Організація робіт в агрегатному відділенні з розробкою технологічного процесу ремонту коробки передач автомобіля УАЗ-452 в умовах ВАТ АТП
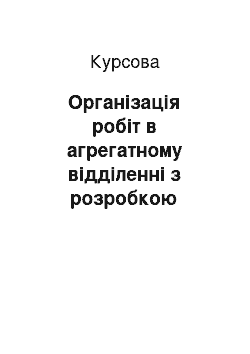
Визначено шість типів (матеріалів) дорожнього покриття: — цементобетон, асфальтобетон, брущатка, мозаїка; — бітумомінеральні суміші (щебінь або гравій, оброблені бітумом); — щебінь (гравій) без оброблення, дьогтебетон; — кругляк, колотий камінь, ґрунт і маломіцний камінь, оброблені в’яжучими матеріалами, дорога по снігу; — ґрунт, укріплений або поліпшений місцевими матеріалами, лежневі й брусові… Читати ще >
Організація робіт в агрегатному відділенні з розробкою технологічного процесу ремонту коробки передач автомобіля УАЗ-452 в умовах ВАТ АТП (реферат, курсова, диплом, контрольна)
Міністерство освіти і науки, молоді та спорту України Технічний коледж Тернопільського національного технічного університету імені Івана Пулюя Відділення туризму і комерційного навчання КУРСОВИЙ ПРОЕКТ З дисципліни
«Технічна експлуатація автомобілів»
На тему
«Організація робіт в агрегатному відділенні з розробкою ТП ремонту КПП автомобіля УАЗ-452 в умовах ВАТ АТП»
Виконав Студент групи ТОА-314п Явний В. М Керівник проекту Яскілка С. З Тернопіль — 2012р.
ВСТУП Технічне обслуговування і ремонт забезпечують справний технічний стан автомобільного транспорту. Одна з найважливіших проблем, яка стоїть перед автомобільним транспортом, є підвищення експлуатаційної надійності автомобілів, і зниження затрат на їх утримання. Вирішення цієї проблеми з однієї сторони, забезпечується автомобільною промисловістю за рахунок випуску автомобілів з великою надійністю і технічністю, з іншої сторони — вдосконалення методів технічної експлуатації автомобілів, підвищення продуктивності праці, зниженням трудомісткості робіт по технічному обслуговуванню і ремонту автомобілів, збільшення їх міжремонтних пробігів. Це потребує створення потрібної виробничої бази для підтримки рухомого складу в справному стані, широкого застосування засобів механізації і автоматизації виробничих процесів, збільшення будівництва і покращення станів доріг.
Вимоги до надійності транспортних засобів підвищується у зв’язку з швидким ростом і інтенсивністю руху, потужності, вантажопідйомності і в місткості автомобілів, а також технологічними і організаційними зв’язками автомобільного транспорту з обслуговуючими підприємствами та іншими видами транспорту.
Утримання автомобільного парку вимагає великих затрат, це пов’язано з його технічним обслуговуванням і ремонтом. Автомобільний транспорт витрачає значну кількість запасних частин, що є економічно не вигідно. Трудомісткість ремонту вантажного автомобіля середньої і великої вантажопідйомності в залежності від інтенсивності експлуатації може в кілька разів перевищувати трудомісткість виготовлення нового автомобіля.
Організація, методи і засоби збереження рухомого складу повинні забезпечувати його збереження в міжзмінний час і своєчасну підготовку для роботи на лінії.
Важливим завданням технічної експлуатації автомобілів є удосконалення методів проектування технічної бази АТП які забезпечують виконання всіх потреб по утриманню парку автомобілів.
Курсовій проект містить розробку прогресивної технології та організації робочих місць на виробничих ділянках.
1. ЗАГАЛЬНИЙ РОЗДІЛ
1.1 Характеристика проектування агрегатного відділення і ДТЗ Агрегатні роботи включають розбирально — збиральні, мийні, діагностичні та регулювальні операції по коробці передач, яка демонтована з автомобіля для поточного ремонту (ПР) в агрегатному відділенні.
В агрегатному відділенні встановлюється необхідне технологічне обладнання, яке забезпечує весь технологічний процес ремонту агрегатів.
Після діагностики технічного стану агрегат, знятий з автомобіля для ПР, встановивши на транспортний візок, транспортують в агрегатне відділення для зовнішнього миття. Попередньо з картерів агрегатів зливають масло.
Після зовнішнього миття агрегат направляється на спеціалізований стенд, який забезпечує вільний доступ до агрегату, а також поворот та нахил агрегату для зручності виконання ремонтних робіт. Розбирально — збиральні роботи різних вузлів проводяться в основному на верстаках із застосуванням універсального інструмента та спеціальних пристроїв, також використовують спеціальні пристрої, преси та відповідний інструмент.
Розібрані агрегати знежирюють в гарячому содовому розчині з подальшою промивкою в гарячій воді. Після закінчення ремонту механізмів, вузлів та деталей агрегат складають, після чого проводяться контрольно регулювальні роботи.
В середньому орієнтовний розподіл загальних трудовитрат агрегатних робіт по коробок передач становить — 8% .
Оскільки у загальних трудовитратах агрегатних робіт значна доля (більше 50%) припадає на ремонт двигунів та їх систем, тому обслуговування і ремонт двигунів виконуються в окремому приміщенні (моторному відділенні).
В даному агрегатному відділенні встановлено необхідне технологічне обладнання, яке забезпечує весь технологічний процес ремонту агрегатів.
Коротка техніко-експлуатаційна характеристика автомобіля наведена у таблиці 1.1
Таблиця 1.1 Коротка технічна характеристика автомобіля УАЗ — 452
Показники | Одиниці виміру | Значення | |
Марка, модель, призначення | УАЗ — 452 призначений для перевезення вантажів по будь яких видах дорожнього покриття і бездоріжжю. | ||
Колісна формула | 4х4 | ||
Вантажопідйомність Пасажиромісткість — 2 | т (чол.) | ||
Габаритні розміри | |||
Довжина | мм | ||
Ширина | мм | ||
Висота | |||
Власна вага | Кг (Н) | ||
Розміщення двигуна | переднє | ||
Тип двигуна | 4х тактний з вприском палива | ||
Об'єм двигуна | л | 2,4 | |
Максимальна потужність | кВт (к.с.) | ||
Витрата палива | л/100км | 15,4 | |
Розмір шин | 225/75 R16 | ||
Максимальна швидкість | км/год | ||
Дорожній проміжок | мм | ||
Заправка пальним | л | ||
Заправка системи охолодження | л | 11,5 | |
1.2 Будова і принцип роботи КПП Коробка передач служить для зміни крутного моменту по величіні та напрямку, короткочасного від'єднання двигуна від трансмісії та їх плавного з'єднання, під час стоянки або при русі автомобіля по інерції, а також для руху автомобіля заднім ходом.
Передачі перемикаються пересуванням шестерень, які по черзі входять у зачеплення з іншими шестернями, або блокуванням шестерень на валу за допомогою синхронізаторів. Синхронізатори вирівнюють частоту обертання шестерень, що вмикаються, і блокують одну з них із веденим валом. Пересуванням шестерень або синхронізаторів керує водій при вимкненому зчепленні.
