Ремонт машин
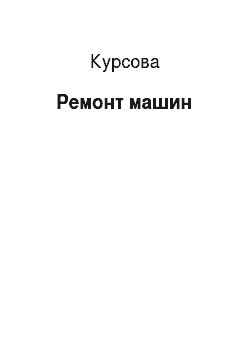
Можливість отримання наплавленого металу з потрібною твердістю і зносостійкістю без додаткової термообробки за допомогою охолоджувальної рідини (5%-й розчин кальцинованої соди). При однаковому матеріалі проволки можна отримати різні структури наплавленого металу, залежно від кількості рідини і способу її підводу; Деталь передає зусилля від шківа до лопатей водяного насосу і сприймає навантаження… Читати ще >
Ремонт машин (реферат, курсова, диплом, контрольна)
1. Загальний розділ
1.1 Призначення та конструкція деталі
Деталь циліндричної форми зі змінним перерізом, має шпоночні пази та метричну різьбу. Матеріал Сталь 45 ГОСТ 1050– — 88. Загальна шорсткість поверхні має сьомий клас точності, що відповідає = 1,25 — 0,63, є поверхня шостого класу =2,5 — 1,25, бокова поверхня під шпоночний паз п’ятого класу відповідно =20 — 10. Термообробка даної деталі - загальне гартування з високим відпуском.
Деталь передає зусилля від шківа до лопатей водяного насосу і сприймає навантаження згину і кручення. Підшипники кочення змащуються пластичним мастилом. Вид мащення — мокре. Марка мастила «ЛІТОЛ — 24» ГОСТ — 21 150−88. Робоча температура знаходиться у межах 80 — С.
Можливі дефекти:
— Згин — може виникнути у разі неправильної натяжки паса;
— кручення — може виникнути у разі динамічних навантажень від дії приводу;
— зношення посадочних місць — у разі «провертання» підшипника;
— зношення шпоночних пазів — у разі надмірних динамічних навантажень (під час запуску, зупинки, різкої зміни частоти обертання;
— тріщини — це може бути виробничий дефект, або умови експлуатації, вказані вище.
1.2 Ремонтне креслення деталі
В відповідності зі стандартом ГОСТ 2.604−88 розроблене ремонтне креслення деталі.
1.3 Карта технічних вимог на дефектацію деталі
Карту технічних вимог на дефектацію деталі виконано у відповідності з ЄСКД по «Форма 33».
2. Технологічний розділ
2.1 Встановлення кількості маршрутів
Маршрут 1
1. Зношення різьби.
2. Зношення шпоночних пазів.
Маршрут 2
1. Зношення різьби.
2. Зношення шпоночних пазів.
3. Згин і кручення.
4. Тріщини.
Маршрут 3
1. Згин і кручення.
2. Тріщини.
3. Зношення посадочних місць.
Маршрут 4
1. Зношення різьби.
2. Зношення посадочних місць.
2.2 Вибір раціонального способу ремонту, схема технологічного процесу усунення кожного дефекту по маршруту 4
Дефект 1. Зношення різьби.
Вибрано раціональний спосіб відновлення дефекту — автоматична вібродугова наплавка.
Цей спосіб має наступні переваги:
— невеликий нагрів деталі;
— можна наплавляти деталі діаметром менше 50 мм;
— мала зона термічного впливу;
— можливість отримання наплавленого металу з потрібною твердістю і зносостійкістю без додаткової термообробки за допомогою охолоджувальної рідини (5%-й розчин кальцинованої соди). При однаковому матеріалі проволки можна отримати різні структури наплавленого металу, залежно від кількості рідини і способу її підводу;
— великий діапазон регулювання режиму наплавки за допомогою електричних і механічних параметрів;
— великий діапазон товщини наплавленого шару (0,5…3,5 мм);
— достатньо висока продуктивність (8…10).
