-економічних показників виробництва можна домогтися шляхом широко він й подальшого вдосконалення методів і коштів неруйнуючого контролю за якістю заготовок і готові изделий.
Однією з істотних елементів сучасної прогресивної технологи виробництва підшипникових сталей є широке застосування неразрушающих випробувань, які дають вихідному контролю високу надійність і забезпечують повну і безперервну інформацію якість продукції процесі її виготовлення. Завдяки цьому з’являється можливість своєчасно коригувати технологічні процеси та підтримувати на заданому рівні показники качества.
Основна сферу застосування неразрушающих випробувань якості прокату підшипникових сталей — перевірка макроструктури, дефектів поверхні і є змін хімічного складу в поверхневих слоях.
Якість цими методами носить їх у час додатковий характер. І впровадження неразрушающих методів контролю у ролі основних, і навіть розробка ефективніших і прогресивних технологій контролю, в час однією з основних шляхів вдосконалення виробництва підшипниковому стали за кордоном, і на Україні. Так було в проект нових Держстандартів на подшипниковую сталь вже включені ультразвукові методи контроля.
Нині триває робота по створення критеріїв оцінки якості при автоматизованому 100-%-ном неразрушающем контроль знань поверхні калиброванной стали. [8].
Слід згадати високі техніко-економічні показники, одержувані підприємствами у впровадженні вакуумшлакового рафінування металу. У стали, обробленою на промислової УВСШ (установка рафінування в стовпі шлаку), зміст кисню нижче, ніж у металі, обработанном синтетичним шлаком, вдвічі (до 0,002% і менше), сірки — у два разу (до 0,003% і менше), водню в 1−1,5 разу (до 2,5−3,0см3/100г). Кількість неметалевих включень після обробки шлаком раціонального складу на УВСШ знижується в 3−5 раз проти металом, опрацьованим на інших технологиям.
Ефективність використання способу вакуумирования почав із обробкою в стовпі шлаку визначається співвідношенням додаткових витрат у металургії, пов’язаних із упровадженням способу. І економічного ефекту від заміни в споживачів металу звичайній виплавки металом, выплавленным з вакуумшлаковой обработкой.
На самому металургійному заводі економічний то може бути отримано рахунок збільшення продуктивності печей, доплат за якість металу, і навіть рахунок скорочення чи усунення противофлокенной обробки прокату. Народно-господарський ефект ж виявиться головним чином збільшенні довговічності подшипников.
Порівнюючи даних про вартості позапічної обробки стали при використанні різних способів рафінування (малюнок 2), можна зробити висновок у тому. Що за досягненні проектної продуктивності УВСШ подорожчання металу нічого очікувати значно перевищувати вартість обробки на установках RH і DH і буде набагато нижче, аніж за використанні способу ASEA-SKF (слив металу у ківш, вакуумна дегазація, електромагнітне перемішування, додатковий підігрів металу дугою і слив). У той самий час спосіб ВСШ, як не відомий способів позапічної обробки, дозволяє швидко комплексно вирішувати проблему рафінування стали, здійснюючи її десульфурацию, розкислення, дегазацію і очищення від неметалічних включень. При відповідному конструктивному оформленні установка ВСШ не складніше у роботі, ніж установки типу RH і DH, а теплові втрат металу може бути так само, як у установках зазначеного типа.
Використання способу ВСШ в обробці конструкційних сталей інших марок також може бути дуже ефективно, оскільки саме у цих сталях важливо провести сув’язь рафінування металу від сірки, газів і неметалевих включень, дозволяє значно підвищити механічні і службові властивості сталей, зменшити металлоёмкость деталей машин і конструкцій. Реалізація процесу обробки сталі у вакуумі в стовпі шлаку дозволить досягти якісно нового рівня властивостей металла.
[pic].
[pic].
Малюнок 2 — Зміна витрат за вакуумну обробку залежно від кількості оброблюваного металу і застосовуваних способів обробки: 1−6 — способи вакуумирования: 1 — при звичайній розливанні, 2 — в ковші, 3- RH і DH, 4 — Финкл, 5 — ASEA-SKF, 6 — ВСШ.
Слід зазначити, можливості способу вакуумшлакового рафінування не обмежуються лише стандартним варіантом обробки. Великі переваги можна отримати також за поєднанні даного способу рафінування з горизонтальними і радіальними МБЛЗ, з модифицированием металу редкоземельными і щелочноземельными металами, при роботі установки ВСШ комплексно зі сталеплавильными агрегатами (конвертор, САНД), з підвищеної продуктивністю. Постачання установки пристосуванням для підігріву металу у процесі чи влітку після обробки дозволить вивести вакуумшлаковое рафінування олії за паливною ефективністю однією з дорогим способом ASEA-SKF при значно менших видатках. [10].