На автомобілі УАЗ-452 коробка передач механічна, чотирьохступінчаста, має чотири передачі переднього ходу і одну передачу заднього ходу. Кріпиться до картеру зчеплення з допомогою чотирьох шпильок. Крутний момент двигуна передається на первинний вал коробки передач через ведений диск зчеплення. Зубчасті колеса приводу проміжного валу, 3-ї і 2-ї передач косозубі і знаходяться в постійному зачеплені.
Первинний вал має дві опори. Передній підшипник розміщений в гнізді колінчастого валу, а задній — в передній стінці картера коробки передач. Задній підшипник закріплений на валу спеціальною гайкою з лівою різьбою. З внутрішньої сторони картера підшипник закритий масловідбивачем. На задній частині валу нарізані два зубчастих вінця. Для зручності монтажу прямозубий вінець і частина конічної поверхні валу мають дугоподібний виріз. Між підшипником і торцем валу встановлений масловідбивач. Проміжний вал встановлений на двох кулькових підшипниках, в передній і задній стінках картера. Передній підшипник закріплений на валу спеціальною гайкою, яка стопориться шляхом вдавлювання її буртика в паз вала. Задній підшипник має на зовнішній обоймі упорне кільце. На валі задній підшипник закріплений за допомогою тарілчастої шайби і спеціального болта з лівою різьбою. Блок шестерень заднього ходу з підшипником в зборі встановлений на осі, яка стопориться в картері спеціальним різьбовим штифтом.
Синхронізатор забезпечує безшумне включення передач переднього ходу через вирівнювання частоти обертання. Четверта (пряма) і 3-тя передачі для полегшення включення мають синхронізатор інерційного типу. Механізм синхронізатора зібраний на маточині. Маточина має три поздовжніх пази прямокутної форми для розміщення сухарів. У центрі кожного паза зроблено в радіальному напрямку отвір. При складанні механізму в отвори маточини встановлюються пружини, а в отвори сухарів сталеві кульки. Щоб не допустити випадків випадання кульок синхронізатора, отвори в сухарях виконані ступінчастими. У синхронізатор сухарі встановлюються стороною з отворами меншого діаметра в бік муфти. При включенні передачі муфта під дією вилки перемикання пересувається в бік включається шестерні. Конусна поверхня блокуючого кільця синхронізатора починає стикатися з конусною поверхнею шестірні і таким чином, в початковий момент включення, частота обертання кільця й шестірні не є різними, на поверхнях дотику виникають сили тертя. У результаті сил тертя їх частота обертання вирівнюється, кільце повертається проти обертання, сухарі займають центральне положення що до пазів і утоплюються в них, а зуби муфти входять у зачеплення з зубами кільця і включається шестерні, блокуючи її на валі. Перша і друга передачі включаються переміщенням шестірні на веденому валі. Задній хід включається переміщенням блоку проміжних шестірень, що входять одночасно в зачеплення з веденою і проміжною шестернями першої передачі.
Механізм перемикання передач має три вилки перемикання, що входять у з'єднання з рухомими елементами коробки передач. Всі вилки кріпляться на штоках за допомогою болтів, що мають на кінці конус. Штоки разом з вилками переміщаються в осьовому напрямку. Для фіксування положення нейтралі і включеної передачі штоки мають пружинні фіксатори. Між штоками встановлено замковий пристрій, який перешкоджає одночасному включенню двох передач. Один з штоків, виведений з нейтралі, замикає інші. Бічна кришка має отвір для гвинта установки вимикача ліхтаря заднього ходу.
Рисунок 1.1
1 — ведучий вал; 2 — підшипники; 3 і 14 — зубчасті колеса постійного зачеплення ведучого и проміжного валів; 4- муфта включення третьої і четвертої передач; 5 і 13 — зубчасті колеса третьої передачі; 6 і 12 — зубчасті колеса другої передачі; 7 і 11 — зубчасті колеса першої передачі; 8 — вилка включення; 9 — ведений вал; 10 — блок зубчастих коліс передачі заднього ходу; 15 — картер коробки передач; 16 — блок шестерень проміжного вала.
2. ТЕХНОЛОГІЧНИЙ РОЗДІЛ
2.1 Розрахунок виробничої програми АТП по ТО і ремонту рухомого складу Виробнича програма по ТО і ПР рухомого складу встановлює кількість ТО (за видами) і капітальних ремонтів (КР), а також трудові витрати на їх виконання за розрахунковий період (добу, рік) по всьому парку автомобілів. Розрахунки виконуються окремо по автомобілях кожної марочної групи, або за середньозваженими величинами (приведеною кількістю автомобілів). Вихідними даними для розрахунків служать:
· тип і марка рухомого складу (задається наперед або вибирається на основі техніко економічного обґрунтування);
· спискова кількість одиниць рухомого складу — автомобілів, причепів, напівпричепів (задається або також обґрунтовується);
· середньодобовий пробіг автомобілів (задається або розраховується за відомими вимірниками транспортної роботи, може встановлюватись за даними звітів);
· технічний стан автомобілів, що характеризується їх пробігом з початку експлуатації;
· дорожні умови експлуатації автомобілів, що характеризуються типом дорожнього покриття, рельєфом місцевості і умовами руху (у відповідності до Положення про технічне обслуговування і ремонт рухомого складу автомобільного транспорту ділиться на п’ять категорій у додатку, таблиця
· режим ТО і ремонту рухомого складу, що визначається за видами ТО, діагностування і ремонту їх періодичністю, тривалістю простою автомобілів в ТО і ремонті.
Види технологічних дій встановлені Положенням про технічне обслуговування і ремонт дорожньо-транспортних засобів автомобільного транспорту і періодичність.
Вихідними нормативами для технологічного розрахунку АТП служать: пробіг автомобілів до КР, періодичності ТО, трудомісткості ТО і ПР рухомого складу, тривалості простою рухомого складу в КР, ТО-1, ТО-2 і ПР.
Там же окремим показником наведена кількість СО протягом року для кожної моделі автомобіля з урахуванням рекомендацій заводів-виробників автомобільної техніки.
Наведені нормативи характеризують режими ТО і ПР рухомого складу в найбільш сприятливих умовах експлуатації. Для визначення режимів ТО і ПР в реальних умовах експлуатації дорожніх транспортних засобів вихідні нормативи періодичностей впливів і трудомісткості коректуються за допомогою коефіцієнтів.
Заправні операції, постановку автомобілів на стоянку, а також перевірку технічного стану виконують водії у підготовчо заключний час разом з механіком контрольно-технічного пункту (КТП). Трудомісткість додаткових робіт СО відносно трудомісткості ТО-2 при експлуатації автомобілів в умовах України становить 20%.
До складу допоміжних належать такі роботи: обслуговування устаткування, складські, прибиральні та інші роботи, пов’язані з ТО і ремонтом рухомого складу.