До недоліків слід віднести зниження втомливої міцності (30…40%). Отже, ці параметри і переваги визначають область застосування вібродугової наплавки, її застосовують при відновленні деталей із сталі, ковкого і сірого чавунів при нарощуванні зовнішніх і внутрішніх поверхонь, а також різьбових поверхонь. Цей спосіб порівняно не дороговартісний, в ньому не застосовують дорогі флюси, захисні гази та інше. Значним досягненням є можливість наплавки деталей малого діаметру.
Схема технологічного процесу усунення дефекту 1:
Операція 1. Токарна Операція 2. Наплавочна Операція 3. Токарна Операція 4. Контрольна Дефект 2. Зношення посадочних місць на валу під кульковий підшипник.
Вибрано раціональний спосіб відновлення дефекту — автоматична вібродугова наплавка.
Цей спосіб має наступні переваги:
— невеликий нагрів деталі;
— можна наплавляти деталі діаметром менше 50 мм;
— мала зона термічного впливу;
— можливість отримання наплавленого металу з потрібною твердістю і зносостійкістю без додаткової термообробки за допомогою охолоджувальної рідини (5%-й розчин кальцинованої соди). При однаковому матеріалі проволоки можна отримати різні структури наплавленого металу, залежно від кількості рідини і способу її підводу;
— великий діапазон регулювання режиму наплавки за допомогою електричних і механічних параметрів;
— великий діапазон товщини наплавленого шару (0,5…3,5 мм);
— достатньо висока продуктивність (8…10).
До недоліків слід віднести зниження втомливої міцності (30…40%). Отже, ці параметри і переваги визначають область застосування вібродугової наплавки, її застосовують при відновленні деталей із сталі, ковкого і сірого чавунів при нарощуванні зовнішніх і внутрішніх поверхонь, а також різьбових поверхонь. Цей спосіб порівняно не дороговартісний, в ньому не застосовують дорогі флюси, захисні гази та інше. Значним досягненням є можливість наплавки деталей малого діаметру.
Схема технологічного процесу усунення дефекту 2.
Операція 1. Токарна Операція 2. Наплавочна Операція 3. Токарна Операція 4. Шліфувальна Операція 5. Контрольна
2.3 План технологічних операцій для заданого маршруту 4
Операція 1. Токарна Проточити поверхню зношення різьби: 1-від діаметру 16 мм до діаметру 12 мм на довжину 12 мм; проточити поверхню зношення посадочного місця: 2-від діаметру 16,9 мм до діаметру 15 мм на довжину 26 мм.
Операція 2. Наплавочна.
Наплавити вібродуговою наплавкою проточені поверхні: 2-від діаметру 15 мм до діаметру 19 мм на довжину 26 мм;
1-від діаметру 12 мм до діаметру 18 мм на довжину 12 мм.
Операція 3. Токарна.
Проточити наплавлені поверхні: 2 — від діаметру 19 мм до діаметру 17, 1 мм на довжину 26 мм; 1 — від діаметру 18 мм до діаметру 15, 8 мм на довжину 12 мм; нарізати різьбу: 2-М16 крок 1,5.
Операція 4. Шліфувальна.
Шліфувати проточену поверхню: 2 — від діаметру 17,1 мм до діаметру 17 мм на довжину 26 мм.
Операція 5. Контрольна.
Контролювати геометричні розміри відновленої деталі.
2.4 Розробка кожної операції
Операція 1. Токарна Проточити поверхню зношення різьби: 1-від діаметру 16 мм до діаметру 12 мм на довжину 12 мм; проточити поверхню зношення посадочного місця: 2-від діаметру 16,9 мм до діаметру 15 мм на довжину 26 мм.
2.4.1 Розбивка операції на переходи
Перехід, А Встановити і закріпити деталь Перехід 1
Проточити поверхню зношення різьби: 1-від діаметру 16 мм до діаметру 12 мм на довжину 12 мм Перехід Б Зняти, повернути деталь на, втановити і закріпити деталь.