Багато досліджень, що проводилися час, спрямовані вже й не так на вдосконалення існуючих технологій, але в розробку цілком нових. Так було в Японії знаходить обмежений застосування труднообрабатываемая жаропрочная быстрорежущая сталь SKH4A (18%W, 4%Cr, 1%Vn, 10%Co). [1] У останніми роками створено новий жароміцний матеріал для підшипників з нітриду кремнію, довговічність якого на 300−800% вище довговічності звичайних підшипникових матеріалів, що працюють у умовах високих температур й у коррозионных середовищах. Дослідження, виконані Америці, показали, що нітрид кремнію, спресований в гарячому стані, забезпечує довговічність 5,7 замість 1,8 млн. циклів у разі швидкорізальної інструментальної стали вакуумного переплаву. Підшипник з нітриду кремнію успішно працював при 9000С і швидкості обертання валу 30 000 об./хв. [7].
У остаточному підсумку, нині дуже важливим для підшипниковому промисловості є максимальне об'єднання зусиль науковців світу й технологів різних галузей: хіміків, фізиків, металургів, конструкторів, й у першу чергу економістів, як нашої держави, і інших країнах для забезпечення неухильного зростання виробництва та її подальшого розвитку технології виробництва недорогих, і найголовніше високоякісних і довговічних підшипників, як металевих, і з урахуванням композиційних матеріалів, у майбутньому, створення практично вічних підшипників, термін служби яких вимірюватися не десятки років, а столетиями.
4. Вибір і з використання нових прогресивних розробок на технології виплавки шарикоподшипниковых сталей.
Постійно ростучі вимоги до якості стали можуть сыть задоволені лише за виробництві металу з низькими змістами сірки, кисню, водню і неметалічних включень. Але це пов’язано з значними труднощами: лише спосіб обробки, який отримав назву ASEASKF (під назвою двох які розробили його шведських фірм), дозволяє комплексно рафінувати сталь, але ці дуже дорогою, і трудомісткий процесс.
УкрНИИспецсталью що з заводом «Дніпроспецсталь» та інші організаціями розроблено спосіб мислення та устрою для вакуумирования почав із одночасної обробкою в стовпі синтетичного шлаку (УВСШ). Спосіб дозволяє вакуумировать сталь широтою діапазону, поєднуючи переваги процесів вакуумирования і методи обробки металу синтетичним шлаком при порівняно невисоких затратах.
Сутність способу ось у чому: метал, виплавлений в сталеплавильному агрегаті, піддається вакуумированию в струмені, та був рафинируется в шлаку, проходячи через стовп шлакового розплаву заввишки понад 3 м. Стовп шлаку формується рахунок різниці атмосферного і залишкового тиску у вакуумній камері. Кількість шлаку визначається барометрической висотою і поперечним перерізом шлакового стовпа. Схема виплавки металу з вакуумшлаковой обробкою приведено малюнку 3.
Дотримуючись схемою, метал з сталеплавильного агрегату вступає у передатний ківш, який встановлюється на вакуум-камеру, після чого починається донний випуск із дегазацією металу у струмені. Распылённый метал стікає на дно вакуум-камеры й потрапляє в шлак рукав, заповнений шлаком, і, спускаючись крізь шар шлаку вниз, рафинируется. У вакуумну камеру шлак постачається з приёмного ковша шлакоплавильной печі. Під жужільним рукавом розташовується приймальний ківш, з яких метал надходить безпосередньо на разливку, що виробляється або у изложницы, або, що краще, в чужу машину безперервного лиття заготовок.
[pic].
Малюнок 3 — Схема способу вакуумирования з обробкою в стовпі шлаку: 1- сталеплавильна піч, 2 — передатний ківш з вихідним металом, 3 — вакуумна камера, 4 — шлак рукав, 5 — стовп рідкого шлаку, 6 — приймальний ківш з синтетичним шлаком, 7- шлакоплавильная піч, 8- изложницы, 9- МНЛЗ.
Як було встановлено проведеними дослідженнями, спосіб вакуумирования з одночасної обробкою в стовпі шлаку має низку кінетичних переваг над іншими способами обробки. Так, при вакуумировании поруч із дегазацией в струмені спостерігається плёночное, крапельне, або у вигляді дрібних струменів протягом металу по стінок і коническому днища вакуумної камери, що підвищує ефективність дегазації. При русі металу через стовп шлаку відбувається освіту шлакометаллической емульсії, у якій дисперсная фаза — метал — має в діаметрі частинок в межах 0,05−1,0 див, а максимальна маса крапель має фракції розміром 0,3−0,6 см.