Вихідні дані розрахунку виробничої програми показані у таблиці 1.2
Таблиця 1.2 Вихідні дані виробничої програми
Марка ДТЗ | Аі авт. | Lсд. км | Умови експлуатації і режими роботи ДТЗ | |||
КУЕ | Др. дні | Тн.год | ||||
УАЗ-452 | IV | |||||
При розрахунках приймаємо наступні позначення:
Аі - спискова (інвентарна) кількість автомобілів;
Lсд — середньодобовий пробіг одиниці рухомого складу;
КУЕ — коефіцієнт, що враховує категорію умов експлуатації;
— дні роботи підрозділу в році;
Lпробіг до ремонту або ТО одиниці рухомого складу;
N — кількість ремонтів або ТО на одиницю рухомого складу за цикл або за рік;
Д — число днів простою одиниці рухомого складу в ТО або ремонті.
Для величин L, N і Д використовуються індекси, які характеризують вид ремонту і ТО:
КР — капітальний ремонт;
ПР — поточний ремонт ЩО — щоденне технічне обслуговування;
ТО-1 — перше технічне обслуговування;
ТО-2 — друге технічне обслуговування;
СО — сезонне обслуговування.
2.1.1 Вибір та корегування нормативів Автотранспортним підприємствам надане право корегувати нормативи ТО і ремонту зміненням числових значень, якщо автомобіль працює в умовах, що відрізняються від тих, які прийняті для вихідних нормативів. З урахуванням конкретних умов експлуатації можна змінити ресурсні і оперативні нормативи.
Коригування полягає у зміненні числових значень нормативів ТО, переліку операцій ТО, співвідношення між обсягом робіт ТО і ремонту внаслідок включення до ТО характерних (що часто повторюються) операцій ПР.
Нормативи ТО і ремонту рухомого складу за рекомендаціями автомобільних заводів корегують залежно від категорії умов експлуатації, які характеризуються типом дорожнього покриття D, типом рельєфу місцевості Р якою пролягає дорога, та умовами руху.
Визначено шість типів (матеріалів) дорожнього покриття: — цементобетон, асфальтобетон, брущатка, мозаїка; - бітумомінеральні суміші (щебінь або гравій, оброблені бітумом); - щебінь (гравій) без оброблення, дьогтебетон; - кругляк, колотий камінь, ґрунт і маломіцний камінь, оброблені в’яжучими матеріалами, дорога по снігу; - ґрунт, укріплений або поліпшений місцевими матеріалами, лежневі й брусові покриття; - природні ґрунтові дороги, тимчасові внутрішньокар'єрні й відвальні дороги, під'їзні шляхи, що не мають твердого покриття. Визначено також п’ять типів рельєфу місцевості: — рівнинний (до 200 м); Р2 — слабогорбистий (200…300); Р3 — горбистий (300… 1000); Р4 — гористий (1000…2000); Р5 -гірський (понад 2000м).
Оперативне корегування переліків операцій ТО в певних умовах експлуатації здійснюють тільки після впровадження на ВАТ АТП рекомендацій Положення і за наявності достовірної інформації про напрацювання на випадок ПР і витрат на виконання робіт. При цьому використовують діагностування технічного стану автомобілів.
Ремонт, як правило, виконується за потребою, виявленою під час технічного обслуговування або в процесі експлуатації, та має за мету поновлення технічно справного стану.
Перелік видів технічних обслуговувань і ремонтів, їх періодичності та об'єми виконуваних при цьому робіт встановлюють заводи-виробники автомобільної техніки, але власнику транспортних засобів (керівнику АТП) надано право коректувати заводські нормативи в залежності від конкретних умов експлуатації рухомого складу.
Згідно з цими аргументами і враховуючи рекомендації, наведені в інструкціях заводів — виробників автомобільної техніки, на АТП передбачаються наступні види технічних обслуговувань і ремонтів: щоденне обслуговування (ЩО), перше технічне обслуговування (ТО-1), друге технічне обслуговування (ТО-2), сезонне технічне обслуговування (СО); поточний ремонт (ПР).
Згідно Положення про технічне обслуговування і ремонт рухомого складу автомобільного транспорту періодичність ТО-1 і ТО-2 для автомобіля УАЗ-452 становить:
(км)
(км)
(км) де — коефіцієнт корегування нормативу в залежності від умов експлуатації.
, — скориговані періодичності ТО-1, ТО-2, КР;
, — нормативні періодичності ТО-1, ТО-2, КР.
Трудомісткість робіт ЩО становить:
де - нормативна трудомісткість робіт ЩО:
— відкоригована трудомісткість робіт ЩО;
— коефіцієнт механізації робіт ЩО.
Коефіцієнт механічних робіт ЩО становить:
Мдоля механізованих робіт в ЩО %
Трудомісткість СО становить:
(2.1)
(2.2)
(2.3)
де — трудомісткість робіт СО.
Нормативний пробіг автомобіля до КР становить:
Час простою автомобіля в ТО і ремонті становить:
(2.4)
де — час на доставку автомобіля на АРЗ і в зворотному напрямку, днів;
— нормативний час простою автомобіля в КР, днів.
Час простою автомобіля в КР становить:
ДД=0,15· 12=1,8(дні)
де L (H)ТО-1, L (H)ТО -2 — нормативна періодичність до ТО-1 і ТО-2.
2.1.2 Визначення кількості ТО і КР за цикл Кількість ТО за цикл становить:
Періодичність пробігу до ТО-1 з врахуванням середньо — добового пробігу становить:
Періодичність до ТО-2 і пробігу до КР становить:
де — відкорегована величина періодичності до КР.
Кількість ТО за цикл становить:
тому =1(КР);
де — кількість ТО-2 за цикл;
— кількість ТО-1 за цикл.
Кількість ЩО за цикл становить:
де — кількість ЩО за цикл.
2.1.3 Розрахунок технічної готовності і використання автомобілів Коефіцієнт технічної готовності автомобілів становить:
де — кількість днів експлуатації автомобіля за цикл,
— кількість днів простою автомобіля в ТО і ремонті за цикл.
де — коефіцієнт зменшення простою автомобілів в ТО і ПР за рахунок часткового виконання робіт в міжзмінний час;
Коефіцієнт використання автомобілів становить:
де — кількість робочих днів автомобіля за рік,
— кількість календарних днів в році.
2.1.4 Визначення річного пробігу автомобіля деінвентарна (спискова) кількість автомобілів.
2.1.5 Розрахунок коефіцієнтів переходу від циклу до року Коефіцієнт переходу від циклу до року становить:
декоефіцієнт переходу від циклу до року.
2.1.6 Визначення кількості ТО і КР автомобіля за рік Кількість КР за рік становить:
Кількість ТО за рік становить:
Кількість обслуговувань на посту поглибленої діагностики Д-2 за рік становить:
де — кількість з діагностичних дій з поглибленої діагностики за рік для парку автомобілів.
Кількість обслуговувань на постах загальної діагностики Д-1 за рік становить:
де — кількість діагностичних дій загальної діагностики за рік.
2.1.7 Визначення змінної програми ТО автомобілів Визначення змінної програми ТО:
де — кількість днів роботи зони ЩО в році;
с — кількість змін.
де — кількість днів роботи зони ТО-1 в році.
де — кількість днів роботи зони ТО-2 в році.
Кількість діагностичних дій з загальної діагностики Д-1 за зміну:
де — кількість днів роботи поста Д-1 в році .
Кількість діагностичних дій з поглибленої по елементної діагностики Д-2 за зміну становить:
де — кількість днів роботи поста Д-2 в році.