Перехід 2
проточити поверхню зношення посадочного місця: 2-від діаметру 16,9 мм до діаметру 15 мм на довжину 26 мм.
Перехід В Зняти деталь.
2.4.2 Призначення обладнання
Для виконання даної операції призначити верстат 1А616К.
2.4.3 Вибір установочних баз
Вибрати чорнову базу між посадочним місцем під підшипник і посадочним місцем під шків.
2.4.4 Вибір пристрою
Для встановлення і кріплення деталі використати трьох кулачковий патрон ГОСТ 2675– — 88
2.4.5 Підбір матеріалу
Для виконання даної операції матеріал не використовується.
2.4.6 Підбір інструменту
Підбір ріжучого інструменту Для виконання чорнової токарної обробки вибрано різець прохідний Т15К6 2 007 045 ГОСТ 18 884–88;
Підбір вимірювального інструменту Для замірів діаметрів застосувати універсальний вимірювальний інструмент штангенциркуль ШЦ-1 по ГОСТ 166–88
2.4.7 Встановлення кваліфікації робіт
Для виконання даної операції з врахуванням складності виконуємо роботи згідно Тарифно-кваліфікаційного довідника вибрано кваліфікацію токаря 3-го розряду.
Операція 2. Наплавочна Наплавити вібродуговою наплавкою проточені поверхні: 2-від діаметру 15 мм до діаметру 19 мм на довжину 26 мм; 1-від діаметру 12 мм до діаметру 18 мм на довжину 12 мм.
2.4.1 Розбивка операції на переходи
Перехід, А Встановити і закріпити деталь Перехід 1
Наплавити вібродуговою наплавкою проточені поверхню: 2-від діаметру 15 мм до діаметру 19 мм на довжину 26 мм;
Перехід Б Зняти, повернути деталь на, втановити і закріпити деталь.
Перехід 2
Наплавити вібродуговою наплавкою проточені поверхню: 1-від діаметру 12 мм до діаметру 18 мм на довжину 12 мм.
Перехід В Зняти деталь.
2.4.2 Призначення обладнання
Для виконання даної операції призначити: головка вібродугова наплавочна ОКС — 6559; токарно-гвинторізний верстат 1К62; зварювальний перетворювач ПСО-500.
2.4.3 Вибір установочних баз
Вибрати чорнову базу між посадочним місцем під підшипник і посадочним місцем під шків.
2.4.4 Вибір пристрою
Для встановлення і кріплення деталі використати трьох кулачковий патрон ГОСТ 2675– — 88
2.4.5 Підбір матеріалу
Для виконання даної операції використати: зваювально-наплавочний дріт Нп-30 ГОСТ 2254–88;
2.4.6 Підбір інструменту
Підбір ріжучого інструменту Для виконання даної операції ріжучий інструмент не використовується.
Підбір вимірювального інструменту Для замірів діаметрів застосувати універсальний вимірювальний інструмент штангенциркуль ШЦ-1 по ГОСТ 166–88.
2.4.7 Встановлення кваліфікації робіт
Для виконання даної операції з врахуванням складності виконуємо роботи згідно Тарифно-кваліфікаційного довідника вибрано кваліфікацію зварювальника — верстатника 3-го розряду.
Операція 3. Токарна.
Проточити наплавлені поверхні: 2 — від діаметру 19 мм до діаметру 17, 1 мм на довжину 26 мм; 1 — від діаметру 18 мм до діаметру 15, 8 мм на довжину 12 мм; нарізати різьбу: 2-М16 крок 1,5.
Встановити і закріпити деталь Перехід 1
Проточити наплавлену поверхню: 2 — від діаметру 19 мм до діаметру 17, 1 мм на довжину 26 мм;
Перехід Б Зняти, повернути деталь на, втановити і закріпити деталь.
Перехід 2
Проточити наплавлену поверхню:; 1 — від діаметру 18 мм до діаметру 15, 8 мм на довжину 12 мм.