Поверхня контакту металу зі шлаком у процесі опрацювання в стовпі шлаку становить понад 300 м2/т стали, що у багато перевищує аналогічний показник в обробці синтетичним шлаком в ковше.
Обробку в стовпі шлаку можна охарактеризувати як взаємодія фаз при противотоке у разі, коли швидкість руху одній з фаз (у цьому разі шлаку) близька нанівець. Тому ефективність видалення розчинних домішок з металу при обробці в стовпі шлаку вище, аніж за традиційному перемішуванні фаз обсягом (наприклад, при обробці синтетичним шлаком в ковші). Зростанню ефективності рафінування сприяє також те що, що метал після обробки не контактує з загрязнённым шлаком, ніж не може зворотний перехід домішок з шлаку в металл.
На установці заводу «Дніпроспецсталь» обробляли подшипниковую сталь. Її виплавляли в 60-т печах переплавом відходів з продувкой киснем, шлак під час доводки не раскисляли і для випуском металу з печі не видаляли. Усі проведені експерименти і аналізи плавок дали позитивні результати. [10].
Економічний і народногосподарський ефекти застосування цієї технології наведено выше.
Враховуючи всі переваги даної технології над іншими, можна вважати, що на цей момент вона є найпередовіший і перспективної, отже, слід зробити всіх заходів для швидкого й ефективного впровадження даної технології на великих промислових підприємствах України, що дозволить їм успішно конкурувати із зарубіжними металургійними підприємствами, такими, наприклад, як ASEA-SKF.
Выводы.
Проаналізувавши весь розглянутий матеріал можна зробити такі выводы:
1. Необхідно вдосконалення критеріїв оцінки якості металу і готові виробів, і навіть повсюдне застосування неразрушающих методів контроля.
2. Необхідно розробити зважену та застосовувати єдину методику з оцінки експлуатаційних властивостей підшипникових сталей, узгоджену між представниками металургійної і підшипниковому промышленности.
3. Сортамент існуючих підшипникових сталей доцільно удосконалювати шляхом запровадження стандарт нових марок з молібденом і ванадием.
4. Найперспективнішими у плані підвищення якості сталі у час є спеціальні способи виробництва (ЭШП, ВДП, ЭЛП, ВСШ і др.).
5. Самій прогресивної технологією, яка має найкращим співвідношенням ціна-якість є спосіб вакуумирования металу у стовпі рідкого шлака.
Перелік ссылок.
1. Структура й властивості підшипникових сталей / Спектор О. Г., Зельбет.
Б.П., Кисельова С. А. — М.: «Металургія», 1980 г. — 264с.
2. Электрометаллургия сталі та феросплавів / Поволоцкий Д. Я., Рощин.
В.Є., Рысс М. А., Строганов А.І., Ярцев М. А. — Підручник для вузов.
Вид. 2-ге, переробіт. І доп. — М.: «Металургія», 1984 г. — 568с.
3. Збірник технологічних інструкцій по виплавкою сталі в основних дугових електропечах: [Збірник] / Міністерство металургії СРСР, завод «Дніпроспецсталь» — Запоріжжі, Друкарня издательства.
«Комунар», 1977 г. -480с.
4. Машинобудівні стали. Вид. 2-ге., перероблене і доповнене /.
Журавльов В.М., Миколаєва О.И., — М.: «Машинобудування», 1968 г.-332с.
5. Шепеляковский К. З., Фонштейн М. М., Девяткин В. П. та інших. — МиТОМ,.
1976, № 5, з. 40−44.
6. Підвищення якості та поліпшення сортаменту підшипниковому сталі у країнах-членах СЭВ-М.: Ин-т «Черметинформация». 1979 г., ч.1, с.27−37.
7. Mullins Peter J. — IAMI, 1972, v. 11,№ 11, p.25−29.
8. Підвищення якості та поліпшення сортаменту підшипниковому сталі у країнах-членах СЭВ-М.: Ин-т «Черметинформация». 1979 г., ч.1, з. 3−26.
9. Підвищення якості та поліпшення сортаменту підшипниковому сталі у країнах-членах СЭВ-М.: Ин-т «Черметинформация». 1979 г., ч.1, з. 38−47.
10. Підвищення якості та поліпшення сортаменту підшипниковому сталі у країнах-членах СЭВ-М.: Ин-т «Черметинформация». 1979 г., ч.1,с.92−102.
11. Посібник із оформленню курсових, дипломних робіт і проектів /.
В.В. Лебедєв, В. В Беренда, А. Я. Жук.- Запоріжжі, ЗГИА, 1999 — 18с.
12. Методичні вказівки до виконання курсової роботи з курсу.
«Технологія виробництва спеціальних сталей і сплавів» / С.А.
Воденников.- Запоріжжі, ЗГИА, 2002 — 8с.