2.1.8 Визначення річного обсягу робіт з ТО і ремонту автомобілів Річний обсяг робіт з ТО і ПР визначаю із трудових затрат на одне обслуговування де — річний обсяг робіт ЩО;
— річний обсяг робіт ТО-1;
— річний обсяг робіт ТО-2;
— річний обсяг робіт СО;
— річний обсяг робіт ПР.
Таблиця 2.1 Річний обсяг робіт з ТО і ремонту автомобілів
Вид робіт | Позначення | Кількість обслуговувань за рік | Трудомісткість одного обслуговування (люд. год) | Річний обсяг робіт (люд. год) | |
Річний пробіг парку автомобілів (км) | |||||
ЩО | 0,225 | ||||
ТО-1 | 0,48 | ||||
ТО-2 | 7,6 | ||||
СО | 1,52 | ||||
ПР | 0,58 | ||||
Всього | ; | ; | |||
2.1.9 Визначення обсягу робіт по самообслуговуванню автомобільного парку підприємства Загальна трудомісткість робіт при ТО за рік становить:
де — - загальна трудомісткість робіт при ТО за рік.
Роботи з ТО і ПР називаються виробничими, тому:
де — загальна трудомісткість виробничих затрат за рік;
трудомісткість робіт при ПР за рік.
Роботи з ТО і ПР називаються виробничими, тому:
де b — коефіцієнт визначення обсягу допоміжних робіт.
Річний обсяг робіт з самообслуговування зводиться в таблицю 2.2 враховуючи рекомендований розподіл за видами робіт.
Таблиця 2.2 Річний обсяг робіт з самообслуговування
Вид робіт | Обсяг робіт | ||
% | люд.год | ||
Електротехнічні | 2579,75 | ||
Механічні | |||
Слюсарні | |||
Ковальські | 2063,8 | ||
Зварювальні | 4127,6 | ||
Бляхарські | 4127,6 | ||
Мідницькі | 103,2 | ||
Трубопровідні | 2270,2 | ||
Ремонтно-будівельні | |||
Всього самообслуговування | |||
Таблиця 2.3 Річний обсяг загально-виробничих робіт
Вид робіт | Обсяг робіт | ||
% | люд.год | ||
Транспортні | |||
Переганяння автомобілів | |||
Приймання зберігання, видача матеріальних цінностей | |||
Прибирання території, приміщень | |||
Всього | |||
2.2 Розрахунок об'єкту проектування
2.2.1 Розподіл обсягу робіт по виробничих зонах, дільницях і цехах Виробничі роботи (роботи з ТО і ПР автомобілів) виконуються на робочих постах в цехах і дільницях де обслуговуються і відновлюються вузли та механізми зняті з автомобіля. Відповідно до цього загальну трудомісткість виробничих робіт поділяємо на:
- трудомісткість постових робіт
- трудомісткість цехових робіт тому:
Трудомісткість постових робіт становить:
де — коефіцієнт долі постових робіт при виконанні ТО-2;
— коефіцієнт постових робіт при виконанні ПР.
Трудомісткість цехових робіт становить:
Таблиця 2.4. Річний обсяг постових робіт
Вид робіт | Обсяг робіт | ||
% | люд.год. | ||
Загальне діагностування | 1331,5 | ||
Поглиблене діагностування | 6657,7 | ||
Кріпильні і розбірно-складальні | |||
Регулювальні | 9986,5 | ||
Мастильно-заправні | 6657,7 | ||
Електромеханічні | 6657,7 | ||
Обслуговування приладів системи живлення | 6657,7 | ||
Шино монтажні | 4660,4 | ||
Всього постових робіт | 66 577,2 | ||
Таблиця 2.5 Річний обсяг цехових робіт
Вид робіт | Обсяг робіт | ||
% | люд.год. | ||
Агрегатні | 6162,5 | ||
Слюсарно-механічні | |||
Електромеханічні | 3204,5 | ||
Акумуляторні | 1232,5 | ||
Ремонт приладів системи живлення | 2218,5 | ||
Шиномонтажні | |||
Вулканізація | |||
Ковальські | 739,5 | ||
Мідницькі | |||
Зварювальні | 1231,5 | ||
Бляхарські | |||
Деревообробні | |||
Обойні | 739,5 | ||
Арматурні | 246,5 | ||
Всього | |||
Трудомісткість цехових робіт по відділенні, цеху, дільниці становить:
де С — відсоток трудомісткості робіт за спеціальностями;
— трудомісткість робіт у відділенні, цеху, дільниці.
При проектуванні зон ТО-1,ТО-2 і ПР визначаємо трудомісткість постових робіт
— для зони прибирально — мийних робіт:
— для зони ТО-1:
— для зони ТО-2:
— для зони ПР де в — частина трудомісткості постових робіт ПР,%;
— для агрегатної дільниці:
2.2.2 Розрахунок кількості робітників До виробничих робітників відносяться робітники різних зон і відділень, які безпосередньо виконують роботи з ТО і ПР рухомого складу. При такому розрахунку розрізняють технологічне і штатне число робітників. При розрахунку кількості робітників відділення визначають технологічно необхідну і штатну кількість робітників. Технологічно необхідну кількість робітників визначають за формулою.
агрегатний ремонт коробка передача де — річний виробничий фонд часу робочого місця при однозмінній роботі
Визначаємо річний виробничий фонд робочого часу:
де — продовжність робочої зміни;
— число календарних днів в році;
— число вихідних днів в році;
— число святкових днів в році;
— передсвяткові дні, скорочені на 1 годину;
— кількість робочих суботніх днів, згідно робочого графіку які скорочені на 2 години;
— продовжуваність зміни (год).
дні,
днів, днів, дні,
днів, год.
Приймаємо 11 робітників.
Визначаємо штатну кількість робітників:
де — виробничий фонд робочого часу штатного робітника.
де — втрата часу за поважних причин;
де — продовжуваність щорічної відпустки.
де — кількість днів відпустки робітника.
Приймаємо 13 робітників.
2.2.3 Організація робіт в агрегатному відділенні і схема технологічного процесу Агрегати і вузли потрапляючи в агрегатну дільницю поступають на зовнішнє миття і після на розбирання. Після розбирання агрегату чи вузла деталі поступають на миття у спеціальних ваннах, після чого виконується контроль і сортування. Справні деталі направляються на збирання вузлів і агрегатів. Браковані викидають в брухт. Деталі і складальні одиниці, що потребують ремонту, поступають в ремонт і після здійснення ремонтних операцій їх направляють на збирання або на зберігання в складі оборотних агрегатів.
Приклад схеми технологічного процесу ремонту коробки передач приведений на рисунку 2.1.
Рисунок 2.1- Схема технологічного процесу ремонту коробок передач
2.2.4 Розробка технологічного процесу ремонту коробки передач Догляд за коробкою передач полягає в підтяжці її кріплень до картера зчеплення і перевірці рівня оливи в її картері, доливання її і зміні відповідно до карти змащення.
Зливати оливу потрібно відразу після поїздки, поки вона гаряча. Якщо відпрацьована олива виявляється сильно забрудненою, коробку варто промити рідкою мінеральною оливою.