Перехід В Замінити різець прохідний на різець різьбонарізний, перемістити супорт Перехід 3
нарізати різьбу: 2-М16 крок 1,5.
Перехід Г Зняти деталь.
2.5 Розробка карти ескізів
В графічній частині курсового проекту розроблено 4 карти ескізів за формою, яка відповідає ГОСТ 3.1107−88.
2.6 Розробка маршрутної карти
В додатку до пояснювальної записки курсового проекту приведено маршрутну карту, виконану за формою згідно ГОСТ 3.1107−88.
2.7 Розробка операційних карт
В додатку до пояснювальної записки курсового проекту приведено чотири операційних карти, які виконані і відповідності з ГОСТ 3.1107−88.
3. Розрахунковий розділ
3.1 Розрахунок партії деталей
В умовах ремонтного виробництва розмір партії деталей приймається рівним місячній чи квартальній потребі в ремонтуємих деталях.
Розрахунок партії деталей проводиться за формулою [6]
=75 шт. (3,1)
де N=1000 шт. — виробнича програма заводу;
m=2 — кількість однойменних деталей у вузлі;
kp=0,9 — коефіцієнт ремонту деталі
3.2 Розрахунок найвигідніших режимів і прогресивних норм часу по операціям
3.2.1 Операція 1. Токарна
Проточити поверхню зношення різьби: 1-від діаметру 16 мм до діаметру 12 мм на довжину 12 мм; проточити поверхню зношення посадочного місця: 2-від діаметру 16,9 мм до діаметру 15 мм на довжину 26 мм.
Перехід, А Допоміжний час на встановлення, кріплення і зняття деталі
Тд1=0,8 хв Перехід 1
Розрахунок режимів
D=16 мм — діаметр поверхні до точіння;
d=12 мм — діаметр поверхні після точіння;
l=12 мм — довжина поверхні точіння.
Розрахунок припуску [2]
(3,2)
Знаходження глибини різання
t=2 мм Розрахунок кількості проходів [2]
(3,3)
Розрахунок довжини обробки
L= l + l1+ l2 = 12+3,5+0=15,5 мм, (3,4)
де l=12 мм — довжина поверхні точіння (по кресленню);
l1=3,5 мм — врізання різця;
l2=0 мм — перебіг різця Знаходження табличної подачі
Sтабл = (0,15−0,4) мм/об Знаходження верстатної подачі
Sвр = 0,39 мм/об Знаходження табличної швидкості різання
VТ = 48 м/хв.
Розрахунок скоректованої швидкості різання
VР = VТ • Км • Кмр • Кх • Кох = 48 •1,31 •3,0 •0,85 • 1 = 160 м/хв, (3,5)
де Км =1,31 — коефіцієнт залежності від оброблюваного матеріалу;
Кмр = 3 — коефіцієнт залежності від матеріалу різця;
Кх = 0,85 — коефіцієнт залежності від характеру обробка поверхні;
Кох = 1 — коефіцієнт залежності від застосування охолодження.
Розрахунок частоти обертання деталі
(3,6)
Знаходження верстатної частоти обертання деталі
nв = 1800 об/хв Розрахунок основного часу
(3,7)
Знаходження допоміжного часу, пов’язаного з проходом Тд2 = 0,6 хв Тд3 = 0,05 хв Перехід 2
Розрахунок режимів
D=16,9 мм — діаметр поверхні до точіння;
d=15 мм — діаметр поверхні після точіння;
l=26 мм — довжина поверхні точіння.
Розрахунок припуску [2]
(3,8)
Знаходження глибини різання
t=0,95 мм Розрахунок кількості проходів [2]
(3,9)
Розрахунок довжини обробки
L= l + l1+ l2 = 26+3,5+0=29,5 мм, (3,10)
де l=26 мм — довжина поверхні точіння (по кресленню);
l1=3,5 мм — врізання різця;
l2=0 мм — перебіг різця Знаходження табличної подачі
Sтабл = (0,15−0,4) мм/об Знаходження верстатної подачі
Sвр = 0,39 мм/об Знаходження табличної швидкості різання
VТ = 48 м/хв.
Розрахунок скоректованої швидкості різання
VР = VТ • Км • Кмр • Кх • Кох = 48 •1,31 •3,0 •0,85 • 1 = 160 м/хв, (3,11)
де Км =1,31 — коефіцієнт залежності від оброблюваного матеріалу;
Кмр = 3 — коефіцієнт залежності від матеріалу різця;
Кх = 0,85 — коефіцієнт залежності від характеру обробка поверхні;
Кох = 1 — коефіцієнт залежності від застосування охолодження.
Розрахунок частоти обертання деталі
(3,12)
Знаходження верстатної частоти обертання деталі
nв = 1800 об/хв Розрахунок основного часу
(3,13)
Знаходження допоміжного часу, пов’язаного з проходом Т" д2 = 0,6 хв Розрахунок загального допоміжного часу Тдоп=Тд1 + Тд2 + Т" д2 + Тд3 = 0,8+0,6+0,6+0,05=2,5 хв (3,14)
Розрахунок загального основного часу
+ 0,02 + 0,04 = 0,06 (3,15)
Розрахунок оперативного часу Топ = ТО + Тдоп = 0,06 + 2,5 = 2,11 хв (3,16)
Розрахунок додаткового часу
(3,17)
де Кдод=6,5% - коефіцієнт додаткового часу від оперативного [5, табл. 25]
Розрахунок штучного часу Тшт = Топ + Тдод = 2,11+ 0,14 =2,25 хв (3,18)
Знаходження підготовочно-заключного часу ТПЗ = 13 хв Знаходження технічної норми часу
(3,19)
3.2.2 Операція 2. Наплавочна
Наплавити вібродуговою наплавкою проточені поверхні: 2-від діаметру 15 мм до діаметру 19 мм на довжину 26 мм; 1-від діаметру 12 мм до діаметру 18 мм на довжину 12 мм.
Перехід, А Допоміжний час на встановлення, кріплення та зняття деталі
Тд1=1 хв Перехід 1
Розрахунок режимів
D=15 мм — діаметр поверхні до наплавки;
d=19 мм — діаметр поверхні після наплавки;
l=26 мм — довжина наплавки.
Розрахунок припуску
(3,20)
Розрахунок кількості проходів
(3,21)
Знаходження табличної подачі
Sт = 2,0 мм/об Знаходження верстатної подачі
Sвр = 1,9 мм/об Знаходження табличної швидкості наплавки
V = 0,8 м/хв.
Розрахунок частоти обертання деталі
(3,22)
де Vдр=1,1 м/хв — швидкість подачі дроту;
d др =2 мм — діаметр дроту;
? = 0,85 — коефіцієнт наплавки Верстатна частота обертання деталі
nвр =12 об/хв Розрахунок основного часу
(3,23)
Допоміжний час, пов’язаний з наплавкою Тд2 = 0,9
Тд3 = 0,05
Перехід 2
Розрахунок режимів
D=12 мм — діаметр поверхні до наплавки;
d=18 мм — діаметр поверхні після наплавки;
l=12 мм — довжина наплавки.
Розрахунок припуску
(3,24)
Розрахунок кількості проходів
(3,25)
Знаходження табличної подачі
Sт = 2,5 мм/об Знаходження верстатної подачі
Sвр = 2,42 мм/об Знаходження табличної швидкості наплавки
V = 0,4 м/хв.