Перевірку рівня оливи роблять через заливний отвір на автомобілі, який розміщують на горизонтальній площині. Перевірку варто робити через якийсь час після поїздки, щоб дати можливість охолонути і стікти оливі зі стінок, а піні осісти.
У процесі експлуатації варто звертати особливу увагу на стан сапуна. Він служить для з'єднання внутрішньої порожнини коробки з атмосферою, і його забруднення приводить до підвищення тиску і виникненню течі оливи.
У початковий період експлуатації до приробляння сальників допускаються незначне (без каплепадіння) просочування оливи і поява масляного нальоту на днищі кузова.
Основні зовнішні дефекти коробок передач: підвищений шум і стуки під час роботи машини; погане включення або самовиключення шестерень внаслідок спрацювання підшипників та їх посадочних місць, спрацювання шестерень, шліцьових, шпонкових і різьбових з'єднань, а також тріщини і зломи в деталях.
Підвищене спрацювання підшипників кочення і зубів шестерень по товщині є причиною попадання абразивних частинок у мастило через нещільності.
Торцеві руйнування зубів шестерень з боку включення — результат неточного регулювання зчеплення і неправильного переключення передач.
Втомлювальне викришування робочих поверхонь зубів значно підвищується при неправильному зачепленні шестерень — збільшенні або зменшенні міжосьової відстані, неповному включенні, перекосі зчеплення, неправильному регулюванні конічного зачеплення. Спрацювання шліців (по товщині) і шпонкових канавок — результат високих питомих тисків і ударних навантажень при збільшеному зазорі у шліцьовому або шпонковому з'єднанні.
Розбирання. Повністю коробки передач розбирають тільки при капітальному ремонті. При поточному ремонті або експлуатаційному ремонті автомобіля після зовнішнього і внутрішнього миття й часткового розбирання перевіряють технічний стан деталей коробки: вимірюють ступінь спрацювання зубів по довжині і товщині; по осьовому і радіальному переміщенню валів визначають ступінь спрацювання підшипників; ступінь спрацювання шліцьових і шпонкових з'єднань, а також міцність посадки вінців на втулках контролюють переміщенням шестерень. При потребі коробку направляють на капітальний ремонт.
Повністю коробку розбирають на спеціальних або універсальних стендах, застосовуючи при цьому прості й універсальні знімачі і пристрої.
Коробки передач, встановлені на універсальний стенд, розбирають приблизно у такій послідовності:
— коробку встановити на стенд, викручують болти з шайбами, знімають механізм перемикання передач в зборі, знімають прокладку.
— Викручують гвинти з шайбами і знімають кришку в зборі з ричагом і ущільнювачем, пружину і прокладку.
— Випресовують три заглушки отворів штоків.
— Викручують заглушку гнізда фіксатора, викручують пружину і кульку, викручують запобіжний клапан.
— Розшплінтовують і викручують болти вилок.
— Вибивають штоки і заглушки з протилежної сторони, знімають вилки.
При вибиванні штоків 3, 4 передач і заднього ходу слідкують за тим, щоб не загубити кульку, так як його виштовхує пружина.
— Витягнути кульку і пружину фіксаторів штоків.
— Витягнути два замкові плунжери.
— Відкрутити гвинти з пружинними шайбами, зняти кришку, прокладку пружину.
— Зняти стопорне кільце, витягнути запобіжник.
Рисунок 2.2 — Механізм перемикання передач
1 — бокова кришка; 2, 17, 28 — шайби; 3, 10, 29, 38 — болти; 4 шток включення заднього ходу; 5 — шток включення ІІІ і ІV передач; 6, 23 — штифти; 7, 19 — заглушки; 8 — стопорний палець; 9 шток включення І і ІІ предач; 11- кулька фіксатора; 12 — стопорне кільце; 13, 30, 34 — пружини; 14, 31, 32 — прокладки; 15 — кришка; 16, 27 — гвинти; 18- замкові пружини; 20 — клапан; 21 — кришка; 22 — кришка в зборі; 24 — ущільнювач; 25 — ричав; 26 — рукоятка; 33 — запобіжник; 35 — вилка включення І і ІІ передач; 36 — вилка включення ІІІ і IV передач; 37 — вилка включення заднього ходу; 39 шплінт
— Відкрутити болти з шайбами кріплення кришки, зняти кришку, прокладку, скобу відтяжної пружини.
— Провертаючи первинний вал в зборі, направити дугоподібний виріз в сторону шестерні приводу проміж уточного валу і випре совати первинний вал в зборі, зняти кільце синхронізатора.
— Закріпити первинний вал в зборі в лещата.
— Зняти стопорне кільце роликового підшипника і витягнути ролик з гнізда первинного вала.
— Відкрутити гайку кріплення підшипника (ліва різьба), зняти упорне кільце.
— Перезакріпити первинний вал в лещатах, спресувати підшипник з первинного вала і зняти масло відбивач.
— Викрутити стопорний гвинт осі блока шестерень заднього ходу і випер сувати вісь, одночасно знімаючи блок шестерень заднього ходу.
— Викрутити гвинти і зняти стопорні пластини підшипника.
— Зняти стопорне кільце маточини синхронізатора, випер сувати вторинний вал в зборі.
Вторинний вал випресовується з допомогою перехідної втулки 71−2070, яка входить в комплект 71−1612.
— Зняти з вала муфту в зборі, кільце блокуюче, шайбу упорну, шестерню третьої передачі в зборі, шестерню другої передачі в зборі і шестерню першої передачі.
— Витягнути вторинний вал з підшипником в зборі з картера.
— Взяти муфту в зборі, витягнути маточину, витягнути сухарі, кульки, пружини.
— Закріпити вторинний вал в зборі в лещатах, зняти стопорне кільце .
— Зпресувати підшипник з вала, зняти масло відбивач, зняти вал з лещат.
— Відкрутити кришку переднього підшипника проміжного вала, зняти упорне кільце.
— Відкрутити гайку переднього підшипника проміжного вала і випресувати вал разом з підшипником.
— Зняти з проміжного вала упорну шайбу, шестерню, шестерні третьої і другої передач, розпірну втулку.
— Витягнути проміж уточний вал з підшипником в зборі з картера.
— Закріпити проміжний вал в зборі в лещатах, викрутити болт кріплення заднього підшипника, зняти упорне кільце і тарілчасту пружину.
— Спресувати задній підшипник з вала і зняти вал з лещат.
— Випресувати з картера передній підшипник проміжного вала.
— Викрутити пробки масло заливного і масло зливного отворів.
— Промити деталі коробки передач.
— Перевірити технічний стан деталей.
Технічні вимоги на контроль, сортування і ремонт деталей.
В картері не допускаються:
— Пробої і обломи, а також тріщини вух кріплення коробки передач, захоплюючі тіло картера; тріщини на поверхнях картера, які входять в отвори під підшипники, вісь блока шестерень заднього ходу і прилягаючі площини;
— Діаметр отвору D1 під підшипник первинного вала більше ніж 80,03 мм;
— Діаметр отворів D2 i D3 під підшипники вторинного вала і під задній підшипник проміжного вала більше ніж 72,03 мм;
— Діаметр отвору D4 під передній підшипник проміжного вала більше ніж 62,04 мм;
— Діаметр отворів D5 i D6 під вісь блока шестерень заднього ходу більше ніж 19,04 мм;
— Зношення торцевих поверхонь приливів під вісь блока шестерень заднього ходу: розмір К більше ніж — 85+0,1 мм, розмір Л менше ніж — 14−0,43 мм;
— Зняття або зрив різьби М, Н, П, Р, С, Ф більше двох ниток.