Розрахунок частоти обертання деталі
(3,26)
де Vдр=1,7 м/хв — швидкість подачі дроту;
d др =1,8 мм — діаметр дроту;
? = 0,85 — коефіцієнт наплавки Верстатна частота обертання деталі
nвр =9 об/хв Розрахунок основного часу
(3,27)
Допоміжний час, пов’язаний з наплавкою Т" д2 = 0,9
Розрахунок загального основного часу
(3,28)
Розрахунок допоміжного часу
Тд = Тд1 + Тд2 + Т" д2 + Тд3 = 1 + 0,9 + 2,85 = 2,8 хв (3,29)
Розрахунок оперативного часу Топ = ТО + Тд = 1,64 + 2,85 = 4,49 хв (3,30)
Розрахунок додаткового часу
(3,31)
де =15%-коефіцієнт додаткового часу від оперативного [5, с. 170]
Розрахунок штучного часу Тшт = Топ + Тдод = 4,49+ 0,67 = 5,19 хв (3,32)
Підготовочно-заключний час ТПЗ = 16 хв Розрахунок норми часу на операцію
(3,33)
Операція 3. Токарна.
Проточити наплавлені поверхні: 2 — від діаметру 19 мм до діаметру 17, 1 мм на довжину 26 мм; 1 — від діаметру 18 мм до діаметру 15, 8 мм на довжину 12 мм; нарізати різьбу: 2-М16 крок 1,5.
Перехід, А Допоміжний час на встановлення, кріплення і зняття деталі
Тд1=0,8 хв Перехід 1
Розрахунок режимів
D=19 мм — діаметр поверхні до точіння;
d=17,1 мм — діаметр поверхні після точіння;
l=26 мм — довжина поверхні точіння.
Розрахунок припуску [2]
(3,34)
Знаходження глибини різання
t=0,95 мм Розрахунок кількості проходів [2]
(3,35)
Розрахунок довжини обробки
L= l + l1+ l2 = 26+2+0=28 мм, (3,36)
де l=26 мм — довжина поверхні точіння (по кресленню);
l1=2 мм — врізання різця;
l2=0 мм — перебіг різця Знаходження табличної подачі
Sтабл = (0,15−0,4) мм/об Знаходження верстатної подачі
Sвр = 0,39 мм/об Знаходження табличної швидкості різання
VТ = 70 м/хв.
Розрахунок скоректованої швидкості різання
VР = VТ • Км • Кмр • Кх • Кох = 70 •1,31 •3 •0,75 • 1 = 206,3 м/хв, (3,37)
де Км =1,31 — коефіцієнт залежності від оброблюваного матеріалу;
Кмр = 3 — коефіцієнт залежності від матеріалу різця;
Кх = 0,75 — коефіцієнт залежності від характеру обробка поверхні;
Кох = 1 — коефіцієнт залежності від застосування охолодження.
Розрахунок частоти обертання деталі
(3,38)
Знаходження верстатної частоти обертання деталі
nв = 1800 об/хв Розрахунок основного часу
(3,39)
Знаходження допоміжного часу, пов’язаного з проходом Тд2 = 0,6 хв Тд3 = 0,05 хв Перехід 2
Розрахунок режимів
D=18 мм — діаметр поверхні до точіння;
d=15,8 мм — діаметр поверхні після точіння;
l=12 мм — довжина поверхні точіння.
Розрахунок припуску [2]
(3,40)
Знаходження глибини різання
t=1,1 мм Розрахунок кількості проходів [2]
(3,41)
Розрахунок довжини обробки
L= l + l1+ l2 = 12+2+0=14 мм, (3,42)
де l=12 мм — довжина поверхні точіння (по кресленню);
l1=2 мм — врізання різця;
l2=0 мм — перебіг різця Знаходження табличної подачі
Sтабл = (0,15−0,4) мм/об Знаходження верстатної подачі
Sвр = 0,39 мм/об Знаходження табличної швидкості різання
VТ = 70 м/хв.
Розрахунок скоректованої швидкості різання
VР = VТ • Км • Кмр • Кх • Кох = 70 •1,31 •3,0 •0,75 • 1 = 206,3 м/хв, (3,43)
де Км =1,31 — коефіцієнт залежності від оброблюваного матеріалу;
Кмр = 3 — коефіцієнт залежності від матеріалу різця;
Кх = 0,75 — коефіцієнт залежності від характеру обробка поверхні;
Кох = 1 — коефіцієнт залежності від застосування охолодження.
Розрахунок частоти обертання деталі
(3,44)
Знаходження верстатної частоти обертання деталі
nв = 1800 об/хв Розрахунок основного часу
(3,45)
Знаходження допоміжного часу, пов’язаного з проходом Т" д2 = 0,6 хв Перехід В Замінити різець прохідний на різець різьбонарізний Тд3 = 1,1 хв Розрахунок режимів
Розрахунок довжини обробки
L= l + l1+ l2 = 12+2+0=14 мм, (3,46)
Знаходження верстатної подачі
Sвр = 1,5 мм/об Знаходження табличної швидкості різання
= 36 м/хв
= 64 м/хв Розрахунок скорегованої швидкості різання
=• Км • Кмр • Кх • Кох =36 •1,31 •3,0 •0,85 • 1 = 150,3 м/хв (3,47)
=• Км • Кмр • Кх • Кох =64 •1,31 •3,0 •0,85 • 1 =267,24 м/хв (3,48)
Розрахунок частоти обертання деталі
(3,49)
(3,50)
Вибір верстатної частоти обертання
nв = 1800 об/хв
nв = 1800 об/хв Розрахунок основного часу
(3,52)
(3,53)
Знаходження допоміжного часу пов’язаного з проходом Тд2 = 0,6 хв Тд2 = 0,6 хв Розрахунок загального основного часу
(3,54)
Розрахунок загального допоміжного часу Тд=Тд1+Тд2+Т" д2+Тд3+Тд4+Тд4=0,8+0,6+0,6+0,05+0,6+0,6=
=3,25 хв Розрахунок оперативного часу Топ = ТО + Тдоп = 0,09 + 3,25 = 3,34 хв (3,55)
Розрахунок додаткового часу
(3,56)
де Кдод=6,5% - коефіцієнт додаткового часу від оперативного [5, табл. 25]
Розрахунок штучного часу Тшт = Топ + Тдод = 3,34+ 0,22 =3,56 хв (3,57)
Знаходження підготовочно-заключного часу ТПЗ = 12 хв Знаходження технічної норми часу
(3,58)
Операція 4. Шліфувальна Шліфувати проточену поверхню: 2 — від діаметру 17,1 мм до діаметру 17 мм на довжину 26 мм.
Перехід, А Допоміжний час на встановлення, кріплення і зняття деталі
Тд1=0,9 хв Перехід 1
Розрахунок режимів
D=17,1 мм — діаметр поверхні до точіння;
d=17 мм — діаметр поверхні після точіння;
Розрахунок припуску на шліфування [2]
(3,59)
Розрахунок припуску на чорнове шліфування [2]
= 0,8 0,04 мм (3,60)
Розрахунок припуску на чистове шліфування [2]
= 0,2 0,01 мм (3,61)
Визначення глибини різання
0,020 мм
0,005 мм Визначення повздовжньої подачі в частках ширини круга
= 0,50 мм — при чор. оброб.
=0,25 мм — при чис. оброб Розрахунок поздовжньої подачі
= = 0,5 16 = 8 мм/об при чор. обр. (3,62)
= 0,25 16 = 4 мм/об при чис. обр. (3,63)
Кількість проходів.
= = = 2 — при чор. обробці (3,64)
= = = 2 — при чис. обробці. (3,65)
Знаходження теоретичної швидкості різання.
= 8 м/хв — теор. шв. при чор. обр.
= 20 м/хв — теор. шв. при чис. обр.