Тріщини, які не входять в отвори під підшипники і вісь блока шестерень заднього ходу, усуваються заварюванням з послідуючою зачисткою.
Рисунок 2.3 — Картер коробки передач Тріщини або обломи вух кріплення коробки передач, які не захоплюють тіло картера, ліквідуються заваркою з обробкою поверхні.
Зношення отворів під вісь блока шестерень заднього ходу більше ніж 19,04 мм усуваються вставкою втулок.
Зношення торцевих поверхонь під вісь блока шестерень заднього ходу усувається наплавкою.
Зминання різьби в отворах більше двох ниток усувається прогонкою.
На первинному валі не допускаються:
— Тріщини або обломи, крошіння на робочих поверхнях зубів, задири на конусній пверхні, зношення або облом зубів (шліців) з торця включення по довжині і по ширині;
— Сліди від роликів на поверхні отвору під передній підшипник вторинного вала;
— Діаметр D1 шийки під передній підшипник менше ніж 16,95 мм;
— Діаметр D2 шийки під кришку підшипника первинного вала менше ніж 34,6 мм;
— Діаметр D3 шийки під задній підшипник менше ніж 39,98 мм;
— Діаметр D4 отвору під передній підшипник вторинного вала більше ніж 30,32 мм;
Рисунок 2.4 — Первинний вал
— Довжина B зуба менше ніж 2,8 мм;
— Товщина S зуба менше ніж 5,2 мм (заміряється на висоті головки зуба, h=4.416 мм);
— Ширина Г шліців менше ніж 5,28 мм;
— Зминання різьби К більше двох ниток.
На проміжному валі не допускаються:
— Тріщини або обломи, крошіння на робочих поверхнях зубів;
— Діаметр D1 шийки під передній підшипник менше ніж 24,98 мм;
— Діаметр D2 шийки під задній підшипник менше ніж 29,98 мм;
— Товщина S зуба менше 6,8 мм (замірюється по висоті головки зуба, h=5.53 мм);
— Довжина l зуба 1 менше ніж 17 мм;
— Зминання або зрив різьби A, Б більше двох ниток.
Забої і заусенці на шліцах і зубах усуваються зачисткою.
Зминання різьби А, Б більше двох ниток усувається прогонкою.
Рисунок 2.5 — Проміжний вал На блоці шестерень заднього ходу не допускається:
— Тріщини чи обломи, крошіння на роботчих поверхнях зубів;
— Товщина зуба менше ніж 6,8 мм (замірюється на висоті головки зуба, h=5.53 мм);
— Зношення отвору втулки під вісь блока шестерень заднього ходу більше ніж 19,12 мм;
— Зношення пазу під вилку переключення передач по ширині до розміру більше ніж 6,0 мм;
— Довжина зуба менше ніж 14 мм.
При зношенні отвору під вісь блока шестерень заднього ходу більше ніж на 19,12 мм — замінити втулку. Нова втулка не повинна виступати за торцеві поверхні блока. Отвори в втулці для підводу мастила повинні співпадати з отворами в шестерні.
При зношуванні або відколюванні зубів з торця включення по довжині зачистити торці і скруглити гострі кромки зубів.
На осі блоку шестерень заднього ходу не допускається:
— Діаметр шийки під втулку блока шестерень заднього ходу і внутрішній отвір картера коробки передач менше ніж 18,97 мм;
— Діаметр шийки під зовнішній отвір картера коробки передач менше 18,99 мм.
На вторинному валі не допускаються:
— Тріщини або обломи;
Рисунок 2.6 — Вторинний вал
— Діаметр шийки D1 під роликовий підшипник менше ніж 19,2 мм;
— Діаметр шийки D3 під втулку шестерні другої передачі менше ніж 41,92 мм;
— Діаметр шийки D4 під задній підшипник менше ніж 34,98 мм;
— Діаметр шийки D2 під втулку шестерні третьої предачі менше ніж 29,94 мм.
На вилці переключення предач не допускаються:
— Тріщини або обломи;
— Товщина C кінців вилок: вилки включення передач заднього ходу — менше ніж 4,6 мм, вилки включення першої і другої передач — менше ніж 6,0 мм, вилки включення третьої і четвертої передач — менше ніж 8,5 мм;
— Ширина K паза під ричав переключення предач більше ніж 13,8 мм;
— Зношення отворів D під шток переключення предач більше ніж 13,1 мм;
Рисунок 2.7 — Вилка перемикання ІІІ і IV передач Збирання коробки передач.
— Вкрутити пробки маслозаливного і масло зливного отворів.
— Напресуваи на проміжний вал підшипник.
Канавка на зовнішньому кільці підшипника повинна бути повернута в сторону від шестерні проміжного вала.
— Закрутити болт з тарілчастою пружиною.
— Встановити упорне кільце в канавку підшипника.
— Встановити на проміжний вал розпірну втулку, вставити вал отвір картера.
Підбір шестерні по шліцах вала повинен забезпечити відсутнє відчуття кутового люфту при вільному ковзанні шестерні по шліцах вала. Після підбору деталі не повинні розкомплектовуватись.
— Підібрати шестерню другої предачі, шестерню третьої предачі, шестерню приводу проміжного вала по шліцах проміжного вала і встановити шестерні на вал.
— Запресувати проміжний вал з підшипником в зборі до упору кільця в стінку картера.
— Встановити упорну шайбу на передній кінець проміжного вала.
— Запресувати підшипник проміжного вала в отвір картера з одночасною напре совкою його на передній кінець проміжного вала до упору в упорну шайбу.
— Закрутити гайку кріплення підшипника проміжного вала, розкернити гайку з допомогою кернера.
Осьове преміщення шестерень на проміжному валі не допускається.
— Встановити в кришку ущільнююче кільце.
Перекручування кільця не допускається.
— Закрутити кришку з ущільнюючим кільцем в отвір картера.
Торець кришки не повинен виступати за торець картера.
— Встановити на вторинний вал з сторони шліцевого кінця масло відбивач.
— Напресувати підшипник на шийку вала до упору.
Канавка на зовнішньому кільці підшипника повинна бути повернута в сторону від масловідбивача.
— Встановити на вторинний вал упірне і стопорне кільця.
Зазор між цпірним кільцем і стопорним не повинен перевищувати 0,2 мм.
— Встановити на конусну поверхню шестерні третьої предачі в зборі блокувальне кільце синхронізатора і провірити прилягання конусних поверхонь. Зняти кільце.
Плоша прилягання конусних поверхонь блокуючого кільця синхронізатора і конусної поверхні шестерні третьої предачі повинні бути не менше 65% загальної площ конусної поверхні.
Допускається притирання конусних поверхонь. Зазор між торцями блокуючого кільця і зубчастого вінця шестерні третьої предачі повинен бути 0,60−1,25 мм. Після притирання деталі промити.