Розрахунок скорегованої швидкості
= = 8 1 1 = 8 м/хв (3,66)
= = 20 1 0,75 = 15 м/хв (3,67)
Розрахунок частоти обертання деталі
= 318 = 149,6 м/хв (3,68)
= 318 = 374,1 м/хв (3,69)
Знаходження верстатної частоти обертання деталі
Знаходження довжини шліфуємої поверхні
l = 26 мм Розрахунок величини врізання і перебігу в одну сторону
l = 0,5 = 0,5 16 = 8 мм (3,70)
L = 26 + 8 + 0 = 34 мм (3,71)
= 1,3 — коефіцієнт зачисних ходів
= 1,25.
Розрахунок основного часу;
На чорнову обробку:
= L = 34 = 0,07 хв (3,72)
На чистову обробку:
= L = 34 = 0,06 хв (3,73)
Розрахунок основного часу на операцію
= + = 0, 07 + 0, 06 = 0, 13 хв (3,74)
Розрахунок допоміжного часу, пов’язаного з обробкою:
при чорновому шліфуванні.
= + (- 1) = 1,6 + 0,06 (2 — 1) = 1, 66 хв (3,75)
при чистовому шліфуванні:
= + (- 1) = 0,8 + 0,06 (2 — 1) = 0,86 хв (3,77)
Розрахунок допоміжного часу на шліфування:
= + + = 0,9 + 1,66 + 0,86 = 3,42 хв (3,78)
Розрахунок оперативного часу Топ = ТО + Тдоп = 0,13 + 3,42 = 3,55 хв (3,79)
Розрахунок додаткового часу
(3,80)
де Кдод=9% - коефіцієнт додаткового часу від оперативного [5, табл. 25]
Розрахунок штучного часу Тшт = Топ + Тдод = 3,55+ 0,32 =3,87 хв (3,81)
Знаходження підготовочно-заключного часу ТПЗ = 8 хв Знаходження технічної норми часу
(3,82)
Список джерел
1. Гурвич И. С. Методика технического нормирования в ремонтном производстве. — Ростов-Дон, 1986;293 с.
2. Кузьмінський В. З. Методичний посібник для виконання курсових проектів з предмету Ремонт машин. — Житомир, 2001;34с
3. Клебанов Б. В. Ремонт автомобилей. — М.: Транспорт, 1968;360 с.
4. Румянцев С. И., Бортов В. Ф. Ремонт автомобилей. — М.: Транспорт, 1981;462 с.
5. Канарчук В. Е. Техническое обслуживание, ремонт и хранение автотранспортных средств. — Київ: Вища шк., 1991;359 с.
6. Тайц В. Г. Ремонт подъемно-транспортных, строительных и дорожных машин. — М.: Академия, 2007;336 с.
7. Карагодин В. И. Ремонт автомобилей и двигателей. — М.: Академия, 2003 — 496 с.
8. Годик Е. И. Хаскин А.М. Справочное руководство по черчению. — М.: Машиностроение, 1974;660 с.
9. Данилевский В. В. Технология машиностроения.-М.: Москва, Высшая школа, 1984;416 с.
10. Горошкин А. К. Приспособления для металорежущих станков. — М.: Машиностроение, 1974;384 с.
11. Роговцев В. Л. Автомобили и тракторы. — М.: Транспорт, 1986 — 311 с.
12. Родичев В. А., Родичева Г. И. Тракторы и автомобили. — М.: Агропромиздат, 1986;251 с.
13. Гуревич А. М., Сорокин Е. М. Тракторы и автомобили. — М.: Колос, 1978;479 с.
14. Примак Т. О Економіка підприємства. — М.: Викар, 2003 — 219 с.
15. Стрюков Б. Ф. Экономика, организация и планирование эксплуатации и ремонта дорожных машин. — М.:Транспорт, 1984;216 с.
16. Шваб Л.І. Економіка підприємства. — Київ: Каравела, 2005 — 568 с.
17. Дудников А. А. Основы стандартизации, допуски, посадки и технические измерения.-М.: Агропромиздат, 1989 — 176 с.
18. Панчук Б. М. Допуски та посадки.-Житомир.
деталь маршрут дефект режим