Після підбирання і притирки кільце і шестерня не повинні розкомплектовуватись.
— Підібрати ковзаючу муфту синхронізатора по шліцах маточини.
Боковий зазор між зубами муфти і маточини повинен бути не більше 0,05 мм, прекоси в шліцах не повинні перевищувати 0,35 мм.
— Встановити в гнізда маточини пружини, кульки і сухарі синхронізатора. Встановити на маточину муфту.
Для виключення випадків випадання кульок синхронізатора отвори в сухарях виконані ступінчастими. В синхронізаторі сухарі встановлюються стороною з отворами меншого діаметру в сторону муфти.
Більш довгі частини маточини і муфти повинні бути розміщені в одну сторону і при встановленні на вторинний вал повинні бути обернені в сторону первинного вала.
Рисунок 2.8 — Синхронізатор
1 — муфта; 2 — маточина; 3 — сухар; 4 — кулька
— Підібрати ковзаючу шестерню першої предачі по кульках вторинного вала.
— Змастити шийки вторинного вала трансмісійною оливою, встановити вал в отвір картера.
— Встановити на вал підібрану шестерню першої предачі, шестерню другої предачі, шестерню третьої предачі з блокуючим кільцем синхронізатора, упорну шайбу, муфту в зборі.
Шестерні повинні вільно, без заїдання і заклинювання, обертатись на шийках вала.
— Встановити стопорне кільце в канавку вторинного вала.
— Запресувати в отвір картера вторинний вал з підшипником в зборі.
Передній торець канавки підшипника об'єднати з площиною картера.
— Встановити стопорні пластини в канавку підшипника і закріпити їх гвинтами.
— Встановити на конусну поверхню первинного вала блокуюче кільце синхронізатора і провірити прилягання конусних поверхонь. Зняти кільце.
— Встановити на шийку первинного вала маслоутримувач.
— Напресувати підшипник на шийку первинного вала до упору в маслоутримувач.
Підшипник повинен бути встановлений так, щоб канавка під стопорні кільця була повернута в шліців вала, а внутрішня кромка маслоутримувача була щільно затиснута по всій окружності між торцем внутрішнього кільця підшипника і торцями зубів шестерні первинного вала.
— Закрутити гайку кріплення підшипника первинного вала і застопорити гайку кернінням.
Керніння не повинно визивати надколів і тріщин на гайці.
— Встановити упорне кільце в канавку зовнішнього кільця підшипника первинного вала.
— Встановити ролик в гніздо первинного вала.
Перед встановленням ролика ретельно промити, обдути стиснутим повітрям і змастити консистентним мастилом.
— Встановити стопорне кільце роликів підшипника вторинного вала.
— Ввести первинний вал з блокувальним кільцем синхронізатора в отвір картера, встановити кільце синхронізатора в муфту і встановити роликовий підшипник первинного вала на хвостовик вторинного вала .
— Повернути первинний вал так, щоб технологічна лиска на валу була направлена в сторону шестерні приводу, запресувати первинний вал в зборі в картер до упору кільця в торець картера.
— Нанести на прокладку кришки підшипника первинного вала тонкий шар герметизуючої пасти і накласти її на картер, при цьому отвори в прокладці і отвори в картері повинні співпадати.
— Встановити скобу відтяжної пружини під головки двох болтів, які знаходяться ближче до роз'ємну картера з кришкою, встановити решту болтів з пружинними шайбами, і затягнути.
— Закрутити стопорні гвинти кришки переднього підшипника, проміжного вала і законтрагаїти його гайкою.
— Провірити обертання первинного вала.
Первинний вал повинен обертатись вільно, без заїдання, від зусилля руки.
— Змастити втулку блоку шестерень заднього ходу і встановити блок в картер.
— Встановити вісь в отвір картера і в отвір блоку шестерень заднього ходу, зміщуючи отвори під штопорний гвинт в осі з отвором в стінці картера.
— Закрутити штопорний гвинт в отвір картера до упору і надійно затягнути його.
— Провірити обертання блоку шестерень заднього ходу.
Блок шестерень заднього ходу повинен обертатись вільно, без заїдання, від зусилля руки.
— Встановити в нейтральне положення муфту включення третьої і четвертої передач, шестерню включення першої і другої передач і блок шестерень заднього ходу.
— Встановити в гніздо бокової кришки пружину і кульку фіксатора.
— Встановити запобіжник внутрішньою стороною в гніздо кришки, стискаючи одночасно пружину фіксатора.
— Встановити штопорне кільце на плунжер.
— Вставити в отвір запобіжника пружину, нанести на прокладку тонкий шар герметизуючої пасти, змастити гвинти пастою і закріпити кришку.
— Встановити пружину і кульку в отвір фіксатора штока заднього ходу.
— Встановити з зовнішньої сторони отвору штока (з сторони фіксатора) оправку так, щоб її клиновий кінець «втопив» кульку повністю в гніздо фіксатора, і повернути оправку на півоберта (Рисунок — 2.9). Змастити шток трансмісійною оливою.
— Встановити в отвір кришки і вилки включення заднього ходу шток, і пересуваючи його, виштовхнути оправку на зовню.
Рисунок 2.9 — Приспосіблення для збирання штоків і фіксаторів:
а — збирання фіксаторів; б — встановлення штока
— Встановіть шток і вилку включення задньої передачі в нейтральне положення, змістивши при цьому отвори в штоку в вилці під штопорний болт.
— Закрутити болт і зашплінтувати.
— Встановити один плунжер в отвір бокової кришки.
— Виконати пункти зазначені раніше для штока в зборі і вилки включення третьої і четвертої передач.
Пункт для штока включення третьої і четвертої передач виконується в зборі з штопорним пальцем і штифтом.
— Встановити другий плунжер в отвір кришки.
— Виконати пункти зазначені раніше для штока і вилки включення першої і другої передач.
Вилки включення передач повинні бути надійно закріплені на штоках, люфт не допускається. Штоки перемикання передач повинні переміщуватись в отворах бокової кришки вільно, без заїдання і заклинювання.
Фіксатори штоків повинні забезпечувати чітке перемикання передач без великого зусилля при надійній фіксації штоків в нейтральному роботчому положенні, а замковий пристрій повинен надійно запобігати одночасному включенню двох предач.
— Встановити кульку і пружину в отвір під плунжери замка, змастити заглушку герметизуючою пастою і закрутити.
Пружини фіксатора штока першої і другої передач в вільному стані мають велику довжину, аніж дві інші пружини фіксатора.
— Змастити герметизуючою пастою заглушки штоків переключення передач, вставити їх в отвори штоків і розчеканити.
— Встановити ричаг перемикання передач в кришку.
— Нанести на прокладку кришки тонкий шар герметизуючої пасти і встановити прокладку на бокову кришку.
— Встановити в кришку бокової виточки конічну пружину.
— Змастити гвинти кріплення кришки герметизуючою пастою.
— Встановити кінець ричага в паз одної із вилок перемикання передач, встановити кришку і закріпити її гвинтами з пружинними шайбами.
— Надягнути ущільнювач на ричаг і кришку.
— Вкрутити запобіжний клапан.
— Нанести на прокладку бокової кришки тонкий шар герметизуючої пасти, накласти прокладку на роз'єм картера коробки передач.
— Встановити механізм перемикання передач в зборі таким чином, щоб вилки перемикання передач зайшли відповідно в пази: ковзаючої шестерні першої передачі, муфти включення третьої і четвертої передач і блоку шестерень заднього ходу.
— Закрутити і затягнути болти з пружинними шайбами кріплення бокової кришки до картера коробки передач.
В зібраній коробці предач всі вали повинні повертатись вільно, баз заїдань на всіх предачах.
Передачі повинні премикатись чітко, без заїдання і заклинювання і надійно фіксуватись.
Включення пердач повинно бути повним.
2.2.5 Вибір технологічного устаткуванання Перелік устаткування відділення подано в таблиці 2.5
Таблиця 2.5 Перелік устаткування відділення
№ | Назва обладнання | Тип або модель | Коротка технічна характеристика | Площа обл., м2 | К — сть одиниць | |
Стелаж для деталей | Власного виготовлення | Габарити 1400×600×800 | 0,84 | |||
Скриня для ганчір'я | Власного виготовлення | Габарити 800×400×600 | 0,32 | |||
Верстат для розточування гальмових барабанів і обточування накладок | Р-114 | Максимальні діаметри поверхонь, що обробляються, 350 і 750 мм. Потужність привода — 2,2 кВт. Хід супорта 140 і 250 мм. Габарити 1700×1000×1315 | 1,7 | |||
Телефон і радіо | ||||||
Настільний свердлильний верстат | ГМ-112 | Діаметр свердла до 12 мм. Потужність привод -0,6 кВт. Габарити 730×355×820 | 0,26 | |||
Слюсарний верстак | ОРГ-1468−01−060А | Габарити 1200×800×800 | 1,92 | |||
Шафа настінна для приладів і інструментів | Власного виготов-лення | Габарити 400×800×800 | 0, 64 | |||
Стенд для розбирання і регулювання зчеплень на підставці | Р-207 | Тиск повітря — 0,4 МПа. Зусилля — 15 кН. Габарити 625×565×405 | 0,35 | |||
Прес гідравлічний 40т | 2135−1М | Максимальний хід штока — 250 мм, тиск в системі - 28 МПа, потужність привода -2,2 кВт, габарити 1470×640×2090 | 0,94 | |||
Стенд для ремонту редукторів задніх мостів | Р-640 | Потужність привода -0,37 кВт. Габарити 850×650×985 | 0,55 | |||
Стенд для клепання гальмівних накладок | Р-304 | Пневматичний, максимальний діаметр заклепки — 8 мм, зусилля 18 кН, габарити 600×400×600 | 0,24 | |||
Підвісна кран — балка | Вантажопідйомність -1 т; потужність привода -2,2 кВт. | |||||
Лещата | ГОСТ 4045–75 | |||||
Стелаж для інструментів | Власного виготов-лення | Габарити 490×1390×1700 | 0,68 | |||
Настільний прес на підставці | Р-324 | Зусилля на плунжері - 8… 100 кН, тиск насоса — 40 МПа, габарити 376×100×600 | 0,38 | |||
Стенд, для ремонту карданних валів і рульових механізмів | Р-217 | Стаціонарний, універсальний, маса — 53 кг. Габарити 900×600×1265 | 0,54 | |||
Миюча ванна для деталей | К54СБ | Габарити 975×660×860 | 0,64 | |||
Заточний верстат | 332Б | Стаціонарний на два круга діаметром 300 мм. Потужність привода -1,7 кВт. Габарити 812×480×800 | 0,39 | |||
Електрополотенце | ||||||
Умивальник | ||||||
Скриня для відходів | Власного виготовлення | Габарити 900×400×600 | 0,36 | |||
Стенд для ремонту передніх і задніх мостів | Відcтань між зажимами 580…843 мм. Габарити 1300×1180×1006 | 1,53 | ||||
Стенд для ремонту коробок передач | Р201 | Стаціонарний, габарити 690×800×500 | 0,55 | |||
2.6 Розрахунок площі і обґрунтування планувальних рішень Площу виробничих приміщень визначають з наступних методів:
— аналітично (наближено) по надільній площі, при падаючій на один автомобіль, одиницю обладнання чи одне роботче місце;
— графічно (більш точно) по схемі, на якій в прийнятому масштабі викреслюються пости (поточні лінії) і вибране технологічне обладнання з урахуванням категорії рухомого складу із зберіганням всіх нормативних відстаней між автомобілями, обладнанням і елементами будівлі;
— графоаналітично (комбінований метод) — шляхом планувальних рішень і аналітичних обчислень.
Площа відділення визначається за формулою:
F (ВІД)=KГУСТИНИ ?FОБЛ КГУСТИНИ — коефіцієнт розташування обладнання;
КГУСТИНИ = 4;
?FОБЛ. — сумарна площа обладнання;
?FОБЛ. = 13,4(м2) .
F (ВІД)=4•13,4=53,6?54(м2).
Приймаємо площу відділення 54 м².
3. ОРГАНІЗАЦІЙНИЙ РОЗДІЛ
3.1 Організація і схема управління підрозділом (з використанням ЦУВ) Для організації управління підрозділом з використанням ЦУВ складено схему показану на рисунку 3.1.
Рисунок 3.1 Схема управління підрозділом
3.2 Схема технологічного процесу виробництва авто підприємства
Схема 3.2 Схема технічного обслуговування та поточного ремонту з попереднім діагностуванням
3.3 Техніка безпеки при виконанні технологічного процесу у відділенні і санітарно — гігієнічні вимоги Безпечність виробничого процесу — це властивість виробничого процесу відповідати вимогам безпеки праці під час проведення його в умовах, установлених нормативною документацією. У відповідності з нормативами безпечність виробничих процесів забезпечується:
· правильним вибором технологічних процесів, робочих операцій та порядку обслуговування виробничого устаткування;
· вибором виробничих приміщень чи зовнішніх майданчиків;
· вибором виробничого устаткування;
· розташуванням виробничого устаткування та організацією робочих місць;
· вибором способів зберігання та транспортування вихідних матеріалів, заготовок, напівфабрикатів, готової продукції та відходів виробництва розподілом функцій між людиною та устаткуванням з метою зменшення важкості праці;
· професійним відбором та навчанням працівників;
· застосуванням засобів захисту працівників;
· включенням вимог безпеки в нормативно-технічну та технологічну документацію.
При проектуванні, організації та проведенні технологічних процесів передбачають:
— усунення безпосереднього контакту працівників з вихідними матеріалами, напівфабрикатами, готовою продукцією та відходами виробництва, які мають на них небезпечний та шкідливий вплив;
— заміну технологічних процесів та операцій, пов’язаних з виникненням небезпечних та шкідливих виробничих чинників, процесами та операціями, при виконанні яких ці чинники відсутні або мають меншу інтенсивність .
— застосування комплексної механізації, автоматизації: та комп’ютеризації виробництва;
— застосування дистанційного керування технологічними процесами та операціями при наявності небезпечних і шкідливих виробничих чинників.
— використання засобів колективного захисту працівників;
— раціональну організацію праці та відпочинку з метою профілактики, та зниження важкості праці;